Проектирование зерноочистительного и размольного отделений мукомольного завода по производству хлебопекарной пшеничной муки с развитой схемой технологического процесса



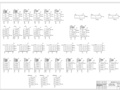
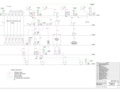
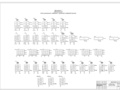
- Добавлен: 24.01.2023
- Размер: 868 KB
- Закачек: 2
Описание
Состав проекта
![]() |
![]() ![]() ![]() |
![]() ![]() ![]() |
![]() ![]() ![]() |
![]() ![]() ![]() |
![]() ![]() ![]() |
![]() ![]() ![]() |
![]() ![]() ![]() |
![]() ![]() ![]() |
![]() ![]() ![]() |
![]() ![]() ![]() |
![]() ![]() ![]() |
![]() ![]() ![]() |
![]() |
![]() ![]() ![]() ![]() |
![]() ![]() ![]() ![]() |
![]() ![]() ![]() ![]() |
Дополнительная информация
Введение.docx
В Казахстане в настоящее время активно наращивается экспорт муки на внешние рынки. За последние годы объём экспорта муки из страны вырос в 2 раза. Необходимо отметить что в общем объеме экспорта продуктов переработки сельхозпродукции в Казахстане мука занимает около 80% общего объёма. Доля Казахстана в общем мировом экспорте муки составляет более 14%.
Современный мировой рынок муки имеет свои сложившиеся за годы деятельности характерные особенности определяющих данный рынок на практике «жестким». Важной характерной чертой мирового рынка муки является его ограниченный объём – не более 10 млн. тонн но в последние годы наблюдается тенденция к его увеличению до 11 млн. тонн. Это связано прежде всего с резким повышением цен на пшеницу что стимулирует спрос на муку. Следующей особенностью рынка является небольшое количество крупнейших стран экспортеров пшеничной муки оперирующих на данном рынке. Среди них можно отметить такие страны как Франция Бельгия Германия Италия США Казахстан Турция и другие.
Устойчивая позиция Казахстана на мировом рынке муки обеспечивается благодаря особым хлебопекарным свойствам казахстанской муки производимой из отечественной пшеницы хорошо известной в странах ближнего и дальнего зарубежья своим высоким качеством. Это позволяет казахстанской муке быть конкурентоспособной на мировом рынке и обеспечивать хорошие рынки сбыта в различных странах мира. Высокая конкурентоспособность казахстанской муки на внешних рынках подтверждается Индексом Конкурентных преимуществ оценивающего конкурентоспособность товара на внешних рынках который сложился по муке на уровне 75 единиц согласно Концепции по улучшению имиджа сельхозпродукции Казахстана подготовленной в рамках проекта Всемирного Банка и Министерства сельского хозяйства РК «Повышение конкурентоспособности сельскохозяйственной продукции в Казахстане» [1].
читать.docx
В Казахстане в настоящее время активно наращивается экспорт муки на внешние рынки. За последние годы объём экспорта муки из страны вырос в 2 раза. Необходимо отметить что в общем объеме экспорта продуктов переработки сельхозпродукции в Казахстане мука занимает около 80% общего объёма. Доля Казахстана в общем мировом экспорте муки составляет более 14%.
Современный мировой рынок муки имеет свои сложившиеся за годы деятельности характерные особенности определяющих данный рынок на практике «жестким». Важной характерной чертой мирового рынка муки является его ограниченный объём – не более 10 млн. тонн но в последние годы наблюдается тенденция к его увеличению до 11 млн. тонн. Это связано прежде всего с резким повышением цен на пшеницу что стимулирует спрос на муку. Следующей особенностью рынка является небольшое количество крупнейших стран экспортеров пшеничной муки оперирующих на данном рынке. Среди них можно отметить такие страны как Франция Бельгия Германия Италия США Казахстан Турция и другие.
Устойчивая позиция Казахстана на мировом рынке муки обеспечивается благодаря особым хлебопекарным свойствам казахстанской муки производимой из отечественной пшеницы хорошо известной в странах ближнего и дальнего зарубежья своим высоким качеством.
Особенности перерабатываемой культуры
1 Анатомическое строение зерна пшеницы
Зерно пшеницы состоит из нескольких анатомических частей – оболочек эндосперма и зародыша и др. которые характеризуются различными физиологическими функциями и в связи с этим имеют разное строение и химический состав.
3 – плодовые оболочки; 456 – семенные оболочки; 7 – алейроновый слой; 8 – слои клеток плодовой оболочки пшеницы с поверхности; 9 – эндосперм; 10 – щиток; 11 – почечка; 12 – осевая часть зародыша; 13 – корешок;
Рисунок 1. Продольный разрез зерна пшеницы
Соотношение анатомических частей зерна пшеницы
Около 45 массы зерновки составляет эндосперм. Это характерно для большинства злаков – пшеницы ржи овса ячменя и др. Соотношение других частей колеблется в зависимости от ряда факторов. Например содержание оболочек зерновки ржи выше чем у пшеницы а у твердой пшеницы выше чем у мягкой.
Зерно пшеницы имеет сложный химический состав. Оболочки состоящие в основном из неусвояемых человеческим организмом веществ не имеют пищевой ценности. Для изготовления сортовой муки используются не все части зерновки а преимущественно эндосперм и небольшой процент измельченных периферийных частей зерна – алейронового слоя и оболочек. Зародыш содержит много полноценных белковых веществ жиров углеводов а также витаминов но при сортовых помолах муки зародыш удаляется.
Эндосперм – источник белков и крахмала. Из злаковых культур наиболее богато белками зерно пшеницы 11-18%. Белковые вещества в зерне пшеницы и муке образуют клейковину.
Химический состав зерна пшеницы
В технологическом процессе при переработке зерна учитывают разную пищевую ценность частей зерна и используя различные свойства этих частей при сортовых помолах формируют сорта муки объединяя потоки муки с разных систем в тот или иной сорт.
2 Технологические свойства зерна пшеницы
Технологические свойства сырья на мукомольных заводах определяются следующими основными показателями: выходом готовой продукции суммарно и по сортам; качеством готовой продукции; удельными эксплуатационными расходами. На технологические свойства зерна оказывает влияние комплекс их физико-химических структурно-механических теплофизических биохимических свойств которые изменяются под воздействием гидротермической обработки.
Натура и масса 1000 зерен. Натура - это масса одного литра зерна в граммах. До середины 19 века натура зерна была единственным показателем качества. В настоящее время показатель натуры широко применяется в международной торговле зерном.
На показатель натуры влияет много параметров: размеры форма масса 1000 зерен выравненность по крупности влажность засоренность плотность и т.д. Именно поэтому один показатель натуры не может служить признаком определяющим мукомольные достоинства зерна. Однако в совокупности с другими показателями натура остается важным показателем качества зерна.1000 зерен более строго чем натура отражает его крупность и относительное содержание оболочек зародыша и эндосперма.
Если масса 1000 зерен основного зерна достаточно отличается от массы 1000 зерен засорителей то эта разница используется для очистки зерна на инерционных очистителях и на пневмосепараторах. Показатель массы 1000 частиц промежуточных продуктов помола в совокупности с их размерами можно использовать при определении нагрузок на вальцовые станки.
Зольность. Следует также отметить что несмотря на большой диапазон зольности зерна и его составных частей для разных партий пшеницы технологу необходимо получить муку с зольностью не выше нормы.
Стекловидность. Стекловидность характеризует структурно-механические свойства эндосперма поэтому этот показатель определяет режимы гидротермической обработки зерна и режимы первых систем сортового помола.
Влажность. Исходная влажность зерна как сырья для мукомольного завода должна интересовать технолога в той мере насколько она позволяет ему управлять мукомольными свойствами зерна при гидротермической обработке. Если влажность зерна поступающего на мельзавод с элеватора низкая (до 125 135%) то у технолога больше возможностей улучшить мукомольные свойства зерна при помощи двух - трехкратной гидротермической обработки. Если же влажность зерна высокая (больше 145%) то у технолога остается единственная возможность увлажнить его только перед размолом.
3 Мукомольные свойства зерна пшеницы
Качество зерна поступающего на переработку в муку оценивают по следующим показателям:
Обязательным общим – характеризуют свежесть или здоровье зерна и его состояние. По этим показателям судят о стойкости зерна при хранении возможности его использования необходимости и режимах обработки. Их определяют в зерне независимо от целевого назначения;
Обязательным специфическим – характеризуют технологические достоинства зерна. Это типовой состав натура крупность и выравненность стекловидность количество и качество клейковины зольность и другие;
Дополнительным – определяемым в случае необходимости или по особому указанию (прочность полный химический состав или содержание отдельных веществ например белков активность ферментов количественный и качественный состав микрофлоры остаточное содержание фумигантов в зерне).
Все методы определения показателей качества зерна стандартизированы. Качество зерна определяют в лабораторных условиях органолептически или с применением различных приборов и устройств.
Органолептически определяется цвет запах и вкус зерна. Эти показатели характеризуют его свежесть и по ним можно судить о состоянии зерна его стойкости при хранении и т.д.
В лабораторных условиях с применением приборов определяют зольность влажность засоренность выравненность стекловидность натуру массу 1000 зерен плотность зараженность вредителями хлебных запасов количество и качество клейковины и др.
Известно 27 видов пшеницы самым распространенным является мягкая. Самой лучшей яровой мягкой пшеницей является Саратовская 29. К сортам сильной пшеницы относится Целинная 20 Новосибирская 67 Уральская 52.
Твердая пшеница является преимущественно яровой – харьковская 46.
Мягкую пшеницу по качеству получаемой муки содержанию белка клейковины и по хлебопекарным свойствам подразделяют на 3 группы: сильная слабая средняя.
Сильной является пшеница с натурой не ниже 730-755 гл в зависимости от района произрастания со стекловидностью не менее 60% и сырой клейковиной 28%. Сильная пшеница дает муку образующую тесто с хорошей упругостью с высокой устойчивостью способное удержать длительное брожение. Хлеб из сильной муки получается хорошей формы с равномерной сильно-развитой пористостью большого объема.
Слабая пшеница имеет стекловидность не менее 40% клейковина 20% группа клейковины 23. Такая пшеница дает муку образующее липкое вяжущее тесто из которого хлеб получается малого объема расплывшейся формы с плохо разрыхленным мякишем. Слабая пшеница самостоятельно не используется.
Средняя по силе пшеница не может улучшать слабую пшеницу но при самостоятельном использовании дает стандартный по качеству хлеб.
Твердая пшеница используется для выработки макаронной муки т.к. она обладает клейковиной с высокой упругостью но малой растяжимостью что позволяет хорошо сохранить приданную макаронным изделиям форму.
Стандартами пшеница заготовляемая и распределяемая подразделяется на 5 типов в зависимости от вида и времени выращивания: яровая краснозерная яровая дурум яровая белозерная озимая краснозерная озимая белозерная.
По стекловидности и оттенку зерна 1 и 4 типов подразделяются на 5 подтипов. 2 и 3 типы делятся на 2 подтипа 5 тип на подтипы не делят. С принадлежностью зерна к тому или иному типу и подтипу связаны хлебопекарные свойства пшеницы 1 и 4 типа является сильной 5 тип – слабая пшеница.
Пшеница заготовляемая по качеству может быть базисных и ограничительных кондиций.
4 Характеристика поступающего сырья на переработку
Показатели качества зерна пшеницы при определении расчетных выходов продукции [7]:
зольность зерна (очищенного от сорной примеси) – 185% при сортовых помолах;
содержание сорной примеси – 1% в том числе вредной – 01%;
содержание зерновой примеси – 1%;
натура при сортовых помолах – 775 гл;
общая стекловидность при сортовых помолах – 50%;
Технологическая часть. Подготовительное отделение мукомольного завода
В подготовительном отделении мукомольного завода качество зерна и его технологические свойства должны быть улучшены. Достигается это очисткой зерновой массы от примесей обработкой поверхности зерна в обоечных и щеточных машинах мойкой и гидротермической обработкой. Важно также чтобы была стабилизация технологических свойств зерна на оптимальном уровне в течение возможно более длительного времени. Для этого необходимы определенный режим гидротермической обработки (ГТО) и рациональный подбор состава помольной смеси.
