Профилирование кулачкового механизма, Расчет эвольвентного зацепления


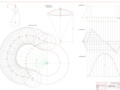
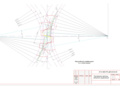
- Добавлен: 24.01.2023
- Размер: 310 KB
- Закачек: 0
Описание
Состав проекта
![]() |
![]() |
![]() |
![]() ![]() ![]() ![]() |
![]() ![]() ![]() |
![]() |
![]() ![]() ![]() |
![]() |
![]() ![]() ![]() ![]() |
![]() |
Дополнительная информация
Эвольвентное зацепление (на печать).dwg

-К-389.ПТС.ДМ.03.03.03
Масштабный коэффициент Кl = 0
Расчет геометрических параметров зубчатого зацепления.doc
В прямозубой передаче без смещения по принятому делительному модулю m и числу зубьев шестерни z1 и колеса z 2 определяем их основные размеры.
исходные данные: m=95мм; z1=25; z2=22.
Диаметры начальных окружностей:
dw1=9525=2375мм ; dw2=9522=209мм
Диаметр основных окружностей:
На профиле есть единственная точка для которой угол профиля равен углу режущего инструмента. По ГОСТ 13754-81 профильный угол инструмента a=20°.
db1=2375 094=22325мм;
Диаметр вершин зубьев:
Диаметр впадин зубьев:
df=95(25-25)=21375мм;
df=95(22-25)=18525мм
Окружной шаг по начальной окружности
рwt= рt =р=31495=2983мм.
Окружная толщина зуба по начальной окружности:
swt= s t =s=29832=1491 мм
Окружная ширина впадин зубьев по начальной окружности:
Межосевое расстояние:
aw=а=0595(25+22)=22325мм
построение картины зацепления
Для наглядности профилей зубьев выбираем масштаб построения так чтобы высота зуба h на чертеже была не менее 30÷50 мм. Масштабный коэффициент определим по формуле:
kl =h(30÷50)=2.25·m40=2.25·9.540=0.534 мммм.
Поделив на kl все основные размеры определяем их значения в масштабе (по этим данным строится картина зацепления):
dw1= 237.50.534=444.7мм
dw2= 2090.534=391.3мм
db1=223.250.534=418мм
db2=196.460.534=367.9мм
da=256.50.534=480.3мм
da2=2280.534=426.9мм
df=213.750.534=400.2мм
df2=185.250.534=346.9мм
s=е=14.910.534=279мм
aw=223.250.534=418мм
Из центров О1 и О2 удаленных друг от друга на величину аw=418 мм проводим начальные окружности касающиеся в точке W (полюсе зацепления).
Через точку W проводим общую касательную к начальным окружностям ТТ и под углом α=20º проводим линию NN.
Из центров О1 и О2 опускаем перпендикуляры на линию NN (rb1 и rb2) и проводим этими радиусами основные окружности (db1 db2). Линия NN является нормалью к профилям зубьев ее также называют линией зацепления.
Строим эвольвенты которые описывает точка W прямой при перекатывании ее по основным окружностям.
Для построения первой эвольвенты делим отрезок N1W на равные части длиной 15÷20мм каждый ( и т.д.). За точкой N1 также откладываем несколько таких отрезков. Основную окружность делим начиная с т. N1 на столько частей на сколько разделена линия зацепления. Приближенно считая длину дуги равной длине отрезка из точки N1 раствором циркуля делаем засечку на основной окружности получаем точку 3. Из точки 3этим же раствором - 2. Также получают остальные точки .
Через точки 1; 2; 3 и т.д. проводим касательные к основной окружности (они радиусам О11; О12; О13 и т.д.) и на них откладывают отрезки 1’1” 2’2” 3’3” соответственно равные отрезкам 1W 2W 3W .
Соединяя точки 1 2 3 и т.д. плавной кривой получаем эвольвенту для первого колеса.
Начиная с деления отрезка N2W на равные части подобным образом строим эвольвенту для второго зубчатого колеса.
Строим окружности вершин. Точки пересечения с эвольвентами определяют крайние точки головок зубьев А1 А2 см. рисунок 8.
Строим окружности впадин колес. Построение профиля ножки зуба:
В нашем случае dfdb поэтому от основания эвольвенты проводим радиальный отрезок (радиус основной окружности) а затем у основания зуба делаем закругление R=025 m.
R=025 · m=025 · 95 = 24 (2.5 мм)
