Расчёт и конструирование станка на базе 2М55




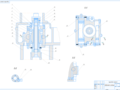
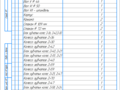
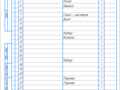
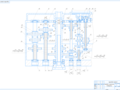
- Добавлен: 25.01.2023
- Размер: 2 MB
- Закачек: 2
Описание
Расчёт и конструирование станка на базе 2М55
Состав проекта
![]() |
![]() |
![]() |
![]() |
![]() ![]() ![]() ![]() |
![]() ![]() ![]() ![]() |
![]() |
![]() ![]() ![]() ![]() |
![]() ![]() ![]() ![]() |
![]() |
![]() ![]() ![]() ![]() |
![]() |
![]() ![]() ![]() |
![]() |
![]() |
![]() |
![]() ![]() ![]() |
Дополнительная информация
Коробка скоростей.spw

Колесо зубчатое Z=36
Колесо зубчатое Z=30
Колесо зубчатое Z=42
Блок зубчатых колес Z=40
Блок зубчатых колес Z=55
Колесо зубчатое Z=40
Колесо зeбчатое Z=59
Колесо зубчатое Z=59
Блок зубчатых колес Z=25
Колесо зубчатое Z=70
Колесо зубчатое Z=47
Блок зубчатых колес Z=58
Колесо зубчатое Z=55
Колесо зубчатое Z=58
Колесо зубчатое Z=96
Колесо зубчатое Z=20
Колесо забчатое Z=27
Шпонка 7x7x24 ГОСТ23360-78
Шпонка 10х8х27 ГОСТ23360-78
Шпонка 14х9х30 ГОСТ23360-78
Шпонка 16х10х40 ГОСТ23360-78
Шпонка 22х14х50 ГОСТ23360-78
Шпонка 6х6х23 ГОСТ 23360-78
Кольцо упорное А26 ГОСТ 13943-86
Кольцо упорное А32 ГОСТ 13943-86
Кольцо упорное А46 ГОСТ13943-86
Кольуо упорное А50 ГОСТ 13943-86
Кольцо упорное А85 ГОСТ 13943-86
Подшипник 304 ГОСТ 8338-75
Подшипник 50304 ГОСТ 2893-82
Подшипник 205 ГОСТ 8338-75
Подшипник 50205 ГОСТ 2893-82
Подшипник 217 ГОСТ 8338-75
Кольцо уплотнительное
Коробка скоростей.cdw

Узел.cdw

узел.spw

Кинематическая схема.cdw

Компоновка станка.frw

Записка.docx
2Технические характеристики станка5
3Описание основных узлов станка.6
Расчет режимов резания8
Кинематический расчет14
1. Определение диапазона регулирования и выбор знаменателя.14
2. Выбор оптимального варианта множительной структуры.15
3. Построение графика частот вращения шпинделя.19
4. Определение числа зубьев зубчатых колес.20
5. Построение кинематической схемы коробки скоростей и выбор электродвигателя.21
6. Расчет фактических значений частот вращения шпинделя.25
8. Расчет зубчатых колес28
Силовые расчёты основных механизмов.35
1. Предварительный расчет валов.35
2. Расчет валов на прочность.36
3. Расчет валов на жесткость.49
4. Выбор подшипников.57
Список использованной литературы60
Сверлильные станки предназначены для обработки и получения глухих либо сквозных отверстий в пластмассе металле дереве и другом материале. На таких станках производятся такие технологические операции как: развертывание зенкерование сверление нарезание резьбы и рассверливание. Потому сверлильные станки имеют довольно широкий спектр применения. На сегодня они применяются в сборочных инструментальных и ремонтных цехах небольших и крупных примышленных предприятий либо мелких ремонтных мастерских.
Требуется упомянуть что в зависимости от области применения сверлильные станки делятся на специализированные вертикально-сверлильные центровальные радиально-сверлильные и др. При этом независимо от типа всякий радиально-сверлильный станок характеризуется такими параметрами как конус шпинделя наибольший диаметр обработки наибольший ход шпинделя мощность двигателя и диапазон скорости вращения шпинделя.
