Электропривод и автоматизация скиповой подъемной установки Алтайского рудника г.Риддер




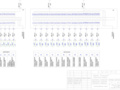
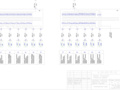
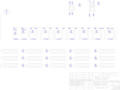
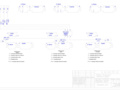
- Добавлен: 24.01.2023
- Размер: 452 KB
- Закачек: 0
Описание
Состав проекта
![]() |
![]() |
![]() ![]() ![]() |
![]() ![]() ![]() |
![]() |
![]() ![]() ![]() |
![]() ![]() ![]() |
![]() |
![]() ![]() ![]() ![]() |
![]() ![]() ![]() ![]() |
![]() ![]() ![]() ![]() |
![]() ![]() ![]() |
![]() ![]() ![]() |
Дополнительная информация
3 Безопасность и экологичность проекта (чистовик).doc
1 Техника безопасности.
1.1 Требования ПБ к подъемным установкам. Так как шахтные подъемные установки являются источником повышенной опасности то к ним предъявляются особые требования соответствующие «Правилам эксплуатации подъемных установок».
а) Подъемные машины. Отношение наименьшего диаметра навивки к диаметру каната должно быть не менее:
- для одноканатных подъемных машин со шкивом трения – 120;
- для многоканатных подъемных машин с отклоняющим шкивом – 100;
- для направляющих шкивов и барабанов подъемных машин на поверхности и многоканатных подъемных машин без отклоняющего шкива – 79;
- для направляющих шкивов и барабанов подземных подъемных машин и лебедок а также проходческих машин и лебедок – 60;
- для стационарных и передвижных аварийных подъемных машин направляющих шкивов и барабанов лебедок терриконов и откаточных лебедок – 50.
Для грузолюдских и людских подъемов на вертикальных и наклонных (выше 60О) эксплуатационных шахтах навивка каната на барабане должна быть однослойной.
Для подъемных машин грузовых вертикальных подъемов установленных на поверхности допускается двухслойная навивка канатов на барабаны.
Прикрепление каната к барабану подъемной машины должно быть выполнено таким образом чтобы при проходе каната через щель в оболочке барабана он не деформировался острыми краями щели. Запрещается прикрепление конца каната к валу барабана. Крепление концов каната к барабану производится к специально предусмотренным на барабане устройствам позволяющим закрепить канат не менее чем в трех точках.
Для ослабления натяжения каната в месте его прикрепления к барабану на поверхности барабана должно быть не менее трех витков трения при барабанах футерованных деревом или пресс-массой и не менее пяти витков трения на барабанах не футерованных фрикционными материалами. Кроме витков трения должны быть запасные витки для периодических испытаний. Запасные витки могут располагаться как на поверхности барабана так и внутри его.
Подъемные машины и лебедки должны быть снабжены аппаратом (индикатором) показывающим машинисту (оператору при дистанционном управлении) положение сосудов в стволе и автоматическим замком сигнализирующем о необходимости начала периода замедления.
Каждая подъемная установка должна быть снабжена следующими предохранительными устройствами:
- двумя концевыми выключателями установленными на копре предназначенными для выключения подъемной машины и включения предохранительного тормоза при подъеме сосуда на 05 м выше уровня приемной площадки (нормального положения его при разгрузке) и двумя концевыми выключателями установленными на указателе глубины (регуляторе подъема) и предназначенными для дублирования работы концевых выключателей установленных на копре.
Подъемные установки с опрокидными клетями должны иметь дополнительные концевые выключатели установленные на копре на 05 м выше уровня площадки предназначенной для посадки людей в клети. Работа этих концевых выключателей должна также дублироваться концевыми выключателями установленными на указателе глубины.
Дополнительные концевые выключатели (основные и дублирующие) должны быть включены в схему таким образом чтобы они включались в зависимости от поданного сигнала: "Груз" или "Люди";
- аппаратом выключающим установку при превышении нормальной скорости на 15%;
- ограничителем скорости не допускающим подхода подъемного сосуда к нормальному верхнему положению со скоростью выше 15 мсек. Для действующих грузовых подъемных установок указанная скорость не должна превышать 2 мсек.
Эти требования обязательны для подъемных установок движущихся с максимальной скоростью выше 3 мсек;
- максимальной и нулевой защитой действующей при перегрузке машины и отсутствии напряжения.
Каждая подъемная машина должна иметь исправно действующие: самопишущий скоростемер (для машин движущихся со скоростью свыше 3 мсек) вольтметр манометры показывающие давление сжатого воздуха или масла в тормозной системе. В каждой подъемной машине и лебедке должно быть предусмотрено рабочее и предохранительное механическое торможение с независимым включением привода. Указанные виды торможения могут быть осуществлены одним или двумя тормозными приводами.
Предохранительное торможение подъемной машины должно производится грузом или пружинами. Количество пружин создающих тормозное усилие. Должно быть таким чтобы при поломке одной из них тормозное усилие в целом не уменьшалось более чем на 15%.
Для грузолюдских подъемных установок с пружинными приводами обязательно наличие двух приводов. Исполнительный орган предохранительного тормоза должен быть колодочного типа и действовать на тормозные шкивы находящиеся на валу органа навивки и скрепленные с ободом этого органа.
Предохранительное торможение должно осуществляться как машинистом так и автоматически. Включение предохранительного торможения должно сопровождаться автоматическим отключением подъемного двигателя от сети.
Продолжительность холостого хода предохранительного тормоза не должна превышать для подъемных машин 05 сек. Под холостым ходом тормоза подразумевают время протекающее с момента включения предохранительного тормоза до прикосновения тормозных колодок к ободу.
Время срабатывания предохранительного тормоза (с учетом времени холостого хода) не должно превышать 08 сек. Под временем срабатывания тормоза следует понимать время протекающее с момента включения предохранительного тормоза до нарастания тормозного момента равного по величине статическому.
Главный механик шахты не реже одного раза в 15 дней должен производить проверку правильности работы предохранительного тормоза и всех выключателей против переподъема путем искусственного переподъема при замедленной скорости.
Помимо тормоза на случай регулирования положения барабанов или ремонта тормозного устройства в каждой подъемной машине должно быть предусмотрено специальное стопорное устройство.
Угол отклонения (девиации) струны каната на направляющих (копровых) шкивах и барабанах одноканатных подъемных машин не должен превышать 1О30; при бицилиндроконических барабанах допускается увеличение угла отклонения каната до 2О со стороны малого цилиндра барабана если он имеет желобчатую поверхность. Во вновь устанавливаемых одноканатных подъемных установках со шкивами трения направляющие (копровые) шкивы должны располагаться в одной вертикальной плоскости со шкивами трения.
б) Подъемные канаты. Канаты для подъемных установок всех систем должны иметь при навеске запас прочности не ниже:
– кратного для подъемных установок служащих исключительно для спуска и подъема людей;
– кратного для грузолюдских подъемных установок;
– кратного для подъемных установок служащих исключительно для спуска и подъема груза;
– кратного для аварийных подъемных установок и канатных проводников эксплуатационных шахт;
– кратного для подъемных установок со шкивами трения (людских грузолюдских и грузовых) и грузолюдских многоканатных подъемных установок;
– кратного для грузовых многоканатных подъемных установок;
– кратного от динамической нагрузки для канатов парашютов.
Запрещается применение плоских канатов на главных и вспомогательных подъемных установках.
Допускается применение плоских канатов на проходческих установках а также в качестве нижних уравновешивающих канатов на всех подъемах.
Все подъемные канаты вертикальных и наклонных шахтных подъемов за исключением канатов на только грузовых наклонных подъемах с уклоном менее 30о должны быть перед навеской испытаны на канатноиспытательных станциях зарегистрированных в МакНИИ или ВостНИИ.
Подъемные канаты за исключением канатов в установках с одноканатными и многоканатными шкивами трения и нижних уравновешивающих канатов должны повторно испытываться через каждые 6 месяцев.
Для исключительно грузовых и аварийных подъемов первое повторное испытание канатов допускается через 12 месяцев и затем через каждые шесть месяцев. Срок повторных испытаний канатов исчисляется с момента их навески.
Для испытания каната отрезают его конец длиной не менее15 м. Для повторных испытаний отрезают кусок каната над последним жимком запанцировки или клиновым регулируемым коушем длиной 15 м.
Каждый подъемный и нижний уравновешивающий канаты в установках со шкивами трения должны ежесуточно тщательно осматриваться при скорости движения не более 03 мсек. При этом определяют общее число оборванных проволок по всей длине каната. Еженедельно должен производиться дополнительный осмотр канатов при этом подсчитывается число обрывов проволок на одном шаге свивки в наиболее поврежденных местах. Участок (шаг) на котором число оборванных проволок превышает 2% общего числа проволок каната отмечают в "Книге записи осмотра подъемных канатов и их расхода".
Тормозные канаты парашютов проводниковые канаты эксплуатационных шахт и нижние уравновешивающие канаты подъемных установок с барабанными машинами осматривают еженедельно.
Ежемесячно должен производиться осмотр подъемного каната при этом его поверхность очищают от корок затвердевшей смазки и внимательно осматривают места где наиболее вероятны повреждения (под коушем жимками и т.д.) и имеется наибольшее число оборванных проволок.
Указанные места следует осматривать при неподвижном канате. Если при осмотре канатов окажется что на каком-либо участке равном шагу свивки число оборванных проволок достигает 5% общего числа проволок в подъемном канате и 10% в нижнем уравновешивающем канате то канат должен быть замене другим.
Если число оборванных проволок подъемного каната достигает на шаге свивки 5% в месте крепления его к подвесному устройству то разрешается конец каната с оборванными проволоками отрубить и снова прикрепить канат к коушу.
Подъемные канаты следует смазывать специальной канатной смазкой не реже одного раза в неделю. Перед смазкой канат должен быть очищен от грязи и старой смазки.
Для головных канатов со шкивом трения можно применять только антикоррозийную фрикционную смазку.
в) Подъемные сосуды. Клеть для людских и грузолюдских подъемов должна иметь двойную независимую подвеску. Если в качестве рабочей применяют только одну подвеску то должна быть предусмотрена другая – предохранительная. Предохранительная подвеска может быть выполнена предохранительными цепями.
Клети для спуска и подъема людей должны быть снабжены устройствами (парашютами) предназначенными для плавного торможения и остановки их в случае обрыва подъемного каната. Все шарнирные соединения парашютов необходимо систематически смазывать и свободно проворачивать. Испытания парашютов следует производить не реже одного раза в 6 месяцев.
Зазор между направляющими опорами подъемных сосудов и проводниками при их установке не должен превышать: для рельсовых проводников 5 мм и для деревянных – 10 мм на сторону. Проводники подлежат замене при износе: рельсовые – свыше 8 мм деревянные – свыше 15 мм на сторону. Износ направляющих опор клети при рельсовых проводниках допускается до 8 мм на сторону при этом суммарный износ проводника и опоры не должен превышать 10 мм на сторону.
Машинистами подъемных машин на эксплуатационных шахтах могут назначаться лица с общим производственным стажем работы на шахте не менее 3 лет а проходческих машин и лебедок – не менее одного года. Лица имеющие специальное горнотехническое образование и производственный стаж работы на шахте не менее одного года также могут назначаться машинистами подъемных машин и лебедок. Все эти лица должны предварительно пройти медицинское освидетельствование специальное обучение и сдать по утвержденной программе квалификационной комиссии экзамены на право управления подъемными машинами и иметь двухмесячный стаж по управлению подъемной машиной под руководством опытного машиниста.
Машинисты персонально утверждаются главным инженером шахты и ежегодно проходят всестороннее медицинское переосвидетельствование и проверку знаний по специальности.
