Разработка технологическо процесса деталей вала маховика и корпуса пневмоцилиндра. Проектирование механического цеха




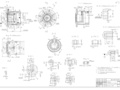
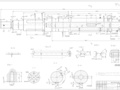
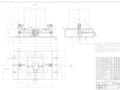
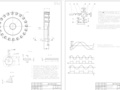
- Добавлен: 24.01.2023
- Размер: 3 MB
- Закачек: 1
Описание
Состав проекта
![]() |
![]() ![]() ![]() ![]() |
![]() ![]() ![]() ![]() |
![]() ![]() ![]() ![]() |
![]() ![]() ![]() ![]() |
![]() ![]() ![]() ![]() |
![]() ![]() ![]() |
![]() ![]() ![]() ![]() |
![]() ![]() ![]() ![]() |
![]() ![]() ![]() |
![]() ![]() ![]() ![]() |
Дополнительная информация
Схемы наладок обработки корпуса пневмоцилиндра.ЛИСТ 7, 8.dwg

Оборудование: Токарно-карусельный станок 1508.
Операция 015. Фрезерная.
Оборудование: Широкоуниверсальный
консольный станок 6Р83Ш
Таблица режимов резания и норм времени
Резец автоматный про-
Резец токарный проход-
Резец токарный подрез-
Операция 020. Сверлильная.
Оборудование: Радиально-сверлильный
Сверло спиральное с
коническим хвостовиком
Сверло для обрабтки
глубоких отверстий с
цилиндрической резьбы
Метчик для метричес-
Зенковка цилиндрическая
с направляющей цапфой
Зенковка центровочная
Режущий и измерительный инструмент ЛИСТ10, 11..dwg

ГОСТ 4543-71. Твердость 32
Материал ножей-твердый сплав Т5К10
по ГОСТ 2209-82. Твердость 88 HRA.
Материал клиньев-сталь У8А по
ГОСТ 1435-74. Твердость 41
Неуказанные предельные отклонения-
отверстий Н14; валов остальных
размеров ±IT142 по ГОСТ 25347-82.
Маркировать на ножах: марку стали
диаметр и длину фрезы
завода изготовителя (Т5К10-250 45- )
Фреза торцевая насад-
Схема контроля размера шейки вала
ø150k6 интерферометром со
счетом полос на основе частотной
зационная призма-куб
-измерительный отражатель
-блок управления и обработки
В качестве регестрирующего устройства
изменения входной величины служит
мультиплексный интерференционный
волоконно-оптический датчик.
интерференционных сигналов.
Корпус пневмоцилиндра. ЛИСТ2..dwg

допускаются раковины.
* Размеры для справок.
** Размеры обеспечиваются
Вал маховика. ЛИСТ1..dwg

* Размеры обеспечить инструментом.
Заготовка вала маховика. ЛИСТ3..dwg

Твердость 174 203 НВ.
Неуказанные отклонения
радиального биения - 5мм.
Класс точности изготовления - Т4
сложности - С1. ГОСТ 7505-89.
Материал - сталь 40Х.
План механического цеха. ЛИСТ 12..dwg
Горизонтально-расточной
Круглошлифовальный станок
Продольно-строгальный
двухстоечный станок 7110
Внутришлифовальный станок
Копировально-фрезерный
Зубофрезерный универсальный
Фрезерно-центровальный
Токарно-карусельный станок
Радиально-сверлильный станок
Широкоуниверсальный консоль-
ный фрезерный станок 6Р83Ш
Ящики для инструмента
Место технического контроля
Пункт медицинской помощи
Помещения для инженерно-
технических работников
Токарно-револьверный
прутковый автомат 1Б136
Вертикально-сверлильный
одношпиндельный станок 2Н135
Склад реализуемых деталей
Станочное приспособление с гидравлическим приводо. ЛИСТ9.dwg

В рабочей полости цилиндра допускаются
Механический КПД цилиндра должен быть
Цилиндр должен быть герметичным при
давлении рабочей среды 150 кгссм.
Неуказанные предельные отклонения разме-
ров деталей: Н14; ±IT142.
Станочное приспособ-
ление с гидравличес-
Заготовка корпуса пневмоцилиндра. ЛИСТ4..dwg

Неуказанные литейные радиусы R5.
На необработывемых поверхностях
допускается раковины до ø3 и глубиной
Точность отливки 10 10 4 7
Материал - сталь 35Л.
Пояснительная записка.doc
Область применения – машиностроение.
Деталь "вал маховика" имеет длину – 1555 мм; диаметр – 180 мм; массу – 225 кг; материал – сталь 40Х.
Деталь "корпус пневмоцилиндра" имеет длину – 346 мм; диаметр – 470 мм; массу – 135 кг; материал – сталь 35Л.
Показатели экономической эффективности:
от реализации деталей вала маховика – 8495.45 тыс. грн.
от реализации деталей корпуса пневмоцилиндра – 10731.3 тыс. грн.
Ведомость про объем пояснительной записки: количество разделов – 12; иллюстраций – 24; таблиц – 31; приложений – 2; литературных источников – 42.
Данное внедрение при проектировании усовершенствованной технологии изготовления деталей является экономически целесообразным.
Ключевые слова: МАШИНОСТРОЕНИЕ ПРОЦЕСС СТАНКОЕМКОСТЬ ОПЕРАЦИЯ ТОЧЕНИЕ СВЕРЛЕНИЕ РАЗВЕРТЫВАНИЕ ФРЕЗЕРОВАНИЕ ШЛИФОВАНИЕ ГРУППОВАЯ ФОРМА ОРГАНИЗАЦИИ СРЕДНЕСЕРИЙНОЕ ПРОИЗВОДСТВО ТАКТ ВЫПУСКА ДЕТАЛЕЙ.
Аналитический раздел.
1. Анализ технологичности конструкций деталей вала маховика
и корпуса пневмоцилиндра 6
Технологический раздел
1. Определение типа производства и формы его организации ..9
2. Выбор и экономическое обоснование способа получения заготовок ..20
3. Выбор технологических баз деталей вала маховика и
корпуса пневмоцилиндра 23
4. Разработка маршрута обработки деталей 26
5. Определение припусков на обработку и размеров заготовок
вала маховика и корпуса пневмоцилиндра 32
6. Выбор технологического оборудования 39
7. Определение режимов обработки заготовки вала маховика
и корпуса пневмоцилиндра 48
8. Нормирование операций технологического процесса 89
9. Проектирование схем наладок 101
Конструкторский раздел.
1. Проектирование станочного приспособления.
1.1. Расчет сил закрепления 110
1.2. Расчет точности станочного приспособления 112
1.3. Выбор гидроцилиндра и сборочных элементов приспособления 114
2. Проектирование режущего инструмента 115
1. Исследования температуры в зоне резания при точении на
2. Влияние различных факторов на температуру резания
по экспериментальным данным 130
Автоматизация технологических процессов.
1. Принцип измерения расстояний и линейных перемещений 135
2. Интерферометр со счетом полос на основе частотной модуляции 136
Организационный раздел.
1. Организация участка цеха по производству деталей вала маховика.
1.1. Определение потребного количества оборудования и его загрузка 142
1.2. Определение потребного количества основных рабочих 146
1.3. Определение потребного количества вспомогательных рабочих
2. Организация участка цеха по производству деталей корпуса
2.1. Определение потребного количества оборудования и его загрузка 149
2.2. Определение потребного количества основных рабочих 152
2.3. Определение потребного количества вспомогательных рабочих
Экономический раздел.
1. Расчет технико-экономических показателей участка
производства детали вала маховика.
1.1. Определение затрат на основные материалы 154
1.2. Фонд оплаты труда производственных рабочих 156
1.3. Расчет фонда оплаты труда вспомогательных рабочих
1.4. Калькуляция единицы продукции 159
1.5. Технико-экономические показатели участка 163
1.6. Анализ прибыльности производственной деятельности
2. Расчет технико-экономических показателей участка
производства детали корпуса пневмоцилиндра.
2.1. Определение затрат на основные материалы 168
2.2. Фонд оплаты труда производственных рабочих 170
2.3. Расчет фонда оплаты труда вспомогательных рабочих
2.4. Калькуляция единицы продукции 172
2.5. Технико-экономические показатели участка 174
2.6. Анализ прибыльности производственной деятельности
Проектирование цеха 179
Раздел охраны труда и окружающей среды.
1. Анализ опасных и вредных факторов производственного процесса 182
2. Инженерно-технические мероприятия по охране труда 184
3. Пожарная профилактика 188
Корпус пневмоцилиндра.2.
Заготовка вала маховика.3.
Заготовка корпуса пневмоцилиндра.4.
Схемы наладок обработки вала маховика.5.
Схемы наладок обработки вала маховика.6.
Схемы наладок обработки корпуса пневмоцилиндра.7.
Схемы наладок обработки копуса пневмоцилиндра.8.
Станочное приспособление с гидравлическим приводом.9.
Фреза торцевая насадная сборная.10.
Схема контроля размера шейки вала.11.
План механического цеха.12.
Машиностроение является важнейшей отраслью народного хозяйства т. к. обеспечивает технологические процессы средствами производства – машинами и механизмами. Технология машиностроения как отрасль науки изучает закономерности действующие в процессе производства машин чтобы использовать эти закономерности для обеспечения требуемого качества машин при наименьшей их себестоимости.
Основная задача отечественного машиностроения – на базе новейших достижений науки и техники и современных технологий выпускать в необходимом количестве для народного хозяйства высококачественные машины и орудия производства отвечающих требованиям и уровню мировых стандартов.
Различие машиностроительных производств определяется спецификой выпускаемого оборудования масштабами его производства. Поэтому создание обобщающих научных трудов по технологии машиностроения сочетается с работами отражающими условия и опыт отдельных машиностроительных производств. Одной из таких развитых отраслей машиностроения Украины является горное машиностроение. Заводы этого профиля действуют в Харькове Днепропетровске Горловке Донецке Краматорске Конотопе Александрии Кривом Роге и др. городах.
Горное машиностроение характеризуется широкой номенклатурой изделий что обусловлено не только большим разнообразием горных машин но и стремлением приспособить их к разнообразным горногеологическим условиям эксплуатации. В результате этого на заводах отрасли практически отсутствовало крупносерийное и массовое производство что повышало себестоимость изготовления горной техники. Снижение удельных затрат обеспечивалось постепенным повышением уровня стандартизации размеров формы и относительного расположения обрабатываемых поверхностей детали и присоединительных поверхностей сборочных единиц горных машин. Результатом этого процесса явилось изменение масштабов производства что позволило резко повысить уровень автоматизации горного машиностроения. Большое значение в настоящее время имеет широкое внедрение гибких переналаживаемых производственных систем и высокого эффективного оборудования со встроенными средствами управления и контроля на базе микропроцессорной техники.
Особенности горного машиностроения отражены в научной дисциплине "Технология производства горных машин". Горное машиностроение характеризуется широкой номенклатурой изделий большим разнообразием габаритных размеров массы горных машин и видов производства – единичного мелкосерийного серийного и массового. К горным машинам предъявляются специальные требования вытекающие из специфики условий их применения - взрывобезопасность пыленепроницаемость ограничение габаритных размеров коррозионная стойкость способность противостоять ударным нагрузкам. Все эти требования необходимо учитывать в процессе непрерывного развития и совершенствования машин приборов и механизмов для горной промышленности.
Технический прогресс в горной промышленности определяется значительным увеличением выпуска существующих горных машин и комплексов и освоением большого числа новых высокопроизводительных машин. Большое внимание при этом должно уделяться повышению качества надежности и долговечности машин а также их прогрессивному обслуживанию ремонту и монтажу.
Повышение надежности – одна из важнейших задач современности. Важность проблемы повышения надежности в широком смысле этого понятия непрерывно возрастает в связи с интенсификацией технологических процессов горного производства повышением производительности оборудования и увеличением воздействующих на него нагрузок.
АНАЛИТИЧЕСКИЙ РАЗДЕЛ.
1. АНАЛИЗ ТЕХНОЛОГИЧНОСТИ КОНСТРУКЦИИ ДЕТАЛЕЙ ВАЛА МАХОВИКА И КОРПУСА ПНЕВМОЦИЛИНДРА.
Обработка конструкции на технологичность представляет собой комплекс мероприятий по обеспечению необходимого уровня технологичности конструкций по установленным показателям направлена на повышение производительности труда снижение затрат и сокращение времени на изготовление изделия при обеспечении необходимого качества.
Технологическому контролю подлежат чертежи двух деталей взятые из узла включения пресса вал маховика и корпус пневмоцилиндра. Для оценки количественных показателей технологичности (ГОСТ 14.201 – 83) определяем коэффициент унификации конструктивных элементов
гдеQу.э. – число унифицированных типоразмеров конструктивных элементов (резьбы фаски отверстия шпонки и пр.);
Qэ. – число конструктивных элементов в детали.
Коэффициент использования материала
гдеmд – масса детали кг;
mз – масса заготовки кг.
Коэффициент унификации конструктивных элементов
Для корпуса пневмоцилиндра
Числовые значения коэффициентов должны лежать в пределе 0K1. Условие выполняется.
Соответственно ГОСТу 2.121 – 73 качественная оценка технологичности конструкции характеризуется следующими показателями: хорошо (допустимо) плохо (недопустимо). Каждый показатель оценивается знаком "+" или "-". Качественный анализ технологичности конструкции деталей выполняют соответственно таблице 1.1.
Результат качественного анализу технологичности конструкции деталей.
Показатели технологичности конструкции деталей
Оценка технологичности вала маховика
Оценка технологичности корпуса пневмоцилиндра
Наличие у деталей стандартных и унифицированных элементов.
Возможность изготовления деталей из стандартных или унифицированных заготовок (прокат штамповка литье и т. д.).
Наличие оптимальной точности и шероховатости поверхностей.
Соответствие физико-химических и механических свойств материала твердости формы и размеров детали требованиям технологии механической и термической обработки.
Соответствие показателей базовых поверхностей детали (размеры точность шероховатость) требованиям установки обработки и контролю
Соответствие оформления рабочего чертежа детали требованиям ЕСКД и ЕСДП СЭВ.
ТЕХНОЛОГИЧЕСКИЙ РАЗДЕЛ.
1. ОПРЕДЕЛЕНИЕ ТИПА ПРОИЗВОДСТВА И ФОРМЫ ЕГО ОРГАНИЗАЦИИ.
Тип производства определим взяв за основу массу деталей и годовой объем выпуска деталей.
Масса детали вала маховика – 225 кг годовая программа выпуска – 800 штгод. Определяем среднесерийное производство.
Масса детали корпуса пневмоцилиндра – 135 кг годовая программа выпуска – 1000 штгод. Определяем среднесерийное производство.
Формы организации технологических процессов в соответствии с ГОСТ 14.312 – 74 зависят от установленного порядка выполнения операций расположения технологического оборудования количества изделий и направления их движения при изготовлении.
Существуют две формы организации технологических процессов – групповая и поточная. Решение о целесообразности организации поточной формы производства обычно принимается на основании сравнения заданного суточного производства выпуска изделий Nc и расчетной суточной производительности поточной линии Qс при двусменном режиме работы и ее загрузке на 75 – 85%.
Заданный суточный выпуск изделий
гдеN – годовая программа выпуска изделий шт;
3 – количество рабочих дней в году.
Для детали вала маховика
Для детали корпуса пневмоцилиндра
Суточная производительность поточной линии
гдеFc – суточный фонд времени работы оборудования (при двусменном режиме работы – 960мин);
Tср – средняя станкоемкость основных операций мин;
з – коэффициент загрузки оборудования – 0.85.
Среднюю станкоемкость операций определим по формуле:
гдеTшт – штучное время основной
n – количество основных операций;
Kв – средний коэффициент выполнения норм времени – 1.3.
Составим ведомость выполнения основных операций обработки вала маховика (таблица 2.1).
Ведомость выполнения основных операций обработки вала маховика.
Фрезерование двух торцов
Черновая обточка за один проход
Нарезание резьбы метчиком
Штучное время по операциям определим по формуле:
гдеTo.cp. – среднее основное технологическое время;
K – коэффициент непрерывности работы станков.
Среднее основное технологическое время по операциям определим по приближенным формулам (См. [2] стр. 384).
гдеl – длина фрезерования.
Суммарное Tо.ср.=1.41мин.
Черновая проточка за один проход
гдеd – диаметр участка вала.
Суммарное Tо.ср.=41.52мин.
гдеn – количество отверстий одинакового диаметра и длины.
Суммарное Tо.ср.=28.82мин.
Суммарное Tо.ср.=1.146мин.
Суммарное Tо.ср.=2.047мин.
Определим штучное время по операциям Tшт по формуле (2.4).
Определим среднюю станкоемкость операций по формуле (2.3).
Определим суточную производительность поточной линии по формуле (2.2).
Суточная производительность поточной линии больше суточного выпуска деталей поэтому применяем групповую форму организации производства.
При групповой форме организации производства запуск изделий производится с определенной периодичностью а = 3 6 12 24 дня. По упрощенной формуле определим количество деталей в партии:
Величину партии уточним следующим образом:
Определим расчетное число смен на обработку всей партии деталей на основных рабочих местах и округлим до ближайшего целого числа:
гдеTшт. ср. – среднее штучное время по основным операциям мин;
0 – расчетный фонд времени работы станка;
85 – коэффициент загрузки станка.
Определим принятое число деталей в партии
гдеFд – годовой действительный фонд работы станка ч; при односменной работе ч;
m – число смен работы станка в сутки;
N – годовая программа выпуска деталей шт.
Составим ведомость выполнения основных операций обработки корпуса пневмоцилиндра (таблица 2.2).
Штучное время по операциям определим по формуле (2.4)
Суммарное Tо.ср.=3.29мин.
Суммарное Tо.ср.=7.76мин.
Суммарное Tо.ср.=4.33мин.
Суммарное Tо.ср.=12.26мин.
Суммарное Tо.ср.=5.4мин.
Суммарное Tо.ср.=0.22мин.
Суммарное Tо.ср.=12.92мин.
При групповой форме организации производства запуск изделий производится с определенной периодичностью а = 3 6 12 24 дня. По упрощенной формуле определим количество деталей в партии по формуле (2.11)
Определим расчетное число смен на обработку всей партии деталей на основных рабочих местах и округлим до ближайшего целого числа по формуле (2.12)
2. ВЫБОР И ЭКОНОМИЧЕСКОЕ ОБОСНОВАНИЕ СПОСОБА ПОЛУЧЕНИЯ ЗАГОТОВОК.
При выборе способа получения заготовки главным образом нужно обеспечить необходимое качество детали при ее минимальной себестоимости. На выбор способа получения заготовки большое влияние оказывают: конфигурация размеры масса марка материала необходимая точность и качество поверхностей заготовки тип производства.
Способ получения заготовки вала маховика выбираем на основании технико-экономического анализа двух возможных вариантов.
По двум вариантам определим массу заготовки с учетом припусков и напусков на механическую обработку. Приблизительно масса заготовки определяется по формуле:
где Q – масса детали;
П – процент отхода материала в стружку.
Вариант 1. Вид заготовки – штамповка.
гдеP1 – оптовая цена за 1 кг заготовки по прейскуранту P1 = 30 грн;
Kт – коэффициент который учитывает транспортно-заготовительные затраты равный 1.05;
д – масса реализованных отходов;
P2 – цена 1 кг отходов P2 = 4.6 грн.
Вариант 2. Вид заготовки – поковка.
Разница между стоимостью выбранных заготовок
Определим основную зарплату станочника
гдеОс – основная зарплата станочника за 1 мин грн.
Основная зарплата наладчика с учетом обслуживания 4-х станков.
Цеховая себестоимость
гдеН – размер цеховых накладных расходов в процентах для данного типа производства Н = 250%.
Разница между цеховой себестоимостью обработки и разницей стоимости заготовок.
