Проектирование технологического процесса сборки ключа трещоточного 7813-4019




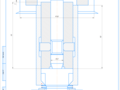
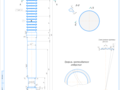
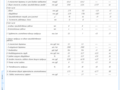
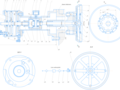
- Добавлен: 24.01.2023
- Размер: 3 MB
- Закачек: 0
Описание
Состав проекта
![]() |
![]() |
![]() ![]() ![]() ![]() |
![]() ![]() ![]() ![]() |
![]() ![]() ![]() |
![]() ![]() ![]() |
![]() ![]() ![]() |
![]() ![]() ![]() |
![]() ![]() ![]() |
![]() ![]() ![]() ![]() |
![]() ![]() ![]() |
![]() ![]() ![]() ![]() |
![]() ![]() ![]() ![]() |
![]() |
![]() ![]() ![]() |
![]() ![]() ![]() |
![]() ![]() ![]() |
![]() ![]() ![]() |
![]() |
![]() ![]() ![]() ![]() |
![]() ![]() ![]() ![]() |
![]() ![]() ![]() ![]() |
![]() |
![]() ![]() ![]() |
![]() ![]() ![]() |
![]() ![]() ![]() |
![]() ![]() ![]() |
![]() ![]() ![]() |
![]() |
![]() ![]() ![]() ![]() |
![]() ![]() ![]() ![]() |
![]() ![]() ![]() ![]() |
![]() ![]() ![]() ![]() |
![]() ![]() ![]() ![]() |
![]() ![]() ![]() ![]() |
![]() ![]() ![]() ![]() |
![]() ![]() ![]() ![]() |
![]() ![]() ![]() ![]() |
![]() ![]() ![]() ![]() |
![]() ![]() ![]() ![]() |
![]() ![]() ![]() ![]() |
![]() ![]() ![]() ![]() |
![]() ![]() ![]() ![]() |
![]() ![]() ![]() |
![]() ![]() ![]() |
![]() ![]() ![]() |
![]() ![]() ![]() ![]() |
![]() ![]() ![]() ![]() |
![]() |
![]() ![]() ![]() ![]() |
![]() ![]() ![]() ![]() |
![]() ![]() ![]() ![]() |
![]() ![]() ![]() |
![]() |
![]() ![]() ![]() |
![]() ![]() ![]() |
![]() ![]() ![]() ![]() |
![]() ![]() ![]() ![]() |
![]() ![]() ![]() ![]() |
![]() ![]() ![]() |
![]() ![]() ![]() |
![]() ![]() ![]() |
![]() ![]() ![]() |
![]() ![]() ![]() |
![]() ![]() ![]() |
![]() ![]() ![]() |
![]() ![]() ![]() ![]() |
![]() ![]() ![]() ![]() |
![]() ![]() ![]() |
![]() ![]() ![]() |
![]() |
![]() ![]() ![]() |
![]() ![]() ![]() |
![]() ![]() ![]() |
![]() |
![]() ![]() ![]() |
![]() ![]() ![]() ![]() |
![]() ![]() ![]() ![]() |
![]() ![]() ![]() ![]() |
![]() ![]() ![]() ![]() |
![]() ![]() ![]() ![]() |
![]() ![]() ![]() ![]() |
![]() ![]() ![]() ![]() |
![]() ![]() ![]() ![]() |
![]() ![]() ![]() ![]() |
![]() ![]() ![]() ![]() |
![]() ![]() ![]() ![]() |
![]() ![]() ![]() ![]() |
![]() ![]() ![]() |
Дополнительная информация
контроль.cdw

допуск перпендикурности 0
ДП 03.01.753.00.00.000
Контрольное приспособление
Сборка.cdw

