Производство керамического кирпича методом жесткой экструзии объемом 30 млн. шт. в год


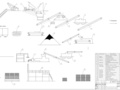
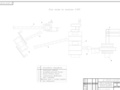
- Добавлен: 24.01.2023
- Размер: 315 KB
- Закачек: 0
Узнать, как скачать этот материал
Подписаться на ежедневные обновления каталога:
Описание
Производство керамического кирпича методом жесткой экструзии объемом 30 млн. шт. в год
Состав проекта
![]() |
![]() ![]() ![]() |
![]() ![]() ![]() ![]() |
![]() ![]() ![]() ![]() |
Дополнительная информация
Контент чертежей
нулевой.dwg

техносхема1.dwg

Рекомендуемые чертежи
- 30.03.2024
- 18.02.2014
Свободное скачивание на сегодня
Обновление через: 9 часов 50 минут
Другие проекты
- 23.08.2014