Проектирование редуктора - СГАУ




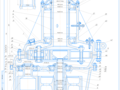
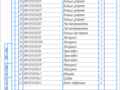
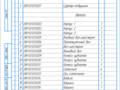
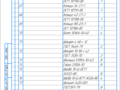
- Добавлен: 24.01.2023
- Размер: 792 KB
- Закачек: 0
Описание
Состав проекта
![]() |
![]() ![]() ![]() ![]() |
![]() ![]() ![]() ![]() |
![]() ![]() ![]() ![]() |
![]() |
![]() ![]() ![]() |
![]() |
![]() ![]() ![]() ![]() |
![]() ![]() ![]() ![]() |
![]() ![]() ![]() ![]() |
![]() ![]() ![]() ![]() |
![]() ![]() ![]() ![]() |
![]() ![]() ![]() ![]() |
![]() ![]() ![]() ![]() |
![]() ![]() ![]() ![]() |
Дополнительная информация
корпус.cdw

стакан подшипника.cdw

Неуказанные предельные отклонения
Ст.40х по ГОСТ 1050-88
Вал-шестерня.cdw

Твёрдость сердцевины по HRC 37 44.
Неуказанные радиусы механической обработки 0
Неуказанные предельные отклонения
Коэффициент смещения
Детали машин.doc
Самарский государственный Аэрокосмический Университет
имени академика С.П.Королева
по курсу «Д е т а л и м а ш и н»
Задание № 1 вариант № 1
Спроектировать цилиндрическо-планетарный редуктор
Кинематическая схема редуктора
За расчетную (номинальную) нагрузку принимается максимальная из длительно действующих нагрузок при которой число циклов перемены напряжений
Коэффициент нагрузки при этом число перемены циклов напряжений
График режима работы
Пояснительная записка: стр.52 рис.8 источников 5.
Графическая документация: 3 листа А1.
РЕДУКТОР ПОДШИПНИК ГАЙКА БОЛТ ВАЛ КОРПУС ЗУБЧАТОЕ КОЛЕСО.
Разработана конструкция редуктора для передачи и усиления крутящего момента с вала двигателя на винт. Обоснована целесообразность использования зубчатых колёс.
Кинематический расчет редуктора6
1 Определение общего передаточного отношения и распределение его по ступеням6
2 Определение частот вращения всех элементов привода6
3 Определение числа сателлитов для планетарной ступени6
4 Определение КПД ступени и мощности на валах7
5 Определение крутящих моментов на валах7
Расчет зубчатых передач редуктора8
1 Выбор материала зубчатого колеса и обоснование термообработки8
2 Определение допускаемых напряжений8
3 Определение допускаемых напряжений изгиба11
4 Расчет цилиндрической передачи13
4.1 Определение основных параметров цилиндрической прямозубой некорригированной зубчатой передачи из условия прочности13
4.2 Определение модуля и числа зубьев13
4.3 Проверочный расчет передачи на контактную прочность14
4.4 Проверочный расчет передачи на выносливость по изгибу15
4.5 Проверочный расчет передачи на статическую прочность при перегрузках16
4.6 Определение геометрических размеров передачи17
5 Расчет планетарной передачи17
5.1 Определение габаритов передачи “a-g”17
5.2 Определение модуля зацепления18
5.3 Подбор чисел зубьев и уточнение передаточных отношений19
5.4 Определение геометрических параметров зацепления передачи19
5.5 Определение ширины коронки (колеса b)20
5.6 Проверочный расчет передачи на контактную прочность21
5.7 Проверочный расчет передачи на изгибную прочность22
5.8 Проверочный расчет передачи на статическую прочность при перегрузках22
Определение усилий в зацеплениях23
1 Расчет усилий в зацеплениях цилиндрической передачи23
2 Расчет усилий в зацеплениях планетарной передачи23
Обоснование конструкции и определение размеров основных деталей и узлов привода24
1 Предварительное определение диаметров валов и осей24
2 Эскизная компоновка и определение размеров основных деталей привода26
3 Определение реакций в опорах валов26
4 Уточненный расчет валов и осей27
4.1 Построение эпюры изгибающих и крутящих моментов27
4.2 Расчет валов на статическую прочность в опасных сечениях28
Проверочный расчет валов на выносливость28
5 Расчёт долговечности подшипников качения31
Расчет шлицевых соединений33
СПИСОК ИСПОЛЬЗОВАННЫХ ИСТОЧНИКОВ36
Производственные процессы в большинстве отраслей народного хозяйства выполняют машины и дальнейший рост материального благосостояния тесно связан с развитием машиностроения.
