Проектирование и исследование механизмов насосной установки с электроприводом




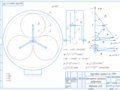
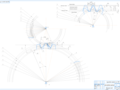
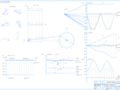
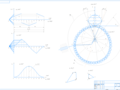
- Добавлен: 24.01.2023
- Размер: 5 MB
- Закачек: 2
Описание
Состав проекта
![]() |
![]() |
![]() ![]() ![]() ![]() |
![]() |
![]() ![]() ![]() |
![]() |
![]() ![]() ![]() ![]() |
![]() |
![]() ![]() ![]() ![]() |
![]() |
![]() ![]() ![]() |
![]() ![]() ![]() ![]() |
![]() ![]() ![]() |
![]() ![]() ![]() |
![]() |
![]() |
![]() ![]() ![]() ![]() |
![]() ![]() ![]() |
![]() |
![]() |
Дополнительная информация
лист3.cdw

Курсовой проект по ТММ
Динамическое исследование
РПЗ 5лист.docx
Наименование параметра
Числовые значения для вариантов
Угловая скорость кулачка
Угол рабочего профиля кулачка
Ход толкателя кулачкового механизма
Максимально допустимый угол давления в кулачковом механизме
Числа зубьев колес 45
Число оборотов коленчатого вала
2. Постановка задачи
построить кинематические диаграммы движения толкателя с учетом заданного характера изменения аналогов ускорения толкателя;
определить основные размеры кулачкового механизма наименьших габаритов с учетом максимально допустимого угла давления;
построить центровой и конструктивный профили кулачка и проверить выполнение передаточных функций.
3. Требования при проектировании кулачкового механизма
обеспечение заданного закона движения ведомого звена – толкателя;
обеспечение отсутствия заклинивания при выполнении условия
обеспечение наименьших размеров кулачкового механизма.
4. Построение кинематических диаграмм
Выбираем масштаб горизонтальной оси φ = 200*360320*2*п = 35.81 ммрад. Данный масштаб будет у горизонтальных осей для графиков зависимостей аналогов ускорений скоростей и перемещения. По условию задан график зависимости аналога ускорения от угла рабочего профиля кулачка при этом задано соотношение по которому можно определить max и min графика.
Для построения графика аналога ускорения используем симметричность трапеций.
Площадь графика ниже горизонтальной оси равна площади графика выше горизонтальной оси следовательно S1+ S2= S3+ S4. a1= 0.5*a2 и φпод= φсп= =φр 2 тогда примем a1=20мм и В=200мм.
Строим график зависимости аналога ускорения аq от угла рабочего профиля кулачка.
Для нахождения графиков аналога скорости и перемещения в зависимости от угла рабочего профиля кулачка используем методы графического интегрирования: разбиваем график на 12 частей и интегрированием получаем график аналога скорости VqВ и график аналога перемещений SB от угла рабочего профиля кулачка.
Снимаем максимальную ординату с графика аналога перемещений: yh max=74.17 мм.
Эта ордината в масштабе равна ходу толкателя кулачкового механизма следовательно можно получить масштабы вертикальных осей найденных выше графиков т.к. эти масштабы взаимосвязаны:
s= yh max hmax = 74.170.015=4945 ммм
Так как отрезки интегрирования К1=К2=31.8 то
5. Построение вспомогательной диаграммы (SB Vq). Определение размеров кулачка
Выбираем прямоугольную систему координат (SB Vq). По оси ординат откладываем аналог перемещения толкателя а по оси абсцисс – отрезки передаточной функции в масштабе S. Определяем область возможных решений для положения центра вращения кулачка.
Определяем область возможных решений для положения центра вращения кулачка проведя к крайним точкам диаграммы два луча под углами αдоп к векторам скоростей толкателя. Если центр кулачка взять в точке пересечения этих лучей то расстояние от этой точки до нулевого положения на диаграмме будет минимальным нулевым теоретическим радиусом при котором в любом положении механизма угол давления будет меньше допустимого.
Расстояние от полученного центра до начала координат равно r0 min
r0 min = yr S = 72534945 = 0.014 м.
6. Профилирование кулачка
Для построения теоретического профиля кулачка используется метод обращения движения суть которого заключается в следующем: мысленно придаем всему механизму вращение вокруг центра вращения кулачка с угловой скоростью (-1) равной но противоположно направленной угловой скорости кулачка. Тогда угловая скорость кулачка становится равной 1 + (-1) = 0 т. е. кулачок как бы становится неподвижным. Таким образом метод обращения движения позволяет при проектировании рассматривать движение при котором сам кулачок становится как бы неподвижным звеном.
Рабочий угол 320° соответствующий движению толкателя делим на части в соответствии с графиком перемещения т.е. на 12 равных частей – каждая часть по 26°40’. В каждом положении определяем положение толкателя. На полученных прямых от окружности минимального радиуса откладываем отрезки равные перемещению толкателя в соответствующих положениях выраженных в том же масштабе S.