РУпов.frw

Рубаза.frw

3 Технико.doc
Обеспечением инструментом оборудования занимается ИРК. ИРК предназначена для своевременного обеспечения участков цеха настроенным инструментом. Сюда входит секция хранения и комплектации инструмента секция доставки инструмента к рабочим местам. В секции хранения и комплектации инструмента производится получение инструмента из центрального инструментального склада и раскладка его по стеллажам а также поддержание оборотного фонда и подачи инструмента карт наладки в секцию инструмента. Получив из зоны сборки и настройки готовый настроенный инструмент комплектовщик отправляет его в зону доставки к рабочим местам. Доставка осуществляется поштучно блоками и комплектами целыми инструментальными магазинами в зависимости от вида оборудования. Доставляется и возвращается инструмент к оборудованию:
транспортными рабочими;
внутрицеховым транспортом;
Заточка инструмента производится в заточном отделении которое организовывается в цехе. Так как количество станков 150 300.
Существуют следующие способы замены режущего инструмента.
Замена инструмента по отказам т.е. замена инструмента производится по мере выхода его из строя.
Смешанная замена т.е. каждый заменяют принудительно через определенный промежуток времени а инструмент вышедший из строя раньше этого периода заменяют по отказу.
Смешанно-групповая замена т.е. инструменты имеющие одинаковые среднюю стойкость и закон ее распределения заменяют одновременно по мере достижения ими определенного периода времени независимо от времени работы каждого инструмента.
При смешанном и смешанно-групповом способах замены режущих инструментов в производстве применяют принудительное восстановление инструментов.
При числе станков в цехе более 100 200 организуется мастерская по ремонту инструментальной и технологической оснастки. В мастерской по ремонту оснастки выполняют малый ремонт приспособлений и другой оснастки.
Уход и надзор за действующим оборудованием планово-предупредительный ремонт технических средств всех видов а также модернизацию существующего и изготовление нестандартного выполняет ремонтно-механический цех завода а также цеховые ремонтные базы и отделения по ремонту электрооборудования и электронных систем. Ремонтные базы цеха производят малые и средние ремонты а ремонтно-механический цех – капитальный ремонт оборудования. Для периодического осмотра и ремонта электродвигателей вентиляционных систем цеха устройств электроавтоматики и электронных систем предназначено отделение по ремонту электрооборудования и электронных систем.
Произведем расчет количества получаемой стружки:
где m – удельная масса стружки приходящаяся на 1 м2 площади участка;
S – площадь участка по изготовлению детали.
Так как удельная масса стружки меньше допустимой [m]=300 кгм2 то удаление стружки производится без комплексно-автоматизированной системой линейных и магистральных конвейеров. Стружка собирается в специальные контейнеры затем отправляется на утилизацию.
СОЖ передают по трубопроводам из центральной установки к разборным кранам установленным на участках. В процессе работы станка используется автономная система охлаждения станка которая ежесуточно пополняется из разборных кранов для восполнения потерь жидкости вследствие ее разбрызгивания уноса со стружкой и обработанной заготовкой.
Предприятия обеспечиваются электроэнергией от линий электропередач напряжением 110кВ. Для понижения напряжения используют следующий каскад: открытая понижающая станция 11035 кВ затем открытые центральные распределительные подстанции 3510-6кВ и цеховые закрытые трансформаторные подстанции 6-100.4кВ. Подстанции приближают к основным потребителям электроэнергии для уменьшения потерь в сети.
При производстве вала широко используют сжатый воздух для приводов пневматических зажимных устройств. Давление сжатого воздуха в сети составляет 05 06 МПа. Компрессорные станции размещены в изолированном помещении вследствие высокого уровня создаваемого ими шума.
1.doc
1 Назначение и конструкция сборочной единицы
Заданные детали (ротор и рукоятка) входят в состав ключа трещоточного.
Ротор предназначен для базирования на нём составных сборочных ключа трещоточного. Ротор не является симметричным имеются два глухих отверстия причем одно из них перпендикулярно оси ротора.
Рисунок 1.1 – Эскиз ротора
Рукоятка предназначена для удобного использования ключа трещоточного и для базирования ротора на нём. Конструкция рукоятки проста и удобна. Есть сквозное отверстие которое получается штамповкой.
Рисунок 1.2 – Эскиз рукоятки
Ключ трещоточный состоит из: 1 – крышки 2 - ротора 3 - сектора 4 – пружины 5 – рукоятки 6 – гранулы полиэтилена 7 - винта.
Рисунок 1.3 – Эскиз ключа трещоточного
Установить ротор на подставку с неподвижной головкой. Надеть ручку на ротор. Взять пружину и сектор и вставить пружину двумя концами в отверстие сектора. Вставить в паз ротора сектор с пружиной. Наложить крышку вставив штифт в перегиб пружины. Завернуть винт до упора затем отвернуть его на 12 34 оборота. Переключить крышку 2-3 раза удостоверившись в работе сектора. Проверить работоспособность ключа. Для этого установить ключ квадратом ротора в неподвижную головку квадрата 10 и ключ в обе стороны (в одну сторону ключ работает на Мкр в другую слышен характерный треск сектора по зубьям рукоятки).
К детали предъявляются высокие требования по точности жёсткости а к материалу по прочности износостойкости.
Для повышения физических свойств поверхностного слоя деталь подвергают термообработке - ТВЧ.
Материал детали – конструкционная легированная сталь 40Х (ГОСТ 4543-71) широко используется для изготовления различных видов и типоразмеров валов осей шестерен и т.п. работающих в условиях требующих повышенной прочности и износостойкости.
Таблица 1.1 - Химический состав стали 40Х (ГОСТ 4543-71) .
Таблица 1.2 - Механические свойства стали 40Х (ГОСТ 4543-71) .
Предел прочнос-ти в МПа
Предел текучес-ти т МПа
Относи-тельное удлинение %
Относи-тельное сужение %
Рассмотрим основные поверхности ротора исходя из ее служебного назначения.
Рисунок 1.4 – Поверхности ротора
Основные конструкторские базовые поверхности применяемые для базирования детали в механизме.
Основными базовыми поверхностями являются: торцы буртов 4 5.
Вспомогательные конструкторские базовые поверхности применяемые для базирования других деталей в механизме.
Такими поверхностями будут являться: резьбовое отверстие 17 боковая поверхность отверстия 11 16 цилиндрическая поверхность 3.
Исполнительные поверхности посредством которых деталь выполняет свои функции в механизме: цилиндрические поверхности 10.
Свободные поверхности предназначены для ограничения размера детали и не имеют функционального назначения их размер и форма выбирается произвольно. Такими поверхностями являются 1 2 6 7 8 9 12 13 14 15.
Рисунок 1.5 – Поверхности рукоятки
Основных базовых поверхностей нет.
Вспомогательные конструкторские базовые поверхности: 2 3 4 5.
Исполнительные поверхности: 4 6 8.
Свободные поверхности: 1 7 9 10.
2 Анализ технических условий изготовления детали
Проведём анализ технологичности конструкции деталей (ротора и рукоятки).
При получении заготовок отсутствуют сложные разъемы отрезных штампов.
Основные поверхности являются удобными для базирования и закрепления поэтому дополнительные поверхности не вводятся.
Материал детали сталь Ст40Х механическая обработка которого не вызывает сложностей при обработке твердым сплавом.
Доступность поверхностей деталей для обработки и измерения.
В конструкции ротора присутствуют места резких изменений формы концентраторы напряжений а в рукоятке нет.
Для получения требуемой точности размеров и шероховатости деталей можно применять станки нормального класса точности.
Ротор и рукоятка – жесткие изделия.
Наличие глухих отверстий в роторе одно из которых перпендикулярно к оси детали.
Учитывая все вышеперечисленные факторы у данных деталей удовлетворительная технологичность.
3 Ориентировочное определение типа производства
Предварительно тип производства определяем по таблице 3 с.8 [2]. С учетом массы деталей (0045 и 0125 кг) и годовой программы 30 000принимаем среднесерийный тип производства. Среднесерийное производство характеризуется большой номенклатурой изделий изготовляющихся не большими партиями и не большим объемом выпуска. При среднесерийном производстве используются как универсальные так и станки с ЧПУ которые оснащаются большим количеством инструмента что позволяет снизить трудоемкость и обеспечить высокую гибкость производства при переналадке его на другой тип производства. После разработки технологического процесса механической обработки а также расчета количества основного оборудования тип производства будет уточнен.
4 Анализ базового варианта технологического процесса
Анализ базового технологического процесса обработки детали приведём с точки зрения обеспечения заданного качества детали (точность и шероховатость обрабатываемых поверхностей а также технических требований к детали) производительности обеспечения заданного объёма выпуска.
Метод получения заготовки ротора – прокат нормальной точности. Этот метод не позволяет получить точную заготовку. Можно было бы получать заготовку штамповкой на КГШП с напусками лишь на концах заготовки.
В целом для условий серийного производства технологический процесс выполнен согласно требованиям типовых техпроцессов. Недостатком можно считать большую дифференциацию операций что приводит к увеличению количества используемого оборудования.
Можно было бы использовать более совершенное оборудование концентрировать обработку на станках что привело бы к снижению материальных затрат.
Таким образом можно было бы операции 010-ю 015-ю 020-ю совместить в одну токарно-гидрокопировальную используя станок 1713Ц оснащенный 4-х сторонним поворотным барабаном это уменьшит затраты вспомогательного времени на изготовление детали повысит точность обработки она будет произведена за 1 установ. Позволит уменьшить энергетические и материальные затраты используемого оборудования. Так же это позволит убрать операцию 035-ю т. к. точности полученной на токарно-гидрокопировальном станке в ходе предыдущей обработки будет достаточно для проведения дальнейшей обработки.
Анализируя данный техпроцесс можно отметить использование настольно-сверлильных станков НС-12А на сверлильных операциях. На мой взгляд использование в среднесерийном производстве настольно-сверлильных станков является нерациональным. По-моему использование оборудования на операциях 025 035 065 090 нецелесообразным так как размеры детали малы а точность невелика. Предлагаю использовать на всех вышеуказанных операциях станок меньших габаритов. Экономическую выгоду мы получим уменьшая время на механическую обработку за счёт использования более прогрессивного оборудования. Также целесообразно провести оптимизацию режимов резания по функции минимальных затрат. На 065-й операции использование двух метчиков можно заменить одним так как точность резьбы М6-Н7 не требует двух инструментов.
Используемые в базовом техпроцессе станочные приспособления являются стандартными (кроме специальных станков автоматов и полуавтоматов) и нет существенных причин их замены на специальные.
Режущий инструмент используемый в базовом техпроцессе - из быстрорежущей стали он стандартизирован. Его можно оставить таким же за исключением применения специального инструмента используемого на 035 – ой операции: резец фасонный. Это позволит уменьшить основное время обработки и повысить производительность оборудования.
Контрольный и измерительный инструмент в базовом варианте – штанген-инструмент средства активного контроля и специальные калибры подходят для использования в условиях серийного производства и не требуют кардинального пересмотра схем контроля в новом техпроцессе.
Для удобства анализа базового технологического процесса изготовления ротора представим его в виде таблицы 1.3.
Метод получения заготовки рукоятки – штамповка на молотах. Этот метод позволяет получить довольно таки точную заготовку без напусков.
Для условий серийного производства технологический процесс рукоятки выполнен согласно требованиям типовых техпроцессов. Недостатком можно считать небольшую дифференциацию операций что приводит к увеличению количества используемого оборудования на одну единицу.
Таким образом можно было бы операции 060-ю 070-ю совместить в одну вертикально-сверлильную используя станок 2Р135Ф2 это уменьшит затраты вспомогательного времени на изготовление детали повысит точность обработки она будет произведена за 1 установ. Позволит уменьшить энергетические и материальные затраты используемого оборудования.
Используемые в базовом техпроцессе станочные приспособления являются специальным.
Режущий инструмент используемый в базовом техпроцессе является в большинстве своем из быстрорежущей стали он стандартизирован. Его можно оставить таким же за исключением применения специального инструмента используемого на следующих операциях: 060 – зенкер 105 – специальная прошивка. Это позволит уменьшить основное время обработки и повысить производительность оборудования.
Контрольный и измерительный инструмент в базовом варианте – штанген-инструмент средства активного контроля и специальные пробки подходят для использования в условиях серийного производства.
Для удобства анализа базового технологического процесса изготовления рукоятки представим его в виде таблицы 1.4.
5 Выбор метода получения заготовки
Метод получения заготовки ее качество и точность определяют объем механической обработки (количество рабочих ходов операций техпроцесса). Выбор метода получения заготовки зависит от типа производства массы заготовки ее конфигурации размеров.
В базовом варианте технологического процесса обработки ротора применяется в качестве заготовки стальной стержень круглого сечения полученный процессом проката (пруток из сортового проката нормальной точности).
При этом способе заготовка ротора имеет массу 0187 кг когда сама деталь обладает массой 0045 кг. В данном случае КИМ составляет 24%.
Выбор заготовки – это выбор наиболее рациональной экономичной и технологичной заготовки. С целью получения наиболее точной и качественной заготовки предлагаем заготовку-поковку получаемую на КГШП более приближённую по форме и размерам.
Так как заготовка не похожа по форме и размерам на деталь то изготовление детали будет сопряжено со снятием большого количества металла с заготовки для придания ей необходимой формы и размеров что свидетельствует о немалой трудоемкости механической обработки. Метод получения заготовки ее качество и точность определяет объем механической обработки который в свою очередь устанавливает количество рабочих ходов (операций) технологического процесса.
Использование проката вынуждает снимать дополнительные припуски что приводит к увеличению механической обработки увеличению технологического времени износу инструмента. Поэтому необходимо сравнить два метода получения заготовки: сортовой прокат и поковку на КГШП.
В качестве заготовки принимаем поковку в открытых штампах.
Назначим припуски на обработку ротора по ГОСТ 7505-89 [2].
Штамповочное оборудование – КГШП.
Класс точности принимаем Т4 (т.к. основное деформирующее оборудование: кривошипный горячештамповочный пресс технологический процесс: открытая штамповка)
Группа стали М2 (т.к. сталь поковки с массовой долей углерода свыше 035 до 065 00)
Степень сложности С2 (т.к. отношение массы поковки к массе геометрической фигуры в которую вписывается форма поковки от 032 до 063)
Ориентировочная величина расчетной массы поковки определяется по формуле:
где Мп.р – расчетная масса поковки кг;
Мп.р – масса детали кг;
Кр – расчетный коэффициент принимаем 15(приложение 3 [2]).
Мп.р = 004515=00675 кг
Конфигурация поверхности разъема – плоская.
Принимаем исходный индекс 9.
Припуски на механическую обработку:
основные припуски на размеры в мм:
– ширина и высота 10
Минимальная величина радиусов закруглений наружных углов поковки 10 мм.
длина 25+132 = 276 мм;
ширина и высота 10+13·2=126 мм;
ширина 9+132 =116 мм;
диаметр 30+132 =326 мм
Допускаемые отклонения размеров:
ширина и высота 126-04+08
Допуск радиусов закруглений внутренних и наружных углов 1 мм.
Остаточный облой 07 мм.
Допускаемые отклонения штампованных уклонов ±025 их номинальной величины.
Штампованные уклоны:
на наружной поверхности 7°
Экономическое обоснование выбора заготовки
Определим стоимость поковки по формуле:
Sотх – базовая стоимость одной тонны отходов руб.; Sотх=28 руб т
кт – коэффициент зависящий от класса точности;
кс – коэффициент зависящий от группы сложности;
кв – коэффициент зависящий от массы;
км – коэффициент зависящий от марки материала;
кп – коэффициент зависящий от объема производства.
Q-масса заготовки кг;
кт =09; кс = 077; кв = 129; км = 118; кп =1
где - плотность материала заготовки =7800 кгм3;
v - объём заготовки м3.
Q=7800·00000011630=0090 кг;
Определим стоимость заготовки из проката .
Пруток из сортового проката нормальной точности на завод поступает длиной 1 м диаметром 35 мм.
Количество заготовок из данной длины проката можно получить 37 штук (1000-(25·37)=75 мм). Так же нужно учесть длину которая будет использоваться при резке проката на заготовки пилой ленточной 2 мм (т.к. количество заготовок 37 штук (37·2=74 мм)). Очевидно что оставшейся длины проката 75 мм хватит на данные операции.
Масса одной заготовки:
отходов приходящиеся на одну заготовку:
Общая масса заготовки и отходов:
М=Мзаг.+Мотх.=0187+00015=0188 кг.
Найдём стоимость одной заготовки:
Определим КИМ для обеих методов получения заготовки:
Т.к. для прутка из сортового проката нормальной точности коэффициент использования металла меньше в 2 раза коэффициента использования металла при втором способе получения то принимаем заготовку изготавливаемую на КГШП в открытом штампе.
Назначим припуски на обработку рукоятки по ГОСТ 7505-89 [2].
Штамповочное оборудование – штамповка на молотах.
Степень сложности С2 (т.к. отношение массы поковки к массе геометрической фигуры в которую вписывается форма поковки от 016 до 032)
Кр – расчетный коэффициент принимаем 13(приложение 3 [1]).
Мп.р = 012513=01625 кг
Минимальная величина радиусов закруглений наружных углов поковки 06 мм.
длина 180+13 = 1813 мм;
высота 13 +13·2=156 мм;
диаметр 253-132 =227 мм;
диаметр 32+132 =346 мм
Q=7800·0000020512=016 кг;
7 Выбор методов обработки
При назначении метода обработки следует стремиться к тому чтобы одним и тем же методом обрабатывать возможно большее количество поверхностей заготовки что дает возможность разработать операции с максимальным совмещением обработки отдельных поверхностей сократить общее количество операций длительность цикла обработки повысить производительность и точность обработки заготовки.
При выборе метода обработки необходимо пользоваться приведенными справочными таблицами экономической точности обработки в которых содержаться сведения о технологических возможностях различных методов обработки. Назначаем метод обработки поверхностей ротора и рукоятки и заносим их в табл. 1.5 и 1.6 соответственно.
Таблица 1.5 - Выбор методов обработки ротора.
Заготовка 16 квалитет
Шлифование черновое 14 квалитет
Наружная цилиндрическая
Точение черновое 13 квалитет
Точение чистовое 11 квалитет
Внутренняя цилиндрическая
Сверление черновое 13 квалитет
Точение черновое 14 квалитет
Сверление черновое 14 квалитет
Однократное фрезерование
Проверим число переходов которые обеспечат заданную точность размеров формы и взаимного расположения поверхностей по величине требуемого уточнения.
Требуемая величина уточнения для определенной поверхности находится по формуле:
где Ку—требуемая величина уточнения;
dзаг—допуск размера формы или расположения поверхностей заготовки;
dдет—допуск размера формы или расположения поверхностей детали.
Затем определяется расчетная величина уточнения по выбранному маршруту обработки поверхности:
где Ку.расч.—расчетная величина уточнения;
К1 К2 Кn—величины уточнения по каждому переходу или операции при обработке рассматриваемой поверхности.
где d1—величина максимальной погрешности размера формы или расположения поверхностей которая имеет место на первом переходе (операции) при обработке рассматриваемой поверхности.
где d2—величина максимальной погрешности размера формы или расположения поверхностей которая имеет место на втором переходе (операции) при обработке рассматриваемой поверхности.
где dn—величина максимальной погрешности размера формы или расположения поверхностей которая имеет место на n—переходе (операции) при обработке рассматриваемой поверхности.
После выбора методов обработки поверхностей детали проверим правильность выбора методов для 2-х поверхностей путём расчёта заданного и расчетного уточнений.
Для поверхности 253-013 ротора.
Заготовка— поковка КГШП соответствует 16 квалитету d=13 мм.
точение черновое 13 квалитет d=033м.
точение чистовое 11 квалитет d=013м.
Расчетное уточнение на первом переходе:
Расчетное уточнение на втором переходе:
Общая расчетная величина уточнения:
Так как Ку=Кур (10=10) то назначенный маршрут обработки поверхности 253-013 обеспечит заданную точность.
На основании выборочных способов обработки разработаем технологический маршрут для детали ротор.
По предварительному маршруту обработки произведем выбор оборудования и составим маршрут обработки.
5 Вертикально-фрезерная с ЧПУ
5 Вертикально-сверлильная с ЧПУ
Таблица 1.6 - Выбор методов обработки рукоятки.
Высота головки 13-02
Шлифование 12 квалитет
Зенкерование 13 квалитет
Растачивание 12 квалитет
Для поверхности внутренней цилиндрической 253+01.
Сверление черновое 14 квалитет d=052 мм.
Сверление чистовое 12 квалитет d=021 мм.
Так как КуКур (62606) то назначенный маршрут обработки внутренней цилиндрической 253+01 обеспечит заданную точность.
На основании выборочных способов обработки разработаем технологический маршрут для детали рукоятка.
0 Вертикально-сверлильная с ЧПУ
0 Плоскошлифовальная
0 Вертикально-протяжная
После выбора технологического маршрута обработки и выбора оборудования заполняем маршрутные карты технологического процесса по ГОСТ 3.11.03-82.
8 Выбор технологических баз
Выбор баз для механической обработки производится с учетом достижения требуемой точности взаимного расположения поверхностей детали по линейным и угловым размерам обеспечения доступа инструментов к обрабатываемым поверхностям обеспечения простоты и унификации станочных приспособлений а так же удобства установки в них заготовки.
В процессе обработки ротора предлагаю использовать следующие схемы базирования.
Чистовыми базами на дальнейших операциях механической обработки ротора будут являться поверхность 30 и поверхности квадратного хвостовика. Установка детали на токарных фрезерных и сверлильных станках позволяет обеспечить доступ к большинству обрабатываемых поверхностей ротора.
Для сверления и нарезания резьбы в качестве баз используем квадратный хвостовик с установкой в оправку.
Рисунок 1.6 – Схема базирования при нарезании внутренней цилиндрической резьбы
Для точения уступа ротор базируется на спутнике по хвостовику.
Рисунок 1.7 – Схема базирования при точении уступа
При фрезеровании уступа ротор в качестве баз используем квадратный хвостовик с установкой в оправку.
Рисунок 1.8 – Схема базирования при фрезеровании уступа
Для точения наружной цилиндрической поверхности ротор закрепляется в патрон.
Рисунок 1.9 – Схема базирования при точении наружной цилиндрической поверхности
Для сверления отверстия 51 в качестве чистовой базы используется 30. Ротор устанавливается в патрон.
Рисунок 1.10 – Схема базирования при сверлении отверстия
При точении ротора по контуру и подрезке торца со стороны хвостовика деталь устанавливается в патрон.
Рисунок 1.11 – Схема базирования при контурном точении наружной поверхности и подрезке торца
При фрезеровании хвостовика деталь устанавливается в патрон
Рисунок 1.12 – Схема базирования при фрезеровании квадратной поверхности
Рисунок 1.13 – Схема базирования при точении наружной цилиндрической поверхности
В процессе обработки рукоятки предлагаю использовать следующие схемы базирования.
Для протягивания внутреннего цилиндрического отверстия рукоятка устанавливается в патрон быстросменный.
Рисунок 1.14 – Схема базирования при протягивании внутреннего цилиндрического отверстия
Устанавливается деталь на магнитной плите при шлифовании торцов.
Рисунок 1.15– Схема базирования при шлифовании торцов
При подрезке торцов растачивании и снятии фаски на внутреннем цилиндрическом отверстии рукоятка устанавливается в патрон.
Рисунок 1.16 – Схема базирования при сверлении внутреннего цилиндрического отверстия
При зенкеровании внутреннего цилиндрического отверстия рукоятка устанавливается в патрон.
Рисунок 1.17 – Схема базирования при зенкеровании внутреннего цилиндрического отверстия
9 Разработка технологического маршрута обработки
На данном этапе разрабатывается общий план обработки детали определяется содержание операций техпроцесса. При этом заполняются маршрутные карты техпроцесса (приложение).
При составлении маршрута обработки воспользуемся базовым технологическим процессом а также следует учитывать следующие положения:
-каждая последующая операция должна уменьшить погрешность и улучшить качество поверхности;
-в первую очередь следует обрабатывать те поверхности которые будут служить технологическими базами для следующих операций.
Предварительная разработка и выбор варианта технологического маршрута ротора
Операция 005 Транспортная
Доставить заготовки на участок обработки
Операция 010 Токарная с ЧПУ
Станок: токарный с ЧПУ 16А20ФЗС15
Точить наружную цилиндрическую поверхность 30 мм
Операция 015 Вертикально-фрезерная с ЧПУ
Станок: вертикально-фрезерный 6Т13Ф20
Фрезеровать квадратный хвостовик
Операция 020 Токарная с ЧПУ
Точить по контуру со стороны хвостовика
Операция 025 Вертикально-сверлильная с ЧПУ
Станок: вертикально-сверлильный 2Р135Ф2
Сверлить внутреннее глухое отверстие 51мм
Операция 030 Токарная с ЧПУ
Подрезать торец в размер 25-05 и точить 253 мм
Операция 035 Вертикально-фрезерная с ЧПУ
Операция 040 Токарная с ЧПУ
Операция 045 Сверлильная
Станок: сверлильный 2Н135
Сверлить внутреннее отверстие и нарезать резьбу М6-7Н
Операция 050 Слесарная
Калибрование резьбы. Опиливание острых кромок.
Операция 055 Моечная
Операция 060 Контрольная
Операция 065 Транспортная
Транспортировать деталь на участок сборки
Предварительная разработка и выбор варианта технологического маршрута рукоятки
Операция 005 Транспортная.
Доставить заготовки на участок обработки
Операция 010 Вертикально-сверлильная с ЧПУ
Зенкеровать отверстие 23+04 мм
Операция 015 Токарная с ЧПУ
Станок: токарный 16А20ФЗС15
Подрезать торец расточить отверстие 25 и снять фаску
Операция 020 Плоскошлифовальная
Шлифовать торцы в размер 13-02
Операция 025 Полировальная
Полировать ручку по контуру
Операция 030 Вертикально-протяжная
Протянуть зубья по внутреннему отверстию
Операция 035 Моечная
Операция 040 Контрольная
Операция 045 Транспортная
10 Разработка технологических операций
На этом этапе окончательно определяется состав и порядок выполнения переходов в пределах каждой технологической операции производится выбор моделей оборудования станочных приспособлений режущих и измерительных инструментов.
Разработка технологических операций для детали ротор
Доставить заготовки на участок обработки.
Трактор-погрузчик Q=20кН. Тара Р1448 2ЯН1286 Q=2тс
Приспособление: четырехкулачковый патрон специальный
Режущий инструмент: Резец проходной 2102-1371 ГОСТ 24996-81
Измерительный инструмент: штангенциркуль ШЦ-1-125-005 ГОСТ 166-89
Фрезеровать квадратный хвостовик в размер 10-0565-0475 и 127-03
Приспособление: фрезерное 7220-6095
Режущий инструмент: фреза 2223-0116 ГОСТ 166-89
Точить по контуру со стороны хвостовика подрезать торец выдерживая длину 11-011 и фаску 06x45°.
Приспособление: трёхкулачковый патрон специальный
Режущий инструмент: резец проходной 2102-1371 ГОСТ 24996-81 резец фасон.2126-4007
Приспособление: оправка 6030-4008
Режущий инструмент: сверло 2300-6175 ГОСТ 10902-77 метчик 2620-1115 ГОСТ 3266-81
Измерительный инструмент: штангенциркуль ШЦ-I-125-01 ГОСТ 166-89 пробка 8130-4159 калибр 8389-40005
Подрезать торец в размер 25-05 .
Черновое точение 253 мм.
Получистовое точение 253 мм.
Чистовое точение 253 мм.
Режущий инструмент: резец проходной 2102-1371 ГОСТ 24996-81
Фрезеровать уступ выдерживая размеры 7+01 и 176+03.
Приспособление: фрезерное 7220-6095.
Режущий инструмент: фреза 2234-0355Р9 ГОСТ 9140-78.
Измерительный инструмент: штангенциркуль Ц 111-1-125-0.05 ГОСТ 166-89
Точить уступ R50 выдерживая размеры 2 и 95-05.
Приспособление: пневмопривод спутник М305.01.001
Режущий инструмент: резец 01214-080404 ГОСТ 19048-80
Измерительный инструмент: штангенциркуль ШЦ-I-125-01 ГОСТ 166-89 шаблон 1176.000
Режущий инструмент: сверло 2300-6175 ГОСТ 10902-77 метчик №1 2620-1115 ГОСТ 3266-81
Разработка технологических операций для детали рукоятка
Зенкеровать отверстие 23+04 мм
Приспособление: подставка 7347-4275 патрон 109-В16 ГОСТ 15935-79
Режущий инструмент: зенкер 2330-4015
Измерительный инструмент: пробка 8154-4088 пробка 8154-4087
Подрезать торец в размер 13 расточить отверстие 25 и снять фаску 06x45°
Приспособление: патрон трёхкулачковый с пневмозажимом
Режущий инструмент: резец подрезной 2112-0007 ГОСТ 18880-73 резец проходной 2102-4003
Измерительный инструмент: пробка 8130-4187
Шлифовать торцы головки в размер 13-02
Приспособление: плита магнитная 7208-83
Режущий инструмент: круг шлиф.1450x63x203 24А40СМ 1К ГОСТ 2424-83
Измерительный инструмент: скоба 8150-4217
Полировать торец ручки соблюдая плавность перехода с полированной поверхностью
Режущий инструмент: круг войлочный Пг400x40x45 ГОСТ 10684
Приспособление: патрон быстросменный 6153-4023 приспособление 7632-4025
Режущий инструмент: прошивка 7632-40254-61
Измерительный инструмент: пробка 8130-4385
11 Технологический процесс сборки
Рисунок 1.18 – Эскиз ключа трещоточного
12 Аналитический расчет припусков на обработку
Произведём расчёт припусков расчётно-аналитическим методом на две различные поверхности а так же построим для них схемы расположения припусков и допусков.
Рассчитаем припуски и предельные размеры по переходам на обработку наружной цилиндрической поверхности ротора 253-013.
Исходные данные: Заготовка – поковка. Класс точности Т4. Группа стали М2. Степень точности С2. Исходный индекс 9 ГОСТ 7505-89.заготовки 009 кг. Обработка детали ведется в патроне. Параметры поковки: 16 кв Rz=80 мкм h=150 мкм (т.27[2]).
Составим технологический маршрут получения поверхности 25-013 с указанием Rz и h по переходам(т.29[2]):
-й переход – точение черновое 14 квалитет Rz=50 мкм h=50 мкм;
-й переход – точение получистовое 12 квалитет Rz=30 мкм h=30мкм;
-й переход – точение чистовое 11 квалитет Rz=25 мкм h=25 мкм.
Пространственное отклонение формы поверхности заготовки рассчитаем по формуле:
где ρсм –смещение полуматриц друг относительно друга штампуемой части заготовки относительно стержня исходного материала ρсм=03 мм (т.34[2]);
ρкор –коробление(кривизна) заготовки.
где Δк – удельная кривизна заготовки Δк=6 мкммм (т.32[2]);
l – длина поверхности l=L2=252=125 мм.
Следовательно имеем : ρкор = 6 · 125 = 75 мкм.
Остаточное пространственное отклонение по переходам определяем по формуле:
где Ку – коэффициент уточнения формы.
-й переход – ρ1 =006·ρ=006·309=1854 мкм;
-й переход – ρ2 =004·ρ=005·1854=0927 мкм;
-й переход – ρ3=002·ρ=004·0927=004 мкм.
Погрешность установки детали на всех операциях у равна нулю (базирование в патроне).
Расчёт минимальных значений межоперационных припусков производим по формуле:
где i – выполняемый переход.
Тогда минимальный припуск по переходам будет следующим:
Расчётные размеры рассчитываем начиная с конечного максимального чертёжного размера последовательным вычитанием 2Zmini каждого технологического перехода:
-й переход DP3 =2517 мм;
-й переход DP2 =2517 +0122=25292 мм;
-й переход DP1 = 25292 +0237=25529 мм;
Заготовка Dр.загот =25529 +1078=26607 мм.
Назначаем допуски на технические переходы по таблице а допуски на заготовку по ГОСТ 7505 – 85.
Заготовка - 1300 мкм;
-й переход – 520 мкм;
-й переход – 210 мкм;
-й переход – 130 мкм;
Предельный размер Dmin определяем округляя Dp до большего значения в пределах допуска на данном переходе а Dmax определяем прибавлением к Dmin допусков соответствующих переходов:
-й переход: D3 m D3 ma
-й переход: D2 m D2 ma
-й переход: D1 m D1 ma
заготовка Dзаг.min=265мм Dзаг.max=265+13=278 мм.
Максимальное предельное значение припусков 2×Zmax.ПР находим как разность наибольших предельных размеров выполняемого и предшествующего переходов а минимальные значения 2×Zmin.ПР – как разность наименьших предельных размеров выполняемого и предшествующих переходов.
Z1 minПР = 265-257=08 мм.
Общий минимальный припуск находим как сумму минимальных промежуточных припусков а общий максимальный – как сумму максимальных припусков:
Z0min=08+03+023=17 мм.
Общий номинальный припуск 2Z0ном вычисляем по формуле:
Z0ном=Z0min+Нз-Нд (1.12)
где Нз и Нд – соответственно нижнее отклонение допуска заготовки и детали.
Z0ном=17+05-013=233мм.
Следовательно номинальный диаметр поверхности заготовки будет равен:
DЗном=DДном+2Z0ном=253+233=2763 мм.
Производим проверку правильности расчётов по формулам:
Zmaxi-2Zmini=Di-1- Di (1.13)
Z0max-2Z0min=DЗ- DД (1.14)
Для нашего случая имеем:
-й переход 210-130=310-230; т.е. 80=80;
-й переход 520-210=610-300; т.е. 310=310;
-й переход 1300-520=1580-800; т.е. 780=780;
общий припуск 2800-1630=1300-130; т.е1170=1170.
Расчёт произведён правильно.
Все расчёты параметров припусков приведём в таблицу 1.11.1.
Таблица 1.7 – Результаты расчёта припусков на поверхность ротора 253-013.
Технологи-ческие переходы обработки поверхности 45js7
Элементы припуска мкм
Расчётный припуск 2Zmin мкм
Расчётный размер Dр мм
Допуск на размер D мкм
Предельный размер мм
Предельные значения припусков мм
На основании таблицы строим схему графического расположения припусков и допусков на обработку поверхности ротора 253-013.
Рисунок 1.19 — Схема графического расположения припусков и допусков на обработку поверхности диаметром 253-013
Выберем технологический маршрут обработки отверстия 253+01 и определим величины Rz и h по переходам:
Заготовка 16 квалитета: Rz = 80 h = 150
-й переход: зенкерование 13 кв. Rz = 40 h = 40
-й переход: растачивание 12 кв. Rz = 32 h = 30
Определим значения пространственных отклонений для заготовки.
где rсм – смещение оси головки относительно общей оси; rсм = 0
rкор – коробление вала;
где К – удельная кривизна заготовки К =8;
l – длина заготовки.
rзаг=rкор = 13×8 = 104 мкм
Остаточное пространственное отклонение по формуле:
где КУ – коэффициент уточнения формы.
Погрешность установки детали на выполняемом переходе eу определяем по формуле:
где eb – погрешность базирования eb = 0;
eз – погрешность закрепления eз = 80.
-й переход r1 = 005×104 = 52 мкм; e1 = 80×005 = 4 мкм
-й переход r2 = 004×52 = 0208 мкм; e2 = 4×004 = 016 мкм
Расчёт минимальных межоперационных припусков:
Расчётный размер диаметра отверстия DР вычислим начиная с конечного максимального чертёжного размера путём последовательного вычитания минимального припуска каждого предыдущего перехода:
-й переход: DР растч.. =254-2×0045 = 2531 мм
-й переход: DР зенк. = 2531-2×0334 = 24642 мм
Назначаем допуски на технологические переходы:
Заготовка – 1300 мкм
-й переход – 330 мкм
-й переход – 210 мкм
Предельный размер Dmax определяем округляя Dp до меньшего значения в пределах допуска на данном переходе а Dmin определяем вычитая из Dmax допуски соответствующих переходов:
-й переход: Dma Dmin растч..= 254-021=2519 мм
-й переход: Dma Dmin зенк. = 2531-033 = 2498 мм
заготовка: Dmax заг. = 24642 мм Dmin заг. = 24642-13 = 23342 мм
Минимальные предельное значение припусков 2×Zmin.ПР. находим как разность наибольших предельных размеров выполняемого и предшествующего переходов а максимальные значения 2×ZmaxПР – как разность наименьших предельных размеров выполняемого и предшествующих переходов.
Общий минимальный припуск находим как сумму минимальных промежуточных припусков а общий максимальный – как сумму максимальных припускав:
Общий номинальный припуск находим по формуле:
где ВЗ – верхнее отклонение заготовки по ГОСТ 2590 – 71
ВД – верхнее отклонение детали по чертежу.
Тогда номинальный диаметр заготовки:
Проверяем правильность произведённых расчётов:
-й переход: 021-009 =033-021 мм 012=012 мм
-й переход: 1638-0668 = 13-033 мм 097=097 мм
Общий припуск: 1848-0758 = 13-021 мм 109=109 мм
Проверка правильна значит расчёты межоперационных припусков произведены верно. Все расчёты параметров припусков приведём в таблицу 1.11.2.
Таблица 1.8 Результаты расчёта припусков на поверхность рукоятки 253+01
переходы обработки поверхности
Расчётный припуск 2×Zmin мкм
Расчётный размер Dp мкм
Допуски размеров мкм
Предельные размеры припусков мкм
На основании таблицы строим схему графического расположения припусков и допусков на обработку поверхности рукоятки 25+01.
Рисунок 1.20 — Схема графического расположения припусков и допусков на обработку отверстия 25+01
13 Расчет режимов резания
Произведем расчет режимов резания для двух разных типов операций. Одной – чернового точения поверхности ротора 253-013 на операции « 030 Токарная с ЧПУ». Другой – протягивания отверстия рукоятки 253+01 на операции « 030 Токарная с ЧПУ».
Расчет проведем по эмпирическим формулам по методике [3].
Произведём расчёт режимов резания обработки размера 25-13 точением.
Глубина резания – t = 2 мм;
Подача– So = 06 ммоб.
Скорость резанья при точении – окружная скорость вращения заготовки:
Т – период стойкости и показатели степеней находим по таблицам:
СV = 290; y = 035; m = 02; T = 60 мин.
KV = KМV× KПV× KИV(1.22)
где KМV – коэффициент учитывающий качество обрабатываемого материала;
KПV – коэффициент учитывающий состояние поверхности заготовки;
KИV – коэффициент учитывающий материал инструмента.
где sB – физический параметр характеризующий обрабатываемый материал;
КГ и nv – коэффициент и показатель степени характеризующие группу стали по обрабатываемости.
KИV = 115; KПV = 08;
Определяем окружную скорость вращения заготовки:
Силы резания при точении Н:
где Ср – поправочный коэффициент Ср =300;
х у n – показатели степеней х=1 у=075 n = -015;
Кр – поправочный коэффициент.
где - коэффициенты учитывающие фактические условия резания
Кφp=108 Кλp=1 Кp=087.
Определяем Кмр по формуле:
где n0 - показатель степени nv = 09.
Определим частоту вращения по формуле:
где n - частота вращения шпинделя мин-1;
Частота вращения заготовки:
Принимаем n = 1350 oб мин.
Определяем мощность затрачиваемую на резание по формуле:
Находим мощность резания:
Определяем основное время То:
где Sо - оборотная подача обмин ;
Таблица 1.19 - Сводная таблица режимов резания ротора
Наименование операции или перехода
Вертикально-фрезерная с ЧПУ
Вертикально-свер-лильная с ЧПУ
-получистовое точение
Вертикально-фрезерная с ЧПУ
14 Определение норм времени на операции
При серийном производстве норма штучного времени определяется по формуле:
где То—основное (машинное) время обработки детали мин;
Тв—вспомогательное время на операцию (время на установку и снятие детали подвод и отвод инструмента время на управление станком и т.д.) мин;
Тобс—время на техническое и организационное обслуживание рабочего места (время на замену затупившегося инструмента время на уборку рабочего места в конце работы) мин;
Тотд—время на отдых и личные надобности мин.
где Тус—время на установку и снятие детали мин;
Тзо—время на закрепление и открепление детали мин;
Туп—время на приемы управления мин;
Тиз—время на измерение детали мин.
где Ттех—время на техническое обслуживание рабочего места мин;
Торг—время на организационное обслуживание рабочего места мин.
Оперативное время Топ:
Время на организационное и техническое обслуживание определяется в процентах от оперативного времени.
Tтех + Tорг =к*Tоп100%
где П—затраты времени на отдых в процентном отношении к оперативному.
Рассчитаем норму штучного калькуляционного времени для операции 015 ротора (вертикально-фрезерной). Производство среднесерийное масса детали 045 кг.
Тус+Тзо=006+0024=0084 мин Туп=001+02=021 мин. — время на включение станка и подвод инструмента (станок включается кнопкой)
Время на измерение штангенциркулем ШЦ-I-125-005 Тиз=012 мин
Вспомогательное время:
Тв=0084+021+012=0414 мин
Топ=16+0414 =2014 мин
То=16 - основное время на обработку заготовки на данной операции
Затраты времени на обслуживание рабочего места и отдых в процентном отношении к оперативному равно 7% тогда:
Тобс=2014·7100=0145 мин
Подставляем полученные значения времен:
Тшт=16+0414+0145=215 мин
Tп.з.- подготовительно-заключительное время на партию заготовок
- время на наладку станка и установку приспособлений 14 мин
- время на установку фрез (1 шт.) 2 мин
- получить наряд чертеж технологическую документацию режущий и вспомогательный инструмент контрольно-измерительный инструмент приспособление заготовки исполнителем до начала и сдать их после окончания обработки партии деталей 13 мин
-ознакомится с работой чертежом технологической документацией осмотреть заготовки 20 мин
-инструктаж мастера 20 мин
Tп.з.=14+2+13+2+2=33 мин
Количество деталей в партии:
n=50000·6254=1181 шт.
Время приходящееся на одну заготовку из партии:
Tшт.к.=0028+215=218 мин
Рассчитаем норму штучного калькуляционного времени для операции 015 рукоятки (Токарная с ЧПУ). Производство среднесерийное масса детали 0125 кг.
- установить заданное взаимное положение детали и инструмента по координатам XYZ и при необходимости произвести подналадку 032 мин
- включить и выключить лентопротяжный механизм 004 мин
- открыть и закрыть крышку лентопротяжного механизма перемотать заправить ленту в считывающее устройство 031 мин
- проверить переход деталиинструмента в заданную точку после
- продвинуть перфоленту в исходное положение 019 мин
- установить и снять щиток от набрызгивания эмульсией 003 мин
Тус+Тзо=005+0024=0074 мин
Туп=031+004+032+015+019+003=0752 мин.
Время на измерение штангенциркулем ШЦ-I-125-005: Тиз=012 мин Вспомогательное время:
Тв=0074+0752+012=0946 мин
Топ=0946+065=1596 мин
То=065 - основное время на обработку заготовки на данной операции
Затраты времени на обслуживание рабочего места и отдых в процентном отношении к оперативному равно 6% тогда:
Тобс=1596·6100=0096 мин
Тшт=0946+065+0096=169 мин
- получить наряд чертеж технологическую документацию программоноситель режущий и вспомогательный инструмент контрольно-измерительный инструмент приспособление заготовки исполнителем до начала и сдать их после окончания обработки партии деталей 13 мин
-ознакомится с работай чертежом технологической документацией осмотреть заготовки 20 мин
-установить и снять патрон трехкулачковый 25 мин
- установить исходные режимы станка 015 мин
- установить и снять кулачки 65 мин
-расточить кулачки 62 мин
-установить и снять инструментальный блок или отдельный режущий инструмент (время на один инструмент( блок)) 02 мин
-установить программоноситель в считывающее устройство
-проверить работоспособность считывающего устройства и
-ввести программу в память системы с ЧПУ с
программоносителя 15 мин
-установить исходный координаты X и Z (настроить нулевое
Tп.з.=13+2+2+25+015+65+62+02+1+1+15+2=385 мин
Время приходящиеся на одну заготовку из партии
Tшт.к.=003+169=17 мин
Нормы времени на остальные операции назначаем по нормативным справочникам. Рассчитанные и назначенные времена сведем в таблицу.
Таблица 1.20 - Сводная таблица технических норм времени по операциям ротора мин.
Вертикально-сверлильная с ЧПУ
15 Определение необходимого количества оборудования
Для серийного производства количество станков S определяется по формуле:
Тшт—штучное время обработки изделия мин;
F—действительный годовой фонд времени работы оборудования час.
Коэффициент загрузки оборудования:
где Sпр—принятое количество станков.
Объём выпуска деталей “ротор” – 50000
На основании рассчитанных коэффициентов строим график загрузки оборудования.
Рисунок 1.21 – График степени загружённости станков на операциях ротора:
-й столбец Токарная с ЧПУ станок модели 16А20Ф3С15
-й столбец Вертикально-фрезерная станок модели 6Т13Ф20
-й столбец Вертикально-сверлильная станок модели 2Р135Ф2
-й столбец Сверлильная станок модели 2Н135
Анализируя полученные данные необходимо отметить неудовлетворительную загрузку станков. Поэтому следует совместить токарную обработку и выполнять операции 010 020030 и 040 на одном станке. Загрузка оборудования в этом случае будет составлять около 75%. Большинство оборудования универсальное поэтому его следует догружать операциями по обработке других деталей для увеличения коэффициента загрузки оборудования.
Объём выпуска деталей “рукоятка” – 50000
Рисунок 1.22 – График степени загружённости станков на операциях рукоятки:
-й столбец Плоскошлифовальная станок модели 2Н118
-й столбец Вертикально-протяжная станок модели 3М6341.16 Уточнение типа производства по коэффициенту закрепления операций.
Уточненный расчет типа производства основывается на определении коэффициента закрепления операций Кзо:
где О—количество всех различных технологических операций выполненных в течении месяца;
Р—число рабочих мест необходимых для выполнения месячной программы.
Согласно ГОСТа для среднесерийного типа производства Кзо=10 20
Число рабочих мест для выполнения определенной i-ой операции определяем по формуле:
где Nм—месячный объем выпуска детали (2500 шт);
Тшт—штучное время на выполнение определенной операции мин;
Fм—месячный фонд времени работы оборудования (196 час);
Кв—коэффициент выполнения норм времени. Кв=11 13
Рассчитанное число рабочих мест округляем до ближайшего большего целого числа Рi.
Коэффициент загрузки данных рабочих мест выполняемой операцией:
Количество операций выполняемых на этом рабочем месте при его нормативной загрузке определяем по формуле:
где: hн=07 085—нормативный коэффициент загрузки для среднесерийного
Общее количество операций выполняемых на всех рабочих местах проектируемого техпроцесса и общее количество рабочих мест определяется как сумма всех операций и сумма всех рабочих мест соответственно.
Результаты расчетов сведем в таблицу.
Таблица 1.22 — Определение типа производства детали “ротор”.
Определяем коэффициент закрепления операций:
Коэффициент Кзо находится в промежутке от 1 до 10 причем ближе к 10. Следовательно принимаем среднесерийный тип производства.
Таблица 1.23 — Определение типа производства детали “рукоятка”.
Коэффициент Кзо равен 10. Следовательно принимаем среднесерийный тип производства.
Определим такт выпуска продукции t:
где F—действительный годовой фонд времени работы оборудования при 2-ух сменной работе (4015 час).
Расчёт и проектирование средств технологического оснащения
1 Проектирование станочного приспособления
1.1 Описание конструкции и работы приспособления
Проектируемое приспособление предназначено для точения уступа. В данном случае приспособление устанавливается на токарный станок с ЧПУ модели 16А20Ф3С15.
Приспособление представляет собой спутник на который устанавливаются восемь деталей ротора по окружности и прижим в центре. С помощью переходника который соединен со штоком пневмоцилиндра происходит прижим спутника к планшайбе. Торец ротора упирается в диафрагму. На периферии установлен штифт который не предохраняет спутник от проворота относительно планшайбы. Планшайба установлена на шпинделе токарного станка. Приспособление является восьмиместным что увеличивает производительность в условиях среднесерийного производства.
Закрепление детали осуществляется следующим образом:
детали устанавливаются в спутник;
спутник устанавливается на планшайбу;
включают пневмоцилиндр который осуществляет зажим спутник.
1.2 Расчет сил зажима заготовки
Расчет сил зажима сводится к решению задачи статики на равновесие твердого тела под действием внешних сил. Величина сил зажима определяется из условия равновесия всех сил при полном сохранении контакта технологических баз обрабатываемой заготовки с установочными элементами приспособления и невозможности ее сдвига или поворота в процессе обработки.
Условия установки и закрепления детали в приспособлении дают возможности считать приспособление на возможность перекоса заготовки относительно своей оси. Поэтому будем вести расчет на перекос оси под действием силы резания Рх.
Рисунок 2.1 - Схема расположения сил резания
На заготовки действуют сила зажима Р1 и сила резания Рx
Запишем уравнение равновесия:
где kз—коэффициент запаса; kз =25
l1 l2—плечи соответственно сил Px P1
коэффициенты и показатели степеней определяем по таблицам:
СР = 339; х = 10; у = 05; n=-04.
Тогда окружная сила резания равна:
Из приведенных выше расчетов видно что сила зажима необходимая для того что бы избежать перекоса заготовки намного выше силы резания Рх = 880 Н.
Рассчитаем диаметр пневмоцилиндра необходимого для создания силы зажима.
Определяем диаметр цилиндра D:
где p—давление в пневмосистеме (р = 05 МПа);
h = 085—КПД пневмоцилиндра;
Pш – усилие на штоке.
Принимаем стандартное значение диаметра D = 180 мм.
1.3 Расчет приспособления на точность
Цель расчета приспособления на точность заключается в определении требуемой точности изготовления приспособления по выбранному точностному параметру и задании допусков размеров деталей и элементов приспособления.
где Епр—погрешность приспособления мм;
d—допуск выполняемого размера мм;
Кт—коэффициент учитывающий отклонение рассеивания значений составляющих величин от закона нормального распределения (Кт = 11);
Kт1—коэффициент учитывающий уменьшение предельного значения погрешности базирования при работе на настроенных станках (kт1 = 08);
eб—погрешность базирования мм;
eз—погрешность закрепления мм;
eу—погрешность установки приспособления на станке мм;
eи—погрешность положения рабочих поверхностей рабочих элементов в результате их изнашивания в процессе эксплуатации приспособления мм;
eпи—погрешность от перекоса инструмента из-за неточности изготовления направляющих элементов приспособления мм;
kт2—коэффициент учитывающий долю погрешности обработки в суммарной погрешности вызываемой факторами независящими от приспособления (kт2 = 07);
v—экономическая точность обработки (v = 04 мм).
eб = 62 мкм – величина допуска для размера R50 выполненного по 14 квалитету.
eу = 0 т. к. эта погрешность будет одинакова для всей партии заготовок и ее можно компенсировать настройкой инструмента. Погрешность от износа определяем по формуле:
где b — постоянная зависящая от вида установочного элемента и условия контакта (b = 00008 мкм);
N—количество контактов заготовки с опорой (установок в приспособление снятий с него) в год.
eпи=0 — погрешности ос перекоса инструмента не будет
Подставим все значения в (2.5):
На основании расчета можно сделать вывод что погрешность размера R50 при изготовлении приспособления не должна превышать 0307 мм.
123.doc
1 Назначение и конструкция сборочной единицы
Заданные детали (ротор и рукоятка) входят в состав ключа трещоточного.
Ротор предназначен для базирования на нём составных сборочных ключа трещоточного. Ротор не является симметричным имеются два глухих отверстия причем одно из них перпендикулярно оси ротора.
Рисунок 1.1 – Эскиз ротора
Рукоятка предназначена для удобного использования ключа трещоточного и для базирования ротора на нём. Конструкция рукоятки проста и удобна. Есть сквозное отверстие которое получается штамповкой.
Рисунок 1.2 – Эскиз рукоятки
Ключ трещоточный состоит из: 1 – крышки 2 - ротора 3 - сектора 4 – пружины 5 – рукоятки 6 – гранулы полиэтилена 7 - винта.
Рисунок 1.3 – Эскиз ключа трещоточного
Установить ротор на подставку с неподвижной головкой. Надеть ручку на ротор. Взять пружину и сектор и вставить пружину двумя концами в отверстие сектора. Вставить в паз ротора сектор с пружиной. Наложить крышку вставив штифт в перегиб пружины. Завернуть винт до упора затем отвернуть его на 12 34 оборота. Переключить крышку 2-3 раза удостоверившись в работе сектора. Проверить работоспособность ключа. Для этого установить ключ квадратом ротора в неподвижную головку квадрата 10 и ключ в обе стороны (в одну сторону ключ работает на Мкр в другую слышен характерный треск сектора по зубьям рукоятки).
К детали предъявляются высокие требования по точности жёсткости а к материалу по прочности износостойкости.
Для повышения физических свойств поверхностного слоя деталь подвергают термообработке - ТВЧ.
Материал детали – конструкционная легированная сталь 40Х (ГОСТ 4543-71) широко используется для изготовления различных видов и типоразмеров валов осей шестерен и т.п. работающих в условиях требующих повышенной прочности и износостойкости.
Таблица 1.1 - Химический состав стали 40Х (ГОСТ 4543-71) .
Таблица 1.2 - Механические свойства стали 40Х (ГОСТ 4543-71) .
Предел прочнос-ти в МПа
Предел текучес-ти т МПа
Относи-тельное удлинение %
Относи-тельное сужение %
Рассмотрим основные поверхности ротора исходя из ее служебного назначения.
Рисунок 1.4 – Поверхности ротора
Основные конструкторские базовые поверхности применяемые для базирования детали в механизме.
Основными базовыми поверхностями являются: торцы буртов 4 5.
Вспомогательные конструкторские базовые поверхности применяемые для базирования других деталей в механизме.
Такими поверхностями будут являться: резьбовое отверстие 17 боковая поверхность отверстия 11 16 цилиндрическая поверхность 3.
Исполнительные поверхности посредством которых деталь выполняет свои функции в механизме: цилиндрические поверхности 10.
Свободные поверхности предназначены для ограничения размера детали и не имеют функционального назначения их размер и форма выбирается произвольно. Такими поверхностями являются 1 2 6 7 8 9 12 13 14 15.
Рисунок 1.5 – Поверхности рукоятки
Основных базовых поверхностей нет.
Вспомогательные конструкторские базовые поверхности: 2 3 4 5.
Исполнительные поверхности: 4 6 8.
Свободные поверхности: 1 7 9 10.
2 Анализ технических условий изготовления детали
Проведём анализ технологичности конструкции деталей (ротора и рукоятки).
При получении заготовок отсутствуют сложные разъемы отрезных штампов.
Основные поверхности являются удобными для базирования и закрепления поэтому дополнительные поверхности не вводятся.
Материал детали сталь Ст40Х механическая обработка которого не вызывает сложностей при обработке твердым сплавом.
Доступность поверхностей деталей для обработки и измерения.
В конструкции ротора присутствуют места резких изменений формы концентраторы напряжений а в рукоятке нет.
Для получения требуемой точности размеров и шероховатости деталей можно применять станки нормального класса точности.
Ротор и рукоятка – жесткие изделия.
Наличие глухих отверстий в роторе одно из которых перпендикулярно к оси детали.
Учитывая все вышеперечисленные факторы у данных деталей удовлетворительная технологичность.
3 Ориентировочное определение типа производства
Предварительно тип производства определяем по таблице 3 с.8 [2]. С учетом массы деталей (0045 и 0125 кг) и годовой программы 30 000принимаем среднесерийный тип производства. Среднесерийное производство характеризуется большой номенклатурой изделий изготовляющихся не большими партиями и не большим объемом выпуска. При среднесерийном производстве используются как универсальные так и станки с ЧПУ которые оснащаются большим количеством инструмента что позволяет снизить трудоемкость и обеспечить высокую гибкость производства при переналадке его на другой тип производства. После разработки технологического процесса механической обработки а также расчета количества основного оборудования тип производства будет уточнен.
4 Анализ базового варианта технологического процесса
Анализ базового технологического процесса обработки детали приведём с точки зрения обеспечения заданного качества детали (точность и шероховатость обрабатываемых поверхностей а также технических требований к детали) производительности обеспечения заданного объёма выпуска.
Метод получения заготовки ротора – прокат нормальной точности. Этот метод не позволяет получить точную заготовку. Можно было бы получать заготовку штамповкой на КГШП с напусками лишь на концах заготовки.
В целом для условий серийного производства технологический процесс выполнен согласно требованиям типовых техпроцессов. Недостатком можно считать большую дифференциацию операций что приводит к увеличению количества используемого оборудования.
Можно было бы использовать более совершенное оборудование концентрировать обработку на станках что привело бы к снижению материальных затрат.
Таким образом можно было бы операции 010-ю 015-ю 020-ю совместить в одну токарно-гидрокопировальную используя станок 1713Ц оснащенный 4-х сторонним поворотным барабаном это уменьшит затраты вспомогательного времени на изготовление детали повысит точность обработки она будет произведена за 1 установ. Позволит уменьшить энергетические и материальные затраты используемого оборудования. Так же это позволит убрать операцию 035-ю т. к. точности полученной на токарно-гидрокопировальном станке в ходе предыдущей обработки будет достаточно для проведения дальнейшей обработки.
Анализируя данный техпроцесс можно отметить использование настольно-сверлильных станков НС-12А на сверлильных операциях. На мой взгляд использование в среднесерийном производстве настольно-сверлильных станков является нерациональным. По-моему использование оборудования на операциях 025 035 065 090 нецелесообразным так как размеры детали малы а точность невелика. Предлагаю использовать на всех вышеуказанных операциях станок меньших габаритов. Экономическую выгоду мы получим уменьшая время на механическую обработку за счёт использования более прогрессивного оборудования. Также целесообразно провести оптимизацию режимов резания по функции минимальных затрат. На 065-й операции использование двух метчиков можно заменить одним так как точность резьбы М6-Н7 не требует двух инструментов.
Используемые в базовом техпроцессе станочные приспособления являются стандартными (кроме специальных станков автоматов и полуавтоматов) и нет существенных причин их замены на специальные.
Режущий инструмент используемый в базовом техпроцессе - из быстрорежущей стали он стандартизирован. Его можно оставить таким же за исключением применения специального инструмента используемого на 035 – ой операции: резец фасонный. Это позволит уменьшить основное время обработки и повысить производительность оборудования.
Контрольный и измерительный инструмент в базовом варианте – штанген-инструмент средства активного контроля и специальные калибры подходят для использования в условиях серийного производства и не требуют кардинального пересмотра схем контроля в новом техпроцессе.
Для удобства анализа базового технологического процесса изготовления ротора представим его в виде таблицы 1.3.
Метод получения заготовки рукоятки – штамповка на молотах. Этот метод позволяет получить довольно таки точную заготовку без напусков.
Для условий серийного производства технологический процесс рукоятки выполнен согласно требованиям типовых техпроцессов. Недостатком можно считать небольшую дифференциацию операций что приводит к увеличению количества используемого оборудования на одну единицу.
Таким образом можно было бы операции 060-ю 070-ю совместить в одну вертикально-сверлильную используя станок 2Р135Ф2 это уменьшит затраты вспомогательного времени на изготовление детали повысит точность обработки она будет произведена за 1 установ. Позволит уменьшить энергетические и материальные затраты используемого оборудования.
Используемые в базовом техпроцессе станочные приспособления являются специальным.
Режущий инструмент используемый в базовом техпроцессе является в большинстве своем из быстрорежущей стали он стандартизирован. Его можно оставить таким же за исключением применения специального инструмента используемого на следующих операциях: 060 – зенкер 105 – специальная прошивка. Это позволит уменьшить основное время обработки и повысить производительность оборудования.
Контрольный и измерительный инструмент в базовом варианте – штанген-инструмент средства активного контроля и специальные пробки подходят для использования в условиях серийного производства.
Для удобства анализа базового технологического процесса изготовления рукоятки представим его в виде таблицы 1.4.
5 Выбор метода получения заготовки
Метод получения заготовки ее качество и точность определяют объем механической обработки (количество рабочих ходов операций техпроцесса). Выбор метода получения заготовки зависит от типа производства массы заготовки ее конфигурации размеров.
В базовом варианте технологического процесса обработки ротора применяется в качестве заготовки стальной стержень круглого сечения полученный процессом проката (пруток из сортового проката нормальной точности).
При этом способе заготовка ротора имеет массу 0187 кг когда сама деталь обладает массой 0045 кг. В данном случае КИМ составляет 24%.
Выбор заготовки – это выбор наиболее рациональной экономичной и технологичной заготовки. С целью получения наиболее точной и качественной заготовки предлагаем заготовку-поковку получаемую на КГШП более приближённую по форме и размерам.
Так как заготовка не похожа по форме и размерам на деталь то изготовление детали будет сопряжено со снятием большого количества металла с заготовки для придания ей необходимой формы и размеров что свидетельствует о немалой трудоемкости механической обработки. Метод получения заготовки ее качество и точность определяет объем механической обработки который в свою очередь устанавливает количество рабочих ходов (операций) технологического процесса.
Использование проката вынуждает снимать дополнительные припуски что приводит к увеличению механической обработки увеличению технологического времени износу инструмента. Поэтому необходимо сравнить два метода получения заготовки: сортовой прокат и поковку на КГШП.
В качестве заготовки принимаем поковку в открытых штампах.
Назначим припуски на обработку ротора по ГОСТ 7505-89 [2].
Штамповочное оборудование – КГШП.
Класс точности принимаем Т4 (т.к. основное деформирующее оборудование: кривошипный горячештамповочный пресс технологический процесс: открытая штамповка)
Группа стали М2 (т.к. сталь поковки с массовой долей углерода свыше 035 до 065 00)
Степень сложности С2 (т.к. отношение массы поковки к массе геометрической фигуры в которую вписывается форма поковки от 032 до 063)
Ориентировочная величина расчетной массы поковки определяется по формуле:
где Мп.р – расчетная масса поковки кг;
Мп.р – масса детали кг;
Кр – расчетный коэффициент принимаем 15(приложение 3 [2]).
Мп.р = 004515=00675 кг
Конфигурация поверхности разъема – плоская.
Принимаем исходный индекс 9.
Припуски на механическую обработку:
основные припуски на размеры в мм:
– ширина и высота 10
Минимальная величина радиусов закруглений наружных углов поковки 10 мм.
длина 25+132 = 276 мм;
ширина и высота 10+13·2=126 мм;
ширина 9+132 =116 мм;
диаметр 30+132 =326 мм
Допускаемые отклонения размеров:
ширина и высота 126-04+08
Допуск радиусов закруглений внутренних и наружных углов 1 мм.
Остаточный облой 07 мм.
Допускаемые отклонения штампованных уклонов ±025 их номинальной величины.
Штампованные уклоны:
на наружной поверхности 7°
Экономическое обоснование выбора заготовки
Определим стоимость поковки по формуле:
Sотх – базовая стоимость одной тонны отходов руб.; Sотх=28 руб т
кт – коэффициент зависящий от класса точности;
кс – коэффициент зависящий от группы сложности;
кв – коэффициент зависящий от массы;
км – коэффициент зависящий от марки материала;
кп – коэффициент зависящий от объема производства.
Q-масса заготовки кг;
кт =09; кс = 077; кв = 129; км = 118; кп =1
где - плотность материала заготовки =7800 кгм3;
v - объём заготовки м3.
Q=7800·00000011630=0090 кг;
Определим стоимость заготовки из проката .
Пруток из сортового проката нормальной точности на завод поступает длиной 1 м диаметром 35 мм.
Количество заготовок из данной длины проката можно получить 37 штук (1000-(25·37)=75 мм). Так же нужно учесть длину которая будет использоваться при резке проката на заготовки пилой ленточной 2 мм (т.к. количество заготовок 37 штук (37·2=74 мм)). Очевидно что оставшейся длины проката 75 мм хватит на данные операции.
Масса одной заготовки:
отходов приходящиеся на одну заготовку:
Общая масса заготовки и отходов:
М=Мзаг.+Мотх.=0187+00015=0188 кг.
Найдём стоимость одной заготовки:
Определим КИМ для обеих методов получения заготовки:
Т.к. для прутка из сортового проката нормальной точности коэффициент использования металла меньше в 2 раза коэффициента использования металла при втором способе получения то принимаем заготовку изготавливаемую на КГШП в открытом штампе.
Назначим припуски на обработку рукоятки по ГОСТ 7505-89 [2].
Штамповочное оборудование – штамповка на молотах.
Степень сложности С2 (т.к. отношение массы поковки к массе геометрической фигуры в которую вписывается форма поковки от 016 до 032)
Кр – расчетный коэффициент принимаем 13(приложение 3 [1]).
Мп.р = 012513=01625 кг
Минимальная величина радиусов закруглений наружных углов поковки 06 мм.
длина 180+13 = 1813 мм;
высота 13 +13·2=156 мм;
диаметр 253-132 =227 мм;
диаметр 32+132 =346 мм
Q=7800·0000020512=016 кг;
7 Выбор методов обработки
При назначении метода обработки следует стремиться к тому чтобы одним и тем же методом обрабатывать возможно большее количество поверхностей заготовки что дает возможность разработать операции с максимальным совмещением обработки отдельных поверхностей сократить общее количество операций длительность цикла обработки повысить производительность и точность обработки заготовки.
При выборе метода обработки необходимо пользоваться приведенными справочными таблицами экономической точности обработки в которых содержаться сведения о технологических возможностях различных методов обработки. Назначаем метод обработки поверхностей ротора и рукоятки и заносим их в табл. 1.5 и 1.6 соответственно.
Таблица 1.5 - Выбор методов обработки ротора.
Заготовка 16 квалитет
Шлифование черновое 14 квалитет
Наружная цилиндрическая
Точение черновое 13 квалитет
Точение чистовое 11 квалитет
Внутренняя цилиндрическая
Сверление черновое 13 квалитет
Точение черновое 14 квалитет
Сверление черновое 14 квалитет
Однократное фрезерование
Проверим число переходов которые обеспечат заданную точность размеров формы и взаимного расположения поверхностей по величине требуемого уточнения.
Требуемая величина уточнения для определенной поверхности находится по формуле:
где Ку—требуемая величина уточнения;
dзаг—допуск размера формы или расположения поверхностей заготовки;
dдет—допуск размера формы или расположения поверхностей детали.
Затем определяется расчетная величина уточнения по выбранному маршруту обработки поверхности:
где Ку.расч.—расчетная величина уточнения;
К1 К2 Кn—величины уточнения по каждому переходу или операции при обработке рассматриваемой поверхности.
где d1—величина максимальной погрешности размера формы или расположения поверхностей которая имеет место на первом переходе (операции) при обработке рассматриваемой поверхности.
где d2—величина максимальной погрешности размера формы или расположения поверхностей которая имеет место на втором переходе (операции) при обработке рассматриваемой поверхности.
где dn—величина максимальной погрешности размера формы или расположения поверхностей которая имеет место на n—переходе (операции) при обработке рассматриваемой поверхности.
После выбора методов обработки поверхностей детали проверим правильность выбора методов для 2-х поверхностей путём расчёта заданного и расчетного уточнений.
Для поверхности 253-013 ротора.
Заготовка— поковка КГШП соответствует 16 квалитету d=13 мм.
точение черновое 13 квалитет d=033м.
точение чистовое 11 квалитет d=013м.
Расчетное уточнение на первом переходе:
Расчетное уточнение на втором переходе:
Общая расчетная величина уточнения:
Так как Ку=Кур (10=10) то назначенный маршрут обработки поверхности 253-013 обеспечит заданную точность.
На основании выборочных способов обработки разработаем технологический маршрут для детали ротор.
По предварительному маршруту обработки произведем выбор оборудования и составим маршрут обработки.
5 Вертикально-фрезерная с ЧПУ
5 Вертикально-сверлильная с ЧПУ
Таблица 1.6 - Выбор методов обработки рукоятки.
Высота головки 13-02
Шлифование 12 квалитет
Зенкерование 13 квалитет
Растачивание 12 квалитет
Для поверхности внутренней цилиндрической 253+01.
Сверление черновое 14 квалитет d=052 мм.
Сверление чистовое 12 квалитет d=021 мм.
Так как КуКур (62606) то назначенный маршрут обработки внутренней цилиндрической 253+01 обеспечит заданную точность.
На основании выборочных способов обработки разработаем технологический маршрут для детали рукоятка.
0 Вертикально-сверлильная с ЧПУ
0 Плоскошлифовальная
0 Вертикально-протяжная
После выбора технологического маршрута обработки и выбора оборудования заполняем маршрутные карты технологического процесса по ГОСТ 3.11.03-82.
8 Выбор технологических баз
Выбор баз для механической обработки производится с учетом достижения требуемой точности взаимного расположения поверхностей детали по линейным и угловым размерам обеспечения доступа инструментов к обрабатываемым поверхностям обеспечения простоты и унификации станочных приспособлений а так же удобства установки в них заготовки.
В процессе обработки ротора предлагаю использовать следующие схемы базирования.
Чистовыми базами на дальнейших операциях механической обработки ротора будут являться поверхность 30 и поверхности квадратного хвостовика. Установка детали на токарных фрезерных и сверлильных станках позволяет обеспечить доступ к большинству обрабатываемых поверхностей ротора.
Для сверления и нарезания резьбы в качестве баз используем квадратный хвостовик с установкой в оправку.
Рисунок 1.6 – Схема базирования при нарезании внутренней цилиндрической резьбы
Для точения уступа ротор базируется на спутнике по хвостовику.
Рисунок 1.7 – Схема базирования при точении уступа
При фрезеровании уступа ротор в качестве баз используем квадратный хвостовик с установкой в оправку.
Рисунок 1.8 – Схема базирования при фрезеровании уступа
Для точения наружной цилиндрической поверхности ротор закрепляется в патрон.
Рисунок 1.9 – Схема базирования при точении наружной цилиндрической поверхности
Для сверления отверстия 51 в качестве чистовой базы используется 30. Ротор устанавливается в патрон.
Рисунок 1.10 – Схема базирования при сверлении отверстия
При точении ротора по контуру и подрезке торца со стороны хвостовика деталь устанавливается в патрон.
Рисунок 1.11 – Схема базирования при контурном точении наружной поверхности и подрезке торца
При фрезеровании хвостовика деталь устанавливается в патрон
Рисунок 1.12 – Схема базирования при фрезеровании квадратной поверхности
Рисунок 1.13 – Схема базирования при точении наружной цилиндрической поверхности
В процессе обработки рукоятки предлагаю использовать следующие схемы базирования.
Для протягивания внутреннего цилиндрического отверстия рукоятка устанавливается в патрон быстросменный.
Рисунок 1.14 – Схема базирования при протягивании внутреннего цилиндрического отверстия
Устанавливается деталь на магнитной плите при шлифовании торцов.
Рисунок 1.15– Схема базирования при шлифовании торцов
При подрезке торцов растачивании и снятии фаски на внутреннем цилиндрическом отверстии рукоятка устанавливается в патрон.
Рисунок 1.16 – Схема базирования при сверлении внутреннего цилиндрического отверстия
При зенкеровании внутреннего цилиндрического отверстия рукоятка устанавливается в патрон.
Рисунок 1.17 – Схема базирования при зенкеровании внутреннего цилиндрического отверстия
9 Разработка технологического маршрута обработки
На данном этапе разрабатывается общий план обработки детали определяется содержание операций техпроцесса. При этом заполняются маршрутные карты техпроцесса (приложение).
При составлении маршрута обработки воспользуемся базовым технологическим процессом а также следует учитывать следующие положения:
-каждая последующая операция должна уменьшить погрешность и улучшить качество поверхности;
-в первую очередь следует обрабатывать те поверхности которые будут служить технологическими базами для следующих операций.
Предварительная разработка и выбор варианта технологического маршрута ротора
Операция 005 Транспортная
Доставить заготовки на участок обработки
Операция 010 Токарная с ЧПУ
Станок: токарный с ЧПУ 16А20ФЗС15
Точить наружную цилиндрическую поверхность 30 мм
Операция 015 Вертикально-фрезерная с ЧПУ
Станок: вертикально-фрезерный 6Т13Ф20
Фрезеровать квадратный хвостовик
Операция 020 Токарная с ЧПУ
Точить по контуру со стороны хвостовика
Операция 025 Вертикально-сверлильная с ЧПУ
Станок: вертикально-сверлильный 2Р135Ф2
Сверлить внутреннее глухое отверстие 51мм
Операция 030 Токарная с ЧПУ
Подрезать торец в размер 25-05 и точить 253 мм
Операция 035 Вертикально-фрезерная с ЧПУ
Операция 040 Токарная с ЧПУ
Операция 045 Сверлильная
Станок: сверлильный 2Н135
Сверлить внутреннее отверстие и нарезать резьбу М6-7Н
Операция 050 Слесарная
Калибрование резьбы. Опиливание острых кромок.
Операция 055 Моечная
Операция 060 Контрольная
Операция 065 Транспортная
Транспортировать деталь на участок сборки
Предварительная разработка и выбор варианта технологического маршрута рукоятки
Операция 005 Транспортная.
Доставить заготовки на участок обработки
Операция 010 Вертикально-сверлильная с ЧПУ
Зенкеровать отверстие 23+04 мм
Операция 015 Токарная с ЧПУ
Станок: токарный 16А20ФЗС15
Подрезать торец расточить отверстие 25 и снять фаску
Операция 020 Плоскошлифовальная
Шлифовать торцы в размер 13-02
Операция 025 Полировальная
Полировать ручку по контуру
Операция 030 Вертикально-протяжная
Протянуть зубья по внутреннему отверстию
Операция 035 Моечная
Операция 040 Контрольная
Операция 045 Транспортная
10 Разработка технологических операций
На этом этапе окончательно определяется состав и порядок выполнения переходов в пределах каждой технологической операции производится выбор моделей оборудования станочных приспособлений режущих и измерительных инструментов.
Разработка технологических операций для детали ротор
Доставить заготовки на участок обработки.
Трактор-погрузчик Q=20кН. Тара Р1448 2ЯН1286 Q=2тс
Приспособление: четырехкулачковый патрон специальный
Режущий инструмент: Резец проходной 2102-1371 ГОСТ 24996-81
Измерительный инструмент: штангенциркуль ШЦ-1-125-005 ГОСТ 166-89
Фрезеровать квадратный хвостовик в размер 10-0565-0475 и 127-03
Приспособление: фрезерное 7220-6095
Режущий инструмент: фреза 2223-0116 ГОСТ 166-89
Точить по контуру со стороны хвостовика подрезать торец выдерживая длину 11-011 и фаску 06x45°.
Приспособление: трёхкулачковый патрон специальный
Режущий инструмент: резец проходной 2102-1371 ГОСТ 24996-81 резец фасон.2126-4007
Приспособление: оправка 6030-4008
Режущий инструмент: сверло 2300-6175 ГОСТ 10902-77 метчик 2620-1115 ГОСТ 3266-81
Измерительный инструмент: штангенциркуль ШЦ-I-125-01 ГОСТ 166-89 пробка 8130-4159 калибр 8389-40005
Подрезать торец в размер 25-05 .
Черновое точение 253 мм.
Получистовое точение 253 мм.
Чистовое точение 253 мм.
Режущий инструмент: резец проходной 2102-1371 ГОСТ 24996-81
Фрезеровать уступ выдерживая размеры 7+01 и 176+03.
Приспособление: фрезерное 7220-6095.
Режущий инструмент: фреза 2234-0355Р9 ГОСТ 9140-78.
Измерительный инструмент: штангенциркуль Ц 111-1-125-0.05 ГОСТ 166-89
Точить уступ R50 выдерживая размеры 2 и 95-05.
Приспособление: пневмопривод спутник М305.01.001
Режущий инструмент: резец 01214-080404 ГОСТ 19048-80
Измерительный инструмент: штангенциркуль ШЦ-I-125-01 ГОСТ 166-89 шаблон 1176.000
Режущий инструмент: сверло 2300-6175 ГОСТ 10902-77 метчик №1 2620-1115 ГОСТ 3266-81
Разработка технологических операций для детали рукоятка
Зенкеровать отверстие 23+04 мм
Приспособление: подставка 7347-4275 патрон 109-В16 ГОСТ 15935-79
Режущий инструмент: зенкер 2330-4015
Измерительный инструмент: пробка 8154-4088 пробка 8154-4087
Подрезать торец в размер 13 расточить отверстие 25 и снять фаску 06x45°
Приспособление: патрон трёхкулачковый с пневмозажимом
Режущий инструмент: резец подрезной 2112-0007 ГОСТ 18880-73 резец проходной 2102-4003
Измерительный инструмент: пробка 8130-4187
Шлифовать торцы головки в размер 13-02
Приспособление: плита магнитная 7208-83
Режущий инструмент: круг шлиф.1450x63x203 24А40СМ 1К ГОСТ 2424-83
Измерительный инструмент: скоба 8150-4217
Полировать торец ручки соблюдая плавность перехода с полированной поверхностью
Режущий инструмент: круг войлочный Пг400x40x45 ГОСТ 10684
Приспособление: патрон быстросменный 6153-4023 приспособление 7632-4025
Режущий инструмент: прошивка 7632-40254-61
Измерительный инструмент: пробка 8130-4385
11 Технологический процесс сборки
Рисунок 1.18 – Эскиз ключа трещоточного
12 Аналитический расчет припусков на обработку
Произведём расчёт припусков расчётно-аналитическим методом на две различные поверхности а так же построим для них схемы расположения припусков и допусков.
Рассчитаем припуски и предельные размеры по переходам на обработку наружной цилиндрической поверхности ротора 253-013.
Исходные данные: Заготовка – поковка. Класс точности Т4. Группа стали М2. Степень точности С2. Исходный индекс 9 ГОСТ 7505-89.заготовки 009 кг. Обработка детали ведется в патроне. Параметры поковки: 16 кв Rz=80 мкм h=150 мкм (т.27[2]).
Составим технологический маршрут получения поверхности 25-013 с указанием Rz и h по переходам(т.29[2]):
-й переход – точение черновое 14 квалитет Rz=50 мкм h=50 мкм;
-й переход – точение получистовое 12 квалитет Rz=30 мкм h=30мкм;
-й переход – точение чистовое 11 квалитет Rz=25 мкм h=25 мкм.
Пространственное отклонение формы поверхности заготовки рассчитаем по формуле:
где ρсм –смещение полуматриц друг относительно друга штампуемой части заготовки относительно стержня исходного материала ρсм=03 мм (т.34[2]);
ρкор –коробление(кривизна) заготовки.
где Δк – удельная кривизна заготовки Δк=6 мкммм (т.32[2]);
l – длина поверхности l=L2=252=125 мм.
Следовательно имеем : ρкор = 6 · 125 = 75 мкм.
Остаточное пространственное отклонение по переходам определяем по формуле:
где Ку – коэффициент уточнения формы.
-й переход – ρ1 =006·ρ=006·309=1854 мкм;
-й переход – ρ2 =004·ρ=005·1854=0927 мкм;
-й переход – ρ3=002·ρ=004·0927=004 мкм.
Погрешность установки детали на всех операциях у равна нулю (базирование в патроне).
Расчёт минимальных значений межоперационных припусков производим по формуле:
где i – выполняемый переход.
Тогда минимальный припуск по переходам будет следующим:
Расчётные размеры рассчитываем начиная с конечного максимального чертёжного размера последовательным вычитанием 2Zmini каждого технологического перехода:
-й переход DP3 =2517 мм;
-й переход DP2 =2517 +0122=25292 мм;
-й переход DP1 = 25292 +0237=25529 мм;
Заготовка Dр.загот =25529 +1078=26607 мм.
Назначаем допуски на технические переходы по таблице а допуски на заготовку по ГОСТ 7505 – 85.
Заготовка - 1300 мкм;
-й переход – 520 мкм;
-й переход – 210 мкм;
-й переход – 130 мкм;
Предельный размер Dmin определяем округляя Dp до большего значения в пределах допуска на данном переходе а Dmax определяем прибавлением к Dmin допусков соответствующих переходов:
-й переход: D3 m D3 ma
-й переход: D2 m D2 ma
-й переход: D1 m D1 ma
заготовка Dзаг.min=265мм Dзаг.max=265+13=278 мм.
Максимальное предельное значение припусков 2×Zmax.ПР находим как разность наибольших предельных размеров выполняемого и предшествующего переходов а минимальные значения 2×Zmin.ПР – как разность наименьших предельных размеров выполняемого и предшествующих переходов.
Z1 minПР = 265-257=08 мм.
Общий минимальный припуск находим как сумму минимальных промежуточных припусков а общий максимальный – как сумму максимальных припусков:
Z0min=08+03+023=17 мм.
Общий номинальный припуск 2Z0ном вычисляем по формуле:
Z0ном=Z0min+Нз-Нд (1.12)
где Нз и Нд – соответственно нижнее отклонение допуска заготовки и детали.
Z0ном=17+05-013=233мм.
Следовательно номинальный диаметр поверхности заготовки будет равен:
DЗном=DДном+2Z0ном=253+233=2763 мм.
Производим проверку правильности расчётов по формулам:
Zmaxi-2Zmini=Di-1- Di (1.13)
Z0max-2Z0min=DЗ- DД (1.14)
Для нашего случая имеем:
-й переход 210-130=310-230; т.е. 80=80;
-й переход 520-210=610-300; т.е. 310=310;
-й переход 1300-520=1580-800; т.е. 780=780;
общий припуск 2800-1630=1300-130; т.е1170=1170.
Расчёт произведён правильно.
Все расчёты параметров припусков приведём в таблицу 1.11.1.
Таблица 1.7 – Результаты расчёта припусков на поверхность ротора 253-013.
Технологи-ческие переходы обработки поверхности 45js7
Элементы припуска мкм
Расчётный припуск 2Zmin мкм
Расчётный размер Dр мм
Допуск на размер D мкм
Предельный размер мм
Предельные значения припусков мм
На основании таблицы строим схему графического расположения припусков и допусков на обработку поверхности ротора 253-013.
Рисунок 1.19 — Схема графического расположения припусков и допусков на обработку поверхности диаметром 253-013
Выберем технологический маршрут обработки отверстия 253+01 и определим величины Rz и h по переходам:
Заготовка 16 квалитета: Rz = 80 h = 150
-й переход: зенкерование 13 кв. Rz = 40 h = 40
-й переход: растачивание 12 кв. Rz = 32 h = 30
Определим значения пространственных отклонений для заготовки.
где rсм – смещение оси головки относительно общей оси; rсм = 0
rкор – коробление вала;
где К – удельная кривизна заготовки К =8;
l – длина заготовки.
rзаг=rкор = 13×8 = 104 мкм
Остаточное пространственное отклонение по формуле:
где КУ – коэффициент уточнения формы.
Погрешность установки детали на выполняемом переходе eу определяем по формуле:
где eb – погрешность базирования eb = 0;
eз – погрешность закрепления eз = 80.
-й переход r1 = 005×104 = 52 мкм; e1 = 80×005 = 4 мкм
-й переход r2 = 004×52 = 0208 мкм; e2 = 4×004 = 016 мкм
Расчёт минимальных межоперационных припусков:
Расчётный размер диаметра отверстия DР вычислим начиная с конечного максимального чертёжного размера путём последовательного вычитания минимального припуска каждого предыдущего перехода:
-й переход: DР растч.. =254-2×0045 = 2531 мм
-й переход: DР зенк. = 2531-2×0334 = 24642 мм
Назначаем допуски на технологические переходы:
Заготовка – 1300 мкм
-й переход – 330 мкм
-й переход – 210 мкм
Предельный размер Dmax определяем округляя Dp до меньшего значения в пределах допуска на данном переходе а Dmin определяем вычитая из Dmax допуски соответствующих переходов:
-й переход: Dma Dmin растч..= 254-021=2519 мм
-й переход: Dma Dmin зенк. = 2531-033 = 2498 мм
заготовка: Dmax заг. = 24642 мм Dmin заг. = 24642-13 = 23342 мм
Минимальные предельное значение припусков 2×Zmin.ПР. находим как разность наибольших предельных размеров выполняемого и предшествующего переходов а максимальные значения 2×ZmaxПР – как разность наименьших предельных размеров выполняемого и предшествующих переходов.
Общий минимальный припуск находим как сумму минимальных промежуточных припусков а общий максимальный – как сумму максимальных припускав:
Общий номинальный припуск находим по формуле:
где ВЗ – верхнее отклонение заготовки по ГОСТ 2590 – 71
ВД – верхнее отклонение детали по чертежу.
Тогда номинальный диаметр заготовки:
Проверяем правильность произведённых расчётов:
-й переход: 021-009 =033-021 мм 012=012 мм
-й переход: 1638-0668 = 13-033 мм 097=097 мм
Общий припуск: 1848-0758 = 13-021 мм 109=109 мм
Проверка правильна значит расчёты межоперационных припусков произведены верно. Все расчёты параметров припусков приведём в таблицу 1.11.2.
Таблица 1.8 Результаты расчёта припусков на поверхность рукоятки 253+01
переходы обработки поверхности
Расчётный припуск 2×Zmin мкм
Расчётный размер Dp мкм
Допуски размеров мкм
Предельные размеры припусков мкм
На основании таблицы строим схему графического расположения припусков и допусков на обработку поверхности рукоятки 25+01.
Рисунок 1.20 — Схема графического расположения припусков и допусков на обработку отверстия 25+01
13 Расчет режимов резания
Произведем расчет режимов резания для двух разных типов операций. Одной – чернового точения поверхности ротора 253-013 на операции « 030 Токарная с ЧПУ». Другой – протягивания отверстия рукоятки 253+01 на операции « 030 Токарная с ЧПУ».
Расчет проведем по эмпирическим формулам по методике [3].
Произведём расчёт режимов резания обработки размера 25-13 точением.
Глубина резания – t = 2 мм;
Подача– So = 06 ммоб.
Скорость резанья при точении – окружная скорость вращения заготовки:
Т – период стойкости и показатели степеней находим по таблицам:
СV = 290; y = 035; m = 02; T = 60 мин.
KV = KМV× KПV× KИV(1.22)
где KМV – коэффициент учитывающий качество обрабатываемого материала;
KПV – коэффициент учитывающий состояние поверхности заготовки;
KИV – коэффициент учитывающий материал инструмента.
где sB – физический параметр характеризующий обрабатываемый материал;
КГ и nv – коэффициент и показатель степени характеризующие группу стали по обрабатываемости.
KИV = 115; KПV = 08;
Определяем окружную скорость вращения заготовки:
Силы резания при точении Н:
где Ср – поправочный коэффициент Ср =300;
х у n – показатели степеней х=1 у=075 n = -015;
Кр – поправочный коэффициент.
где - коэффициенты учитывающие фактические условия резания
Кφp=108 Кλp=1 Кp=087.
Определяем Кмр по формуле:
где n0 - показатель степени nv = 09.
Определим частоту вращения по формуле:
где n - частота вращения шпинделя мин-1;
Частота вращения заготовки:
Принимаем n = 1350 oб мин.
Определяем мощность затрачиваемую на резание по формуле:
Находим мощность резания:
Определяем основное время То:
где Sо - оборотная подача обмин ;
Таблица 1.19 - Сводная таблица режимов резания ротора
Наименование операции или перехода
Вертикально-фрезерная с ЧПУ
Вертикально-свер-лильная с ЧПУ
-получистовое точение
Вертикально-фрезерная с ЧПУ
14 Определение норм времени на операции
При серийном производстве норма штучного времени определяется по формуле:
где То—основное (машинное) время обработки детали мин;
Тв—вспомогательное время на операцию (время на установку и снятие детали подвод и отвод инструмента время на управление станком и т.д.) мин;
Тобс—время на техническое и организационное обслуживание рабочего места (время на замену затупившегося инструмента время на уборку рабочего места в конце работы) мин;
Тотд—время на отдых и личные надобности мин.
где Тус—время на установку и снятие детали мин;
Тзо—время на закрепление и открепление детали мин;
Туп—время на приемы управления мин;
Тиз—время на измерение детали мин.
где Ттех—время на техническое обслуживание рабочего места мин;
Торг—время на организационное обслуживание рабочего места мин.
Оперативное время Топ:
Время на организационное и техническое обслуживание определяется в процентах от оперативного времени.
Tтех + Tорг =к*Tоп100%
где П—затраты времени на отдых в процентном отношении к оперативному.
Рассчитаем норму штучного калькуляционного времени для операции 015 ротора (вертикально-фрезерной). Производство среднесерийное масса детали 045 кг.
Тус+Тзо=006+0024=0084 мин Туп=001+02=021 мин. — время на включение станка и подвод инструмента (станок включается кнопкой)
Время на измерение штангенциркулем ШЦ-I-125-005 Тиз=012 мин
Вспомогательное время:
Тв=0084+021+012=0414 мин
Топ=16+0414 =2014 мин
То=16 - основное время на обработку заготовки на данной операции
Затраты времени на обслуживание рабочего места и отдых в процентном отношении к оперативному равно 7% тогда:
Тобс=2014·7100=0145 мин
Подставляем полученные значения времен:
Тшт=16+0414+0145=215 мин
Tп.з.- подготовительно-заключительное время на партию заготовок
- время на наладку станка и установку приспособлений 14 мин
- время на установку фрез (1 шт.) 2 мин
- получить наряд чертеж технологическую документацию режущий и вспомогательный инструмент контрольно-измерительный инструмент приспособление заготовки исполнителем до начала и сдать их после окончания обработки партии деталей 13 мин
-ознакомится с работой чертежом технологической документацией осмотреть заготовки 20 мин
-инструктаж мастера 20 мин
Tп.з.=14+2+13+2+2=33 мин
Количество деталей в партии:
n=50000·6254=1181 шт.
Время приходящееся на одну заготовку из партии:
Tшт.к.=0028+215=218 мин
Рассчитаем норму штучного калькуляционного времени для операции 015 рукоятки (Токарная с ЧПУ). Производство среднесерийное масса детали 0125 кг.
- установить заданное взаимное положение детали и инструмента по координатам XYZ и при необходимости произвести подналадку 032 мин
- включить и выключить лентопротяжный механизм 004 мин
- открыть и закрыть крышку лентопротяжного механизма перемотать заправить ленту в считывающее устройство 031 мин
- проверить переход деталиинструмента в заданную точку после
- продвинуть перфоленту в исходное положение 019 мин
- установить и снять щиток от набрызгивания эмульсией 003 мин
Тус+Тзо=005+0024=0074 мин
Туп=031+004+032+015+019+003=0752 мин.
Время на измерение штангенциркулем ШЦ-I-125-005: Тиз=012 мин Вспомогательное время:
Тв=0074+0752+012=0946 мин
Топ=0946+065=1596 мин
То=065 - основное время на обработку заготовки на данной операции
Затраты времени на обслуживание рабочего места и отдых в процентном отношении к оперативному равно 6% тогда:
Тобс=1596·6100=0096 мин
Тшт=0946+065+0096=169 мин
- получить наряд чертеж технологическую документацию программоноситель режущий и вспомогательный инструмент контрольно-измерительный инструмент приспособление заготовки исполнителем до начала и сдать их после окончания обработки партии деталей 13 мин
-ознакомится с работай чертежом технологической документацией осмотреть заготовки 20 мин
-установить и снять патрон трехкулачковый 25 мин
- установить исходные режимы станка 015 мин
- установить и снять кулачки 65 мин
-расточить кулачки 62 мин
-установить и снять инструментальный блок или отдельный режущий инструмент (время на один инструмент( блок)) 02 мин
-установить программоноситель в считывающее устройство
-проверить работоспособность считывающего устройства и
-ввести программу в память системы с ЧПУ с
программоносителя 15 мин
-установить исходный координаты X и Z (настроить нулевое
Tп.з.=13+2+2+25+015+65+62+02+1+1+15+2=385 мин
Время приходящиеся на одну заготовку из партии
Tшт.к.=003+169=17 мин
Нормы времени на остальные операции назначаем по нормативным справочникам. Рассчитанные и назначенные времена сведем в таблицу.
Таблица 1.20 - Сводная таблица технических норм времени по операциям ротора мин.
Вертикально-сверлильная с ЧПУ
15 Определение необходимого количества оборудования
Для серийного производства количество станков S определяется по формуле:
Тшт—штучное время обработки изделия мин;
F—действительный годовой фонд времени работы оборудования час.
Коэффициент загрузки оборудования:
где Sпр—принятое количество станков.
Объём выпуска деталей “ротор” – 50000
На основании рассчитанных коэффициентов строим график загрузки оборудования.
Рисунок 1.21 – График степени загружённости станков на операциях ротора:
-й столбец Токарная с ЧПУ станок модели 16А20Ф3С15
-й столбец Вертикально-фрезерная станок модели 6Т13Ф20
-й столбец Вертикально-сверлильная станок модели 2Р135Ф2
-й столбец Сверлильная станок модели 2Н135
Анализируя полученные данные необходимо отметить неудовлетворительную загрузку станков. Поэтому следует совместить токарную обработку и выполнять операции 010 020030 и 040 на одном станке. Загрузка оборудования в этом случае будет составлять около 75%. Большинство оборудования универсальное поэтому его следует догружать операциями по обработке других деталей для увеличения коэффициента загрузки оборудования.
Объём выпуска деталей “рукоятка” – 50000
Рисунок 1.22 – График степени загружённости станков на операциях рукоятки:
-й столбец Плоскошлифовальная станок модели 2Н118
-й столбец Вертикально-протяжная станок модели 3М6341.16 Уточнение типа производства по коэффициенту закрепления операций.
Уточненный расчет типа производства основывается на определении коэффициента закрепления операций Кзо:
где О—количество всех различных технологических операций выполненных в течении месяца;
Р—число рабочих мест необходимых для выполнения месячной программы.
Согласно ГОСТа для среднесерийного типа производства Кзо=10 20
Число рабочих мест для выполнения определенной i-ой операции определяем по формуле:
где Nм—месячный объем выпуска детали (2500 шт);
Тшт—штучное время на выполнение определенной операции мин;
Fм—месячный фонд времени работы оборудования (196 час);
Кв—коэффициент выполнения норм времени. Кв=11 13
Рассчитанное число рабочих мест округляем до ближайшего большего целого числа Рi.
Коэффициент загрузки данных рабочих мест выполняемой операцией:
Количество операций выполняемых на этом рабочем месте при его нормативной загрузке определяем по формуле:
где: hн=07 085—нормативный коэффициент загрузки для среднесерийного
Общее количество операций выполняемых на всех рабочих местах проектируемого техпроцесса и общее количество рабочих мест определяется как сумма всех операций и сумма всех рабочих мест соответственно.
Результаты расчетов сведем в таблицу.
Таблица 1.22 — Определение типа производства детали “ротор”.
Определяем коэффициент закрепления операций:
Коэффициент Кзо находится в промежутке от 1 до 10 причем ближе к 10. Следовательно принимаем среднесерийный тип производства.
Таблица 1.23 — Определение типа производства детали “рукоятка”.
Коэффициент Кзо равен 10. Следовательно принимаем среднесерийный тип производства.
Определим такт выпуска продукции t:
где F—действительный годовой фонд времени работы оборудования при 2-ух сменной работе (4015 час).
Расчёт и проектирование средств технологического оснащения
1 Проектирование станочного приспособления
1.1 Описание конструкции и работы приспособления
Проектируемое приспособление предназначено для точения уступа. В данном случае приспособление устанавливается на токарный станок с ЧПУ модели 16А20Ф3С15.
Приспособление представляет собой спутник на который устанавливаются восемь деталей ротора по окружности и прижим в центре. С помощью переходника который соединен со штоком пневмоцилиндра происходит прижим спутника к планшайбе. Торец ротора упирается в диафрагму. На периферии установлен штифт который не предохраняет спутник от проворота относительно планшайбы. Планшайба установлена на шпинделе токарного станка. Приспособление является восьмиместным что увеличивает производительность в условиях среднесерийного производства.
Закрепление детали осуществляется следующим образом:
детали устанавливаются в спутник;
спутник устанавливается на планшайбу;
включают пневмоцилиндр который осуществляет зажим спутник.
1.2 Расчет сил зажима заготовки
Расчет сил зажима сводится к решению задачи статики на равновесие твердого тела под действием внешних сил. Величина сил зажима определяется из условия равновесия всех сил при полном сохранении контакта технологических баз обрабатываемой заготовки с установочными элементами приспособления и невозможности ее сдвига или поворота в процессе обработки.
Условия установки и закрепления детали в приспособлении дают возможности считать приспособление на возможность перекоса заготовки относительно своей оси. Поэтому будем вести расчет на перекос оси под действием силы резания Рх.
Рисунок 2.1 - Схема расположения сил резания
На заготовки действуют сила зажима Р1 и сила резания Рx
Запишем уравнение равновесия:
где kз—коэффициент запаса; kз =25
l1 l2—плечи соответственно сил Px P1
коэффициенты и показатели степеней определяем по таблицам:
СР = 339; х = 10; у = 05; n=-04.
Тогда окружная сила резания равна:
Из приведенных выше расчетов видно что сила зажима необходимая для того что бы избежать перекоса заготовки намного выше силы резания Рх = 880 Н.
Рассчитаем диаметр пневмоцилиндра необходимого для создания силы зажима.
Определяем диаметр цилиндра D:
где p—давление в пневмосистеме (р = 05 МПа);
h = 085—КПД пневмоцилиндра;
Pш – усилие на штоке.
Принимаем стандартное значение диаметра D = 180 мм.
1.3 Расчет приспособления на точность
Цель расчета приспособления на точность заключается в определении требуемой точности изготовления приспособления по выбранному точностному параметру и задании допусков размеров деталей и элементов приспособления.
где Епр—погрешность приспособления мм;
d—допуск выполняемого размера мм;
Кт—коэффициент учитывающий отклонение рассеивания значений составляющих величин от закона нормального распределения (Кт = 11);
Kт1—коэффициент учитывающий уменьшение предельного значения погрешности базирования при работе на настроенных станках (kт1 = 08);
eб—погрешность базирования мм;
eз—погрешность закрепления мм;
eу—погрешность установки приспособления на станке мм;
eи—погрешность положения рабочих поверхностей рабочих элементов в результате их изнашивания в процессе эксплуатации приспособления мм;
eпи—погрешность от перекоса инструмента из-за неточности изготовления направляющих элементов приспособления мм;
kт2—коэффициент учитывающий долю погрешности обработки в суммарной погрешности вызываемой факторами независящими от приспособления (kт2 = 07);
v—экономическая точность обработки (v = 04 мм).
eб = 62 мкм – величина допуска для размера R50 выполненного по 14 квалитету.
eу = 0 т. к. эта погрешность будет одинакова для всей партии заготовок и ее можно компенсировать настройкой инструмента. Погрешность от износа определяем по формуле:
где b — постоянная зависящая от вида установочного элемента и условия контакта (b = 00008 мкм);
N—количество контактов заготовки с опорой (установок в приспособление снятий с него) в год.
eпи=0 — погрешности ос перекоса инструмента не будет
Подставим все значения в (2.5):
На основании расчета можно сделать вывод что погрешность размера R50 при изготовлении приспособления не должна превышать 0307 мм.
РУпок.cdw

