Проектирование привода цепного конвейера




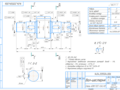
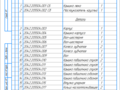
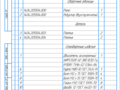
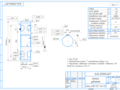
- Добавлен: 24.01.2023
- Размер: 1 MB
- Закачек: 0
Описание
Проектирование привода цепного конвейера
Состав проекта
![]() |
![]() |
![]() ![]() ![]() ![]() |
![]() ![]() ![]() |
![]() ![]() ![]() ![]() |
![]() ![]() ![]() ![]() |
![]() ![]() ![]() |
![]() ![]() ![]() ![]() |
![]() ![]() ![]() ![]() |
![]() ![]() |
Дополнительная информация
Чертеж - вал-шестерня.cdw

Чертеж - сборочный.cdw

Спецификация.spw

Чертеж - Колесо.cdw

Спецификация на приводную станцию.spw

Рекомендуемые чертежи
- 25.10.2022
Свободное скачивание на сегодня
Другие проекты
- 29.08.2014