Концы отрезков соединяем плавной линией которая является центровым или теоретическим профилем кулачка. Этот профиль представляет собой траекторию центра ролика в обращенном движении кулачкового механизма. Конструктивный профиль кулачка отстоит от центрального профиля на величину радиуса ролика.
Получают его как огибающую окружностей ролика толкателя изображенных в каждом положении.
Радиус ролика выбираем: rр= 0.015 м.
7. Проверка передаточных функций.
Передаточные функции кулачкового механизма получаем с планов скоростей и ускорений построенных в масштабе для заменяющего механизма.
При построении заменяющего механизма высшую пару на центровом профиле кулачка заменяем двумя низшими и дополнительным звеном. Полученный кривошипно-шатунный механизм является заменяющим для кулачкового механизма в выбранном положении. Передаточные функции для обоих механизмов совпадают.
Планы скоростей и ускорений строим в масштабе v и а соответственно.
Получим с планов скоростей и ускорений следующие значения
aqB = = = 0.00744 м.
Значения этих же параметров снятые с кинематических диаграмм:
VqBк.д. = 0.00706 м aqBк.д. = 0.00539 м.
Т.о. погрешность составляет:
v = (VqB - VqBк.д.) VqB = (0.00737-0.00706)0.00737= 47 %
а = (аqB - аqBк.д.) аqB = (0.00744-0.00539)0.00744= 275 %.
Построили кинематические диаграммы движения толкателя с учетом заданного характера изменения ускорения толкателя; определили основные размеры кулачкового механизма наименьших габаритов с учетом максимально допустимого угла давления:
Построили центровой и конструктивный профили кулачка и проверили выполнение передаточных функций. Погрешности в построении:
лист1.cdw

лист4.cdw

РПЗ 4лист(есть косяк приличный и соответственно в компасовском документе тоже. советую очень подробно пересмотреть).doc
Положение центра тяжести звена 2 и 2’
Момент инерции шатуна относительно оси проходящей через центр его тяжести
Угловая координата кривошипа для силового расчета
Угловая скорость в положении 11
Угловое ускорение в положении 11
2. Постановка задачи
Определение реакции в кинематических парах Qik и движущего момента.
3. Построение механизма в заданном положении.
Силовой расчет механизма проводим для одного положения заданного числовым значением угловой координаты начального звена =240o. Строим заданный кривошипно-ползунный механизм в положении φ1. Выбираем масштаб ml = 1000 ммм. Размеры кривошипа шатуна и ползунов берем из динамического исследования основного механизма (см.3). Таким образом рычажный механизм на листе формата А1 изображен в натуральную величину.
4. Построение плана скоростей и ускорений.
4.1. Построение плана скоростей
Линейную скорость точки А и А` звена 1 определяем по формулам для вращательного движения
VА = w1 × lAО = 21.98*0.05=1.099 мс
на плане скоростей вектор VА изображаем отрезком pa. Зададим величину этого отрезка
и определим масштаб плана скоростей
mv = paVA = 47.91641.099 = 43.6 мм(м×с-1).
Строим два плана скоростей т.к. данный механизм имеет два ползуна.
Для определения скорости точки B (для точки B` находим аналогично) составим векторное уравнение плоского движения
из графического решения этого уравнения определим величины скоростей для двух ползунов
VB1 = pb mv =46.545443.6 = 1.067 мс
VB2 = pb mv =36.448243.6 = 0.836 мс
VBA1 = ba mv =24.484443.6= 0.561 мс
VBA2 = ba mv =24.484443.6= 0561 мс
Скорость центра масс звена 2 определяем пропорциональным делением отрезков плана скоростей
baas2 = BAAS2 as2 = (AS2BA)×ba =0.25*24.4844=6.1211 мм
VS21 = ps2mv = 46.38143.6 = 10637 мс
VS22 = ps2mv = 44.064743.6 = 101 мс.
Угловую скорость звена 2 определяем по следующей формуле
w2 = VBA1 lBA = 0.5610.21=2.67 радс.
Угловую скорость звена 4 определяем по следующей формуле
w4 = VBA2 lBA = 0.5610.21=2.67 радс.
4.2. Построение плана ускорений
Ускорение точки A и А` звена 1 определяем по формулам вращательного движения
anA - нормальная составляющая ускорения
anA = w12× lAO = 21.982*0.05 = 24.156 мс2
atA - тангенциальная составляющая ускорения
atA = e1× lОА = 408*0.05= 0.204 мс2.
Ускорение точки В звена 2 (аналогично ускорение точки В` звена 4) определяется решением векторного уравнения
aB = aA + anBA + atBA
qb = qan + ana + abn + bnb
Аналогично плану скоростей план ускорений также строим для двух ползунов.
Задаемся величиной отрезка qa изображающего на плане ускорений ускорение точки А
и определяем масштаб плана ускорений
ma = qa aA = 48.313724.156 = 2 мм(м*с-2).