Как правило подготовку отдельных компонентов помольной смеси различающихся показателями качества и свойствами ведут раздельно смешивая их только после завершения ГТО. Если мелкая фракция зерна не выделена в элеваторе то организуют ее отбор в подготовительном отделении. Предварительное шелушение зерна при многосортных помолах не применяют так как удаление плодовых оболочек приводит к более интенсивному измельчению семенных оболочек и алейронового слоя частицы которых засоряют муку.
При поступлении в размольное отделение зерно должно иметь следующие показатели качества: влажность на оптимальном уровне т. е. в пределах 150 165%;содержание сорной примеси не более 04% в том числе вредной не более 005%; минеральная примесь не допускается;содержание зерновой примеси (ржи и ячменя в пшенице) не более 4%; содержание сырой клейковины для пшеницы при сортовых помолах не менее 26% [4].
1 Выбор и обоснование схемы подготовительного отделения мукомольного завода
Схема подготовки зерна к помолу была разработана на основе типовых схем и последовательности операций [3]. Главной особенностью разработанной схемы является применение новых технологий ГТО [3].
При сортовом помоле зерна отделить частицы оболочек от эндосперма чрезвычайно трудно поскольку их структурно – механические свойства отличаются незначительно. При помощи гидротермической обработки стремятся усилить различие свойств оболочек и эндосперма. Кроме того комплекс мероприятий по воздействию на зерно теплом и водой позволяет улучшить биохимические свойства и в конечном итоге хлебопекарные качества муки.
На современных мукомольных предприятиях применяют в основном два метода гидротермической обработки: холодное и скоростное кондиционирование.
Холодные способы ГТО применяют при подготовке мягкой пшеницы и ржи к хлебопекарным сортовым и обойным помолам при подготовке твердой и высокостекловидной пшеницы к макаронным помолам а также при подготовке пшеницы к переработке в крупу.
Холодное кондиционирование состоит в увлажнении зерна и последующей выдержке его (отволаживании) в бункерах. Название метода обусловлено тем что его проводят без подогрева зерна. При скоростном кондиционировании зерно обрабатывают паром а затем моют в холодной воде. Благодаря такому воздействию свойства зерна изменяются быстрее и необходимая продолжительность отволаживания сокращается.
Общим для обоих методов ГТО является обязательное доувлажнение зерна на 03 05% и отволаживание его в течение 20 40 мин перед подачей в измельчающую машину (вальцовый станок I драной системы). Это необходимо для увлажнения поверхностных слоев зерна (оболочек и алейронового слоя). В результате их прочность резко повышается они плохо измельчаются образуя крупные частицы отрубей. Последние легко отделяются на ситах.
При холодном кондиционировании зерно обрабатывают в моечной машине или мокром шелушителе дополнительно увлажняют отволаживают. При высокой стекловидности рекомендуется двукратное увлажнение и отволаживание. Это необходимая последовательность этапов данного метода ГТО.
При скоростном кондиционировании после кратковременного (20 40°С) пропаривания в аппарате типа АСК нагретое зерно выдерживают в теплоизолированном бункере. Затем его моют холодной водой обрабатывают во влагоснимателе доувлажняют и отволаживают. Скоростной метод гидротермической обработки наиболее эффективен для пшеницы со слабой клейковиной и для мукомольных заводов с ограниченной вместимостью емкостей для отволаживания. Благодаря тепловому воздействию при пропаривании а также подогреву зерна во влагоснимателе интенсифицируется влагоперенос и процесс разрыхления эндосперма.
Важную роль играет правильная организация отволаживания зерна в бункерах. Если в днище бункера только одно выпускное отверстие то вследствие особенностей истечения сыпучих материалов выходящее зерно будет неоднородным по технологическим свойствам. Мукомольные заводы переведены на непрерывное (поточное) отволаживание. Бункера разгружают и загружают не периодически а непрерывно и зерно в них постоянно перемещается сверху вниз. Для того чтобы свойства зерна оставались стабильными в днище бункера делают отверстия (примерно по одному на 06 10 м2 сечения бункера). Продолжительность отволаживания регулируют скоростью движения зерна в бункере.
Наивысшей технологической эффективности достигают при раздельной подготовке каждого из компонентов помольной смеси. Например при раздельной подготовке зерна пшеницы методом холодного кондиционирования при трехсортном помоле общий выход муки составил 794% средневзвешенная зольность — 077%. При совместной подготовке этого зерна выход муки снизился до 786% а зольность увеличилась до 084%. Более чем на 11% повысился и удельный расход энергии на помол. Выход муки высоких сортов уменьшился на 26%. Результаты заметно повышаются если применяют двукратное увлажнение — отволаживание зерна.
На ряду с этими способами ГТО существуют и такой как горячее кондиционирование.
Метод горячего кондиционирования рекомендуется использовать для сортовых помолов пшеницы. В настоящее время метод находит ограниченное применение из-за высокой стоимости аппаратуры и оборудования а также тепловой энергии [6].
В результате ГТО в зерне развиваются сложные физико-химические коллоидные и биохимические процессы которые вызывают изменение технологических свойств зерна – разрыхление эндосперма образование микротрещин оболочки становятся более эластичными.
Длительность отволаживания во многом зависит от исходной влажности твердозёрности и стекловидности зерна. Например высокостекловидное зерно отволаживается в два этапа в течение более 48 ч.
Длительность времени отволаживания необходимость большого количества оперативных бункеров которые занимают большой объем производственных помещений и нуждаются в транспортных линиях связывающих гидротермическую обработку зерна с технологическим процессом – все эти факторы значительно усложняют эксплуатацию мельницы и повышают себестоимость готовой продукции.
Для оптимизации гидротермической обработки зерна а также для увеличения производственной мощности мельницы без дополнительных затрат на строительство бункеров для отволаживания в настоящее время существует вибрационный метод увлажнения зерна.
Немецкая компания ММW Technologie GmbH предлагает установку VIBRONET в которой осуществляется вибрационное увлажнение зерна.
Холодное кондиционирование зерна (традиционный метод увлажнения)
Вибрационное увлажнение зерна
Установка для увлажнения
Шнек интенсивного увлажнения А1-БШУ-2
Основные рабочие органы увлажняющей машины
Бичевой ротор индикатор наличия зерна система управления подачи воды
Камера смешивания зерна с водой вибрационная шахта система автоматизированного управления подачи воды
Производительность установки для увлажнения
Увлажняемые культуры
Пшеница рожь ячмень овёс кукуруза рис бобовые культуры
Длительность отволаживания
Увеличение влажности зерна
Расход электроэнергии
Количество этапов отволаживания
Как видно из таблицы вибрационное увлажнение зерна имеет несколько значительных преимуществ:
Сокращение времени отволаживания в 3-5 раз.
Зерно не подвергается механическому травмированию.
Значительная экономия электроэнергии.
Всего один этап ГТО и возможность добавления до 10-12% воды за один этап.
Возможность увеличить производственные мощности мельницы без дополнительных затрат на строительство бункеров для отволаживания.
Повышение общего выхода муки до 1%.
Вырабатывается гигиенически чистый продукт т.к. не увеличивается общее количество бактерий за счёт короткого времени отволаживания.
Простой монтаж установки VIBRONET даже при самых современных схемах размола.
Простой технический уход малый износ.
То есть благодаря современному методу вибрационного увлажнения зерна значительно снижается расход электроэнергии и несколько увеличивается общий выход готовой продукции. Таким образом принимаем к установке вибрационный увлажнитель который охарактеризовал себя как более практичный.
Рассказать схему подготовительного отделения.
4 Размольное отделение мукомольного завода
Сам процесс измельчения при сортовом помоле требует особой организации. Прежде всего при сортовом помоле его проводят в два приема. Вначале осуществляют достаточно грубое дробление зерна с целью измельчения (отбора) эндосперма в виде крупных промежуточных продуктов: крупок и дунстов. Затем проводят операции повышения их добротности – ситовеечный процесс. Полученные в результате этих операций чистые мелкие крупки и дунсты окончательно измельчаются в муку.
Конечно и на этапе первоначального дробления зерна получается некоторое количество муки но качество ее ниже чем при измельчении обогащенных продуктов. Основную массу муки получают на заключительном этапе помола – в размольном процессе.
Вымол сходовых продуктов в драном (др.) и размольном (р.) процессах производят на вымольных машинах раздельно или совместно.
Сита в рассевах и технологическую характеристику измельчающих вальцов подбирают исходя из типа помола. Подбор сит на ситовеечной машине зависит от характеристики поступающего на нее продукта – нижнего схода с рассевов I др.с. и II др.с.
5 Выбор и обоснование технологической схемы размольного отделения
Зерно из подготовительного отделения поступает на первую драную систему измельчается на вальцовом станке и поступает одну секцию рассева работающего по схеме 1. Сход с верхнего и второго сита направляется на вторую драную систему. Сход с последнего сита направляется на ситовеечную машину №1. Проход третьего сита (смесь муки дунстов и мелкой крупки) направляется на сортировочную машину №1 проход с последнего сита (средняя крупка) направляется на ситовеечную машину №2.
Вторая драная система. Сход с верхнего сита направляется на третью драную крупную систему со второго сита – на третью драную мелкую систему сход с последнего сита (крупная и средняя крупка) – на ситовеечную машину №3. Проход третьего сита (смесь муки дунстов и мелкой крупки) направляется на сортировочную систему №2 проход последнего сита (средняя крупка) – на ситовеечную систему №4.
Третья драная система крупная. Сход с верхнего сита направляется на первую бичевую машину. Сход со второго сита – на четвертую драную крупную систему сход с последнего сита –четвертую драную мелкую систему. Проход третьего сита (мука дунст) направляется на сортировочную систему №3 проход последнего сита (мелкая крупка) – ситовеечную систему №5.
Третья драная система мелкая. Сход с верхнего сита направляется на бичевую машину №1. Сход со второго сита – на четвертую драную крупную систему сход с последнего сита – четвертую драную мелкую систему. Проход третьего сита (мука дунст) направляется на сортировочную машину №3 проход последнего сита (мелкая крупка) – ситовеечную систему №5.
Четвертая драная система крупная. Сход с верхнего сита направляется на вторую бичевую машину. Сход со второго сита – на третью бичевую машину сход с последнего сита – на третью бичевую машину. Проход третьего сита (мука дунст) направляется на сортировочную систему №4 проход последнего сита (мука 1с) – на контроль муки первого сорта.
Четвертая драная система мелкая. Сход с верхнего сита направляется на вторую бичевую машину. Сход со второго сита – на третью бичевую машину сход с последнего сита – на третью бичевую машину. Проход третьего сита (мука дунст) направляется на сортировочную систему №4 проход последнего сита (мука 1с) – на контроль муки первого сорта.
Сортировочная система №1. Система работает по схеме №3. Сход с четвертой группы сит направляется на шестую ситовеечную систему. Проход первой второй третьей группы сит направляется на вторую размольную систему проход последнего сита – на седьмую ситовеечную систему.
Сортировочная система №2. Система работает по схеме №3. Сход с четвертой группы сит направляется на шестую ситовеечную систему. Проход первой второй группы сит – мука высшего сорта направляется на контроль муки проход третьей группы сит – на вторую размольную систему проход последнего сита – на седьмую ситовеечную систему.
Сортировочная система №3. Система работает по схеме №3. Сход с четвертой группы сит направляется на шестую ситовеечную систему. Проход первой второй группы сит направляется на контроль муки первого сорта проход с третьего сита – на третью размольную систему проход последнего сита – на седьмую ситовеечную систему.
Сортировочная система №4. Система работает по схеме №2. Сход с первой группы сит направляется на десятую размольную систему. Сход с четвертой группы сит направляется на седьмую размольную систему. Проход второй третьей группы сит направляется на контроль муки первого и второго сорта проход последнего сита – на пятую размольную систему.
