Модернизация электрооборудования токарного станка с ЧПУ модели 16А20Ф3




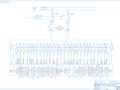
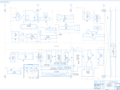
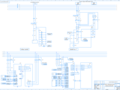

- Добавлен: 25.01.2023
- Размер: 4 MB
- Закачек: 6
Описание
Состав проекта
![]() |
![]() |
![]() ![]() ![]() |
![]() ![]() ![]() |
![]() |
![]() ![]() ![]() ![]() |
![]() ![]() ![]() ![]() |
![]() ![]() ![]() ![]() |
![]() ![]() ![]() ![]() |
![]() |
![]() |
![]() |
Дополнительная информация
диплом токарного станка 16А20Ф3.doc
1.3. Предварительный выбор двигателя
2. Выбор рода тока и типа электропривода
3. Выбор комплектного силового электрооборудования
3.1. Выбор преобразователя (комплектного электропривода) .
4. Проверка работоспособности электропривода и электрооборудования
4.1. Построение тахограммы .
4.2. Построение нагрузочной диаграммы
4.3. Проверка работоспособности электропривода
5. Выбор способа подвода электропитания
6. Расчет сечения питающих линий. Проверка на нагрев и просадку напряжения . ..
6.1. Расчёт и выбор сечений и типа питающего кабеля станок .
7. Выбор распределительного коммутационного и защитного электрооборудования ..
7.1. Выбираем кабель для питания двигателя М1 М3 и защитный аппарат ..
7.2. Выбираем вводной автоматический выключатель ..
8. Выбор электронных систем управления
Исследовательская часть
1. Выбор установленной мощности и типа двигателя
2. Оптимизация режимов системы ПЧ-АД ..
3.Основные пути повышения энергетической эффективности асинхронных электроприводов ..
4.Обеспечение технологических требований к показателям переходных процессов за счет систем управления электроприводом .
5.Эффективность применения преобразователей частоты на примере преобразователей Parvex .
Технико-экономический расчет .
1. Расчет капитальных затрат ..
2. Расчет эксплуатационных расходов
2.1. Сокращение затрат на электроэнергию потребляемую электрооборудованием станка
2.2. Сокращение затрат на переналадку станка ..
2.3. Сокращение затрат на ремонт и обслуживание станка
2.4. Суммарное сокращение эксплуатационных расходов
3. Расчет годового экономического эффекта .
Безопасность и жизнедеятельность
1. Безопасность проекта
1.1. Общая характеристика производства (рабочего места участка) и электрооборудования с точки зрения безопасности ..
1.2. Категория помещения по электробезопасности
1.3. Анализ электротравматизма ..
1.4. Средства индивидуальной и коллективной защиты
1.5. Квалификационные требования к персоналу эксплуатирующему и обслуживающему станок
1.6. Организационные и технические мероприятия обеспечивающие безопасное обслуживание и ремонт разрабатываемой в проекте электроустановки
1.8. Производственное освещение .
1.8.1. Расчет искусственного освещения
2. Чрезвычайные ситуации . ..
2.1. Пожарная безопасность ..
Библиографический список .
В настоящем проекте рассматриваются вопросы модернизации электрооборудования токарного станка с ЧПУ модели 16А20Ф3.
В проекте исходя из паспортных данных произведен расчет мощности двигателя шпинделя выбран комплектный привод.
Произведен расчет кинематической схемы продольных перемещений на основании которого с учетом требований к станку произведен выбор комплектного электропривода привода подачи.
В конструкторской части проведен расчет тахограммы нагрузочной диаграммы привода подач. Произведен расчет сечения питающих линий произведена проверка на нагрев и просадку напряжения расчет и выбор распределительного коммутационного и защитного электрооборудования.
В исследовательской части приведены результаты моделирования динамических режимов работы асинхронного частотного электропривода главного движения с векторной системой автоматического управления и уточненная проверка работоспособности электропривода. Исследования проводятся методом имитационного математического моделирования для чего в приложении Simulink пакета Matlab собрана модель асинхронного электропривода.
В проекте приведено технико-экономическое обоснование модернизации станка рассмотрены вопросы безопасности жизнедеятельности чрезвычайных ситуаций.
Пояснительная записка состоит из 108 страниц на листах формата А4. Графическая часть дипломного проекта состоит из 7 листов формата А1.
ПЕРЕЧЕНЬ ЛИСТОВ ГРАФИЧЕСКИХ ДОКУМЕНТОВ
Наименование документа
Обозначение документа
Схема однолинейная электроснабжения участка
Схема электрическая расположения
Схема кинематическая станка мод. 16А20Ф3
Тахограмма и нагрузочная диаграмма привода подач
Схема электрическая принципиальная
Модель главного электропривода
Технико-экономические показатели
В настоящее время на промышленных предприятиях большая часть станков с ЧПУ представлена оборудованием 90-х 80-х и даже 70-х годов. Рано или поздно руководители предприятий вынуждены решать вопрос о судьбе старого парка станков. Ограниченность в ресурсах и в тоже время желание обновить станочный парк заставляет предприятия идти путем модернизации оборудования.
Модернизация станка с ЧПУ обычно ассоциируется с заменой системы ЧПУ. После замены УЧПУ пользователь хотел бы получить современный станок превышающий старый по производительности и надежности.
Однако как показывает практика это происходит далеко не всегда. Новая система управления после модернизации станка безусловно надежнее старой. Но надежность станка вряд ли увеличится если на нём остались старые привода измерительная система и устройства электроавтоматики. Причем возникают новые проблемы связанные с освоением системы ЧПУ наладчиками операторами технологами электронщиками. Значительного увеличения надежности можно ожидать только тогда когда вместе с ЧПУ устанавливаются при новые привода и проводится средний а лучше капитальный ремонт электрической части станка. Но в этом случае затраты на модернизацию возрастут по меньшей мере в 3-5 раз даже при условии приобретения самых дешевых электроприводов и выполнения работ собственными силами. Стоимость модернизации станка с ЧПУ на заводе изготовителе или на специализированном ремонтном предприятии которая как правило проводится совместно с его капитальным ремонтом обычно составляет 70-80 % от стоимости нового станка.
Конечно надежность старых моделей систем ЧПУ и электроприводов ниже чем современных и они периодически выходят из строя. Но если для их восстановления применить современные приборы и методы ремонта электронных устройств то небольшая группа электронщиков справится с ремонтом всех электронных систем станков на предприятии.
Подводя итог вышесказанному можно отметить что для успешной эксплуатации старого парка станков с ЧПУ достаточно выполнить замену части физически изношенных устройств станка и организовать ремонт остальных устройств станка.
Токарный станок с ЧПУ 16А20Ф3 оснащен устаревшей системой ЧПУ «Электроника НЦ31» с приводами «Размер 2М-5-21». Они сделаны на устаревшей элементной базе и давно сняты с производства поиск комплектующих для них - целая проблема. И это не принимая во внимание их ограниченные возможности низкую надежность и моральное старение. [2]
Модернизация включает в себя:
–замену ЧПУ (NC 201М NC 210 S
–установку приводов подач по координатам X и Z фирм КЕВ S
–установка привода главного движения фирм КЕВ S
–замену пускорегулирующей и защитной аппаратуры во встроенных шкафах управления станком фирмы Schne
–замену датчиков измерительной системы обратной связи (круговые датчики типа ЛИР-158А) на конечном кинематическом звене т.е. на винте шариковинтовой передачи.
–замена встроенной в пульт управления УЧПУ NC-201М ф. Балт-Систем электронный штурвал на выносном пульте оператора ф. Балт-Систем использовать модули ввода-вывода поставляемые фирмой производителем системы ЧПУ.
Преимущества модернизации станка
При установке современных систем ЧПУ и управления приводами достигаются следующие преимущества:
–повышение надежности работы станка;
–выпуск деталей с заданными точностными параметрами;
–повышение производительности и удобства работы;
–расширение технологических возможностей для работы современным режущим инструментом;
–улучшение ремонтопригодности;
–возможность диагностики составления и установки управляющих программ с удаленного компьютера;
–возможность включения станка в единую компьютерную сеть для контроля его загрузки и простоев.
Ориентировочная стоимость модернизации в табл.1.1. [3]
ТОКАРНЫЕ СТАНКИ С ЧПУ. МОДЕРНИЗАЦИЯ
NC-201М «Балт-Систем» (Россия)
NC-210 «Балт-Систем» (Россия)
ВЭМЗ-КЕВ (Россия-Германия)
Размер (Россия) КЕМТОККЕМРОС (Болгария)
Simodrive 611 Siemens
Обзор литературных источников
Несколько готовых к производству проектов модернизации станка 16А20Ф3
1. Готовый к производству проект модернизации станка 16А20Ф3 на базе системы ЧПУ NC-210
Токарный станок 16А20Ф3 с системой ЧПУ NC-210 (ООО «Балт-Систем») является на сегодняшний день лучшей модернизацией токарного станка распространённой отечественной модели. Современная система ЧПУ имеет программную поддержку различных технологических операций интерактивный диалог не отнимающий много времени для программирования сложных обработок. Интерфейс УЧПУ русифицирован прост и доступен в обучении. Подобные УЧПУ предоставляют ряд преимуществ по сравнению с УЧПУ аппаратная часть которых основана на базе обыкновенного компьютера с разработанным программным обеспечением. Совершенная программная поддержка разработки программ электроавтоматики позволила сократить различные устройства электроавтоматики до минимума тем самым повысив надёжность станка в целом.
Станок оснащен двухкоординатным тиристорным преобразователем БУТП и тиристорным преобразователем главного движения БУТГ (ООО «Мехатроника») либо новыми болгарскими приводами SDC-IV-27(Подачи) и MDC2-II (Главный).
В качестве двигателя главного движения используется двигатель постоянного тока MR-132 в качестве двигателей подач используются стандартные двигатели постоянного тока «Болгария» датчики перемещений - ЛИР-158А (ОАО «СКБ ПС»).
Управляющие программы вводятся в память системы управления с клавиатуры пульта оператора а так же с дискеты с помощью встроенного «FDD»-дисковода и могут корректироваться с пульта оператора УЧПУ с визуализацией и возможностью прорисовки на жидкокристаллическом дисплее УЧПУ. [4]
2. Готовый к производству проект модернизации станка 16А20Ф3 на базе системы ЧПУ Sinumerik-802D
Проект включает в себя:
Система ЧПУ Sinumerik-802D:
–PP 7248 - 2 модуля (1 для пульта оператора MCP и 1 для управления электроавтоматикой);
–ADI 4 – модуль управления аналоговыми приводами;
–Блок питания ~380В.
Проект привязки системы ЧПУ Sinumerik-802D к станку реализующий представленную схему электроавтоматики.
Консоль управления с системой ЧПУ Sinumerik-802D
В стандартную консоль станка 16А20Ф3 встроены:
–Блок управления системы ЧПУ S
–Станочный пульт MCP не фото справа от блока управления Sinumerik-802D.
В левом отсеке консоли установлена панель управления на ней расположены:
–Кнопка «Съезд с аварийных конечников».
Внутри консоли расположен модуль PP 7248 обеспечивающий связь панели MCP с блоком управления.
Правая панель полностью очищена на ней располагается:
–DIN-рейка с набором необходимого количества 24В реле;
–блок питания ~380В в =24В питающий систему ЧПУ и цепь входных сигналов;
–автоматический выключатель защищающий вводную цепь питания станка.
Центральная панель:
–магнитные пускатели;
–на DIN-рейке набор автоматических выключателей защищающих различные цепи станка;
–в центре сверху твердотельное реле управляющее револьверной головкой Pragat
–слева на DIN-рейке клеммник связывающий элементы электроавтоматики с модулем PP 7248 расположенным на правой панели.
В панели приводов установлены:
–современные привода
–привод главного движения 15
–привод оси Z 12F5A1D.
Привода подач имеют повторители сигналов фотоимпульсного датчика позиции эти сигналы проецируются в модуль ADI-4 а через него информация о позиции попадает в систему.
К приводу главного движения подключен датчик с двигателя а к модулю ADI-4 датчик резьбонарезания станка.
Использование современных приводов повышает надежность и обеспечивает высокое качество управления по сравнению со старыми приводами.
Применение модуля ADI-4 позволило использовать привода KEB и оставить имеющиеся на станке асинхронные двигатели. Эти меры позволили несколько снизить стоимость проекта по сравнению с полным переоснащением станка приводами SIMODRIVE и соответствующими двигателями. [5]
3. Готовый к производству проект модернизации станка 16А20Ф3 на базе системы ЧПУ NC-201М с приводами фирмы Parvex НМ-НА
–Стандартное фрезерно-токарное программное обеспечение;
–Каналы входоввыходов.
Внешние модули входоввыходов:
–Модуль индикации входов NC-210-402;
–Модуль релейной коммутации выходов NC-210-401;
–Электронный штурвал NC-110-75В.
