Производство водорода электролитическим методом. Мощность 200 т\год


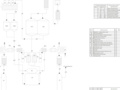
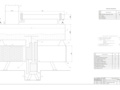
- Добавлен: 25.01.2023
- Размер: 1 MB
- Закачек: 1
Подписаться на ежедневные обновления каталога:
Описание
Производство водорода электролитическим методом. Мощность 200 т\год
Состав проекта
![]() |
![]() ![]() ![]() |
![]() ![]() ![]() ![]() |
![]() ![]() ![]() ![]() |
Дополнительная информация
Контент чертежей
Производство водорода диплом.docx
1. Аналитический обзор4
2 Теоретические основы технологического процесса12
3 Характеристика сырья и готового продукта.16
4. Описание технологической схемы21
6. Аналитический контроль22
7. Автоматизация производства29
8 Характеристика электролизёра30
ТЕХНОЛОГИЧЕСКИЕ И КОНСТРУКТИВНЫНЫЕ РАСЧЁТЫ33
1. Материальный баланс электролизёра33
2. Тепловой баланс электролизёра35
3. Расчёт основных параметров аппарата40
В природе и в жизни человека водород имеет большое значение. По распространённости элементарный водород занимает 1 место во Вселенной так как является основной частью состава звёзд и межзвёздного газа. В земной коре его содержание составляет 1% от всей массы — десятый элемент по распространённости. Практически весь водород на Земле присутствует в виде различных соединений большая часть из которых — органические молекулы. В свободном состоянии встречается довольно редко например в вулканическом газе и продуктах разложения органических остатков.
На сегодняшний день водород имеет множество применений:
в химической промышленности для производства аммиака (прямое взаимодействие с азотом) метанола (каталитический синтез из оксида углерода и водорода) и соляной кислоты (на первой стадии для получения газообразного хлороводорода);
в нефтепереработке при крекинге и очистке;
в пищевой промышленности для производства твёрдых растительных жиров;
в металлургии для восстановления металлов из оксидов;
в качестве охладителя на тепловых и атомных электростанциях;
в жидком виде в качестве ракетного топлива [1].
ТЕХНОЛОГИЧЕСКАЯ ЧАСТЬ
1. Аналитический обзор
В химической промышленности существует несколько основных способов получения водорода:
паровая конверсия метана и оксида углерода водяным паром;
термическое разложение углеводородов;
Рассмотрим каждый из этих методов.
Паровая конверсия метана водяным паром является одним из самых распространённых способов. Его суть заключается во взаимодействии метана с водяным паром в присутствии катализатора (оксида никеля нанесённого на оксид алюминия) при высоких температурах(800-900°С) по следующему уравнению:
Образующаяся смесь оксида углерода(II) и водорода называется синтез-газом. Её используют либо для производства азотоводородной смеси необходимой для синтеза аммиака либо на производство метанола.
Образовавшийся оксид углерода(II) используют для получения дополнительного количества водорода:
В результате конверсии решается проблема с очисткой синтез-газа от (так как прочие методы довольно дорогостоящие) а также получают дополнительное количество водорода. От диоксида углерода конвертированный газ очищается жидкими органическими абсорбентами (хемосорбция) [2].
На рис. 1 представлена схема конверсии метана по способу C.C.R (Cyclic Catalitic Reforming Process).
Конверсия сырья происходит в агрегате состоящего из двух вертикальных шахт — камеры сгорания 2 и камеры конверсии соединённых между собой
каналом. В камере сгорания расположена огнеупорная насадка а в камере конверсии — никелевый катализатор 11 расположенный над огнеупорным сводом.
Рис.1. Схема каталитической конверсии углеводородов с водяным паром по способу C.C.R:
– вентилятор; 2 – камера сгорания; 3 – камера конверсии; 4 – пароперегреватель; 5 – котёл-утилизатор; 6 – дымовая труба; 7 – гидрозатвор; 8 – промыватель; 9 – аккумулятор пара; 10 – горелка; 11 – катализатор.
В верхнюю камеру сгорания поступают отопительный газ или жидкое топливо а также воздух с вентилятора 1. Продукты горения проходят камеру сгорания сверху вниз а камеру конверсии снизу вверх передавая часть своего тепла насадке и катализатору. Углеводородное сырьё подаётся в соединительный канал между камерами а пар в нижнюю часть камеры сгорания(над огнеупорной насадкой) что позволяет ему перегреваться. Смесь исходного газа и пара поступает снизу в камеру конверсии где на катализаторе происходит превращение. Продукты горения после использования их тепла в котле-утилизаторе 5 и пароперегревателе 4 удаляются через дымовую трубу 6. Конвертированный газ также проходит через утилизатор и подвергается очистке и охлаждению в промывателе 4.
Основным преимуществом этой схемы является то что в качестве сырья можно использовать не только метан но и многие другие углеводороды.
После очистки газ поступает на дальнейшее конвертирование. На рисунке 2 представлена принципиальная схема двухступенчатой конверсии
Рис.2. Принципиальная схема двухступенчатой конверсии оксида углерода(I)
– сатуратор; 2 – теплообменник; 3 – конвертор; 4 – водонагревательная башня; 5 – холодильник; 6 – циркуляционные насосы.
Синтез-газ подаётся в сатурационную башню где орошается горячей водой нагревая газ примерно до 80°С и насыщая его водяными парами. Затем нагретый газ поступает в двухступенчатый конвертор проходя перед этим стадию смешивания с горячим водяным паром и теплообменник где смесь нагревается примерно до 400°С. Сама конверсия происходит в 2 ступени: первая происходит на среднетемпературном катализаторе(Fe-Cr) вторая осуществляется на низкотемпературном катализаторе(Zn-Cr-Cu) предварительно охладив газ до 250-300°С. Затем конвертированный газ проходит через теплообменник отдавая своё тепло и поступает в
водонагревательную башню 4 где температура газа снижается за счёт орошения водой поступающей из сатуратора до температуры 80-85°С.
Образовавшийся конденсат откачивается обратно в сатуратор циркуляционными насосами 6. Оставшаяся вода конденсируется в холодильнике в котором газ охлаждается до 30°С и отправляется на дальнейшую переработку.
