Проектирование и испытание станков




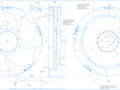
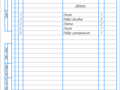
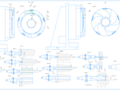
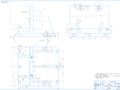
- Добавлен: 25.01.2023
- Размер: 1 MB
- Закачек: 0
Описание
Состав проекта
![]() |
![]() ![]() ![]() ![]() |
![]() ![]() ![]() ![]() |
![]() |
![]() ![]() ![]() |
![]() ![]() ![]() ![]() |
![]() ![]() ![]() ![]() |
![]() |
![]() |
Дополнительная информация
Приспособа.cdw

Деталь.cdw

Наладки1.cdw

Спецификация.spw

Рекомендуемые чертежи
- 24.01.2023