Проектирование заготовок




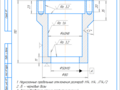
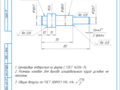
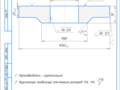
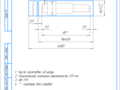
- Добавлен: 24.01.2023
- Размер: 218 KB
- Закачек: 1
Описание
Состав проекта
![]() |
![]() ![]() ![]() ![]() |
![]() ![]() ![]() |
![]() ![]() ![]() ![]() |
![]() ![]() ![]() |
![]() ![]() ![]() ![]() |
![]() ![]() ![]() ![]() |
![]() ![]() ![]() ![]() |
![]() ![]() ![]() ![]() |
- Архиватор zip файлов
- Компас или КОМПАС-3D Viewer
- Microsoft Word
Дополнительная информация
Вал заготовка.cdw

Минимальное значение некратности 11
* - размеры для справок
Сводная таблица результатов расчёта размеров поковки.docx
Размер поковки с припуском
Для размеров в плоскости разъёма
Допуск размера поле допуска
Размер горячей поковки
Длина горизонтальных отрезков
*((3282)*tg10°) = 58
Корпус.cdw

Термообработка: отжиг графитизирующий
╧ЁюхъЄшЁютрэшх чруюЄютюъ.doc
ГОСУДАРСТВЕННОЕ ОБРАЗОВАТЕЛЬНОЕ УЧРЕЖДЕНИЕ
ВЫСШЕГО ПРОФЕССИОНАЛЬНОГО ОБРАЗОВАНИЯ
САМАРСКИЙ ГОСУДАРСТВЕННЫЙ ТЕХНИЧЕСКИЙ УНИВЕРСИТЕТ
Кафедра «Технология машиностроения»
«Проектирование заготовок»
Вариант №02 (отливка)
(подпись) (инициалы и фамилия)
(должность) (подпись и дата)(инициалы и фамилия)
Страниц 20 рисунков 9 таблиц 3 источников 2 4 листа графического материала формата А4 2 листа графического материала формата А3.
ДЕТАЛЬ ЗАГОТОВКА ПРОКАТ ШТАМПОВКА СОРТАМЕНТ НЕКРАТНОСТЬ ДЛИНЫ ТОРГОВАЯ ДЛИНА КОЭФФИЦИЕНТ ИСПОЛЬЗОВАНИЯ МАТЕРИАЛА НОРМА РАСХОДА ТЕХНОЛОГИЧЕСКАЯ СЕБЕСТОИМОСТЬ ПРЕСС КЛАСС ТОЧНОСТИ ГРУППА СТАЛИ РАСЧЁТНАЯ МАССА СТЕПЕНЬ СЛОЖНОСТИ ИСХОДНЫЙ ИНДЕКС ПЛОСКАЯ ПЕРЕМЫЧКА.
В данной контрольной работе спроектированы три заготовки: круглый стальной прокат отливка и поковка штампованная.
Проектирование заготовки из круглого стального проката 5
Проектирование отливки в разовой песчаной форме 9
Проектирование поковки штампованной 15
В машиностроении основными видами заготовок для деталей являются штамповки из черных и цветных металлов и сплавов и различные профили проката.
Основным показателем характеризующим экономичность выбранного метода получения заготовок является коэффициент использования материал (КИМ) выражающий отношение массы детали к норме расхода металла на деталь.
Способ получения заготовки должен быть наиболее экономичным при заданном объеме выпуска деталей. Технико-экономическое обоснование выбора заготовки для обрабатываемой детали производят по нескольким направлениям: металлоемкости трудоемкости и себестоимости учитывая при этом конкретные производственные условия. Технико-экономическое обоснование ведется по двум или нескольким конкурирующим вариантам в следующем порядке:
– устанавливают метод получения заготовки согласно типу производства конструкции детали материалу шероховатости необрабатываемых поверхностей и другим техническим требованиям на изготовление детали;
– назначают припуски на обрабатываемые поверхности детали согласно выбранному методу получения заготовки по нормативным таблицам соответствующих стандартов или производят расчет аналитическим методом при наличии маршрута обработки;
– определяют расчетные размеры на каждую поверхность заготовки;
– назначают предельные отклонения на размеры заготовки по нормативным таблицам в зависимости от метода ее получения;
– производят расчет массы заготовки на сопоставляемые варианты;
– определяют норму расхода материала с учетом неизбежных технологических потерь для каждого вида заготовки (на литниково-питающую систему прибыли угар облой некратность и т. п.);
– определяют коэффициент использования материала по каждому из вариантов изготовления заготовок с технологическими потерями и без потерь;
– определяют себестоимость изготовления заготовки по каждому из вариантов изготовления для сопоставления и определения экономического эффекта получения заготовки;
– определяют годовую экономию материала по сопоставляемым вариантам получения заготовки;
– определяют годовую экономию от выбранного варианта заготовки в денежном выражении.