Смещение по разъёму не более 0.3 мм
Остаток облоя по контуру не более 0.3 мм
коробление и спиральность не более 0.6 мм
Неуказанные радиусы закруглений углов R1 мм
На поверхностях поковок
не подлежащих меха нической обработке
не должно быть кузнечных дефектов
влияющих на прочность и ухуд-
шающих внешний вид изделия
Дефекты на поверхностях поковок
подлежащих механической обра-
если их глубина такова
что на механическую
обработку остаётся не менее 50% номинального одностороннего при-
Твердость 187 217 HB (сталь 40Х)
Поверхность поковок должна быть очищена от окалины
Поковка с примерной массой 0.2 кг
*Допускается ширина площади среза облоя при обрезка или обдирке
Сталь 40Х ГОСТ4543-71
Рукоятка.frw

Наладка.cdw

Схема движения инструмента Т02
Схема движения инструмента Т01
Карта инструментальной
план.cdw

ДП 03.01.753.30.00.000
- шина электрическая
- фонтанчик питьевой
- подвод сжатого воздуха
Условные обозначения.
- контейнер для деталей и заготовок
- железобетонная опора
Служба механика цеха
картыР.doc
Наименование операции
Обозначение программы
При выполнении операции соблюдать инструкцию по охране труда
Установить деталь в приспособление и закрепить
Приспособление четырехкулачковый патрон
Точить наружную цилиндрическую поверхность 30 мм
Резец проходной 2102-1371 ГОСТ 24996-81
Штангенциркуль ШЦ-1-125.01 ГОСТ 166-89
Открепит деталь снять и уложить в тележку
ГОСТ 3.1404-86 Форма 2
Вертикально-фрезерная с ЧПУ
Приспособление фрезерное 7220-6095
Фрезеровать квадратный хвостовик в размер 10-0565-0475 и 127-03
Фреза 2223-0116 ГОСТ 166-89
Штангенциркуль ШЦ-1-125-005 ГОСТ 166-89
Приспособление трёхкулачковый патрон
Точить по контуру со стороны хвостовика подрезать торец выдерживая длину 11-011 и фаску 06x45°
Резец проходной 2102-1371 ГОСТ 24996-81 резец фасон.2126-4007
Вертикально-сверлильная с ЧПУ
Приспособление оправка 6030-4008
Сверлить внутреннее глухое отверстие 51мм
Сверло 2300-6175 ГОСТ 10902-77 метчик 2620-1115 ГОСТ 3266-81
Штангенциркуль ШЦ-I-125-01 ГОСТ 166-89 пробка 8130-4159 калибр 8389-40005
Подрезать торец в размер 25-05 .
Черновое точение 253 мм.
Получистовое точение 253 мм.
Чистовое точение 253 мм.
Приспособление фрезерное 7220-6095.
Фрезеровать уступ выдерживая размеры 7+01 и 176+03.
Фреза 2234-0355Р9 ГОСТ 9140-78.
Приспособление пневмопривод спутник М305.01.001
Точить уступ R50 выдерживая размеры 2 и 95-05.
Резец 01214-080404 ГОСТ 19048-80
Штангенциркуль ШЦ-I-125-01 ГОСТ 166-89 шаблон 1176.000.
Приспособление четырехкулачковый патрон.
Сверлить внутреннее отверстие и нарезать резьбу М6-7Н.
Сверло 2300-6175 ГОСТ 10902-77 метчик №1 2620-1115 ГОСТ 3266-81
картыСБ.doc
Наименование операции
Обозначение программы
При выполнении операции соблюдать инструкцию по охране труда
Установить ротор на подставку с неподвижной головкой
Надеть ручку на ротор
Взять пружину и сектор и вставить пружину двумя концами в отверстие сектора
Вставить в паз ротора сектор с пружиной
Наложить крышку вставив штифт в перегиб пружины
Положить в отверстие под винт1-2 гранулы полиэтилена
Переключить крышку 2-3 раза удостоверившись в работе сектора. Проверить работоспособность ключа.
Для этого установить ключ квадратом ротора в неподвижную головку квадрата 10 и ключ в обе стороны
(в одну сторону ключ работает на Мкр в другую слышен характерный треск сектора по зубьям рукоятки)
ГОСТ 3.1404-86 Форма 2
Установить деталь в приспособление и закрепить
Приспособление патрон трёхкулачковый с пневмозажимом
Подрезать торец в размер 13
Резец подрезной 2112-0007 ГОСТ 18880-73 резец проходной 2102-4003
Расточить отверстие 25 и снять фаску 06x45°
Открепит деталь снять и уложить в тележку
Приспособление плита магнитная 7208-83
Шлифовать торцы головки в размер 13-02
Круг шлиф.1450x63x203 24А40СМ 1К ГОСТ 2424-83
Полировать торец ручки соблюдая плавность перехода с полированной поверхностью
Круг войлочный Пг400x40x45 ГОСТ 10684
Вертикально-протяжная
Приспособление патрон быстросменный 6153-4023 приспособление 7632-4025
Протянуть зубья по внутреннему отверстию в размер 253
Прошивка 7632-40254-61
карты.doc
Наименование операции
Вертикально-сверльльная с ЧПУ
Обозначение программы
При выполнении операции соблюдать инструкцию по охране труда
Установить деталь в приспособление и закрепить
Приспособление подставка 7347-4275 патрон 109-В16 ГОСТ 15935-79
Зенкеровать отверстие 23+04 мм
Пробка 8154-4088 пробка 8154-4087
Открепит деталь снять и уложить в тележку
ГОСТ 3.1404-86 Форма 2
Приспособление патрон трёхкулачковый с пневмозажимом
Подрезать торец в размер 13
Резец подрезной 2112-0007 ГОСТ 18880-73 резец проходной 2102-4003
Расточить отверстие 25 и снять фаску 06x45°
Приспособление плита магнитная 7208-83
Шлифовать торцы головки в размер 13-02
Круг шлиф.1450x63x203 24А40СМ 1К ГОСТ 2424-83
Полировать торец ручки соблюдая плавность перехода с полированной поверхностью
Круг войлочный Пг400x40x45 ГОСТ 10684
Вертикально-протяжная
Приспособление патрон быстросменный 6153-4023 приспособление 7632-4025
Протянуть зубья по внутреннему отверстию в размер 253
Прошивка 7632-40254-61
Фрагмент.frw

Сборка11.cdw

РУ.cdw

** Размеры для справок
Допускается применение стали 40ХФА по
HRCэ для рукояток из стали 40Х
HRCэ для рукояток из стали 40ХФА
На поверхности ручек не допускаются раковины
Отклонение от плоскостности не должно пре-
Остальные технические требования по ГОСТ
605-83 и тУ2-035-590-84
Покрытие: Хим. окс. прм.
Ц15.хр. или Н12.Х1 по
Сталь 40Х ГОСТ4543-71
ОперЭскРу.cdw

Вертикально-фрезерная с ЧПУ
Вертикально-сверлильная
МКРСБ.DOC
Код наименования операции
Обозначение документа
Код наименования оборудования
Подбор групп деталей и их внешний осмотр
Недопускаются раковины трещины следы коррозии
Сборка ключа трещоточного
Проверить работоспособность ключа в обе стороны
МКРУ1.DOC
Код наименования операции
Обозначение документа
Код наименования оборудования
Вертикально -сверлильная
МКР1.DOC
Код наименования операции
Обозначение документа
Код наименования оборудования
Вертикально -фрезерная
Вертикально -сверлильная
МКРУ 2.DOC
Код наименования операции
Обозначение документа
Код наименования оборудования
Наименование детали сб. единицы или материала
Вертикально-протяжная
МКР 2.DOC
Код наименования операции
Обозначение документа
Код наименования оборудования
Наименование детали сб. единицы или материала
Вертикально -фрезерная
контроль.cdw

Втулку после запресовки шлифовать
допуск перпендикурности 0
ДП 03.01.753.22.00.000
Контрольное приспособление
РУпок.cdw

Смещение по разъёму не более 0.3 мм
Остаток облоя по контуру не более 0.3 мм
коробление и спиральность не более 0.6 мм
Неуказанные радиусы закруглений углов R1 мм
На поверхностях поковок
не подлежащих меха нической обработке
не должно быть кузнечных дефектов
влияющих на прочность и ухуд-
шающих внешний вид изделия
Дефекты на поверхностях поковок
подлежащих механической обра-
если их глубина такова
что на механическую
обработку остаётся не менее 50% номинального одностороннего при-
Твердость 187 217 HB (сталь 40Х)
Поверхность поковок должна быть очищена от окалины
Поковка с примерной массой 0.2 кг
*Допускается ширина площади среза облоя при обрезка или обдирке
ДП 03.01.753.13.00.000
Сталь 40Х ГОСТ4543-71
Схема Сборки.cdw

ДП 03.01.753.18.00.00.000
ДП 03.01.753.00.00.005 1
ДП 03.01.753.00.00.003 1
ДП 03.01.753.00.00.04 1
ДП 03.01.753.00.00.006 1
ДП 03.01.753.00.00.001 1
ДП 03.01.753.00.00.007 1
ДП 03.01.753.00.00.002
ДП 03.01.753.00.00.000 СБ
план.cdw

ДП 03.01.753.30.00.000
- шина электрическая
- фонтанчик питьевой
- подвод сжатого воздуха
Условные обозначения.
- контейнер для деталей и заготовок
- железобетонная опора
Служба механика цеха
Сборка11.cdw

