Проектирование производственного элеватора ёмкостью 55000 т



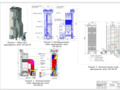
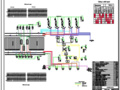
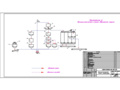
- Добавлен: 24.01.2023
- Размер: 4 MB
- Закачек: 1
Описание
Состав проекта
![]() |
![]() ![]() ![]() |
![]() ![]() ![]() |
![]() ![]() ![]() |
![]() ![]() ![]() |
![]() ![]() ![]() |
![]() ![]() ![]() ![]() |
![]() ![]() ![]() |
![]() ![]() ![]() |
![]() ![]() ![]() ![]() |
![]() ![]() ![]() ![]() |
![]() ![]() ![]() |
![]() ![]() ![]() |
![]() ![]() ![]() |
Дополнительная информация
введение.docx
Преимущество Казахстана в области зернового производства складывается из объемов пахотных земель запасов водных ресурсов; природно-климатических условий позволяющих выращивать высококачественное и экологически чистое зерно; относительно низкой по сравнению с крупнейшими странами-экспортерами стоимости ресурсов (энергии земли рабочей силы); территориальной близости Казахстана к важным и растущим рынкам сбыта таким как страны Центральной Азии Среднего и Ближнего Востока Южной Европы Северной Африки.
Эти факторы для Казахстана носят стратегический характер и учитывая предоставленные природой возможности в случае успешного развития экономики в перспективе можно будет ставить зерно в один ряд с такими экспортными товарами как нефть газ металл и электроэнергия. При этом надо учитывать что зерно является ежегодно возобновляемым ресурсом. Возможность длительного хранения и транспортабельности зерна определяют его ведущую роль в создании стратегических запасов продовольствия и ведущая роль в создании и хранении таких запасов отводится элеваторам которые осуществляют две функции: технологическую – преобразование разрозненных потоков зернового сырья поступающего от производителей в товарные относительно выровненные по качеству партии и экономическую – продвижение товара на внутреннем и внешнем рынках. Научно-обоснованный прогноз и техническая политика развития заготовительных элеваторов строится на анализе основных показателей производства и использования зерна в целом по республике и регионам. Эффективность производства зерна связана с объемами вложенных средств и в тоже время она в значительной степени зависит от погодных условий и стихийных бедствий. Показатель среднедушевого производства зерна (кгчел.) в отличие от предыдущих имеет норму. Согласно мировым нормативам производство 1 т зерна на человека в год покрывает все потребности страны: населения в продовольствии животноводства в кормах промышленности в сырье и сельского хозяйства в семенах. При этом уровне производства переходящие и страховые запасы обеспечивают её продовольственную безопасность [1].
Содержание по элеватору.doc
1 Задачи элеваторной промышленности
2 Структура элеваторной промышленности
Производственные элеваторы
1 Способы сушки зерна
2 Требования предъявляемые к зерносушилкам
3 Классификация зерносушилок
5 Зерносушилка У13-СШ-50
6 Зерносушилка ДСП-32
Технологическая часть. Расчет потребного основного технологического и транспортного оборудования
1 Выбор принципиальной схемы элеватора
2 Определение годового объема приемки и отпуска зерна и объемы работы элеватора в наиболее напряженные сутки
3 Расчет необходимого оборудования для приемки обработки и отпуска зерна
3.1 Устройство для контроля качества зерна
3.2 Выгрузка зерна из автомобильного транспорта
3.3 Разгрузка зерна из железнодорожных вагонов
6 Внутреннее перемещение зерна
7 Определение необходимого числа основных норий
8 Выбор типа и количества весов рабочего здания
9 Выбор типа и количества распределительных кругов
10 Выбор производительности и количества транспортеров
11 Обработка и хранение отходов
12 Расчет вместимости и высот бункеров
12.1 Расчет вместимости надсепараторного и подсепараторного бункеров
12.2 Расчет вместимости надсепараторного бункера для отходов
13 Расчет вместимости бункера для отходов
14 Расчет вместимости силосов
Описание рабочей схемы движения зерна и отходов на элеваторе
Список использованной литературы
Приложение А Принципиальная схема движения зерна и отходов на элеваторе
Приложение Б Техническая характеристика оборудования
Сушка зерна. часть 3.docx
Сушка – это процесс удаления влаги из твердых влажных пастообразных и жидких материалов путем ее испарения и отвода образовавшихся паров.
Сушка зерна — один из самых эффективных приемов подготовки зерна к длительному хранению. Она улучшает хлебопекарные мукомольные и другие товарные качества зерна значительно сокращает расходы по перевозкам повышает производительность перерабатывающих предприятий (мельниц крупорушек и т. п.) и уменьшает износ оборудования а следовательно и стоимость переработки.
1 Способы сушки зерна
Для удаления излишней влаги из зерна его сушат на солнце или проветривают с применением вентиляторов. Однако такая сушка может применяться только при благоприятных условиях погоды и небольших партиях зерна.
По способам тепловой сушки различают:
- сушка горячим и нагретым воздухом
- сушка током высокой частоты;
- сушка с нагревом зерен;
- сушка смесью топочных газов;
- сушка инфракрасными лучами;
- сушка во взвешенном состоянии
Но чаще используют сушку нагретым воздухом. Этот методом применяет уже более 50 лет.
Способы искусственной сушки разнообразны. Они различаются главным образом по признаку передачи тепла зерну и удаления из него влаги и по характеру среды. Тепло может передаваться зерну контактным способом т. е. соприкосновением зерна с нагретой поверхностью различных сушильных печей (подовые сушилки) подогретым воздухом или смесью воздуха с дымовыми газами называемой газовой смесью.
В первом случае воздух соприкасаясь с нагретым зерном отнимает от него часть тепла и одновременно поглощает испаряющуюся из зерна влагу.
Сушка подогретым воздухом может быть представлена в такой простейшей схеме: атмосферный воздух содержащий известное количество влаги нагревается калорифером и повышает влагоемкость. Поступая затем под влиянием искусственной тяги в сушильную камеру подогретый воздух нагревает зерно и одновременно поглощает выделяющуюся из него влагу. Со сниженной температурой и повышенной влажностью (относительной и абсолютной) воздух удаляется из сушилки.
Сушка смесью воздуха с дымовыми газами отличается от сушки подогретым воздухом лишь способом нагрева воздуха. В смесительной камере атмосферный воздух смешивают с дымовыми газами в количестве необходимом для достижения требуемой температуры.
По составу газовая смесь близка к воздуху: на 1 м3 дымовых газов в смесительной камере добавляется примерно 15 25 м наружного воздуха.
При сушке зерна газовой смесью расходуется в 2 25 раза меньше топлива чем при сушке нагретым воздухом и потому она получила наибольшее распространение. В настоящее время почти все отечественные сушилки работают на газовой смеси.
Для сохранения качественных показателей зерна при искусственной сушке важное значение имеет предельная температура воздуха или газовой смеси поступающих в сушильную камеру максимальная температура нагретого зерна и продолжительность сушки.
Числовые значения отдельных факторов режима сушки зависят от типа и степени совершенства конструкций сушилок назначения зерна и его начальной влажности. Если конструкция сушилки менее совершенна значит менее равномерно распределяется тепло среди всей массы зерна в сушильной камере и тем ниже должна быть температура теплоносителя. В сушилках с равномерным движением теплоносителя и интенсивным перемешиванием зерна можно повысить температуру и скорость движения теплоносителя (воздуха или газовой смеси).
Высокая температура сушащей среды вызывая быстрый нагрев и энергичное испарение влаги с поверхности зерна отрицательно влияет на его семенные качества поэтому для сушки семенного зерна назначают более низкие температуры теплоносителя и нагрева зерна чем для продовольственного зерна.
Одним из условий правильно организованной сушки зерна является обязательное последующее охлаждение его до температуры близкой к температуре наружного воздуха.
2 Требования предъявляемые к зерносушилкам
В рационально построенной зерносушилке зерно сушится без снижения его качества. Ее стоимость а также эксплуатационные затраты на топливо энергию обслуживание ремонт и т. п. приходящиеся на 1 т просушенного зерна должны быть наименьшими. Кроме того зерносушилка должна быть компактной несложной по устройству приспособленной для работы на местном топливе безопасной в пожарном отношении удобной для осмотра и обслуживания при полной механизации всех процессов сушки и охлаждения зерна.