От точки W вправо и влево по начальным окружностям откладываем окружную толщину зуба S. Поделив S пополам и соединив эти точки с центрами О1 и О2 получаем оси симметрии зубьев. Из точки О1 через построенную часть зуба проводим ряд окружностей произвольного радиуса и относительно оси симметрии достраиваем вторую половину зуба.
Оси симметрии зубьев отстоят друг от друга на угол α:
Из точки О1 проводим дугу радиусом О1n1 до пересечения с профилем шестерни в точке В1.
Из точки О2 проводят дугу радиусом О2n2 до пересечения с профилем колеса в точке В2. Активные профили зубьев А1В1 и А2В2 не равны т.к. зубья перекатываются со скольжением
Коэффициент перекрытия
Одним из качественных показателей зацепления является коэффициент перекрытия – отношение дуги зацепления к шагу р.
Первый способ нахождения графический:
α-угол зацепления равный 20 для передачи без смещения
-длина активной части линии зацепления мм. (определяется графическим путем и равна 8409 мм).
Второй способ аналитический:
Расхождение результатов не должно превышать 5%. В нашем случае результаты нахождения коэффициента перекрытия графическим и аналитическим способами – совпали.
Кулачковый механизм.doc
Данные для расчета:
Отношение ускорения:
Максимальный ход толкателя hт =12мм (0012м)
Фазовые углы поворота кулачка:
Допустимый угол давления:
Отложим углы подьема φп верхнего выстоя φвв и опускания φо на оси абсцисс.
Рассчитаем масштабный коэффициент оси абсцисс:
Рассчитаем ординаты диаграмм (а1 а2). Сравним углы удаления и возврата; в нашем случае они равны поэтому график будет симметричный.
Рассчитаем полюсное расстояние:
Проинтегрируем графически диаграмму ускорения (φ) по правилам интегрирования чтобы получить график скорости (φ). Полученную ломаную превращаем в плавную кривую. Затем интегрируем график скорости (φ) и получаем диаграмму перемещений S(φ)
Рассчитаем масштабный коэффициент диаграмм:
Определение минимального радиуса профиля кулачка r0.
Для этого строим диаграмму S методом исключения угла поворота кулачка. Масштабы по осям координат должны быть одинаковыми.
По оси ординат откладываем положения S центра ролика согласно диаграмме перемещений а по оси абсцисс откладываем величины взятые из графика скоростей предварительно повернув их на 90° в сторону вращения кулачка. К диаграмме проведем две касательные справа и слева под заданным допустимым углом давления .
Найдем точку их пересечения O. Приняв эту точку за центр вращения кулачка получим наименьший радиус теоретического (центрового) профиля кулачка при котором угол давления не выходит за допустимые пределы.
Построение теоретического и рабочего профиля кулачковой шайбы.
Проводим окружность rо=0139м в масштабе:
Построение ведем в положении начала подъема толкателя используя метод обращения движения:
а) Ряд последовательных положений 1 2 3 4 и т. д. переносим с диаграммы перемещения в масштабе:
б) Делим окружность радиуса r0 на части пропорциональные углам φо
φвв φп отсчитываем от радиуса ОA0 в направлении обратном вращению
кулачка( так как угол φп = φо в целях экономии места на чертеже отсчитываем в сторону вращения кулачка).
в) Дуги окружности г0 соответствующие углам φо и φп делим на 7
г) Для построения теоретического профиля кулачка из центра О через
точки 123 и т.д. проводим дуги до пересечения с соответствующими делениями углов φо φп и φвв
д) Соединяя последовательно найденные точки пересечения получим
теоретический профиль.
е) Теоретический профиль на участке φнв очерчивается дугой
окружности с центром в точке О.
Определение радиуса ролика проводим методом проб т. е. находим участок с наибольшей кривизной и описываем круг кривизны с радиусом ρmin. Радиус ролика определяется так:
Из этих двух величин берем наименьшую. Последнее условие связано с прочностью кулачка.
Для построения конструктивного (рабочего) профиля кулачка из произвольных точек центрового профиля проводим окружности радиусом rрол и строим их огибающую.
Кулачки (на печать).dwg

Рекомендуемые чертежи
- 24.01.2023
- 19.05.2023