г) Защитное заземление. Защитное заземление оборудования подъемных установок предназначено для защиты от поражения электрическим током рабочих обслуживающих подъемную установку. Все металлические части электрических устройств и оборудования подъемной установки которые могут оказаться под напряжением вследствие нарушения изоляции должны быть заземлены.
На подъемных установках должны быть заземлены:
- станины и кожухи электрических машин трансформаторов выключателей и других электрических аппаратов;
- приводы электрической аппаратуры:
- вторичные обмотки измерительных трансформаторов тока и напряжения;
- каркасы распределительных устройств магнитных станций управления роторных сопротивлений и других щитов управления;
- корпуса кабельных муфт металлические оболочки кабелей;
- барьеры металлические ограждения частей находящихся под напряжением металлические фермы балки площадки управления рама подъемной машины и другие металлические части доступные для прикосновения обслуживающего персонала и которые могут оказаться под напряжением.
Присоединение заземляющих проводов к корпусам электрических устройств и оборудования и к заземлителям должно осуществляться болтовыми соединениями или сваркой с обеспечением надежного контакта. От каждого заземляемого устройства должен идти отдельный провод непосредственно к заземлителю или к общей заземляющей сети соединенной с заземлителем.
Не реже одного раза в год на каждой подъемной установке должно проверяться состояние наружной части заземляющей проводки и производиться измерение сопротивления заземления которое не должно превышать 2 Ом.
После каждого ремонта оборудования необходимо проверять надежность присоединения заземляющих проводов.
д) Меры безопасности при обслуживании электрооборудования подъемной установки. При эксплуатации подъемных установок а также при проведении ремонтных и наладочных работ следует руководствоваться Правилами эксплуатации и безопасного обслуживания электроустановок промышленных предприятий.
Лица обслуживающие электротехнические устройства должны пройти обучение безопасным методам работ и проверку знаний квалификационной комиссией с отнесением их к определенной группе по технике безопасности. Персонал производящий ремонтные и наладочные работы на подъемной установке обязан иметь разрешение (удостоверение) дающее право на производство указанных работ.
При осмотрах и регулировках электрооборудования подъемной установки персонал должен пользоваться индивидуальными защитными средствами (диэлектрическими перчатками галошами изолирующими подставками и резиновыми ковриками). Инструмент должен быть с изолированными ручками.
Во время работы подъемной установки запрещается производить какие-либо действия связанные с прикосновением к вращающимся частям.
При осмотрах и наладках электрооборудования подъемной установки необходимо обращать особое внимание на исправное состояние всех блокировочных и защитных устройств предохраняющих от случайного прикосновения к токоведущим частям сторон высокого и низкого напряжения.
Для обеспечения безопасности работ на электрооборудовании подъемных установок напряжением выше 1000 В работу выполняют в такой последовательности:
- выключают масляный выключатель и вводные разъединители;
- на всех ключах управления и приводах масляных выключателей и разъединителей с помощью которых может быть подано напряжение к месту работы вывешивают плакаты "Не включать – работают люди";
- проверяют отсутствие напряжения для чего применяют указатель высокого напряжения. Непосредственно перед проверкой отсутствия напряжения должна быть проверена исправность указателя приближением его к токоведущим частям заведомо находящимся под напряжением. Проверять отсутствие напряжение необходимо на всех зажимах отключенного оборудования а у выключателей – на всех шести выводах;
- наложить заземление на отключенные токоведущие части со всех сторон откуда может быть подано напряжение. На месте работ после наложения заземления вывешивают плакат "Работать здесь".
На панелях или вблизи места размещения релейной аппаратуры запрещается производить работы вызывающие сильное сотрясение аппаратуры и могущие вызвать ложные действия схемы управления подъемной установкой.
При необходимости разрыва токовой цепи измерительных приборов и реле цепь вторичной обмотки трансформатора тока должна быть замкнута накоротко.
Работы в цепях низкого напряжения связанные с настройкой аппаратов следует производить по исполнительным схемам. Работа по памяти запрещается.
При работах в цепях трансформаторов напряжения с подачей напряжения от постороннего источника необходимо вынуть предохранители с высокой и низкой сторон и отключить коммутацию от вторичных обмоток. Реле и вспомогательные устройства по окончании ремонта и наладки должны быть запломбированы за исключением тех уставка которых меняется в зависимости от режимов работы подъемной установки.
По окончании ремонтных работ необходимо осмотреть оборудование проверить отсутствие посторонних предметов и инструмента и чистоту места где производились работы. Пуск оборудования в работу может быть произведен только после снятия переносных заземлений удаления временных ограждений и предостерегающих плакатов.
Сопротивление изоляции можно измерять только тогда когда испытуемая часть электроустановки полностью отключена. Перед началом измерения следует убедиться в отсутствии людей работающих на присоединяемой к мегомметру части электроустановки и запретить находящимся вблизи нее прикасаться к токоведущим частям во избежание несчастных случаев.
Мегомметр должен быть расположен так чтобы исключалось всякое случайное прикосновение как самого работника так и проводов прибора к частям установки находящимся под напряжением.
Перед испытанием кабелей их необходимо разрядить т.е. один конец гибкого провода присоединить к земле а второй соединить со всеми фазами кабеля. Разрядку кабеля следует производить в диэлектрических перчатках и галошах.
е) Защитные средства. На подъемной установке должны быть следующие защитные средства и инструмент: диэлектрические перчатки; диэлектрические боты; резиновые коврики; изолирующие подставки; указатель высокого напряжения; комплект переносного заземления; комплект плакатов по технике безопасности; инструмент с изолирующими ручками.
Защитные средства должны всегда быть в исправном состоянии и периодически испытываться:
- диэлектрические перчатки –один раз в 6 месяцев
-диэлектрические боты –один раз в год
-указатель высокого напряжения – один раз в год
-изолирующие штанги – один раз в год
ж) Меры безопасности при обслуживании механического оборудования подъемной установки. Машинист принимающий смену перед началом работы обязан проверить исправность машины. Спуск и подъем людей разрешается после предварительного перегона клети вхолостую. Результаты проверки подъемной машины машинист обязан занести в "Книгу приемки и сдачи смен". Обо всех замеченых повреждениях машинист подъемной машины обязан сообщить главному механику шахты.
Главный механик шахты не реже одного раза в 15 дней должен проверять правильность работы предохранительного тормоза и всех выключателей защиты от переподъема путем искусственного переподъема на замедленной скорости. Результаты проверки надо записывать в "Книгу записи осмотра подъемной установки".
Не реже одного раза в шесть месяцев каждая подъемная установка должна подвергаться ревизии и испытанию специализированной бригадой с участием главного механика шахты.
Все работы по ревизии и ремонту барабанов редукторов муфт двигателей шкивов парашютов и других узлов машины должны выполняться при заторможенной машине. Ревизию и наладку тормоза следует производить при заторможенной машине. Для этого барабаны необходимо закрепить стопорами предварительно поставив разгруженные подъемные сосуды на посадочные устройства так чтобы сосуд переставного барабана находился на верхней приемной площадке. При отсутствии посадочных устройств сосуды необходимо поставить посередине ствола в уравновешенном положении и оба барабана закрепить стопорами. Во время ревизии тормозов запрещается находиться под грузами и рычагами. Запрещается производить ремонт на ходу движущихся и вращающихся частей машины.
В здании подъемной машины должно быть хорошее освещение и исправное аварийное освещение от автономного источника питания. Смазку следует осуществлять при неработающей подъемной машине или агрегате и для смазочного материала применять специальные масленки и шприцы. Течь масла не допускается. Пролитое масло необходимо немедленно удалить обтирочными концами и опилками.
Спецодеждой служат комбинезоны. Женщинам рекомендуется носить береты (не косынки) и не работать с непокрытой головой чтобы волосы не могли быть захвачены движущимися частями механизмов.
1.2 Противопожарные мероприятия. В машинном здании должен находится комплект противопожарного инвентаря – сухие огнетушители ящик с песком лопаты и пр.; смазочные материалы следует хранить в металлических баках. Использованные обтирочные материалы надо складывать в металлические ящики. Машинист подъема должен хорошо знать противопожарные мероприятия так как при возникновении пожара внутри здания подъемной машины он должен первым принять меры.
Ручные огнетушители являются хорошим средством для быстрого тушения небольших очагов пожара особенно для тушения легко воспламеняющихся жидкостей (масла керосина).
Огнетушители могут быть жидкопенными и порошкоструйными. Жидкопенные огнетушители нельзя применять для тушения воспламенившихся обмоток электрических установок кабелей и проводов находящихся под током так как это может привести к поражению электрическим током рабочего пользующегося огнетушителем. Для этих целей применяют порошкоструйные огнетушители. Для тушения очагов пожара можно применять также сухой песок и инертную пыль. При воспламенении проводов электроустановок прежде всего необходимо отключить эту установку от сети.
Для предупреждения пожаров деревянные части здания покрывают огнезащитными красками или пропитывают их специальными составами.
Согласно требованиям ПБ устья стволов и надшахтные здания должны быть оборудованы противопожарными устройствами – спринклерными и дренчерными установками противопожарным водопроводом.
Спринклерное устройство состоит из водопроводной сети с разбрызгивающими головками располагаемыми в защищаемых местах и приводимыми в действие автоматически под действием тепла возникающего очага пожара. Дренчерные головки предназначены для защиты зданий снаружи и отличаются от спринклерных тем что подача воды из них производится не автоматически а обслуживающим персоналом после сигнала о пожаре.
На всех шахтах на поверхности следует устанавливать специальные баки.
1.3 Основные мероприятия по безопасности труда. В соответствии с ЕПБ при разработке рудных нерудных и россыпных месторождений подземным способом должна начинаться только после проведения предусмотренных проектом подготовительных и нарезных выработок необходимых для начала очистных работ осуществления мер по проветриванию и борьбе с пылью и других мероприятий.
Запрещается одновременно отрабатывать блоки расположенные один под другим по падению в двух смежных этажах входить в очистные камеры. При обнаружении признаков самообрушения работы в очистном забое должны быть приостановлены люди выведены в безопасное место оставлять выработанные камеры без закладки с незаконченной закладкой. Закладка должна производиться так чтобы не было зависания и незаложенных пустот.
До заполнения камер твердеющей закладкой во всех выпускных дучках (заездах) должны быть установлены надежные перемычки. Очистные работы в смежных с закладкой камерах могут начинаться только после набора закладкой нормативной прочности.
При отработке участков рудных тел с высоким содержанием серы необходимо осуществлять газо-температурный контроль при выпуске руды в забое и на исходящей струе воздуха из блока соблюдать строгую очередность проектной отработки слоевых заходок подэтажей и камер и полноту закладки.
После окончания закладочных работ затвердевания закладки и получения результатов контрольного бурения составляется акт искусственной кровли который утверждается главным инженером рудника.
Основными мероприятиями по борьбе с вибрацией являются:
-режимы работы подземных рабочих с продолжительностью рабочей смены не более шести часов;
-организация труда при которой рабочий в течение смены выполняет различные виды работ в том числе не связанные с вибрацией;
-применение виброзащитных кареток тросового типа виброзащитного устройства при бурении телескопными перфораторами ПТ-36;
Для снижения вредного влияния шума рекомендуется: установка на выхлопных отверстиях перфораторов глушителей шума и на вентиляторах местного проветривания ГШ-5 и ГШ-6.
Применение хвостовика буров со втулкой из синтетического материала.
Применение индивидуальных средств защиты органов: слухо-наушников пластинчатых вкладышей АШ-2 одноразового использования.
Для измерения уровня вибрации и шума рекомендуется аппаратура: глушители шума и вибрации ШИВ-1 прибор НВА-1 для измерения в широкой полосе частот шумометр малогабаритный ШМ-1.