3 Классификация зерносушилок
Зерносушилки для искусственной сушки зерна в сельском хозяйстве на хлебоприемных пунктах элеваторах мельничных комбинатах и других зерноперерабатывающих предприятиях классифицируются:
-по способу сушки зерна — горячим воздухом или смесью горячих дымовых газов с наружным воздухом;
-по способу загрузки и выгрузки зерна — сушилки периодического действия с периодической загрузкой и выгрузкой просушенного зерна и сушилки непрерывного действия с автоматическим непрерывным движением зерна через сушильный аппарат;
-по способу расположения зерна—сушилки с расположением зерна горизонтальными вертикальными или наклонными слоями и
-сушилки в которых зерном заполняется вся шахта сушильного аппарата (шахтные сушилки);
-по схеме движения теплоносителя по отношению к просушиваемому зерну и расположению вентиляторов по отношению к сушильной камере;
-по состоянию (структуре) зернового слоя при сушке (сплошной пересыпающийся слой взвешенное состояние зерна);
-по конструкции сушильного аппарата — стационарные или передвижные;
-по производительности (в сутки или час) и снижению при этом процента влажности зерна.
Виды зерносушилок представлены несколькими основными типами: шахтные вибрационные барабанные камерные рециркуляционные.
Шахтные зерносушилки состоят из двух шахт которые имеют равную вместимость и вертикальную норию*. Обычно их монтируют на постоянном фундаменте. Принцип действия простой. Зерно под действием собственного веса проходит через сушилку. Подача горячего воздуха осуществляется снизу вверх. После сушки зерно подаётся в специальные охлаждающие камеры. Шахтные сушилки рассчитаны на партии в 8 и 16 тонн зерна. Для продовольственного и семенного зерна режимы сушки различны. Так при сушке продовольственного зерна за один цикл удаляется 5-6% влаги и производительность составляет 8-16 тоннчас в то время как у семенного зерна удаляется 3-4% влаги при производительности 4-8 тоннчас. Для сушки зерна в шахтных сушилках необходима предварительная очистка от соломы и шелухи для предотвращения возгорания.
Барабанные сушилки по производительности и удалению влаги за один цикл (5-6% продовольственное зерно и 3-4% семенное) не уступают шахтным. Основные конструктивные элементы сушилки: топка барабан камера охлаждения. Ось барабана оснащена металлическими пластинами. Они заставляют зерно двигаться по горизонтальной спирали. Барабанные сушилки отличаются компактностью. Благодаря этому они легко транспортируются. Но не смотря на это чаще всего они применяются в качестве стационарных.
Камерные сушилки занимают значительную площадь. Подача зерна осуществляется механическим способом. У сушилок данного типа имеется воздуховод. Они состоят из двух камер с перфорированным полом. Зерно насыпается слоем не превышающим 80 см. В противном случае зерно может плохо просушиться. Процесс сушки заключается в продувании зерна воздухом который может быть немного подогрет. В сушилку загружается первый слой затем после его высыхания второй. И так далее. До полного заполнения силоса зерном. Для наполнения силоса зерном и удаления слоя равной толщины существует специальное оборудование. Для равномерного удаления влаги в сушилке имеются встроенные шнеки для перемешивания зерна в процессе сушки. Влага удаляется за одну загрузку до сухого состояния зерна.
Рециркуляционные зерносушилки конструктивно похожи на шахтные. Но у них есть существенные отличия. В этих сушилках зерно которое подаётся в шахту сверху нагревается за несколько секунд и под действием своего веса падает на дно шахты. Здесь часть зерна отправляется на хранение а часть направляется в другую шахту в которой происходит перемешивание уже нагретого сухого зерна с только что поступившим сырым. В результате зерно сразу частично высушивается. Далее оно отправляется в первую шахту для сушки. Процесс смешения сухого и влажного зерна введён не случайно. Дело в том что он позволяет экономить топливо. Такие сушилки предназначены для продовольственного зерна. Их производительность достаточно велика и может достигать 70 тоннчас.
5 Зерносушилка У13-СШ-50
Перед закладкой на хранение зерновую массу необходимо просушить. В противном случае возникнут потери части урожая из-за гниения и размножения патогенных микроорганизмов. А сухое зерно предотвращает размножение вредных бактерий в результате чего зерно хранится долгое время.
Технология сушки зерна основывается на цепочке из нескольких связанных между собой теплофизических операций которые производятся в определенном порядке. Первая операция любой технологии сушки зерна это передача тепла к поверхности зерна от сушильного агента что приводит к испарению жидкости с поверхности. Далее на поверхность зерна выводится жидкость изнутри которая тоже испаряется. Заключительная операция сушильным агентом поглощается вся жидкость которая испарилась и выносится из зерносушилки в атмосферу.
Степень нагревания зерна и температура сушильного агента имеют непосредственное влияние на качественные показатели сухого зерна. Испарение жидкости происходит интенсивнее при высоких температурах агента. Однако чересчур высокий уровень температуры и пересушивание негативным образом сказывается на качестве зерна: снижается показатель всхожести и энергии прорастания сокращается содержание и качество клейковины образуются трещины на поверхности..
В настоящее время различают несколько способов сушки зерна. Каждый способ имеет свою технологию сушки зерна которая отличается видом подачи тепла к зерновой массе.
Зерносушилка шахтная У13-СШ-50 предназначена для сушки семян пшеницы подсолнуха кукурузы и других зерновых культур обеспечивая высокий съем влаги (6 %) и очистку отработанного агента сушки (воздуха) от легких примесей. Производительность зерносушилки при снижении влажности пшеницы с 20% до 14% с объемной массой 750 - 760 кгм3 при температуре окружающей среды +10°С относительной влажности атмосферного воздуха 70% и при атмосферном давлении 991 кПа составляет не менее – 50 тч.
Общая потребляемая мощность зерносушилки – 94 кВт (при полной комплектации).
Расход газа при температуре окружающей среды +10°С не более – 450 м3ч (12 – 15 м³%т при давлении газа 68 – 15 кПа Hu=100 кВтmn³)
В случае отклонения в показателях давления газа а также его отопительного качества они должны быть обговорены до начала изготовления заказанной сушилки.
Расход агента сушки не более – 150 000 м3ч.
Зерносушилка состоит из вертикальной сушильной шахты гарячой камеры и холодной камеры составляющих единую конструкцию из металлических секций а также выпускных механизмов надсушильного бункера вентиляционного оборудования теплогенератора шкафа управления системы очистки отработанного агента сушки (как дополнительная опция).
Зерносушилка может быть изготовлена из оцинкованного или черного металла.
6 Зерносушилка А1-ДСП-32
Зерносушилка А1-ДСП-32 предназначена для сушки различных зерновых зернобобовых культур и маслосемян обеспечивая высокий съем влаги очистку отработавшего теплоностителя (агента сушки) и воздуха от легких примесей и пыли. Сушильная и охладительные шахты работают на нагнетание
Зерносушилка работает на газообразном топливе но может работать на смеси топочных газов с воздухом
Зерносушилка А1-ДСП-32 состоит из двух вертикальных шахт и составляет единую конструкцию из металлических секций тепловлагообменника с регулируемым охлаждением охладителя выпускных механизмов надсушильных бункеров вентиляторов норий топки и шкафа управления
Сырое зерно подают из оперативного бункера и смешивают его с сухим нагретым зерном которое поступает из второй сушильной шахты. Смесь направляют в надсушильный бункер (он же служит тепловлагообменником) и далее в первую сушильную шахту и тепловлагообменник с регулируемым охлаждением
Затем зерно поступает на вторую рециркуляционную норию которая подает его в надсушильный бункер второй сушильной шахты. Из надсушильного бункера зерно направляют во вторую сушильную шахту и в охладитель шахтного типа. Выпуск просушенного и охлажденного зерна производят выпускными механизмами периодического действия
Агент сушки и воздух отработанного теплоносителя из топки засасывается вентиляторами Ц - 70 - 10 смешивается и подается через диффузор в напорно-распределительную камеру в подводящие короба сушильных шахт проходит через слой зерна и выходит из отводящих коробов в осадочную камеру и затем в атмосферу. Просушенное и охлаждённое зерно из второй сушильной шахты подаётся на норию сухого зерна и далее в накопительный бункер или зернохранилище
Контроль состояния зерна по влажности осуществляется поточным влагомером датчики которого устанавливаются в шахте окончательной сушки. Влагомер может быть автоматическим (для управления работой выпускным механизмом) или для визуального наблюдения. Поставка влагомеров производится отдельно
Контроль температуры теплоносителя (агента сушки) нагрева зерна и температуры охлаждённого зерна осуществляется первичными датчиками установленными в диффузорах и шахтах где зерно нагревается максимально и затем охлаждается атмосферным воздухом. Вторичный датчик манометрический или электронный устанавливается в шкафу. Для контроля температуры в необходимой точке используется переключатель
Система управления и контроля автоматизации зерносушилки обеспечивают стабильный и экономичный режим сушки зерна при минимальных затратах ручного труда
Конструкция зерносушилки соответствует требованиям безопасности установленным в действующих стандартах. Вращающиеся и движущиеся части закрыты ограждениями. Горячие поверхности имеют теплоизоляцию. Электробезопасность обеспечивается прокладкой электропроводов в металлических трубах и гибких проводах. Зерносушилка имеет автоматическое устройство контроля наличия факела а также звуковую и световую сигнализацию
Для эксплуатации зерносушилки допускается специально обученный персонал под наблюдением опытного специалиста. Весь процесс сушки зерна фиксируется в вахтенном журнале.
