Проектирование технологического процесса детали Вал шлицевый




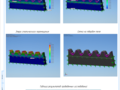
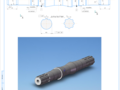
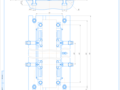
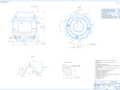
- Добавлен: 24.01.2023
- Размер: 5 MB
- Закачек: 3
Описание
Состав проекта
![]() |
![]() |
![]() ![]() ![]() |
![]() |
![]() |
![]() |
![]() |
![]() |
![]() |
![]() |
![]() |
![]() |
![]() |
![]() |
![]() |
![]() |
![]() |
![]() |
![]() |
![]() |
![]() ![]() ![]() ![]() |
![]() ![]() ![]() ![]() |
![]() ![]() ![]() ![]() |
![]() ![]() ![]() ![]() |
![]() ![]() ![]() |
![]() ![]() ![]() ![]() |
![]() ![]() ![]() ![]() |
![]() ![]() ![]() ![]() |
![]() ![]() ![]() ![]() |
Дополнительная информация
Исследование прочности рейки методом конечных элементов.cdw

Токарная_многорезцовая.cdw

Шлифовальная1.cdw

Шлицефрезерная.cdw

Приспособление.cdw

Чертеж детали и 3D.cdw

наладка фреза.cdw

Фрезерно-центровальная.cdw

Рекомендуемые чертежи
- 24.01.2023
- 07.06.2021
- 24.01.2023
- 24.01.2023