К важнейшим требованиям предъявляемым к проектируемой машине относятся экономичность в изготовлении и эксплуатации удобство и безотказность обслуживания надёжность и долговечность.
Для обеспечения этих требований детали должны удовлетворять ряду критериев важнейшие среди которых - прочность надёжность износостойкость жёсткость виброустойчивость теплостойкость технологичность.
Зубчатые передачи в современной промышленности имеют большое значение. Благодаря высокому КПД они широко применяются в технике. В данной работе произведен расчет необходимый для того чтобы спроектировать редуктор вертолёта. Расчет осуществляется в трёх вариантах. Это необходимо для выбора оптимального подбора зубчатых колёс.
Курсовой проект по деталям машин является первой конструкторской работой студента и поэтому её значение весьма существенно. Изучение основ конструирования (проектирования) начинают с конструирования простейших узлов машин - приводов редукторов. Опыт и знания приобретенные студентом при конструировании этих узлов машин являются основой для его дальнейшей конструкторской работы а также для выполнения курсовых проектов по специальным дисциплинам и дипломного проекта.
Кинематический расчет редуктора
1 Определение общего передаточного отношения и распределение его по ступеням
Согласно заданию имеем частоту вращения валов
Общее передаточное число редуктора
Согласно рекомендации имеем
2Определение частот вращения всех элементов привода
Частота вращения вала I (см. исходные данные)
Частота вращения вала II
Частота вращения вала III (см. исходные данные)
Частота вращения зубчатого колеса «а» при остановленном водиле
Частота вращения зубчатого колеса «b» при остановленном водиле
- частота вращения сателлита «g»
3 Определение числа сателлитов для планетарной ступени
Число сателлитов для планетарной ступени определяется по формуле
округляем до целого так чтобы отсюда .
4 Определение КПД ступени и мощности на валах
Т.к. передача авиационная она требует обеспечения высокой надежности работает с умеренными скоростями и высокими нагрузками то согласно рекомендации [1] для всех зубчатых колес выбираем 7-ю степень точности. Для нее имеем:
цилиндрическая передача
Мощности на валах определяются по следующей формуле:
5 Определение крутящих моментов на валах
Крутящие моменты на валах определяются по следующей формуле:
крутящий момент на валу I: ;
крутящий момент на валу II:
крутящий момент на валу III: ;
момент действующий на колесо «a»: ;
момент предаваемый с шестерни «а» к сателлиту «g»: где
- коэффициент неравномерности при одном плавающем колесе и числе сателлитов согласно рекомендации [2] имеем отсюда
момент передаваемый от сателлита «g» к корончатому колесу «b»:
Расчет зубчатых передач редуктора
1 Выбор материала зубчатого колеса и обоснование термообработки
Т.к. передача авиационная требующая обеспечения высокой надежности малой массы и габаритов то для всех зубчатых колес привода выбираем высокопрочную легированную сталь 12Х2Н4А с химико-термической обработкой – цементацией заготовка – штамповка; механические свойства приведены в таблице:
Механические характеристики
2 Определение допускаемых напряжений
Контактные напряжения для каждого зубчатого колеса определяются по формуле:
j – номер зубчатого колеса
- базовый предел выносливости.
