Проект участка термической обработки лезвийных режущих инструментов в условиях ХК Лугансктепловоз: Сверло, метчик, фреза




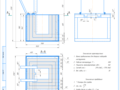
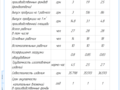
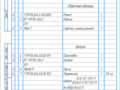
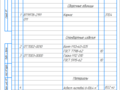
- Добавлен: 24.01.2023
- Размер: 7 MB
- Закачек: 3
Описание
Состав проекта
![]() |
![]() ![]() ![]() |
![]() ![]() ![]() |
![]() ![]() ![]() |
![]() ![]() ![]() |
![]() |
![]() ![]() ![]() ![]() |
![]() ![]() ![]() ![]() |
![]() ![]() ![]() ![]() |
![]() ![]() ![]() ![]() |
![]() ![]() ![]() ![]() |
![]() ![]() ![]() ![]() |
![]() ![]() ![]() ![]() |
![]() ![]() ![]() ![]() |
![]() ![]() ![]() ![]() |
![]() ![]() ![]() ![]() |
![]() ![]() ![]() ![]() |
![]() ![]() ![]() ![]() |
![]() ![]() ![]() ![]() |
![]() ![]() ![]() ![]() |
![]() ![]() |
![]() ![]() ![]() ![]() |
![]() ![]() ![]() |
![]() ![]() ![]() |
![]() ![]() ![]() |
![]() ![]() ![]() |
Дополнительная информация
9986-924.spw

ВТ 9978-2192 (Ванна электродная и каркас).cdw

9978-3641 (Ванна электродная соляная).cdw

Графики.cdw

Колодец нагревательный.cdw

Метчик Р М.cdw

Фреза червячная.cdw

9986-924 (Бак закалочный масляный).cdw

ЛТ9968-522 (Пескоструйная камера на влажном песке).cdw

ВТ 9978-2192.spw

7.9978.2643.0.00.000.spw

ЛТ9968-522 (Пескоструйная камера на влажном песке) А1.cdw

Экономика.cdw

Планировка участка цеха1.cdw

Сверло Р М .cdw
