Нормирование точностных параметров типовых соединений деталей сборочной единицы



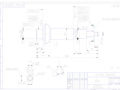
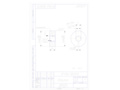
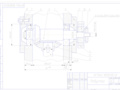
- Добавлен: 25.10.2022
- Размер: 2 MB
- Закачек: 0
Описание
Состав проекта
![]() |
![]() ![]() ![]() |
![]() ![]() ![]() |
![]() ![]() ![]() |
![]() ![]() ![]() |
![]() ![]() ![]() ![]() |
![]() ![]() ![]() ![]() |
![]() ![]() ![]() |
![]() ![]() ![]() ![]() |
Дополнительная информация
Чертеж Узел.cdw

Чертеж втулка.cdw

МСиС КР ПЗ.docx
Расчет и выбор посадок подшипников качения6
Анализ и расчет цилиндрического соединения.10
Анализ и расчет точностных характеристик шпоночного соединения.12
Анализ и расчет цилиндрического соединения деталей 8 и 9 с корпусом 6.13
Выбор и анализ посадок элементов шлицевого соединения15
Расчет резьбового соединения17
Выбор значений шероховатости допусков формы и расположения элементов деталей20
Выбор средств измерения деталей 11 и 12.22
Расчет размерной цепи23
1 Метод полной взаимозаменяемости.23
2 Вероятностный метод25
Однократное измерение27
Переход России к рыночной экономике обусловил более высокие требования в отношении качества изделий уровень которого в основном определяет их конкурентоспособность на внутреннем и международном рынках.
Качественные показатели современных изделий приборостроения и машиностроения в значительной степени зависят от требуемой точности изготовления соответствия требуемым параметрам и характеристикам их отдельных составных частей: элементов деталей узлов.
Конструкторская и технологическая документации обычно представляют
собой чертежи и технологические карты на которых дается изображение деталей и сборочных единиц с целым рядом указаний к процессу обработки или сборки. Большинство из этих указаний направлены на ограничение погрешностей возникающих при обработке или сборке деталей. Причин возникновения погрешностей много: неточность оборудования приспособлений инструментов; неоднородность заготовок для деталей по размерам форме твердости механическим свойствам; неточности установки и закрепления заготовок в приспособлениях; влияние температуры; упругие деформации деталей оборудования приспособлений режущих инструментов и обрабатываемых изделий; несоблюдение установленных режимов обработки (скоростей подач глубин резания и др.); вибрации фундамента на котором установлено оборудование и т.д.
Учесть все погрешности практически невозможно. Поэтому проблема правильного и обоснованного нормирования точности параметров кинематических пар и цепей является особенно актуальной.
Всякое необоснованное назначение допусков приводит к удорожанию производства. Например излишнее ужесточение допусков вызывает потребность в более точном оборудовании оснастке и приводит к увеличению длительности изготовления деталей; чрезмерное расширение допусков ведет к большому количеству пригоночных и доделочных работ по сборке что увеличивает трудоемкость и себестоимость изготовления изделий.
В процессе конструирования изделий необходим всесторонний анализ влияния входных точностных параметров изделия на его функциональные характеристики с учетом технико-экономических показателей так как точность выходного параметра механизма прибора или машины определяется точностью изготовления и сборки отдельных его звеньев.
Принцип действия сборочной единицы
В собранном изделии отдельные детали взаимосвязаны и взаимозависимы.
Отклонения размеров формы и расположения осей или поверхностей одной какой-либо из деталей вызывают отклонения размеров или формы в сборочной единице. Последние суммируясь оказывают влияние на качественные характеристики изделия (точность работоспособность надежность и др.).
По этой причине при выборе посадок допусков размеров деталей допусков формы и расположения поверхностей следует учитывать:
) назначение изделия и условия его работы;
) назначение детали в сборочной единице и требования предъявляемые к ней;
) роль отдельных поверхностей деталей;
) влияние отклонений размеров формы и расположения шероховатости поверхностей на функционирование кинематической пары и размерной цепи;
) влияние суммы отклонений точностных параметров всех деталей на качественные показатели изделия (точность плавность вращения; бесшумность долговечность работы);
) экономические факторы при производстве и эксплуатации изделий.