Проектирование заготовки из круглого стального проката
По конструкторскому чертежу и заданию определяем размеры заготовки по формулам (1) и (2) и допускаемые отклонения на диаметр и длину заготовки (см. прил. 1.1-1.3).
Диаметр проката определяется исходя из диаметра наибольшей ступени вала к нему прибавляют общий припуск на механическую обработку 2Z0 определяемый по табл. П1.1.1 в зависимости от отношения всей длины вала L к диаметру его наибольшей ступени Dmax (LDmax) [1]:
Dз = Dд max + 2Z0 (1)
где 2Z0 – припуск на обработку в диаметральном выражении на диаметр наибольшей ступени детали мм.
По расчетному диаметру заготовки Dз и прил. 1.2 из сортамента [2] подбираем ближайший наибольший диаметр круглого стального проката назначаем точность прокатки (В) и определяем предельные отклонения диаметра заготовки.
Затем определяем длину заготовки. По табл. П1.1.2 назначаем двусторонний припуск на обработку обоих торцов детали. Тогда длина заготовки Lз составит:
где 2Z0 – двусторонний припуск на обработку торцов заготовки мм [3].
Определяем общие потери металла (формула 3) массу заготовки (формула 13) норму расхода металла (формула 11).
Предельные отклонения на длину заготовки зависят от способа резки проката на штучные заготовки и определяются по табл. П1.3.1.
Принимаем: 96±08 мм.
Общие потери материала Побщ на деталь изготавливаемую из проката состоят из потерь на некратность торговой длины проката длине заготовки Пнк на торцовую обрезку Пто на зажим Пзаж опорных концов и на отрезку Потр в виде стружки при разрезании:
Побщ = Пнк + Пто + Пзаж + Потр (3)
Некратность длины заготовки определяется исходя из торговой длины проката и длины заготовки с учетом потерь от выбранного метода заготовительного раскроя. Средневероятностная расчетная длина некратности при раскрое немерного проката составляет примерно половину длины заготовки.
В соответствии с [2] торговая длина проката выбирается в интервале 2-6 метров для качественных конструкционных сталей по ГОСТ 1050-88. При расчёте некратности необходимо стремиться к минимальным величинам.
Определяем диапазон торговых длин проката исходя из марки материала по п. 8 прил. 1.2. Для выбранного диапазона торговых длин с шагом в 1000 мм находим целое число заготовок (формула 5) и потери на некратность (формула 7) для каждой торговой длины. Окончательно выбираем ту торговую длину для которой потери на некратность наименьшие.
Длина торцового обрезка зависит от размеров сечения проката и при резке ножовочной пилой обычно составляет:
Lто = (03 05)*D3 (4)
где Dз = 27 – диаметр проката мм.
Lто = (03 05)*27 = 03*27 = 81 мм
Число заготовок изготавливаемых из принятой длины проката:
где Lпр – торговая длина проката из сортамента (2000-6000);мм;
Lзаж = 40 – минимальная длина опорного (зажимного) конца проката выбираемая по табл. П1.1.2 мм;
Lр = 25 – ширина реза выбираемая по табл. П1.1.2 мм;
Lз = 96 – длина заготовки мм.
Некратность в зависимости от принятой длины проката:
Lнк = Lпр – Lто – Lзаж – n*(Lз + Lр) (6)
где Lнк – величина некратности длины заготовки торговой длине проката Lпр мм;
n – целое число заготовок изготавливаемых из принятой торговой длины проката шт.
