Отчет по практике по теме: Основы технологии производства автомобилей




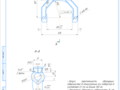
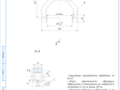
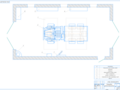
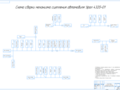
- Добавлен: 25.01.2023
- Размер: 5 MB
- Закачек: 0
Описание
Состав проекта
![]() |
![]() ![]() ![]() ![]() |
![]() ![]() ![]() ![]() |
![]() ![]() ![]() ![]() |
![]() ![]() ![]() |
![]() ![]() ![]() ![]() |
Дополнительная информация
Ремонтный чертёж вилки выключения сцепления.cdw

Неуказанные шероховатости обработать по
Допуск параллельности образующих
поверхностей Д относительно оси отверстия Б
мм на длинне 100 мм.
Отклонение образующих поверхностей Д от
общей прилегающей цилиндрической
поверхности не более 0
Допуск симметричности шпоночного паза
относительно диаметральной плоскости
отверстия Б составляет 0
Вилка переключения передач.cdw

Сталь 45 ГОСТ 1050-85
Допуск параллельности образующих
поверхностей Ж относительно оси отверстия Б
мм на длинне 100 мм.
Отклонение образующих поверхностей Ж от
общей прилегающей цилиндрической
поверхности не более 0
Допуск симметричности шпоночного паза
относительно диаметральной плоскости
отверстия Б составляет 0
Схема сборки сцепления.cdw

К1-Проверить положение упорного кольца 2 и при необходимости
К2-Проверить и при необходимости провести статическую
балансировку кожуха сцепления в сборе с нажимнымдиском.
К3-Проверить правильность сборки ведомого диска.
К4-проверить правильность сборки среднего ведущего диска.
Совместить концы вилок 8 с отверстиями кожуха 12.
Сжать нажимные пружины.
Застопорить регулировочные гайки 13 отгибанием стопорных
Нанести смазку Литол-24 тонким слоем.
Схема сборки механизма сцепления автомобиля Урал 4320-01
отпа Отчет по практике.doc
молодёжи и спорта Украины
Севастопольский национальный технический университет
по практическим работам по дисциплине
«Основы технологии производства автомобилей»
Практическая работа №13
Метрологическая экспертиза конструкторской и технологической документации3
Практическая работа №2 Проектирование технологического процесса сборки7
Практическая работа №3 Расчет режимов сборочных операций12
Практическая работа №4 Нормирование сборочных операций14
Практическая работа №5 Выбор заготовки с экономическим обоснованием17
Практическая работа №6 Разработка маршрутного тех. процесса обработки детали18
Практическая работа №7 Расчет режимов резания21
Практическая работа № 8 Нормирование технологической операции25
Приложение А сборочный чертеж31
Приложение Б вилка переключения передач32
Приложение В схема сборки механизма сцепления33
ПРАКТИЧЕСКАЯ РАБОТА №1
МЕТРОЛОГИЧЕСКАЯ ЭКСПЕРТИЗА КОНСТРУКТОРСКОЙ И
ТЕХНОЛОГИЧЕСКОЙ ДОКУМЕНТАЦИИ
Цель работы: Приобретение практических навыков по анализу служебного назначения и технологичности конструкций агрегатов узлов и деталей автотранспортных средств.
Разработаем технологические процессы сборки механизма сцепления автомобиля
Урал 4320-01 и изготовления вилки сцепления в условиях мелкосерийного производства.
Описание конструкции и служебного назначение узла
Базовый автомобиль – Урал 4320-01. Выпускаются Уральским автозаводом (г.Миасс) с 1988 г. Урал-4320-01 н Урал-43202-01 являются модернизированными автомобилями соответственно Урал-4320 и Урал-43202 которые выпускались с 1977 по 1988гг. Кузов Урал-4320-01 - металлическая платформа армейского типа с откидным задним бортом оборудована боковыми откидными и съемной средней скамейками съемными дугами и тентом дополнительными боковыми и передними надставными решетчатыми бортами. Кузов Урал-43202-01 - деревянная платформа с откидными боковыми и задним бортами оборудована съемными двумя боковыми и одним передним надставными бортами предусмотрена установка дуг и тента. Кабина - трехместная с термо- и шумоизоляцией расположена за двигателем сиденье регулируется по длине высоте и наклону спинки. На автомобиле Урал-4320-01 предусмотрена установка лебедки [1].Общий вид автомобиля показан на рис.1.1.
Рисунок 1.1 – Общий вид автомобиля Урал 4320-01
Краткие технические характеристики:
Колесная формула - 6x6
Полная масса кг -19 800
Масса перевозимого груза кг - 10 000
Распределение полной массы автомобиля кг:
- на передний мост 5 090
- на заднюю тележку 14 710
Полная масса буксируемого прицепа кг - 11 500
Максимальная скорость кмч - 75
Двигатель: ЯМЗ-238М2 дизельный
номинальная мощность при 2 100 мин-1 кВт (л.с.) 176 (240)
максимальный крутящий момент при 1 350 мин-1 Нм (кгс.м) 883 (90)
Трансмиссия 5-ступенчатая коробка передач 2-ступенчатая раздаточная коробка с межосевым блокируемым дифференциалом. Агрегаты оборудованы системой герметизации.