Одной из основных задач которые решаются при проектировании изделия является определение необходимой точности размеров формы (расположения) поверхностей деталей и взаимного расположения отдельных частей изделия обеспечивающих требуемую точность и длительность его функционирования а также заданные экономические показатели.
При конструировании очень важно правильно выбрать соответствующие допуски сопрягаемых размеров определяемые назначенными квалитетами поскольку последние определяют и качественные и экономические показатели изделий.
При выборе квалитета необходимо учитывать ряд общих положений.
) Технико-экономические факторы.
) Технологические возможности достижения намеченной точности.
) Средний уровень точности гарантирующий работоспособность продукции.
) Возможность контроля намеченной точности размеров изготовленных
) Наличие соответствующих посадок и их видов.
При выборе квалитетов часто используют опыт проектирования и эксплуатации аналогичных изделий на основе которого можно сформулировать следующие рекомендации:
- 4-й и 5-й квалитеты применяются сравнительно редко в основном в особо точных соединениях требующих высокой однородности зазора или натяга.
- 6-й и 7-й квалитеты используются для ответственных соединений в механизмах.
- 8-й и 9-й квалитеты применяются для посадок обеспечивающих выполнение деталями определенных служебных функций (передачу усилий перемещение и др.) при относительно невысоких требованиях.
Основными характеристиками посадок являются наименьшие натяги и зазоры и их допуски.
Для подбора посадок применяются методы: прецедентов подобия и расчетный. Метод прецедентов заключается в том что конструктор отыскивает в однотипных или других машинах находящихся в эксплуатации случаи применения сборочной единицы подобной проектируемой и назначает такие же или аналогичные допуск и посадку.
Расчет и выбор посадок подшипников качения
1. Определение номинальных размеров конструктивных элементов заданного подшипника:
d = 30мм; D = 72мм; В=19мм; r = 2мм.
2. Определение вида нагружения колец подшипника.
Внутреннее кольцо подшипника вращается вместе с валом следовательно оно испытывает циркуляционную нагрузку для этого кольца принимаем посадку с натягом. Внешнее кольцо подшипника находится в неподвижном состоянии в корпусе соответственно для него принимаем свободную посадку.
3. Выбор полей допусков колец подшипника.
Исходя из того что применяется подшипник 306 класса точности 0 принимаем для внутреннего и наружного колец подшипника поля допусков и соответственно.
4. Назначение поле допуска поверхности детали сопрягаемой с местнонагруженным кольцом.
Исходя из того что используется подшипник класса точности 0 исходя из рекомендаций и применяя таблицу Е.2 [1] принимаем для внешнего кольца подшипника поле допуска .
5. Рассчет интенсивности радиальной нагрузки циркуляционно нагруженного кольца.
Рассчет интенсивности радиальной нагрузки циркуляционно нагруженного кольца производится по формуле:
где R - радиальная реакция опоры на подшипник Н;
b- рабочая ширина посадочного места м
где В - ширина подшипника м;
r - ширина фаски кольца подшипника м;
к] - динамический коэффициент посадки зависит от характера нагрузки;
к2 - коэффициент учитывающий степень ослабления посадочного
натяга при полом вале или тонкостенном корпусе;
к3 - коэффициент неравномерности распределения радиальной
PR = *1*1*1.4 =9333 kHм.
6. Выбор полей допусков детали сопрягаемой с циркуляционно нагруженным кольцом.
Определив интенсивность радиальной нагрузки циркуляционно нагруженного кольца применяя таблицу Е.4 [1] выбираем рекомендуемую посадку внутреннего кольца подшипника для данного вида нагружения.
Принимаем для внутреннего кольца подшипника поле допуска .
7. Определить точностные характеристики сопрягаемых деталей: предельные отклонения допуски предельные размеры.
8. Определить точностные характеристики сопряжений: предельные зазоры натяги допуск посадки.