После определения масштаба находим оставшиеся необходимые неизвестные компоненты для решения векторного уравнения.
anBA - нормальное ускорение точки B в относительном вращении вокруг точки A (принимает одинаковые значения и для первого и для второго ползунов).
anBA = w22× lBA = 2.672*0.21=1.497 мс2
Тангенциальные составляющие ускорений определим из плана ускорений
atBA2 = bnbma =21.16794= 5.292 мс2
atBA4 = bnbma =21.16794= 5.292 мс2
aB3 = qb ma =14.80134 = 3.7 мс2
aB5 = qb ma =9.00144 = 2.25 мс2.
Ускорение центра масс звена 2 и звена 4 определим методом пропорционального деления отрезков плана ускорений
aS2 = qs2 ma = 20.1994 = 5.049 мс2
aS4 = qs4 ma = 19.32584 = 4.831 мс2 .
По величине тангенциальной составляющей находим угловое ускорение звена 2 и звена 4
e2 = atBA2 lBA = 5.2920.21= 25.2 радс2
e4 = atBA4 lBA = 5.2920.21= 25.2 радс2 .
5. Определение сил инерции Фi и моментов от сил инерции Мiф
При силовом расчете используем метод с помощью которого уравнениям динамики по форме придаем вид уравнений статики введя в уравнения силы инерции и моменты инерции. Выделяем статически определимую группу Ассура и обозначаем все реальные и расчетные силы действующие на нее. В этом случае геометрическая сумма задаваемых сил реакций связи и сил инерции равна нулю. Аналогично сумма моментов от заданных сил реакций связи сил инерции и моментов инерции равна нулю:
Для тела совершающего плоское движение различают главный вектор сил инерции звена приложенный в центре масс определяемый формулой:
и главный момент сил инерции определяемый формулой:
Определим значения сил и моментов действующих на механизм.
Звено 1: Ф1 = m1× aS1 = 0 т.к. aS1 = 0
MФ1= e1 × JS1= 0 т.к. JS1 = 0.
Звено 2: Ф2 = m2× aS2 =6.5*5.049 = 32.8185 Н
MФ2= e2 × JS2= 25.2 *0.19 = 4.788 Н*м.
Звено 3: Ф3 = m3× aS3 =16*3.7 =59.2
MФ3= e3 × JS3= 0 т.к. e3 = 0.
Звено 4: Ф4 = m4× aS4 =6.5*4.831 = 31.4015 Н
MФ4= e4 × JS4= 25.2 *0.19 = 4.788 Н*м.
Звено 5: Ф5 = m5× aS5 =16*2.25 =36 Н
MФ5= e5 × JS5= 0 т.к. e5 = 0.
6. Силовой расчет. Определение реакций в кинематических парах и недостающей нагрузки Qik
Силовой расчет механизма проводим методом расчленения его на структурные группы и отдельные звенья. При решении используем алгебраические уравнения моментов сил и векторные уравнения для сил приложенных к звеньям механизма.
Схема 1. Составляем векторное уравнение относительно точки S3
Из полученного уравнения находим :
Определив строим план сил в масштабе mF = 0.01 ммН действующих на группу звеньев 2-3:
Определяем силу и учитывая что определяем
Схема 2. Запишем векторное уравнение для звена 3 для нахождения неизвестной реакции
Строим план сил в масштабе mF = 0.5 ммН и определяем силу
Схема 3 и 4. Производим аналогичные действия как в схеме 1 и 2 только для второго ползуна 5 и шатуна 4. В результате составления векторных уравнений и построения планов сил получаем
Схема 5. Найдем реакцию . Составим векторное уравнение:
Строим план сил в масштабе mF = 0.01 ммН и определяем
Записываем уравнение суммы моментов относительно точки О действующих на первое звено :
Из уравнения находим Мдв1 :
7. Сравнение с динамическим расчетом
Мдв с третьего листа курсового проекта составляет 329.4 Нм таким образом погрешность составляет:
Δ= (Мдв1 - Мдв ) Мдв1 = (388.058-329.4)388.058 = 015
Определили реакции во всех кинематических парах Qik и движущий момент. Сравнили полученное значение с величиной найденной в третьем листе данного курсового проекта. Определили погрешность расчетов которая составила 15%.
лист2.cdw

Проектирование планетарного
КФ МГТУ гр. ПТМ.И-51
РПЗ 3лист.docx
Средняя скорость плунжера
Число оборотов коленчатого вала
Отношение длины шатуна к длине кривошипа
Положение центра тяжести звена 2 и 2’
Положение центра тяжести звена 3
Момент инерции шатуна относительно оси проходящей через центр его тяжести
неравномерности вращения вала 1
Момент инерции коленчатого вала (без маховика)
Маховой момент ротора электродвигателя
Момент инерции редуктора приведенный к кривошипу
Угловая координата кривошипа для силового расчета
Модуль колес 14 и 15
Число сателлитов в планетарном редукторе
Передаточное отношение планетарного редуктора
Ход плунжера 16” масляного насоса 16
Максимально допустимый угол давления в кулачковом механизме
Угол рабочего профиля кулачка
2. Постановка задачи
а) спроектировать кривошипно-ползунный механизм; б) определить закон движения коленчатого вала 1(φ1); в) обеспечить заданный коэффициент неравномерности вращения коленчатого вала .
