Проектирование вала



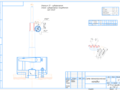
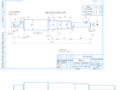
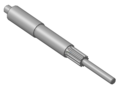
- Добавлен: 24.01.2023
- Размер: 501 KB
- Закачек: 0
Описание
Состав проекта
![]() |
![]() |
![]() ![]() ![]() ![]() |
![]() ![]() ![]() ![]() |
![]() ![]() |
![]() ![]() ![]() |
Дополнительная информация
Валик с колесом зубчатым.cdw

Наладка.cdw

Станок: зубофрезерный полуавтомат
Схема технологической
Вал 3D.m3d

ОТМС .doc
Белгородский государственный технологический университет
Конструкция и назначение детали.3
Назначение технологических баз.6
Технологический маршрут.7
Технологическая операция.9
Припуски на обработку.10
Режим обработки силы и моменты сил резания.12
Размерные и точностные расчеты технологических процессов.14
Качество поверхности.15
Техническое нормирование 16
Экономическая оценка технологического процесса 18
Список используемой литературы.20
Конструкция и назначение детали.
Деталь является составной частью патрона для зажима материала и предназначена для передачи вращательного движения в возвратно- поступательное на рейку.
Деталь «Вал с колесом зубчатым» является телом вращения с габаритными размерами - 42х412. Наибольший диаметр вала 42 мм а наименьший диаметр 18 мм. Вал выполнен ступенчато. В переходах с одного диаметра на другой оформлены канавки шириной 3 мм и глубиной на 05мм меньше наименьшего диаметра. На валу имеются два центровых отверстия они выполнены с точностью Н9 ОТС 3725. Дальнейшее описание вала произвожу слева на право по участкам: 1 длиной L=39мм и диаметром d=22k6мм слева имеется фаска 2х45° а также на участке есть отверстие диаметром 8p6мм под штифт цилиндрический сверлить и развернуть при сборке 2 L=97мм d=42мм слева имеется фаска 15х45 3 L=110мм d=38f7мм (в переходе с участка 3 на 4 нет тех. канавки) 4 зубчатое колесо L=55мм d=355+01мм: колесо зубчатое с числом зубьев 11 модуль зубьев 25 диаметр делительной окружности 305мм угол зацепления 20° степень точности 4. Ширина зубчатого венца 355мм длина 40мм 5 L=108мм d=18мм а также на участке есть отверстие диаметром 5мм сверлить при сборке(сверлить на небольшую глубину 5мм) и справа имеется фаска 2х45. Ось вала является контролем на соосность для участка 3 отклонения составляют 003мм.
Химический состав стали Сталь 45 ГОСТ 1050-88 . Это сталь углеродистая конструкционная. содержание С 042 05% Si 017 037% Мп 05 08%. Твердость без ТО НВ не более 229.
Требования к точности и шероховатости всех функциональных поверхностей указаны на чертеже и составляют 25 микрометров. Все остальные поверхности обладают шероховатостью 125 микрометров.
Твердость составляет 35 40 единиц по шкале HRC. Зубчатое колесо закаливается отдельно токами ТВЧ на глубину h=08 12мм твердость составляет 45 50 единиц по шкале HRC
Масса детали G=265кг.
Тип производства устанавливают в зависимости от номенклатуры и объема выпуска изделий в год их массы и габаритных размеров а также других характерных признаков.
С учетом годовой программы N = 6000и массы детали М=265 по табл.1[1] примем тип производства серийным и рассчитаем для условий серийного производства размер партии одновременно обрабатываемых заготовок предварительно допустив что для бесперебойной работы сборочного цеха должен быть запас готовых деталей на 10 дней тогда:
n=a×N254=10×6000254=236
a- периодичность запуска (необходимость запаса деталей) дней
N- годовая программ выпуска изделий шт.
Принимаем n=250Соразмерив величину n с таблицей 2 [1] будем считать производство крупносерийным.
Рассчитаем такт выпуска:
tв=60×FдN=60×40156000=40 мин
Fд- действительный фонд рабочего времени ч (две смены)
Принимая во внимание конфигурацию детали у которой большая разница размеров поперечного сечения - ø42 и продольного 412 - и материал Сталь 45 ГОСТ 1050-88 выбираем метод обработки давлением. Учитывая тип производства крупносерийным выбираем способ - штамповка на горизонтально-ковочных машинах. Штамповки получаемые на ГКМ позволяют несколько снизить объем механической обработки и обеспечить коэффициент использования материала в пределах hМ=07 075. В случае получения заготовок из проката объем механической обработки резко возрастает а величина hМ падает до 04 и ниже. Преимущество штамповки на ГКМ - высокая производительность и экономное использование металла.
