Проектирование скиповой установки



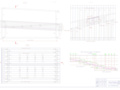
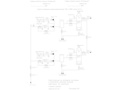
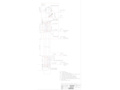
- Добавлен: 24.01.2023
- Размер: 1 MB
- Закачек: 0
Описание
Состав проекта
![]() |
![]() |
![]() ![]() ![]() |
![]() |
![]() ![]() ![]() |
![]() |
![]() ![]() ![]() ![]() |
![]() ![]() ![]() ![]() |
![]() ![]() ![]() ![]() |
![]() |
![]() ![]() ![]() |
![]() ![]() ![]() |
![]() ![]() ![]() |
![]() ![]() ![]() |
![]() ![]() ![]() |
![]() ![]() ![]() |
![]() ![]() ![]() |
![]() ![]() ![]() |
![]() ![]() ![]() |
![]() |
![]() |
![]() ![]() ![]() |
![]() ![]() ![]() |
![]() ![]() ![]() |
Дополнительная информация
экон.doc
2.1.Расчёт состава единовременных дополнительных капитальных затрат
Производим замену подъемной машины МК 5*4 на машину ЦШ 5*4.
Стоимость оборудования
Подъемная машина МК 54
Подъемная машина ЦШ 54
Стоимость силовых машин и оборудования подлежащих демонтажу в результате внедрения проекта модернизации – 3700 000 руб.
Балансовая стоимость монтируемых силовых машин и оборудования в результате внедрения нового проекта составляет –3800 000 руб.
Стоимость демонтажных и монтажных работ рассчитываем укрупненным методом – 15% от стоимости демонтируемого и устанавливаемого силового оборудования.
Стоимость демонтажных и монтажных работ составит :
(3 700 000 + 3800 000) × 010 = 750000 руб.
Общая стоимость единовременных дополнительных капитальных затрат по проекту составит : Кд = Фо + См (руб.)
Кд = 3800 000 + 750 000 = 4550000 руб. где :
Фо – стоимость основных средств предусмотренных проектом;
См – стоимость демонтажных и монтажных работ.
2.2. Расчет годового фонда рабочего времени персонала
Плановый годовой фонд рабочего времени определяем на основании планового баланса рабочего времени который составляется на 1го работника соответствующий категории персонала.
Баланс рабочего времени 1го рабочего за год
Дежурный и ремонтный персонал стволовые.
Дежурный и ремонтный персонал машинисты ПУ.
Календарный фонд времени
Номинальный фонд времени
Планируемые неявки всего в т.ч.:
Дни неявок по болезни
Эффективный фонд времени
Продолжительность рабочей смены
Дежурный и ремонтный персонал машинисты ПУ (40 ч. Нед.):
×2ВД = 16ВД 59-16=43 дня
Дежурный ремонтный персонал и стволовые (36 ч.нед.):
×2ВД = 24ВД 83-24 = 59 дня
ИТР; АУП: 66к.д.7к.д.= 9нед.
×2ВД = 18ВД 66-18 = 48 дней
Эффективный фонд рабочего времени за год составит:
Тэф=250 – 50 = 200 к.д. 200 ×8 = 1600 челч
Дежурный ремонтный персонал и стволовые (36 ч. Нед):
Тэф=250 – 66 =184к.д. 184×72 = 13248 челч
Тэф=250 – 55 =195 к.д. 195×8 = 1560 челч
2.3. Расчет структуры ремонтного цикла электромеханического оборудования и нормативы трудоемкости работ
Расчёт структуры ремонтного цикла (Рц) механического оборудования (базовый вариант).
Ремонтные нормативы для скипов 2СН-11-2К
Норматив периодичности
Норматив трудоёмкости
Норматив продолжительности
Расчет нормативной трудоёмкости для скипов 2СН-11-2К:
ТЕ.НОРМ.ТО = 32 × 4 × 152 = 19 456 чел × час
ТЕ.НОРМ.Т1 = 6 × 4 × 486 = 11664 чел × час
ТЕ.НОРМ.К = 1 × 4 × 1564 = 6 256 чел × час
Время плановых простоев за период рем. цикла(32 мес.) составит:
Тр.ц. = 84 + 22 × 6 + 7 × 32 = 440 час.
Время плановых простоев за 1 кал. год составит:
Тгод. = 44027 =163 час.
Ремонтные нормативы для подъёмных установок МК 5*4
Рц = К + 16Т1 + 100ТО
Расчет нормативной трудоёмкости для подъёмных установок МК 5*4
ТЕ.НОРМ.ТО = 100 × 2 × 336 = 67 200 чел × час
ТЕ.НОРМ.Т1 = 16 × 2 × 649 = 20 768 чел × час
ТЕ.НОРМ.К = 1 × 2 × 2258 = 4 516 чел × час
Время плановых простоев за период рем. цикла(54 мес.) составит:
Тр.ц. = 97 + 35 × 16 + 9 × 100 = 1 557 час.
Тгод. = 1 55742 =371 час.
Ремонтные нормативы для тормозных устройств
Рц = К + 12Т1 + 96ТО
Расчет нормативной трудоёмкости для тормозных устройств
ТЕ.НОРМ.ТО = 96 × 2 × 78 = 14 976 чел × час
ТЕ.НОРМ.Т1 = 12 × 2 × 237 = 5 688 чел × час
ТЕ.НОРМ.К = 1 × 2 × 973 = 1 946 чел × час
Время плановых простоев за период рем. цикла(48 мес.) составит:
Тр.ц. = 80 + 36 × 12 + 4 × 96 = 896 час.
Тгод. = 8964 = 224 час.
Расчёт структуры ремонтного цикла (Рц) энергооборудования (базовый вариант).
Ремонтные нормативы для двигателей П2-800-255-8КУХЛ4
Расчет нормативной трудоёмкости для двигателей
ТЕ.НОРМ.ТО = 9 × 2 × 36 = 648 чел × час
ТЕ.НОРМ.Т1 = 3 × 2 × 110 = 660 чел × час
ТЕ.НОРМ.К = 1 × 2 × 432 = 864 чел × час
Время плановых простоев за период рем. цикла(9 мес.) составит:
Тр.ц. = 64 + 24 × 3 + 4 × 9 = 172 час.
Тгод. = 172075 = 229 час.
2.4. Расчет плановой численности персонала и плановой сметы годового ФОТ
Явочная численность дежурного персонала составит:
поверхностный персонал:
Те норм то 67 200 + 14 976 + 648
подземный персонал обслуживающий скипы:
Явочная численность ремонтного персонала занятого на текущих ремонтах составит:
Те норм т1 20 768 + 5 688 + 660
Явочная численность ремонтного персонала занятого на капитальных ремонтах составит:
Те норм к 4 516 + 1946 + 846
подземный персонал обслуживающий скипы:
Явочный состав рабочих с учетом подменного штата образует списочный состав.
Численность подменного штата определяется величиной коэффициента списочного состава (Ксп) который определяется:
Списочная численность определяется: Чсп =Чя · Ксп
Определяем списочную численность дежурного персонала занятого на ТО.
Чсп то = Чя то Ксп то = 42 128 = 54 чел.
Чсп то = Чя то Ксп то = 11 135 = 15 чел.
Списочная численность ремонтного персона занятого на Т1:
Чсп т1 = Чя т1 Ксп т1 = 14 128 = 18 чел
Чсп т1 = Чя т1 Ксп т1 = 7 135 = 10 чел
Списочная численность ремонтного персона занятого на К:
Чсп к = Чя к Ксп к = 4 128 = 5 чел
Чсп к = Чя к Ксп к = 4 135 = 6 чел
Списочная численность машинистов ПУ:
Необходимое количество машинистов П.У. в смену 2 чел. а в сутки 6 чел.
Чсп маш. = Чя маш. · Ксп
Ксп = Тном.Тэф = 19921 560 = 128
Чсп маш. = 6 · 128 = 8 чел.
Списочная численность стволовых:
Явочная численность стволовых в смену на подземных работах 4чел. а в сутки 12чел.
Чсп.ствол.= Чя ствол. · Ксп
Ксп = Тном.Тэф = 1 7921 3248 = 135
Чсп.ствол = 12 · 135 = 16чел.
Тарифные разряды и ставки поверхностных рабочих.
Чсп(3Р)Тсп +Чсп(4Р)Тсп
Средний тарифный разряд:
Средняя тарифная ставка дежурного персонала:
· 2006+21 · 2331+12 · 2708 + 3202 · 7
Тст ср = = 2443 руб.
Средняя тарифная ставка ремонтного персонала занятого на Т1:
· 2331+5 · 2708+3 · 3202
Тст ср = = 2581 руб.
Средняя тарифная ставка ремонтного персонала занятого на К:
· 2331+2 · 2708+2 · 3202
Тст ср = = 2830 руб.
Средний тарифный разряд дежурного персонала:
Средний тарифный разряд ремонтного персонала занятого на Т1:
Средний тарифный разряд ремонтного персонала занятого на К:
Тарифные разряды и ставки подземных рабочих.
· 2714+5 · 3157+2 · 3670 + 4346 · 1
Тст ср = = 3098 руб.
· 3157+3 · 3670+2 · 4346
Тст ср = = 3549 руб.
Тст ср = = 3801 руб.
Средняя тарифная ставка стволовых:
Тст ср = = 2548 руб.
Средний тарифный разряд стволовых:
Определяем норматив ФДЗП:
Нфдзп = · 100% (00%)
ПН – плановые неявки по плановому годовому балансу рабочего времени (дни)
Тэф – эффективный фонд одного работника по плановому годовому балансу рабочего времени (дни)
Для дежурного и ремонтного персонала занятого на Т1 и К на поверхности:
Для дежурного и ремонтного персонала занятого на Т1 и К и стволовых занятых на подземных работах составит:
Смета годового ФОТ персонала рабочих (базовый вариант).
Списочная численность
Плановый фонд рабочего
времени 1-го человека
Часовая тарифная ставка
Дневная тарифная ставка
Доплаты за работу во
вредных условиях 11%
Премиальный фонд 43%
Премиальный фонд 45%
Районный коэффициент
Северный коэффициент
ЕСН – 40% = 13788 120 руб.
ФОТ ИТР АУП рассчитываем укрупненным методом 14% от Годового ФОТ рабочих с учетом ЕСН составит:
470 300 · 014 = 4825 842 руб.
ЕСН – 40% = 1930 337 руб.
Расчет структуры ремонтного цикла (Рц) внедряемого оборудования (проектный вариант):
Ремонтные нормативы для подъёмных установок ЦШ 5*4
Рц = К + 13Т1 + 108ТО
Расчет нормативной трудоёмкости для подъёмных установок ЦШ 5*4:
ТЕ.НОРМ.ТО = 108 × 2 × 316 = 68 256 чел × час
ТЕ.НОРМ.Т1 = 13 × 2 × 633 = 16 458 чел × час
ТЕ.НОРМ.К = 1 × 2 × 2217 = 4 434 чел × час
Время плановых простоев за период рем. Цикла (54 мес.) составит:
Тр.ц. = 96 + 32 × 13 + 6 × 108 = 1 160 час.
Время плановых простоев за 1 кал. Год составит:
Тгод. = 1 16045 =258 час.
Структуры ремонтных циклов остального оборудования не меняются следовательно нормативная трудоемкость и время плановых простоев скипов тормозных устройств и электродвигателя остаются прежними.
Те норм то 68 256 + 14 976 + 648
Те норм т1 16 458 + 5 688 + 660
Те норм к 4 434 + 1946 + 846
Чсп т1 = Чя т1 Ксп т1 = 12 128 = 15 чел
Тарифные разряды и ставки рабочих (проектный вариант).
Средняя тарифная ставка рабочих определяется как сумма произведений часовой тарифной ставки на списочную численность по каждому тарифному разряду деленная на полную списочную численность рабочих:
· 2331+3 · 2708+2 · 3202
Тст ср = = 2523 руб.
Смета годового ФОТ персонала рабочих (проектный вариант).
ЕСН – 40% = 13508 928 руб.
Фот ИТР и АУП в проектном варианте не изменяется.
2.5. Расчет годовой суммы амортизационных отчислений
Стоимость оборудование и годовая сумма амортизации
Тормозное устройство
2.6. Расчет стоимости потребляемой силовой электроэнергии
МД - суммарная мощность двигателей кВт;
ТКАЛ - календарный фонд времени работы оборудования днях;
КЭ - коэффициент экстенсивности;
КИ - коэффициент интенсивности 08;
КП - коэффициент потерь электроэнергии в сети 11;
ТСМ - число смен в течение суток;
tСМ - продолжительность смены час;
ЦЭ - цена 1 кВт×ч по тарифу руб;
При расчете затрат на электроэнергию для электродвигателей не учитывается вариант расчета т. к. в проектный вариант не входит замена электродвигателя.
Затраты на электроэнергию для электродвигателей П2 – 800 – 255 – 8КУХЛ4 составят:
000 · 365 · 085 · 08 · 11 · 0334 · 3 · 8
Ээ = = 21885 283 руб.
Мд = 2 · 5000 = 10 000 кВт
Трц = 64 + 24 3 + 4 9 =172 час.
Тэф = Тк – Тг = 365 · 24 – 229 = 8531 час
С учетом технологических перерывов 1 час в смену а в сутки 3 часа.
Коэффициент экстенсивности двигателя составит:
Всего затраты на силовую электроэнергию по базовому (проектному) варианту составят:
2.7. Расчет потребности в комплектующих и материалах для нужд ремонтов и ТО
Потребность в материалах для текущего содержания и ремонта определяется согласно установленному годовому нормативу в % от балансовой стоимости установленного оборудования. Годовые плановые нормативы по материалам и комплектующим составят:
ТО – 4 % 4573 480 × 004 = 182939 руб.
Т1 – 6% 4573480 × 006 = 274 409 руб.
К – 10 % 4573480 × 01 = 457 348 руб.
ТО – 4 % 7608 322 × 004 = 304333 руб.
Т1 – 6% 7608 322 × 006 = 456 499 руб.
К – 10 % 7608 322 × 01 = 760 832 руб.
2.8. Расчет статьи “ Прочие расходы”
Статьи “Прочие расходы” предполагает затраты на подготовительные работы и работы по обслуживанию ремонтного участка в процессе выполнения работ:
-монтаж коммуникаций
-эксплуатация транспорта и подъемных механизмов
-оплата труда вспомогательного персонала
-оплата труда ИТР занятых управлением и организацией ремонтных работ
Размер “Прочих расходов” определяется в соответствии с нормативом в % от суммы учтенных затрат по смете (2%)
266 919 × 005 = 3016 892 руб.
590813 × 005 = 1579541 руб.
2.9. Расчет затрат на охрану труда
Примерный перечень состава затрат на охрану труда:
-износ спец. одежды и спец. обуви
- стирка спец. одежды
- стоимость спец. питания
-расходы на содержание санитарно-бытовых помещений (вода для душевых тепло для душевых стоимость санитарно-гигиенических средств и т.д.) и прочие расходы
Затраты на охрану труда определяют из расчета годовых норм расхода этих средств на 1-го работника:
Cо.т. = Но.т. × Чсп (руб)
Но.т. – норма затрат на охрану труда в расчете на 1-го работника (руб.)
Чсп – списочное число работников (чел.)
Затраты на охрану труда трудящихся:
Cо.т. = 1302015 × 132 = 1718 660 руб.
Cо.т. = 1302015 × 129 = 1679 599 руб.
2.10. Смета затрат на содержание и ремонт оборудования
Смета затрат на содержание и ремонт оборудования
Затраты на эксплуатацию и содержание
2Стоимость электроэнергии
3ФОТ дежурного персонала (пов.)
4ФОТ дежурного персонала (подз.)
5Отчисления на социальные нужды
6Материалы и запчасти
Затраты на текущий ремонт оборудования.
1ФОТ рабочих – ремонтников (Т1)(пов.)
2ФОТ рабочих – ремонтников (Т1)(подз.)
3Отчисления на социальные нужды
4Материалы и запасные части
Затраты на капитальный ремонт.
1ФОТ рабочих – ремонтников (К) (пов.)
2ФОТ рабочих – ремонтников (К) (подз.)
2.11. Сводная смета годовых накладных расходов по стволу СС - 2.
Сводная смета годовых накладных расходов по стволу СС - 2.
Содержание персонала участка.
4Отчисления на социальные нужды
Содержание эксплуатация и ремонт оборудования.
Мероприятия по охране труда.
Всего затрат по смете:
2.12. Экономическое обоснование проекта
Годовая экономия средств на эксплуатационных затратах составляет:
Сб. – Сп. = 81735504 – 81364664 = 370 838 (руб)
Снижение себестоимости обеспечивается на 05%
Рост производительности труда за счёт снижения трудоемкости работ по текущему ремонту составит :
Показатель экономической эффективности проекта (рентабельности):
Годовой объём транспортируемого п.и.
Годовой объем эксплуатационных затрат
Снижение удельных затрат по проекту
Рост производительности труда за счет снижения трудозатрат
Единовременные дополнительные капитальные затраты в проект
Рентабельность проекта
Планово – экономические показатели
Проект модернизации подъемной машины предполагает получение годовой экономии средств от внедрения проекта на сумму 370 838 руб. за счёт снижения трудоемкости по ремонту.
Снижение удельных эксплуатационных затрат обеспечивается на 05 % при этом рост производительности труда за счёт снижения трудозатрат составит 23 %.
Сумма единовременных КВ в проект составляет 4550 000 руб.
SHEMA1.DOC
1. Организация труда на участке подъема
Один из основных путей повышения эффективности производства на горнорудных предприятиях- внедрение научной организации труда (НОТ).
НОТ позволяет наилучшим образом соединить технику и людей в едином производственном процессе обеспечивает наиболее эффективное использование материальных и трудовых ресурсов непрерывное повышение производительности труда способствует сохранению здоровья и высокой работоспособности человека. Основные направления НОТ следующие:
- разработка и внедрение рациональных форм и кооперации труда;
- улучшение организации и обслуживания рабочих мест;
- улучшение условий труда;
- подготовка и повышения квалификации кадров;
- совершенствование нормирования и оплаты труда.
В зависимости от степени разделения и кооперации труда применяются две основные формы его организации: индивидуальные и коллективные
При индивидуальной форме каждый рабочий получает отдельное задание выполняет его самостоятельно и получает зарплату в зависимости от результатов своего труда. Коллективной называется такая форма при которой группа рабочих одной или нескольких профессий выполняют определённую работу или целый комплекс работ. При коллективной форме организации труда рабочие объединяются в бригады.
На участке подъема СС-2 применяется бригадная форма организации труда. Для обслуживания участка созданы бригады электрослесарей слесарей стволовых и машинистов подъема. Эл.слесари обслуживают эл.оборудование участка слесари - механическое оборудование участка стволовые обслуживают горизонты принимая скип с грузом п.и. машинисты подъема управляют подъемной машиной находясь в пультовой. Также рабочие участка подъема СС-2 делятся на подземных и поверхностных.
К подземным рабочим относятся стволовые электрослесаря и слесаря. Продолжительность рабочей недели подземного персонала – 36 час. а поверхностного – 40 час.
В связи с вредными факторами производства рабочему персоналу производятся доплаты за работу во вредных условиях в размере 11%. Также подземному персоналу производят оплату питания а поверхностным рабочим – оплату месячной нормы молочных продуктов.
Каждый рабочий обеспечивается спецодеждой и средствами индивидуальной защиты.
В зависимости от вредности условий труда всему рабочему персоналу производится прибавка дней отпуска:
- ИТР и АУП – 14 дней;
- подземный персонал – 31 день;
- поверхностный персонал и машинисты подъемных машин – 7 дней.
На рисунке 3.1.1 показана структурная схема управления участком сипового подъема СС-2.
ЭнергетикМеханик Сменный механик
Эл.слесариСлесари Деж. эл.слесарь Стволовые
Рис.3.1.1 Структура управления участком
Схема воздухосборн ПМ СС-2.dwg

Предохранительный клапан
Емкость для конденсата
Реле давления АК-11Б
для сброса конденсата
Схема включения воздухосборников СПМ и ЮПМ копра СС-2
рудника "Октябрьский
Ответственный за исправное состояние
и безопасное действие сосудов
работающих под давлением
Cист к печати.dwg

вент. закл. уклон N6 гор - 850 м.