Приложение Б.docx
Таблица Б1 – Техническая характеристика автомобилеразгрузчика КГС-100-500
Производительность техническая тч
Большой платформы мм
Боковой платформы мм
Время наклона платформы:
Большой платформы сек.
Боковой платформы сек.
Время опускания платформы:
Угол наклона платформ град.
Таблица Б2 – Техническая характеристика сепаратора для предварительной очистки зерна марки А1-ДЗС
Производительность (на зерне пшеницы с объемной массой не менее 750 тм3 и влажностью не более 16%) тч
Содержание нормального зерна в крупных примесях %
Суммарная мощность двух электровибраторов кВт
Расход воздуха на аспирацию м3ч не более
Частота колебаний сита об.мин
Амплитуда колебаний сита мм
Таблица Б3 – Техническая характеристика ситовоздушного сепаратора А1-БИС-100
Производительность тч
Эффективность очистки зерна %
Число ситовых рам шт.:
Размеры ситовых рам мм
Частота колебаний ситового кузова об.мин
Радиус колебания ситового кузова мм
привода электродвигателя
Расход воздуха на аспирацию м3ч
Таблица Б4 – Техническая характеристика триерного блока Р1-ББТ-700-16
Эффективность очистки зерна пшеницы % не менее:
Установленная мощность кВт
Содержание основного зерна в отходах %
Расход воздуха на аспирацию м3мин
Частота вращения цилиндра обмин
Габаритные размеры мм
Таблица Б5 – Техническая характеристика сепаратора А1-БМС-6
Колебания ситового корпуса:
Угол наклона сит град
В том числе в канале продувки:
Мощность электродвигателя кВт
Таблица Б6 – Техническая характеристика нории НМ-175
НМ-175 высотой от 11 м до 25 м
НМ-175 высотой от 26 м до 35 м
НМ-175 высотой от 36 м до 50 м
НМ-175 высотой от 51 м до 60 м
Производительность по зерну при влажности 17 % натура 750 гл тч не менее
Максимальная высота подъема м
Расход воздуха на аспирации нории м3час
Масса при максимальной высоте кг
Таблица Б7 – Техническая характеристика ленточного конвейера У9-УКБ-65
Мощность эл. двигателя кВт
Таблица Б8 – Техническая характеристика поворотных труб ТП-6
Количество выпускных патрубков шт
Диаметр выпускных патрубков мм
Диаметр входного патрубка мм
Частота вращения трубы обмин
Габаритные размеры мм:
Таблица Б9 – Техническая характеристика весов ДН-2000
Взвешиваемый продукт
Пределы дозирования кг
Вместимость ковша м3
Мощность привода кВт
Документы начальные.doc
ВОСТОЧНО-КАЗАХСТАНСКИЙ ГОСУДАРСТВЕННЫЙ УНИВЕРСИТЕТ ИМ. С.АМАНЖОЛОВА
ФАКУЛЬТЕТ МАТЕМАТИКИ ФИЗИКИ И ТЕХНОЛОГИЙ
КАФЕДРА ПРОФЕССИОНАЛЬНОГО ОБУЧЕНИЯ И ТЕХНОЛОГИИ
г. Усть-Каменогорск 2012 г.
ПОЯСНИТЕЛЬНАЯ ЗАПИСКА
к курсовой работе по дисциплине
«Проектирование перерабатывающих производств c основами САПР»
к.ф. – м.н. Дёмина И.А.
Усть-Каменогорск 2012 г.
на курсовую работу по дисциплине
для специальности 5В072800 – «Технология перерабатывающих производств»
студенту (ке) Воротниковой Виктории
группа 4Т-1 (очное отделение)
факультет математики физики и технологий
Тема курсовой работы: Проектирование производственного элеватора ёмкостью 55000 т.
-тип зернохранилища (элеватора) - производственный;
-зона строительства - район с сырым и влажным зерном;
- вместимость элеватора - 55000 т;
- коэффициент оборота - 11;
- расчетный период заготовок - 30 суток;
- с автомобильного транспорта - 30 %;
- с железнодорожного транспорта –70 %;
-на производство – 100 %;
-качество зерна поступающего от хлебосдатчиков:
-сухое и средней сухости - 10 %;
-сырое с влажностью до 22 % - 35 %;
-сырое с влажностью до 26 % - 30 %;
-по содержанию сорной примеси:
-средней чистоты - 20 %;
-сорное до ограничительных кондиций - 50 %;
-сорное свыше ограничительных кондиций - 30 %;
-по содержанию зерновой примеси:
-чистое (до 1% включительно) - 10 %;
-средней чистоты (от 1% до 3%) - 40 %;
-сорное до ограничительных кондиций (от 3 до 5%) - 50 %;
-сорное свыше ограничительных кондиций (свыше 5%) - 0 %.
Содержание курсовой работы
Содержание пояснительной записки (перечень подлежащих разработке вопросов):
Введение структура элеваторной промышленности производственные элеваторы сушка зерна зерносушилки расчет технологического и транспортного оборудования (норий) элеватора технологическая схема движения зерна на элеваторе заключение список использованной литературы.
Перечень графического материала (с точным указанием обязательных чертежей):
Рабочая схема движения зерна на элеваторе емкостью 55000 т (формат А1).
Технологическая схема зерносушилки У13-СШ-50 (формат А1).
Дата выдачи « 6» сентября 2012 г.
Дата окончания « 6 » декабря 2012 г.
Руководитель курсовой работы: к.ф.-м.н. ассоц.профессор Дёмина И.А.
Студент (ка) Воротникова В.Н.
Принципиальная схема элеватора практическая работа №1. Воротникова.dwg

Конвейер приёмный с водного транспорта
Конвейер приёмный с автомобильного транспорта
Бункер надсепараторный
Контрольный сепаратор
Подсепараторный бункер
Подсилосный конвейер
Автомобильный транспорт
Приложение А Принципиальная схема движения зерна
Расчет. Часть 4.docx
1 Выбор принципиальной схемы элеватора
Выбираем одноступенчатую схему в которой весы расположены выше надсилосных конвейеров. Приемку зерна с автомобильного и железнодорожного транспорта предусматриваем через накопительные бункера.
2 Определение годового объема приемки и отпуска зерна и объемы работы элеватора в наиболее напряженные сутки
В соответствии с формулой 1 рассчитываем годовой грузооборот элеватора в соответствии:
где E – паспортная вместимость зернохралища т
Ko - коэффициент оборота.
В соответствии с формулой 2 определяем годовой объем приемки и отпуска зерна в зависимости от вида транспорта:
где Q – годовой грузооборот элеваторат
n – доля приемки зерна с определенного вида транспорта %
Тогда годовой объем приемки зерна с автотранспорта составляет
Годовой объем приемки зерна с железнодорожного транспорта составляет
Максимальное суточное поступление зерна автотранспортом ас определяем по формуле 3:
где 08–коэффициент учитывающий поступление зерна в расчетный период заготовок;
–количество зерна поступающего от хлебосдатчиков автотранспортом за весь период заготовок т;
Кс – коэффициент суточной неравномерности поступления зерна;
Пр – продолжительность расчетного периода заготовок сут.
