Нормирование точности типовых элементов деталей машин





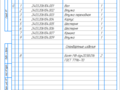
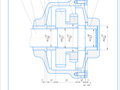
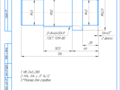
- Добавлен: 24.01.2023
- Размер: 252 KB
- Закачек: 0
Описание
Состав проекта
![]() |
![]() |
![]() ![]() ![]() ![]() |
![]() ![]() ![]() ![]() |
![]() ![]() ![]() ![]() |
![]() ![]() ![]() |
![]() ![]() ![]() ![]() |
Дополнительная информация
Сборочный чертеж.cdw

Спецификация.cdw

Рабочий чертеж.cdw

Пояснительная записка.doc
1 Расчет среднего давления 7
2 Расчет толщины масляного слоя 8
3 Расчет наименьшего функционального зазора 8
4 Проверка выбранной посадки 9
5 Расчет наименьшей толщины масляного слоя при Smin 10
6 Расчет запаса прочности по толщине масляного слоя при Smin 10
7 Расчет наибольшого функционального зазора 11
8 Определение коэффициента нагруженности 11
9 Расчет наименьшей толщины масляного слоя при SmaxF 11
10 Расчет запаса надежности по толщине масляного слоя
11 Схема расположения полей допусков 12
Расчет и подбор гладкого калибра для вала 13
2 Контрольные размеры калибра 13
3 Допуски и отклонения калибра 13
4 Предельные размеры калибра 14
5 Схема расположения допусков калибра 16
Расчет резьбового соединения 17
1 Определение основных параметров резьбы 17
2 Выбор характера соединения 17
3 Выбор класса точности посадки 17
4 Схема полей допусков 19
5 Определение предельных размеров 19
Выбор контрольных параметров зубчатого колеса 22
1 Определение контрольных параметров 22
2 Числовые значения контрольных параметров 23
3 Средства контроля параметров 24
Список использованной литературы 25
РАСЧЁТ ПОСАДОК ДЛЯ ГЛАДКИХ ЦИЛИНДРИЧЕСКИХ СОЕДИНЕНИЙ С ЗАЗОРОМ
Диаметр вала D = 45мм; длина соединения число оборотов n= =1500 обмин; радиальная нагрузка Fr= 800 Н; смазка — масло индустриальное 20.
Для обеспечения наибольшей долговечности изделий ответственные соединения с зазором должны работать в условиях жидкостного трения. Установлено что жидкостное трение создается лишь в определенном диапазоне диаметральных зазоров ограниченном наименьшим SminF наибольшим SmaxF функциональными зазорами. [5 с.212]
Существующий метод расчета посадок с зазором сводится к определению наименьшего функционального зазора SminF при котором обеспечивается жидкостное трение и наибольшего функционального зазора SmaxF при котором еще сохранилось жидкостное трение и работоспособность подшипника.
1 Расчет среднего давления
Среднее давление P Нм2 для определения предельных функциональных зазоров SminF и SmaxF находим по формуле:
где Fr – радиальная нагрузка Н;
d – диаметр посадочной поверхности мм.
2 Расчет толщины масляного слоя
Толщину масляного слоя hж.т. мкм при котором обеспечивается жидкостное трение находим по формуле:
где Кжт– коэффициент запаса надежности по толщине масляного слоя (Кжт ≥ 2);
Rz1 и Rz2 – высоты неровностей вкладыша подшипника и цапфы вала которые после приработки соответственно равны 1-3 и 1-4 мкм;
g - добавка учитывающая отклонение нагрузки скорости температуры от расчётных и других неучтенных факторов находится в пределах 2-3 мкм.
Принимаем Кжт = 2; Rz1 = 1 мкм; Rz2 = 1 мкм; g = 2 мкм.
3 Расчет наименьшего функционального зазора
Определяем величину наименьшего функционального зазора SminF мкм при котором обеспечивается жидкостное трение по формуле:
где k и m - коэффициенты постоянные для заданного значения
- динамическая вязкость смазки Па·С;
– угловая скорость радс.
Для наименьшего зазора принимается tpаб = 70°С. Значение динамической вязкости масла при температуре 50°С 50 = 0016 Па·С [3 с.11].
