Разработка технологического процесса изготовления детали Шестерня




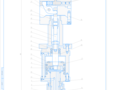
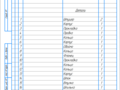
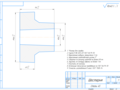
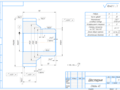
- Добавлен: 24.01.2023
- Размер: 851 KB
- Закачек: 2
Описание
Состав проекта
![]() |
![]() ![]() ![]() ![]() |
![]() ![]() ![]() |
![]() ![]() ![]() ![]() |
![]() ![]() ![]() ![]() |
![]() ![]() ![]() ![]() |
![]() ![]() ![]() ![]() |
![]() ![]() ![]() ![]() |
![]() |
![]() ![]() ![]() |
![]() ![]() ![]() |
![]() ![]() ![]() |
![]() ![]() ![]() |
![]() ![]() ![]() |
![]() ![]() ![]() |
![]() ![]() ![]() |
![]() ![]() ![]() ![]() |
Дополнительная информация
Оправка.cdw

Пояснительная_записка.docx
Определение типа производства9
Выбор оборудования и технологической оснастки12
Проектирование маршрутной технологии13
1. Разбивка на этапы операции13
1. Составление совмещенной схемы обработки и граф-дерева размерных связей15
2. Расчет операционных припусков операционных размеров18
3. Расчет размеров заготовки20
Расчет режимов резания на основные операции механической обработки21
Расчет норм времени27
Проект станочного приспособления28
1. Описание конструкции приспособления28
2. Расчет на точность30
Список использованной литературы35
Машиностроительный комплекс как и вся промышленность в настоящее время развивается под влиянием преобразований обеспечивающих переход к рыночной экономике. Одной из сложных проблем для машиностроения остается новый этап развития после падения объемов производства проблем с неплатежами и т.п.
В настоящий момент машиностроительной отрасли предстоит повысить эффективность собственного производства путем совершенствования техники углубления специализации улучшения структуры парка металлорежущего оборудования роста производительности труда и рационального использования основных производственных фондов и других материальных ресурсов. Дальнейший рост производительности труда в машиностроении во многом определяется уровнем механовооруженности труда количественными и качественными показателями парка металлообрабатывающего оборудования пополнения его современными автоматизированными и высокоточными металлообрабатывающими станками и машинами – важнейшая государственная задача в решении которой должны принимать активное участие все организации и предприятия занимающиеся вопросами технического перевооружения. Повышение эффективности производства в машиностроении требует значительного увеличения выпуска автоматизированного оборудования и в первую очередь станков с ЧПУ.
Применение станков с ЧПУ обеспечит высокую степень автоматизации обработки деталей повышение производительности труда и качества выпускаемой продукции а также позволит снизить себестоимость изделий за счет снижения времени обработки и возможность использования менее квалифицированной рабочей силы исключить изготовление большого количества оснастки на проектируемом участке.
Технологической оснасткой в машиностроении называют дополнительные устройства к технологическому оборудованию применяемые при выполнении технологических операций (обработка заготовок сборка изделий контроль и др.).
Сложность построения технологических процессов в машиностроении обусловливает большое разнообразие конструкций приспособлений и высокий уровень предъявляемых к ним требований. Неправильные технологические и конструктивные решения при изготовлении приспособлений приводят к удлинению сроков подготовки производства к снижению его эффективности.
Использование приспособлений способствует: повышению производительности и точности обработки сборки и контроля; облегчению условий труда рабочих; строгой регламентации длительности выполняемых операций; расширению технологических возможностей оборудования; повышению безопасности работы и исключению аварий. При использовании приспособлений снижается потребная квалификация и численность рабочих.
Повышение производительности достигается путем устранения разметки заготовок сокращение вспомогательного времени на их установку и снятие применение многоинструментальной и многоместной обработки а также повышение режимов резания в результате увеличения жесткости технологической системы.
Применение приспособлений расширяет использование обычных универсальных станков. Так например вертикально-сверлильными станками часто заменяют расточные. Одношпиндельные сверлильные станки оснащенные многошпиндельными головками заменяют многошпиндельные станки.
Очень часто быстрая замена устаревшего оборудования бывает невозможна. В этом случае повысить производительность труда можно применяя приспособления.
Использование приспособлений снижает себестоимость продукции. Затраты на изготовление приспособлений специального назначения ограничивают однако их употребляют в производствах с малой программой выпуска изделий. Целесообразность применения этих приспособлений должна в каждом случае подтверждаться экономическими расчетами.