Сейчас в металлообрабатывающей промышленности наибольшей популярностью пользуются радиально-сверлильные и вертикально-сверлильные станки. В вертикально-сверлильных станках совмещение осей отверстия и инструмента осуществляется только при помощи перемещения детали. Следовательно эти станки широко применяются в индивидуальном и мелкосерийном производстве для обработки небольших отверстий На радиально-сверлильных станках при помощи возможности перемещения шпинделя станка относительно заготовки возможно совмещение осей инструмента и отверстий при закрепленной детали. Потому такие станки используются в основном для обработки и сверления отверстий в деталях крупных размеров.
1Описание разрабатываемого станка
1 Назначение и область применения спроектированного станка
Спроектированный радиально-сверлильный станок с ЧПУ предназначен для широкого применения в промышленности.
Благодаря своей универсальности станок находит применение везде где требуется обработка отверстий – от ремонтного цеха до крупносерийного производства в частности – для обработки отверстий в ступицах грузовых автомобилей.
На станке можно производить сверление в сплошном материале рассверливание зенкерование развертывание подрезку торцов нарезку резьбы метчиками и другие подобные операции.
Применение приспособлений и специального инструмента значительно повышает производительность станков и расширяет круг возможных операций позволяя производить на них выточку внутренних канавок вырезку круглых пластин из листа и т. д. При соответствующей оснастке на станке можно выполнять многие операции характерные для расточных станков.
Общая компоновка спроектированного станка
Компоновка станка представлена на рисунке 1.
Основанием станка является фундаментная плита 1 на которой неподвижно закреплен цоколь. В цоколе на подшипниках монтируется вращающаяся колонна 8 выполненная из стальной трубы. Рукав 4 станка со шпиндельной бабкой 6 размещен на колонне и перемещается по ней с помощью механизма подъема 5 смонтированного в корпусе на верхнем торце колонны. В этом же корпусе расположено гидромеханическое устройство для зажима колонны и токопроводящее устройство для питания поворотных и подвижных частей станка. Механизм подъема связан с рукавом ходовым винтом 3.
Шпиндельная бабка 6 выполнена в виде отдельного силового агрегата. Она заключает в себе шпиндель 7 который перемещается в бабке вертикально при помощи реечной передачи. Сама бабка перемещается по направляющим рукава при помощи шариковинтовой пары работающий от асинхронного двигателя.
Рисунок 1. – Компоновка спроектированного станка
В фундаментной плите 1 выполнен бак и насосная установка для подачи охлаждающей жидкости к инструменту; На плите устанавливается стол 2 для обработки на нем деталей небольшого размера. Для обработки крупногабаритных деталей стол убирается.
Все органы управления станком сосредоточены на специальном пульте. На панели цоколя размещены только кнопки вводного выключателя подключающего станок к внешней электросети и выключатели управления насосом охлаждения.
2Технические характеристики станка
Основные параметры и нормы согласно ГОСТ 1222 - 71
класс точности станка по ГОСТ 8-71
Наибольший условный диаметр сверления мм: 50
Вылет шпинделя от образующей колонны мм:
Расстояние от торца шпинделя до плиты мм
Количество ступеней скоростей шпинделя: 16
Пределы скоростей шпинделя обмин: 16-2731
Количество ступеней механических подач шпинделя: 12
Пределы подач шпинделя ммоб: 0056-25
Наибольшая эффективная мощность на шпинделе кВТ: 45
Наибольший крутящий момент на шпинделе кН см: 71
Наибольшее усилие подачи кН: 20
Габаритные размеры станка мм:
Масса станка кг: 4700
Диаметр колонны мм: 315
Зажим колонны: гидравлический
Наибольший ход рукава по колонне мм 750
Скорость вертикального перемещения ммин: 14
Наибольший угол поворота вокруг оси колонны градусов: 360
Зажим в колонне: электромеханический автоматического действия
Наибольший ход по направляющим рукава м: 1225
Зажим на направляющих рукава: гидравлический
точность позиционирования 01
Размер конуса шпинделя по ГОСТ 2847-68: Морзе №5
Ширина фундаментной плиты мм: 1000
Ширина паза по ГОСТ 1574-75 мм: 28
Расстояние между пазами мм: 160
Количество пазов шт: 4
3Описание основных узлов станка.