Для других значений температуры динамическая вязкость масла t Па·С определяется по формуле:
где t – фактическая температура масла;
n – показатель степени зависящий от кинематической вязкости масла [5 с 12];
По таблице 17 [5] по величине SminF подбираем ближайшую посадку H7e8. Ближайшая по ГОСТ 25346-89 посадка 45 H7e8 с Smin= 50 мкм.
4 Проверка выбранной посадки
Производим проверку выбранной посадки на наличие жидкостного трения при наименьшем стандартном зазоре SminF.
Подсчитываем коэффицент нагруженности подшипника CR по формуле:
где - относительный зазор равный Smind (Smin- наименьший зазор посадки
выбранной по стандарту).
По таблице 2 [3 с.10] находим величину относительного эксцентриситета в зависимости от значений ld и CR. При этом должно выполняться условие ≥04. При ≤04 существует зона неустойчивой работы соединения. По таблице 2 при ld = 08 и CR = 049 величина относительного эксцентриситета = 045 >04. Следовательно режим работы устойчивый.
Окончательно принимаем для гладкого цилиндрического соединения согласно ГОСТ 25346-89 посадка 45 H7e8 с Smin = 50 мкм и Sma x= 114 мкм.
5 Расчет наименьшей толщины масляного слоя при Smin
Находим наименьшую толщину масляного слоя hmin мкм при Smin по формуле:
6 Расчет запаса прочности по толщине масляного слоя при Smin
Определяем запас надежности по толщине масляного слоя kж.т. по формуле:
Расчет показывает что посадка по наименьшему зазору выбрана правильно так как при Smin = 50 мкм обеспечивается жидкостное трение и создается запас на-
дежности по толщине масляного слоя. Следовательно Smin можно принять за SminF.
7 Расчет наибольшого функционального зазора
Подсчитываем величину наибольшего зазора SmaxF мкм при котором еще сохранится жидкостное трение и работоспособность подшипника:
Для наибольшего зазора принимается tраб=50°С и 2 = 0016 ПаС [3 с.11] тогда:
8 Определение коэффициента нагруженности
Определяем коэффициент нагруженности подшипника по уравнению (1.6):
По таблице 2 [3 с. 10] при ld = 08 и CR = 127 величина относительного эксцентриситета =068.
9 Расчет наименьшей толщины масляного слоя при SmaxF
Подсчитываем наименьшую толщину масляного слоя по уравнению (1.7):
10 Расчет запаса надежности по толщине масляного слоя при SmaxF
Определяем запас надежности по толщине масляного слоя из (1.8):
Таким образом при SmaxF = 369 мкм обеспечивается жидкостное трение.
11 Схема расположения полей допусков посадки с зазором
Рисунок 1 – Схема расположения полей допусков посадки с зазором
РАСЧЕТ И ПОДБОР ГЛАДКОГО КАЛИБРА ДЛЯ ВАЛА
Калибр для вала 45е8.
Для вала с номинальным диаметром 45 мм выбираем калибр-скобу.
2Контрольные размеры калибра
Согласно ГОСТ 3325-55 приняли посадки на вал: .
Наибольший предельный размер вала dmax мм определяем по формуле:
где es – наибольшее предельное отклонение вала мм;
dmax= 45 - 005 = 4495 мм.
Наименьший предельный размер вала Dmin мм определяем по формуле:
dmin= 45 – 0089 = 44911 мм.
3Допуски и отклонения калибра
Согласно ГОСТ 24853-81 для расчета гладких калибров для размеров до
0 мм принимаем следующие значения (для 8-го квалитета):
Для расчета приняли: d = 45 мм dmin = 44911 мм dmax = 4495 мм.
4Предельные размеры калибра
Проходной максимальный размер рабочего калибра определяем по формуле:
Проходной минимальный размер рабочего калибра определяем по формуле:
Проходную изношенную сторону рабочего калибра определяем по формуле:
Непроходной максимальный размер рабочего калибра определяем по формуле:
Непроходной минимальный размер рабочего калибра определяем по формуле:
Проходной максимальный размер контрольного калибра определяем по формуле
Проходной минимальный размер контрольного калибра определяем по формуле
Проходную изношенную максимальную сторону контрольного калибра определяем по формуле
Проходную изношенную минимальную сторону контрольного калибра определяем по формуле
Непроходной максимальный размер контрольного калибра определяем по формуле
Непроходной минимальный размер контрольного калибра определяем по формуле
5 Схема расположения полей допусков калибра
Построим схему расположения полей допусков калибра для контроля деталей.