–Привод HA-75 (Япония);
–Двигатель HM-13-017-0200 (17 Нм);
–Тормозной резистор.
–Преобразователь 690C-011-4-BS (11 кВт);
–Двигатель асинхронный MA-100P (11 кВт);
Привод с двигателем оси X и Z НМ-НА-13-17-2000 (17 Нм).
Привод главного движения PARVEX с двигателем MA-100 P-FB 11кВт. с принудительным охлаждением.
Готовое конструктивное решение позволяющее встроить блок управления системы NC-201М в консоль пульта оператора станка 16А20Ф3. Конструкция выделяется простотой монтажа современным дизайном и использованием качественных материалов. Продуманное расположение органов управления с интеллектуальной индикацией обеспечивает простое и удобное управление станком позволяет быстро и адекватно реагировать на возможные аварийные ситуации.[6]
Технологическая часть
1.1.Технологический процесс всего цеха выпускаемая продукция
Технологический процесс – это часть производства включающая в себя последовательное изменение размеров формы внешнего вида или внутренних свойств предмета производства и их контроль.
Цех включает в себя: термо-кузнечное отделение механо-штамповое отделение инструментальное отделение отделение по изготовлению кристаллизаторов и отделение матриц и резцов.
Основное оборудование копировально-фрезерные фрезерные шлифовальные универсально-заточные токарно-винторезные станки. В цехе производят термическую обработку штампов производят кристаллизаторы матрицы для прессования оправки для производства сложных профилей из алюминиевого сплава формовочные калибровочные валки трубосварочных станов прокатные и правильные валки приспособления для обработки титановых штамповок режущий инструмент (ножи гильотинные дисковые спец. металлорежущий инструмент резцы дереворежущий инструмент).
Основной задачей цеха № 35 является выпуск качественной оснастки и технологического инструмента в соответствии с планами производства и требованиями цехов организации.
1.2.Технологический процесс токарного станка с ЧПУ мод. 16А20Ф3
Весь комплекс программного управления металлорежущим оборудованием включает: станок с ЧПУ устройство числового программного управления УЧПУ управляющую программу к станку для выполнения конкретной операции УП. Входом в этот комплекс являются данные от операции которую предстоит выполнить выходом – детали обработанные в соответствии с этой операцией.
Управляющая программа должна содержать изложенную сжато в определенной последовательности всю необходимую информацию для выполнения одной операции технологического процесса обработки детали.
После выбора формы заготовки и составления маршрутной технологии начинают подробную разработку поэлементного технологического процесса с тщательными расчетами а именно все эти операции как правило проводятся с применением ЭВМ:
Составляют геометрический план обработки детали т.е. эскиз обработки с указанием величин припусков технологических баз и мест крепления заготовки;
Разрабатывают попереходный комплекс программного управления технологический процесс – операционную карту с режимом резания режущим инструментом и необходимыми технологическими приспособлениями – оснасткой;
Проектируют карту наладки станка по переходам с назначением величины припусков инструментов в резцедержателе за инструментом закрепляют блоки коррекции;
Производят расчет и графическое построение траектории движения инструмента что особенно важно при обработке детали со сложными криволинейными поверхностями;
Записывают управляющую программу на ЧПУ;
Выявляют и корректируют недоработки в управляющей программе после контроля при обработке первой детали из партии.
1.3.Роль станка в общем технологическом процессе
Токарный станок с ЧПУ 16А20Ф3 предназначен для токарной обработки в полуавтоматическом режиме наружных и внутренних поверхностей деталей типа тел вращения со ступенчатым и криволинейным профилем различной сложности.
Область применения станка: мелкосерийное и серийное производство.
Используются высокоэффективные технологические способы обработки элементарных поверхностей:
–обработка широкими резцами с поперечной подачей;
–обтачивание фасонными резцами наружных и внутренних поверхностей;
–применение резьбонарезных головок и т. д.
Применяется концентрация обработки заготовки несколькими инструментами одновременно: двумя и более резцами резцами и сверлом и т. п. Сочетание указанных и других приемов позволяет быстро и точно вести обработку.
Компенсирует затраты на наладку автомата и сокращает трудовые затраты на изготовление партии деталей.
Конструкция и кинематическая схема механизма
2.1.Конструктивное исполнение станка параметры паспортные данные кинематические схемы
Расположение и обозначение составных частей оборудования приведено на рис. 2.2.1.
Рис. 2.2.1. Компоновка станка
– Основание с транспортером стружки; 2 – Станина; 3 – Суппортная группа; 4 – Передача винт-гайка качения (ВГК) продольного перемещения; 5 – Опора левая винта продольного перемещения; 6 – Патрон механизированный с электромеханическим приводом; 7 – Ограждение неподвижное; 8 – Ограждение подвижное; 9 – бабка шпиндельная; 10 – Шкафы управления; 11 – Головка автоматическая; 12 – Ограждение суппортной группы; 13 – Бабка задняя; 14 – Электромеханический привод пиноли задней бабки; 15 – Разводка коммуникаций; 16 – Пульт управления; 17 – Кронштейн пульта управления; 18 – Опора правая винта продольного перемещения; 19 – Станция смазки шпиндельной бабки; 20 – Установка моторная; 21 – Ограждение задней зоны; 22 – Привод поперечного перемещения; 23 – Передача ВГК поперечного перемещения.
2.2.Основные технические параметры
Особенности конструкции:
–высокопрочная станина выполненная литьем из чугуна марки СЧ20 с термообработанными шлифованными направляющими обеспечивают длительный срок службы и повышенную точность обработки;
–привод главного движения включающий главный двигатель 11 кВт и шпиндельную бабку обеспечивает наибольший крутящий момент до 800 Нм;
–высокоточный шпиндель с отверстием 55 мм (по заказу 64 мм) позволяющий обрабатывать детали из пруткового материала зона обработки может быть оснащена как линейной наладкой так и револьверной головкой в зависимости от требований покупателя;
–надежная защита шарико-винтовых пар обеспечивает долговечность работы механизмов перемещения по координатам X и Z станок оснащается системами ЧПУ и электроприводами как отечественного производства так и производства зарубежных фирм.
Техническая характеристика станка модели 16А20Ф3
Класс точности станка по ГОСТ 8-82
Наибольший диаметр изделия устанавливаемого над станиной
Наибольший диаметр обрабатываемого изделия
Наибольшая длина обрабатываемого изделия
Наибольшая длина устанавливаемого изделия в центрах
Диаметр цилиндрического отверстия в шпинделе
Наибольший ход суппорта
Максимальная рекомендуемая скорость рабочей подачи
Минимальная скорость рабочей подачи
Количество управляемых координат
Количество одновременно управляемых координат
Наибольшие усилие продольной подачи
Точность позиционирования
Максимальная скорость быстрых перемещений
Диапазон частот вращения шпинделя
Пределы частот вращения шпинделя в трех переключаемых вручную диапазонах
Наибольший крутящий момент на шпинделе не менее
Габаритные размеры станка
длина (с транспортером отвода стружки)
Масса станка (без транспортера отвода стружки)
Техническая характеристика электрооборудования
Род тока питающей сети
Продолжение табл. 2.2.3
Напряжение цепи управления В
Напряжение цепи местного освещения В
Кол-во электродвигателей на станке
Тип электродвигателя главного движения*
АБ2П132М4ПБ или МР132М (НРБ)
Номинальная мощность электродвигателя
главного движения кВт
Номинальная частота вращения электродвигателя
главного движения мин-1
Диапазон регулировки частота вращения
электродвигателя главного движения
00 4500 или 1000 3500 (НРБ)
Тип электродвигателей приводов подач
Номинальный крутящий момент электродвигателей приводов подач Нм (кгм):
Суммарная мощность всех электродвигателей кВт
Суммарная потребляемая мощность кВт (с учетом приводов и УЧПУ)
2.3.Описание кинематической схемы
Кинематическая схема станка мод. 16А20Ф3 представлена на рис. 2.2.3.1. В качестве привода главного движения используют электродвигатель М1 (N=11 кВт n=1460 мин-1): регулируемый постоянного тока либо частотно-регулируемый асинхронный.
Рис. 2.2.3.1. Кинематическая схема станка
В описываемой схеме двигатель М1 - частотно-регулируемый асинхронный.
От двигателя М1 через клиноременную передачу с диаметрами шкивов D=115 мм и D=257 мм) вращение передается на вал I шпиндельной бабки а затем через зубчатые колеса 1 и 3 на вал II. Далее обеспечиваются три диапазона частоты вращения шпинделя (20-285; 60-830; 175-2500 обмин). В пределах каждого диапазона частота вращения регулируется бесступенчато путем изменения частоты вращения электродвигателя М1.
Датчик резьбонарезания (ДР) связанный со шпинделем беззазорной зубчатой парой z=61-61 осуществляет связь между шпинделем и ходовым винтом исходя из условия что за один оборот шпинделя резец должен переместится на величину шага нарезаемой резьбы. Зубчатые колеса 10 и 9 служат для вращения датчика BE-178 резьбонарезания.
Кинематическая цепь привода подач суппорта по оси X (поперечное перемещение) применяют электродвигатель М2 пару винт-гайка качения с шагом винта Рх.в. = 5 ммоб. Винт соединен непосредственно с валом двигателя. КПД механической передачи составляет 95%. Обратная связь по пути осуществляется фотоимпульсным датчиком ВЕ - 178.
Кинематическая цепь привода подач суппорта по оси Z (продольное перемещение) представляет собой электродвигатель М3 пару винт-гайка качения с шагом винта Рх.в. =10 ммоб и числом заходов винта равным 6. Винт соединен непосредственно с валом двигателя. КПД механической передачи составляет 95%. Обратная связь по пути осуществляется фотоимпульсным датчиком ВЕ - 178.
Механическая часть привода продольной подачи служит для преобразования вращательной скорости на валу двигателя в поступательную скорость перемещения суппорта станка. На суппорте установлен привод продольной подачи и магазин инструментов.
Рис. 2.2.3.2. Кинематическая схема продольной подачи
Для согласования вращательной и поступательной скоростей необходимо определить радиус приведения скорости кинематической передачи определяемой по формуле
где h – шаг винта равный 10-2моб; zp – число заходов винта равное 6.
Механическая часть представляет собой жесткую механическую схему с реактивной нагрузкой что не требует дополнительного проведения расчетов упругих связей и применения механического тормоза.
Момент инерции механической схемы определяется
где mc – масса суппорта кг; mc=60 кг; ρ – радиус приведения скорости кинематической передачи м.
2.4.Краткая характеристика электрооборудования
Электрооборудование включает в себя:
–устройство числового программного управления (УЧПУ) для управления циклом обработки детали;
–электропривод асинхронный глубокорегулируемый комплектный для управления приводами подач и приводом главного движения;
–электродвигатели для управления приводами резцедержателя патрона охлаждения пиноли смазки направляющих смазки шпиндельной бабки транспортера стружкоудаления;
–фотоимпульсные датчики контроля перемещения по осям и резьбонарезания;
–аппараты защиты управления и сигнализации;
–другие аппараты и устройства осуществляющую коммутацию подсоединение электрических цепей и управление механизмами.
Технические характеристики УЧПУ датчиков электродвигателей.
Сведения о системе питания электрооборудования
Электрооборудование станка работает от сети трехфазного переменного тока с напряжением 380 В (+10%;-15%) и частотой 50 Гц (+2%;-2%) с глухозаземленной нейтралью.
На станке используется переменный и постоянный ток со следующими параметрами:
Гц 3~ 380 В – цепи асинхронных электродвигателей питание комплектного электропривода трансформаторов управления;
Гц ~ 220 В – цепи вводного пускателя УЧПУ вентиляторов;
Гц ~ 110 В – цепи управления;
Гц ~ 24 В – цепи местного освещения и сигнализации;
– 24 – цепи управления и сигнализации.
Все металлические части станка (станина корпус электродвигателей каркас шкафов пульт управления и т.д.) которые могут оказаться под напряжением выше 42В – заземлены.
3.Характеристика существующей системы электроснабжения установки
Потребителями инструментального отделения являются металлообрабатывающие станки средней мощности к ним относятся: круглошлифовальный токарно-револьверный вертикально-сверлильный токарный полуавтомат токарный с ЧПУ горизонтально-проточный горизонтально-расточный горизонтально-фрезерный токарно-винторезный радиально-сверлильный и другие.
Металлообрабатывающие станки являются трехфазными по надежности электроснабжения относятся ко второй категории. Устанавливаются стационарно и по площади цеха распределены равномерно.
В проектируемом цехе имеются приемники работающие в повторно-кратковременном режиме – это электроприемники контактной сварки (точечные стационарные сварочные стыковые сварочные шовные роликовые сварочные точечные сварочные стационарные машины).
Все электроприемники рассчитаны на переменный ток напряжением 380 В промышленной частоты.
Питание осуществляется от цеховой КТП-53 с двумя трансформаторами марки ТМЗ –10001004.