Платформа металлическая с задним откидным бортом оборудована съемными дугами и тентом боковыми откидными и съемной скамейками
Количество мест для перевозки людей - 36
Кабина цельнометаллическая трехместная оборудована системой вентиляции и отопления
Шины 1200x500-508 156F
ИД-П284 с регулируемым давлением
Емкость топливного бака л - 300
Контрольный расход топлива при скорости - 60 кмч л100 км 40
Запас хода по контрольному расходу топлива при скорости - 60 кмч км 720
Габаритные размеры автомобиля мм - 9 545x2 500x3 075
Дорожный просвет мм - 360
Внешний габаритный радиус поворота м -14
Преодоление препятствий: - подъем % 27 - брод м 12
Базовый узел – механизм сцепления (приложение А). Является элементом трансмиссии. Предназначен для временного отсоединения двигателя от коробки переключения передач а также плавного трогания с места.
Сцепление (см. рис. 1.2) мод. КамАЗ-14 сухое фрикционное двухдисковое с перифирийным расположением нажимных привод выключения - механический с пневматическим усилителем.
При нажатии водителем на педаль сцепления. Механически с помощью рычагов и тяг а также благодаря пневматическому усилению происходит нажатие вилкой на муфту выключения сцепления. Муфта в свою очередь действует на оттяжной рычаг и происходит отсоединение ведущих дисков от ведомых.
Анализ технологичности конструкции
Технологичность конструкции детали анализируют с учётом условий её производства рассматривая особенности конструкции и требования качества как технологические задачи изготовления. Под технологичностью конструкции изделия понимается совокупность свойств обеспечивающих оптимальное использование различных видов ресурсов при технической подготовке производства изготовлении эксплуатации и ремонте с учетом обеспечения требуемого уровня технических характеристик и качества[4].
Конструкция базового узла - механизма сцепления – в целом технологична и предусматривает:
Максимальное упрощение конструкции узлов и деталей;
рациональность членения и компоновки изделий и их составных частей; конфигурация и размерные соотношения деталей и узлов не вызывают трудностей при их изготовлении сборке и контроле;
широкое использование принципов конструкторской и технологической преемственности унификации стандартизации;
рациональное ограничение количества марок и сортамента применяемых материалов; использование недефицитных материалов и материалов обработка которых не вызывает трудностей;
рациональное назначение термообработки допусков шероховатости поверхностей;
возможность применения прогрессивных технологических процессов и высокопроизводительного оборудования не ухудшающих точность но значительно облегчающих изготовление деталей;
удобство обслуживания и ремонта изделия в процессе эксплуатации.
Базовая деталь – вилка выключения сцепления (ПриложениеБ) – относится к классу рычаги и вилки и приводит в действие механизм сцепления. Деталь работает в условиях динамических переменных нагрузок и повышенного износа на посадочной поверхности и ушке. Через вал передаются крутящие моменты. Наиболее точными поверхностями являются посадочное отверстие и поверхность Ж. Предъявляется допуск параллельности и отклонения к пов-ти Ж.
Деталь выполнена из стали 45л по ГОСТ 977-75 методом литья. Химический состав и механические свойства стали приводятся в таблице 1.2.
Вывод: В данной практической работе были приобретены практические навыки по анализу служебного назначения и технологичности конструкций агрегатов узлов и деталей грузового автомобиля Урал 4320-01.
ПРАКТИЧЕСКАЯ РАБОТА №2
ПРОЕКТИРОВАНИЕ ТЕХНОЛОГИЧЕСКОГО ПРОЦЕССА СБОРКИ
Цель работы: изучение методов проектирования маршрута процесса сборки изделий.
1. Теоретический раздел
Сборка является одним из наиболее ответственных этапов при производстве и ремонте изделий. К исходным данным необходимым для проектирования процесса сборки относят:
количество изготавливаемых автомобилей или их составных частей;
сборочные чертежи узла составных частей спецификации деталей входящих в узел;
технические условия на сборку и испытания изделия технологические инструкции на подбор деталей контроль и регулировку сопряжении и сборочных единиц;
каталоги и справочники по используемому при сборке оборудованию и технологической оснастке.
При проектировании технологического процесса сборки необходимо учитывать рекомендации ГОСТ 14.301 – 95. Проектирование технологического процесса выполняют после анализа служебного назначения и технологичности конструкции изделия. На первом этапе составляется схема общей и узловой сборки. При большой программе выпуска (массовое и крупносерийное производство) технологический процесс сборки изделия разрабатывают подробно при малой сокращенно.
На последовательность сборки влияют: функциональная взаимосвязь элементов изделия конструкция базовых элементов условия монтажа силовых и кинематических передач постановка легко повреждаемых элементов в конце сборки размеры и масса присоединяемых элементов пень взаимозаменяемости элементов изделия.
Технологические схемы сборки являются основой для последующего проектирования технологических процессов сборки. Сначала составляют схему общей сборки а затем схемы узловой сборки (рисунок 2.1).