Так как цеховая себестоимость механической обработки меньше чем разница стоимости заготовок то принимаем менее точную заготовку – поковку.
Годовая экономическая эффективность выбранного способа получения заготовки:
Расчеты по выбору способа получения заготовки корпуса пневмоцилиндра произведем в той же последовательности что и для детали вала маховика.
По двум вариантам определим массу заготовки с учетом припусков и напусков на механическую обработку по формуле (2.19):
Вариант 1. Вид заготовки – литье в песчаные формы.
Стоимость заготовки (2.20):
Вариант 2. Вид заготовки – литье в оболочковые формы.
Разница между стоимостью выбранных заготовок (2.21):
Определим основную зарплату станочника (2.22):
Основная зарплата наладчика с учетом обслуживания 4-х станков (2.23):
Цеховая себестоимость (2.24):
Разница между цеховой себестоимостью обработки и разницей стоимости заготовок (2.25):
Так как цеховая себестоимость механической обработки меньше чем разница стоимости заготовок то принимаем менее точную заготовку – литье в песчаные формы.
Годовая экономическая эффективность выбранного способа получения заготовки (2.26):
3. ВЫБОР ТЕХНОЛОГИЧЕСКИХ БАЗ ДЕТАЛЕЙ ВАЛА МАХОВИКА И КОРПУСА ПНЕВМОЦИЛИНДРА.
Рисунок 2.1. Схема базирования заготовки вала маховика.
В соответствии с ГОСТ 21495 – 76 базирование т. е. положение объекта относительно выбранной системы координат осуществляется с помощью выбранных на объекте баз в виде принадлежащих ему поверхностей осей точек или их сочетаний.
В процессе механической обработки при выборе технологических баз необходимо придерживаться следующих рекомендаций:
- при обработке заготовки необработанные поверхности в качестве баз можно использовать только на первых операциях;
- в качестве технологических баз следует принимать поверхности достаточных размеров что обеспечивает большую точность базирования и закрепления заготовки в приспособлении эти поверхности должны иметь более высокий класс точности наименьшую шероховатость не иметь поверхностных дефектов;
- в качестве баз на первой операции следует принимать поверхности с наименьшими припусками;
- при чистовой обработке рекомендуется соблюдать принцип совмещения баз;
- базы окончательной обработки должны иметь наибольшую точность наименьшую шероховатость поверхностей.
На первой операции механической обработки вала маховика необходимо подготовить технологические базы которые бы использовались на последующих операциях. В качестве технологических опорных баз вала выбираем поверхности В и Г (Рисунок 2.1). Для их подготовки в качестве черновых баз выбираем необработанные поверхности А и Б. Выбранные поверхности обладают достаточной протяженностью для закрепления заготовки вала в призмах которые обеспечат надежное закрепление и точность подготовки баз при фрезеровании и центровании торцов вала. На дальнейших этапах обработки в качестве чистовых направляющих баз принимаем поверхности Е и Д которые обладают более высоким классом точности и имеют наименьшую шероховатость.
Рисунок 2.2. Схема базирования заготовки корпуса пневмоцилиндра.
Пользуясь выше перечисленными рекомендациями выберем технологические базы при обработке заготовки корпуса пневмоцилиндра (Рисунок 2.2).
По теоретической схеме базирования заготовка корпуса пневмоцилиндра лишается шести степеней свободы в выбранной системе координат X Y Z. Поверхности заготовки на которые налаживаются шесть геометрических связей являются базовыми и делятся на установочную базу направляющую и опорную.
На первой операции в качестве черновой базы выбираем поверхность В которая на последующих операциях не обрабатывается имеет значительную протяженность и обеспечивает удобную установку заготовки в приспособлении. На последующих операциях в качестве установочной базы выбираем сочетание поверхностей А и Г лишающую заготовку трех степеней свободы. Опорной базой служит поверхность Д.
4. РАЗРАБОТКА МАРШРУТА ОБРАБОТКИ ДЕТАЛЕЙ.
Основной задачей разработки маршрута является составление общего плана обработки детали формулировка содержания операций технологического процесса. Результаты оформляются в виде таблицы 2.3.
При установлении общей последовательности обработки рекомендуется учитывать следующие положения.
Каждая последующая операция должна уменьшать погрешности и улучшать качество поверхности.
В первую очередь следует обрабатывать поверхность которая будет служить технологической базой для последующих операций.
Затем следует обрабатывать поверхности с которых снимается наибольший слой металла что позволит своевременно обнаружить возможные внутренние дефекты заготовки.
Операции при которых возможно появление брака из-за внутренних дефектов в заготовке следует производить вначале.
Обработка остальных поверхностей ведется в последовательности обратной степени их точности: чем точнее должна быть поверхность тем позже она обрабатывается.
Заканчивается обработка той поверхностью которая является наиболее точной и имеет наибольшее значение для эксплуатации детали.
Отверстия нужно сверлить в конце технологического процесса за исключением тех случаев когда они служат базами для установки.
Если деталь подвергается термической обработке по ходу технологического процесса механическая обработка расчленяется на две части: до термической обработки и после нее.
Технический контроль намечают после тех этапов обработки где вероятно повышенное количество брака перед сложными и дорогостоящими операциями после законченного цикла а также в конце обработки детали.
Разработку маршрута обработки детали вала маховика проведем с использованием типового технологического процесса на данную деталь.
Наименование операций соответствует требованиям классификатора технологических операций в машиностроении.
Технологический маршрут обработки вала маховика.
Технологические базы
Технологическая оснастка.
Заготовительная. Производство поковки.
Гидравлический пресс.
Термическая. Нормализация. Охлаждение на воздухе.
Фрезерно-центровальная. Фрезеровать торцы в размер выдержав размер .
Центровать с двух сторон А10 (ГОСТ 14034 – 74).
Шейка вала 155k6 поверхность 180f9.
Призмы опорные зажим.
Токарная. Точить поверхность 85 под резьбу окончательно выдержав размер 715. Точить канавку 8579 шириной 4.8мм точить фаску . Выполнить галтель R5.5. Нарезать резьбу М85×4 левую. Точить поверхность 125h6 до 125.5 точить фаску . Выполнить галтель R3. Точить поверхность 155k6 до 155.5 точить фаску . Выполнить галтель R3. Точить поверхность 170k6 до 170.5 точить фаску . Выполнить галтель R3. Точить поверхности 168 210 180h12 окончательно. Выполнить галтель R3. Точить канавку 180166 шириной 5.9 точить фаску выполнить галтель R7.
Центровые отверстия А10. Поверхность 150k6.
Центры вращающиеся поводковая планшайба хомутик.
Токарная. Сверлить и развернуть отверстие 58Н12 окончательно выдержать размер 900. Зенкеровать и развернуть отверстие 65Н12 выдержать размер 150 точить фаску . Точить поверхность 150k6 до 150.5 выдержать размер 521 точить фаску
выполнить галтель R3. Точить поверхность 175 под резьбу точить фаску . Нарезать резьбу М175×6.
Поверхности 125h6 и 180h12.
Патрон трехкулачковый самоцентрирующийся люнет.
Фрезерная. Фрезеровать паз окончательно выдержать размер 8. Сверлить два отверстия 10 глубиной . Зенковать фаски . Нарезать резьбу М12 глубиной . Развернуть заготовку на . Фрезеровать паз предварительно в размер 26 с двух сторон симметрично. Фрезеровать паз окончательно с двух сторон симметрично. Зенковать две фаски . Фрезеровать паз окончательно выдержать размер .
Развернуть заготовку на . Фрезеровать другой паз выдержать размер .
Поверхности и 150k6.
Делительная головка центра пробка с центровым отверстием планшайба поводковая хомутик.
Сверлильная. Сверлить 4 отверстия 14 глубиной . Зенковать фаски . Нарезать резьбу М16 глубиной .
Поверхности и 150k6.
Термическая. Поверхностная закалка до HRC 34 42 с отпуском.
Шлифовальная. Шлифовать поверхности и окончательно.
Шлифовальная. Шлифовать поверхность окончательно.
Поверхности 125h6 и 170k6.
Промыть деталь удалить заусеницы.
Технический контроль ОТК.
Разработку маршрута обработки детали корпуса пневмоцилиндра проведем с использованием типового технологического процесса на данную деталь. Технологический маршрут оформляется в таблицу 2.4.
Технологический маршрут обработки корпуса пневмоцилиндра.
Оборудование технологическая оснастка.
Заготовительная. Производство заготовки – отливка в песчаные формы. Подготовка к механической обработке.
Токарная. Точить поверхность окончательно. Подрезать торец 270h8 выдержать размер . Точить поверхность 270 окончательно точить фаску . Подрезать торец 270h8 выдержать размер . Расточить поверхность выдержать размер . Расточить поверхность до 170.5 в размер точить фаску . Точить канавку выдержать размер . Расточить отверстие окончательно выдержать размер выполнить галтели R5. Расточить поверхность 160 H8 до 159.5. Подрезать торец 160H8190H8 точить фаску . Точить канавку 160Н8 окончательно выдержать размер .
Патрон трехкулачковый самоцентрирующийся борштанга.
Токарная. Подрезать торец 350276Н11 выдержать размер . Расточить поверхность 276Н11 выдержать размер . Расточить поверхность 260Н8 до 260.5. Расточить поверхность 190Н8. Подрезать торец 190Н8230 выдержать размер точить фаску .
Сверлильная. Сверлить четыре сквозных отверстия на делительной окружности 400. Сверлить отверстие в размер . Сверлить четыре сквозных отверстия на делительной окружности 400 цековать бобышки 45 в размер . Сверлить четыре отверстия глухих 18 под резьбу в размер зенковать четыре фаски нарезать резьбу М20 в размер . Сверлить четыре отверстия глухих 9 под резьбу в размер зенковать четыре фаски нарезать резьбу М10 в размер .
Поверхности 350 поверхность 270h8.
Кондуктор кондукторная плита.
Сверлильная. Сверлить отверстие в размер рассверлить отверстие 9 под резьбу в размер зенковать фаску нарезать резьбу в размер . Развернуть заготовку на.Сверлить сквозное отверстие выдержать размер . Рассверлить отверстие 14 под резьбу в размер . Зенковать фаску нарезать резьбу в размер . Сверлить два сквозных отверстия 36 предварительно под фрезерование выдержать размер и межцентровое расстояние .
Поверхности 260Н8 и .
Делительная головка пробки с центровыми отверстиями центра планшайба поводковая хомутик.
Фрезерная Фрезеровать сквозной паз в размер . Фрезеровать платик .
Поверхности 350 поверхность 270h8 отверстия .
Опоры прихваты пальцы.
Сверлильная. Сверлить отверстие сквозное 14 выдержать размер . Зенковать фаску нарезать резьбу . Сверлить отверстие сквозное 30 выдержать размер . Зенковать фаску . Нарезать резьбу трубную .
Поверхность 260Н8 отверстия .
Оправка кондуктор кондукторная плита.
Термическая. Отпуск средний.
Токарная. Расточить поверхности 160Н8 и окончательно. Точить фаски и .
Промыть деталь очистить заусеницы.
5. ОПРЕДЕЛЕНИЕ ПРИПУСКОВ НА ОБРАБОТКУ И РАЗМЕРОВ ЗАГОТОВОК ВАЛА МАХОВИКА И КОРПУСА ПНЕВМОЦИЛИНДРА.
Расчет припусков деталей и назначение их ведется по таблицам ГОСТов.
На основании технико-экономического обоснования способ получения заготовки вала маховика выбираем поковку изготовляемую на гидравлическом прессе в открытых штампах.
Расчет допусков и припусков на обработку заготовки вала маховика определим по ГОСТ 7505 – 89.
Класс точности поковки устанавливается в зависимости от технологического процесса и оборудования для ее изготовления: основное деформирующее оборудование – гидравлический пресс выбираем класс точности – Т4.
Материал детали вала маховика – сталь 40Х; выбираем группу стали – М2.
Степень сложности поковки С определим путем вычисления отношения массы Gп поковки к массе Gф геометрической фигуры в которую вписывается форма поковки.
При вычислении отношения GпGф принимают ту из геометрических фигур масса которой меньше. Величину расчетной массы поковки в первом приближении допускается вычислять по формуле:
гдеМд – масса детали кг.
Кр – расчетный коэффициент Кр = 1.4.
Поковка ступенчатого вала вписывается в геометрическую фигуру цилиндра.цилиндра Gф = 423 кг. Отношение:
Численное значение отношения (формула 2.27) соответствует степени сложности поковки – С1.
Исходный индекс для последующего назначения основных припусков допусков и допускаемых отклонений определяется в зависимости от массы марки материала и класса точности поковки.
Масса поковки – 315 кг; группа стали – М2; степень сложности поковки – С1; класс точности – Т4. Определяем исходный индекс – 17.
Определим основные припуски на механическую обработку в зависимости от исходного индекса линейных размеров и шероховатости поверхности детали. Значения припусков на сторону по каждой поверхности детали сведем в таблицу 2.5.
Припуски на механическую обработку детали вала маховика.
Номинальный размер мм
Шероховатость поверхности Ra мкм
Припуск на сторону мм
Допуск размеров поковки мм
Допустимая величина остаточного облоя определяется в зависимости от массы поковки конфигурации поверхности разъема и класса точности поковки.поковки - 270 кг; поверхность разъема плоская; класс точности поковки – Т4. Допустимая величина остаточного облоя – 1.8мм.
Допустимая величина высоты заусенца на поковке по контуру обрезки облоя не должна превышать 6 мм.
На поковке допускается след в виде впадины или выступа образующийся от выталкивателя или от зажимных элементов штампа. Глубина впадины должна быть не более 0.5 величин фактического припуска. Высота выступа допускается до 3 мм на обрабатываемой поверхности.
Допускаемые отклонения штампованных уклонов на поковках устанавливаются в пределах ± 0.25 их номинальной величины. Величина уклона -
Допуск радиального биения цилиндрических поверхностей поковки не должен превышать 5 мм.
Эскиз заготовки вала маховика показан на рисунке 2.3.
Рисунок 2.3. Эскиз поковки вала маховика.
Заготовку корпуса пневмоцилиндра получим литьем в песчаные формы.Заготовки получаемые литьем в песчаные формы характеризуются минимальной стоимостью изготовления большими припусками и высокими параметрами шероховатости. В песчаных формах можно получить отливки самой сложной конфигурации и массой от нескольких граммов до сотен тонн. Этот способ литья чаще применяется в серийном производстве.
Допуски размеров массы и припуски на механическую обработку определим согласно ГОСТ 26645 – 85.
Номинальный размер отливки следует принимать равным номинальному размеру детали для необрабатываемых поверхностей и сумме среднего размера детали и общего припуска на обработку – для обрабатываемых поверхностей. При определении номинальных размеров отливок учитывают технологические напуски.
Определим класс размерной точности отливки. Способ литья – литье в пес-чано-глинистые сырые формы из низко влажных высокопрочных смесей. Выбираем – 10 класс размерной точности.
По классу размерной точности определим допуски на линейные размеры. Значения допусков сведем в таблицу 2.6.
Допуски линейных размеров отливки корпуса пневмоцилиндра.
Определим степень коробления элементов отливки. Отношение наименьшего размера элемента отливки к наибольшему – 0.74 которое соответствует 4 степени коробления.
Определим допуски формы и расположения элементов отливки. Числовые значения сведем в таблицу 2.7. За номинальный размер нормируемого участка при определении допусков формы и расположения принимаем наибольший из размеров нормируемого участка элемента отливки.
Определим общие допуски элементов отливки учитывающие совместное влияние допуска размера от поверхности до базы и допуска формы и расположения поверхностей. Числовые значения сведем в таблицу 2.8.
Допуски формы и расположения элементов отливки.
Общие допуски элементов отливки.
Допуск размера от поверхности до базы мм
Допуск формы и расположения поверхностей мм
Общий допуск элемента отливки мм
Определим степень точности поверхности отливки. Способ получения - литье в песчано-глинистые сырые формы из низко-влажных высокопрочных смесей. Наибольший габаритный размер св. 250 до 630 мм. Выбираем степень точности поверхностей – 14.
По известной степени точности поверхностей определим ряд припусков на обработку отливки. Выбираем 7 ряд припусков.
Минимальный литейный припуск на сторону – 0.8 мм.
Определим припуски элементов отливки. Числовые значения сведем в таблицу 2.9.
Общие припуски на сторону.
Общий припуск на сторону мм
Значение шероховатости для 14 степени точности поверхности отливки выбираем Ra = 40 мкм.
Эскиз заготовки корпуса пневмоцилиндра показан на рисунке 2.4.
Рисунок 2.4. Эскиз отливки корпуса пневмоцилиндра.
Минимальный диаметр отверстий выполняемых литьем выбираем так чтобы избежать сильного перегрева и пригара стержня к стенкам отверстия. Возможность спекания стерневой смеси и пригара определяется массой окружающего металла поэтому минимальный размер литых отверстий зависит от толщины стенки длины стержня и может быть определен по формуле:
гдеdo – исходный диаметр для сталей do = 10 мм.
s – толщина стенка мм.
Формовочные уклоны назначают с целью облегчения удаления модели из формы и стержня из стержневого ящика. Уклоны устанавливаются по ГОСТ 3212 – 80 в зависимости от размеров углублений и вида модельного комплекта. Числовые значения сведем в таблицу 2.10.
Формовочные уклоны отливки.
Высота формообразующей поверхности мм
6. ВЫБОР ТЕХНОЛОГИЧЕСКОГО ОБОРУДОВАНИЯ.
Общие правила выбора технологического оборудования установлены ГОСТ 14.404 – 73. Выбор модели станка прежде всего определяется его возможностью обеспечить точность размеров и формы а также качество поверхности изготовляемой детали. Поэтому модель станка выбираем из следующих соображений:
- соответствие станка по производительности заданному масштабу производства;
- возможность работы на оптимальных режимах резания;
- соответствие механизации и автоматизации выполняемой обработки;
- наименьшая себестоимость обработки;
- реальная возможность приобретения станка;
- необходимость использования имеющихся станков.
Руководствуясь выше перечисленными соображениями выбираем станки по каждой операции обработки вала маховика.
Фрезерно-центровальная.
Выбираем продольно-фрезерный двухстоечный станок 6620.
Техническая характеристика станка размеры в мм.
Размеры рабочей поверхности стола
Наибольшая масса обрабатываемой заготовки кг50000
Расстояние до поверхности стола:
от оси горизонтального шпинделя0 – 1765
от торца вертикального шпинделя175 – 2180
Расстояние между торцами горизонтальных шпинделей1550 – 2250
Число шпиндельных бабок:
Наибольшее перемещение:
стола продольное6800
Число скоростей шпинделя18
Частота вращения шпинделя обмин20 – 1000
шпиндельной бабки10 – 2000
гильз шпинделей5 – 1000
Мощность электродвигателя7.5
привода главного движения кВт
Определим ряд чисел оборотов шпинделя станка. Коэффициент знаменателя геометрического ряда φ = 1.26. Ряд чисел оборотов обмин: 20 25.2 32 40 50 63 79. 4 100 126 158.8 200 252 317 400 504 635 800 1008.
Выбираем токарно-винторезный станок 16К40П.
Наибольший диаметр обрабатываемой детали:
Наибольшая длина обрабатываемой детали2000
Предел чисел оборотов шпинделя обмин6.3 – 1250
Число скоростей шпинделя24
Пределы рабочих подач суппорта мммин:
Мощность электродвигателя 18.5
Ряд чисел оборотов шпинделя станка обмин: 6.3 8 10 12.6 16 20 25 31.5 40 50 63 79 99.5 125 157.5 198 249.5 314 396 499 629 792 998 1257.
Ряд чисел оборотов шпинделя станка обмин: 20.2 25.5 32 40 50.4 63.5 80 101 127.3 160.4 202 254.5 320.7 404 509 641.3 808 1018.
Выбираем горизонтально-расточной станок 2636Ф1. Тип компоновки станка – с неподвижной передней стойкой и поворотным столом имеющим продольное и поперечное перемещение.
