Привод цепного конвейера с двухступенчатым косозубым редуктором




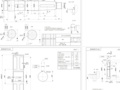
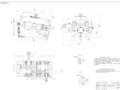
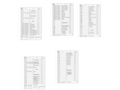
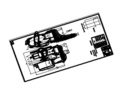
- Добавлен: 24.01.2023
- Размер: 3 MB
- Закачек: 0
Описание
Состав проекта
![]() |
![]() |
![]() ![]() ![]() |
![]() ![]() ![]() |
![]() ![]() ![]() ![]() |
![]() ![]() ![]() ![]() |
![]() ![]() ![]() |
![]() ![]() ![]() ![]() |
![]() ![]() ![]() ![]() |
Дополнительная информация
реф.doc
ПРИВОД ЭЛЕКТРОДВИГАТЕЛЬ РЕДУКТОР РАСЧЕТ КИНЕМАТИЧЕСКИЙ ПЕРЕДАТОЧНОЕ ОТНОШЕНИЕ ПЕРЕДАЧА ЗУБЧАТАЯ РАСЧЕТ ПРОЕКТИРОВОЧНЫЙ РАСЧЕТ ПРОВЕРОЧНЫЙ ВАЛ КОЛЕСО ШЕСТЕРНЯ КОРПУС РЕДУКТОРА ПОДШИПНИК ШПОНКА МУФТА.
Целью проекта является разработка привода цепного конвейера.
В ходе работы над проектом был выбран электродвигатель проведены кинематический и силовой расчет привода расчет механических передач валов редуктора определены конструктивные размеры зубчатых колес и корпуса выбраны и проверены на долговечность подшипники определен коэффициент запаса прочности валов проверена прочность шпоночных соединений выбрана смазка передач редуктора и подшипников проработаны вопросы сборки и регулировки редуктора.
При компоновке редуктора были решены вопросы рационального размещения передач с учетом влияния на их размеры твердости активной поверхности зубьев и коэффициента ширины зубчатого венца колеса зубчатой передачи.
В результате работы разработаны сборочный чертеж редуктора и рабочие чертежи деталей редуктора.
пз.doc
Кинематический и силовой расчет привода9
Расчет передач привода11
Ориентировочный расчет валов33
Конструктивные размеры зубчатых колес37
Конструктивные размеры корпуса редуктора39
Проверка долговечности подшипников40
Проверка прочности шпоночных соединений45
Уточненный расчет валов47
Выбор посадок деталей редуктора54
Выбор соединительных муфт 54
Сборка и регулировка55
Список использованных источников57
Целью курсового проектирования является приобретение навыков принятия самостоятельных конструктивных решений усвоение последовательности разработки механизмов общего назначения закрепление учебного материала по расчету типовых деталей машин.
Задачей проекта является разработка привода цепного конвейера.
Привод состоит из электродвигателя и двухступенчатого цилиндрического редуктора. Вращательное движение от электродвигателя редуктору передается упругой муфтой.
Электродвигатель выбирается по требуемой мощности и ориентировочной частоте вращения. Цилиндрические зубчатые передачи проектируются по критерию контактной прочности активной поверхности зубьев проверяются по контактным изгибным напряжениям а также при действии пиковых нагрузок. Ориентировочный расчет валов проводится на чистое кручение по пониженным допускаемым напряжениям. Подшипники выбираем по характеру нагрузки на валы и по диаметрам валов проверяем на долговечность по динамической грузоподъемности. Шпоночные соединения проверяем на смятие. Валы проверяются на сопротивление усталости по коэффициентам запаса прочности при совместном действии изгиба и кручения с учетом масштабных факторов и концентраторов напряжений.
Способ смазки и уровень масла обусловлены компоновкой механизма. Масло выбирается исходя из действующих контактных напряжений и окружной скорости в зацеплениях.
В результате работы должна быть получена компактная и эстетичная конструкция редуктора отвечающая современным требованиям предъявляемым к механизмам данного назначения.
ВЫБОР ЭЛЕКТРОДВИГАТЕЛЯ
1.Кинематическая схема привода и индексация кинематических звеньев
– шестерня цилиндрической косозубой передачи;
– колесо цилиндрической косозубой передачи;
– колесо цилиндрической косозубой передачи.