Сортировочная система №5. Система работает по схеме №2. Сход с первой группы сит - отруби. Сход с четвертой группы сит направляется на одиннадцатую размольную систему. Проход второй третьей группы сит направляется на контроль муки второго сорта проход последнего сита – на девятую размольную систему.
Бичевая машина №1. Сход с нее направляется на четвертую драную систему крупную проход на сортировочную систему 4.
Бичевая машина №2. Сход с нее - отруби проход направляется на сортировочную систему №5.
Бичевая машина №3. Сход с нее - отруби проход направляется на сортировочную систему №5.
Шлифовочная система №1. Сход с первых сит направляется на четвертую драную мелкую сход со второй группы сит – на первую ситовеечную сход с последних сит – на вторую ситовеечную систему. Проходом с третьей группы сит выделяется мука высшего сорта а проход с последнего сита направляют на первую размольную систему.
Шлифовочная система №2. Сход с первых сит направляется на четвертую драную мелкую сход со второй группы сит – на третью ситовеечную систему сход с последних сит – на четвертую ситовеечную систему. Проходом с третьей группы сит выделяется мука высшего сорта а проход с последнего сита направляют на первую и вторую размольную систему.
Ситовеечная машина 1. Сход с первого и второго ярусов сит возвращается на третью драную систему мелкую сход третьего яруса сит – на первую шлифовочную систему проход последнего яруса сит – на первую шлифовочную и на первую размольную.
Ситовеечная машина 2. Сход с первого и второго ярусов сит возвращается на третью драную систему мелкую сход третьего яруса сит – на первую шлифовочную систему проход последнего яруса сит – на первую шлифовочную и на первую размольную а также возможно выделение манной крупы.
Ситовеечная машина 3. Сход с первого и второго ярусов сит возвращается на третью драную систему мелкую сход третьего яруса сит – на первую шлифовочную систему проход последнего яруса сит – на первую шлифовочную и на первую размольную.
Ситовеечная машина 4. Сход с первого и второго ярусов сит возвращается на четвертую драную систему мелкую сход третьего яруса сит – на четвертую размольную систему проход последнего яруса сит – на первую шлифовочную с выделением манной крупы.
Ситовеечная машина 5. Сход с первого и второго ярусов сит возвращается на четвертую драную систему мелкую сход третьего яруса сит – на четвертую размольную систему проход последнего яруса сит направляется на вторую шлифовочную и на четвертую размольную.
Ситовеечная машина 6. Сход с первого яруса сит направляется на седьмую размольную систему со второго яруса сит – на четвертую размольную сход третьего яруса сит – на вторую размольную систему проход последнего яруса сит – на вторую шлифовочную на первую и вторую размольную системы.
Ситовеечная машина 7. Сход с первого яруса сит направляется на седьмую размольную систему со второго и третьего ярусов сит – на пятую размольную проход последнего яруса сит направляется на вторую шлифовочную а также на первую и вторую размольную системы.
Первая размольная система. Сход с последнего сита направляется на четвертую размольную систему проход первого второго и третьего сит – на контроль муки высшего сорта проход последнего сита – на вторую размольную систему.
Вторая размольная система. Сход с последнего сита направляется на четвертую размольную систему проход первого второго и третьего сит – на контроль муки высшего сорта проход последнего сита – на третью размольную систему.
Третья размольная система. Сход с последнего сита направляется на четвертую размольную систему проход первого второго и третьего сит – на контроль муки высшего сорта проход четвертого сита – на пятую размольную систему.
Четвертая размольная система. Сход с последнего сита направляется на седьмую размольную систему проход первой второй группы сит – на контроль муки высшего сорта проход с третьей группы сит – на контроль муки первого сорта проход последнего сита – на пятую размольную систему.
Пятая размольная система. Сход с последнего сита направляется на седьмую размольную систему проход первой второй группы сит – на контроль муки высшего сорта проход с третьей группы сит – на контроль муки первого сорта проход последнего сита – на шестую размольную систему.
Шестая размольная система. Сход с последнего сита направляется на седьмую размольную систему проход первой второй и третьей группы сит – на контроль муки первого сорта проход последнего сита – на восьмую размольную систему.
Седьмая размольная система. Сход с первого сита направляется на десятую размольную систему сход с последнего сита направляется на девятую размольную систему проход первой второй группы сит – на контроль муки первого сорта проход с третьей группы сит – на контроль муки второго сорта проход последнего сита – на восьмую размольную систему.
Восьмая размольная система. Сход с первого сита направляется на десятую размольную систему сход с последнего сита направляется на девятую размольную систему проход второй и третьей группы сит – на контроль муки первого сорта проход последнего сита – на контроль муки второго сорта.
Девятая размольная система. Сход с первого сита направляется на вторую драную систему сход с последнего сита направляется на вторую драную систему проход второй третьей и четвертой группы сит – на контроль муки первого и высшего сорта.
Десятая размольная система. Сход с первого сита направляется на одиннадцатую размольную систему сход с последнего сита направляется на одиннадцатую размольную систему проход второй третьей и четвертой группы сит – на контроль муки второго сорта.
Одиннадцатая размольная система. Сход с первого сита - отруби сход с последнего сита - отруби проход второй третьей и четвертой группы сит – на контроль муки второго сорта.
Контроль муки высшего сорта. Сход с последнего сита направляется на третью размольную систему проход всех сит – в готовую муку высшего сорта.
Контроль муки первого сорта. Сход с последнего сита направляется на шестую размольную систему проход всех сит – в готовую муку первого сорта.
Контроль муки второго сорта. Сход с последнего сита направляется на восьмую размольную систему проход всех сит – в готовую муку второго сорта.
Техническая характеристика систем измельчения приведена в приложении Б.
6 Теоретический количественный баланс помола
Баланс помола представляет количественную или качественно-количественную характеристику всех продуктов по технологической схеме помола. различают количественный и качественный балансы. Количественный баланс учитывает только количество продукта в % качественный баланс составляют по следующим показателям: зольность белок клетчатка и т.д. Различают следующие виды баланса: баланс технологической схемы баланс отдельного процесса (драного шлифовочного размольного) полный баланс помола.
Существует качественный баланс помола который снимается на действующем предприятии и теоретический который рассчитывается для проектируемых или реконструируемых мельниц.
На основе баланса помола корректируют режимы на отдельных технологических системах группируют потоки продуктов формируют сорта муки рассчитывают необходимое количество оборудования распределяют его по отдельным системам. Пользуясь балансом можно правильно оценить технологический процесс исправить недостатки и наметить пути дальнейшего его совершенствования. Разработка баланса заключается в уравнении количества продуктов поступивших на систему и уходящих с него.
Баланс помола изображают в виде таблицы-шахматки.
В левой части таблицы вертикально записывают все технологические системы и нагрузки на них в % к первой драной системе.
В верхней строке записывают все системы кроме первой драной а также записывают готовую продукцию.
Количество поступившего на каждую систему продукта записывается в строке против соответствующей системы.
Сумма полученных продуктов по горизонтали должна быть равна количеству поступившего продукта нагрузки по вертикали.
При разработки теоретического количественного баланса руководствуются схемой технологического процесса рекомендациями изложенными в правилах организации и ведения технологического процесса по режимам измельчения на драных шлифовочных и размольных системах для каждого вида помола; извлечению крупок дунстов и муки; распределению продуктов на ситовеечных системах.
Также необходимо знать общие и частные положения технологии мукомольного производства схемы сортирования продуктов в рассевах а также классификацию промежуточных продуктов.
В состав продуктов извлечения входят крупная средняя мелкая крупки жесткий и мягкий дунсты и мука. Нагрузку на I др.с. обычно принимают за 100% поскольку рекомендуемые режимы систем и этапов указаны в процентах по отношению к нагрузке на эту систему. При этом необходимо учитывать что во всех существующих видах помолов выход муки общий и по сортам указан по отношению к количеству зерна базисного качества поступившему на очистку. При выборе режимов систем и этапов необходимо учитывать стекловидность зерна и вид помола по ассортименту и выходам муки т.к. режимы дифференцированы по указанным признакам.
Особенностью методики является то что количество поступающего на первую драную систему зерна принимают за 100% хотя 29% при сортовых помолах пшеницы или 34% при ржаных помолах остается в подготовительном отделении в виде отходов и потерь. То есть на первую драную систему поступает 971% при помоле пшеницы и 966% при помоле ржи. При расчете исходят из базисных показателей качества зерна. Указанная особенность определяет необходимость пересчета запланированных выходов муки и отрубей так чтобы их сумма была равна 100% т.е. количеству зерна поступившему на первую драную систему. Потерями в размольном отделении в результате усушки пренебрегают.
Перед тем как приступить к разработки баланса важно учесть наличие заворотов то есть продуктов возвращаемых с последних систем на предыдущие. Так например схода с ситовеечных машин после обогащения крупной и средней крупок возвращаются на третью драную систему мелкую. Схода с контрольных рассевов возвращаются на размольные системы. Количество подобных заворотов для разных схем помола разное все их необходимо выявить в схеме и вписать в таблицу-шахматку предполагаемую массу заворотов в соответствующие системы.
Количество сходового продукта с контрольных рассевов не должно превышать 5% от поступающего продукта.
Количественный баланс помола мукомольного завода представлен в приложении Б.
Выход муки – 78% высший сорт – 15% I сорт – 50% II сорт – 13% отруби – 191%.
В размольное отделение поступает 971% следовательно:
Таким образом после контроля муки выход высшего сорта должен составить - 1544% первого сорта - 5149% второго сорта – 1339 % отрубей должно получиться – 1967%.
В данной курсовой работе представлены чертежи и расчеты технологического оборудования подготовительного и размольного отделений мукомольного завода.
Поэтажная компоновка подготовительного отделения выполнена на основе принципиальной схемы с некоторыми изменениями. Главной особенностью спроектированного мукомольного завода является применение новых технологий гидротермической обработки. В основу был положен способ виброувлажнения. Таким образом гидротермическая обработка влияет на структурно-механические и биохимические свойства зерна различных культур что способствует увеличению выхода готовой продукции и улучшению её качества.
Размольное отделение выполнено по типовой схеме. Оборудование подобранное в размольное отделение: 13 вальцовых станков марки ВМ-2П 3 бичевых машины марки МБО 8 рассевов марки ЗРШ-4М 7 ситовеечных машин марки А1-БСО.
Таким образом курсовая работа выполнена с внедрением новых технологий в совокупности с давно использующимся оборудованием на основе типовых схем.
Приложение А.docx
Таблица А1 – Техническая характеристика автоматических весов АД-50-3Э
Предел допускаемой погрешности %
Наибольший предел производительности тч
Потребляемая мощность кВ·А
Расход воздуха приведенный к нормальным условиям (температура 20 0С и давление 01 МПа) м3ч
Габаритные размеры и масса: (Длина × ширина × высота × масса)
Таблица А2 – Техническая характеристика сито-воздушного сепаратора А1-БМС-6
Производительность тч
Колебания ситового корпуса:
Угол наклона сит град
В том числе в канале продувки:
Мощность электродвигателя кВт
Габаритные размеры мм
Таблица– Техническая характеристика камнеотделительной машины РЗ-БКТ
Площадь ситовой поверхности м2
Угол наклона деки град
Частота колебаний колмин
Амплитуда колебаний мм
Разряжение в корпусе (без нагрузки) Па
Мощность электровибратора кВт
Таблица А4 – Техническая характеристика триеров
Частота вращений ротора обмин
Расход воздуха на аспирацию м3ч
Таблица А5 – Техническая характеристика магнитного сепаратора У1-БМЗ-01
Количество магнитов в одном блоке
Магнитная индукция на расстоянии 15 мм от оси магнитного блока мТл
Таблица А6 – Техническая характеристика обоечной машины РЗ-БГО-6
Сетчатый цилиндр мм:
Частота вращения ротора обмин
Таблица А7 – Техническая характеристика виброувлажнительной машины VIBRONET 75S
Увеличение влажности зерна %
Размеры цилиндрической части корпуса мм:
Зазор между гонками и корпусом мм
Таблица А8 – Техническая характеристика аспиратора А1-БДЗ-6
Эффективность очистки %
Таблица А9 – Техническая характеристика вальцового станка марки ВМ-2П
Техническая производительность одной половины станка тсут
Номинальная длина бочки вальца мм
Установленная мощность электродвигателей привода кВт
Масса станка (без электропривода) кг
Таблица А10 – Техническая характеристика бичевой машины МБО
частота вращения обмин
Число пар бичей на роторе пары
Окружная скорость бичей мс
Диаметр ситового цилиндра мм
Зазор между ротором и ситовым цилиндром мм
Мощность установленного электродвигателя кВт
Габариты (длина ширина высота) мм
Таблица А11 – Техническая характеристика рассева ЗРШ-4М
Средняя удельная нагрузка кгм2сут
Техническая производительность на I драной системе тч
Число секций (приемов)
Размеры ситовых рам мм
Общая полезная площадь сит м2
Радиус круговых колебаний мм
Частота круговых колебаний об.мин
Габариты мм: (Длина×Ширина×Высота)
Таблица А12 – Техническая характеристика ситовеечной машины А1-БСО
Размер ситовых рам мм
Число ярусов ситовых рам
Число колебаний ситового корпуса колеб.мин
Амплитуда колебаний ситового корпуса мм
титульный мука.doc
ВОСТОЧНО-КАЗАХСТАНСКИЙ ГОСУДАРСТВЕННЫЙ УНИВЕРСИТЕТ ИМ. С.АМАНЖОЛОВА
ФАКУЛЬТЕТ МАТЕМАТИКИ ФИЗИКИ И ТЕХНОЛОГИЙ
КАФЕДРА ПРОФЕССИОНАЛЬНОГО ОБУЧЕНИЯ И ТЕХНОЛОГИИ
г. Усть-Каменогорск 2012 г.