Рисунок 2.1 – Схема сборочного процесса
По методике профессора В.М. Кована [3] основное направление сборочного процесса в пределах сборочной операции отображают горизонтальным отрезком левый конец которого обозначает начало а правый - окончание сборочного процесс. Каждый элемент изделия будь то сборочная единица деталь или законченное изделие условно обозначают прямоугольником разделенным на три части. В верхней части указывают название элемента в нижней левой - его индекс в нижней правой количество устанавливаемых в данном месте операции элементов. К началу горизонтальной линии схемы пристраивают прямоугольник (рис. 2.2.) обозначающий базовый элемент конструкции с которого начинают сборку Для отличия сборочных единиц от деталей у первых рядом с индексом проставляют «Сб». В конце горизонтальной линии пристраивают прямоугольник обозначающий объект сборки – сборочную единицу. Над горизонтальной линией вертикально располагают прямоугольники обозначающие детали поступающие на данную операцию поштучно без какого-либо предварительного соединения. Под горизонтальной линией располагают прямоугольники обозначающие сборочные единицы. Сборочные единицы собранные на предыдущих участках и комплектующие изделия - сборочные единицы поступающие на данный завод с других специализированных заводов например шарикоподшипники электродвигатели насосы приборы показываются без расшифровки процесса сборки.
Рисунок 2.2 – Элемент сборки
Технологическую схему сборки снабжают дополнительными надписями которые указывают содержание работ трудно определяемых по схеме (совместно сверлить и развернуть регулировать зазор смазать сварить запрессовать и т.д.). Эти указания записывают либо на полках выносных линий идущих от точек пересечения линий связи на схеме либо под схемой в виде пронумерованного текста согласно порядковым номерам операций (1 2 3 и т.д.) которые помещают в кружках в местах пересечения линий связи. Контрольным операциям присваивают номера начиная с первого с индексом К (например К1).
На схемах сборки следует указывать только контрольные операции предусмотренные ТУ и инструкциями. В них указывают: содержание последовательность выполнения допустимые отклонения контролируемого параметра и другие требования.
Зная исходные данные установленные методы сборки и принятый тип производства выбирают организационную форму сборочного процесса (сборка на стендах подвижная сборка поточная сборка автоматическая сборка). По принятым схемам сборки выявляют технологические и вспомогательные сборочные операции. Содержание операций устанавливают так чтобы на каждом рабочем месте выполнялась однородная по своему характеру и технологически законченная работа что способствует лучшей специализации рабочих и повышению производительности их труда. При массовом производстве длительность операций должна быть равна или кратна такту выпуска изделий. Разработанный технологический процесс оформляют в виде маршрутной карты (ГОСТ 3.1105-84 форма 13 и 13а) в которой приводится описание технологического процесса по всем операциям в технологической последовательности с указанием данных по оборудованию оснастке материальным и трудовым затратам.
При наличии сложных сборочных единиц в изделии рекомендуется составлять укрупненные схемы сборки. В данном случае на том же листе приводятся развернутые схемы сборки сборочных единиц.
Разработаем маршрутный технологический процесс сборки сцепления автомобиля Урал 4320-01. Т.к. производство мелкосерийное выбираем стационарную сборку на стендах с применением методов полной и неполной взаимозаменяемости.
Схема сборки приводится в приложении В.
Маршрутный технологический процесс сборки
Установить в отверстие оттяжных рычагов 3 (рис.2.3) с помощью технологических пальцев игольчатые ролики 4соединить рычаги3 с вилками 8запрессовать оси 5 рычагов поставить пружины 9надеть плоские шайбы 7 и упорные кольца 6.
Установить нажимной диск на стенд.
Установить в отверстия оттяжных рычагов игольчатые ролики.
Ввести поочередно оттяжные рычаги 10 в сборе с вилками и пружинами в прорези бобышек нажимного диска 1вставить оси 5 в совмещенные отверстия бобышек и рычаговвыталкивая технологические пальцыи установить упорные кольца 6.
Установить нажимной диск подкладки 22шайбы 21 и нажимные пружины 20.
Установить петли 11 пружин упорного кольца и упорное кольцо 2.
Установить кожух 12 сцепления на нажимные пружинысовместить концы вилок 8 с отверстиями кожуха 12сжать нажимные пружиныввернув стяжные болты 18 в нажимной диск.
Завернуть регулировочные гайки 13 на вилки рычагов.
Проверить положение упорного кольца 2 и при необходимости отрегулировать его.
Установить стопорные шайбы 14 регулировочных гаек.
Установить опорные 15 и запорные 16 пластины регулировочных гаекввернуть болты 17застопорить болты отгибанием усов запорных пластин 16застопорить регулировочные гайки 13 отгибанием стопорных шайб 14.
Проверить и при необходимости провести статическую балансировку кожуха сцепления в сборе с нажимным диском.
Снять кожух сцепления в сборе с нажимным диском со стенда.
Совместить отверстия фрикционных накладок 2 (рис.2.4) и 4 с отверстиями ведомого диска 3 сцепления и прижать накладки к диску струбциной.
Вставить заклёпки 1 в совмещенные отверстия накладок и дискаустановить диск на опору пресса и расклепать заклёпки.
Перевернуть ведомый диск в сборевставить заклёпки в отверстияустановить диск на опору пресса и расклепать заклёпки.
Проверить правильность сборки ведомого диска сцепления.
Нанести на оси 6 (рис.2.5) смазку Литол-24 тонким слоем.
Установить на оси 6 втулки5 рычаги 4пружины 3стопорные шайбы 2.
Ввернуть оси с рычагами в средний ведущий диск 1.
Застопорить оси среднего ведущего дискаотогнув с двух сторон стопорные шайбы 2.
Проверить правильность сборки среднего ведущего диска.
Вывод: В данной практической работе была составлена схема сборки механизма сцепления автомобиля Урал 4320-01.