3. Проектирование механизма и построение его в 12 положениях
3.1. Определение размеров механизма Определение длины кривошипа lAО
VВср = 2НТоборота где
Н=ОВ0-ОВ6= lAО + lAВ – ( lAВ - lAО ) =2 lAО
lAО = 60VВср(4n1ср) = 15*0.7210= 0.05 м.
Определение длины звена 2
lBА = 2 lAО = 4.20.05 = 0.21 м.
Определение положения центра масс звена 2
l АS2 = S2 lBА = 0.250.21 = 0.0525 м.
3.2. Построение механизма
Произвольно выбираем место расположения шарнира О проводим через точку О прямую на которой расположены шарниры А и А’. Кроме того проводим из т. О окружность радиусом OA. Разбиваем окружность через равные углы на 12 равных частей
После этого откладываем длину шатуна и строим ползуны. Разница между крайними положениями точки В соответствует ходу ползуна.
Вычерчиваем на листе кинематическую схему основного рычажного механизма в произвольном положении в масштабе
4. Построение индикаторной диаграммы Рi(Si) и диаграммы сил Fi(φ1)
Динамический анализ начинают с определения сил и моментов которыми нагружен механизм так как их характер определяет закон движения механизма. В данном случае задано давление в цилиндре: Рмах = 48*105 и Рмin = 05*105. Для первого циллиндра положениям 01..6 соответствуют холостому ходу (ХХ) или всасыванию а 67..12 – рабочий ход (РК) или нагнетание. Для второго циллиндра наоборот. Выбираем масштаб построения диаграммы сил:
P= yPmaxPmax=96(48*105)=2*10-5 ммПа
Сила и давление связаны следующим соотношением:
Fi= Рi*A где А=п*d4 = п*0.05224=0.00212 м2. Тогда
F = PA=2*10-5000212 =9.417 * 10^(-3) ммН
Масштаб горизонтальной оси φ= 1802п=28.647 ммрад.
5. Построение плана скоростей и определение передаточных функций
Передаточные функции определяются из плана скоростей. Для того чтобы построить план скоростей определяем скорость точки А
=*n130= 3.14*21030= 21.98 с^(-1).
Так как шатун совершает плоское движение можно записать уравнение скорости в следующем виде:
Строим планы скоростей 12 6 положений механизма и находим передаточные функции по следующим формулам:
VqS2х= VS2х 1= VS2х*
VqS2у= VS2у 1= VS2у*
U21 = 2 1= VBA * lAО (VA * lAB) = (bapa) (lAOlAB).
Рассчитываем передаточные функции для всех 12 положений. (В расчетно-пояснительной записке показан такой расчет только для нулевого положения).
U210 = (bapa) (lAOlAB)=-(11.979111.9791) (0.050.21)= -0.238 мм.
Повторяя такой расчет для каждого положения получаем значения передаточных функций для каждого положения. Результаты вычислений сводим в таблицу.
Таблица 1 – Значения передаточных функций
Результаты расчета проверены на ЭВМ. Распечатка прилагается.
6. Методика приведения и динамическая модель
Для того чтобы упростить определение закона движения сложной системы реальный механизм заменяют динамической моделью. Модель представляет собой стойку и вращающееся звено называемое звеном приведения инерционность которого определяется суммарным приведенным моментом инерции = JIпр+ JIIпр. На звено приведения действует суммарный приведенный момент сил Mпр = Mдвпр + Mcпр. Параметры динамической модели и определяют так чтобы законы движения звена приведения динамической модели и движения начального звена реального механизма совпадали:
φмод (t)= φмех(t); мод (t)= мех(t).
Указанные выше два выражения являются первыми двумя условиями перехода от реального механизма к модели (Рисунок 1). Третье условие: равенство элементарных работ модели и механизма dAмод= dAмех. Четвертое условие: равенство кинетических энергий реального механизма и модели Тмод=Тмех.
Рисунок 1 – Динамическая модель
В качестве начального звена механизма выбран кривошип 1. Таким образом
обобщенная координата для механизма φмод = φмех=φ1 и определяются методом приведения сил и масс.
7. Приведение сил и построение графика Мiпр(φ1) и графика работы А(φ1)
Особенность методики приведения и динамической модели состоит в том что весь механизм заменяем одним звеном – кривошипом к которому прикладываем все силы и моменты действующие на основной механизм. Порядок приведения в данном случае следующий:
Mпр = MFcпр + MG2пр + MG3пр + MMдпр;
MFc+G2+G3пр* 1 = Fc*VBх+G2у*VS2у+G3у* VS3у;
MFc+G2+G3пр = Fc*VBх 1+G2у*VS2у 1+G3у* VS3у 1=
= Fc*VqBх+G2*VqS2у+G3* VqS3у
Величины G2 и G3 малы по сравнению с силами сопротивления поэтому ими можно пренебречь. После такого допущения выражение принимает вид:
MFc+G2+G3пр = Fc*VqBх.
По полученной формуле рассчитываем приведенный момент движущих сил для 12 положений механизма. (В расчетно-пояснительной записке показан расчет только для нулевого(двенадцатого) положения).
М0(12)= Fc*VqBх= 0.5*105*0.00212*0=0.