Т.к. для всех зубчатых колес материал одинаковый то согласно рекомендации [1] имеем:
- коэффициент безопасности т.к. заготовка – штамповка то согласно рекомендации [1] имеем:
- коэффициент долговечности определяется по формуле:
- базовое число циклов перемены напряжений т.к. HRc>56 то согласно рекоменда-ции [1] имеем:
- расчетное число циклов перемены напряжений при переменном режиме определяется по формуле:
- число зацеплений каждого колеса за 1 оборот
i – номер режима тогда
для корончатого колеса «b»:
Т.к. и то . Для остальных колес имеем:
Тогда допускаемые напряжения будут равны:
В качестве расчетных допускаемых напряжений для каждой пары зубчатых колес принимаем наименьшее значение из двух полученных:
3 Определение допускаемых напряжений изгиба
Допускаемые напряжения изгиба для каждого зубчатого колеса определяются по формуле:
- коэффициент безопасности согласно рекомендации [1] имеем:
- базовое число циклов перемены напряжений согласно рекомендации [1] имеем:
т.к. HB>350 то тогда
Т.к. зубья колес 1 2 шестерни «а» и корончатого колеса «b» работают одной стороной то согласно рекомендации [1] имеем: . Т.к. зубья сателлита «» работают двумя сторонами то согласно рекомендации [1] имеем: . Тогда допускаемые напряжения будут равны:
4 Расчет цилиндрической передачи
4.1 Определение основных параметров цилиндрической прямозубой некорригированной зубчатой передачи из условия прочности
Определим рабочую ширину зубчатого венца колеса по формуле:
(согласно рекомендации [1]) - коэффициент ширины колеса относительно межосевого расстояния.
- межосевое расстояние.
К – коэффициент нагрузки. Согласно рекомендации [1] К=1.2..1.4. Примем К=1.4.
Исходя из расчетов полученных ранее МПа
Округлив до целого значения получим .
Увеличим до 54 мм чтобы обеспечить контактную прочность: .
4.2 Определение модуля и числа зубьев
Определим модуль зацепления колеса по формуле:
возьмем из данных полученных ранее
- коэффициент формы зуба для 7-ой степени точности согласно рекомендации [1]
Округлим до ближайшего по ГОСТ 9563-60 () получим .
Определим число зубьев первой шестерни:
Определим число зубьев второй шестерни:
. Округлив до целого значения получим .
Вычислим передаточное число по формуле: .
Согласно рекомендации [1]: если тогда вычислим значение делительного диаметра шестерни по формуле: .
4.3 Проверочный расчет передачи на контактную прочность
Фактическое напряжение определим по формуле:
возьмем из данных полученных ранее.
Коэффициент нагрузки К вычислим по формуле: где
- коэффициент динамической нагрузки; определяется согласно рекомендации [1](приложение 5) в зависимости от окружной скорости и степени точности.
. Если то согласно рекомендации [1](приложение 5) имеем для 7-ой степени точности .
Определим коэффициент неравномерности распределения нагрузки по ширине зубчатого венца .
Различают начальный коэффициент концентрации нагрузки равный коэффициенту концентрации для неприрабатываюшихся колес и коэффициент концентрации после приработки . Согласно рекомендации [1](приложение 5) для стальных колес с твердостью поверхности зуба НВ>350.
определяется в зависимости от расположения опор и величины коэффициента ширины зубчатого венца относительно начального диаметра шестерни .
Так как и коническая передача расположена на консоли то коэффициент тогда .
Определим фактическое напряжение:
Определим погрешность е:
Согласно рекомендации [1] если то искомые параметры найдены верно т.е.