Данный метод очень хорошо подходит для крупнотоннажных производств. Недостатками метода можно назвать металлоёмкость и громоздкость оборудования достаточно высокие затраты на обогрев реакционной зоны (решается введением циркуляции топочных газов) [3].
В основе метода термического разложения углеводородов лежит процесс нагревания углеводородов без присутствия окислителя. Этот метод нашёл ограниченное применение в промышленности до определённого времени так как получаемый водород загрязнён большим количеством примесей а установки были только периодически действующими. На настоящее время существуют непрерывные установки с чистотой водорода 97-98 В качестве сырья могут использоваться как жидкое углеводородное сырьё (в основном это остаточные продукты переработки нефти) так и газообразное (чаще всего низшие алканы). При использовании газообразного сырья образуется либо чистый водород либо с примесью сажи.
Высокотемпературная обработка связана с образованием наиболее термически устойчивого углеводорода – метана так что процесс будет лимитироваться именно стадией распада метана уравнение которой выглядит следующим образом:
Скорость этой реакции можно увеличить если использовать катализаторы содержащие железо никель и некоторые другие металлы
однако в таком случае процесс усложняется так как начинают образовываться карбиды металлов.
Непрерывные способы получения водорода данным методом предусматривают применение движущей насадки которая используется как
теплоноситель и является катализатором одновременно. Полученная сажа
откладывается на насадке и либо выжигается либо используется для выработки водяного газа. На рис. 3 показана схема данного метода.
Рис.3. Принципиальная схема непрерывного термического разложения углеводородных газов:
– регенератор; 2 – реактор; 3 – камера охлаждения; 4 – бункер для свежей насадки;
– питатель для пневмотранспортёра; 6 – бункер для избыточной насадки 7 – дымовая труба 8 – гидрозатворы 9 – воздуходувка 10 – насос
Насадка выводится снизу реактора и направляется в питатель пневнотранспортёра 5 оттуда по пневмотрубе поступает в регенератор 1
в котором происходит её очистка и разогревание до 1350-1400°С. Из регенератора насадка поступает в реактор замыкая циркуляцию теплоносителя. Исходный газ подаётся в нижнюю часть реактора и направляется противотоком к теплоносителю. При соприкосновении газа с насадкой происходит
термическое разложение а насадка охлаждается до 500°С. Получившийся водород поступает в камеру охлаждения 3 где орошается холодной водой и охлаждается до 200°С .
Термическое разложение жидких углеводородов отличается несущественно. Происходит оно в два этапа: разложение жидких углеводородов до углеводородного газа и его термическое разложение.
Недостатком данного метода можно считать недостаточную чистоту конечного продукта(по сравнению с другими методами) а также высокую температуру процесса [4].
В основе метода электролиза воды лежит электролитический распад воды на водород и кислород по уравнению:
Так как расход энергии достаточно велик (до 5 кВт-ч на 1 ) данный способ в больших промышленных масштабах применяется в регионах с низкой стоимостью электроэнергии таких как Япония и Норвегия.
В качестве сырья используется очищенная (деминерализованная) водопроводная вода с добавлением небольшого количества щёлочи (обычно это раствор KOH). Процесс проходит следующим образом: в растворе под действием электрического тока происходит электролитическая диссоциация и перемещение ионов к электродам:
Затем на катоде происходит процесс дегидратации оксония с образованием воды и водорода а на аноде – разряд и дегидратация гидроксила:
На рис. 4 представлена схема производства водорода данным методом.
Рис.4. Технологическая схема производства водорода методом электролиза воды:
– барабаны со щёлочью; 2 – бак-растворитель; 3 – ёмкости; 4 – фильтр для очистки воды; 5 – ёмкость для кислотного регенерационного раствора; 67 –ионнообменные колонны 8 – ёмкость для щелочного регенерационного раствора
–сборники очищенной воды 10 – питательный бак 11 – фильтры для очистки газов от щелочного тумана 12 – аппарат каталитической очистки водорода 13 – аппарат дожигания примесей 14 – холодильники газов 15 – осушители газов 16 – ресиверы водорода и кислорода 17 – клапанные регуляторы давления газов 1819 – промыватели газов 20 – разделительные колонны 21 – электролизёр 22 – баллоны с азотом для продувки 23 – преобразователь тока
Раствор электролита готовят растворением твёрдой щёлочи из барабанов 1 в баке растворителе 2. Полученный раствор проходит через
ёмкости 3 и попадает в электролизёр 21. Вода очищенная на фильтре 4 направляется последовательно в колонны 6 и 7 наполненные ионнообменными смолами проходит глубокую очистку и попадает в сборник 9 откуда перекачивается насосом в питательный бак 10 и проходя промыватель газа
подаётся в электролизёр. Получаемые водород и кислород отделяются от циркулирующего раствора электролита в колонках 20 и поступают в промыватели 18 и 19 где охлаждаются и из них удаляется щёлочь. Дальше через клапанные регуляторы давления 17 газы поступают потребителю. Если нужна дополнительная очистка то газы проходят дальше. На насадочных фильтрах 11 газы очищаются от щелочного тумана. В контактных аппаратах 12 и 13 происходит каталитическая очистка от следов других газов. После полной очистки газы попадают в холодильники 14 и оттуда в осушительные колонны 15 а затем через ресиверы 16 – потребителям.
Водород полученный таким методом имеет очень высокую степень чистоты(99.7%). Этот метод применяется для малотоннажных производств. К недостаткам можно отнести завышенную себестоимость конечного продукта вследствие высоких затрат на электроэнергию но использование альтернативных источников энергии таких как солнечные батареи или ветряные генераторы позволяет снизить стоимость в несколько раз [5].
Существуют также и другие методы производства водорода:
газификация угля (нагревание угля в присутствии водяного пара до 800-1300°С);
выделение из водородосодержащих газов путём глубокого охлаждения;
биотехническое производство водорода(из группы зелёных водорослей) [6].
Но эти методы либо похожи на уже описанные (газификация) либо не используются в промышленности или используются в небольших количествах.