Рисунок 2 – Схема расположения полей допусков калибра для контроля деталей
Согласно ГОСТ 16775-93 для калтбра-скобы приняли следующие значения: D = 45 мм D1 = 120 мм Н = 100 мм В = 17 мм S = 5 мм l = 25 мм h = 44 мм.
РАСЧЕТ РЕЗЬБОВОГО СОЕДИНЕНИЯ
1 Определение основных параметров резьбы
Резьбовое соединение болта и корпуса. Резьба метрическая с диаметром d = 8 мм и шагом p = 15 мм. Данное сопряжение предназначено для закрепления крышки (позиция 7) к корпусу (позиция 4).
По ГОСТ 9150-81 установим следующие параметры резьбы:
- наружный диаметр резьбы D(d) = 8 мм;
- внутренний диаметр резьбы D1(d1) = 6376 мм;
- средний диаметр резьбы D2(d2) = 7026 мм;
- угол профиля резьбы α = 600;
- высота исходного треугольника резьбы H = 1299 мм.
2 Выбор характера соединения
Исходя из условий работы резьбового сопряжения и выполняемой функции а именно резьбовое соединение крепит крышку к корпусу приняли что данное соединение является переходным.
3 Выбор класса точности посадки
Эксплуатационные требования к резьбам зависят от их назначения. Требования надежности долговечности и свинчиваемости без подгонки независимо от изготовленных резьбовых деталей при сохранении эксплуатационных качеств соединений являются общими для всех резьб.
В заданном узле на резьбовое сопряжение не установлено дополнительных
требований по точности поэтому назначаем средний класс точности.
По ГОСТ 16093-81 приняли предельное отклонение диаметров внутренней и наружной резьбы (в мм) для М8×15 6H6g (длина свинчивания нормальная – N) и занесли в таблицу 1.
Таблица 1 – Численные значения полей допусков для посадки 6H6g.
4 Схема полей допусков резьбового соединения
Рисунок 3 – Схема полей допусков резьбового соединения М8×15 6H6g.
5 Определение предельных размеров наружной и внутренней резьбы
Вычислим предельные значения диаметров наружной и внутренней резьбы и занесем их в таблицу 2:
Для наружной резьбы:
Максимальный диаметр наружней резьбы определяем по формуле
Минимальный диаметр наружней резьбы определяем по формуле
Максимальный диаметр средней резьбы определяем по формуле
d2max = d2 + es (3.3)
Минимальный диаметр средней резьбы определяем по формуле
d2min = d2 + ei (3.4)
Максимальный диаметр внутренней резьбы определяем по формуле
d1max = d1 + es (3.5)
Минимальный диаметр внутренней резьбы не назначаем
Для внутренней резьбы:
Максимальный диаметр наружней резьбы не назначаем;
D2max = D2 + ES (3.7)
D2min = D2 + EI (3.8)
D1max = D1 + ES (3.9)
Минимальный диаметр внутренней резьбы определяем по формуле
D1min = D1 + EI (3.10)
D1min = 6376 + 0 = 6376 мм.
Таблица 2 - Численные значения предельных размеров для посадки 6H6g.
Численное значение мм
ВЫБОР КОНТРОЛЬНЫХ ПАРАМЕТРОВ ЗУБЧАТОГО КОЛЕСА
Исходные данные: зубчатое колесо с модулем m = 35; число зубьев z = 48; делительный диаметр d = 168 мм; диаметр окружности вершин da= 175 мм; диаметр окружности впадин df = 161 мм.
1 Определение контрольных параметров.
Допуски цилиндрических зубчатых передач нормируются ГОСТ 1643-81 и распространяются на эвольвентные цилиндрические зубчатые передачи внешнего и внутреннего зацепления с прямозубыми косозубыми и шевронными зубчатыми колесами с делительным диаметром до 6300 мм. шириной венца или полушеврона до 1250 мм с модулем зубьев от 1 до 56 мм.