Трехфазные трансформаторы с естественным масляным охлаждением ТМЗ-1000 предназначены для преобразования электрической энергии и питания различных потребителей в сетях переменного тока.
В трансформаторах ТМЗ-1000 предусмотрены 5 ступеней регулирования напряжения ВН: ±2х25% от номинального.
Вид регулирования - ПБВ (переключение без возбуждения). Переключение трансформатора ТМЗ-1000 на другой диапазон производится в ручном режиме в отключенном состоянии.
Трансформаторы ТМЗ изготавливаются в герметичном исполнении в качестве конструктивной защиты масла используется сухой азот (принцип азотной подушки между зеркалом масла и крышкой трансформатора). Основные технические характеристики трансформатора ТМЗ-100010 приведены в табл. 2.3.
Номинальная мощность кВА
Номина-льное высшее напряже-ние кВ
Номиналь-ное низшее напряже-ние кВ
Потери холос-того хода кВт.
Потери короткого замыка-ния кВт.
Ток холос-того хода %
Напряже-ние короткого замыка-ния %
Схема и группа соедине-ния обмоток
Схема однолинейная электроснабжения участка изображена на рис. 2.3.1.
Рис. 2.3.1. Схема однолинейная электроснабжения инструментально отдела
3.1.Конструктивное исполнение распределительной сети
Основной тенденцией в проектировании электроснабжения является сокращение протяженности сетей низшего напряжения путем максимального приближения высшего напряжения (трансформаторной подстанции) к потребителям электроэнергии.
Сети напряжением до 1000 В подразделяются на питающие прокладываемые от трансформаторной подстанции или вводного устройства до силовых пунктов и распределительные к которым присоединяются ЭП. В комплекс внутрицехового электроснабжения входят питающие и распределительные линии РП напряжением до 1000 В аппаратура коммутации и защиты сетей и ответвлений к отдельным ЭП. Питающие и распределительные сети могут быть выполнены по радиальным магистральным и смешанным схемам.
Радиальные схемы наиболее часто используются для питания отдельных относительно мощных ЭП (двигатели компрессорных и насосных установок печи и т.д.) а также в случаях когда мелкие по мощности ЭП распределяются по цеху неравномерно и сосредоточены группами на отдельных участках (ремонтные мастерские отдельные участки с не поточным производством и т.п.). К достоинствам радиальных схем относятся: высокая надежность питания (выход из строя одной линии не сказывается на работе потребителей питающихся от других линий) а также возможность автоматизации переключений и защиты.
Магистральные схемы применяются для питания ЭП обслуживающих один агрегат и связанных единым технологическим процессом когда прекращение питания любого из этих ЭП вызовет необходимость прекращения работы всего технологического агрегата. Магистральные схемы находят широкое применение для питания большого числа мелких ЭП распределенных относительно равномерно по площади цеха (металлорежущие станки в цехах механической обработки металлов и другие потребители).
На практике наибольшее распространение находят смешанные схемы сочетающие в себе элементы радиальных и магистральных схем. Смешанные схемы характерны для крупных цехов металлургических заводов для литейных кузнечных и механосборочных цехов машиностроительных заводов.
Конструктивное исполнение распределительной сети инструментального отдела выполнено по радиальной схемы.
3.2.Анализ существующие проблемы пути решения
На данный момент на предприятии имеется значительное количество морально и физически устаревшего оборудования требующего замены. Однако предприятие не располагает достаточными средствами для полной замены устаревшего парка оборудования.
Одним из выходов из сложившейся ситуации может быть частичная модернизация имеющегося оборудования в частности электрооборудования.
Модернизация электрооборудования предполагает внесение изменений в электрическую схему с целью улучшения технических и экономических показателей станка что позволит предотвратить (ликвидировать) моральный износ оборудования.
При технической возможности и экономической целесообразности модернизация оборудования может осуществляться централизованно заводом -изготовителем и в единичных случаях может проводиться потребителями. Это позволяет при незначительных затратах увеличить годовые объемы производства производительность оборудования и труда снизить себестоимость продукции.
На предприятии имеется значительный парк металлорежущих (токарных сверлильных фрезерных и т.д.) станков требующих модернизации. Поэтому выбранная тема дипломного проекта является актуальной и соответствует современным требованиям.
Первоначально в станке 16А20Ф3 был использован привод асинхронный «Размер 2М-5-21». Этот привод использовался в токарных станках с ЧПУ для управлении электродвигателями двух механизмов подач и электродвигателем шпинделя.
В комплект электропривода входят:
–шкаф электропреобразователей;
–три асинхронные машины со встроенными датчиками положения и температуры и вентиляторами;
–диагностические устройства сигнатурного контроля;
–блок трансформаторов.
Электропривод обеспечивает работу во всех 4 квадрантах механической характеристики при изменении управляющего напряжения в пределах ±10 В.
Максимальная частота вращения 1000 или 1500 мин-1 в зависимости от типоразмера привода.
Типоразмеры привода охватывают ряд номинальных моментов двигателей от 7 до 70 Нм.
Электропривод вырабатывает импульсные сигналы перемещения которые могут использоваться в устройстве ЧПУ для измерения перемещения механизмов подач.
Две серии импульсных сигналов Sin и Cos с фазовым сдвигом 90 эл. градусов несут информацию о величине и направлении перемещении. За один оборот вала двигателя выдается 2000 или 1000 импульсов в зависимости от исполнения привода. Сигнал нуль-метки НМ выдается два раза за один оборот вала двигателя и используется в УЧПУ для формирования меток начала отсчета.
Главный привод имеет частоту вращения от 45 до 4500 мни-1. Мощность привода 11 кВт. Электропривод реализован в соответствии с частотно-токовым способом управления. Привод обеспечивает двухзонное регулирование частоты вращения.
Привода подачи выполнены по схеме подчиненного регулирования с контурами регуляторов тока скорости частоты скольжения и положения. Контур положения замыкается через устройство ЧПУ.
Традиционные для подобного оборудования 10-летней давности приводы переменного тока в настоящее время есть более современные асинхронные двигатели и преобразователи частоты. Это обусловлено высокой надежностью двигателей низкой стоимостью асинхронных двигателей их массовым выпуском и простыми требованиями к обслуживанию. Современные преобразователи частоты позволяют обеспечивать широкий диапазон регулирования скорости вращения и компенсировать снижение мощности двигателя на малых оборотах. Постоянное удешевление преобразователей частоты и реализация все более современных режимов управления способствуют широкому их применению.
Для повышения контроля линейного перемещения ходового винта исполнительного механизма необходимо заменить датчик измерительной системы обратной связи (круговые датчики типа ЛИР-158А) на конечном кинематическом звене. В отличие от разработанного свыше 30 лет назад BE-178 датчики серии ЛИР-158А выполнены на современной элементной базе и объективно качественно превосходят аналоги по сроку службы надежности и стабильности работы
4.Требования предъявляемые к электрооборудованию
Требования к электроприводам и системам управления станками определяются технологией обработки конструктивными возможностями станка и режущего инструмента.
Основными технологическими требованиями согласно являются обеспечение:
–самого широкого круга технологических режимов обработки с использованием современного режущего инструмента;
–максимальной производительности;
–наибольшей точности обработки;
–высокой чистоты обрабатываемой поверхности.
Удовлетворение всем этим и другим требованиям зависит от характеристик станка и режущего инструмента мощности главного привода и электромеханических свойств приводов подач и системы управления.
4.1.Требования к приводу механизма главного движения токарного станка
В современных станках с числовым программным управлением (ЧПУ) функции выполняемые электроприводом главного движения значительно усложнены. Помимо стабилизации частоты вращения при силовых режимах резания требуются обеспечение режимов позиционирования шпинделя при автоматической смене инструмента что неизбежно ведет к увеличению требуемого диапазона регулирования частоты вращения.
Частотный преобразователь должен обеспечивать двухзонное регулирование скорости электродвигателя.
Преобразователь должен использовать векторный алгоритм управления позволяющий получить высокий стартовый момент и сохранить его до номинальной скорости асинхронного двигателя обеспечивает высокое качество регулирования по скорости при скачкообразном изменении момента сопротивления на валу.
Стабильность работы привода характеризуется перепадом частоты вращения при изменении нагрузки напряжении.
Динамические характеристики электропривода по нагрузке практически определяют точность и чистоту обработки изделия а также стойкость инструмента. Устойчивый процесс резания при необходимой точности и чистоте поверхности возможен если параметры настройки привода обеспечивают при набросе номинального момента нагрузки максимальный провал скорости не более 40% при времени восстановления не превышающем 025 с.
Отличительной особенностью главного привода станков с ЧПУ является необходимость применения реверсивного провода. Требование обеспечения эффективного торможения и подтормаживания при снижении частоты вращения и режимов поддержания постоянной скорости резания приводит к необходимости применения реверсивного привода с целью получения нужного качества переходных процессов.
Итак главный привод в станках обладает рядом особенностей:
значительно большие мощности;
необходимость использования всей мощности двигателя в большом диапазоне частот вращения шпинделя станка;
работа большей части времени на постоянно заданной частоте вращения;
большие моменты инерции во много раз превосходящие собственные моменты инерции двигателей на высших передачах коробки скоростей;
высокая точность позиционирования;
применение реверсивного электропривода для обеспечения эффективного торможения и подтормаживания при снижении частоты вращения и режимов поддержания постоянной скорости резания.
4.2.Требования к приводу механизма подачи токарного станка
В современных металлорежущих станках и автоматизированных обрабатывающих центрах устанавливаются два или более электроприводов. Один из них именуемый главным предназначен для вращения детали относительно режущего инструмента (токарные операции) или наоборот (фрезерные или сверлильные операции). Остальные приводы именуемые приводами подач выполняют функцию перемещения инструмента. Главный привод обладает большой мощностью т.к. именно он преодолевает силы сопротивления резанию приводы же подач по мощности на порядок и более могут уступать главному но именно они обеспечивают точность и чистоту обработки детали и одновременно производительность оборудования поскольку от них зависит как точность взаимного позиционирования инструмента и обрабатываемой детали так и быстрота перемещения инструмента при смене операций. В связи с этим к двигателям составляющим основу приводов подач предъявляются высокие требования в плане широты диапазона регулирования частоты вращения линейности регулировочных характеристик быстродействия способности выдерживать высокие перегрузки по току и моменту. Аналогичные требования предъявляются и к двигателям устанавливаемым в приводах для промышленных роботов.
Необходимость сочетания всех указанных требований привели к тому что до 70-х гг. монополистами в этой области были коллекторные двигатели постоянного тока. Они обладали всеми необходимыми свойствами однако в то же время и всеми недостатками привносимыми щеточно-коллекторным узлом: низкая надежность необходимость периодического ухода высокий уровень помех вызванных искрением на коллекторе малый срок службы. Выходом из создавшегося положения был переход в наиболее развитых странах на вентильные двигатели который стал возможен в связи с прогрессом в области электроники (особенно силовой) и в области создания постоянных магнитов с высокими значениями остаточной индукции и коэрцитивной силы. Обладая практически теми же характеристиками что и двигатели постоянного тока они полностью лишены всех недостатков обусловленных вращающимися контактами.
К электроприводу подач предъявляются следующие требования:
минимальные размеры электродвигателя при высоком вращательном моменте;
высокая максимальная скорость;
значительная перегрузочная способность привода в режимах кратковременной и повторно-кратковременной нагрузки;
широкий диапазон регулирования;
высокая стабильность характеристик;
высокое быстродействие при разгоне и торможении подключении и отключении нагрузки;
высокая равномерность движения при различной нагрузке при всех скоростях вплоть до самых малых;
удобство конструктивной установки двигателя на станке и встраивания управляемых преобразователей в шкафы и ниши шкафов и ниши станков.
4.3.Требования к надежности
Необходимы следующие требования к надежности работы электропривода в производственных условиях связанные со спецификой производства:
–наработка на отказ не менее 700 ч;
–средний срок службы не менее 10 лет;
–средний ресурс не менее 30000 ч.
4.4.Требования к безопасности
Процесс резания и обработки металла связан с выбросом металлической стружки и наличием токопроводящей пыли поэтому во избежание аварийных ситуаций и обеспечения безопасности персонала электропривод должен соответствовать следующим требованиям безопасности:
–правилам пожаробезопасности относящимся к категории А Б или В;
–правилам электробезопасности для помещений с повышенной опасностью.
Электропривод должен иметь в своем составе следующие технические решения обеспечивающие безопасность работ:
–все необходимые технологические пуско-наладочные и защитные блокировки;
–изолированный и доступный для оператора пульт управления;
–на всех пультах управления должны находиться кнопки останавливающие работу ЭП;
–аппаратуру управления питающуюся пониженным напряжением до 42В;
–на станине электрошкафах пультах управления каретке должны быть предусмотрены болты заземления;
–наличие кнопки «Общий стоп»;
–все необходимые защитные устройства связанные с обработкой металла (защитные щиты кожухи металлорукава и т.д.).