Техническая характеристика станка размеры в мм:
Диаметр выдвижного шпинделя125
Конус для крепления инструментов Метрический 80
в выдвижном шпинделе
Размеры встроенного поворотного стола
Наибольшая масса обрабатываемой заготовки кг8000
Наибольшее перемещение
вертикальное шпиндельной бабки1400
продольное выдвижного шпинделя1000
радиального суппорта200
шпинделябесступенчатое регулирование
планшайбыбесступенчатое регулирование
Частота вращения обмин:
шпиндельной бабки1 – 1000
стола (продольная и поперечная)1 – 1000
радиального суппорта0.63 – 630
Мощность электродвигателя привода19
главного движения кВт
Выбираем круглошлифовальный станок 3М194.
Наибольшие размеры устанавливаемой заготовки:
Наибольший диаметр шлифования350
Наибольшая длина шлифования3800
Высота центров над столом520
Наибольшее продольное перемещение стола4240
Угол поворота стола град:
по часовой стрелке0.5
против часовой стрелки6
Конус Морзе шпинделя передней бабки Метрический 80
и пиноли задней бабки
Наибольшие размеры шлифовального круга:
Частота вращения шпинделя600 – 1300
шлифовального круга обмин
Габаритные размеры (с приставным оборудованием):
Масса (с приставным оборудованием) кг34300
Выберем станки по каждой операции обработки корпуса пневмоцилиндра.
Выбираем токарно-карусельный станок 1508.
Наибольший диаметр детали над:
вертикальным суппортом800
боковым суппортом710
высота обрабатываемой детали800
масса обрабатываемой детали кг1300
Диаметр планшайбы710
Ход ползуна вертикального суппорта650
Число: ступеней оборотов планшайбы18
оборотов планшайбы в минуту10 – 500
Вертикальная и горизонтальная подача суппортов в мммин3.6 – 378
Мощность электродвигателя22
Ряд чисел оборотов обмин: 10 12.6 16 20 25.2 32 40.3 51 64.3 81 102 128.5 162 204 257 324 408 514.
Выбираем радиально-сверлильный станок 2Ш55.
Наибольший условный диаметр сверления в стали50
Расстояние от оси шпинделя до образующей колонны850 – 1600
Расстояние от нижнего торца шпинделя до
рабочей поверхности плиты150 – 1800
вертикальное рукава на колонне1250
горизонтальное сверлильной головки по рукаву750
Наибольшее вертикальное перемещение шпинделя400
Конус Морзе отверстия в шпинделе5
Число скоростей шпинделя21
Частота вращения шпинделя обмин10 – 1000
Подача шпинделя мммин6 – 67.2
Наибольшая сила подачи МН16
Мощность электродвигателя4
Ряд чисел оборотов шпинделя обмин: 10 12.6 16 20 25.2 32 40 50 63 79.4 100 126 158.8 200 252 317.5 400 504 635 800 1008.
Выбираем широкоуниверсальный консольный станок 6Р83Ш.
Расстояние от оси горизонтального шпинделя до
поверхности стола30 – 450
Расстояние от торца вертикального шпинделя
до поверхности стола70 – 570
Наибольший угол поворота вертикальной фрезерной
головки в плоскости параллельной:
продольному ходу стола360
поперечному ходу стола:
Конус отверстия шпинделя по ГОСТ 15945 – 82:
Число ступеней шпинделя
Число оборотов шпинделя в минуту31.5 – 1600
вертикальная8.3 – 416.6
Мощность электродвигателя11
главного привода кВт
Ряд чисел оборотов шпинделя станка обмин: 31.5 40 50.4 63.5 80 101 127 160 202 254.5 321 404.5 510 642.6 809.7 1020 1285 1616.
7. ОПРЕДЕЛЕНИЕ РЕЖИМОВ ОБРАБОТКИ ЗАГОТОВКИ ВАЛА МАХОВИКА И КОРПУСА ПНЕВМОЦИЛИНДРА.
Режимы обработки вала маховика определим для всех операций пользуясь эмпирическими выражениями и таблицами из нормативно-справочной литературы (См. [3] [4] [5]).
Фрезерно-центровальная. Фрезерование торцов заготовки.
Ширина фрезерования мм и мм припуск мм материал – сталь 40Х. Припуск снимаем за один проход поэтому глубина резания мм.
Выбор режущего инструмента. Для обработки базовых поверхностей выбираем торцовую насадную фрезу сборную (ГОСТ 24359 – 80) с пластинками из твердого сплава Т5К10. Размеры: мм мм 26 мм мм.
Назначение подачи. Рекомендуемая подача ммзуб. Поправочные коэффициенты на подачу (См. [5] стр. 302) в зависимости от материала инструмента вида обработки шероховатости - .
Действительная подача на зуб
Скорость резания. Рекомендуемая скорость резания ммин. Поправочные коэффициенты на скорость резания в зависимости от материала обрабатываемой заготовки материала инструмента состояния поверхности главного угла в плане условия обработки с СОЖ – 3 – 5%-ная эмульсия Уникрол – 1 отношение фактической ширины фрезерования к нормативной – до 1.0 . Действительная скорость резания
гдеD – диаметр фрезы мм;
V – скорость резания ммин.
Корректируем по ряду частот вращения шпинделя станка. Принимаем обмин. Тогда действительная скорость резания
Основное технологическое время.
l1 – величина перебега и врезания инструмента.
i – количество проходов.
Для ширины фрезерования мм
Определим силу резания и крутящий момент.
где Cp – поправочный коэффициент на условия резания;
Kmp – поправочный коэффициент учитывающий влияние качества обрабатываемого материала на силовые зависимости
гдев – предел прочности материала заготовки МПа.
Мощность электродвигателя главного привода станка Nд = 7.5 кВт. Так как Nд > Ne то обработка не возможна. Принимаем решение уменьшить частоту вращения до n = 32 обмин.
Тогда для ширины фрезерования мм: Pz = 18950 H; Мкр = 3032 V = 15.7 ммин; Т0 = 1.5 мин; Ne =4.9 кВт.
Для ширины фрезерования мм: Pz = 9733.3 H; Мкр = 443 V = 9.1 ммин; Т0 = 0.8 мин; Ne =1.45 кВт.
Сверление центровых отверстий А10. Глубина сверления h = 22.5 диаметр d = 10 мм d1 = 21.2 мм.
Выбор режущего инструмента. Выбираем центровочное сверло комбинированное (ГОСТ14952 – 75) из быстрорежущей стали Р6М5 типа А. Размеры: d = 10 мм d1 = 21.2 мм L = 103 мм l = 12.8 мм 2φ = .
Подача. Рекомендуемая подача 0.01 – 0.07 ммоб. (См. [3] стр.393). Принимаем S = 0.07 ммоб.
Скорость резания. Рекомендуемая V0 = 32 ммин. С учетом поправочных коэффициентов принимаем V = 24.75 ммин.
Корректируем по ряду частот шпинделя станка: n = 400 обмин. Тогда V = 26.6 ммин.
гдеL – длина прохода сверла в направлении подачи мм;
SM – минутная подача;
гдеKp – поправочный коэффициент на условия резания (См. [4] стр. 271).
Точить поверхность 85. Припуск h = 2.7мм длина 155мм. Шероховатость поверхности Ra = 5 мкм. Припуск снимаем за два прохода: t1 = 1.7мм t2 = 1.0мм.
Выбор режущего инструмента. Выбираем резец токарный проходной упорный (ГОСТ 18879 – 73) с пластинкой из твердого сплава Т5К10. Размеры: мм L = 100мм l = 12мм сечение мм.
Определим режимы резания при черновой обработке поверхности.
Подача. Рекомендуемая подача S0 = 0.46ммоб. С учетом поправочных коэффициентов (См. [5] стр. 236) принимаем S = 0.37ммоб.
Скорость резания. При черновой обработке – V0 = 192ммин. Принимаем скорость резания с учетом поправочных коэффициентов (См. [5] стр. 244) V = 80ммин.
По ряду частот: n = 314 обмин. Тогда V = 89.2ммин.
гдеКр – обобщенный поправочный коэффициент на условия резания.
Определим режимы резания при чистовой обработке поверхности.
Подача. Рекомендуемая подача при чистовой обработке S0 = 0.19ммоб. Принимаем S = 0.15ммоб.
Скорость резания. При чистовой обработке – V0 = 280ммин. Принимаем V = 116.5ммин.
По ряду частот: n = 499 обмин. Тогда V = 136.4ммин.
Точить поверхность 125 до 125.5 под шлифование. Припуск снимается за один проход t = 3.05мм. Длина прохода резца L = 134мм.
Подача. Рекомендуемая подача S0 = 0.45ммоб. С учетом поправочных коэффициентов принимаем S = 0.37ммоб.
Скорость резания. Рекомендуемая скорость резания – V0 = 182ммин. Принимаем V = 75.75ммин.
По ряду частот: n = 198 обмин. Тогда V = 81.86ммин.
Точить поверхность 155 до 155.5 под шлифование. Припуск снимаем за один проход t = 3.05мм.
Выбор режущего инструмента. (См. Точение поверхности 125 до 125.5).
Подача. Рекомендуемая подача S0 = 0.45ммоб. С учетом поправочных коэффициентов принимаем S = 0.38ммоб.
Скорость резания. Рекомендуемая скорость резания – V0 = 182ммин. Принимаем V = 81.5ммин.
По ряду частот: n = 157.5 обмин. Тогда V = 80ммин.
Точить поверхность 170 до 170.5 под шлифование. Припуск снимаем за один проход t = 3.25мм.
Скорость резания. Рекомендуемая скорость резания – V0 = 170ммин. Принимаем V = 76.1ммин.
По ряду частот: n = 157.5 обмин. Тогда V = 87.6ммин.
Точить поверхность 150 до 150.5 под шлифование. Припуск снимаем за один проход t = 3.05мм.
По ряду частот: n = 157.5 обмин. Тогда V = 77.5ммин.
Точить поверхность 175 окончательно. Припуск h = 3.2мм длина 56мм.
Шероховатость поверхности Ra = 5 мкм. Припуск снимаем за два прохода: t1 = 2мм t2 = 1.2мм.
Подача. Рекомендуемая подача S0 = 0.55ммоб. С учетом поправочных коэффициентов принимаем S = 0.47ммоб.
Скорость резания. При черновой обработке – V0 = 182ммин. Принимаем V = 81.5ммин.
По ряду частот: n = 157.5 обмин. Тогда V = 90ммин.
Подача. Рекомендуемая подача при чистовой обработке S0 = 0.19ммоб. Принимаем S = 0.16ммоб.
Скорость резания. При чистовой обработке – V0 = 250ммин. Принимаем V = 112ммин.
По ряду частот: n = 157.5 обмин. Тогда V = 111.6ммин.
Точить поверхность 180 окончательно. Припуск h = 3.3мм длина 465мм.
Шероховатость поверхности Ra = 5 мкм. Припуск снимаем за два прохода: t1 = 2мм t2 = 1.35мм.
Скорость резания. При черновой обработке – V0 = 171ммин. Принимаем V = 76.6ммин.
По ряду частот: n = 125 обмин. Тогда V = 73.2ммин.
По ряду частот: n = 198 обмин. Тогда V = 113.5ммин.
Точить поверхность 210 окончательно. Припуск h = 2.6мм длина 30мм.
Шероховатость поверхности Ra = 20 мкм. Припуск снимаем за один проход: t1 = 2.6 мм.
По ряду частот: n = 125 обмин. Тогда V = 84.5ммин.
Точить поверхность 168 окончательно. Припуск h = 1мм длина 83мм.
Шероховатость поверхности Ra = 20 мкм. Припуск снимаем за один проход.
Выбор режущего инструмента. Выбираем резец токарный проходной прямой (ГОСТ 18869 – 73) с пластинкой из твердого сплава Т5К10. Размеры: мм L = 100мм l = 12мм сечение мм.
Скорость резания. При черновой обработке – V0 = 202ммин. Принимаем V = 90.4ммин.
По ряду частот: n = 157.5 обмин. Тогда V = 84.1ммин.
Точить канавку 175166 окончательно. Ширина канавки b = 12.9мм глубина h = 4.5мм.
Выбор режущего инструмента. Выбираем токарный канавочный резец с пластинкой из твердого сплава Т15К6.
Подача. Рекомендуемая подача S0 = 0.36ммоб. С учетом поправочных коэффициентов (См. [5] стр. 236) принимаем S = 0.3ммоб.
Скорость резания. При черновой обработке – V0 = 190ммин. Принимаем V = 71.25ммин.
По ряду частот: n = 125 обмин. Тогда V = 68.72ммин.
Точить канавку 8579 окончательно. Ширина канавки b = 10.3мм глубина h = 3мм.
Подача. Рекомендуемая подача S0 = 0.28ммоб. С учетом поправочных коэффициентов (См. [5] стр. 236) принимаем S = 0.24ммоб.
Скорость резания. При черновой обработке – V0 = 214ммин. Принимаем V = 80.25ммин.
По ряду частот: n = 314 обмин. Тогда V = 83.85ммин.
Сверлить отверстие 57 под развертывание. Отверстие глухое глубина сверления 900мм. Сверление производится на токарно-винторезном станке 16К40П. Движением резания является вращение заготовки.
Выбор режущего инструмента. Для обработки глубокого глухого отверстия выбираем сверло одностороннего резания с эжекторным отводом стружки (ТУ 2 – 035 – 857 – 81) диаметром d = 57мм длиной L = 1070мм с пластинками из твердого сплава Т15К6.
Рекомендуемая подача при диаметре сверла св. 50мм S0 = 0.66ммоб. Выберем подачу с учетом поправочных коэффициентов (См. [5] стр. 267). S = 0.15ммоб.
Скорость резания. Рекомендуемая скорость резания V0 = 32ммин. С учетом поправочных коэффициентов (См. [5] стр. 270) принимаем V = 14.4ммин.
Корректируем по ряду частот шпинделя станка: n = 79 обмин. Тогда V = 14.4 ммин.
Зенкеровать отверстие 57 до 64. Припуск t = 3.5мм глубина отверстия h = 150мм.
Выбор режущего инструмента. Выбираем зенкер цельный насадной (ГОСТ 3231 – 71) оснащенный пластинками из твердого сплава Т15К6. Размеры: d = 65мм d0 = 25мм L = 50мм z = 4.
Рекомендуемая подача S0 = 0.90 – 1.1ммоб. Выберем S = 0.95ммоб.
Рекомендуемая скорость резания V0 = 64ммин. Принимаем V = 64ммин.
Корректируем по ряду частот шпинделя станка: n = 314 обмин. Тогда V = 641ммин.
l – величина врезания и перебега инструмента мм.
Развернуть отверстия 58Н12 и 65Н12 . Глубина резания t = 0.5мм.
Выберем режущий инструмент и определим режимы резания для обработки отверстия 58.
Выбираем развертку машинную насадную (ГОСТ 883 – 71) со вставными ножами из быстрорежущей стали Р9К5. Размеры в мм: d = 58 l1 = 2 L = 74 z = 10 φ = .
Рекомендуемая подача S0 = 1.4ммоб. Выберем S = 0.7ммоб.
Рекомендуемая скорость резания V0 = 11ммин. Принимаем V = 11ммин.
Корректируем по ряду частот шпинделя станка: n = 63 обмин. Тогда V = 11.5ммин.
Выберем режущий инструмент и определим режимы резания для обработки отверстия 65.
Выбираем развертку машинную насадную (ГОСТ 883 – 71) со вставными ножами из быстрорежущей стали Р9К5. Размеры в мм: d = 65 l1 = 2 L = 74 z = 10 φ = .
Корректируем по ряду частот шпинделя станка: n = 50 обмин. Тогда V = 10.2ммин.
Сверлить четыре отверстия 14мм под резьбу. Глубина h = 45.
Выбор режущего инструмента. Выбираем сверло центровальное с цилиндрическим хвостовиком (ОСТ И20 – 5 – 80) из быстрорежущей стали Р9. Размеры сверла в мм: d = 14 L = 100 l = 45 2φ = .
Рекомендуемая подача S0 = 0.34ммоб. Выберем подачу с учетом поправочных коэффициентов S = 0.1ммоб.
Скорость резания. Рекомендуемая скорость резания V0 = 34ммин. С учетом поправочных коэффициентов принимаем V = 20.4ммин.
Сверлить два отверстия 10мм под резьбу. Глубина h = 32.
Выбор режущего инструмента. Выбираем сверло центровальное с цилиндрическим хвостовиком (ОСТ И20 – 5 – 80) из быстрорежущей стали Р9. Размеры сверла в мм: d = 10 L = 80 l = 32 2φ = .
Рекомендуемая подача S0 = 0.25ммоб. Выберем подачу с учетом поправочных коэффициентов S = 0.15ммоб.
Скорость резания. Рекомендуемая скорость резания V0 = 37ммин. С учетом поправочных коэффициентов принимаем V = 22ммин.
Фрезеровать сквозной паз с двух сторон симметрично предварительно. Глубина прохода инструмента 65мм длина 96мм ширина 26мм. Припуск снимаем за 10 ходов фрезы. Глубина резания t = 6.5мм.
Выбор режущего инструмента. Выбираем фрезу концевую с коническим хвостовиком (ГОСТ 17026 – 71) из быстрорежущей стали Р9К5. Размеры: d = 26мм l = 70мм L = 140мм z = 5 конус Морзе – 3.
S0 = 0.12ммзуб. Принимаем Sz = 0.032ммзуб.
V0 = 64ммин. Принимаем V = 43.8ммин.
По ряду частот выбираем n = 509обмин. Тогда V = 41.6ммин.
Фрезеровать сквозной паз с двух сторон симметрично окончательно. Глубина прохода инструмента 65мм длина 95.5мм ширина 26.5мм. Припуск снимаем за 5 ходов фрезы. Глубина резания t = 13мм.
Выбор режущего инструмента. Выбираем фрезу концевую с коническим хвостовиком (ГОСТ 17026 – 71) из быстрорежущей стали Р9К5. Размеры: d = 26.5мм l = 70мм L = 140мм z = 5 конус Морзе – 3.
S0 = 0.18ммзуб. Принимаем Sz = 0.03ммзуб.
V0 = 80ммин. Принимаем V = 54.7ммин.
По ряду частот выбираем n = 641.3обмин. Тогда V = 53.4ммин.
Фрезеровать шпоночный паз b = 45мм.Глубина фрезерования h = 15мм. Припуск снимаем за 5 ходов – t = 3мм.
Выбираем фрезу концевую (ГОСТ 17026 – 71) из быстрорежущей стали Р9К5 конус Морзе – 3 d = 45мм z = 6.
S0 = 0.25ммзуб. Принимаем Sz = 0.08ммзуб.
V0 = 66ммин. Принимаем V = 34.15ммин.
По ряду частот выбираем n = 254.5обмин. Тогда V = 36ммин.
Фрезеровать два шпоночных паза b = 40мм.Глубина фрезерования h = 13мм. Припуск снимаем за 4 ходов – t = 3.25мм.
Выбираем фрезу концевую (ГОСТ 17026 – 71) из быстрорежущей стали Р9К5 конус Морзе – 3 d = 40мм z = 6.
По ряду частот выбираем n = 254.5обмин. Тогда V = 32ммин.
Нарезать резьбу резцом левую длиной l = 135.7мм.
Выбираем резец токарный резьбовой для наружной метрической резьбы с шагом P = 4мм (ГОСТ 18876 – 73). Размеры: мм L = 125мм. Оснащенный твердосплавной пластинкой Т15К6.
Число рабочих ходов – 6. Подача S0 = 0.6 – 0.8ммоб. Принимаем S = 0.6ммоб.
Скорость резания – V0 = 122ммин. Принимаем V = 84.2ммин.
По ряду частот выбираем n = 314обмин. Тогда V = 84ммин.