Приспособления должны быть удобными для работы и быстродействующими достаточно жесткими для обеспечения заданной точности рациональными с точки зрения техники безопасности удобными для установки на станок что особенно важно при периодической смене приспособлений в серийном производстве простыми и дешевыми в изготовлении доступными для ремонта и смены изношенных деталей.
Описание детали анализ ее технологичности
Технологичность – это свойство конструкции изделия обеспечивать минимизацию затрат на всех основных стадиях жизненного цикла изделия (проектирование изготовление эксплуатация ремонт утилизация).
Проведем количественную оценку технологичности детали. Количественная оценка предполагает получение коэффициентов анализируя которые для двух однотипных деталей можно сделать вывод какая из них более технологична.
В качестве основных коэффициентов используют [1 стр. 39]:
Коэффициент средней точности:
Ti –квалитет точности i-ой поверхности.
Коэффициенты средней шероховатости:
ni – число размеров или поверхностей для каждого параметра шероховатости.
Raср = (32*6+63*7)(6+7) = 49
И коэффициент точности и коэффициент шероховатости меньше 1 следовательно деталь технологична.
Характеристика материала детали
Химический состав и механические свойства стали 45 ГОСТ 1050-88
Заменитель: 40Х 50 50Г2
Классификация : сталь конструкционная углеродистая качественная
Применение: вал-шестерни коленчатые и распределительные валы шестерни шпиндели бандажи цилиндры кулачки и другие нормализованные улучшаемые и подвергаемые поверхностной термообработке детали от которых требуется повышенная прочность.
Таблица 1. Химический состав в % стали 45
Технологические свойства Стали 45
Свариваемость: трудносвариваемая.
Флокеночувствительность: малочувствительна.
Склонность к отпускной хрупкости: не склонна.
Механические свойства при Т=20°С стали 45
В = 600МПа - Предел кратковременной прочности
T = 355Мпа - Предел пропорциональности (предел текучести для остаточной деформации)
= 16% - Относительное удлинение при разрыве
= 40% - Относительное сужение
HB 10-1 = 229МПа - Твердость по Бринеллю
Определение типа производства
Тип производства оказывает решающее влияние на особенности его организации управления и экономические показатели. Организационно-технические особенности типа производства влияют на экономические показатели предприятия на эффективность его деятельности.
Таблица 2. Характеристики типов производства в сравнении
Одно или несколько изделий
Повторяемость выпуска
Периодически повторяется
Постоянно повторяется
Применяемое оборудование
Универсальное частично специальное
В основном специальное
Расположение оборудования
Разработка технологического процесса
Укрупненный метод (на изделие на узел)
Подетально-пооперационная
Применяемый инструмент
Универсальный в значительной степени специальный
Универсальный и специальный
Преимущественно специальный
Закрепление деталей и операций за станками
Специально не закреплены
Определенные детали и операции закреплены за станками
На каждом станке выполняется одна и та же операция над одной деталью
Квалификация рабочих
В основном невысокая но имеются рабочие высокой квалификации (наладчики инструментальщики)
Себестоимость единицы изделия
Серийное производство — наиболее распространенный тип производства.
Характеризуется постоянством выпуска довольно большой номенклатуры изделий. При этом годовая номенклатура выпускаемых изделий шире чем номенклатура каждого месяца. Это позволяет организовать выпуск продукции более или менее ритмично. Выпуск изделий в больших или относительно больших количествах позволяет проводить значительную унификацию выпускаемых изделий и технологических процессов изготовлять стандартные или нормализованные детали входящие в конструктивные ряды большими партиями что уменьшает их себестоимость.
Серийный тип производства характерен для станкостроения производства проката черных металлов и т.п.
Организация труда в серийном производстве отличается высокой специализацией. За каждым рабочим местом закрепляется выполнение нескольких определенных деталеопераций. Это дает рабочему хорошо освоить инструмент приспособления и весь процесс обработки приобрести навыки и усовершенствовать приемы обработки.Особенности серийного производства обуславливают экономическую целесообразность выпуска продукции по циклически повторяющемуся графику.
Подтипы серийного производства:
Мелкосерийное тяготеет к единичному а крупносерийное — к массовому. Это деление носит условный характер. Например в соответствии с классификацией предложенной Вудворд выделяются единичное и мелкосерийное производство (Unit Production) массовое (Mass Production) и непрерывное (Process Production).