отк. кв - г N6 гор - 960 м.
отк кв - г N6 гор. - 900 м.
пром. вент. закл. уклон N6
зап. отк отк. кв - г N25
вент. закл. кв - г N 5 гор. 850 м.
вент. закл. кв - г гор. 900 м.
вент. закл. кв - г гор. 700 м.
Отк. кв - г N 6 гор 750 м.
вент. закл. кв - г гор. 650 м.
Зап.транспортн. уклон
Л-19 Л-17 Л-15 Л-13 Л-11 Л-9 Л-7
Л-5 Л-3 Л-1 Л-2 Л-4 Л-6 Л-8 Л-10 Л-12 Л-14 Л-16
Вент. закл. вкершлаг
Л-19 Л-17 Л-15 Л-13 Л-11 Л-9 Л-7 Л-5 Л-3 Л-1 Л-2 Л-4 Л-6 Л-8 Л-10 Л-12 Л-14 Л-16 Л-18
Направление движения фронта работ
Система разработки р-ка "Октябрьский
Схема вскрытия и система разработки.
Схема.dwg

Грузовой откаточный квершлаг -700м.
Грузовой откаточный квершлаг гор. -950м.
Порожняковый откаточный квершлаг гор. -950м.
Грузовой откаточный квершлаг гор.-900м
Порожняковый откаточный квершлаг гор. -900м
Главный откаточный квершлаг гор. -850м
Порожняковый откаточный квершлаг гор. -800м.
Грузовой откаточный квершлаг гор.-800м
Выр-ка проссора КС-2
Компл-с в-к водоотлива
Восточный откаточный штрек
Западный откаточный штрек
Людской ходок в рембазу
Порожняковый откаточный квершлаг -700м.
Промежуточный откаточный
Вент. квершл. на ГС гор.-650м.
Соединительная выработка ВС-4 гор. -950м.
Соединительный квершлаг на ВС-4 гор. -900м
Соединительный квершлаг на ВС-4 гор. -800м
Запад. откаточный штрек
Западный вентиляционно-закладочный уклон гор. -800м
Восточный вентил. штрек гор. -700м
II з.в.з.у. гор. -850м
пром. вент.закл. уклон
Оконтуривающий штрек гор. -800м
Соед. кв-г на гор. 850м
Западный вентиляционно-закладочный штрек гор. 600 м
Западный откаточный штрек гор. -700м
Вост. вент. закл. штрек гор. -650м
Восточный вентиляционный квершлаг гор. -650м
Западный вент. квершлаг гор. -650м
Вент. уклон гор. -700м
Западный вентиляционный квершлаг гор.-700м
Восточный вентиляционный квершлаг гор.700м
Промежут. вент. квершлаг
Западный вентиляционный квершлаг гор. -600м
промежуточный вент. кв-г
Западный вентиляционно-закладочный штрек-1 гор.-500 м
Полещук Александр Анатольевич
великий создатель графической части ПЛА
- звуковая сигнализация ИГАС
- номер позиции с реверсивным режимом проветривания
- номер позиции с норм. режимом проветривания
- метанодатчик ДМТ-3
- восстающие и рудоспуски
- решетчатое ограждение
- участковый запасный выход
- общешахтный запасный выход
- вентилятор местного проветривания нагнетающий
- исходящая вентиляционная струя
- дверь вентиляционная автоматическая
- станция замера воздуха
- вентиляционный парус
- противопожарная дверь
- дверь вентиляционная
- входящая вентиляционная струя
Условные обозначения:
- Копер КС-1 с помещениями
здания подъемных машин и лебедок
- Клетьевой ствол КС-1
- Копер КС-2 выше отметки -4
копер КС-1 выше отм.-9
- Клетьевой ствол КС-2
- Копер СС-2 и поверхность
- Скиповой ствол СС-2
- Поверхность СС-1 ( копер и трансп.гал. )
- Транспортная галерея с узлами перегруза
- Вентиляционный ствол ВС-3
- Поверхностные сооружения ВС-3
- Главная вент.установка ВС-3
вент.канал до пп ляд
- Поверхностные здания и сооружения ГС
- Грузовой ствол ( ГС )
- Поверхностные здания и сооружения ВЗС
- Вспомогательно-закладочный ствол ( ВЗС )
- Поверхностные здания и сооружения ВСС
- Вспомогательно-скиповой ствол ( ВСС )
- Вент.ствол N 1 ( ВС-1 )
вент. канал до пп ляд
- Поверхностные здания и сооружения ВС-1
- Главная вент.установка ВС-1
- Вент.ствол N 2 ( ВС-2 )
- Поверхностные здания и сооружения ВС-2
- Главная вент.установка ВС-2
- Затопление горных выработок
- Несчастный случай ( поражение электрическим током
падение в восстающий
- обрушение горной массы
отравление ядовитыми газоми
несчастный случай в восстающих
проходимых с применением КПВ )
- Завал горной выработки или оьрушение от горного удара
- Авария подъемной установки грузолюдского подъема КС-1
- Полное аварийное отключение электроэнергии
- Клетьевой ствол КС-2. Околоствольные выработки КС-2.
- Клетьевой ствол КС-1. Околоствольные выработки КС-1 гор.-800м
- Попадание дыма в галерею СС-2 из рудника "Таймырский
- Вентиляционный ствол N 4
копер с примыкающими помещениями.
- Поверхностные сооружения ВС-4
- Главная вент. установка ВС-4
вент.канал до пп ляд.
- Башенный копер КС-2 выше отметки -4
ИзмЛист N докум. ПодписьДата
Ур. кромки загрузочного окна
Подъемная машина "Север
hпер .- высота переподъема
- расстояние от уровня разгрузочного лотка (загрузочного окна)
hа.у. - аварийный уровень переподъема
hк - длина отвесов подъемных (головных) канатов в копре
lж.в. - длина пути скипа в верхних жестких проводниках
до приемного бункера (лотка дозатора)
lж.н. - длина пути скипа в нижних жестких проводниках
L - общая длина отвесов канатов
hз - длина отвесов хвостовых (уравновешивающих) канатов в зумпфе
Проектирование скиповой подъемной установки CC-2
ДП 2068046-1806-04-02
1,6 Электроснабжение предприятия.doc
Электрические нагрузки и расход электроэнергии. Основными потребителями электроэнергии на поверхности рудника является являются электродвигатели б кВ и 0.4 кВ подъемных машин турбо компрессоров вентиляторов калориферов и электроосвещение. Источником электроэнергии для электроприемников рудника "Октябрьский" является ТЭЦ-2. Основными потребителями электроэнергии на поверхности рудника являются электродвигатели 6кВ подъёмных машин турбокомпрессоры вентиляторы калориферы элекгроосвещение.
Потребители электроэнергии рудника «Октябрьский» по степени
бесперебойности электроснабжения относятся к I и П категориям по классификации ПУЭ.
Источником электроэнергии для электроприёмников рудника «Октябрьский» является Норильская ТЭЦ-2 электроснабжение всех ГПП рудника осуществляется от ТЭЦ-2 по ВЛ 110кВ.
Схемы коммутации ГПП принимаются без выключателей на стороне высшего напряжения с установкой короткозамыкателей в цепях трансформаторов.
На ОРУ-110кВ принята упрощённая схема с отделителями и короткозамыкателями и «мостиком» со стороны ВЛ.
РУ бкВ выполняется с одинарной системой шин секционированный на четыре секции с АВР на секционных масляных выключателей предусматриваются комплектные устройства БПРУ.
Предусматриваются следующие виды защит на трансформаторах ТРДН-25000110:
Продольная диф.защита.
Максимальная токовая защита с выдержкой времени с вольтметровой
блокировкой на стороне высшего напряжения.
Максимальная токовая защита с выдержкой времени на вводах бкВ.
Газовая защита в баке трансформатора действующая на отключение и на
Газовая защита в баке переключающего устройства действующая на
отключение и на сигнал.
Реле уровня масла с действием на сигнал.
Защита от перегрузки с действием на сигнал.
Защиты дефференциальная газовая максимальная действуют на включение
короткозамыкателя для отключения питающей линии 110 кВ со стороны ТЭЦ-2.
После включения короткозамыкателя в первую бестоковую паузу производится отключение повреждённого трансформатора с помощью отделителя.
На питающих линиях 110кВ на ТЭЦ-2 (яч.621) предусматривается 2-х
ступенчатая токовая защита от междуфазных к.з. и 2-х ступенчатая земляная
защита. Ячейка №6 оборудована вышеуказанной защитой для ячейки №21
необходимо предусматривать защиту вновь.
Предусматривается УРДВ. На секционных маслянных выключателях
предусматривается максимальная токовая защита с выдержкой времени с
ускорением при действии АВР.
На линиях ТП предусматривается максимальная токовая защита от однофазных
замыканий с действием на сигнал.
На линиях электродвигателей турбокомпрессоров предусматривается
дифференциальная защита от асинхронного хода с реле мощности защита от
однофазных замыканий с действием на отключение защита минимального
напряжения защита от перегрузки Предусматриваются следующие автоматические
АВР СМВ 6кВ при отключении одного из трансформаторов или
питающей линии. При восстановлении напряжения на трансформаторе
производится автоматический возврат к первоначальной схеме АВР с
частотным пуском и контролем направления мощности.
АПВ вводов 6Кв на ГПП при отключении на длительное время одного из
трансформаторов которое вводится вручную на оставшемся в работе
АВР собственных нужд 220в.
Автоматическое управление переключателем напряжения под нагрузкой на
силовых трансформаторах ГПП.
Управление обдувкой трансформаторов ГПП.
Автоматические осциллографы для записи аварийных процессов на ГПП.
Управление вводными и секционными выключателями 6кВ на ГПП
предусматривается со щита управления на котором размещается также
аппаратура защиты и автоматики силовых трансформаторов и секционных
выключателей. Управление выключателями линий 6кВ производится с помощью ключей установленных на камерах. Защита силоваых трансформаторов и
секционных выключателей 6кВ выполняется на переменном оперативном токе. В качестве источника энергии для отключения вводных и секционных выключателей 6кВ и отделителей 110 кВ используются предварительно заряженные конденсаторы.
Релейная защита управление автоматика и сигнализация отходящих линий бкВ выполняется на выпрямленном оперативном токе с применением выпрямительных блоков БПТ и БПН с выходным напряжением 220В.
Для подключения блоков на выводах бкВ предусматривается установка второго комплекта трансформаторов тока 2-х фазах.
Питание цепей соленоидов включения электромагнитных приводов
выключателей предусматривается от комплектных выпрямительных устройств типа БПРУ.
Предусматривается аварийная и предупредительная сигнализация на подстанции приспособленная для выдачи телесигналов диспетчеру сетей и подстанций.
Предусматривается измерение тока на вводах 6;04кВ всех отходящих линий бкВ. Измерение напряжения на шинах 6;04;022кВ.
Учёт активной и реактивной электроэнергии производится на вводах бкВ на отходящих линиях бкВ.
Распределительные устройства 110кВ открытого типа ~ ОРУ 110кВ) всех ГПП выполнены по упрощенной схеме с отделителями и короткозамыкателями.
На ОРУ 110кВ для обслуживания оборудования сооружаются специальные решетчатые площадки.
Из-за больших снежных заносов всё электрооборудование ОРУ 110кВ приподнято над землёй.
Распредилительные устройства 6кВ всех ГПП (РУ-6кВ) выполняется закрытого типа комплектуются шкафами серии КРУ2-6Э с выключателями ВМГ-10К и приводами ПЭ-11.
Закрытая часть ГПП выполняется в одноэтажном исполнении с продуваемым кабельным подпольем.
Для защиты окрытой части ГПП от прямых ударов молний наприёмных
порталах 110кВ и зданиях ГПП устанавливаются стержневые молниеотводы. Для защиты оборудования от атмосферных перенапряжений на вводах ГПП со стороны 110кВ и на шинах 6кВ устанавливаются комплекты вентильных разрядников.
Трансформаторное маслянное хозяйство проектом не предусматривается.
Ремонт ревизия трансформаторов и очистка масла производться централизованно в цехе ремонта трансформаторов комбината.
Отвод масла из-под гравия в аварийных случаях существляется в подземный резервуар для слива масла расчитанный на полный объём масла одного трансформатора. Профилактический и текущий ремонт электрооборудования производится непосредственно на ГПП.
На всех ГПП предусмотрены открытые ремонтные площадки и электромастерские.
Распределительные подстанции 6кВ и трансформаторные подстанции 604кВ выбраны с учётом распределения нагрузок удобства обслуживания.
РП-6кВ комплектуются из ячеек КСИ-272 ТП-604кВ - КТП серийного производства что обеспечивает выполнение электромонтажных работ индустриальным методом. На вводах 6кВ ГПП-3О-бис РП-395-Т ПР-315-1Т расположенных на промплощадке ВПС-1 для ограничения мощности трехфазного КЗ устанавливаются токоограничивающие реакторы;
-защита подземных кабельных сетей на стороне 04кв основана напринципе опережающего отключения комплекса коммутационных операций
исключающих возможность появления опасных электрических разрядов в месте
повреждения кабеля или электроаппарата;
-защита выполнена автоматами АФВ и пускателями установленными на отводящих линиях 04кВ;
-защита от токов утечки в низковольтных подземных сетях выполняется с помощью реле утечки УАКИ действующих на отключение при снижении уровня изоляции в кабельных сетях ниже допустимых значений.
Схема электроснабжения подземных электроустановок на стороне 6кВ должна отвечать следующим условия
-мощность трехфазного КЗ в любой точке сети 6кв менее 50мВА; -максимальная токовая защита на всех участках выполняется на отключение выключателя без выдержки времени типовыми камерами
ЯК6400 ВВД-6 КРУВ-6;
-отключение всех электрически связанной поврежденной сети при замыканиях на землю и опасных токах утечки.
Виды работ выполняемые слесарем дежурным по ремонту оборудования:
-техническое обслуживание работающего оборудования;
-установление причин неисправности оборудования демонтаж агрегатов узлов и деталей;
-разборка очистка ремонт сборка и установка отремонтированных агрегатов узлов и деталей на оборудование;
-запуск отремонтированного оборудования в эксплуатацию.
К работе слесарем дежурным по ремонту оборудования допускаются лица в возрасте не моложе 21 года прошедшие специальное обучение сдавшие экзамены и получившие соответствующее удостоверение.
При поступлении на рудник слесарь должен пройти медицинское освидетельствование и в дальнейшем проходить его в установленном порядке с обязательной рентгенографией.
При поступлении на работу а также при переводе с одного участка на другой допуск слесарей к самостоятельной работе производится после инструктажа по технике безопасности.
Периодически один раз в пол года все слесари обязаны пройти повторный инструктаж по технике безопасности проводимый участковым техническим надзором ознакомиться под роспись с планом ликвидации аварий в части относящейся к месту их работы и с правилами личного поведения во время аварии.
Выполнять порученную работу слесарь должен в предусмотренной для этой цели спецодежде и спецобуви и при необходимости использовать предохранительные приспособления и средства индивидуальной защиты (предохранительный пояс очки и т.д.). Спецодежда должна быть соответствующих размеров куртка и рукава должны быть застёгнуты и не иметь свисающих концов каска зафиксированна под бородочным ремнём.
Слесарь обязан внимательно относиться к выполнению полученной работы следить за сигналами имеющими отношение как к его напосредственной работе так и за сигналами предупреждающими о возникновении опасности; не отвлекаться от работы посторенними разговорами и внимательно относиться к личной безопасности.
На месте ремонта оборужования слесарь долженн иметь исправный инмтрумент и приспособления.
В своей работе слесарь должен руководствоваться общими инструкциями по безопасности труда рабочими технологическими инструкциями инструкциями на отдельные виды работ технологическими картами проектами производства работ картами безопасности и настоящей инструкцией.
1,1Горно-геологические условия месторождения.doc
1. Горно-геологические условия месторождения
Талнахский рудный узел объединяющий Талнахское и Октябрьское сульфидные медно – никеливые месторождения является в настоящее время основной сырьевой базой Норильского горно-металлургического комбината. Генетически связанный с крупным сложным по морфологии Талнахским интрузивом габбро-долеритов месторождение представляет собой концентрацию на относительно небольшой площади сульфидных медно-никелевых руд открытых в 1960-1965 гг. и заканчиваемых ( на глубине свыше 1500 метров ) разведкой в на- стоящее время.
Талнахский рудный узел (территория около 100 км2) расположен в Норильском горно-промышленном районе на правобережье Норилки и приурочен к юго-западной оконечности плато Хараелах в области денудации его системами рек Талнах и Хараелах.В пределах рудного узла выделяются два месторождения сульфидных медно-никелевых руд: Талнахское и Октябрьское приуроченные к различным ветвям Талнахского интрузива габбро-долеритов.
В административном отношении площадь месторождения относит- ся к Дудинскому району Таймырского автономного Красноярского края. Разрабатываемые месторождения связаны между собой железной дорогой НГМК и с морским портом в Дудинке.
По характеру рельефа выделяют горную и равнинные части. Горная восточная часть занимающая более 60% площади поля представляет собой плато с абсолютными отметками 500-600 метров расчленённое на отдельные возвышенности. Поверхность плато пологого (1-3’) наклонена на восток. Юго-западные склоны возвышенностей круто обрываются к равнине. В районе месторождения протекают реки и мелкие ручьи с небольшим сбросом в зимнее время и сильно разливающиеся в весенне-летний период имеются мелкие озера.
Климат района суровый полярный. Снежный покров держится с середины сентября до середины июня. Среднегодовая температура воздуха равна 86°. Особенностью климата являются сильные ветры наиболее частые в зимний период.
Мерзлота распространена повсеместно. Мощность многолетне-мёрзлых пород в горной части достигает 300-400 метров в долинной под руслами рек и озёр развиты талики.
Источниками промышленного и бытового водоснабжения являются артезианские скважины и р.Норилка.
Промышленное значение имеют Норильск-1 Талнахское и Октябрьское месторождения.
Все месторождения локализуются в сложной по строению зоне Норильско-Хараелахского разлома в узлах пересечения его с северной частью Норильской и южной частью Хараелахской мульд.
В пределах Талнахского рудного узла выделяются 4 рудоносные ветви: Центральная (юго-западная) Северо-восточная Северо-западная и Нижняя.
Рудник «Октябрьский» строится на базе запасов богатых и медистых руд западного фланга Октябрьского месторождения приуроченного к Северо-Западной (Хараелахской) ветви Талнахского рудоносного интрузива габбро-долеритов локализованного в сульфатно-карбонатно-глинистой толще пород нижне- и средне-девонского возраста
Норильско-Хараелахский глубинный разлом делит южную часть Хара-елахской мульды на два блока. В западном опущенном блоке локализуется Северо-западнаяветвьТалнахской рудоносной интрузии.
Поле рудника «Октябрьский» на западе севере и юге ограничено геологическими контурами выклинивания залежи на востоке горным сбросом отделяется от поля рудника «Таймырский». Горный сброс имеет амплитуду около 50м угол падения плоскости сместителя около 70°. Геологическое строение этой части месторождения осложняется развитием просадочных структур. В окончательном формировании пликативных и дизъюктивных структур месторождения значительную роль сыграло воздействие внедрившейся интрузии.
Залежь богатых руд разбита серией ступенчатых субмеридиальных разрывных нарушений и опирающих их разнонаправленных трещин на узкие вытянутые преимущественно с севера на юг блоки.
Общую тектоническую ситуацию поля определяют грабеногореподобные локальные структуры состоящие обычно из нескольких клиновидных блоков неоднократно смещенных относительно друг друга на расстоянии от 5 до 20-25м по круто наклонным плоскостям.
Норильский район относится к северо - западной окраине Тунгусского артезианского бассейна и приурочен к зоне многолетней мерзлоты. Основные черты гидрогеологий Норильского района определяются геолого- тектоническим строением северо - западной части Сибирской платформы схемой формирования движение и разгрузки подземных вод и характером распределения многолетней мерзлоты. Многолетняя мерзлота распределена весьма неравномерно отсутствует в зона распространения глубоких водоёма (талики) и достигает максимальной величены на высокогорье (до 300 метров).
Многолетняя мерзлота обусловливает наличие трех видов вод: надмерзлотных межмерзлотных и подмерзлотных. Многолетняя мерзлота является водоупором и в сочетании с физической характеристикой горных пород и их структурными особенностями определяет напорный режим надмерзлотных и подмерзлотных вод и затрудняет гидравлическую связь.