Рисунок 1.1 - Кинематическая схема привода
Присваиваем индексы валам в соответствии с размещенными на них звеньями передач:
– быстроходный (входной) вал редуктора;
- 3 – промежуточный вал редуктора;
- тихоходный (выходной) вал редуктора.
В дальнейшем параметры вращательного движения геометрические параметры передач и другие величины будем обозначать в соответствии с индексами валов к которым они относятся.
Определение требуемой мощности электродвигателя
В качестве приводного используется трехфазный асинхронный электродвигатель переменного тока.
Потребная мощность электродвигателя вычисляется по формуле 1
где Рвых – мощность на тихоходном валу привода кВт;
hОБЩ = hМm×h12×h34× hПn – общий КПД привода
где h12 h34 hМ·hП – КПД отдельных передач соединительной муфты и подшипников. КПД подшипников hП берется в степени n равной числу пар подшипников в приводе n=4. КПД муфт hМ берется в степени m равной числу муфт в приводе m=2.
Принимаем согласно 1: hМ=098; hП=099; h12=097; h34=097; тогда
hОБЩ = 0982×097×097×0994 = 0868.
где Ft – окружное усилие кН;
V – значение окружной скорости мс;
Рвых =325 × 045=1462 кВт.
Р’ЭД = 1462 0868 = 1685 кВт
2.Определение частоты вращения приводного вала.
Частота вращения тихоходного вала привода может быть определена следующим образом
nвых = n4 = 60×1000×V (z×t)
гдеz t – число зубьев и шаг тяговой звездочки.
n вых= 60×1000×045 (12×65) = 34615 обмин.
3.Определение ориентировочной частоты вращения вала электродвигателя.
Требуемая частота вращения вала электродвигателя ориентировочно равна
гдеnвых – частота вращения тихоходного вала привода мин-1;
Принимаем согласно [1] i’12 = 5 i’34=5 тогда
i’ОБЩ = 5×5 = 25 тогда
n’ЭД = 34615×25= 865 обмин
По каталогу 3 выбираем электродвигатель с ближайшим к n’ЭД и Р’ЭД значениями. Таковым электродвигателем является АИР100L6 (см. рис.1.2).
Его параметры: РЭД = 22 кВт nЭД = 945 обмин.
Рисунок 1.2 - Эскиз электродвигателя
Таблица 1.1- Основные размеры электродвигателя мм
КИНЕМАТИЧЕСКИЙ И СИЛОВОЙ РАСЧЕТ ПРИВОДА
1. Определение расчетных передаточных чисел
Общее передаточное отношение привода
iобщ = 945 34615 = 273.
Передаточное отношение тихоходной передачи редуктора вычисляется по формуле [3 табл.1.3 стр.9]:
2 Определение частоты вращения валов
Быстроходный вал:n1 = nэд = 945 обмин;
Промежуточный вал:n23 = n1
Тихоходный вал:n4 = n23
3.Угловые скорости валов
Угловые скорости определяем по формуле 1
w1 = wэд = ×nЭД 30 = 3142×945 30 = 9896 радc;
w23= ×n23 30 = 3142×1594 30 = 1669радс;
w4= ×n4 30 = 3142×3464 30 = 363 радс;
4 Определение мощностей на валах
Мощность на входном валу редуктора
Р1 = Р’ЭД·hМ·hП =1685 ·098·099 = 1635 Вт;
Мощность на промежуточном валу редуктора
Р23= Р1·h12·hП = 1635·097·099 = 1570 Вт;
Мощность на выходном валу редуктора
Р4 = Р23·h34·hП = 1570·097·099 = 1508 Вт.
5. Определение крутящих моментов на валах.
Крутящий момент на входном валу редуктора
Т1= Р1 w1 = 1635 9896 = 1652 Нм.
На промежуточном валу редуктора
Т23 = Р23 w23 = 15701669 = 9407 Нм.
На выходном валу редуктора
Т4= Р4 w4 = 1508363 = 4154 Нм.
Таблица 2.1 - Результаты расчета
Передаточное отношение
РАСЧЕТ ПЕРЕДАЧ ПРИВОДА.
1 Цилиндрическая косозубая передача 1-2
Критерии работоспособности и расчета. Передача 1-2 является закрытой поэтому основной критерий работоспособности и расчета – контактная выносливость рабочих поверхностей зубьев. Цель расчета: определить геометрические размеры зубчатой передачи.