Производство мелкосерийное является переходным от единичного к серийному. Выпуск изделий может осуществляться малыми партиями.
Для изготовления стакана в качестве заготовки можно принять прокат круглого сечения или штампованную заготовку. Исходя из требований задания выбираем штампованную заготовку.
В качестве исходных заготовок для штамповки применяют слитки и прокат. В результате обработки изменяется структура исходной заготовки: при ковке слитка возникает волокнистая макроструктура при обработке деформированного полуфабриката исходные волокна изменяют направление и ориентируются по течению металла и форме изделия. Поскольку волокнистая структура определяет анизотропию механических свойств изделия рекомендуется учитывать направление волокон в заготовке. Волокна должны либо огибать контур детали либо совпадать с направлением максимальных эксплуатационных напряжений в детали. Перерезать волокна при механической обработке поковок крайне нежелательно.
Горячая объёмная штамповка поковок осуществляется в штампах. Штамп состоит из двух разъёмных частей внутренние полости которых в собранном виде образуют ручьи. Течение металла при деформации ограничивается формой и размерами внутренней полости штампа. Получаемые поковки отличаются высокой точностью размеров большей сложностью конфигурации хорошим качеством поверхности и меньшими допусками. Следовательно штамповка обеспечивает значительную экономию металла снижает трудоёмкость обработки в кузнечном цехе и при последующей механической обработке повышает коэффициент использования металла и увеличивает производительность оборудования.
Выбор оборудования и технологической оснастки
Выбор модели станка прежде всего определяется его возможностью обеспечить точность размеров и формы а также качество поверхности изготовляемой детали. Если эти требования можно обеспечить обработкой на различных станках определенную модель выбирают из следующих соображений:
Соответствие основных размеров станка габаритам обрабатываемой деталей устанавливаемых по принятой схеме обработки;
Соответствие станка по производительности заданному масштабу производства;
Возможность работы на оптимальных режимах резания;
Соответствие станка по мощности;
Возможность механизации и автоматизации выполняемой обработки;
Наименьшая себестоимость обработки;
Реальная возможность приобретения станка;
Необходимость использования имеющихся станков.
Проектирование маршрутной технологии
1. Разбивка на этапы операции
Данный технологический процесс изготовления стакана состоит из ряда операций последовательность выполнения которых обусловлена условиями технологической целесообразности получения обработки поверхностей заготовки. Процесс изготовления детали происходит в нескольких цехах и включает ряд операций:
Контроль геометрических параметров заготовки химического состава исследование на наличие раковин и трещин производится на столе ОТК
Протачивается наружный диаметр предварительно
Подрезается торец и растачивается внутренний диаметр
Подрезаются торцы с другой стороны и протачивается наружный диаметр
Шлифуется наружный диаметр
0 Внутришлифовальная
Шлифуется внутренний диаметр
Контроль геометрических параметров всех обработанных поверхностей и отверстий заготовки
5 Консервация и упаковка
Консервация помещением в пленочный чехол с осушителем – силикагелем. Для упаковки используют потребительскую и транспортную тару.
Базирование - это придание детали требуемого положения относительно траектории режущей кромки инструмента.
База - это элемент заготовки (поверхность ось точка) который используют для базирования.
Базы которые выбирает технолог для ориентации детали при ее установке в приспособление или на стол станка называются установочными или технологическими.
Назначение базирования - обеспечить точность тех размеров которыми обрабатываемая поверхность задана относительно других элементов детали на чертеже или эскизе операции.
В серийном и массовом производстве точное положение детали в рабочей зоне станка обеспечивается установкой ее в специальное приспособление и определенным положением приспособления относительно траектории режущей кромки инструмента. Последнее условие обеспечивается наладкой станка на необходимые размеры.
На станке налаженном на выполнение операции все детали партии занимают одинаковое положение относительно инструмента. Поэтому у всей партии деталей получают заданные размеры с необходимой точностью при условии прилегания базовых поверхностей заготовки к опорным элементам приспособления. Деталь зажимают в этом положении на время обработки.
Работа на станке налаженном на операцию требует минимальных затрат времени на базирование т.к. исключает разметку и выверку каждой заготовки относительно инструмента.