Надмерзлотные воды в течение 8-9 месяцев образую твёрдую фазу (лёд) и заполняя рыхлые отложения играют роль цемента. В летнее время из них формируется фильтрационный поток в поверхности отложения представленных валунно - галечными грунтами супесями и суглинками. Эти воды характерны для долин рек и подножий склонов глубина их залегания 02-15 метров от поверхности мощность водоносного горизонта колеблется от 04-12 до 24-36 метров. Водообильность низкая (003-01 лс до 04-065 лс). Кф для супесей и суглинков 0003-002 мсут. В летнее время надмерзлотные воды характеризуются безнапорным режимом а в период частичного промерзания водного почвенного слоя - напорным при этом возможно образование наледей. Общим стоком намерзлотных и поверхностных вод является озеро Пясино. Для хозяйственно - питьевых целей эти воды интереса не представляют.
Подмерзлотные воды Норильского рудного района образуют единый водоносный комплекс в пределах которого выделяются в несколько взаимосвязанных тектоническими трещинами водоносных блоков. В выделении водоносных зон кроме этого важное значение имеет литолого - стратиграфический характер пород последний обусловливает разделение всего водоносного комплекса на две зоны. В верхнюю зону входят поровые воды четвертичных отложений горизонты трещено - пластовых вод в туфолавовых породах и в породах тунгусской серии. Эти воды отличаются гидрокарбонатно - кальциево - натриевым составом общей минерализацией 01-10 гл. Мощность верхней зоны в пределах плато достигает 250-1100 метров в долинах рек Норильской Рыбной Талнах - не более 35-90 метров. В долинах верхняя зона образована четвертичными гравийно - галечными породами.
Воды нижней водоносной зоны распространены в карбонатной - сульфатных и галогенных породах девона силура ордовика и верхнего кембрия. Режим этого горизонта застойный что объясняется весьма незначительной водопроницаемостью пород. Важным источником водоснабжения Талнахского рудного поля является гравийно - галечный водоносный горизонт заполняющий глубокую эрозионную впадину совпадающую с долиной реки Талнах. Это воды напорные в южной части плато (h=7080 м) и безнапорные в северной. Гидрогеологические условия месторождений Талнахского рудного поля весьма благоприятны - рудники сухие.
Hа месторождении развиты три водоносных горизонта Горизонт верхнечетвертичных и современных аллювиальных отложений приурочен к гравийно-галечным супесчано-суглинистым отложениям имеет мощность от 5 до 25м. Коэффициент фильтрации п*10 мсут. водопритока п*100м.куб.сут. Характер потока -безнапорный. Подземные воды горизонта пополняются атмосферными осадками. Воды гидрокарбонатные пресные.
Горизонт ниже-среднечетвертичных аллювиальных отложений локализуется в валунно-гравийно-галечных отложениях. Коэффициент фильтрации пород -п*100мсут. и коэффициент водопритока п*1000м. куб.сут. Воды напорные гидрокарбонатные с минерализацией до 05гл. Водоносный горизонт коренных пород приурочен к комплексу водовмещающих пород : базальтом осадком тунгусской сериив девоне а также интрузивным образованиям. Коэффициент фильтрации 44мсут коэффициент водопроводимости 1161м.куб.сут. Проницаемость коренных пород с глубиной уменьшается. Воды по химическому составу относятся к гидрокарбонатно-кальциевому ас глубины 315м- хлоридно-сульфатно-натриевым. Минерализация достигает 179гл. Руда и рудоносная интрузии не обнаруживают значительной проницаемости. По данным гидрогеологической службы для рудника "Октябрьский" максимальный водоприток составляет 3-5 м.куб.ч.
В поле рудника выделяются три промышленных типа руд: богатые медистые и вкрапленные. Все типы руд пространственно тесно связаны и образуют общую субгоризонтальную по форме рудную зону тяготеющую к подошве интрузива к контакту его с вмещающими породами. Оруденение принадлежит интрузиву что определило объединение всех различных типов и разновидностей руд в принципиально единую систему в которой по условиям кондиций выделяются несколько горизонтов и залежей промышленных типов руд.
Запасы медистых руд сосредоточены в горизонте кулисообразно продолжающим в западную зону локализации богатых руд. Залежь имеет длину 1000м ширину 800м. Глубина залегания 350м глубина распространения 1100 м при средней мощности 40-100м. Морфология тел медистых руд определяется конфигурацией и пространственным положением блоков вмещающих пород и интрузивных инъекций.
Главной текстурой медистых руд является брекчиевидная обусловленная наличием обломков осадочно-метаморфических пород сцементированных массивными сульфидами.
Вкрапленные руды прослеживаются по всей площади распространения рудного интрузива и локализуются в зоне нижнего эндоконтакта последнего. В поле рудника выделяются несколько горизонтов вкрапленных руд из которых выделяется основной. Ширина залежи по простиранию от 400 до 1200 м длина по падению –800-1000 м. Глубина залегания-800 м глубина распространения – 1000 м. Мощность горизонтов вкрапленных руд достигает 40м.
Пирротиновыеруды являются наиболее распространенной минеральной разновидностью. Главные минералы представлены: пирротином - 40-70% халькопиритом - 10-30% пенландитом - 10-15% магнетитом - 5-10%. Отношение содержания меди к сере в рудах составляет менее 03. Имеются платиноиды.
Халькопиритовые руды сложены: халькопиритом талнахитом - 40-70% кубанитом - 10-40% петландитом - 8-13%. Медь к сере составляет 06. Имеются платиноиды.
Кубанитовые руды - вторая по распространенности минеральная разновидность богатых руд. Эти руды характеризуются следующим составом: кубанита - 35-55% троилита - 20-40% петландита - 10-15% халькопирита – 5-15% магнетита - 5-8%. Отношение содержания меди к сере 03 - 045. Имеются платиноиды. Основным концентратом никеля во всех разновидностях богатых руд является петландит (98% всего никеля). Кобальт рассеян в рудообразующих минералах (73-82% в петландите 5-20% в ипрротине 21%вхалькопиритовыхрудах). Всямедь содержится в халькопирите и кубаните (99%). Железо входит во все главные минералы богатых руд. Среднее содержание никеля- 28% меди- 38%. Богатые руды находятся в подошве интрузива.
Медистые руды по основным рудным минералам выделяются пять минеральных разновидностей: пирротиновая пирротин-халькопиритовая пиритовая и валлериитовая. Первыедве являются промышленными залежами. В распределении минеральных разновидностей наблюдается зональность: пирротиновые руды располагаются ближе к контакту интрузива по удалении от него сменяются халькопиритовыми рудами затем идут пиритовые руды. Минеральный состав пирротиновых руд: пирротин халькопирит петландит магнетит. Нерудными минералами являются пироксены плагиоклаз карбонаты граниты серпентины ангидрит хлорит.
Халькопиритовой разновидности характерны халькопиритпетландит миллерит борнит кубанит пирит магнетит. Нерудные минералы те же что и в пирротиновых рудах. Среднее содержание никеля- 265% меди-66%.
По минеральному составу вкрапленные руды в интрузиве относятся к пирротиновой разновидности и располагаются между богатыми рудами и медистыми. Содержание металлов в руде колеблется по никелю от 0 до 15% по меди от 22%. По всем сортам руд содержание металлов увеличивается по мощности вниз.
Породы всех горизонтов разреза поля рудника в ненарушенном состоянии имеют высокую прочность f = 8-14. По мере приближения к зонам тектонических нарушений прочностные свойства их снижаются. В целом породы обладают интенсивной тектонической нарушенностью при трещиной пустотности в нарушенных участках в среднем 5-10%.
Нарушенность сплошных руд в зоне ведения очистных работ оценивается на 60-70% как сильная в остальной части - средняя. Устойчивость руды средняя. Нарушенность габбро-долеритов залегающих в кровле залежи богатых руд такая же как и в рудах. В породах подошвы представленных ороговикованными аргиллитами и мергелями трещины крутопадающие открытого типа. Нарушенность от сильной дослабой. Устойчивость пород соответственно средняя и слабая. Контакт кровли рудной залежи с перекрывающими ее габбро-долеритами по всему полю изобилует многочисленными ответвлениями прожилков сульфидов образующих на отдельных участках штокверковые зоны богатого оруденения зачастую переходящего во вкрапленные.
По трещинам в породах кровли развиваются ослабляющие минералы тальк хлорит серпентин. Выше в зоне вкрапленного оруденения габбро-долериты разбиты трещинами отдельности на блоки от 1 м3 и более.
В интервале до 10 м ниже контакта подошвы рудной залежи почти всегда происходит обрушение подстилающих пород до плоского контакта.
Ниже подошвы сульфидной залежи в 25-40 м залегает слой долеритов высокая устойчивость которых в сочетании со слабой устойчивостью аргилитов и мергелей являются осложняющим фактором при проходке и эксплуатации рудоспусков а также вент. восстающих.
Халькопиритовые разности сульфидных руд в отбитой массе склонны к быстрому окислению с выделением тепла. Случаев самовозгорания вкрапленных в интрузиве и медистых руд до сих пор не наблюдалось.
Все породы рудника руды газоносны. Абсолютная метаноносность примерно 200 м3сут. В этой связи рудник «Октябрьский» работает на индивидуальном газовом режиме безотнесения к определенной категории по газу.
1,4 Рудничный транспорт.doc
Основным видом транспорта рудниках является рельсовый транспорт. Откатка руды и породы производится по шести главным откаточным горизонтам. - 700м - 750м - 800м - 850м - 900м - 950м. Для откатки горной массы по главным откаточным выработкам со свежей струей воздуха приняты контактные электровозы К10 К14 К14М. Контактные электровозы К10 имеют сцепной вес 106 кН скорость длительного режима 184 кмч. Привод электровоза с внешним источником питания на два двигателя марки ДТН33 мощностью 33 кВт. Контактные электровозы К14 и К14М аналогичны только К14М — модернизированный. Сцепной вес 140 кН скорость длительного режима 136 кмч привод с внешним источником питания на два двигателя марки ДТН46 мощностью по 46 кВт.
Контактная сеть электровозов состоит из контактного провода (+) рельсового пути (-). Основным типом преобразовательных уставок для питания контактной сети подземной электровозной откатки являются автоматические шахтные тяговые подстанции АТП-500275М которые преобразуют трехфазный переменный ток частотой 50 Гц в постоянный.
Для контактных электровозов на руднике “Октябрьский” применяют вагонетки с глухим жестко закрепленным кузовом ВГ 45А; ВГ90А.
Вагонетки ВГ 45А вместимостью кузова 45 м3 грузоподъемность 135т; масса 4200кг.
Вагонетки ВГ 90А вместимостью кузова 9м3 грузоподъемность 27т; масса 8900кг.
Для откатки породы на вентзакладочном горизонте -650м а также при проходке тупиковых выработок на откаточных горизонтах приняты аккумуляторные электровозы АМ8Д АРП14.
Аккумуляторный модернизированный электровоз АМ8Д с массой 8т имеет
сцепной вес 87кН скорость длительного режима 11 кмч а также два двигателя марки ДТР8М мощностью по 13 кВт.
Аккумуляторные электровозы АРП14 рудничный повышенной надежности
сцепной вес 134 кН скорость длительного режима 18 кмч а также два двигателя марки ДРТ235 мощностью по 235 кВт.
Источниками энергии для аккумуляторных является тяговые щелочные никель-кадмиевые и никель-железные шахтные батареи типа 66ТНЖШ-350-У5
и 112ТНЖШ-500-У5. Емкости батарей 350 и 500 Ач.
Руда на всех горизонтах доставляется к опрокидывателям скиповых стволов СС –1 и СС –2. Порода со всех горизонтов направляется к опрокидывателям вспомогательного скипового ствола ВСС на горизонте – 800м. Разгрузка груженых составов производится в круговых опрокидывателях.
Руда на всех горизонтах шахты №1 доставляется к круговым опрокидывателям типа ОКЭ 40-860 скипового ствола СС-1 на гор. -950м. Круговые опрокидыватели типа ОКЭ 40-860 одновременно разгружают две вагонетки мощность двигателей 40 кВт. Шахты №2 к круговым опрокидывателям типа ОКЭ 40-410 скипового ствола СС-2. Круговые опрокидыватели типа ОКЭ40-410 одновременно разгружают только одну вагонетку мощность двигателей 30кВт. Порода со всех горизонтов направляется к опрокидывателям вспомогательного скипового ствола ВСС на гор. -800м. Перестановка вагонеток в опрокидывателях и на погрузочных пунктах осуществляется электровозом. Загрузка составов горной массой на погрузочных пунктах откаточных горизонтов принята с помощью вибропитателей типа ПВПА -4514 и ПВУ. Вибропитатели ПВРА -4514 имеют техническую производительность 1200тч мощность привода 265кВт угол наклона 10°-20°.
Вибропитатели ПВУ имеют техническую производительность 1000тч мощность привода 21кВт угол наклона 0°-10°. При этом размер кондиционного куска выпускаемой горной массы принят 600 мм.
Для ремонта электровозов и других видов рельсового оборудования на каждом откаточном горизонте проектом предусматривается ДЕПО ремонта электровозов.
1,2 Вскрытие месторождения.doc
Вскрытие залежи отрабатываемых богатых руд осуществляется одиннадцатью вертикальными стволами и главными квершлагами откаточных и вентиляционно-закладочных горизонтов -600м -700м -750м -800м -850м -900м -950м.
На основной площадке рудника находится четыре ствола. Клетевые стволы КС-1 и КС-2 и скиповые стволы СС-1 и СС-2.На вспомогательной площадке рудника находится три ствола. Вспомогательно-закладочный ствол (ВЗС) грузовой ствол (ГС) и вспомогательно-скиповый ствол (ВСС). На промплощадке вентиляционных стволов находится четыре вентиляционных ствола. ВС-1 ВС-2 ВС-3 ВС-4. Отработка месторождения ведется расходящимися фронтами – от центра к флангам.
Размещение стволов определялось с учетом ряда факторов а именно. условия залегания рудных тел рельеф местности гидрогеологические данные разведочного и контрольного стволового бурения меры охраны стволов от вредного влияния горных работ т.п. Немаловажным является также фактор размещения поверхностных объектов рудника во взаимосвязи с существующими и строящимися объектами и коммуникациями. Сечения стволов определены проектом из условий размещения в них подъемных сосудов и пропуска расчетного количества воздуха.
Скиповой ствол СС-1 размещается посередине линии простирания месторождения вне зоны сдвижения горных пород. Диаметр ствола в свету – 65 м; глубина – 875 м. Сопряжения на отметках. -860 м -792 м 725 м -875 м (зумпфовый водоотлив)предназначен для подъема руды первой шахты.
Клетевой ствол КС-1 расположен в 50 м к северо-западу от скипового ствола (СС) на одной промплощадке. Диаметр ствола в свету – 80 м; глубина – 875 м. Сопряжения на отметках. -792 м -860 м -875 м (зумпфовый водоотлив) предназначен для спуска-подьема людей материалов оборудования ВВ. Армировка ствола жёсткая из двутавра.
Вспомогательно-закладочный ствол ВЗС располагается посередине линии простирания в лежачем боку месторождения вне зоны сдвижения горных пород на юг от ствола СС. Диаметр ствола в свету – 80 м; глубина – 735 м. Сопряжения на отметках. -725 м -740 м (зумпфовый водоотлив) предназначен для подачи закладочных смесей по трубопроводам спуска материалов длинномера самоходного оборудования и др.
Грузовой ствол ГС. Диаметр ствола в свету – 65 м; глубина – 928 м предназначен для спуска самоходных машин длинномерных материалов крупногабаритного оборудования под специальным контейнером-траверсой.
Вспомогательно-скиповой ствол ВСС. Диаметр ствола в свету – 65 м; глубина – 936 м предназначен для выдачи руды и породы двухскиповыми подъемными установками.
Вентиляционный стволВС-1 размещается посередине линии падения месторождения вне зоны с движения горных пород а ВС-2 с боку месторождения. Диаметры стволов в свету – 65 м; глубина – 827 м служит для выдачи нисходящей струи воздуха из шахты. Армировка ствола выполнена с канатными проводниками. В стволе имеется лестничное отделение.
Вентиляционный ствол ВС-2. Размещается с боку месторождения. Диаметры стволов в свету – 65 м; глубина – 810 м служит для выдачи нисходящей струи воздуха из шахты. Армировка ствола выполнена с канатными проводниками. В стволе имеется лестничное отделение.
Вентиляционный ствол ВС-3. Диаметр ствола в свету – 65 м; глубина – 1106 м служит для выдачи исходящей струи воздуха из шахты.
Вентиляционный ствол ВС-4. Диаметр ствола в свету – 65 м; глубина – 1053 м служит для выдачи исходящей струи воздуха из шахты и аварийного выхода людей из шахты.
1,5 Стационарные установки.doc
5.1.Подъёмные установки
Скиповой ствол СС – 1. предназначен для подъема руды первой шахты. Ствол оснащен двумя двухскиповыми подъемными машинами МК 5×4 установленными в железобетонном копре и скипами с неподвижным кузовом и секторным затвором 2СH11-2К емкостью 11 м3. Многоканатная машина МК 5×4 имеет максимальную скорость подъема 16мс и высотой подъема 1600м. Привод машины с двигателем постоянного тока по системе Г-Д (генератор-двигатель).Генератор с независимым возбуждением П22-42-13к мощность 5350кВт частотой вращения 375 обмин.
Тихоходный двигатель постоянного тока П2-800-255-8КУ4мощность 5000кВт частота вращения 50 обмин.
Для возбуждения генератора принят синхронный двигатель СДС3-290-12 мощность 5800 кВт частота вращения 375 обмин.
К установке принят тиристорный преобразователь ШЭА4093-32Б3.
Годовая производительность одной подъемной установки при 14 часах работы в сутки и 305 дней в году с учетом коэффициента неравномерности работы подъема - 125 и коэффициента реверса подъема 11 составляет 2540000 т.
В качестве головных канатов приняты трехграннопрядные канаты ЛК - 36×25 уравновешивающие канаты плоские резинотросовые в огнестойком исполнении. Приняты канаты закрытой конструкции 045 мм.
Разгрузка скипов производится в копре в приемный бункер емкостью 220т. Руда из башенного копра подается на ОФ-2 или открытый склад руды по цепочке - бункер пластинчатый питатель типа ПТ-2-12-45 промежуточный ленточный конвейер сборочный конвейер конвейерная галерея ОФ-2.
Скиповой ствол СС – 2. Предназначен для подъема руды со второй шахты. Оборудование ствола и подъемных установок аналогично СС-1. Привод подъемных машин с тиристорными преобразователями аналогично СС-1. Производительность по руде одной скиповой подъемной установки ствола 23450000 тгод.
Клетевой ствол КС – 1. Предназначен для спуска-подъема людей материалов оборудования ВВ. По стволу проложены трубопроводы сжатого воздуха противопожарный три става водоотлива и детали различного назначения. Ствол оснащен многоканатными подъемными установками с машинами МК 4×4 с неопрокидными двухэтажными клетями 2КП 6.5-2 и 2Кн 4.5-2.
Многоканатная машина МК4×4 имеет максимальную скорость 14мс высота подъема 1000м. Привод машины асинхронный двигатель с контактными кольцами нормального исполнения АКН-2-19-41-16У4 мощность 2000 кВт частота вращения 370 обмин. Генератор П20-25-12к мощность 2580 кВт частота вращения 750 обмин. Головные канаты трехграннопрядные ЛК-36×25.
Клетевой ствол КС – 2. По назначению и оборудованию аналогичен КС-1 предназначен для обслуживания второй шахты. Вспомогательно-закладочный ствол ВЗС. Предназначен для подачи закладочных смесей по трубопроводам спуска материалов длинномера самоходного оборудования и др. Клетевая подъемная установка с однобарабанной подъемной машиной ЦР-6×3205 с безредукторным приводом и с одноэтажной неопрокидной клетью 1КHР45-1.
Цилиндрическая однобарабанная машина с разрезным барабаном ЦР-6×3205; скорость подъема 1мс с приводным асинхронным двигателем АКН-2-18-43-16У4 мощность 100 кВт частота вращения 370 обмин. Генератор 1П20-30-12К мощность 1890 кВт частота вращения 500 обмин. Двигатель постоянного тока для возбуждения генератора принят марки П21-85-9К мощностью 2100 кВт частота вращения 56 обмин.