Вращающий момент на шестерне 1 Т1 (Н×м) .1652
Вращающий момент на колесе 2 Т23 (Н×м) 9407
Частота вращения вала 1n1(обмин) . ..945
Частота вращения вала 2-3n23(обмин) .. 1594 Передаточное число i12 .. ..593
Cрок службы передачи Lгод(годы) . .5
1.1 Выбор материалов термообработки и твёрдости
Для равномерного изнашивания зубьев и лучшей их прирабатываемости твердость шестерни НВ1назначается больше твердости колеса НВ2 Разность средних твердостей рабочих поверхностей зубьев шестерни и колеса при твердости материала Н≤350НВ в передачах с прямыми и непрямыми зубьями составляет НВ1-НВ2=20 50.
Твёрдость поверхности НВ
Твёрдость серцевины НВ
Твёрдость средняя НВ
1.2.1 Определение допускаемых контактных напряжений.
Допускаемые контактные напряжения в соответствии с ГОСТ 21354-75:
где -коэффициент безопасности (однородная структура);
- предел контактной выносливости поверхности зубьев соответствующий базовому числу циклов перемены напряжений Нмм2; - коэффициент долговечности
где - базовое число циклов перемены напряжений - эквивалентное число циклов перемены напряжений соответствующее делительному пределу выносливости.
Предел контактной выносливости поверхности зубьев согласно таблице 4.1 [1] (Н≤350НВ).
где - частота вращения рассчитываемого колеса обмин; - число вхождений в зацепление зуба рассчитываемого колеса за один его оборот; с=1 - максимальный из длительно действующих моментов; - момент действующий в - время действия ti определяется в долях от суммарного времени работы передачи согласно графику нагрузки.
- срок службы передачи годы; - коэффициент годового использования - коэффициент суточного использования.
При для переменной нагрузки принимаем =1
Для косозубых передач в качестве расчетного принимается [3]
Нмм2-неравенство выполняется.
1.2.2. Определение допускаемых значений напряжений при расчете зубьев на усталостный изгиб [1].
где SF - коэффициент безопасности; - предел выносливости при изгибе соответствующий базовому числу циклов изменения напряжений Нмм2 -коэффициент долговечности
По табл.4.2[1] согласно выбранных сталей - 40Х 45 (углеродистая и легированная) принимаем SF=175.
По Табл.4.2. [1] принимаем
Коэффициент долговечности: .
Для зубчатых колёс с твёрдостью и зубчатых колёс со шлифованной переходной поверхностью независимо от твёрдости mF=6.
- базовое число циклов перемены напряжений;
- эквивалентное число циклов перемены напряжений;
1.2.3. Определение допускаемых предельных напряжений при расчете на контактную и изгибную прочность по максимальным нагрузкам.
Для зубьев зубчатых колес подвергнутых нормализации улучшению или объемной закалки с низким отпуском.
Допускаемое предельное напряжение при расчете на контактную прочность:
где - предел текучести материала при растяжении Нмм2.
Допускаемое напряжение при расчете на изгибную прочность:
где - предельное значение напряжения не вызывающее остаточных деформаций или хрупкого излома зуба Нмм2; - коэффициент безопасности.
; (стали легированные и углеродистые при нормализации улучшении)
1.3. Определение коэффициентов нагрузки.
Коэффициенты нагрузки находятся по следующим зависимостям:
при расчете на контактную выносливость ;
при расчете на изгибную выносливость
где - коэффициенты учитывающие неравномерность распределения нагрузки по длине зуба (ширине зубчатого венца) при расчете по контактным и изгибным напряжениям соответственно;
- динамические коэффициенты (учитывают внутреннюю динамику передачи) при расчете по контактным и изгибным напряжениям соответственно.
1.3.1. Коэффициент концентрации нагрузки.
По ГОСТ 21354-75 установлено 7 основных схем расположения элементов передач относительно опор. Принимаем для передачи 1-2[1стр.31]. Для передачи 1-2 принимаем схему 3. Для выбора коэффициентов рассчитываем параметр .
Тогда из графиков ориентируясь по рисунку 5.1. [1] и определяем значения коэффициентов концентрации нагрузки.
1.3.2. Динамические коэффициенты.
Значения коэффициентов и выбирают в зависимости от окружной скорости в зацеплении точности изготовления передачи и твердости.