Предельные зазоры натяги определяются по формулам:
Smax=Dmax(ES) –dmin(ei)
Smin=Dmin(EI) –dmax(es)
Nmax=dmax(es) –Dmin(EI)
Nmin=dmin(ei) –Dmax(ES)
Nmin=0+0.002=0.002мм
Nmax=0.015+0.01=0.025мм
Nср=0.5*(0002+0025)=0.0135мм
Smax=0-(-0.043)=0.043мм
Sср=0.5*0.043=0.0215 мм
9. Расчет допускаемого натяга.
Для проверки правильности выбранных допусков производим проверочный расчет максимального натяга по формуле:
где [Р] - допустимое напряжение на растяжение Нм2
d или D - диаметр соответствующего кольца подшипника м;
к - коэффициент принимаемый для подшипников средней серии равным 2.3 легкой серии - 2.8 тяжелой - 2.0.
Условие проверки выполняется.
10. Cхемы полей допусков соединений:
) вал - внутреннее кольцо:
)отверстие корпуса - наружное кольцо подшипника:
Анализ и расчет цилиндрического соединения.
Вал 11 и зубчатое колесо 12.
Вал предназначен для поддержания сидящих на нём деталей и передачи вращающегося момента. Зубчатые колёса используются с целью преобразования вращающего момента и числа оборотов валов на входе и выходе.
В данном соединении передача крутящего момента и числа оборотов с колеса на вал производится за счет применяемой в соединении шпонки которая так же обеспечивает взаимную неподвижность деталей.
При выборе посадки руководствуемся следующими условиями:
вал является выходным и передает большие крутящие моменты;
применение конусных зубчатых колес требующих точной фиксации и минимальных осевых смещений деталей;
использование шпонки передающей крутящий момент;
Разборка узла предусмотрена только в случае монтажа или ремонта.
Исходя из данных требований выбираем переходную посадку H7n6 (типа глухой) которая дает наиболее прочные соединения и в то же время позволяет разбирать узел.
Соответственно применяем для вала поле допуска а для колеса .
Для данной посадки рассчитываем максимальный зазор и натяг по формулам:
Smax=0021 – 0015=0006 мм
Nmax=0022 – 0 = 0022 мм
Строим поля допусков:
Втулка 10 и зубчатое колесо 4.
Основная задача зубчатого колеса – передача крутящего момента поэтому для надлежащей работы узла для данного соединения применима посадка с натягом исходя из рекомендаций [1] принимаем для соединение поле допуска H8u8.
Nmax=0.133 –0=0.133мм
Nmin=0087 –0046=0041мм
Nср=0.5(0041+ 0133)= 0087мм
Анализ и расчет точностных характеристик шпоночного соединения.
Посадки элементов шпоночных соединений зависят от выбора способа центрирования сопрягаемых поверхностей. Выбор способа центрирования обуславливается требованиями предъявляемыми к конструкции механизма и технологическим возможностям.
В соединении данного механизма к которому предъявляются высокие требования по кинематической точности неподвижности соединения и отсутствие реверсивного движения назначим центрирование по D. Оно рекомендуется когда втулку можно обработать чистовой протяжкой до требуемых размеров а вал фрезеровать с последующей шлифовкой до окончательного размера по центрирующей поверхности D.
Ввиду того что в данном соединении требуется обеспечение высокой кинематической точности сопрягаемых деталей и передача высокого крутящего момента принимаем для данного соединения нормальную посадку шпонки.
Принимаем для соединения переходную посадку P9h9 и соответственно поля допусков для шпон – паза вала и колеса а для шпонки .
Рассчитываем для данной посадки максимальный натяг и зазор и строим поля допусков:
Smax=0022 – (-0043) = 0021 мм
Nmax=0–(- 0074)=0074 мм
Анализ и расчет цилиндрического соединения деталей 8 и 9 с корпусом 6.
Для легкости сборки крышки с корпусом рекомендуются посадка с зазором невысокой точности. Для унифицированных в ряде отраслей крышек подшипников рекомендованы поля допусков предпочтительного применения: d11 - для глухих крышек и d9 - для крышек с отверстием.