4.4 Проверочный расчет передачи на выносливость по изгибу
Согласно рекомендации [1] фактические напряжения должны быть меньше допускаемых:
Рассчитаем фактические изгибные напряжения по формулам:
здесь - рабочая ширина зубчатого венца
- крутящий момент первого вала
К=1.4 – коэффициент нагрузки
- делительный диаметр
- модуль зубчатого венца конического колеса
- коэффициенты формы зуба для 7-ой степени точности. Они зависят от смещения х в нашем случае х=0 и от числа зубьев .
так как передача прямозубая.
Тогда согласно приложению 9 (рекомендация [1]) а ;
- коэффициент учитывающий наклон зубьев согласно рекомендации [1] при ;
- коэффициент учитывающий перекрытие зубьев согласно рекомендации [1] при .
Так как допускаемое изгибное напряжение МПа то
Так как допускаемое изгибное напряжение МПа то .
Следовательно МПа МПа.
4.5 Проверочный расчет передачи на статическую прочность при перегрузках
Найдем максимальные фактические напряжения при перегрузках . Они должны быть меньше допускаемых: :
где отношение согласно примечанию задания.
Так как способ обработки – цементация то согласно рекомендации [1] МПа т.е. .
Согласно рекомендации [1] найдем максимальное допускаемое изгибное напряжение по формуле: так как НВ>350. По приложению 2 предел прочности для стали 12Х2Н4А равен 1200 МПа следовательно МПа.
Следовательно МПа МПа
4.6 Определение геометрических размеров передачи
Определим делительное межосевое расстояние по формуле :
Определим межосевое расстояние по формуле :
Примем все смещения равными нулю тогда .
Определим внешний делительный диаметр шестерни по формуле:
Определим внешний делительный диаметр колеса:
Рассчитаем начальные диаметры шестерни и колеса соответственно:
Найдем диаметр вершин зубьев шестерни и колеса.
Для внешнего зацепления имеем:
Вычислим диаметры впадин зубьев для внешнего зацепления:
Рассчитаем угол профиля производящей рейки в сечении перпендикулярном к оси сцепляющегося с ней зубчатого колеса: .
Определим угол зацепления: .
Основной угол наклона для прямозубой передачи.
5 Расчет планетарной передачи
5.1 Определение габаритов передачи “a-g”
Найдем диаметр центральной шестерни “a” по формуле:
- крутящий момент передаваемый от шестерни “a” к сателлиту “g” .
- передаточное число передачи “a-g”.
- допустимое контактное напряжение.
- предварительный коэффициент нагрузки. Согласно рекомендации [2] . Примем .
- предварительный коэффициент ширины зубчатого венца относительно начального диаметра шестерни. Согласно рекомендации [2] имеем . Примем .
Определим рабочую ширину зубчатого венца по формуле:
округлив до целого получим .
Вычислим конечное значение коэффициента по формуле: . В зависимости от этого значения определим значение коэффициента неравномерности распределения нагрузки по ширине зубчатого венца - согласно рекомендации [2].
Вычислим конечное значение коэффициента нагрузки: .
- коэффициент динамической нагрузки зависит от окружной скорости . Вычислим окружную скорость по формуле: . Тогда согласно рекомендации [2] ;
следовательно согласно рекомендации [2]
5.2 Определение модуля зацепления
Выберем минимальное значение модуля зацепления. Так как у нас химико-термическая обработка – цементация то согласно рекомендации [2] .
Рассчитаем предварительный модуль зацепления: где
- коэффициент нагрузки;
- предварительный коэффициент формы зуба;
- выберем наименьшее из допускаемых напряжений согласно рекомендации [2]. значит берем
Примем по ГОСТ 9563-60 согласно таблице 2 приложения (рекомендация [2]) .
Рассчитаем предварительное число зубьев шестерни по формуле:
Подберем согласно рекомендации [2] коэффициент формы зуба для 7-ой степени точности:
5.3 Подбор чисел зубьев и уточнение передаточных отношений
- количество зубьев центральной шестерни “a”.
Вычислим коэффициент по формуле: . Округлив до целого значения получим: .
Вычислим количество зубьев коронки “b” : .