Так как штамповка в открытых штампах то необходимо предусмотреть операцию под отрезку облоя.
Штамповка относится к 1-й группе сложности.
С=МпМФ=125×МдМф=125×151223=0846
Припуски на механическую обработку примем согласно [3] (табл. 21)
Допуски на каждый размер назначим согласно [3] (табл. 23)
C учетом припусков расчетная масса составит 3395 кг.
Ориентировочная стоимость заготовки составит руб. [4]
Sзаг=(Сб×Мз1000)×Кт×Кс×Кв×Км×Кп-(Мз-Мд)×Сотх1000=09
гдеСб- базовая стоимость 1 тонны металла373 р.
Мз- масса заготовки 3395 кг
Мд- масса детали265кг
Кт- к-нт зависящий от точности (с.37)1
Кс- к-нт зависящий от группы сложности 075
Кв- к-нт зависящий от массы (таб. 2.12 с.38)114
Км- к-нт зависящий от марки материала1
Кп- к-нт зависящий от типа производства1
Сотх- цена 1 тонны отходов26 р.
Назначение технологических баз.
Согласно чертежу и техническим требованиям на изготовление детали обработке подлежат следующие поверхности (рис. 1):
Рис. 1. Поверхности заготовки.
и 18 центровое отверстие; 21917 . торцы; 458910111314 наружная цилиндрическая поверхность 2716 фаски 615 отверстие 12 зубчатая поверхность.
Для облегчения базирования заготовки при токарной обработке используем искусственную технологическую базу - центровые отверстия 118 которые оставшись после окончательной обработки детали не будет оказывать существенного влияния на конструкцию детали.
Назначим виды механической обработки и базовые поверхности с учетом шероховатости поверхности. Результаты сведем в таблицу 1.
Название поверхности
Лишение 6 степеней свободы
Фрезерование черновое
Наружная поверхность вала
Точение: черновое чистовое
Лишение 5 степеней свободы
Зубчатая поверхность
Сверление(при сборке)
Технологический маршрут.
Технологический маршрут изготовления детали
Эскиз базирование примечания
Фрезерно-центровальная. 1 Фрезеровать торцы.
Сверлить центровые отверстия.
Фрезерно-центровальный станок МП-78
Предварительная токарная обработка поверхности вала.
Токарно-винторезный станок 16К20РФ3
Чистовая токарная обработка поверхности вала.
См. эскиз к операции №10 (Rz 20)
Фрезеровать 11 зубьев
Зубофрезерный полуавтомат 53А20
Закалка зубчатого колеса до HRC 45-50 и на глубину 08-12
Исправление центровых отверстий.
Шлифовать правое центровое отверстие.
Шлифовать левое центровое отверстие.
Станок для доводки центровых отверстий 3912
Шлифовать поверхность вала
Круглошлифовальный станок 3М150
Контрольные приспособления
Технологическая операция.
Рассмотрим операцию 20-фрезерную на которой согласно технологическому маршруту нарезаются зубья (z=11; m=25; a=20).
С учетом серийности производства деталей операцию можно выполнять на зубофрезерном полуавтомате станке модели 53А20 за один установ соответствующим инструментом - дисковой фрезой.
Операция включает несколько переходов. Заготовка закрепляется в патроне базируясь на ранее обработанные поверхности 1188 и обрабатывается (нарезаются зубья).
Припуски на обработку.
Определим расчетно-аналитическим методом общий и промежуточные припуски необходимые для механической обработки левой опорной шейки вала-шестерни.
В соответствии с технологическим маршрутом выделяем 4 перехода обработки поверхности опорной шейки: заготовка предварительное точение чистовое точение и шлифование. Затем определяем значения составляющих элементов припусков предельные значения размеров и припусков для каждого технологического перехода. Результаты расчетов сводим в табл. 3.
Расчет припусков и предельных размеров по технологическим
переходам на обработку поверхности 22k6 вала-шестерни. Таблица 3
По чертежу и техническим требованиям к заготовке Rz=150 мкм;h=250 мкм;
= 300 мкм ; =250 мкм; =500 мкм =634 мкм
Для черновой токарной обработки:
Rz=100 мкм; h=100 мкм;=37 мкм;
Для чистовой токарной обработки
Rz=25 мкм; h=25 мкм;=00925 мкм;
Rz=5 мкм; h=20 мкм;=00046 мкм.
Внесем исходные данные в таблицу и рассчитаем величину минимальных припусков мкм:
zimin=2(Rzi-1+hi-1+)
Для чистовой токарной обработки:
Проверка правильности выполненных расчетов:
zобщmax=2zобщmin+(Тзаг-Тдет)
zобщmax-2zобщmin=Тзаг-Тдет
25185-2642185=(2000-17)
rкор = 01 × 15=15 мкм » 00015 мм.