Поле допуска для корпуса H7 выло выбрано в пункте 2. В соответствии с выбранными полями допусков принимаем для глухой крышки посадку H7d11 для крышки с отверстием H7d9. Для данных посадок рассчитываем зазоры и строим поля допусков:
Глухая крышка – корпус:
Smin=0 +0065=0065 мм
Sср=0.5(0065+ 022)=01425 мм
Крышка с отверстием – корпус:
Smax+003+0117=0147 мм
Sср=0.5(0065+ 0147)=0106 мм
Выбор и анализ посадок элементов шлицевого соединения
Посадки элементов шлицевых деталей зависят от выбора способа центрирования сопрягаемых поверхностей. Выбор способа центрирования обуславливается требованиями предъявляемыми к конструкции механизма и технологическим возможностям.
Посадки в шлицевых соединениях назначаются в системе отверстия и осуществляются по центрирующему размеру и по боковым сторонам зубьев или только по боковым сторонам зубьев
К шлицевому соединению данного механизма предъявляются высокие требования кинематической точности ввиду того что используется зубчатое зацепление и дополнительная фиксация зубчатого колеса также данное соединение испытывает небольшую нагрузку о чем свидетельствует диаметр вала. Приняв во внимание данные условия а также то что в механизме отсутствует реверсивное движение назначим центрирование по D. Оно рекомендуется когда втулку можно обработать чистовой протяжкой до требуемых размеров а вал фрезеровать с последующей шлифовкой до окончательного размера по центрирующей поверхности D.
Параметры шлицевого соединения:
d=16 мм D=20 мм b=4мм z=6
Выбираем посадку согласно назначенному виду центрирования по D. [1] (таблицы Ж.1-Ж.4)
Принимаем посадку по центрирующему диаметру H7js6 по боковым сторонам F8f8. Получаем соединение по D-
Для данных посадок определяем точностные характеристики и строим поля допусков:
Посадка по центрирующему размеру:
Smax=0021 + 00065 = 00275 мм
Nmax=0+ 00065=00065 мм
Посадка по боковым сторонам:
Smax=0028+0028=0056 мм
Smin=001 +001=002 мм
Sср=0.5(002+ 0056)=0038 мм
Расчет резьбового соединения
Для данного резьбового соединения деталей 2-3 с параметрами определяем номинальные значения среднего и внутреннего диаметров резьбы болта и гайки [1] (таблица И.2).
Рассчитываем средний диаметр резьбы d2D2
d-1+0513= 12-1+0935= 11935 мм
Рассчитываем внутренний диаметр резьбы d1D1
d-1+0892= 12-1+0892= 11892 мм
Выбор степени точности во многом зависит от длины резьбового соединения и требований к точности. Установлены три группы длин свинчивания:
S- малые N- нормальные и L - большие.
Длины свинчивания свыше 2.24Р 02 до 6.7Р 02 относятся к группе N; длины свинчивания меньше нормальных относятся к группе S а больше – к группе L
Исходя из конструкции сборочной единицы и используя рекомендации [1] (п. 1.9.1) установливаем длину свинчивания и сопоставляем со стандартным значением
Согласно диаметру резьбы и рассчитанной длиной свинчивания выбираем группу N.
Выбираем поля допусков элементов резьбового сопряжения [1] (таблица И.4 - И.6).
Согласно группе N длины свинчивания и среднему классу точности.
Внутренняя резьба (гайка) – 6H
Наружная резьба (болт) - 6g
Определим предельные отклонения используя [2] (таблицу 4.29)
Расчет предельных значений диаметров деталей:
TD2=-=11.411-11.395=0.016 мм
TD1=-=12.128-11.892=0.236 мм
Td2=-=11.909-11.791=0.118 мм
Td=-=11.974-11.795=0.179 мм
Выбор значений шероховатости допусков формы и расположения элементов деталей
Допуски формы и расположения поверхностей валов принимают в соответствии с особенностями конструкции и требованиями к точности работы монтируемых на них деталей.
Чтобы ограничить концентрацию давления на посадочные поверхности валов при монтаже зубчатых и червячных колес муфт шкивов звездочек по посадкам с натягом задают допуск круглости и допуск профиля продольного сечения который определяется по формуле:
Где: Тр – допуск квалитета.