Конструкторская часть
1.Расчет требуемой мощности электропривода и электрооборудования
Электропривод установки должен полностью удовлетворять требованиям технологического процесса и соответствовать условиям окружающей среды в процессе эксплуатации. В то же время для электропривода следует выбирать наиболее простой двигатель по устройству и управлению надежный в эксплуатации имеющий наименьшие массу габариты и стоимость.
Выбор электрических двигателей производится с учетом следующих параметров и показателей:
–рода тока и номинального напряжения;
–номинальной мощности и скорости;
–вида естественной механической характеристики;
–способа пуска и торможения;
–особенностей регулирования скорости;
–конструктивного исполнения двигателя.
Наиболее простыми в отношении устройства и управления надежными в эксплуатации имеющими наименьшие массу габариты при заданной мощности являются асинхронные двигатели с короткозамкнутым ротором.
Выбор двигателя по защите от действия окружающей среды должен производиться в соответствии с условиями в которых он будет работать.
Предварительный выбор мощности двигателя исходя из технологического режима работы по расчетным формулам либо на основе нагрузочных диаграмм рабочей машины либо по удельному расходу электрической энергии на выпуск единицы продукции и др.
Расчет переходных процессов и построение нагрузочных диаграмм электропривода в соответствии с технологическим процессом рабочей машины.
Проверка предварительно выбранного двигателя по нагреву и перегрузочной способности оценка соответствия параметров нагрузочных диаграмм электропривода допустимым параметрам двигателя и технологического процесса.
Расчет мощности электродвигателей металлорежущих станков производится с учетом режимом резания.
1.1.Определение мощности двигателя главного привода
Мощность на валу двигателя главного привода в установившемся режиме складывается из мощности резания зависящей от усилия и скорости резания и мощности потерь в механизмах передач которая зависит от нагрузки числа звеньев кинематической цепи и частоты вращения привода. При расчетах обычно пользуются коэффициентом полезного действия станка который определяется как произведение КПД отдельных звеньев кинематической цепи при работе на данной скорости
При увеличении частоты вращения рабочих органов станка потери в передачах увеличиваются поэтому КПД станка уменьшается. Для станков токарной группы КПД кинематической цепи главного привода при полной нагрузке в среднем составляет 07÷08. Для цепи подачи обычно =01÷02 так как здесь применяются замедляющие передачи имеющие низкий КПД.
Мощность на валу главного двигателя в установившемся режиме с учетом потерь в передачах
угловая частота вращения
где ст. - к.п.д. станка при полной нагрузке (для станков токарной группы в среднем составляет 07÷08). Принимаем ст = 08 =const.
Исходя из паспортных данных изменения частоты вращения крутящего момента мощности на шпинделе посчитаем мощность на всех диапазонах результаты сведем в табл. 3.1.1.1
Диапазон частоты вращения шпинделя
1.2.Определение мощности двигателя привода подачи
Для примера рассмотрим технологический процесс обработки детали «палец». В процессе обработки детали производится точение сразу трех заготовок с последующим отрезанием на необходимый размер. Данная заготовка изображена на рис. 3.1.2.1.
В качестве примера обработки рассмотрим только наружное продольное точение при черновом и чистовом режимах. Это объясняется тем что при снятии фасок не возникает больших нагрузок на привод как при черновом точении а при отрезании используется перемещение поперечной подачи станка.
При черновом точении используем максимально тяжелый режим резания позволяющий снять максимальное количество стружки за один проход.
При чистовом точении следует руководствоваться чистотой обрабатываемой поверхности и принять её максимальной. Чистовой режим точения производим с минимальным количеством снятия стружки что обеспечит высокое значение шероховатости обрабатываемой поверхности.
При механической обработке изделия необходимо провести расчет для двух режимов точения – черновое и чистовое.
Для расчета момента сопротивления рассмотрим некоторые элементы резания при точении.
Скорость резания V – путь проходимый режущей кромкой инструмента относительно обрабатываемой поверхности в ммин.
Подача s –перемещение резца при вспомогательном движении за один оборот обрабатываемой детали в ммоб.
Глубина резания t – толщина слоя материала срезаемого с обрабатываемой поверхности за один проход в мм.
Стойкость инструмента T – период работы инструмента до затупления в мин.
При черновой (предварительной) обработке следует назначать по возможности наиболее тяжелые режимы резания что обеспечивает универсальность станка и запас мощности электропривода. При чистовом точении назначаются меньшие глубина резания и подача исходя из заданного параметра шероховатости.
Элементы режима резания следует устанавливать в следующем порядке:
Глубина резания – принимается равной всему припуску на обработку или большей его части при черновом точении и наименьшей при чистовом.
Подача – устанавливается возможно максимальной исходя из жесткости и прочности системы прочности твердосплавной пластинки и других параметров.
Скорость резания при продольном точении
где T – стойкость резца мин.; для твердосплавного резца Т15К6; Сv – коэффициент характеризующий вид токарной обработки. Для наружного продольного точения проходными резцами; m t – глубина резания мм; s – подача ммоб.
Расчетные коэффициенты для определения скорости резания сведены в табл. 3.1.2.1
Коэффициенты определения скорости резания
Коэффициент режим резания
Kv – поправочный коэффициент определяемый по формуле
где Kпv – коэффициент отражающий состояние поверхности заготовки Kпv=0.85; Kиv – коэффициент учитывающий качество материала инструмента для конструкционной стали Т15К6 Kиv=1.15; Kmv – коэффициент учитывающий качество обрабатываемого материала определяемый по формуле
где KГ – коэффициент характеризующий группу стали по обрабатываемости KГ=1; в – для стали 45 в=750 МПа; nv – показатель степени характеризующий группу стали по обрабатываемости nv=1.
Величины поправочных коэффициентов приведены в табл. 3.1.2.2.
Поправочные коэффициенты для режимов резания
Тогда скорость резания при черновом точении
при чистовом точении
Результаты расчета скорости резания приведены в табл. 3.1.2.3.
Результаты расчета скорости резания
Скорость резания v ммин
Силу резания F принято раскладывать на составляющие силы направленные по осям координат станка (тангенциальную радиальную и осевую). При наружном продольном точении осевая сила резания
где Сp –постоянный для конкретных (расчетных) условий обработки для осевой составляющей силы резания для конструкционной стали с в=750 МПа; s – величина подачи для расчетного режима резания ммоб; v – расчетная скорость резания ммин.
Данные коэффициентов приведены в табл. 3.1.2.4.
Kp – поправочный коэффициент представляющий собой произведение ряда коэффициентов учитывающих фактические условия резания
Kmp – рассчитывается по формуле
Величины поправочных коэффициентов сведены в табл. 3.1.2.5.
Величины поправочных коэффициентов
Определим силу резания для чернового точения
для чистового точения
Результаты расчета силы резания сведены в табл. 3.1.2.6.
Результаты расчета силы резания
где d – диаметр обрабатываемой детали м тогда для чернового точения
Результаты расчета моментов резания сведены в табл. 3.1.2.7.
Результаты расчета моментов резания
1.3.Предварительный выбор двигателя
Электропривод производственного механизма считается работоспособным если он работает в заданном технологическом режиме. Это возможно в том случае когда номинальная мощность двигателя соответствует нагрузке на его валу и режиму его работы.
При расчете номинальной мощности двигателя предварительно можно принять как
где Mma max – максимальная частота вращения вала двигателя в радс.
Определим статические моменты при черновом и чистовом точении по формуле
где F – сила резания для заданного режима Н; ρ=0.0095 – радиус приведения к валу двигателя со скоростью ; =0.95 – КПД механической передачи. Результаты сведем в табл. 3.1.2.8.
Результаты расчета силы резания и статического момента
Из проведенных расчетов видно что максимальному статическому моменту соответствует момент при черновом точении.
Максимальную частоту вращения двигателя определяем исходя из условия обеспечения скорости быстрых перемещений суппорта V=2 ммин
Частота вращения двигателя на рабочих подачах определяется по формуле
Найденные результаты сведены табл. 3.1.2.9.
Результаты расчета угловой скорости
Ускоренное перемещение
Определим необходимую мощность двигателя
2.Выбор рода тока и типа электропривода
Выбор рода тока и типа электропривода целесообразно производить на основе рассмотрения и сравнения технико-экономических показателей ряда вариантов удовлетворяющих техническим требованиям данной рабочей машины. На основании исходных данных и требований предъявляемых к электроприводу необходимо выбрать вариант электропривода способный полностью выполнить требования и быть одновременно максимально экономичным.
«Правила устройства электроустановок» [10] рекомендуют начинать процесс выбора рода тока с двигателей переменного тока.
« V-3-11. Для привода механизмов не требующих регулирования частоты вращения независимо от их мощности рекомендуется применять электродвигатели синхронные или асинхронные с короткозамкнутым ротором.
Для привода механизмов имеющих тяжелые условия пуска или работы либо требующих изменения частоты вращения следует применять электродвигатели с наиболее простыми и экономичными методами пуска или регулирования частоты вращения возможными в данной установке
« V-3-14. Электродвигатели постоянного тока допускается применять только в тех случаях когда электродвигатели переменного тока не обеспечивают требуемых характеристик механизма либо не экономичны »
Для нерегулируемого привода выбор типа двигателя прост. Двигатели переменного тока проще по конструкции стоимость их ниже обслуживание тоже требует меньших затрат. При повторно-кратковременном режиме работы с частыми пусками и торможениями рационально использовать двигатели повышенного скольжения.
Для регулируемого привода задача выбора типа привода решается сложнее. В зависимости от диапазона и плавности регулирования скорости требований к качеству переходных процессов могут быть применены как системы реостатного регулирования скорости так и системы с индивидуальными преобразователями. При глубоком регулировании скорости в большинстве случаев вопрос решается в пользу приводов постоянного тока. Однако конкурентными по своим свойствам являются приводы с частотным и частотно-токовым управлением. Преимущества приводов с асинхронными двигателями – простота конструкции и повышенная надежность двигателей возможность их изготовления в поточном производстве.
Препятствием к быстрому внедрению частотно-регулируемых приводов является сложность систем управления что приводит к недостаточной надежности их работы и повышенной стоимости. Появление на мировом рынке частотно-регулируемых электроприводов с микропроцессорным управлением повышает их надежность но стоимость их не снижается.
Сравнением основные характеристики электроприводов постоянного тока и переменного тока в промышленном применении
Сравнение проводится между 6-пульсными 3-фазными тиристорными приводами постоянного тока с независимым возбуждением [далее называемыми ППТ] и 3-фазными приводами переменного тока на базе преобразователя частоты с широтно-импульсной модуляцией и асинхронного двигателя [далее называемыми ЧРП – частотно регулируемый привод] в следующих типовых категориях:
ППТ - P = 11 kW 5200 U = 200 V 1190 V
ЧРП - P = 0.75 kW 2000 U = 380 V 690 V
Привод постоянного тока Частотно-регулируемый привод
В первом приближении существенных отличий между этими приводами не так и много; однако при более детальном рассмотрении выявляются характерные особенности приводов и различие физических принципов функционирования
Различия между тиристорными преобразователями постоянного тока и преобразователями частоты
Коммутация и преобразование электрической энергии:
Структурная схема 1-квадрантного электропривода постоянного тока. Переход тока от одного тиристора к другому начинается с пускового импульса и после этого продолжается в линейно взаимосвязанном режиме. Это значит что напряжение между коммутируемыми фазами сети поляризуется таким образом что ток вновь открываемого тиристора увеличивается и запирает предшествующий тиристор снижая его ток до ноля. Коммутация тиристоров производится естественным путем (напряжением сети) при переходе тока через ноль и запирание тиристоров происходит без каких-либо проблем даже при значительной перегрузке. Поэтому тиристоры могут выбираться не по пиковому току а по среднедействующему номинальному току нагрузки.
Схема структурная преобразователя частоты
Рис. 3.2.1. Типовая схема преобразователя частоты
На рис. 3.2.1 показан состав силовой части такого преобразователя частоты: сеть переменного тока – неуправляемый выпрямитель В –шины постоянного тока - конденсатор LC-фильтра – автономный инвертор напряжения И с широтно-импульсной модуляцией (ШИМ) – асинхронный двигатель АД к которому приложено переменное 3-фазное напряжение с регулируемой частотой f = var и амплитудой U =var ; управление инвертором осуществляется блоком управления БУ.
Хотя входной выпрямительный мост преобразователя частоты работает подобно приводу постоянного тока однако выпрямленный им ток должен быть преобразован обратно в 3-х фазный переменный с помощью инвертора. Так как у постоянного тока нет никаких переходов через ноль то переключающие элементы (IGBT транзисторы) должны прерывать полный ток нагрузки. Когда IGBT транзистор закрывается ток проходит через обратный диод на противоположный полюс напряжения постоянного тока. Переключение происходит без контроля напряжения но оно возможно в любое время независимо от формы сетевого напряжения.