Заполнив табл. 3 строим схему расположения припусков и допусков
Режим обработки силы и моменты сил резания.
Установить режим обработки рассчитать силы резания и необходимую мощность станка для операции 20. Операция 20-фрезерная. Выполняется на горизонтально-фрезерном станке модели 53А20.
Глубина резания t=52 мм. Подачу примем по [3] Sz=252 мммин.
Эту подачу обеспечивает горизонтально-фрезерный станок модели 53А20.
где Сv-коэффициент скорости резания;
XvYvm uv pv qv-показатели степеней (принимают по [5])
Сv=685; Xv=03; Yv=025; m=026; uv=0; pv=0; qv=03
Kv-коэффициент учитывающий конкретные условия резания:
KMV-коэффициент учитывающий свойства обрабатываемого материала [5 стр424-425]; KMV=1;
KnV-коэффициент учитывающий состояние поверхности заготовки; KnV=08;
KиV- коэффициент учитывающий инструментальный материал; KиV=10;
С учетом всех значений величина
Т-стойкость до затупления [1 стр444] Т=60 мин;
Примем по паспорту станка ближайшую меньшую частоту вращения n=
nI=63 мин-1 при этом действительная скорость резания:
Тангенциальная составляющая сил резания Рz при фрезеровании
Где z-число зубьев фрезы а n-число оборотов фрезы в минуту.
Ср-коэффициент сил резания и показатели степени по [3]:
СP=682; ХP=086; yP=072; uP=10; =0; qP=086;
KP-общий поправочный коэффициент на силу резания. Благодаря особенностям процесса резания при фрезеровании зависит только от качества обрабатываемого материала выражаемого коэффициентом КМР [3].
KP=КМР= где nP=075 KP=48
Эффективная мощность при фрезеровании:
Расчетные значения режимов резания для операции 20.
Мощность главного привода станка 53А20 N=2 кВт. С технической стороны этот станок соответствует требованиям рационального выполнения данной фрезерной операции.
Размерные и точностные расчеты технологических процессов.
Проверим обеспечивается ли точность размера ступени вала диаметром
Условия обработки без брака: (01)
где y-погрешность связанная с деформациями системы СПИД мкм.
т.к погрешность связанная с деформациями системы СПИД незначительна то примем y=0;
н- погрешность настройки станка на размер
Коэффициенты КР=12 и КИ=1 учитывают отклонения закона распределения элементарных величин Р и И от нормального.
Р- погрешность регулирования; Р=10 мкм;
И- погрешность измерения; И=20;
-погрешность базирования; =
и-погрешность обработки вызываемая размерным износом инструмента И=мкм
L-длина резания; L=lобщn=2810=280
ф=0-погрешность связанная с геометрическими неточностями станка т.к. ф очень мала (ф=0001 мкм)
Поскольку допуск на размер 325-Td=100 мкм то условие обработки без брака выполняется.
Качество поверхности.
Согласно технологическому процессу зубчатая поверхность после обработки должна иметь шероховатость поверхности Ra=25 мкм. Проверим обеспечивает ли принятый в операции 20 режим обработки требуемую шероховатость.
Величину шероховатости при фрезеровании определяем по формуле:
=5 20°-передний угол;
-закругление режущих кромок; =05 20
Rа=027 Таким образом в процессе обработки будет обеспечиваться заданная шероховатость зубчатой поверхности.
Техническое нормирование.
Выполнить расчет производительности и определить зарплату рабочего за выполнение операции 20. По укрупненным нормативам установить время выполнения остальных механических операций.
где to-основное время; tв- вспомогательное время операции; tоб- время на обслуживание рабочего места мин;
tоб= tорг+ tтех где tорг- время на организационное обслуживание мин; tорг=003 мин;
tтех- время на техническое обслуживание рабочего места мин; tтех=0028;
tоб=003+0028=0058 мин.
tот- время перерывов на отдых и личные надобности мин; tот=0067 мин.
По ранее посчитанному S определим основное время обработки по формуле:
Dф- диаметр фрезы; S-продольная подача в мммин; h-высота зуба в мм; t-величина врезания на один ход фрезы в мм.
tв- вспомогательное время операции состоит из затрат времени на отдельные приемы:
tв=tус+tз.о.+tуп+tиз где
tус- время на установку и снятие детали мин; tус=0043;
tз.о- время на закрепление и открепление детали; tз.о=0024;
tуп- время на приемы управления; tуп=0085;
tиз- время на измерение детали; tиз=011;
tIоп=tо+tв=113+0272=14;
tшт=113+0262+0058+0067=15
где tш-к- штучно-калькуляционное время мин;
tп-з- подготовительно-заключительное время мин
tш-к=15+27400=156 мин.