Допускается декоративное покрытие пластизолем Д 9ЭН ТУ-02-56-90
РУ.cdw

** Размеры для справок
Допускается применение стали 40ХФА по
HRCэ для рукояток из стали 40Х
HRCэ для рукояток из стали 40ХФА
На поверхности ручек не допускаются раковины
Отклонение от плоскостности не должно пре-
Остальные технические требования по ГОСТ
605-83 и тУ2-035-590-84
Покрытие: Хим. окс. прм.
Ц15.хр. или Н12.Х1 по
ДП 03.01.753.12.00.000
Сталь 40Х ГОСТ4543-71
ОперЭскРу.cdw

Вертикально-сверлильная
Вертикально-протяжная
ДП 03.01.753.17.00.000
экономика.cdw

Проектируемый вариант
Годовой выпуск продукции:
в натуральном выражении
- в стоимостном выражении по цене базового предприятия
Общая стоимость основных производственных фондов
Производственная площадь цеха (участка)
Численность работающих
- основных производственных рабочих
- вспомогательных рабочих
Трудоёмкость изготовления единицы продукции
Выпуск продукции на одного производственного
- в стоимостном выражении
- в натуральном выражении
Фондовооруженность труда
Средняя загрузка оборудования
Цеховая стоимость годового объема выпуска продукции
Размер чистой прибыли
Рентабельность продукции
Абсолютная (общая) эффективность капиталовложений
Годовой экономический эффект
технико-экономические
ДП 03.01.753.51.00.000
Основные технико-экономические показатели проекта
стан.cdw

Масленку заполнить смазкой ЦИАТИМ - 202 ГОСТ
В плоскости 1-1 обеспечить зазор 0
Маркировать обозначение чертежа
ДП 03.01.753.21.00.000
Протяга.cdw

*. Размеры для справок
Материал : рабочей части -сталь Р6М5 (ГОСТ 19265-85)
вой части-сталь Р6М5 (ГОСТ 19265-85).
Размеры центровочных отверстий по ГОСТ 14034-74
Твердость режущей части и задней направляющей HRC 61 66
Неуказанные предельные отклонения размеров h14
Остальные технические требования по ГОСТ 9126-76
Маркировать :обозначение протяжки
материал режущей части
товарный знак завода-изготовителя.
ДП 03.01.753.23.00.000
Сталь Р6М5 ГОСТ 19265-85
Предельное отклонение
Профиль режущих зубьев (10:1)
Схема резания протяжки
ОперЭскР.cdw

Р.cdw

Твердость 41.5 46.5 41.5 46.5 HRCэ
Покрытие хим. окс. прм. по ГОСТ 9.306-85
* Размер обеспечивается инструментом
ДП 03.01.753.11.00.000
Рпок.cdw

Смещение по разъёму не более 0.3 мм
Остаток облоя по контуру не более 0.3 мм
коробление и спиральность не более 0.6 мм
Неуказанные радиусы закруглений R1 мм
Допускаемые отклонения штампованных уклонов
Твердость 187 217 HB (сталь 40Х)
Поверхность поковок должна быть очищена от окалины
Поковка с примерной массой 0.0675 кг
*Допускается ширина площади среза облоя при обрезке или обдирке
ДП 03.01.753.14.00.000
Сталь 40Х ГОСТ4543-71
наладка1.cdw

нал.frw

ПЗ.doc
Важная роль в ускорении научно-технического прогресса в машиностроении отводится подготовке высоко квалифицированных инженерных кадров освоению ими современных способов изготовления и контроля продукции методик проектирования прогрессивных технологических процессов.
Данный курсовой проект ставит перед собой цель изучение методики разработки технологического процесса изготовления ключа трещоточного а также проектирования станочных и контрольных приспособлений на базе имеющихся данных. В данном курсовом проекте будут рассмотрены такие вопросы как:
– определение типа производства;
– анализ конструкции и технологичности детали;
– выбор схем базирования и методов обработки поверхностей;
– выбор оборудования;
– расчет и назначение припусков;
– расчет режимов резания и нормирование операций;
– расчет и проектирование технологического оснащения производства;
Помимо всего курсовой проект включает в себя необходимый минимум графического материала по рассмотренным вопросам документацию к чертежам и сам технологический процесс.
Разработка технологического процесса изготовления детали
1 Назначение и конструкция сборочной единицы
Заданные детали (ротор и рукоятка) входят в состав ключа трещоточного.
Ротор предназначен для базирования на нём составных сборочных ключа трещоточного. Ротор не является симметричным имеются два глухих отверстия причем одно из них перпендикулярно оси ротора.
Рисунок 1.1 – Эскиз ротора
Рукоятка предназначена для удобного использования ключа трещоточного и для базирования ротора на нём. Конструкция рукоятки проста и удобна. Есть сквозное отверстие которое получается штамповкой.
Рисунок 1.2 – Эскиз рукоятки
Ключ трещоточный состоит из: 1 – крышки 2 - ротора 3 - сектора 4 – пружины 5 – рукоятки 6 – гранулы полиэтилена 7 - винта.
Рисунок 1.3 – Эскиз ключа трещоточного
Установить ротор на подставку с неподвижной головкой. Надеть ручку на ротор. Взять пружину и сектор и вставить пружину двумя концами в отверстие сектора. Вставить в паз ротора сектор с пружиной. Наложить крышку вставив штифт в перегиб пружины. Завернуть винт до упора затем отвернуть его на 12 34 оборота. Переключить крышку 2-3 раза удостоверившись в работе сектора. Проверить работоспособность ключа. Для этого установить ключ квадратом ротора в неподвижную головку квадрата 10 и ключ в обе стороны (в одну сторону ключ работает на Мкр в другую слышен характерный треск сектора по зубьям рукоятки).
К детали предъявляются высокие требования по точности жёсткости а к материалу по прочности износостойкости.
Для повышения физических свойств поверхностного слоя деталь подвергают термообработке - ТВЧ.
Материал детали – конструкционная легированная сталь 40Х (ГОСТ 4543-71) широко используется для изготовления различных видов и типоразмеров валов осей шестерен и т.п. работающих в условиях требующих повышенной прочности и износостойкости.
Таблица 1 - Химический состав стали 40Х (ГОСТ 4543-71) .
Таблица 2 - Механические свойства стали 40Х (ГОСТ 4543-71) .
Предел прочнос-ти в МПа
Предел текучес-ти т МПа
Относи-тельное удлинение %
Относи-тельное сужение %
Рассмотрим основные поверхности ротора исходя из ее служебного назначения.
Рисунок 1.4 – Поверхности ротора
Основные конструкторские базовые поверхности применяемые для базирования детали в механизме.
Основными базовыми поверхностями являются: торцы буртов 4 5.
Вспомогательные конструкторские базовые поверхности применяемые для базирования других деталей в механизме.
Такими поверхностями будут являться: резьбовое отверстие 17 боковая поверхность отверстия 11 16 цилиндрическая поверхность 3.
Исполнительные поверхности посредством которых деталь выполняет свои функции в механизме: цилиндрические поверхности 10.
Свободные поверхности предназначены для ограничения размера детали и не имеют функционального назначения их размер и форма выбирается произвольно. Такими поверхностями являются 1 2 6 7 8 9 12 13 14 15.
Рисунок 1.5 – Поверхности рукоятки
Основных базовых поверхностей нет.
Вспомогательные конструкторские базовые поверхности: 2 3 4 5.
Исполнительные поверхности: 4 6 8.
Свободные поверхности: 1 7 9 10.
2 Анализ технических условий изготовления детали
Проведём анализ технологичности конструкции деталей (ротора и рукоятки).
При получении заготовок отсутствуют сложные разъемы отрезных штампов.
Основные поверхности являются удобными для базирования и закрепления поэтому дополнительные поверхности не вводятся.
Материал детали сталь Ст40Х механическая обработка которого не вызывает сложностей при обработке твердым сплавом.
Доступность поверхностей деталей для обработки и измерения.
В конструкции ротора присутствуют места резких изменений формы концентраторы напряжений а в рукоятке нет.
Для получения требуемой точности размеров и шероховатости деталей можно применять станки нормального класса точности.
Ротор и рукоятка – жесткие изделия.
Наличие глухих отверстий в роторе одно из которых перпендикулярно к оси детали.
Учитывая все вышеперечисленные факторы у данных деталей удовлетворительная технологичность.
3 Ориентировочное определение типа производства
Предварительно тип производства определяем по таблице 3 с.8 [2]. С учетом массы деталей (0045 и 0125 кг) и годовой программы 50 000принимаем среднесерийный тип производства. Среднесерийное производство характеризуется большой номенклатурой изделий изготовляющихся не большими партиями и не большим объемом выпуска. При среднесерийном производстве используются как универсальные так и станки с ЧПУ которые оснащаются большим количеством инструмента что позволяет снизить трудоемкость и обеспечить высокую гибкость производства при переналадке его на другой тип производства. После разработки технологического процесса механической обработки а также расчета количества основного оборудования тип производства будет уточнен.
4 Анализ базового варианта технологического процесса
Анализ базового технологического процесса обработки детали приведём с точки зрения обеспечения заданного качества детали (точность и шероховатость обрабатываемых поверхностей а также технических требований к детали) производительности обеспечения заданного объёма выпуска.
Метод получения заготовки ротора – прокат нормальной точности. Этот метод не позволяет получить точную заготовку. Можно было бы получать заготовку штамповкой на КГШП с напусками лишь на концах заготовки.
В целом для условий серийного производства технологический процесс выполнен согласно требованиям типовых техпроцессов. Недостатком можно считать большую дифференциацию операций что приводит к увеличению количества используемого оборудования.
Можно было бы использовать более совершенное оборудование концентрировать обработку на станках что привело бы к снижению материальных затрат.
Таким образом можно было бы операции 010-ю 015-ю 020-ю совместить в одну токарно-гидрокопировальную используя станок 1713Ц оснащенный 4-х сторонним поворотным барабаном это уменьшит затраты вспомогательного времени на изготовление детали повысит точность обработки она будет произведена за 1 установ. Позволит уменьшить энергетические и материальные затраты используемого оборудования. Так же это позволит убрать операцию 035-ю т. к. точности полученной на токарно-гидрокопировальном станке в ходе предыдущей обработки будет достаточно для проведения дальнейшей обработки.
Анализируя данный техпроцесс можно отметить использование настольно-сверлильных станков НС-12А на сверлильных операциях. На мой взгляд использование в среднесерийном производстве настольно-сверлильных станков является нерациональным. По-моему использование оборудования на операциях 025 035 065 090 нецелесообразным так как размеры детали малы а точность невелика. Предлагаю использовать на всех вышеуказанных операциях станок меньших габаритов. Экономическую выгоду мы получим уменьшая время на механическую обработку за счёт использования более прогрессивного оборудования. Также целесообразно провести оптимизацию режимов резания по функции минимальных затрат. На 065-й операции использование двух метчиков можно заменить одним так как точность резьбы М6-Н7 не требует двух инструментов.
Используемые в базовом техпроцессе станочные приспособления являются стандартными (кроме специальных станков автоматов и полуавтоматов) и нет существенных причин их замены на специальные.
Режущий инструмент используемый в базовом техпроцессе - из быстрорежущей стали он стандартизирован. Его можно оставить таким же за исключением применения специального инструмента используемого на 035 – ой операции: резец фасонный. Это позволит уменьшить основное время обработки и повысить производительность оборудования.
Контрольный и измерительный инструмент в базовом варианте – штанген-инструмент средства активного контроля и специальные калибры подходят для использования в условиях серийного производства и не требуют кардинального пересмотра схем контроля в новом техпроцессе.
Для удобства анализа базового технологического процесса изготовления ротора представим его в виде таблицы 1.4.1.
Метод получения заготовки рукоятки – штамповка на молотах. Этот метод позволяет получить довольно таки точную заготовку без напусков.
Для условий серийного производства технологический процесс рукоятки выполнен согласно требованиям типовых техпроцессов. Недостатком можно считать небольшую дифференциацию операций что приводит к увеличению количества используемого оборудования на одну единицу.
Таким образом можно было бы операции 060-ю 070-ю совместить в одну вертикально-сверлильную используя станок 2Р135Ф2 это уменьшит затраты вспомогательного времени на изготовление детали повысит точность обработки она будет произведена за 1 установ. Позволит уменьшить энергетические и материальные затраты используемого оборудования.
Используемые в базовом техпроцессе станочные приспособления являются специальным.
Режущий инструмент используемый в базовом техпроцессе является в большинстве своем из быстрорежущей стали он стандартизирован. Его можно оставить таким же за исключением применения специального инструмента используемого на следующих операциях: 060 – зенкер 105 – специальная прошивка. Это позволит уменьшить основное время обработки и повысить производительность оборудования.
Контрольный и измерительный инструмент в базовом варианте – штанген-инструмент средства активного контроля и специальные пробки подходят для использования в условиях серийного производства.
Для удобства анализа базового технологического процесса изготовления рукоятки представим его в виде таблицы 1.4.2.
5 Выбор метода получения заготовки
Метод получения заготовки ее качество и точность определяют объем механической обработки (количество рабочих ходов операций техпроцесса). Выбор метода получения заготовки зависит от типа производства массы заготовки ее конфигурации размеров.
В базовом варианте технологического процесса обработки ротора применяется в качестве заготовки стальной стержень круглого сечения полученный процессом проката (пруток из сортового проката нормальной точности).
При этом способе заготовка ротора имеет массу 0187 кг когда сама деталь обладает массой 0045 кг. В данном случае КИМ составляет 24%.
Выбор заготовки – это выбор наиболее рациональной экономичной и технологичной заготовки. С целью получения наиболее точной и качественной заготовки предлагаем заготовку-поковку получаемую на КГШП более приближённую по форме и размерам.
Так как заготовка не похожа по форме и размерам на деталь то изготовление детали будет сопряжено со снятием большого количества металла с заготовки для придания ей необходимой формы и размеров что свидетельствует о немалой трудоемкости механической обработки. Метод получения заготовки ее качество и точность определяет объем механической обработки который в свою очередь устанавливает количество рабочих ходов (операций) технологического процесса.
Использование проката вынуждает снимать дополнительные припуски что приводит к увеличению механической обработки увеличению технологического времени износу инструмента. Поэтому необходимо сравнить два метода получения заготовки: сортовой прокат и поковку на КГШП.
В качестве заготовки принимаем поковку в открытых штампах.
Назначим припуски на обработку ротора по ГОСТ 7505-89 [2].
Штамповочное оборудование – КГШП.
Класс точности принимаем Т4 (т.к. основное деформирующее оборудование: кривошипный горячештамповочный пресс технологический процесс: открытая штамповка)
Группа стали М2 (т.к. сталь поковки с массовой долей углерода свыше 035 до 065 00)
Степень сложности С2 (т.к. отношение массы поковки к массе геометрической фигуры в которую вписывается форма поковки от 032 до 063)
Ориентировочная величина расчетной массы поковки определяется по формуле:
где Мп.р – расчетная масса поковки кг;
Мп.р – масса детали кг;
Кр – расчетный коэффициент принимаем 15(приложение 3 [2]).
Мп.р = 004515=00675 кг
Конфигурация поверхности разъема – плоская.
Принимаем исходный индекс 9.
Припуски на механическую обработку:
основные припуски на размеры в мм:
– ширина и высота 10
Минимальная величина радиусов закруглений наружных углов поковки 10 мм.
длина 25+132 = 276 мм;
ширина и высота 10+13·2=126 мм;
ширина 9+132 =116 мм;
диаметр 30+132 =326 мм
Допускаемые отклонения размеров:
ширина и высота 126-04+08
Допуск радиусов закруглений внутренних и наружных углов 1 мм.
Остаточный облой 07 мм.
Допускаемые отклонения штампованных уклонов ±025 их номинальной величины.
Штампованные уклоны:
на наружной поверхности 7°
Экономическое обоснование выбора заготовки
Определим стоимость поковки по формуле:
Sотх – базовая стоимость одной тонны отходов руб.; Sотх=28 руб т
кт – коэффициент зависящий от класса точности;
кс – коэффициент зависящий от группы сложности;
кв – коэффициент зависящий от массы;
км – коэффициент зависящий от марки материала;
кп – коэффициент зависящий от объема производства.
Q-масса заготовки кг;
кт =09; кс = 077; кв = 129; км = 118; кп =1
где - плотность материала заготовки =7800 кгм3;
v - объём заготовки м3.
Q=7800·00000011630=0090 кг;
Определим стоимость заготовки из проката .
Пруток из сортового проката нормальной точности на завод поступает длиной 1 м диаметром 35 мм.
Количество заготовок из данной длины проката можно получить 37 штук (1000-(25·37)=75 мм). Так же нужно учесть длину которая будет использоваться при резке проката на заготовки пилой ленточной 2 мм (т.к. количество заготовок 37 штук (37·2=74 мм)). Очевидно что оставшейся длины проката 75 мм хватит на данные операции.
Масса одной заготовки:
отходов приходящиеся на одну заготовку:
Общая масса заготовки и отходов:
М=Мзаг.+Мотх.=0187+00015=0188 кг.
Найдём стоимость одной заготовки:
Определим КИМ для обеих методов получения заготовки:
Т.к. для прутка из сортового проката нормальной точности коэффициент использования металла меньше в 2 раза коэффициента использования металла при втором способе получения то принимаем заготовку изготавливаемую на КГШП в открытом штампе.
Назначим припуски на обработку рукоятки по ГОСТ 7505-89 [2].
Штамповочное оборудование – штамповка на молотах.
Степень сложности С2 (т.к. отношение массы поковки к массе геометрической фигуры в которую вписывается форма поковки от 016 до 032)
Кр – расчетный коэффициент принимаем 13(приложение 3 [1]).
Мп.р = 012513=01625 кг
Минимальная величина радиусов закруглений наружных углов поковки 06 мм.
длина 180+13 = 1813 мм;
высота 13 +13·2=156 мм;
диаметр 253-132 =227 мм;
диаметр 32+132 =346 мм
Q=7800·0000020512=016 кг;
7 Выбор методов обработки
При назначении метода обработки следует стремиться к тому чтобы одним и тем же методом обрабатывать возможно большее количество поверхностей заготовки что дает возможность разработать операции с максимальным совмещением обработки отдельных поверхностей сократить общее количество операций длительность цикла обработки повысить производительность и точность обработки заготовки.
При выборе метода обработки необходимо пользоваться приведенными справочными таблицами экономической точности обработки в которых содержаться сведения о технологических возможностях различных методов обработки. Назначаем метод обработки поверхностей ротора и рукоятки и заносим их в табл. 1.7.1 и 1.7.2 соответственно.
Таблица 1.7.1 - Выбор методов обработки ротора.
Заготовка 16 квалитет
Шлифование черновое 14 квалитет
Наружная цилиндрическая
Точение черновое 13 квалитет
Точение чистовое 11 квалитет
Внутренняя цилиндрическая
Сверление черновое 13 квалитет
Точение черновое 14 квалитет
Сверление черновое 14 квалитет
Однократное фрезерование
Проверим число переходов которые обеспечат заданную точность размеров формы и взаимного расположения поверхностей по величине требуемого уточнения.
Требуемая величина уточнения для определенной поверхности находится по формуле:
где Ку—требуемая величина уточнения;
dзаг—допуск размера формы или расположения поверхностей заготовки;
dдет—допуск размера формы или расположения поверхностей детали.
Затем определяется расчетная величина уточнения по выбранному маршруту обработки поверхности:
где Ку.расч.—расчетная величина уточнения;
К1 К2 Кn—величины уточнения по каждому переходу или операции при обработке рассматриваемой поверхности.
где d1—величина максимальной погрешности размера формы или расположения поверхностей которая имеет место на первом переходе (операции) при обработке рассматриваемой поверхности.
где d2—величина максимальной погрешности размера формы или расположения поверхностей которая имеет место на втором переходе (операции) при обработке рассматриваемой поверхности.
где dn—величина максимальной погрешности размера формы или расположения поверхностей которая имеет место на n—переходе (операции) при обработке рассматриваемой поверхности.
После выбора методов обработки поверхностей детали проверим правильность выбора методов для 2-х поверхностей путём расчёта заданного и расчетного уточнений.
Для поверхности 253-013 ротора.
Заготовка— поковка КГШП соответствует 16 квалитету d=13 мм.
точение черновое 13 квалитет d=033м.
точение чистовое 11 квалитет d=013м.
Расчетное уточнение на первом переходе:
Расчетное уточнение на втором переходе:
Общая расчетная величина уточнения:
Так как Ку=Кур (10=10) то назначенный маршрут обработки поверхности 253-013 обеспечит заданную точность.
На основании выборочных способов обработки разработаем технологический маршрут для детали ротор.
По предварительному маршруту обработки произведем выбор оборудования и составим маршрут обработки.
5 Вертикально-фрезерная с ЧПУ
5 Вертикально-сверлильная с ЧПУ
Таблица 1.7.2 - Выбор методов обработки рукоятки.
Высота головки 13-02
Шлифование 12 квалитет
Зенкерование 13 квалитет
Растачивание 12 квалитет
Для поверхности внутренней цилиндрической 253+01.
Сверление черновое 14 квалитет d=052 мм.
Сверление чистовое 12 квалитет d=021 мм.
Так как КуКур (62606) то назначенный маршрут обработки внутренней цилиндрической 253+01 обеспечит заданную точность.
На основании выборочных способов обработки разработаем технологический маршрут для детали рукоятка.
0 Вертикально-сверлильная с ЧПУ
0 Плоскошлифовальная
0 Вертикально-протяжная
После выбора технологического маршрута обработки и выбора оборудования заполняем маршрутные карты технологического процесса по ГОСТ 3.11.03-82.
8 Выбор технологических баз
Выбор баз для механической обработки производится с учетом достижения требуемой точности взаимного расположения поверхностей детали по линейным и угловым размерам обеспечения доступа инструментов к обрабатываемым поверхностям обеспечения простоты и унификации станочных приспособлений а так же удобства установки в них заготовки.
В процессе обработки ротора предлагаю использовать следующие схемы базирования.
Чистовыми базами на дальнейших операциях механической обработки ротора будут являться поверхность 30 и поверхности квадратного хвостовика. Установка детали на токарных фрезерных и сверлильных станках позволяет обеспечить доступ к большинству обрабатываемых поверхностей ротора.
Для сверления и нарезания резьбы в качестве баз используем квадратный хвостовик с установкой в оправку.
Рисунок 1.8.1 – Схема базирования при нарезании внутренней цилиндрической резьбы
Для точения уступа ротор закрепляется на спутнике за хвостовик.
Рисунок 1.8.2 – Схема базирования при точении уступа
При фрезеровании уступа ротор в качестве баз используем квадратный хвостовик с установкой в оправку.
Рисунок 1.8.3 – Схема базирования при фрезеровании уступа
Для сверления отверстия 51 в качестве чистовой базы используется 30. Ротор устанавливается в патрон.
Рисунок 1.8.4 – Схема базирования при сверлении отверстия
Для точения наружной цилиндрической поверхности ротор закрепляется в патрон.
Рисунок 1.8.5 – Схема базирования при точении наружной цилиндрической поверхности
При точении ротора по контуру и подрезке торца со стороны хвостовика деталь устанавливается в патрон.
Рисунок 1.8.6 – Схема базирования при контурном точении наружной поверхности и подрезке торца
При фрезеровании хвостовика деталь устанавливается в патрон
Рисунок 1.8.7 – Схема базирования при фрезеровании квадратной поверхности
Рисунок 1.8.8 – Схема базирования при точении наружной цилиндрической поверхности
В процессе обработки рукоятки предлагаю использовать следующие схемы базирования.
Для протягивания внутреннего цилиндрического отверстия рукоятка устанавливается в патрон быстросменный.
Рисунок 1.8.9 – Схема базирования при протягивании внутреннего цилиндрического отверстия
Устанавливается деталь на магнитной плите при шлифовании торцов.
Рисунок 1.8.9 – Схема базирования при шлифовании торцов
При подрезке торцов растачивании и снятии фаски на внутреннем цилиндрическом отверстии рукоятка устанавливается в патрон.
Рисунок 1.8.10 – Схема базирования при сверлении внутреннего цилиндрического отверстия
При зенкеровании внутреннего цилиндрического отверстия рукоятка устанавливается в патрон.
Рисунок 1.8.11 – Схема базирования при зенкеровании внутреннего цилиндрического отверстия
9 Разработка технологического маршрута обработки
На данном этапе разрабатывается общий план обработки детали определяется содержание операций техпроцесса. При этом заполняются маршрутные карты техпроцесса (приложение).
При составлении маршрута обработки воспользуемся базовым технологическим процессом а также следует учитывать следующие положения:
-каждая последующая операция должна уменьшить погрешность и улучшить качество поверхности;
-в первую очередь следует обрабатывать те поверхности которые будут служить технологическими базами для следующих операций.
Предварительная разработка и выбор варианта технологического маршрута ротора
Операция 005 Транспортная
Доставить заготовки на участок обработки
Операция 010 Токарная с ЧПУ
Станок: токарный с ЧПУ 16А20ФЗС15
Точить наружную цилиндрическую поверхность 30 мм
Операция 015 Вертикально-фрезерная с ЧПУ
Станок: вертикально-фрезерный 6Т13Ф20
Фрезеровать квадратный хвостовик
Операция 020 Токарная с ЧПУ
Точить по контуру со стороны хвостовика
Операция 025 Вертикально-сверлильная с ЧПУ
Станок: вертикально-сверлильный 2Р135Ф2
Сверлить внутреннее глухое отверстие 51мм
Операция 030 Токарная с ЧПУ
Подрезать торец в размер 25-05 и точить 253 мм
Операция 035 Вертикально-фрезерная с ЧПУ
Операция 040 Токарная с ЧПУ
Операция 045 Сверлильная
Станок: сверлильный 2Н135
Сверлить внутреннее отверстие и нарезать резьбу М6-7Н
Операция 050 Слесарная
Калибрование резьбы. Опиливание острых кромок.
Операция 055 Моечная
Операция 060 Контрольная
Операция 065 Транспортная
Транспортировать деталь на участок сборки
Предварительная разработка и выбор варианта технологического маршрута рукоятки
Операция 005 Транспортная.
Доставить заготовки на участок обработки
Операция 010 Вертикально-сверлильная с ЧПУ
Зенкеровать отверстие 23+04 мм
Операция 015 Токарная с ЧПУ
Станок: токарный 16А20ФЗС15
Подрезать торец расточить отверстие 25 и снять фаску
Операция 020 Плоскошлифовальная
Шлифовать торцы в размер 13-02
Операция 025 Полировальная
Полировать ручку по контуру
Операция 030 Вертикально-протяжная
Протянуть зубья по внутреннему отверстию
Операция 035 Моечная
Операция 040 Контрольная
Операция 045 Транспортная
10 Разработка технологических операций
На этом этапе окончательно определяется состав и порядок выполнения переходов в пределах каждой технологической операции производится выбор моделей оборудования станочных приспособлений режущих и измерительных инструментов.
Разработка технологических операций для детали ротор
Доставить заготовки на участок обработки.
Трактор-погрузчик Q=20кН. Тара Р1448 2ЯН1286 Q=2тс
Приспособление: четырехкулачковый патрон
Режущий инструмент: Резец проходной 2102-1371 ГОСТ 24996-81
Измерительный инструмент: штангенциркуль ШЦ-1-125-005 ГОСТ 166-89
Фрезеровать квадратный хвостовик в размер 10-0565-0475 и 127-03
Приспособление: фрезерное 7220-6095
Режущий инструмент: фреза 2223-0116 ГОСТ 166-89
Точить по контуру со стороны хвостовика подрезать торец и точить фаску 16x45° выдерживая длину 11-011 и фаску 06x45°.
Режущий инструмент: резец проходной 2102-1371 ГОСТ 24996-81 резец фасон.2126-4007
Приспособление: оправка 6030-4008
Режущий инструмент: сверло 2300-6175 ГОСТ 10902-77 метчик 2620-1115 ГОСТ 3266-81
Измерительный инструмент: штангенциркуль ШЦ-I-125-01 ГОСТ 166-89 пробка 8130-4159 калибр 8389-40005
Подрезать торец в размер 25-05 .
Черновое точение 253 мм.
Получистовое точение 253 мм.
Чистовое точение 253 мм.
Режущий инструмент: резец проходной 2102-1371 ГОСТ 24996-81
Фрезеровать уступ выдерживая размеры 7+01 и 176+03.
Приспособление: фрезерное 7220-6095.
Режущий инструмент: фреза 2234-0355Р9 ГОСТ 9140-78.
Измерительный инструмент: штангенциркуль Ц 111-1-125-0.05 ГОСТ 166-89
Точить уступ R50 выдерживая размеры 2 и 95-05.
Приспособление: пневмопривод спутник М305.01.001
Режущий инструмент: резец 01214-080404 ГОСТ 19048-80
Измерительный инструмент: штангенциркуль ШЦ-I-125-01 ГОСТ 166-89 шаблон 1176.000
Режущий инструмент: сверло 2300-6175 ГОСТ 10902-77 метчик №1 2620-1115 ГОСТ 3266-81
Разработка технологических операций для детали рукоятка
Зенкеровать отверстие 23+04 мм
Приспособление: подставка 7347-4275 патрон 109-В16 ГОСТ 15935-79
Режущий инструмент: зенкер 2330-4015
Измерительный инструмент: пробка 8154-4088 пробка 8154-4087
Подрезать торец в размер 13 расточить отверстие 25 и снять фаску 06x45°
Приспособление: патрон трёхкулачковый с пневмозажимом
Режущий инструмент: резец подрезной 2112-0007 ГОСТ 18880-73 резец проходной 2102-4003
Измерительный инструмент: пробка 8130-4187
Шлифовать торцы головки в размер 13-02
Приспособление: плита магнитная 7208-83
Режущий инструмент: круг шлиф.1450x63x203 24А40СМ 1К ГОСТ 2424-83
Измерительный инструмент: скоба 8150-4217
Полировать торец ручки соблюдая плавность перехода с полированной поверхностью
Режущий инструмент: круг войлочный Пг400x40x45 ГОСТ 10684
Приспособление: патрон быстросменный 6153-4023 приспособление 7632-4025
Режущий инструмент: прошивка 7632-40254-61
Измерительный инструмент: пробка 8130-4385
11 Разработка технологии сборки
11 Аналитический расчет припусков на обработку
Произведём расчёт припусков расчётно-аналитическим методом на две различные поверхности а так же построим для них схемы расположения припусков и допусков.
Рассчитаем припуски и предельные размеры по переходам на обработку наружной цилиндрической поверхности ротора 253-013.
Исходные данные: Заготовка – поковка. Класс точности Т4. Группа стали М2. Степень точности С2. Исходный индекс 9 ГОСТ 7505-89.заготовки 009 кг. Обработка детали ведется в патроне. Параметры поковки: 16 кв Rz=80 мкм h=150 мкм (т.27[2]).
Составим технологический маршрут получения поверхности 25-013 с указанием Rz и h по переходам(т.29[2]):
-й переход – точение черновое 14 квалитет Rz=50 мкм h=50 мкм;
-й переход – точение получистовое 12 квалитет Rz=30 мкм h=30мкм;
-й переход – точение чистовое 11 квалитет Rz=25 мкм h=25 мкм.
Пространственное отклонение формы поверхности заготовки рассчитаем по формуле:
где ρсм –смещение полуматриц друг относительно друга штампуемой части заготовки относительно стержня исходного материала ρсм=03 мм (т.34[2]);
ρкор –коробление(кривизна) заготовки.
где Δк – удельная кривизна заготовки Δк=6 мкммм (т.32[2]);
l – длина поверхности l=L2=252=125 мм.
Следовательно имеем : ρкор = 6 · 125 = 75 мкм.
Остаточное пространственное отклонение по переходам определяем по формуле:
ρост = ρ·Ку (1.11.3)
где Ку – коэффициент уточнения формы.
-й переход – ρ1 =006·ρ=006·309=1854 мкм;
-й переход – ρ2 =004·ρ=005·1854=0927 мкм;
-й переход – ρ3=002·ρ=004·0927=004 мкм.
Погрешность установки детали на всех операциях у равна нулю (базирование в патроне).
Расчёт минимальных значений межоперационных припусков производим по формуле:
где i – выполняемый переход.
Тогда минимальный припуск по переходам будет следующим:
Расчётные размеры рассчитываем начиная с конечного максимального чертёжного размера последовательным вычитанием 2Zmini каждого технологического перехода:
-й переход DP3 =2517 мм;
-й переход DP2 =2517 +0122=25292 мм;
-й переход DP1 = 25292 +0237=25529 мм;
Заготовка Dр.загот =25529 +1078=26607 мм.
Назначаем допуски на технические переходы по таблице а допуски на заготовку по ГОСТ 7505 – 85.
Заготовка - 1300 мкм;
-й переход – 520 мкм;
-й переход – 210 мкм;
-й переход – 130 мкм;
Предельный размер Dmin определяем округляя Dp до большего значения в пределах допуска на данном переходе а Dmax определяем прибавлением к Dmin допусков соответствующих переходов:
-й переход: D3 m D3 ma
-й переход: D2 m D2 ma
-й переход: D1 m D1 ma
заготовка Dзаг.min=265мм Dзаг.max=265+13=278 мм.
Максимальное предельное значение припусков 2×Zmax.ПР находим как разность наибольших предельных размеров выполняемого и предшествующего переходов а минимальные значения 2×Zmin.ПР – как разность наименьших предельных размеров выполняемого и предшествующих переходов.
Z1 minПР = 265-257=08 мм.
Общий минимальный припуск находим как сумму минимальных промежуточных припусков а общий максимальный – как сумму максимальных припусков:
Z0min=08+03+023=17 мм.
Общий номинальный припуск 2Z0ном вычисляем по формуле:
Z0ном=Z0min+Нз-Нд (1.11.5)
где Нз и Нд – соответственно нижнее отклонение допуска заготовки и детали.
Z0ном=17+05-013=233мм.
Следовательно номинальный диаметр поверхности заготовки будет равен:
DЗном=DДном+2Z0ном=253+233=2763 мм.
Производим проверку правильности расчётов по формулам:
Zmaxi-2Zmini=Di-1- Di (1.11.6)
Z0max-2Z0min=DЗ- DД (1.11.7)
Для нашего случая имеем:
-й переход 210-130=310-230; т.е. 80=80;
-й переход 520-210=610-300; т.е. 310=310;
-й переход 1300-520=1580-800; т.е. 780=780;
общий припуск 2800-1630=1300-130; т.е1170=1170.
Расчёт произведён правильно.
Все расчёты параметров припусков приведём в таблицу 1.11.1.
Таблица 1.11.1 – Результаты расчёта припусков на поверхность ротора 253-013.
Технологи-ческие переходы обработки поверхности 45js7
Элементы припуска мкм
Расчётный припуск 2Zmin мкм
Расчётный размер Dр мм
Допуск на размер D мкм
Предельный размер мм
Предельные значения припусков мм
На основании таблицы строим схему графического расположения припусков и допусков на обработку поверхности ротора 253-013.
Рисунок 1.11.1 — Схема графического расположения припусков и допусков на обработку поверхности диаметром 253-013
Выберем технологический маршрут обработки отверстия 253+01 и определим величины Rz и h по переходам:
Заготовка 16 квалитета: Rz = 80 h = 150
-й переход: зенкерование 13 кв. Rz = 40 h = 40
-й переход: растачивание 12 кв. Rz = 32 h = 30
Определим значения пространственных отклонений для заготовки.
где rсм – смещение оси головки относительно общей оси; rсм = 0
rкор – коробление вала;
где К – удельная кривизна заготовки К =8;
l – длина заготовки.
rзаг=rкор = 13×8 = 104 мкм
Остаточное пространственное отклонение по формуле:
где КУ – коэффициент уточнения формы.
Погрешность установки детали на выполняемом переходе eу определяем по формуле:
где eb – погрешность базирования eb = 0;
eз – погрешность закрепления eз = 80.
-й переход r1 = 005×104 = 52 мкм; e1 = 80×005 = 4 мкм
-й переход r2 = 004×52 = 0208 мкм; e2 = 4×004 = 016 мкм
Расчёт минимальных межоперационных припусков:
Расчётный размер диаметра отверстия DР вычислим начиная с конечного максимального чертёжного размера путём последовательного вычитания минимального припуска каждого предыдущего перехода:
-й переход: DР растч.. =254-2×0045 = 2531 мм
-й переход: DР зенк. = 2531-2×0334 = 24642 мм
Назначаем допуски на технологические переходы:
Заготовка – 1300 мкм
-й переход – 330 мкм
-й переход – 210 мкм
Предельный размер Dmax определяем округляя Dp до меньшего значения в пределах допуска на данном переходе а Dmin определяем вычитая из Dmax допуски соответствующих переходов:
-й переход: Dma Dmin растч..= 254-021=2519 мм
-й переход: Dma Dmin зенк. = 2531-033 = 2498 мм
заготовка: Dmax заг. = 24642 мм Dmin заг. = 24642-13 = 23342 мм
Минимальные предельное значение припусков 2×Zmin.ПР. находим как разность наибольших предельных размеров выполняемого и предшествующего переходов а максимальные значения 2×ZmaxПР – как разность наименьших предельных размеров выполняемого и предшествующих переходов.
Общий минимальный припуск находим как сумму минимальных промежуточных припусков а общий максимальный – как сумму максимальных припускав:
Общий номинальный припуск находим по формуле:
где ВЗ – верхнее отклонение заготовки по ГОСТ 2590 – 71
ВД – верхнее отклонение детали по чертежу.
Тогда номинальный диаметр заготовки:
Проверяем правильность произведённых расчётов:
-й переход: 021-009 =033-021 мм 012=012 мм
-й переход: 1638-0668 = 13-033 мм 097=097 мм
Общий припуск: 1848-0758 = 13-021 мм 109=109 мм
Проверка правильна значит расчёты межоперационных припусков произведены верно. Все расчёты параметров припусков приведём в таблицу 1.11.2.
Таблица 1.11.2 Результаты расчёта припусков на поверхность рукоятки 253+01
переходы обработки поверхности
Расчётный припуск 2×Zmin мкм
Расчётный размер Dp мкм
Допуски размеров мкм
Предельные размеры припусков мкм
На основании таблицы строим схему графического расположения припусков и допусков на обработку поверхности рукоятки 25+01.
Рисунок 1.11.2 — Схема графического расположения припусков и допусков на обработку отверстия 25+01
12 Расчет режимов резания
Произведем расчет режимов резания для двух разных типов операций. Одной – чернового точения поверхности ротора 253-013 на операции « 030 Токарная с ЧПУ». Другой – протягивания отверстия рукоятки 253+01 на операции « 030 Токарная с ЧПУ».
Расчет проведем по эмпирическим формулам по методике [3].
Произведём расчёт режимов резания обработки размера 253+01 протяжкой.
Глубина резания – t =5 мм;
Скорость резанья при протягивании определяемую требованиями к точности обработки и параметрам шероховатости обработанной поверхности выбирают в зависимости от группы скорости устанавливаемой по методике [3]. При нормативной скорости резания заданный параметр шероховатости поверхности может быть достигнут при оптимальных значениях переднего и заднего углов.
Согласно методике [3] выбираем группу скорости 3. Следовательно получаем нормативную скорость резания:
Сравним нормативную скорость резания с максимальной скоростью рабочего хода станка.
где N - мощность двигателя станка кВт; N= 10 кВт
Pz – сила резания при протягивании; Pz=0.8105 H
где KМV – коэффициент учитывающий качество обрабатываемого материала;
KПV – коэффициент учитывающий состояние поверхности заготовки;
KИV – коэффициент учитывающий материал инструмента.
где sB – физический параметр характеризующий обрабатываемый материал;
КГ и nv – коэффициент и показатель степени характеризующие группу стали по обрабатываемости.
KИV = 115; KПV = 08;
Определяем окружную скорость вращения заготовки:
Силы резания при точении Н:
где Ср – поправочный коэффициент Ср =300;
х у n – показатели степеней х=1 у=075 n = -015;
Кр – поправочный коэффициент.
где - коэффициенты учитывающие фактические условия резания
Кφp=108 Кλp=1 Кp=087.
Определяем Кмр по формуле:
где n0 - показатель степени nv = 09.
Определим частоту вращения по формуле:
где n - частота вращения шпинделя мин-1;
Частота вращения заготовки:
Принимаем n = 1350 oб мин.
Определяем мощность затрачиваемую на резание по формуле:
Находим мощность резания:
Определяем основное время То:
где Sо - оборотная подача обмин ;
Таблица 1.12.1 - Сводная таблица режимов резания ротора
Наименование операции или перехода
Вертикально-фрезерная с ЧПУ
Вертикально-свер-лильная с ЧПУ
-получистовое точение
Вертикально-фрезерная с ЧПУ
Таблица 1.12.2 - Сводная таблица режимов резания рукоятки
Вертикально-сверлильная с ЧПУ
- расточить отверстие
Плоскошлифо-вальная
13 Определение норм времени на операции
При серийном производстве норма штучного времени определяется по формуле:
где То—основное (машинное) время обработки детали мин;
Тв—вспомогательное время на операцию (время на установку и снятие детали подвод и отвод инструмента время на управление станком и т.д.) мин;
Тобс—время на техническое и организационное обслуживание рабочего места (время на замену затупившегося инструмента время на уборку рабочего места в конце работы) мин;
Тотд—время на отдых и личные надобности мин.
где Тус—время на установку и снятие детали мин;
Тзо—время на закрепление и открепление детали мин;
Туп—время на приемы управления мин;
Тиз—время на измерение детали мин.
где Ттех—время на техническое обслуживание рабочего места мин;
Торг—время на организационное обслуживание рабочего места мин.
Оперативное время Топ:
Время на организационное и техническое обслуживание определяется в процентах от оперативного времени.
Tтех + Tорг =к*Tоп100%
где П—затраты времени на отдых в процентном отношении к оперативному.
Рассчитаем норму штучного калькуляционного времени для операции 015 ротора (вертикально-фрезерной). Производство среднесерийное масса детали 045 кг.
Тус+Тзо=006+0024=0084 мин Туп=001+02=021 мин. — время на включение станка и подвод инструмента (станок включается кнопкой)
Время на измерение штангенциркулем ШЦ-I-125-005 Тиз=012 мин
Вспомогательное время:
Тв=0084+021+012=0414 мин
Топ=16+0414 =2014 мин
То=16 - основное время на обработку заготовки на данной операции
Затраты времени на обслуживание рабочего места и отдых в процентном отношении к оперативному равно 7% тогда:
Тобс=2014·7100=0145 мин
Подставляем полученные значения времен:
Тшт=16+0414+0145=215 мин
Tп.з.- подготовительно-заключительное время на партию заготовок
- время на наладку станка и установку приспособлений 14 мин
- время на установку фрез (1 шт.) 2 мин
- получить наряд чертеж технологическую документацию режущий и вспомогательный инструмент контрольно-измерительный инструмент приспособление заготовки исполнителем до начала и сдать их после окончания обработки партии деталей 13 мин
-ознакомится с работой чертежом технологической документацией осмотреть заготовки 20 мин
-инструктаж мастера 20 мин
Tп.з.=14+2+13+2+2=33 мин
Количество деталей в партии:
n=50000·6254=1181 шт.
Время приходящееся на одну заготовку из партии:
Tшт.к.=0028+215=218 мин
Рассчитаем норму штучного калькуляционного времени для операции 015 рукоятки (Токарная с ЧПУ). Производство среднесерийное масса детали 0125 кг.
- установить заданное взаимное положение детали и инструмента по координатам XYZ и при необходимости произвести подналадку 032 мин
- включить и выключить лентопротяжный механизм 004 мин
- открыть и закрыть крышку лентопротяжного механизма перемотать заправить ленту в считывающее устройство 031 мин
- проверить переход деталиинструмента в заданную точку после
- продвинуть перфоленту в исходное положение 019 мин
- установить и снять щиток от набрызгивания эмульсией 003 мин
Тус+Тзо=005+0024=0074 мин
Туп=031+004+032+015+019+003=0752 мин.
Время на измерение штангенциркулем ШЦ-I-125-005: Тиз=012 мин Вспомогательное время:
Тв=0074+0752+012=0946 мин
Топ=0946+065=1596 мин
То=065 - основное время на обработку заготовки на данной операции
Затраты времени на обслуживание рабочего места и отдых в процентном отношении к оперативному равно 6% тогда:
Тобс=1596·6100=0096 мин
Тшт=0946+065+0096=169 мин
- получить наряд чертеж технологическую документацию программоноситель режущий и вспомогательный инструмент контрольно-измерительный инструмент приспособление заготовки исполнителем до начала и сдать их после окончания обработки партии деталей 13 мин
-ознакомится с работай чертежом технологической документацией осмотреть заготовки 20 мин
-установить и снять патрон трехкулачковый 25 мин
- установить исходные режимы станка 015 мин
- установить и снять кулачки 65 мин
-расточить кулачки 62 мин
-установить и снять инструментальный блок или отдельный режущий инструмент (время на один инструмент( блок)) 02 мин
-установить программоноситель в считывающее устройство
-проверить работоспособность считывающего устройства и
-ввести программу в память системы с ЧПУ с
программоносителя 15 мин
-установить исходный координаты X и Z (настроить нулевое
Tп.з.=13+2+2+25+015+65+62+02+1+1+15+2=385 мин
Время приходящиеся на одну заготовку из партии
Tшт.к.=003+169=17 мин
Нормы времени на остальные операции назначаем по нормативным справочникам. Рассчитанные и назначенные времена сведем в таблицу.
Таблица 1.13.1 - Сводная таблица технических норм времени по операциям ротора мин.
Вертикально-сверлильная с ЧПУ
Таблица 1.13.2 - Сводная таблица технических норм времени по операциям рукоятки мин.
14. Расчет технологической размерной цепи
Рассчитаем размерную цепь образующуюся при точении наружной цилиндрической поверхности 253-013. Замыкающим звеном является размер длины 11+02 у которого измерительная и технологическая базы не совпадают.
Проведем расчет следующей размерной цепи.
Рисунок 1.14.1 – Размерная цепь
Исходные данные: A1=11+02 мм A2=25-05 мм.
Расчет размерной цепи ведем по [6] методом максимума-минимума.
Номинальный размер замыкающего звена определим по формуле:
А0 = А2-А1= 25-11=14 мм.
Допуск замыкающего звена определяем по формуле:
где: ТАi—допуски звеньев расчетной цепи мм.
ТА0 = ТА2 + ТА1 = 05 + 02= 07 мм.
Координата середины поля допуска замыкающего звена:
ЕсА0 = ЕсА2 + ЕсА1 (1.14.3)
где ЕсАi - координата середины поля допуска составляющих звеньев.
ЕсА0 = -025+01= -015
Верхнее и нижнее отклонения замыкающего звена:
ЕSА0 = ЕсА0 + (1.14.5)
ЕIА0 = ЕсА0 – TA02. (1.14.6)
ЕSА0 = -015+ 072 = 02 мм
ЕIА0= -015– 072 = -05 мм
Замыкающий размер А0= мм.
Проведем проверку правильности решения размерной цепи:
А0 = А2 - А1 = A2=25-05-11+02 =
Допуск полученный в результате проверки входит в расчетный допуск.
Значит цепь рассчитана верно.
15 Определение необходимого количества оборудования
Для серийного производства количество станков S определяется по формуле:
Тшт—штучное время обработки изделия мин;
F—действительный годовой фонд времени работы оборудования час.
Коэффициент загрузки оборудования:
где Sпр—принятое количество станков.
Объём выпуска деталей “ротор” – 50000
На основании рассчитанных коэффициентов строим график загрузки оборудования.
Рисунок 1.15.1 – График степени загружённости станков на операциях ротора:
-й столбец Токарная с ЧПУ станок модели 16А20Ф3С15
-й столбец Вертикально-фрезерная станок модели 6Т13Ф20
-й столбец Вертикально-сверлильная станок модели 2Р135Ф2
-й столбец Сверлильная станок модели 2Н135
Анализируя полученные данные необходимо отметить неудовлетворительную загрузку станков. Поэтому следует совместить токарную обработку и выполнять операции 010 020030 и 040 на одном станке. Загрузка оборудования в этом случае будет составлять около 75%. Большинство оборудования универсальное поэтому его следует догружать операциями по обработке других деталей для увеличения коэффициента загрузки оборудования.
Объём выпуска деталей “рукоятка” – 50000
Рисунок 1.15.2 – График степени загружённости станков на операциях рукоятки:
-й столбец Плоскошлифовальная станок модели 2Н118
-й столбец Вертикально-протяжная станок модели 3М6341.16 Уточнение типа производства по коэффициенту закрепления операций.
Уточненный расчет типа производства основывается на определении коэффициента закрепления операций Кзо:
где О—количество всех различных технологических операций выполненных в течении месяца;
Р—число рабочих мест необходимых для выполнения месячной программы.
Согласно ГОСТа для среднесерийного типа производства Кзо=10 20
Число рабочих мест для выполнения определенной i-ой операции определяем по формуле:
где Nм—месячный объем выпуска детали (4166 шт);
Тшт—штучное время на выполнение определенной операции мин;
Fм—месячный фонд времени работы оборудования (196 час);
Кв—коэффициент выполнения норм времени. Кв=11 13
Рассчитанное число рабочих мест округляем до ближайшего большего целого числа Рi.
Коэффициент загрузки данных рабочих мест выполняемой операцией:
Количество операций выполняемых на этом рабочем месте при его нормативной загрузке определяем по формуле:
где: hн=07 085—нормативный коэффициент загрузки для среднесерийного
Общее количество операций выполняемых на всех рабочих местах проектируемого техпроцесса и общее количество рабочих мест определяется как сумма всех операций и сумма всех рабочих мест соответственно.
Результаты расчетов сведем в таблицу.
Таблица 1.16.1 — Определение типа производства детали “ротор”.
Определяем коэффициент закрепления операций:
Коэффициент Кзо находится в промежутке от 1 до 10 причем ближе к 1.
Определим такт выпуска продукции t:
где: F—действительный годовой фонд времени работы оборудования при
-ух сменной работе (4015 час).
задание11.doc
Факультет: машиностроительный
Кафедра «Технология машиностроения»
Заведующий кафедры А.П. Акулич
на выполнение дипломного проекта
Студенке Григорович Ларисе Викторовне.
Тема проекта: Проектирование технологического процесса сборки ключа трещоточного 7813-4019.
(Утверждена приказом по ВУЗу от 28.03.2006г. № )
Сроки сдачи студентами законченного проекта 15.06.2006 г. .
Исходные данные для проекта
Чертеж детали Ротор 7813-40192-1 рукоятка 7813-40192 .
Объем выпуска 30000в год. .
Режим работы – двухсменный .
Содержание расчетно-пояснительной записки (перечень вопросов которые подлежат разработке): Введение. 1. Разработка технологического процесса изготовления детали. 1.1. Назначение и конструкция детали (сборочной единицы). 1.2. Анализ технических условий изготовления детали. 1.3. Анализ технологичности конструкции детали. 1.4 Ориентировочное определение типа производства. 1.5. Выбор метода получения заготовки. 1.6. Анализ базового технологического процесса изготовления детали. 1.7. Выбор методов обработки (для двух поверхностей: 253-013; 253+01 - рассчитать требуемую величину уточнения; для остальных – выбор сделать по справочным таблицам). 1.8. Выбор технологических баз (показать схемы базирования) 1.9. Разработка технологического маршрута обработки. 1.10. Разработка технологических операций. 1.11. Расчет припусков на обработку ( для двух поверхностей: 253-013 253+01 - припуски определить аналитическим методом; для остальных – в соответствие с п.1.5.). 1.12. Расчет режимов резания ( для двух операций или переходов: протягивание отверстия 253+01 мм; чистовое точение поверхности 253-013 – по эмпирическим формулам; для остальных операций режимы резания определяются по нормативам). 1.13. Определение норм времени ( для двух операций: токарной с ЧПУ и фрезерной – выполнить подробный расчет; нормы времени для остальных операций свести в таблицу). 1.14. Уточненный расчет типа производства ( на основе определения коэффициента закрепления операций). 1.15. Расчет технологической размерной цепи: 7-036 мм. 1.16. Определение необходимого количества оборудования и коэффициентов его загрузки. .
Расчет и проектирование средств технологического оснащения. .
1 Проектирование приспособления для точения 8-ми уступов R50мм. .
2. Проектирование приспособления для контроля отклонения от перпендикулярности. .
3. Проектирование специального режущего инструмента: протяжки для протягивания зубьев.
4. Проектирование средства автоматизации:
Технико-организационная часть. .
Технико-экономический раздел. .
Охрана труда и окружающей среды. .
Перечень графического материала (с точным указанием обязательных чертежей и графиков):
Чертеж детали – 2 листа ф-А2. 2. чертеж заготовки – 2 листа ф-А2. 3. Эскизы операционные – 2 листа ф-А1 (показать операциипереходы:
Наладка инструментальная – 1 лист ф-А2 (для операции: )
Сборочный чертеж приспособления для точения 8-и уступов – 1 лист ф-А1 .
Сборочный чертеж приспособления для контроля перпендикулярности – 1 лист ф-А1 .
Чертеж специального режущего инструмента: протяжки – 1 лист ф-А1 .
Планировка технологическая – 1 лист ф-А1. .
Приспособление для очистки протяжки – 1 лист ф-А1.
Консультанты по проекту:
Технологический и конструкторский разделы – Левданский Алексей Маратович .
Экономический раздел – старший преподаватель Мартиновский Оксана Владимировна .
Охрана труда – доцент Драган Александр Вячеславович .
Руководитель проекта - Левданский Алексей Маратович .
выдачи задания 09.03.2006г. .
Календарный график работы над проектом на весь период проектирования .
согласно графику кафедры .
Задание принял к исполнению (дата) 09. 03. 2006г. .
(подпись студента) .
Примечание: Задание прилагается к законченному проекту и вместе с проектом предоставляется при сдаче проекта в ГЭК.
ОперЭскРу1.cdw