Коммутация в преобразователях частоты происходит с большой частотой и в выходном напряжении появляется высокочастотная составляющая и могут возникнуть проблемы с электромагнитной совместимостью.
В преобразователях постоянного тока есть только один контур преобразования энергии (AC DC). В преобразователях частоты два контура преобразования энергии (AC DC и DC AC) т.е. потери мощности удваиваются по сравнению с приводами постоянного тока.
Потери мощности полученные эмпирическим путем следующие: ППТ – 0.8 % 1.5 % от номинальной мощности; ЧРП – 2 % 3.5 % от номинальной мощности.
Место требуемое для размещения шкафа преобразователя мощностью от 100 kW: ППТ – 100 % ЧРП – 130 % 300 %. Это преимущество приводов постоянного тока обуславливает уменьшение размера и стоимости электрошкафа и системы охлаждения.
Сравнив достоинства и недостатки привода постоянного тока и привода переменного тока выбираю частотно-регулируемый привод.
Сравнительная характеристика синхронного сервопривода на постоянных магнитах и асинхронного сервопривода
Синхронные двигатели на постоянных магнитах
–хорошая управляемость (стабильность скорости);
–большая величина отношения мощностьразмер;
–не требуют обслуживания (нет щёток);
–высокая перегрузочная способность (до 5·Tном);
–пониженный нагрев при малых скоростях;
–высокий динамический коэффициент (Tma
–большой диапазон регулирования (до 32000);
–высокая точность позиционирования;
–обеспечение удержания вала при нулевой скорости.
–Высокая стоимость преобразователя и двигателя;
–Не работает без датчика обратной связи;
–Ограничение максимальной скорости.
Трехфазные асинхронные двигатели (с энкодером)
–большая максимальная скорость;
–обеспечение удержания вала при нулевой скорости;
–может работать без датчика обратной связи.
–нагрев при малых скоростях -> независимая вентиляция;
–перегрузочная способность (до 3 · Tном);
–высокая стоимость (преобразователь энкодер);
–не большая величина отношения мощностьразмер.
Сравнение двух приводов в табл. 3.2.1.
Номинальная мощность: 075 кВт
Ном. скорость: 2825 обмин
Ном. скорость: 3000 обмин
Ном. момент: 25 Н · м
Ном. момент: 24 Н · м
Макс. момент: 66 Н · м
Макс. момент: 120 Н · м
Момент инерции ротора:
Теоретическое время разгона до
Номинальный ток: 30 А
Номинальный ток: 26 А
Номинальное напряжение: 230 В
Номинальное напряжение: 190 В
3.Выбор комплектного силового электрооборудования
3.1.Выбор преобразователя (комплектного электропривода)
На основании требований предъявляемых к электроприводу и анализа результатов предварительной проверки двигателя по производительности нагреву и обеспечению технологических условий осуществляется выбор комплектного электропривода.
Комплектный электропривод состоит из:
силовой трансформатор (или токоограничивающий реактор);
силовой тиристорный преобразователь для питания двигателя состоящий из силовых тиристоров с системой охлаждения защитных предохранителей разрядных фильтрующих и защитных R L С - цепей;
для привода постоянного тока – тиристорный преобразователь для питания обмотки возбуждения при регулируемом магнитном потоке двигателя постоянного тока (или встроенный источник возбуждения или аппаратуру для подключения обмотки возбуждения к сети постоянного напряжения при нерегулируемом потоке двигателя);
систему импульсно-фазового управления устройства выделения аварийного режима контроля предохранителей и защиты от перенапряжений;
коммутационную и защитную аппаратуру в цепях постоянного и переменного тока (автоматические выключатели линейные контакторы рубильники);
сглаживающий реактор в цепи постоянного тока (при необходимости);
устройство динамического торможения (при необходимости);
шкаф высоковольтного ввода (при необходимости);
систему управления электроприводом;
комплект аппаратов приборов и устройств обеспечивающих оперативное управление контроль состояния и сигнализацию электропривода;
узлы питания обмотки возбуждения тахогенератора и электромеханического тормоза.
При выборе модели частотного преобразователя следует исходить из конкретной задачи которую должен решать электропривод:
–типа и мощности подключаемого электродвигателя
–точности и диапазона регулирования скорости
–точности поддержания момента вращения на валу двигателя.
При работе со стандартным асинхронным двигателем преобразователь следует выбирать с соответствующей мощностью. При выборе преобразователя для работы со специальными двигателями (двигатели с тормозами синхронные двигатели высокоскоростные и т.д.) следует руководствоваться прежде всего номинальным током преобразователя который должен быть больше номинального тока двигателя.
Для увеличения точности поддержания момента и скорости на валу двигателя в наиболее совершенных преобразователях реализовано векторное управление позволяющее работать с полным моментом двигателя в области нулевых частот поддерживать скорость при переменной нагрузке без датчиков обратной связи точно контролировать момент на валу двигателя.
где Iн Uн – номинальные значения тока и напряжения двигателя; Iнтп Uнтп – номинальные значения тока и напряжения преобразователя.
Исходя из технологических требований предъявляемых к электрооборудованию выбираю комплектный электропривод главного движения 690C-011-4-BS с двигателем MA-100 P-FB с принудительным охлаждением. Совместное комплектное решение для станочного оборудования мировых производителей фирмы «Балт-Систем» (Россия) и фирмы «SSD Parvex» (Франция).
Технические данные приведены в табл. 3.3.2.1.
Макс. мощность двигателя кВт
Мощность преобразователя кВА
Основные характеристики асинхронного двигателя главного движения в табл. 3.3.2.2.
В качестве привода подач комплектный привод подачи НА-075-HM-13-17.0-020-Z (Япония) (максимальный ток Imax=75 А) с синхронными вентильными электродвигателями HM переменного тока с возбуждением от постоянных магнитов.
Характеристики сервопривода серии НА приведены в табл. 3.3.2.3.
Наименование комплектного
Характеристики синхронного электродвигателя подач в табл. 3.3.2.4.
Электродвигатель оси Z
Привод главного движения 690 P+ с двигателем серии MA
Векторный привод главного движения серии 690 P+
Векторный привод главного движения построен на базе 32-битного микропроцессора и предназначен для управления асинхронным двигателем. Продукция компании PARVEX.
Векторное управление по потоку. Превосходные параметры в режиме регулирования с разомкнутым контуром: крутящий момент 150% при частоте 0.5 Гц.
Бесшумная работа. Режим бесшумной работы без снижения тока (за счет повышения несущей частоты).
Широкий выбор дополнительных карт: сетевые интерфейсы функции ПЛК интерфейс Mechatrolink аналоговые и дискретные входывыходы и т.п.
Программное обеспечение для программирования: CX-drive для настройки параметров .
CASE (прикладное программное обеспечение для инверторов) и дополнительная карта с функциями ПЛК.
Диапазон регулирования скорости:
–1:40 (Vf-регулирование)
–1:100 (векторное управление с разомкнутым контуром)
–1:1000 (векторное управление с замкнутым контуром)
Реакция на управляющее воздействие по скорости 5 Гц регулирование без PG) 30 Гц (регулирование с PG).
Ограничения крутящего момента предусмотрено отдельно для каждого из 4 секторов путем настройки констант.
Погрешность регулирования крутящего момента± 5%
Диапазон частоты 001 - 150 Гц (повышенная нагрузка)
1 - 400 Гц (обычная нагрузка 1 или 2)
Разрешение по выходной частоте 001 Гц
Рабочая температура окружающей среды -10 +40°C (IP20)-10 +45°C (IP00)
Номинальное входное напряжение VAC (5060 Гц) 3х400 В +10% -15%
Номинальное выходное напряжение VAC (5060 Гц) 3х400 В
Асинхронный двигатель главного движения имеет высокие динамические и скоростные характеристики:
Управляется приводом серии 690 P+;
Инкрементальный встроенный энкодер;
Встроенный вентилятор.
Привода данного типа разработаны для использования в станках в качестве шпиндельного привода совместно с асинхронными двигателями переменного тока (например: серии МА) и имеют в зависимости от типа (BCDEF) максимальную мощность 0.37-1000 kW.
Привода могут использоваться как с пассивным резистором сброса энергии двигателя так и совместно с дополнительным рекуперативным 4-Q блоком при больших мощностях.
Схема имеет 4 конфигурируемых 10 битных аналоговых входа и 3 выхода.
Также имеется 8 переназначаемых дискретных (+24 вольт) входа и 3 релейных выхода (3А 230V).
Привод может использоваться без датчика обратной связи по скорости (режим sensorless – точность поддержания скорости 1%) и с энкодером находящимся на валу двигателя - режим closed loop vector (точность поддержания скорости 0.1 %).
Подключение датчика обратной связи производится через терминал С (сигналы) и терминал В (питание энкодера его напряжение выставляется переключателем от 5 до 24 вольт) при этом входное напряжение для блока питания датчика (выводы 1 разъемов А и В) можно использовать от внутреннего источника +24 вольт привода (выводы 1120 разъема ТВ1).
Алгоритм работы контроллера привода находится во внутренней флэш памяти и может быть изменен при помощи внешней программы (например CELite) находящейся на соединенном с приводом через RS 232 компьютере в памяти привода находится несколько стандартных вариантов алгоритма (MACRO 1-9) к которым можно вернуться если попытка изменения алгоритма оказалась неудачной. С пульта управления приводом по умолчанию загружается MACRO 1.
Электроприводы подачи серии HA-HM
Электропривод серий HA-HM (далее – электропривод) представляет собой регулируемые (следящие) однокоординатные реверсивные электроприводы переменного тока с длительным моментом на валу от 10 до 480 Нм. Электропривод применяются для быстродействующих механизмов подачи металлообрабатывающих станков в том числе с числовым программным управлением для исполнительных механизмов промышленных роботов механизмов гибких производственных систем и для других механизмов следящих систем которые требуют точных перемещений и регулирования скорости вращения в широком диапазоне.
В состав электропривода серии HA-HM входят преобразователь серии HA и электродвигатель серии HM.
Электродвигатель HM представляет собой синхронный вентильный электродвигатель переменного тока с возбуждением от постоянных магнитов расположенных на роторе. Электродвигатель HM имеет трёхфазную обмотку якоря. Фазные обмотки якоря электродвигателя соединены треугольником. Синусоидальная форма тока через фазные обмотки якоря двигателя позволяет обеспечить сглаживание кривой момента при низкой скорости вращения требуемое в металлообработке текстильной промышленности упаковочных машинах и т.д.
Электродвигатель HM имеет бесконтактный комбинированный фотоэлектрический датчик (энкодер) который совмещает функции датчика положения ротора (ДПР) и датчика угловых перемещений (2500 импульсов на один оборот). ДПР обеспечивает правильную работу электронного коммутатора во время пуска электродвигателя и в его рабочем режиме. Датчик угловых перемещений преобразует измеряемое перемещение в последовательность электрических сигналов которая несёт в себе информацию о величине и направлении перемещения. Этот датчик выполняет функцию датчика обратной связи (ДОС) в следящих системах.
Преобразователь HA обеспечивает управление электродвигателем HM. Преобразователь HA построен на базе силовых ключей на IGBT транзисторах которые представляют собой комбинацию биполярного и полевого транзисторов.
Преобразователь имеет микропроцессорное управление на основе усовершенствованного 16 разрядного DSP контроллера (Digital Signal Processor) для обеспечения цифрового контроля по скорости и по положению.
Преобразователь HA имеет встроенный блок питания. Конструктивно преобразователи HA выпускают в блочном варианте исполнения они имеют цифровую панель оператора с дисплеем и четырьмя кнопки управления. Основная управляющая программа контроллера хранится в EEPROM (ППЗУ). Меню оператора включает пять режимов.
Используя программное обеспечение панель индикации и кнопки управления можно установить один из режимов работы преобразователя выбрать электродвигатель с которым может работать преобразователь и настроить его рабочие параметры отобразить на панели индикации состояние электропривода редактировать ранее введённые параметры вернуть исходные значения параметров установленные фирмой-изготовителем.
Питание электроприводов производится от трёхфазной промышленной сети переменного тока частотой 50 (60) Гц с линейным напряжением:
0 В – для серии HA-HM.
При подключении электроприводов к сети питания необходимо соблюдать следующие требования:
–электроприводы серии HA-HM допускается подключать к трёхфазной сети 380 В без входного трансформатора.
Электроприводы могут быть двух типов: без тормоза и со встроенным тормозом для фиксации оси станка при пропадании питающего напряжения.
По виду управления электроприводы являются цифроаналоговыми. Электроприводы имеют обратную связь как по скорости так и по положению.
На рис. 3.3.1. приведена функциональная схема электропривода в режиме контроля скорости.
Рис. 3.3.1. Схема функциональная электропривода в режиме контроля скорости
На рис. 3.3.2. приведена функциональная схема электропривода в режиме контроля по положению.