ПОЯСНИТЕЛЬНАЯ ЗАПИСКА
к курсовой работе по дисциплине
ТПП1 Воротникова В.Н.
к.ф.-м.н. Дёмина И.А.
Усть-Каменогорск 2012 г.
на курсовую работу по дисциплине
для специальности 5В072800 – «Технология перерабатывающих производств»
студентке Воротниковой Виктории
группа 4ТПП-1 (очное отделение)
факультет математики физики и технологии
Тема курсовой работы: Проектирование зерноочистительного и размольного отделений мукомольного завода по производству хлебопекарной пшеничной муки с развитой схемой технологического процесса.
Производительность - 100 тонн в сутки;
Нормы выхода продукции
Кормовые зернопродукты
Отходы с механическими потерями (без мойки зерна)
Содержание курсовой работы:
Содержание пояснительной записки (перечень подлежащих разработке вопросов):
Введение анатомическое строение зерна пшеницы структурно-механические свойства зерна пшеницы мукомольные свойства зерна пшеницы количественный баланс помола выбор и обоснование технологических схем подбор и расчет оборудования подготовительного и размольного отделений.
Перечень графического материала (с точным указанием обязательных чертежей):
Технологическая схема зерноочистительного отделения мукомольного завода (формат А1);
Технологическая схема размольного отделения мукомольного завода (формат А1).
Дата выдачи « 6 » сентября 2012 г.
Дата окончания «5 »декабря 2012 г.
Руководитель курсовой работы: ассоциир. профессор к.ф.-м.н. Дёмина И.А.
Студент (ка) Воротникова В.Н.
Часть 1.docx
1 Анатомическое строение зерна пшеницы
Зерно пшеницы состоит из нескольких анатомических частей – оболочек эндосперма и зародыша и др. которые характеризуются различными физиологическими функциями и в связи с этим имеют разное строение и химический состав.
3 – плодовые оболочки; 456 – семенные оболочки; 7 – алейроновый слой; 8 – слои клеток плодовой оболочки пшеницы с поверхности; 9 – эндосперм; 10 – щиток; 11 – почечка; 12 – осевая часть зародыша; 13 – корешок;
Рисунок 1. Продольный разрез зерна пшеницы
Соотношение анатомических частей зерна пшеницы
Около 45 массы зерновки составляет эндосперм. Это характерно для большинства злаков – пшеницы ржи овса ячменя и др. Соотношение других частей колеблется в зависимости от ряда факторов. Например содержание оболочек зерновки ржи выше чем у пшеницы а у твердой пшеницы выше чем у мягкой.
Зерно пшеницы имеет сложный химический состав. При оценке технологических и питательных свойств зерна немаловажное значение имеет количественное соотношение анатомических частей - зародыша оболочек и эндосперма.
Оболочки состоящие в основном из неусвояемых человеческим организмом веществ не имеют пищевой ценности. Это балласт который способствует выведению из организма тяжелых металлов и токсинов.
Для изготовления сортовой муки используются не все части зерновки а преимущественно эндосперм и небольшой процент измельченных периферийных частей зерна – алейронового слоя и оболочек. Зародыш содержит много полноценных белковых веществ жиров углеводов а также витаминов но при сортовых помолах муки зародыш удаляется.
Наибольшее значение как источник легкоусвояемых питательных веществ имеет эндосперм поэтому содержание эндосперма в зерновке и возможность отделения его от оболочек и зародыша представляет практический интерес. Эндосперм состоит из многих жизненно необходимых человеку элементов т.к.: белки углеводы ферменты витамины минеральные вещества и др.
Эндосперм – источник белков и крахмала. Из злаковых культур наиболее богато белками зерно пшеницы 11-18% ржи 9-14%. Белковые вещества в зерне пшеницы и муке образуют клейковину. Ценится мука с высокой клейковиной т.к. тесто из такой муки получается упругим легко формируется не прилипает.
Крахмал содержится в клетках эндосперма в виде крахмальных зерен. Он является важнейшим запасным углеводом зерна а углеводы в живом организме – источник энергии необходимой для биохимических процессов организма.
Вместе с белками (клейковиной) это вещество определяет консистенцию теста и вкус хлеба. В муке содержится до 80% крахмала. При выпечке крахмал клейстеризуется связывая образование сухого эластичного мякиша.
Количество и соотношение различных групп углеводов влияют на технологические свойства зерна на качество хлеба т.к. сахара и крахмал необходимы для развития дрожжей в тесте а крахмал вместе с белками составляет формирующую основу теста.
Из простейших сахаров в составе зерна наибольшее значение имеют глюкоза и фруктоза. Мука может обладать высокой нормальной или низкой сахаробразующей способностью. При образовании теста глюкоза сбраживается дрожжами выделяя углекислый газ который при выпечке хлеба способствует образованию пористости.
Жиры – важный энергетический материал для организма человека и носитель растворимых в жирах витаминов А D Е К. Кроме этих витаминов мука а следовательно и хлеб являются источником водорастворимых витаминов В1 В2 РР необходимых в питании человека.
Химический состав зерна пшеницы
Минеральные вещества мг
Энергетическая ценность ккал
Зерно мягкой пшеницы по своему химическому составу и высокой калорийности является превосходным сырьем для производства муки и приготовления из нее печеного хлеба.
Процесс получения муки состоит из подготовки зерна к помолу: удаление примесей очистка поверхности зерна кондиционирование зерновой массы и самого помола. Помолы делят на обойные (простые) и сортовые (сложные). Сортовые помолы зерна могут быть одно- двух- и трехсортными.
В технологическом процессе при переработке зерна учитывают разную пищевую ценность частей зерна и используя различные свойства этих частей при сортовых помолах формируют сорта муки объединяя потоки муки с разных систем в тот или иной сорт.
2 Технологические свойства зерна пшеницы
Технологические свойства сырья на мукомольных заводах определяются следующими основными показателями: выходом готовой продукции суммарно и по сортам; качеством готовой продукции; удельными эксплуатационными расходами. На технологические свойства зерна оказывает влияние комплекс их физико-химических структурно-механических теплофизических биохимических свойств которые изменяются под воздействием гидротермической обработки.
Натура и масса 1000 зерен. Натура - это масса одного литра зерна в граммах. До середины 19 века натура зерна была единственным показателем качества. В настоящее время показатель натуры широко применяется в международной торговле зерном.
На показатель натуры влияет много параметров: размеры форма масса 1000 зерен выравненность по крупности влажность засоренность плотность и т.д. Именно поэтому один показатель натуры не может служить признаком определяющим мукомольные достоинства зерна. Однако в совокупности с другими показателями натура остается важным показателем качества зерна.1000 зерен более строго чем натура отражает его крупность и относительное содержание оболочек зародыша и эндосперма.
Если масса 1000 зерен основного зерна достаточно отличается от массы 1000 зерен засорителей то эта разница используется для очистки зерна на инерционных очистителях и на пневмосепараторах. Показатель массы 1000 частиц промежуточных продуктов помола в совокупности с их размерами можно использовать при определении нагрузок на вальцовые станки.
Зольность. Зольность зерна и его составных частей варьирует в широких пределах. Решающим для технолога является то обстоятельство что зольность эндосперма во много раз меньше зольности оболочек с алейроновым слоем. Так для пшеницы зольность эндосперма в 18 25 раз меньше зольности оболочек с алейроновым слоем а для ржи - в 10 14 раз. Следовательно показатель зольности отражает примерное соотношение оболочек и эндосперма в промежуточных продуктах помола и в готовой продукции. Для промежуточных продуктов помола (крупки и дунсты) зольность - единственный показатель их качества. Следует также отметить что несмотря на большой диапазон зольности зерна и его составных частей для разных партий пшеницы технологу необходимо получить муку с зольностью не выше нормы.
Стекловидность. Стекловидность характеризует структурно-механические свойства эндосперма поэтому этот показатель определяет режимы гидротермической обработки зерна и режимы первых систем сортового помола. Из стекловидного зерна легче получить требуемый выход муки чем из мучнистого т.к. стекловидное зерно легче вымалывается а на первых системах помола можно получить большое количество крупок.
Зерно мягкой пшеницы по стекловидности делят на три группы. К первой группе относят зерно стекловидностью свыше 60% ко второй – 40 60% к третьей - меньше 40%. Смешивать партии зерна по стекловидности относящиеся к разным группам при размещении и хранении в элеваторе нельзя.
Влажность. Исходная влажность зерна как сырья для мукомольного завода должна интересовать технолога в той мере насколько она позволяет ему управлять мукомольными свойствами зерна при гидротермической обработке. Если влажность зерна поступающего на мельзавод с элеватора низкая (до 125 135%) то у технолога больше возможностей улучшить мукомольные свойства зерна при помощи двух - трехкратной гидротермической обработки. Если же влажность зерна высокая (больше 145%) то у технолога остается единственная возможность увлажнить его только перед размолом.
3 Мукомольные свойства зерна пшеницы
Качество зерна поступающего на переработку в муку оценивают по следующим показателям:
Обязательным общим – характеризуют свежесть или здоровье зерна и его состояние. По этим показателям судят о стойкости зерна при хранении возможности его использования необходимости и режимах обработки. Их определяют в зерне независимо от целевого назначения;
Обязательным специфическим – характеризуют технологические достоинства зерна. Это типовой состав натура крупность и выравненность стекловидность количество и качество клейковины зольность и другие;
Дополнительным – определяемым в случае необходимости или по особому указанию (прочность полный химический состав или содержание отдельных веществ например белков активность ферментов количественный и качественный состав микрофлоры остаточное содержание фумигантов в зерне).
Все методы определения показателей качества зерна стандартизированы. Качество зерна определяют в лабораторных условиях органолептически или с применением различных приборов и устройств.
Органолептически определяется цвет запах и вкус зерна. Эти показатели характеризуют его свежесть и по ним можно судить о состоянии зерна его стойкости при хранении и т.д.
В лабораторных условиях с применением приборов определяют зольность влажность засоренность выравненность стекловидность натуру массу 1000 зерен плотность зараженность вредителями хлебных запасов количество и качество клейковины и др.
Известно 27 видов пшеницы самым распространенным является мягкая. Самой лучшей яровой мягкой пшеницей является Саратовская 29. К сортам сильной пшеницы относится Целинная 20 Новосибирская 67 Уральская 52.
Твердая пшеница является преимущественно яровой – харьковская 46.
