Проектирование ректификационной установки




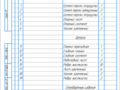
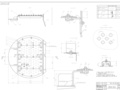
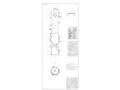
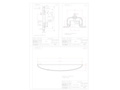
- Добавлен: 25.01.2023
- Размер: 1 MB
- Закачек: 0
Описание
Состав проекта
![]() |
![]() |
![]() ![]() ![]() |
![]() ![]() ![]() |
![]() |
![]() ![]() ![]() ![]() |
![]() ![]() ![]() ![]() |
![]() |
![]() ![]() ![]() ![]() |
![]() ![]() ![]() ![]() |
Дополнительная информация
колонна общий.dwg

тарелка.spw

Тарелка_колпачковая.dwg

деталирование.dwg

Рекомендуемые чертежи
- 25.01.2023
- 16.02.2015
- 10.04.2022