Рис. 3.3.2. Схема функциональная электропривода в режиме контроля по положению
Рис. 3.3.3. Структура условного обозначения электроприводов серии HA-HM
Схемы соединений электропривода серии HA-HM
Электропривод серии HA-HM состоит из преобразователя серии HA и электродвигателя серии HM. Соединение составных частей электропривода серии HA-HM между собой показано на рис. 3.3.4.
Рис. 3.3.4. Соединение составных частей электропривода серии HA-HM
Интерфейс преобразователя
Характеристики входных сигналов:
) вид входного сигнала – напряжение постоянного тока;
) уровень входного сигнала:
- логический «0» – 0-7 В;
- логическая «1» – 15-30 В.
) номинальный входной ток – 16 мА24 В;
) электрическая прочность оптоизоляции – 1500 В не менее.
Характеристики выходных сигналов:
) тип выхода – открытый коллектор;
) коммутируемое напряжение – 15-30 В;
) номинальный выходной ток – 40 мА24 В.
- тип входа – дифференциальный;
- амплитуда сигналов – 0-5 В;
- диапазон входного тока – 7-15 мА.
- входное сопротивление – 10 кОм;
- входное напряжение +- 10 В.
Вид преобразователя – транзисторный
Диапазон регулирования скорости – 1:10000
Внешнее дополнительное питание – +24 В100мА
Допустимые отклонения питающей сети:
– напряжение питающей сети – от минус 20 до плюс 15% от номинала
– частоты питающей сети – +2% от номинала
4.Проверка работоспособности электропривода и электрооборудования
4.1.Построение тахограммы
Для построения тахограммы привода продольной подачи необходимо определить время протекания расчетных режимов резания в соответствии с заданным технологическим процессом.
Определим время пуска и торможения для каждого режима работы
где – частота вращения двигателя в конце переходного режима радс; E – допустимое ускорение электропривода E =100радс2. Полученные результаты приведены в табл. 3.4.1.1.
Результаты расчета времени переходных процессов
Ускоренные перемещения
Время точения заготовки длинной 140мм определим по формуле
где V – поступательная скорость суппорта для заданного режима резания ммин.
Время точения заготовки
Для построения тахограммы необходимо определить величину и время перемещения суппорта на холостом ходу и при возврате в исходное при ускоренных перемещениях.
Найдем ускорения суппорта в переходных режимах
Определим перемещения суппорта в переходных режимах
где a – ускорение суппорта ммин2; t – время пуска или торможения для расчетного режима работы привода.
Для чернового точения
для ускоренных перемещений
Тогда перемещения на холостом ходу для режимов точения определим:
где lп – перемещения во время переходных режимов для чернового и чистового точения.
Перемещение суппорта на холостом ходу при ускоренных перемещениях определяется
Перемещения суппорта в переходных режимах
Время перемещения на холостом ходу для каждого из режимов определим по формуле
Тогда для чернового точения
для возврата в исходное положение на быстром ходу
Произведем расчет всех временных интервалов технологического процесса.
c – время паузы между операциями необходимое для подвода отвода резца.
Тахограмма для чернового точения изображена на рис. 3.4.1.1.
Рис. 3.4.1.1 Тахограмма чернового точения
Возврат суппорта в исходное положение на ускоренном ходу
Тахограмма для возврата в исходное положение изображена на рис. 3.4.1.2.
Рис. 3.4.1.2 Тахограмма возврата в исходное положение
Тахограмма для чистового точения изображена на рис. 3.4.1.3.
Рис. 3.4.1.3 Тахограмма для чистового точения
Интервал времени t20=3мин=180с время необходимое для смены заготовки.
Результаты расчета всех временных интервалов приведены табл. 3.4.1.4.
Результаты расчета тахограммы
Продолжение табл. 3.4.1.4
4.2.Построение нагрузочной диаграммы
Для построения нагрузочной диаграммы необходимо определить величину моментов на данных промежутках времени.
Динамический момент при разгоне определяется
где E – допустимое ускорение радс2 положительная величина которого принимается при пуске а отрицательная при торможении; JΣ – суммарный момент инерции механической передачи и двигателя кгм2;
Момент холостого хода принимаем
При пусках и торможениях суммарный момент равен
При ускоренных перемещениях и при перемещениях на рабочих подачах без нагрузки:
Произведем расчет моментов приведенных к валу двигателя для каждого режима в соответствии с временными интервалами тахограммы.
Нагрузочная диаграмма для чернового точения приведена на рис. 3.4.2.1.
Рис 3.4.2.1 Нагрузочная диаграмма чернового точения
Нагрузочная диаграмма для возврата в исходное положение приведена на рис. 3.4.2.2.
Рис. 3.4.2.2 Нагрузочная диаграмма возврата в исходное положение
Нагрузочная диаграмма для чистового точения приведена на рис. 3.4.2.3.
Рис. 3.4.2.3 Нагрузочная диаграмма чистового точения
Все данные расчетов сведены в табл. 3.4.2.1.
Результаты расчета нагрузочной диаграммы
Полная тахограмма и нагрузочная диаграмма приведена на рис. 3.4.2.4.
Рис. 3.4.2.4. Тахограммма и нагрузочная диаграмма
4.3.Проверка работоспособности электропривода
Предварительная проверка работоспособности электропривода привода продольной подачи производится на основании нагрузочной диаграммы. Будем считать что механическая часть имеет прочную структуру. Слабым звеном будем считать двигатель.
Для проверки работоспособности электропривода по условиям нагревания двигателя следует использовать один из методов эквивалентных величин.
При расчете электропривода работающего в повторно-кратковременном режиме (S3) эквивалентный за время работы момент определенный на основе нагрузочной диаграммы следует сопоставить с номинальным для данного двигателя моментом при той же продолжительности включения.
Если двигатель работоспособен то энергетическая часть устойчива.
Работоспособность по перегрузке:
Проверку работоспособности электропривода проведем методом эквивалентного момента. В данном случае МI.
где αi – коэффициент теплоотдачи для каждого участка тахограммы ti – временной интервал тахограммы.
Для самовентилируемых двигателей коэффициент αi учитывающий изменение условий охлаждения двигателя при изменении скорости вращения его вала следует определять следующим образом:
если скорость двигателя изменяется и ma
если скорость двигателя постоянна и maxн.
В приведенном алгоритме max соответствует максимальному значению скорости вращения достигаемой на i-м участке.
Коэффициент a0 характеризует условия охлаждения для неподвижного двигателя. Для двигателей закрытого исполнения можно принять a0=05.
По условию 3 определим значение ai для установившихся режимов
Для ускоренных перемещений ai=1 так как двигатель работает со скоростью выше номинальной
При =0 принимают ai=0.5
Для переходного процесса принимают среднее значение α между началом и концом переходного процесса
Для удобства расчета все расчетные параметры сводим в табл. 3.4.3.1.
Результаты расчета коэффициента теплоотдачи
Так как двигатель работает в повторно-кратковременном режиме то необходимо привести его к режиму S1.
Определим продолжительность включения как отношение время работы Тр ко времени цикла Тц
Так как реальная продолжительность включения не совпадает со стандартной продолжительностью включения эквивалентный момент пересчитывается по формуле
где ст=06 – стандартная продолжительность включения.
Номинальный момент двигателя больше эквивалентного следовательно выбранный двигатель по условиям нагревания работоспособен.
5.Выбор способа подвода электропитания
Потребителями электроэнергии на участке являются небольшие по мощности металлообрабатывающие станки. Все приемники рассчитаны на трехфазный переменный ток и напряжение 380 В промышленной частоты устанавливаются стационарно и по площади распределены равномерно.
Для приема и распределения электроэнергии к группам потребителей применяют силовые распределительные шкафы и пункты (РП). Сеть от КТП №53 до РП-18А выполненная по радиальной схеме кабелем уложенным в изоляционных трубах в полу.
Для цехов с нормальными условиями окружающей среды изготовляют шкафы серий СП-62 защищенного исполнения а для пыльных и влажных - шкафы серий СПУ-62. Шкафы имеют на вводе рубильник а на выводах - предохранители типа ПН2 или НПН2. Номинальные токи шкафов СП-62 составляют 250 А а шкафов СПУ-62 - 175 А.
Силовые пункты и шкафы выбирают с учётом окружающей среды числа подключаемых приемников электроэнергии к силовому пункту и их расчётной нагрузки (расчётный ток группы приёмников подключаемых к силовому пункту должен быть не больше номинального тока пункта Iрасч ≤ Iном).
В качестве распределительного шкафа (пункта) используется шкаф силовой распределительный СПУ-62 изображенном на рис. 3.5.1. с вводным рубильником и предохранителями на 8 присоединений к электроприемникам. Для размыкания контактов рубильника и снятия напряжения со всех предохранителей предусмотрена рукоятка 7 выведенная наружу. Шины 1 3 4 соединены с рубильником 6 и предохранителями 8. К зажимам 9 предохранителей подсоединяются провода групповых щитов или электрических приемников.
Рис 3.5.1. Силовой распределительный шкаф СПУ-62: а - общий вид; б – схема электрическая
Технические параметры приведены в табл. 3.5.1
Номинальное напряжение В:
Количество отходящих линий
Расположение силовых пунктов (РП) и трасс кабельных линий приводится на рис. 3.5.2.
Рис. 3.5.2. План расположения электрооборудования инструментального отделения
6.Расчет сечения питающих линий. Проверка на нагрев и просадку напряжения
Исходными данными для проведения расчетов являются схема цеховой электрической сети с расположением аппаратов защиты Uн сети расчетные получасовые максимумы нагрузки каждого участка сети Рмах пиковые (пусковые) токи на различных уровнях схемы номинальные мощности ЭП.
Выбор сечения проводника связан с выбором аппаратов зашиты поэтому выбор сечения проводника цеховой сети и защитных аппаратов выполняется совместно.
Для сетей напряжением до 1 кВ определяющим в выборе сечения проводника являются не экономические а технические требования и условия: нагрев проводников их механическая прочность потери напряжения термическая устойчивость к токам КЗ.
Согласно рекомендаций ПУЭ расчету по экономической плотности тока не подлежат силовые сети до 1 кВ при числе часов использования максимума нагрузки (Тм) менее 4000-5000 часов и все осветительные сети.
В связи с многообразием режимов работы ЭП (по Тм) совместным питанием силовой и осветительной нагрузок в проектной практике при расчете цеховых сетей напряжением до 1 кВ любого назначения фактор экономической плотности тока как правило не учитывается [8]. Практически по экономической плотности тока рассчитываются лишь сети постоянного тока в электролизных установках для которых Тм>8000 часов. Практика показала что выбранные по экономической плотности тока сечения проводников в сетях напряжением до 1 кВ в 2-3 раза превышают расчетные сечения по техническим условиям.
Выбор сечений проводников по техническим условиям включает:
–выбор по условиям теплового нагрева;
–по их пропускной способности и условиям зашиты;
–потерям напряжения;
–термической стойкости к токам КЗ;
–механической прочности.
На механическую прочность проверяются голые провода и принимаются сечения из условий механической прочности для алюминиевых проводов S > 35 мм2 и стальных S> 25 мм2.
Сечение проводника в основном зависит от величины расчетного тока (Iр) от того требуется ли защищать сеть от перегрузки или нет от температурных условий окружающей среды характера помещения и типа изоляции проводника. Прежде необходимо выбрать марку проводника определиться с условиями его прокладки и затем выполнять расчет.
Сечение проводников цеховой сети выбирается по расчетному току нагрузки таким образом чтобы проводники при токах нагрузки соответствующих работе в длительном режиме и условиям нормированной для них температуры среды не перегревались бы сверх допустимых пределов.
За расчетный ток нагрузки принимается максимальная токовая нагрузка за получасовой интервал времени Im вычисленная по
Выбор сечения проводников производится по таблицам ПУЭ «Длительно допустимые нагрузки» при этом должно быть выполнено условие когда
где Iдоп - длительно допустимый ток нагрузки на провода кабели и шины для данного сечения по ПУЭ.
При прокладке нескольких кабелей и более четырех проводов в одной трубе траншее лотке коробе и т.п. в расчетную формулу (4.1) вводится коэффициент Кпрокл поправочный коэффициент на условия прокладки проводов и кабелей
При нормальных условиях (на открытом воздухе один кабель) Кпрокл = 10; в остальных случаях его значение определяется по табл. 1.3.3 [10]. Например Кпрокл = 0.68 - для 5-6 проводов в одной трубе. Кпрокл = 0.63 - для 7-9 проводов.
Согласно ПУЭ для силовых сетей отклонение напряжения от номинального должно составлять не более ± 5% Uн. Для осветительных сетей промышленных предприятий и общественных зданий допускается отклонение напряжения от +5 до -25% Uн для сетей жилых зданий и наружного освещения ±5% Uн. Эти требования обусловлены тем что величина вращающего момента асинхронных электродвигателей пропорциональна квадрату подведенного напряжения и его уменьшение может не обеспечить пуск механизмов в сетях освещения снижение напряжения приводит к резкому уменьшению светового потока.