Определим предварительное количество зубьев сателлита “g”:
Рассчитаем передаточное отношение планетарной передачи:
Определим погрешность: .
Так как то далее вычислим передаточные отношения:
5.4 Определение геометрических параметров зацепления передачи
Определим межосевое расстояние по формуле:
Вычислим начальные диаметры центральной шестерни “a” коронки “b” и сателлита “g” соответственно:
Определим диаметры окружности вершин зубьев центральной шестерни “a” коронки “b” и сателлита “g” соответственно:
Вычислим Sn центральной шестерни “a” коронки “b” и сателлита “g” соответственно:
5.5 Определение ширины коронки (колеса b)
Вычислим коэффициент формы зуба коронки по формуле:
Определим рабочую ширину зубчатого венца коронки при изгибе по формуле:
- коэффициент формы зуба;
- крутящий момент передаваемый сателлитом “g” коронке “b”;
- коэффициент формы зуба коронки ;
- диаметр сателлита “g” ;
- модуль зацепления;
- допускаемое изгибное напряжение коронки .
Рассчитаем коэффициент торцевого перекрытия по формуле:
Определим коэффициент учитывающий суммарную длину контактных линий по формуле: .
Вычислим ширину коронки с учетом контактной прочности:
Согласно рекомендации [2] так как то . Округляя до целого получим .
5.6 Проверочный расчет передачи на контактную прочность
Вычислим фактическое контактное напряжение по формуле:
- крутящий момент передаваемый центральной шестерней “a” сателлитe “g” ;
- диаметр центральной шестерни “a” ;
- передаточное отношение ;
- рабочая ширина зубчатого венца;
Так как то следовательно .
5.7 Проверочный расчет передачи на изгибную прочность
Вычислим фактические изгибные напряжения центральной шестерни “a” и сателлита “g”. Они должны быть меньше допускаемых: ;
Фактические напряжения вычислим по формуле:
согласно рекомендации [2] ;
а из предыдущих расчетов имеем: ;
5.8 Проверочный расчет передачи на статическую прочность при перегрузках
отношение согласно примечанию задания.
Так как способ обработки – цементация то согласно рекомендации [2]
Согласно рекомендации [2] найдем максимальное допускаемое изгибное напряжение по формуле: так как НВ>350. По приложению 2 предел прочности для стали 12Х2Н4А равен 1200 МПа следовательно МПа.
СледовательноМПа МПа МПа
Определение усилий в зацеплениях
1 Расчет усилий в зацеплениях цилиндрической передачи
Определим усилия в зацеплениях цилиндрической передачи. Полное усилие в зацеплении направлено по линии зацепления по общей нормали к профилю. Разложим силу на составляющие: - окружное усилие и силу (см. рис.3).
Вычислим окружное усилие .
Сила определяется по формуле где - угол зацепления тогда .
Определим полное усилие по формуле: .
2 Расчет усилий в зацеплениях планетарной передачи
Определим окружные усилия в центральной шестерне “a” и сателлите “g” по формулам: ;
Обоснование конструкции и определение размеров основных деталей и узлов привода
1 Предварительное определение диаметров валов и осей
В авиастроении применяют пустотелые валы для уменьшения массы летательного аппарата.
Определим предварительные диаметры валов по уравнению сопротивления материалов:
коэффициент пустотелости.
допускаемые напряжения кручения.
Тогда наружные диаметры (см. рис.5):
Наружные диаметры: так как то .
2 Эскизная компоновка и определение размеров основных деталей привода
Для проектирования выбираем вариант редуктора рассчитанный вручную по рекомендации преподавателя.
Результаты расчета и размеры основных деталей привода приведены в предыдущих параграфах.
3 Определение реакций в опорах валов
Упрощенно представим вал в виде балки нагруженной осевыми окружными и радиальными силами действующими в зацеплениях. Расчёт ведётся исходя из уравнений равновесия балки. Реакции опор определяем из уравнений статического равновесия: сумма моментов внешних сил относительно рассматриваемой опоры и момента реакции в другой опоре равна нулю.
