Проектирование технологического процесса механической обработки детали Корпус с использованием станков с ЧПУ




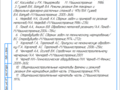
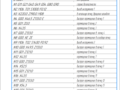

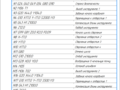
- Добавлен: 24.01.2023
- Размер: 7 MB
- Закачек: 1
Описание
Состав проекта
![]() |
![]() |
![]() |
![]() |
![]() ![]() ![]() |
![]() ![]() ![]() ![]() |
![]() ![]() ![]() ![]() |
![]() ![]() ![]() ![]() |
![]() ![]() ![]() ![]() |
![]() ![]() ![]() ![]() |
![]() ![]() ![]() ![]() |
![]() ![]() ![]() ![]() |
![]() ![]() ![]() ![]() |
![]() ![]() ![]() ![]() |
![]() ![]() ![]() ![]() |
![]() ![]() ![]() ![]() |
![]() ![]() ![]() ![]() |
![]() ![]() ![]() ![]() |
![]() ![]() ![]() ![]() |
![]() ![]() ![]() ![]() |
![]() ![]() ![]() ![]() |
![]() ![]() ![]() ![]() |
![]() ![]() ![]() ![]() |
![]() ![]() ![]() |
![]() ![]() ![]() ![]() |
![]() ![]() ![]() ![]() |
![]() ![]() ![]() ![]() |
![]() ![]() ![]() ![]() |
![]() ![]() ![]() ![]() |
![]() ![]() ![]() ![]() |
![]() ![]() ![]() ![]() |
![]() ![]() ![]() ![]() |
![]() ![]() ![]() ![]() |
![]() ![]() ![]() ![]() |
![]() ![]() ![]() ![]() |
![]() ![]() ![]() ![]() |
![]() |
![]() |
![]() |
![]() |
![]() |
![]() |
![]() |
![]() |
![]() |
![]() |
![]() |
![]() |
![]() |
![]() ![]() ![]() ![]() |
![]() ![]() ![]() ![]() |
![]() ![]() ![]() ![]() |
![]() |
![]() |
![]() |
![]() |
![]() ![]() ![]() ![]() |
![]() ![]() ![]() ![]() |
![]() |
![]() |
![]() ![]() ![]() ![]() |
![]() ![]() ![]() ![]() |
![]() ![]() ![]() ![]() |
![]() ![]() ![]() ![]() |
![]() ![]() ![]() ![]() |
![]() ![]() ![]() ![]() |
![]() |
![]() |
![]() |
![]() |
![]() ![]() ![]() ![]() |
![]() ![]() ![]() ![]() |
![]() ![]() ![]() ![]() |
![]() |
![]() |
![]() ![]() ![]() ![]() |
![]() ![]() ![]() ![]() |
![]() ![]() ![]() ![]() |
![]() ![]() ![]() ![]() |
![]() |
![]() ![]() ![]() ![]() |
![]() ![]() ![]() ![]() |
![]() ![]() ![]() ![]() |
![]() ![]() ![]() ![]() |
![]() ![]() ![]() ![]() |
![]() ![]() ![]() ![]() |
![]() ![]() ![]() ![]() |
![]() ![]() ![]() ![]() |
![]() |
![]() ![]() ![]() ![]() |
![]() ![]() ![]() ![]() |
![]() ![]() ![]() ![]() |
![]() |
![]() ![]() ![]() ![]() |
![]() ![]() ![]() ![]() |
![]() ![]() ![]() ![]() |
![]() ![]() ![]() ![]() |
![]() ![]() ![]() ![]() |
![]() |
![]() |
![]() |
![]() ![]() ![]() ![]() |
![]() |
![]() |
![]() ![]() ![]() ![]() |
![]() ![]() ![]() ![]() |
![]() ![]() ![]() ![]() |
![]() ![]() ![]() ![]() |
![]() ![]() ![]() ![]() |
![]() ![]() ![]() ![]() |
![]() ![]() ![]() ![]() |
![]() ![]() ![]() ![]() |
![]() ![]() ![]() ![]() |
![]() ![]() ![]() ![]() |
![]() ![]() ![]() ![]() |
![]() ![]() ![]() ![]() |