Исходя из задания выберем метод электролиза воды так как необходимо производить небольшое количество водорода а метод паровой конверсии рассчитан на большие объёмы производств. Технологическая схема используемая в работе приведена в приложении 1.
Небольшая доля электролитического водорода в общем объёме его производства обусловлена достаточно высоким расходом электроэнергии.
Но современный уровень развития данного метода является достаточно экономичным для производства небольших количеств водовода.
Основными задачами для усовершенствования процесса являются:
увеличение единичной мощности электролизёра;
снижение удельных затрат электричества на получение целевых продуктов;
снижение удельных капиталовложений для организации крупного производства.
Для усовершенствования процесса можно использовать следующие технологические решения:
развитие рабочей электродной поверхности при разработке специальных конструкций электродов например при помощи пористых электродов обеспечивающих лучший отвод газов из зоны электролиза;
выполнение электродов из оксидов металлов которые обеспечивают нормальную эксплуатацию электродов при высоких температурах;
повышение рабочей температуры и давления процесса;
применение альтернативных источников энергии;
применение новых защитных и конструкционных материалов.
Одним из путей интенсификации процесса электролиза является использование твёрдых электролитов. Электролиз с такими электролитами водяного пара при температуре 800-1000 может быть осуществлён при напряжении около 1.3 В
и при плотности тока до 30 кАм2. Использование полимерного твёрдого электролита включающего в свой состав перфторуглеродный полимер с ионоактивными сульфогруппами позволяет снизить рабочую температуру до 150 при плотности тока около 20кАм2 и напряжении 1.6-1.75 В [6].
2 Теоретические основы технологического процесса
Электролиз - физико-химический процесс состоящий в выделении на электродах составных частей растворённых веществ или других веществ являющихся результатом вторичных реакций на электродах который возникает при прохождении электрического тока через раствор либо расплав электролита.
В электрохимических процессах реакция протекает за счёт подведённой электрической энергии в отличие от химических реакций при протекании которых происходит поглощение либо выделение тепла. При проведении электролиза к уже имеющимся факторам таким как температура давление активность компонентов прибавляется ещё один – потенциал электрода который можно изменять в определённых границах влияя на кинетику и направление процесса.
Во многих случаях применение электрохимических методов имеет по сравнению с чисто химическими способами ряд преимуществ. Иногда схема электролитического производства гораздо проще исходное сырьё используется более полно чистота получившегося продукта также может быть выше в некоторых случаях.
В большей степени протекание процесса зависит от материала используемого для изготовления электродов. На перенапряжение на электродах и ход процесса можно повлиять изменяя электрохимические свойства материалов поверхность электродов а также изменяя плотность тока и величину рН вводя добавки в электролит.
На данный момент электролиз в промышленности применяется для получения гипохлоратов хлоратов хлорной кислоты перманганатов диоксида марганци ряда органических веществ (фторпроизводные тетраэтилсвинца и т.д) но наиболее крупные производства – водород хлор гидроксиды натрия и калия а также гидроэлектрометаллургия.
Течение катодных и анодных реакций при электролизе определяется следующими двумя законами Фарадея.:
вещества выделившегося при электролизе на катоде или перешедшего с анода в электролит пропорциональна количеству прошедшего через электролит электричества:
Коэффициент пропорциональности называется электрохимическим эквивалентом вещества. Он численно равен массе вещества выделившегося при прохождении через электролит единичного электрического заряда и зависит от химической природы вещества.
выделенного при электролизе вещества одним и тем же количеством электричества прямо пропорциональна атомной массе вещества М и обратно пропорциональна его валентности n:
в данном уравнении – постоянная Фарадея равная 96480 Кл·моль-1.
Теоретически на каждые 96480 Кл пропущеного через ячейку постоянного тока должно выделяться по 1 экв водорода и кислорода. Практически же выход по току снижается из-за протекания побочных процессов на электродах которые приводят к загрязнению продуктов и бесполезной затрате тока. Отношение количества газа практически полученного в ячейке к количеству газа которое должно выделиться при полном использовании тока и называется выходом по току.
В промышленных электролизёрах выход по току обычно колеблется в районе 0.95.
Процесс электролиза воды описывается следующим уравнением:
В результате электролиза выделяется водород и кислород в виде газов которые затем улавливаются разделяются и направляются потребителю.
Для протекания данной реакции необходима диссоциация молекулы воды на электроны:
Механизм процесса заключается в переносе ионов к электронов к электродом
где они отдают свой заряд с образованием молекул водорода и кислорода.
Так как вода относится к веществам с малой электропроводностью и низкой степенью диссоциации на практике ведут электролиз не чистой воды а водного раствора щёлочи – гидроксида калия или натрия. Электролит – это водный раствор щёлочи применяемый при электролизе.
Ионы образовавшиеся в результате диссоциации находятся в хаотичном движении. При пропускании постоянного электрического тока поместив вводу электроды движение становится направленным: отрицательно заряженные ионы будут перемещаться к аноду а положительно заряженные – к катоду. На них и происходит отдача электрического заряда и выделение газов.
На катоде протекает следующая реакция:
Но в растворе едких щелочей наблюдается малая концентрация водородных ионов и главным образом происходит разложение воды:
H2O + 2e- = H2 + 2OH-
На аноде процесс носит следующий характер:
Из всего приведённого следует что электролиз протекает по следующей схеме:
H2O + 4e- = 2 H2 + 4OH- (катод);
OH- - 4e- = 4H2O + O2 (анод)
На каждый 1 м3 получаемого водорода в качестве побочного продукта получается 0.5 м3 кислорода.
Для разложения воды теоретически необходимо поддерживать разность потенциалов между электродами равную 1.23 В. Это напряжение называется напряжением разложения.
Практически же для обеспечения непрерывного процесса напряжение следует поддерживать значительно выше (до 2.3 В). Разность между фактическим напряжением и напряжением разложения называется перенапряжением и зависит от многих факторов (например состояния электродов температура электролита). При повышении температуры перенапряжение уменьшается из за этого электролиз ведут при 50-90оС. Необходимо учитывать что чем выше энергия перенапряжения тем больше удельный расход электроэнергии на производство водорода [5].
3 Характеристика сырья и готового продукта.