Мягкую пшеницу по качеству получаемой муки содержанию белка клейковины и по хлебопекарным свойствам подразделяют на 3 группы: сильная слабая средняя.
Сильной является пшеница с натурой не ниже 730-755 гл в зависимости от района произрастания со стекловидностью не менее 60% и сырой клейковиной 28%. Сильная пшеница дает муку образующую тесто с хорошей упругостью с высокой устойчивостью способное удержать длительное брожение. Хлеб из сильной муки получается хорошей формы с равномерной сильно-развитой пористостью большого объема.
Слабая пшеница имеет стекловидность не менее 40% клейковина 20% группа клейковины 23. Такая пшеница дает муку образующее липкое вяжущее тесто из которого хлеб получается малого объема расплывшейся формы с плохо разрыхленным мякишем. Слабая пшеница самостоятельно не используется.
Средняя по силе пшеница не может улучшать слабую пшеницу но при самостоятельном использовании дает стандартный по качеству хлеб.
Твердая пшеница используется для выработки макаронной муки т.к. она обладает клейковиной с высокой упругостью но малой растяжимостью что позволяет хорошо сохранить приданную макаронным изделиям форму.
Стандартами пшеница заготовляемая и распределяемая подразделяется на 5 типов в зависимости от вида и времени выращивания: яровая краснозерная яровая дурум яровая белозерная озимая краснозерная озимая белозерная.
По стекловидности и оттенку зерна 1 и 4 типов подразделяются на 5 подтипов. 2 и 3 типы делятся на 2 подтипа 5 тип на подтипы не делят. С принадлежностью зерна к тому или иному типу и подтипу связаны хлебопекарные свойства пшеницы 1 и 4 типа является сильной 5 тип – слабая пшеница.
Пшеница заготовляемая по качеству может быть базисных и ограничительных кондиций.
4 Характеристика поступающего сырья на переработку
Показатели качества зерна пшеницы при определении расчетных выходов продукции [7]:
зольность зерна (очищенного от сорной примеси) – 185% при сортовых помолах;
содержание сорной примеси – 1% в том числе вредной – 01%;
содержание зерновой примеси – 1%;
натура при сортовых помолах – 775 гл;
общая стекловидность при сортовых помолах – 50%;
Расчеты. подг отд.docx
Для обеспечения бесперебойной работы мукомольного завода создания определенного запаса зерна производительность подготовительного отделения увеличивают на определенную величину называемую коэффициентом запаса Кз. мы принимаем его равным 12.
В соответствии с этим расчетная производительность Qр тсут подготовительного отделения определяется по формуле
где Qр – расчетная производительность подготовительного отделения тсут;
Кз – коэффициент запаса [7];
Q – производительность мукомольного завода тсут.
Сущность расчета и подбора оборудования сводится к определению его количества путем сравнивания производительностей завода на данном этапе и оборудования. Производительность оборудования может быть задана различными способами. В подготовительном отделении – это часовая паспортная производительность которая является основной характеристикой сепарирующих машин машин для гидротермической обработки и обработки поверхности зерна.
Расчет весового оборудования т.е. количество весов nвычисляется по формуле
где p – вместимость весового ковша кг;
q – производительность весов количество взвешиваний в минуту.
Принимаем одни весы марки АД-50-3Э. Техническая характеристика приведена в Приложении А1.
Для расчета оборудования предварительной очистки используют формулу (3):
где n – количество машин шт;
q – паспортная производительность оборудования тч.
Коэффициент использования k % рассчитывают по формуле (4):
где Qзад – производительность мукомольного завода тсут;
qм – производительность оборудования тч.
Расчет оборудования для предварительной очистки зерна производим по формуле (3):
количество воздушно-ситовых сепараторов
Принимаем один сепаратор А1-БМС-6. Коэффициент использования k=84%. Техническая характеристика приведена в Приложении А2.
количество камнеотделительных машин
Принимаем одну камнеотделительную машину РЗ-БКТ. Коэффициент использования k=84%. Техническая характеристика приведена в Приложении А3.
Принимаем один триер А9-УТК-6 и один триер А9-УТО-6. Коэффициент использования k=84%. Техническая характеристика приведена в Приложении А4.
количество магнитных сепараторов
Принимаем один магнитный сепаратор У1-БМЗ-01. Коэффициент использования k=56%. Техническая характеристика приведена в Приложении А5.
количество обоечных машин
Принимаем одну обоечную машину РЗ-БГО-6. Коэффициент использования k=84%. Техническая характеристика приведена в Приложении А6.
количество воздушных сепараторов
Принимаем один сепаратор А1-БДЗ-6. Коэффициент использования k=100%. Техническая характеристика приведена в Приложении А7.
количество увлажнительных машин (виброувлажнительная машина V75S)
Принимаем одну машину V75S. Коэффициент использования k=67%. Техническая характеристика приведена в Приложении А8.
Расчет оборудования для окончательной очистки зерна ведем по формуле (3):
Принимаем одну машину РЗ-БГО-6.
Принимаем один сепаратор А1-БДЗ-6.
3 Расчет бункеров для оперативного хранения
На мукомольных заводах бункера используют для оперативного хранения зерна промежуточных и конечных продуктов. Вместимость бункеров будет зависеть от их назначения объемной массы хранящегося продукта а также от геометрических размеров. Наибольшую вместимость должны иметь бункера обеспечивающие длительное оперативное хранения зерна и других продуктов. Фактическая вместимость бункера всегда несколько меньше его геометрического объема. Последнее связано с устройством конусных днищ у бункеров а также со свойством сыпучих материалов располагаться при загрузки под углом естественного откоса.
При расчете вместимости бункеров для неочищенного зерна необходимо учитывать рекомендации о запасе зерна в этих бункерах на 50 часов работы подготовительного отделения. Такой запас необходим для эффективного смешивания зерна различного качества при формировании помольных партий.
Общую вместимость бункеров для неочищенного зерна V0 м3 находят по формуле (5):
где t – время нахождения зерна в бункерах ч;
- объемная масса зерна тм3 [7];
k – коэффициент использования бункера k=085[7].
При устройстве железобетонных бункеров размером 3×3 м2 площадь их поперечного сечения принимают 7 м2 учитывая размер сетки привязочных осей бункеров и их строительных конструкций. Тогда объем занимаемый бункерами V1 м3 учитывая что высота каждого этажа 48 м составит:
где h – количество этажей на которых расположены бункера.
Число бункеров для неочищенного зерна nсоставит:
Находим ёмкость бункеров для неочищенного зерна по формуле 8:
Аналогично рассчитываем бункера для отволаживания.
Принимаем 6 бункеров для неочищенного зерна и 2 бункера для отволаживания [7].
Рассчитываем бункера для кормовых и некормовых отходов. Расчетное значение вместимости бункера Ер для кормовых отходов:
где Q – производительность мукомольного завода тсут;
t – время нахождения продукта в бункерах ч;
- объемная масса продукта тм3 [7];
Сп – нагрузка на систему (поступление от производительности завода) %.
Строительную вместимость бункера рассчитывают с учетом коэффициента использования объема:
где Ки – коэффициент использования объема.
Число бункеров на данной операции находят в зависимости от вместимости единичного бункера и строительного объёма.
Величину nр округляют до целого значения и рассчитывают фактическую вместимость бункера.
Находим ёмкость бункеров для кормовых отходов по формуле 8:
Расчетное значение вместимости бункера Ер для некормовых отходов:
Таким образом для кормовых отходов устанавливаем бункер ёмкостью 115т а для некормовых отходов не целесообразно ставить бункер.
Содержание мука.docx
1 Анатомическое строение зерна пшеницы
2 Технологические свойства зерна пшеницы . .
3 Мукомольные свойства зерна пшеницы ..
4 Характеристика поступающего сырья на переработку. ..
Технологическая часть. Подготовительное отделение мукомольного завода
1 Выбор и обоснование схемы сортового помола пшеницы
2 Расчет технологического оборудования подготовительного отделения мукомольного завода ..
3 Расчет бункеров для оперативного хранения ..
4 Размольное отделение мукомольного завода
5 Выбор и обоснование рабочей схемы ..
6 Теоритический количественный баланс помола .. ..
7 Расчет оборудования размольного отделения мукомольного завода
7.1 Расчет вальцовой линии
7.2 Расчет бичевых машин ..
7.3 Расчет просеивающей поверхности .
7.4 Расчет ситовеечных машин
Список использованной литературы . ..
Приложение А. Технические характеристики оборудования ..
Приложение Б. Техническая характеристика процесса измельчения .
Приложение В. Баланс помола .
Приложение Г. Схема размольного отделения с указанием продуктов помола ..
Выбор техн. схемы подг. отд..docx
В подготовительном отделении мукомольного завода качество зерна и его технологические свойства должны быть улучшены. Достигается это очисткой зерновой массы от примесей обработкой поверхности зерна в обоечных и щеточных машинах мойкой и гидротермической обработкой. Важно также чтобы была стабилизация технологических свойств зерна на оптимальном уровне в течение возможно более длительного времени. Для этого необходимы определенный режим гидротермической обработки (ГТО) и рациональный подбор состава помольной смеси.
Как правило подготовку отдельных компонентов помольной смеси различающихся показателями качества и свойствами ведут раздельно смешивая их только после завершения ГТО. Если мелкая фракция зерна не выделена в элеваторе то организуют ее отбор в подготовительном отделении. Предварительное шелушение зерна при многосортных помолах не применяют так как удаление плодовых оболочек приводит к более интенсивному измельчению семенных оболочек и алейронового слоя частицы которых засоряют муку.
При поступлении в размольное отделение зерно должно иметь следующие показатели качества: влажность на оптимальном уровне т. е. в пределах 150 165%;содержание сорной примеси не более 04% в том числе вредной не более 005%; минеральная примесь не допускается;содержание зерновой примеси (ржи и ячменя в пшенице) не более 4%; содержание сырой клейковины для пшеницы при сортовых помолах не менее 26% [4].
1 Выбор и обоснование схемы подготовительного отделения мукомольного завода
Схема подготовки зерна к помолу была разработана на основе типовых схем и последовательности операций [3]. Главной особенностью разработанной схемы является применение новых технологий ГТО [3].
При сортовом помоле зерна отделить частицы оболочек от эндосперма чрезвычайно трудно поскольку их структурно – механические свойства отличаются незначительно. При помощи гидротермической обработки стремятся усилить различие свойств оболочек и эндосперма. Кроме того комплекс мероприятий по воздействию на зерно теплом и водой позволяет улучшить биохимические свойства и в конечном итоге хлебопекарные качества муки.
На современных мукомольных предприятиях применяют в основном два метода гидротермической обработки: холодное и скоростное кондиционирование. При этом на отдельных предприятиях и климатических зонах имеют место некоторые отличия. Так в районах с холодным климатом зерно перед поступлением на машины зерноочистительного отделения мельницы подогревается тогда как при умеренном и тёплом климате этого не делают. Однако в целом придерживаются отработанных схем [5].
Холодные способы ГТО применяют при подготовке мягкой пшеницы и ржи к хлебопекарным сортовым и обойным помолам при подготовке твердой и высокостекловидной пшеницы к макаронным помолам а также при подготовке пшеницы к переработке в крупу.
Холодное кондиционирование состоит в увлажнении зерна и последующей выдержке его (отволаживании) в бункерах. Название метода обусловлено тем что его проводят без подогрева зерна. При скоростном кондиционировании зерно обрабатывают паром а затем моют в холодной воде. Благодаря такому воздействию свойства зерна изменяются быстрее и необходимая продолжительность отволаживания сокращается.
Общим для обоих методов ГТО является обязательное доувлажнение зерна на 03 05% и отволаживание его в течение 20 40 мин перед подачей в измельчающую машину (вальцовый станок I драной системы). Это необходимо для увлажнения поверхностных слоев зерна (оболочек и алейронового слоя). В результате их прочность резко повышается они плохо измельчаются образуя крупные частицы отрубей. Последние легко отделяются на ситах.
При холодном кондиционировании зерно обрабатывают в моечной машине или мокром шелушителе дополнительно увлажняют отволаживают. При высокой стекловидности рекомендуется двукратное увлажнение и отволаживание. Это необходимая последовательность этапов данного метода ГТО.