Для Lпр = 2000 ммLнк = 2000 – 81 – 40 – 19*(96 + 25) = 804
Для Lпр = 3000 ммLнк = 3000 – 81 – 40 – 29*(96 + 25) = 954
Для Lпр = 4000 ммLнк = 4000 – 81 – 40 – 40*(96 + 25) = 119
Для Lпр = 5000 ммLнк = 5000 – 81 – 40 – 50*(96 + 25) = 269
Для Lпр = 6000 ммLнк = 6000 – 81 – 40 – 60*(96 + 25) = 419
Потери материала на некратность %:
Потери на торцовую обрезку проката %:
Потери на зажим опорного конца проката при выбранной длине зажима %:
Потери на отрезку заготовки при выбранной по табл. П1.1.2 ширине реза %:
Побщ = 030% + 020% + 10% + 006% = 156%
Норма расхода материала на деталь с учетом всех потерь:
Vз = 314*135 2 *96 = 54937 мм 3 = 55 см 3
Масса заготовки составляет:
где ρ = 7850 кг м 3 = 785 кг см 3 – плотность материала (сталь);
Мз = 55*785 = 431 г = 0431 кг
КИМ = (016*100%)0438 = 37%
В зависимости от выбранного способа резки проката по формулам (15; 14) определяем tмаш и tшт.к а также технологическую себестоимость заготовительных операций (формула 16).
Штучно-калькуляционное время приближенно определяется в виде:
tшт.к. = tмаш* φк (14)
где tмаш – машинное время при разрезании заготовки мин;
φк – коэффициент равный 184 для условий единичного и мелкосерийного производства.
По данным [3] [7] приближенная формула для расчета tмаш при разрезании ножовочной пилой:
tмаш = 00877*Dз (15)
tмаш = 00877*27 = 237 мин
tшт.к. = 237*184 = 436 мин
Технологическая себестоимость i-той заготовительной операции:
i = 2 – резка и правка.
tшт.к.i – штучно-калькуляционное время выполнения i-той заготовительной операции мин.
Определяем стоимость См материала заготовки (формула 17).
Затраты на материал заготовки См определяются по массе проката расходуемой на изготовление детали и массе возвращаемой в виде отходов (стружки):
где С = 18905 – цена 1 т материала заготовки рубт [4];
Сотх = 10% от С = 18905 – цена 1 т отходов материала рубт [5];
Мн Мд – норма расхода и масса детали кг.
Стоимость заготовок из проката определяется выражением:
где См – затраты на материал заготовки руб;
n – число заготовительных операций.
Сз = 775 + 570 = 1345 руб.
Вычерчиваем на формате А4 два графических документа: чертеж детали выполненный в соответствии с вариантом задания и чертеж заготовки выполненный по результатам расчетов.
Проектирование отливки в разовой песчаной форме
Заготовки получают путём заливки жидкого металла в формы. Основные способы изготовления отливок – литьё в разовые песчано-глинистые формы (ПГФ) в оболочковые формы в кокиль по выплавляемым моделям центробежное литьё литьё под давлением. Последние пять способов называют специальными. Литье в разовые песчаные формы – самый распространенный способ литья с помощью которого в машиностроении изготавливают 75-80% отливок.
В современных литейных цехах технологический процесс изготовления отливок разделяется на отдельные операции осуществляемые коллективом литейщиков различных профессий: формовщиками стерженщиками сборщиками форм плавильщиками обрубщиками термистами контролерами и др. В формовочное отделение поступают модели опоки и формовочные смеси для изготовления полуформ. При сырой формовке полуформы после изготовления поступают на сборку минуя операцию сушки. Сборка форм состоит в проверке качества формы установке стержней соединении и скреплении нижней и верхней половин формы. Собранные формы поступают на заливку куда из плавильного отделения в специальных ковшах подается расплав. После затвердевания и охлаждения отливок формы разрушают отливки поступают в очистное отделение а выбитая из опок смесь возвращается в смесеприготовительное отделение. В отделении очистки и обрубки из отливок выбивают стержни очищают отливки от приставшей формовочной смеси и удаляют с их поверхности заусенцы и заливы. Затем если необходимо отливки подвергают термической обработке и после контроля размеров механических свойств и химического состава передают на склад литья откуда они поступают в механический цех на обработку.
Исходным документом для проектирования является рабочий чертеж детали. Деталь представляет собой корпус. Материал – чугун серый СЧ20 ГОСТ 1412-85 масса 231 кг. Термообработка – отжиг графитизирующий. Производство мелкосерийное (Nгод = 1000 шт.) механизированное.
Анализ чертежа детали на соответствие требованиям литейной технологии.