Используемую воду подвергают очистке дистилляцией электроосмосом или обессоливанием на ионитах. Дистилляционный метод прост но требует больших затрат энергии. Электроосмотический метод более сложен по аппаратурному оформлению. Наиболее широкое распространение получил ионообменный метод благодаря простоте экономичности и высокой степени очистки. Затраты на очистку воды окупаются повышением длительности и надёжности работы электролизёра.
После очистки вода должна отвечать требованиям по содержанию того или иного вещества представленным в таблице 1.
Содержание веществ в обессоленной воде
Чтобы вода не загрязнялась продуктами коррозии все промежуточные сборники ёмкости для хранения и трубопроводы следует выполнять из нержавеющей стали или алюминия.
Хорошие результаты наблюдались при хранении и транспортировке слабо подщелочной воды в ёмкостях и трубопроводах из обычной углеродистой стали при этом отсутствовало загрязнение ионами железа.
Однако в этом случае следует строго следит за подщелачиванием очищенной воды. Для большей гарантии от попадания гидроксида железа в воду на линии перед входом в аппарат иногда устанавливают фильтры с войлочной насадкой или плотной репсовой сеткой из никелевой проволки.
Раствор КОН применяется в качестве электролита для прохождения процесса электролиза. Раствор обычно готовится на месте путём разбавления концентрированного КОН в виде гранул. Твёрдый гидроксид калия обычно
поставляется в стальных барабанах. Приготовление производится вымыванием щёлочи из барабанов водой. В баке для растворения есть несколько гнёзд в виде корзины куда устанавливаются вскрытые барабаны.
В гнёздах имеются штуцеры соединённые с насосом для подачи дистиллята.
Струя воды под напором растворяет щёлочь стекает в бак и снова подаётся насосом в барабан до полного вымывания щёлочи. По окончании растворения щёлочи в бак добавляют очищенную воду. На выходе получается раствор с
массовой долей КОН 30-35%. Для удаления механических примесей раствор фильтруют через плотную никелевую сетку и перекачивают в хранилища откуда по мере надобности забирают для заполнения электролизёра.
При длительной эксплуатации электролит загрязняется продуктами разрушения футеровочных материалов частей электролизёра а также примесями содержащимися в воде и воздухе поэтому периодически его следует заменять свежим. Щёлочь может быть очищена и возвращена в производство. Обычно очистка происходит химическим методом – осаждением гидроксидом кальция примесей (карбонаты и сульфаты). После отстаивания и слива осадок выбрасывается а регенерированный электролит доводят до необходимой концентрации и возвращают на заполнение электролизёров [8].
Водород в чистом виде представляет собой лёгкий бесцветный газ не имеющий запаха. Легко воспламеняется и горит голубоватым пламенем. Имеет низкие температуры кипения (-2528°С) и плавления(-2591°С) а также наибольшую теплопроводность(0174 при давлении 1 атм. и температуре 0°С).
В обычном состоянии и низких температурах водород малоактивен(это объясняется тем что энергия связи в молекуле водорода составляет
6кДжмоль) и без нагревания реагирует только с F2.
C хлором может реагировать только в присутствии солнечного света
с бромом только при повышенной температуре и менее энергично а с йодом
реакция не доходит до конца даже при высоких температурах.
Водород является хорошим восстановителем его можно использовать для восстановления металлов из их оксидов:
При высоких температурах может реагировать с щелочными и щелочно-земельными металлами образуя гидриды:
С неметаллами водород реагирует лучше чем с металлами. Например энергично реагирует с серой (в отличие от реакций с селеном или теллуром из той же группы которые проходят гораздо медленнее) :
Для некоторых реакций с неметаллами требуется присутствие катализатора как например в случае с реакцией с азотом:
К кислородом также взаимодействие происходит при высокой температуре (400°С) а если довести температуру до 600°С то водород начнёт взаимодействовать с воздухом.
Смесь водорода и кислорода (или воздуха) взрывоопасна и называется гремучим газом. При атмосферном давлении и температуре 510°С способен к самовоспламенению. При комнатной температуре способен взорваться при даже слабом источнике огня(для инициирования взрыва достаточно искры с
энергией 17 микроджоулей).[9]
После процесса электролиза получаемый водород имеет состав:
Объёмная доля водорода -999%;
Содержание кислорода-≤ 1 000 мкгкг;
Содержание воды -≤ 2 100 мкгкг или атмосферная точка росы: -12°С;
Содержание KOH -10-30 мкг KOH Н·м3 Н2
От щелочного тумана избавляются пропусканием газов через насадочные фильтры плотно забитые стекловатой. Мелкие капли щёлочи осаждаются на вате и стекают в нижнюю часть фильтра.
От примеси кислорода в водороде избавляются в контактном аппарате на палладиевом катализаторе который нанесён на силикагель либо пемзу.
Также используют более дешёвые никельалюминиевый или никельхромовый катализаторы. На катализаторе происходит взаимодействие двух газов с образованием воды при 100-130°С. Подогрев газовой смеси происходит при поступлении газа в аппарат в дальнейшем подогрев не требуется так как в процессе реакции выделяется тепло. После газ охлаждается и поступает на осушку.
Для большинства потребителей содержащийся водяной пар не является вредной примесью. Нежелательно присутствие воды при транспортировании в зимнее время. Для осушки газы охлаждают до -10°С пропуская через рассольные холодильники. Также распространение получила осушка газов сорбентами. В большинстве установок используется силикагель либо алюмогель.
В результате выпускаемый водород полностью соответствует требуемым стандартам а именно ГОСТ 3022-80(водород газообразный технический электролизный марка «Б»):
Объёмная доля водорода – не менее 9995 %;
Объёмная доля кислорода – не более 005%;
Содержание воды - точка росы -80°С.
Кислород получающийся в качестве побочного продукта в процессе электролиза имеет состав:
Объёмная доля кислорода – 990 %;
Содержание водорода - ≤ 3 000 мкгкг;
Содержание воды -≤ 2 100 мкгкг ;
Содержание KOH -10-30 мкг KOH Н·м3 О2.