гдеn1 – частота вращения шпинделя при обратном ходе обмин.
гдеР – шаг резьбы мм.
Нарезать резьбу резцом длиной l = 47.6мм.
Число рабочих ходов – 8. Подача S0 = 0.6 – 0.8ммоб. Принимаем S = 0.6ммоб.
Скорость резания – V0 = 114ммин. Принимаем V = 67ммин.
По ряду частот выбираем n = 125обмин. Тогда V = 68.72ммин.
Нарезать резьбу в четырех отверстиях М16 длиной l = 35мм шаг Р = 2мм.
Выбираем метчик машинный из быстрорежущей стали Р10К5Ф5 с винтовыми канавками (ГОСТ 3266 – 81). Размеры: d = 16мм P = 2мм L = 102мм l = 32мм длина заборной части l1 = 6мм.
Скорость резания – V0 = 14.5ммин. Принимаем V = 7.97ммин.
По ряду частот выбираем n = 159обмин. Тогда V = 8ммин.
Нарезать резьбу в двух отверстиях М12 длиной l = 26мм шаг Р = 1.75мм.
Выбираем метчик машинный из быстрорежущей стали Р10К5Ф5 с винтовыми канавками (ГОСТ 3266 – 81). Размеры: d = 12мм P = 1.75мм L = 89мм l = 29мм длина заборной части l1 = 5.2мм.
По ряду частот выбираем n = 212обмин. Тогда V = 8ммин.
Шлифовать поверхности вала 125h6 длиной 150k6 длиной 155k6 длиной 170k6 длиной l = 96мм и длиной l = 132мм. Припуск на сторону h = 0.25мм.
Выбираем шлифовальный круг типа ПВ – с выточкой (ГОСТ 2424 – 83). Размеры: D = 200мм; Вк = 50мм; d = 50мм. Материал шлифовального круга – электрокорундбелый 25А связка бакелитовая Б3 зернистость – 40 твердость – СМ1. Скорость шлифовального круга.
гдеDк – диаметр круга мм:
nк – частота вращения шпинделя шлифовальной бабки (по паспорту станка) обмин;
Окружная скорость заготовки Vз = 15 – 55ммин. Принимаем Vз = 20ммин.
Глубина шлифования t = 0.005 – 0.015мм. Принимаем t = 0.015мм.
Продольная подача S = (0.2 – 0.4)Bк. Принимаем S = 12.5ммоб.
Определим режимы резания для обработки поверхности 125мм.
Частота вращения заготовки.
Скорость продольного хода стола
гдеL – длина шлифуемой поверхности;
Кп – число сторон перебега (Кп = 2 при сбеге круга в две стороны; Кп = 1 при сбеге круга в одну сторону);
m – перебег в долях ширины круга m = 0.5 Bк мм;
h – припуск на сторону мм;
К – коэффициент выхаживания К = 1.2.
Определим режимы резания для обработки поверхности 150мм.
Определим режимы резания для обработки поверхности 155мм.
Определим режимы резания для обработки поверхности 170мм длиной l = 96мм.
Определим режимы резания для обработки поверхности 170мм длиной l = 132мм.
где d – диаметр шлифования мм.
Мощность электродвигателя привода главного движения станка Nд = 25кВт.
Результаты расчетов режимов резания сил резания мощности и основного технологического времени по каждой операции сведем в таблицу 2.11.
Режимы обработки заготовки корпуса пневмоцилиндра определим в такой же последовательности как и для обработки заготовки вала маховика. Методика расчетов режимов резания такая же как и для обработки заготовки вала маховика.
Режущий инструмент необходимый для обработки заготовки корпуса пневмоцилиндра сведем в таблицу 2.12.
Численные значения режимов резания по операциям сведем в таблицу 2.13.
Ведомость режущего инструмента для обработки заготовки корпуса пневмоцилиндра.
Наименование тип и основные размеры режущего инструмента в мм
Резец автоматный проходной с пластинкой из твердого сплава Т15К6 (ТУ 2 – 036 – 491 – 76)
Размеры: ; L = 140; ; ; .
Резец токарный подрезной торцовый с пластинкой из твердого сплава Т15К6(ГОСТ 18880 – 73). Размеры: ; L = 140; ; r = 1.
Резец токарный проходной упорный (18879 – 73) с пластинкой из твердого сплава Т15К6. Размеры: ; L = 140; ; ; r = 1.
Резец токарный расточной для сквозных отверстий (ГОСТ 18882 – 73) с пластинкой из твердого сплава Т15К6. Размеры: ; L = 200; ; .
Резец токарный расточной для глухих отверстий (ГОСТ 18883 – 73) с пластинкой из твердого сплава Т15К6. Размеры: ; L = 200; ; .
Резец канавочный с пластинкой из твердого сплава Т15К6 (ГОСТ 25412 – 82). Размеры: ; L = 100; ; .
Резец токарный подрезной торцовый для обработки на проход (ГОСТ 18871 – 73) с пластинкой из твердого сплава Т15К6. Размеры: ; L = 120; ; r = 1.
Фреза концевая с коническим хвостовиком (ГОСТ 17026 – 71) из быстрорежущей стали Р9К5. Размеры: d = 36; L = 200; z = 5; конус Морзе – 3; .
Фреза торцевая насадная со вставными ножами (ГОСТ 1092 – 80) из быстрорежущей стали Р9К5. Размеры: ; 10; ; .
Сверло спиральное с коническим хвостовиком (ГОСТ 10903 – 77) из быстрорежущей стали Р9К5. Размеры: d = 30; конус Морзе – 3; 2φ = .
Сверло спиральное с коническим хвостовиком (ГОСТ 10903 – 77) из быстрорежущей стали Р9К5. Размеры: d = 14; L = 189; конус Морзе – 1; 2φ = .
Сверло для обработки глубоких отверстий с внутренним подводом СОЖ (ТУ 2 – 035 – 655 – 79). Рабочая часть сверла выполнена из твердого сплава ВК8. Размеры: d = 5; L = 500.
Сверло для обработки глубоких отверстий с внутренним подводом СОЖ (ТУ 2 – 035 – 655 – 79). Рабочая часть сверла выполнена из твердого сплава ВК8. Размеры: d = 6; L = 500.
Сверло спиральное с коническим хвостовиком (ГОСТ 10903 – 77) из быстрорежущей стали Р9К5. Размеры: d = 9; L = 140; конус Морзе – 1; 2φ = .
Сверло спиральное с коническим хвостовиком (ГОСТ 10903 – 77) из быстрорежущей стали Р9К5. Размеры: d = 22; L = 248; конус Морзе – 2; 2φ = .
Сверло спиральное с коническим хвостовиком (ГОСТ 10903 – 77) из быстрорежущей стали Р9К5. Размеры: d = 32; L = 334; конус Морзе – 4; 2φ = .
Сверло спиральное с коническим хвостовиком (ГОСТ 10903 – 77) из быстрорежущей стали Р9К5. Размеры: d = 18; L = 228; конус Морзе – 2; 2φ = .
Зенковка цилиндрическая с направляющей цапфой под сквозное отверстие (ГОСТ 11284 – 75) из быстрорежущей стали Р9К5. Размеры: d = 45; dц = 16; L = 110; z = 4.
Зенковка центровочная (ГОСТ 14953 – 69) из быстрорежущей стали Р9К5. Размеры: d = 40; d0 = 6; L = 190; z = 4; 2φ = .
Метчик машинный для нарезания трубной цилиндрической резьбы (ГОСТ 19879 – 74) оснащенный твердосплавными пластинками Т15К6. Размеры: d = 33.249; d1 = 40; z = 6; длина заборной части φ = ; число шагов – 11.
Метчик машинный для метрической резьбы с мелким шагом (ГОСТ 9522 – 60) из быстрорежущей стали Р18. Размеры: d = 16; d1 = 9; длина заборной части шаг резьбы Р = 1.5.
Метчик для метрической резьбы с мелким шагом (ГОСТ 9522 – 60) из быстрорежущей стали Р18. Размеры: d = 10; d1 = 6; длина заборной части шаг резьбы Р = 1.
Метчик для метрической резьбы (ГОСТ 3266 – 81) из быстрорежущей стали Р18. Размеры: d = 20; длина заборной части шаг резьбы Р = 2.5.
8. НОРМИРОВАНИЕ ОПЕРАЦИЙ ТЕХНОЛОГИЧЕСКОГО ПРОЦЕССА.
Нормирование операций технологического процесса осуществляется на каждую станочную операцию методом технического расчета по нормативам.
Техническая норма времени независимо от типа станка и метода обработки
гдеТш.к. – норма штучно-калькуляционного времени мин;
Тшт – норма штучного времени мин;
ТПЗ – норма подготовительно-заключительного времени мин;
n – размер партии деталей шт.
Для серийного производства оптимальное количество деталей в партии для одновременного запуска в производство
гдеN – годовая программа выпуска деталей шт;
f – число дней на которое необходимо иметь запас деталей на складе: для крупных – 2 3 дня; для мелких – 5 10 дней;
Ф – число рабочих дней в году Ф = 253 дня.
Норма штучного времени
гдеТо – основное технологическое время мин;
Тв – вспомогательное время мин;
Ттех – время технического обслуживания мин;
Торг – время организационного обслуживания рабочего места мин;
Тнп – время перерыва мин.
Основное время определяется расчетом для каждого технологического перехода в зависимости от режима резания.
Вспомогательное время устанавливается для каждого технологического перехода по нормативам.
Оперативное время операции
Время технического обслуживания можно принимать до 6% организационного обслуживания – до 8% времени перерыва – до 2.5% от оперативного времени.
Для каждой операции определяется количество станков:
гдеtв – такт выпуска деталей мин.
Расчетное количество станков округляется до ближайшего целого числа.
Определим нормы времени по операциям технологического процесса обработки вала маховика.
Фрезерно-центровальная.
Основное технологическое время – То = 3.9мин.
Вспомогательное время:
на установку и снятие детали – 7.5мин;
связанное с переходом: фрезерование торцов вала – 0.16мин;
сверление центровых отверстий – 0.12мин;
на контрольные измерения – 0.13мин;
включить и выключить вращение шпинделя – 0.06мин;
установить и снять инструмент – 0.44мин.
Вспомогательное время на операцию:
Время технического обслуживания – Ттех = 0.74мин;
Время организационного обслуживания – Торг = 1мин;
Время перерыва – Тнп = 0.3мин.
Количество деталей в партии
Такт выпуска деталей – 152.25мин.
Норма подготовительно-заключительного времени:
на наладку станка – 29мин;
при установке зажимного приспособления – 5мин;
на операцию – ТПЗ = 34мин.
Норма штучно-калькуляционного времени
Принимаем М = 1 станок.
Основное технологическое время – То = 146.13мин.
на установку и снятие детали – 6мин;
связанное с переходом:
продольное точение резцом установленным на размер:
продольным точением резцом со взятием пробных стружек по 8 9 квалитету:
проточка канавок с измерением длины расположения размера – 0.42мин;
нарезание резьбы резцом:
черновой рабочий ход – 1.17мин;
чистовой рабочий ход:
св. 100мм – 0.49мин;
сверление зенкерование развертывание – 0.55мин;
Изменить частоту вращения шпинделя – 1.26мин.
Изменить величину или направление подачи – 0.9мин.
Установить и снять инструмент:
резец проходной подрезной – 0.4мин;
резец резьбовой отрезной – 1.2мин;
сверло зенкер развертка – 0.4мин.
Включить гайку ходового винта вначале и выключить по окончании нарезания резьбы – 0.08мин.
Переместить каретку суппорта в продольном направлении на длину свыше 200мм до 500мм – 0.075мин.
Вспомогательное время на операцию – 22.3мин.
Время технического обслуживания – Ттех = 10.1мин;
Время организационного обслуживания – Торг = 13.5мин;
Время перерыва – Тнп = 4.2мин.
на наладку станка – 18мин;
при обработке с люнетом – 5мин;
на операцию – ТПЗ = 23мин.
Основное технологическое время – То = 0.6мин.
на установку и снятие детали – 10.3мин;
на совмещение оси шпинделя с осью обрабатываемого отверстия – 6.2мин;
связанное с переходом – 0.96мин;
изменить частоту вращения – 0.24мин;
изменить величину подачи – 0.18мин;
на измерение – 0.15мин.
Вспомогательное время на операцию – 18.03мин.
Время технического обслуживания – Ттех = 1.12мин;
Время организационного обслуживания – Торг = 1.5мин;
Время перерыва – Тнп = 0.5мин.
на наладку станка – 22мин;
при установке зажимного приспособления – 3мин;
на операцию – ТПЗ = 25мин.
Основное технологическое время – То = 59.54мин.
на установку и снятие детали – 9мин;
связанное с переходом – 2мин;
на изменение числа оборотов шпинделя – 0.36мин;
на изменение подачи – 0.32мин;
перемещение стола св. 500 до 1000мм – 0.13мин;
перемещение шпиндельной головки – 0.17мин.
Вспомогательное время на операцию – 12мин
Время технического обслуживания – Ттех = 4.3мин;
Время организационного обслуживания – Торг = 5.7мин;
Время перерыва – Тнп = 1.8мин.
Основное технологическое время – То = 23.62мин.
Вспомогательное время на операцию – 17.88мин.
Время технического обслуживания – Ттех = 2.49мин;
Время организационного обслуживания – Торг = 3.32мин;
Время перерыва – Тнп = 1.04мин.
Основное технологическое время – То = 68.72мин.
на установку и снятие детали – 6.9мин.
Вспомогательное время на операцию – 6.9мин.
Время технического обслуживания – Ттех = 4.54мин;
Время организационного обслуживания – Торг = 6.05мин;
Время перерыва – Тнп = 1.9мин.
на наладку станка – 12мин;
при обработке с люнетом – 3мин;
при установке шлифовального круга – 8мин.
Определим нормы времени по операциям технологического процесса обработки корпуса пневмоцилиндра.
Основное технологическое время – То = 20.87мин.
на продольное и поперечное растачивание с предварительным промером – 12.35мин;
со взятием пробных стружек – 2.4мин;
изменить частоту вращения планшайбы – 1.52мин;
резец расточной – 4.8мин;
резец прорезной – 1мин;
время на установку и снятие детали – 4.1мин.
Вспомогательное время на операцию – 23.77мин.
Время технического обслуживания – Ттех = 2.68мин;
Время организационного обслуживания – Торг = 3.57мин;
Время перерыва – Тнп = 1.12мин.
на наладку станка – 27мин;
Такт выпуска деталей – 121.8мин.
Основное технологическое время – То = 13.3мин.
связанное с переходом – 0.42мин;
на изменение числа оборотов шпинделя – 0.18мин;
на изменение подачи – 0.16мин;
Вспомогательное время на операцию – 8.26мин
Время технического обслуживания – Ттех = 1.3мин;
Время организационного обслуживания – Торг = 1.7мин;
Время перерыва – Тнп = 0.54мин.
на наладку станка – 19мин;
при установке зажимного приспособления – 2мин;
на операцию – ТПЗ = 21мин.
Основное технологическое время – То = 31.38мин.
связанное с переходом – 2.16мин;
изменить частоту вращения шпинделя – 1.44мин;
изменить величину подачи – 1.44мин;
установить и снять инструмент – 2.16.
Вспомогательное время на операцию – 14.7мин.
Время технического обслуживания – Ттех = 2.8мин;
Время организационного обслуживания – Торг = 3.7мин;
Время перерыва – Тнп = 1.15мин.
на операцию – ТПЗ = 15мин.
Основное технологическое время – То = 25.4мин.
связанное с переходом – 0.18мин;
изменить частоту вращения – 0.48мин;
изменить величину подачи – 0.72мин;
Вспомогательное время на операцию – 8.9мин.
Время технического обслуживания – Ттех = 2.06мин;
Время организационного обслуживания – Торг = 2.7мин;
Время перерыва – Тнп = 0.86мин.
9. ПРОЕКТИРОВАНИЕ СХЕМ НАЛАДОК.
Схемы наладок разрабатываются для всех станочных операций и изображаются на листах формата А – 1 в графической части. Предварительно эскизы схем наладок чертятся на листах формата А – 4. На эскизах изображается заготовка в произвольном масштабе. Указываются технологические размеры с граничными отклонениями связанные с технологическими базами шероховатость поверхностей режущие инструменты в конце рабочего хода опоры и зажимы приспособления направление движения инструмента. На листах графической части кроме перечисленного приводят режимы обработки для всех инструментов.
В пояснительной записке представлены эскизы схем наладок обработки вала маховика и корпуса пневмоцилиндра.
КОНСТРУКТОРСКИЙ РАЗДЕЛ.
1. ПРОЕКТИРОВАНИЕ СТАНОЧНОГО ПРИСПОСОБЛЕНИЯ.
1.1. РАСЧЕТ СИЛ ЗАКРЕПЛЕНИЯ.
Приспособление проектируется для фрезерной операции механической обработки корпуса пневмоцилиндра.
Исходными данными для проектирования станочного приспособления являются:
- рабочий чертеж заготовки и готовой детали;
- технологический процесс на предшествующую и выполняемую операции с технологическими эскизами;
- годовой объем выпуска деталей;
- альбом типовых конструкций приспособлений;
- паспортные данные станка.
Для расчета сил закрепления в наиболее общем случае необходимо знать условия проектируемой обработки – величину направление и место приложения сил сдвигающих заготовку а также схему ее установки и закрепления. Расчет сил закрепления может быть сведен к задаче статики на равновесие заготовки под воздействием приложенных к ней внешних сил. Сила закрепления должна быть достаточной для предупреждения смещения установленной в приспособлении заготовки. В процессе фрезерования поверхности на заготовку действует сила резания Рz которая смещает заготовку. Определим силу закрепления Q по формуле:
гдеРz – сила резания;
К – коэффициент запаса прочности;
гдеК0 – коэффициент учитывающий внезапные факторы;
К1 – учитывающий неровности поверхностей;
К2 – увеличение сил резания от затупления режущего инструмента;
К3 – увеличение силы резания при прерывистом фрезеровании;
К4 – учитывающий тип устройства;
К5 – удобное положение рукоятки;
К6 – наличие моментов стремящихся повернуть заготовку.
f1 – коэффициент трения между поверхностью заготовки и рычага;
f2 – коэффициент трения между поверхностью заготовки и опорами.
Для определения усилия N на штоке гидроцилиндра (рисунок 3.1) рассмотрим рычаг закрепляющий заготовку как статически определимую систему сходящихся сил и находящуюся в равновесии. Определим внешние силы и опорные реакции методом построения силового многоугольника (рисунок 3.2).
Исходными данными является сила зажима Q которая возникает от прижатия двух рычагов к заготовке угол трения φ = коэффициент масштаба .
По построенному многоугольнику сил определили: Q2 = 18.2 кН R1 = 18.5кН R2 = 12.5 кН F1 = 3.5 кН F2 = 2.4кН N = 12.3кН S = 22.3кН.
1.2. РАСЧЕТ ТОЧНОСТИ СТАНОЧНОГО ПРИСПОСОБЛЕНИЯ.
Проектируемое станочное приспособление должно обеспечивать требуемый уровень точности что соответствует выполнению условия:
где – действительная величина погрешности;
[] – допустимая величина погрешности.
Допустимая величина погрешности зависит от принятой схемы базирования величина допуска на размер и погрешностей механической обработки.
где IT – допуск на выполняемый размер мкм;
Ky – коэффициент ужесточения точности обработки: Ky = 0.6;
W – средне экономическая точность обработки.
Действительная погрешность приспособления включает три составляющие:
где- погрешность базирования;
- погрешность закрепления;
- погрешность положения.
Погрешность базирования = 0 потому что установочная база совмещается с конструкторской базой.
Погрешность закрепления определяется по формуле
гдеKRz – коэффициент учитывающий шероховатость поверхности;
KHB – коэффициент учитывающий твердость поверхности;
С – коэффициент характеризующий условия контакта;
Q – сила действующая на опору Н;
F – площадь контакта опоры с заготовкой см2.