При этом величину коэффициента суточной неравномерности поступления зерна выбираем в соответствии с таблицей 1.2 для элеватора с расчетным периодом заготовок Пр=30 суток и объемом заготовок за расчетный период равным 08·=08·18150=14150 т. Следовательно в соответствии с таблицей 1.2 Кс=16. Таким образом величина ас составит:
Максимальное часовое поступление зерна автотранспортом находится в соответствии с формулой 4:
где Кч – коэффициент часовой неравномерности поступления зерна установленный технологическими изысканиями а для типовых проектов в соответствии с таблицей 1.3 составит 29;
t – расчетное время подвоза зерна автотранспортом в течение суток t=24ч.
Расчетный (максимальный) суточный объем приемки и отпуска зерна на железнодорожный транспорт Вр пр (отп) находят в соответствии с формулой 5:
где Ажд – годовой объем приемки или отпуска зерна на железнодорожный транспорт т;
Км1Кс1–коэффициенты месячной и суточной неравномерности. Принимать по данным МПС установленным изысканиями. Для типовых проектов коэффициент месячной неравномерности Км1=2 коэффициент суточной неравномерности Кс1=25;
– расчетное число суток в году в течение которых производится разгрузка (погрузка).
3 Расчет необходимого оборудования для приемки обработки и отпуска зерна
3.1 Устройство для контроля качества зерна
В соответствии с таблицей 1.10 [8] элеватор с годовым объемом заготовок 60500т относится ко II группе предприятий. Для II группы предприятий предусматривают приемную центральную и цеховую лаборатории.
Согласно таблице 1.11 [8] число механизированных пробоотборников типа А1-УПЗ-А или А1-УПП оставит 4по два пробоотборника с двух сторон приемной лаборатории число устройств для формирования среднесуточных проб У1-УФ-5 с пультом управления-2шт. число бункеров для среднесуточных проб (50х2)=2шт.
С учетом выбранного оборудования принимаем приемную лабораторию по типовому проекту.
Примерная численность работников приемной лаборатории составит на период заготовок 34 человека в том числе:
–на приемке зерна – 6 чел;
–на разделке и анализе среднесуточных проб – 14 чел;
–на контроле сушки – 3 чел;
–на контроле очистки – 3 чел;
–на отгрузке и приемке с железнодорожного транспорта – 6 чел;
–на контроле хранения зерна – 2 чел.
На период работы в течение года в соответствии с таблицей 1.13 [8] – 10 человек в том числе:
–на контроле качества зерна в процессе подработки и составления помольных партий – 3 чел;
–на контроле качества зерна в процессе сушки – 1 чел;
–на контроле качества зерна при отгрузке и приемке с железнодорожного транспорта – 4 чел;
–на контроле качества зерна в процессе хранения – 2 чел.
3.2 Выгрузка зерна из автомобильного транспорта
Для расчета необходимого числа технологических линий приемки зерна с автомобильного транспорта по таблице 1.17 [8] находят число партий зерна поступающих на предприятие в течение расчетного периода заготовок Р=5 шт
Затем по таблице 1.18 [8] определяем число партий поступающих на предприятие за сутки Рс =3 шт.
Затем путем перебора возможных вариантов по числу партий зерна направляемых на линию в сутки Рсл и производительностью транспортного оборудования Qл в соответствии с формулой 6 находим Nл для приемного устройства с накопительными бункерами:
где ач – максимальное часовое поступление зерна автотранспортом тч;
– коэффициент учитывающий разнотипность средств доставки;
Qл – производительность линии приемки зерна с автотранспорта тч;
Кк – коэффициент учитывающий снижение производительности транспортного оборудования при перемещении культур с натурой отличающейся от пшеницы Кк=1 в соответствии с таблицей 1.14 [8];
Квз –коэффициент снижения производительности транспортного оборудования при перемещении зерна различного по влажности и засоренности.
Квз -определяем в соответствии с таблицей 1.5 [8] с учетом средневзвешенного качества зерна. Поступающего автомобильныи транспортом.
Средневзвешенная влажность зерна в соответствии с формулой 7 составит:
где 154035 – качество зерна поступающего от хлебосдатчиков по влажности в соответствии с заданием %;
51620–влажность зерна пшеницы сухого и средней сухости влажного а также сырого с влажностью до 20% в соответствии с приложением Б [3] %.
Средневзвешенная сорная примесь в соответствии с формулой 8 составит:
где 203050 – качество зерна поступающего от хлебосдатчиков в соответствии с заданием %;
55 35 –содержание сорной примеси в зерне пшеницы средней чистоты в сорном зерне до ограничительных кондиций в сорном зерне свыше ограничительных кондиций в соответствии с приложением Б [3] %.
Средневзвешенная зерновая примесь в соответствии с формулой 9 составит:
где 10 40 50 – качество зерна поступающего от хлебосдачиков в соответствии с заданием %;
25 45–содержание зерновой примеси в зерне пшеницы чистом средней чистоты и сорном до ограничительных кондиций %.
Итого средневзвешенное содержание отделимой примеси в соответствии с формулой 10 Qср.вз. составит:
Таким образом Квз =08.
Подбираем число технологических линий Nл для производительности транспортного оборудования Qм=100тч.
Принимаем число партий поступающих на линию =3тогда по таблице 1.14 [8] принимаем G=8т находим Qл=75тч тогда Nл будет равно:
При подаче трёх партий на одну линию а всего их две то тогда примут 6 партий при необходимости 3 партий.
Подбираем число технологических линий Nл для производительности транспортного оборудования Qм=175тч
Принимаем число партий поступающих на линию =3тогда по таблице 1.14 [8] принимаем G=8т находим Qл=175тч тогда Nл будет равно:
При этом идет подача трёх партий на одну линию при необходимости 3 партий в сутки
Таким образом для Qп = 175тч необходимо принять Nл=1=3при этом соблюдается условие формулы 11:
где Рс – число партий поступающих на предприятие сут;
n – число линий приемки зерна с автотранспорта шт;
– число партий направляемых на i-тую линию в сутки
Рассчитываем производительность автомобилеразгрузчика Qa для выбранного варианта по формуле 12:
где – техническая производительность автомобилеразгрузчика определенной марки в зависимости от средней грузоподъемности автомобилеразгрузчика Ga в соответствии с таблицей 1.15 [8] равна 140 тч;
Кк– коэффициент снижения технической производительности автомобилеразгрузчика в зависимости от производительности транспортирующего оборудования числа партий поступающих на линии в сутки средней грузоподъемности автотранспорта в соответствии с таблицей 1.16 равен 088;
Квз– коэффициент изменения производительности автомобилеразгрузчика в зависимости от состояния зерна по влажности и засоренности равен 08;
– коэффициент учитывающий разнотипность средств доставки зерна.
Принимаем марку автомобилеразгрузчика ГУАР-15с с производительностью 8 тч.
Так как Qa>Qл (Qa=97 тч Qл=175 тч) следует предусмотреть установку 3 автомобилеразгрузчиков на линию. Общее число автомобилеразгрузчиков ГУАР-15с с учетом числа приемных линий составит 3 шт.
Вместимость приемных бункеров в соответствии с рисунком 1 под каждым автомобилеразгрузчиком принимаем 30 т.
Так как сечение бункера составляет 3х3 м следовательно АВ=3м. ОХ – высота пирамиды вычисляется по формуле 13:
h1 h2 – высота конусной и прямоугольной части бункера; α=450 – угол естественного откоса
Рисунок 1. Бункер для приема зерна с автотранспорта и его разрез
Сторона выпускного отверстия NC=04 [3] тогда КХ вычисляется по формуле 14:
Найдем объем усеченной пирамиды в соответствии с формулой 16:
где S1 и S2 – площадь большего и меньшего сечения пирамиды.
Вместимость бункера в соответствии с формулой 17 составит:
где V1V2 – объем конусной и прямоугольной части бункера м3;
γ – объемная масса тм3;
5 – коэффициент вместимости бункера.
Высота прямоугольной части бункера вычисляется по формуле 18:
Высота всего бункера складывается из суммы h1 и h2 и составляет 603м. Так как бункер получился очень высоким делим его на 2 более маленьких бункера. Следовательно принимаем 3 бункера высотой 3 м и вместимостью 30 т.
3.3 Разгрузка зерна из железнодорожных вагонов
Расчетный (максимальный) объем приемки зерна с железнодорожного транспорта составляет 30тсут. Принимаем массу зерна в одной подаче 1000 т за одну подачу.