Очистка от примесей водорода в кислороде требуется когда нужен кислород высокой чистоты либо при использовании в процессах протекающих без
участия водорода который вследствие этого может накапливаться до взрывоопасной концентрации. В этих случаях необходима предварительная очистка дожиганием водорода на катализаторе (платина либо гопкалит). Достаточная скорость и полнота очистки достигается при 50°С.
После очистки от водорода КОН и воды кислород начинает соответствовать требованиям ГОСТ 5583-78 (Кислород газообразный технический марка «Б»):
Объёмная доля кислорода – не менее 995 %;
Объёмная доля водорода – не более 005%;
4. Описание технологической схемы
В приложении 1 указана используемая технологическая схема.
Водопроводная вода поступает на очистку сначала от механических примесей на фильтре Ф а затем в колоннах ИК 1-2 от ионов металлов солей жёсткости. Из сборников СВ1-2 часть воды поступает на приготовление раствора гидроксида кальция. Раствор электролита готовят растворением твёрдой щёлочи из барабанов Б1-3 в баке растворителе БР. Полученный раствор проходит через ёмкости 3 и попадает в электролизёр ЭЛ. Туда же подаётся и очищенная вода проходя через промыватели газов ПГ1-2.
а затем через ресиверы Р1-2 уходят либо напрямую по трубопроводу на дальнейшее производство либо на заполнение баллонов и дальнейшую продажу.
Производство водорода методом электролиза хорошо тем что почти не имеет вредных выбросов в окружающую среду.
По путям попадания вещества на производстве делятся на два вида:
Вещества попадающие в окружающую среду в случае утечек (водород кислород гидроксид калия вода);
Вещества попадающие в окружающую среду в случае плановых выбросов на этапах продувки (водород азот).
Водород соединяется с кислородом воздуха с образованием воды.
Кислород и азот представляют собой такие же двухатомные газы какие находятся в атмосфере и так как являются двумя основными составляющими воздуха то не представляют никакой угрозы.
Гидроксид калия попадает в окружающую среду только в случае какой-либо утечки из баков. Чтобы не допустить подобного в соответствии регламентом проводится профилактика оборудования (периодический осмотр проверка герметичности) а на случай заметных утечек имеется набор для нейтрализации утекшего электролита (нейтрализующая кислота поглощающие тампоны мешки для утилизации).
В случае водой так же проводятся профилактические мероприятия во избежание утечек из баков.
6. Аналитический контроль
На электрохимических производствах обычно предусмотрены 2 вида контроля продуктов – в автоматическом и ручном режимах.
В автоматическом режиме контроль водорода осуществляется корректором
СПГ762. Данный прибор предназначен для измерения электрических сигналов соответствующих параметрам технических газов различного состава и последующего вычисления расхода и объёма газа приведённых к стандартным условиям. Корректор обеспечивает вычисление массового расхода объёмного расхода при стандартных условиях а так же вычисление массы и объёма с учётом измеряемых величин (температура давление перепад давления плотность относительная влажность).
В автоматическом режиме кислород анализируется газоанализатором O2X1.
Парамагнитные свойства кислорода обуславливают втягивание в магнитное поле пробы газа. Введение кислородсодержащей газовой смеси в магнитное поле и ее нагрев приводит к возникновению вынужденного движения газовой смеси при котором нагретая газовая смесь непрерывно вытесняется холодной смесью. Образующий конвекционный поток газа приводит к изменению сопротивления пары термисторов которые включены в мост Уитстона. Результирующий сигнал а также измеренные значения теплоемкости и вязкости используются микропроцессором для точного расчета концентрации кислорода [7].
Вручную количество оставшегося кислорода в водороде определяют колориметрическим методом при помощи сосуда для анализа типа СВ7636-М как предписывает ГОСТ 3022-80. Этот метод основан на окислении бесцветного медноаммиачного комплекса одновалентной меди кислородом
содержащимся в водороде при этом раствор окрашивается в синий цвет характерный для медноаммиачного комплекса двухвалентной меди. Уравнение выглядит следующим образом:
Готовятся раствор аммиачный раствор однохлористой меди и колориметрическая шкала. Затем происходит отбор проб. Для этого открывают
краны 1 и 3 и присоединяют сосуд для анализа к месту отбора пробы. Продувают сосуд пятнадцатикратным объемом водорода (3-10 мин) затем
уменьшают поток водорода закрывают краны 1 и 3 и отсоединяют сосуд от места отбора пробы. Затем давление в сосуде выравнивают с атмосферным быстрым поворотом крана 3. Отмечают атмосферное давление и температуру окружающего воздуха. Заполняют колбу 2 сосуда для анализа через кран 1 раствором однохлористой меди предварительно сливая из сифона первую порцию раствора и закрывают кран 1. Сравнивают окраску раствора с окраской растворов шкалы сравнения на фоне молочно-белого стекла. Отмечают номер пробирки шкалы сравнения окраска раствора в которой соответствует окраске раствора в колбе 2. Раствор однохлористой меди переливают в колбу 4.
Энергично встряхивают сосуд до полного поглощения раствором кислорода из водорода т. е. до прекращения изменения окраски раствора.
Возвращают раствор в колбу 2 и вновь сравнивают окраску раствора с окраской растворов шкалы сравнения отмечают номер пробирки окраска раствора в которой соответствует окраске раствора в колбе 2.
Объемную долю кислорода в процентах вычисляют по формуле:
где - объемы кислорода соответствующие подобранной окраске растворов шкалы сравнения до и после поглощения кислорода из пробы газа поглотительным раствором однохлористой меди соответственно см;
- объем пробы газа равный вместимости колбы 4см; f- фактор приведения объема газа к 20 °С и 1013 кПа (760 мм рт. ст.) [10].
Рис.5. Сосуд для анализа типа СВ 7636-М
– одноходовой кран; 24 – колбы; 3 – двухходовой кран
Количество водорода в кислороде в ручном режиме определяется на газоанализаторе со сжигательной пипеткой (рисунок 6) согласно ГОСТ 5583-78.
Для подготовки прибора заполняют спиралями из медной проволоки верхнюю часть поглотительного сосуда и вставляют ее через пробку в нижнюю склянку сосуда заполненную аммиачным раствором хлористого
аммония. В уравнительную склянку и в нижний сосуд сжигательной пипетки заливают раствор соляной кислоты подкрашенный несколькими каплями раствора метилового оранжевого.
