Привод ковшового элеватора (двухступенчатый коническо-цилиндрический редуктор)



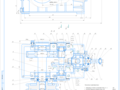

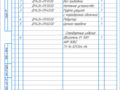
- Добавлен: 24.01.2023
- Размер: 747 KB
- Закачек: 1
Описание
Привод ковшового элеватора (двухступенчатый коническо-цилиндрический редуктор)
Состав проекта
![]() |
![]() ![]() ![]() |
![]() ![]() ![]() ![]() |
![]() ![]() ![]() ![]() |
![]() ![]() ![]() ![]() |
Дополнительная информация
спецификация А5.cdw

спецификация А1.cdw

Курсовой детали машин.cdw