Находим реакции опор. Схема нагружения в вертикальной плоскости.
Согласно уравнению моментов запишем:
Схема нагружения в горизонтальной плоскости.
Определяем суммарные реакции опор.
Находим реакции опор.
Схема нагружения в вертикальной плоскости.
RА= Fн -RВ =20782-+856=2934 кН.
4 Уточненный расчет валов и осей
4.1 Построение эпюры изгибающих и крутящих моментов
4.2 Расчет валов на статическую прочность в опасных сечениях
Проверочный расчет валов на выносливость
Проверяем опасное сечение с наибольшим изгибающим моментом (концентратор напряжения – эвольвентные шлицы).
Определяем моменты сопротивления изгибу и кручению.
где К –и Кt эффективные коэффициенты концентрации напряжений.
Определяем коэффициенты запаса прочности на выносливость:
Для легированной стали имеем:
Значение коэффициента учитывающего влияние асимметрии цикла принимаем:
Полученный коэффициент запаса больше допускаемого [S]=18. Расчет верен.
где К и Кt - эффективные коэффициенты концентрации напряжений.
Проверяем опасное сечение с наибольшим изгибающим моментом.
Значение масштабных факторов по изгибу и кручению:
Полученный коэффициент запаса больше допускаемого [S]=18 . Расчет верен.
5 Расчёт долговечности подшипников качения
Для всех подшипников принимаем :
Кинетический коэффициент V=1 т.к. в каждом случае вращается внутреннее кольцо а наружное неподвижно относительно приложенной нагрузки ;
Коэффициент безопасности Kd = 12 ;
Температурный коэффициент Kt = 1 .
Расчет долговечности подшипников входного вала
Выбраны подшипники №210 ГОСТ 8338-75 и №2210 ГОСТ 8328-75.
Опора 210 - шарикоподшипник радиальный его динамическая грузоподъемность равна С=35100 Н статическая С0=19800 Н
Динамическая приведенная нагрузка равна:
Долговечность подшипника равна:
Чтобы повысить ресурс подшипника применяем: более качественную подшипниковую сталь двойного (электрошлакового + вакуумно – дугового) переплава которая повысит грузоподъёмность подшипника на 50%.
Окончательно выбираем подшипники 210 из стали двойного (электрошлакового + вакуумно – дугового) переплава.
Опора 2210 - роликоподшипник радиальный его динамическая грузоподъемность равна С=45700 Н статическая С0=27500 Н
Окончательно выбираем подшипники 2210 из стали двойного (электрошлакового + вакуумно – дугового) переплава.
Расчет долговечности подшипников промежуточного вала
Выбраны подшипники №211 ГОСТ 8338-75 и №2211 ГОСТ 8328-75.
Опора 211 - шарикоподшипник радиальный его динамическая грузоподъемность равна С=43600 Н статическая С0=25000 Н
Окончательно выбираем подшипники 211 из стали двойного (электрошлакового + вакуумно – дугового) переплава.
Опора 2211 - роликоподшипник радиальный его динамическая грузоподъемность равна С=56100 Н статическая С0=34000 Н
Окончательно выбираем подшипники 2211 из стали двойного (электрошлакового + вакуумно – дугового) переплава.
Расчет долговечности подшипников выходного вала
Выбраны подшипники 7217
Опора 7217 - конический роликоподшипник радиально – упорный его динамическая грузоподъемность равна С=130000 Н статическая С0=10900 Н.
Окончательно выбираем подшипники 7217 из стали двойного (электрошлакового + вакуумно – дугового) переплава.
Расчет шлицевых соединений
Шлицевые соединения рассчитываются на напряжения смятия:
R – средний радиус шлицев;
f – коэффициент высоты профиля;
Допускаемое напряжение смятия [см]=100 МПа.