Риддер-Сокольное месторождение с глубины 600 м отнесено к угрожаемым по горным ударам так как на этой глубине действуют высокие гравитационные напряжения а руды и породы характеризуются высокой хрупкостью и коэффициентами крепости. В соответствии с требованиями Госгортехнадзора на руднике должна быть организована служба прогноза горных ударов.
Безопасность ведения горных работ в условиях возникновения удароопасных ситуаций может быть достигнута путем снижения нагрузок на участок массива вмещающего выработку или снижения его способности к накоплению потенциальной энергии сжатия путем изменения механических свойств слагающих его пород.
Основными мероприятиями по приведению участков массива в неудароопасное состояние на локальных участках месторождений являются применение камуфлетного взрывания зарядов ВВ и бурение разгружающих шпуров и скважин диаметром 4256 и 105 мм.
Приведение в неудароопасное состояние участков массива и целиков прилегающих к ранее пройденным выработкам путем изменения механических свойств пород или снижения нагрузок на их краевую часть выполняется при невозможности разгрузки участка отработкой защитного слоя или создания разгружающей полости по кровле или почве рудного тела.
Предпосылками к применению способов снижения степени удароопасности выработок путем изменения механических свойств пород или снижения нагрузок на краевую часть массива и целиков прилегающих к ним являются:
-стреляния пород сотрясения и толчки в массиве и целиках;
-возникновение процессов интенсивного заколообразования в бортах или кровле выработок;
-отнесение выработок или их участка ко 2 категории удароопасности.
Приведение выработок и целиков в неудароопасное состояние достигается путем создания в краевой части массива или целиках прилегающих к выработке так называемой защитной зоны шириной Lз = 05 d где d – наибольший размер поперечного сечения выработки. Минимальная ширина Lз должна быть не менее 2 м. Защитная зона создается путем камуфлетного взрывания зарядов ВВ в шпурах диаметром 4256 мм или бурением строчки разгружающих шпуров без взрывания камуфлетных зарядов.
2 Экологичность проекта
Промплощадка Алтайского рудника характеризуется как чрезвычайно опасный экологический объект. По данным Министерства природных ресурсов и охраны окружающей среды горно-металлургические предприятия являются основными загрязнителями воздушного и водного бассейнов.
Существующие очистные сооружения очистки шахтных вод не обеспечивают необходимого времени контактирования с реагентом и осаждения взвешенных веществ и гидроокисей металлов.
Отсутствует система очистки сточных вод с промплощадки от нефтепродуктов.
Кроме этого происходит загрязнение атмосферного воздуха от выбросов котельной рудника в холодный период из-за отсутствия пылеулавливающих циклонов превышение ПДК на промплощадке рудника по пыли неорганической.
По системе экологического мониторинга осуществляется наблюдение за загрязненностью поверхностных вод и производятся замеры на источниках выбросов в атмосферу.
Платежи в ФОП в настоящее время осуществляются за сброс очищенных шахтных вод неочищенных сточных вод компрессорной размещение текущей горной породы и выбросы в атмосферу.
Наиболее экологически опасным объектом на промплощадке Алтайского рудника является хвостохранилище обогатительной фабрики которое введено в эксплуатацию в 1989 г.
В соответствии с утвержденным проектом в хвостохранилище складировались хвосты сульфидного и баритового циклов обогащения и пиритный концентрат. Хвостохранилище было образовано в виде трех самостоятельных чаш для каждого вида отвальных хвостов которые в соответствии с проектом обеспечивали складирование сульфидного и баритового циклов в течение 12 лет а пиритного концентрата - 5 лет.
За период с 1989-1996 гг. обогатительная фабрика не достигла проектной производительности по переработке 12 млн. тонн руды в год. В связи с этим по состоянию на апрель 1996г. заполнение хвостохранилища по объемам и отметкам отставало от проекта.
Первоначально было запроектировано хвостохранилище наливного типа по условиям крупности укладываемых хвостов.
Существующее положение по имеющимся емкостям для складирования хвостов характеризуется следующим образом:
- емкость сульфидной чаши первой очереди исчерпана;
- емкость баритовой чаши первая очередь обеспечивает складирование обшего объема хвостов образуемых в процессе обогащения в течении 3-35 лет;
- емкость пиритной чаши обеспечивает складирование общего объема хвостов в течение 1 года.
Наращивание ограждающих дамб которое производится в настоящее время до отм.2715 м обеспечивает складирование хвостов в течение 8 лет с учетом имеющихся емкостей пиритной и баритовой чаш. Общий срок эксплуатации (начиная с 1996г.) составит 12 лет.
В составе сооружений хвостового хозяйства имеется система отвода поверхностных вод с водосборной площади в бассейн р. Филиповки. Данные водосборные сооружения практически обеспечивают отвод поверхностных вод минуя территории хвостохранилища и исключая смешение с фильтрационными водами дамб хвостохранилища.
С целью охраны воздушного бассейна конструкция ограждающих дамб предусматривает покрытие откосов и гребня дамб скальными непылящими грунтами.
2.1 Охрана воздушного бассейна. Загрязнителями воздушного бассейна на руднике являются: котельная рудника бетонно-закладочный комплекс и воздуховыдающая шахта "Белкина-2". В целях снижения вредного влияния этих объектов на окружающую среду предусмотрено:
в котельной рудника - гидрозолоудаление при сжигании пылевидного топлива;
на бетонно-закладочном комплексе - оборудование пневмотранспортных систем подачи цемента в силосные башни разгрузителями-пылеуловителями;
по шахте "Белкина-2" - устройство водяных завес на квершлагах к шахте на всех горизонтах.
Характеристика хвостохранилища как источника загрязнения атмосферы
Хвостохранилище на Алтайском руднике оказывает отрицательное воздействие на атмосферу и на территорию вокруг него и сопровождается пылеобразованием. Наиболее интенсивными источниками пылеобразования является пылящая поверхность хвостохранилища
Все источники выбросов вредных веществ являются неорганизованными.
2.2 Охрана водного бассейна. В проекте предусматриваются физико-химические методы очистки шахтных вод и ливневых стоков с промплощадок шахт от взвесей нефтепродуктов и ионов тяжелых металлов. После очистки шахтные воды могут быть использованы как для приготовления твердеющей закладки так и для полива сельхозугодий.
Для хозбытовых стоков с промплощадок рудника предусматривается полная биологическая очистка в соответствии с действующими нормами и правилами.
Дополнительно вводимые в процесс подготовки закладочной смеси полуводный гипс гранулированные шлаки и сульфатно-дрожжевая бражка мало токсичны поэтому разработки и организации дополнительных мероприятий не требуется.
2.3 Анализ источников загрязнения для бетонно-закладочного комплекса. Основными источниками пылеобразования на БЗК являются:
пневмовыгрузка цемента;
доставка инертных материалов автосамосвалами и железнодорожным транспортом и погрузочно-разгрузочные работы;
доставка и загрузка инертных материалов в расходные бункера;
линия подачи материалов в мельницу;
линия подачи инертного материала в смеситель;
дробильно-сортировочный узел.
Основными путями борьбы с загрязнением атмосферы являются: надежная герметизация узлов и элементов пневморазгрузочных устройств и транспорта цемента и гипса; оснащение стационарных источников пылеобразования пылеулавливающими установками; увлажнение автодорог и пылевыделяющих поверхностей и укрытие их в кузове.
Аннотация.doc
Система Г-Д обладает широким диапазоном высокой плавностью и экономичностью при регулировании угловой скорости. Однако для создания этой системы требуются значительные капитальные вложения поскольку снижается к.п.д. установки в целом из-за троекратного преобразования энергии в электрических машинах. Эксплуатация преобразовательных агрегатов требует значительных затрат на обслуживание. Фактический расход электроэнергии увеличивается так как приводной двигатель генератора при останове двигателя подъема продолжает работать.
На основе проделанных анализов и экономических расчетов выбран более эффективный способ работающий по системе ТП-Д где для питания двигателя подъема используется установка с управляемыми статическими преобразователями. Данная система имеет более высокий к.п.д. вследствие однократного преобразования энергии меньшие размеры массу а также первоначальную стоимость позволяет автоматически регулировать скорость вращения электродвигателя подъема.
Произведено экономическое обоснование целесообразности внедрения данной системы.
2 Экономика и организация производства.doc
1 Организационно – производственная структура участка подъема
Начальник участка подъема - осуществляет контроль над работой всех служб.
Электромеханик подъема - следит за надлежащим техническим состоянием электромеханического оборудования планирует организацию ремонтов и технического обслуживания электромеханического оборудования подъема обеспечивает своевременное проведение осмотров ремонтов и испытаний энергетического оборудования и электрических сетей.
Электромеханическая служба - состоит из ремонтного и обслуживающего персонала.
Машинист подъемной установки управляет подъемной машиной следит за показаниями приборов контроля участвует в ремонтах ревизиях и наладках подъемной машины.
3 Определение капитальных вложений или инвестиций.
Капитальные вложения включают затраты на следующие цели:
- строительно-монтажные работы связанные с возведением зданий и сооружений монтажом оборудования всех видов сооружение воздушных и кабельных линий;
- приобретение машин и оборудования инструмента и инвентаря относимых к основным фондам ОПФ;
- изысканные и проектные работы.
Для этого проводим расчет.
Определим капитальные вложения до автоматизации:
К1= Коб+Кнеучет+Кзд (до авт) (2.1)
Где К1 – капитальное вложение до автоматизации;
Коб – балансовая стоимость оборудования;
Кнеучет – балансовая стоимость неучтенного оборудования;
Кзд(до авт) – стоимость здания до автоматизации.
К1= 17946200 + 5383860 + 11424000 =34754060тенге
Капитальные вложения после автоматизации рассчитывают по формуле:
К2=Коб+Кнеучет+Кзд(после авт)+Кавт (2.2)
Где Кзд (после авт) – стоимость здания после автоматизации;
Кавт – стоимость средств автоматизации.
К2= 17946200 + 5383860 + 13924000 + 2500000 = =39754060 тенге
Прирост капитальных вложений составит:
К = 39754060 – 34754060 = 5000000 тенге
Полученные данные сводим в таблицу 1.
4 Режим работы участка подъема.
Режим работы – это установленный порядок и продолжительность производственной деятельности службы во времени.
Режим работы включает в себя:
- годовой режим работы – непрерывный;
- число календарных дней в году– 365;
- число смен: 3 смены;
- продолжительность рабочего дня – 8 часов;
- продолжительность рабочей недели – 40 часов (согласно КЗОТ)
На основании принятого режима работы в соответствии с трудовым законодательством РК составляем годовой плановый баланс рабочего времени на 1 человека (таблица 2)
Определим коэффициент списочного состава.
Это отношение фонда номинального (Фном) к фонду эффективному (Фэф).
Кспис = ФномФэф (2.4)
Определяем количество смен Ксм необходимых для непрерывного надзора и управления подъемной установкой.
Ксм = Тк * 24 Фэф(р) (2.5)
где Тк – количество дней в году умноженное на 24 час в сутки – количество часов в году
Фэф(р) – эффективный фонд рабочего времени одного рабочего час.
Принимаем 4 (четыре) бригады.
На основании принятого режима работы и планового баланса рабочего времени составляем график выходов основных категорий рабочих на работу (таблица 3).
Таблица1 – Технико–экономическая характеристика ОФП
Балансовая стоимость
Синхронный двигатель
Трансформа-тор ТСЗР-2500
Неучтенное. оборудование
Здание до автоматиза-ции
Здание после автоматиза-ции
Всего после автоматиза-ции
Таблица 2 – Плановый баланс рабочего времени.