Вертикально-фрезерная с ЧПУ
Вертикально-сверлильная
Чертеж.cdw

Лариса.spw

Болт М6x12.66.05 ГОСТ7805-70
Винт по ГОСТ 11738-84
Кольцо по ГОСТ 9833-73
Шайба по ГОСТ6401-70
Фитр влагоотделитель
приспособд.frw

ОперЭскР.cdw

Содержание1.DOC
1 Назначение и конструкция детали
2 Анализ технических условий изготовления детали . .. .
3 Анализ технологичности конструкции детали
4 Ориентировочное определение типа производства
5 Выбор метода получения заготовки ..
6 Анализ базового варианта технологического процесса ..
7 Выбор методов обработки ..
8 Выбор технологических баз
9 Разработка технологического маршрута обработки .
10 Разработка технологических операций
11 Разработка технологии сборки .
12 Расчет припусков на обработку .. ..
13 Расчет режимов резания
14 Определение норм времени ..
15 Уточненный расчет типа производства .. ..
16 Определение необходимого количества оборудования ..
17 Расчет технологической размерной цепи ..
Расчет и проектирование средств технологического оснащения ..
1 Проектирование приспособления для сверления 8-ми отверстий
1.1 Служебное назначение и описание конструкции приспособления
для точения 8-ми уступов R50
1.2 Расчет сил зажима заготовки .
1.3 Расчет приспособления на прочность ..
1.4 Расчет приспособления на точность
2 Проектирование приспособления для контроля отклонения от перпендикулярности .
3 Расчёт конструктивных элементов протяжки .
4 Проектирование приспособления для очистки протяжки.
Технико-организационная часть .
Расчет технико-экономических показателей обработки детали ..
1 Определение исходных данных для расчета технико-экономических показателей обработки детали ..
2 Определение потребности в материально-технических и трудовых ресурсах
ДП 03.01.753.00.00.000 ПЗ
№ докум. оцонооокуруеркоомрсггааангагндаподокумента
Датаааааааааааааааааааа
Разработка технологии сборки ключа трещеточного
Спец контр.DOC
Болт по ГОСТ 7798-70
Индикатор ИЧ 10 кл. 1
Приспособление для контроля перпендикулярности
Спецификация оборудования 111.cdw

Вертикальносверлильный
Вертикальнофрезерный
оборудования по плану ДП 03.01.723.03.00.000
Держатель подлинника
Протяжка.cdw

Материал : рабочей части -сталь Р6М5 (ГОСТ 19265-85)
вой части-сталь Р6М5 (ГОСТ 19265-85).
Размеры центровочных отверстий по ГОСТ 14034-74
Твердость режущей части и задней направляющей HRC 61 66
Неуказанные предельные отклонения размеров h14
Остальные технические требования по ГОСТ 9126-76
Маркировать :обозначение протяжки
материал режущей части
товарный знак завода-изготовителя.
Профиль протягиваемого
ДП 03.01.753.30.00.000
Сталь Р6М5 ГОСТ 19265-73
Профиль режущих зубьев (10:1)
Предельное отклонение
Припуски, допуски.frw

точения чернового 25.7
точения чернового 0.52 мм
точения получистового 25.61 мм
точения получистового 25.4 мм
точения получистового 0.21 мм
точения чистового 25.3 мм
точения чистового 25.17 мм
точения чистового 0.13 мм
Zmin при точении получистовом 0.3 мм
Zmax при точении получистовом 0.61 мм
Zmin при точении черновом 0.8 мм
Zmax при точении черновом 1.58 мм
Zmax при точении чистовом 0.31 мм
Zmin при точении чистовом 0.23 мм
ГОСТ Форма.doc
Министерство образования Республики Беларусь
Учреждение образования
Брестский Государственный технический университет
на технологический процесс изготовления
ключа трещоточного 7813-4019
Руководитель: Левданский А.М.
Н. контроль: Левданский А.М.
литература.doc
А.Ф. Горбацевич В.А. Шкред. Курсовое проектирование по ТМ. Минск «Высшая школа» 1989г.
Справочник технолога-машиностроителя в двух томах. Под ред. А.Г. Косиловой. М.; Машиностроение 1983г.
Методические указания к выполнению лабораторных работ по дисциплине «Современные технологии». Машинский В. В. Акулич Л. И. Брест 1997г.
Маталин А.А. Технология машиностроения. М.; Машиностроение 1993г.
Балакшин Б.С. Основы технологии машиностроения. М.; Машиностроение 1986г.
Егоров М.Е. Дементьев В.И. Технология машиностроения. М.; Высшая школа 1986г.
Косилова А.Г. Мещеряков Р.К.; Точность обработки заготовки и припуски машиностроения. Справочник технолога. М.; Машиностроение 1986г.
Общемашиностроительные нормативы режимов резания для технологического нормирования работ на металлорежущих станках. М.; Машиностроение 1984г.4-1 – 416 с. 4-2 – 200 с.
Основы технологии машиностроения. Под ред. В.С. Корсакова. М.; Машиностроение 1987г.
Шатин В.П. Денисов П.С. Режущий и вспомогательный инструмент. М.; Машиностроение 1988г.
Гавриш А.Г. Ефремов А.И. Автоматизация технологической подготовки машиностроительного производства. Киев Техника 1992г.
Зазерский Е.И. Технология обработки деталей на станках с программным управлением. Л.; Машиностроение 1985г.
Справочник по расчету теплоснабжения и вентиляции. Под ред. Р. В. Щекин Киев Будевельник 1986г.
Общемашиностроительные укрупнённые нормативы времени на работе выполняемые на металлорежущих станках. Ч. 1 2. М.; Экономика 1988г.
Кузнецов Ю.И. Маслов А.Р. Оснастка для станков с ЧПУ. Справочник. М.; Машиностроение 1989г.
Микитянский В.В. Точность приспособлений в машиностроении. М.; Машиностроение 1984г.
Антонюк В.Е. Конструктору станочных приспособлений. Минск «Беларусь».; 1991г.
Горошкин А.К. Приспособление для металлорежущих станков. М.; 1979г.
Кузнецов В.С. Универсально-сборочное приспособление в машиностроении. М.; 1991г.
Алексеев Г.А. Кричёвская А.М. Конструирование инструментов. М.; 1979г.
Рбаза.frw