Рисунок 2.5 Рисунок 2.6
ПРАКТИЧЕСКАЯ РАБОТА №3
РАСЧЕТ РЕЖИМОВ СБОРОЧНЫХ ОПЕРАЦИЙ
Цель работы: приобретение практических навыков по проектированию сборочных операций.
1.Теоретический раздел
Для проектирования операций необходимо знать маршрутную технологию схему базирования и закрепления изделия намеченное ранее содержание операций для поточной линии - такт выпуска изделий. Проектирование операции рекомендуется выполнять в следующей последовательности:
уточняется схема базирования и содержание операции устанавливается последовательность и возможность совмещения переходов во времени;
окончательно выбирается оборудование приспособления и инструменты (или даются задания на их проектирование);
рассчитываются или выбираются режимы работы сборочного оборудования;
рассчитываются или назначаются нормы времени;
при необходимости проводится технико-экономический анализ вариантов выполнения сборочной операции;
заполняются операционные карты и карты эскизов и схем.
В зависимости от конструкции изделия вида сборочной операции возможны следующие варианты базирования.
) Базовую деталь изделия базируют на необработанную поверхность и при одной установке производят его полную сборку (применяется преимущественно при ручной сборке простых изделий в приспособлениях обеспечивающих их неподвижное расположение).
) Базовую деталь изделия базируют на обработанную поверхность. Схему базирования применяют при ручной сборке в приспособлениях обеспечивающих точное положение сопрягаемых деталей а также при механизированной и автоматической сборке.
) Базовую деталь изделия устанавливают на различные последовательно сменяемые базы.
Содержание операций определяет тип основные размеры и техническая характеристика сборочного оборудования и технологической оснастки (приспособлений рабочего и измерительного инструмента). При серийном производстве технологическое оборудование и оснастку применяют универсального переналаживаемого типа. В массовом производстве преимущественно используют специальное оборудование и оснастку. Тип основные размеры и грузоподъемность подъёмно-транспортных систем определяют по установленным организационным формам сборки размерным характеристикам изделий и их массе. Выбор оборудования и технологической оснастки рекомендуется проводить по справочной литературе [3] [4] [5].
Режимы работы сборочного оборудования определяют либо аналитически либо по нормативным и справочным данным. Более подробно выполняют расчет режимов на типовые сборочные операции такие как соединения с натягом резьбовые соединения клёпанные соединения.
Для большинства резьбовых соединений автомобилей нормируется момент затяжки. Минимальная сила затяжки выбирается из условия плотности соединения (не раскрытия стыка). Она определяется в зависимости от внешней силы Р по формулам
для осевой силы ; (3.1)
для касательной силы (3.2)
где К - коэффициент увеличения внешней нагрузки: К=125 2 - постоянная; К=25 4 - переменная; К=125 25 - при условии обеспечения герметичности с мягкими прокладками; К=25 35 - тоже с металлическими прокладками;
а = 02 04 - коэффициент основной нагрузки учитывающий податливость резьбовых соединений;
- коэффициент трения в резьбе. При стальном стержне для стального корпуса ; для чугунного - ; для алюминиевого или бронзового .
Момент затяжки для метрической резьбы с углом резьбы 600 равен:
где - средний диаметр резьбы мм;
- наружный и внутренний диаметры опорных кольцевых поверхностей гайки головки болта мм;
fр и - коэффициенты трения по резьбе и по опорной поверхности гайки. Зависят от вида покрытия и смазочных материалов состояния трущихся поверхностей повторяемости сборки скорости завинчивания и т.д. ;
d - номинальный диаметр резьбы.
Для проверки полученных значений необходимо рассчитать максимальный момент затяжки из условия прочности стержня. Если значение силы Р точно неизвестно то максимальный момент принимается в качестве расчетного с учетом коэффициента запаса (большие значения принимать для ответственных соединений).
Для болтовых и шпилечных соединений ориентировочно можно рассчитать:
где - предел прочности материала стержня МПа.
Для винтов с цилиндрической сферической или шестигранной головкой:
для винта с потайной головкой
где - предел текучести материала винта МПа.
Рассчитаем усилие затяжки стяжными болтами (4 шт) при резьбовой сборки кожуха с пружинами и нажимным диском
По формуле (3.5) рассчитаем режимы сборки.
Рассчитаем момент затяжки для болта стяжного сделанного из материала Сталь 10 с шестигранной головкой : Нм
Инструмент: ключ динамометрический.
Вывод: В данной практической работе мы рассчитали момент затяжки стяжного болта без смазки.
ПРАКТИЧЕСКАЯ РАБОТА №4
НОРМИРОВАНИЕ СБОРОЧНЫХ ОПЕРАЦИЙ
Цель работы: изучить методику нормирования технологического процесса сборки.
Нормирование сборочных операций выполняют по установленным методикам. Для массового производства подготовительно-заключительное время равно нулю. Штучное время вычисляется как сумма основного вспомогательного времен времени на организационно-техническое обслуживание рабочего места и отдых.
При нормировании операций технологического процесса серийного производства определяют штучно-калькуляционное время по зависимости
где Тпз – подготовительно-заключительное время связанное со сборкой партии изделий (10 15 мин);
n – число изделий в партии;
Тшт - штучное время.
Для массового производства подготовительно-заключительное время равно нулю. Штучное время вычисляют как сумму основного То вспомогательного Тв времен времени на организационно-техническое обслуживание рабочего места Торг.тех. об. и отдых Те.