Окружную скорость определяем по формуле 5.3 [1]:
где - частота вращения шестерни рассчитываемой пары колёс обмин; - вспомогательный коэффициент; - момент на колесе рассчитываемой пары Н·м.
По табл.5.1. [1] принимаем (У1+У2 косозубое).
Степень точности согласно табл.5.2 [1] для цилиндрических косозубых передач - 8-ая.
Коэффициент принимаем по табл.5.3 [1]
Коэффициент принимаем по табл.5.4 [1]
1.4 Геометрические параметры
1.4.1 Расчёт межосевого расстояния
Определяем предварительное значение межосевого расстояния по формуле:
; где - крутящий момент на валу колеса Н·м - расчётное допускаемое напряжение Нмм2 - коэффициент нагрузки - коэффициент ширины зубчатого колеса по табл.6.3 [1]
1.4.2 Расчёт модуля зацепления
Модуль зацепления определяется из эмпирического соотношения:
принимаем т.к. при твердости поверхности зубьев Н≤НВ350 берется нижнее значение указанного интервала.
1.4.3 Определяем числа зубьев зубчатых колёс
Суммарное число зубьев определяется из следующего соотношения:
где - угол наклона на делительном цилиндре.
Так как значение угла является неизвестным то предварительно задаются величиной а затем уточняют.
Число зубьев шестерни:
Число зубьев колеса:
1.4.3 Определение геометрических размеров зубчатых колёс
Ширина зубчатого венца колеса определяется из следующей зависимости:
для снижения влияния погрешностей монтажа ширина шестерни принимается больше ширины колеса на 5мм.
Минимальное значение угла
Диаметры делительных окружностей:
Проверим межосевое расстояние:
Диаметры окружностей вершин:
Диаметры окружностей впадин:
1.5 Проверочные расчёты зацепления
После определения размеров зацепления проводятся проверочные расчёты по контактным напряжениям напряжениям изгиба и кратковременным перегрузкам.
Уточняем значение окружной скорости: мс.
1.5.1 Проверочный расчёт передачи по контактным напряжениям
1.5.2 Проверочный расчёт по напряжениям изгиба
Предварительно определим коэффициенты прочности зуба шестерни и колеса по табл.6.4 4.стр.30 в зависимости от приведенного числа зубьев колес ().
Проверочный расчет по напряжениям изгиба выполняется отдельно для зуба шестерни и колеса.
1.5.3 Проверочный расчет по кратковременным перегрузкам
Условие выполняется.
1.5 Силы действующие в зацеплении
Окружная сила в зацеплении:
Радиальная сила в зацеплении:
где: - угол зацепления
Осевая сила в зацеплении:
Таблица 3.2 - Результаты расчета передачи 1-2
Рассчитываемый параметр
Межосевое расстояние
Число зубьев шестерни
Нормальный модуль зацепления
Диаметр делительной окружности шестерни
Диаметр делительной окружности колеса
Диаметр окружности выступов шестерни
Диаметр окружности выступов колеса
Диаметр окружности впадин шестерни
Диаметр окружности впадин колеса
Ширина зубчатого венца шестерни
Ширина зубчатого венца колеса
Степень точности передачи
Окружная сила в зацеплении
Радиальная сила в зацеплении
Осевая сила в зацеплении
2. Цилиндрическая косозубая передача 3-4
Вращающий момент на шестерне 3 Т23 (Н×м) ..9407
Вращающий момент на колесе 4 Т4 (Н×м) .4154
Частота вращения вала 2-3n23(обмин) .. 1594
Частота вращения вала 4-5n4(обмин) .. 3464
Передаточное число i34 46
Cрок службы передачи Lгод(годы) . 5
2.1 Выбор материалов термообработки и твёрдости
Критерии работоспособности и расчета. Передача 3-4 является закрытой поэтому основной критерий работоспособности и расчета – контактная выносливость рабочих поверхностей зубьев. Цель расчета: определить геометрические размеры зубчатой передачи.
2.2.1 Определение допускаемых контактных напряжений.
2.2.2. Определение допускаемых значений напряжений при расчете зубьев на усталостный изгиб.
2.2.3. Определение допускаемых предельных напряжений при расчете на контактную и изгибную прочность по максимальным нагрузкам.
2.3. Определение коэффициентов нагрузки.
2.3.1. Коэффициент концентрации нагрузки.