Непрерывное производство
Число календарных. дней в году Тк
Число выходных.и нерабочих .дней согласно графику сменности Твых
Твых =10 (праздн.) +
+84 (выходные по графику)
+52 (воскр) + 52 (субб)
Номинальный фонд рабочего времени Фном
Планируемые невыхода:
Экологический отпуск
Эффективный фонд. Фэф.
Фэф = Фном - план.невых
Средняя продолжительность рабочей смены
Эффективный фонд рабочего времени одного рабочего
Фэф.1рабочего= Фэф х кол-во час за смену
Фэф.1рабочего= Фэф х
Таблица – 3 – График непрерывной работы производства при 8 часовом рабочем дне
Примечание:1 смена - с 0 до 8 часов;
смена - с 8 до 16 часов;
смена - с 16 до 24 часов
5 Организация труда и заработной платы
Для выполнения производственных программ и задач стоящих перед проектируемой службой принимаем коллективную форму организации труда в виде комплексной бригады работающей на условии бригадного подряда с использованием КТУ имеющего значения от 1 до 2.
Состав работ профессии основных категорий рабочих определяем по единому тарифно-квалификационному справочному (ЕТКС)
В проекте принимаем рабочих следующих профессий
- 5 машинистов подъемной установки 5 разряда;
- 5 электрослесарей 5 разряда;
Часовые тарифные ставки принимаем по нормам предприятия:
- машинист 5 разряда – 105 тенгечас
- электрослесарь 5 разряда – 100 тенгечас
В состав работы обслуживающего персонала бригады входит: осмотр подъемной установки; управление подъемной машиной при подъеме горной массы по стволу; включение и переключение системы управления подъемной машиной; спуск – подъем скипа во время ремонтных работ; наблюдение и осмотр подъемных сосудов канатов армировки ствола оборудования дозаторных; проверка работы сигнализации защитных пусковых и контрольно-измерительных приборов; проверка работы компрессора и масляной системы подача сигналов; загрузка и разгрузка скипа.
Зарплата – это цена труда в зависимости от количества и качества труда вложенного на производство продукции. Размер оплаты труда определяется спросом и предложением труда.
Различают 3 формы оплаты труда:
Для проектируемого объекта выбираем оплату труда повременно-премиальную.
Повременно-премиальнаяя система обеспечивает единство в оплате одинакового количества труда равной квалификации при одинаковых условиях. Она включает следующие элементы:
- тарифно – квалификационный справочник;
- схемы должностных окладов руководителей ИТР и служащих.
Разрывы в оплате труда различной квалификации определяются тарифными сетками. Правильная организация зарплаты предполагает соблюдение следующих принципов:
- максимального соответствия зарплаты работника;
- количеству и качеству его труда;
- материальной заинтересованности работников в повышении результатов труда обеспечении более высоких темпов роста производительности труда по сравнению с темпами роста зарплаты как необходимого условия для расширения производства.
Основными способами организации зарплаты являются тарифная система оплаты труда и нормирования труда.
Фонд зарплаты повременщиков за проработанное время определяют умножением часовых тарифных ставок повременщиков на количество подлежащих отработке за плановый период часов.
где tc – тарифная ставка;
Т – количество отработанных часов;
Для машиниста подъема 105тг*1800=189000 тенге
Для электрослесаря100тг*1640=164000 тенге
Кроме того для работающих по беспрерывному графику проводят доплату за ночные и праздничные дни.
Фонд оплаты по труду есть основной и дополнительный.
ФОТ – состоит из тарифного заработка плюс доплата за ночные и праздничные дни плюс надбавка по повышенному коэффициенту который берется по максимуму равному 2.
Основной фонд оплаты по труду рассчитывают на списочный состав на год.
6 Планирование производства.
Планирование производства предусматривает мероприятия по внедрению систем методов организационных форм и структур управления способствующих наиболее полному выявлению и использованию внутрипроизводственных резервов сокращению численности и удешевлению содержания управленческого аппарата ликвидации непроизводительных затрат совершенствованию внутрипроизводственного планирования и расчета улучшению систем материально- технического обеспечения внедрению вычислительной техники.
6.1 Планирование численности обслуживающего персонала. Для обслуживания проектируемой подъемной установки требуются машинисты 5 разряда в количестве 4 человек и электрослесари 5 разряда в количестве 4 человек
Вся численность работников подразделяется на:
Для расчета численности необходимо знать годовой баланс рабочего времени нормативы численности нормы обслуживания.
Норматив численности – показывает минимально необходимое количество работников закрепленное для обслуживания единицы оборудования.
Определяем коэффициент списочного состава для машинистов ПУ по следующей формуле (2.4):
Ксп = Фном.маш Фэф.маш
Согласно проекту явочная численность машинистов ПУ Nяв.маш = 4 человека.
Устанавливаем списочную численность машинистов ПУ.
Nсписоч = Nяв * Ксп (2.7)
Nсписоч = 4*12 = 48 человек
Определяем коэффициент списочного состава для электрослесарей по следующей формуле (2.4):
Ксп = Фном.эл.сл Фэф. эл.сл
Таблица 4- численность работающих.
Машинист подъемной установки
Согласно графика службы графика ППР принимаем в проекте для выполнения всех ремонтных работ связанных с обслуживанием ПУ явочную численность электрослесарей Nяв.эл.сл. =4 человека.
Рассчитываем списочный состав ремонтного персонала по формуле (2.7):
Nсписоч = 4 х 122 = 49 человека.
Исходя из режима работы подъемной установки принимаем:
В смену 1 человека – машинист подъемной установки;
- человека – электрослесари ходят постоянно в одну смену с 8 до 17 часов с часовым перерывом на обед.
6.2 Планирование фонда заработной платы. На проектируемом участке подъема применяется форма оплаты труда – повременно-премиальная.
Суть формы – зарплата определяется исходя из часовой тарифной ставки соответствующего разряда и эффективного фонда рабочего времени по годовому балансу (1800 часов для машинистов ПУ и 1640 часов для электрослесарей)
Расчет планового фонда заработной платы.
Электрослесарь 5 разряда – часовая тарифная ставка 100 тенге (смена с 8 до 17 часов)
Машинист подъемной установки 5 разряда – часовая тарифная ставка 105 тенге (трехсменный график – по 8 часов за смену)
Месячный тарифный заработок машиниста подъемной установки: часовая тарифная ставка умноженная на время работы в часах в месяц
Тмес = Tc х tмес (2.8)
Тмес = 105 х 184 = 19320 тенге
Определяем тарифный фонд оплаты труда
ФОТтариф = Nсп х (Тс х tмес) х 12мес (2.9)
ФОТтариф = 5 х 19320 х 12 = 1159200 тенге
Доплата за ночные часы рассчитывается
часов24 х 50% = 167% (2.10)
Годовая доплата за ночные часы на 5 машинистов составит
Нгод = ФОТтариф х 167 100% (2.11)
59200 х 167 100% = 1935864 тенге
Годовая доплата за праздничные дни:
За 2005 год 10 праздничных дней определяем как
Пгод = 10365 х 100 = 273% от ФОТтариф (2.12)
59200 х 273100 = 3164616 тенге
Основной фонд оплаты труда за год составляет:
ФОТосн.год = ФОТтариф + доплата за ночные + +доплата за праздничные (2.13)
ФОТосн.год = 1159200 + 1935864 + 3164616 = =138443256 тенге
ФОТдоп составляет 10 % от основного фонда оплаты труда за год
ФОТдоп = 138443256 х 01 = 138443256 тенге
Тогда фонд заработной платы годовой составит:
Σ ФЗПобщ = ФОТосн.год + ФОТдоп (2.14)
Σ ФЗПобщ = 138443256 + 138443256 = =1522875816тенге
Фонд заработной платы с учетом надбавочного коэффициента Кнад = 2 (КТУ) составляет:
ФЗПк = Σ ФЗПобщ х Кнад (2.15)
ФЗПк = 1522875816 х 2 = 3045751632 тенге
Месячная зарплата на одного машиниста составит :
ЗПмес = Σ ФЗПобщ х Кнад (Nсп х 12мес) (2.16)
ЗПмес =3045751632 (5 х 12) = 507625272 тенге
Для электрослесаря- ремонтника 5 разряда зарплата рассчитывается аналогично дежурного оператора (таблица 5) кроме следующих пунктов:
- ночные часы отсутствуют т к режим работы с 8 до 17 часов.
- праздничные дни не оплачиваются т к в эти дни бригада отдыхает.
Таблица 5 - Расчет планового фонда зарплаты
Количество часов работы
Σ ФЗПобщ с учетом надбавки
Месячная зарплата на одного рабочего
ИТОГО Фонд Оплаты Труда общий: 5 368 951 тенге
7 Планирование эксплутационных затрат.
Накладные расходы – это расходы связанные с обслуживанием производства. Состав накладных расходов для разработанного проекта рассчитываем так:
Рассчитаем затраты на материалы и сырье Возьмем 8% от стоимости оборудования (табл 1)
- до автоматизации: 34754060 · 008=27803248тенге
-после автоматизации:39754060·008=31803248тенге
Рассчитаем энергозатраты.
Так как в проекте предусмотрена замена системы Г-Д на систему ТП-Д то расчет энергозатрат сводим к сравнению потребления электроэнергии различными системами. Система Г-Д отличается тем что при останове двигателя подъема электроэнергия продолжает потребляться приводным двигателем генератора. А при системе ТП-Д тиристорный преобразователь во время останова двигателя подъема работает на холостом ходу.
Получаем энергозатраты при работе по системе Г-Д:
Wа = ΣР х nдн х nч (2.17)
где ΣРГ-Д = 2000 + 250 = 2250 кВт – суммарная мощность потребителей;
00 – мощность двигателя кВт;
0 – мощность трансформатора собственных нужд кВт
nдн = 304 дня – число рабочих дней в году;
nч = 24 – число часов работы в сутки.
WаГ-Д = 2250 х 304 х 24 = 16 416 000 кВтчгод
Рассчитаем затраты на электроэнергию при цене 1кВтч= 16 тенге (по данным предприятия):
S Г-Д = WаГ-Д 16 (2.18)
S Г-Д = 16 416 000 16 = 26 265600 тенге в год.
При работе по системе ТП-Д получаем следующие энергозатраты:
ΣРТП-Д = 1600 + 250 = 1850 кВт – суммарная мощность потребителей
где 1600 – мощность тиристорного преобразователя кВт;
nч = 16 – число часов работы в сутки (3 и 1 смена)
Wа ТП-Д = 1850 304 16 = 8 998 400 кВтчгод
Затраты на электроэнергию составят:
SТП-Д =8 998400 16 = 14 397 440 тенге в год.
Сравним расходы на электроэнергию двух систем
S Г-Д = 26 265600 тенге в год > SТП-Д = =14397440тенге в год
Экономия электроэнергии составит около 12 млн. тенге в год
Затраты на основную и дополнительную зарплату(ФОТобщ) составят
689516 тенге (таблица 5).
Рассчитаем отчисления от зарплаты (социальный налог) который составляет 20 % от ФОТобщ
689516 02 = 107379032 тенге
Рассчитаем общие производственные затраты (комплексные)
1 амортизация оборудования (таблица 1)
- до автоматизации 1390162 тенге;
- после автоматизации 1490162 тенге.
2 текущий ремонт который составит 8% от величины амортизации
- до автоматизации 1390162 008 = 11121296 тенге;
- после автоматизации 1490162 008 =11921296 тенге.
3 содержание оборудования которое составляет 4% от стоимости оборудования (таблица 1)
-до автоматизации 34754060 004 =13901624 тенге;
-после автоматизации39754060004=15901624тенге.