Тшт=То+Тв+Торг.тех.об.+Те (4.2)
Составляющие времен можно определять по типовым технологическим процессам и справочной литературе [6]. Определить основное время сборочных работ с 5 15 % точностью можно на основе имеющихся эмпирических зависимостей приведенных в таблице 5.1.
Если сборочная операция имеет несколько переходов то основное время на операцию определяется суммированием основных времен отдельных переходов.
Вспомогательное время составляет 15 60 % от основного а оперативное время равно:
Дополнительное время на сборочные операции составляет примерно 6 10 % от оперативного а подготовительно-заключительное – 3 6 %. Тогда штучно-калькуляционное время можно подсчитать по формуле:
Таблица 4.1 - Эмпирические зависимости для расчета основного времени
Эмпирическая зависимость
Завертывание штуцеров
Установка шплинтов и штифтов
Установка шайб прокладок втулок
В таблице 2.1 - среднее арифметическое значение элемента детали (длина ширина и т.п.) мм; - количество одинаковых элементов используемых при сборке.
Рекомендуется следующая последовательность нормирования операции:
Рассчитать нормы времени на одну операцию (таблица 4.2). При выполнении сборочной операции в ней выделяют следующие переходы:
Проверить наличие клейм на деталях и состояние сопроводительной документации.
В содержание перехода входят ключевые слова характеризующие метод обработки выраженные глаголом в неопределенной форме. Ключевые слова: закрепить запрессовать зачистить застопорить контрить клепать маркировать нарезать опилить отрубить очистить отрезать притереть пломбировать развинтить распрессовать сверлить смазать свинтить собрать установить штифтовать и т.п.
В конце всех переходов записывается контроль исполнителем.
Пример записи переходов:
Установить шайбу поз.5. Свинтить детали поз.5 и 6 выдерживая размер 1 собрать детали поз.2 и 3 выдержав размер 1.
Выполнить эскиз технологической наладки выполнения операции.
Для операции рассмотренной в практической работе №3 в условиях мелкосерийного производства рассчитаем по формулам (4.1) (4.4) штучное время.
Результаты расчётов сведём в табл. 4.2.
Таблица 4.2 - Нормирование технологического процесса сборки изделия
Установить кожух 12 сцепления на нажимные пружины
Совместить концы вилок 8 с отверстиями кожуха 12
Надеть на болты стопорные шайбы
Сжать нажимные пружины ввернув стяжные болты (12 шт) 18 в нажимной диск с моментом 2358 Нм.
=(0006*25 +0144)*12=353
Оперативное время мин
Топ=То+Твсп=353+071=424
Вспомогательное время мин
Время на организационно-техническое обслуживание рабочего места и отдых
=Топ*(6..10%)=008*424=034
Вывод: В данной практической работе было нормирована операция резьбового соединения.
ПРАКТИЧЕСКАЯ РАБОТА №5
ВЫБОР ЗАГОТОВКИ С ЭКОНОМИЧЕСКИМ ОБОСНОВАНИЕМ
Цель работы: изучить основные способы получения заготовок факторы определяющие выбор способа получения заготовки выбрать наиболее экономически целесообразный способ получения заготовки.
Теоретический раздел
1.1. Основные понятия и определения
Заготовкой называется предмет труда из которого изменением формы размеров свойств поверхности и материала изготавливается деталь. Заготовка отличается от готовой детали по размерам (на величину припусков и напусков на механическую обработку).
Припуск на механическую обработку – это слой металла удаляемый с поверхности заготовки с целью получения требуемых по чертежу формы и размеров детали. Напуск –избыток металла на поверхности заготовки (сверх припуска) обусловленный технологическими требованиями упростить конфигурацию заготовки для облегчения условий её получения. В большинстве случаев напуск удаляется последующей механической обработкой.
Основные способы получения заготовок: литьё обработка металлов давлением (ОМД) сварка пайка. К заготовительным операциям технологического процесса относятся также правка прутков и проволоки отрезка заготовок прессование и редуцирование заготовок подготовка под сварку отжиг заготовок обработка торцов и центрование заготовок и т.д.
Рассматриваемая деталь представляет собой вилку предназначенную для управления включением и отключением механизма сцепления. Конструктивные особенности: наличие четырех точных отверстий два из которых должны быть соосными в другом отверстии выполнен шпоночный паз. Деталь работает в условиях повышенных температур и нагрузок. Поэтому деталь выполнена из углеродистой стали 45. Заготовка для вилки в условиях мелкосерийного производства может быть получена литьем в металлические формы.
Способы литья в многоразовые (металлические) формы:
) Литьё в кокиль – наиболее дешевый среди специальных способов литья. Предназначен для получения отливок простой формы из стали чугуна цветных сплавов в серийном производстве. Главная особенность этого способа – многократное использование металлической формы – кокиля. В связи с большой теплопроводностью материала формы скорость кристаллизации достаточно велика. Это повышает механические свойства отливки но в то же время затрудняет получение отливок с тонкими стенками. Литьё в кокиль позволяет получить отливки со следующими параметром шероховатости поверхности: отливки из черных металлов - Rz=40 мкм Rа=10 мкм из цветных сплавов Rz=10 мкм Rа=2 мкм.
) Литьё под давлением заключается в заливке расплавленного металла под давлением в металлическую пресс-форму и его кристаллизации. Применяется для производства тонкостенных отливок (до 05 мм) из цветных сплавов (массой до 50кг) в серийном и массовом производстве. Литьём под давлением можно получить сложные близкие по конфигурации к готовым деталям тонкостенные заготовки. Шероховатость поверхности отливок при этом способе литья Rz=10 мкм Rа=2 мкм.