![]() ![]() ![]() ![]() |
![]() |
![]() |
![]() |
![]() |
![]() |
![]() |
![]() |
![]() |
![]() |
![]() |
![]() |
![]() |
![]() |
![]() |
![]() |
![]() |
![]() |
![]() |
![]() |
![]() |
![]() |
![]() |
![]() |
![]() |
![]() |
![]() |
![]() |
![]() |
![]() |
![]() |
![]() |
![]() |
![]() |
![]() |
![]() ![]() ![]() |
![]() ![]() ![]() |
![]() ![]() ![]() ![]() |
![]() ![]() ![]() ![]() |
![]() ![]() ![]() ![]() |
![]() ![]() ![]() |
![]() ![]() ![]() ![]() |
![]() ![]() ![]() ![]() |
![]() ![]() ![]() |
![]() ![]() ![]() ![]() |
![]() ![]() ![]() |
![]() ![]() ![]() |
![]() ![]() ![]() ![]() |
![]() |
![]() |
![]() |
![]() |
![]() |
![]() |
![]() ![]() ![]() ![]() |
![]() ![]() ![]() ![]() |
![]() ![]() ![]() ![]() |
![]() ![]() ![]() ![]() |
![]() ![]() ![]() ![]() |
![]() ![]() ![]() ![]() |
![]() ![]() ![]() ![]() |
![]() |
![]() ![]() ![]() ![]() |
![]() |
![]() ![]() ![]() |
![]() ![]() ![]() ![]() |
![]() ![]() ![]() ![]() |
![]() ![]() ![]() ![]() |
![]() |
![]() |
![]() |
![]() |
![]() |
![]() |
![]() |
![]() |
![]() |
![]() |
![]() ![]() ![]() ![]() |
![]() |
![]() |
![]() ![]() ![]() ![]() |
![]() |
![]() |
![]() |
![]() |
![]() |
![]() ![]() ![]() ![]() |
![]() |
![]() |
![]() |
![]() |
![]() |
![]() |
![]() |
![]() |
![]() |
![]() ![]() ![]() ![]() |
![]() |
![]() ![]() ![]() ![]() |
![]() ![]() ![]() ![]() |
![]() ![]() ![]() ![]() |
![]() ![]() ![]() ![]() |
![]() ![]() ![]() ![]() |
![]() ![]() ![]() ![]() |
![]() ![]() ![]() ![]() |
![]() ![]() ![]() ![]() |
![]() ![]() ![]() ![]() |
![]() |
![]() ![]() ![]() ![]() |
![]() ![]() ![]() ![]() |
![]() ![]() ![]() ![]() |
![]() ![]() ![]() ![]() |
![]() ![]() ![]() ![]() |
![]() ![]() ![]() ![]() |
![]() ![]() ![]() ![]() |
![]() |
![]() ![]() ![]() ![]() |
![]() ![]() ![]() ![]() |
![]() |
![]() ![]() ![]() ![]() |
![]() |
![]() |
![]() ![]() ![]() ![]() |
![]() ![]() ![]() ![]() |
![]() ![]() ![]() ![]() |
![]() ![]() ![]() ![]() |
![]() |
![]() ![]() ![]() ![]() |
![]() ![]() ![]() ![]() |
![]() ![]() ![]() ![]() |
![]() ![]() ![]() ![]() |
![]() ![]() ![]() ![]() |
![]() ![]() ![]() ![]() |
![]() ![]() ![]() ![]() |
![]() ![]() ![]() ![]() |
![]() ![]() ![]() ![]() |
![]() ![]() ![]() ![]() |
![]() |
![]() ![]() ![]() ![]() |
![]() |
![]() |
![]() |
![]() |
![]() |
![]() ![]() ![]() ![]() |
![]() |
![]() |
![]() |
![]() |
![]() ![]() ![]() ![]() |
![]() |
![]() |
![]() |
![]() ![]() ![]() ![]() |
![]() |
![]() |
![]() |
![]() |
![]() ![]() ![]() ![]() |
![]() ![]() ![]() ![]() |
![]() |
![]() |
![]() |
![]() |
![]() |
![]() |
![]() ![]() ![]() ![]() |
![]() ![]() ![]() |
![]() ![]() ![]() ![]() |
Дополнительная информация
OK-165.cdw

