Расчет и проектировка главного редуктора вертолета




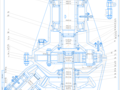
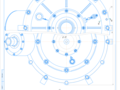
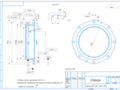
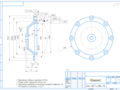
- Добавлен: 25.01.2023
- Размер: 2 MB
- Закачек: 0
Описание
Состав проекта
![]() |
![]() |
![]() ![]() ![]() ![]() |
![]() ![]() ![]() |
![]() ![]() ![]() ![]() |
![]() ![]() ![]() ![]() |
![]() ![]() ![]() ![]() |
![]() ![]() ![]() ![]() |
![]() ![]() ![]() ![]() |
Дополнительная информация
val_.cdw

stakan_.cdw

glav_vid reduktora.cdw

vid sverhu-snizu.cdw

kryshka reduktora.cdw

Koleso_zubchatoe_.cdw

Рекомендуемые чертежи
- 20.12.2022