Отбирают в бюретку прибора через кран 8 пробу несколько превышающую 100 см3. Приводят давление газа в бюретке к атмосферному удаляя избыток кислорода через кран 10 и резиновую трубку 4 погруженную в сосуд с водой на глубину 15-20 мм. Затем кранами 8 и 9 соединяют бюретку с поглотительным сосудом и переводят в него кислород.
Рис. 6. Газоанализатор со сжигательной пипеткой
- уравнительная склянка; 2 - трансформатор на 60 Вт (первичная обмотка на 220 В вторичная на 2-3 В); 3 - реостат на 3-5 Ом 5-6 А; 4 7 - резиновые трубки; 5 - спираль из платиновой проволоки диаметром 03 мм длиной 60 мм; 6 - сжигательная пипетка с водяным охлаждением; 8 9 10 - краны распределительной гребенки; 11 - водяная рубашка; 12 - поглотительный сосуд; 13 - измерительная бюретка; 14 - переходник
Поглощают около половины объема кислорода; остаток газа возвращают в бюретку и измеряют его объем. Затем повернув краны 8 и 9 вводят газ из бюретки в сжигательную пипетку так чтобы уровень запорной жидкостиопустился на 10-12 мм ниже платиновой спирали. Включают трансформатор и регулируют реостатом ток накала платиновой спирали доводя накал нити до слабого красного каления. По мере сжигания водорода анализируемый кислород по частям переводят из бюретки в сжигательную пипетку. По окончании сжигания водорода весь оставшийся кислород возвращают из пипетки в бюретку и измеряют его объем. Повторяют сжигание до постоянного остаточного объема.
Объемную долю водорода (Х2) в процентах вычисляют по формуле:
где V1 - объем пробы оставшийся после поглощения кислорода см3;
V 2 - объем пробы оставшийся после сжигания водорода см3;
V 3 - объем пробы кислорода взятый для анализа см3.
За результат анализа принимают среднее арифметическое результатов двух параллельных определений относительное расхождение между которыми не превышает допускаемое расхождение равное 10 %.
Количество кислорода в кислороде определяется согласно ГОСТ 5583-78 на приборе АК-M1 (рис. 7) .
Отбирают в бюретку прибора через отросток 3 крана пробу кислорода. Пережимают резиновую трубку 10 и быстрым поворотом крана выпускают из бюретки избыток газа в атмосферу. Затем поворотом крана соединяют бюретку с пипеткой и поднимая уравнительную склянку вытесняют весь кислород из бюретки в цилиндрическую часть пипетки. После заполнения раствором капиллярной трубки пипетки кран закрывают. Для лучшего поглощения кислорода прибор осторожно встряхивают. Поворотом крана соединяют бюретку с пипеткой и медленно опуская уравнительную склянку переводят в бюретку непоглощенный остаток пробы. Как только аммиачный раствор начинает поступать в бюретку кран закрывают. Газ в бюретке приводят к атмосферному давлению устанавливая на одной высоте уровни жидкости в бюретке и уравнительной склянке. Объем остаточных газов в бюретке измеряют через 1-2 мин выжидая пока жидкость стечет со стенок бюретки. Поглощение кислорода повторяют. Анализ заканчивают если после повторного поглощения измерение объема остаточных газов не превышает 005 см3. За результат анализа принимают среднее арифметическое результатов двухпараллельных определений абсолютное расхождение между которыми не превышает допускаемое расхождение равное 005 % [11].
- бюретка; 2 - двухходовой кран; 34 - отростки крана; 56 - капиллярные стеклянные трубки; 7 - поглотительная пипетка с капиллярной трубкой; 8 - штатив; 9 - уравнительная склянка; 10 11 - резиновые трубки
Количество щелочного тумана периодически определяется при помощи фильтров Петрянова представляющие собой слои синтетических волокон диаметром 1-2 мкм нанесённые на подложку из более толстых волокон . Через такой фильтр пропускают определённое количество газа измеренное газовыми часами. На фильтре почти полностью улавливается примесь щёлочи в газе. Затем фильтр снимают помещают в колбу заливают дистиллированной водой и титруют соляной кислотой. Найденное количество щёлочи относят к общему количеству пропущенного через фильтр газа.
Концентрацию электролита определяют реометром или аналитически – титрованием кислотой. Периодически в электролите общепринятыми методами проверяют содержание примесей карбонатов хлоридов и железа.
Дистиллят контролируют на содержание хлор-ионов железа и органических
примесей. Удельное омическое сопротивление является наиболее надёжным показателем так как значительно изменяется в присутствии примесей любых ионов. Омическое сопротивление замеряется при помощи солемеров например CO-1.
7. Автоматизация производства
Возможность полной автоматизации и устойчивость технологического процесса являются преимуществами электрохимического производства.
Сила тока в аппарате может автоматически регулироваться в зависимости от необходимой производительности. Нагрузки регулируются изменением напряжения постоянного тока подаваемого от выпрямителя. Питание электролизёра водой производится через регулирующие клапаны. При чрезмерном повышении или понижении уровня возможна автоматическая сигнализация либо отключение. Также автоматическое отключениевозможно при чрезмерном повышении давления газов увеличения температуры или снижения чистоты продукта по сигналу от автоматического газоанализатора.
Технологический процесс электролиза достаточно устойчив легко контролируется и поддаётся автоматическому регулированию.
Напряжение на электролизёре контролируется вольтметром который показывает общее напряжение. Рабочее напряжение зависит от нагрузки концентрации электролита и температуры.
Сила тока устанавливается исходя их необходимой производительности по газу и не должна превышать предельно допустимую. Она регулируется подачей соответствующего напряжения на электролизёр и контролируется показаниями амперметра.
Контроль за уровнем жидкости ведут с помощью водомерных стёкол. В большинстве случаев применяется автоматическое регулирование количества подаваемой воды по уровню жидкости.
Температура электролита и выходящих газов непрерывно измеряются
дистанционными манометрическими термометрами или термометрами сопротивления. На автоматизированных установках подачу охлаждающей воды регулируют с помощью термосигнализаторов.