Потеря напряжения в сети определяется по формуле %
где Iр – расчётный ток линии на данном участке А; L – расстояние от точки питания до точки приложения равнодействующей нагрузки км; rо cosj – коэффициент мощности данного участка о.е.; Uл – линейное напряжение равное 380 В.
Активное сопротивление проводов и кабелей определяется по справочной литературе или из выражения
где γ [мОм мм2] - удельная проводимость (для алюминия γ = 30 для меди γ = 50); s - сечение фазы проводника [мм2].
Расчётную максимальную токовую нагрузку линии питающей РП-18А определяем по установленной (номинальной) мощности станка Руст которую с некоторыми допущениями можно принять равной сумме номинальных мощностей двигателей станка.
От данного РП запитано 6 станков наименование и мощность указана в табл. 3.6.1.
Токарно-винторезный станок с ЧПУ мод.16А20Ф3
Токарно-винторезный станок мод.16К20
Токарно-винторезный станок мод. 1М65
Токарный универсальный станок мод. ТNА- 400 «ТRAUB»
Расчетный ток линии питающей РП-18А найдем по формуле (3.6.1)
Ориентируемся на применение одножильных медных проводов с резиновой изоляцией; прокладка в трубе. По табл. 4.1 [7] принимаем сечение 70 мм2; допустимая токовая нагрузка при прокладке трёх одножильных проводов в одной трубе Iдоп = 210 А. Для питания РП принимается марка провода ПРТО 3(1*70) рекомендуемая для прокладки в несгораемых трубах.
Для выбранного провода по (3.6.2)
Условие выполняется.
Далее определяются sinj нагрузки данной КЛ
По [7] провод с медными жилами имеет следующие значения: r0 = 0265 Омкм x0 = 0082 Омкм.
Потеря напряжения в линии %
Значит потеря напряжения в проводе не превышает допустимого значения 5%.
6.1.Расчёт и выбор сечений и типа питающего кабеля станок
Расчётную максимальную токовую нагрузку определяем по установленной (номинальной) мощности станка Руст которую с некоторыми допущениями можно принять равной сумме номинальных мощностей двигателей станка Руст = 24 кВт.
Расчетный ток линии питающей станок
Для питания по табл. 4.1 [7] для прокладки принимается провода с медной жилой марки АПВ 4 (1*16) проложенные в одной трубе Iдоп = 46А в оплётке из хлопчатобумажной ткани.
Для выбранного провода
По [7] провод с медными жилами имеет следующие значения: r0 = 037 Омкм x0 = 00625 Омкм.
Для проводов предусматриваем скрытую прокладку в изоляционных трубах в полу. Диаметр труб D выбираем по формуле
где d1 d2 .dn - наружные диаметры проводов; п1 п2 пп - число проводов и кабелей данного диаметра.
Выбранные кабели и провода питающие РП-18А и электрооборудование указаны в табл. 3.6.2.
Наименование электрооборудования
Внутрен-ний диаметр трубы мм
станок с ЧПУ м.16А20Ф3
Схема однолинейная питающих проводов электрооборудование от РП-18А изображена на рис. 3.6.1.
Рис. 3.6.1.1. Схема оборудования присоединенного к РП-18А
7.Выбор распределительного коммутационного и защитного электрооборудования
Выбор сечений проводов распределительной сети
При выборе вида электропроводки и способа прокладки проводов и кабелей должны учитываться требования электробезопасности и пожарной безопасности. Сечение проводов и кабелей цепей питания управления сигнализации измерения и т.п. должны выбираться из условия допустимого их нагрева электрическим током [10].
Условия нагрева проводов длительным расчетным током имеет вид
Iдлит. доп ≥ Iрасч(3.7.1)
а условие соответствия выбранному аппарату защиты
Iдлит. доп. ≥ КзIз(3.7.2)
где Iдлит.доп – допустимый длительный ток для провода или кабеля при нормальных условиях прокладки определяемый по таблицам допустимых токовых нагрузок на провода и кабели; Iрасч – длительный расчетный ток линии (суммируются все номинальные токи электроприемников которые получают питание по данному проводу или кабелю); Iз– номинальный ток или ток срабатывания защитного аппарата; Кз – кратность допустимого длительного тока для провода или кабеля по отношению к номинальному току или току срабатывания защитного аппарата (согласно ПУЭ для провода который защищен автоматическим выключателем Кз=1 а предохранителем Кз = 033).
При проектировании и модернизации электрооборудования для подвода электрической энергии в настоящее время применяются следующие установочные провода:
ПВ1 - провод (П) с медной жилой с поливинилхлоридной изоляцией (В). Провода изготавливаются сечением от 05 до 95 мм2. Пример полной марки: ПВ 1х15. ПВ2 - то же но гибкий. Сечение от 20 до 70 мм2. ПВ3 – повышенной гибкости. Изготавливается одножильным или двухжильным. Сечение одножильного от 05 до 95 мм2. Двухжильный - сечение от 05 до 4 мм2 каждой жилы. Примеры: ПВ3 1х25; ПВ3 2х25.
ППВ - провод с медными жилами с поливинилхлоридной изоляцией плоский (вторая П) с разделительным основанием. Выпускается одножильным сечение от 075 до 95 мм2; двухжильным и трехжильным - сечением от 075 до 4 мм2. Примеры: ППВ 1х15; ППВ 2х15; ППВ 3х15.
Установочные провода выпускаются также и с алюминиевыми жилами. Эти провода изготавливаются одно- двух- и трехжильными. Примеры обозначений: АПВ 1х25; АПВ 3х25; АППВ - 2х25.
При значительных токах в основном для питания силовых элементов станка (электродвигателей электромагнитов и т.д.) могут применяться кабели.
Выбор автоматических выключателей
При эксплуатации оборудования возможны нарушения нормального режима работы:
–короткие замыкания.
–выбор аппаратуры защиты производятся с учетом требований:
–номинальный ток и напряжение аппарата защиты должно соответствовать расчетному длительному току и напряжению электрической цепи;
–время действия аппаратов защиты должно быть по возможности меньшим и должна обеспечить селективность действия защиты;
–аппараты защиты не должны отключать установку при перегрузках возникающих в условиях нормальной эксплуатации.
Выбор автоматических выключателей производится по номинальным напряжению и току с соблюдением условий
Uном.а≥Uном.с (3.7.3)
где Uном.а - номинальное напряжение автоматического выключателя; Uном.с - номинальное напряжение сети;
Iном.а ≥ Iдлит(3.7.4)
где Iном.а - номинальный ток автоматического выключателя; Iдлит - длительный расчетный ток цепи.
Кроме того должны быть правильно выбраны:
–номинальный ток расцепителей Iном.расц.;
–ток уставки электромагнитного расцепительного элемента комбинированного расцепителя Iуст.эл.мат.;
–номинальный ток уставки теплового расцепителя или теплового элемента комбинированного расцепителя - Iном.уст.тепл.
Номинальные токи электромагнитного теплового или комбинированного расцепителя должны быть не меньше номинального тока двигателя
Iном.расц≥ Iном.дв.(3.7.5)
Ток уставки электромагнитного расцепителя (отсечки) или электромагнитного элемента комбинированного расцепителя с учетом неточности срабатывания расцепителя и отклонений действительного пускового тока от паспортных данных выбирается из условия
Iуст.эл.магн≥125·Iпуск (3.7.6)
где Iпуск - пусковой ток двигателя.
Номинальный ток уставки теплового расцепителя или теплового элемента комбинированного расцепителя
Iном.уст.тепл≥ Iном.дв.(3.7.7)
Так же выбираются уставки расцепителей автоматических выключателей и для защиты цепей других электроприемников разумеется если в этом возникает необходимость так как в большинстве случаев для защиты электроприемников малой мощности по соображениям чувствительности оказывается необходимым применять плавкие предохранители. При этом надо учитывать что если автоматический выключатель с электромагнитным расцепителем устанавливается в цепях электроприемников при включении которых не возникают броски пускового тока то ток уставки электромагнитного расцепителя в этом случае должен выбираться минимально возможным.
Контактор (модульный контактор силовое реле) - это дистанционно управляемый коммутационный аппарат позволяющий коммутировать мощные (в том числе индуктивные) нагрузки как переменного так и постоянного тока. Основной особенностью контакторов является то что они разрывают токовую цепь в нескольких точках одновременно в отличие от электромагнитных реле которые обычно разрывают цепь в одной точке.
Основные области применения контакторов: управление мощными электродвигателями коммутация цепей компенсации реактивной мощности и т.п. - там где необходимо осуществлять частые пуски коммутацию электрических устройств с большими токами нагрузки. Контакторы имеют следующие основные узлы: контактную и дугогасительную системы электромагнитный механизм и систему блок-контактов. В контакторах с электромагнитным приводом главные и вспомогательные контакты связаны непосредственно с якорем электромагнита управляющего включающей катушкой.
Электромагнитные контакторы делятся на контакторы постоянного тока контакторы переменного тока и контакторы постоянно-переменного тока. Контакторы переменного тока применяются для управления асинхронными трехфазными двигателями с короткозамкнутым ротором для выведения пусковых резисторов включения трехфазных трансформаторов нагревательных устройств тормозных электромагнитов и других электротехнических устройств. Контакторы постоянного тока применяются для включения и отключения приемников электрической энергии в цепях постоянного тока; в электромагнитных приводах высоковольтных выключателей; в устройствах автоматического повторного включения.
По номинальному напряжению главной цепи контакторы делятся 2 группы: с напряжением 220 440В и 380 660В. Контакторы могут иметь от 1 до 5 главных полюсов.
Описание защит и блокировок
При включении станка QF1 в цепи QF3-AV1-AV2-QF9 происходит ввод в работу блоков питания входов-выходов УЧПУ NC 201. Далее идет проверка состояния аварийных кнопок «СТОП» (пульт управления УЧПУ) и конечников крайних положений рабочих органов станка (SQ26 - крайнее положение оси Z). При нормальном состоянии блоки входов УЧПУ. После тестирования УЧПУ и при наличии нормальной работы блока питания входных сигналов (провод 15) включается реле SPEPN (УЧПУ) собирается цепь питания блоков выходных сигналов УЧПУ и контакторы питания привода главного движения КМ6 привода подачи КМ10.
В момент возникновения аварийной ситуации (срабатывание аварийной кнопки «СТОП» наезд на конечник аварийного останова (SQ26 SQ27 SQ28) отключается реле КМ12 обесточиваются блоки входов-выходов УЧПУ привода главного движения и подачи. Съезд с аварийных конечников положения возможен при нажатой кнопке SB5.
Цепи питания блоков AVI AV2 УЧПУ освещение шкафов управления выполнены через развязывающие трансформаторы Т1 Т2 защищены автоматическими выключателями QF2 QF5 QF10 QF3 QF4 QF8 QF9.
Привод главного движения и привод подач кроме штатных встроенных устройств защищены автоматическими выключателями QF15 QF18. QF16 защищает вентилятор охлаждения двигателя главного движения.
7.1.Выбираем кабель для питания двигателя М1 М3 и защитный аппарат
Прежде чем провести выбор автоматического выключателя главного двигателя QF15 по основным техническим параметрам необходимо рассчитать номинальный и пусковой токи двигателя
Iном.расц.≥ 125Iном.дв = 125222=2775 А;
Iном.авт ≥ Iном.расц.
Для защиты ответвления к данному электродвигателю по каталогу исходя их стандартной мощности трехфазных двигателей 50 Гц по категории АС-3 выберем комбинированный пускатель LC1-D25 со встроенной защитой от перегрузки трехполюсный автоматический выключатель фирмы Schneider El. GV2_ME 3 (с кнопками) имеют комбинированный термомагнитный расцепитель обеспечивая защиту от токов КЗ и при тепловой перегрузке на номинальный ток 32 А. [11]
Комбинированные пускатели прямого включения нереверсивные от 006 кВт до 15 кВт при 400415 В координация: тип 1.
Пускатели в сборе включают в себя:
–1 автоматический выключатель серии GV2_
–1 трехполюсный контактор;
–1 блок GV2_AF3 для соединения автоматического выключателя и контактора.
Пускатели электромагнитные LC1-D25 предназначены для дистанционного пуска непосредственным подключением к сети остановки и реверсирования трехфазных асинхронных электродвигателей с короткозамкнутым ротором при напряжении до 660В переменного тока частотой 50Гц а в исполнении с трехполюсными тепловыми реле серии LR1-D - для защиты управляемых электродвигателей от перегрузок недопустимой продолжительности и от токов возникающих при обрыве одной из фаз.
Часто используются как четырехконтактное силовое реле.
Диапазон рабочих температур - от -40°C до +55°С. Окружающая среда - взрывобезопасная не содержащая пыли в количестве нарушающем работу пускателя а также агрессивных газов и паров в концентрациях разрушающих металлы и изоляцию. Рабочее положение - крепление на вертикальной плоскости допускается отклонение не более 30° в любую сторону. Является аналогом контакторов ПМЛ-2100 и КМИ-22510.
