Разработка системы адаптивного управления на базе токарного станка с ЧПУ 16К20Ф3




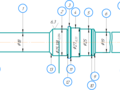
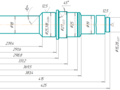
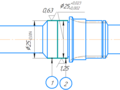
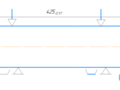
- Добавлен: 24.01.2023
- Размер: 2 MB
- Закачек: 1
Описание
Состав проекта
![]() |
![]() ![]() |
![]() ![]() ![]() |
![]() ![]() |
![]() ![]() ![]() |
![]() ![]() ![]() |
![]() ![]() |
![]() ![]() |
![]() ![]() |
![]() ![]() |
![]() ![]() |
![]() ![]() ![]() |
![]() ![]() |
![]() ![]() |
![]() ![]() ![]() |
![]() ![]() ![]() |
![]() ![]() |
![]() ![]() ![]() |
![]() ![]() ![]() |
![]() ![]() ![]() |
![]() |
![]() ![]() ![]() |
![]() |
![]() ![]() ![]() |
![]() ![]() ![]() |
![]() ![]() |
Дополнительная информация
ФРАГМЕНТ ОПЕР 005.FRW

ФРАГМЕНТ ОПЕР 020.FRW

ФРАГМЕНТ ОПЕР 010.FRW

ФРАГМЕНТ ОПЕР 015.FRW

ФРАГМЕНТ ОПЕР 045.FRW

КЭ вала.cdw

КЭ1 005.cdw

ФРАГМЕНТ ОПЕР 040.FRW

Рекомендуемые чертежи
- 29.05.2022
- 12.05.2020
Свободное скачивание на сегодня
Другие проекты
- 29.08.2014