Полученное значение округляем до ближайшего стандартного по таблице Н.3 [1] и выбранные данные заносим в таблицу 1.
Таблица 1. Значения допусков круглости и профиля продольного сечения для валов.
Допуск профиля продольного сечения
Шпоночные пазы должны быть параллельны и симметричны соответствующей посадочной поверхности вала. При этом допуск симметричности шпоночного паза при одной шпонке может быть в 4 раза больше допуска параллельности плоскости симметрии паза. В соответствии с этим допуски параллельности и симметричности соответственно принимают по соотношениям:
где IT 9 - допуск девятого квалитета (т.к. шпонки по размеру в изготавливают
с полем допуска h9).
Отрицательное воздействие на работу подшипников и следовательно на все изделие оказывают также отклонение от перпендикулярности базовых торцов на валу и в корпусе и перекос колец подшипников.
Принимаем отклонение от перпендикулярности базовых торцов на валу и в корпусе 8мкм.
Для ограничения отклонений расположения поверхностей установлены допуски торцового биения заплечиков валов и отверстий (размеры заплечиков - по ГОСТ 20226) а также (рекомендуемые) допуски соосности посадочных поверхностей. Числовые значения этих допусков представлены в таблицах Н.7 Н.8.[1]
Допуски соосности посадочных поверхностей вала относительно общей оси при посадочной длине подшипника больше 10мм определяются по формуле:
Где: ТТ – табличное значение допуска для подшипника с посадочной поверхностью 10мм
В – длина посадочной поверхности подшипника.
Полученное значение округляем до ближайшего табличного значения принимаем допуск соосности посадочной поверхности вала
Допуски торцового биения заплечиков валов и отверстий выбираем из таблицы Н.7[1] принимаем 25 мкм.
Шероховатость шлицев вала определяется по формуле:
где: ТР – значение поля допуска для данного размера.
Полученное значение округляется в меньшую сторону до ближайшего стандартного значения таблица Н.9.[1].
Шероховатость посадочных поверхностей под подшипники на валах и в корпусах из стали а также опорных торцов заплечиков приведена в таблице Н.9.[1]
Таблица 2. Значения параметров шероховатости
Посадочные поверхности
подшипников по ГОСТ 520
Параметр шероховатости мкм
По внешнему диаметру
Выбор средств измерения деталей 11 и 12.
Средства измерения выбирают в зависимости от большого числа факторов: метрологических экономических формы размеров и конструктивных особенностей изделий объема производства и др.
Обычно прежде всего выбор измерительных средств осуществляется в зависимости от точности изготовления изделий.
При выборе средств измерений необходим анализ основных метрологических показателей: цены деления шкалы диапазона показаний предела измерений погрешности измерения и др. обращая особое внимание при этом на точность.
При выборе измерительного средства необходимо учитывать допускаемую погрешность измерения которая зависит от допуска на изготовление детали. Для размеров от 1 до 500 мм и квалитетов 2 – 17 допускаемые погрешности измерения даны в ГОСТ 8.051 (таблица Л. 1) [1].
Выбор средства измерения заключается в сравнении его основной погрешности (пределы допускаемой погрешности) (таблица Л.2) с допускаемой погрешностью измерения (таблица Л.1).
При этом основная погрешность средства измерения должна быть меньше допускаемой погрешности измерения. Типы средств измерений их характеристики и пределы допускаемой погрешности приведены в таблице Л.2. [1].
Номинальный диаметр деталей 11 и 12 равен 30мм в соответствии с таблицей Л.1. выбираем допускаемые погрешности измерения:
Принимаем для детали 12 измерительный прибор: Микрометр МК-50-1 ГОСТ 6507 (пределы измерения 25-50 мм; класс точности 1).
Для детали 11: Нутромер мод. 109 ГОСТ 9244.
Расчет размерной цепи
1 Метод полной взаимозаменяемости.
А1 А4 А5– уменьшающие звенья
А2 – увеличивающие звено
Определяем среднее количество единиц допуска (коэффициент точности).