Погрешность положения
где - погрешность из-за неточности изготовления и сборки деталей СП;
- погрешность из-за неточности установки на столе станка;
- погрешность из-за износа поверхностей установочных элементов.
где – коэффициент определяющий влияние условий обработки на величину износа;
N – годовая программа выпуска деталей;
α – угол между направлением выполняемого размера и направлением перпендикулярным поверхности установочного элемента в зоне контакта.
Погрешность из-за неточности установки на столе станка равна = 100 мкм.
Тогда погрешность положения равна
Действительная погрешность равна
Условие выполняется.
1.3. ВЫБОР ГИДРОЦИЛИНДРА И СБОРОЧНЫХ ЭЛЕМЕНТОВ ПРИСПОСОБЛЕНИЯ.
Усилие зажима заготовки в приспособлении передается от гидроцилиндра двустороннего действия через рычажную систему.
Зная усилие на штоке N = 12.3 кН определим диаметр поршня в гидроцилиндре:
гдер = 2.5 МПа – давление масла на поршень;
= 0.85 – КПД гидроцилиндра.
Из стандартного ряда выбираем D = 80мм. По известному номинальному диаметру поршня выбираем гидроцилиндр двустороннего действия (См [3] Т3 стр. 583):
Номинальный диаметр мм80
Усилие теоретическое Н:
Обозначение гидроцилиндра: 7021 – 0274 ГОСТ 19900 – 74.
В качестве уплотнения для крышки и поршня гидроцилиндра применяем два уплотнительных кольца 080 – 085 – 30 ГОСТ 9833 – 81 сечением 3 мм.
В качестве уплотнения штока применяем: уплотнительное кольцо 036 – 040 – 25 ГОСТ 9833 – 81 сечением 3 мм.
Выбираем сальниковое кольцо из грубошерстного войлока изготовляемого по ГОСТ 6418 – 67; внутренний диаметр кольца – 35мм; наружный диаметр – 48мм; ширина – 5.0мм.
Выбираем болты откидные: 7002 – 0607 ГОСТ 14274 – 69.
Выбираем рычаги угловые: 7018 – 0438 ГОСТ 12472 – 67.
Ось 6 – . 40X. Ц15 ГОСТ 9650 – 80;
Выбираем опоры сферические 7034 – 0328 ГОСТ 13441 – 68.
2. ПРОЕКТИРОВАНИЕ РЕЖУЩЕГО ИНСТРУМЕНТА.
Для проектирования режущего инструмента исходными данными являются операция в которой участвует режущий инструмент режимы резания механической обработки.
Проектируемый режущий инструмент – фреза торцовая сборная насадная.
Предварительно задаемся длиной фрезы L=45мм и соответственно ее диаметром D=250мм числом зубьев z=26.
Скорость резания V=15.7 ммин; подача S=124.8 мммин; глубина резания t=3.7мм сила резания Pz = 18950Н; Т0 = 1.5мин.
Определим диаметр отверстия под оправку
гдеМсум – суммарный момент при изгибе и скручивании оправки ;
и.д. – допустимое напряжение на изгиб оправки для конструкционных сталей и.д. = 250МПа.
Суммарный момент определим по формуле
гдеР – равнодействующая сил Pz и
l – длина посадочного участка оправки l = 40мм.
Принимаем ближайший диаметр отверстия фрезы по ГОСТ 9472 – 83: .
Устанавливаем окончательно наружный диаметр фрезы: D = 3d = мм. Так как диаметр торцовой фрезы зависит и от ширины фрезерования то по СТ СЭВ 201 – 75 выбираем D = 250мм. Длину фрезы L = 45мм.
Окончательное число зубьев фрезы
гдеm – коэффициент зависящий от типа фрезы m = 1.2.
Принимаем четное число зубьев z = 20.
Определяем шаг зубьев фрезы:
окружной торцовый шаг
Проверим полученные величины z и Sос на условие равномерного фрезерования:
где В – ширина фрезерования В = 156.6 мм.
Полученная величина должна быть целым числом или величиной близкой к нему.
Условие равномерного фрезерования обеспечено.
Отверстие фрезы и шпоночный паз выполняем по ГОСТ 9472 – 83.
Определим геометрические параметры рабочей части фрезы: главный задний угол α = ; передний угол γ = ; ширина ленточки f = 1.5 мм.
Выбираем материал фрезы: корпуса – сталь 40Х; ножей – твердый сплав Т5К10; клиньев – сталь У8А.
Назначаем твердость деталей фрезы после термической обработки: корпуса 32 – 42 HRCэ; режущей части ножей – не менее 88.5 клиньев 41 – 52 HRCэ.
Допуск на основные элементы фрезы и другие технические требования принимаем по ГОСТ 8721 – 69. Предельные отклонения размеров рифлений – по ГОСТ 2568 – 71.
Рабочий чертеж фрезы с указанием основных технологических требований выполнен в графической части диплома. Методику расчетов смотрите [7] стр. 243.
1. ИССЛЕДОВАНИЕ ТЕМПЕРАТУРЫ В ЗОНЕ РЕЗАНИЯ ПРИ ТОЧЕНИИ НА ТОКАРНОМ СТАНКЕ.
Один из главнейших факторов определяющих процесс резания — теплота образующаяся в результате работы резания. Законы теплообразования объясняют ряд явлений связанных с нагрузкой резца его стойкостью качеством обработанной поверхности. Чтобы правильно использовать режущий инструмент необходимо знать эти законы.
Теплота Q в процессе резания образуется в результате:
)внутреннего трения между частицами обрабатываемого металла в процессе деформации Qдеф;
)внешнего трения стружки о переднюю поверхность резца Qп.т.
)внешнего трения поверхности резания и обработанной поверхности о задние поверхности резца Qз.тр.;
)отрыва стружки диспергирования Qдисп (образования новых поверхностей)
Предполагая что механическая работа резания полностью переходит в теплоту получим
где Q— количество теплоты в ккалмин; R — работа резания в кгс ммин (R = Рzv);
Е — механический эквивалент теплоты (Е = 427 кгс мккал).
В действительности в теплоту обращается не вся работа резания: небольшая часть ее переходит в потенциальную энергию искаженной кристаллической решетки. Поэтому более правильно формулу выразить так:
где — коэффициент учитывающий указанные потери незначительные по величине. В обычных расчетах этой потерей пренебрегают.
Для успешного воздействия на процесс резания важно знать не только количество теплоты но и распределение ее т. е. степень концентрации теплоты в различных участках изделия стружки и резца. Если бы вся образующаяся теплота быстро и равномерно распределялась по всему объему изделия и инструмента она быстро отводилась бы в пространство не причиняя им вреда. В действительности процесс протекает иначе: большое количество теплоты концентрируется в определенных зонах сильно повышая их температуру. Здесь неизбежны потеря резцом твердости и затупление его и даже возможно изменение структуры тончайшего слоя обработанной поверхности если не будут приняты соответствующие меры.
Некоторые исследователи (А. Я. Малкин) полагают что регулированием потока теплоты можно воздействовать на процесс резания в благоприятную сторону и тем облегчить работу
инструмента и повысить качество обработанной поверхности.
На основе теоретического и экспериментального исследований процесса теплообразования можно выявить законы изменения температуры резания (на поверхности контакта стружки с передней гранью резца) а также температуры режущего инструмента и обрабатываемой детали в зависимости от различных факторов.
Надо полагать что в процессе образования сливной стружки теплота концентрируется в трех основных зонах (рис.1): в зоне сдвига элементов стружки АМ где происходит пластическая
деформация; на площади контакта стружки по передней поверхности инструмента АО; на площади контакта задней грани инструмента с обрабатываемой деталью.
Работой диспергирования обычно пренебрегают.
Каждый источник теплоты имеет свою сферу непосредственного воздействия (рис. 1)
Следовательно наиболее высокая температура — температура резания — должна наблюдаться в стружке в зоне контакта ее с передней поверхностью инструмента так как здесь концентрируется
наибольшее количество теплоты Рисунок 1. Зоны теплоты.
образующейся в результате деформации стружки и трения ее по передней поверхности резца. Например наибольшее количество теплоты образующейся вследствие деформации (на поверхности АМ) остается в стружке и частично поглощается обрабатываемой деталью. Теплота трения стружки (на поверхности АО) остается в основном в стружке и частично (3—5%) направляется в инструмент. Теплота трения по задним граням инструмента (поверхность АР) направляется в деталь и резец. При обработке металлов с низкой теплопроводностью например жаропрочных и титановых сплавов в резец отводится до 20—40% всей теплоты.
Потери теплоты от конвекции и радиации в процессе резания ничтожно малы; невелико количество теплоты уходящей в деталь так как стружка весьма быстро формируется в зоне резания и столь же быстро проходит зону контакта с резцом. Однако теплота поглощаемая изделием из жаропрочных сталей и сплавов резко возрастает и при малых скоростях может достичь 35—45% всей теплоты резания.
Пренебрегая работой трения по задним граням инструмента (которая мала при достаточно острой режущей кромке и большом заднем угле) можно полагать что подавляющее количество теплоты должно сосредоточиваться в стружке. Опыты Н. Н. Савина Я. Г. Усачева С. С. Можаева и др. определявших количество теплоты в стружке калориметрическим методом показали что в зависимости от скорости резания глубины резания и подачи при обработке конструкционной стали в стружке содержалось 60—80% всей теплоты резания а при скоростных режимах резания свыше 90%.
На рис. 2 а показана схема сил действующих в зоне резания. Считая что вся работа резания в единицу времени работа трения стружки по передней поверхности — усадка стружки) получим работу деформации стружки
Но (пренебрегаем силой трения по задней поверхности резца) и следовательно работа деформации стружки
Повышение температуры стружки благодаря ее деформации составит в среднем
где — средняя температура стружки когда последняя покидает зону деформации в °С;
— температура окружающей среды в °С; — коэффициент учитывающий потерю теплоты
на скрытую энергию деформации (принимаем = 095); — коэффициент учитывающий переход части тепла в изделие (по Вейнеру = 01 при v = 100 ммин = 005 при
v = 300 ммин); Е — механический эквивалент теплоты (Е = 427 *10 -3 кгс мккал);
с — теплоемкость нагретой стружки в ккалкгс град; d — плотность стружки (78 *10-6 кгсмм3);
b — ширина среза в мм; а — толщина среза в мм.
Рис. 2. Схема сил действующих в процессе резания (а)
и схема контакта стружки и резца (б)
Принимая — р кгсмм2 (удельная сила резания) и пренебрегая значением получим
Покидая зону деформации нагретая до температуры стружка трется по передней поверхности резца со скоростью на площади контакта шириной b и длиной l (рис. 2 б).
Теплота работы силы трения по передней грани в единицу времени
Чтобы определить температуру на передней поверхности резца полученную в результате трения стружки будем рассматривать резец как твердый стержень с поперечным сечением равным blна одной стороне которого поддерживается постоянная температура . Для решения поставленной задачи используется уравнение теплопроводности
где — температуропроводность; — теплопроводность резца; с' — теплоемкость резца; d'— плотность; — время в течение которого стружкапроходит площадь контакта длиной l;
Решая уравнение по М. П. Левицкому при начальных и граничных условиях при x = 0 при получим уравнение
где — температура возникающая от теплоты трения в данной точке и в данный момент времени ; — глубина на которую проникает теплота трения за время .
Минуя промежуточные вычисления и пренебрегая температурой внешней среды получим
Суммируя температуры деформации стружки и трения ее по передней поверхности инструмента получим температуру резания т. е. среднюю температуру на площади контакта стружки и инструмента
Формула показывает закономерность изменения температуры резания в зависимости от разных факторов. На основе ее построены графики изменения составляющих температуры
резания в зависимости от скорости резания для минералокерамического (рис.3 а) и для твердосплавного резца (рис. 3 б). Как видим с увеличением скорости резания уменьшается температура деформации но возрастает температура трения. В результате температура резания повышается но в значительно меньшей степени чем сама скорость.
Вместе с тем при одних и тех же условиях температура резания получается более высокой при работе минералокерамическим резцом (рис. 3 а) сравнительно с твердосплавным (рис. 3 б)
что подтверждается практикой.
Надо ожидать что температура резания в действительности должна быть более высокой чем это получается расчетом по теоретической формуле так как здесь не учтена теплота трения по задней поверхности резца. Последняя будет все более проявляться с увеличением скорости резания по мере затупления резца; при этом особенно заметно будет повышаться температура обрабатываемой детали.
Обрабатываемая деталь нагревается в основном теплотой деформации. Очевидно температура детали должна уменьшаться с увеличением скорости резания поскольку при этом уменьшается (рис. 3). Подобный вывод подтверждается на практике при работе острым резцом в нормальных условиях. Однако по мере затупления резца и значительного уменьшения
Скорость резания v мминСкорость резания v ммин
Рис. 3. Изменение составляющих температур резания при обработке стали: а — для минералокерамического резца; б — для твердосплавного резца; сталь ОХН4М; t = 2 мм; s = 014 ммоб; = 10°
заднего угла и угла в плане положение меняется. В этом случае с увеличением силы трения заметно растут работа и теплота трения по задней поверхности резца и поэтому температура детали повышается с увеличением скорости резания v. На рис. 4 показано изменение температуры детали при фрезеровании резьбы вращающимся резцом (вихревое нарезание). Замечаем неизменное повышение температуры детали по мере затупления резца. Вместе с тем температура обрабатываемой детали уменьшается с увеличением подачи s. Это вполне закономерно так как с увеличением s сила трения на задней поверхности резца остается почти неизменной но при определенной длине детали сокращается относительный путь резца (время обработки) и следовательно уменьшается работа силы резания.
Сложнее обстоит дело с температурным полем резца. Можно было бы предполагать что наибольшая температура должна быть вблизи режущей кромки так как здесь располагаются основные источники теплоты На рис. 5 схематично представлено температурное поле стружки и резца составленное Н. И. Резниковым по опытным данным других исследователей. Линии постоянных температур т т (изотермы) в стружке расположены параллельно поверхности сдвига (ориентировочно) а у резца почти концентрично вокруг режущей кромки. В этом случае согласно теории теплопроводности тепловые потоки должны быть направлены нормально изотермам; в схеме они показаны соответствующими кривыми со стрелками: п — в деталь; п' — в стружку; k — в резец.
Наиболее высокие температуры наблюдаются вблизи режущей кромки и в зоне нароста В действительности положение более сложное так как температура резания зависит и от длины кон-
такта поверхности резания и стружки по задней и передней поверхностям инструмента. Чем
меньше длина контакта на задней поверхности тем ниже среднее значение температуры
резания и тем ближе к режущей кромке располагается ее максимум. С уменьшением длины контакта стружки с передней поверхностью средняя температура также снижается но максимум температуры удаляется от режущей кромки. При скоростной обработке температура в зоне резания доходит до 800° С а на поверхности трения по передней грани достигает даже 1200° С
и выше. Низкая теплопроводность твердых сплавов и особенно минералокерамики является
Износ по задней грани h3 мм
Рис. 4 Температура обрабатываемой детали при резании вращающимся резцом в зависимости от подачи s и износа резца
причиной того что теплота резания сосредоточивается в передней части резца прилегающей к его вершине что способствует ее пластической деформации. При этом режущие способности инструмента сохраняются ввиду его значительной красностойкости. Однако очень высокий температурный градиент свойственный минералокерамическому резцу способствует тепловому
удару разрушающему режущую кромку инструмента.
Любопытно что нагрев державки с малотеплопроводной режущей пластиной из твердого сплава и особенно минералокерамики происходит не только посредством контактной передачи
тепла от пластины к державке но и в значительной степени через лучеиспускание от стружки и поверхности резания перемещающихся мимо резца и передающих ему часть теплоты. Это имеет
существенное значение для стойкости режущего инструмента и точности обработки детали зависящей от температурной деформации резца. На рис. 6 показаны кривые температурного удлинения минералокерамического резца при обработке стали ОХН4М. Можно заметить значительное уменьшение деформации резца
Рис. 5 Температурное поле в зоне резания и резца.
Продолжительность работы резца Т мин
Рис 6 Кривые температурного удлинения минералокерамического резца:
— l = 15 мм 2 — l = 3 мм 3 — стружка отводилась от резца
или задние грани державки изолировались.
с удалением режущей кромки от державки резца или при изоляции задней поверхности резца.
Эффект лучеиспускания в большой степени зависит от способности тела поглощать тепловые лучи. Например абсолютно черное тело поглощает все падающее на него тепло — условный коэффициент = 1:
Значения для различных тел
Чугун шероховатый сильно окисленный .094
Железо матовое окисленное 096
Железо блестящее отполированное 029
Медь полированная .013—017
Медь прокатанная .064
Медь шероховатая 076
Эти данные представляют значительный интерес так как показывают большую роль блестяще обработанных граней режущего инструмента в отношении его стойкости и качества обработанной поверхности.
При весьма низкой температуре всего изделия и больших скоростях резания тонкий слой его обработанной поверхности может иметь достаточно высокую температуру способную изменить структуру этого слоя. Поэтому назначая режим резания необходимо учитывать последующую чистовую обработку при которой будет удален поврежденный слой детали.
Теоретический расчет температуры резания встречает значительные трудности так как в соответствующих расчетных формулах независимые переменные являются в действительности
взаимозависимыми параметрами. Так теплоемкость С увеличивается а теплопроводность уменьшается с возрастанием температуры. Длина контакта стружки и резца уменьшается
с увеличением скорости резания но заметно растет по мере износа резца и образования лунки на передней поверхности резца.
Значения постоянных коэффициентов также изменяются в зависимости от различных факторов. К этому надо добавить что температура резания зависит и от вида процесса
резания: при несвободном резании резец нагревается больше чем при свободном резании. Поэтому для расчета температуры резания чаще пользуются эмпирическими формулами показывающими закономерности изменения температуры резания в зависимости от различных факторов и справедливыми в определенных границах и условиях.
2. ВЛИЯНИЕ РАЗЛИЧНЫХ ФАКТОРОВ НА ТЕМПЕРАТУРУ РЕЗАНИЯ
ПО ЭКСПЕРИМЕНТАЛЬНЫМ ДАННЫМ
Как уже отмечено температура резания растет менее интенсивно чем скорость. По мере нагрева резца разность температур стружки и резца падает а поэтому интенсивность передачи теплоты от стружки резцу уменьшается. Следовательно с увеличением скорости резания v температура резца значительно поднимается но в меньшей степени чем скорость. Современные экспериментальные исследования процесса резания высокопрочных сталей с ультравысокими скоростями (до 72 000
Рис. 7. Влияние скорости резания на температуру резания Ст.3:
— а = 05 мм; 2 — а = 02 мм
ммин) когда процесс происходил адиабатически (без теплообмена) показали температуру в зоне резания на уровне 30—65° С вполне допустимом стойкостью быстрорежущего резца1. Надо полагать что кривые 9—v с повышением скорости резания будут приближаться к уровню температуры плавления обрабатываемого материала а затем снижаться с дальнейшим повышением скорости (рис. 7). Последние графики получены по опытным данным Д. X. Касрадзе2 при резании Ст.3 при v = 1000-60 000 ммин. Подобное явление сопровождается резким снижением сил резания и значительным охрупчиванием металла в зоне резания. Этот процесс способствует быстрому отрыву стружки при полном отсутствии пластической деформации (усадки) стружки. Наблюдающаяся отрицательная усадка (удлинение стружки) могла быть вызвана центробежными силами при весьма больших скоростях.
Влияние глубины резания и подачи. Не трудно предугадать зависимость между глубиной резания t подачей s и температурой если рассмотреть изменение прироста и отвода теплоты на резце с изменением t и s. С увеличением подачи возрастает давление стружки на резец а вместе с ним и работа деформации. Но при этом как известно усадка стружки уменьшается и следовательно работа деформации приходящаяся на 1 мм3 стружки также уменьшается. К тому же трение на задней поверхности инструмента с увеличением подачи мало изменяется. Поэтому количество теплоты образующейся в стружке будет увеличиваться в меньшей степени сравнительно с увеличением подачи. В то же время с утолщением стружки отвод теплоты улучшается т.к. площадь контакта стружки с резцом расширяется. В результате температура резания повышается с увеличением подачи но в меньшей степени чем при повышении скорости.