Вспомогательно-скиповой ствол ВСС. Предназначен для выдачи руды и породы двух скиповыми подъемными установками.
В стволе проложены трубопроводы сжатого воздуха и противопожарный а также кабели различного назначения.
Ствол оснащен двумя двух скиповыми подъемными установками с подъемными машинами ЦР-6×3.20.5 и скипами с неподвижным кузовом 1СH5-1 грузоподъемность 15т объем скипа 5м
Подъемные канаты закрытой конструкции 043 мм. Максимальная скорость подъема - 15 мс. Производительность подъема по руде 1410000 тгод по породе 1040000 тгод. Комплекс сооружений на поверхности состоит из надшахтного здания и здания подъемных машин.
Вентиляционный ствол ВС – 1. Служит для выдачи исходящей струи воздуха из шахты и аварийного выхода людей из шахты. Ствол оснащен двумя подъемными установками и клетью без противовеса второй подъем - с бадьей.
Армировка ствола выполнена с канатными проводниками. В стволе имеется лестничное отделение.
Вентиляционный ствол ВС – 2. Служит для выдачи исходящей струи воздуха из шахты. Ствол не оборудован постоянными подъемными установками.
Для производства осмотра состояния крепи ствола в копре установлена лебедка ЛПК-4 с бадьей емкостью 1.5 м3. По стволу предусмотрена выдача породы с гор. -900м -850м и -950м на гор.-800м.
Армировка ствола выполнена с канатными проводниками. Ствол оснащен многоканатной подъемной установкой сподъемной машиной клетью и противовесом.
Вентиляционный ствол ВС – 3. Служит для выдачи исходящей струи воздуха из шахты. Тип подъема – одноканатный. Ствол оснащен бадьей вместимостью 3м3 двумя подъемными машинами Ц 352А и МК 2254.
Вентиляционный ствол ВС – 4. Служит для выдачи исходящей струи воздуха из шахты и аварийного выхода людей из шахты. Тип подъема – клетьевой одноканатный. Ствол оснащен двумя подъемными машинами Ц 352.
Грузовой ствол ГС. предназначен для спуска самоходных машин длинномерных материалов крупногабаритного оборудования под специальным контейнером-траверсой. Подъемная машина с максимальной скоростью подъема 1 мсек. Заводка оборудования на ствол и вывод оборудования из ствола на горизонте производится наплатформе по опорной ляде перекрывающей ствол на время выполнения операции по заводке. Комплекс сооружений на поверхности состоит из копра надшахтного здания калориферной установке и здания подъемной машины. Копер металлический одноукосный высотой 35 м.
5.2.Вентиляторные установки
Основные воздухо-подающие стволы КС-1 КС-2 и ВЗС оборудованы калориферными установками и вентиляторами подпора ВОД-40. Главные вентиляторные установки построены на вентиляционных стволах ВС-1 ВС-2 и ВС-3. Все вентиляторные установки аналогичны.
По данным приведенным в таблице 1.5.1 произведем орентировачный выбор вентиляторов.
Данные для орентировачного выбора вентиляторов
Исходящая струя воздуха
Рис. 1.5.1 Сводный график областей промышленного использования шахтных центробежных вентиляторов главного проветривания
Ориентировочный выбор вентиляторов соответствует вентиляторам установленным на предприятии.
Характеристики вентиляторных установок
Способ проветривания
Производительность м3ч
Центробежный вентилятор двухстороннего всасывания ВЦД-475М «Север» предназначен для главного проветривания глубоких труднопроветриваемых шахт и рудников горнодобывающей промышленности при температуре окружающей среды от -45 до +50 С.
Вентиляторная установка позволяет регулировать производительность и давление в широком диапазоне.
Конструкция вентилятора ВЦД-475М «Север» разработана онгипроуглемашем и НИИТИуглегормашем. Каждая вентиляторная установка состоит из рабочего и резервного вентиляторов и устройств для переключения и реверсирования воздушной струи. Всасывающие и нагнетательные каналы сблокированы в единую систему. Переключение с рабочего вентилятора на резервный и реверсирование воздушной струи производится восемью самоходными лядами (по четыре на каждый вентилятор) установленными в каналах.
Все операции по переключению ляд производятся при закрытых лопатках устройства для сброса мощности что позволяет снять давление с ляд.
Вентиляторные установки рассчитаны на работ в автоматическом режиме.
Максимальный уровень звукового давления издаваемый вентагрегатами 100-110 дБ. Во избежание распределения шума по воздуховодам и через стройконструкции и доведение его на рабочих местах до допустимого проектом предусматривается:
-создание вентагрегатов с воздуховодами через мягкие вставки;
-КПД вентагрегата принимается не ниже 09 максимального;
-вентустановки принимаются с виброизоляторами и устанавливаются как правило в выгороженных помещениях с дополнительной звукоизоляцией ограждающих конструкций.
Проветривание скиповых стволов СС - 1 и СС - 2 с дозаторами и дробильными камерами осуществляется обособленно поверхностными вентиляторами ВЦ - 25. Вспомогательно-скиповой ствол ВСС проветривается за счет общешахтной депрессии.
Техническая характеристика вентиляторов главного проветривания
Диаметр рабочего колеса мм
Частота вращения мин-1
Диапазон в зоне промышленного использования.
- статическое давление Па
Мощность установки кВт
Максимальный статический КПД установки
Технические данные вентиляторов местного проветривания
Наименование основных параметров.
Номинальный диаметр мм
Номинальная подача м3сек
Номинальное давление Па
Мощность эл. Двигателя кВт
5.3. Компрессорные установки
Потребителями пневматической энергии на руднике являются буровые установки "Бумер-135" "Бумер-121" станки для бурения закладочных скважин БМH-9 машины для оборки кровли ПЕК-24 комплексы для проходки восстающих выработок КПВ-4Б установки для возведения набрызгбетонной крепи "Алива" и БМ-68 пневмоцилиндры механизмов околоствольных дворов закладочный комплекс на поверхности и другие пневмоприемники. Значительный расход сжатого воздуха требуется на пневмотранспорт закладочного бетона.
Перечень основного технологического оборудования
Окончание таблицы 1.5.6
Техническая характеристика компрессорной станции
Компрессорная станция
Производительность м3мин
Абсолютное конечное давление МПа
Установленная мощность электродвигателя кВт
Компрессорная станция расположенная на основной объекте рудника состоит из шести рабочих и двух резервных турбокомпрессоров типа
К-500-61-5. Производительность каждого компрессора 525 м3мин. рабочее давление 08 МПа.
Для механизации подъемно-транспортных работ при ремонте турбокомпрессоров используется мостовой электрический кран грузоподъемностью 205 тонн.
Компрессорная станция рудника входит в единую систему пневмоэнергетического хозяйства Талнахского промрайона.
Расход сжатого воздуха по технологическим процессам
Расход сжатого воздуха
Бурение заряжание и крепление выработок
Приготовлениеи транспорт закладочного бетона
Механизмы околоствольных дворов и дозаторных
Механизмы надшахтных здании и механические мастерские
Общий расход сжатого воздуха по руднику м3мин.
Подача сжатого воздуха к подземным потребителям осуществляется по двум магистральным воздухопроводам 600 мм проложенным в стволах КС-1 и КС-2 и одному магистральному воздухопроводу 500 мм проложенному от компрессорной до вспомогательного объекта стволов и далее по стволу ВСС.
1,3 Система разработки месторождения.doc
Для отработкизапасовбогатыхруд на руднике приняты сплошная слоеваяс параметрами очистного пространства 120м * 8м * 10м и камерная системы разработки с параметрами очистного пространства 40м * 8м * 40м с применением самоходного оборудования и закладкой выработанного пространства твердеющими смесями. Выбор применения для отработки отдельных участков месторождения вариантов сплошной системы разработки (с комбинированным или нисходящим порядком выемки слоев) а также камерной системой определяется рабочими чертежами в зависимости отконкретных горногеологических условий.
Подготовка блока очистных слоев к очистной выемке заключается в проходке транспортных штреков слоевых и разведочных ортов штреков подкровельного перекрытия и разрезных штреков а также вентиляционных восстающих и рудоспусков. Удельный объем подготовительно-нарезных работ при слоевой системе разработки на 1000тонн добычи составляет 98-104 м3 или 7.5-8.0 м проходки.
Подготовка блока очистных камер к отработке заключается в проходке транспортных штреков и фланговых уклоновтранспортно-доставочных и буровых штреков вентиляционных штреков и разрезных штреков верхней подсечки атакже рудоспусков и вентиляционных восстающих. Удельный объем подготовительно-нарезных работ при камерной системеразработки на 1000тонн добычи составляет 50-52м3 или 4.3 -4.4 м проходки.
Проходка капитальныхподготовительных нарезных и очистных вы-
работокпредусматривается буровзрывным способом. В соответствии с опытом эксплуатации рудника принят следующий удельный расход ВВ:
очистные работы- 1.9 0.3
подготовительно-нарезные работы- 2.8 0.7
Для зарядки шпуров и скважин зерногранулитом АС-8 используются
На основных и вспомогательных процессах очистной выемки и подго-товительно-нарезных работах предусматривается использование самоходного оборудования с дизельным приводом.
Для условий рудника «Таймырский» предусматривается применение сплошной слоевой системы разработки с восходящим нисходящим и комбинированным порядком выемки слоев.
Направление фронта очистных работ принято в проекте на восток от западной границы.
На очистных и проходческих работах предусмотрено применение самоходного дизельного оборудования.
Сущность сплошных систем разработки с твердеющей закладкой и особенности их применения на рудниках Талнаха.
Большая мощность перекрывающих друг друга залежей руд различного качества экономическая целесообразность первоочередной отработки сплошных (богатых) руд и необходимость сохранения вкрапленных руд для последующей их выемки обусловили управление горным давлением при очистной выемке полной закладкой выработанного пространства твердеющими смесями.
Сплошные системы разработки рекомендуется применять при отработке сильно нарушенных руд а также при выемке руд любой нарушенности на глубинах свыше 500 м.
Сплошные системы разработки характеризуются отсутствием выработанном пространстве рудных целиков воспринимающих нагрузку вне зоны защиты рудным массивом. Ширина такой зоны (защитной) в условиях рудников Талнаха лежит в пределах 40-70 м.
К классу сплошных систем разработки с твердеющей закладкой относятся:
камерно-слоевая (комбинация слоевой и камерной).
Особенности применения на рудниках Талнаха сплошных систем с твердеющей закладкой выработанного пространства заключаются в следующем:
глубина залегания рудных залежей – 150-1500 м угол падения – 3-25омощность залежей сплошных руд до 40 м;
большие площади рудных залежей;
высокая ценность сплошных руд;
сильная тектоническая раздробленность большинства рудных полей в частности рудников «Таймырский» и «Октябрьский»;
нарушенность сплошных руд и пород непосредственной почвы и кровли от весьма сильной до слабой иногда резко меняется в плане и разрезе;
потенциальная удароопасность сплошных руд и ряда вмещающих пород;
Склонность сплошных руд к слеживанию и самовозгоранию.
Сплошные слоевые системы разработки.
Исходя из горногеологических условий и принципов сплошной слоевой системы разработки горизонтальными или слабонаклонными слоями возможны три порядка выемки рудного тела по его мощности (три варианта системы):
Снизу верх (восходящий порядок выемки)
Сверху вниз (нисходящий)
Сочетание первых двух (комбинированный)
Общим для всех вариантов является разделение рудного на выемочные участки (панели) с возможным независимым ведением работ на каждом из них.
Сущность восходящего порядка выемки слоев состоит в том что рудное тело в пределах панели разделяется на вертикальные полосы – ленты которые отрабатываются слоями снизу вверх причем как правило между кровлей слоя и поверхностью закладки оставляют свободное так называемое технологическое пространство.
Восходящий порядок выемки слоев может применятся при разработке слабо- и средненарушенных руд на глубинах до 800 м. Этот вариант может применятся и в том случае если в отрабатываемой ленте встречаются участки сильнонарушенных руд длиной не более двукратной ширины ленты (очистной выработки).
Преимущества восходящего порядка выемки:
сравнительно небольшая продолжительность развития работ в панели;
возможность совмещения во времени в одной очистной выработке процессов бурения погрузки и доставки руды;
невысокие требования к прочности закладки обнажаемой только в стенке очистной выработки;
сравнительно простые схемы подготовки и проветривания.
Недостатки этого варианта:
возможность применения до определённых пролётов и глубины разработки вследствие разрушения руды в стенке очистной выработки и консольно нависающем массиве;
невозможность использования в сильнонарушенных рудах;
сравнительно невысокая производительность панели из-за ограниченного числа одновременно действующих забоев.
Сущность нисходящего порядка выемки слоёв заключается в том что рудное тело по мощности разделяют на горизонтальные (слабонаклонные) слои которые отрабатывают заходками (одновременно или последовательно) независимо друг от друга с некоторым опережением верхними нижних. Нисходящий порядок выемки слоёв может применяться при разработке руд любой нарушенности залегающих на всех глубинах.
Преимущества нисходящего порядка выемки слоёв:
возможность применения в любых горно-технических условиях;
все слои кроме первого находятся в разгруженной (надработанной) зоне;
меньшая по сравнению с восходящей выемкой изрезанность рудного массива подготовительными выработками в результате применнения слоёв большей высоты; более высокая по сравнению с восходящим порядком производительность понели за счёт возможности вовлечения в одновременную работу большего числа очистных забоев.
К числу существенных недостатков нисходящего порядка отработки слоёв относятся:
большее время (по сравнению с восходящей выемкой) для достижения максимальной производительности панели;
значительный удельный объём нарезных работ при расположении в каждой заходке разрезных штреков;
высокие требования к прочности закладки и технологии закладочных работ при формировании несущего слоя (пачки слоёв) искусственной кровли;
сложность схемы проветривания заходок.
Сущность комбинированного порядка выемки слоев заключается в том что верхний (подкровельный) слой отрабатывают с опережением а остальную часть рудного тела - аналогично варианту с восходящим порядком выемки.
Комбинированный порядок выемки слоёв может применяться при отработке слабо- и сильно нарушенных руд а также при сильно нарушенных и раздробленных породах кровли. Этот вариант можно также применять при разработке участков рудного тела в нижней части которого (в разрезе) залегают слабо- или средне нарушенные руды а в верхней – сильно нарушенные. В таком случае сильно нарушенные руды отрабатывают нисходящими слоями а надработанные слабо- или средне нарушенные руды – восходящими.
Надработкой рудного тела верхним (подкровельным) слоем расположенным как правило в наиболее нарушенных породах кровли и рудного тела очистной забой разгружается от повышенного опорного давления приводится в неудароопасное состояние призабойная часть сплошных руд и существенно уменьшается влияние прогиба пород на рудную консоль. За счёт комбинированного порядка расширяется область применения технологии восходящей выемки однако остаются недостатки этого варианта кроме первого.
Очистные работы на руднике "Октябрьскии" при отработке богатых руд ведутся с закладкой выработанного пространства твердеющими смесями. Подготовка закладочной смеси производится на поверхностном закладочном комплексе (ПЗК)размещенномна вспомогательной площадке рудника у вспомогательного закладочного ствола (ВЗС). Составы закладочныхсмесей выбираются в зависимостиот применяемых систем разработки порядков отработки слоев в соответствии с "Технологической инструкцией по производству закладочных работ на рудниках HГМК"ТH 0401.14.44-11-66-86.
В 1990 годувыполнен проектна установку 4-й мельницы 4*13.5
производительность 145 тчас таким образом общая производительность закладочного комплекса составила 550 тчас.
Режим работы закладочного комплекса:
-количество рабочих дней в году -305;
-количествосмен в сутки -3;
-продолжительность сменычас -7;
-подача закладки в подземные выработки -6 час.
Приготовление закладочной смеси производится в помольно-смесительном отделении (ПСО).
Доставка материаловна склад закладочного комплекса осуществляется по следующей схеме:
- граншлак и ангидрит - железнодорожным транспортомв думпкарах;
- цемент и щебень (песок)- автомобильным транспортом.
Приготовленная закладочная смесь поскважинам диам.273мм пробуренным с поверхности на соответствующий вентиляционно-закладочный горизонт поступает в камеру приема бетона (здесь же сооружена камера аварийного сброса бетона). Далее закладочная смесь по трубопроводам диам.273мм или 219мм проложенным по выработкам вент.-закладочного горизонта в самотечно-пневматическом режиме доставляется кучасткам очистных работ и подается в выработанное пространство. Для подачи смеси в выработанное пространство с вентиляционно-закладочного горизонтав слои пробуриваются скважины диам.150-200мм. Параллельнобетоновода по выработкам вентиляционно-закладочного горизонта прокладываются трубопроводы сжатого воздуха и воды с подключением контрольной аппаратуры.
Закладочныеработы производятся в соответствии с "Технологи-ческой инструкции по производству закладочных работ ". В зависимости от порядка выемки слоев передподачейзакладки производятся подготовительные работы:
-зачистка почвы выработки
-настилка полиэтиленовой пленки
-установка закладочных перемычек
-бурение закладочных скважин и т. д.
Выбор закладочных смесей производится в зависимости от применяемой системы разработки. Для отработкимедистых руд приняты три основных системы:
-сплошная слоевая система с нисходящим порядком выемки слоев (СH);
-сплошная камерная система разработки - "вертикальные блоки" (ВБ);
-камерная-целиковая система разработки (КЦ).
Сплошная слоевая система с нисходящим порядком выемки слоев.
Hормативнаяпрочность закладки в искусственной кровле (несущий слой 1.5-2.0 м) должна бытьне менее 6 МПав стенках заходок 1-2МПа что соответствует маркам М-80 и М-20 (прочность в возрасте 180 сутокРТР HП 17Г 62.01.02.04).
Камерно-целиковая система разработки.
Продолжительность набора прочности закладки при различной высоте
Продолжительность набора прочности суток
При мощности рудного тела более 25м первичные камеры дорабатываются подэтажами в нисходящем порядке. В этом случае в почве верхней камеры создается несущий слой из закладки марки М-80.
Сплошнаякамерная система разработки - "вертикальные блоки".
Эта система в условиях Талнахских рудниковпока не испытана и устойчивость рудных иискусственных стенок вертикальных блоков пока неизучена. Проектом предусматриваетсявозможность применения данной системыпосле промышленных испытаний. В этом случае предусматривается два варианта закладки (см. РТР HП-175 02.01.02.04.):
-монолитная закладки марки М-20 при высоте обнажения до 30м и марки М-40 при высотеобнажения до 50м;
-разнопрочная закладка слоями по 4 м марки М-20перемежаемая слоями толщиной 1 мзакладкой маркиМ-40.
Расчет производительности закладочного комплекса.
Потребный годовой объем закладочных смесейна 2001расчетный год составляет 1821540 м.куб.
Продолжительность подачи закладки в смену - 6 часов.
Годовой фонд времени на подачу закладки составит:
Т год.= 305*3*6=5490 часов.
Потребная часовая производительность закладочного комплекса:
У час.з.=18215405490=332 м.куб.час.
Объем пустот потипам руд м3
Удельный вес систем разработки по руднику "Октябрьский
Потребность марки закладки при выемке руды определенной системы
КЦ Камерно- целиковая
СH Сплошная нисходящая
КС Слоевая комбиниров
ПП Подкровельн перекр.
Распределение пустот по потребности в закладке м3
Распределение марочных объемов твердеющей закладки по закладочным
смесям на 2001 год м3
Потребность в материалах и удельный расход материалов на
рассчитанные объемы закладки
Уд. расход 2001гтм3.
Для борьбы с запыленностью и загазованностью рудничного воз духа предусматривается комплекс организационно-технических мер в соответствии с действующим на руднике проектом «Комплексное обеспылевание» который будет дополняться или пересматриваться по мере развития горных работ.
Борьба с пылью как профессиональным заболеванием обеспечивается в соответствии с требованиями пар. 686 «Единых правил безопасности » и «Санитарными правилами для предприятий по добыче и обогащению рудных нерудных и россыпных полезных ископаемых» 1987 г.