Полученные результаты сводим в таблицу.
Таблица 2 – Значения приведенного момента сил сопротивления
График Мiпр(φ1) строим по точкам которые соответствуют значениям момента в конкретных положениях механизма. Данную зависимость изображаем в масштабе
м = ymпрмахМmaxпр = 103515 = 0.2 ммН*м.
Особенность построения данного графика заключается в следующем: строим кривую для первого ползуна исходного механизма затем – для второго ползуна и суммируем данные кривые. В результате получаем график Мiпр(φ1).горизонтальной оси:
φ= 1802п=28.647 ммрад
Для того чтобы получить график работы А(φ1) выполняем следующие действия:
)графически интегрируем график МFcпр(φ1) и получаем график работы Ас
)ординату yAcцикл переносим вверх и получаем ординату yAдцикл. Исследование ведется в установившемся режиме работы для которого характерно следующее тождество АСцикл = АДцикл. На первом звене момент имеет постоянное значение поэтому зависимость изображается прямой линией;
)графически суммируем графики Ас и . Ад Получаем график А(φ1).
)находим масштаб А по следующей формуле:
А= М *φ к=0.2 * 28.647150 = 0.038 ммДж;
)масштаб горизонтальной оси φ= 1802п=28.647 ммрад.
8. Приведение масс и построение графика JIIпр(φ1) переход к графику ТII(φ1)
График построения JIIпр(φ1) также строится по точкам. Для нахождения точек соответствующих положениям механизма получим соотношение:
Jпр = JIпр + JIIпр ;
JIIпр = J2пр + J3пр – величина переменная;
JIпр = J10 + Jредпр + Jзуб. механизмапр + + Jдоп;
JIIпр* 122=m3*VS322 + m2*VS222 + JS2*222;
JIIпр = m3*VS32 12 + m2*VS22 12 + JS2*22 12 = m3*VqS32 + m2*VqS22 + JS2*U212.
По последней формуле считаем приведенный момент второй группы звеньев для 12 положений механизма. (В расчетно-пояснительной записке показан расчет только для нулевого(двенадцатого) положения).
J0(12)=m3*VqS32+m2*VqS22+JS2*U212=16*0+6.5*0.03752+0.19*0.2382= = 0.0199 кг*м2
Таблица 3 – Значения приведенного момента инерции второй группы звеньев
Особенность построения графика приведенного момента инерции второй группы звеньев – получение кривой для первого ползуна и сдвиг этой прямой на 180° в результате получаем график для второго ползуна.
Полученная кривая является одновременно графиком и JIIпр(φ1) и ТII(φ1). Обосновать данного заключения: т.к. коэффициент неравномерности вращения коленчатого вала = (1max - 1min) 1cp – мал угловые скорости приблизительно равны 1 = 1ср то график JIIпр приведенного момента инерции второй группы звеньев пропорционален графику кинетической энергии второй группы звеньев ТII.
Однако масштабы этих зависимостей разные:
T = 2*I 1cp2 = 2*I(п*n130)= 2*1000(21.98)2 = 4.17 ммДж
Масштаб горизонтальной оси φ= 1802п=28.647 ммрад.
9. Построение приближенного графика TI(φ1). Расчет маховика
Теоретическое обоснование построения графика TI(φ1): перестраиваем график работы А(φ1)
переносим ось φ1 на величину тогда график А( является графиком Т()
Графически вычитаем график ТII(φ1) из графика Т(φ’1) и получаем график TI(φ’1)
= yTT * A (мм) – считаем для каждого положения исходного механизма отдельно. Полученные значения сводим в таблицу.
Таблица 4 – Значения ординат yTA
Максимальное приращение кинетической энергии ТIma
JIпр = ТImax (1cp2*) = (10.480.038) * 1(21.982* (130))= 17.125 кг*м2.
Исследуем данную систему на предмет необходимости маховика:
JIпр = J10 + Jредпр + Jдвпр + + Jдоп;
Jдоп = JIпр – (J10 + Jредпр + Jдвпр + ) где
Jдв = GD24=0.08*0.084=0.0016
Jдвпр* 122 = Jдв* д22;
U8-12 =дв 1. Зная U8-12 = 10.9 находим Jдвпр =Jдв*дв2 12=0.0016*10.92=0.19 кг*м2
Jдоп = 17.125 – 0.09-0.19-0.5=16.345 кг*м2>0 – нужен маховик.
Принимаем конструктивное исполнение маховика - кольцо. Тогда его основные размеры и масса определятся по следующим зависимостям:
Jmax = п*b*ρ*(D4 – d4) 32 где
D - наружный диаметр
d- внутренний диаметр d=0.8*D
ρ(сталь) = 7800 кгм3.
Выражаем все параметры через наружный диаметр:
(п*0.25*D*780032)*(D4 – 0.84*D4) = 0.9*16.345;
Cтроим маховик в следующем масштабе
l маховик = 250 ммм.