По ГОСТ 21354-75 установлено 7 основных схем расположения элементов передач относительно опор. Принимаем для передачи 3-4 [1стр.31]. Для передачи 3-4 принимаем схему 5. Для выбора коэффициентов рассчитываем параметр .
2.3.2. Динамические коэффициенты.
2.4 Геометрические параметры
2.4.1 Расчёт межосевого расстояния
; где - крутящий момент на валу колеса Н·мм - расчётное допускаемое напряжение Нмм2 - коэффициент нагрузки - коэффициент ширины зубчатого колеса по табл.6.3 [1]
2.4.2 Расчёт нормального модуля зацепления
2.4.3 Определяем числа зубьев зубчатых колёс
2.4.3 Определение геометрических размеров зубчатых колёс
2.5 Проверочные расчёты зацепления
Уточняем значение окружной скорости: мс.
Коэффициенты и не изменятся.
2.5.1 Проверочный расчёт передачи по контактным напряжениям
- условие выполняется.
2.5.3 Проверочный расчет по кратковременным перегрузкам
2.5 Силы действующие в зацеплении
Таблица 3.4 - Результаты расчета передачи 3-4
Наименование рассчитываемого параметра
Модуль передачи (норм.)
Диаметр начальной окружности шестерни
Диаметр начальной окружности колеса
ОРИЕНТИРОВОЧНЫЙ РАСЧЕТ ВАЛОВ
Диаметры различных участков вала.
1. Быстроходный вал 1
Находим наименьший диаметр на данном валу – диаметр под ступицу полумуфты:
где-момент на быстроходном валу.
Принимаем значение диаметра вала равное стандартному диаметру вала под ступицу Муфты упругой со звездочкой 63-28-1.25-11.2-У3 ГОСТ 14084-93: мм.
Диаметр вала под подшипником:
Диаметр буртика подшипника:
где r – радиус скругления галтели r = 2мм.
2 Промежуточный вал 2-3
где - момент на промежуточном валу.
Диаметр буртика колеса:
Диаметр вала под полумуфту:
- момент на тихоходном валу
мм. Принимаем = 45 мм
Диаметр вала под колесом: .
Диаметр буртика колеса (f = 16 мм):
4 Предварительный выбор подшипников
На валы устанавливаем шариковые радиальные подшипники (рис. 4.4) т.к. на опоры не действует больших осевых нагрузок.
Шариковые радиальные
Диаметр внутреннего кольца d (мм)
Диаметр наружного кольца D (мм)
Грузоподъёмность Сr (кН)
Грузоподъёмность С0r (кН)
КОНСТРУКТИВНЫЕ РАЗМЕРЫ ЗУБЧАТЫХ КОЛЕС
Внутренний диаметр: мм.
Наружный диаметр: мм.
Длина: мм принимаем мм.
мм мм –условие не выполняется следовательно принимаем мм.
Радиусы закруглений: .
Длина: принимаем мм.
КОНСТРУКТИВНЫЕ РАЗМЕРЫ КОРПУСА
Толщина стенки корпуса и крышки редуктора:
Толщина верхнего пояса (фланца) корпуса: мм.
Толщина нижнего пояса (фланца) крышки корпуса:
Диаметр винта крепления редуктора к плите (раме):
Число z винтов принимают в зависимости от межосевого расстояния (мм) тихоходной ступени: z=4 при мм.
Диаметр болтов крепления крышки и корпуса редуктора у подшипников: мм;
Диаметр болтов крепления крышки и корпуса редуктор в прочих местах мм.
Принимаем К2=33мм К3=28мм С2=18мм С3=16мм.
Расстояние от зубчатых колес до корпуса
ПРОВЕРКА ДОЛГОВЕЧНОСТИ ПОДШИПНИКОВ
1 Пространственная схема привода
2.1 Радиальные реакции опор от сил в зацеплении – в плоскости YOZ
R1z+R2z+Fr2-Fr3 =513+632+429-1574 = 0 – реакции найдены правильно.
Радиальные реакции опор от сил в зацеплении – в плоскости XOY
R1х- Ft2 - Ft3 +R2х = 2281 – 1156 – 4230+3105 = 0 - реакции найдены правильно.
Cуммарные реакции опор
2.2 Реакции опор для расчета подшипников
FR1 max = R1 = 2338Н
FR2 max = R2 = 3169Н.
Внешняя осевая сила действующая на вал:
FA max =Fa3 - Fa2 = 902-235=667Н.