анализ ТП.doc
Наименование и состав операции
Измерительный инструмент
Уложить 15 прутков калибровки в призмы тисков установить размер 25 по упору станка.
Зажать заготовки гидротисками.
Пила лент. БМ 32x11x63 ТУ2 0350224638 1182-89
Уложить заготовку на магнитную плиту
Шлифовать заготовки в размер 25-05
Плита магнитная 7208-83
Круг шлиф.1450x63x203 24А40СМ 1К ГОСТ2424-83
Токарно- револьверная
Торцевать деталь в размер 11+02+05
Центровать отверстие
Проточить в размер 253 на длину 9+02
Цанга зажимная 7010-40402-02
Снять фаску со стороны квадрата 16x45° выдерживая размер 11-05
Цанга зажимная 7010-407
Штангенциркуль ШЦ-I-125-01 ГОСТ 166-89
Вертикально-сверлильная
Сверлить отверстие 51+018 на глубину h=8-05
Патрон 6-В12 гост 8522-79
Горизонтально-фрезерная
Фрезеровать уступ выдерживая размеры 7+03 и 176+03
Образцы шерох. №1 ГОСТ 9378-75
Отпилить заусенцы после фрезерования
Проточить уступ шириной 3-05 по радиусу R50 выдержав размер 95-05
Нарезать резьбу М6-Н7 на длине 7+01 №1
Переустановить метчик
Нарезать резьбу М6-Н7 на длине 7+01 №2
Очистить резьбу от окалины
Таблица 1.4.2 - Анализ базового техпроцесса рукоятки
Зенкеровать отверстие в размер 23+04
Подставка 7347-4275 патрон 109-В16 ГОСТ 15935-79
Полировать головку по контуру
2. Полировать ручку по контуру
Лента б.а. С14А25Н CФЖ Гост 13344-70
Расточить отверстие в размер 25+013 мм
Патрон трёхкулачковый с пневмозажимом
Резец проходной 2102-4003 резец подрезной 2112-0007 ГОСТ 18880-73
Шлифовать головку в размер 13-02
Притупить острые кромки
Полировать торец ручки соблюдая плавность перехода с полированной поверхностью
Круг войлочный Пг400x40x45 ГОСТ 10684
Вертикально-протяжная
Протянуть зубья по внутреннему отверстию
Патрон быстросменный 6153-4023 приспосбление 7632-4025
Прошивка 7632-40254-61
уступ.doc
1 Назначение и конструкция сборочной единицы
Заданные детали (ротор и рукоятка) входят в состав ключа трещоточного.
Ротор предназначен для базирования на нём составных сборочных ключа трещоточного. Ротор не является симметричным имеются два глухих отверстия причем одно из них перпендикулярно оси ротора.
Рисунок 1.1 – Эскиз ротора
Рукоятка предназначена для удобного использования ключа трещоточного и для базирования ротора на нём. Конструкция рукоятки проста и удобна. Есть сквозное отверстие которое получается штамповкой.
Рисунок 1.2 – Эскиз рукоятки
Ключ трещоточный состоит из: 1 – крышки 2 - ротора 3 - сектора 4 – пружины 5 – рукоятки 6 – гранулы полиэтилена 7 - винта.
Рисунок 1.3 – Эскиз ключа трещоточного
Установить ротор на подставку с неподвижной головкой. Надеть ручку на ротор. Взять пружину и сектор и вставить пружину двумя концами в отверстие сектора. Вставить в паз ротора сектор с пружиной. Наложить крышку вставив штифт в перегиб пружины. Завернуть винт до упора затем отвернуть его на 12 34 оборота. Переключить крышку 2-3 раза удостоверившись в работе сектора. Проверить работоспособность ключа. Для этого установить ключ квадратом ротора в неподвижную головку квадрата 10 и ключ в обе стороны (в одну сторону ключ работает на Мкр в другую слышен характерный треск сектора по зубьям рукоятки).
К детали предъявляются высокие требования по точности жёсткости а к материалу по прочности износостойкости.
Для повышения физических свойств поверхностного слоя деталь подвергают термообработке - ТВЧ.
Материал детали – конструкционная легированная сталь 40Х (ГОСТ 4543-71) широко используется для изготовления различных видов и типоразмеров валов осей шестерен и т.п. работающих в условиях требующих повышенной прочности и износостойкости.
Таблица 1.1 - Химический состав стали 40Х (ГОСТ 4543-71) .
Таблица 1.2 - Механические свойства стали 40Х (ГОСТ 4543-71) .
Предел прочнос-ти в МПа
Предел текучес-ти т МПа
Относи-тельное удлинение %
Относи-тельное сужение %
Рассмотрим основные поверхности ротора исходя из ее служебного назначения.
Рисунок 1.4 – Поверхности ротора
Основные конструкторские базовые поверхности применяемые для базирования детали в механизме.
Основными базовыми поверхностями являются: торцы буртов 4 5.
Вспомогательные конструкторские базовые поверхности применяемые для базирования других деталей в механизме.
Такими поверхностями будут являться: резьбовое отверстие 17 боковая поверхность отверстия 11 16 цилиндрическая поверхность 3.
Исполнительные поверхности посредством которых деталь выполняет свои функции в механизме: цилиндрические поверхности 10.
Свободные поверхности предназначены для ограничения размера детали и не имеют функционального назначения их размер и форма выбирается произвольно. Такими поверхностями являются 1 2 6 7 8 9 12 13 14 15.
Рисунок 1.5 – Поверхности рукоятки
Основных базовых поверхностей нет.
Вспомогательные конструкторские базовые поверхности: 2 3 4 5.
Исполнительные поверхности: 4 6 8.
Свободные поверхности: 1 7 9 10.
2 Анализ технических условий изготовления детали
Проведём анализ технологичности конструкции деталей (ротора и рукоятки).
При получении заготовок отсутствуют сложные разъемы отрезных штампов.
Основные поверхности являются удобными для базирования и закрепления поэтому дополнительные поверхности не вводятся.
Материал детали сталь Ст40Х механическая обработка которого не вызывает сложностей при обработке твердым сплавом.
Доступность поверхностей деталей для обработки и измерения.
В конструкции ротора присутствуют места резких изменений формы концентраторы напряжений а в рукоятке нет.
Для получения требуемой точности размеров и шероховатости деталей можно применять станки нормального класса точности.
Ротор и рукоятка – жесткие изделия.
Наличие глухих отверстий в роторе одно из которых перпендикулярно к оси детали.
Учитывая все вышеперечисленные факторы у данных деталей удовлетворительная технологичность.
3 Ориентировочное определение типа производства
Предварительно тип производства определяем по таблице 3 с.8 [2]. С учетом массы деталей (0045 и 0125 кг) и годовой программы 30 000принимаем среднесерийный тип производства. Среднесерийное производство характеризуется большой номенклатурой изделий изготовляющихся не большими партиями и не большим объемом выпуска. При среднесерийном производстве используются как универсальные так и станки с ЧПУ которые оснащаются большим количеством инструмента что позволяет снизить трудоемкость и обеспечить высокую гибкость производства при переналадке его на другой тип производства. После разработки технологического процесса механической обработки а также расчета количества основного оборудования тип производства будет уточнен.
4 Анализ базового варианта технологического процесса
Анализ базового технологического процесса обработки детали приведём с точки зрения обеспечения заданного качества детали (точность и шероховатость обрабатываемых поверхностей а также технических требований к детали) производительности обеспечения заданного объёма выпуска.
Метод получения заготовки ротора – прокат нормальной точности. Этот метод не позволяет получить точную заготовку. Можно было бы получать заготовку штамповкой на КГШП с напусками лишь на концах заготовки.
В целом для условий серийного производства технологический процесс выполнен согласно требованиям типовых техпроцессов. Недостатком можно считать большую дифференциацию операций что приводит к увеличению количества используемого оборудования.
Можно было бы использовать более совершенное оборудование концентрировать обработку на станках что привело бы к снижению материальных затрат.
Таким образом можно было бы операции 010-ю 015-ю 020-ю совместить в одну токарно-гидрокопировальную используя станок 1713Ц оснащенный 4-х сторонним поворотным барабаном это уменьшит затраты вспомогательного времени на изготовление детали повысит точность обработки она будет произведена за 1 установ. Позволит уменьшить энергетические и материальные затраты используемого оборудования. Так же это позволит убрать операцию 035-ю т. к. точности полученной на токарно-гидрокопировальном станке в ходе предыдущей обработки будет достаточно для проведения дальнейшей обработки.
Анализируя данный техпроцесс можно отметить использование настольно-сверлильных станков НС-12А на сверлильных операциях. На мой взгляд использование в среднесерийном производстве настольно-сверлильных станков является нерациональным. По-моему использование оборудования на операциях 025 035 065 090 нецелесообразным так как размеры детали малы а точность невелика. Предлагаю использовать на всех вышеуказанных операциях станок меньших габаритов. Экономическую выгоду мы получим уменьшая время на механическую обработку за счёт использования более прогрессивного оборудования. Также целесообразно провести оптимизацию режимов резания по функции минимальных затрат. На 065-й операции использование двух метчиков можно заменить одним так как точность резьбы М6-Н7 не требует двух инструментов.
Используемые в базовом техпроцессе станочные приспособления являются стандартными (кроме специальных станков автоматов и полуавтоматов) и нет существенных причин их замены на специальные.
Режущий инструмент используемый в базовом техпроцессе - из быстрорежущей стали он стандартизирован. Его можно оставить таким же за исключением применения специального инструмента используемого на 035 – ой операции: резец фасонный. Это позволит уменьшить основное время обработки и повысить производительность оборудования.
Контрольный и измерительный инструмент в базовом варианте – штанген-инструмент средства активного контроля и специальные калибры подходят для использования в условиях серийного производства и не требуют кардинального пересмотра схем контроля в новом техпроцессе.
Для удобства анализа базового технологического процесса изготовления ротора представим его в виде таблицы 1.3.
Метод получения заготовки рукоятки – штамповка на молотах. Этот метод позволяет получить довольно таки точную заготовку без напусков.
Для условий серийного производства технологический процесс рукоятки выполнен согласно требованиям типовых техпроцессов. Недостатком можно считать небольшую дифференциацию операций что приводит к увеличению количества используемого оборудования на одну единицу.
Таким образом можно было бы операции 060-ю 070-ю совместить в одну вертикально-сверлильную используя станок 2Р135Ф2 это уменьшит затраты вспомогательного времени на изготовление детали повысит точность обработки она будет произведена за 1 установ. Позволит уменьшить энергетические и материальные затраты используемого оборудования.
Используемые в базовом техпроцессе станочные приспособления являются специальным.
Режущий инструмент используемый в базовом техпроцессе является в большинстве своем из быстрорежущей стали он стандартизирован. Его можно оставить таким же за исключением применения специального инструмента используемого на следующих операциях: 060 – зенкер 105 – специальная прошивка. Это позволит уменьшить основное время обработки и повысить производительность оборудования.
Контрольный и измерительный инструмент в базовом варианте – штанген-инструмент средства активного контроля и специальные пробки подходят для использования в условиях серийного производства.
Для удобства анализа базового технологического процесса изготовления рукоятки представим его в виде таблицы 1.4.
Таблица 1.3 - Анализ базового техпроцесса ротора.
Наименование и состав операции
Измерительный инструмент
Уложить 15 прутков калибровки в призмы тисков установить размер 25 по упору станка.
Зажать заготовки гидротисками.
Пила лент. БМ 32x11x63 ТУ2 0350224638 1182-89
Уложить заготовку на магнитную плиту
Шлифовать заготовки в размер 25-05
Плита магнитная 7208-83
Круг шлиф.1450x63x203 24А40СМ 1К ГОСТ2424-83
Токарно- револьверная
Торцевать деталь в размер 11+02+05
Центровать отверстие
Проточить в размер 253 на длину 9+02
Цанга зажимная 7010-40402-02
Снять фаску со стороны квадрата 16x45° выдерживая размер 11-05
Цанга зажимная 7010-407
Штангенциркуль ШЦ-I-125-01 ГОСТ 166-89
Вертикально-сверлильная
Сверлить отверстие 51+018 на глубину h=8-05
Патрон 6-В12 гост 8522-79
Горизонтально-фрезерная
Фрезеровать уступ выдерживая размеры 7+03 и 176+03
Образцы шерох. №1 ГОСТ 9378-75
Отпилить заусенцы после фрезерования
Проточить уступ шириной 3-05 по радиусу R50 выдержав размер 95-05
Нарезать резьбу М6-Н7 на длине 7+01 №1
Переустановить метчик
Нарезать резьбу М6-Н7 на длине 7+01 №2
Очистить резьбу от окалины
Таблица 1.4 - Анализ базового техпроцесса рукоятки
Зенкеровать отверстие в размер 23+04
Подставка 7347-4275 патрон 109-В16 ГОСТ 15935-79
Полировать головку по контуру
2. Полировать ручку по контуру
Лента б.а. С14А25Н CФЖ Гост 13344-70
Расточить отверстие в размер 25+013 мм
Патрон трёхкулачковый с пневмозажимом
Резец проходной 2102-4003 резец подрезной 2112-0007 ГОСТ 18880-73
Шлифовать головку в размер 13-02
Притупить острые кромки
Полировать торец ручки соблюдая плавность перехода с полированной поверхностью
Круг войлочный Пг400x40x45 ГОСТ 10684
Вертикально-протяжная
Протянуть зубья по внутреннему отверстию
Патрон быстросменный 6153-4023 приспосбление 7632-4025
Прошивка 7632-40254-61
5 Выбор метода получения заготовки
Метод получения заготовки ее качество и точность определяют объем механической обработки (количество рабочих ходов операций техпроцесса). Выбор метода получения заготовки зависит от типа производства массы заготовки ее конфигурации размеров.
В базовом варианте технологического процесса обработки ротора применяется в качестве заготовки стальной стержень круглого сечения полученный процессом проката (пруток из сортового проката нормальной точности).
При этом способе заготовка ротора имеет массу 0187 кг когда сама деталь обладает массой 0045 кг. В данном случае КИМ составляет 24%.
Выбор заготовки – это выбор наиболее рациональной экономичной и технологичной заготовки. С целью получения наиболее точной и качественной заготовки предлагаем заготовку-поковку получаемую на КГШП более приближённую по форме и размерам.
Так как заготовка не похожа по форме и размерам на деталь то изготовление детали будет сопряжено со снятием большого количества металла с заготовки для придания ей необходимой формы и размеров что свидетельствует о немалой трудоемкости механической обработки. Метод получения заготовки ее качество и точность определяет объем механической обработки который в свою очередь устанавливает количество рабочих ходов (операций) технологического процесса.
Использование проката вынуждает снимать дополнительные припуски что приводит к увеличению механической обработки увеличению технологического времени износу инструмента. Поэтому необходимо сравнить два метода получения заготовки: сортовой прокат и поковку на КГШП.
В качестве заготовки принимаем поковку в открытых штампах.
Назначим припуски на обработку ротора по ГОСТ 7505-89 [2].
Штамповочное оборудование – КГШП.
Класс точности принимаем Т4 (т.к. основное деформирующее оборудование: кривошипный горячештамповочный пресс технологический процесс: открытая штамповка)
Группа стали М2 (т.к. сталь поковки с массовой долей углерода свыше 035 до 065 00)
Степень сложности С2 (т.к. отношение массы поковки к массе геометрической фигуры в которую вписывается форма поковки от 032 до 063)
Ориентировочная величина расчетной массы поковки определяется по формуле:
где Мп.р – расчетная масса поковки кг;
Мп.р – масса детали кг;
Кр – расчетный коэффициент принимаем 15(приложение 3 [2]).
Мп.р = 004515=00675 кг
Конфигурация поверхности разъема – плоская.
Принимаем исходный индекс 9.
Припуски на механическую обработку:
основные припуски на размеры в мм:
– ширина и высота 10
Минимальная величина радиусов закруглений наружных углов поковки 10 мм.
длина 25+132 = 276 мм;
ширина и высота 10+13·2=126 мм;
ширина 9+132 =116 мм;
диаметр 30+132 =326 мм
Допускаемые отклонения размеров:
ширина и высота 126-04+08
Допуск радиусов закруглений внутренних и наружных углов 1 мм.
Остаточный облой 07 мм.
Допускаемые отклонения штампованных уклонов ±025 их номинальной величины.
Штампованные уклоны:
на наружной поверхности 7°
Экономическое обоснование выбора заготовки
Определим стоимость поковки по формуле:
Sотх – базовая стоимость одной тонны отходов руб.; Sотх=28 руб т
кт – коэффициент зависящий от класса точности;
кс – коэффициент зависящий от группы сложности;
кв – коэффициент зависящий от массы;
км – коэффициент зависящий от марки материала;
кп – коэффициент зависящий от объема производства.
Q-масса заготовки кг;
кт =09; кс = 077; кв = 129; км = 118; кп =1
где - плотность материала заготовки =7800 кгм3;
v - объём заготовки м3.
Q=7800·00000011630=0090 кг;
Определим стоимость заготовки из проката.
Пруток из сортового проката нормальной точности на завод поступает длиной 1 м диаметром 35 мм.
Количество заготовок из данной длины проката можно получить 37 штук (1000-(25·37)=75 мм). Так же нужно учесть длину которая будет использоваться при резке проката на заготовки пилой ленточной 2 мм (т.к. количество заготовок 37 штук (37·2=74 мм)). Очевидно что оставшейся длины проката 75 мм хватит на данные операции.
Масса одной заготовки:
отходов приходящиеся на одну заготовку:
Общая масса заготовки и отходов:
М=Мзаг.+Мотх.=0187+00015=0188 кг.
Найдём стоимость одной заготовки:
Определим КИМ для обеих методов получения заготовки:
Т.к. для прутка из сортового проката нормальной точности коэффициент использования металла меньше в 2 раза коэффициента использования металла при втором способе получения то принимаем заготовку изготавливаемую на КГШП в открытом штампе.
Назначим припуски на обработку рукоятки по ГОСТ 7505-89 [2].
Штамповочное оборудование – штамповка на молотах.
Степень сложности С2 (т.к. отношение массы поковки к массе геометрической фигуры в которую вписывается форма поковки от 016 до 032)
Кр – расчетный коэффициент принимаем 13(приложение 3 [1]).
Мп.р = 012513=01625 кг
Минимальная величина радиусов закруглений наружных углов поковки 06 мм.
длина 180+13 = 1813 мм;
высота 13 +13·2=156 мм;
диаметр 253-132 =227 мм;
диаметр 32+132 =346 мм
Q=7800·0000020512=016 кг;
7 Выбор методов обработки
При назначении метода обработки следует стремиться к тому чтобы одним и тем же методом обрабатывать возможно большее количество поверхностей заготовки что дает возможность разработать операции с максимальным совмещением обработки отдельных поверхностей сократить общее количество операций длительность цикла обработки повысить производительность и точность обработки заготовки.
При выборе метода обработки необходимо пользоваться приведенными справочными таблицами экономической точности обработки в которых содержаться сведения о технологических возможностях различных методов обработки. Назначаем метод обработки поверхностей ротора и рукоятки и заносим их в табл. 1.5 и 1.6 соответственно.
Таблица 1.5 - Выбор методов обработки ротора.
Заготовка 16 квалитет
Шлифование черновое 14 квалитет
Наружная цилиндрическая
Точение черновое 13 квалитет
Точение чистовое 11 квалитет
Внутренняя цилиндрическая
Сверление черновое 13 квалитет
Точение черновое 14 квалитет
Сверление черновое 14 квалитет
Однократное фрезерование
Проверим число переходов которые обеспечат заданную точность размеров формы и взаимного расположения поверхностей по величине требуемого уточнения.
Требуемая величина уточнения для определенной поверхности находится по формуле:
где Ку—требуемая величина уточнения;
dзаг—допуск размера формы или расположения поверхностей заготовки;
dдет—допуск размера формы или расположения поверхностей детали.
Затем определяется расчетная величина уточнения по выбранному маршруту обработки поверхности:
где Ку.расч.—расчетная величина уточнения;
К1 К2 Кn—величины уточнения по каждому переходу или операции при обработке рассматриваемой поверхности.
где d1—величина максимальной погрешности размера формы или расположения поверхностей которая имеет место на первом переходе (операции) при обработке рассматриваемой поверхности.
где d2—величина максимальной погрешности размера формы или расположения поверхностей которая имеет место на втором переходе (операции) при обработке рассматриваемой поверхности.
где dn—величина максимальной погрешности размера формы или расположения поверхностей которая имеет место на n—переходе (операции) при обработке рассматриваемой поверхности.
После выбора методов обработки поверхностей детали проверим правильность выбора методов для 2-х поверхностей путём расчёта заданного и расчетного уточнений.
Для поверхности 253-013 ротора.
Заготовка— поковка КГШП соответствует 16 квалитету d=13 мм.
точение черновое 13 квалитет d=033м.
точение чистовое 11 квалитет d=013м.
Расчетное уточнение на первом переходе:
Расчетное уточнение на втором переходе:
Общая расчетная величина уточнения:
Так как Ку=Кур (10=10) то назначенный маршрут обработки поверхности 253-013 обеспечит заданную точность.
На основании выборочных способов обработки разработаем технологический маршрут для детали ротор.
По предварительному маршруту обработки произведем выбор оборудования и составим маршрут обработки.
5 Вертикально-фрезерная с ЧПУ
5 Вертикально-сверлильная с ЧПУ
Таблица 1.6 - Выбор методов обработки рукоятки.
Высота головки 13-02
Шлифование 12 квалитет
Зенкерование 13 квалитет
Растачивание 12 квалитет
Для поверхности внутренней цилиндрической 253+01.
Сверление черновое 14 квалитет d=052 мм.
Сверление чистовое 12 квалитет d=021 мм.
Так как КуКур (62606) то назначенный маршрут обработки внутренней цилиндрической 253+01 обеспечит заданную точность.
На основании выборочных способов обработки разработаем технологический маршрут для детали рукоятка.
0 Вертикально-сверлильная с ЧПУ
0 Плоскошлифовальная
0 Вертикально-протяжная
После выбора технологического маршрута обработки и выбора оборудования заполняем маршрутные карты технологического процесса по ГОСТ 3.11.03-82.
8 Выбор технологических баз
Выбор баз для механической обработки производится с учетом достижения требуемой точности взаимного расположения поверхностей детали по линейным и угловым размерам обеспечения доступа инструментов к обрабатываемым поверхностям обеспечения простоты и унификации станочных приспособлений а так же удобства установки в них заготовки.
В процессе обработки ротора предлагаю использовать следующие схемы базирования.
Чистовыми базами на дальнейших операциях механической обработки ротора будут являться поверхность 30 и поверхности квадратного хвостовика. Установка детали на токарных фрезерных и сверлильных станках позволяет обеспечить доступ к большинству обрабатываемых поверхностей ротора.
Для сверления и нарезания резьбы в качестве баз используем квадратный хвостовик с установкой в четырёхкулачковый патрон специальный.
Рисунок 1.6 – Схема базирования при нарезании внутренней цилиндрической резьбы
Для точения уступа ротор базируется на спутнике по хвостовику.
Рисунок 1.7 – Схема базирования при точении уступа
При фрезеровании уступа ротор в качестве баз используем квадратный хвостовик с установкой в оправку.
Рисунок 1.8 – Схема базирования при фрезеровании уступа
Для точения наружной цилиндрической поверхности ротор закрепляется в патрон.
Рисунок 1.9 – Схема базирования при точении наружной цилиндрической поверхности
Для сверления отверстия 51 в качестве чистовой базы используется 30. Ротор устанавливается в патрон.
Рисунок 1.10 – Схема базирования при сверлении отверстия
При точении ротора по контуру и подрезке торца со стороны хвостовика деталь устанавливается в патрон.
Рисунок 1.11 – Схема базирования при контурном точении наружной поверхности и подрезке торца
При фрезеровании хвостовика деталь устанавливается в патрон
Рисунок 1.12 – Схема базирования при фрезеровании квадратной поверхности
Рисунок 1.13 – Схема базирования при точении наружной цилиндрической поверхности
В процессе обработки рукоятки предлагаю использовать следующие схемы базирования.
Для протягивания внутреннего цилиндрического отверстия рукоятка устанавливается в патрон быстросменный.
Рисунок 1.14 – Схема базирования при протягивании внутреннего цилиндрического отверстия
Устанавливается деталь на магнитной плите при шлифовании торцов.
Рисунок 1.15– Схема базирования при шлифовании торцов
При подрезке торцов растачивании и снятии фаски на внутреннем цилиндрическом отверстии рукоятка устанавливается в патрон.
Рисунок 1.16 – Схема базирования при подрезке торцов растачивании и снятии фаски на внутреннем цилиндрическом отверстии
При зенкеровании внутреннего цилиндрического отверстия рукоятка устанавливается в патрон.
Рисунок 1.17 – Схема базирования при зенкеровании внутреннего цилиндрического отверстия
9 Разработка технологического маршрута обработки
На данном этапе разрабатывается общий план обработки детали определяется содержание операций техпроцесса. При этом заполняются маршрутные карты техпроцесса (приложение).
При составлении маршрута обработки воспользуемся базовым технологическим процессом а также следует учитывать следующие положения:
-каждая последующая операция должна уменьшить погрешность и улучшить качество поверхности;
-в первую очередь следует обрабатывать те поверхности которые будут служить технологическими базами для следующих операций.
Предварительная разработка и выбор варианта технологического маршрута ротора
Операция 005 Транспортная
Доставить заготовки на участок обработки
Операция 010 Токарная с ЧПУ
Станок: токарный с ЧПУ 16А20ФЗС15
Точить наружную цилиндрическую поверхность 30 мм
Операция 015 Вертикально-фрезерная с ЧПУ
Станок: вертикально-фрезерный 6Т13Ф20
Фрезеровать квадратный хвостовик
Операция 020 Токарная с ЧПУ
Точить по контуру со стороны хвостовика
Операция 025 Вертикально-сверлильная с ЧПУ
Станок: вертикально-сверлильный 2Р135Ф2
Сверлить внутреннее глухое отверстие 51мм
Операция 030 Токарная с ЧПУ
Подрезать торец в размер 25-05 и точить 253 мм
Операция 035 Вертикально-фрезерная с ЧПУ
Операция 040 Токарная с ЧПУ
Операция 045 Сверлильная
Станок: сверлильный 2Н135
Сверлить внутреннее отверстие и нарезать резьбу М6-7Н
Операция 050 Слесарная
Калибрование резьбы. Опиливание острых кромок.
Операция 055 Моечная
Операция 060 Контрольная
Операция 065 Транспортная
Транспортировать деталь на участок сборки
Предварительная разработка и выбор варианта технологического маршрута рукоятки
Операция 005 Транспортная.
Доставить заготовки на участок обработки
Операция 010 Вертикально-сверлильная с ЧПУ
Зенкеровать отверстие 23+04 мм
Операция 015 Токарная с ЧПУ
Станок: токарный 16А20ФЗС15
Подрезать торец расточить отверстие 25 и снять фаску
Операция 020 Плоскошлифовальная
Шлифовать торцы в размер 13-02
Операция 025 Полировальная
Полировать ручку по контуру
Операция 030 Вертикально-протяжная
Протянуть зубья по внутреннему отверстию
Операция 035 Моечная
Операция 040 Контрольная
Операция 045 Транспортная
10 Разработка технологических операций
На этом этапе окончательно определяется состав и порядок выполнения переходов в пределах каждой технологической операции производится выбор моделей оборудования станочных приспособлений режущих и измерительных инструментов.
Разработка технологических операций для детали ротор
Доставить заготовки на участок обработки.
Трактор-погрузчик Q=20кН. Тара Р1448 2ЯН1286 Q=2тс
Приспособление: четырехкулачковый патрон специальный
Режущий инструмент: Резец проходной 2102-1371 ГОСТ 24996-81
Измерительный инструмент: штангенциркуль ШЦ-1-125-005 ГОСТ 166-89
Фрезеровать квадратный хвостовик в размер 10-0565-0475 и 127-03
Приспособление: фрезерное 7220-6095
Режущий инструмент: фреза 2223-0116 ГОСТ 166-89
Точить по контуру со стороны хвостовика подрезать торец выдерживая длину 11-011 и фаску 06x45°.
Приспособление: трёхкулачковый патрон специальный
Режущий инструмент: резец проходной 2102-1371 ГОСТ 24996-81 резец фасон.2126-4007
Приспособление: оправка 6030-4008
Режущий инструмент: сверло 2300-6175 ГОСТ 10902-77 метчик 2620-1115 ГОСТ 3266-81
Измерительный инструмент: штангенциркуль ШЦ-I-125-01 ГОСТ 166-89 пробка 8130-4159 калибр 8389-40005
Подрезать торец в размер 25-05 .
Черновое точение 253 мм.
Получистовое точение 253 мм.
Чистовое точение 253 мм.
Режущий инструмент: резец проходной 2102-1371 ГОСТ 24996-81
Фрезеровать уступ выдерживая размеры 7+01 и 176+03.
Приспособление: фрезерное 7220-6095.
Режущий инструмент: фреза 2234-0355Р9 ГОСТ 9140-78.
Измерительный инструмент: штангенциркуль Ц 111-1-125-0.05 ГОСТ 166-89
Точить уступ R50 выдерживая размеры 2 и 95-05.
Приспособление: пневмопривод спутник М305.01.001
Режущий инструмент: резец 01214-080404 ГОСТ 19048-80
Измерительный инструмент: штангенциркуль ШЦ-I-125-01 ГОСТ 166-89 шаблон 1176.000
Режущий инструмент: сверло 2300-6175 ГОСТ 10902-77 метчик №1 2620-1115 ГОСТ 3266-81
Разработка технологических операций для детали рукоятка
Зенкеровать отверстие 23+04 мм
Приспособление: подставка 7347-4275 патрон 109-В16 ГОСТ 15935-79
Режущий инструмент: зенкер 2330-4015
Измерительный инструмент: пробка 8154-4088 пробка 8154-4087
Подрезать торец в размер 13 расточить отверстие 25 и снять фаску 06x45°
Приспособление: патрон трёхкулачковый с пневмозажимом
Режущий инструмент: резец подрезной 2112-0007 ГОСТ 18880-73 резец проходной 2102-4003
Измерительный инструмент: пробка 8130-4187
Шлифовать торцы головки в размер 13-02
Приспособление: плита магнитная 7208-83
Режущий инструмент: круг шлиф.1450x63x203 24А40СМ 1К ГОСТ 2424-83
Измерительный инструмент: скоба 8150-4217
Полировать торец ручки соблюдая плавность перехода с полированной поверхностью
Режущий инструмент: круг войлочный Пг400x40x45 ГОСТ 10684
Приспособление: патрон быстросменный 6153-4023 приспособление 7632-4025
Режущий инструмент: прошивка 7632-40254-61
Измерительный инструмент: пробка 8130-4385
11 Технологический процесс сборки
Рисунок 1.18 – Эскиз ключа трещоточного
Рисунок 1.19 – Схема сборки ключа трещоточного
12 Аналитический расчет припусков на обработку
Произведём расчёт припусков расчётно-аналитическим методом на две различные поверхности а так же построим для них схемы расположения припусков и допусков.
Рассчитаем припуски и предельные размеры по переходам на обработку наружной цилиндрической поверхности ротора 253-013.
Исходные данные: Заготовка – поковка. Класс точности Т4. Группа стали М2. Степень точности С2. Исходный индекс 9 ГОСТ 7505-89.заготовки 009 кг. Обработка детали ведется в патроне. Параметры поковки: 16 кв Rz=80 мкм h=150 мкм (т.27[2]).
Составим технологический маршрут получения поверхности 25-013 с указанием Rz и h по переходам(т.29[2]):
-й переход – точение черновое 14 квалитет Rz=50 мкм h=50 мкм;
-й переход – точение получистовое 12 квалитет Rz=30 мкм h=30мкм;
-й переход – точение чистовое 11 квалитет Rz=25 мкм h=25 мкм.
Пространственное отклонение формы поверхности заготовки рассчитаем по формуле:
где ρсм –смещение полуматриц друг относительно друга штампуемой части заготовки относительно стержня исходного материала ρсм=03 мм (т.34[2]);
ρкор –коробление(кривизна) заготовки.
где Δк – удельная кривизна заготовки Δк=6 мкммм (т.32[2]);
l – длина поверхности l=L2=252=125 мм.
Следовательно имеем : ρкор = 6 · 125 = 75 мкм.
Остаточное пространственное отклонение по переходам определяем по формуле:
где Ку – коэффициент уточнения формы.
-й переход – ρ1 =006·ρ=006·309=1854 мкм;
-й переход – ρ2 =004·ρ=005·1854=0927 мкм;
-й переход – ρ3=002·ρ=004·0927=004 мкм.
Погрешность установки детали на всех операциях у равна нулю (базирование в патроне).
Расчёт минимальных значений межоперационных припусков производим по формуле:
где i – выполняемый переход.
Тогда минимальный припуск по переходам будет следующим:
Расчётные размеры рассчитываем начиная с конечного максимального чертёжного размера последовательным вычитанием 2Zmini каждого технологического перехода:
-й переход DP3 =2517 мм;
-й переход DP2 =2517 +0122=25292 мм;
-й переход DP1 = 25292 +0237=25529 мм;
Заготовка Dр.загот =25529 +1078=26607 мм.
Назначаем допуски на технические переходы по таблице а допуски на заготовку по ГОСТ 7505 – 85.
Заготовка - 1300 мкм;
-й переход – 520 мкм;
-й переход – 210 мкм;
-й переход – 130 мкм;
Предельный размер Dmin определяем округляя Dp до большего значения в пределах допуска на данном переходе а Dmax определяем прибавлением к Dmin допусков соответствующих переходов:
-й переход: D3 m D3 ma
-й переход: D2 m D2 ma
-й переход: D1 m D1 ma
заготовка Dзаг.min=265мм Dзаг.max=265+13=278 мм.
Максимальное предельное значение припусков 2×Zmax.ПР находим как разность наибольших предельных размеров выполняемого и предшествующего переходов а минимальные значения 2×Zmin.ПР – как разность наименьших предельных размеров выполняемого и предшествующих переходов.
Z1 minПР = 265-257=08 мм.
Общий минимальный припуск находим как сумму минимальных промежуточных припусков а общий максимальный – как сумму максимальных припусков:
Z0min=08+03+023=17 мм.
Общий номинальный припуск 2Z0ном вычисляем по формуле:
Z0ном=Z0min+Нз-Нд (1.12)
где Нз и Нд – соответственно нижнее отклонение допуска заготовки и детали.
Z0ном=17+05-013=233мм.
Следовательно номинальный диаметр поверхности заготовки будет равен:
DЗном=DДном+2Z0ном=253+233=2763 мм.
Производим проверку правильности расчётов по формулам:
Zmaxi-2Zmini=Di-1- Di (1.13)
Z0max-2Z0min=DЗ- DД (1.14)
Для нашего случая имеем:
-й переход 210-130=310-230; т.е. 80=80;
-й переход 520-210=610-300; т.е. 310=310;
-й переход 1300-520=1580-800; т.е. 780=780;
общий припуск 2800-1630=1300-130; т.е1170=1170.
Расчёт произведён правильно.
Все расчёты параметров припусков приведём в таблицу 1.11.1.
Таблица 1.7 – Результаты расчёта припусков на поверхность ротора 253-013.
Технологи-ческие переходы обработки поверхности 45js7
Элементы припуска мкм
Расчётный припуск 2Zmin мкм
Расчётный размер Dр мм
Допуск на размер D мкм
Предельный размер мм
Предельные значения припусков мм
На основании таблицы строим схему графического расположения припусков и допусков на обработку поверхности ротора 253-013.
Рисунок 1.19 — Схема графического расположения припусков и допусков на обработку поверхности диаметром 253-013
Выберем технологический маршрут обработки отверстия 253+01 и определим величины Rz и h по переходам:
Заготовка 16 квалитета: Rz = 80 h = 150
-й переход: зенкерование 13 кв. Rz = 40 h = 40
-й переход: растачивание 12 кв. Rz = 32 h = 30
Определим значения пространственных отклонений для заготовки.
где rсм – смещение оси головки относительно общей оси; rсм = 0
rкор – коробление вала;
где К – удельная кривизна заготовки К =8;
l – длина заготовки.
rзаг=rкор = 13×8 = 104 мкм
Остаточное пространственное отклонение по формуле:
где КУ – коэффициент уточнения формы.
Погрешность установки детали на выполняемом переходе eу определяем по формуле:
где eb – погрешность базирования eb = 0;
eз – погрешность закрепления eз = 80.
-й переход r1 = 005×104 = 52 мкм; e1 = 80×005 = 4 мкм
-й переход r2 = 004×52 = 0208 мкм; e2 = 4×004 = 016 мкм
Расчёт минимальных межоперационных припусков:
Расчётный размер диаметра отверстия DР вычислим начиная с конечного максимального чертёжного размера путём последовательного вычитания минимального припуска каждого предыдущего перехода:
-й переход: DР растч.. =254-2×0045 = 2531 мм
-й переход: DР зенк. = 2531-2×0334 = 24642 мм
Назначаем допуски на технологические переходы:
Заготовка – 1300 мкм
-й переход – 330 мкм
-й переход – 210 мкм
Предельный размер Dmax определяем округляя Dp до меньшего значения в пределах допуска на данном переходе а Dmin определяем вычитая из Dmax допуски соответствующих переходов:
-й переход: Dma Dmin растч..= 254-021=2519 мм
-й переход: Dma Dmin зенк. = 2531-033 = 2498 мм
заготовка: Dmax заг. = 24642 мм Dmin заг. = 24642-13 = 23342 мм
Минимальные предельное значение припусков 2×Zmin.ПР. находим как разность наибольших предельных размеров выполняемого и предшествующего переходов а максимальные значения 2×ZmaxПР – как разность наименьших предельных размеров выполняемого и предшествующих переходов.
Общий минимальный припуск находим как сумму минимальных промежуточных припусков а общий максимальный – как сумму максимальных припускав:
Общий номинальный припуск находим по формуле:
где ВЗ – верхнее отклонение заготовки по ГОСТ 2590 – 71
ВД – верхнее отклонение детали по чертежу.
Тогда номинальный диаметр заготовки:
Проверяем правильность произведённых расчётов:
-й переход: 021-009 =033-021 мм 012=012 мм
-й переход: 1638-0668 = 13-033 мм 097=097 мм
Общий припуск: 1848-0758 = 13-021 мм 109=109 мм
Проверка правильна значит расчёты межоперационных припусков произведены верно. Все расчёты параметров припусков приведём в таблицу 1.11.2.
Таблица 1.8 Результаты расчёта припусков на поверхность рукоятки 253+01
переходы обработки поверхности
Расчётный припуск 2×Zmin мкм
Расчётный размер Dp мкм
Допуски размеров мкм
Предельные размеры припусков мкм
На основании таблицы строим схему графического расположения припусков и допусков на обработку поверхности рукоятки 253+01.
Рисунок 1.20 — Схема графического расположения припусков и допусков на обработку отверстия 25+01
13 Расчет режимов резания
Произведем расчет режимов резания для двух разных типов операций. Одной – чернового точения поверхности ротора 253-013 на операции « 030 Токарная с ЧПУ». Другой – протягивания отверстия рукоятки 253+01 на операции « 030 Токарная с ЧПУ».
Расчет проведем по эмпирическим формулам по методике [3].
Произведём расчёт режимов резания обработки размера 253-013 точением.
Глубина резания – t = 2 мм;
Подача– So = 06 ммоб.
Скорость резанья при точении – окружная скорость вращения заготовки:
Т – период стойкости и показатели степеней находим по таблицам:
СV = 290; y = 035; m = 02; T = 60 мин.
KV = KМV× KПV× KИV (1.22)
где KМV – коэффициент учитывающий качество обрабатываемого материала;
KПV – коэффициент учитывающий состояние поверхности заготовки;
KИV – коэффициент учитывающий материал инструмента.
где sB – физический параметр характеризующий обрабатываемый материал;
КГ и nv – коэффициент и показатель степени характеризующие группу стали по обрабатываемости.
KИV = 115; KПV = 08;
Определяем окружную скорость вращения заготовки:
Силы резания при точении Н:
где Ср – поправочный коэффициент Ср =300;
х у n – показатели степеней х=1 у=075 n = -015;
Кр – поправочный коэффициент.
где - коэффициенты учитывающие фактические условия резания
Кφp=108 Кλp=1 Кp=087.
Определяем Кмр по формуле:
где n0 - показатель степени nv = 09.
Определим частоту вращения по формуле:
где n - частота вращения шпинделя мин-1;
Частота вращения заготовки:
Принимаем n = 1350 oб мин.
Определяем мощность затрачиваемую на резание по формуле:
Находим мощность резания:
Определяем основное время То:
где Sо - оборотная подача обмин ;
Таблица 1.19 - Сводная таблица режимов резания ротора
Наименование операции или перехода
Вертикально-фрезерная с ЧПУ
Вертикально-свер-лильная с ЧПУ
-получистовое точение
Вертикально-фрезерная с ЧПУ
Произведём расчёт режимов резания обработки размера 253+01 протяжкой.
Глубина резания – t =5 мм;
Скорость резанья при протягивании определяемую требованиями к точности обработки и параметрам шероховатости обработанной поверхности выбирают в зависимости от группы скорости устанавливаемой по методике [3]. При нормативной скорости резания заданный параметр шероховатости поверхности может быть достигнут при оптимальных значениях переднего и заднего углов.
Согласно методике [3] выбираем группу скорости 3. Следовательно получаем нормативную скорость резания:
Сравним нормативную скорость резания с максимальной скоростью рабочего хода станка.
где N - мощность двигателя станка кВт; N= 10 кВт
Pz – сила резания при протягивании; Pz=0.8105 H
Таблица 1.20 - Сводная таблица режимов резания рукоятки
Вертикально-сверлильная с ЧПУ
- расточить отверстие
14 Определение норм времени на операции
При серийном производстве норма штучного времени определяется по формуле:
где То—основное (машинное) время обработки детали мин;
Тв—вспомогательное время на операцию (время на установку и снятие детали подвод и отвод инструмента время на управление станком и т.д.) мин;
Тобс—время на техническое и организационное обслуживание рабочего места (время на замену затупившегося инструмента время на уборку рабочего места в конце работы) мин;
Тотд—время на отдых и личные надобности мин.
где Тус—время на установку и снятие детали мин;
Тзо—время на закрепление и открепление детали мин;
Туп—время на приемы управления мин;
Тиз—время на измерение детали мин.
где Ттех—время на техническое обслуживание рабочего места мин;
Торг—время на организационное обслуживание рабочего места мин.
Оперативное время Топ:
Время на организационное и техническое обслуживание определяется в процентах от оперативного времени.
Tтех + Tорг =к*Tоп100%
где П—затраты времени на отдых в процентном отношении к оперативному.
Рассчитаем норму штучного калькуляционного времени для операции 015 ротора (вертикально-фрезерной). Производство среднесерийное масса детали 045 кг.
Тус+Тзо=006+0024=0084 мин Туп=001+02=021 мин. — время на включение станка и подвод инструмента (станок включается кнопкой)
Время на измерение штангенциркулем ШЦ-I-125-005 Тиз=012 мин
Вспомогательное время:
Тв=0084+021+012=0414 мин
Топ=16+0414 =2014 мин
То=16 - основное время на обработку заготовки на данной операции
Затраты времени на обслуживание рабочего места и отдых в процентном отношении к оперативному равно 7% тогда:
Тобс=2014·7100=0145 мин
Подставляем полученные значения времен:
Тшт=16+0414+0145=215 мин
Tп.з.- подготовительно-заключительное время на партию заготовок
- время на наладку станка и установку приспособлений 14 мин
- время на установку фрез (1 шт.) 2 мин
- получить наряд чертеж технологическую документацию режущий и вспомогательный инструмент контрольно-измерительный инструмент приспособление заготовки исполнителем до начала и сдать их после окончания обработки партии деталей 13 мин
-ознакомится с работой чертежом технологической документацией осмотреть заготовки 20 мин
-инструктаж мастера 20 мин
Tп.з.=14+2+13+2+2=33 мин
Количество деталей в партии:
n=50000·6254=1181 шт.
Время приходящееся на одну заготовку из партии:
Tшт.к.=0028+215=218 мин
Рассчитаем норму штучного калькуляционного времени для операции 015 рукоятки (Токарная с ЧПУ). Производство среднесерийное масса детали 0125 кг.
- установить заданное взаимное положение детали и инструмента по координатам XYZ и при необходимости произвести подналадку 032 мин
- включить и выключить лентопротяжный механизм 004 мин
- открыть и закрыть крышку лентопротяжного механизма перемотать заправить ленту в считывающее устройство 031 мин
- проверить переход деталиинструмента в заданную точку после
- продвинуть перфоленту в исходное положение 019 мин
- установить и снять щиток от набрызгивания эмульсией 003 мин
Тус+Тзо=005+0024=0074 мин
Туп=031+004+032+015+019+003=0752 мин.
Время на измерение штангенциркулем ШЦ-I-125-005: Тиз=012 мин Вспомогательное время:
Тв=0074+0752+012=0946 мин
Топ=0946+065=1596 мин
То=065 - основное время на обработку заготовки на данной операции
Затраты времени на обслуживание рабочего места и отдых в процентном отношении к оперативному равно 6% тогда:
Тобс=1596·6100=0096 мин
Тшт=0946+065+0096=169 мин
- получить наряд чертеж технологическую документацию программоноситель режущий и вспомогательный инструмент контрольно-измерительный инструмент приспособление заготовки исполнителем до начала и сдать их после окончания обработки партии деталей 13 мин
-ознакомится с работай чертежом технологической документацией осмотреть заготовки 20 мин
-установить и снять патрон трехкулачковый 25 мин
- установить исходные режимы станка 015 мин
- установить и снять кулачки 65 мин
-расточить кулачки 62 мин
-установить и снять инструментальный блок или отдельный режущий инструмент (время на один инструмент( блок)) 02 мин
-установить программоноситель в считывающее устройство
-проверить работоспособность считывающего устройства и
-ввести программу в память системы с ЧПУ с
программоносителя 15 мин
-установить исходный координаты X и Z (настроить нулевое
Tп.з.=13+2+2+25+015+65+62+02+1+1+15+2=385 мин
Время приходящиеся на одну заготовку из партии
Tшт.к.=003+169=17 мин
Нормы времени на остальные операции назначаем по нормативным справочникам. Рассчитанные и назначенные времена сведем в таблицу.
Таблица 1.20 - Сводная таблица технических норм времени по операциям ротора мин.
Вертикально-сверлильная с ЧПУ
Таблица 1.21 - Сводная таблица технических норм времени по операциям рукоятки мин.
Плоскошлифо-вальная
15 Определение необходимого количества оборудования
Для серийного производства количество станков S определяется по формуле:
Тшт—штучное время обработки изделия мин;
F—действительный годовой фонд времени работы оборудования час.
Коэффициент загрузки оборудования:
где Sпр—принятое количество станков.
Объём выпуска деталей “ротор” – 50000
На основании рассчитанных коэффициентов строим график загрузки оборудования.
Рисунок 1.21 – График степени загружённости станков на операциях ротора:
-й столбец Токарная с ЧПУ станок модели 16А20Ф3С15
-й столбец Вертикально-фрезерная станок модели 6Т13Ф20
-й столбец Вертикально-сверлильная станок модели 2Р135Ф2
-й столбец Сверлильная станок модели 2Н135
Анализируя полученные данные необходимо отметить неудовлетворительную загрузку станков. Поэтому следует совместить токарную обработку и выполнять операции 010 020030 и 040 на одном станке. Загрузка оборудования в этом случае будет составлять около 75%. Большинство оборудования универсальное поэтому его следует догружать операциями по обработке других деталей для увеличения коэффициента загрузки оборудования.
Объём выпуска деталей “рукоятка” – 50000
Рисунок 1.22 – График степени загружённости станков на операциях рукоятки:
-й столбец Плоскошлифовальная станок модели 2Н118
-й столбец Вертикально-протяжная станок модели 3М6341.16 Уточнение типа производства по коэффициенту закрепления операций
Уточненный расчет типа производства основывается на определении коэффициента закрепления операций Кзо:
где О—количество всех различных технологических операций выполненных в течении месяца;
Р—число рабочих мест необходимых для выполнения месячной программы.
Согласно ГОСТа для среднесерийного типа производства Кзо=10 20
Число рабочих мест для выполнения определенной i-ой операции определяем по формуле:
где Nм—месячный объем выпуска детали (2500 шт);
Тшт—штучное время на выполнение определенной операции мин;
Fм—месячный фонд времени работы оборудования (196 час);
Кв—коэффициент выполнения норм времени. Кв=11 13
Рассчитанное число рабочих мест округляем до ближайшего большего целого числа Рi.
Коэффициент загрузки данных рабочих мест выполняемой операцией:
Количество операций выполняемых на этом рабочем месте при его нормативной загрузке определяем по формуле:
где: hн=07 085—нормативный коэффициент загрузки для среднесерийного
Общее количество операций выполняемых на всех рабочих местах проектируемого техпроцесса и общее количество рабочих мест определяется как сумма всех операций и сумма всех рабочих мест соответственно.
Результаты расчетов сведем в таблицу.
Таблица 1.22 — Определение типа производства детали “ротор”.
Определяем коэффициент закрепления операций:
Коэффициент Кзо находится в промежутке от 1 до 10 причем ближе к 10. Следовательно принимаем среднесерийный тип производства.
Таблица 1.23 — Определение типа производства детали “рукоятка”.
Коэффициент Кзо равен 10. Следовательно принимаем среднесерийный тип производства.
Определим такт выпуска продукции t:
где F—действительный годовой фонд времени работы оборудования при 2-ух сменной работе (4015 час).
17 Расчет технологической размерной цепи
Технологическую размерную цепь составляем по операции 40.
В качестве замыкающего звена А0 выбираем размер который выдерживается без соблюдения принципа единства баз. Таким размером является размер 7-0.36.
Любой размер можно представить как расстояние между двумя точками (его границами) на условной координатной оси. Это расстояние зависит от координат границ размера то есть от двух размеров связывающих начало координат с этими границами.
Аналогичная зависимость имеет место при формировании размеров деталей в процессе их механической обработки партиями на заранее настроенных станках. При этом используется контактное базирование деталей и режущий инструмент настраивается относительно установочных элементов приспособления контактирующих с технологическими базами детали. В этих условиях начало координат для отсчёта положений границ формируемого размера детали следует принимать на технологической базе ориентирующей деталь в направлении этого размера так как она контактирует с неизменными установочными элементами приспособления и занимает стабильное положение для всех деталей партии. Таким образом исходный размер А0 в общем случае зависит от двух размеров (А1 и А2) которые связывают его границы с соответствующей технологической базой. Один из этих размеров А1=9+0.2 мм связывающий технологическую базу с формируемой режущим инструментом границей исходного звена называется технологическим размером. Второй размер А2=2 -025 мм.
Составляющее звено размерной цепи может быть увеличивающим или уменьшающим. Увеличивающим называется звено размерной цепи увеличение которого способствует увеличению размера исходного звена при фиксированных размерах других составляющих звеньев данной размерной цепи а уменьшающим – такое звено размерной цепи увеличение которого способствует уменьшению размера исходного звена при фиксированных размерах других составляющих звеньев данной размерной цепи.
Проведем расчет следующей размерной цепи.
Рисунок 1.23 – Размерная цепь
Решим проектную задачу методом полной взаимозаменяемости т.е. определим допуски составляющих звеньев по известному допуску замыкающего звена.
Допуск замыкающего звена =036 мм
Так как число составляющих звеньев равно трем то для расчета размерной цепи в первом приближении будем использовать метод равноточных допусков (метод допусков одного квалитета)
где a - число единиц допуска определяет зависимость допуска от
- единица допуска определяет его зависимость от номинального
где - среднее геометрическое границ интервала номинальных
размеров в таблице допусков в который попадает j-е
где и - минимальная и максимальная величина размера
входящие в данный интервал
Найдём среднее геометрическое границ интервала:
Определяем единицы поля допуска:
Найдём среднее число единиц поля допуска:
Величины допусков составляющих звеньев:
По таблице допусков определяем что данные величины допусков соответствуют 14 квалитету.
Допуски составляющих звеньев должны удовлетворять условию:
0≥360- условие выполняется
Расчёт и проектирование средств технологического оснащения
1 Проектирование станочного приспособления
1.1 Описание конструкции и работы приспособления
Проектируемое приспособление предназначено для точения уступа. В данном случае приспособление устанавливается на токарный станок с ЧПУ модели 16А20Ф3С15.
Приспособление представляет собой спутник на который устанавливаются восемь деталей ротора по окружности и прижим в центре. С помощью переходника который соединен со штоком пневмоцилиндра происходит прижим спутника к планшайбе. Торец ротора упирается в диафрагму. На периферии установлен штифт который не предохраняет спутник от проворота относительно планшайбы. Планшайба установлена на шпинделе токарного станка. Приспособление является восьмиместным что увеличивает производительность в условиях среднесерийного производства.
Закрепление детали осуществляется следующим образом:
детали устанавливаются в спутник;
спутник устанавливается на планшайбу;
включают пневмоцилиндр который осуществляет зажим спутник.
1.2 Расчет сил зажима заготовки
Расчет сил зажима сводится к решению задачи статики на равновесие твердого тела под действием внешних сил. Величина сил зажима определяется из условия равновесия всех сил при полном сохранении контакта технологических баз обрабатываемой заготовки с установочными элементами приспособления и невозможности ее сдвига или поворота в процессе обработки.
Условия установки и закрепления детали в приспособлении дают возможности считать приспособление на возможность перекоса заготовки относительно своей оси. Поэтому будем вести расчет на перекос оси под действием силы резания Рх.
Рисунок 2.1 - Схема расположения сил резания
На заготовки действуют сила зажима Р1 и сила резания Рx
Запишем уравнение равновесия:
где kз—коэффициент запаса; kз =25
l1 l2—плечи соответственно сил Px P1
коэффициенты и показатели степеней определяем по таблицам:
СР = 339; х = 10; у = 05; n=-04.
Тогда окружная сила резания равна:
Из приведенных выше расчетов видно что сила зажима необходимая для того что бы избежать перекоса заготовки намного выше силы резания Рх = 880 Н.
Рассчитаем диаметр пневмоцилиндра необходимого для создания силы зажима.
Определяем диаметр цилиндра D:
где p—давление в пневмосистеме (р = 05 МПа);
h = 085—КПД пневмоцилиндра;
Pш – усилие на штоке.
Принимаем стандартное значение диаметра D = 180 мм.
1.3 Расчет приспособления на точность
Цель расчета приспособления на точность заключается в определении требуемой точности изготовления приспособления по выбранному точностному параметру и задании допусков размеров деталей и элементов приспособления.
где Епр—погрешность приспособления мм;
d—допуск выполняемого размера мм;
Кт—коэффициент учитывающий отклонение рассеивания значений составляющих величин от закона нормального распределения (Кт = 11);
Kт1—коэффициент учитывающий уменьшение предельного значения погрешности базирования при работе на настроенных станках (kт1 = 08);
eб—погрешность базирования мм;
eз—погрешность закрепления мм;
eу—погрешность установки приспособления на станке мм;
eи—погрешность положения рабочих поверхностей рабочих элементов в результате их изнашивания в процессе эксплуатации приспособления мм;
eпи—погрешность от перекоса инструмента из-за неточности изготовления направляющих элементов приспособления мм;
kт2—коэффициент учитывающий долю погрешности обработки в суммарной погрешности вызываемой факторами независящими от приспособления (kт2 = 07);
v—экономическая точность обработки (v = 04 мм).
eб = 62 мкм – величина допуска для размера R50 выполненного по 14 квалитету.
eу = 0 т. к. эта погрешность будет одинакова для всей партии заготовок и ее можно компенсировать настройкой инструмента. Погрешность от износа определяем по формуле:
где b — постоянная зависящая от вида установочного элемента и условия контакта (b = 00008 мкм);
N—количество контактов заготовки с опорой (установок в приспособление снятий с него) в год.
eпи=0 — погрешности ос перекоса инструмента не будет
Подставим все значения в (2.5):
На основании расчета можно сделать вывод что погрешность размера R50 при изготовлении приспособления не должна превышать 0307 мм.
2 Проектирование приспособления для контроля перпендикулярности
Приспособление предназначено для измерения перпендикулярности
поверхности уступа с размером 7+01мм относительно бурта ступени ротора 30.
Конструкция приспособления выполнена на плите 1 к которой крепится оправка 2. На оправке размещен индикатор который движется относительно заготовки при нажатии винта 7 во втулке 4 и под действием пружины 5 индикатор возвращается в исходное положение.
На приспособление укладывают контролируемую деталь. Щуп подводим к измеряемой поверхности и устанавливаем шкалы индикатора на 0. Перемещая щуп снять показания индикаторов. Разность максимальных и минимальных показаний и будет характеризовать погрешность перпендикулярности.
Произведем расчет приспособления на точность при определении погрешности перпендикулярности.
Погрешность измерения определим как сумму зазора погрешности индикатора и погрешности перекоса втулки
где Δи – погрешность индикатора Δи = 0004 мм;
Δп – погрешность перекоса Δп=001
Δпр – погрешность передачи приспособления Δпр=0029 мм – зазор во втулке;
– допуск на измеряемый параметр = 01 мм;
Получаем 003≤013=0033 следовательно приспособление обеспечивает необходимую точность измерения.
3 Расчет конструктивных параметров протяжки