Исходя из задания необходимо изготовить стальную отливку средней сложности группа сложности вторая. В условиях мелкосерийного типа производства наиболее экономичным способом изготовления является литьё в разовые песчаные формы. Способ формовки – машинная формовка по разъёмной модели в двух опоках с уровнем уплотнения до твердости формы не ниже 70 единиц. Анализ технических требований и технологичности конструкции детали показывает что она является симметричным телом вращения; наружные поверхности диаметром D = 100 мм D1 = 80 мм переходный конус под углом 45° и нижний торец детали не подлежат механической обработке; наиболее точная поверхность диметром d = 60 мм (база А) выполнена по 8 квалитету точности верхний торец корпуса связан с базой А допуском торцового биения поверхность внутреннего отверстия (d+a) = 70 мм связана с базой А допуском соосности неуказанные предельные отклонения размеров выполнены по 14 квалитету. Минимальная толщина стенок 7 8 мм может быть получена выбранным способом литья. Восемь отверстий М10 не имеет смысла получать литьём они являются напуском. Чугун имеет низкую жидкотекучесть и большую объёмную усадку склонен к образованию горячих трещин. Поэтому целесообразно всю отливку расположить в нижней полуформе вертикально совместив плоскость разъёма формы с её верхним торцом; подводить металл к отливке следует сверху способствуя её направленному затвердеванию и питанию. На массивных верхних частях отливки для питания расплавом необходимо предусмотреть прибыль. Стержнем в отливке будут получены две внутренние цилиндрические поверхности под последующее растачивание в размеры 60H8 и 50H10. Получить стержнем внутреннюю цилиндрическую поверхность глубиной 23 мм под последующее растачивание в размер 70H10 не представляется возможным так как на этом участке уменьшается толщина стенки и затрудняется питание более массивной части отливки расположенной ниже что может вызвать образование усадочной раковины. В качестве черновых баз механической обработки целесообразно принять нижний торец корпуса и цилиндрическую поверхность диаметром D1 = 80 мм реализуя таким образом явную установочную базу по торцу и двойную опорную скрытую базу по цилиндру.
Назначение норм точности отливки.
Пользуясь методическим пособием назначаем нормы и показатели точности отливки (см. табл. 3.3). Принимая во внимание следующие данные: средняя сложность отливки мелкосерийное механизированное производство материал отливки – чугун серый термообрабатываемый с наибольшим габаритным размером лежащим в интервале 100 - 250 мм по табл. П3.2.1 выбираем диапазон классов размерной точности 9т - 13 а с учетом прим. 1 окончательно принимаем класс размерной точности отливки 11 (КР11). По табл. П3.3.1 определяем степень коробления отливки по её элементу с наибольшей степенью коробления. Таким элементом является внутренний цилиндр (d = 60 мм L = 110 мм). Для отношения dL = 055 с учетом разовой формы и термообработки отливки попадаем в интервал 4 - 7 а в соответствии с прим. 1 принимаем 6-ю степень коробления (СК6). Степень коробления отливки в целом принимается по наибольшему значению степени коробления её элемента. По табл. П3.4.1 определяем диапазон степени точности поверхностей отливки 12 - 19 и с учетом примечания окончательно выбираем 15-ю степень точности поверхностей (СП15). По табл. П3.6.1 определяем значение шероховатости поверхностей отливки для 15-й степени точности её поверхностей Ra = 20 мкм; допуск неровностей по табл. П3.7.1 составляет 12 мкм поля допусков (±06 мкм).
По табл. П3.5.1 определяем диапазон классов точности массы отливки 7 - 15 и с учетом примечания принимаем класс точности массы 11т (КМ11т) допуск массы (%) назначаем по табл. П3.7.2 после определения припусков размеров объёма и массы отливки. Допуск смещения отливки по плоскости разъёма не назначаем так как вся отливка располагается в нижней полуформе. По табл. П3.8.1 для 15-й степени точности поверхностей отливки расположенных при заливке снизу или вертикально принимаем 8-й ряд припусков (РП8) а для поверхностей расположенных при заливке сверху принимаем 10-й ряд припусков. Результаты анализа и найденные показатели точности изготовления отливки вносим в карту проектирования техпроцесса (табл. 1).