) Зажим рукава на колонне и механизм его подъёма;
Начнем описание работы зажима рукава и механизма его подъёма:
Рукав охватывает колонну и перемещается по ней в вертикальном направлении. По направляющим рукава в радиальном направлении перемещается сверлильная головка. Специальная шпонка входящая в паз колонны препятствует повороту рукава вокруг колонны. Во всех случаях когда рукав не перемещается на колонне он зажат на ней что разгружает шпонку от усилий возникающих при сверлении и обеспечивает полную безопасность работы на станке работающего.
Перемещение рукава по колонне производится при помощи механизма подъёма. Механизм зажима рукава сблокирован с механизмом подъёма таким образом что освобождение рукава его перемещение и зажим осуществляются автоматически и в одном цикле от одной команды.
Основными элементами механизма подъёма является ШВП. Грузовая гайка имеет отъёмный фланец который на двух упорных подшипниках заперт во втулке с помощью гайки. Наличие отъёмного фланца с которым гайка связана торцевыми зубьями позволяет частично компенсировать ошибки связанные с перекосами винта относительно оси втулки.
В начале вращения винта грузовая гайка ничем не удерживается от проворота и начинает вращаться вместе с винтом. Вспомогательная гайка в это время передвигается по винту так как закрепленная на ней шпонка входит в паз неподвижной втулки чем удерживает гайку от вращения.
Перемещаясь по винту гайка поворачивает рычаг вал и кулак который освобождает ролик в результате чего разгружаются болты. Расточенная часть рукава прорезанная по всей длине вследствие своей упругости разжимается до упора в головки болтов и гайки. При этом рукав растормаживается относительно колонны.
В момент когда рукав полностью от зажимашпонка своим выступом (верхним или нижним – в зависимости от направления вращения винта т.е. от направления перемещения рукава) подходит к выступу грузовой гайки и останавливает её вращение. Так как гайка застопорена а винт вращается начинается перемещение рукава.
После окончания перемещения винт не останавливается а автоматически реверсируется. При этом перемещение рукава немедленно прекращается так как выступы шпонки гайки отходят друг от друга вследствие чего грузовая гайка начинает вращаться вместе с винтом. Вспомогательная гайка при этом перемещается по винту в обратном направлении поворачивая вал и кулак. Под давлением выступа кулака на ролик рычаги поворачиваются вокруг осей и затягивают болты. Рукав с большой силой стягивается между головами болтов и гайками на болтах осуществляя жесткий зажим рукава на колонне.
Гайки на болтах отрегулированы так чтобы обеспечить необходимую жёсткость зажима. В этом положении они заштифтованы. Величина зазора между рукавом и колонной определяемая затяжкой гаек должна иметь определенную величину для того чтобы перемещение проходило плавно без рывков и не вызывало перегрузку привода механизма подъема.
Управление циклом обеспечивается четырьмя конечными выключателями на которые воздействуют кулачки насаженные на вал зажима.
В крайних положениях рукава на колонне (либо верхнем либо нижнем) штанги воздействуют наконечные выключатели которые разрывают цепь питания электродвигателя редуктора.
Износ резьбы грузовой гайкине приводит к падению рукава так как при аварийном опускании рукава на несколько миллиметров кулак поворачивается и своим дополнительным выступом автоматически зажимает рукав на колонне.
Смазка механизма подъема производится с помощью пресс – масленки установленный в гайке. Ось ролика смазывается отдельной пресс – масленкой. Смазка колонныосуществляется с помощью плунжерного насоса который подает масло в кольцевую трубку расположенную под уплотнением в верхней части бочки рукава. Насос подает порцию масла в трубку при повороте кулака который регулированным винтомнажимает на плунжер насоса. Несколько выше располагается пластмассовый резервуар для масла.