-действующие откаточные и вент-закладочные горизонты имеют пылевентиляционную службу и планы мероприятий по борьбе с пылью;
-на вновь строящиеся горизонты распространяется применение аналогичных мероприятий по борьбе с пылью;
-во всех горных и выработках и забоях на рабочих местах со- держание пыли в воздухе не должно превышать уровня ПДК - 4гм3;
-запрещается подавать в шахту и на рабочие места воздух в котором содержание пыли более 30% от установленной санитарной нормы;
-пыль со стен и кровли откаточных выработок должна периодически смываться передвижными установками;
-по всем откаточным вент-закладочным и основным подготовительным выработкам прокладывается противопожарный трубопровод используемый также для подачи воды для борьбы с пылью;
-в местах пылеобразования производится отбор проб воздуха для анализа на запыленность в соответствии с требованиями ЕПБ.
При ведении буровых взрывных и погрузочно-разгрузочных работ с горной массой выполняются следующие мероприятия по пылеподавлению:
-орошение рабочего места перед бурением на расстоянии 10-15 м;
-бурение шпуров (скважин) буровыми установками или ручными перфораторами с промывкой водой с мокрым пылеподавлением или сухим отсосом и последующим эжекционно-циклонным улавливанием пыли;
-применения гидрозабойки внешней водяной забойки из гидромешков а также установка туманообразователей (оросителей) при взрывных работах.
1,5,4 водоотл уст.doc
Откачка притока рудничных вод обеспечивается главной и вспомогательной водоотливными установками заглубленного типа. Главная водоотливная установка расположенная на гор.-800м производит выдачу воды на поверхность по трубопроводам d=350 мм (2 рабочих и 2 резервных) проложенным в стволах КС-1 и КС-2. Hасосные агрегатывспомогательной водоотливной установки расположенной на гор-950 м подают водув водосборники главной водоотливной установки. Схема водоотлива рудника предусматривает самотечное поступление рудничных вод со всех горизонтов шахт 1 и 2 в водосборники соответственно главной и вспомогательной водоотливных установок а также в связи с имеющимся запасом производительности последних прием на горизонтах -800м -950м рудничных вод перекачиваемых с горизонтов-1300м и -1050м рудника "Таймырский". Очистка водосборников принята способом взмучивания водой с откачкой образовавшейся пульпы рабочими насосами.
Для механизации монтажных транспортных и ремонтных работ в насосных камерах предусмотрено использование ручных талей специальных грузовых платформ и грузовых лебедок. Общий водоприток по руднику на период полного развития горных работ по медистым рудам с учетом остаточных водопитоков по вертикальным стволам и технологической воды от закладки выработанного пространства бурения с водой орошения выработок ожидается 3515 - 3815 м3ч из которых естественных приток подземных вод составит 55 - 65 м3ч.
Рудником не производится сброс технических вод в поверхностные водоемы. Вода поступает на очистные сооружения и часть воды расходуется поверхностным закладочным комплексом.
Баланс водопотребления и водоотведения на технологические нужды
Холодная вода питьевая в шахту
Горячая вода в шахту (промывка бункеров)
Естественный водоприток
Получено от рудника «Таймырский»
от рудника «Таймырский»
Передано шахтных вод всего
Данному водопритоку удовлетворяет насос ЦНС 300 – 780 1300.
Насос ЦНС 300 – 780 1300 предназначен для откачки нейтральных вод из шахт угольной и горнорудной промышленности при содержании механических примесей в воде не более 01 гл при размере твердых частиц 01 мм.
Согласно нормам проектирования водоотливных установок работающих в условиях малообводненных рудных месторождений насосная камера оборудуется тремя насосными агрегатами из которых один в работе один в резерве один в ремонте. По Правилам Безопасности предусматриваем установку четырех насосов.
МИН ОБР.DOC
Политехнический колледж
Зам. директора колледжа по УР
подпись инициалы фамилия
ЗАДАНИЕ НА ДИПЛОМНЫЙ ПРОЕКТ
аббревиатура учебного заведения
Содержание пояснительной записки:
Общие сведения о руднике
1. Горно-геологические условия месторождения
2. Вскрытие месторождения
3. Система разработки месторождения
4. Рудничный транспорт
5. Стационарные установки
6. Электроснабжение рудника
Проектирование скиповой подъемной установки СС-2
1. Выбор подъемных сосудов и определение концевой нагрузки
2. Расчет и выбор подъемных канатов
3. Выбор подъемной машины
4. Кинематика и динамика подъемной системы
5. Техническое обслуживание и ремонт оборудования подъемной машины
6. Правила безопасности при обслуживании электромеханического оборудования
Экономика и организация производства
1.Организация труда на участке подъема;
2.Расчет технико–экономических показателей участка;
Перечень графического материала (формат А1):
лист – Схема вскрытия и система разработки рудника «Октябрьский»
лист – Оборудование подъемной установки
лист - Схема скипового подъема СС-2
дата инициалы фамилия
дата инициалы фамилия
Проектирвание ПУ.doc
При расчете скиповой подъемной установки будем выбирать многоканатную подъемную машину т. к. одноканатные ПМ не могут обеспечить подъем грузов с заданной глубины (Нст = 1103 м) . Многоканатные подъемные установки по сравнению с одноканатными имеют следующие преимущества: возможность подъема со значительных глубин больших грузов; большая безопасность работы; диаметр каждого подъемного каната значительно меньше диаметра каната при одноканатном подъеме в связи с чем меньше диаметр органа навивки масса машины и мощность двигателя; меньше число перегибов каната герметизация копра устраняющая влияние атмосферных факторов на канаты; отсутствие крутящего момента приложенного к сосуду со стороны канатов (благодаря применению четного числа канатов и поочередное расположение канатов правой и левой свивки) что способствует уменьшению износа проводников и смягчению ударов на их стыках; нет надобности в применении парашютов в связи с малой вероятностью одновременного обрыва всех канатов.
Многоканатные подъемные машины способны обеспечить подъем полезного ископаемого с глубины до 1600 метров.
Основными параметрами механической части шахтной подъемной установки (ШПУ) являются такие величины как оптимальная масса поднимаемого груза диаметр головных и хвостовых канатов оптимальные скорость ускорение и замедление движения эффективная мощность подъема. Расчет этих параметров и выбор соответствующих изделий - задача проектирования механической части ШПУ.
Рассчитываемая скиповая подъемная установка предназначен для подъема руды со второй шахты.
Годовая производительность (Аг) одной подъемной установки при 14 часах работы в сутки и 305 дней в году с учетом коэффициента неравномерности работы подъема - 125 и коэффициента реверса подъема 11 составляет
45000 т. Глубина вертикального ствола скиповой подъемной установки Нст = 1103 м.
1. Выбор подъемных сосудов и определение концевой нагрузки
Расчетная высота подъема с учетом расположения скипов в копре и нижней части ствола:
Нр=Нст+hзагр+hразгр+2=1103+12+17+035=113235 м
где Нст - глубина вертикального ствола;
hзагр - расстояние по вертикали от отметки откаточного гори-
зонта до нижней кромки загрузочного бункера;
hразгр - расстояние по вертикали от «нулевой» отметки до верх
ней кромки приемного бункера;
Δ – расстояние от уровня разгрузочного лотка (загрузочного лотка) до приемного бункера (лотка дозатора).
Часовая производительность ШПУ:
где Ач - часовая производительность ШПУ тч;
Аг - годовая производительность ШПУ тгод;
С - коэффициент резерва производительности (с=125);
А – коэффициент реверса подъема;
nд - число рабочих дней в году;
t - время работы подъемной установки в сутки ч.
Оптимальная грузоподъемность Qопт кг при которой суммарные годовые эксплуатационные затраты на подъемной установке будут минимальными определяем по формуле для многоканатных двухскиповых подъемов:
Qопт = Ач=755=38680 кг
где Ач - часовая производительность кг;
Нр - высота подъема м;
tп - продолжительность паузы с.
Выбираем стандартный скип 2СН11-2 грузоподъемностью Qп=25т массой Qс=244т путем разгрузки h=24м.
Высота подъема с учетом высоты скипа hс=13м:
Н=Нр+hс=113235+13=114535м
Расстояние от нижней приемной площадки до оси шкива трения:
Нк=Нр+hк=113235+566 1189 м
где Н - высота подъема м;
hк= 566 - длина отвесов подъемных канатов в копре м;
2.Расчет и выбор подъемных канатов
Линейную массу каната Pк кгм определим по формуле:
где Qп и Qс - масса полезного за один раз поднимаемого груза и
собственная масса скипа кг;
sв - временное сопротивление разрыву проволок каната Нм2;
rо - условная плотность каната кгм3;
Нк - расстояние от нижней приемной площадки до оси шкива
Число подъемных канатов nк многоканатного подъема определили по формуле:
где Рк - линейная масса канатов кгм;
Dшт - диаметр шкива трения м;
jк - коэффициент зависящий от конструкции каната;
y - отношение Dшт к диаметру каната dк по ПБ для системы с
отклоняющими канатами y ³ 95.
Принимаем количество канатов nк=4.
Определим линейную массу pк одного подъемного каната:
Предварительно применим четыре каната nк=4 диаметром dк= =485мм линейной массой каната Рк=847 кгм разрывным усилием Qр=1375103Нмм2.
Проверим запас прочности канов:
Это соответствует условию:
Окончательно применим четыре каната nк=4 диаметром dк=485мм линейной массой каната Рк=847 кгм разрывным усилием Qр=1375103Нмм2.
Линейную массу gк уравновешивающих канатов определили по формуле:
где nк - количество подъемных канатов;
Рк - линейная масса подъемного каната кгм;
nук - количество уравновешивающих канатов которых по ПБ дол-
жно быть не менее двух.
Применили три стандартных плоских каната с размерами 170275мм расчетной массой gк=115кгм.
Разность линейных масс:
nкРк=nукgк 4847-3115=06 кгм
Считаем предварительно выбранную систему уравновешенной.
3.Выбор подъемной машины
Наметим к применению многоканатную подъемную машину ЦШ-54 Машины ЦШ по схемным решениям и компоновке идентичны машинам МК но конструкция их более совершенна.
Технические характеристики подъёмной машины ЦШ-54
Наименование параметра
Коренная часть машины:
Массы основных узлов подъёмной машины:
исполнительного органа тормоза т
приводных элементов кг
стоек для сборки приводных элементов кг
постаментов под подшипники т
сборки главного вала т
Ниже приведены технические характеристики подъёмной машины ЦШ-54 необходимые для дальнейших расчётов :
Диаметр канатоведущего шкива трения м5
Количество подъемных канатов4
Статическое натяжение канатов кН не более 1450
Разность статических натяжений канатов кН не более 350
Маховый момент машины без редуктора отклоняющих
шкивов и двигателя кН×м2 4900
Маховый момент отклоняющих шкивов кН×м2 500
Фактические значения статических натяжений канатов и разности статических натяжений канатов рассчитаем по формулам:
Тст max=(Qп+Qс+4РкНк)g=(19343+244103+48471189)981=824298103Н
Тст=824298103 Н(факт)1450103Н(норма);
Fст=[Qп+(4Рк-3q)Нр]g=[19343+(4847 – 3115)113235]981=182787103Н
Fст=182868103Н(факт)350103Н(норма).
Коэффициенты запаса прочности Zо и Zmin рассчитали по формулам:
Zо=== 1282 (факт) > 95 (норма)
= 66 (факт) > 45 (нор)
где Zо Zmin - фактические значения коэффициентов запаса прочнос-
Qп Qс - масса полезного груза и масса сосуда кг;
nк nук - количество подъемных и уравновешивающих канатов;
Qр - суммарное разрывное усилие всех проволок каната Н;
Рк qк - линейная масса подъемного и уравновешивающего кана-
Нк - расстояние от нижней приемной площадки до оси канатов ведущего шкива м;
lз - отвес уравновешивающих канатов в зумпфе м.
По рекомендации заводов изготовителей удельное давление канатов на футеровку канатоведущего шкива () для круглопрядных канатов не должно быть больше 20 Мпа (20 кгсм2) [6] и определяется по формуле:
Проверку по условию нескольжения канатов по шкиву трения машины производят по отношению статического натяжения гружёной ветви канатов (Т1) к натяжению порожней ветви (Т2). При этом коэффициент статических натяжений канатов (kст=Т1Т2) не должен превышать допустимый:
гдеf – коэффициент трения каната о футеровку.
Значения статических натяжений ветвей канатов предоставлены в табл. 2.3.2.
Статические натяжения ветвей канатов
Скип гружёный вверху
Скип порожний вверху
Окончательно применим многоканатную машину типоразмера ЦШ-54 четыре подъемных каната типа ЛК-З диаметром 485мм и три уравновешивающих каната размером 170275мм.
Техническая характеристика машины ЦШ-54.
Диаметр канатоведущего шкива Dш=5м;
Количество подъемных канатов nк=4;
Маховый момент машины GD2м=4900кН×м2;
Маховый момент отклоняющих шкивов GD2ош=500кН×м2;
4.Кинематика и динамика подъемной системы
4.1. Кинематика подъемной установки
Число подъемных операций в час nпч определили по формуле:
nпч=АчQп=75510338 685 = 20.
Расчетная продолжительность подъемной операции Трп определим
Трп=3600nпч=360020=180с.
Продолжительность движения подъемных сосудов Тр рассчитаем по формуле :
Тр=Трп-tп=180-10=170с
где tп - продолжительность паузы с.
Среднюю скорость подъема Vср определяем по формуле :
Vср=НрТр=113235170=67 мс
где Нр - расчетная высота подъема м.
Ориентировочную максимальную скорость подъема Vmax рассчитаем по формуле :
Vmax=acVср=13567=91 мс
где ас - множитель скорости принимаемый 115135 .
Принимаем семипериодную диаграмму скорости а1 = 1 мс2 а3 = 075 мс2 скорости V = V = 08 мс.
Ускорение и замедление скипа в разгрузочных кривых а = a² = 03 мс2.
Продолжительность t t1 движения порожнего скипа при ходе ролика его по разгрузочным кривым продолжительность t² t²1 движения груженого скипа при ходе ролика по разгрузочным кривым определим по формулам :
t=t²=Vа=Va²=0803=3 с ;
Основание трапецеидальной диаграммы скорости То соответствующее путь Но и модуль ускорения ам определим по формулам:
То=Тр-t-t1-t²1-t²+=170-3-2-2-3+=162 c
где Тр - продолжительность движения с;
t t1 t² t²1 -продолжительность движения скипа при ходе по
разгрузочным кривым с;
V и V² - скорость отхода и скорость дотяжки мс;
а1 и а3 - ускорение и замедление мс2.
Но=Нр – 2hр+=113235 – 224+=11283м
где Нр - высота подъема м;
hр - путь движения скипа в разгрузочных кривых м.
ам=а1а3(а1+а3)=1075(1+075)=043мс.
Расчетную максимальную скорость подъема Vmax определили по
Vрм=амТо-=043162 -=74 мс.
Ориентировочная частота вращения двигателя:
Фактическая максимальная скорость:
Ориентировочная мощность двигателя:
где k=11 – коэффициент учитывающий вредные сопротивления ;
r=12 13 – коэффициент динамического режима установки учитывающий динамическую нагрузку .
Намечаем к применению двигатель П2-800-256-8КУХЛ4 [10] со следую-щими параметрами:
Номинальная мощность кВт 5000
Частота вращения обмин 50
Маховый момент двигателя кН×м2 2400
Коэффициент полезного действия % hном=905
Перегрузочная способность (рабочая) lр=16
Перегрузочная способность (выключающая) lв=18
Путь отхода и путь дотяжки:
h = h = V t1= 082=16 м.
Продолжительность t1t3 и путь h1h3 движения скипа с ускорением а1 и замедлением а3 найдем по формулам :
Путь h2 и продолжительность t2 равномерного движения опрелим
h2=Нр – 2hp – h – h – h1 – h3=113235 – 224 – 16 – 16 – 84 – 1125 = 928 м ;
t2=h2Vmax=92813=71с.
Продолжительность движения Т подъемных сосудов определили по
Т=t+t1+t1+t2+t3+t²1+t²=3+2+122+71+163+2+3=110с
Фактический коэффициент резерва производительности Сф нашли
где С=125 - коэффициент резерва производительности.
Окончательно примем параметры диаграммы скоростей и ускоре-
V=V²=08мс; t=t²=3с; hp=24 м; Vma
t1=122 с; h1=84 м h = h = 16 м;
t3=163 с; h3=1125 м; h2=928 м; t2=71 с;
a=a²=03мс2; a1=1 мс2; Т=110 с; Нр=113235м;
t1=t²1=2c . a3=075 мс2
4.2. Динамика подъемной установки
Масса машины типа МК-54 mм отклоняющих шкивов mош и дви-
гателя типа П2-800-255-8КУ4 mд расчитали по формулам :
mм=GD2мgD2шт=490010398152=20103 кг ;
mош=GD2ошgD2шт=50010398152=2038 кг ;
mд=GD2дgD2шт=240010398152=9786 кг .
где GD2м GD2ош GD2д - маховые моменты машины отклоняющих шкивов
и якоря двигателя Н×м2.
Длину подъемных канатов Lпк определяем по формуле:
Lпк=Нр + 2(hк-hск) + pDшт2=113235 + 2(566 – 13) + 31452=12274 м
где Нр – расчетная высота подъема м;
hк – длина отвесов подъемных канатов в копре м;
hс – высота скипа м;
Dшт – диаметр шкива трения м.
Длину уравновешивающих канатов Lук определяем по формуле:
Lук=Нр+30=113235+30 = 116235 м
где 30 - ориентировочная длина каната на образование петли в зумпфе ствола и закрепление каната к подъемным сосудам м.
Массу mп всех движущихся частей подъемной установки приведенную к окружности шкива трения определим по формуле:
mп=Qп+2Qc+Lпк nкР+Lукnукq+mош+mм+mд=
=19343+2244103+122744847+1162353115+20103+2038+9786=
где Qп и Qc - масса полезного груза и масса скипа кг;
P и q - линейная масса подъемного и уравновешивающего кана-
Lпк и Lук - длина подъемных и уравновешивающих канатов кг;
mош mм mд - масса отклоняющего шкива машины и якоря двигателя кг.
Движущие усилия F получаем из основного динамического уравнения академика М.М.Федорова:
F=[115Qп+(Нр – 2hx)( nукq – nкP)]g ± mпа=
=[11519343+(113235 – 2hx)(3115 – 4847)]981 ± 181346103а=
=225105103 – 123hx ± 181652103a .
Эквивалентное усилие Fэк рассчитываем по формуле :
Тп=куд(t+t1+t1+t3+t²+t²1)+t2+kпtп=05(32+22+122+163)+71+02510=93 с;
куд=05 кп=025 - коэффициенты учитывающие ухудшение условий охлаждения во время соответственно ускоренного и замедленного движения;
F и t - усилие и продолжительность элементарного участка на диаграмме усилий.
=(27960062+279571322)+ (225075722+225075722250562+22505622)+
+(40670822+40568342)+ +(22403142+22403142127098+21270982)+
+(7647082+7509832)+ (21133732+2113373211319+2113192)+
+(15682342 + 156794732)= 5991911136994 Н.
Усилия на валу подъемной машины
Диаграммы движущих усилий приведены на рис.2.4.3
Коэффициент перегрузки при подъеме :
где Fmax - максимальное движущее усилие при подъеме груза Н.
Номинальную мощность двигателя Рд выбираем из условия:
Рном ³ Рэф=Nэкв===3300 кВт .
Рис.2.4.1 Диаграмма скоростей
Рис.2.4.2 Диаграмма ускорений
Рис.2.4.3 Диаграмма движущих усилий
Рис.2.4.4 Диаграмма мощностей
Окончательно примем двигатель П2-800-256-8КУХЛ4 номинальной мощностью Рном=5000кВт [14] частотой вращения nном=50обмин так как разность между эквивалентной мощностью и номинальной превышает 5% т.е.:
а перегрузка в период разгона составит:
где lдв - перегрузочная способность выбранного двигателя.
На основании оптимальной грузоподъемности при которой суммарные годовые эксплуатационные затраты будут минимальны был произведен выбор двух скипов марки 2СН11-2 грузоподъемностью 25 т. и массой 244 т.
Были выбраны четыре каната диаметром 485 мм. линейной массой каната 847 кгм и разрывным усилием 1375103Нмм2 и три уравновешивающих плоских каната размером 170275 и линейной массой 115 кгм. Все канаты проверены на запас прочности.