10. Определение закона движения коленчатого вала и проверка коэффициента неравномерности
Определим положение 1cp на графике:
Т.к. максимальное приращение кинетической энергии ТImax пропорционально максимальному приращению угловой скорости (ТImax~1max) то график ТI(φ’1) можно считать графиком 1(φ’’1) который определяет закон движения коленчатого вала. Для нахождения положения 1cp разделим 1max пополам и найдем ординату y 1cp. Считаем масштаб
= JIпр* 1cp*A = 17.125* 21.98*0.038=14.3 ммс-1 тогда
y 1cp = * 1cp = 14.3*21.98 = 314.4 мм.
Проверяем коэффициент неравномерности :
= 130 = 0.0333 – согласно исходным данным
= (1max - 1min) 1cp = y 1max y 1cp = 10.48314.4 = 0.0333.
Спроектировали кривошипно-ползунный механизм; определили закон движения коленчатого вала 1(φ1); обеспечили заданный коэффициент неравномерности вращения коленчатого вала с абсолютной точностью.
РПЗ 1,2лист(Табл.).docx
Число оборотов коленчатого вала
Отношение длины шатуна к длине кривошипа
Положение центра тяжести звена 2 и 2’
Положение центра тяжести звена 3
Момент инерции шатуна относительно оси проходящей через центр его тяжести
неравномерности вращения вала 1
Момент инерции коленчатого вала (без маховика)
Маховой момент ротора электродвигателя
Момент инерции редуктора приведенный к кривошипу
Угловая координата кривошипа для силового расчета
Модуль колес 14 и 15
Число сателлитов в планетарном редукторе
Передаточное отношение планетарного редуктора
Ход плунжера 16” масляного насоса 16
Максимально допустимый угол давления в кулачковом механизме
Угол рабочего профиля кулачка
лист5.cdw

РПЗ 1,2лист.docx
1 Краткое описание работы механизмов поршневого компрессора
ПРОЕКТИРОВАНИЕ ИССЛЕДОВАНИЕ МЕХАНИЗМОВ НАСОСНОЙ УСТАНОВКИ С ЭЛЕКТРОПРИВОДОМ
Установка для перекачки жидких нефтепродуктов представляет собой двухплунжерный насос простого действия с приводом от электродвигателя (рис. 1). Насос состоит из двух кривошипно-ползунных механизмов 123 (и 156) плунжеры 3 и 3’ которых совершают возвратно-поступательное движение в горизонтальных цилиндрах 4.
При движении плунжеров 3 и 3’ вправо происходит всасывание жидкости в цилиндры 4 и 4' при давлении нижа атмосферного Рmin а при движении плунжера влево - нагнетание жидкости при давлении Рmax (см. индикаторную диаграмму рис.1б). Рабочий цикл при этом совершается за один оборот кривошипа I который приводится во вращательное движение от электродвигателя 7 черев планетарный редуктор с колесами 891011 и водилом 12. Для обеспечения требующейся равномерности движения имеется маховик 13. Смазка подвижных соединений механизмов установки осуществляется под давлением от масляного насоса 16 кулачкового типа (рис. 1В). Закон движения толкателя 16’’ в пределах рабочего угла поворота кулачка φраб. представлен на рисунке 2в. Вращение кулачка 16’ осуществляется от кривошипа 1 через зубчатые колеса 14 и 15.
Средняя скорость плунжера
Число оборотов коленчатого вала
Отношение длины шатуна к длине кривошипа
Положение центра тяжести звена 2 и 2’
Положение центра тяжести звена 3
Момент инерции шатуна относительно оси проходящей через центр его тяжести
неравномерности вращения вала 1
Момент инерции коленчатого вала (без маховика)
Маховой момент ротора электродвигателя
Момент инерции редуктора приведенный к кривошипу
Угловая координата кривошипа для силового расчета
Модуль колес 14 и 15
Число сателлитов в планетарном редукторе
Передаточное отношение планетарного редуктора
Ход плунжера 16” масляного насоса 16
Максимально допустимый угол давления в кулачковом механизме
Угол рабочего профиля кулачка
Лист 1: Проектирование цилиндрической эвольвентной зубчатой передачи
1. Исходные данные для проектирования
Модуль зацепления m = 40 мм;
Угол наклона линии зуба = 0º;
Число зубьев шестерни z1 = 13;
Число зубьев колеса z2 = 30;
Параметры исходного контура по ГОСТ 13755 - 81:
коэффициент высоты зуба ha* = 1
коэффициент радиального зазора c* = 0.25 .
2. Постановка задачи:
необходимо произвести расчет эвольвентной зубчатой передачи;
выбрать коэффициент смещения
построить проектируемую зубчатую передачу и станочное зацепление для колеса
проверить графически коэффициент перекрытия.
3. Обоснование выбора коэффициентов смещения x1 x2
Задаем коэффициенты смещения на отсутствие подреза:
Обеспечиваем отсутствие заострения
Обеспечиваем непрерывность зацепления: определяем коэффициент перекрытия для прямозубой передачи
= (z1* (tga2 - tgw ) - z2* ( tga2 - tgw ))2*.