) Шпиндельная бабка ее устройство
Шпиндельная бабка размещена на направляющих рукава по которым легко перемещается в радиальном направлении. Легкое перемещение сверлильной головки обеспечивается применением комбинированных направляющих качения – скольжения. Трение между боковыми направляющими не затрудняет перемещения так как центр тяжести головки располагается примерно в плоскости этих направляющих.
Данная конструкция обеспечивает подвод инструмента к обрабатываемой поверхности и осуществляет процессы резания. Эти направляющие обеспечивают высокую точность перемещения. Шпиндельная бабка размещается на горизонтальных направляющих траверсы по которым легко перемещается в радиальном направлении при помощи ШВП.
Шпиндель перемещается в вертикальном направлении за счёт перемещения рейки. Она связана с электродвигателем шагового типа через предохранительную муфту.
Расчет режимов резания
Скорость резания при сверлении определяется по следующей формуле:
где - коэффициент [2 стр. 278 таблица 28]
- диаметр сверления мм
- коэффициент учитывающий влияние различных факторов
- среднее значение стойкости инструмента мин
- показатели степени.
Скорость резания при зенкеровании рассверливании и развертывании определяется по следующей формуле:
где - коэффициент [2 стр. 279 таблица 29]
- глубина резания мм
Сверлить отверстие ø20мми l=60мм.
Материал заготовки – сталь 45 НВ=220.
Материал сверла – Р6М5 заточка – двойная с подточкой поперечной кромки
Зенкеровать отверстие выдерживая размеры ø20мми l=60мм.
Материал заготовки – СЧ20 НВ=190.
Материал зенкера – ВК8 зенкер с пластинами из твердого сплава.
Рассверливание отверстия
Рассверлить отверстие выдерживая размеры ø30мм.
Материал заготовки – Сталь 45 НВ=220.
Сверлить отверстие диаметром ø10мм и l=40мм напроход.
Материал заготовки – 12Х18Н9Т НВ=141.
Развернуть отверстие ø25мм и l=55vv
Материал развертки – Р6М5 машинная цельная развертка.
Материал заготовки – КЧ30 НВ 150.
Кинематический расчет
1. Определение диапазона регулирования и выбор знаменателя.
Определяем наибольшие и наименьшие частоты вращения шпинделя по формулам [2]:
где и - предельные скорости резания ммин.;
и - предельные диаметры обрабатываемых отверстий мм.
По паспорту станка-прототипа 2M55 определяем:
Определяем диапазон регулирования частот вращения.
Учитывая совершенствование режущего инструмента за время эксплуатации станка увеличиваем диапазон на 15-20%.
Определяем знаменатель ряда геометрической прогрессии :
в соответствии с заданием на КП ;
Принимаем для данного станка .
2. Выбор оптимального варианта множительной структуры.
При выборе оптимального варианта структурной сетки следует руководствоваться следующим критерием: уменьшение габаритов коробки скоростей при сохранении наиболее благоприятных кинематических и динамических характеристик.
Перед построением структурных сеток определяемся со структурными формулами. Распределение частот вращения по валам осуществляется разбиением заданного количества частот (скоростей; z=16) на множители 2 3 и тд.
Рисунок 2.1 – Варианты структурных формул и сеток.
Анализируя полученные варианты структурных сеток исходя из условия обеспечения минимальных габаритов веса коробки скоростей числа валов и зубчатых колес следует:
Самым оптимальным из представленных вариантов следует считать вариант I. Во-первых данная структурная сетка имеет веерообразный характер. Во-вторых структурная формула имеет возрастание характеристик переборных групп передач по мере приближения к шпинделю что означает уменьшение передаточных отношений а так как величина передаваемых ведомым валом крутящих моментов обратно пропорциональна величине передаточных отношений то первые валы работают при больших скоростях и меньших нагрузках – это определяет малые диаметры валов и модули зубчатых колес. В-третьих высокие скорости вращения шпинделя будут обеспечиваться короткими кинематическими цепями.
Для обеспечения оптимальных условий работы принимаются предельные ограничения на передаточные отношения:
3. Построение графика частот вращения шпинделя.