Минимальный диаметр отверстия под протягивание: d = 25 мм; диаметр отверстия получаемое после протягивания: D = 26 мм. Предельное отклонение диаметра D по чертежу детали: =0067 мм длина протягиваемого отверстия: = 009 мм.
Материал заготовки: Сталь 40Х: = 900 МПа; HB = 187
Рисунок 2.2 - Профиль обрабатываемого отверстия
D1= 25-05 = 245 мм. (2.10)
где d - минимальный диаметр отверстия под протягивание мм.
Расчетную величину D1 округляем до ближайшей меньшей величины соответствующей ГОСТ 4044-70. Принимаем D1 = 22 мм. Остальные размеры хвостовика и размеры шейки принимаем соответственно с ГОСТ 4044-70:
D1' =17 мм; D2 = 215 мм;
R1= 03 мм; R2 = 1 мм; C = 05 мм; α = 20.
Рисунок 2.3 - Хвостовик протяжки
Длину конуса принимаем L = 15 мм так как диаметр отверстия под протягивание D = 25 мм. Диаметры конуса: меньший равен диаметру шейки (мм): больший – передней направляющей части (мм).
Диаметр передней направляющей части мм
Dпн= d = 25 мм (2.11)
Предельное отклонение Dпн по e8.
Длина передней направляющей Lпн равна расстоянию от конца переходного конуса до первого зуба режущей части то есть включая длину первой стружечной канавки.
Lпн = т.к. lдD = 1006 ≤ 15 (2.12)
где lд - длина протягиваемого отверстия
D- диаметр отверстия получаемого после протягивания мм.
Главные режущие кромки зубьев имеют форму концентрических дуг диаметр которых Di постепенно увеличивается от первого зуба к последнему. Вспомогательные режущие кромки зубьев имеют криволинейную форму в зависимости от профиля обрабатываемой детали.
Величины углов в нормальном сечении по главной режущей кромке для стали 40Х принимаем:
Предельные отклонения углов по ГОСТ16492-70
γ = (-1;+ 2); α = 30;
Для уменьшения трения на вспомогательных режущих кромках делают угол равный 1 располагающийся позади ленточки шириной 08 1 мм. Для обработки заготовки принимаем зубья с криволинейной спинкой.
Ориентировочные размеры режущих зубьев и расположенных между ними стружечных канавок могут быть определены следующим соотношением:
t = (125 15) = (125 15) = 45 54 мм
Принимаем шаг зубьев 5 мм
Глубина стружечной канавки:
h = (035 06)t = (035 06)5= 175 3 мм;
с = (03 035)t = (03 035)5 = 15 175 мм;
Принимаем с = 16 мм;
R = (05 055)h = (05 055)3= 15 165 мм;
Рисунок 2.4 - Размеры стружечных канавок на режущей части протяжки
Диаметр первого зуба протяжки мм
Dz1 = Dпн = 25 мм; (2.13)
Диаметр последнего зуба режущей части протяжки мм;
где Dк –диаметр калибрующих зубьев протяжки мм;
Dк = (D + ) – p = (26 + 0067) – 0012 = 26055 мм;
р - величина разбивания отверстия; p= 0012 мм.
Диаметры промежуточных зубьев режущей части протяжки получают последовательным прибавлением к диаметру первого зуба удвоенного значения толщины срезаемого слоя.
Dz2 = Dz1 + 2·а (2.15)
Определение толщины срезаемого слоя
Фасонные протяжки срезают припуск заготовки как правило по генераторной схеме резания. Толщина срезаемого слоя (а) равна разности высот или полуразности диаметров пары смежных режущих зубьев. Ширина срезаемого слоя b равна длине главной режущей кромки зуба протяжки.
Режущая кромка первого зуба – окружность следовательно
Режущие кромки последующих зубьев - дуги концентрических окружностей поэтому ширина срезаемого слоя одним зубом равна сумме длин дуговых участков главной режущей кромки данного зуба т.е.
где b – длина одного дугового участка на режущей кромке данного зуба;
n – число дуговых участков на режущей кромке зуба.
Длина дуговых участков режущей кромки уменьшается при увеличении диаметра от d до D. Схема резания при протягивании зависит от площади срезаемого слоя
P= f(ab) поэтому для сохранения постоянной силы P за весь период протягивания отверстия пропорционально уменьшению b увеличивают толщину срезаемого слоя a.
Последовательность определения толщины срезаемого слоя:
а) определяем общий припуск под протягивание мм:
А = (D +)2-d2 = (26 + 0067)2 – 252 = 05335 мм; (2.18)
б) делить величину А на ступени не обязательно так как высота протягиваемых зубьев маленькая:
в) определим толщину срезаемого слоя а из условия прочности протяжки по впадине первого зуба:
а1 = (F1· []р (10·Cрb1·zк·кγ·кб))118 мм (2.19)
где F1- площадь сечения по впадине первого зуба протяжки мм2
Рисунок 2.5 – Генераторная схема резания для протяжки
F1= ·(Dz1-2h)24 = 314· (25 - 2·2)24 = 356185 мм2; (2.20)
[]р - допустимое напряжение при деформации растяжения в материале режущей части протяжки МПа.
b1 - длина режущей кромки первого зуба протяжки мм
b1 = ·Dz1 = 314·25 = 785 мм
zк - число зубьев протяжки участвующих одновременно в резании.
кб = 134 т.к. обработка без эмульсии;
а = (356185·400(10·212·785 ·3·093·134))118 = 017 мм;
Так как а=017 не оптимально (выше 02 не рекомендуется так как получается низкое качество поверхности) то принимаем а=01. Это повысит качество протягиваемого отверстия и предельно допустимую прочность первого зуба.
г) проверим возможность размещения стружки в канавке между зубьями при срезании протяжкой максимальной толщины срезаемого слоя аi max .
где Kc-коэффициент заполнения стружечной канавки Kc = 3;
Условие выполняется.
Проверим прочность протяжки на разрыв по шейке хвостовика.
где P- сила резания при протягивании Н
P = 10·Cр·а085b·zк·кγ·к0 (2.23)
P = 10·212·01085·785·3·093·134 = 08105 H;
Fx = ·( D1')24 (2.24)
где D1'- диаметр вала хвостовика мм
Для стали 40X ГОСТ - []
Условие не выполняется изготавливаем цельную протяжку из материала сталь Р6М5 []x = 400 МПа
Проверка протяжки по тяговой силе протяжного станка.
Q = Р09 = 0810509 = 889 кН
где Q - номинальная тяговая сила протяжного станка.
Выбрали: модель станка 7Б55 с максимальной длиной рабочего хода каретки 1250 мм и номинальной тяговой силой Q = 100 кН.
Калибрующая часть протяжки состоит из пяти зубьев одинакового диаметра равного диаметру последнего режущего зуба. Стружечные канавки имеют такую же форму и размеры как и на режущей части протяжки. Шаг калибрующих зубьев принимают равным шагу режущих зубьев.
Вершину калибрующих зубьев снабжают фаской 02 06 мм которая предназначена для сохранения диаметральных размеров протяжки при переточках.
Передний угол γк принимают равным γ так как при эксплуатации протяжки в результате переточек затупившихся зубьев происходит постепенный переход калибрующих зубьев в режущие.
Задний угол имеет небольшую величину αк =130 ±15 по сравнению с режущими зубьями. Это вызвано необходимостью обеспечить медленное уменьшение диаметральных размеров зубьев при переточках.
Заднюю направляющую часть у фасонных протяжек выполняют цилиндрической. Диаметр задней направляющей части мм:
где d –минимальный диаметр отверстия под протягивание мм
Dзн = 25 мм предельное отклонение по f7.
Длину задней направляющей части принимаем Lзн = 20 мм.
Предельное отклонение диаметра зуба по ГОСТ 164992-70 равно –0.02 мм.
Таблица 2.24 - Режущие зубья протяжки
Таблица 2.25 - Калибрующие зубья протяжки
Рисунок 2.6 – Режущий и калибрующий зубья протяжки
4 Проектирование приспособления для очистки протяжек от стружки
Для механического удаления стружки разработано автоматически действующее приспособление которое может быть использовано как на вертикальных так и на горизонтальных станках при протягивании отверстий различной формы. Приспособление применено на вертикально-протяжном станке 3М634 используемом на проектируемом участке.
Приспособление устроено следующим образом. Цилиндр 12 и кронштейн 5 винтами 10 и 11 крепят на столе станка. Шток цилиндра соединён тягой 8 с рычагом 6 при помощи муфты 7. Рычаг 6 жёстко соединён с диском 2 расположенным в корпусе 1. Диск имеет 6 спиралеобразных пазов в которые входят пальцы 9 подвижных кареток 3. На каждой подвижной каретке закреплены щётки 4 из стальной проволоки диаметром 05мм. В корпусе 1 имеются пазы по которым перемещаются подвижные каретки 3. При движении протяжки вниз во время рабочего хода масло приступает в правую полость цилиндра. Поршень перемещаясь влево поворачивает рычаг 6 и диск против часовой стрелки. При помощи пазов и диска 2 подвижные каретки 3 разводятся и протяжка свободно проходит в патрон рабочей каретки. При движении протяжки вверх во время обратного хода каретки станка масло поступает в левую полость цилиндра. Поршень перемещается вправо а рычаг 6 и диск 2 поворачиваются по часовой стрелке. Подвижные каретки 3 подводятся к центру устройства так что диаметр отверстия образуемого щётками получается на 2-3мм меньше диаметра протяжки.
Технико-организационная часть
Обеспечением инструментом оборудования занимается ИРК. ИРК предназначена для своевременного обеспечения участков цеха настроенным инструментом. Сюда входит секция хранения и комплектации инструмента секция доставки инструмента к рабочим местам. В секции хранения и комплектации инструмента производится получение инструмента из центрального инструментального склада и раскладка его по стеллажам а также поддержание оборотного фонда и подачи инструмента карт наладки в секцию инструмента. Получив из зоны сборки и настройки готовый настроенный инструмент комплектовщик отправляет его в зону доставки к рабочим местам. Доставка осуществляется поштучно блоками и комплектами целыми инструментальными магазинами в зависимости от вида оборудования. Доставляется и возвращается инструмент к оборудованию:
транспортными рабочими;
внутрицеховым транспортом;
Заточка инструмента производится в заточном отделении которое организовывается в цехе. Так как количество станков 150 300.
Существуют следующие способы замены режущего инструмента.
Замена инструмента по отказам т.е. замена инструмента производится по мере выхода его из строя.
Смешанная замена т.е. каждый заменяют принудительно через определенный промежуток времени а инструмент вышедший из строя раньше этого периода заменяют по отказу.
Смешанно-групповая замена т.е. инструменты имеющие одинаковые среднюю стойкость и закон ее распределения заменяют одновременно по мере достижения ими определенного периода времени независимо от времени работы каждого инструмента.
При смешанном и смешанно-групповом способах замены режущих инструментов в производстве применяют принудительное восстановление инструментов.
При числе станков в цехе более 100 200 организуется мастерская по ремонту инструментальной и технологической оснастки. В мастерской по ремонту оснастки выполняют малый ремонт приспособлений и другой оснастки.
Уход и надзор за действующим оборудованием планово-предупредительный ремонт технических средств всех видов а также модернизацию существующего и изготовление нестандартного выполняет ремонтно-механический цех завода а также цеховые ремонтные базы и отделения по ремонту электрооборудования и электронных систем. Ремонтные базы цеха производят малые и средние ремонты а ремонтно-механический цех – капитальный ремонт оборудования. Для периодического осмотра и ремонта электродвигателей вентиляционных систем цеха устройств электроавтоматики и электронных систем предназначено отделение по ремонту электрооборудования и электронных систем.
Произведем расчет количества получаемой стружки:
где m – удельная масса стружки приходящаяся на 1 м2 площади участка;
S – площадь участка по изготовлению детали.
Так как удельная масса стружки меньше допустимой [m]=300 кгм2 то удаление стружки производится без комплексно-автоматизированной системой линейных и магистральных конвейеров. Стружка собирается в специальные контейнеры затем отправляется на утилизацию.
СОЖ передают по трубопроводам из центральной установки к разборным кранам установленным на участках. В процессе работы станка используется автономная система охлаждения станка которая ежесуточно пополняется из разборных кранов для восполнения потерь жидкости вследствие ее разбрызгивания уноса со стружкой и обработанной заготовкой.
Предприятия обеспечиваются электроэнергией от линий электропередач напряжением 110кВ. Для понижения напряжения используют следующий каскад: открытая понижающая станция 11035 кВ затем открытые центральные распределительные подстанции 3510-6кВ и цеховые закрытые трансформаторные подстанции 6-100.4кВ. Подстанции приближают к основным потребителям электроэнергии для уменьшения потерь в сети.
При производстве вала широко используют сжатый воздух для приводов пневматических зажимных устройств. Давление сжатого воздуха в сети составляет 05 06 МПа. Компрессорные станции размещены в изолированном помещении вследствие высокого уровня создаваемого ими шума.
Расчет технико-экономических показателей обработки детали
1 Определение исходных данных для расчета технико-экономических показателей обработки детали
Для расчета экономической эффективности вариантов технологического процесса прежде всего необходимо заполнить приведенную ниже таблицу исходных данных.
Таблица 4.1 – Исходные данные для выполнения экономического раздела дипломного проекта базовый вариант ротора
Штучное время на выполнение операции мин
Трудоемкость программы выпуска час
Количество оборудования
Коэффициент загрузки оборудования
Годовая программа выпуска 30 000 штук.
Масса заготовки 0187 кг.
Масса детали 0045 кг.
Производственная площадь участка 95 м2.
Таблица 4.2 – Исходные данные для выполнения экономического раздела дипломного проекта проектируемый вариант
Масса заготовки 009 кг.
Производственная площадь участка 64 м2.
2 Определение потребности в материально-технических и трудовых ресурсах
Состав оборудования и дорогостоящей оснастки сведем в 2 таблицы по вариантам базовому и проектируемому.
Таблица 4.3 - Состав оборудования и оснастки (базовый вариант)
Модель оборудова-ния
Количество на программу шт.
Коэффи-циент загрузки оборудо-вания
Стоимость единицы оборудова-ния в тыс. руб.
Мощ-ность приво-дов кВт
Таблица 4.4 - Состав оборудования и оснастки (проектируемый вариант)
Количество основных материалов на годовую программу рассчитывается по нормам расхода qз материалов:
Мосн = qз. Nзапгод (4.1)
где qз - масса заготовки кг;
Nзапгод –годовая программа выпуска Nзапгод = 30 000шт.
где QП – количество единиц оборудования на участке шт.
Мосн =0187×30000= 5610 кг.
Мвсп =01875×8= 15 кг.
Итого: М = 56415 кг.
Проектируемый вариант:
Мосн = 009×30000 = 2700 кг.
Мвсп =009×8= 07 кг.
Итого: М = 27007 кг.
Количество производственных рабочих (кроме производственных рабочих автоматических линий и наладчиков-операторов оборудования) определяется по формуле:
где Чр —расчетное количество производственных рабочих;
Тст—трудоемкость механической обработки на годовую программу станко-ч;
Фр – эффективный годовой фонд времени рабочего ч.; Фр = 1860 ч.
Расчеты сведем в таблицы 4.5 и 4.6.
Таблица 4.5 - Количество работающих (базовый вариант)
Таблица 4.6 - Количество работающих (проектируемый вариант)
Число производственных рабочих в первой смене принимаем 50% от общего количества производственных рабочих.
Предусматриваем наличие следующих вспомогательных рабочих и служащих:
вспомогательные рабочие: 1 наладчик по токарным станкам; 1 наладчик по фрезерным станкам 1 слесарь-механик 1 слесарь-электрик 1 слесарь по общему ремонту 1 смазчик; 1 кладовщик-приемщик и 1 рабочий по доставке инструментов и приспособлений на рабочие места.
Инженерно-технические работники: 1 мастер и 1 технолог.
Число вспомогательных рабочих в первой смене принимаем 55% от общего количества вспомогательных рабочих.
Число уборщиц конторских помещений принимаем 1 человек.
3 Расчет технико-экономических показателей
Расчет капитальных вложений рассчитываем по следующей формуле:
К = Коб+Кзд+Косн+Кинв+ОбС (4.4)
где Коб – капиталовложения в оборудование (техническое энергетическое подъемно-транспортное средства контроля и управления) млн. руб.;
Кзд – капиталовложения в здание млн. руб.;
Косн – капиталовложения в дорогостоящую оснастку (приспособления штампы модели режущий и мерительный инструмент и тому подобное) млн. руб.;
Кинв – капиталовложения в инвентарь млн. руб.;
ОбС – капиталовложения в запасы материалов (оборотные средства) млн. руб.
Капиталовложения в оборудование:
Коб = ЦБi·Оi·i (4.5)
i – коэффициент занятости.
где Тгод – трудоемкость программы выпуска рассматриваемой продукции чгод;
Тобщ – объем работ по изготовлению всей закрепленной за данным оборудованием продукции чгод.
Результаты оформим в виде таблицы.
Таблица 4.7 – Капиталовложения в оборудование(базовый вариант).
Коэффициент занятости i
Капиталовложения в оборудование Коб
Таблица 4.8 – Капиталовложения в оборудование (проектируемый вариант).
Капиталовложения в здание определяются следующим образом:
Кзд = (Sц+Sтс) ×mср×Цзд (4.7)
где Sц – производственная площадь занимаемая участком цехом м2 ;
Цзд - стоимость 1 м2 площади механического цеха. Цзд=170 т.р.;
ms - коэффициент занятости площади при изготовлении рассматриваемой продукции.
Кздб = 95×170×017 = 27455 т.р.;
Кздп = 64×170×014 = 15232 т.р.
В механических цехах в первом приближении вложения в оснастку принимаются в долях от стоимости станочного оборудования.
Коснб = 007×36461=25523 т.р.;
Коснпр = 007×25109=17576 т.р.
Капиталовложения в запасы материалов охватывают вложения в запасы основных комплектующих изделий и рассчитываются следующим образом:
где w - число видов материалов необходимых для производства продукции;
Мосн с - потребное количество материалов с-го вида на объем выпуска продукции Мосн с = 27 т;
Дп - длительность рассматриваемого периода дн;
Цм с - оптовая цена материала с-го вида рубт; (рубшт): по соответствующим прейскурантам;
Ктз с - коэффициент учитывающий транспортно-заготовительные расходы по приобретению материалов с-го вида; коэффициент Ктз с может быть принят в первом приближении равным 104 - 108 для основных материалов (заготовок) и 108 - 110 для вспомогательных материалов.
Доб - длительность одного оборота оборотных средств дн.
Доб = Stшт i ·k (60 · 24) + Тз (4.10)
где tшт - штучное время выполнения операций технологического процесса мин;
k - коэффициент учитывающий длительность операций связанных с перемещением маркировкой оформлением документов и др. (k = 15 – 25);
Тз - количество дней на которое создается текущий страховой транспортный запасы принимается в зависимости от частоты поставок материалов дн (Тз = 5-30 дн).
Определим длительность одного оборота оборотных средств и капиталовложения в запасы материалов для базового варианта:
ОбС=561·15·106·1460260=50088 т.р.
Найдем те же величины и для проектируемого варианта:
ОбС=27·15·106·1460260=24107 т.р.
В первом приближении вложения в производственный инвентарь определяются по следующим укрупненным показателям: 1 - 2% от стоимости основного оборудования.
Кинв = Коб×15% (4.11)
Кинвб = 0015× 3211 = 482 т.р.;
Кинвпр = 0015×1704 = 256 т.р.
Рассчитанные величины сведем в таблицу 4.7.
Таблица 4.7 - Состав капитальных вложений
Проектируе мый вариант
Капиталовложения в оборудование
Капиталовложения в здание
Капиталовложения в оснастку
Капиталовложения в запасы материалов (оборотные средства)
Капиталовложения в инвентарь
Капиталовложения – всего
Произведем расчет себестоимости продукции.
Затраты на материалы:
где w – число видов материалов применяемых при изготовлении изделия;
Мс – потребности в материале с-го вида т;
Цмс – оптовая цена на материал с-го вида с учетом транспортно-заготовительных расходов млн. рубт;
Мотх.с – реализуемые отходы материалов с-го вида т;
Цотх.с – цена отходов материала млн. рубт.
С= 561·1460-426·292 = 81147млн. руб.
С=271460-135292=35478 млн. руб
Основная заработная плата рабочих:
С= (С+С)·kот·kм (4.13)
где С С – прямой фонд заработной платы рабочих-сдельщиков и рабочих-повременщиков млн. руб.;
kот=12 – отраслевой коэффициент
kм=10-16 – коэффициент доплат за многостаночное обслуживание.
Прямой фонд заработной платы рабочих-сдельщиков:
С= Тгод·Сз сч (4.14)
где Тгод – суммарная трудоемкость изготовления продукции за год чел·ч;
Сз сч – средняя часовая тарифная ставка заработной платы в цехе (на участке) рубч.
Прямой фонд заработной платы рабочих-повременщиков:
С= nФэр· Сз сч ·кзан (4.15)
где n–потребное количество рабочих-повременщиков чел.;
Фэр – эффективный фонд времени рабочего ч.
кзан– коэффициент занятости работника выпуском рассматриваемой продукции.
Среднечасовая тарифная ставка рассчитывается как средневзвешенная величина:
где n n n – количество рабочих соответствующих разрядов чел.;
С С С – тарифные часовые ставки этих рабочих руб.
СБ = 4·1820·68085 = 49 млн. руб.;
СПР =4·1820·68085 = 49 млн. руб.
Основная и дополнительная зарплата повременщиков:
СБ = 47953·12·2763 = 16 млн. руб.;
СПР =47953·12·3520 = 2 млн. руб
Дополнительная заработная плата сдельщиков:
Дополнительная заработная плата рабочих:
где k - коэффициент учитывающий дополнительную плату с учетом премиальных выплат (принимается 10-50%).
Отчисления на социальное страхование с заработной платы рабочих:
С= (С+ С)·kсс100 (4.18)
где kсс – коэффициент учитывающий отчисления на социальное страхование.
Вспомогательные рабочие:
СБ = 76 ·035 = 266 млн. руб.;
СПР = 76 ·035 =266 млн. руб.
СБ = 048 ·035 = 017 млн. руб.;
СПР = 06 ·035 =021 млн. руб.
Годовой фонд заработной платы ИТР и служащих с отчислением на соцстрах находящихся на штатно-окладной системе:
С= С= пи·Зм· k (4.3.16)
где пи – количество работающих определенной специальности чел.;
Зм – месячный оклад работающего определенной специальности рубмес;
Кзан – коэффициент занятости.
С Б = (1·350000+1·290000+1200000) ·12·135 = 136 млн. руб.;
С ПР = (1·350000+1·290000+1200000) ·12·135 = 136 млн. руб.
Затраты на амортизацию оборудования транспортных средств и дорогостоящей оснастки:
где h – количество моделей оборудования;
На – норма годовых амортизационных отчислений на замену оборудования
- значение коэффициента занятости оборудования i-го вида изготовлением рассматриваемой продукции.
А= (1·15·01+1·6941·017)·+ (1·142·006+1·06·006+1·2572·017+
+1·2976·009+1·3334·09+1·1636·005)· = 028 млн. руб.
А= (1·0788·003+1·6301·026+1·1454·006+1·1274·007
+1·1484·006+1·1758·007+1·6059·025+1·0916·006)· = 03 млн. руб.;
Затраты на ремонт оборудования:
Ср= (3-10)%·Коб (4.21)
С = 008·3211=0 26млн. руб.;
С = 008·1704= 014млн. руб.
Сэ=Стэ+Ссж+Спар+Стоп (4.22)
где Стэ - затраты на силовую и технологическую электроэнергию;
Ссж - затраты на сжатый воздух;
Спар - затраты на пар;
Стоп - затраты на топливо.
Стэ = Мэi·Fдi·kод·kп·Цэ (4.23)
kод – коэффициент спроса электроэнергии 103-107;
kп – коэффициент учитывающий потери в сети 103-107;
Цэ – цена 1 кВт·ч электроэнергии руб кВт·ч.
СтэБ =105105190(10400+20671+15240+75250+10288
+15352+15377+15185)= 83 млн.руб.
СтэПР =105105190(10130+101075+10240+10280+10245+10300
+751000+75250) = 94 млн.руб.
Ссж = Нсж·Fд· kп·Цсж (4.24)
где Нсж – среднечасовая норма расхода сжатого воздуха на один станок (1 3 м3час);
Fд – действительный суммарный фонд времени работы оборудования использующего сжатый воздухч;
kп – коэффициент учитывающий потери сжатого воздуха 15;
Цсж – цена 1 м3·сжатого воздуха рубм3.
СсжБ = 3·2763· 15 · 20 =027 млн. руб.
СсжПР = 3·3520· 15 · 20 = 032 млн. руб.
Спар = Цп·(Нр.пар·Рпод+Рсущ)·Мс (4.25)
где Цп – цена 1 тонны·пара рубм3.
Нр.пар – норма расхода воды в моечной машине (035 м3т);
Рпод – расход пара на подогрев 1 м3 воды (016 019 тт)
Рсущ – расход пара на сушку 1 тонны деталей (01 тт);
Мс – годовой объем выпуска продукции т.
Сэб = 83+027+0+0=857 млн. руб.;
Сэпр = 94 +032+0+0=972 млн. руб.
Затраты на воду складываются из:
- затраты на промывку деталей;
- затраты на приготовление СОЖ;
- затраты на охлаждение оборудования;
- затраты на бытовые нужды.
Затраты на промывку деталей равны:
Свп = Нр.вод·Мс·Цв.п (4.26)
где Нр.вод – расход воды на производственные нужды в моечной машине (35 м3т);
Цв.п – стоимость 1 м3 воды на производственные нужды рубм3.
Свп = 35·135·260=0001 млн.руб.
Затраты на приготовление СОЖ (Ссож) и охлаждение оборудования (Сохл) принимаем соответственно в размере 5% и 3% от затрат воды для промывки деталей.
Ссож=005·0001= 000005 тыс. руб
Сохл=003·0001= 000003 тыс. руб
Затраты на воду для бытовых нужд:
Св.б=Нв.б·кзан·п·Цв.б (4.27)
где Нв.б – норма расхода воды на одного работающего в смену (006 м3);
Цв.б – стоимость 1 м3 воды для бытовых нужд рубм3;
п - количество работающих чел;
кзан – коэффициент занятости работника выпуском рассматриваемой продукции.
С = 006·07·14·260·151= 0023 млн руб.;
С = 006·07·14·260·151= 0023 млн руб.
Затраты на смазочно-обтирочные (вспомогательные) материалы для оборудования:
Св = Оi·Нр.в.м (4.28)
где Нр.в.м – средняя величина затрат на смазочно-обтирочные материалы за год в расчете на единицу оборудования i-го вида (рубгод)ед.об.
Оi – количество принятого производственного оборудования i-го вида шт.
С = 25000·8= 02 млн. руб.;
С = 25000·8= 02 млн. руб.
Затраты по приспособлениям режущему и мерительному инструментам и прочей оснастке:
Синстр.= 18%·Косн (4.29)
С= 018·255= 046 млн. руб.;
С= 018·175= 03 млн. руб.
Затраты на содержание помещений охватывают расходы на ремонт отопление освещение и уборку.
Ссод. зд.= Sц·Рм2 (4.30)
где Sц – производственная площадь занимаемая участком м2;
Рм2 - среднегодовые расходы на содержание помещений приходящихся на 1м2 площади рубгод м2.
Для механического цеха расходы на содержание помещений можно принять 15-232% от его стоимости.
Ссод. здб= 002·32215 = 064 млн. руб
Ссод. здпр= 002·162911 = 033 млн. руб
Затраты на текущий ремонт зданий (Ср.зд) и инвентаря (Ср.зд.) составляют 05-1% от их первоначальной стоимости с учетом коэффициента использования.
Ср.зд б= 0007·32215·05 = 011 млн. руб;
Ср.зд б= 0007·162911·037 = 004 млн. руб.
Затраты на амортизацию зданий и инвентаря:
Аздб = 0012·32215·05 = 019 млн. руб;
Аздпр = 0012·162911·037 =007 млн. руб.
Расходы на испытания опыты исследования рационализацию и изобретательство принимаем как и в базовом варианте 15 млн. руб. в год на одного работающего.
Расходы на охрану труда:
Сохр.тр.= 5%· С (4.31)
С= 005·35 = 0175 млн. руб.;
С= 005·35 = 0175 млн. руб.
Затраты на малоценный и быстроизнашивающийся инвентарь принимаем как и в базовом варианте 034 млн. руб в год на одного работающего.
Смби.=034· ЧР · (4.32)
Смби.=034· 8 ·079= 215 млн. руб.;
Смби.=034· 8 ·086= 234 млн. руб.
На основании произведенных расчетов заполняем таблицы 4.10 – 4.12.
Таблица 4.10 – Смета расходов на содержание и эксплуатацию оборудования.
Наименование статей расходов
Проектируемый вариант
Амортизация оборудования транспортных средств ценного инструмента и приспособлений
Затраты на эксплуатацию оборудования:
- стоимость вспомогательных материалов;
- основная и дополнительная зарплата вспомогательных рабочих с отчислениями на соцстрах;
- затраты на энергию для технологических целей;
- затраты по приспособлениям режущему и мерительному инструментам и прочей оснастке.
Затраты на текущий ремонт оборудования и транспортных средств
Таблица 4.11 – Смета цеховых расходов млн. руб.
Содержание аппарата управления цехом участком (зарплата ИТР)
Текущий ремонт зданий
Испытания опыты и исследования рационализация и изобретательство
Прочие расходы (3% от суммы затрат пунктов 1-6)
Таблица 4.12 – Калькуляция цеховой себестоимости продукции млн. руб.
Стоимость основных материалов за вычетом возвратных отходов
Основная заработная плата производственных рабочих
Дополнительная заработная плата производственных рабочих
Налоги и отчисления в бюджет и внебюджетные фонды с зарплаты производственных рабочих
Расходы на содержание и эксплуатацию оборудования
4 Оценка экономической эффективности варианта технологического процесса
Общая экономическая эффективность проекта оценивается показателем (коэффициентом) характеризующим величину прироста чистой прибыли предприятия на каждый рубль необходимых для получения этой прибыли капиталовложений:
где Пч – чистая прибыль предприятия от реализации годового объема производственных изделий млн. руб.;
К – капиталовложения необходимые для производства годового объема изделий млн. руб.
Как следует из формулы (4.4.1) для определения коэффициента общей экономической эффективности надо знать размер чистой прибыли которая определяет цель деятельности предприятия по выпуску продукции.
Пч = Q-(С+Ннед+Нпр) (4.34)
где Q – годовой объем выпуска продукции в стоимостном выражении млн. руб.
где С – себестоимость годового выпуска продукции млн. руб.;
Пб – балансовая прибыль по выпускаемой продукции млн. руб.
где R – реальная или введенная норма рентабельности базового проекта %.
Ннед – сумма налога на недвижимость млн. руб.:
Ннед = (Коб+Кзд) · (4.37)
где Тнед – ставка налога на недвижимость %.
Нпр – сумма налога на прибыль млн. руб.:
Коб Кзд – капиталовложения в оборудование и здания млн. руб.:
Сумма налога на прибыль:
где П – прибыль предприятия облагаемая налогом на прибыль млн. руб.;
Тпр – ставка налога на прибыль %.
Подставив численные значения в формулы получим:
Пб Б = 5285· = 1057 млн. руб.;
Q= Q=5285+1057 = 6342 млн. руб.;
Пб ПР= 6342-4878= 1464 млн. руб.
Н= (3211+27455) · = 006 млн. руб.;
Н= (1704+15232) · = 0032млн. руб.
ПБ = 1057 - 006 = 1051 млн. руб.;
ППР = 1464 - 0032 = 1462 млн. руб.
Н= 1051 · = 252 млн. руб.;
Н= 1462· = 35 млн. руб.
Пч Б = 6342 -(5285+006 +252) =8 млн. руб.;
Пч ПР = 6342-(4878+0032 +35) = 111 млн. руб.
Важнейшими показателями сравнительной экономической эффективности по которым оценивается предпочтительность того или иного варианта проекта являются приведенные суммарные затраты Зпр по каждому рассматриваемому варианту годовой экономический эффект Эг и срок окупаемости дополнительных капиталовложений Т.
Эг = (СБ-СПР)-Ен·(КПР-КБ) (4.41)
где Ен – нормативный коэффициент сравнительной экономической эффективности принимается равным процентной ставке за пользование долгосрочным кредитом.
- разность капиталовложений
- разность себестоимостей продукции.
З= 5285+015·109677= 545 млн. руб.;
З= 4878+015·74212= 4989 млн. руб.
Эг = (5285-4878)-015·(109677-74212) = 37 млн. руб.
5 Основные технико-экономические показатели проекта
Таблица 4.13 – Основные технико-экономические показатели проекта.
Наименование показателя
Годовой выпуск продукции:
- в натуральном выражении
-в стоимостном выражении по цене базового предприятия
Общая стоимость основных производственных фондов всего
Производственная площадь цеха (участка)
Численность рабочих всего
- Основных производственных рабочих
- Вспомогательных рабочих
Трудоемкость изготовления единицы продукции
- в стоимостном выражении
Фондовооруженность труда
Средняя загрузка оборудования
Цеховая стоимость годового объема выпуска продукции
Размер чистой прибыли
Рентабельность продукции
Абсолютная (общая) эффективность капиталовложений
Годовой экономический эффект
Охрана труда и окружающей среды
1 Задачи в области охраны труда
Правила по технике безопасности содержат требования технического характера направленные на защиту работающих от воздействия предметов и средств труда безопасную работу машин оборудования и инструментов снабжение станков и машин конструктивными ограждениями предохранительными приспособлениями и др.
В ГОСТ 12.0.002-80 техника безопасности определена как система организационных мероприятий предотвращающих воздействие на рабочих опасных производственных факторов а производственная санитария – как система организационных технических средств предотвращающих или уменьшающих воздействие на работающих вредных производственных факторов.
Нормы по производственной санитарии и гигиене труда определяют устройство производственных и бытовых помещений рабочих мест в соответствии с физиологией и гигиеной труда а также безопасные пределы содержания в воздухе производственных помещений пыли газов паров и др.
Улучшение условий труда повышение его безопасности и безвредности имеет большое экономическое значение. Оно влияет на экономические результаты производства на производительность труда качество и себестоимость выпускаемой продукции.
Производительность труда повышается благодаря сохранению здоровья и работоспособности человека экономии живого труда путем повышения уровня использования рабочего времени продление периода активной трудовой деятельности человека уменьшение числа аварий и т.п.
Существенное влияние на работоспособность рабочих оказывает освещение производственного участка. Для освещения используются люминесцентные лампы ЛСП. Для местного освещения используют лампы накаливания с йодным циклом. Срок службы таких ламп больше чем у простых ламп накаливания.
Оптимальными условиями для работы в производственных помещениях являются: температура воздуха 18°-20°С скорость движения воздуха в зимнее время года—02-05 мс в летнее—02-10 мс относительная влажность—65%.
2 Техника безопасности и производственная санитария
2.1 Обоснование размеров производственных помещений
Объемно-планировочные и конструктивные решения производственных зданий и сооружений должны приниматься с учетом требований соответствующих СНиП норм технологического проектирования.
Объем производственных помещений на одного работающего должен составлять не менее 15м3 а площадь помещений не менее 45 м2. Высота от пола до низа несущих конструкций должна быть кратна 06 м но не менее 3 м. Высота пролетов зависит от высоты устанавливаемого оборудования массы и габаритных размеров обрабатываемых деталей условий их транспортировки. Принимаем высоту 10 м. Высота здания 12 м. Сетка колонн здания 24x12 м. Шаг колонн 6 м. Площадь проектируемого производственного участка составляет 64 м2.
Планировка оборудования на участке выбрана с учетом грузопотоков и людских потоков на участке. Восемь станков на участке проставлены по технологическому процессу. Многооперационное обслуживание отсутствует. Перемещение заготовок осуществляется на карах. Уборка стружки осуществляется конвейером. Для ремонта и обслуживания станков предусмотрено расстояние в 700 мм. Опасные зоны станков оснащены защитными щитками или ограждениями.
Для тушения пожаров которые могут возникнуть на участке установлено противопожарное оборудование: пожарный щит пожарный кран. Для тушения электрооборудования используются порошковые и углекислотные огнетушители. При пожаре рабочие должны выйти на магистральные проезды и по ним двигаться на выход.
Проходы проезды выделяются отличающейся краской. Проходы шириной 1 м проезды имеют ширину 55 м. Все двери в производственных цехах открываются наружу.
Потребность воды для бытовых целей определяется по нормам:
- для питья 25 л в смену на одного работающего.
Установлен питьевой фонтанчик недалеко от участка.
Вспомогательные помещения размещаются на пути следования рабочих от входов на предприятие к местам работы.
Вспомогательные помещения располагаются в производственных зданиях путем устройства планировочных вставок шириной 12 м. В помещениях с постоянными рабочими местами предусмотрено естественное освещение в остальных - искусственное освещение.
2.2 Санитарно-гигиенические требования в рабочей зоне
Очистка воздуха перед выбросом в атмосферу проходит двух ступенчато. Поскольку металлическая пыль может быть крупной (больше 10 мкм) необходимо отделить от мелкой – первая степень очистки для этого применяем циклоны – действие основано на принципе центробежной сепарации. Степень очистки до 90 %. Очищенный в циклоне воздух подаётся в ячейковые фильтры представляющие собой каркасы с фильтрующими элементами выполненными из набора металлических сеток. Степень очистки до 80 %. Концентрация в пределах 3-5 мгм3 марка фильтра ФИАП.
Для очистки воздуха от паров и щелочи используем волоконные и сетчатые туманоуловители. Принцип действия основан на осаждении капель смачивающей жидкости поверхности пор с последующим стеканием жидкости под действием силы тяжести.
Воздухообмен при естественной вентиляции осуществляется за счёт разности температур (плотностей) воздуха в помещении и наружного воздуха (тепловой напор) или в результате действия ветра (ветровой напор). Наиболее распространённым видом естественной вентиляции является аэрация – организованная общеобменная вентиляция которая реализуется в холодных цехах за счёт ветрового напора а в горячих – за счёт совместного действия теплового и ветрового напоров.
Воздух поступает из зоны I – II за счёт разряжения существующего ниже плоскости равных давлений в места с наименьшим выделением вредных веществ влаги тепла (на высоте 12 15 м. над полом) и удаляется из наиболее загрязнённых зон III за счёт избыточного давления которое существует выше плоскости равных давлений I.
Рисунок 5.1 - Схема аэрации здания цеха.
Такая естественная вентиляция наиболее простая экономична но имеет ряд недостатков: она применима только в помещениях в которых нет больших выделений вредных веществ воздух поступает неочищенный от пыли и других примесей а в холодное время года происходит расход большого количества тепла и рост числа простудных заболеваний работающих.
Поэтому цех имеет механическую приточную вентиляцию позволяющую подавать в цех очищенный подогретый воздух и вытяжную вентиляцию поддерживающую надёжный воздухообмен.
Местная вентиляция предназначена для удаления вредных веществ или избытка теплоты непосредственно из зоны выделения она препятствует их распространению по всему объёму производственного помещения. В соответствии со СНиП 2.04.05 – 84 расчет потребного воздухообмена при всеобменной вентиляции проводится в зависимости от количества работающих наличия в воздухе рабочей зоны вредных веществ избытков теплоты и влаги.
Защита тела человека обеспечивается применением спецодежды спецобуви головных уборов рукавиц. Органы зрения защищаются очками как от механических повреждений (стружка окалина пыль и т.п.) так и от действия токсических веществ инфракрасного и ультрафиолетового излучения слепящей яркости видимого света.
2.3 Естественное освещение
Естественное освещение - это освещение помещений светом неба (прямым или отраженным) проникающим через световые проемы в ограждающих конструкциях. Подразделяется на боковое - через проемы в стенах верхнее - через светоаэрационные фонари световые проемы в перекрытии а также через проемы в местах перепада высот здания и комбинированное – сочетание верхнего и бокового.
Помещения с постоянным пребыванием людей должны иметь естественное освещение.
При верхнем или верхнем и боковом естественном освещении нормируется среднее значение коэффициентов естественного освещения (КЕО). Значения КЕО установленные в СНБ 2.04.05-98 приведены в таблице 5.2.
Производственное помещение где расположен проектируемый участок в соответствии со СНБ 2.04.05-98 по задачам зрительной работы относится к 1-ой группе. Выполняемые работы соответствуют 3-му разряду зрительной работы. Нормированное значение КЕО для данного производства верхнее и комбинированное освещение 5% боковое 20%.
2.4 Искусственное освещение
Искусственное освещение согласно СНБ 2.04.05-98 подразделяется на рабочие аварийное эвакуационное и охранное.
Искусственное освещение по способу размещения источников света подразделяется на общее (равномерное или локализированное) местное и комбинированное (к общему освещению добавляется местное).
В осветительных установках производственных помещений применяем лампы накаливания и газоразрядные лампы низкого и высокого давления - люминесцентные металлогалогенные натриевые и ксеноновые.
Местное освещение рабочих мест предусмотрено конструкцией оборудования.
2.5 Техника безопасности при работе на оборудовании
В разработанном технологическом процессе изготовления детали используется следующее оборудование: токарные станки с ЧПУ вертикально-сверлильные станки вертикально-фрезерные станки шлифовальный станок вертикально-протяжной станок.
Требования безопасности перед началом работы:
-привести в порядок рабочую одежду застегнуть или подвернуть обшлага рукавов надеть головной убор;
-принять рабочее место от сменщика: проверить хорошо ли убран станок от стружки; ознакомиться с имеющимися в предыдущей смене неполадками и с принятыми мерами их устранения;
-проверить наличие и исправность заземления ограждения и предохранительных устройств;
-разложить инструмент и приспособления в удобном для пользования порядке применять только исправный инструмент.
Требования безопасности при выполнении работы:
-перед каждым включением станка необходимо убедиться что пуск станка никому не угрожает опасностью;
-выполнять указания по обслуживанию и уходу за станком изложенные в руководстве по эксплуатации станка;
-работать только на станках к которым допущены и выполнять работу которая поручена администрацией цеха;
-постоянно контролировать исправность основного и вспомогательного оборудования;
-не оставлять на работающем оборудовании инструменты и другие вспомогательные материалы;
-удалять стружку с заготовки и станка только специальными крючками и щетками-сметками;
-запрещается работать на станке превышая его номинальную мощность;
-для защиты глаз применять защитный экран или надевать защитные очки;
-не переналаживать станок во время работы;
-запрещается работать на станке в рукавицах или перчатках а также с забинтованными пальцами без резиновых напальчников;
-при обработке деталей применять режимы резания указанные в операционной карте для данной детали и не увеличивать их без ведома мастера;
-содержать в чистоте рабочее место в течении рабочего дня и не загромождать его деталями заготовками и другими предметами;
-не разрешать уборщику убирать у станка во время его работы и не делать это самому.
Требования безопасности по окончанию работы:
-все подвижные узлы станка привести в исходное положение после этого выключить станок отключить электрооборудование вводным выключателем;
-привести в порядок свое рабочее место;
-убрать инструмент в отведенное для этой цели места при необходимости помыть его и отправить в заточное отделение;
-при сдаче смены сообщить сменщику или мастеру о замеченных дефектах станка и о принятых мерах по их устранению;
-о всякой замеченной опасности немедленно заявить администрации;
-вымыть лицо и руки теплой водой с мылом или принять душ.
2.6 Защита от шума и вибрации
Шум – совокупность звуков различной частоты и интенсивности нежелательных для человека.
Объективно действие шума проявляется в виде повышенного кровяного давления учащенного пульса и дыхания снижения остроты слуха и ослабления внимания. Субъективно действие шума может выражаться в виде головной боли головокружения бессонницы общей слабости. При значительном шуме снижается производительность труда возрастает частота несчастных случаев.
Борьба с шумом на производстве осуществляется по следующим направлениям:
-разработка шумобезопасной техники;
-применение средств и методов коллективной защиты;
-применение средств индивидуальной защиты.
Средства коллективной защиты от шума в зависимости от способа реализации подразделяются на:
-архитектурно-планировочные (размещение на генеральном плане предприятия цехов с избыточным выделением шума и внутрицеховом размещении оборудования);
-организационно-технические (своевременное обслуживание оборудования регулярные медосмотры работников);
-акустические (средства звукоизоляции и звукопоглощения);
-санитарно-гигиенические (комплекс медицинских и профилактических мероприятий).
Вибрация—колебательные движения материальной точки или механической системы.
Уменьшение вредного воздействия вибрации на работающего может происходить при выполнении следующих технологических мероприятий:
-снижение параметров вибрации в самом источнике (отстройка от режима резонанса балансировка своевременный ремонт);
-снижение параметров вибрации на путях ее перемещения от источника (виброгасящие фундаменты виброизоляция применение средств индивидуальной защиты).
Используем виброизоляцию как наиболее доступный и достаточно эффективный способом защиты рабочих мест. Этот способ защиты заключается в уменьшении передачи колебаний от источника возбуждений защищаемому объекту при помощи виброизоляторов помещаемых между ними.
Для уменьшения вибрации кожухов ограждений и других деталей выполняемых из стальных листов колебания которых происходит в резонансном режиме применяем виброгашение. Это достигается нанесением на вибрирующую поверхность материалов обладающих большим внутренним трением.
2.7Проектирование вытяжной вентиляции
Вентиляция - это организованный воздухообмен заключающийся в удалении из рабочего помещения загрязненного воздуха и подаче вместо него свежего наружного воздуха.
Обеспечение чистоты воздуха и заданных метеорологических условий производственного помещения в котором происходит технологический процесс обеспечиваем смешанной вентиляцией т.е. естественной и механической. Системами механической вентиляции оборудованы как цех так и непосредственно рабочие места.
Естественная вентиляция - это поступление и удаление воздуха происходящее через неплотности и поры наружных ограждений (инфильтрация) окна форточки дверные проемы ворота (аэрация проветривание). Открывая форточки и фрамуги в окнах и светоаэрационных фонарях с помощью механического привода периодически производим аэрацию. Приток воздуха в помещение предусматриваем в теплый период года на высоте не более 1.8 м от пола а в холодный - не ниже 4 м от пола чтобы обеспечить лучший воздухообмен и устранить возможность простудных заболеваний. Для улучшения отсоса воздуха из помещений при естественной вентиляции используем дефлекторы.
На участке обработки деталей « ротор » и « рукоятка » смонтирована приточно-вытяжная вентиляция. Воздухообмены рассчитаны на ассимиляцию теплоизбытков и разбавки вредностей выделяющихся от технологического оборудования.
Местная приточная вентиляция служит для создания требуемых условий воздушной среды в ограниченной зоне производственного помещения. Установка приточной вентиляции состоит из следующих элементов:
- воздухозаборного устройства расположенного снаружи здания в местах с минимальным содержанием вредных веществ; металлических воздуховодов по которым воздух подается в помещение; фильтров для очистки воздуха от пыли; калориферов; вентилятора; приточных отверстий или насадков; регулирующих устройств устанавливаемых на ответвлениях воздуховодов.
Приточный воздух очищается в рулонных фильтрах приточных камер. Воздух подается в различные зоны помещения по воздуховодам через распределительные насадки причем скорость выхода воздуха ограничена допустимым шумом и подвижностью воздуха на рабочем месте.
Применение местной вытяжной вентиляции основано на улавливании и удалении вредных веществ непосредственно у источника их образования. Она позволяет полностью устранить запыленность помещения. Воздух удаляемый местными отсосами - содержащий вредности (пыль пары и др.) перед выбросом в атмосферу очищается в пылеуловителях и фильтрах
При проектировании приточно-вытяжной системы вентиляции участка по производству вала необходимо сначала определить объем всего цеха.
Объем механического участка определим по формуле:
где Sуч – площадь проектируемого участка(цеха) м2;
Тогда объем всего цеха ориентировочно принимаем Vц = 2560 м3 считая что наш цех рассчитан на четыре подобные участка для совместного изготовления сектора крышки.
Норма скорости движения воздуха в рабочей зоне производственного цеха принимается по таблице VII.7 [14]: u = 01 03 мс.
Необходимый воздухообмен на 1 человека определим по формуле:
где G – интенсивность выделения вредных веществ 6000 мгч.;
С – теплоемкость воздуха 024 ккалкг;
qв – предельно допустимая содержание вредных веществ в вытягиваемом воздухе qв = 1200 мгм3;
qпр – предельно допустимая содержание вредных веществ в приточном воздухе qвр = 10 мгм3.
Для машиностроительных помещений величина воздухообмена L составляет 20 30 м3ч. Следовательно по таблице VII.8 [14] необходимый воздухообмен всего производственного цеха составит: L = 6200 м3ч.
Кратность воздухообмена составит:
Для машиностроительных помещений величина кратности воздухообмена К составляет около 11 15 м3ч.
Для полученных параметров процесса вентиляции принимаем центробежный вентилятор ЦЧ – 70 с характеристиками: Lв = 6500 м3ч. P = 44 кгсм2 n = 900 мин-1 в = 08.
Мощность электродвигателя для вентилятора:
где Lв – производительность вентилятора м3ч;
P – полное давление вентилятора кгсм2;
в – коэффициент полезного действия вентилятора;
п – коэффициент полезного действия привода вентилятора при плоскоременной передаче п = 09;
k – коэффициент запаса k = 105 15
Диаметр подводящего патрубка дефлектора:
где vп – скорость воздуха в патрубке дефлектора vп = 2 мс.
Принимаем стандартный диаметр трубы D = 06 м.
3 Защита населения в чрезвычайных ситуациях
На предприятии для производства продукции нередко используются различные взрывоопасные вещества к которым относятся разнообразные газы такие как кислород водород ацетилен кислоты жидкости для смазки и охлаждения и тому подобные вещества. Все они требуют очень внимательного подхода к реализации их хранения транспортировки и эксплуатации. Для этого на предприятии организуются различные службы задача которых заключается в контроле правильности хранения транспортировки и эксплуатации этих веществ. Но не всегда удается безопасно пользоваться взрывоопасными веществами и тогда на предприятиях в результате ошибки рабочего обслуживающего персонала либо ИТР а может и просто в следствие природных условий может произойти авария.
Каждому бедствию аварии присущи свои характерные особенности характер поражений объем и масштаб разрушений. В результате производственных аварий возможны пожары взрывы выбросы различных вредных веществ в атмосферу а как их следствие—повреждение и разрушения зданий сооружений оборудования техники а также и человеческие жертвы. Степень и характер разрушений зависит не только от мощности взрыва но и от состояния сооружений характера застройки расположения оборудования и его закрепления.
Причинами взрывов на машиностроительных предприятиях могут быть: ошибки в использовании углеводородных газов (пропан метан) котлов в котельных газовой аппаратуры; попадание масла в пневмосистему предприятия возгорание электропроводки вследствие перегрузки сети несоблюдение правил техники безопасности при хранении транспортировке и перемещении грузов неправильное использование подъемно-транспортных механизмов небрежное отношение к своим обязанностям рабочих МОП и многое другое.
При аварии очень важно предупредить и организовать эвакуацию персонала объекта а также предупредить проживающее в непосредственной близости население. Для этих целей на предприятии организовывается система оповещения. Производится эвакуация персонала из опасной зоны. После оповещения в первую очередь необходимо организовать спасательные работы обеспечить локализацию очага аварии произвести работы по устранению причин аварии для чего на предприятии организовываются специальные подразделения из производственных рабочих. Все работы ведутся с соблюдением требований техники безопасности. Также необходимо оказать первую медицинскую помощь пострадавшим и доставить их в лечебное учреждение.
После ликвидации чрезвычайной ситуации на предприятии создается специальная комиссия целью которой является выявление причин возникновения аварии а также принятие необходимых мер по предотвращению подобных случаев в дальнейшем.
4 Охрана окружающей среды
Забота об оздоровлении экологической обстановки создание более благоприятных с экономической точки зрения условий для жизни и деятельности людей становится одной из важнейших задач как мирового сообщества так и каждой отдельно взятой страны.
Основными загрязнителями воздушного бассейна являются оксиды углерода оксиды серы углеводород оксиды азота а также высокотоксичные соединения свинца.
Не менее острой является проблема загрязнения подземных и надземных вод. Оценка состояния водного бассейна свидетельствует о тенденции роста концентраций минерального азота фосфора калия сульфатов и др. элементов поступающих с сельскохозяйственных угодий в результате сброса загрязняемых сточных вод городов и других населенных пунктов.
Ряд природоохранительных проблем вызван крупномасштабной мелиорацией и освоением новых земель.
Возникли негативные процессы приведшие к загрязнению поверхностных и грунтовых вод к эрозии почв и деградации естественных ландшафтов исчезновению отдельных видов растений и животных.
Одной из серьезнейших проблем Беларуси является проблема утилизации обезвреживания и захоронения промышленных отходов.
Сложившаяся экологическая обстановка в республике значительно снижает качественный уровень жизни населения ограничивает возможность развития таких природоохранительных мероприятий которые бы обеспечивали снижение либо исключение загрязнения окружающей среды.
Важное место в этом направлении должна занимать подготовка экологически грамотных специалистов в высшей школе. С учетом существующих проблем законами Республики Беларусь «Об образовании» и «Об охране окружающей среды» закреплена приоритетность экологического образования во всех учебных заведениях.
В связи с описанными проблемами с 1.07.97 на промышленные предприятия изготавливается экологический паспорт который составляется согласно ГОСТ 17.0.04.90:
Экологический паспорт промышленного предприятия – это нормативно-технический документ включающий данные предприятия об использовании ресурсов и определения его влияния на окружающую среду.
Экологический паспорт предприятия представляет комплекс данных выраженных через систему показателей отражающих уровень использования предприятием природных ресурсов и степень его воздействия на окружающую среду.
Экологический паспорт разрабатывается за счет его средств и утверждается руководителем предприятия по согласованию с территориальными органами по охране труда и природе где он регистрируется.
Основой для разработки экологического паспорта являются согласованные и утвержденные показатели производства разрешенные на предприятии разрешение на природопользование паспорта газо- и водоочистных сооружений и установок по утилизации отходов.
Экологический паспорт не заменяет и не отменяет действующие формы и виды государственной отчетности.
5 страниц 29 иллюстраций 61 таблиц 21 источник литературы 6 приложений 115 листов графического материала.
В данном дипломном проекте я провела анализ назначения конструкции и технологичности детали базового варианта технологического процесса. Определила тип производства. Сделала выбор заготовки технологических баз методов обработки. Произвела разработку технологических операций. При помощи РАМОП произвела аналитический расчет припусков на обработку. Рассчитала режимы резания технические нормы времени на технологические операции технологическую размерную цепь. Определила необходимое количество оборудования. Произвела расчет и проектирование приспособления для точения уступа приспособления для контроля перпендикулярности протяжки приспособления для очистки протяжки. Спроектировала планировку участка по изготовлению ротора с учетом всех норм правил и требований в помещениям механических цехов. Осуществила расчет технико-экономических показателей обработки детали. Экономический эффект проектируемого варианта по сравнению с базовым составляет 37 млн. руб. Определила основные задачи в области охраны труда. Указала требования техники безопасности производственной санитарии санитарно-гигиенических требований в рабочей зоне естественного и искусственного освещения вентиляции защиты населения в чрезвычайных ситуациях охраны окружающей среды.
Необходимая техническая документация оформлена в виде комплекта документов на изготовление детали в соответствии с требованиями ЕСКД на соответствующие карты по ГОСТ 3.1118-82 ГОСТ 3.1105-84 ГОСТ 3.1302-85 ГОСТ 3.1404-86 и другие.
Содержание2.doc
4 Оценка экономической эффективности варианта технологического процесса .
5 Основные технико-экономические показатели проекта ..
Охрана труда и окружающей среды ..
1 Задачи в области охраны труда
2 Техника безопасности и производственная санитария .
2.1 Обоснование размеров производственных помещений
2.2 Санитарно-гигиенические требования в рабочей зоне
2.3 Естественное освещение .
2.4 Искусственное освещение ..
2.5 Техника безопасности при работе на оборудовании
2.6 Защита от шума и вибрации
2.7Проектирование вытяжной вентиляции ..
3 Защита населения в чрезвычайных ситуациях ..
4 Охрана окружающей среды .
Ведомость проекта.doc
Технологический процесс
механической обработки
Чертеж приспособления
для точения 8 уступов
для очистки протяжки
Эскизы операционные
ДП 03.01.753.00.00.000
Ведомость дипломного проекта
Р.cdw