8 Характеристика электролизёра
Электролизёр – это аппарат в котором происходит процесс электролиза. Основными узлами электролизёров являются:
Устройства для циркуляции электролита;
Диафрагмы и мембраны.
Корпус изготавливается из стали Ст.3 или Ст.30 а затем выполняется футеровка пластиком для защиты от коррозии. В качестве футеровочноко материала обычно используют полипропилен фторопласт винипласт.
Электрод – это проводник обладающий электронной проводимостью и контактирующий с электролитом.
От устройства электродов зависят напряжение на ячейке и расход электроэнергии поэтому технологические и экономические показатели работы
определяются их типом и конструкцией. Материал электродов должен быть дешёв доступен удобен для обработки иметь невысокое перенапряжение выделения водорода на катоде и кислорода на аноде обладать коррозионной стойкостью (в качестве материалов для изготовления анодов обычно используют графит свинец и его сплавы титановые сплавы платину или углеграфитовые материалы катоды обычно изготавливают из стали также существуют аппараты с жидкими электродами). Конструкция электродов должна обеспечивать возможность создания максимально развитой рабочей поверхности для снижения истинной плотности тока на поверхности. Конструкцией электродов должен предусматриваться удобный отвод пузырьков газа из рабочего пространства для уменьшения степени газонаполнения электролита.
Некоторые их данных требований взаимно противоречат друг другу.
Иногда приходится усложнять конструкцию электролизёра из за стремления максимально развить рабочую поверхность.
По способу подключения электродов аппараты различают монополярные и биполярные электролизёры (МПЭ и БПЭ соответственно). В первом случае электролитические ячейки соединены параллельно с монополярными электродами(подключенные непосредственно к внешней электрической цепи) а во втором – последовательно с биполярными электродами (включёнными в цепь через проводники второго рода).
При одинаковой производительности разница будет в том что у МПЭ будет большая токовая нагрузка и низкое напряжение на клеммах а у БПЭ наоборот – низкая токовая нагрузки и высокое напряжение.
Для разделения водорода и кислорода обычно используют диафрагмы. Она в
процессе электролиза должна устранять попадание газовых пузырьков из одного электродного пространства в другое. Диафрагма должна иметь малое сопротивление прохождение тока. Поскольку материал диафрагмы не принимает участия в прохождении тока её сопротивление определяется сопротивлением электролита. Материал иметь хорошую смачиваемость иначе
может происходить накопление пузырьков в порах что ухудшает проводимость. Похожий эффект наблюдается при набухании диафрагмы и выделение на поверхности большого количества осадков.
Разделяют диафрагмы на:
погружённые (непроточные);
фильтрующие (проточные);
ионообменные (мембраны).
Погруженная диафрагмы просто разделяет продукты электролиза при этом уровни католита и анолита одинаковы а питание катодного и анодного пространств раздельно. Фильтрующая диафрагма разделяет продукты а также обеспечивает направленный поток электролита из анодного пространства в катодное либо наоборот. Ионообменные по своей сути непроточны ток в них переносится определёнными ионами.
Конструкции современных электролизёров компактны. Существуют компании которыми уже были проведены испытания и налажено серийное производство электролизёров степень превращения воды в которых достигает 99% а выход по току – 70%. Например в линейке электролизёров одной бельгийской компании на производство 1 водорода расходуется обычно 42 кВт-час электроэнергии а энергопотребление в масштабах всей установки не превышает 48 кВт-час. Обе эти цифры характеризуют установки с максимальным током через модуль 440 А.
Для электролиза воды обычно используют аппараты с биполярными электродами. Исходя из задания остановимся на электролизёре типа «Демаг» так как он рассчитан на небольшое производство (от 0.05 до 380 в зависимости от модификации) и имеет небольшие размеры. В одноблочной конструкции количество электролитических ячеек достигает 50 а в двухблочной – 100.
В приложении 2 представлен одноблочный биполярный электролизёр типа «Демаг».
Вода с раствором щёлочи поступает в блок электролитических ячеек где происходит разложение раствора электролита под действием электрического тока. Оттуда газы сборник-холодильник где очищаются от брызг воды охлаждаются затем разделяются на диафрагме и отправляются по газопроводу на дальнейшую очистку а вода возвращается в ячейки [7].
ТЕХНОЛОГИЧЕСКИЕ И КОНСТРУКТИВНЫНЫЕ РАСЧЁТЫ
1. Материальный баланс электролизёра
В основу любого технологического расчёта лежат 2 закона:
закон сохранения массы;
закон сохранения энергии.
На первом базируется материальный расчёт. Закон заключается в том что во всякой замкнутой системе масса вещества остаётся неизменной независимо от того какие изменения происходят с веществом. Для расчёта материального баланса какого-либо производства принимают следующую формулировку: масса исходных продуктов процесса должна быть равна массе его конечных продуктов.
Производительность = 200 тонн в год
Степень превращения = 095
Схема материальных потоков:
Запишем уравнение реакции:
Переведём производительность из тоннгод в м3час
=== 22254367 м3г = 25405 м3час
Где кг м3– плотность H2
Рассчитаем объём получающихся газов:
По уравнению (2.1) видно следовательно:
Рассчитаем массу получающихся газов:
Согласно закону сохранения массы необходимо воды для получения данного количества газов:
Рассчитываем общую массу воды в аппарате:
Масса непрореагировавшей воды:
Определим общий объём а также объём непрореагировавшей воды:
Составляем конечную таблицу материального баланса:
Материальный баланс электролизёра (расчёт на 1 час)
2. Тепловой баланс электролизёра
Данные теплового баланса используют при проектировании и эксплуатации химических производств. На его основе определяются энергетические затраты (расход теплоносителя или количество получаемого пара) рассчитываются поверхности охлаждающих и греющих элементов подбирается оптимальный режим процесса. Тепловой баланс отражает закон сохранения энергии согласно которому сумма всех видов энергии постоянна в замкнутой системе. Так как теплота – вид энергии то применительно к тепловому балансу закон можно сформулировать так: приход вносимое веществами в аппарат должно быть равно расходу тепла в том же аппарате то есть =
Температура поступающей воды = 20
Температура аппарата = 60
Температура выходящих веществ = 60
Термодинамические свойства веществ
Коэффициенты уравнения Cp=f(T)
Составим уравнение материального баланса:
(если реакция экзотермическая);
(если реакция эндотермическая);
потери на нагрев оборудования и в окружающую среду (если присутствуют).