Проверяем достаточность полученного коэффициента перекрытия:
4. Геометрический расчет эвольвентной зубчатой передачи
Определяем минимальное число зубьев z min
Определяем x min12 по формуле
x min12 = ha* * ( z min - z12 ) z min
Задаем коэффициенты смещения на отсутствие подреза для проектируемой передачи
Находим угол зацепления по inv w = inv + 2* (
inv w=0.0149+2*(0.6+0)*0.364(13+30)=0.025
Определяем коэффициент воспринимаемого смещения
y = (z1+z2) * (cos cos w - 1 )2;
y=(432)*((0.9390.916)-1)=0.5398 мм;
y*m=0.5398*4.0=2.1592;
Подсчитаем коэффициент уравнительного смещения
y=(0.6+0)-0.5398=0.0602 мм;
Вычисляем радиусы делительных окружностей
Определяем радиусы основных окружностей
rb1 =26*0.939=24.414 мм;
rb2 =60*0.939=56.34 мм;
Определим радиусы начальных окружностей
r w12 = m*z12* cos (2* cos w ) ;
r w1 =24.4140.915=26.652 мм;
r w2 =56.340.915=61.506 мм;
Найдем межосевое расстояние
a w = r 1 + r 2 + y*m=m*((z1+
a w = 4.0*(432+0.5398)=88.159 мм;
a w =26.652+61.506=88.158 мм;
Определяем радиусы окружностей вершин
ra12 = m (z 122 + ha* +
ra1=(132+1+0.6-0.0602)*4.0=32.16 мм;
ra2=(302+1+0-0.0602)*4.0=63.76 мм;
Определяем радиусы окружностей впадин
rf12 = m (z 122 - h a* - c * +
rf1=(132-1+0.6-0.25)*4.0=23.4 мм;
rf2=(302-1+0-0.25)*4.0=55 мм;
h = h1 = h2 = m( 2h a* + c * - y);
h= (2*1+0.25-0.0602)*4.0=8.76 мм;
a w = r a1 + r f 2 + c*m;
a w =32.16+55+0.25*4.0=88.16 мм;
a w=63.76+23.4+0.25*4.0=88.16 мм;
Определяем толщину зубьев по дуге делительной окружности
s 1=4.0*(2 +2*0.6*0.939)=8.0272 мм;
s 2=4.0*(2 +0)=6.28 мм;
Определяем толщину зубьев по окружности вершин
s12 = m *cos *(2 +2* x 12*tg - z12* (inv - inva12) )cosa12 )
где a12 = arccos (d b12d a12);
s1= 4.0*(0.9390.7591)*[2 +2*0.6*0.364-13*(0.14936-0.0149)]=1.28 мм;
s2= 4.5*(0.9390.8836)*[2 +2*0*0.364-30*(0.0427-0.0149)]=3.641 мм;
Проверяем отсутствие заострения
sa12 ≥ 0.2m 0.2m=0.8
Определяем коэффициент перекрытия для прямозубой передачи
= (z1* (tga2 - tgw ) - z2* ( tga2 - tgw ))2*;
=[13*(0.859-0.4383)+30*(0.5317-0.4383)] 2*=1.316
Проверочный расчет выполняем на ЭВМ.
5.Построение зубчатой передачи.
По результатам расчета для выбранных коэффициентов смещения строим схему зацепления колес z1 и z2 в масштабе l = 4000 ммм следующим образом:
Откладывается межосевое расстояние aw и проводятся окружности: начальные rw1 делительные r1 и основные rв1 rв2; окружности вершин rа1 rа2; и впадин rf1 . Начальные окружности должны касаться в полюсе зацепления. Расстояние между делительными окружностями по осевой линии равно величине воспринимаемого смещения yт. Расстояние между окружностями вершин одного колеса и впадин другого измеренное также по осевой линии должно быть равно величине радиального зазора c*m
Через полюс зацепления касательно к основным окружностям колес проводится линия зацепления колес. Точки касания N1 и N2 называются предельными точками линии зацепления. Линия зацепления образует с перпендикуляром восстановленном к осевой линии в полюсе угол зацепления aw.
Буквами В1 и В2 отмечается активная линия зацепления. Точка В1 является точкой пересечения окружности вершин второго колеса с линией зацепления и называется точкой начала зацепления а точка В2 является точкой пересечения окружности вершин первого колеса с линией зацепления и называется точкой конца зацепления.
На каждом колесе строятся профили трех зубьев причем точка контакта К
должна располагаться на активной линии зацепления.
6.Построение эвольвенты.
Эвольвенту для колеса 1 и колеса 2 строим в следующем порядке:
На основной окружности циркулем откладываем 7 10 равных отрезков (5 20 мм).
Проводим в каждой точке касательные к основной окружности.
На каждой касательной откладываем тем же раствором циркуля
(5 20 мм) соответствующее количество отрезков.
Получившиеся точки соединяем плавной кривой называемой эвольвентой.
По окружности вершин и делительной окружности откладываем толщины
зуба Sa и S соответственно
Делим их пополам и через точки деления проводим ось зуба которая должна пройти через центр колеса.
Рассчитываем величину углового шага =360z12 учитывая строим линии симметрии зубьев.