) Центробежное литьё заключается в заливке расплавленного металла во вращающуюся форму (изложницу) которая вращается до окончания кристаллизации металла. Получают полые заготовки имеющие форму тел вращения диаметром 50 –1000 мм (трубы втулки зубчатые колеса кольца) из чугуна стали реже из цветных сплавов. За счёт вращения формы достигается большая плотность металла отливки. К недостаткам можно отнести ограниченный ассортимент отливок по форме. Шероховатость поверхности при этом способе литья следующая: отливки из черных металлов Rz =40 мкм Rа= 10 мкм из цветных сплавов –Rz=20мкм Rа=5мкм.
Чертеж заготовки - см. приложение Г.
Вывод: наиболее экономически целесообразный способ получения заготовки – литье в кокиль.
ПРАКТИЧЕСКАЯ РАБОТА №6
РАЗРАБОТКА МАРШРУТНОГО ТЕХНОЛОГИЧЕСКОГО ПРОЦЕССА
Цель работы: изучение последовательности и методов проектирования маршрутов технологических процессов обработки деталей автомобиля.
Разработаем маршрутный технологический процесс изготовления вилки в условиях мелкосерийного производства.
Для обоснования выбора варианта технологического процесса определяются методы обработки отдельных поверхностей из которых формируют маршруты обработки детали. Выбор метода обработки зависит от конфигурации детали её габаритов точности и качества обрабатываемых поверхностей вида принятой заготовки. Маршруты обработки поверхностей сводятся в таблицу 6.1. Маршрут обработки детали сводится в таблицу 6.2.
Таблица 6.1 – Маршруты обработки поверхностей детали
Требования к поверхности
Технологический приём обеспечивающий технические требования
Шерохова-тость Ra мкм
Технические требования
развёртывание черновое
допуск перпендикулярности
Таблица 6.2. – Последовательность выполнения операций при обработке детали
Содержание операции (обрабатываемые поверхности)
Оборудованиеоснастка
Горизонтально фрезерная
Фрезеровать торцы 1011
Вертикально сверлильная
Сверлить зенкеровать и развернуть предварительно отв. 1зенковать фаску 9
Сверлить отв. 3 зенковать фаски 5
Горизонтально фрезерный станок модели 6Р81Г
Технический контроль
Выбор технологических баз.
Операция 015- в качестве базы будут необработанные поверхности 12.Операция 020025035040 – база пов.12 Приспособления:тиски.
Вывод: В ходе практической работы изучили последовательность и методы проектирования маршрутов технологических процессов обработки деталей автомобиля на примере вилки выключения сцепления автомобиля Урал-4320-01.
ПРАКТИЧЕСКАЯ РАБОТА №7
РАСЧЕТ РЕЖИМОВ РЕЗАНИЯ
Цель работы: Освоить методики выбора режимов резания при обработке деталей на различном технологическом оборудовании.
) Выбор типа фрезы. Конфигурация обрабатываемой поверхности определяет тип применяемой фрезы. Ее размеры определяются размерами обрабатываемой поверхности и глубиной срезаемого слоя. Диаметр фрезы для сокращения основного технологического времени и расхода инструментального материала выбирают по возможности наименьшей величины учитывая при этом жесткость технологической системы схему резания форму и размеры обрабатываемой заготовки.
) Глубина фрезерования t и ширина фрезерования В – понятия связанные с размерами слоя заготовки срезаемого при фрезеровании. Во всех видах фрезерования за исключением торцового t определяет продолжительность контакта зуба фрезы с заготовкой измеренную в направлении перпендикулярном к оси фрезы. Ширина фрезерования В определяет длину лезвия зуба фрезы участвующую в резании измеренную в направлении параллельном оси фрезы. При торцовом фрезеровании эти понятия меняются местами.
) При фрезеровании различают подачу на один зуб (sz ммзуб) подачу на один оборот фрезы (s ммоб) и подачу минутную (sМ мммин) которые находятся в следующем соотношении
где n – частота вращения фрезы обмин;
z – число зубьев фрезы.
При черновом фрезеровании подача задается величиной sz ммзуб а при чистовом – s ммоб. Рекомендуемые значения подач приводятся в справочной литературе [2 с. 283 – 286].
) Скорость резания – окружная скорость фрезы ммин
Значения коэффициента Cv показателей степени и периода стойкости можно найти в таблицах [2 с.286 – 290].
) Сила резания. Главной составляющей силы резания при фрезеровании является окружная сила Н
где z – число зубьев фрезы;
n – частота вращения фрезы обмин.
Значения коэффициентов и показателей степени входящих в формулу определяются по таблицам [2 с. 291-292].
) Крутящий момент Н·м на шпинделе
где D – диаметр фрезы.
) Эффективная мощность резания N кВт.
) Основное время определяется по формуле
l2 – перебег фрезы в конце фрезерования мм. Длина перебега l2 определяется техническими нормами на выключение механизма подачи: в среднем l2 =1 2 мм.
Рассчитаем режимы резания для операции 040 горизонтально-фрезерная.
Рассматриваемая деталь представляет собой вилку предназначенную для управления включением и отключением механизма сцепления. Основные свойства приведены в практической работе №1. Заготовка получена литьем кокиль.
Инструмент: Фреза дисковая трёхсторонняя по ГОСТ 3755-78 (см. рис.7.1).