Выбирая схему базирования заготовки технолог ориентируется на несколько основополагающих принципов с которыми студенты знакомятся
при изучении дисциплины «Технология машиностроения». В этой работе не ставится цель сформировать окончательно это комплексное умение. Решая данную задачу необходимо научиться выбирать схему базирования во-первых в зависимости от числа размеров для наладки станка на операцию во- вторых в зависимости от конфигурации детали.
Первое умение основано на знании «правила шести точек» и понятии о полном и неполном базировании. Второе умение опирается на знание основных принятых в технике схем базирования.
Принцип базирования детали должен строго соответствовать ГОСТ 21495-76. Составляем маршрут обработки и сводим его в таблицу.
При выборе технологических баз руководствуются рядом общих положений. Наибольшая точность достигается при использовании на всех операциях одних и тех же баз то есть при соблюдении принципа единства баз. Желательно совмещать технологические базы с измерительными базами. При совмещении технологических и измерительных баз погрешность базирования равна нулю. Выбранные технологические базы совместно с зажимными устройствами должны обеспечить правильное базирование и надежное крепление заготовки гарантирующее неизменность ее положений во время обработки а также простую конструкцию приспособления удобство установки и снятия заготовки. Необходимо найти такую схему установки при которой погрешность базирования по выдерживаемым размерам равна нулю. Если по тем или иным причинам это не удается то схема установки считается приемлемой при условии что погрешность базирования на превышает допуска на размер выдерживаемого на выполняемом технологическом переходе.
Исходными данными для назначения технологических баз являются:
сборочный чертеж изделия;
объем выпуска продукции;
наличие и состояние технологического оборудования;
оснащенность приспособлениями;
оснащенность режущим инструментом;
оснащенность измерительным инструментом;
квалификация рабочих.
При разработке технологической документации технолог должен соблюдать принципы совмещения и постоянства баз.
Суть принципа совмещения состоит в том что в качестве технологических баз следует назначать поверхности которые одновременно являются конструкторскими и измерительными базами.
Основное преимущество данного принципа в том что точность не зависит от размеров получаемых при выполнении предыдущих операций. Однако часто расположение конструктивных элементов не позволяет выдержать принцип совмещения полностью либо возникает необходимость применения сложной технологической оснастки на отдельных операциях.
Нарушение принципа совмещения баз приводит к удорожанию процесса обработки и снижению производительности. Если технологическая база не совпадает с конструкторской или измерительной возникает необходимость замены размеров заданных конструкторской документацией более удобными технологическими размерами проставленными от технологических баз. Это приводит к образованию технологических размерных цепей и соответственно требуется ужесточение некоторых конструкторских размеров отсюда удорожание процесса. Поэтому и нужно придерживаться принципа совмещения везде где позволяет расположение конструктивных элементов.
Принцип постоянства баз.
При разработке и реализации технологического процесса необходимо стремиться к использованию одного и того же комплекта технологических баз на всех операциях изготовления изделия (детали).
Смена технологических баз по ходу технологического процесса приводит к увеличению длины технологических размерных цепей увеличивая тем самым погрешности обработки.
При обработке сложных многочисленных поверхностей полностью обеспечить принципы совмещения и постоянства баз практически невозможно. В любом случае при выборе установочных и направляющих баз предпочтение отдают конструктивным элементам с наибольшими габаритными размерами и точностью наложенных размерных связей.
На точность и экономичность установки кроме размерной характеристики оказывает влияние доступность конструктивных элементов которые выполняют функцию баз. Само собой разумеется что поверхность открытая для контакта и сопряжения по всем координатным направлениям будет наиболее удобна в качестве базы.
Также точность и удобство базирования зависят от формы базовых элементов. Приоритет конструктивных элементов при выборе баз следующий:
призматические (с плоскими поверхностями);
конические (с центрирующими и направляющими поверхностями);
цилиндрические (с направляющими и опорными поверхностями);
фасонные (со сложной конфигурацией).
Когда конструктивные элементы не могут служить базами обеспечивающими требуемую точность установки можно применять элементы искусственно созданные исключительно для базирования. Самый яркий пример искусственных баз – центровые отверстия валов создаваемые для их базирования при изготовлении.
Технологические базы бывают черновые и чистовые. Черновые базы являются необработанными и используются на первой операции технологического процесса. Отсюда следуют особые требования к этим базам:
черновые базы в связи со своей низкой точностью должны использоваться только один раз на первой установке;
для обеспечения правильного взаимного положения обработанных и необработанных поверхностей в готовом изделии черновыми базами необходимо назначать поверхности которые в готовом изделии остаются черновыми.