При скоростном кондиционировании после кратковременного (20 40°С) пропаривания в аппарате типа АСК нагретое зерно выдерживают в теплоизолированном бункере. Затем его моют холодной водой обрабатывают во влагоснимателе доувлажняют и отволаживают. Скоростной метод гидротермической обработки наиболее эффективен для пшеницы со слабой клейковиной и для мукомольных заводов с ограниченной вместимостью емкостей для отволаживания. Благодаря тепловому воздействию при пропаривании а также подогреву зерна во влагоснимателе интенсифицируется влагоперенос и процесс разрыхления эндосперма.
Важную роль играет правильная организация отволаживания зерна в бункерах. Если в днище бункера только одно выпускное отверстие то вследствие особенностей истечения сыпучих материалов выходящее зерно будет неоднородным по технологическим свойствам. Мукомольные заводы переведены на непрерывное (поточное) отволаживание. Бункера разгружают и загружают не периодически а непрерывно и зерно в них постоянно перемещается сверху вниз. Для того чтобы свойства зерна оставались стабильными в днище бункера делают отверстия (примерно по одному на 06 10 м2 сечения бункера). Продолжительность отволаживания регулируют скоростью движения зерна в бункере.
Наивысшей технологической эффективности достигают при раздельной подготовке каждого из компонентов помольной смеси. Например при раздельной подготовке зерна пшеницы методом холодного кондиционирования при трехсортном помоле общий выход муки составил 794% средневзвешенная зольность — 077%. При совместной подготовке этого зерна выход муки снизился до 786% а зольность увеличилась до 084%. Более чем на 11% повысился и удельный расход энергии на помол. Выход муки высоких сортов уменьшился на 26%. Результаты заметно повышаются если применяют двукратное увлажнение — отволаживание зерна.
На ряду с этими способами ГТО существуют и такой как горячее кондиционирование.
Метод горячего кондиционирования рекомендуется использовать для сортовых помолов пшеницы. В настоящее время метод находит ограниченное применение из-за высокой стоимости аппаратуры и оборудования а также тепловой энергии [6].
В результате ГТО в зерне развиваются сложные физико-химические коллоидные и биохимические процессы которые вызывают изменение технологических свойств зерна – разрыхление эндосперма образование микротрещин оболочки становятся более эластичными.
Длительность отволаживания во многом зависит от исходной влажности твердозёрности и стекловидности зерна. Например высокостекловидное зерно отволаживается в два этапа в течение более 48 ч.
Длительность времени отволаживания необходимость большого количества оперативных бункеров которые занимают большой объем производственных помещений и нуждаются в транспортных линиях связывающих гидротермическую обработку зерна с технологическим процессом – все эти факторы значительно усложняют эксплуатацию мельницы и повышают себестоимость готовой продукции.
Для оптимизации гидротермической обработки зерна а также для увеличения производственной мощности мельницы без дополнительных затрат на строительство бункеров для отволаживания в настоящее время существует вибрационный метод увлажнения зерна.
Немецкая компания ММW Technologie GmbH предлагает установку VIBRONET в которой осуществляется вибрационное увлажнение зерна.
Вибрационное увлажнение зерна заключается в следующем: необходимое количество воды для увлажнения поступает вместе с очищенным зерном в камеру для смешивания где зерно смачивается водой без интенсивного истирания и механических повреждений. Увлажненное зерно непрерывно поступает через вибрационную шахту которая в зависимости от пропускной способности состоит из одного или двух каналов. Специально сконструированные вибрационные моторы приводят в движение шахту. Вибрационная энергия снимает поверхностное натяжение воды таким образом что вода как пленка обволакивает зерновки. Вибрационная энергия «заставляет» воду равномерно и быстро проникать через внешние оболочки к эндосперму что приводит к образованию большого количества микротрещин и способствует более интенсивному и экономичному измельчению зерна. Механизм вывода зерна обеспечивает непрерывный выход из вибрационной шахты с заданной степенью увлажнения и отправляет его на отволаживание.
Вибрационная установка для увлажнения зерна VIBRONET имеет систему автоматизированного управления подачи воды в зависимости от исходной влажности зерна. С помощью этой системы во время работы мельницы в потоке непрерывно измеряется исходная влажность зерна температура натурный вес и в зависимости от технологической задачи автоматически регулируется подача точного количества воды необходимого для увлажнения. Система автоматизированного управления подачи воды обеспечивает определенное количества влаги в зерне и равномерное увлажнение. Сравнительный анализ традиционного увлажнения и вибрационного метода увлажнения представлен в таблице 2.
Для достижения наибольшей технологической эффективности увлажнения рекомендуется в зимнее время подогревать зерно т.к. оптимальная температура зерна перед помолом +20°С.
Сравнительный анализ методов увлажнения
Холодное кондиционирование зерна (традиционный метод увлажнения)
Вибрационное увлажнение зерна
Установка для увлажнения
Шнек интенсивного увлажнения А1-БШУ-2
Основные рабочие органы увлажняющей машины
Бичевой ротор индикатор наличия зерна система управления подачи воды
Камера смешивания зерна с водой вибрационная шахта система автоматизированного управления подачи воды
Производительность установки для увлажнения
Увлажняемые культуры
Пшеница рожь ячмень овёс кукуруза рис бобовые культуры
Длительность отволаживания
Увеличение влажности зерна
Расход электроэнергии
Количество этапов отволаживания
Как видно из таблицы вибрационное увлажнение зерна имеет несколько значительных преимуществ:
Сокращение времени отволаживания в 3-5 раз.
Зерно не подвергается механическому травмированию.
Значительная экономия электроэнергии.
Всего один этап ГТО и возможность добавления до 10-12% воды за один этап.
Возможность увеличить производственные мощности мельницы без дополнительных затрат на строительство бункеров для отволаживания.
Повышение общего выхода муки до 1%.
Вырабатывается гигиенически чистый продукт т.к. не увеличивается общее количество бактерий за счёт короткого времени отволаживания.
Простой монтаж установки VIBRONET даже при самых современных схемах размола.
Простой технический уход малый износ.
Таким образом благодаря современному методу вибрационного увлажнения зерна значительно снижается расход электроэнергии и несколько увеличивается общий выход готовой продукции существенно сокращаются строительно-наладочные работы за счет уменьшения объемов бункеров для отволаживания и простоты установки для вибрационного увлажнения что особенно актуально в настоящее время при реконструкции и модернизации действующих мельниц [3].
Таким образом принимаем к установке вибрационный увлажнитель который охарактеризовал себя как более практичный.
Зерно поступает с элеватора на ленточный конвейер (позиция 1Т) откуда транспортируется в бункера для неочищенного зерна вместимостью т которые рассчитываются на 50часов [7]. Зерно из бункеров для неочищенного зерна направляют через дозаторы (позиция 2Т) на смесительный шнек (позиция 3Т) после чего взвешивается на весах (позиция 4Т) и подается на норию №1. Нория №1 поднимает зерно на 5 этаж и подает на сито-воздушный сепаратор А1-БМС-6 (позиция 5Т) в котором происходит очистка от примесей отличающихся от пшеницы аэродинамическими свойствами и линейными размерами (шириной и толщиной). После очистки на сито-воздушном сепараторе происходит очистка на камнеотделительной машине (позиция 6Т) в которой происходит сепарирование за счет вибрационного и инерционного движений. Затем оно поступает на очистку в триеры куколеотборник (позиция 7Т) и овсюгоотборник (позиция 8Т) в которых отделяются примеси отличающиеся по длине от основной культуры. После чего зерно направляется на обоечную машину (позиция 9Т) предназначенную для очистки поверхности от пыли и надорванных оболочек а также для снижения зольности. Затем зерно самотеком через магнитную защиту (позиция 10Т) направляется на норию №2 и подается на аспиратор (позиция 11Т). Аспиратор необходим для очистки от легких примесей то есть частиц оболочек которые были отделены на обоечной машине.
Зерно направляют на гидротермическую обработку. ГТО проводят в виброувлажнительной машине VIBRONET 75S (позиция 12Т) после указанного метода ГТО отволаживание происходит в течении 6-8 часов [3] в бункерах для отволаживания (позици 8Б-9Б). Увлажнение проходит в один этап что существенно сокращает время переработки.
После ГТО увлажненное зерно из бункеров для отволаживания дозаторами (позиция 13Т) подается на смесительный шнек (позиция 14Т) где смешивается и направляется на норию №3. После ГТО необходима еще одна очистка поверхности на обоечной машине (позиция 15Т) от надорванных оболочек вследствие чего снижается зольность на 004%. Затем зерно поступает в аспиратор (позиция 16Т) где также удаляются легкие примеси выделенные на обоечной машине.
Заключительным этапом подготовки зерна к помолу перед подачей в размольное отделение является взвешивание этот процесс осуществляется на весах марки АД-50-3Э (позиция 17Т).
На контроль отходов в бурат (18Т) поступают отходы выделенные на сито-воздушном сепараторе (позиция 5Т). Зерно выделенное на контроле отходов направляется на норию №1 а отходы – в бункер для кормовых зерноотходов.
Некормовые отходы выделенные на камнеотделительной машине (позиция 6Т) триерах (позиции 7Т 8Т) обоечной машине (позиция 9Т) собираются на норию №4 и самотеком направляются в бункер для некормовых отходов.
Технические характеристики оборудования приведены в Приложении А.
Список использованной литературы.docx
Мастер – план [Электронный ресурс]: справ. Система Респ. центр правовой информации. – Электрон. дан. – Астана: РЦПИ [2012]
Чеботарев О.Н. Технология муки крупы комбикормов: учеб. пособие О.Н. Чеботарев А.Ю Шаззо Я.Ф. Мартыненко. – М.: Издательский центр «Март» Ростов-нД 2004.– 688с.
Могучева Э.П. Проектирование мукомольных заводов. Ч. 1. Проектирование подготовительного отделения: учеб. пособие Э.П. Могучева Л. В. Устинова. – Барнаул: Изд-во АлиГТУ 2009. – 178 с.
Неретина В.М. Курсовое и дипломное проектирование по мукомольно –крупяному производству: учеб. пособие В.М. Неретина.– М.: Колос 1984. – 220 с.
Правила организации и ведения технологического процесса на мукомольных заводах. – Москва: Производственно – издательский комбинат ЦНТИИТЭИ хлебопродуктов 1991.-129 с.
Демский А.Б. Оборудование для производства муки и крупы: справочник А.Б. Демский М.А. Борискин В.Ф. Веденьев Е.В. Тамаров А.С. Чернолихов. – Санкт-Перербург: Изд-во «Профессия» 2000.– 624с.
Мартыненко Я.Ф. Проектирование мукомольных и крупяных заводов с основами САПР Я.Ф. Мартыненко О.Н. Чеботарев. – М.: Изд-во «Агропромиздат» 1992. – 239 с.
Миназбекова С.К. Проблемы развития экономики мукомольной промышленности Казахстана С.К. Миназбекова Исследования результаты. – 2005. №2. – С. 127.
Кисаева Г.Г. Контроль за безопасностью продуктов Г.Г. Кисаева В.В. Голдобина Пищевая и перерабатывающая промышленность Казахстана. – 2002. №3. – С.30.
Дёмина И.А. Методические указания к выполнению дипломных (курсовых) работ (проектов) для студентов специальности 5В072800 – «Технология перерабатывающих производств» И.А.Дёмина С.Ф.Колосова.- Усть-Каменогорск: ВКГУ 2011. – 36с.
Заключение.docx
Поэтажная компоновка подготовительного отделения выполнена на основе принципиальной схемы с некоторыми изменениями. Главной особенностью спроектированного мукомольного завода является применение новых технологий гидротермической обработки. В основу был положен способ виброувлажнения. Таким образом гидротермическая обработка влияет на структурно-механические и биохимические свойства зерна различных культур что способствует увеличению выхода готовой продукции и улучшению её качества.