Еще меньше влияет на температуру резания глубина резания т.к. нагрузка на единицу длины режущей кромки не изменяется: с увеличением глубины резания при постоянном угле в плане пропорционально увеличивается длина работающей и режущей кромки почти в такой же степени усиливается теплоотвод от нее и следовательно на единицу длины режущей кромки увеличение притока теплоты будет весьма незначительным; в результате температура мало изменится с увеличением глубины резания.
Влияние материала резца и обрабатываемого материала на температуру резания. Естественно ожидать что при резании хрупких металлов например чугуна когда работа пластической деформации весьма мала и удельные силы резания незначительны температура резания заметно ниже чем при обработке стали. Давление чугунной стружки сосредотачивается непосредственно на режущей кромке или вблизи нее но это весьма неблагоприятное обстоятельство влияет больше на абразивно-механический износ режущей кромки чем на температуру резания.
Само собой разумеется что нагрев инструмента зависит от теплоемкости и особенно от теплопроводности материала изделия и самого инструмента. Например при обработке цветных металлов температура резания должна быть сравнительно низкой не только из-за малой нагрузки но и вследствие большой теплопроводности цветных металлов. И наоборот при резании жаропрочных сталей и сплавов обладающих низкой теплопроводности значительно повышается
температура резания (в два – три раза) сравнительно с конструкционными сталями. То же можно сказать относительно инструмента: чем ниже теплопроводность тем выше температура его режущей кромки.
По этой причине температура резания при работе твердосплавными резцами получается более низкой по сравнению с минералокерамическими (рис. 3). То же самое можно сказать и о влиянии резца на температуру резания. Последняя уменьшается с увеличением площади поперечного сечения резца.
Более того оказывается возможным работать резцами из цветных металлов поскольку
при v = 27 000—36 000 ммин силы резания резко снижались.
См.: Термические явления при сверхскоростном резании металлов. Труды ГИСХ XIV Сухуми 1970 г.
Влияние геометрии резца на температуру резания. Как известно с увеличением угла резания увеличивается сила резания следовательно должны повышаться количество образующейся теплоты и температура резания. Отвод тепла в данном случае также будет усиливаться с увеличением угла клина (угла заострения) но в меньшей степени чем теплообразование и в результате температура будет расти.
Величина угла в плане также влияет на температуру резания. С уменьшением угла несколько увеличивается нагрузка на резец и казалось бы нагрев его должен усиливаться. Однако
на самом деле получается обратное: с уменьшением угла удлиняется режущая кромка увеличивается угол при вершине и как следствие значительно улучшается теплоотвод.
В заключение надо отметить заметное влияние на температуру резания смазочно-охлаждающих жидкостей. При этом падение температуры вызвано как охлаждающим эффектом так и уменьшением трения в процессе резания.
Путем математической обработки опытных графиков А М. Даниелян вывел общую формулу зависимости температуры резания от различных факторов при нормальной обработке стали
быстрорежущим резцом
Здесь ; r — радиус закругления вершины резца; F — площадь поперечного сечения резца; — постоянная зависящая от обрабатываемого материала и инструмента или в упрощенном виде для стали ( = 77 кгсмм2 = 22%)
и для чугуна (приблизительно)
АВТОМАТИЗАЦИЯ ТЕХНОЛОГИЧЕСКИХ ПРОЦЕССОВ.
1. ПРИНЦИП ИЗМЕРЕНИЯ РАССТОЯНИЙ И ЛИНЕЙНЫХ ПЕРЕМЕЩЕНИЙ.
Обобщенная схема измерения расстояний и линейных перемещений посредством линейных интерференционных сигналов (ЛИС) на основе двулучевого интерферометра изображена на рис. 1а.
Рассматривая принципы и методы измерения излучение лазера 1 будем считать идеальной плоской волной. Интерферометр состоящий из светоделителя 2 опорного отражателя 3 и измерительного отражателя 4 настроен на бесконечно широкую полосу. Интенсивность интерференционного сигнала I на фотоприемнике 5 изменяется по закону (рис. 1б)
где I0 и I~ - постоянная составляющая и амплитуда переменной составляющей сигнала соответственно; 2L - геометрическая разность хода интерферирующих пучков; - длина волны излучения. Расстояние от нуля интерферометра О до измерительного отражателя 4:
где P - порядок интерференции - фаза интерференционного сигнала I определяемого формулой (5.1).
Метод счета полос заключается в измерении (счете) числа периодов изменения интерференционного сигнала при изменении геометрической разности хода (ГРХ) сигнала. Для предотвращения ложного счета вследствие механических вибраций и турбулентности воздуха осуществляют реверсивный счет при котором определяют знак каждого счетного периода приращения порядка интерференции.
Применяют два способа реверсивного счета полос: со счетом полос на основе квадратурных сигналов и на основе частотной модуляции.
Контроль размера шейки вала маховика 150k6 осуществляется интерферометром со счетом полос на основе частотной модуляции.
2 ИНТЕРФЕРОМЕТР СО СЧЕТОМ ПОЛОС НА ОСНОВЕ ЧАСТОТНОЙ МОДУЛЯЦИИ.
На рисунке 2а приведен пример схемы ЛИС. Двухчастотный лазер 1 излучает две волны с частотами 1 и 2 одна из которых поляризована параллельно а другая - перпендикулярно плоскости чертежа. Светоделитель 2 отклоняет часть излучения каждой частоты для формирования опорного сигнала I0. Поляризационная призма-куб 3 разделяет составляющие излучения разных частот и направляет их в разные плечи интерферометра. Пластины 4 - позиция 7 оптические оси которых составляют угол 450 с плоскостью чертежа меняют состояние поляризации дважды прошедших пучков на ортогональное.
Поляризационная призма-куб 3 обеспечивает суперпозицию пучков возвращенных отражателями 4 и 5 в направлении I1. После поляризаторов 6 ось пропускания которых составляет угол 450 с плоскостью чертежа в результате интерференции пучков с разными частотами образуются опорный I0 и измерительный I1 сигналы биения. Поскольку номенклатура двухчастотных лазеров и значения разности частот которые они обеспечивают ограничены в качестве источника излучения часто используют одночастотный лазер сдвигая частоты ортогональных составляющих его излучения акустооптическими модуляторами которые устанавливают на входе выходе или в одном из плеч интерферометра . В этом случае опорный сигнал I0 может быть получен непосредственно из модулирующих сигналов подаваемых на акустооптические модуляторы.
Частота частотной модуляции аналогично частоте фазовой модуляции ограничивает время измерения . Однако при использовании акустооптических модуляторов она может быть установлена достаточно большой чтобы этим ограничением можно было пренебречь. Тогда время однократного измерения фазы определяется временем задержки фазоизмерительного устройства и составляет для современных ЛИС около 10 мкс .
Так как ЛИС на основе частотной модуляции обеспечивают время измерения на порядок меньше чем ЛИС на основе фазовой модуляции допустимые скорости изменения ГРХ в них на порядок выше. Эти ЛИС считаются в большей степени подходящими для высокоточных измерений в реальном масштабе времени . При равной погрешности они имеют несколько больший диапазон измерения ГРХ.
На основе методов прямого измерения фазы разрабатывают ЛИС для измерения медленно меняющихся во времени и незначительных по величине расстояний с высокой точностью. Основная область применения таких ЛИС - контроль профиля и шероховатости поверхностей в том числе оптических. Другая обширная сфера применения - интерференционные датчики физических величин изменение которых можно преобразовать в изменение геометрической или оптической разности хода интерферирующих лучей (давление и влажность атмосферы температура напряженность электрического и магнитного полей и др.).
Частотную модуляцию интерференционного сигнала обеспечивают путем суперпозиции двух волн разной оптической частоты. В этом случае закон изменения интенсивности имеет вид
где I1 и I2 - интенсивности 1 и 2 - оптические частоты 1 и 2 - фазы интерферирующих волн.
Все переменные составляющие сигнала (4) кроме последней вследствие высокой частоты не могут быть детектированы фотоприемником непосредственно.
Выбирая близкие оптические частоты интерферирующих волн получают частоту b=1-2 последней составляющей удобную для обработки в фотоэлектронной системе. Эту частоту называют сигналом биения.
Особенность сигнала биения в том что даже в отсутствие изменения ГРХ между интерферирующими волнами интенсивность изменяется по гармоническому закону. Если одна из интерферирующих волн проходит дополнительный геометрический путь 2L то сигнал биения получает дополнительный фазовый сдвиг =L эквивалентный фазе немодулированного интерференционного сигнала на длине волны при
ГРХ интерферирующих лучей равной 2L. Чтобы определить ГРХ измеряют фазовый сдвиг (рис. 3б)
между опорным и измерительным сигналами биения:
I0(t)=A0 *COS[2(1-2)t+(1-2)]
I1(t)=A1 *COS[2(1-2)t+(1-2)+(t)]
где A0 и A1 - их амплитуды.
Вместо непрерывного измерения разности фаз между сигналами подсчитывают число биений каждого из них N0 и N1 и отслеживают разность N=N1-N0 (рис. 3в). Если ГРХ в интерферометре не меняется частоты опорного и измерительного сигналов равны f=f1=12 и N=0. При движении отражателя 4 частота биения измерительного сигнала становится равной f1=1-2+ где=(t) t. Изменение ГРХ равно L==(N1-N0)*. Знак при n зависит от направления движения отражателя 4. Связь между знаками L и остается однозначной до тех пор пока [][1-2]. Чтобы исключить влияние низкочастотных шумов на работу ЛИС обеспечивают ¦¦[1-3]+ш где ш - верхняя граничная частота шумов. Таким образом в ЛИС со счетом полос на основе частотной модуляции имеет место принципиальное ограничение скорости изменения измеряемых расстояний. В современных ЛИС она не превышает 1 мс. При счете числа биений сигналов дискрета измерения приращений ГРХ равна . Для повышения точности измерения уменьшают дискрету счета умножая частоты этих сигналов в электронной системе. Чаще всего обеспечивают дискрету 64 . Метод счета полос на основе частотной модуляции также как и на основе квадратурных интерференционных сигналов не ограничивает максимальное значение измеряемых расстояний которые в известных ЛИС достигают 100 м.
ЛИС со счетом полос применяют для измерения больших расстояний и быстрых линейных перемещений с интерференционной точностью. Благодаря достигнутому уровню технических характеристик и высокой надежности они находят широкое применение в метрологии (аттестация станков и технологического оборудования поверка вновь разрабатываемых инструментов измерения расстояний и т.д.). Очень перспективная область их применения - преобразователи линейных перемещений координатно-измерительных систем станков и технологического оборудования.
Наибольшее распространение в практике получили интерферометры типа Маха – Цандера и Майкельсона.
Мультиплексный волоконно-оптический датчик применяется для измерения широкого класса различных физических величин.
В мультиплексных интерференционных ВОД одномодовый волоконный световод применяется не только в качестве чувствительного элемента но и служит также подводящим трактом оптически связывающим чувствительные элементы с источником и приемником излучения. Поэтому система обработки сигнала в таком датчике должна обеспечивать как измерение величины внешнего воздействия на чувствительный элемент так и должна позволить разделить воздействия на различные чувствительные элементы.
Чувствительные элементы различаются по групповой задержке интерферирующих лучей методом когерентной частотной рефлектометрии. Чувствительные элементы ВОД представляют собой участки одномодового волоконного световода расположенные между отражателем с малым коэффициентом отражения.
При изменении частоты излучения лазера по линейному закону отклик фотоприемника на отраженный сигнал представляет суперпозицию гармонических составляющих частота которых пропорциональна групповому запаздыванию отраженных волн амплитуда – амплитуде этих волн а фаза определяется фазовой задержкой излучения в световоде. Если расстояние между отражателями в всетоводе больше чем пространственное разрешение в методе когерентной частотной рефлектометрии то с помощью низкочастотного фильтра в сигнале можно выделить гармоническую составляющую соответствующую отражению от каждого из отражателей. Измерив разность фаз в гармонических составляющих сигнала соответствующих отражению от двух соседних отражателей мы определим фазовую задержку излучения при распространении его на участке световода между ними. Таким образом участки световода между отражателями можно рассматривать как чувствительные элементы ВОД подключенные к волоконно-оптической линии связи.
ОРГАНИЗАЦИОННЫЙ РАЗДЕЛ.
1. ОРГАНИЗАЦИЯ УЧАСТКА ЦЕХА ПО ПРОИЗВОДСТВУ ДЕТАЛЕЙ ВАЛА МАХОВИКА.
1.1. ОПРЕДЕЛЕНИЕ ПОТРЕБНОГО КОЛИЧЕСТВА ОБОРУДОВАНИЯ И ЕГО ЗАГРУЗКА.
Потребное количество станков определим по формуле
гдеТΣК – суммарное нормировочное время необходимое для обработки на станках данного типа годового количества деталей ч;
Fд – действительное (расчетное) годовое число часов работы одного станка при работе в одну смену;
m – число смен работы станка в сутки.
Суммарное нормировочное время для обработки одной детали на станках данного типа определим по формуле
гдеtк – штучно-калькуляционное время для обработки одной детали на станках данного типоразмера мин;
D – количество одноименных деталей обрабатываемых в год на станках данного типоразмера.
Определим действительный годовой фонд времени работы одного станка в часах по формуле
гдеFк – число календарных дней в году;
Fв – количество выходных и праздничных дней в расчетном году;
tсм – продолжительность смены ч;
FППД – количество предпраздничных дней в году;
s – число смен работы оборудования принимаем 1 смену;
Кр – коэффициент учитывающий время пребывания станка в ремонте; для крупных станков – Кр = 0.9;
Коэффициент загрузки для всех станков определяется по формуле:
гдеСР – расчетное количество станков;
СП – принятое количество станков.
Для всех станков участка принимаем коэффициент загрузки КЗ = 0.85 1.
Определим потребное количество станков по операциям:
Принимаем количество фрезерных станков СП = 5. Тогда необходимое количество одноименных деталей обрабатываемых в год равно
Принимаем СП = 10. Тогда
Принимаем СП = 5. Тогда
Определим общее количество деталей необходимых для загрузки станков на всех операциях в год.
Принимаем N=5000 штгод.
Определим коэффициент загрузки станков по каждой операции:
Необходимо разгрузить станок на 863 детали тогда
Догружаем станок на 863 детали тогда
На основании произведенных расчетов строим график загрузки оборудования на участке (рисунок 6.1).
Рисунок 6.1. График загрузки оборудования на участке.
Данные о количестве мощности электродвигателей и стоимости оборудования на участке заносим в таблицу 6.1.
Сводная ведомость оборудования.
Мощность электродвигателя
Горизонтально-расточной
1.2. ОПРЕДЕЛЕНИЕ ПОТРЕБНОГО КОЛИЧЕСТВА ОСНОВНЫХ РАБОЧИХ.
Количество рабочих – станочников определяется на основе суммарного штучно-калькуляционного времени на каждую операцию по формуле:
гдеFдр – эффективный годовой фонд рабочего времени станочника ч.
Эффективный годовой фонд времени при пятидневной рабочей неделе определяется по формуле:
гдеКн – коэффициент учитывающий использование номинального фонда времени из-за неявки на работу Кн = 0.89.
Определим число рабочих станочников на каждую операцию:
Фрезерно-центровальная
Принимаем Рст = 5 человек.
Принимаем Рст = 10 человек.
Результаты расчетов сведем в таблицу 6.2.
Сводная ведомость основных рабочих
Количество рабочих по разрядам
Определим число человеко-разрядов: .
Определим средний тарифно-квалификационный разряд:
1.3. ОПРЕДЕЛЕНИЕ ПОТРЕБНОГО КОЛИЧЕСТВА ВСПОМОГАТЕЛЬНЫХ РАБОЧИХ ИТР СКП МОП.
Определение потребного количества вспомогательных рабочих инженерно-технических работников (ИТР) счетно-конторского (СКП) и младшего обслуживающего персонала (МОП) ведут с учетом того что большая их часть выполняет общецеховые функции обслуживая несколько участков цеха. Поэтому количество работников задается определенной долей в процентах от числа основных рабочих участка.
Количество вспомогательных рабочих (наладчиков бригадиров кладовщиков раздатчиков инструмента браковщиков и др.) составляет 15 20%; человек.
Количество ИТР СКП и МОП принимается от общего числа рабочих в следующем соотношении:
ИТР – 10 12%; принимаем человека.
СКП – 1 3%; принимаем человек.
МОП – 2 – 3%; принимаем человек.
Результаты расчетов сведем в таблицу 6.3.
Сводная ведомость списочного состава работающих на участке.
к числу производственных
Отношение к общему числу рабочих %
Отношение к общему числу работающих
2. ОРГАНИЗАЦИЯ УЧАСТКА ЦЕХА ПО ПРОИЗВОДСТВУ ДЕТАЛЕЙ КОРПУСА ПНЕВМОЦИЛИНДРА.
2.1. ОПРЕДЕЛЕНИЕ ПОТРЕБНОГО КОЛИЧЕСТВА ОБОРУДОВАНИЯ И ЕГО ЗАГРУЗКА.
Принимаем количество фрезерных станков СП = 10. Тогда необходимое количество одноименных деталей обрабатываемых в год равно
Принимаем N=19000 штгод.
Необходимо разгрузить станок на 3088 деталей тогда
Необходимо догрузить станок на 13040 деталей тогда
Необходимо разгрузить станок на 9952 детали тогда
На основании произведенных расчетов строим график загрузки оборудования на участке (рисунок 6.2).
Рисунок 6.2. График загрузки оборудования на участке.
Данные о количестве мощности электродвигателей и стоимости оборудования на участке заносим в таблицу 6.4.
Широкоуниверсальный консольный фрезерный
Радиально-сверлильный
2.2. ОПРЕДЕЛЕНИЕ ПОТРЕБНОГО КОЛИЧЕСТВА ОСНОВНЫХ РАБОЧИХ.
Принимаем Рст = 18 человек.
Результаты расчетов сведем в таблицу 6.5.
2.3. ОПРЕДЕЛЕНИЕ ПОТРЕБНОГО КОЛИЧЕСТВА ВСПОМОГАТЕЛЬНЫХ РАБОЧИХ ИТР СКП МОП.
Количество вспомогательных рабочих (наладчиков бригадиров кладовщиков раздатчиков инструмента браковщиков и др.) составляет 15 20%; человек; принимаем – 7 человек.
ЭКОНОМИЧЕСКИЙ РАЗДЕЛ.
1. РАСЧЕТ ТЕХНИКО-ЭКОНОМИЧЕСКИХ ПОКАЗАТЕЛЕЙ УЧАСТКА ПРОИЗВОДСТВА ДЕТАЛИ ВАЛА МАХОВИКА.
1.1. ОПРЕДЕЛЕНИЕ ЗАТРАТ НА ОСНОВНЫЕ МАТЕРИАЛЫ.
Определение затрат на основные материалы производят по следующим исходным данным:
Марка материалаСталь 40Х
Вид исходной заготовкиПоковка
Масса заготовки кг290
Масса реализуемых отходов кг65
Стоимость материала и отходов принимается по заводским данным.
Стоимость материала на одну деталь определяется по формуле:
гдеmз – масса исходной заготовки кг;
mот – масса реализуемых отходов кг;
а – стоимость одного килограмма материала грн;
в – стоимость одного килограмма отходов грн.
К цене материала необходимо прибавить расходы связанные с доставкой материала на завод равные 10% цены:
Стоимость материала на весь годовой объем выпуска из N деталей равна
После расчета стоимости основных материалов на годовой объем выпуска заполняем таблицу 7.1.