1. Составление совмещенной схемы обработки и граф-дерева размерных связей
Рисунок 1. Схема обработки
Рисунок 2. Совмещенный граф
Таблица3. Выявление размерных цепей
Последовательность вершин графа
Уравнение размерной цепи
Проверка на обеспечение точности конструкторских размеров
7 ≥ 087Условие выполнено;
3 ≥ 043Условие выполнено;
≥ 087-087+03=03 Условие выполнено;
2. Расчет операционных припусков операционных размеров
Расчет аналитическим методом
Таблица 5. Этапы обработки
Т.к. с0 = 1 ρ1 = Δу х l
ρ1 = Δу х l = 13 х 100 = 130мкм
ρ2 = ρ1 х Ку2 = 130 х 005 = 6мкм
ρ3 = ρ2 х Ку3 = 6 х 002 = 01мкм = 0мкм
З2 = 005 х 31 = 005х70 = 35мкм
З3 = 005 х 32 = 005х35 = 0мкм
zmin2 = 2(Rz1 + T1 +) = 2(40+60 +) = 448мкм = 0448мм
zmin3 = 2(Rz2 + T2 +) = 2(40+60 +) = 212мкм = 0212мм
Dmax3 = 60 + 0030 = 60030мм
Dmax2 = Dmax3 - 2zmin3 = 60030 – 0212 = 59818мм
Dmax1 = Dmax2 - 2zmin2 = 59818 – 0448 = 59370мм
Dmin2 = Dmax2 - es2 = 59818 – 012 = 59698мм
Dmin1 = Dmax1 - es1 = 59370 – 0300 = 59070мм
3. Расчет размеров заготовки
Таблица 6. Размеры детали и заготовки
Размер после перехода
Расчет режимов резания на основные операции механической обработки
Табличным методом рассчитаем режимы резания на операции 015 и 020.
Операция 015 Автоматная.
Исходные данные для расчета: инструменты: резец 2103-0701 Т5К10 ГОСТ 20872-80 резец 2151-0020 Т5К10 ГОСТ 21151-75 – 2 штуки.
Уточняем подачи по паспорту станка:
Стойкость инструмента:
Скорость резания находим по формуле:
где VТ - скорость резания табличная;
k1 - коэффициент учитывающий свойства обрабатываемого материала;
k2 - коэффициент учитывающий материал инструмента;
k3 - коэффициент учитывающий свойства поверхностного состояния заготовки.
k1=075; k2=105; k3=10
VT1=100 ммин; VT2=105 ммин
Подставим значения в формулу:
V1= 100×075×105×10=788 ммин
V2=105×075×105×10=827 ммин
Частота вращения шпинделя находим по формуле:
Корректируем частоту вращения по паспорту станка n=200 мин-1.
Фактическая скорость резания находим по формуле:
Подставив значения получаем:
Минутная подача находится по формуле:
SM1=048×200=96 мммин
SM2=024×200=48 мммин
Главная составляющая силы резания находим по формуле:
где Pz-табличное значение главной составляющей силы резания;
k1- коэффициент учитывающий свойства обрабатываемого материала;
k2- коэффициент учитывающий скорость резания и материал инструмента.
Pz1табл=340H Pz2табл=250Н
Подставив эти значения в формулу получаем:
Pz2=250×085×10=2125Н
Эффективная мощность резания определяется по формуле:
Подставляем все значения и получаем:
Определяем основное время по формуле:
Операция 020 Автоматная.
Исходные данные для расчета: инструменты: резец 2103-0701 Т5К10 ГОСТ 20872-80 резец 2151-0020 Т5К10 ГОСТ 21151-75.
Таблица 7. Сводная таблица норм времени
Наименование операции
Вспомогательное время
Проект станочного приспособления
1. Описание конструкции приспособления
Приспособление с гидромассой с применение пневмоцилиндра используется для установки по наружной или внутренней поверхности деталей обрабатываемых на токарных фрезерных и др. станках. На приспособление с тонкостенной втулкой обрабатываемые детали наружной или внутренней поверхностью устанавливают на цилиндрическую поверхность втулки. При разжиме втулки гидропластом детали центрируются или зажимаются. Приспособление обеспечивает быстрый зажим обрабатываемой детали по сравнению с ручным закреплением за счёт подачи сжатого воздуха в пневмоцилиндр обеспечивают регулирование и контроль силы зажима заготовки удобны в направлении и не требуют приложения больших физических усилий.