Вычерчиваем зубья учитывая радиусы переходных профилей. Отмечаем точки B1 В2 и строим эвольвентные части рабочих частей профилей.
7.Графическое определение коэффициента перекрытия.
где В1В2 - линия зацепления мм (61.75 мм с чертежа)
Р - шаг мм (49.78 мм с чертежа).
8.Построение станочного зацепления.
Профиль зуба колеса z1 получаем методом обращенного движения производящей рейки относительно неподвижного колеса z1. Схема станочного зацепления строится следующим образом:
Проводятся делительная и основная окружности окружность вершин и впадин.
От делительной окружности (с учетом знака) откладывается расчетное смещение х1m и проводится делительная прямая исходного производящего контура реечного инструмента. На расстоянии h*a*m вверх и вниз от делительной прямой проводятся прямые граничных точек а на расстоянии h*a*m +c*m) - прямая вершин и впадин; станочно-начальная прямая проводится касательной к делительной окружности в точке P0 (полюс станочного зацепления).
Проводится линия станочного зацепления N-P0 через полюс станочного зацепления P0 касательно к основной окружности в точке N. Эта линия образует с прямыми исходного производящего контура инструмента углы равные a.
Строится исходный производящий контур реечного инструмента так чтобы ось симметрии впадины совпадала с вертикалью.
Производится построение профиля зуба проектируемого колеса касающегося профиля исходного производящего контура в точке К.
Произвели расчет эвольвентной зубчатой передачи предварительно выбрали коэффициенты смещения построили проектируемую зубчатую передачу и станочное зацепление для колеса проверили графически коэффициент перекрытия погрешность составила 612%.
Лист 2: Проектирование планетарного редуктора
2. Постановка задачи
)подобрать числа зубьев планетарного редуктора;
)построить планетарный редуктор в масштабе;
)провести кинематическое исследование графическим способом.
3.Основные условия проектирования многосателлитных планетарных механизмов.
)Передаточное отношение планетарного механизма
)Обеспечение соосности (геометрического совпадения осей)
)Обеспечение свободного размещения сателлитов на окружности r = aw (условие соседства)
sin (k) > max(z 23+2)( z 1+z 2).
)Обеспечение собираемости механизма (условие сборки)
(U 1в* z 1 k) ( k p + 1 ) = N
где В - произвольное целое число
)Обеспечение отсутствия подрезания колес с внешними зубьями
)Обеспечение отсутствия заклинивания во внутреннем зацеплении
z4-3 > 8 - разность в числах зубьев колес.
)Обеспечения минимальных габаритов механизма.
4. Подбор чисел зубьев планетарного редуктора
Представим передаточное отношение обращенного механизма в виде произвольной комбинации сомножителей
(B D)(A C) = (z2 z4)( z1 z3) = U1в -1 = 10.9-1=9.9=
выбираем (z2 * z4)( z1 * z3) =(9*11)(2*5)
z1= (D - C) A q = (11 - 5) 2 q = 24 q
z2= (D - C) B q = (11-5) 9 q = 54 q
z3= (A + B) C q = (2+9) 5 q = 55 q
z4= (A + B) D q = (2+9) 11 q =121 q
где q - произвольное число обеспечивающее выполнение условий проектирования
принимаем q = 2 тогда
z1= 48 z2= 108 z3=110 z4= 242 .
Проверяем условие сборки
10.9( 3p + 1) 3 = N - целое при p=3 ( N = 872 ) то есть условие выполняется и условие соседства
sin 3 > (108+2)(24+108)
условие тоже выполняется.
5. Построение планетарного редуктора и кинематическое исследование графическим способом.
5.1. По рассчитанным числам зубьев колес находим значения радиусов:
5.2. В масштабе центры колес и точки зацеплений которые выносятся на вертикальную ось радиусов. Производим расчеты
nдв=U1-в*n1=10.9*210=2289 обмин;
=*nдв30= 3.14*228930= 239.582 1c.
Вычисляем vA= 1*r1=239.582*12*10-3=2.87 мс. Откладываем отрезок АА’ в масштабе v===21.746 . Скорость Vс=0. Строим линию распределения скоростей блока сателлитов A’C (лрс 2-3). Отрезок ОА’ – лрс 1-го звена. Отрезок ВВ’ – скорость точки В в масштабе v. Получаем отрезок ОВ’ – линия распределения скоростей водила (лрсв).
5.3. Проверка передаточного отношения (графически из плана угловых скоростей). Для построения плана угловых скоростей проводим горизонтальную линию угловых скоростей. Выбираем полюс Р на произвольном расстоянии от нее проводим из него лучи параллельные линиям распределения скоростей до пересечения с осью. Отрезки кв к1 и к2 выражают в масштабе w = к1 1=65.61239.582=0.2738 ммс-1 угловые скорости соответствующих звеньев.
U1в= 1 в = к1кв = 65.616.02=10.898;
Подобрали числа зубьев планетарного редуктора 24 108 110 и 242; построили планетарный редуктор в масштабе провели кинематическое исследование графическим способом проверили передаточное отношение графическим способом: погрешность составила 0.018%.
Рекомендуемые чертежи
- 10.08.2016