Рисунок 2.2 – График частот вращения шпинделя.
4. Определение числа зубьев зубчатых колес.
Получив передаточные отношения в передачах переборных групп и используя таблицы для подбора числа зубьев в зависимости от передаточных отношений определяем для каждой переборной группы.
Первая переборная группа (валы II-III)
Вторая переборная группа (валы III-IV)
Третья переборная группа (валы IV-V;IV-VII)
Четвертая переборная группа (валы V-VI)
Пятая переборная группа (валы VI-VII)
5. Построение кинематической схемы коробки скоростей и выбор электродвигателя.
После расчета чисел зубьев зубчатых колес всех переборных групп строим кинематическую схему коробки скоростей с модулем зубчатых колес .
Рисунок 2.3 – Кинематическая схема коробки скоростей.
Выбор электродвигателя
Мощность электродвигателя определяют на черновых режимах обработке по формуле:
где- составляющая силы резания Н;
- минимальная скорость резания ммин;
- коэффициент использования равный 07;
где- КПД механизма подачи – 096;
- КПД коробки скоростей.
- КПД зубчатой передачи;- число ЗП;
- КПД подшипников качения;- число подшипников.
Для определения силы резания рассчитаем режимы резания при черновом сверлении.
Рассверлить отверстие выдерживая размеры ø30мм l=40
Рассчитываем составляющую силы резания - Н.
- глубина резания мм;
- скорость резания ммин;
- коэффициент учитывающий влияние геометрических параметров режущей части инструмента на составляющие силы резания.
[2 стр. 281 таблица 32]
[2 стр. 264 таблица 9]
Далее определяем мощность электродвигателя:
По таблице 4.1 [2 стр. 36] в соответствии с рекомендациями выбираем электродвигатель модели 4А1122M4У3
Мощность данного электродвигателя ; частота вращения ; КПД - .
6. Расчет фактических значений частот вращения шпинделя.
Рассчитываем отклонение фактической частоты вращения шпинделя от расчетной частоты по формуле:
Величина погрешности не должна превышать
8. Расчет зубчатых колес
В коробках скоростей на стадии проектных разработок расчет зубчатых колес ведется обычно на выносливость (усталость) поверхностных слоев по контактным напряжениям и проверяется по напряжениям изгиба.
Модуль цилиндрических зубчатых колес определяют по контактным напряжениям:
по напряжениям изгиба:
N – мощность в цепи от электродвигателя до рассчитываемой шестерни с учетом КПД и с учетом предполагаемой перегрузки электродвигателя кВт;
n – число оборотов (обмин) шестерни передачи расчетной кинематической цепи по которой на шпиндель передается примерно верхняя частота нижней трети диапазона регулирования;
z – число зубьев рассчитываемой шестерни;
- отношение ширины зубчатого колеса bк модулю
y – коэффициент формы зуба;
- допустимое контактное напряжение МПа;
- допустимое напряжение на изгиб МПа;
k – коэффициент долговечности;
- коэффициент неравномерности распределения нагрузки;
- коэффициент динамичности;
При расчете на изгиб следует принять а при расчете на контактное напряжение:
где - коэффициент характеризующий предполагаемое изменение мощности передаваемой рассчитываемой шестерней [1 стр. 45 табл. 4.5];
Т – расчетное время работы передачи в часах Т=10000 для передач включенных постоянно и Т=10000Х для передач включаемых поочередно (Х – число включаемых передач);
– базовое число циклов нагружений для материала рассчитываемой шестерни;
- наименьшая частота вращения рассчитываемой шестерни при которой передается полная мощность двигателя обмин;
- коэффициент характеризующий работу передачи на различных частотах вращения [1 стр. 45 табл. 4.6] [1 стр. 46 рис. 4.13];
Производим расчет модулей.
Материал зубчатого колеса: Сталь 45
ТО: нормализация НВ 170-217 .
;z=36; ; ; ;T=33333; ; y=0110.
Принимаем модуль m=25мм.
Материал зубчатого колеса: Сталь 45.
;z=40; ; ; ;T=5000; ; y=0113.
;z=21; ; ; ;T=5000; ; y=0113.