Карта проектирования техпроцесса
Материал термообработка
Чугун серый СЧ20 ГОСТ 1412-85 отжиг графитизирующий
Литьё в разовые песчано-глинистые формы
Способ формовки твердость формы после уплотнения
Машинная формовка в двух опоках по разъёмной модели до твердости после уплотнения не ниже 70 единиц
Нормы точности отливки по ГОСТ 26645-85
Класс размерной точности отливки
Степень коробления отливки
Степень точности поверхностей
Класс точности массы отливки
Допуск смещения по плоскости разъёма формы в диаметральном выражении мм
Шероховатость поверхности отливки мкм
Допуск неровностей поверхности отливки
Уровень точности обработки
Проектирование поковки штампованной
Современная структура продукции КШП в машиностроении примерно такова: кованые поковки изготовляемые из слитков – 16% из проката – 14% штампованные поковки – 70%. Замена ковки прогрессивными методами штамповки вальцовки прокатки позволяет максимально приблизить форму и размеры поковок к контурам готовых деталей и тем самым более экономно расходовать металл за счёт снижения отходов в стружку в процессе обработки резанием. При этом высвобождается значительная часть парка металлорежущих станков снижаются затраты легированной стали расходуемой на изготовление режущего инструмента сберегаются энергоресурсы. Кроме того следует учесть что в процессе штамповки обрабатываемый металл претерпевает не только наружные (контурные) но и внутренние (структурные) изменения способствующие повышению прочности деталей по сравнению с изготовленными обработкой резанием или методами литья.
Форма поковки определяется конфигурацией детали и принятым способом штамповки. Все элементы штампованной поковки должны иметь простую геометрическую форму и плавно сопрягаться друг с другом.
При отработке конструкции штампованной поковки на технологичность следует проверить возможность изменения конструкции детали или её элементов с целью упрощения конструкции поковки. Необходимо проверять возможность получения поковки в закрытом ручье вместо открытого или перевода штамповки с молота на другие кузнечные машины применения комбинированных способов изготовления поковки (вальцовка-штамповка на молоте или прессе и другие). Для уменьшения расхода металла и упрощения штамповки иногда рационально разбить деталь на две и более частей простой формы для штамповки их порознь с последующей сваркой. Для мелких поковок более выгодна штамповка двух и более заготовок в одной поковке с последующей разрезкой. С целью уменьшения стоимости технологической оснастки необходимо стремиться к унификации поковки для различных деталей применению групповых поковок.
Заготовка детали «Фланец» относится к группе штампованных поковок симметричных в плане. Такие поковки изготовляют штамповкой вдоль оси (в торец). Материал - жаропрочная низколегированная сталь 15ХМ ГОСТ 4543-71 с содержанием углерода 011 – 018% и легирующих элементов 244%. Термообработка – нормализация. Группа поковки - II по ГОСТ 8479-71. Тип производства – мелкосерийный при m = 319 кг и объёме выпуска NГ = 1000 штгод. Штамповочное оборудование по заданию - кривошипный горячештамповочный пресс (КГШП) закрытый. В условиях мелкосерийного производства поковок экономически оправдано применение пламенного нагрева заготовок. Исходные данные вносим в карту проектирования технологического процесса (табл. 3).
Годовой объём выпуска шт.
Сталь 15ХМ ГОСТ 4543-71 нормализация
Группа поковки по ГОСТ 8479-71
Штамповочное оборудование
Кривошипный горячештамповочный пресс (КГШП)
Способ нагрева исходной заготовки
Разработка технологических переходов штамповки
Изобразим эскизы технологических переходов для нашего варианта штамповочного оборудования способа штамповки и размеров детали.
Определение исходного индекса поковки
Для определения исходного индекса вычислим конструктивные характеристики и расчетную массу поковки.
Класс точности поковки. По табл. 2.2 для закрытой штамповки на КГШП при пламенном нагреве рекомендуется класс точности Т4.
Группа стали. Материал поковки – сталь 15ХМ. Массовая доля углерода в этой марке – 011 018% суммарная массовая доля легирующих элементов – свыше 2% до 5% (244%). Устанавливаем группу стали М2.
Расчетная масса поковки. По формуле (2.6) и табл. П2.3.1 расчетная масса поковки
где Мд = 319 кг - масса детали;
= 15 18 - коэффициент зависящий от формы поковки (табл. П2.3.1).
Мпр = 319*15 = 479 кг.
Степень сложности поковки. Определим отношение tD для нашего варианта размеров: 20160 = 0125 02 – то есть поковка содержит тонкий элемент t 25 мм. Поэтому для таких поковок с тонкими элементами и пробиваемыми перемычками стандартом устанавливается степень сложности С4.