2.3 Для типового режима нагружения коэффициент эквивалентности
Вычисляем эквивалентные нагрузки:
2.4 Предварительно назначаем подшипники шариковые радиальные однорядные легкой серии - 206. Схема установки подшипников – враспор.
2.5 Для принятых подшипников
Коэффициент осевого нагружения:
В соответствии с табл. 7.3 3.стр.114 имеем:
2.6 Эквивалентная динамическая радиальная нагрузка
Рассматриваем подшипник опоры 1:
Отношение что больше (коэффициент V=1 при вращении внутреннего кольца).
Окончательно принимаем по табл. 7.2 3.стр.113:
Х=056; Y=044е=0440254=1732.
Рассматриваем подшипник опоры 2:
(коэффициент V=1 при вращении внутреннего кольца). Т.к. на подшипник не действует осевых сил кончательно принимаем по табл. 7.2 3.стр.113:
где КБ = 14 – коэффициент безопасности КТ = 1 при tраб 100 - коэффициент температурного влияния.
1.7 Вычисляем расчетный скорректированный ресурс при а1 = 1; а23 = 08 и k = 3
Расчетный ресурс больше требуемого: L10ah>L10ah (19020> 3811).
1.8 Проверка выполнения условия РЭ max ≤ 0.5Cr
Эквивалентная динамическая радиальная нагрузка
Условие РЭ max ≤ 0.5Cr выполнено: 4437 05 19500 = 9750 Н.
1.9 Т.к. расчетный ресурс больше требуемого и выполнено условие
РЭ max ≤ 0.5Cr то подшипник 206 пригоден при требуемом ресурсе надежности выше 90%
ПРОВЕРКА ПРОЧНОСТИ ШПОНОЧНЫХ СОЕДИНЕНИЙ
Проверка шпонок на смятие по напряжению смятия:
- допускаемое нормальное напряжение на смятие при стальной ступице и спокойной нагрузке МПа [6].
Полумуфта 1(на быстроходном валу редуктора):
Шестерня 5: шпонка подходит.
УТОЧНЕННЫЙ РАСЧЕТ ВАЛОВ
Выполним уточненный расчет промежуточного вала 2-3. Проверяем прочность вала в опасных сечениях на сопротивление усталости. Материал вала сталь 40Х.
1 Сечение A-A (концентратор напряжений – зубчатый венец)
1.1 Расчет на статическую прочность
В расчете определяем нормальные и касательные напряжения в рассматриваемом сечении вала при действии максимальных нагрузок:
где - суммарный изгибающий момент Нм;
- крутящий момент Нм;
и - моменты сопротивления сечения вала при расчете на изгиб и кручение мм3;
- площадь поперечного сечения мм2.
где - коэффициент выбирается в зависимости от смещения х и количества зубьев z принимаем =099; - диаметр центрального отверстия =0. мм3;
где - коэффициент выбирается в зависимости от смещения х и количества зубьев z принимаем =098;
Частные коэффициенты запаса прочности по нормальным и касательным напряжениям (пределы текучести и материала ):
- общий коэффициент запаса прочности;
=2. Вал пригоден к эксплуатации.
1.2 Расчет на сопротивление усталости
- коэффициент запаса прочности
где и - коэффициенты запаса по нормальным и касательным напряжениям.
Напряжения в опасных сечениях вычисляем по формулам:
где - результирующий изгибающий момент Нм;
Пределы выносливости вала в рассматриваемом сечении:
где и - пределы выносливости гладких образцов при симметричном цикле изгиба и кручения (табл.10.2 3.стр.185);
и - коэффициенты снижения предела выносливости.
где и - отношение концентрации напряжений (табл. 10.13 3.стр.192);
и - коэффициенты влияния абсолютных размеров поперечного сечения (табл. 10.7 3.стр.191);
и - коэффициенты влияния качества поверхности (табл.10.8 3.стр.191);
- коэффициент влияния поверхностного упрочнения (табл.10.9 3.стр.191).
Для зубчатого зацепления .
где - коэффициент чувствительности к асимметрии цикла напряжений в рассматриваемом сечении;
- коэффициент чувствительности материала к асимметрии цикла напряжений (табл. 10.2 3.стр.185);
- среднее напряжение цикла .
=25. Вал пригоден к эксплуатации.