Принимаем модуль m=3мм.
;z=25; ; ; ;T=5000; ; y=0113.
ТО: улучшение НВ 170-217 .
;z=24; ; ; ;T=5000; ; y=0137.
Расчет размеров зубчатых колес
Таблица 3.1 – Геометрические размеры зубчатых колес.
Диаметр окружности вершин зубьев
Силовые расчёты основных механизмов.
1. Предварительный расчет валов.
Для предварительного прочерчивания валов их диаметры определяют по формуле:
где P – мощность передаваемая валом кВт;
n– минимальная частота вращения вала обмин.
Мощность на валах берем из расчетов модулей зубчатых колес а минимальные частоты вращения валов определяем по ГЧВ.
2. Расчет валов на прочность.
Полный расчет проводим для шпинделя и предпоследнего вала.
Определим угловые скорости и крутящие моменты на валах:
Расчет на прочность вала VI
Рисунок 3.1 – Схема нагружения вала VII.
На вал действуют следующие силы
На зубчатое колесо (ведущее в паре ) действует окружная сила и радиальная . На колесо - силы и .
где d – делительный диаметр меньшего колеса м.
Радиальное усилие рассчитываем по формуле:
где – угол зацепления.
На зубчатое колесо действуют силы и .
В принятой системе координат XOYсоставляющие и раскладываются по проекциям:
Рисунок 3.2 – Проекции сил в системе координат ХОУ.
Таким образом радиальная составляющая будет равна сумме
а окружное усилие -
Расчет реакции в опорах
Опасное сечение вала в точке D
Определяем эквивалентный момент проходящий через точку D:
Рисунок 3.3 – эпюры моментов действующих на вал VI.
Определим диаметр из формулы:
где W– осевой момент сопротивления мм3;
Подставим данные в формулу
Расчет на прочность шпинделя (вала IХ)
Рисунок 3.4– схема нагружения вала IX.
На зубчатое колесо (ведомое в паре ) действует окружная сила и радиальная .
Определим силу резанияиз уравнения:
Возьмем скорость резания для черновой обработки стали 45 примем V=85.5ммин.
Опасное сечение вала в точке С
Определяем эквивалентный момент проходящий через точку С:
Рисунок 3.5 – эпюры моментов действующих на вал VII.
3. Расчет валов на жесткость.
Расчет вала VI на жесткость
Расчет валов на жесткость ведется по формулам из таблицы с учетом всех сил действующих на шпиндель и непосредственно на вал VI и определяем суммарный прогиб с учетом всех знаков.
Определяем углы наклона осей в плоскости действия окружных усилий:
– модуль упругости МПа для стального вала;
J – осевой момент инерции сечения вала
Общая сила действующая на вал:
т.к. вал не имеет свободного конца.
- не рассчитывается;
Рисунок 3.6 – Схема действия сил на вал VI.
Взаимный перекос определяется как алгебраическая сумма:
Из условия соотношения наибольших и наименьших контактных напряжений зуба взаимный перекос не должен превышать значение:
Так как суммарный перекос получился меньше то зубчатые колеса и валы подобраны правильно.
Существует следующая норма допускаемых перегибов и углов наклона поперечных сечений осей и валов; прогиб максимальный
в месте установки зубчатых колес
Так как все значения прогиба в сечении вала находятся в допустимых пределах то диаметр вала выбран правильно и пересчета конструктивных размеров не требуется.
Расчет шпинделя (вала VII)на жесткость.
Расчет шпинделя ведется по формулам из таблицы 4.9 с учетом всех сил действующих на шпиндель и определяем суммарный прогиб с учетом всех знаков.
Определим углы наклона оси шпинделя в плоскости действия окружных усилий:
Общая сила действующая на колеса шпинделя:
Из условия соблюдения наибольших и наименьших контактных напряжений по длине зуба взаимный перекос не должен превышать значения:
Условие выполняется.
Приближенный расчет шпинделя на жесткость без учета податливости опор сводится к определению деформации изгиба и деформации кручения.