4 охрана труда составляет 10% от ФОТобщ
20349 01 = 5820349 тенге
5 прочие расходы составляют 8%от суммы предыдущих затрат (5.1-5.4)
ΣЗатрат1 = 1390162 + 11121296 + 13901624 + +5820349 = 347357226 тенге
7357226 008 = 2778857 тенге
- после автоматизации
ΣЗатрат2 = 1490162 + 11921296 + 15901624 + +5820349= = 372757226 тенге
2757226 008 = 2982057808 тенге
Итог по общепроизводственным затратам до автоматизации составил
7357226 + 2778857808 = 3 751 45804 тенге;
Итог по общепроизводственным затратам после автоматизации составил
2757226 + 2982057808 = 4 025 77804 тенге
Составим таблицу накладных расходов (таблица 6)
Таблица 6 - Накладные расходы
Наименование статей затрат
Материальные затраты
Энергетические затраты
Основная и дополнительная зароботная плата
Отчисления на социальный налог
Общепроизводствен-ные затраты
8 Экономическая оценка вариантов проектируемых решений.
Так как проектом предусмотрено внедрение средств автоматизации то необходимо рассмотреть и определить экономическую эффективностью от нее.
Для этого необходимо сделать сравнение капитальных вложений и эксплуатационных затрат.
Экономическая эффективность- Е рассчитывается по формуле:
К1- капитальные вложения до автоматизации;
К2-капитальные вложения после автоматизации;
С1- сумма эксплуатационных затрат до автоматизации;
С2- сумма эксплуатационных затрат после автоматизации;
Производим расчет согласно формуле (2.20)
ΔК = 39754060 – 34754060 = 5000000 тенге
Эс=С1-С2=3924012476–2777196476=11468160 тенге – получена за счет снижения расхода электроэнергии в результате внедрения автоматизации.
Е=ЭсΔК = 5000000 11468160= 044 > Ен=033
Тр = 1044 = 23 года.
9 Технико-экономические показатели.
В состав технико – экономических показателей входят:
- стоимость капитальных вложений;
- численность работников;
- среднемесячная зарплата;
- эксплутационные затраты.
Данные берем из рассчитанных по данному проекту значений и сводим их в таблицу 7.
Таблица 7- Технико – экономические показатели.
Капитальные вложения
Численность работников:
Общий фонд зарплаты ОФП
Эксплутационные затраты
ИТОГО:7936313576 7289497576
Общая экономия от внедрения системы ТП-Д составит около 65 млн. тенге в год.
1 Введение.Основной раздел.doc
Шахтные подъемные установки предназначены для выдачи на поверхность полезного ископаемого быстрого и безопасного спуска и подъема из шахты людей транспортировки крепежного леса горно-шахтного оборудования и материалов. При помощи подъемной установки производят также осмотр и ремонт армировки и крепления ствола шахты.
Основным и самым сложным элементом скиповой ПУ является подъемная машина которая находится в машинном отделении и с помощью подъемного каната производит подъем скипа по стволу шахты на поверхность где руда разгружается в бункер обогатительной фабрики. Подъемный канат проходит через шкив находящийся на копре. Под землей скип загружается с вагоноопрокидывателя через мерный ящик.
На крупных современных шахтах всегда имеется две – три действующие подъемные установки при этом каждая из них выполняет свои особые функции (выдачу руды спуск-подъем людей выдачу породы и т.д.) а не являются резервом другой. Это придает большое значение подъемным установкам во всем комплексе электромеханического оборудования шахт и предъявляет к ним особые требования в отношении надежности и безопасности работы. От надежной бесперебойной и производительной работы шахтного подъема зависит ритмичная работа всей шахты в целом.
Электропривод подъемных установок потребляет до 40% (иногда до 50%) всей электроэнергии расходуемой шахтой. Подъемные машины устанавливаются на весь срок эксплуатации шахты.
Подъемные установки разделяются:
по назначению: на главные или грузовые (для транспортировки руды) вспомогательные или грузо-людские (для транспортировки породы материалов и оборудования а также спуска и подъема людей); людские (только для спуска и подъема людей);
по типу ствола шахты: на вертикальные и наклонные;
по типу органов навивки подъемных канатов: на машины с постоянным радиусом навивки (с цилиндрическими барабанами или ведущим шкивом трения) и бицилиндроконические.
1.2 Краткие сведения о руднике. Разработка Лениногорской группы месторождений началась с открытия Риддерского месторождения которое было обнаружено в 1784 году офицером горного корпуса Филиппом Риддером. После Риддерского были обнаружены Крюковское Филипповское и Сокольное месторождения.
Добыча свинцово-серебрянных руд на Риддерском месторождении велась с момента его открытия до 1862 года. На Сокольном месторождении в этот период велась только разведка. В связи с общим упадком горного дела после 1862 года работы на месторождении почти не велись. До 1903 года проводились лишь добыча и промывка золотосодержащих кварцев и глин. С 1903 года по 1914 год добычные работы были почти полностью прекращены. Риддерский рудник в это время принадлежал австрийской концессии «Турни-Таксис» которая затем перепродала его Федорову и Таманову. Последние в этом же 1914 году перепродали рудники английскому концессионеру Лесли Уркарту.
В 1916 году Риддерский рудник был законсервирован и работы переместились на Сокольное месторождение где отрабатывались богатые сплошные сульфидные руды и велась разведка. В 1918 году после Октябрьской революции работы на руднике были прекращены часть оборудования была снята и рудники заброшены. В 1921-1923 годах в советском Правительстве шла дискуссия какие месторождения отдать в концессию. Риддерские рабочие предложили собственными силами восстановить рудники. После решительной поддержки В.И.Лениным лично инструктировавшего первого директора в 1925 году был организован комбинат «Риддер-золото» который начал восстановление хозяйства и незначительные разведочные работы. С 1930года разведочные работы значительно расширены. Эксплуатация велась в эти годы в основном на Риддерском руднике. Богатые места Сокольного месторождения подготавливались к отработке а первый план добычи был дан в 1938 г. С 1952 года отработку юго-западного фланга Сокольного месторождения ведет выделенный из Сокольного рудника Быструшинский рудник который сейчас носит название «40 лет ВЛКСМ».
В октябре 1959 года у деревни Познапаловка Лениногорская геологоразведочная экспедиция обнаружила месторождение богатых полиметаллических руд названное позднее Тишинским.
В 1961 году после утверждения запасов Государственной комиссией на базе этого месторождения прошли шахту РЭШ для проведения геологоразведочных работ и попутной добычи руды. В том же году началось строительство карьера – первой очереди Тишинского рудника. Директором строящегося рудника был назначен горный техник А.Е.Михайленко.
Риддерский горно-обогатительный комплекс в состав которого входят: рудник - Тишинский обогатительная фабрика и вспомогательные цеха;
Зыряновский горно-обогатительный комплекс в состав которого входят 2 рудника (Малеевский и Греховский) обогатительная фабрика и ряд вспомогательных производств;
Текелийский горно-обогатительный комплекс в его составе:
Текелийский рудник обогатительная фабрика и ряд вспомогательных производств;
Металлургическое производство включающее Усть-Каменогорский цинковый Усть-Каменогорский свинцовый Риддерский цинковый заводы а так же вспомогательные цеха: Риддерский ремонтно-механический завод;
Бухтарминский гидроэнергетический комплекс; Текелийский энергетический комплекс.
1.3 Горно-геологическая характеристика месторождения В пределах Лениногорского рудного поля находятся два крупных полиметаллических месторождения – Риддер-Сокольное и Тишинское которые разрабатывает Риддерский ГОК.
Риддер-Сокольное месторождение приурочено к вулкано-осадочной толще пород среднего девона которые представлены в стратиграфическом отношении четырьмя подсвитами (снизу вверх); Лениногорской подсвитой Крюковской Ильинской и Сокольной.
Лениногорская подсвита представлена агломератовыми туфами с прослоями алевролитов. Мощность 250-400 м. Сокольная подсвита завершает девонские отложения в рудном поле. Представлена известняковыми алевролитами аргалитами с прослоями песчаников и лавобрекчий фальзит-порфиров. Мощность до 500м.
Промышленное оруднение образует два горизонта : верхний и нижний . Первый представлен рудами свинцового –цинкового состава второй- медно-цинкового. Под верхним горизонтом выделяется рудный под горизонт. В верхнем горизонте руды размещались в куполах где образовывали линзообразные залежи.
Толща пород среднего девона разбита тектоническими нарушениями на отдельные блоки и имеет сложное ступенчатое строение .Центральный блок месторождения приподнят он ограничен с запада сбросом скважин 50-53 а с востока Николаевским сброс сдвигом .В нём расположены основная Риддерская и Центральная медно-цинковая залежи. Западный блок состоит из ряда ступеней одна из которых ограничена сбросом скважин 50-53 на востоке и западным сбросом на западе является местом локализации II Риддерской залежи.
На северном фланге под аллохтоном северного надвига в сложных тектонических условиях расположена Заводская залежь. Оруднение приурочено к толще пород Крюковской подсвиты . Платообразные и линзообразные рудные тела верхней части купольной структуры практически уже отработаны.
На глубоких горизонтах залежей оруднение представлено крутопадающими жильными телами в сланцах туфах микро кварцитах. Свинцово-цинковые руды приурочены к сериям кварцевых жил и прожилков которые объединяются в рудные зоны мощностью от 2 до 15-20 м протяженностью по простиранию 100-150 м и по падению до 60-80м.
Рудовмещающие породы сернисто-глинисто-углистые сланцы (северный фланг II Риддерской залежи) агломератовые туфы (Центральная медно-цинковая залежь). Коэффициент крепости по шкале проф. Протодьяконова М.М от 8-10 до 15-16.
Рудовмещающие породы преимущественно устойчивые допускающие значительные площадки обнажения без крепления горных выработок.
Гидрогеологические условия эксплуатации месторождения являются сложными. Непосредственно под древней долиной и руслом реки Филлиповка и долиной реки Быструха расположены ряд залежей месторождения. Долины рек заполнены мощными валунно – и гравийно-галечными отложениями. Суммарный водоприток в горные выработки по фактическим замерам 1966 года на 11 горизонт колеблется в пределах 850-950-кубических метровчас а по 13 горизонту 750-950кубических метровчас.
Наиболее распространенные минералы : галенит сфалерит халькопирит пирит.
Объёмный вес руд –28 ткубических метров вмещающих пород –27кубических метров.
Риддер-Сокольное месторождение вскрыто стволами шахт Новая Скиповая Скиповая-2 Андреевская шахта №2 шахта №3 Белкина-2 Вентиляционная Соколок Вент. Шурф.
1.4 Механизация подготовительных и очистных работ. Подготовительные работы заключаются в проведение капитальных выработок подготовки новых горизонтов а так же подготовки выемочных участков. Главными направлениями технического развития при подготовительных работах являются повышения уровня механизации проходческих работ создание и внедрение средств комплексной механизации широкое применение анкерной крепи улучшение организации производства и труда. Многие проходческие бригады применяя совершенную технологию НОТ и умело используя высокопроизводительную проходческую технику добиваются высоких скоростей проведения горных выработок. При проведение выработок выполняют ряд производственных процессов: бурение шпуров производится переносными перфораторами бурильными установками восстающие бурятся телескопными перфораторами шпуры заряжаются специальными зарядными устройствами. При проветривание используют вентиляторы местного проветривания. При креплении горных выработок применяют машины разбрызгивающие торкрет бетонную смесь .Очистные работы заключаются в отработке подготовленных горных участков а так же в транспортировке горной массы на гора . На Риддер – Сокольном руднике применяют систему отработки этажного обрушения с отбойной руды глубокими скважинами. Скважины бурятся станками ЛПС. Уборка горной массы осуществляется скреперными лебедками а также погрузоуборочными машинами типа ППН-1. Транспортировка от горнодобывающего участка до ствола осуществляется электровозной откаткой.