2 Сечение Б-Б (концентратор напряжений – посадка с натягом шпоночный паз)
2.1.Расчет на статическую прочность
Частные коэффициенты запаса прочности по нормальным и касательным напряжениям (пределы текучести и материала см. табл. 10.2 3.стр.185):
Вал пригоден к эксплуатации.
2.2 Расчет на сопротивление усталости
где и - эффективные коэффициенты концентрации напряжений (табл. 10.11 3.стр.192);
Для посадки с натягом .
Для шпоночного паза .
. Вал пригоден к эксплуатации.
ВЫБОР ПОСАДОК ДЕТАЛЕЙ РЕДУКТОРА
Посадка зубчатых колёс и звездочек на вал - (переходная посадка).
Посадка подшипников на вал (посадка с натягом).
Посадки подшипниковых крышек и стаканов (посадка с зазором).
Посадка подшипников в корпус .
Посадка муфты на вал редуктора -(переходная посадка).
ВЫБОР СОЕДИНИТЕЛЬНЫХ МУФТ
Муфту выбираем по диаметрам соединяемых валов. Для соединения вала электродвигателя (28мм) с входным валом (25мм) редуктора принимаем Муфту упругую втулочно-пальцевую 125-28-1.25-11.2-У3 ГОСТ 21425-93.
Проверка муфты Т·к[T]
Т – момент на валу ·к – коэффициент запаса принимаем к=15 [T] =125Нм.
52·15=2478125- муфта подходит.
Для соединения выходного вала редуктора (45мм) с валом звездочки (45мм) принимаем Муфту упругую втулочно-пальцевую 710-45-2.45-2-У3 ГОСТ 21425-93.
Т – момент на валу ·к – коэффициент запаса принимаем к=15 [T] =710Нм.
54·15=6231710- муфта подходит.
Зацепления смазываются окунанием зубчатых колес в масло заливаемое внутрь корпуса до погружения венца зубчатых колес 2 и 4.
Выбираем вязкость 34 мм2с при мс и Нмм2 и принимаем масло И-Г-А-32 (см стр. 200 [3]).
Так как окружная скорость промежуточных зубчатых колёс больше 1мс то для смазки подшипников можно применить картерный способ (подшипники смазываются тем же маслом что и детали передач).
Слив масла осуществляем через сливное отверстие закрываемое пробкой с цилиндрической резьбой.
Устанавливаем ручку отдушину М12х1.75.
СБОРКА И РЕГУЛИРОВКА
В сквозные крышки подшипниковых узлов запрессовываем манжеты. На ведущий вал напрессовываем подшипники и надеваем дистанционное кольцо и крышку на вал. Вал помещаем в основание корпуса обеспечив установку буртика сквозной крышки в соответствующую канавку в отверстии под подшипник. Устанавливаем глухую крышку и дистанционное кольцо противоположного подшипникового узла. В пазы промежуточного и ведомого вала закладываем шпонки и напрессовываем зубчатые колеса до упора в бурт на валу. Надеваем на валы распорные кольца до упора в торец ступицы колеса. Напрессовываем на валы подшипники. Надеваем сквозную крышку и упорное кольцо на ведомый вал. Валы устанавливаем в основание корпуса. Закладывают глухие крышки и упорные кольца.
Надеваем на основание крышку корпуса покрыв предварительно плоскость разъема специальным герметиком. Крышка фиксируется двумя штифтами которые устанавливаются в специальные отверстия во фланце корпуса. Надеваем пружинные шайбы на болты и завинчиваем их.
В пазы выходных концов валов закладываем шпонки. Вкручиваем пробку маслосливного отверстия. Монтируем маслоуказатель. Через люк в крышке корпуса заливаем масло контролируя при этом уровень по маслоуказателю и закрываем люк крышкой.
Дополнительных регулировок редуктору не требуется.
Собранный редуктор подвергается обкатке и испытанию по программе предусмотренной техническими условиями.
При работе над курсовым проектом были закреплены знания методик
расчётов типовых деталей машин общего назначения получены навыки принятия решений при компоновке редуктора и конструировании его деталей.
Был выбран электродвигатель. В ходе расчёта зубчатых передач проработан вопрос оптимального их размещения в корпусе редуктора.
При компоновке механизма и вычерчивании сборочного чертежа определены способы фиксации колёс и подшипников на валах.