Ведомость потребности и затрат основных материалов.
Годовой объем выпуска шт
Стоимость материалов с учетом транспортных расходов грн
Стоимость реализуемых отходов грн
Стоимость материалов за вычетом отходов грн
на годовой объем выпуска
1.2. ФОНД ОПЛАТЫ ТРУДА ПРОИЗВОДСТВЕННЫХ РАБОЧИХ.
Фонд заработной платы производственных рабочих складывается из основной и дополнительной заработной платы. Для расчета основной заработной платы вначале следует определить расценки на все операции технологического процесса обработки изделия.
Расценки определяем по формуле
гдеСсд – часовая тарифная ставка соответствующего разряда выполняемых работ грн;
tшт – норма времени на данную операцию мин.
Расценки на обработку заготовки вала маховика сводим в таблицу 7.2.
Сводная ведомость норм времени и расценок на обработку заготовки вала маховика.
Наименование операции
Заработную плату по сдельным расценкам на изготовление N деталей годового объема выпуска определим по формуле
Определим фонд премии
где γ = 40% - процент премии от фонда заработной платы.
Определим фонд доплаты
где γ = 4% - процент доплаты выплачиваемый рабочим в связи с отступлением от нормальных условий производства:
Фонд основной заработной платы производственных рабочих включает оплату по сдельным нормам и фонды доплат и премий:
Дополнительная заработная плата Здоп включает оплату отпуска выполнение государственных обязанностей учебных отпусков доплаты по прогрессивно-сдельной системе доплаты за работу в ночное время и принимается в определенной доле от основной сдельной заработной платы.
гдеКд = 17% - принятый процент дополнительной заработной платы.
Начисления в фонд социального страхования равны Сст = 52.5% от суммы основной и дополнительной заработной платы:
Общий фонд заработной платы основных рабочих равен
Среднемесячная заработная плата производственных рабочих
гдеРст – количество производственных рабочих.
1.3. РАСЧЕТ ФОНДА ОПЛАТЫ ТРУДА ВСПОМОГАТЕЛЬНЫХ РАБОЧИХ ИТР СКП МОП.
Фонд определяется на основе тарифных ставок должностных окладов и принятого количества работающих.
Обслуживание отдельного участка механического цеха производится общецеховым персоналом. В этом случае годовая заработная плата вспомогательных рабочих ИТР СКП и МОП определяется по формуле
гдеРв – расчетное количество персонала;
Ов – средняя месячная заработная плата данной категории работников.
Для вспомогательных рабочих
Для инженерно-технических работников
Для счетно-конторского персонала
Для младшего обслуживающего персонала
Премия из фонда заработной платы складывается из премии по положению которая рассчитывается в долях годового фонда заработной платы и составляет для вспомогательных рабочих – 12% для ИТР – 30% для СКП – 15% для МОП – 10%.
Общий месячный фонд заработной платы:
вспомогательных рабочих
Годовой фонд заработной платы вспомогательных рабочих ИТР СКП и МОП равен – 152340 грн.
1.4. КАЛЬКУЛЯЦИЯ ЕДИНИЦЫ ПРОДУКЦИИ.
Под калькуляцией понимают определение себестоимости единицы продукции. Расходы на себестоимость единицы продукции классифицируются по калькуляционным статьям затрат исходя из норм расходов. Под статьей понимают затраты которые отличаются между собой функциональным назначением местом их образования и соотнесены с единицей продукции.
Расчет калькуляционных статей сводится к определению затрат на приведенный годовой объем выпуска.
Затраты на силовую электроэнергию вычисляют по формуле
гдеЦЧ – стоимость 1 электроэнергии грн;
WЭ – годовой расход электроэнергии .
гдеNуст – установленная мощность всех станков на участке кВт;
Fд – эффективный годовой фонд производственного времени оборудования ч;
Кз – средний коэффициент загрузки оборудования;
о – коэффициент одновременной работы оборудования = 0.7 0.75;
Кс – коэффициент потерь в электрической сети;
д – кпд электродвигателей д = 0.85 0.9.
Затраты на сжатый воздух вычислим по формуле
гдеЦСЖ – стоимость 1 м3 сжатого воздуха грн;
QСЖ – годовой расход сжатого воздуха м3.
гдеСПН – количество станков с пневматическими зажимами;
СОБ – количество станков с применением обдувки;
q – расход сжатого воздуха на один станок с пневматическим зажимом;
q1 = 1м3 – расход сжатого воздуха на один станок с обдувкой.
Затраты на воду для производственных нужд вычислим по формуле
гдеЦВ – стоимость 1 м3 водопроводной воды;
QВ – годовой расход воды на один станок QВ = 25 м3;
s – число смен работы оборудования;
n – количество станков.
Амортизация оборудования транспортных средств и дорогостоящей оснастки принимается в долях стоимости основных фондов:
для производственных зданий норма составляет – 3.2%: грн;
для металлорежущих станков работающих неабразивным инструментом – 12.2%: грн;
для металлорежущих станков работающих абразивным инструментом – 12%: грн.
Затраты на текущий ремонт и обслуживание оборудования принимаются в размере 7% от их первоначальной стоимости: грн.
Затраты на износ малоценного инвентаря и инструмента составляют по заводским данным: грн.
Затраты на вспомогательные материалы могут быть определены ориентировочно по укрупненному нормативу в размере в год на один станок 5% от фонда основной заработной платы производственных рабочих: грн. Для всего участка: грн.
Затраты на основную и дополнительную заработную плату вспомогательных рабочих ИТР СКП и МОП с отчислением на социальное страхование отчисляются в размере 52.5%:
для вспомогательных рабочих грн;
Затраты на охрану труда и обеспечение техники безопасности составляют в год на одного рабочего 2% от фонда основной зарплаты производственных рабочих: грн; для всего участка грн.
Расходы на отопление и освещение производственных помещений воду для санитарно-технических и хозяйственных нужд канцелярские и другие расходы составляют 5 15% от суммы затрат по всем статьям: грн.
Рассчитанные статьи калькуляции сводятся в таблицу 7.3.
Калькуляция себестоимости единицы продукции по предприятию.
Материалы (за вычетом возвратных отходов)
Энергия для технологических целей
Основная и дополнительная заработная плата производственных рабочих
Начисления на заработную плату производственных рабочих:
Расходы по содержанию и эксплуатации оборудования
Итого: технологическая себестоимость
амортизация зданий сооружений
инвентаря цехового назначения
расходы по охране труда
возмещение износа малоценного инвентаря
Итого: цеховая себестоимость
Общепроизводственные расходы:
оплата труда общепроизводственного персонала
расходы на осуществление технологического контроля
расходы на отопление освещение и прочее содержание производственных помещений
Итого: производственная себестоимость
Внепроизводственные расходы
Итого: полная себестоимость единицы продукции по предприятию
Определим цену единицы продукции
Сi – полная себестоимость i-ой продукции.
Уровень рентабельности цеха – 30% поэтому
1.5. ТЕХНИКО-ЭКОНОМИЧЕСКИЕ ПОКАЗАТЕЛИ УЧАСТКА.
Комплекс итоговых данных характеризующих экономическую сторону работы спроектированного участка сведем в таблицу 7.4.
Комплекс технико-экономических показателей участка.
Годовой объем выпуска заданного изделия
Годовой объем выпуска с учетом догрузки
Общее количество работающих
Средний тарифный разряд основных рабочих
Выработка на одного работающего
Выработка на одного рабочего
Фонд заработной платы по участку
Среднегодовая заработная плата одного работающего
Среднегодовая заработная плата одного рабочего
Количество оборудования
Общая стоимость оборудования
Суммарная мощность оборудования
Средняя единичная мощность оборудования
Средняя загрузка оборудования
Производственная площадь участка
Производственная площадь на единицу оборудования
Себестоимость единицы изготовляемого изделия
1.6. АНАЛИЗ ПРИБЫЛЬНОСТИ ПРОИЗВОДСТВЕННОЙ ДЕЯТЕЛЬНОСТИ ПРЕДПРИЯТИЯ.
При рассмотрении влияния себестоимости на доходность предприятия все текущие затраты по отношению к объему реализованной продукции целесообразно разделить на постоянные и переменные. Это позволяет показать аналитически и графически зависимость между выручкой от реализации себестоимостью и прибылью определить необходимый минимум объема продукции обеспечивающий безубыточную деятельность при необходимости спрогнозировать зоны прибыльной и убыточной деятельности предприятия.
Главная задача при построении графика рентабельности заключается в определении точки безубыточности – точки в которой денежные доходы (полученная выручка) равны денежным расходам. Для этого надо знать условно постоянные затраты переменные затраты объем продажи отношение переменных затрат к объему продаж и к объему выпуска. График рентабельности показан на рисунке 7.1.
Экономическая оценка эффективности предлагаемого проекта оценена по системе показателей используемых в международной и отечественной практике.
При оценке экономической эффективности использованы показатели:
- чистая текущая стоимость (NPU);
- срок окупаемости капитаолвложений;
- коэффициент эффективности инвестиций.
В принятии решения о целесообразности внедрения проекта необходимо учитывать значение всех показателей потому что каждый показатель несет в себе свой объем информации и только все они в совокупности могут дать полное представление о реальной эффективности (таблица 7.5).
Расчет чистых денежных поступлений от производства детали вала маховика.
Капитальные вложения
Объем производства проектируемой детали
Полная себестоимость 1 детали
Полная себестоимость реализованной продукции
Амортизационные отчисления на весь объем
Прибыль от реализации 1 детали
Прибыль от реализации всего объема продукции
Ставку налога на прибыль
Чистая прибыль на весь объем
Чистые денежные поступления
Коэффициент дисконтирования
Дисконтированные денежные поступления
Чистая текущая стоимость доходов:
Показатель экономической эффективности (NPU) – чистая текущая стоимость доходов за годы реализации внедрения (5 лет) станков с ЧПУ составит 42477.27 тыс. грн. т. е. отвечает условиям эффективности так как NPU > 0.
Средний срок окупаемости капиталовложений составит менее 1 года.
Таким образом показатели эффективности свидетельствуют о том что данное внедрение при проектировании усовершенствованной технологии изготовления для детали "вал маховика" является экономически целесообразным.
2. РАСЧЕТ ТЕХНИКО-ЭКОНОМИЧЕСКИХ ПОКАЗАТЕЛЕЙ УЧАСТКА ПРОИЗВОДСТВА ДЕТАЛИ КОРПУСА ПНЕВМОЦИЛИНДРА.
2.1. ОПРЕДЕЛЕНИЕ ЗАТРАТ НА ОСНОВНЫЕ МАТЕРИАЛЫ.
Марка материалаСталь 35Л
Вид исходной заготовкиОтливка
Масса заготовки кг160
Масса реализуемых отходов кг25
Определим стоимость материала на одну деталь
К цене материала прибавим расходы связанные с доставкой материала на завод равные 10% цены:
После расчета стоимости основных материалов на годовой объем выпуска заполняем таблицу 7.6.
Ведомость потребности и затрат основных материалов
Корпус пневмоцилиндра
2.2. ФОНД ОПЛАТЫ ТРУДА ПРОИЗВОДСТВЕННЫХ РАБОЧИХ.
Определим расценки на все операции на обработку заготовки корпуса пневмоцилиндра и сведем в таблицу 7.7.
Сводная ведомость норм времени и расценок на обработку заготовки корпуса пневмоцилиндра.
Определим заработную плату по сдельным расценкам
Фонд основной заработной платы производственных рабочих:
Определим дополнительную заработную плату
Общий фонд заработной платы основных рабочих
2.3. РАСЧЕТ ФОНДА ОПЛАТЫ ТРУДА ВСПОМОГАТЕЛЬНЫХ РАБОЧИХ ИТР СКП МОП.
Годовая заработная плата вспомогательных рабочих ИТР СКП и МОП равна
Годовой фонд заработной платы вспомогательных рабочих ИТР СКП и МОП равен – 194256 грн.
2.4. КАЛЬКУЛЯЦИЯ ЕДИНИЦЫ ПРОДУКЦИИ.
Затраты на силовую электроэнергию
Затраты на сжатый воздух
Затраты на воду для производственных нужд
Затраты на вспомогательные материалы:грн. Для всего участка: грн.
Затраты на охрану труда и обеспечение техники безопасности: грн; для всего участка грн.
Прочие расходы: грн.
Рассчитанные статьи калькуляции сводятся в таблицу 7.8.
2.5. ТЕХНИКО-ЭКОНОМИЧЕСКИЕ ПОКАЗАТЕЛИ УЧАСТКА.
Комплекс итоговых данных характеризующих экономическую сторону работы спроектированного участка сведем в таблицу 7.9.
2.6. АНАЛИЗ ПРИБЫЛЬНОСТИ ПРОИЗВОДСТВЕННОЙ ДЕЯТЕЛЬНОСТИ ПРЕДПРИЯТИЯ.
График рентабельности показан на рисунке 7.2. Результаты расчета чистых денежных поступлений от производства детали корпуса пневмоцилиндра занесены в таблицу 7.10.
Расчет чистых денежных поступлений от производства детали корпуса пневмоцилиндра.
Показатель экономической эффективности (NPU) – чистая текущая стоимость доходов за годы реализации внедрения (5 лет) станков с ЧПУ составит 53656.5 тыс. грн. т. е. отвечает условиям эффективности так как NPU > 0.
Таким образом показатели эффективности свидетельствуют о том что данное внедрение при проектировании усовершенствованной технологии изготовления для детали "корпус пневмоцилиндра" является экономически целесообразным.
ПРОЕКТИРОВАНИЕ ЦЕХА.
Общие размеры и площадь цеха определяют на основе планировки оборудования и всех помещений цеха. Размеры зданий состоящих из нескольких пролетов определяют по размерам и числу пролетов.
Каждый пролет характеризуется основными размерами шагом колонн t и шириной пролета L или иначе сеткой колонн .
Ширина пролета здания L называется расстояние между осями подкрановых стоек или колонн. Ширина пролета здания находится в установленной размерной зависимости от пролета мостового крана. В механическом цеху применяют краны грузоподъемностью до 15 тонн. Ширину пролета мостового крана выбираем 23м тогда ширина пролета здания будет L = 24м расстояние от оси колонн до вертикальной оси кранового рельса равна l = 500мм. Шаг колонн выбираем равным t = 12м.
Наибольший не доход главного крюка для кранов грузоподъемностью до 15 тонн составляет l1 = 1300мм.
Длина пролета цеха определяется суммой размеров производственных и вспомогательных отделений последовательно расположенных вдоль пролета проходов и других участков цеха. Основным размером определяющим длину пролета является длина технологической линии станков расположенных вдоль пролета.
Длина пролета цеха определяемая графически на основе планировки оборудования и всех отделений и участков расположенных вдоль пролета складывается при типовой схеме компоновки.
Общая длина цеха должна быть кратной величине шага колонн который для всех цехов и размеров пролетов в настоящее время принимается равным 12 и 6м.
Высоту пролета цеха определяют исходя из размеров изготовляемых изделий габаритных размеров оборудования (по высоте) размеров и конструкции мостовых кранов а также санитарно-гигиенических требований.
Общая высота здания Н от пола до нижней выступающей части верхнего перекрытия или до нижней точки стропильной затяжки слагается из расстояния Н1 от пола до головки подкранового рельса и расстояния h от головки рельса до нижней выступающей части верхнего перекрытия которое для кранов грузоподъемностью до 10м принимаем h = 2200мм.
Величина Н1 складывается из следующих величин:
гдеk – высота наиболее высокого станка;
z – промежуток между транспортируемым изделием принимается равным 0.5 – 1.0м;
e – высота наибольшего по размеру изделия в положении транспотирования;
f – расстояние от верхней кромки наибольшего транспортируемого изделия до центра крюка крана в верхнем его положении необходимое для захвата изделия канатом принимается 1м;
c – расстояние от предельного верхнего положения крюка до горизонтальной линии проходящей через вершину головки рельса принимаем 1м.
Среднюю высоту здания принимаем равную сумме высоты Н – от пола до нижнего пояса фермы и а – от нижнего пояса фермы до горизонтальной линии проходящей через середину фонаря. Высота а принимается 15 ширины пролета здания а = 4800мм. Среднюю высоту пролета здания принимаем 17200мм.
Высоту помещений в цехе по санитарно-гигиеническим требованиям принимаем до 8.4м.
Железобетонные стропильные фермы для пролетов 24м изготовляют сборными (составными). Высота стропильных ферм равна 3.7м.
В здании предусмотренные прямоугольные фонари сооружения служащие для естественного освещения и аэрации воздуха внутри цеха.
Прямоугольные фонари имеют вертикальное остекленение которое меньше загрязняется и препятствует проникновению в цех прямых солнечных лучей.
Ширина фонарей для пролетов 24м принимаем 12м.
Расположение фонарей предусматривают не реже чем через 84м по длине пролета. Разрывы между фонарями должны быть не менее 6м.
В световых фонарях делается одинарное остекленение. Переплеты остекленения фонарей делаются в один ярус открывание фонарных створок производится снизу с уровня пола с помощью специальных механизмов. При открывании и закрывании длинных лент поясов остекленения пользуются электродвигателями.
Очистка от загрязнения внутренней поверхности остекленения фонарей производится со специальных тележек.
В цеху несущие функции выполняют каркас состоящий из железобетонных колонн и балок. Для обеспечения необходимой жесткости размеры колонн квадратного сечения () определяются по формуле
Принимаем а = 500мм.
Ширина ворот для прохода железнодорожных вагонов – 5м высота ворот – 5.6м. Ворота выполнены с автоматическим открыванием.
Для зациты рабочих мест от холодного воздуха при частом открывании ворот предусматривается утепление проемов при помощи воздушно-тепловых завес. Включение воздушно-тепловых завес блокируется с открытием ворот.
Также предусмотрены административно-бытовые помещения. Бытовые помещения располагаются вместе с административно-конторскими в одном специальном здании. Это здание пристроено к торцовой стороне здания цеха.
РАЗДЕЛ ОХРАНЫ ТРУДА И ОКРУЖАЮЩЕЙ СРЕДЫ.
1. АНАЛИЗ ОПАСНЫХ И ВРЕДНЫХ ФАКТОРОВ ПРОИЗВОДСТВЕННОГО ПРОЦЕССА.
При механической обработке материалов на металлорежущих станках возникает ряд физических химических и биологических опасных и вредных производственных факторов.
Движущиеся части производственного оборудования передвигающиеся изделия и заготовки стружка обрабатываемых материалов осколки инструментов высокая температура поверхности обрабатываемых деталей и инструмента повышенное напряжение в электроцепи или статического електричества при котором может произойти замыкание через тело человека – относятся к категории физических опасных факторов.
Физическими вредными производственными факторами характерными для процесса резания являются повышенная запыленность и загазованность воздуха рабочей зоны; высокий уровень шума и вибрации; недостаточная освещенность рабочей зоны; наличие прямой и отраженной блескости; повышенная пульсация светового потока.
Наличие опасных и вредных факторов возникающих при выполнении технологического процесса сведем в таблицу 9.1.
Опасные и вредные факторы технологического процесса.
Операция технологического процесса
Опасные и вредные факторы
Заготовительная: обрубка отливок зачистка заусенцев обработка поверхностей заготовки реактивами установка приспособлений
Шум вибрация электрическое напряжение травмирование осколками работа с реактивами запыленность загазованность слабое освещение.
Обработка деталей: механическая обработка резанием на металлорежущих станках.
Движущиеся и вращающиеся механизмы наличие стружки электрическое напряжение разлетающиеся осколки запыленность загазованность работа с воспламеняющимися жидкостями слабое освещение высокий нагрев поверхностей заготовок.
Контрольная операция: технический контроль выполняемых размеров.
Наличие заусенцев шероховатость острые кромки слабая освещенность электрическое напряжение.