Внешним силам действующим на шпиндель будут сила и усилие в зацеплении приводной шестерни коробки скоростей . Сила резания является равнодействующей максимальных значений составляющих силы резания и .
Сила в зацеплении зубчатых колес определяется через окружную составляющую силы в зацеплении . Угол зацепления и угол трения
- делительный диаметр окружности зубчатого колеса шпинделя
- расчетный диаметр шпинделя.
Взаимный перекос определяется как алгебраическая сумму углов наклона .
При определении прогиба шпинделя углов наклона сечений шпинделя при изгибе и допустимых углов закручивания φ шпинделя на основе опыта станкостроения могут быть предложены следующие эмпирические зависимости:
б) прогиб на конце шпинделя не должен превышать 13 допуска на биение конца шпинделя.
в) для нормальной работы зубчатых колес прогиб оси шпинделя под ними не должен превышать:
где m – модуль зубчатого колеса.
Максимальная величина прогиба переднего конца шпинделя не должна превышать 003 мм.
Жёсткость подшипниковых узлов можно представить в виде суммы податливости колец подшипников в контакте с телами качения () и этих же колец в контакте с посадочными поверхностями вала и корпуса ().
Податливость в зависимости от нагрузки на подшипник имеет величину
- опорная реакция Н;
и - коэффициенты [1 таблица 4.11]
d D B – соответственно внутренний и наружный диаметры и ширина подшипника мм;
- меньшее значения для посадок с натягом
По полученным податливостям имее жесткость опоры В (передний конец шпинделя).
Подсчитаем жесткость опоры А (задний конец шпинделя).
Определим величину прогиба переднего конца шпинделя:
Рисунок 3.7 – Расчетная схема для определения прогиба шпиндельного узла.
Прогиб шпинделя в точке С составляет 734 мкм.
4. Выбор подшипников.
Для валов II и IIIвыбираем:
- верхний подшипник шариковый радиальный однорядный 304 по ГОСТ 8338-75:
Габаритные размеры: d ;;.
-нижний подшипник шариковый радиальный со стопорной канавкой 50304 по ГОСТ 2895-82:
Для вала IVвыбираем:
- верхний подшипник шариковый радиальный однорядный 205 по ГОСТ 8338-75:
-нижнийподшипник шариковый радиальный со стопорной канавкой 50205 по ГОСТ 2895-82:
-верхний подшипник шариковый радиальный однорядный 208 по ГОСТ 8338-75:
-нижнийподшипник шариковый радиальный однорядный со стопорной канавкой 50208 по ГОСТ 2895-82:
Для вала VIвыбираем:
-верхний подшипник шариковый радиальный однорядный 209 по ГОСТ 8338-75:
-нижнийподшипник шариковый радиальный однорядный со стопорной канавкой 50209 по ГОСТ 2895-82:
Для вала VII(шпиндель)выбираем подшипники шариковые радиальные однорядные 217 по ГОСТ 8338-75:
В процессе курсового проектирования был разработан радиально-сверлильный станок с ЧПУ на базе радиально-сверлильного станка модели 2М55. Были произведены расчёты режимов резания коробки скоростей количество числа зубьев зубчатых колёс а так же силовые расчёты основных механизмов. Так же построены структурные сетки и графики вращения.
В графической части курсового проекта были выполнены чертежи основных узлов спроектированного станка а так же его кинематическая схема.
Список использованной литературы
Справочник технолога-машиностроителя в 2-х т. Т.2 под редакцией А.Г. Косиловой. М.: Машиностроение 1985. - 496с.
Анурьев В.И. - Справочник конструктора-машиностроителя в 3-х т. Т.1 под редакцией И.Н. Жестковой. М.: Машиностроение 2001. - 920с.
Анурьев В.И. - Справочник конструктора-машиностроителя в 3-х т. Т.2 под редакцией И.Н. Жестковой. М.: Машиностроение 2001. - 912с.
Кучер А.М. Немые кинематические схемы металлорежущих станков. Альбом. Издание 2е 1977г.
Рекомендуемые чертежи
- 24.01.2023
- 24.01.2023
Свободное скачивание на сегодня
- 23.02.2023