По расчетам была принята многоканатная подъемная машина ЦШ 5*4 со статическим натяжением канатов 1450 кН разностью статических натяжений 350 кН. Была произведена проверка на статическое натяжение и разность статических натяжений канатов.
Также была произведена проверка по удельному давлению канатов на футеровку канатоведущего шкива и проверка по условию нескольжения канатов по шкиву трения.
Произвели расчет кинематики и динамики подъемной системы проверили на коэффициент перегрузки при подъеме.
В конце расчета был подтвержден выбор электропривода постоянного тока марки П2-800-256-8КУХЛ4 номинальной мощностью 5000 кВт и частотой вращения 50 обмин он был проверен на разность эквивалентной и номинальной мощностей и на перегрузку в период разгона.
Пб.doc
6.1. Правила безопасности при обслуживании электрооборудования
Электротехнический персонал обслуживающий электроустановки должен ясно представлять технологические особенности своего предприятия знать и выполнять Правила технической эксплуатации электроустановок потребителей. Правила техники безопасности при эксплуатации электроустановок потребителей выдержки из которых приводятся ниже.
Лицо ответственное за техническую эксплуатацию электроустановок и электросетей предприятия обязано обеспечить: надежную экономичную и безопасную работу электроустановок; организацию и своевременное проведение планово-предупредительного ремонта и профилактических испытаний электрооборудования аппаратуры и сетей; наличие и своевременную проверку защитных средств и противопожарного инвентаря; организацию своевременного расследования аварий и браков
в работе электроустановок а также несчастных случаев от поражения электрическим током.
Дежурный во время своего дежурства несет ответственность за правильное обслуживание и безаварийную работу всего оборудования на порученном ему участке.
Работы в действующих электроустановках в отношении мер безопасности разбивают на четыре категории в зависимости от выполнения:
при полном снятии напряжения; при частичном снятии напряжения;
без снятия напряжения вблизи и на токоведущих частях находящихся под напряжением; без снятия напряжения вдали от токоведущих частей находящихся под напряжением.
Для подготовки рабочего места при работах с частичным или полным снятием напряжения должны быть выполнены в указанной ниже последовательности следующие технические мероприятия: производство необходимых отключений и принятие мер препятствующих подаче напряжения к месту работы из-за ошибочного или самопроизвольного включения коммутационной аппаратуры; вывешивание плакатов: "Не включать — работают люди" и при необходимости установка ограждений; присоединение к "земле" переносных заземлений и проверка отсутствия напряжения на токоведущих частях на которые должно быть наложено заземление; наложение заземлений (непосредственно после проверки отсутствия напряжения) т. е. отключение заземляющих ножей или там где они отсутствуют наложение переносных заземлений; ограждение рабочего места и вывешивание плакатов: "Стой — высокое напряжение" "Не влезай — убьет" "Работать здесь" "Влезать здесь". При необходимости производят ограждение оставшихся под напряжением токоведу-щих частей; в зависимости от местных условий установку этих ограждений выполняют до или после наложения заземлений.
Перед началом всех видов работ в электроустановках со снятием напряжения необходимо проверить отсутствие напряжения на участке работы. Проверка отсутствия напряжения между всеми фазами и каждой фазы по отношению к земле и к нулевому проводу на отключенной для производства работы части электроустановки должна быть проведена допускающим лицом после вывешивания предупредительных плакатов.
Организационные мероприятия обеспечивающие безопасность работы в электроустановках следующие: оформление работы нарядом или распоряжением; допуск к работе; надзор во время работы; оформление в наряде перерыва в работе перевода на другое рабочее место и окончания работы.
При работе без снятия напряжения вблизи токоведущих частей находящихся под напряжением должны быть выполнены мероприятия препятствующие приближению работающих лиц к этим токоведущим частям.
К числу таких мероприятий относятся: безопасное расположение работающих лиц по отношению к находящимся под напряжением токоведущим частям; организация беспрерывного надзора за работающими;
применение основных и дополнительных изолирующих защитных средств.
Работы вблизи и на токоведущих частях находящихся под напряжением должны проводиться по наряду. При этом работающие должны иметь одежду с опущенными и застегнутыми у кистей рук рукавами и головной убор.
Выводы обмоток и кабельные воронки у электродвигателей должны быть закрыты ограждениями снятие которых приводит к отвинчива-нию гаек или вывинчиванию винтов. Снимать эти ограждения во время работы электродвигателя запрещается. Вращающиеся части электродвигателей — контактные кольца шкивы муфты вентиляторы — должны быть ограждены.
Операции по отключению и включению электродвигателей напряжением выше 1000 В пусковой аппаратурой с приводами ручного управления должны производить с применением диэлектрических перчаток и изолирующего основания.
Уход за щетками их замену на работающем электродвигателе допускается проводить одному лицу оперативного персонала или специально обученному лицу с квалификационной группой не ниже III при соблюдении следующих мер предосторожности: рабочие должны остерегаться захвата одежды или обтирочного материала вращающимися частями машин; у возбудителей со стороны коллекторов и у колец ротора должны быть разостланы резиновые диэлектрические маты при их отсутствии работу должны проводить в диэлектрических галошах; запрещается касаться руками одновременно токоведущих частей различной полярности или токоведущих частей и заземленных частей машины. Должен применяться инструмент с изолированными ручками.
Кольца ротора допускается шлифовать на вращающемся электродвигателе лишь при помощи колодок из изоляционного материала.
При ремонтных работах без разборки деталей на механической части электродвигателя или механизма приводимого в движение электродвигателем последний должен быть остановлен а на ключе управления или приводе выключателя повешен плакат "Не включать - работают
Если при работах на электродвигателе или механизме ремонтный
персонал может иметь соприкосновение с их вращающимися частями то кроме выключателя отключается также разъединитель на привод которого вывешивается плакат "Не включать — работают люди" а если электродвигатель питается от ячейки комплектных распредустройств (КРУ) то тележку с выключателем выкатывают в испытательное положение.
Перед пуском электродвигателя главного привода агрегатов боль-.
шого габарита или электродвигателей управляемых с разных мест должен даваться предупреждающий звуковой сигнал.
Перед началом работы на электродвигателях приводящих в движение насосы или тягодутьевые механизмы должны быть приняты меры препятствующие вращению электродвигателя со стороны механизма (насос может работать как турбина вентилятор может начать вращаться в обратную сторону в результате засоса воздуха через всасывающий канал). Такими мерами являются закрывание соответствующих задвижек или шиберов их заклинивание или перевязка цепью с запиранием на замок (или снятием штурвала) и вывешиванием плакатов "Не открывать — работают люди".
При отсоединении от электродвигателя питающего кабеля концы
всех трех фаз кабеля должны быть замкнуты накоротко и заземлены.
В женском платье и халатах электродвигатели обслуживать запрещается. В КРУ с оборудованием на выкатываемых тележках запрещается без снятия напряжения с шин и их заземления проникать в отсеки ячеек не отделенные сплошными металлическими перегородками от шин или от непосредственно соединенного с ними оборудования.
Для производства работ на кабельных воронках и прочем оборудова- нии установленном в отсеках КРУ за выключателем тележки с выключателями следует полностью выкатывать на дверцах или на задней стенке отсека из которого выкачена тележка с выключателем вывешивать плакат "Не включать — работают люди" автоматические шторки запирать на замок на верхней шторке вывешивать плакат "Стой — высокое напряжение". После этого для доступа в отсек снимают вертикальную перегородку внутри шкафа (при расположении КРУ вплотную к стенке) или заднюю стенку (при наличии прохода между КРУ и стенкой); на кабелях по которым возможна подача напряжения проверяют его отсутствие и накладывают заземление; в отсеке вывешивают плакат "Работать здесь".
Для производства работ на оборудовании КРУ расположенном на тележках последние следует полностью выкатить и на оборудовании вывесить плакат "Работать здесь".
При производстве работ в отсеках плакат "Работать здесь" вывешивают внутри отсека. После выкатывания тележки дверцы шкафов запирают и на них вывешивают плакат "Не включать — работают люди". При отсутствии дверец запирают автоматические шторки и на них вывешивают плакат "Стой — высокое напряжение".
При производстве работ на приборах реле во вторичных цепях без выкатывания тележек с оборудованием на запертых Дверцах отсека с оборудованием или на рукоятке фиксации тележки выключателя если дверцы должны быть открыты вывешивают плакат "Не включать — работают люди"; а на месте производства работ — плакат "Работать здесь".
Для обеспечения безопасности работ проводимых в цепях измерительных приборов и устройств релейной защиты все вторичные обмотки измерительных трансформаторов тока и напряжения должны иметь постоянное заземление.
При производстве работ на трансформаторах тока или в их вторичных цепях должны соблюдаться следующие меры безопасности: шины первичных цепей не должны использоваться в качестве вспомогательных токопроводов при монтаже или токоведущих цепей при выполнении сварочных работ; присоединение к зажимам указанных трансформаторов тока цепей измерений и защиты должны проводиться после полного окончания монтажа вторичных схем; при проверке полярности приборы которыми она производится должны быть до подачи импульса тока в первичную обмотку надежно присоединены к зажимам вторичной обмотки.
Работу в цепях устройств РЗА и Т должны проводить по исполнительным схемам; работа без схем по памяти запрещается.
При работах в устройствах РЗА и Т необходимо пользоваться специальным электротехническим инструментом с изолированными ручками:
металлический стержень отверток должен быть изолирован от ручки до жала отвертки.При работах в цепях трансформаторов напряжения с подачей напряжения от постороннего источника необходимо вынуть предохранители со стороны высшего и низшего напряжений и отключить автоматы от' вторичных обмоток.
Запрещается на панелях или вблизи места размещения релейной аппаратуры проводить работы вызывающие ее сильное сотрясение грозящее ложным действием реле.
Чистку изоляции без снятия напряжения можно проводить в закрытых распредустройствах специальными щетками или пылесосами снабженными специальными изолирующими штангами.
Чистка изоляции без снятия напряжения в закрытых распредустройствах допускается при наличии в них проходов достаточной ширины позволяющих свободно оперировать пылеудаляющими средствами и должна производиться только с пола или с устойчивых подмостей.
Работу по очистке изоляции без снятия напряжения должны производить в диэлектрических перчатках.
то.doc
5.1. Техническое обслуживание и ремонт механического оборудования подъемной машины
Органы навивки коренные валы подшипники соединительные муфты. Органы навивки — барабаны и канатоведущие шкивы — несущие элементы подъемных машин воспринимающие высокие статические и динамические нагрузки. Срок службы механической части крупных подъемных машин составляет не менее 20—25 лет.
При работающей подъемной машине машинист проверяет температуру нагрева подшипников которая не должна превышать для подшипников качения 100° С а для подшипников скольжения 80° С. Шум в подшипниках при работе машины должен быть незначительным и ровным без стуков и других посторонних звуков. Не допускается также утечка смазки из подшипников.
Ежесуточно органы навивки подъемных машин должны осматривать шахтные электрослесари закрепленные за данным видом оборудования.
Наиболее простой диагностический параметр определяющий состояние органов навивки подъемных машин — скрип барабана или стук в нем появляющийся при работе машины. Причинами скрипа барабана могут быть: ослабление крепления болтов лобовины к ступице ослабление заклепок или расшатывание швов. Стук барабана во время работы может появиться из-за ослабления шпонок или износа вкладышей переставного барабана.
В многоканатных подъемных машинах осматривается пространство между ребордами канатоведущего шкива и боковыми поверхностями щитка в котором не должно быть грязи.
Ежесуточно обслуживающий персонал при остановленной подъемной машине проверяет целостность и надежность крепления защитного кожуха соединительной муфты осматривает участки валов примыкающие к муфтам. Не допускается течь смазки из муфт.
Еженедельно проверяют крепление футеровки канатоведущих шкивов многоканатных машин. Проверку производят обычно простукиванием молотком болтов и крепежных колодок.
Появление дребезжащего звука при простукивании свидетельствует о слабой затяжке болтов. Ослабленные болты освобождают от проволоки затягивают и попарно стопорят проволокой. Деформированные и срезанные болты заменяют новыми.
Ежемесячно детально осматривают металлоконструкции канатове-дущего шкива или барабана. Для этого их внутреннюю поверхность очищают От грязи и простукиванием молотком проверяют целостность обечайки колец жесткости лобовин сварных швов заклепок а также состояние и затяжку резьбовых соединений разъемных частей органа навивки. Сомнительные места осматривают при помощи лупы 7-10-кратного увеличения. Дефектные заклепки с трещинами в головке или основании и не имеющие плотного прилегания к поверхности обечайки заменяют новыми.
При эксплуатации подъемной машины важное значение имеет состояние места соединения ступицы барабана (шкива) с коренным валом. Износ вкладышей переставного барабана вызывает увеличение зазора между валом и вкладышем.
Зазор между валом и вкладышем измеряют набором щупов.
Повышенный износ вкладышей проявляется в увеличении осевого '"разбега переставного барабана. Ремонт производят подтягиванием вкладыша если это возможно либо вкладыши заменяют новыми.
В практике эксплуатации подъемных машин в частности устаревших конструкций известны случаи разрушения коренных валов в зонах напряженных шпоночных соединений. Анализом причин поломок коренных валов из-за высоких контактных давлений установлено что все разрушение происходили при больших зазорах в сопряжениях валов со ступицами. Поэтому ослабленные шпонки должны туго расклиниваться и фиксироваться а деформированные или сильно ослабленные следует заменять новыми.
Ежемесячно проверяют и смазывают зубчатую муфту. Для этого подъемную машину затормаживают предохранительным тормозом и демонтируют защитный кожух муфты. Проверяют надежность затяжки болтов. Для равномерного распределения общей нагрузки между болтами желательно чтобы все болты имели примерно одинаковый натяг. Из-за неодинакового натяга отверстия и болты изнашиваются что приводит к увеличению зазора в сопряжении и к срезанию болтов. Отверстия при этом принимают форму эллипса что требует проведения довольно сложного ремонта.
Проверку и смазку пружинной муфты производят ежеквартально. При этом проверяют степень затяжки болтов и надежность посадки ступиц на валах. Муфту периодически заполняют смазкой.
Ежеквартально проводят детальный внешний осмотр футеровки барабанов и канатоведуших шкивов. На барабанах с помощью линеек проверяют высоту футеровки от поверхности желоба до головок болтов крепящих футеровку.
Износ футеровки более чем на 13 ее высоты не допускается при этом расстояние от поверхности желобов футеровки до головок крепежных болтов должно составлять не менее 4 мм. футеровка не должна иметь треснувших тростей эллипсности по окружности навивки а также уступов по ручью между соседними тростями. Ослабевшие болты крепящие футеровку к обечайке затягивают деформированные заменяют. При этом головки новых болтов должны быть утоплены на 13 высоты футеровки. Лопнувшие или надколотые трости заменяют обеспечивая при этом их точную подгонку к смежным. Минимальный зазор между витками каната должен быть не менее 2 мм. Если вследствие износа спиральной нарезки футеровки это требование нарушено то делают соответствующую запись в Книге осмотра подъемной установки при ремонте футеровка протачивается и ручьи нарезаются вновь. При проточке футеровки следует иметь в виду что головки болтов должны быть утоплены не менее чем на 5 мм. Если толщина футеровки не допускает проточки то ее необходимо заменить.
раз в полгода производят проверку состояния и смазку подшипников качения органа навивки.
Перед выполнением данной работы порожние подъемные сосуды устанавливают в середине ствола (наперевес) а подъемная машина затормаживается. Затем вскрывают боковые крышки подшипникового узла и с помощью скребков из дерева или цветного металла удаляют засохшую смазку и грязь. Очищенные места промывают ацетоном или бензолом. Внешним осмотром проверяют состояние шариков или роликов сепараторов колец и уплотнений а также отсутствие трещин на кольцах роликах и сепараторах. Обнаруженные цвета побежалости указывают на нагревание подшипников. Смазка в подшипниковом узле должна быть чистой без признаков разложения (специфический запах клейкость) . При необходимости смазку пополняют. Если же смазка испорчена и требуется ее заменить то подшипниковый узел полностью очищают от старой смазки и промывают ацетоном или бензолом.
Характерная неисправность подшипник ов качения крупных подъемных машин — проворот внутреннего кольца подшипника относительно шейки вала. Поэтому рекомендуется на валу и внутреннем кольце подшипника наносить контрольные метки периодически наблюдая за положением которых можно установить факт проворачивания внутреннего кольца на шейке вала.
Подшипниковый узел считают исправным если при работе подъемной машины в нем слышен легкий равномерный шелест отсутствуют перемежающиеся стуки а температура не превышает допустимую.
В подшипниках скольжения с кольцевой смазкой при работе машины смазочные кольца должны вращаться а масло должно быть залито до требуемого уровня. При принудительной системе смазки указатели течения масла должны быть исправны масло в них не должно накапливаться. Не допускается течь масла в местах разъема подшипника и через уплотнения.
Ежегодно специализированные бригады наладочной организации проводят ревизию и наладку органов навивки коренного вала подшипниковой соединительных муфт подъемных машин.
Отклоняющие шкивы. В качестве отклоняющих на многоканатных подъемных установках применяют сварные шкивы с коническими лобовинами.
Целостность футеровки и состояние подшипниковых опор отклоняющих шкивов ежесменно проверяют машинисты принимающие смену а ежесуточно в ремонтную смену электрослесари. По меткам нанесенным на футеровку и обод шкива устанавливают было ли перемещение футеровки относительно шкива.
В отклоняющих шкивах устаревшей конструкции еженедельно производят смазку бронзовых втулок свободно посаженных шкивов.
Для этого порожние подъемные сосуды устанавливают наперевес машину затормаживают предохранительным тормозом и затем через тавотницы подают смазку Литол-24.
Ежемесячно отклоняющие шкивы снаружи очищают от грязи. Простукиванием молотком проверяют целостность металлоконструкции шкивов-дисков ободов колец жесткости сварных швов. Наличие дребезжащего звука при простукивании свидетельствует о наличии дефекта в металлоконструкции шкива.
Ежеквартально смазывают подшипники отклоняющих шкивов. Эту операцию выполняют в порядке аналогичном смазке подшипниковых опор подъемной машины.
Тормозные устройства подъемных машин. Тормозное устройство состоит из исполнительного органа непосредственно воздействующего на движущуюся систему подъемной машины привода создающего нужные для торможения усилия а также системы управления приводом. Для удержания подъемной машины в неподвижном положении при ремонте тормозного устройства каждая машина имеет стопорное устройство в виде форкопфа жестко связывающего барабан или канатоведущий шкив с фундаментом машины.
Тормозное устройство подъемных машин может иметь спаренный исполнительный орган с общим приводом или два самостоятельных комплекта исполнительного органа с отдельными приводами.
В зависимости от рода источника усилия тормозные приводы подъемных машин подразделяют на грузовые гидрогрузовые пружинно-гидравлические пружинно-пневматические (с тормозными грузами и без тормозных грузов) и грузопневматические.
Перед приемкой смены дежурный персонал производит внешний осмотр состояния тормозного устройства во время работы подъемной машины. При этом не должно быть вибраций тормозных колодок и тяг ход поршня цилиндра рабочего торможения должен ограничиваться отмеченными метками поставленными при ревизии и наладке. Тормозные грузы должны быть надежно закреплены а в яме под ними не должно быть воды масла или каких-либо предметов. С помощью щупов проверяют зазор между тормозными колодками и ободом который должен быть в пределах установленных в период последней наладки но не более 2 мм. Осматривают также элементы панели тормоза. Необходимо убедиться в исправной работе воздушной масленки визуальным контролем через смотровое стекло подачи масла. Исправной работе масленки соответствует подача одной капли масла за время впуска воздуха в тормозные цилиндры. При необходимости производят регулировку подачи масла.
Ежесуточное техническое обслуживание тормозных устройств включает в себя визуальный осмотр всех деталей рычажно-шарнирного механизма — тяг рычагов стоек тормозных колодок шарниров буферных пружин и др. Эти детали не должны иметь дефектов а элементы крепления надежно застопорены. Простукиванием молотком проверяют надежность крепления тормозных тяг грузов.
