Привод пластинчатого конвейера схема 33 вариант 11




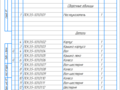
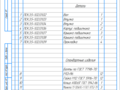
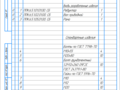
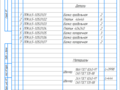
- Добавлен: 24.01.2023
- Размер: 1 MB
- Закачек: 0
Описание
Состав проекта
![]() |
![]() ![]() ![]() ![]() |
![]() ![]() ![]() ![]() |
![]() ![]() ![]() |
![]() ![]() ![]() ![]() |
![]() ![]() ![]() ![]() |
![]() ![]() ![]() ![]() |
![]() ![]() ![]() ![]() |
![]() ![]() ![]() ![]() |
![]() ![]() ![]() ![]() |
![]() ![]() ![]() ![]() |
![]() ![]() ![]() ![]() |
Дополнительная информация
Общий вид.cdw

Спецификация(лист1).spw

Спецификация Рама.spw

Спецификация Общий вид.spw

Эскиз. компоновка+.cdw

Рама редуктора+.cdw

Спецификация привод вал (лист 2).spw

Сборочный (лист1)+.cdw

Деталировка А3.cdw

Приводной вал(лист2)+.cdw