Твердость 41.5 46.5 41.5 46.5 HRCэ
Покрытие хим. окс. прм. по ГОСТ 9.306-85
* Размер обеспечивается инструментом
Припуски, допуски Ру.frw

зенкерования 0.33 мм
растачивания 25.4 мм
растачивания 25.19 мм
растачивания 0.21 мм
Zmin при растачивании 0.09 мм
Zmax при растачивании 0.21 мм
Zmin при зенкеровании 0.668 мм
Zmax при зенкеровании 1.638 мм
Протяжка.doc
Минимальный диаметр отверстия под протягивание: d = 25 мм; диаметр отверстия получаемое после протягивания: D = 26 мм. Предельное отклонение диаметра D по чертежу детали: =0067 мм длина протягиваемого отверстия: = 009 мм.
Материал заготовки: Сталь 40Х: = 900 МПа; HB = 187
Рисунок 2.2 - Профиль обрабатываемого отверстия
D1= 25-05 = 245 мм. (2.10)
где d - минимальный диаметр отверстия под протягивание мм.
Расчетную величину D1 округляем до ближайшей меньшей величины соответствующей ГОСТ 4044-70. Принимаем D1 = 22 мм. Остальные размеры хвостовика и размеры шейки принимаем соответственно с ГОСТ 4044-70:
D1' =17 мм; D2 = 215 мм;
R1= 03 мм; R2 = 1 мм; C = 05 мм; α = 20.
Рисунок 2.3 - Хвостовик протяжки
Длину конуса принимаем L = 15 мм так как диаметр отверстия под протягивание D = 25 мм. Диаметры конуса: меньший равен диаметру шейки (мм): больший – передней направляющей части (мм).
Диаметр передней направляющей части мм
Dпн= d = 25 мм (2.11)
Предельное отклонение Dпн по e8.
Длина передней направляющей Lпн равна расстоянию от конца переходного конуса до первого зуба режущей части то есть включая длину первой стружечной канавки.
Lпн = т.к. lдD = 1006 ≤ 15 (2.12)
где lд - длина протягиваемого отверстия
D- диаметр отверстия получаемого после протягивания мм.
Главные режущие кромки зубьев имеют форму концентрических дуг диаметр которых Di постепенно увеличивается от первого зуба к последнему. Вспомогательные режущие кромки зубьев имеют криволинейную форму в зависимости от профиля обрабатываемой детали.
Величины углов в нормальном сечении по главной режущей кромке для стали 40Х принимаем:
Предельные отклонения углов по ГОСТ16492-70
γ = (-1;+ 2); α = 30;
Для уменьшения трения на вспомогательных режущих кромках делают угол равный 1 располагающийся позади ленточки шириной 08 1 мм. Для обработки заготовки принимаем зубья с криволинейной спинкой.
Ориентировочные размеры режущих зубьев и расположенных между ними стружечных канавок могут быть определены следующим соотношением:
t = (125 15) = (125 15) = 45 54 мм
Принимаем шаг зубьев 5 мм
Глубина стружечной канавки:
h = (035 06)t = (035 06)5= 175 3 мм;
с = (03 035)t = (03 035)5 = 15 175 мм;
Принимаем с = 16 мм;
R = (05 055)h = (05 055)3= 15 165 мм;
Рисунок 2.4 - Размеры стружечных канавок на режущей части протяжки
Диаметр первого зуба протяжки мм
Dz1 = Dпн = 25 мм; (2.13)
Диаметр последнего зуба режущей части протяжки мм;
где Dк –диаметр калибрующих зубьев протяжки мм;
Dк = (D + ) – p = (26 + 0067) – 0012 = 26055 мм;
р - величина разбивания отверстия; p= 0012 мм.
Диаметры промежуточных зубьев режущей части протяжки получают последовательным прибавлением к диаметру первого зуба удвоенного значения толщины срезаемого слоя.
Dz2 = Dz1 + 2·а (2.15)
Определение толщины срезаемого слоя
Фасонные протяжки срезают припуск заготовки как правило по генераторной схеме резания. Толщина срезаемого слоя (а) равна разности высот или полуразности диаметров пары смежных режущих зубьев. Ширина срезаемого слоя b равна длине главной режущей кромки зуба протяжки.
Режущая кромка первого зуба – окружность следовательно
Режущие кромки последующих зубьев - дуги концентрических окружностей поэтому ширина срезаемого слоя одним зубом равна сумме длин дуговых участков главной режущей кромки данного зуба т.е.
где b – длина одного дугового участка на режущей кромке данного зуба;
n – число дуговых участков на режущей кромке зуба.
Длина дуговых участков режущей кромки уменьшается при увеличении диаметра от d до D. Схема резания при протягивании зависит от площади срезаемого слоя
P= f(ab) поэтому для сохранения постоянной силы P за весь период протягивания отверстия пропорционально уменьшению b увеличивают толщину срезаемого слоя a.
Последовательность определения толщины срезаемого слоя:
а) определяем общий припуск под протягивание мм:
А = (D +)2-d2 = (26 + 0067)2 – 252 = 05335 мм; (2.18)
б) делить величину А на ступени не обязательно так как высота протягиваемых зубьев маленькая:
в) определим толщину срезаемого слоя а из условия прочности протяжки по впадине первого зуба:
а1 = (F1· []р (10·Cрb1·zк·кγ·кб))118 мм (2.19)
где F1- площадь сечения по впадине первого зуба протяжки мм2
Рисунок 2.5 – Генераторная схема резания для протяжки
F1= ·(Dz1-2h)24 = 314· (25 - 2·2)24 = 356185 мм2; (2.20)
[]р - допустимое напряжение при деформации растяжения в материале режущей части протяжки МПа.
b1 - длина режущей кромки первого зуба протяжки мм
b1 = ·Dz1 = 314·25 = 785 мм
zк - число зубьев протяжки участвующих одновременно в резании.
кб = 134 т.к. обработка без эмульсии;
а = (356185·400(10·212·785 ·3·093·134))118 = 017 мм;
Так как а=017 не оптимально (выше 02 не рекомендуется так как получается низкое качество поверхности) то принимаем а=01. Это повысит качество протягиваемого отверстия и предельно допустимую прочность первого зуба.
г) проверим возможность размещения стружки в канавке между зубьями при срезании протяжкой максимальной толщины срезаемого слоя аi max .
где Kc-коэффициент заполнения стружечной канавки Kc = 3;
Условие выполняется.
Проверим прочность протяжки на разрыв по шейке хвостовика.
где P- сила резания при протягивании Н
P = 10·Cр·а085b·zк·кγ·к0 (2.23)
P = 10·212·01085·785·3·093·134 = 08105 H;
Fx = ·( D1')24 (2.24)
где D1'- диаметр вала хвостовика мм
Для стали 40X ГОСТ - []
Условие не выполняется изготавливаем цельную протяжку из материала сталь Р6М5 []x = 400 МПа
Проверка протяжки по тяговой силе протяжного станка.
Q = Р09 = 0810509 = 889 кН
где Q - номинальная тяговая сила протяжного станка.
Выбрали: модель станка 7Б55 с максимальной длиной рабочего хода каретки 1250 мм и номинальной тяговой силой Q = 100 кН.
Стружкоделительные канавки на режущих зубьях протяжки.
Канавки делают на зубьях имеющих длину режущей кромки 5 10 мм размещают их в шахматном порядке.
nk1 = b1(5 10) = 785(5 10) = 151 785
Калибрующая часть протяжки состоит из пяти зубьев одинакового диаметра равного диаметру последнего режущего зуба. Стружечные канавки имеют такую же форму и размеры как и на режущей части протяжки. Шаг калибрующих зубьев принимают равным шагу режущих зубьев.
Вершину калибрующих зубьев снабжают фаской 02 06 мм которая предназначена для сохранения диаметральных размеров протяжки при переточках.
Передний угол γк принимают равным γ так как при эксплуатации протяжки в результате переточек затупившихся зубьев происходит постепенный переход калибрующих зубьев в режущие.
Задний угол имеет небольшую величину αк =130 ±15 по сравнению с режущими зубьями. Это вызвано необходимостью обеспечить медленное уменьшение диаметральных размеров зубьев при переточках.
Заднюю направляющую часть у фасонных протяжек выполняют цилиндрической. Диаметр задней направляющей части мм:
где d –минимальный диаметр отверстия под протягивание мм
Dзн = 25 мм предельное отклонение по f7.
Длину задней направляющей части принимаем Lзн = 20 мм.
Предельное отклонение диаметра зуба по ГОСТ 164992-70 равно –0.02 мм.
АНнОТАЦИЯ.doc
В данном дипломном проекте я провела анализ назначения конструкции и технологичности детали базового варианта технологического процесса. Определила тип производства. Сделала выбор заготовки технологических баз методов обработки. Произвела разработку технологических операций. При помощи РАМОП произвела аналитический расчет припусков на обработку. Рассчитала режимы резания технические нормы времени на технологические операции технологическую размерную цепь. Определила необходимое количество оборудования. Произвела расчет и проектирование приспособления для точения уступа приспособления для контроля перпендикулярности протяжки приспособления для очистки протяжки. Спроектировала планировку участка по изготовлению ротора с учетом всех норм правил и требований в помещениям механических цехов. Осуществила расчет технико-экономических показателей обработки детали. Экономический эффект проектируемого варианта по сравнению с базовым составляет 37 млн. руб. Определила основные задачи в области охраны труда. Указала требования техники безопасности производственной санитарии санитарно-гигиенических требований в рабочей зоне естественного и искусственного освещения вентиляции защиты населения в чрезвычайных ситуациях охраны окружающей среды.
Необходимая техническая документация оформлена в виде комплекта документов на изготовление детали в соответствии с требованиями ЕСКД на соответствующие карты по ГОСТ 3.1118-82 ГОСТ 3.1105-84 ГОСТ 3.1302-85 ГОСТ 3.1404-86 и другие.
1РУ.doc
Наименование операции
Наименование марка материала
Сталь 40ХН ГОСТ4345-71
Наименование оборудования
Контролируемые параметры
Наименование средств ТО
Контроль внешним осмотром
Штангенциркуль ГОСТ 166-89
Технический контроль
1.doc
Наименование операции
Наименование марка материала
Сталь 40ХН ГОСТ4345-71
Наименование оборудования
Контролируемые параметры
Наименование средств ТО
Контроль внешним осмотром
Образцы шероховатости
Штангенциркуль ГОСТ 166-89
Технический контроль
2.doc
Контролируемые параметры
Наименование средств ТО
Штангенциркуль ГОСТ 166-89
Приспособление контрольное
035.frw

040.frw

025.frw

010РУ.frw

045.frw

015РУ.frw

020.frw

015.frw

010.frw

020РУ.frw

030РУ.frw

Рпок.cdw

Смещение по разъёму не более 0.3 мм
Остаток облоя по контуру не более 0.3 мм
коробление и спиральность не более 0.6 мм
Неуказанные радиусы закруглений R1 мм
Допускаемые отклонения штампованных уклонов
Твердость 187 217 HB (сталь 40Х)
Поверхность поковок должна быть очищена от окалины
Поковка с примерной массой 0.0675 кг
*Допускается ширина площади среза облоя при обрезке или обдирке
Сталь 40Х ГОСТ4543-71
2.doc
Технологическую размерную цепь составляем по операции 40.
В качестве замыкающего звена А0 выбираем размер который выдерживается без соблюдения принципа единства баз. Таким размером является размер 7-0.36.
Любой размер можно представить как расстояние между двумя точками (его границами) на условной координатной оси. Это расстояние зависит от координат границ размера то есть от двух размеров связывающих начало координат с этими границами.
Аналогичная зависимость имеет место при формировании размеров деталей в процессе их механической обработки партиями на заранее настроенных станках. При этом используется контактное базирование деталей и режущий инструмент настраивается относительно установочных элементов приспособления контактирующих с технологическими базами детали. В этих условиях начало координат для отсчёта положений границ формируемого размера детали следует принимать на технологической базе ориентирующей деталь в направлении этого размера так как она контактирует с неизменными установочными элементами приспособления и занимает стабильное положение для всех деталей партии. Таким образом исходный размер А0 в общем случае зависит от двух размеров (А1 и А2) которые связывают его границы с соответствующей технологической базой. Один из этих размеров А1=9+0.2 мм связывающий технологическую базу с формируемой режущим инструментом границей исходного звена называется технологическим размером. Второй размер А2=2 -025 мм.
Составляющее звено размерной цепи может быть увеличивающим или уменьшающим. Увеличивающим называется звено размерной цепи увеличение которого способствует увеличению размера исходного звена при фиксированных размерах других составляющих звеньев данной размерной цепи а уменьшающим – такое звено размерной цепи увеличение которого способствует уменьшению размера исходного звена при фиксированных размерах других составляющих звеньев данной размерной цепи.
Проведем расчет следующей размерной цепи.
Рисунок 1.14.1 – Размерная цепь
Решим проектную задачу методом полной взаимозаменяемости т.е. определим допуски составляющих звеньев по известному допуску замыкающего звена.
Допуск замыкающего звена =036 мм
Так как число составляющих звеньев равно трем то для расчета размерной цепи в первом приближении будем использовать метод равноточных допусков (метод допусков одного квалитета)
где a - число единиц допуска определяет зависимость допуска от
- единица допуска определяет его зависимость от номинального
где - среднее геометрическое границ интервала номинальных
размеров в таблице допусков в который попадает j-е
где и - минимальная и максимальная величина размера
входящие в данный интервал
Найдём среднее геометрическое границ интервала:
Определяем единицы поля допуска:
Найдём среднее число единиц поля допуска:
Величины допусков составляющих звеньев:
По таблице допусков определяем что данные величины допусков соответствуют 14 квалитету.
Допуски составляющих звеньев должны удовлетворять условию:
0≥360- условие выполняется
Рекомендуемые чертежи
- 24.01.2023
- 20.01.2016
- 24.01.2023