Тщательно осматривают и проверяют состояние рабочих поверхностей тормозных ободов барабанов и шкивов трения. При обнаружении воды или грязи рабочая поверхность тормозных ободов должна быть немедленно очищена и промыта ацетоном или бензолом. При обнаружении на тормозных ободах трещин а на их рабочих поверхностях неровностей делают запись в Книге осмотра подъемной установки и намечают меры по их устранению.
Не допускается сильный нагрев тормозного обода. Причинами этого могут быть плохая подгонка тормозных колодок неправильная регулировка исполнительного органа тормоза неполное оттормаживание машины выпуклость обода при местном его нагреве.
Проверяют зазор и равномерность его распределения по дуге между тормозными ободами и колодками при отторможенном положении машины. Для этого порожние подъемные сосуды устанавливают в середине ствола (наперевес) а барабан или канатоведущий шкив стопорится стопорным устройством. Зазор между тормозными ободами и колодками должен быть равномерно распределен по дуге охвата колодками тормозного обода а его значение должно быть не более 2 мм
Одновременно при застопоренном органе навивки проверяют исправность рабочего и предохранительного торможения. В машинах с приводами тормоза пружинно-пневматическим или пневматическим пружинно-грузовым при медленном затормаживании давление воздуха в цилиндрах рабочего торможения должно уменьшаться плавно без скачков. При оттормаживании машины давление в цилиндрах рабочего торможения и выход штока из цилиндра должны быть не ниже значений указанных в отчете по ревизии и наладке тормозные грузы должны опуститься. При пневмогрузовом приводе тормоза проверяют величину выхода поршня цилиндра рабочего торможения которая не должна превышать 120мм.
Внешним осмотром проверяют целостность воздухопроводов подводящих воздух к тормозным цилиндрам очищают от пыли и грязи шкаф и узлы панели тормоза выпускают конденсат из воздухосборника панели тормоза.
Еженедельно следует смазывать шарниры и трущиеся поверхности штоков тормозного устройства. Смазку подают специальным шприцем через тавотницы при расторможенной машине. С помощью щупа проверяют уровень масла в кольцевой выточке поршня цилиндра рабочего торможения. Уровень масла должен составлять 35—40 мм. При необходимости масло доливают.
В пневмогрузовых приводах тормозов производят продувку цилиндров. Для этого при отторможенном положении машины вывинчивают пробки из днищ цилиндров рабочего торможения и включением рабочего торможения продувают до полного удаления масла и конденсата из-под поршней.
Смазку шарниров и трущихся поверхностей штоков и поршней таких тормозных устройств производят 1 раз в две недели.
Один раз в две недели при участии главного механика или его помощника проверяют правильность работы предохранительного торможения.
Ежемесячно следует проверять электропневматический регулятор давления панели тормоза. Для этого при заторможенной машине доступ сжатого воздуха к панели тормоза перекрывается вентилем и выпускается сжатый воздух из воздухосборника панели тормоза. Регулятор давления отсоединяют от воздухопровода и производят его разборку с извлечением золотника. Тщательно осматривают внутреннюю полость корпуса регулятора а также рабочие поверхности втулки и золотника которые должны быть чистыми без царапин или задиров. Поверхности втулки и золотника смазывают. Далее отсоединяют фильтр регулятора давления разбирают и осматривают его сетки. Если сетки не имеют порывов то их промывают в ацетоне или бензоле в противном случае их заменяют новыми. Осматривают и прочищают калиброванное отверстие проверяют состояние уплотнений и дефектные заменяют новыми.
Ежеквартально необходимо проверять электромагнитный клапан тормозной системы. Произведя операции аналогичные операциям при демонтаже регулятора давления от корпуса клапана отсоединяют пневмоусилитель с электромагнитом. Промывают в керосине корпус пневмоуснлителя и золотник осматривают их рабочие поверхности. Проверяют диафрагму и в случае ее неудовлетворительного состояния заменяют. Рабочие поверхности золотника и втулки смазывают индустриальным маслом И-20А (И-25А).
С такой же периодичностью проверяют состояние воздухораспределительного клапана с электромагнитным вентилем пневмогрузового привода тормоза. При остановленной подъемной машине от воздухопровода панели тормоза отсоединяют клапан с вентилем. Клапан разбирают извлекают седло и шток с поршнем. Все элементы промывают керосином продувают сжатым воздухом и просушивают. Внешним осмотром проверяют состояние элементов клапана дефектные детали заменяют. После сборки шток должен перемещаться легко без заеданий. Затем от крышки с катушкой отсоединяют корпус электромагнитного вентиля. Извлекают верхний и нижний клапаны. Все элементы вентиля (кроме катушки) промывают в керосине продувают сжатым воздухом и просушивают. Рабочие поверхности клапанов и втулки не должны иметь царапинки раковин. После сборки верхний клапан должен перемещаться легко без заеданий.
Характеристики тормоза ухудшаются если ход поршня для выбора зазоров в шарнирах превышает 20 % от максимального хода.
Принятые методы измерения зазоров шарнирных соединений: прямой - с разборкой шарнира косвенный - щупами косвенный — специальным приспособлением и щупом.
При зазорах между валиком и отверстием превышающих допустимые производят ремонт шарнирных соединений.
Для восстановления работоспособности шарнирных соединений применяется метод основанный на использовании металлокерамических самосмазывающихся втулок (железографит ГР-3). Для установки втулок отверстия растачиваются на 10 мм (на диаметр) а диаметр валика уменьшается на 5 мм т. е. толщина новой втулки должна составлять 75 мм. Износившиеся втулки допускается растачивать до 13 их толщины а диаметр валика при этом увеличивается на такое же значение.
Надежность работы тормоза во многом зависит от состояния тормозного обода. Особенно серьезный дефект тормозного обода - эллипсность вызывающая биение и являющаяся причиной увеличения продолжительности холостого хода и времени срабатывания тормоза а также величины хода поршней тормозных цилиндров. В связи с этим необходимо периодически измерять биение тормозного обода.
На машинах находящихся в эксплуатации допускаются большие биения которые могут составлять: до 12 мм - для барабанных машин с диаметром барабана свыше 35 м и параллельным перемещением тормозных колодок до 08 мм — для остальных подъемных машин. Если биение тормозного обода вновь смонтированной машины превышает допустимые значения то обод протачивается и шлифуется с доведением чистоты поверхности не ниже 25.
В процессе эксплуатации на тормозных ободьях подъемных машин появляются трещины причина которых — усталость металла. Для устранения данного дефекта подъемные сосуды следует установить на опорные конструкции барабан разгрузить от внешней нагрузки и застопорить развести тормозные колодки. Трещину перед заваркой разделать ее крайние точки засверлить. Место сварки на барабане заземляют и подогревают до 100-150 С. Сварочный ток - постоянный марка электродов 346 Э 50 диаметром 4 и 5 мм. Электроды перед сваркой необходимо прокалить при температуре 300 "С в течение 2ч.
При необходимости замены накладного листа тормозного обода рекомендуется применять сталь 09Г2С12 или Ст. 3. Привариваемый лист крепят к ободу струбцинами с шагом 700 мм и прихватывают с двух сторон в шахматном порядке швом длиной 100 мм катетом 5 мм через каждые 300 мм. Основную обварку производят одновременно с двух сторон листа катетом 10 мм с перекрытием швов прихватки.
Система смазки подъемных машин. Современные подъемные машины имеют центральную циркуляционную систему смазки подшипников в зубчатого зацепления редуктора.
Маслосистема подъемных машин состоит из: маслонасоса резервуара фильтра вентилей маслопроводов манометров.
Ежесуточно во время работы подъемной машины проверяют состояние маслосистемы отсутствие утечек масла в местах соединения маслопровода с другими узлами. Проверяют нагрев сальников маслонасоса. Определяют разность показаний манометров установленных до и после фильтра. Увеличение разности показаний свыше 01 МПа указывает на загрязнение фильтра и его нужно промыть керосином.
. Контролируют подачу масла к местам смазки. В случае необходимости регулировкой указателей подачи масла увеличивают или уменьшают поступление масла в точки смазки.
Еженедельно в плановом порядке производят очистку фильтра маслостанции. Для этого при остановленной подъемной машине перекрывают маслопровод с обеих сторон фильтра. В пластинчатом фильтре вывинчивают пробку из стакана и рукоятку фильтра несколько раз проворачивают на полный оборот. После того как стечет грязь пробку устанавливают на место.
Аналогичная проверка выполняется 1 раз в полгода но с извлечением фильтра и промывкой его в керосине. Проверяют также состояние уплотнений дефектные заменяют новыми.
Ежегодно нужно производить замену масла. Для этого масло сливают из системы в специально подготовленные емкости. Маслопроводы продувают паром и сжатым воздухом для удаления с их стенок отложений парафина. Резервуар и картер редуктора очищают от грязи.
5.2. Техническое обслуживание и ремонт электрического оборудования подъемной машины
Электропривод подъемных машин. Для привода подъемных машин применяют асинхронный электродвигатель переменного тока и электродвигатель постоянного тока.
Асинхронный двигатель получил наибольшее распространение в угольной промышленности. Двигатель с фазным ротором разгоняют последовательным уменьшением сопротивления в роторной цепи с помощью контакторов ускорения которые своими силовыми контактами закорачивают ступени сопротивлений. При спуске груза используют генераторное торможение. При необходимости экстренного торможения может быть применено торможение противовключением. На многих установках для замедления привода применяют динамическое торможение.
Электропривод постоянного тока бывает двух видов: с электромашинным преобразователем Г — Д (генератор — двигатель) и со статическим преобразователем — тиристорным.
Электропривод подъемных машин осматривает ежесменно машинист принимающий смену. При работающем электродвигателе обращают внимание на отсутствие искрения щеток повышенной вибрации и нагрева подшипников повышенного гудения.
Ежесуточно обслуживающий персонал дополнительно проверяет чтобы при осевом разбеге вала асинхронного электродвигателя в момент его пуска между изоляционными перегородками разделяющими контактные кольца и щетками оставался зазор. Между контактными кольцами не должно быть загрязнений. Проверяют температурный режим подшипников и железа статора двигателя. Температура нагрева подшипников качения не должна превышать 100 ° С подшипников скольжения 80 °С а железа статора 75 ° С. Аналогично проверяют и электрические машины преобразовательной группы.
Еженедельно следует проверять состояние контактных колец и щеточного аппарата асинхронного электродвигателя. Щетки должны быть притерты по всей поверхности прилегания к контактным кольцам. Зазор между щеткой и щеткодержателем должен составлять 02—03 мм. Поверхности контактных колец в местах касания со щетками не должны иметь неровностей царапин и горелых мест. Не допускается попадание масла из подшипниковых узлов на токосъемное устройство. Проверяют перемещение щеток в щеткодержателях.
В двигателе постоянного тока проверяют состояние коллектора и щеточного аппарата очищают их от пыли. Поверхность коллектора должна иметь гладкий полированный вид щетки должны иметь зеркально блестящую рабочую поверхность по всей площади соприкосновения с коллектором.
Ежемесячно в электромашинах (двигателях асинхронном постоянного тока генераторе) проверяют состояние изоляции лобовых частей обмоток отсутствие повреждений стали статора ротора и якоря крепление бандажей и клиньев исправность выводов и надежность присоединения их к зажимам надежность и плотность посадки обмоток на полюсах состояние болтов крепящих полюса затяжку фундаментных и крепежных болтов наличие и состояние контрольных шпилек. Производят обдув сжатым воздухом электрических машин в следующем порядке: станина и обмотки статора обмотки ротора токосъемный аппарат. Воздух должен быть чистым и сухим а его давление — не более 02 МПа. При обдувке не рекомендуется пользоваться металлическим наконечником.
Наиболее характерная неисправность приводных асинхронных двигателей — нарушение паяных соединений обмотки ротора (так называемых "петушков"). Причины нарушения — их невысокая надежность и перегрев двигателя.
Поскольку признаком снижения надежности паяного соединения является повышение температуры его во время работы то представляет
ся возможным осуществить оперативный контроль состояния "петушков" электродвигателя с использованием серийно выпускаемых бесконтактных пирометров.
Более детальная проверка состояния приводного электродвигателя производится 1 раз в полгода. При этом с помощью щупов в четырех точках сдвинутых относительно друг друга на 90° проверяют равномерность воздушного зазора между ротором и статором. Ширина щупа должна быть не более 8 мм. При длине ротора до 600 мм измерения проводят только с одной стороны двигателя а при длине более 600 мм — с двух сторон. Если зазор хотя бы в одном месте превышает 10 % то его регулируют с помощью прокладок под лапами статора и передвижением статора по горизонтали. После регулировки зазоров проверяют центровку соединительной муфты двигателя.
Проверяют состояние заземления. Заземляющие проводники к заземляющей магистрали должны быть приварены а к корпусу двигателя — приболчены. Заземляющий контур не должен иметь механических повреждений.
Проверяют также состояние пазовых клиньев стяжных шпилек щеточного аппарата и контактных колец. Подтягивают резьбовые соединения.
Проверяют биение контактных колец значение которого не должно превышать 01 мм для колец диаметром до 300 мм и 02 мм для колец диаметром свыше 300 мм.
Биение контактных колец измеряют индикатором часового типа при отключенной машине и медленном проворачивании ротора.
Если биение превышает указанные нормы то кольца обтачивают а затем шлифуют мелкозернистым камнем. При проточке и шлифовке конгактных колец необходимо следить за тем чтобы стружка или абразивная пыль не попали внутрь машины.
Один раз в полгода смазка в подшипниках заменяется.
Аппаратура управления подъемными машинами. К аппаратуре управления относят высоковольтные реверсоры низковольтную релейно-кон-тактную аппаратуру роторные сопротивления электромашинные и магнитные усилители и др.
С помощью высоковольтных реверсоров производят дистанционное управление высоковольтными асинхронными двигателями. На шахтном подъеме применяют реверсоры типа КТР уже снятые с производства и реверсоры типа РВМ выпускаемые серийно.
Монтируемая на станциях управления электроприводами подъемной машины низковольтная электромагнитная и электрическая аппаратура имеет нормальное открытое исполнение.
На подъемных установках с асинхронным приводом в качестве пусковых сопротивлений применяют ящики сопротивлений открытого исполнения ЯС-2 (с чугунными элементами) КФ (с фехралевыми элементами) и нормального рудничного исполнения ЯС-130.
Электромагнитные и магнитные усилители применяют в схемах автоматизированных подъемных установок с асинхронным приводом и на подъемных установках с приводом Г — Д.
Для обеспечения нормальной работы аппаратуры управления подъемными машинами производят профилактический осмотр и проверку ее состояния.
Ежесменно машинист подъема проверяет работу реверсора состояние пусковых сопротивлений роторной магнитной станции и других элементов. Обращает внимание на отсутствие местного нагрева искрения или переключения ступеней четкость включения и отсутствие сильного гудения при работе контакторов.
Ежесуточно электрослесари производят осмотр высоковольтных реверсоров КТР РВМ роторных сопротивлений магнитной станции управления.
При осмотре реверсоров типа КТР проверяют отсутствие на полу посторонних предметов отсутствие пыли на изоляционных элементах механических повреждений шин дугогасительных камер сердечников и втягивающих катушек электромагнитных контакторов. При включении-отключении контакторов "Вперед-Назад" обращают внимание на отсутствие затяжного горения дуги на силовых контактах сильного свечения сбоку дугогасительных камер темных налетов или копоти на боковых поверхностях дугогасительных камер и изоляционных штанг а также других отклонений от нормальной работы.
В реверсоре типа РВМ внешним осмотром проверяют состояние шкафа очищают вентиляционные жалюзи от посторонних предметов и грязи.
При осмотре роторных сопротивлений визуально проверяют отсутствие искрения и чрезмерного нагрева элементов. Проверяют исправность изоляторов. Температура окружающего воздуха в месте установки ящиков сопротивлений не должна превышать +40 °С.
В магнитной станции управления проверяют отсутствие повреждений отсоединившихся или незакрепленных элементов станции. Обращают внимание на четкость включений и отключений контакторов и реле отсутствие дребезжания контактов затяжного горения дуги на силовых и блокировочных контактах. Гибкие соединения подвижных контактов не должны иметь изломов а в местах контактных соединений коммутационных проводов не должно быть искривлений.
Один раз в две недели электрослесари производят осмотр и проверку высоковольтных реверсоров типа РВМ. При этом проверяют наличие и исправность всех деталей магнитной системы дугогасительных камер гибких связей контактной системы силовой части и схем управления опорных подшипников и коммутационных проводов. Со всех элементов удаляют пыль и продукты ионизации.
Снимают дугогасительные камеры и удаляют пыль и копоть образующиеся на стенках. Производят обтяжку винтов стягивающих керамические плитки и асбестовые уплотнения.
Воздушный зазор между подвижным контактом и керамическими щетками при установке дугогасительных камер на место должен быть равномерным; зазор от подвижного контакта до вспомогательных рогов — в пределах 3—4 мм.
Проверяют состояние катушек магнитного дутья. При этом обращают особое внимание на наличие и исправность изоляционных прокладок между витками катушек.
Зачищают силовые контакты регулируют одновременность их прилегания проверяют провалы и усилие нажатия. Провалы определяют по зазору между кронштейном и регулировочным винтом. Провал считают нормальным если зазор составляет 15—2 мм приуменьшении его до 1 мм силовые контакты необходимо заменить. Усилие конечного нажатия силовых контактов должно быть 90-100 Н а зазор 25 ±2 мм. Изношенные контакты заменяют. Усилие пружины при нажатии на мостик блок-контактов должно быть в разомкнутом положении не более 1 Н провал — не менее 25 мм.
Ежемесячно производят детальный осмотр станции управления реверсора типа.КТР и роторных сопротивлений.
Станция управления обдувается сухим сжатым воздухом. Пластины дугогасительных камер очищаются от ионизирующего слоя и нагара. Проверяют состояние гибких связей. Зазор между средними полюсами контакторов II и III типоразмеров должен составлять 025—035 мм а контакторов IV и V типоразмеров — 01—02 мм.
При ручном включении аппаратов перемещение их должно происходить без перекосов и заеданий. Крайние полюса контакторов при втянутом якоре должны плотно прилегать друг к другу.
Проверяют надежность крепления аппаратов к панелям станции катушек контакторов и реле на сердечниках.
Проверяют состояние поверхностей прилегания якоря к сердечнику наличие и состояние немагнитных прокладок. Толщина прокладок должна быть не менее 01 мм.
Последовательно вручную замыкают магнитную систему каждого реле. Якорь реле должен легко проворачиваться а люфт якоря в притянутом положении должен быть минимальным
Если горение дуги на контактах затягивается то проверяют зазор между контактами и при необходимости увеличивают его до требуемого размера.
Проверяют последовательность срабатывания реле при подаче напряжения и отсутствие перегрева их контактов а также состояние силовых контактов реверсора его блок-контактов и дугогасительных камер удаляют с них нагар наплывы меди и потемнения от перегрева. При зачистке контактных поверхностей необходимо сохранять первоначальную их форму и снимать возможно меньший слой удаляя только наплывы до выравнивания поверхности но не до выведения раковин. После зачистки контакторы протереть ветошью.
Ход контакторов должен быть плавным без заеданий. Главные контакты должны включаться одновременно. Легкость хода контактора и одновременное прилегание контакторов проверяют путем замыкания его вручную. Зазор между подвижными и неподвижными контактами должен быть 25—30 мм.
Проверяют исправность короткозамкнутых витков на полюсах маг-нитопроводов контакторов при питании втягивающих катушек переменным током действие механических блокировок от одновременного включения контакторов "Вперед" "Назад" и "Динамическое торможение" отсутствие заеданий в шарнирных соединениях. Производят обтяжку резьбовых соединений.
Роторные сопротивления обдувают сжатым воздухом. Проверяют их исправность и обтирают сухой чистой ветошью. Проверяют исправность контактных соединений надежность крепления к каркасу ящиков сопротивлений. Подгоревшие контактные соединения ошиновки разбирают зачищают. Элементы непригодные к дальнейшей работе заменяют. Проверяют состояние коммутационных кабелей и их наконечников.
Детальную проверку высоковольтных реверсоров типа КТР и РВМ и магнитной станции управления производят также 1 раз в полгода. Для этого снимают силовые контакты и зачищают их поверхности прилегания чтобы в замкнутом состоянии они касались один другого нижними частями образуя контакт по всей рабочей ширине (не менее 80 %).