Время разгрузки одной подачи принято 316 ч.
Необходимое количество приемных потоков определяем по формуле:
где Qпод – масса зерна в одной подаче т;
Qтр –производительность убирающего транспортного потока принята с учетом производительности разгрузки вагона – зерновоза равной 500тч;
Ки – коэффициент использования норий на данной операции в соответствии с таблицей 1.18 [3] равен 09;
Кк – коэффициент учитывающий изменения производительности оборудования в зависимости от просушиваемой культуры равен 1;
Т – общая продолжительность разгрузки одной подачи вагона ч.
Необходимое число разгрузочных точек определяем по формуле:
6 – время разгрузки при одной подаче ч;
Qрм – эксплуатационная производительность вагоноразгрузчика тч. В соответствии с приложением Б1 [4] принимаем производительность устройства для разгрузки вагонов зерновозов через 2 пары люков 80тч.
С учетом объемно планировочных решений устройства для разгрузки жд вагонов целесообразно иметь 1 разгрузочную точку.
С учетом максимального суточного объема приемки зерна выбираем величину подачи 1000 т. Принимаем что в первую смену обрабатывается одна подача вагонов. Число вагонов в одной подаче рассчитывается по формуле:
Ев – грузоподъемность вагона т.
Производительность накопления приемного бункера QH находят в соответствии с таблицей 4.2 [3] QH=500 тч (вагон-зерновоз).
Производительность опорожнения приемного бункера определяется по формуле:
где Qкп – паспортная производительность приемного конвейера тч;
Ки – коэффициент использования паспортной производительности приемного конвейера в соответствии с таблицей 4.3 [3] Ки=075.
Необходимая вместимость приемного бункера Еб рассчитывается в соответствии с формулой:
где Ев –грузоподъемность вагона т;
Qн–производительность наполнения приемного бункера тч. принимаем равной эксплуатационной производительности вагоноразгрузчиков то есть 500 тч в соответствии с таблицей 4.2 [3];
Qо–производительность опорожнения приемного бункера тч. Принимаем равной фактической производительности приемного конвейера – 80тч.
Время наполнения tH и опорожнения t0 приемного бункера находится в соответствии с формулами:
Qн–производительность наполнения приемного бункера тч. Принимаем равной эксплуатационной производительности вагоноразгрузчиков то есть 500 тч в соответствии с таблицей 4.2 [3];
где Ев – грузоподъемность вагона т;
Qо–производительность опорожнения приемного бункера тч.
Принимаем равной фактической производительности приемного конвейера – 80тч.
Бункер и его разрез представлены на рисунке 2.
Так как сечение бункера составляет 4х4 м следовательно АВ=4м. ОХ – высота пирамиды вычисляется по формуле 26:
Рисунок 2. Бункер для приема зерна с жд транспорта и его разрез
Сторона выпускного отверстия NC=04 [3] тогда КХ вычисляется по формуле;
Найдем объем усеченной пирамиды в соответствии с формулой 16:
Тогда в соответствии с формулой 17 V2 будет равно:
Высота всего бункера складывается из суммы h1 и h2 и составляет 7 м. В связи с большой высотой бункера делим его на два меленьких бункера высотой 45 м и вместимостью 30 т.
Расчет начинается для подбора оборудования для предварительной очистки. В соответствии с формулой 34 определяем фактическую производительность машин для предварительной очистки
где Qсппред – паспортная производительность машин используемых для предварительной очистки тч;
Кко – коэффициент зависящий от культуры зерна влажности и содержания отделимой примеси.
Паспортную производительность машин принимем 175 тч величину Кко находим в соответствии с таблицей 1.21 [3]. При средневзвешенной влажности зерна 208% и содержания отделимой примеси 755% Кко=08.
Число машин для предварительной очистки Nпр.о. находим по формуле:
Принимаем сепаратор марки А1-ДЗС производительностью 175тч техническая характеристика представлена в приложении Б2.
Общую производительность сепараторов для очистки зерна SQc рассчитываем в соответствии с формулой:
где Пр –продолжительность расчетного периода заготовок сут;
А1А2 Аn–количество зерна данной культуры поступающего на пред приятие в течение всего периода заготовок т;
Кко1 Кко Ккоn–коэффициенты зависящие от культуры зерна влажности и содержания отделимой примеси.
Необходимое число сепараторов находим в соответствии с формулой:
где SQc – общая производительность сепараторов для очистки зерна тч;
Qсп – паспортная производительность сепаратора тч.
Принимаем сепаратор А1-БИС-100 производительностью 100 тч техническая характеристика представлена в приложении Б3.
Необходимое число триеров Пт определяем в соответствии с формулой:
где Апр – количество зерна поступающего от хлебосдатчиков за весь период заготовок т;
φ – доля зерна подлежащего очистке на триерах. При разработке типовых проектов принимаем φ=10%;
Qтр – паспортная производительность триера тч.
Принимаем к установке 1 триерный блок Р1-ББТ-700-16. Техническая характеристика представлена в Приложении Б4.
Годовой объем сушки зерна поступающего от хлебосдатчиков Ас рассчитываем по формуле:
где Апр – количество зерна поступающего от хозяйств производимый за весь период заготовок т;
Кв – коэффициент перевода физических тонн в плановые тонны сушки устанавливают исходя из количества влажного и сырого зерна в общем объеме заготовок. Для типовых проектов для районов с сырым и влажным зерном Кв=11;
Киср–средневзвешенный коэффициент учитывающий изменение производительности зерносушилок в зависимости от назначения зерна Киср=10;
Кксср–средневзвешенный коэффициент учитывающий изменения производительности зерносушилок в зависимости от просушиваемой культуры Кксср=10.
Число партий влажного и сырого зерна требующего сушки в соответствии с таблицей 1.24 [8] cоставляет 10. Величину партий зерна определяем в соответствии с таблицей 1.9 [8].
Принимаем производительность зерносушилки Qзсп1=32 пл.тч как видно из таблицы 1.26 [3] эта сушилка может просушить 5 партий зерна за 30 суток в количестве 7100 пл.т при необходимости 58564 пл.т. Затем 3 партии направляем на вторую сушилку производительностью Qзсп2=32 пл.тч которая просушит 17100 пл.т при необходимости 164044 пл.т. Оставшиеся 2 партии объединяем в 1 партию и направляем на 3-ю сушилку производительностью Qзсп3=50 пл.тч которая может просушить 31400 пл.т. при необходимости 308792пл.т. Следовательно общий объем просушиваемого зерна составит
Выбранные зерносушилки могут просушить за 30 суток 55600 пл.т что полностью перекрывает величину годового объема сушки. Тогда принимаем одну зерносушилку У13-СШ-50 производительностью 50тч и две зерносушилки ДСП-32 производительностью 32тч.
6 Внутреннее перемещение зерна
Объем внутреннего перемещения зерна расчитывается в соответствии с формулой:
где qпр – прием зерна со всех видов транспорта т;
qоч – объем очистки зерна т;
qсуш – объем сушки т;
qотп – отпуск зерна на все виды транспорта т [4].
7 Определение необходимого числа основных норий
Расчетное число норий для одновременного выполнения внутренних операций определяется в соответствии с формулой 43:
где –сумма необходимого числа часов работы норий на всех одновременно выполняемых операциях ч;
– расчетное время работы норий ч;
Необходимое число основных норий определяем из условия выполнения в сутки максимальной работы следующих операций таблица 1.
Определение необходимого количества основных норий
Наименование внутренних операций
Суточный объем внутренних операций
Подача зерна в бункера надсушильные
Подача с автотранспорта в бункера надсепараторные
Подача зерна в надсепараторные бункера на производственном элеваторе
Подача зерна в бункера для передачи на производство
Транспортирование зерна из подсушильных бункеров
Транспортирование зерна из подсепараторных бункеров
Необходимое число норий для одновременного выполнения внутренних операций находится по формуле:
где Kt – коэффициент использования основных норий по времени находится в соответствии с таблицей 1.34 [3].
8 Выбор типа и количества весов рабочего здания
Количество весов на элеваторах принимается равным числу основных норий рабочего здания. Так как количество норий равно шести следовательно число весов составляет 6Принимаем автоматические весы марки ДН-2000 производительность 100-200 тч.
Вместимость бункера над весами составляет 15 т.