D=125мм B=8-28 d(H7)32 z=22.
Рисунок 7.1 – Фреза дисковая трёхсторонняя по ГОСТ 3755-78[3]
Станок 6Р81Г предназначен для выполнения разнообразных фрезерных работ цилиндрическими дисковыми фасонными торцевыми и пальцевыми фрезами.
Технические характеристики:
Размеры рабочей поверхности стола мм: 320х1250
Наибольший ход стола мм:
Расстояние от оси горизонтального шпинделя до рабочей поверхности стола мм: 30-400
Пределы частот вращения шпинделя обмин: 315-1600
продольных и поперечная 25-1250
вертикальная 83-4166
Мощность электродвигателя главного движения кВт 75
Габариты (мм) — 2260х1745х1660
Расчет режимов резания
Принимаем глубину резания B=3 мм.
Период стойкости инструмента 80 мин.
Подача задается величиной sz=015 ммзуб.
Скорость резания – окружная скорость фрезы ммин:
=(3540125045) 025(1300.332903015042201)=04
Частота вращения фрезы n обмин:
=(1000794)(314125)=1
Минутная подача sМ мммин:
Основное время определяется по формуле мин:
Сила резания. Главной составляющей силы резания при фрезеровании является окружная сила Н
=(106822903 01504 31 22) 13(125021600)=287572
Крутящий момент Н·м на шпинделе
=(2875720125)(2100)=18
Эффективная мощность резания N кВт:
.=(28757204)(1020*60)=019
Таблица 7. 1 – Сводные данные по режимам резания
Наименование операцииперехода позиции
Глубина резания t мм
Период стойкости Т TТмин
Частота вращения шпинделя n обмин
Скорость резания v ммин
Скорость подачи sM мммин
Основное время To мин
Вывод: Рассчитали режимы резания при обработке детали на горизонтально-фрезерном станке.
ПРАКТИЧЕСКАЯ РАБОТА № 8
НОРМИРОВАНИЕ ТЕХНОЛОГИЧЕСКОЙ ОПЕРАЦИИ
Цель работы: закрепить на практике теоретические знания по техническому нормированию; изучить структуру нормы времени методы и порядок определения норм времени; рассчитать норму времени на технологические операции обработки детали на металлорежущих станках.
Технологическая операция как составная часть технологического процесса в свою очередь состоит из большого числа элементов (переходов позиций и др.). Все эти элементы связаны между собой как логическими так и физическими (пространственными временными материальными) связями. Цель нормирования – установление технически обоснованной нормы времени на операцию анализ уменьшения времени на операцию и соответственно повышения эффективности производства.
Под техническим нормированием понимают установление нормы времени на выполнение определенной работы или нормы выработки в штуках в единицу времени. Величина затрат времени на изготовление той или иной продукции при надлежащем качестве ее является одним из основных критериев для оценки совершенства технологического процесса планирования в цехе и на предприятии расчета с производственными рабочими. В машиностроении норма времени обычно устанавливается на технологическую операцию.
Техническая норма времени – регламентированное время выполнения данной операции при определенных организационно – технических условиях и наиболее эффективном использовании всех средств производства.
Существует три метода нормирования:
) Метод аналитического расчета норм времени с использованием нормативов. При этом методе технологическая операция разлагается на элементы; каждый из элементов подвергается анализу с целью исключения лишних непроизводственных действий сокращение пути всех движений рук ног и корпуса рабочего и т. д. Определяются элементы операции перекрываемые другими элементами. Затем для неперекрываемых элементов производится расчет их длительности по формулам или точным нормативам. Данный метод применяется в массовом крупносерийном и среднесерийном производстве.
) Опытно – статистический метод нормирования. При этом методе норма времени устанавливается на всю операцию в целом путем сравнения с типовыми нормами и фактической трудоемкостью выполнения в прошлом аналогичной работы. Для данного метода разработаны укрупненные нормы времени на типовые операции. Данный метод применяется в единичном и мелкосерийном производстве.
) Метод определения норм времени на основе изучения затрат рабочего времени наблюдения (хронометраж фотография рабочего дня). Данный метод производится непосредственно на рабочем месте и предназначен для изучения и обобщения передовых приемов труда а также для разработки нормативов используемых при первом методе.
Метод аналитического расчета технической нормы времени
В результате расчетов определяется норма штучно – калькуляционного времени на технологическую операцию:
где – штучное время мин;
– подготовительно-заключительное время на партию деталей мин;
N – партия запуска шт.
Подготовительно-заключительное время затрачивается на подготовку рабочих и средств производства к выполнению технологической операции и приведение их в первоначальное состояние после ее окончания. Подготовительно – заключительное время включает в себя:
время на ознакомление рабочего с работой чертежом технологической документацией изучение инструктажа;
время на получение материалов инструментов приспособлений наладку оборудования;
время на пробную обработку деталей (на станках с автоматическим циклом);
время на снятие инструментов и приспособлений по окончании обработки партии деталей;
время на сдачу готовой продукции инструментов приспособлений документации.
Подготовительно-заключительное время затрачивается один раз на всю партию n обрабатываемых изделий и не зависит от числа изделий в партии. Норму подготовительно-заключительного времени определяют по нормативам.