Проверяют состояние и качество крепления гибких связей. Регулируют одновременность замыкания силовых контактов. Для этого собирают электрическую схему включив последовательно с электрическими лампами силовые контакты на пониженное напряжение. На якорь нажимают вручную и следят при этом за включением ламп. Одновременность включения (загорания) ламп соответствует одновременному включению контактов. Одновременность замыкания силовых контактов регулируется винтом. Силу натяжения контактов проверяют динамометром ДПУ-002—2. Для этого необходимо при отсутствии высокого напряжения включить один из контакторов подав на его втягивающую катушку номинальное напряжение. Между силовыми контактами поместить полоски бумаги. Затем с помощью динамометра поочередно оттянуть каждый из подвижных контактов. Показание динамометра в момент когда помещенные между контактами полоски бумаги выпадут будет соответствовать конечному нажатию контактов его проверяют для всех контакторов и фаз. Конечное нажатие контактов должно быть 60—80 Н. Необходимо косвенно по зазору между кронштейном и регулировочным винтом проверять провалы силовых контактов. Указанный зазор зависит от степени износа силовых контактов при износе он уменьшается. При уменьшении зазора по сравнению с первоначальным в 2 раза контакты необходимо заменить и обеспечить первоначальные зазоры которые для контакторов типа КТР должны составлять 55—6 мм.
Измеряют сопротивление втягивающих катушек контакторов постоянному току сравнивают его с паспортными данными. Проверяют действие реле дуговой блокировки выдержка времени'которого должна составлять 10±01 с и блокировку положения дверей ограждения реверсора отключающую масляный выключатель при ее открывании. Шарнирные соединения очищают от грязи старой смазки и промывают. Проверяют состояние элементов шарниров элементы пригодные к дальнейшей эксплуатации заменяют новыми смазывают техническим вазелином. Осевой люфт в подшипниках вала якоря контактора не должен превышать 03 мм. После подачи высокого напряжения проверяют работу реверсора в общей схеме подъемной машины под нагрузкой.
В реверсоре типа РВС проверяют пакеты керамических плиток дугогасительных камер. При обнаружении темных налетов или копоти на боковой поверхности керамических плиток дугогасительную камеру заменяют.
Опробуют работу реверсора без включения высокого напряжения для этого подают напряжение на втягивающую катушку и несколько раз включают и отключают контактор. Проверяют отсутствие дребезжания якоря контактора которое происходит при отсутствии или повреждении короткозамкнутых витков на полюсах якоря питании втягивающей катушки переменным током чрезмерном (более 100 Па) нажатии силовых контактов перекосах якоря по отношению к сердечнику.
Проверяют состояние концевой заделки кабелей. При заделке их в воронки обращают внимание на отсутствие утечки компаундного заполнителя из воронки а также (во всех случаях) утечки кабельной пропитки из разделанного участка кабеля. При обнаружении течи устраняют ее и пополняют воронки компаундным заполнителем.
Проверяют действие электрической блокировки положения дверей шкафа реверсора.
В магнитной станции управления проверяют плотность прилегания якорей к сердечникам контакторов. Проверка выполняется следующим образом. Между полюсами магнитопровода помещают листы белой и копировальной бумаги. Затем вручную включают контактор и получают на белой бумаге отпечаток поверхности контакта. Плотность прилегания якорей считают удовлетворительной если отпечаток контакта занимает не менее 23 рабочей поверхности.
Проверяют также одновременность замыкания контактов всех фаз и зазоры между кронштейном и регулировочным винтом. Настраивают реле времени измеряют сопротивление изоляции релейно-контрольной аппаратуры.
Высоковольтные распредустройства служат для коммутации силовых цепей высоковольтных асинхронных приводных двигателей подъемных машин или приводных синхронных или асинхронных двигателей преобразовательных агрегатов для системы Г — Д.
Высоковольтные распредустройства типа КСО комплектуют масляными выключателями различных типов и приводами к ним разъединителями измерительными устройствами.
При ежесуточном техническом обслуживании внешним осмотром проверяют исправность разъединителя и ошиновки фарфоровых изоляторов трансформаторов тока и напряжения. В масляном выключателе проверяют исправность измерительных приборов целостность бака выключателя отсутствие течи масла исправность кабельных муфт состояние шарнирных соединений приводов целостность рукояток приводов и крепежных деталей.
Аппаратура защиты и блокировки шахтных подъемных установок. В соответствии с требованиями Правил безопасности шахтные подъемные установки оборудуют защитными аппаратами и блокировками воздействующими на отключение подъемного двигателя от сети с одновременным включением предохранительного тормоза при нарушениях режима работы установки и ошибочных действиях обслуживающего персонала.
Поскольку при нормальной работе подъемной установки аппараты защиты и блокировки не работают необходима периодическая проверка их технического состояния и функционирования.
Ежесменно машинист подъемной установки сдающий смену и машинист принимающий смену в соответствии с действующей Инструкцией для машинистов шахтных подъемных установок в специально выделенное время обязаны вдвоем проверить действие следующих аппаратов защиты и блокировки: конечных выключателей аппаратов защиты и переподъема конечных выключателей от чрезмерного износа колодок (ВИК) ограничителя скорости аварийной кнопки (АК) защиты от напуска каната защиты от потери возбуждения генератора динамического торможения или подъемного двигателя в системе Г — Д блокировку рабочего тормоза блокировку нулевого положения рукоятки управления командоконтроллером.
Ежесуточно аналогичные проверки производят электрослесари обслуживающие подъемную установку которые проверяют также блокировки — положения масляного выключателя от самовосстановления цепи защиты и системы маслосмазки; сигнализацию о выдергивании тормозных канатов из натяжных устройств; исправность защиты от проскальзывания канатов многоканатных подъемных машин (аппарат АЗП).
Правильность работы защиты один раз в две недели проверяют в присутствии главного механика или его помощника. Всякое размыкание цепи защиты должно вызывать предохранительное торможение действие которого может быть прекращено только машинистом или обслуживающим персоналом.
Для проверки работы защиты от напуска каната разгруженный подъемный сосуд устанавливают на перекрытие ствола и создается искусственный напуск каната до 15 м. При этом должен сработать предохранительный тормоз. Проверяют также исправность блокировок: включенных в цепь реверсора; предотвращающих опасность поражения электрическим током обслуживающего персонала; в цепях стволовой сигнализации. В зависимости от вида блокировки ее срабатывание должно привести к включению предохранительного тормоза или отключению масляного выключателя и реверсора.
Ежемесячно электрослесари производят осмотр и проверку исправности электрических ограничителей скорости типа РОС и ЭОС.
Для осмотра снимают крышку и кожух ограничителя скорости РОС удаляют пыль и грязь со всех доступных внутренних частей и проверяют состояние контактных соединений. Подвижные контакты должны быть надежно прикреплены к рычагам свободно перемещаться по неподвижным контактам и одновременно иметь с ними электрическую связь.
При ослаблении контактного соединения нужно подтянуть гайки окислившиеся контактные поверхности зачистить бархатным напильником и вытереть сухой ветошью. Проверяют срабатывание ограничителя скорости и включение предохранительного торможения: в случае отсутствия возбуждения в цепи одного из тахогенераторов (срабатывает реле РКН); в случае отсутствия возбуждения на обоих тахогенераторах (срабатывает реле РКВ); при изменении напряжения одного из тахогенераторов или параметров его цепей; при потере цепи или отсоединении одного из командоаппаратов от машины. Если предохранительное торможение не срабатывает хотя бы в одном случае то дальнейшая работа машины запрещается до выяснения и устранения причины отказа.
Проверяют состояние коллекторов траверс щеток щеткодержателей тахогенераторов. Удаляют с них пыль. Поверхность коллектора должна быть зеркально чистой щетки должны надежно прижиматься пружинами к коллектору.
При необходимости доливают масло в редукторы тахогенераторов и пополняют подшипники смазкой.
В электрическом ограничителе скорости типа ЭОС ежемесячно проверяют надежность затяжки клеммных зажимов и фиксирующих гаек переменных резисторов. Кроме того проверяют и при необходимости зачищают контакты реле. Один раз в полгода проверяют состояние коммутации аппаратов. Изоляция проводов должна быть целой. Провода с поврежденной изоляцией и неисправные элементы сопротивлений заменяют новыми.
Проверяют усилие нажатия подвижного контакта на неподвижный которое должно быть в пределах 5 Н. Усилие нажатия определяют на нескольких участках контактного хода пружинным динамометром со шкалой до 30 Н. Проверяют установку профилей на ретардирующих дисках. Выход ролика в точку максимальной высоты профиля должен строго соответствовать нормальному контролируемому положению подъемных сосудов.
Проверяют исправность механической передачи для привода тахо-генератора производят замену масла в редукторе. Осматривают и регулируют щеточный аппарат тахогенератора.
Указатели глубины и путевые программные устройства. Указатели глубины подъемных машин предназначены для выдачи информации о положении подъемных сосудов в стволе подачи сигнала в момент начала замедления подъемного сосуда и защиты его от переподъема.
На подъемных машинах применяют как механические так и электрические (сельсинные) указатели глубины которые конструктивно совмещают с элементами соответственно механического или электрического ограничителя скорости.
Механические указатели глубины колонкового типа снабжены двумя ретардирующими дисками на которых закрепляют профили ограничителя скорости.
Управление крупными шахтными подъемными машинами и контроль их работы осуществляют с помощью аппаратов задания и контроля ходаАЗК-1.
Функции выполняемые аппаратом АЗК-1: выдача путевых команд в отдельных точках пути движения подъемного сосуда в схему управления и защиты; измерение сельсинным указателем глубины пути пройденного подъемными сосудами; задание программы изменения скорости в каждой точке пути; контроль превышения скорости сверх допустимой; корректировка положения элементов аппарата в соответствии с действительным положением подъемного сосуда в стволе если такое соответствие по какой-либо причине нарушается.
Ежесменно машинист принимающий смену внешним осмотром сначала при остановленной подъемной машине а затем и при ее работе должен проверять состояние элементов механического указателя глубины а также соответствие показаний стрелок указателя положению подъемных сосудов. Элементы указателя глубины должны быть целыми и надежно закреплены зубчатые передачи подшипники и ходовые винты должны быть смазаны. При приемке смены осматривают и сельсинный указатель глубины. На остановленной подъемной машине проверяют соответствие показаний стрелок указателя глубины положению подъемных сосудов.
Ежесуточно указатели глубины в том же порядке осматривают электрослесари обслуживающие подъемную машину и кроме этого проверяют исправность предохранительной звуковой сигнализации. При заключительной части подъемного цикла должны последовательно подаваться два четких сигнала: первый — о необходимости начала торможения второй — о подходе сосуда к приемной площадке или начале последнего оборота органа навивки.
В механическом указателе глубины проверяют также состояние трансмиссий для его привода.
Визуально осматривают крепление шарнирных и перекидных рычагов путевых выключателей состояние программных дисков и сельсинов аппарата АЗК-1.
Еженедельно в аппаратах АЗК проверяют состояние этажных выключателей с подвижными рычагами пружин с роликами микровыключателей командоаппаратов программных дисков. Проверяют наличие смазки в приводе аппарата блоке сельсин-датчиков и в редукторах программных устройств. Масло должно находиться на уровне не выше второго деления масломера. Проверяют настройку на срабатывание путевого выключателя соответствующего истинному положению подъемных сосудов.
Ежемесячно в блоке сельсин-датчиков аппарата АЗК проверяют надежность стопорения тахогенераторов и сельсинов к корпусу. При работе подъемной машины на скорости не более 15 мс проверяют исправность кинематических цепей передачи вращения от подъемной машины к приводам путевых выключателей и блоку сельсин-датчиков.
Проверяют состояние роликов шарнирных валов и пружин возвращающих шарнирные рычаги в исходное положение. Ролики должны быть смазаны и свободно проворачиваться. Пружины которые не обеспечивают надежный возврат рычагов заменяют новыми. Зачищают контакты путевых выключателей. При необходимости пополняют маслом масленку расположенную между двигателями привода аппарата.
Один раз в полгода проверяют состояние зубчатых передач привода АЗК и блоков сельсин-датчиков редукторов программирования. Шарикоподшипники и зубчатые передачи очищают от старой смазки и смазывают заново.
Скоростемеры контрольно-измерительные приборы аппараты сигнализации и связи. Согласно ПБ каждая подъемная машина должна иметь исправно действующие самопишущий скоростемер (для машин со скоростью свыше 3 мс) вольтметр амперметр и манометры.
Скоростемеры служат для показаний и записи скорости подъема а также подачи звукового сигнала при превышении скорости.
На подъемных машинах применяют самопишущие Скоростемеры СШ-1 с сельсинным приводом или вольтметры-самописцы Н-340 со шкалой отградуированной в обмин или мс.
Контрольно-измерительные приборы служат для контроля за исправностью отдельных узлов подъемной установки и режимов ее работы. В подъемной установке контролируют: ток — статора асинхронного подъемного двигателя в двигательном режиме и режиме динамического торможения статора и возбуждения синхронного двигателя преобразовательного агрегата системы Г — Д в цепи РОС; напряжение — сети на якоре генератора динамического торможения на якоре главного генератора тахогенератора в цепях управления питания вспомогательных приводов; давление — в пневматической сети масла в гидросистеме в системе смазки.
Каждая подъемная установка должна быть снабжена устройством для
подачи сигнала от стволового к рукоятчику и от рукоятчика к машинисту а также ремонтной сигнализацией используемой при осмотре ствола.
На (Людских и грузо-людских подъемных установках кроме рабочей и ремонтной сигнализации должна предусматриваться также и резервная электрическая сигнализация с обособленным питанием. Кроме того между машинистом подъемной машины и рукоятчиком а также между рукоятчиком и стволовым должна иметься прямая телефонная связь.
В настоящее время промышленностью освоен выпуск бесконтактной системы шахтной стволовой сигнализации типа АШС. Комплект аппаратуры АШС обеспечивает стволовую сигнализацию в четырех режимах работы подъемной установки: "Люди" "Груз" "Оборудование" и "Ревизия".
При ремонте и осмотре ствола и подъемных сосудов разрешается пользоваться только ремонтной сигнализацией.
Ремонтная сигнализация осуществляется с помощью аппаратуры СШР-1. Аппаратура предназначена для передачи обслуживающим и ремонтным персоналом пяти фиксированных сигналов машинисту подъемной установки как из подъемного сосуда так и вне его а также для обеспечения двусторонней громкоговорящей симплексной связи между
этим персоналом и машинистом.
На шахтах для связи машиниста подъема с движущимся подъемным сосудом применяют также аппаратуру 1ЯВС-ЗА и АСМК-1.
Аппаратура ШВС-ЗА построена по принципу одночастотного симплекса с частотной модуляцией и представляет собой два приемопередатчика один из которых установлен в здании подъема другой — в клети. В качестве канала связи служит подъемный канат. Вызов машиниста со стороны клети осуществляется голосом а вызов сигналиста клети —фоническим сигналом.
Ежесменно машинист принимающий смену при работающей машине должен проверять исправность скоростемера наличие чернил и бумаги исправность работы контрольно-измерительных приборов аппаратуры сигнализации.
Ежесуточно осмотр и проверку работы скоростемера и аппаратуры сигнализации производят электрослесари подъема. Предварительно с помощью реле утечки проверяют исправность электрических цепей сигнализации и отсутствие утечки напряжения. Затем проверяют исправность индикаторов звуковой и световой сигнализации наличие замков на крышках колонок.
Пульты управления подъемных машин. Местное и дистанционное управление подъемными установками с крупными барабанными и многоканатными подъемными машинами имеющими электрический привод на переменном и постоянном токе осуществляется с помощью пульта управления ПШП. Для управления малыми подъемными машинами предназначен пульт ПММ-1.
Пульты ПШП изготовляют в 12 вариантах по набору сигнальной и коммутирующей аппаратуры для различных типов подъемных машин.
Функции пульта управления: управление разгоном и замедлением электрического привода подъемной установки с помощью командоап-парата; управление работой привода рабочего торможения с помощью командоаппарата; контроль за скоростью движения подъемного сосуда и его положением в стволе; сигнализация о наличии напряжения в силовых цепях с помощью сигнальных ламп; контроль тока статора в режимах — двигательном и динамического торможения; сигнализация о давлении масла в гидросистеме и цилиндре рабочего торможения; управление агрегатами динамического торможения; аварийное отключение подъемной машины.
Исправность пульта и его надежность в работе могут быть обеспечены при условии регулярного технического обслуживания его узлов и своевременного устранения неисправностей.
Машинист подъемной установки ежесменно осматривает и проверяет пульт управления.
Электрослесари при ежесуточном техническом обслуживании проверяют надежность крепления командоаппарата к площадке пульта управления и надежность действия фиксаторов положения рукоятки в промежуточном крайних и нулевом положениях. Производят также внешний осмотр всех контрольно-измерительных приборов установленных на пульте.
Ежемесячно в командоаппаратах проверяют исправность ограничителя поворота кулачков взаимодействие механизмов и узлов состояние контактов пружин и фиксаторов. Измеряют раствор контактов который должен быть в пределах 12—16 мм.
Один раз в полгода в пульте проверяют состояние и крепление всех элементов управления блокировок и защиты. Рукоятки управления должны перемещаться легко звуковой сигнал должен быть четким лампочки подсветок исправными шкала точного отсчета указателя глубины должна вращаться равномерно. Проверяют состояние контактов командоаппаратов универсальных переключателей кнопок КУ конечных выключателей. Производят обтяжку винтовых соединений коммутационных проводов в клеммных сборках. Провода с поврежденной изоляцией заменяют новыми контакты зачищают от нагара и окисления.
Аппаратура автоматизации подъемных установок. Система автоматизации должна обеспечивать надежную работу подъемной установки без постоянного присутствия обслуживающего персонала: бесперебойное выполнение операций по подъему груза и соблюдение заданной диаграммы скорости; автоматическое отключение и предохранительное торможение подъемной машины при нарушении установленного режима работы; самоконтроль системы управления.
Схема управления автоматизированной подъемной установкой предусматривает ряд защит и блокировок обеспечивающих предохранительное торможение машины. Перечень данных защит и блокировок определен ПТЭ. Проверку исправности работы защит и блокировок производят ежесуточно.
Проверяют защиту от обратного хода машины. Для этого при подъеме груза в автоматическом режиме в момент нахождения сосудов в середине ствола рукоятку командоконтроллера устанавливают в нулевое положение. После остановки машины и начала движения ее в обратную сторону должно наложиться предохранительное торможение.
Проверяют защиту от превышения заданного времени пуска и дотя-гивания. Для этого рукоятку рабочего тормоза переводят в положение "Заторможено" а рукоятку командоконтроллера — в нулевое положение. После включения реверсора с выдержкой времени определяемой уставкой защиты должно наложиться предохранительное торможение.
При остановленной подъемной машине проверяют работу аварийных кнопок установленных в положениях разгрузки загрузки и на пульте. При нажатии на кнопку должно наложиться предохранительное торможение.
Производят проверку блокировки перехода с ручного режима работы на автоматический. Для этого во время стоянки при заряженной машине рукоятку избирателя режима переводят в положение "Автоматика". При этом должен наложиться предохранительный тормоз.
Проверяют исправность аппаратуры контроля температуры подшипников. Проверка производится при остановленной машине уменьшением температурной уставки датчика до срабатывания световой и звуковой сигнализации.
Проверяют также блокировку препятствующую пуску машины при заполнении приемного бункера. Проверку изотопных реле производят отключением питания реле а реле ИКС — замыканием электрода на землю. В обоих случаях должен наложиться предохранительный тормоз.
Для проверки блокировки положения сосудов в стволе сосуды устанавливают в промежуточное положение ключ избирателя режимов переводят в положение "Автоматика" а кнопку (ручку) зарядки — в положение "Зарядка". Машина должна зарядиться в конечных положениях сосудов (точная остановка) в промежуточных же положениях машина не должна заряжаться.
Проверяют блокировку закрывания дозатора загрузки. Признак закрытия дозатора — загорание сигнальной лампы у машиниста подъема.
Специализированная бригада наладочной организации через каждые 6 мес проводит ревизию и наладку аппаратуры автоматизированных подъемных установок.
Рекомендуемые чертежи
Свободное скачивание на сегодня
- 25.10.2022