Время необходимое на единичное переключение маршрута движения зерна при переключении маршрута движения зерна при переходе с партии на партию при диспетчерском автоматизированном управлении оборудованием задвижками и клапанами составляет 005 ч.
9 Выбор типа и количества распределительных кругов
Количество и тип распределительных кругов устанавливается в зависимости от числа и производительности основного транспортного оборудования норий элеватора.
Для трех основных норий производительностью 175 тч рекомендуются распределительные круги типа ТП-6. Принимаем 6 распределительных кругов.
Техническая характеристика поворотных труб ТП-6 представлена в Приложении Б8[6].
10 Выбор производительности и количества транспортеров
Производительность транспортеров принимаем равно 175тч. Количество транспортеров выбираем в зависимости от основных операций производимых на элеваторе:
Для приемки зерна с автомобильного транспорта принимаем 1 транспортер;
Для приемки зерна с железнодорожного транспорта принимаем 1 транспортер;
Количество надсилосных транспортеров составляет 2шт;
Количество подсилосных транспортеров составляет 2 шт.
Принимаем 6 транспортеров марки КСГ -100-500 производительность 175тч.
11 Обработка и хранение отходов
Величину расчетного суточного объема очистки зерна поступающего от хлебосдатчиков железнодорожным транспортом находится по формуле:
где Врпр – расчетный (максимальный) суточный объем приемки и отпуска зерна на железнодорожный транспорт т.
Величину расчетного суточного объема очистки зерна поступающего от хлебосдатчиков автомобильным транспортом находится по формуле:
где –количество зерна поступающего от хлебосдатчиков автотранспортом за весь период заготовок т;
Пр– продолжительность расчетного периода заготовок сут.
Количество отходов выделяемых в сутки на газорециркуляционных сушилках G2 тсут рассчитывают в соответствии с формулой:
где Апр – количество зерна поступающего от хлебосдатчиков;
ρ – доля сырого и влажного зерна подлежащего сушке ρ=75%;
С2 – количество выделенных на газорециркуляционных сушилках отходов %. Принимаем при отсутствии предварительной очистки зерна С2=С·03=15·03=045%;
Количество отходов выделяемых в сутки при очистке зерна на сепараторах определяется по формуле:
где Q – исходное содержание отделимой примеси %;
– расчетный суточный объем очистки зерна поступающего от хлебосдатчиков автомобильным транспортом т;
– расчетный суточный объем очистки зерна поступающего от хлебосдатчиков железнодорожным транспортом т;
С3 – содержание отделимой примеси в зерне поступающего железнодорожным и водным транспортом %. Принимаем С3=30%;
G1 – количество отходов выделяемых в сутки при предваритель-ной очистке зерна тсут;
G2 – количество отходов выделяемых в сутки на газорециркуля- ционных сушилках тсут.
Число сепараторов необходимое для обработки каждой фракции отходов Nсотхопределяется по формуле:
где G3 – количество отходов выделяемых в сутки при очистке зерна на сепараторах тсут;
– количество отходов в зависимости от фракций %;
Qcom – паспортная производительность сепараторов для обработки отходов тч
К’ – коэффициент снижения паспортной производительности сепараторов для обработки отходов К’=04.
Следовательно принимаем 1 сепаратор марки А1-БМС-6 производительностью 6 тч.
Количество зерносмеси G4 выделяемой при обработке отходов определяют в соответствии с формулой:
где G3 – количество отходов выделяемых в сутки при очистке зерна на сепараторах тсут.
Вместимость бункеров для отходов над и под зерноочистительными машинами должны приниматься не менее чем на двух часовую работу машины [4].
12 Расчет вместимости и высот бункеров
12.1 Расчет вместимости надсепараторного и подсепараторного бункеров
Принимаем время работы машин 60 мин. Тогда объем бункера рассчитываем на 1 час бесперебойной работы сепаратора. Так как производительность сепаратора составляет 100 тч следовательно вместимость бункера составляет 100 т.
Необходимый объем бункера находим по формуле (35):
где m – масса зерна кг;
ρ – плотность зерновоймассы кгм3;
K – коэффициент вместимости бункера.
Надсепараторный бункер представлен на рисунке 4.
Так как сечение бункера составляет 4х4 м следовательно АВ=4 м. ОD – высота пирамиды вычисляется по формуле (9):
Принимаем KX= OX тогда KX=04.
h1 h2 – высота конусной и прямоугольной части бункера; α=450 – угол естественного откоса
Рисунок 4. Бункер надсепараторный
Найдем объем усеченной пирамиды в соответствии с формулой (10):
Так как общий объем бункера составляет 157 м3 следовательно
где Vпар – объем параллелепипеда м3;
Vо – общий объем бункера м3;
Vпир – объем усеченной пирамиды м3.
Высота прямоугольной части бункера вычисляется по формуле (12):
Высота всего бункера складывается из суммы h1 и h2 и составляет 108 м. В связи с большой высотой бункера делим его на два маленьких бункера высотой 54 м и общей вместимостью 100 т.
Надсепараторные и подсепараторные бункера рекомендуется устанавливать одинаковой емкости следовательно вместимость подсепараторных бункеров составляет 100 т а высота каждого 54 м [6].
Аналогично рассчитываем надсепараторные и подсепараторные бункера для А1-ДЗС. Принимаем три бункера высотой 6 м каждый и общей вместимостью 175т.
12.2 Расчет вместимости надсепараторного бункера для отходов
Принимаем время работы машин 120 мин. Тогда объем бункера рассчитываем на 2 часа бесперебойной работы сепаратора для отходов. Так как производительность сепаратора составляет 6 тч следовательно вместимость бункера составляет 12 т [8] .
Надсепараторный бункер представлен на рисунке 5.
Так как сечение бункера составляет 3х3 м следовательно АВ=3м. ОD – высота пирамиды вычисляется по формуле (9):
Принимаем KX= OX тогда KX=03.
Рисунок 5. Бункер надсепараторрный для отходов
Так как общий объем бункера составляет 188 м3 следовательно
Высота всего бункера складывается из суммы h1 и h2 и составляет 28 м. Надсепараторные и подсепараторные бункера рекомендуется устанавливать одинаковой емкости следовательно вместимость подсепараторных бункеров составляет 12 т а высота каждого 28 м.[6]. Устанавливаем бункера одинаковой емкости для легких и тяжелых отходов.
Аналогично рассчитываем бункера для триеров. Принимаем два подсепараторных бункера высотой 28 м каждый и общей вместимостью 12 т.
13 Расчет вместимости бункера для отходов
Вместимость отдельностоящих бункеров для хранения пыли и отходов получаемых при предварительной очистке и сушке зерна на противоточнорециркуляционных зерносушилках предусматривают из расчета накапливания их в течение суток; для остальных отходов получаемых после зерноочистительных машин – в течение 3 суток. Принимаем бункера вместимостью из расчета оборудования в течение 3 суток. Так как производительность сепаратора составляет 6 тч а время работы принимаем 24 ч следовательно вместимость бункера составляет 144 т [8].
Бункер предназначенный для отходов представлен на рисунке 6.
Так как сечение бункера составляет 4х4 м следовательно АВ=4м. ОD – высота пирамиды вычисляется по формуле (9):
Рисунок 6. Бункер для отходов
Так как общий объем бункера составляет 2259 м3тогда в соответствии с формулой:
Высота всего бункера складывается из суммы h1 и h2 и составляет 151 м. В связи с большой высотой бункера делим его на 3 маленьких бункера высотой 503 м.
14 Расчет вместимости силосов
Расчет вместимости силосов производится с учетом того что силосы элеваторов сооружают различной формы и в самых различных сочетаниях (круглые квадратные многогранные и т.д.).
Вместимость силоса можно определить по приближенной формуле (36):
где – коэффициент использования объема принимаем в соответствии с таблицей 1;
– объемная масса зерна тм3;
– площадь поперечного сечения силоса м2;
– высота силоса от надсилосной плиты до выпускного отверстия м.
Принимаем силос квадратного сечения размером 6x6 и высотой 30м. Следовательно:
Количество силосов определяем по формуле (37):
где – емкость элеватора т;
Ес – вместимость силоса т.
Для производственного элеватора выбираем однокрылый элеватор с двумя силосными корпусами по 96 силосов в каждом.
где n – количество силосов в длину;
m – количество силосов в ширину.