где - допуск замыкающего звена мкм;
- суммарный допуск стандартных деталей которые входят в состав данной размерной цепи;
- значение единицы допуска каждого составляющего звена мкм [1] (таблица М. 1)
Стандартные значения коэффициента относительной точности аст приведены в таблице М.2. [1]
Назначаем на звенья А1 - и на звенья А4 А2 -
Определяем допуски составляющих звеньев ТА по выбранному квалитету точности и номинальным размерам соответствующих звеньев Аi используя данные таблицы М2 [1]
Назначаем предельные отклонения составляющих звеньев кроме корректирующего. Их назначают с учетом того что для охватывающих размеров отклонения принимают по Н для охватываемых - по h для остальных (например глубина отверстия ширина уступа межцентровые расстояния ступень) - по симметричному отклонению Js.
Проверяем правильность назначенных предельных отклонений составляющих звеньев.
2 Вероятностный метод
Вероятностный расчет размерных цепей применяется обычно при серийном и массовом производстве деталей. Допуски составляющих звеньев при вероятностном методе по сравнению с методом полной взаимозаменяемости получаются значительно большими при незначительной вероятности несоблюдения предельных значений замыкающего звена что снижает стоимость изготовления деталей.
Определяем среднее количество единиц допуска:
где t - коэффициент принятого процента риска замыкающего звена принимаем t = 3
λ - коэффициент относительного рассеяния принимаем λ = .
Производим выбор квалитета точности используя таблицу М.2[1].
Назначаем на звенья А2 А4 - и на звенья А1-
Проводим проверку соблюдения условия:
Определяем координаты середин допусков звеньев:
Проводим проверку правильности решения задачи:
Однократное измерение
Особенностью метрологического анализа однократных измерений является то что из множества возможных значений получается одно случайное.
При однократном измерении физической величины полученные показания средств измерения х=10.
Определить чему равно значение измеренной величины если экспериментатор обладает аппаратурой информацией о средстве измерения и условиях выполнения измерений согласно следующим данным:
)Определим пределы в которых находится значение заданной величины без учета погрешности:
где: ΔX – предельно допустимая абсолютная погрешность средств измерения при его показании Х.
Для определения ΔX используем показания о классе точности стедства измерения γ
Q1=10-02=98 Q2=10+02=102
Вносим в результат измерений мультипликативную поправку и уточняем результаты измерений:
В результате выполнения курсовая работы студента закрепляют полученные теоретические знания по дисциплине "МСиС" и приобретают практические навыки: в работе с таблицами ЕСДП. В расшифровке обозначений отклонений и посадок на чертежах и в технической документации; в расчете и выборе посадок с натягом; в выборе универсальных средств измерения и контроля размеров и отклонений деталей гладких цилиндрических соединений; в расчете и выборе посадок подшипников качения в зависимости от вида и условий нагружения подшипникового узла. В выборе конструкций гладких предельных рабочих калибров и расчете их исполнительных размеров; в обозначении посадок подшипников качения на чертежах; в выборе и обозначении на чертежах посадок шпоночных шлицевых и
резьбовых соединений; в расчете допусков входящих в размерные цепи.
Самостоятельно выполненная курсовая работа способствует глубокому пониманию рассматриваемых вопросов и дальнейшему квалифицированному применению полученных знаний при курсовом и дипломном проектировании а так же в дальнейшей практической деятельности.
Нормирование точностных параметров типовых соединений деталей приборов и машин (в курсовом и дипломном проектировании): Учебное пособие З.П. ЛисовскаяВ.Н. Есипов. - Орел: ОрелГТУ 2002. - 122 с.
Справочник конструктора-машиностроителя. В 3-ёх томах – 8-е изд. перераб. и доп. – М.: Машиностроение2001. 920с. ил.
Единая система допусков и посадок СЭВ в машиностроении и приборостроении справочник в 2 томах – 2-е изд. перераб.-М.:Издательство стандартов. 1989.
Чертеж Вал.cdw

Рекомендуемые чертежи
- 24.01.2023
Свободное скачивание на сегодня
Другие проекты
- 24.04.2014