Переводим температуры из в К:
Рассчитываем мольную теплоемкость входящей воды:
Переводим мольную теплоемкость в объёмную:
Определяем тепло вносимое входящими веществами:
Теплосодержание входящих веществ:
Определяем тепловой эффект при стандартных условиях:
Так как значение>0 делаем вывод о том что реакция является эндотермической
Рассчитываем коэффициенты необходимые для решения уравнения Кирхгофа:
Определяем тепловой эффект реакции при 333 К по уравнению Кирхгофа:
Определяем количество тепла выделившегося в ходе реакции:
Так как реакция эндотермическая в уравнении теплового будет использоваться слагаемое и значение с положительным знаком будет
заноситься в статью расхода тепла.
Находим количество теплоты отнесённое к 1 килограмму воды
Так как вода реагирует не вся с учётом этого теплота реакции будет равна:
Рассчитываем мольные теплоемкости выходящих веществ:
Переводим мольную теплоемкость в удельную:
Определяем тепло уносимое выходящими веществами:
Теплосодержание выходящих веществ:
Расходуемое тепло составляет:
Так как расходуемое тепло больше чем вносимое необходимо подводить тепло извне. Рассчитываем количество подведённой теплоты:
Так как > принимают значение =0
Составим конечную таблицу теплового баланса:
Тепловой баланс электролизёра
Q1 – тепло вносимое веществами
Q4 – тепло уносимое веществами
Q3 – тепло необходимое на подогрев
Q5 – теплота эндотермической реакции
3. Расчёт основных параметров аппарата
Размер выбранного аппарата будет зависеть от размеров блока электролитических ячеек. Эти значения одинаковы исходя из конструкции аппарата. В аппарат поступает вода в объёме V=20287 л. Для стабильной работы необходимо чтобы около 10% объёма оставалось свободными. Исходя из этого примем объём сборника равным Vсб=230л=230 дм3
По конструкции блок имеет круглое сечение малую высоту и ширину и большое значение длины.
Так как блок имеет в сечении круг значение высоты будет совпадать со значением ширины и будет равно радиусу сечения. Объём аппарата в таком случае можно будет рассчитать по формуле:
где r – радиус сечения а – длина аппарата.
Отсюда можно найти радиус:
Примем длину аппарата a=1м=10дм. Тогда подставив известные значения получим:
Размеры сборника составляют:
Длина a =10 дм = 1 м;
Ширина b = 3.34 дм = 027 м
Высота h = 3.34 дм = 027 м
В данной выпускной квалификационной работе был проведён аналитический обзор используемых способов получения водорода. На основе задания был выбран подходящий – электрохимический способ. Были разобраны теоретические основы процесса электролиза воды с получением водорода рассмотрены такие важные части производства как подготовка сырья автоматизация процесса аналитический контроль продуктов.
Во второй части выпускной квалификационной работы были произведены расчёты материального и теплового балансов основного аппарата производства – электролизёра а также расчёт конструктивных размеров.
Волков A.М. Большой химический справочник Волков A.М. Жарский И.M. — М.: Современная школа 2005. -
Химическая технология неорганических веществ. Подготовка сырья. Курс лекций. Т.М. Шевченко. — Кемерово: Кузбассвузиздат 2012. -
Кондауров Б.П. Общая химическая технология Кондауров Б.П. Александров В.И. Артемов А.В – М.: Академия 2005. - 586 с
Производство водорода в нефтеперерабатывающей промышленности М.К Письмен — М: Химия 1976. -
Якименко Л.Н. Получение водорода кислорода хлора и щелочей. Л.Н. Якименко — Москва Химия 1981. -
Радченко Р.В. Водород в энергетике. Учебное пособие. Радченко Р.В. Мокрушин А.С. В.В. Тюльпа - Екатеринбург: Издательство Уральского университета 2014. - с 229
Оборудование электрохимических производств. Учебное пособие. Истомина Н.В. Сосновская Н.Г. Ковалюк Е.Н – Ангарск: АГТА 2010
Руководство по монтажу и эксплуатации системы HySTАТ-А. – Ойвел(Бельгия) 2007г. – 242 с.
Пожаровзрывоопасность веществ и материалов и средства их тушения. Справочник: в 2-х частях. Часть 1. Корольченко А. Я. Корольченко Д. А— М.: Ассоциация «Пожнаука» 2004.
ГОСТ 3022-80. Водород технический. Технические условия. - Москва: Изд-во стандартов 1980 с 27
ГОСТ 5583-78. Кислород газообразный технический и медицинский. Технические условия. - Москва: Изд-во стандартов 1978 с 14
Электролизёр (1).dwg

Электролизная ячейка
Раствор гидроксида калия
Сборник-холодильник газа
Разделительная стенка
Техническая характеристика
Рабочее давление в аппарате 1
3кгссм² 2. Рабочая температура среды: в электролизных ячейчках 60°С 3. Среда: вода раствор гидроксида калия 30% кислород водород взрывоопасная
коррозионная 4. Геометрическая емкость 0
м³ 5. Температура стенки 70°С 6. Группа аппарата ОСТ 26-291-71
Производство водорода
Электролизёр марки "Демаг"
Водород ТС.dwg

Условное обозначение
Наименование среды в трубопроводе
Раствор гидроксида калия
Технический кислород
Технологическая схема
Барабан с гидроксидом калия
Сборник раствора гидроксида калия
Фильтр для очистки воды
Ионообменная колонна
Фильтр для очистки газов от щёлочи
Аппарат для каталитической очистки
Аппарат для дожигания примесей
Клапанной регулятор давления газов
Разделительная колонна
Вода деминерализованная
Рекомендуемые чертежи
Свободное скачивание на сегодня
Обновление через: 41 минуту
Другие проекты
- 09.07.2014