Наиболее широко распространены колеса 6-9-й степеней точности. Для каждой степеней точности зубчатых колес и передач устанавливаются три нормы точности: кинематическая плавности работы и контакта зубьев.
Для зубчатых колес работающих при повышенных скоростях и умеренных нагрузках или наоборот для колес подачи в станках где требуется согласованность движений приняли степень точности 7. Для зубчатого колеса приняли все три контрольных параметра.
Плавность работы колеса - величина составляющих полной погрешности угла поворота зубчатого колеса многократно повторяющихся за оборот колеса.
Контакт зубьев - точность выполнения относительных размеров пятна контакта сопряженных зубьев колес в передаче.
Кинематическая погрешность - погрешность угла поворота зубчатого колеса за оборот.
По ГОСТ 1643-81 приняли: 7 -С - цилиндрическая передача со степенью
точности 7 по всем трем нормам с видом сопряжения зубчатых колес С и соответсвием между видом сопряжения и видом допуска на боковой зазор (вид допуска с) а также между видом сопряжения и классом отклонений межосевого расстояния.
2 Числовые значения контрольных параметров.
Таблица 3 – Числовые значения контрольных параметров.
Нормы кинематической точности
Допуск на радиальное биение зубчатого венца
Допуск на колебание длины общей нормали
Допуск на погрешность обката
Допуск на колебание измерительного межосевого расстояния
Нормы плавности работы
Допуск на местную кинематическуцю погрешность
Предельное отклонение шага
Предельное отклонение шага зацепления
Допуск на погрешность профиля зуба
Допуск на колебание измерительного межосевого расстояния на одном зубе
Нормы контакта зубьев
Допуск на накопленную погрешность k шагов
Допуск на направления зуба
Допуск параллельности осей
Допуск на перекос осей
Нормы бокового зазора
Наименьшее дополнительное смещение исходного контура
Отклонение средней длины общей нормали
Продолжение таблицы 3.
Наименьшее отклонение толщины зуба
Отклнение средней длины общей нормали
Допуск на среднюю длину общей нормали
Допуск на толщину зуба
3 Средства контроля параметров
Таблица 4 – Средства контроля параметров зубчатых колес
Контролируемый размер
Контроль норм плавности работы колес
Контроль разности окружных шагов
Контроль осевого шага
Контроль норм контакта зубьев в передаче
Контроль пятна контакта
Контрольно-обкатные станки
Контроль контактной линии
Контроль норм кинематической точности
Контроль кинематической погрешности
Прибор контроля кинематической погрешности
Контроль длины общей нормали
Микрометрический нормалемер
Контроль норм бокового зазора
Контроль межцентрового расстояния
Контроль бокового зазора
Взаимозаменяемость стандартизация и технические измерения: Учебное пособие для машиностроительных специальностей вузов А.Д. Никифоров. – 2-е изд. стер. – М.: Высшая школа 2002. – 510 с
Метрология стандартизация (взаимозаменяемость): Учебное пособие по выполнению расчетно-графической работы Н.С.Буткин Р.М. Янбухтин. – Уфа УГАТУ 2004 г. – 40 с.
Метрология стандартизация и сертификация. Взаимозаменяемость: Учебное пособие Р.М. Янбухтин В.М. Кишуров Э.В.СафинЛ.Н.Кубышко Г.А.Панова. – Уфа УГАТУ 2004. – 120 с.
В.И. Анурьев Справочник конструктора-машиностроителя: В 3-х т. Т2. – 5-е изд. перераб. и доп. – М.: Машиностроение 1980. – 559с.
А.И. Якушев и др. Взаимозаменяемость стандартизация и технические измерения: Учебник для втузовА.И.Якушев Л.Н.ВоронцовН.М.Федоров. – 6-е изд. перераб. И дополнит. – М.:Машиностроение 1987. – 352 с.: ил.
Калибр-скоба.cdw

или стали 5 ГОСТ 380-94.
Заготовки твердосплавных пластинок по ГОСТ 21125-75.
паять на корпус медью М3 ГОСТ 859-2001
или латунью Л68 ГОСТ 15567-70.
Острые кромки измерительных поверхностей поз.1 и 2
Покрытие нерабочей поверхности покрыть молотковой эмалью
МЛ-165 ГОСТ 12034-77.
Рекомендуемые чертежи
- 24.01.2023