Приспособление состоит из:
Тонкостенной втулки;
Пневмоцилиндр 2-х стороннего действия;
Муфта для подачи сжатого воздуха.
Оправка базируется на столе станка.
Оправка состоит из корпуса на который посажена тонкостенная втулки упорное кольцо. В корпусе выполнены проточки и каналы заполненные гидропластмассой. Центральный канал закрыт заглушкой зафиксированной гайкой. Слева по каналу перемещается плунжер на который воздействует толкатель связанный со штоком пневмоцилиндра. При заполнении оправки гидропластмасой воздух выходит через специальные каналы которые после заполнения закрываются заглушками.
Пневмоцилиндр устанавливается с помощью промежуточного фланца и закрепляется с помощью 6-ти болтов на нём. К распределительной муфте подсоединены ниппели через которые проходит сжатый воздух и попадает в муфту а затем через установленный в муфте вал с каналами для подачи воздуха попадает в штоковую или безштоковую полость в зависимости от того закрепляется деталь или разжимается.
2. Расчет на точность
Точность центрирования оправки с гидропластом зависит от точности изготовления корпуса и втулки. Корпус изготовляют из стали 20Х с последующей цементацией и закалкой до твердости HRC 55- 58. Параметр шероховатости центровых отверстий оправки не ниже Ra=063-:-032 мкм. Биение контрольных поясков и посадочного диаметра не более 2 мкм. Для оправок диаметром до 40 мм втулку изготовляют из стали 40Х с последующей закалкой до твердости HRC 35-40 для оправок свыше 40 мм - из стали У7 с закалкой до твердости HRC 33-35. Окончательно оправку шлифуют после заливки гидропласта с небольшим поджатием его плунжером. Биение по контрольным пояскам и посадочному диаметру оправки не более 2-5 мкм.
Так как технологическая база совпадает с конструкторской погрешность базирования отсутствует.
Закрепление заготовки в приспособлении производится путем разжима цилиндра.
Усилие закрепления создаётся пневмоцилиндром и передаётся на кулачки через шток.
Для выбора размера пневмоцилидра при проектировании приспособления необходимо определить усилие резания возникающее в процессе обработки отверстия вала.
Расчёт мощности и режимов резания.
Рассчитанные режимы резания:
) Фреза червячная модульная
Режущая часть – Р6М5
φ1 = 3° φ0 = 45° γ = 20° = 15°
) Стойкость инструмента Т = 60мин КTv = 1
) Частота вращения шпинделя
n = (1000v)(D) = (1000 х 67)(314 х 50) = 4209обмин
по паспорту принимаем n = 2000обмин
) Фактическая скорость резания
vф = (Dn)1000 = 157ммин
Sмин = Sz x z х n = 005 х 3 х 1250 = 3142мммин
по паспорту принимаем Sмин = 160мммин
) Рассчитываю силу резания:
1) Назначаю поправочные коэффициенты на силу.
1.1) В зависимости от обрабатываемого материала: Кр=11
1.2) В зависимости от стойкости инструмента: Кр=09
1.3) В зависимости от диаметра инструмента: Кр=105
1.4) В зависимости от переднего инструмента: Кр=104
1.5) В зависимости от качества поверхности: Кр=087
2) Определяю силу с учётом поправочных коэффициентов:
Рисунок 3. Расчетная схема
Рассчитываю необходимое усилие закрепления заготовки:
Nз = 2Pz = 2*1176 = 2352 кг.
Рассчитываю необходимое усилие на штоке с учётом соотношения плеч рычага:
Рассчитываю диаметр пневмоцилиндра:
Усилие создаваемое пневмоцилиндром равно:
отсюда диаметр пневмоцилиндра равен:
Принимаю диаметр пневмоцилиндра по ГОСТ 6540-68 равным:
Определяю фактическое усилие на штоке по принятому диаметру пневмоцилиндра:
Рассчитываю фактическое усилие закрепления детали с учётом соотношения плеч рычага:
Проверяю условие надёжного закрепления заготовки:
Nз.ф.=316 кг. > Nз.=2352 кг.
Вывод: заготовка закреплена надёжно.
Список использованной литературы
Ансеров Ю.М. Дурнев В.Д. Машиностроение и охрана окружающей среды. – Л.: Машиностроение. Ленинградское отделение 1979-224 с. ил.