Зарплата рабочего III разряда за обработку одной детали:
З=tш-кК=156268=418 коп.
где К - минутная ставка станочника (со всеми начислениями).
Часовая норма выработки N=60tшn=6015=40 штч.
Расчеты показывают что стоимость выполнения операции получается низкой а рациональность схемы операции - хорошая.
Расчет штучно-калькуляционного времени выполняется по приближенным формулам [1]:
Операция 05-фрезерно-центровальная tшт-к= to=6l10-3=63810-3151=0785
Операция 10-токарная черновая и чистовая обработка наружных цилиндрических поверхностей и конусной поверхности:
Черновое точение: tшт-к=156=156135=2106 мин;
Чистовое точение: tшт-к=096=096135=1296 мин;
Операция 20-фрезерная: tшт=6
Операция 30-шлифование: tшт=01dl10-3=0958155=148 мин.
Экономическая оценка технологического процесса.
Определим технологическую себестоимость и сделаем заключение об экономической целесообразности выполнения операции 20 на станках модели 53А20 (вариант I) и модели 6Р12 (вариант II).
Технологическая себестоимость складывается из стоимостей материала (заготовки) и себестоимости обработки. Стоимость заготовки для сравниваемых вариантов одинакова и равна 90.
Себестоимость обработки складывается из зарплаты станочника с начислениями Зс и затратами на содержание и эксплуатацию оборудования Зоб.
По варианту I имеем: Зс1=418 коп; tоп=14 мин; tш-к=156 мин.
Для определения Зс2 по варианту II выполним техническое нормирование. Будем считать что обработка на станке 6Р12 ведется с теми же режимами и таким же режущим инструментом как и на станке 53А20. Приняв длительность на каждой позиции равной наибольшему непрерываемому основному времени и с учетом последовательности выполнения переходов определим основное время операции:
Расчет вспомогательного (tвсп) и подготовительно-заключительного (tп-з) времени выполним сложением составляющих элементов.
Время установки заготовки:tуст=0053 мин;
Время на обмер заготовки:tобм=012 мин;
Время на закрепление и открепление детали;tз.о=0024;
Время на приемы управления; tуп=0085;
Оперативное время операции:
tоп= tосн+tвсп=447+0282=4752 мин;
в том числе время работы станка (станкоёмкость)
tIIоп=tосн+tупр=447+03=477 мин;
Примем время на техническое обслуживание рабочего места и перерывы 6% tоп [1] т.е.
а время организационного обслуживания 4% т.е.
tо.об.=0044752=019 мин.
Полное штучно-калькуляционное время операции составит
tш-к2= tоп+tо.об+tд+tп.зn=4752+019+0285+27400=529 мин;
.Зарплата фрезеровщика с начислениями за обработку одной детали:
Зс2=tш.к2К=529268=142 коп;
Затраты связанные с содержанием и эксплуатацией оборудования приходящиеся на одну деталь определим нормативным методом [4]:
где tIоп- станкоемкость; К- коэффициент машино-часа по [4]; К1=1;К2=13
М-минутная стоимость работы станка принятого за эталон; М=0675 копмин;
Тогда Зоб1=14130675=123 коп;
Зоб2=47710675=322 коп.
Все показатели технологической себестоимости сведем в таблицу 6.
Наименование показателей
Зарплата станочника коп
Затраты на содержание и эксплуатацию оборудования коп
Стоимость заготовки коп
Технологическая себестоимость коп
Сравнение показателей позволяет заключить что выполнить операцию 20-нарезание зубьев на станке модели 53А20 целесообразнее. Производительность труда повышается а технологическая себестоимость оказывается ниже.
Список используемой литературы.
Методические указания к практически занятиям по курсу Технология машиностроения» для студентов специальности 12.01
Справочник технолога машиностроителя. т.1. Под ред. А.Г. Косиловой и Р.К. Мещерякова. - м.: Машиностроение 1985.
Справочник технолога машиностроителя. т.2. Под ред. А.Г. Косиловой и Р.К. Мещерякова. - м.: Машиностроение 1985.
Горбацевич А.Ф. Шкред В.А. Курсовое проектирование по ТМС: [Учебное пособие для машиностроительных специальностей Вузов]. - 4-е изд. перераб. и доп. - М.: Высшая школа 1983. - 256 с. ил.
Основы технологии машиностроения. Учебник для вузов. Под ред. В.С. Корсакова - М.: Машиностроение 1988.
Рекомендуемые чертежи
- 31.01.2023
- 24.01.2023
- 26.04.2015
Свободное скачивание на сегодня
- 29.08.2014
- 25.01.2023