OK-20.cdw

160..cdw

мк2корпус лист 2.cdw

OK-90.cdw

ОК-160 лист 2.cdw

130,135.cdw

OK-50.cdw

мк2корпус лист3.cdw

OK-35.cdw

OK-40.cdw

OK-60.cdw

OK-65.cdw

ОК-015 лист 2.cdw

KE-030..cdw

OK-105.cdw

OK-120.cdw

OK-15.cdw

mkкорпус лист 1.cdw

мк2корпус лист5.cdw

OK-155.cdw

KE-045,.cdw

OK-25.cdw

OK-55.cdw

OK-30.cdw

KE-040,.cdw

OK-10.cdw

OK-160.cdw

OK-70.cdw

OK-150.cdw

заготовка.cdw

OK-165.cdw

OK-20.cdw

ОК-040 лист 2.cdw

OK-85.cdw

ОК-070 лист 2.cdw

ОК-110 лист 2.cdw

OK-135.cdw

ОК-105 лист 3.cdw

OK-140.cdw

OK-90.cdw

ОК-160 лист 2.cdw

OK-50.cdw

OK-80.cdw

OK-145.cdw

OK-35.cdw

OK-40.cdw

OK-110.cdw

OK-125.cdw

OK-60.cdw

OK-65.cdw

ОК-105 лист 2.cdw

ОК-015 лист 2.cdw

OK-130.cdw

ОК-130 лист 2.cdw

ОК-135 лист 2.cdw

OK-75.cdw

ОК-115 лист 2.cdw

ОК-165 лист 2.cdw

ОК-065 лист 2.cdw

OK-105.cdw

OK-120.cdw

OK-15.cdw

ОК-140 лист 2.cdw

OK-95.cdw

ОК-155 лист 2.cdw

OK-155.cdw

ОК-125 лист 2.cdw

OK-100.cdw

OK-25.cdw

OK-45.cdw

ОК-045 лист 2.cdw

OK-55.cdw

OK-30.cdw

OK-10.cdw

OK-160.cdw

OK-70.cdw

OK-150.cdw

OK-115.cdw

УП1 160.cdw

УП1 165.cdw

лист УП2.cdw

лист УП2 160.cdw

Список литературы.cdw

лист УП1.cdw

отчет - копия (2).cdw

мк2корпус лист 2.cdw

мк2корпус лист7.cdw

мк2корпус лист3.cdw

мк2корпус лист6.cdw

мк2корпус лист8.cdw

мк2корпус лист9.cdw

мк2корпус лист11.cdw

мк2корпус лист10.cdw

mkкорпус лист 1.cdw

мк2корпус лист12.cdw

мк2корпус лист4.cdw

мк2корпус лист5.cdw

отчет.cdw

отчет - копия (2) - копия.cdw

эскиз для карты контроля1.cdw

обьед..cdw

РТК-105.cdw

175 - копия.cdw

KE-095,100.cdw

160..cdw

150..cdw

KE-050,.cdw

165..cdw

165. - копия.cdw

KE-075,080.cdw

085.cdw

140..cdw

145..cdw

130,135.cdw

KE-015.cdw

120,.cdw

KE-010.cdw

эскиз для карты контроля3.cdw

KE-105,.cdw

175.cdw

KE-110.cdw

KE-020.cdw

KE-030..cdw

KE-055,.cdw

KE-065,070.cdw

115,.cdw

155..cdw

KE-035..cdw

125,.cdw

KE-090.cdw

KE-045,.cdw

KE-060..cdw

KE-040,.cdw

170..cdw

нет.cdw

объединили.cdw

эскиз для карты контроля2.cdw

не надо.cdw

эскиз для карты контроля.cdw

объедин.cdw

нет уже.cdw

отчет - копия.cdw

Рекомендуемые чертежи
- 24.01.2023
- 24.01.2023
- 24.01.2023
- 05.01.2022
Свободное скачивание на сегодня
- 22.08.2014
- 29.08.2014
Другие проекты
- 23.10.2021