Исходный индекс поковки. По табл. 2.4 устанавливаем исходный индекс поковки 15.
Расчёт размеров поковки
Размер D: основной припуск 20 мм (D = 160 мм; Ra =125 мкм; исходный индекс поковки 15); смещение по плоскости разъёма штампа 03 мм (Мпр = 479 кг; класс точности Т4); суммарный припуск на сторону 23 мм (20 + 03); размер поковки 1646 мм (160 + 23*2).
Размер d: основной припуск 25 мм (d = 50 мм; Ra = 08 мкм; исходный индекс поковки 15); смещение по плоскости разъёма штампа 03 мм (Мпр = 479 кг; класс точности Т4); суммарный припуск на сторону 28 мм (25 + 03); размер поковки 444 мм (50 – 28*2).
Размер D1: припуск не назначают так как по этому размеру нет механической обработки.
Размер Т - толщина: основной припуск 23 мм (Т = 30 мм; Ra = 16 мкм; исходный индекс поковки 15); отклонение от плоскостности 05 мм (наибольший размер поковки 1674 мм; класс точности Т4); суммарный припуск на сторону 28 мм (23 + 05); размер поковки 328 мм (30 + 28).
Размер t - толщина: основной припуск 20 мм (t = 20 мм; Ra = 16 мкм; исходный индекс поковки 15); отклонение от плоскостности 05 мм (наибольший размер поковки 1674 мм; класс точности Т4); суммарный припуск на сторону 25 мм (20 + 05). Положение нижнего торца поковки определяется двумя размерами T и t с разными припусками. В соответствии с п. 4.5 ГОСТ 7505-89 необходимо установить наибольшее значение припуска на эту поверхность 28 мм: тогда размер поковки 228 мм (20 + 28).
Штамповочные уклоны назначают по табл. 2.8 на все поверхности расположенные параллельно направлению движения деформирующего инструмента: на наружной поверхности - 7° на внутренней - 10°.
Толщину плоской перемычки S определим по табл. 2.9-2.10 и рис. 2.9.
ds = 05*(d1 + d2) = 05*(D1 + D) (20)
ds = 05*(80 + 160) = 120 мм
Tпок ds = 328120 = 027 ≤ 3 значит S = 8 мм
Назначаем по табл. 2.11 радиусы закруглений наружных углов поковки: 25 мм; радиусы внутренних углов поковки рассчитываем по формуле: r = 2*R = 2*25 = 5 мм.
В закрытом штампе не будет облойной канавки.
В результате в данной контрольной работе спроектированы три заготовки: круглый стальной прокат отливка и поковка штампованная.
Проектирование заготовок в машиностроении: учеб. пособ. В.А. Дмитриев. – Самара: Самар. гос. техн. ун-т 2008. – 174 с.: ил.
Обоснование метода получения заготовок: Метод. указ. к курсовому и дипломному проектированию Сост. В.А. Дмитриев. – Самара; Самар. гос. техн. ун-т 2010. – 25с.: ил.
Корпус заготовка.cdw

Формовочные уклоны за счёт увеличения и уменьшения размеров
отливки: поверхность Б - 1
Неуказанные литейные радиусы R 2 3 мм.
Точность отливки: 11 - 6 - 15 - 11т ГОСТ 26645-85.
ГОСТ 26645-85. Допуск массы
Термообработка - отжиг графитизирующий.
Фланец заготовка.cdw

Сталь 15ХМ ГОСТ 4543-71
Поковка ГрII НВ 143-179 ГОСТ 8479-71. Класс точности Т4
степень сложности С4
Допускаемая величина смещения по поверхности разъема
Допускаемая величина высоты заусенца по внешнему контуру
Допускаемое отклонение от концентричности пробитого
отверстия относительно внешнего контура поковки 1
Допускаемое отклонение от плоскостности 1
Очистка от окалины дробеструйная.
На обрабатываемых поверхностях допускаются внешние дефекты
не более 50% припуска.
(толщина поковки) калибровать 30±0
Фланец.cdw

Термообработка - нормализация
Неуказанные предельные отклонения размеров: Н14;
Вал.cdw

Центровые отверстия по форме С ГОСТ 14034-74
Размеры канавок для выхода шлифовального круга условно не
Общие допуски по ГОСТ 30893.1:
Рекомендуемые чертежи
- 25.10.2022