Размольное отделение выполнено по типовой схеме. Оборудование подобранное в размольное отделение: 13 вальцовых станков марки ВМ-2П 3 бичевых машины марки МБО 8 рассевов марки ЗРШ-4М 7 ситовеечных машин марки А1-БСО.
Таким образом курсовая работа выполнена с внедрением новых технологий в совокупности с давно использующимся оборудованием на основе типовых схем.
часть 3.docx
Организация сортового помола выглядит намного сложнее в соответствии с более сложной задачей получения белой муки с незначительным содержанием в ней частиц поверхностных слоев зерна. Выше было показано что сортовая мука должна быть получена при помоле за счет тонкого измельчения только одного эндосперма: оболочки зерна его алейроновый слой и зародыш не попадать в муку. Это определяет необходимость организации избирательного измельчения зерна. Достижение этой цели обеспечивается целым рядом технологических операций.
Решение этой задачи начинается в подготовительном отделении мельницы в котором проводят кондиционирование зерна. При отволаживании в закромах увлажненного зерна происходит разрыхления эндосперма прочность его вследствие этого существенно понижается т. к. в нем образуются микротрещины которые разрушают его плотную структуру.
Но и сам процесс измельчения при сортовом помоле требует особой организации. Прежде всего при сортовом помоле его проводят в два приема. Вначале осуществляют достаточно грубое дробление зерна с целью измельчения (отбора) эндосперма в виде крупных промежуточных продуктов: крупок и дунстов. Затем проводят операции повышения их добротности – ситовеечный процесс. Полученные в результате этих операций чистые мелкие крупки и дунсты окончательно измельчаются в муку.
Конечно и на этапе первоначального дробления зерна получается некоторое количество муки но качество ее ниже чем при измельчении обогащенных продуктов. Основную массу муки получают на заключительном этапе помола – в размольном процессе.
Вымол сходовых продуктов в драном (др.) и размольном (р.) процессах производят на вымольных машинах раздельно или совместно.
Сита в рассевах и технологическую характеристику измельчающих вальцов подбирают исходя из типа помола. Подбор сит на ситовеечной машине зависит от характеристики поступающего на нее продукта – нижнего схода с рассевов I др.с. и II др.с.
При желании по этой схеме можно получить некоторое количество муки крупчатки которая в настоящее время мукомольной промышленностью не выпускается но которая всегда пользовалась хорошим спросом у потребителей. Для этого в нижней группе сит рассева 2 Р необходимо установить дунстовое сито например №25 или №27 и вывести этот поток муки отдельно – это и есть мука крупчатка.
Число рифлей в драном процессе следует принимать от 5 до 9 на 1см от I др.с. до последней системы на размольных системах необходимо установить 9 10 рифлей на 1см.
Скорость быстровращающегося вальца на всех системах одинаковая 6мс отношение окружных скоростей вальцов везде 25:1 взаимное расположение вальцов на последних системах драного и размольного процессов спсп на основных измельчающих системах осос уклон рифлей на драных системах 8 10% на размольных системах 10 12% углы заострения рифлей 1000 1100 на драных системах вначале 350650 на последней системе 400700 на размольных системах 400700.
5 Выбор и обоснование технологической схемы размольного отделения
Зерно из подготовительного отделения поступает на первую драную систему измельчается на вальцовом станке и поступает одну секцию рассева работающего по схеме 1. Сход с верхнего и второго сита направляется на вторую драную систему. Сход с последнего сита направляется на ситовеечную машину №1. Проход третьего сита (смесь муки дунстов и мелкой крупки) направляется на сортировочную машину №1 проход с последнего сита (средняя крупка) направляется на ситовеечную машину №2.
Вторая драная система. Сход с верхнего сита направляется на третью драную крупную систему со второго сита – на третью драную мелкую систему сход с последнего сита (крупная и средняя крупка) – на ситовеечную машину №3. Проход третьего сита (смесь муки дунстов и мелкой крупки) направляется на сортировочную систему №2 проход последнего сита (средняя крупка) – на ситовеечную систему №4.
Третья драная система крупная. Сход с верхнего сита направляется на первую бичевую машину. Сход со второго сита – на четвертую драную крупную систему сход с последнего сита –четвертую драную мелкую систему. Проход третьего сита (мука дунст) направляется на сортировочную систему №3 проход последнего сита (мелкая крупка) – ситовеечную систему №5.
Третья драная система мелкая. Сход с верхнего сита направляется на бичевую машину №1. Сход со второго сита – на четвертую драную крупную систему сход с последнего сита – четвертую драную мелкую систему. Проход третьего сита (мука дунст) направляется на сортировочную машину №3 проход последнего сита (мелкая крупка) – ситовеечную систему №5.
Четвертая драная система крупная. Сход с верхнего сита направляется на вторую бичевую машину. Сход со второго сита – на третью бичевую машину сход с последнего сита – на третью бичевую машину. Проход третьего сита (мука дунст) направляется на сортировочную систему №4 проход последнего сита (мука 1с) – на контроль муки первого сорта.
Четвертая драная система мелкая. Сход с верхнего сита направляется на вторую бичевую машину. Сход со второго сита – на третью бичевую машину сход с последнего сита – на третью бичевую машину. Проход третьего сита (мука дунст) направляется на сортировочную систему №4 проход последнего сита (мука 1с) – на контроль муки первого сорта.
Сортировочная система №1. Система работает по схеме №3. Сход с четвертой группы сит направляется на шестую ситовеечную систему. Проход первой второй третьей группы сит направляется на вторую размольную систему проход последнего сита – на седьмую ситовеечную систему.
Сортировочная система №2. Система работает по схеме №3. Сход с четвертой группы сит направляется на шестую ситовеечную систему. Проход первой второй группы сит – мука высшего сорта направляется на контроль муки проход третьей группы сит – на вторую размольную систему проход последнего сита – на седьмую ситовеечную систему.
Сортировочная система №3. Система работает по схеме №3. Сход с четвертой группы сит направляется на шестую ситовеечную систему. Проход первой второй группы сит направляется на контроль муки первого сорта проход с третьего сита – на третью размольную систему проход последнего сита – на седьмую ситовеечную систему.
Сортировочная система №4. Система работает по схеме №2. Сход с первой группы сит направляется на десятую размольную систему. Сход с четвертой группы сит направляется на седьмую размольную систему. Проход второй третьей группы сит направляется на контроль муки первого и второго сорта проход последнего сита – на пятую размольную систему.
Сортировочная система №5. Система работает по схеме №2. Сход с первой группы сит - отруби. Сход с четвертой группы сит направляется на одиннадцатую размольную систему. Проход второй третьей группы сит направляется на контроль муки второго сорта проход последнего сита – на девятую размольную систему.
Бичевая машина №1. Сход с нее направляется на четвертую драную систему крупную проход на сортировочную систему 4.
Бичевая машина №2. Сход с нее - отруби проход направляется на сортировочную систему №5.
Бичевая машина №3. Сход с нее - отруби проход направляется на сортировочную систему №5.
Шлифовочная система №1. Сход с первых сит направляется на четвертую драную мелкую сход со второй группы сит – на первую ситовеечную сход с последних сит – на вторую ситовеечную систему. Проходом с третьей группы сит выделяется мука высшего сорта а проход с последнего сита направляют на первую размольную систему.
Шлифовочная система №2. Сход с первых сит направляется на четвертую драную мелкую сход со второй группы сит – на третью ситовеечную систему сход с последних сит – на четвертую ситовеечную систему. Проходом с третьей группы сит выделяется мука высшего сорта а проход с последнего сита направляют на первую и вторую размольную систему.
Ситовеечная машина 1. Сход с первого и второго ярусов сит возвращается на третью драную систему мелкую сход третьего яруса сит – на первую шлифовочную систему проход последнего яруса сит – на первую шлифовочную и на первую размольную.
Ситовеечная машина 2. Сход с первого и второго ярусов сит возвращается на третью драную систему мелкую сход третьего яруса сит – на первую шлифовочную систему проход последнего яруса сит – на первую шлифовочную и на первую размольную а также возможно выделение манной крупы.
Ситовеечная машина 3. Сход с первого и второго ярусов сит возвращается на третью драную систему мелкую сход третьего яруса сит – на первую шлифовочную систему проход последнего яруса сит – на первую шлифовочную и на первую размольную.
Ситовеечная машина 4. Сход с первого и второго ярусов сит возвращается на четвертую драную систему мелкую сход третьего яруса сит – на четвертую размольную систему проход последнего яруса сит – на первую шлифовочную с выделением манной крупы.
Ситовеечная машина 5. Сход с первого и второго ярусов сит возвращается на четвертую драную систему мелкую сход третьего яруса сит – на четвертую размольную систему проход последнего яруса сит направляется на вторую шлифовочную и на четвертую размольную.
Ситовеечная машина 6. Сход с первого яруса сит направляется на седьмую размольную систему со второго яруса сит – на четвертую размольную сход третьего яруса сит – на вторую размольную систему проход последнего яруса сит – на вторую шлифовочную на первую и вторую размольную системы.
Ситовеечная машина 7. Сход с первого яруса сит направляется на седьмую размольную систему со второго и третьего ярусов сит – на пятую размольную проход последнего яруса сит направляется на вторую шлифовочную а также на первую и вторую размольную системы.
Первая размольная система. Сход с последнего сита направляется на четвертую размольную систему проход первого второго и третьего сит – на контроль муки высшего сорта проход последнего сита – на вторую размольную систему.
Вторая размольная система. Сход с последнего сита направляется на четвертую размольную систему проход первого второго и третьего сит – на контроль муки высшего сорта проход последнего сита – на третью размольную систему.
Третья размольная система. Сход с последнего сита направляется на четвертую размольную систему проход первого второго и третьего сит – на контроль муки высшего сорта проход четвертого сита – на пятую размольную систему.
Четвертая размольная система. Сход с последнего сита направляется на седьмую размольную систему проход первой второй группы сит – на контроль муки высшего сорта проход с третьей группы сит – на контроль муки первого сорта проход последнего сита – на пятую размольную систему.
Пятая размольная система. Сход с последнего сита направляется на седьмую размольную систему проход первой второй группы сит – на контроль муки высшего сорта проход с третьей группы сит – на контроль муки первого сорта проход последнего сита – на шестую размольную систему.
Шестая размольная система. Сход с последнего сита направляется на седьмую размольную систему проход первой второй и третьей группы сит – на контроль муки первого сорта проход последнего сита – на восьмую размольную систему.
Седьмая размольная система. Сход с первого сита направляется на десятую размольную систему сход с последнего сита направляется на девятую размольную систему проход первой второй группы сит – на контроль муки первого сорта проход с третьей группы сит – на контроль муки второго сорта проход последнего сита – на восьмую размольную систему.
Восьмая размольная система. Сход с первого сита направляется на десятую размольную систему сход с последнего сита направляется на девятую размольную систему проход второй и третьей группы сит – на контроль муки первого сорта проход последнего сита – на контроль муки второго сорта.
Девятая размольная система. Сход с первого сита направляется на вторую драную систему сход с последнего сита направляется на вторую драную систему проход второй третьей и четвертой группы сит – на контроль муки первого и высшего сорта.
Десятая размольная система. Сход с первого сита направляется на одиннадцатую размольную систему сход с последнего сита направляется на одиннадцатую размольную систему проход второй третьей и четвертой группы сит – на контроль муки второго сорта.
Одиннадцатая размольная система. Сход с первого сита - отруби сход с последнего сита - отруби проход второй третьей и четвертой группы сит – на контроль муки второго сорта.
Контроль муки высшего сорта. Сход с последнего сита направляется на третью размольную систему проход всех сит – в готовую муку высшего сорта.
Контроль муки первого сорта. Сход с последнего сита направляется на шестую размольную систему проход всех сит – в готовую муку первого сорта.
Контроль муки второго сорта. Сход с последнего сита направляется на восьмую размольную систему проход всех сит – в готовую муку второго сорта.
Техническая характеристика систем измельчения приведена в приложении Б.