В условиях массового и крупносерийного производства подготовку рабочего места производят до начала работ наладчики и вспомогательные рабочие поэтому подготовительно-заключительное время в норму времени станочника не входит то есть для данных типов производства:
Штучное время – это время изготовления одного изделия на данной технологической операции. Норма штучного времени при техническом нормировании определяется по формуле
где – основное время на
k – число перекрываемых основных переходов в операции шт;
– вспомогательное время на j-тый переход мин;
m– число неперекрываемых переходов в операции на которые затрачивается вспомогательное время шт;
– время облуживания рабочего места мин;
– время на личные потребности рабочего мин.
В норму штучного времени не включается затраты времени на работы перекрываемые другими работами (например при параллельной обработке поверхностей несколькими инструментами в расчетах учитывается время на самый длительный переход) или временем автоматической работы оборудования (например автоматический контроль в процессе обработки).
Основное (машинное технологическое) время определяется по формуле (для точения):
где – длина обрабатываемой поверхности с недобегом и перебегом мм;
– частота вращения шпинделя мин-1;
– подача инструмента ммоб.
Если процесс управления станком осуществляется рабочим вручную то данное время будет машинно-ручным; если процесс совершается автоматически без непосредственного участия человека – машинно-автоматическим.
В основное время входит:
время на врезание и перебег режущего инструмента;
время на непосредственное воздействие на обрабатываемую поверхность;
время на обратный ход (для протяжных резьбонарезных и других станков);
время на проход инструмента при снятии пробных стружек.
Формулы для определения основного времени при различных видах работ приведены в литературе; величины врезаний перебегов проходов при пробных стружках – в нормативах.
Вспомогательное время – часть штучного времени затрачиваемая на выполнение приемов необходимых для обеспечения изменения и последующего определения состояния предметов труда. Во вспомогательное время входит:
время на установку и снятие заготовки в приспособлении;
время управления станком (пуск остановка смена режимов обработки и т. п.);
время на перемещения инструмента;
время на приемы измерения детали.
Вспомогательное время может быть ручным машинным или машинно–ручным.
Составляющие вспомогательного времени определяются по нормативам.
Сумма основного и вспомогательного времени на операцию называется оперативным временем:
Время обслуживания рабочего места – часть штучного времени затрачиваемая исполнителем на поддержание средств технического оснащения в работоспособном состоянии и уход за ними и рабочим местом. Время обслуживания рабочего места подразделяется на время технического обслуживания и время организационного обслуживания .
Время технического обслуживания рабочего места . затрачивается рабочим на уход за рабочим местом в течение смены и включает:
время на смену затупившегося инструмента;
время на правку инструмента в процессе работы;
время на удаление стружки в процессе работы.
Время технического обслуживания рабочего места определяется по специальным формулам; время организационного обслуживания рабочего места определяется по нормативам в процентах от оперативного времени.
В серийном производстве определяется суммарное время обслуживания рабочего места по нормативам в процентах от оперативного времени.
Время на личные потребности Тотд. – часть штучного времени затрачиваемая человеком на личные потребности и при утомительных работах на дополнительный отдых. Оно определяется по нормативам в процентах от оперативного времени.
Величина партии запуска определяется по формуле
где – число операций в технологическом процессе шт;
К – коэффициент (К=10 для мелкосерийного производства К=20 для среднесерийного производства К=30 для крупносерийного производства).
Норма выработки – регламентированное количество изделий которое должно быть обработано в заданную единицу времени. Например норма выработки в час определяется по формуле
Для операции рассмотренной в практической работе №7 рассчитаем штучное время.
Таблица 8.1 – Нормирование технологических операций
Наименование операции и её элементы
Составляющие штучного времени
5 Установить и закрепить заготовку в приспособлении
0 Подвести инструмент к детали включить подачу
5 Фрезеровать плоскости 67 набором фрез
Вывод: В данной практической работе нами была пронормирована фрезерная операция обработки пов. 67; изучили структуру нормы времени методы и порядок определения норм времени; рассчитали норму времени на технологические операции обработки вилки сцепления автомобиля Урал 4320-01 на горизонтально-фрезерном станке.
Автомобили Урал моделей 4320-01 5507: Устройство и техническое обслуживание С.Л. Антонов В.А. Трофимов А.И. Штурюкин и др. - М.: Транспорт 1994 - 245 с.ил.табл.
КамАЗ Руководство по ремонту и техническому обслуживанию. Издательство "Ливр" 2000г 240с.илл.
Справочник технолога-машиностроителя. В 2-х т. Т. 2 Под ред. А.Г.Косиловой и Р.К.Мещерякова. – 4-е изд. перераб. и доп. – М.: Машиностроение 1985. – 496 с.: ил.
Панов А.А. Обработка металлов резанием: Справочник технолога.А.А. Панов В.В. Аникин; Под общ. ред. А.А.Панова. – М.: Машиностроение 1988. – 450 с.
Методические указания к выполнению практических работы по дисциплине «Основы технологии производства автомобилей» для студентов специальности 6.09.0258 «Автомобили и автомобильное хозяйство» дневной и заочной форм обучения. Часть I II. Сост. П.К. Сопин Л.А. Кияшко. – Севастополь: Изд-во СевНТУ 2007. – 44 с.
Приложение А сборочный чертеж
Приложение Б Вилка переключения передач
Приложение В Схема сборки механизма сцепления
Пост диагностики сцепления.cdw

Шкаф управления тяговым стендо
Стеллаж с комплектом СТД
Устройство для ствола отработавших газов
ОТДА 2012.054.00.РГЗ
Рекомендуемые чертежи
- 04.05.2019