1.5 Транспорт и подъем горной массы. Рудник ведёт работы по добыче руды на нижних горизонтах. Руда и порода с верхних горизонтов перепускается по рудоспускам на 13 и 16 горизонты (основные откаточные горизонты). Откатка осуществляется транспортным участкам ВШТ. По откаточным горизонтам руда доставляется к шахтам “Скиповая” и “Скиповая-2” в вагонных составах вагоны типа УВГ- 4 и УВГ- 45 контактными электровозами К- 14 К-14 м. Количество вагонов в составе 14. Полезный вес состава –90-110 тонн. Время загрузки 15-30 минут в зависимости от кусковатости руды и метода загрузки.
Разгрузка вагонов в бункера производится в круговых опрокидывателях а так же пневмоцилиндрами. Время разгрузки состава 12-16 минут. Производительность опрокидывателя за смену - 420 вагонов. Подъём горной массы «на гора» осуществляется скипами.
С целью увеличения грузопотока между стволами шахты “Скиповая” и добычным участком движения производится по двум параллельным выработкам длинной 1200 метров. Порожние составы движутся по соединительному квершлагу груженные – по грузовому.
Тяговые сети выполнены контактным медным проводом специального профиля. Для снижения износа провода на участках с интенсивным движением применяются стальные катанки 20 мм подвешенные к троллею на специальных зажимах через 2-25 метров. Контактная сеть включена в соответствии с требованиями ЕПБ и питается от автоматической тяговой подстанции типа АТП-500.
Железнодорожный путь на основных откаточных выработках выполнен из рельс тяжелого типа Р-43 и Р-33 на вспомогательных – из рельс Р-24. Рельсы уложены на деревянные шпалы и прикреплены к ним костыльными гвоздями через накладки шпалы уложены на балластный слой состоящий из песчанно-гравийной смеси или мелких горных пород. Ширина железнодорожной колеи составляет 150 мм. На сопряжениях выработок для перевода стрелок применяются полуавтоматические пневматические приводы стрелочных остряков.
На Алтайском руднике для подъёма полезного ископаемого на поверхность спуска-подъема людей и материалов используются подъемные установки:
- шахта «Новая»: подъемная установка типа ЦР5х2306 (грузо-людская) и подъемная установка типа ЦР4х2306 (скиповая);
- шахта «Скиповая» - подъемная установка типа 2Ц5х23 (скиповая);
- шахта «Андреевская» - подъемная установка типа Ц3х32 (грузо-людская);
- шахта «Быструшинская» - подъемная установка типа 2БМ-30001511-4 (грузо-людская);
- шахта «Быструшинская – слепая» - подъемная установка типа 2БМ-25001220-4 (грузо-людская).
Грузо-людские подъемные установки предназначены для спуска-подъема людей материалов и оборудования скиповые – для подъема горной массы на поверхность.
1.6 Вентиляция подземных выработок. Алтайский рудник разделяется на 3 основных площадки :Лениногорская Риддерская Быструшенская. Схема проветривания горных выработок Лениногорской площадки –диагонально-секционная. Способ проветривания –всасывающий .На проветривание горных работ Лениногорской площадки поступает 142 квадратных метровс. свежего воздуха .Подача свежего воздуха осуществляется по стволам шахты Андреевская шахты Белкина –1 шахты Южная ; отработанный воздух выдаётся при помощи вентиляторов главного проветривания установленных на шахте Белкина-2 шахте Вентиляционная.
Схема проветривания горных выработок Риддерской площадки –фланговая .Способ проветривания –всасывающий. Свежий воздух подаётся стволами шахты Новая Скиповая –2 Скиповая-1;выдача на поверхность отработанного воздуха осуществляется по стволам шахт Северная Шахта №3 по вентиляционному восстающему стволу шахты Вентиляционная вентиляционному шурфу.
Схема проветривания горных выработок Быструшинской площадки –диагонально-секционная. Способ проветривания – всасывающий. Основной воздухо-проводящей выработкой является ствол шахты Быструшинская. Так же свежий воздух подаётся по стволу шахты Соколок. Кроме того на проветривание 17 и 18 горизонтов свежий воздух поступает по стволу шахты Слепая – Быструшинская. Основной воздухо-выдающей выработкой является ствол шахты Вентиляционная.
Для лучшего проветривания выработок используется вспомогательный подземный вентилятор ВОД-21 установленный на 14 горизонте. Такой же вентилятор установлен на 16горизонте.
Реверс струи воздуха на шахте №3 производится путём изменения направления вращения вентилятора. На шахте Вентиляционная с помощью обводных каналов перекрытием ляд. Каждая вентиляционная установка обеспечивается резервным электродвигателем и имеет 2 ввода электроснабжения.
1.7 Водоснабжение. Поверхностные объекты Быструшинской площадки снабжаются водой от промышленного водопровода диаметр 150 мм который проложен от насосной станции реки Громотуха.
Для обеспечения подземных работ и компрессорной рудника водой служит насосная на реке Быструха в которой смонтированы два насоса типа АРН –300 производительностью 300 міч напор 7 кг ссм2.
От насосной к стволу шахты Быструшинская проложена магистраль диаметром 150 мм. Расход воды подземных потребителей составляет 200 –220м3ч.
Шахтный водопровод выполняет роль пожарного водопровода. На случай его повреждения при пожаре в шахте в стволе предусмотрено переключение воздушной магистрали на водяную. Давление воды в шахте не регулируется и составляет 15 –25 кг ссм2в зависимости от глубины. На пятнадцатом горизонте магистраль закольцована с магистралью Риддерской площадки.
1.8 Воздухоснабжение. Основными потребителями сжатого воздуха в шахте являются : погрузочные машины перфораторы пневмолебёдки зарядчики и т.д. Сжатый воздух поступает из центральной компрессорной Риддер - Сокольного рудника и компрессорной Быструшинской площадки. В центральной компрессорной установке 11 компрессоров производительностью 100 кубических метра в минуту каждый и турбокомпрессор 250 м3мин.
От компрессорной сжатый воздух по трубам 400 мм поступает к стволу шахты Быструшинская по которому проложены трубы 300 мм до 16 горизонта. На горизонтах с11 по 16 выполнены ответвления трубопроводов .
В компрессорной Быструшинской площадки установлены 4 компрессора типа 5 Г и один 2 ВГ производительностью 100 м3мин..
Давление сжатого воздуха в основных сетях 6-75 кг ссм2. Расход воздуха составляет 130-150 млн. м3год.
1.9 Водоотлив. Водоприток Риддер- Сокольного рудника составляет 3100 кубических метра ч .Быструшенской площадки 400-500 кубических метров ч. Со всех горизонтов вода перепускается на 13 горизонт и по водосточным канавкам направляется к стволу шахты .Новая главная насосная станция расположена на 13 горизонте .В камере установлено 54 ступенчатых насосов типа 14М –22*4 производительностью 2000 кубических метров ч.
Вспомогательные насосы на 11 16 18 горизонтах установлены одноступенчатые .
Камера соединена коллектором с тремя водосборниками общим объёмом 8000 кубических метров. В насосной установлены два става триб один рабочий .другой резервный.
1.9 Электроснабжение Алтайского рудника осуществляется по двум линиям электропередач 110 кв. с Усть-Каменогорской Шульбинской и Бухтарминская ГЭС .ЛЭП подходят к ГПП рудника. На ГПП рудника установлены два силовых трансформатора 1106 кв. мощностью 325МВт каждый. По надёжности электроснабжения предприятие относится к первой категории потребления. Установленная мощность электроприёмников 32747 кВт.
Мощность установленных высоковольтных электродвигателей – 28760 кВт. Электропотребление за рабочие сутки составляет 220000-250000 кВт ч. Потребление энергии в рабочие сутки 1 смена- 30% 2смепа-40% 3смена- 30%.
Для освещения откаточных выработок применяются агрегаты АП-4 и АПШ-1 380127В.В проходческих выработках освещения 24В от трансформаторов ТСМ-4 и ТСМ-25.
В низковольтных сетях распределения электроэнергии идёт через кабели типа АСБ АСБУ СБ ААВБ ААВГ КГ КРПСН и другие различных сечений от 25 до 95 мм2.
Различные участки электрической сети подключены к различным ячейкам с помощью которых можно отключить тот или иной потребитель. Для измерения электрического тока на подстанции установлены трансформаторы тока типа ТПЛ-10-05Р-755 для измерения напряжения используются трансформаторы напряжения НОМ-6.
Все потребители шахты имеют заземление которое соединено в общую заземляющую сеть. Общее сопротивление заземляющей сети не превышает 2 Ома.
Для обеспечения электроэнергией потребителей в подземных горных выработках устанавливаются центральные понизительные подстанции. Подстанций всего пять а именно ЦПП-11 горизонта где установлен трансформатор типаТМШ-3206; ЦПП-13 горизонта один трансформатор Т-3206 и две АТП-500275 с трансформаторами ТСП-1606; ЦПП-14 горизонта имеет два трансформатора ТМШ-3206 и две АТП с трансформаторами ТСП-1806; ЦПП-16 горизонта где установлен трансформатор ТКШВП3206 и две АТП-500275 с трансформаторами ТСП-1606. На ЦПП подаётся напряжение с подстанции 356 шахты «Быструшинская». Также установлено 14 участковых подстанций и 9 тяговых подстанций типа АТП 500275 для питания контактной сети.
Два главных заземлителя установлены в зумпфе и водосборнике ствола шахты «Новая» и в водосборнике водоотлива. Оба заземлителя изготовлены из листового металла-стали площадью 075м2 длиной 25м. толщиной 5 мм. К местным заземлителям присоединяются все электрические установки. Местные заземлители устанавливаются у каждой электромашинной камеры или камеры подстанции у каждого распределителя; у каждой соединительной или осветительной муфты.
1.10 Поверхностный комплекс рудника включает в себя:
Бетонозакладочный комплекс;
Административно-бытовой комбинат;
Компрессорную станцию;
Ремонтные мастерские;
Гараж автотранспорта;
1.11 Устройство подъемной машины. Подъёмная установка шахты «Скиповая» имеет огромное значение и служит основной артерией рудника. Ствол шахты имеет 2 рабочих горизонта. Глубина ствола 450 метров диаметр 5 метров. Ствол закреплён бетоном армирован металлическими коробчатыми проводниками имеет 2 рабочих отделения а также ходовые и трубные отделения. Руддворы односторонние выходы к руддворам оборудованы решетками.
Электроснабжение подъемной установки шахты «Скиповая» осуществляется с подстанции «Новодробильного» отделения № 3 обогатительной фабрики по двум кабельным линиям запитанным с разных секций подстанции. В свою очередь подстанция «Новодробильного» отделения запитана с ГПП 1.
Подъёмная машина типа 2Ц5х23 (приложение 1) двухбарабанная -5 один из которых закреплён на валу жестко а второй является холостым и включается в работу с помощью муфты. Для привода подъемной машины использована система ТП-Д (тиристорный преобразователь – двигатель) которая обладает лучшей управляемостью высокой надежностью и быстродействием улучшает протекание переходных процессов и работает с более высоким к.п.д чем система Г-Д (генератор – двигатель).
Двигатель подъемной машины 1 типа ПБК 38065 с номинальной мощностью 1800 кВт 900 В 38 обмин. Давление масла в системе смазки 15 – 2кгсм2 давление воздуха в тормозной системе 5 – 7 кгсм2. Рабочие канаты диаметром 52 мм. Скорость движения скипов до 9 мс.