Выбранные подшипники проверены на пригодность исходя из их долговечности при расчёте по динамической грузоподъёмности.
Шпоночные соединения проверены на прочность по напряжениям смятия.
Определены опасные сечения валов по действующим нагрузкам и наличию концентраторов напряжений.
Проведён расчёт на усталостную прочность (выносливость) для наиболее опасного сечения вала.
Решены вопросы смазки передач редуктора и подшипников. Смазка подшипников картерная (тем же маслом что и для передач).
Для соединения валов редуктора с электродвигателем была выбрана муфта с упругими элементами компенсирующая погрешности монтажа агрегатов.
Полученная конструкция привода в полной мере отвечает современным
требованиям предъявляемым к механизмам данного типа.
Список использованных источников
Фейгин А.В. Расчет зубчатых передач: Методические указания по курсовому проектированию для студентов специальностей 0611 1012 1104 1201 1202 1502 1704 1709 2401 2405 2601 2602. – Хабаровск: Изд-во Хабар. гос. техн. ун-та 1997. – 39с.
Фейгин А.В. Расчет зубчатых передач (цилиндрические косозубые конические прямозубые): Методические указания по курсовому проектированию для студентов специальностей 0611 1012 1104 1201 1202 1502 1704 1709 2401 2405 2601 2602. – Хабаровск: Изд-во Хабар. гос. техн. ун-та 1997. – 39с.
Дунаев П. Ф. Леликов О. П. Конструирование узлов и деталей машин. – М.: Высшая школа 2003 – 447с. ил.
Курмаз Л. В. Скойбеда А.Т. Детали машин. Проектирование. : Учеб. пособие для техн. спец. вузов. – М.:Высш.шк.2002. – 286 с. ил
Курсовое проектирование деталей машин: Учеб. пособие для техникумовС.А. Чернавский Г.М. Ицкович К.Н. Боков и др. – М.: Машиностроение 1979. – 351 с. ил.
Шейнблит А.Е. Курсовое проектирование деталей машин: Учеб. пособие.- Изд. 2-е перераб. и доп.- Калининград: Янтар. сказ 2003.- 454 с.: ил. черт.- Б. ц.
детали два А3 и А4.dwg

Неуказанные предельные отклонения размеров:
остальных- t 2 по ГОСТ 25670-83
*Размер обеспечиваемый инструментом
Неуказанные радиусы 2мм max
Формовочные уклоны 1
общ A1.dwg

Радиальное смещение валов до 0
Техническая характеристика
Окружная сила на тяговом барабане
Скорость движения конвейерной ленты
Частота вращения приводного вала
Общее передаточное число привода
Привод ленточного транспортера
КП 59-02.00.00.00 ВО
План размещения отверстий под фундаментные болты (1:5)
Ось вала электродвигателя
КП 44-05.00.00.00 ВО
Титульник.doc
Федеральное государственное бюджетное образовательное учреждение высшего профессионального образования
“Тихоокеанский государственный университет”
ПРИВОД ЦЕПНОГО КОНВЕЙЕРА
пояснительная записка к курсовому проекту
по дисциплине “Детали машин”
КП 44-05.00.00.00 ПЗ
Сборочный А1.dwg

Техническая характеристика Момент на выходном валу Т4 =415
Нм. Частота вращения выходного вала n4 =34
обмин. Передаточное число редуктора Uред =27
Поверхности соединений "корпус-крышка" перед сборкой покрыть уплотнительной пастой типа Герметик. 2. После сборки валы редуктора должны проворачиваться свободно
без стуков и заедания. 3. Редуктор обкатать по 10-15 мин. на всех режимах нагрузки.
Редуктор цилиндрический двухступенчатый
A4-СПЕЦИФИКАЦИЯ.dwg

Пояснительная записка
Привод ленточного транспортера
Муфта 710-45-1.45-1-У3
КП 44-05.00.00.00 ВО
КП 44-05.00.00.00 ПЗ
КП 44-05.01.00.00 СБ
Редуктор цилиндрический двухступенчатый
Кольцо дистанционное
КП 44-05.01.01.00 СБ
Манжета ГОСТ 8752-79
Шпонка ГОСТ 23360-78
Фонарный маслоуказатель
Подшипники шариковые радиальные
Муфта 125-28-1.25-1-У3
Рекомендуемые чертежи
- 15.02.2021
- 20.04.2023
- 10.03.2024