Возникающие в рабочей зоне вредные производственные факторы могут превышать величины нормативов предусмотренных ГОСТом. Приведение значений физических величин возникающих в рабочей зоне и сравнение их с нормативными указанны в таблице 9.2.
Нормативные значения
Освещение рабочего места лк
На основе анализа вредных факторов (таблица 9.2) отклонением от нормативных значений являются запыленность и освещенность помещения цеха.
Шум вибрация электрическое напряжение ионизирующее и инфракрасное излучение находятся в пределах нормы.
2. ИНЖЕНЕРНО-ТЕХНИЧЕСКИЕ МЕРОПРИЯТИЯ ПО ОХРАНЕ ТРУДА.
Для устранения травматизма на рабочем месте выполняем следующие требования.
Для работающих обеспечиваются удобные рабочие места не стесняющие их действий во время выполнения работы. На рабочих местах предусмотрена площадь на которой размещаются стеллажи тара столы и другие устройства для размещения оснастки материалов заготовок готовых деталей и отходов производства.
На каждом рабочем месте около станка на полу находятся деревянные решетки на всю длину рабочей зоны а по ширине не менее 0.6м от выступающих частей станка.
Удобное расположение инструмента и приспособлений в тумбочках и на стеллажах заготовок в специальной таре применение планшетов для чертежей позволяет снизить утомление и производственный травматизм рабочего.
Установка обрабатываемых заготовок и снятие готовых деталей во время работы оборудования допускается вне зоны обработки при применении специальных позиционных приспособлений обеспечивающих безопасность труда работающих.
При обработке резанием заготовок выходящих за пределы оборудования установлены переносные ограждения и знаки безопасности по ГОСТ 12.4.026 – 76.
Для исключения соприкосновения рук станочников с движущимися приспособлениям и инструментом при установке заготовок и снятии деталей применяются автоматические устройства.
Контроль на станках размеров обрабатываемых заготовок и снятие деталей для контроля проводятся лишь при отключенных механизмах вращения или перемещения заготовок инструмента и приспособлений.
Стружку от металлорежущих станков и с рабочих мест убирают механизированными способами: скребковыми и пластинчатыми одновинтовыми конвейерами двухвинтовыми и пластинчатыми конвейерами.
При обработке резанием хрупких пылящихся материалов с вредными для здоровья наполнителями удаление стружки осуществляется непосредственно от режущих инструментов с помощью пневматических пылестружкоотсасывающих установок.
Для обеспечения чистоты воздуха и нормализации параметров микроклимата в производственных помещениях помимо местных отсасывающих устройств обеспечивающих удаление вредных веществ из зоны резания предусмотрена приточно-вытяжная общеобменная система вентиляции.
В соответствии с требованиями СНиП 2 – 33 – 75 ворота двери и технологические проемы оборудованы воздушными и воздушно-тепловыми завесами.
Естественное и искусственное освещение производственных помещений соответствует требованиям СНиП 2 – 4 – 79. В помещениях с недостаточным естественным светом и без естественного света применяются установки искусственного ультрафиолетового облучения в соответствии с СН 245 – 71.
Для местного освещения применяются светильники установленные на металлорежущих станках также используются светильники с непросвечиваемыми отражателями с защитным углом не менее . Кроме того предусмотрены меры по снижению отраженной блескости.
Зная геометрические размеры помещения цеха произведем расчет искусственного освещения помещения цеха.
Исходные данные для расчета.
Геометрические размеры помещения: длина А=97.5м; ширина В=49.8м; высота подвеса h=12м.
Характеристика помещения цеха: запыленность помещения – 100мгм3; разряд зрительной работы – 5в; контраст объекта с фоном – большой фон – темный; используется система комбинированного освещения.
Расчет искусственного освещения выполняется методом коэффициента использования светового потока.
Необходимый световой поток ламп в каждому светильнику определим по формуле
гдеЕ – нормированная минимальная освещенность Е = 150лк;
s – площадь освещения м2;
k – коэффициент запаса k = 1.5;
z – коэффициент минимальной освещенности z = 1.5;
N – количество светильников в помещении;
– коэффициент использования светового потока.
Определим общее количество светильников
гдеNр – количество рядов светильников зависящих от размеров помещения
гдеL – расстояние между рядами светильников
гдеλ – отношение расстояния между светильниками до расчетной высоты подвеса; типовая кривая – косинусная (Д) λ = 1.4.
Количество светильников в ряду
гдеl – расстояние между крайними светильниками и стеной: м.
Для определения коэффициента использования светового потока найдем индекс помещения
Значение i округляем до ближайших табличных значений: i = 3.0.
Характеристика отражающих поверхностей: от потолка – ρп = 50%; от стены – ρс = 30%; от пола – ρр = 10%.
По известному индексу и характеристики отражающих поверхностей определяем коэффициент использования светового потока – = 0.61.
Тогда световой поток равен
Исходя из полученного светового потока выбираем лампу типа ДРИ 250 со следующей технической характеристикой:
Мощность лампы Вт250
Световой поток после 100 часов горения лм18700
Отклонение фактической освещенности от заданной составит
При расчетах освещенности допустимая величина отклонений от нормированной составляет: от -10% до +20%.
3. ПОЖАРНАЯ ПРОФИЛАКТИКА.
Проектирование и эксплуатация всех промышленных предприятий регламентируется "Строительными нормами и правилами" (СНиП 2 – 90 – 81 СНиП 2 – 2 – 80) "Правилами устройства электроустановок" (ПУЭ – 76).
В соответствии со СНиП 2 – 2 – 80 все производства делят на следующие категории: А Б – взрывопожароопасные; В – пожароопасные; Г – к этой категории относятся производства в которых используются негорючие вещества и материалы в горячем раскаленном или расплавленном состоянии; Д – это производства в которых обрабатываются негорючие вещества и материалы в холодном состоянии; Е – взрывоопасные.
За степенью пожарной безопасности проектируемое производство относится к категории Д.
Помещения и установки в которых содержатся горючие жидкости (ГЖ) и горючие пыли нижний концентрационный предел которых выше 65 гм3 относятся к пожароопасным и классифицируют следующим образом.
Зона класса П – 1. К ней относят помещения в которых содержатся ГЖ.
Зона класса П – 2. В эту зону входят помещения в которых содержатся горючие пыли с нижним концентрационным пределом выше 65 гм3.
Зона класса П – 2а. К ней относят помещения в которых содержатся твердые горючие вещества не способные переходить во взвешенное состояние.
Зона класса П – 3. К этой зоне относят наружные установки в которых содержатся ГЖ (минеральные масла с температурой вспышки выше С) или твердые горючие вещества.
По пожароопасности помещение цеха можно отнести к классу П – 3.
Здание считается правильно спроектированным в том случае если наряду с решением функциональных прочностных санитарных и других технических и экономических требований обеспечены условия пожарной безопасности.
Повысить огнестойкость зданий и сооружений можно облицовкой или оштукатуриванием металлических конструкций. Для защиты деревянных конструкций из имеющихся видов штукатурки предпочтение отдается известково-цементной толщиной 20мм асбестоцементной или гипсовой.
Искры от промышленных печей и установок с открытым огнем часто являются причинами возникновения пожаров поэтому котельные и установки с открытым огнем располагают с подветренной стороны по отношению к открытым складам ЛВЖ сжиженных газов и т. п.
Для предупреждения распространения пожара с одного здания на другое между ними устраивают противопожарные разрывы. При определении противопожарных разрывов исходят из того что наибольшую пожарную опасность в отношении возможного воспламенения соседних зданий и сооружений представляет тепловое излучение от очага пожара.
К противопожарным преградам относят стены перегородки перекрытия двери ворота люки тамбур-шлюзы и окна. Противопожарные стены должны быть выполнены из несгораемых материалов иметь предел огнестойкости не менее 2.5 ч и опираться на фундаменты. Противопожарные стены рассчитывают на устойчивость с учетом возможности одностороннего обрушения перекрытий и других конструкций при пожаре. Противопожарные двери окна и ворота в противопожарных стенах должны иметь предел огнестойкости не менее 1.2 ч а противопожарные перекрытия – не менее 1 ч. Такие перекрытия не должны иметь проемов и отверстий через которые могут проникать продукты горения при пожаре.
В соответствии с СНиП 2 – 2 – 80 число эвакуационных выходов из зданий помещений должно составлять не менее двух. Эвакуационные выходы должны располагаться рассредоточено. Ширина участков путей эвакуации должна быть не менее 1 м а дверей на путях эвакуации – не менее 0.8 м. Ширина наружных дверей лестничных клеток должна быть не менее ширины марша лестницы высота прохода на путях эвакуации – не менее 2 м.
Удаление газов и дыма из горящих помещений производится через оконные проемы аэрационные фонари а также с помощью специальных дымовых люков легкосбрасываемх конструкций.
Дымовые люки устанавливают в подвальных помещениях в перекрытиях складских и бесфонарных производственных зданий. Площадь сечения дымовых люков определяют расчетом.
Легкосбрасываемые конструкции используют для удаления продуктов горения при взрыве с целью снижения давления до величин безопасных для прочности и устойчивости строительных конструкций. Легкосбрасываемые конструкции представляют собой элементы наружных стен и покрытий. Они вскрываются при повышении давления внутри зданий и обеспечивают стравливание продуктов горения при взрыве. Различают крышевые и стеновые легкосбрасываемые панели (клапаны). Площадь сечения легкосбрасываемых конструкций определяют расчетом в соответствии с нормами СН 502 – 77.
После изложения разделов дипломного проекта сделаем выводы о проделанной работе в следующем:
- в аналитическом разделе произведен анализ чертежей конструкций деталей вала маховика и корпуса пневмоцилиндра с целью определения качественной оценки технологичности конструкций и определения коэффициента унификации деталей представляющего собой количественную оценку технологичности конструкций деталей;
- в технологическом разделе определяется тип производства и форма организации технологического процесса производства деталей вала маховика и корпуса пневмоцилиндра выбирается и экономически обосновывается способ получения заготовок разрабатывается маршрут обработки деталей определяются режимы резания и штучно-калькуляционное время по каждой операции. В отличии от базового технологического процесса применили среднесерийный тип и групповую форму организации производства. Суточная производительность поточной линии производства вала маховика – 33 шт; корпуса пневмоцилиндра – 80Такт выпуска детали вала маховика – 152.25 мин.; корпуса пневмоцилиндра – 121.8 мин. Значительно сократили себестоимость производства заготовок за счет менее дешевого способа получения. В разработанном маршруте обработки деталей достигли более высокой точности и снижения основного технологического времени за счет рациональной последовательности обработки деталей вала маховика и корпуса пневмоцилиндра;
- в конструкторском разделе спроектировано специальное станочное приспособление которое обеспечивает минимальное вспомогательное время на установку закрепление и снятие детали после обработки; необходимую точность и жесткость при закреплении заготовки; безопасные условия обработки на станке.
- в специальном разделе описываются тепловые процессы возникающие во время контакта режущей кромки резца с поверхностью заготовки в процессе обработки на токарном станке. На основе уравнений теплопроводности показана закономерность изменения температурного поля под влиянием различных факторов: изменения геометрических параметров резца материала заготовки и режущей части инструмента изменения режимов резания и др. Также раскрывается влияние различных факторов на температуру резания;
- в разделе автоматизации раскрываются принципы контроля размеров обработанных поверхностей заготовки с помощью линейных интерференционных сигналов (ЛИС). Рассматривается работа интерферометра со счетом полос на основе частотной модуляции;
- в организационном разделе выполняется организация двух участков по производству деталей вала маховика и корпуса пневмоцилиндра. На выполнение годовой программы N = 5000 штгод выпуска изделия вала маховика предусмотрено общее количество – 25 станков на участке общей стоимостью 3130000 грн. Станки загружены на 87%. Общая численность основных рабочих на участке – 25 человек. Всего списочная численность на участке – 36 человек. На участке производства детали корпуса пневмоцилиндра для выполнения годовой программы N = 19000 штгод предусмотрено 30 станков общей стоимостью – 1348000 грн. Станки загружены на 85%. Общая численность основных рабочих на участке – 33 человека. Всего списочная численность на участке – 47 человек;
- в экономическом разделе выполняется расчет технико-экономических показателей участков выполняется расчет денежных поступлений от реализации изделий. На графике рентабельности показаны зоны прибыльной и убыточной деятельности предприятия. Определяется срок окупаемости капиталовложений необходимых для производства изделий. Для участка производства деталей вала маховика:
Годовые затраты на материал грн39105000
Среднемесячная заработная плата основных рабочих грн1556.63
Годовой фонд заработной платы по участку грн619328.55
Цена единицы изделия грн10713.76
Срок окупаемости капиталовложений год0.34
Для участка производства деталей корпуса пневмоцилиндра:
Годовые затраты на материал грн49495000
Среднемесячная заработная плата основных рабочих грн1608
Годовой фонд заработной платы по участку грн831025.1
Цена единицы изделия грн3518.45
Срок окупаемости капиталовложений год0.12
- спроектированный механический цех отвечает всем санитарно-гигиеническим требованиям и требованиям СНиП 2 – 33 – 75 и СНиП 2 – 4 – 79;
- в разделе охраны труда и окружающей среды выполнен анализ опасных и вредных факторов возникающих при выполнении производственного процесса. Для снижения вероятности несчастных случаев на производстве указанны необходимые мероприятия которые должны выполняться на производстве. Произведен расчет искусственного освещения и выбор необходимого типа и количества ламп для освещения помещения цеха. Выбраны лампы типа ДРИ 250 мощностью 250 кВт. Количество светильников – 108Также указаны требования по повышению пожаробезопасности и огнестойкости здания цеха.
Методичні вказівки до кваліфікаційної роботи спеціаліста дипломного проекту. Кафедра ТГМ. Дн-ськ – 2000 р.
Дипломное проектирование по технологии машиностроения. Под общ. ред. В. В. Бабука – Мн.: Высш. школа 1979. – 464с.
Справочник инструментальщика. Под общ. ред. И. А. Ординарцева. – Л.: Машиностроение. Ленинград. отд-ние 1987. – 846 с.
Справочник технолога машиностроителя. В 2-х т. Т. 1. Под общ. ред. А. Г. Косиловой и Р. К. Мещерякова – М.: Машиностроение 1985 – 656с.
Прогрессивные режущие инструменты и режимы резания металлов. Под общ. ред. В. И. Баранчикова. – М.: Машиностроение 1990. – 400с.
Справочник конструктора машиностроителя: В 3-х т. Т3. – 8-е изд. перераб. и доп. Под ред. И. Н. Жесковой. – М.: Машиностроение 2001. – 864с.
Нефедов Н. А. Осипов К. А. Сборник задач и примеров по резанию металлов и режущему инструменту: - 5-е изд. перераб. и доп. – М.: Машиностроение 1990. – 448с.
Горбацевич А. Ф. Шкред В. А. Курсовое проектирование по технологии машиностроения. – Минск: Высшая школа 1983.
Нефедов Н. А. Дипломное проектирование в машиностроительных техникумах. – М.: Высшая школа 1986.
Материалы в машиностроении Т.1 5.Под ред. проф. Кудрявцева Н. В. М. Машиностроение 1967.
Справочник технолога машиностроителя. В 2-х т. Т. 2. Под общ. ред. А. Г. Косиловой и Р. К. Мещерякова – М.: Машиностроение 1985.
Справочник металлиста. Под ред. Богуславского В. А. Т. 5. – М.: Машиностроение 1986.
Общемашиностроительные нормативы режимов резания и времени для технического нормирования работ на металлорежущих станках. – М.: 1991.
Якушев А. М. Справочник контролера машиностроительных заводов. – М.: Машгиз 1970.
Металлорежущие станки с ЧПУ. Каталог. – М.: НИ Имаш 1988.
Руденко П. А. Проектирование технологических процессов в машиностроении. – Киев: Высшая школа 1985.
Обработка металлов резанием. Справочник технолога. Под ред. Панова А. Л. – М.: Машиностроение 1988.
Брюханов А. Н. Ковка и объемная штамповка. – М.: Машиностроение 1975.
Охрименко Я. М. Технология кузнечно-штамповочного производства. – изд. 2-е: Учебник для студентов – М. Машиностроение 1976.
Головин С. Я. Прогрессивные виды литья. – М.: Знание 1964.
Косилова Л. Г. и др. Точность обработки заготовки и припуски в машиностроении: Справочник. – М.: Машиностроение 1976.
ГОСТ 7504 – 74. Допуски и припуски на заготовки получаемые горячей штамповкой на молотах прессах и ГКМ.
ГОСТ 26645 – 85. Отливки из металлов и сплавов. Допуски размеров массы и припуски на механическую обработку.
ГОСТ 21495 – 76. Базирование и базы в машиностроении.
Маталин А. А. Точность механической обработки и проектирования технологических процессов. – Л.: Машиностроение 1970.
Ансеров Н. А. Приспособления для металлорежущих станков. – М.: Машиностроение 1975.
Горошкин Л. К. Приспособления для металлорежущих станков. Справочник. – М.: Машиностроение 1979.
Болотин Х. Л. Костром Ф. П. Станочные приспособления - М.: Машиностроение 1979.
Корсаков В. С. Основы конструирования приспособлений: 2-е изд. перераб. и доп. – М.: Машиностроение 1983.
Белоусов А. П. Проектирование станочных приспособлений: 3-е изд. перераб. и доп. – М.: Высш. школа 1980.
Пуш В. Э. Пичерт Р. Х. Сосонкин В. Д. Автоматические станочные системы. – М.: Машиностроение 1982.
Евстигнеев М. И. Автоматизация технологических процессов в авиадвигателестроении.
Корсаков В. С. Автоматизация производственных процессов. – М.: Высш. школа 1978.
Автоматические приборы для контроля размеров деталей в машиностроении – Каталог. 4.1. – Омск 1969. – 160с.
Егоров М. Е. Основы проектирования машиностроительных заводов: 6-е изд. Учебник для машиностроительных вузов. – М.: Высш. школа 1979.
Санитарные нормы проектирования промышленных предприятий. Сп-243.
Строительные нормы и правила. СН и П-П-П-77. – М.: Стройиздат. 1978.
Безопасность производственных процессов: Справочник. Белов С. В. и др. – М.: Машиностроение 1985.
Охрана труда в машиностроении Под ред. Е. Я. Юдина С. В. Белова – 2-е изд. перераб. и доп. – М.: Машиностроение 1983.
Тиллес С. А. экономика технологических процессов механической обработки. – М.: Машгиз 1964.
Климов А. Н. Оленев И. Д. Соколицын С. А. Организация и планирование производства на машиностроительном заводе. Учебник для машиностроительных вузов. Изд. 3-е перераб. и доп. – Д.: Машиностроение 1979.
Бойко В. В. Економіка підприємств України: Навчальний посібник. – 2-е вид. переробл. і доп. – Дніпропетровськ: Національна гірнича академія України 2002. – 535с.
Схемы наладок обработки вала маховика. ЛИСТ 5, 6..dwg

D=250мм; d=50мм; z=26
Операция 020. Фрезерно-центровальная.
Оборудование: Продольно-фрезерный станок 6620
Фреза торцовая насад-
Операция 025. Токарная.
Оборудование. Токарно-винторезный станок 16К40П
Планшайба поводковая
Резец токарный проход-
Резец канавочный Т15К6
Сверло с эжекторным
отводом стружки Т15К6
Сверло центровочное Р9
Круг шлифовальный:тип
Резец токарный резьбо-
вой для наружной резьбы
Таблица режимов резания и норм времени
Сверло с эжекторным отводом стружки
Операция 035. Фрезерная.
Оборудование: Продольно-фрезерный двухстоечный станок 6620.
Приспособление: Головка делительная
горизонтальная с задней бабкой.
Операция 040. Сверлильная.
Оборудование: Горизонтально-расточной
обработки вала махо-
Операция 050. Шлифовальная.
Оборудование: Круглошлифовальный
Рекомендуемые чертежи
- 24.01.2023
- 25.01.2023
- 07.09.2016