Проектирование механизма шагового транспортёра. Вариант 6



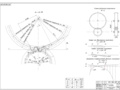
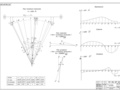
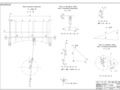
- Добавлен: 24.01.2023
- Размер: 687 KB
- Закачек: 0
Узнать, как скачать этот материал
Подписаться на ежедневные обновления каталога:
Описание
Проектирование механизма шагового транспортёра. Вариант 6
Состав проекта
![]() |
![]() |
![]() ![]() ![]() |
![]() ![]() ![]() ![]() |
![]() ![]() ![]() |
![]() ![]() ![]() |
![]() ![]() ![]() |
![]() ![]() ![]() ![]() |
![]() ![]() ![]() ![]() |
Дополнительная информация
Контент чертежей
Лист 1.Курсовой Ф.dwg

Лист 3.Курсовой Ф.dwg

Лист 4.Курсовой Ф.dwg

Рекомендуемые чертежи
- 19.10.2023
Свободное скачивание на сегодня
Обновление через: 12 часов 11 минут
- 22.08.2014
- 29.08.2014
Другие проекты
- 23.08.2014