Тормозное устройство – один из самых ответственных узлов подъемной машины – состоит из исполнительного органа 3 и привода тормоза 8. Исполнительный орган – та часть тормозного устройства которая непосредственно воздействует на тормозной обод барабанов. Привод тормоза – устройство создающее внешнее усилие необходимое для торможения. Тормозной привод имеет раздельные тормозные системы на каждый барабан. Обеспечивается 2 вида торможения: рабочее и аварийное.
Коренной вал подъёмной машины опирается на 2 подшипника 5 и соединяется с валом двигателя с помощью зубчатой муфты. Подшипники вала смазываются принудительно и снабжены реле контроля протока масла температура нагрева не должна превышать 70*С.
Барабан сварной конструкции не футерован и имеет нарезку для укладки канатов.
Подъёмная машина снабжена указателем глубины 6 в комплексе с ограничителем скорости.
Скип грузоподъемностью 115т объемом 75м3 и собственным весом 125т.
Управление подъемной машиной осуществляется машинистом с пульта управления 7. Автоматизация работы подъемной установки осуществляется аппаратом задания и контроля хода (АЗК) 4.
Скиповой подъем работает в три смены. Первую и третью смены производится выдача руды из шахты на поверхность вторую смену производится осмотр и проверка подъемной установки канатов копра и ствола шахты.
Годовая производительность подъемной установки шахты «Скиповая» - 1500000 тгод.
Данные для расчета скиповой подъемной установки
Годовая производительность
подъема А=1500000 тгод
Глубина вертикального ствола Нств=450 м
Число рабочих дней в годуN=300
Продолжительность работы
подъемной машины в суткиt=18 ч
Коэффициент резерва подъема
2.1 Продолжительность подъемной операции и средняя скорость движения подъемных сосудов.
- часовая производительность подъемной установки по формуле
Принимая высоту загрузки скипа у подземного бункера равной hзаг=40 м и высоту приемного бункера hп.п.=35 м высота подъема составит:
H = Hств + hзаг + hп.п .(1.2)
H = 450 + 40 + 35 = 525 м
- оптимальная грузоподъемность скипа по формуле
где tпаузы = 10 сек – продолжительность паузы между подъемами.
Выбираем стандартный неопрокидной скип с секторным затвором со следующими данными [1]: тоннаж Q=12 т; высота в положении разгрузки hск = 11160 мм; общий путь разгрузки hр = 2170 мм; мертвый вес скипа с зонтом и подвесным устройством Gм=6760кг.
- число подъемных операций в час по формуле:
nп.ч = 41512 = 345 подчас
- продолжительность подъемной операции и время движения подъемных сосудов по формулам:
Продолжительность цикла:
T = 360034.5 = 116 сек
Чистое время подъема:
T = 116-10 = 106 сек
- средняя и ориентировочная максимальная скорости подъема по формулам
а) средняя скорость подъема
Vср = 525106 = 59 мсек
д) допустимое значение максимальной скорости подъема:
Принимая [1] получим ориентировочное значение максимальной скорости подъема:
что соответствует требованиям.
2.2 Расчет и выбор механической части подъемной установки
а) Подъемный канат. Наименьший необходимый по условиям прочности вес 1 м каната:
где Gk - вес концевого груза
Gk = 6760+12000 = 18760 кг
кгсм2 – предел прочности проволоки на растяжение [1];
m = 65 – статический запас прочности (по правилам безопасности [4]);
кгм см2 – фиктивная плотность каната [1];
принимая высоту переподъема равной 3м получим максимальную длину отвеса каната:
Принимаем круглопрядный канат по ГОСТ 7668-55 со следующими техническими данными [2]:
конструкция пряди 1+7+7х7+14
диаметр каната d = 49.5 мм
расчетный вес одного метра каната – pрасч = 939 кг
При кгмм2 суммарное разрывное усилие всех проволок в канате Qz = 161000 кг [2]
Фактическое значение статического запаса прочности:
Mф = Qz(Gk+pH0) (1.11)
Mф = 161000918760+9.39х528 = 68 > 65
Коэффициент статической неуравновешенности подъема:
Уравновешивание системы с помощью хвостового каната в данном случае считается не целесообразным [2]
б) Подъемная машина. Принимаем однобарабанную подъемную машину с разрезным барабаном. Необходимый по правилам безопасности диаметр барабана:
выбираем подъемную машину НКМЗ со следующими техническими данными [2]:
диаметр барабана D = 5 м;
ширина барабана В = 32 м;
ширина разрезной части
барабана Враз = 085 м
максимальное статическое
натяжение каната25 т;
максимальная разность
статических натяжений канатов 18т;
превышение оси вала над
уровнем пола С0 = 1 м:
приведенный вес (без редуктора
и электродвигателя) Gб=28 т
Проверим барабан по ширине:
Необходимая ширина навивочной поверхности барабана
гдеh = 35 м – резервная длина каната для испытаний;
nтр = 4 – число витков трения;
e = 2 мм – расстояние между витками навивающейся и свивающейся ветвей каната;
S = 3 мм – зазор между витками каната.
Необходимая ширина заклиненной части барабана составит
Проверяем барабан на статические нагрузки.
Максимальное статическое натяжение в канате составит:
Smax = kгрQ+Gск+pH0(1.15)
Smax = 10912000+6760+939528 = 24798 кг25000кг
Максимальную разность статических натяжений канатов можно ожидать в начале подъема нормального груза или в момент навески новых канатов.
Tmax = (kпор-1)Q+Gск+pH0(1.17)
Tmax =(106-1)1200+6760+939х528=12438кг 18000кг
в) Расположение подъемной установки относительно ствола шахты. С учетом норм Правил безопасности диаметр направляющего шкива должен быть мм
Выбираем стандартный шкив со следующими техническими данными [2]:
номинальный диаметр навивки4950 мм;
Высота копра составит:
Hк = hп.п+hск+hпер+075Rшк(1.18)
Hк = 35+11160+3+075х25 = 5104 м
Выбираем копер со следующими техническими данными[2]:
высота – Hк = 530 м;
расстояние от оси барабана подъемной машины до оси ствола
В таком случае высота переподъема составит:
h = Hк-(hп.п+hск+075Rшк)(1.19)
h = 53-(35+116+075х25) = 5 м.
Принимаем расстояние от оси барабана до оси каната Е=40м; расстояние между осями подъемных канатов–d0=2250 мм
Исходя из этого длина струн составит:
Углы отклонения каната.
Так как ширина барабана В=3м а ширина барабана занятая одной ветвью каната составляет В0=2м то для получения значений отвечающих требованиям ПТЭ закрепление каната необходимо произвести отступив от реборды на расстояние:
Dp = B-Bраз-B0(1.22)
Угол отклонения короткой струны каната при подходе последнего к реборде находим по следующему соотношению:
- что допустимо [2].
2.3 Кинематика подъемной системы. Приведенный к окружности барабана вес подъемной установки находим из выражения:
гдеLP – где длина одной ветви подъемного каната которая выводится из следующего выражения:
приведенный вес ротора
приведенный вес редуктора
приведенный вес шкива
Приведенная к окружности барабана масса подъемной установки:
Величину ускорения выбираем из условия максимального использования перегрузочной способности двигателя в период пуска.
Усилие на ободе барабана в период пуска составит:
Номинальное усилие двигателя на ободе барабана:
Среднее значение коэффициента перегрузки принимаем равным:
Максимальное усилие на ободе барабана составит:
Приравнивая Fпуск= Fmax определяем
Допуская скорость выхода скипа из разгрузочных кривых равной V0 = 10 мсек определяем величину ускорения за этот период
где hp = 217 м – общий путь разгрузки скипа.
Принимаем тормозное замедление. Величину замедления выбираем так чтобы тормозное усилие в момент входа груженого скипа в направляющие кривые составляло в среднем одну треть полезного груза
Тогда усилие на ободе барабана в момент входа скипа в кривые составит:
Приравнивая Fтор = Fвх определяем
Допуская скорость входа груженого скипа в кривых равной 05 мсек [2]: определяем величину замедления в кривых:
Таким образом принимаем шестипериодную диаграмму скорости (приложение 2) которая применяется для неопрокидных скиповых подъемных установок со следующими расчетными величинами ускорений и замедлений:
- ускорение при перемещении скипа в кривых jo=033мсек2;
- нормальное ускорение скипа вне кривых jo=04мсек2;
- нормальное замедление скипа до входа в кривые j3=-08мсек;
- замедление при перемещении скипа в кривых ja=-023мсек2.
Кинематика подъемной системы.. Скорость выхода порожнего скипа из разгрузочных кривых
Продолжительность периода нормального ускорения
Путь пройденный в период нормального ускорения
Скорость входа груженого скипа в разгрузочные кривые
где Vдот=05 мсек – скорость передвижения скипа в разгрузочных кривых [2].
Продолжительность периода замедления при перемещении скипа в кривых
Продолжительность периода нормального замедления
Путь пройденный в период нормального замедления
Путь пройденный в период равномерной скорости
Продолжительность периода равномерной скорости
Чистое время подъема
Т=t0+t1+t2+t3+tдот+tа
Т =36+1325+60+79+535+44=945 сек
Средняя скорость подъема
По полученным данным строим диаграмму скорости и ускорений подъемной установки (приложение 2)
Фактическое значение множителя скорости
Продолжительность цикла
Годовая производительность подъема
Фактическое значение коэффициента неравномерности подъема
2.4 Динамика подъема
где - коэффициент уменьшения веса полезного груза; подставляется в формулу только один раз в конце подъема; в остальных случаях [2].
Значение усилий на ободе барабана определяются:
- в начале подъема (x=0 j=j0=033 мсек)
F1=18730-13358033=2613800 кг
- в конце периода ускорения при перемещении скипа в разгрузочных кривых ( jo=033 мсек2)
F2=18730-1878217+13358033=2308700 кг
- в начале периода нормального ускорения после выхода скипа из кривых ( j=j1=04 мсек2)
F3=18730-1878217+1335804=2708700 кг
- в конце периода нормального ускорения и в начале периода равномерной скорости ( j=0)
F4=18730-18786697=1781500 кг
- в конце периода равномерной скорости (х=6697+х2=6697+ +4231=490 м; j=0)
F5=18730-18786697=13472 кг
- в начале периода нормального замедления ( j=-08 мсек2)
F6=18730-1878490-1335808=-9528 кг
- в конце периода нормального замедления (х=490+х3=490+ +328=5228 м; j=-08 мсек2)
F7=18730-1878490-1335808= -11581 кг
- в начале движения груженого скипа в разгрузочных кривых с постоянной скоростью (х=5178 м; j=0)
F8=18730-18785178= 11742 кг
- в конце движения с постоянной скоростью (х=5178+5=5228м; j=0):
F9=18730-18785228=2201 кг
- в начале периода замедления в момент входа скипа в разгрузочные кривые (х=5228 м; j=ja=-023 мсек2)
F10=18730-18785228-13358023=-1506 кг
- в конце подъема (х=Н=525 м; j= -023 мсек2; )
F11=18730-0512000-1878525-13358023=-5326кг
По полученным данным строим диаграмму усилий подъемной установки (приложение 3).
2.5 Выбор подъемного двигателя и привода к нему. Для удовлетворения ориентировочной максимальной скорости подъема необходимая скорость вращения барабана составит:
Принимаем редуктор с передаточным отношением i = 115
Найдем скорость вращения приводного двигателя по формуле:
Выбираем стандартную скорость вращения асинхронного двигателя nc = 300 обмин ).