6 Теоретический количественный баланс помола
Баланс помола представляет количественную или качественно-количественную характеристику всех продуктов по технологической схеме помола. различают количественный и качественный балансы. Количественный баланс учитывает только количество продукта в % качественный баланс составляют по следующим показателям: зольность белок клетчатка и т.д. Различают следующие виды баланса: баланс технологической схемы баланс отдельного процесса (драного шлифовочного размольного) полный баланс помола.
Существует качественный баланс помола который снимается на действующем предприятии и теоретический который рассчитывается для проектируемых или реконструируемых мельниц.
На основе баланса помола корректируют режимы на отдельных технологических системах группируют потоки продуктов формируют сорта муки рассчитывают необходимое количество оборудования распределяют его по отдельным системам. Пользуясь балансом можно правильно оценить технологический процесс исправить недостатки и наметить пути дальнейшего его совершенствования. Разработка баланса заключается в уравнении количества продуктов поступивших на систему и уходящих с него.
Баланс помола изображают в виде таблицы-шахматки.
В левой части таблицы вертикально записывают все технологические системы и нагрузки на них в % к первой драной системе.
В верхней строке записывают все системы кроме первой драной а также записывают готовую продукцию.
Количество поступившего на каждую систему продукта записывается в строке против соответствующей системы.
Сумма полученных продуктов по горизонтали должна быть равна количеству поступившего продукта нагрузки по вертикали.
При разработки теоретического количественного баланса руководствуются схемой технологического процесса рекомендациями изложенными в правилах организации и ведения технологического процесса по режимам измельчения на драных шлифовочных и размольных системах для каждого вида помола; извлечению крупок дунстов и муки; распределению продуктов на ситовеечных системах.
Также необходимо знать общие и частные положения технологии мукомольного производства схемы сортирования продуктов в рассевах а также классификацию промежуточных продуктов.
В состав продуктов извлечения входят крупная средняя мелкая крупки жесткий и мягкий дунсты и мука. Нагрузку на I др.с. обычно принимают за 100% поскольку рекомендуемые режимы систем и этапов указаны в процентах по отношению к нагрузке на эту систему. При этом необходимо учитывать что во всех существующих видах помолов выход муки общий и по сортам указан по отношению к количеству зерна базисного качества поступившему на очистку. При выборе режимов систем и этапов необходимо учитывать стекловидность зерна и вид помола по ассортименту и выходам муки т.к. режимы дифференцированы по указанным признакам.
Особенностью методики является то что количество поступающего на первую драную систему зерна принимают за 100% хотя 29% при сортовых помолах пшеницы или 34% при ржаных помолах остается в подготовительном отделении в виде отходов и потерь. То есть на первую драную систему поступает 971% при помоле пшеницы и 966% при помоле ржи. При расчете исходят из базисных показателей качества зерна. Указанная особенность определяет необходимость пересчета запланированных выходов муки и отрубей так чтобы их сумма была равна 100% т.е. количеству зерна поступившему на первую драную систему. Потерями в размольном отделении в результате усушки пренебрегают.
Перед тем как приступить к разработки баланса важно учесть наличие заворотов то есть продуктов возвращаемых с последних систем на предыдущие. Так например схода с ситовеечных машин после обогащения крупной и средней крупок возвращаются на третью драную систему мелкую. Схода с контрольных рассевов возвращаются на размольные системы. Количество подобных заворотов для разных схем помола разное все их необходимо выявить в схеме и вписать в таблицу-шахматку предполагаемую массу заворотов в соответствующие системы.
Количество сходового продукта с контрольных рассевов не должно превышать 5% от поступающего продукта.
Количественный баланс помола мукомольного завода представлен в приложении Б.
Выход муки – 78% высший сорт – 15% I сорт – 50% II сорт – 13% отруби – 191%.
В размольное отделение поступает 971% следовательно:
Таким образом после контроля муки выход высшего сорта должен составить - 1544% первого сорта - 5149% второго сорта – 1339 % отрубей должно получиться – 1967%.
7 Расчет оборудования размольного отделения мукомольного завода
7.1 Расчет вальцовой линии
Найдем общую длину вальцовой линии lо см по формуле (9):
где qо – общая удельная нагрузка вальцовой линии для конкретного помола кгсмсут [4].
Расчетное значение длины вальцовой линии lр.п. каждой конкретной системы определяем в соответствие с формулой (10):
где Qзад – заданная производительность мукомольного завода тсут;
Сп – количество продукта из баланса поступающего на конкретную систему %;
qв.п. – удельная нагрузка на 1 см длины вальцовой линии конкретной системы кгсут [4].
Для I драной системы:
Для II драной системы:
Для III драной системы крупной:
Для III драной системы мелкой:
Для IV драной системы крупной:
Для IV драной системы мелкой:
Для 1 шлифовочной системы:
Для 2 шлифовочной системы:
Для 1 размольной системы:
Для 2 размольной системы:
Для 3 размольной системы:
Для 4 размольной системы:
Для 5 размольной системы:
Для 6 размольной системы:
Для 7 размольной системы:
Для 8 размольной системы:
Для 9 размольной системы:
Для 10 размольной системы:
Для 11 размольной системы:
Число вальцовых станков находят по формуле (11):
lв.ст. – длина мелющей линии вальцового станка см.
Принимаем длину вальцов вальцовых станков 400 мм или 40 см и производим расчет по формуле (10) получаем:
для шлифовочных систем:
для размольных систем:
Данные по расчету и подбору вальцовых станков
Удельная нагрузка на систему по норме кг(смсут)
Принятая величина удельной нагрузки на систему кг(смсут)
Расчетная длина вальцовой линии см
Фактическая длина вальцовой линии мм
Согласно расчета принимаем 13 вальцовых станков марки ВМ-2П. Техническая характеристика приведена в Приложении А9.
Правильность расчетов и подбора вальцовых станков проверяют вычисляя фактическую удельную нагрузку qф по формуле (12):
где lо.ф. – суммарное значение длины мелющей линии выбранных вальцовых станков см.
Таким образом мы видим что вальцовые станки подобраны правильно так как приближается к .
Вальцовые станки предназначены для измельчения зерна и промежуточных продуктов злаковых культур на мукомольных и крупяных предприятиях. Измельчение осуществляется в клиновидном пространстве образованном поверхностями двух цилиндрических параллельных вальцов вращающихся с разными скоростями на встречу друг другу.
Вальцовый станок применяют в составе комплексного оборудования на мукомольных заводах с увеличенным выходом муки высоких сортов.
7.2 Расчет бичевых машин
Число бичевых машин определяют исходя из количества продукта по теоретическому количественному балансу (%) направляемого на эту машину и часовой производительности машин (тч) по формуле 13 :
где Qзад – производительность мукомольного завода тсут;
qм – производительность машины тч.
Принимаем бичевую машину МБО-3 с производительностью 25 тч получаем:
Согласно технологической схемы размольного отделения принимаем три машины МБО-3. Техническая характеристика приведена в Приложении А10.
Бичевая машина МБО-3 предназначена для предварительного сортирования продуктов измельчения зерна после вальцовых станков (снижают нагрузки на рассевы I II III драных систем) и дополнительного отделения остатков эндосперма от оболочек при сортовых помолах пшеницы (снижают нагрузки на вальцовые станки последующих систем) [5].
7.3 Расчет просеивающей поверхности
Находим общую просеивающую поверхность Fо м2 по формуле (13):
где qо – общая удельная нагрузка на просеивающую поверхность кгсмсут [4].
Расчетное значение просеивающей поверхности по каждой конкретной системе рассчитывается по формуле:
qр.п – удельная нагрузка на просеивающую поверхность кгм2сут [4].
Для сортировочных систем:
Для шлифовочных систем:
Для размольных систем:
Принимаем рассев ЗРШ-4М. Его просеивающая поверхность 17 м2. Площадь одной секции рассева - 425 м2.
Расчет количества рассевов.
Принимаем секцию рассева.
Принимаем 12 секцию рассева.
Принимаем 14 секцию рассева.
Принимаем 24 секцию рассева.
Расчет и подбор рассевов
Удельная нагрузка на систему кгм2сут
Принятая величина удельной нагрузки кгм2сут
Расчетная величина просеивающей пов. м2
Фактическая величина просеивающей поверхности м2
Просеивающая пов. ЗРШ-4М м2
Согласно расчету принимаем 8 рассевов марки ЗРШ-4М. Техническая характеристика приведена в Приложении А11.
Правильность расчета просеивающей поверхности проверяем по фактической удельной нагрузке qф по формуле (15):
где Fф – фактическое суммарное значение площади просеивающей поверхности всех систем технологического процесса м2.
7.4 Расчет ситовеечных машин
Ширину приемного сита Вс (см) ситовеечной машины при обогащении крупок различной крупности и качества рассчитывают по формуле (14):
Результаты по расчету и подбору ситовеечных машин для каждой системы приведен в таблице 5.
Расчет и подбор ситовеечных машин
Поступа-ющий продукт
Количест-во поступаю-щего продукта %
Удельная нагрузка на 1 см ширины приемного сита кг(смсут)
Приня-тая удель-ная нагруз-ка кгсм
Расчет-ная ширина прием-ного сита см
Фактичес-кая ширина приемно-го сита см
Согласно технологической схемы принимаем 7 ситовеечных машин марки А1-БСО [4]. Техническая характеристика приведена в Приложении А12.
Технологическая схема подготовительного отделения.dwg

Технологическая схема подготовительного отделения мукомольного завода
Дозаторы ДВТ-ТАУ-100ВП
Смесительный шнек РС-КВ-2-150
Весы автоматические АД-50-3Э
Воздушно-ситовой сепаратор А1-БМС-6
Камнеотделительная машина РЗ-БКТ
Триер-куколеотборник А9-УТК-6
Триер-овсюгоотборник А9-УТО-6
Обоечная машина РЗ-БГО-6
Магнитный сепаратор У1-БМЗ-01
Виброувлажнительная машина V7.5S
Воздушный сепаратор А1-БДА
Условные обозначения:
Кормовые зерноотходы
кормовые зерноотх. (куколь)
кормовые зерноотх. (овсюг)
Бункера для отволаживания
Аспирационная сеть №5
Аспирационная сеть №7
Аспирационная сеть №4
Аспирационная сеть №8
Аспирационная сеть №3
Аспирационная сеть №2
Бункер для кормовых зерноот- ходов
Аспирационная сеть №1
на комбикормовое производство
На комбикормовое производство
Бункера для кормовых зернопродуктов
Аспирационная сеть №6
Приложение Г.dwg

Бункера для неочищенного зерна
Весы автоматические АД-50-3Э
Воздушно-ситовой сепаратор А1-БМС-6
Камнеотделительная машина РЗ-БКТ
Триер-куколеотборник А9-УТК-6
Триер-овсюгоотборник А9-УТО-6
Обоечная машина РЗ-БГО-8
Концетратор А1-БЗК-9
Магнитный сепаратор У1-БМЗ-01
Виброувлажнительная машина V7.5S
Воздушный сепаратор А1-БДА
Условные обозначения:
Кормовые зерноотходы
кормовые зерноотх. (куколь)
кормовые зерноотх. (овсюг)
Обоечная машина РЗ-БГО-6
Бункера для отволаживания
Рабочая схема размольного отделения мукомольного завода
Приложение Г (обязательное) Схема размольного отделения с указанием продуктов размола
рабочая размольное.dwg

Бункера для неочищенного зерна
Весы автоматические АД-50-3Э
Воздушно-ситовой сепаратор А1-БМС-6
Камнеотделительная машина РЗ-БКТ
Триер-куколеотборник А9-УТК-6
Триер-овсюгоотборник А9-УТО-6
Обоечная машина РЗ-БГО-8
Концетратор А1-БЗК-9
Магнитный сепаратор У1-БМЗ-01
Виброувлажнительная машина V7.5S
Воздушный сепаратор А1-БДА
Условные обозначения:
Кормовые зерноотходы
кормовые зерноотх. (куколь)
кормовые зерноотх. (овсюг)
Обоечная машина РЗ-БГО-6
Бункера для отволаживания
Рабочая схема размольного отделения мукомольного завода
5400 n=10 у=8% К=2 V=5
Рекомендуемые чертежи
- 24.01.2023
- 24.01.2023
- 17.05.2023