Анурьев В.И. Справочник конструктора-машиностроителя. – М.: Машиностроение 1992.
Балабанов А.И. Краткий справочник технолога-машиностроителя. – М.: Машиностроение 1992.
Баранчиков В.И. Прогрессивные режущие инструменты и режимы резания металлов. – М.: Машиностроение 1990.
Белкин И.М. Справочник по допускам и посадкам для рабочего-машиностроителя. – М.: Машиностроение 1985.
Гельфгат Ю.И. Сборник задач и упражнений по технологии машиностроения: Учебник– М.: Машиностроение 1985.
Гжиров И.Р. Краткий справочник машиностроителя. – М.: Машиностроение 1984.
ГОСТ 3.1118-82 «Формы и правила оформления маршрутных карт».
ГОСТ 3.115-82 «Формы и правила оформления операционных карт».
ГОСТ 3.1502-85 «Формы и правила оформления документации на «технологический контроль»».
Данилевский В.В. Технология машиностроения: Учебник. – М.: Высшая школа 1984.
Косилова А.Г. Справочник технолога-машиностроителя: в 2-х т. – М.: Машиностроение 1990.
Козьяков А.Ф. Охрана труда в машиностроении. – М.: Машиностроение 1990.
Нефедов Н.А. Сборник задач и примеров по резанию металлов и режущему инструменту: Учебное пособие – М.: Машиностроение 1990.
Новицкий Н.И. Организация производства на предприятиях: Учебно-методическое пособие – М.: «Финансы и статистика» 2001 г.
Ординарцев И.А. Справочник инструментальщика. – М.: Машиностроение 1990.
Родионов Б.Н. Организация планирование и управление машиностроительным производством: Учебное пособие – М.: Машиностроение 1989 г.
Силантьева Н.А. Техническое нормирование в машиностроении. – М.: Машиностроение 1990.
Наладка.cdw

Оборудование - токарный полуавтомат 1286-8
приспособление - трехкулачковый патрон
0 Токарно-автоматная
Заготовка.cdw

HB 269 321 ГОСТ 8479-70.
Неуказанные радиусы закруглений 2 мм.
Неуказанные штамповочные уклоны 5
Смещение по разъему штампов не более 0.8 мм.
Заусенец по контуру обрезки не более 1 мм.
Очистить от окалины.
Остальные технические требования по ГОСТ 8479-70
Точность изготовления
Спецификация.spw

Винт М2-2 ГОСТ 11075-93
Винт М4-10 ГОСТ 10344-80
Винт М4-12 ГОСТ 11074-93
Размерный анализ.cdw

Чертеж детали.cdw

ОК 015.doc
Оборудование устройство ЧПУ
Обозначение программы
Токарный полуавтомат 1286-8
Установить заготовку в патрон
Патрон трехкулачковый гидравлический
Обработать согласно эскизу
ОК 025.doc
Оборудование устройство ЧПУ
Обозначение программы
Шлифовальный станок 3В172
Установить заготовку на оправку
Обработать согласно эскизу
ОК 010.doc
Оборудование устройство ЧПУ
Обозначение программы
Токарный станок 16К20
Установить заготовку в патрон
Патрон трехкулачковый гидравлический
Проточить наружный диаметр как чисто
ОК 035.doc
Оборудование устройство ЧПУ
Обозначение программы
Зубофрезерный станок 5К32
Установить заготовку на оправку
МК.doc
Код наименование операции
Обозначение документа
Код наименование оборудования
Контролировать внешний вид заготовки на
отсутствие дефектов визуально
Контролировать размеры заготовки
Токарный станок 16К20
Токарный полуавтомат 1286-8
Маршрутная карта механообработки
ГОСТ 3.1118-82 Форма 1б
Наименование детали сб. единицы или материала
Шлифовальный станок 3В172
Зубофрезерный станок 5К32
Консервация и упаковка
ОК 020.doc
Оборудование устройство ЧПУ
Обозначение программы
Токарный полуавтомат 1286-8
Установить заготовку в патрон
Патрон трехкулачковый гидравлический
Обработать согласно эскизу
ОК 030.doc
Оборудование устройство ЧПУ
Обозначение программы
Шлифовальный станок 3В172
Установить заготовку в патрон
Патрон трехкулачковый гидравлический
Обработать согласно эскизу
Иллюстрация ТП.cdw

Рекомендуемые чертежи
- 04.06.2017
- 13.12.2022
- 24.01.2023