Проектирование специального приспособления




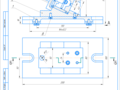
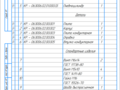
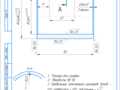
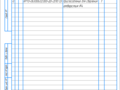
- Добавлен: 25.01.2023
- Размер: 818 KB
- Закачек: 1
Описание
Проектирование специального приспособления
Состав проекта
![]() |
![]() |
![]() |
![]() ![]() ![]() |
![]() ![]() ![]() |
![]() ![]() ![]() |
![]() |
![]() ![]() ![]() ![]() |
![]() ![]() ![]() ![]() |
![]() ![]() ![]() ![]() |
![]() ![]() ![]() ![]() |
![]() |
![]() ![]() |
![]() ![]() |
![]() ![]() |
![]() |
![]() ![]() |
![]() ![]() |
![]() ![]() |
![]() ![]() |
![]() ![]() |
Дополнительная информация
Втулка 32х50 ГОСТ 11525-82.cdw

КР.-Герасимов.cdw

Спецификация.cdw

Ведомость курсовой работы.cdw

Оправка.m3d

Втулка кондукторная.m3d

Штифт.m3d

Быстросъемная шайба.m3d

Плита.m3d

Деталь.m3d

Корпус.m3d

Кондукторная плита.m3d

Рекомендуемые чертежи
- 24.01.2023
- 22.02.2022