Оптимизация критериев процесса механической обработки детали Шпиндель



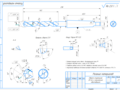
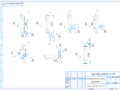
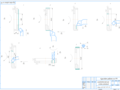
- Добавлен: 24.01.2023
- Размер: 353 KB
- Закачек: 0
Узнать, как скачать этот материал
Подписаться на ежедневные обновления каталога:
Описание
Оптимизация критериев процесса механической обработки детали Шпиндель
Состав проекта
![]() |
![]() |
![]() ![]() ![]() ![]() |
![]() ![]() ![]() ![]() |
![]() ![]() ![]() |
![]() ![]() ![]() ![]() |
![]() |
![]() |
Дополнительная информация
Контент чертежей
Чертеж.cdw

СВЕРЛО.cdw

кинематика Чертеж.cdw

Рекомендуемые чертежи
- 24.01.2023
- 24.01.2023
- 05.01.2022
- 28.05.2016
Свободное скачивание на сегодня
Обновление через: 9 часов 33 минуты