Модуль m=2 мм; число зубьев Z=21; L=48 мм.
Модуль m=2 мм; число зубьев Z=30; L=78 мм
Промежуточный внутренний вал
Модуль m=2 мм; число зубьев Z=30; L=68 мм
Модуль m=2 мм; число зубьев Z=40; L=77 мм
Для уменьшения потерь мощности на трение и снижения интенсивности износа трущихся поверхностей а также для предохранения их заедания задиров коррозии и лучшего отвода теплоты детали должны иметь смазку.
Используем масло марки ИМП-10. Масло подается через форсунки под давлением 4 атм. Смазываются все пары редуктора:
Для подшипников установленных на выходном валу спроектирована подача масла через форсунку и струя СОЖ попадает на тела качения.
Для подшипников установленных на сателлите и всей планетарной передачи предусмотрена система смазки через форсунку.
На подшипники установленные на промежуточном валу масло подается сверху из планетарной передачи и системы смазки выходного вала.
Для системы входного вала используется а также СОЖ из планетарной передачи.
К шлицам внутреннего вала предусмотрен подход масла изнутри.
В спроектированном редукторе предусмотрена система отвода отработанной СОЖ для её охлаждения и очистки.
Для избежания выброса масла из корпуса редуктора через уплотнения и стыки в верхней точке корпуса установлен суфлер-отдушина.
Манжетные уплотнения на входном и выходном валах предотвращают утечку масла из корпуса редуктора и препятствуют попаданию в него пыли и влаги извне.
В данной работе произведён расчёт цилиндрической и планетарной зубчатых передач редуктора вертолёта. Выбран материал для зубчатых колёс и определены допускаемые напряжения. Определены геометрические параметры зубчатых передач. Выполнены кинематический и энергетический расчёты редуктора. Проведена проверка прочности зубчатых передач по контактным и изгибным напряжениям. Выполнена проверка на статическую прочность при перегрузке. Проведен подбор и расчет подшипников на долговечность проектировочный и проверочные расчеты валов расчет шлицевых и резьбовых соединений продумана система смазки уплотнения.
СПИСОК ИСПОЛЬЗОВАННЫХ ИСТОЧНИКОВ
Оси валы и опоры качения. А.М. Циприн М.И. Курушин Е.П. Жильников.Куйбышев КуАИ 1976.
Подшипники качения. Справочник-каталог . Под.ред. В.Н. Нарышкина и Р.В. Коросташевского. М. Машиностроение 1984.
Конструирование узлов и деталей машин. П.Ф.Дунаев О.П.Леликов. М. Выс.шк. 1985
Курсовое проектирование деталей машин. В.Н. Кудрявцев и др. Л. Машиностроение 1984 .
Расчёт на прочность цилиндрической зубчатой передачи с использованием ЭВМ. “Электроника ДЗ–28”.
Курсовое проектирование по деталям машин для авиационных специальностей.
Сп-4.cdw

Сп-1.cdw

Сп-3.cdw

Сп-2.cdw

Сп-5.cdw

крышка подшипника.cdw

Неуказанные радиусы механической обработки 0
Неуказанные предельные отклонения размеров
МА-5 по ГОСТ 14957-76
колесо.cdw

HRC 58 63. Твёрдость сердцевины по HRC 37 44.
Неуказанные радиусы - 4 мм.
Неказанные предельные отклонения
1-1---.cdw

После сборки редуктор промыть маслом ИПМ-10 t=70
Главный редуктор вертолета
Передаточное отношение редуктора 11
Техническая характеристика
Частота вращения входного вала 2200 обмин
Частота вращения выходного вала 200 обмин
Ресурс работы редуктора 2000 ч
Относительное осевое смещение
Лапки стопорных шайб поз. 75
Рекомендуемые чертежи
- 25.01.2023
- 24.01.2023
Свободное скачивание на сегодня
- 23.02.2023