Тогда действительное значение максимальной скорости подъема составит:
Ориентировочную мощность приводного двигателя находим из выражения:
где -коэффициент эффективного усилия подъема [2];
k = 115 – коэффициент шахтных сопротивлений;
Выбираем двигатель постоянного тока П2-800-175-6УХЛ4 со следующими техническими характеристиками [3]:
номинальная мощность Рн = 1250 кВт;
напряжениеUст = 6000 В;
номинальная скорость
вращенияnном = 315 обмин;
напряжениеUp = 600 В;
сила токаIp = 950 А;
маховый моментGD2=9х103кгхм2.
сопротивление якорной
коэффициент мощности=072;
коэффициент перегрузки
пропорциональностиКv=10282
Расчетное значение момента на тихоходном валу редуктора.
Выбираем редуктор со следующими техническими данными[3]:
тихоходном валу5700кгхм;
маховый момент приведенный
к тихоходному валу280000кгхм;
передаточное числоI = 115
Для привода двигателя подъема с учетом номинального напряжения принимаем тиристорный преобразователь ТПЗ-1600660-40ОУ4. Со следующими техническими данными[3]:
номинальное напряжениеUном=660 В;
номинальный токIном=1600 А;
номинальная температура нагрева
число силовых шкафов1;
число тиристоров в плече8;
к.п.д. агрегата954 %
Принятый агрегат необходимо проверить на нагрузочную способность применительно к режиму работы
Эффективное значение выпрямленного тока преобразователя по формуле:
В качестве резерва для привода двигателя подъема принимаем генератор постоянного тока НП172-10КУ мощностью Р = 1600 кВт напряжением U = 660 В ток главной цепи I = 2200 A частота вращения n = 1000 обмин.
Для привода генератора принимаем синхронный двигатель СДС3-15-49-6УЗ мощностью P = 2000 кВт частота вращения n = 1000 обмин.
2.6 Эффективная мощность привода.
Эффективное усилие подъема.
Эффективная мощность приводного двигателя составит:
где 1250кВт – Рном.дв. номинальная мощность двигателя.
Максимальное усилие на ободе барабана получается в начале периода нормального ускорения: Fma перегрузка двигателя при этом составит:
где Fн- номинальное усилие двигателя на ободе барабана получаем из выражения:
- коэффициент перегрузки двигателя.
2.7 Годовой расход электроэнергии и к.п.д. подъемной установки.
Полезный расход энергии:
на один тонно-километр
Тогда фактический расход энергии на один подъем найдем из выражения:
где ΣFt=(F1+F2)t0 2+(F3+F3F4+F4)t1 3+
+(F4+F4F5+F5)t2 3+(F6+F6F7+F7)t3 3+
+(F8+F8F9+F9)tдот 3+(F10+F10F11+F11)tа 3
Удельное значение фактического расхода электроэнергии: на одну тонну:
Годовой расход электроэнергии на подъем руды
Wг=Wф1тА=3241 500 000=4 860 000 кВтч(1.60)
К.п.д. подъемной установки
2.8 Электроснабжение подъемной установки
Электроснабжение подъема производится с помощью двух независимых вводов. От шин подстанции питается:
- трансформатор ТСЗР-2500 питающий тиристорный преобразователь ТПЗ-1600660Т-40ОУ4
- трансформатор собственных нужд ТМ-250.
Определяем расчетную активную и реактивную мощность потребителей двух групп:
расчетная активная мощность
где Кс – коэффициент спроса потребителей учитывающий загрузки электроприемников и неодновременность их работы (Таблица 1.1).
Таблица 1.1-Коэффициерт спроса для основных электроприемников [3]
Наименование групп электроприемников
Электроприемники собственных нужд
Ртп = 2500075 = 1875 кВт
Рт.сн = 25005 = 125 кВт
расчетная реактивная мощность
Qрасч = Ррасчtgφ(1.62)
Qтп = 1875088 = 1630 кВар
Qтсн =1251 = 125 кВар
расчетная активная мощность потребителей двух групп
Pрасч = Ртп+Рт.с.н(1.63)
Pрасч =1875+125=2000 кВт
расчетная реактивная мощность потребителей двух групп
Q=1650+125=1775 кВар
расчетная мощность составит
Выбор сечения питающего кабеля производим по экономической плотности тока по формуле
где Iрасч – расчетный ток нагрузки
- экономическая плотность тока при работе кабеля от 3000 ч до 5000 ч.[3]
Принимаем кабель типа ААБлУ-3х150 мм2 у которого Iдл.доп = 300 А
Iдл.доп = 300 А > Iрасч = 209 А
Для приема и распределения электроэнергии на подстанции подъема устанавливаем комплектное распределительное устройство типа К-104-10-20 [3].
Таблица 1.2-Технические данные К-104-10-20
Номинальное напряжение кВ
Номинальное рабочее напряжение кВ
Номинальный ток: сборных шин разъединителей выключателей А
Номинальный ток отключения кА
Электродинамическая стойкость кА
Термическая стойкость кА
Габаритные размеры (ширина глубина высота) мм
Для КРУ выбираем вакуумный выключатель типа ВВТЭ-10-10630УЗ
2.9 Расчет защитного заземления
Защитное действие заземления состоит в уменьшении электрического тока проходящего через человека при соприкосновении его с металлическими частями электрических установок.
Человек включается в цепь параллельно заземлению и чем больше сопротивление человека по сравнению с сопротивлением заземления тем меньше тока потечет по нему.
К заземлению подлежат все металлические части электрических установок которые могут оказаться под напряжением вследствие нарушения изоляции.
Заземлители делятся на главные и местные.
Главные заземлители устанавливаются в зумпфах и водосборниках и представляют собой стальные шесты S=075 мм2 и толщиной 5 мм.
Местные заземлители устанавливаются в штрековых сточных канавах представляют собой стальные полоски шириной не менее 06 мм толщиной не менее 3 мм длиной не менее 25 м.
В сухих выработках в качестве местных заземлителей допускается применение стальных труб не менее 30 мм и длиной не менее 15 м стенки труб должны быть просверлены на разной высоте и иметь около 20 отверстий 5 мм. Трубы вставляются в пробуренный шнур глубинной не менее 14 м.
Пространство вокруг труб заполняется смесью песка или золы с поваренной солью в соответствии 6:1; для поддержания постоянной влажности в шпур через трубу периодически заливают воду.
Определяем сопротивление вертикального электрода из арматурной стали или трубы.
Rв = 0366р 1 (2 1 d + 1 2 4t +
= 1 4t – 1) Ом(1.68)
где р – удельное сопротивление грунта Ом.
= 3 м – длина электрода
d – диаметр электрода
t – глубина заложения
t = 05 + 1 2 = 05 + 3 2 = 2 м.
Rв = 0366 * 40 3 ( 23 007 + 1 2 4 2 + 34 х х 2 – 3) = 861 Ом.
Ориентировочно принимаем число стержней n = 5.
Определяем сопротивление части заземляющего контура из вертикальных стержней.
R3в = Rв n * nв; Ом (1.69)
где nв = 06 – коэффициент учитывающий экранирование электродов [3].
R3в = 861 5 * 06 = 287 Ом.
Определяем сопротивление горизонтальной полосы связывающей вертикальные электроды между собой.
Rr = (0366 40 15) ( 2 152 005 2) = 375 Ом
Определяем сопротивление растекания.
R3r = Rr nr ; Ом (1.71)
R3r = 375 06 = 595 Ом.
Определяем сопротивление заземляющего контура.
R3 = R3в R3r R3в + R3r ; Ом. (1.71)
R3 = 287 595 287 + 595 = 194 Ом.
4 2 – что допустимо.
3 Автоматизация подъемной установки
Автоматизация работы подъемной установки осуществляется аппаратом задания и контроля хода (АЗК) который выполняет следующие функции:
- программирование хода подъемной машины при работе в нормальном режиме и в режиме разъездов при работе на сниженной скорости;
- контроль фактической скорости в период разгона равномерного хода и замедления;
- преобразование вращения коренного вала подъемной машины в электрические импульсы для измерения сельсинными указателями глубины пути пройденного подъемными сосудами;
- защиту от переподъема;
- корректировку элементов аппарата в соответствии с положением подъемных сосудов в стволе шахты при перестановке барабанов или при проскальзывании канатов;
- контроль целостности кинематической цепи от подъемной машины к блокам сельсин-датчиков указателя глубины и электрического ограничителя скорости.
Особенностью аппарата является симметрическая конструкция с независимой раздельной синхронизацией обеих частей. Так при перестановке барабанов одна часть аппарата остается соединенной с подъемной машиной а другая в процессе перестановки синхронизируется с положением «своего» подъемного сосуда в стволе шахты.
11 Внешние соед (рудная).dwg

Контроль температуры подшипников электродвигателя подъемной машины
Контроль температуры подшипников барабана подъемной машины
Контроль температуры подшипников генератора подъемной машины
Контроль температуры обмотки электродвигателя подъемной машины
Щит системы контроля и аварийной защиты подъемных машин
01 Внешние соед (общая).dwg

- температура подшипников эл. двигателя
- температура воздуха в камере
- температура обмоток
- температура подшипников генератора
- температура обмотки
Внешние соед (нагнетатели __1,3).dwg

Контроль температуры подшипника №2 эл.двигателя
Контроль температуры подшипника №1 эл.двигателя
Контроль температуры подшипника №2
Контроль температуры подшипника №1
Контроль температуры воды на входе в маслоохладитель
Контроль температуры масла после маслоохладителя
Контроль температуры подшипника №2 нагнетателя
Контроль температуры подшипника №1 нагнетателя
Контроль температуры подшипника №2 эл. двигателя
Контроль температуры воды на выходе после маслоохладителя
Щит системы контроля и аварийной защиты компрессорной станции N3
Контроль температуры горячего воздуха (поток №2)
Контроль температуры холодного воздуха эл.двигателя
Контроль температуры воздуха на нагнетании
Контроль температуры воздуха на всасывании
Контроль температуры горячего воздуха (поток №1)
03 Монтажная схема общая.dwg

Содержание.doc
1.3 Горно-геологическая характеристика месторождения12
1.4 Механизация подготовительных и очистных работ14
1.5 Транспорт и подъем горной массы16
1.6 Вентиляция подземных выработок17
1.8 Воздухоснабжение19
1.9 Электроснабжение Алтайского
1.10 Поверхностный комплекс рудника23
1.11 Устройство подъемной машины23
2.1 Продолжительность подъемной
операции и средняя скорость движения подъемных сосудов25
2.2 Расчет и выбор механической части подъемной установки27
2.3 Кинематика подъемной системы31
2.4 Динамика подъема37
2.5 Выбор подъемного двигателя и
2.6 Эффективная мощность привода43
2.7 Годовой расход электроэнергии и
к.п.д. подъемной установки44
2.8 Электроснабжение подъемной
2.9 Расчет защитного заземления48
3 Автоматизация подъемной установки50
ЭКОНОМИКА И ОРГАНИЗАЦИЯ ПРОИЗВОДСТВА53
1 Организационно – производственная
структура участка подъема53
3 Определение капитальных вложений или
4 Режим работы участка подъема55
5 Организация труда и заработной платы60
6 Планирование производства62
6.1 Планирование численности обслуживающего персонала63
6.2 Планирование фонда
7 Планирование эксплутационных затрат68
8 Экономическая оценка вариантов проектируемых решений71
9 Технико-экономические показатели72
БЕЗОПАСНОСТЬ И ЭКОЛОГИЧНОСТЬ ПРОЕКТА74
1 Техника безопасности74
1.1 Требования ПБ к подъемным
1.2 Противопожарные мероприятия85
1.3 Основные мероприятия
по безопасности труда86
2 Экологичность проекта89
2.1 Охрана воздушного бассейна90
2.2 Охрана водного бассейна91
2.3 Анализ источников загрязнения для бетонно-закладочного комплекса91
Рекомендуемые чертежи
- 09.07.2014
- 25.01.2023