Уточняем вместимость силосного корпуса по формуле (38):
где n – количество силосов в длинушт;
m – количество силосов в ширинушт;
Введение элеватор. Часть 1,2.doc
Элеватор – это полностью механизированное зернохранилище предназначенное для хранения зерна и выполнение в нем необходимых операций. Современный элеватор обеспечивает выполнение всех операций с максимальной эффективностью и надежным обеспечением сохранности зерна. В отличие от складов со стационарной механизацией элеватор обладает большей компактностью из-за повышенной высоты сооружения. Существуют различные типы элеваторов.
Хлебоприемные или заготовительные элеваторы. Эти элеваторы принимают зерно поступающее непосредственно от хлебосдатчиков главным образом в автомобильном транспорте подвергают его первичной обработке (очистке сушке) хранят некоторое время и отгружают по назначению железнодорожным водным или автомобильным транспортом. Разветвленная сеть этих хлебоприемных предприятий создана с учетом приближения их к производящим районам с тем чтобы избежать дальних перевозок зерна с полей колхозов и совхозов и в короткие сроки сдать его государству.
Так как значительную массу поступающего зерна нельзя сразу разместить на длительное хранение или передать для переработки зерноперерабатывающим предприятиям на этих элеваторах наряду с приемом проводят послеуборочную .обработку зерна: очистку от примесей сушку и обеззараживание. Кроме того эти элеваторы готовят к посеву семена зерновых масличных бобовых культур кукурузы и семена трав.
Базисные элеваторы служат для хранения оперативных запасов зерна для текущего потребления. На эти предприятия поступает главным образом зерно из хранилищ первого звена прошедшее первичную обработку. Несмотря на это очистка и сушка зерна на базисных элеваторах являются основными операциями. Кроме того на них подготавливают крупные однородные партии зерна удовлетворяющие определенным требованиям. Элеваторы оснащены высокопроизводительным оборудованием и как правило имеют большую емкость. Размещают элеваторы на пересечении водных и железнодорожных путей или на крупных железнодорожных станциях.
Производственные элеваторы (при мукомольных крупяных комбикормовых маслобойных крахмалопаточных и других заводах) принимают зерно преимущественно с железнодорожного и водного транспорта особенности производственных элеваторов: способность быстро разгружать транспортные средства; значительная вместимость; возможность формировать партии для переработки с необходимыми исходными данными по требованиям технологии; длительное хранение принятого зерна и возможность улучшения его качества очисткой вентилированием обеззараживанием от вредителей. Производственные элеваторы на мукомольных и крупяных заводах строят в крупных городах.
Перевалочные элеваторы используются для приема и перегрузки зерна с одного вида транспорта на другой. В некоторых случаях принимают зерно от колхозов и совхозов. Строят в местах примыкания железнодорожного транспорта к водным артериям или железнодорожных линий разной колеи.
Иногда перевалочные элеваторы используют для длительного хранения зерна. Так как подвоз зерна к месту перевалки и его отгрузка неравномерны необходимо чтобы эти элеваторы располагали не только мощными перегрузочными устройствами но и хранилищами позволяющими накапливать зерно в период его интенсивного поступления.
Фондовые элеваторы предназначены для длительного (в речение трех-четырех лет) хранения государственных зерновых резервов. К качеству зёрна поступающего на эти элеваторы предъявляются повышенные требования. Зерно с них отпускают лишь в порядке обновления запасов или для временного восполнения дефицита в отдельных районах. Как правило фондовые элеваторы имеют большие (100—200 тыс. т) емкости и должны иметь возможность принимать и отгружать зерно железнодорожными маршрутами.
Линейные элеваторы принимают зерно в основном с автомобильного транспорта. Прием зерна - с железной дороги предусматривается как случайная операция. Отпуск зерна в железнодорожные вагоны предусмотрен через люки в крыше или через дверной проём с помощью вагонозагрузчика.
1 Задачи элеваторной промышленности
Элеваторная промышленность выполняет важную роль в народном хозяйстве нашей республики соединяя сельскохозяйственное производство и предприятия перерабатывающей промышленности. Кроме того элеваторная промышленность обеспечивает передачу зерна и семян от колхозов и совхозов (производителей) потребителям (зерноперерабатывающим предприятиям предприятиям пищевой промышленности и др.). На предприятиях элеваторной промышленности зерно принимают и обрабатывают для улучшения качества и увеличения сроков хранения.
Элеваторная промышленность выполняет следующие основные задачи: 1)принимает от колхозов и совхозов зерно и семена масличных культур; 2)формирует из них крупные однородные партии;
)применяя очистку и сортирование зерна и семян их сушку и вентилирование улучшает качество зерна доводя его до требований предъявляемых потребителями;
)бесперебойно снабжает зерноперерабатывающую промышленность зерном а население продуктами его переработки необходимого качества в соответствии с действующими стандартами;
)принимает от семеноводческих хозяйств сортовое и семенное зерно и семена трав гибридные и сортовые семена кукурузы очищает и калибрует и хранит их снабжает ими колхозы и совхозы; 6)снабжает колхозы и совхозы комбикормами белково-витаминными добавками (БВД) премиксами [2].
2 Структура элеваторной промышленности
Структура элеваторной промышленности предусматривает передачу зерна от производителей к потребителям современное и качественное выполнение возложенных на неё задач. Согласно принятой в нашей республике структуре все предприятия элеваторной промышленности условно разделены на три звена.
Первое звено. Это хлебоприёмные предприятия и глубинные пункты которые принимают зерно от колхозов и совхозов проводят первичную обработку (очистку сушку вентилирование) хранят его определённое время и отгружают по назначению. К первому звену относят также зернохранилища специального назначения предназначенные для приёмки и хранения кукурузы бобовых культур семенного зерна требующих особых условий хранения и обработки и семяобрабатывающие заводы цеха станции. Хлебоприёмные предприятия первого звена принимают зерно в основном с автомобильного транспорта и отгружают предприятиям второго и третьего звеньев. Хлебоприёмные предприятия строят ближе к производству зерна и транспортным коммуникациям.
Второе звено. Это базисные перевалочные и фондовые элеваторы. Базисные элеваторы обрабатывают и хранят оперативные запасы зерна необходимые для текущего потребления. Базисные предприятия принимают зерно поступающее железнодорожным и водным транспортом хранят очищают сушат вентилируют и отгружают теми же видами транспорта по назначению. Перед отправкой на базисных элеваторах формируют зерно в крупные однородные партии предназначенные для зерноперерабатывающих предприятий или направляемые на экспорт. Базисные элеваторы отличаются значительной вместимостью и высокой производительностью транспортного технологического и другого оборудования.
Перевалочные элеваторы перегружают (переливают) зерно с одного вида транспорта на другой. Например с железнодорожного на водный и наоборот с широкой с железнодорожной коми на узкую. Особенности перевалочных элеваторов следующие: высокая производительность приёмных и отпускных устройств для максимально возможного сокращения простоя транспортных средств под погрузкой и разгрузкой; значительная вместимость зернохранилищ для приёма и отгрузки крупных партий. Для перевалочных элеваторов характерны высокий коэффициент грузооборота и непродолжительность хранения принятого зерна. Перевалочные элеваторы строят на перекрёстке железнодорожных и водных путей.
В фондовых элеваторах длительно хранят высококачественное зерно они отличаются небольшим коэффициентом грузооборота наличием надёжных средств обеспечения сохранности запасов (аппаратуры контроля за состоянием при хранении активного вентилирования обеззараживания и т.д.)
Третье звено. Это производственные и портовые элеваторы а также реализационные базы. Производственные элеваторы (при мукомольных крупяных комбикормовых маслобойных крахмалопаточных и других заводах) принимают зерно преимущественно с железнодорожного и водного транспорта особенности производственных элеваторов: способность быстро разгружать транспортные средства; значительная вместимость; возможность формировать партии для переработки с необходимыми исходными данными по требованиям технологии; длительное хранение принятого зерна и возможность улучшения его качества очисткой вентилированием обеззараживанием от вредителей. Производственные элеваторы на мукомольных и крупяных заводах строят в крупных городах.
Портовые элеваторы подготавливают партии зерна на экспорт отгружая его в морские суда а также принимают зерно по импортным закупкам. Портовые элеваторы размещают в портах республики. Их вместимость рассчитана на одновременную погрузку (разгрузку) крупных сухогрузных морских судов и танкеров при одновременной наибольшей производительности погрузочно-разгрузочного оборудования для максимально возможного сокращения простоя средств доставки (отправки) зерна. Портовые элеваторы с водным и железнодорожным транспортом для этого они должны иметь мощные средства для погрузки и разгрузки крупных партий зерна. При необходимости в портовых элеваторах зерно очищают иногда сушат непродолжительное время хранят. Этим элеваторам свойственно многократное заполнение (опорожнение) силосов у них высокий коэффициент грузооборота.
Приведённая структура элеваторной промышленности условна поскольку отличительная её особенность – совмещение функций различных видов элеваторов. Это выражается в том что элеваторы одних типов часто выполняют функции других. Например производственные элеваторы находящиеся в районах возделывания зерна частично выполняют функции хлебоприёмных элеваторов принимая свежеубранное зерно от колхозов и совхозов. Наоборот хлебоприёмные элеваторы выполняя свои основные задачи по приёмке обработке хранению и обеспечению зерном зерноперерабатывающих предприятий одновременно перерабатывают его в муку и крупу [3].
Производственный элеватор
Элеваторная промышленность как известно работает с зерном разных культур и разного качества принятым от различных хлебосдатчиков; зерновая масса представляет собой комплекс компонентов и большая часть из них – живые организмы.
- зерновая масса обладает специфическими и физиологическими свойствами которые при определенных обстоятельствах могут вызвать значительные изменения в состоянии зерновой массы т.е. сказаться на ее сохранности. Эти обстоятельства зависят от таких внешних факторов как температура влажность засоренность условия хранения зерна и др.;
- для бесперебойного снабжения в течение года населения и других потребителей зерном и зернопродуктами необходимо создать большие массы зерна обеспечивая их надежную сохранность;
- разным потребителям требуется зерно определенных кондиций в соответствии с его целевым использованием.
Итак можно выделить основные функции производственных предприятий элеваторной промышленности – послеуборочная обработка хранение отгрузка зерна.
Производственные элеваторы обеспечивают зерном перерабатывающие предприятия производственные (сооружают при мельницах крупяных комбикормовых крахмалопаточных заводах и. т. п.; 10—150 тыс. т). Эти хранилища должны располагать соответствующей емкостью для обеспечения бесперебойной работы перерабатывающих предприятий а также иметь соответствующее оборудование для подготовки зерновых партий к переработке по заданной рецептуре.
Производственный элеватор специализируется на обработке и оперативном хранении одной культуры с последующей переработкой. Поэтому такие элеваторы имеют устройства для приема зерновых культур с автомобильного и железнодорожного транспорта. Кроме того эти элеваторы имеют оборудование для хранения и сортировки зерновых культур сушки зерна и формирования производственной партии.
Принципиальная схема производственного элеватора представлена в Приложении А.
зерносушилка у-13-сш-50!!!.dwg

Рисунок 1. Общий вид зерносушилки типа У13-СШ-50
Рисунок 2. Конструкционная схема зерносушилки типа У13-СШ-50
Рисунок 3. Технологическая схема зерносушилки типа У13-СШ-50
Рисунок 4. Технологическая схема зерносушилки типа У13-СШ-50
Условные обозначения:
Рабочая схема.wg.dwg

Разгрузка отходов на автотранспорт
Зерносушилка стационарная марки У13-СШ-50
Автоматические весы ДН-2000
Распределительные круги ВШ-6
Сепаратор для отходов А1-БМС- 6
Зерносушилка стационарная А1-ДСП-32
Зерносушилка рециркуляционная А1-ДСП-32
Условные обозначения:
аспирационая сеть №3
аспирационая сеть №2
Надсилослый конвейер КГС-100-500
Подсилосный конвейер КГС-100-500
Конвейер КГС-100-500 для передачи зерна на производство
Бункер для приемки с жд ёмкостью 26т
Бункер для приемки с ат ёмкостью 30т
Надвесовой бункер ёмкостью 1
Накопительный бункер ёмкостью 66
Накопительный бункер ёмкостью 12т
Накопительный бункер ёмкостью 1
Рабочая схема движения зерна на элеваторе
аспирационая сеть №8
аспирационая сеть №4
Конвейер приемный с ат транспорта КГС-100-500
Конвейер приемки с жд транспорта КГС-100-500
Тиерный блок Р1-ББТ-700-16
Сито-воздушный сепаратор А1-БИС- 100
аспирационая сеть №1
аспирационая сеть №6
аспирационая сеть №7
аспирационая сеть №9
аспирационая сеть №10
Часть 5.docx
Зерно от хлебосдатчиков поступает на элеватор либо жд транспортом либо автомобильным. Приемка зерна осуществляется на протяжении 30 суток.
Приемка с жд транспорта осуществляется комплексом оборудования включающего в себя вагоноразгрузчики приемные бункера которые в свою очередь практически непрерывно опоражняются конвейер для приемки зерна с жд транспорта.
Приемка с автотранспорта осуществляется автомобилеразгрузчиками после автомобилеразгрузчиков зерно загружается в бункера и подается на конвейер.
После приемки с жд транспорта зерно направляют на норию №1 либо на норию №2 а с ат – на норию №4 или №5.
Затем зерно направляют на надсилосные конвейеры которыми оно подается в силоса для кратковременного хранения. Из силосов зерно поступает на подсилосные конвейеры а с них на нории откуда и осуществляется его подача на зерносушилки. Зерносушилки на проектируемом предприятии были выбраны А1-ДСП-32 – 2и У13-СШ-50 – 1приведенные зерносушилки могут просушить необходимое количество зерна поступающего от хлебосдатчиков с повышенной влажностью.
Просушенное зерно конвейером подается на нории откуда и идет его распределение по надсепараторным бункерам для дальнейшей очистки.
Из бункеров зерно направляется в сепаратор для первичной очистки А1-БДЗ в котором происходит отделение от грубых примесей.
После сепаратора А1-БДЗ зерно поступает на воздушно-ситовой сепаратор А1-БИС-100 где зерно очищается от примесей отличающихся линейными размерами и аэродинамическими свойствами.
После этого оно направляется на очистку в триерный блок в котором происходит очистка от примесей отличающихся по длине.
Контроль отходов осуществляется на сепараторе А1-БМС-6. Отходы выделенные в сепараторе направляются в бункера для отходов которые рассчитаны на 5 суток. После чего они отгружаются на ат транспорт.
После очистки зерно нориями и конвейерами подается на хранение в силоса. Отгрузка на производство также производится из силосов после чего направляется на конвейеры подсилосные и на нории в рабочей башне. С норий уже и подается на конвейер направляющийся на производство.
Заключение.docx
Список литературы.docx
Жуманазаров К.Б. Ермекбаев СБ. Омаров Т.Е. О проблеме качества зерна и его конкурентоспособности Пищевая технология 2012 №2. – 56с.
Вобликов Е.М. Технология элеваторной промышленности. Учебное пособие. – Ростов нД: издательский центр «МарТ» 2001. – 192 с.
Пунков С.П. Проектирование элеваторов и хлебоприемных предприятий с основами САПР С.П. Пунков Л.В.Ким В.Б.Фейденгольд. – Воронеж: Издательство Воронежского университета 1996. – 284 с.
Резчиков В.А. Налеев О.Н. Савченко С.В. Технология зерносушения. – Алматы: Издательство АТУ 2000. – 400с.
В.Ф. Самочетов Г.А. Джорогян. Зерносушение. – М.: Колос 1990. – 288с.
Жидко В.И. Резчиков В.И. Уколов В.С. Зерносушение и зерносушилки. М.: Колос 1983. – 239с.
В.А. Жидко. Сушка зерна - М: Колос 1986. – 256 с.1 Пунков С.П. Проектирование элеваторов и хлебоприемных предприятий с основами САПР С.П. Пунков Л.В.Ким В.Б.Фейденгольд. – Воронеж: Издательство Воронежского университета 1996. – 284 с.
Анисимова Л.Н. Проектирование элеваторов. Учебное пособие. – Барнаул: Изд-во АлтГТУ 2004. – 167с.
Правила организации и ведения технологического процесса на элеваторах и хлебоприёмных предприятиях. –М.: ВНИИЗ 1984 – 121с.
Дёмина И.А. Методические указания к выполнению дипломных (курсовых) работ (проектов) для студентов специальности 5В072800 (050728) – «Технология перерабатывающих производств» И.А. Дёмина С.Ф. Колосова. – Усть-Каменогорск: Изд-во ВКГТУ им. Серикбаева 2011. – 36с.