Принимаем номинальный ток теплового максимального расцепителя регулируемого автоматического выключателя по двум условиям
I0≥12·Iп =12154=1848 А.
Пусковой ток двигателя (его действующее значение)
Iп = kп Iном.дв = 7222 = 154 А
где Кп – кратность пуска равная 7 для АД.
где K0 – кратность отсечки.
Выбирается проводник и выбирается кабель марки ВВГ с учетом соответствия автоматического выключателя
Iдоп≥kзщ·Iу(п)=135315=425А.
При нормальных условиях прокладки в воздухе kзщ=1.
Выбираем кабель силовой кабель с медными жилами марки ВВГ 3х6+1х25 с длительно допустимым током Iдоп=50А.
Аналогичным образом выбираются кабели и аппараты защиты для двигателя М3.
7.2.Выбираем вводной автоматический выключатель
Для расчета вводного автоматического выключателя QF1 необходимо определить общий расчетный ток цепи которую защищает автоматический выключатель. В нашем случае – это суммарный рабочий ток всех электродвигателей ток схемы управления цепи освещения и электромагнита. Этот ток составляет 419 А.
Номинальный ток автоматического выключателя должен быть равен или больше этого тока. По этому же току выбирается тепловой расцепитель автоматического выключателя.
Для определения тока электромагнитного расцепителя необходимо найти пусковой ток наиболее мощного электродвигателя. В нашем случае М1 который составляет 154 А.
Выбираем автоматический выключатель серии АЕ-2053 с повышенной отключающей способностью с номинальным током на 63 А. Автоматический выключатель широкого применения. Используется для защиты потребителей в составе аппаратуры распределения электроэнергии в жилых и общественных зданиях.
Параметры и технические данные комбинированного пускателя прямого включения сведем в таблицу табл. 3.7.2.
Позиционное обозначение
Фиксированная уставка магн.
8.Выбор электронных систем управления
В последнее время заметно оживление отечественной металлообрабатывающей промышленности. Многие предприятия начинают получать заказы и вдруг обнаруживается что станочное оборудование произведенное в 70-90-х годах прошлого века большую часть времени ремонтируется. Иногда изношенность механических узлов не позволяет достичь требуемой точности но обычно оборудование не используется из-за частых отказов причем в большинстве случаев причиной сбоев является системы ЧПУ и гидравлика. И если гидравлические узлы еще можно как-то залатать то системы ЧПУ однозначно требуют замены - не только из-за физического старения электронных компонентов но и по причине морального старения - перфоленты релейные схемы управления резольверы устаревшие устройства цифровой индикации причем отсутствие запасных частей к старым системам ЧПУ затрудняет их ремонт.
Рассмотрим более подробно устройства ЧПУ выпускаемые этими фирмами в табл. 3.8.1.
Сравнение систем ЧПУ
SINUMERIK 802D в одном компоненте соединяет все необходимые блоки и коммуникации. Система ЧПУ приводы и модули входоввыходов объединяются в единую систему через общий интерфейс. Осуществляет цифровое управление максимум 4 осями и 1 шпинделем.
NC-201 применяется для управления токарными станками. Устройство предназначено для управления 3-мя осями и дискретными входамивыходами не более 4024.
NC-202 применяется для управления токарными станками. Устройство предназначено для управления 3 осями с цифровымимпульсным управлением (с дополнительным аналоговым каналом) и дискретными входамивыходами не более 4024.
Продолжение табл. 3.8.1
SINUMERIK 810D объединяет в модуле все задачи ЧПУ регулирования и коммуникации имеет 6 измерительных каналов и может осуществлять цифровое управление максимум 5 осями (или 4осями + 1 шпинделем).
NC-210 применяется для управления станками с количеством осей не более четырех и дискретными входамивыходами не более 6448. Применяется для управления фрезерными токарными газопламенными и лазерными станками.
NC-220 применяется для управления оборудованием с шаговыми приводами исполнительных механизмов. Устройство управляет 4-мя оси и дискретными входамивыходами не более 6448.
Область применения: прецизионные 2-5 координатные станки с несколькими шпинделями высокоскоростные станки обрабатывающие центры роботы-манипуляторы автоматические линии и ротационные станки.
Область применения: для комплектования деревообрабатывающего и металлообрабатывающего оборудования фрезерно-сверлильно-расточной токарно-карусельно-револьверной и шлифовальной групп а также газо-плазменного и лазерного оборудования.
Стоимость УЧПУ NC-201М 202 210 SINUMERIK 802D
Стандартное фрезерно-токарное программное обеспечение Комплект ответных частей разъёмов
Исходя из несколько готовых к производству проектов модернизации станка 16А20Ф3 стоимости замены требованиям к системе управления простоте управления выбираю УЧПУ компании «Балт-Систем» NC-201М.
Современная система ЧПУ имеет программную поддержку различных технологических операций интерактивный диалог не отнимающий много времени для программирования сложных обработок. Интерфейс УЧПУ русифицирован прост и доступен в обучении. Подобные УЧПУ предоставляют ряд преимуществ по сравнению с УЧПУ аппаратная часть которых основана на базе обыкновенного компьютера с разработанным программным обеспечением. Совершенная программная поддержка разработки программ электроавтоматики позволила сократить различные устройства электроавтоматики до минимума тем самым повысив надёжность станка в целом.
Устройство ЧПУ NC-201М представляет собой малогабаритное моноблочное одноплатное устройство для управления токарными станками.
УЧПУ NC-201М имея малые габариты (432x322x105) включает в себя мощное программное обеспечение совместимое по программным и операторским функция с УЧПУ NC-110 NC-210.
Устройство числового программного управления NC-201М применяется в машиностроении станкостроении металлообрабатывающей и в других отраслях промышленности.
УЧПУ используют как комплектующее изделие при создании комплексов «устройство - объект управления» например технологических комплексов установок высокоавтоматизированных станков и обрабатывающих центров таких групп как фрезерно-сверлильно-расточные токарно-карусельно-револьверные газоплазменные лазерные и т. д.
Представляет собой компактное модульное устройство ЧПУ в котором объединены в единое целое: блок управления пульт оператора и станочный пульт в сочетании с многофункциональным программным обеспечением.
По уровню излучаемых индустриальных радиопомех УЧПУ относится к оборудованию класса А по СИСПР 22-97.
Обозначение УЧПУ при заказе потребителем или запись его в документации другой продукции в которой оно может быть применено должно иметь вид:
«Устройство числового программного управления NC-201М ТУ 4061-004-47985865-2003» где
NC - буквенное обозначение принятое на предприятии- изготовителе;
1М - серия устройства.
УЧПУ должно эксплуатироваться в закрытых помещениях с соблюдением следующих требований к условиям эксплуатации:
температура окружающей среды от 5 до 40 °С;
относительная влажность воздуха от 40 до 80% при 25 °С.
температура окружающей среды от 5 до 50 °С;
относительная влажность воздуха не более 80% при 25 °С.
Технические характеристики УЧПУ
Количество каналов датчика перемещений- 3
Количество каналов ЦАП (14 разрядов)- 4
Количество каналов электронного штурвала- 1
Количество каналов датчика касания- 1
Количество дискретных каналов вх.вых.- 4024
ОЗУ (память УЧПУ + буфер кадра)- SDRAM: (56+8) МВ
Интерфейсы внешних устройств вводавывода:
интерфейс FDD35" (144МВ)- 1 канал на 2 FDD:
последовательный интерфейс- RS232(COM1)
интерфейс Keyboard&Mouse- клавиатурамышь
интерфейс VGA CRT- CRT монитор
интерфейс LAN- Ethernet: 10100 Мбитс
Номинальное напряжение питания- 220 В 50 Гц
Потребляемая мощность (без периферии)- 60 ВА не более
Потребляемый ток (без периферии)- 250 мА не более
Степень защиты оболочкой:
лицевая панель- IP54
Габаритные размеры (корпус А):- 432x322x105 мм
Исследовательская часть
В рамках данного проекта производится исследование динамических режимов работы асинхронного частотного электропривода главного движения с векторной системой автоматического управления и уточненная проверка работоспособности электропривода.
Исследования проводятся методом имитационного математического моделирования для чего в приложении Simulink пакета Matlab собрана модель асинхронного электропривода (рис. 4.1.) в которую вошли:
–модель АД в неподвижной системе координат;
–модель преобразователя частоты;
–векторная система автоматического управления в системе координат
–преобразователи координат;
–блоки задания управляющих воздействий;
–блоки индикации и контроля результатов моделирования.
Параметры модели асинхронного двигателя были определены на основании его паспортных данных и представлены в таблице 4.1.
Расчет параметров модели АД
Напряжение обмотки статора (линейное ном.)
Коэффициент мощности (ном.)
Скорость вращения ротора (ном.)
Момент максимальный (ном.)
Продолжительность включения
Угловая скорость вращения магн. поля (ном.)
Угловая скорость вращения ротора (ном.)
Продолжение табл. 4.1
Скольжение номинальное
Скольжение критическое
Полное сопротивление короткого замыкания (ном.)
Активное сопротивление короткого замыкания (ном.)
Активное сопротивление обмотки статора (ном.)
если R1н не задано то R1н=Rкн*sн (1+sн)
Активное сопротивление обмотки ротора (ном.)
Реактивное сопротивление короткого замыкания
Реактивное сопротивление рассеяния обм. статора (ном.)
если X1н не задано то X1н=13 Xкн
Реактивное сопротивление рассеяния обм. ротора (ном.)
Взаимная индуктивность между обм. статора и ротора
если ток хх (I0н) не задан то I0н=0.35 I1н
Индуктивность рассеяния обмотки статора (ном.)
Индуктивность рассеяния обмотки ротора (ном.)
Собственная индуктивность обмотки статора (ном.)
Собственная индуктивность обмотки ротора (ном.)
Коэффициент связи между 3ф и 2ф системами
Модуль вектора потокосцепления ротора (ном.)
Расчет параметров упрощенной модели АД (используется для синтеза САУ)
Общее активное сопротивление цепей АД
Электромагнитная постоянная времени статора (ном.)
Электромагнитная постоянная времени ротора (ном.)
Рис. 4.1. Simulink-модель электропривода
ПАСПОРТНЫЕ ДАННЫЕ АСИНХРОННОГО ДВИГАТЕЛЯ
Pn=11000мощность двигателя номинальная (Вт);
n=157.08скорость вращения двигателя номинальная (радс);
U1n=220фазное напряжение статора номинальное (В);
I1n=23ток статора номинальный (А);
Zp=2число пар полюсов;
cosφ=0.86коэффициент мощности номинальный;
fnom=50частота питающего напряжения номинальная (Гц);
prg=2.5перегрузочная способность двигателя;
Jdv=0.21момент инерции вращающихся частей двигателя (кгм2);
Mn=Pnnноминальный момент двигателя (Нм).
ПАРАМЕТРЫ МЕХАНИЧЕСКОЙ ЧАСТИ ЭЛЕКТРОПРИВОДА
Jmeh=0.2момент инерции механизма приведенный к скорости двигателя (кгм2);
J=Jdv+Jmehсуммарный момент инерции механической части электропривода (кгм2).
ПАРАМЕТРЫ МОДЕЛИ АСИНХРОННОГО ДВИГАТЕЛЯ В НЕПОДВИЖНОЙ СИСТЕМЕ КООРДИНАТ (alfa betta)
L12=0.08675максимальная взаимная индуктивность между любой обмоткой статора и любой обмоткой ротора при совпадении их осей (Гн);
L1=0.08905полная эквивалентная индуктивность обмотки статора (L1=L1s+L12) (Гн);
L2=0.09136полная эквивалентная индуктивность обмотки ротора (L2=L2s+L12) (Гн);
R1=0.2646активное сопротивление обмотки статора (Ом);
R2=0.2646приведенное к статорной обмотке активное сопротивление обмотки ротора (Ом);
F2n=0.77номинальное потокосцепление ротора (Вб);
K2=L12L2коэффициент электромагнитной связи ротора;
T1=(L1-(L12^2)L2)(R1+(K2^2) R2)электромагнитная постоянная времени статорных цепей (с);
T2=L2R2электромагнитная постоянная времени роторных цепей (с).
Usau=10базовый уровень сигналов элементов САУ;
Uogr=10уровень ограничения сигналов САУ;
Tmu=0.01некомпенсируемая постоянная времени САУ.
Kot=Usau(I1n·2.5)коэффициент обратной связи по току;
Kopt=UsauF2nкоэффициент обратной связи по потокосцеплению;
Kow=Usauwnкоэффициент обратной связи по скорости;
Krt=(R1+R2)(31·Kot·2·Tmu)коэффициент регулятора тока;
Trt=(31·Kot·2·Tmu)(R1+R2)постоянная времени регулятора тока;
Krpt=(T2·Kot)(K2·L2·Kopt·4·Tmu)коэффициент регулятора потокосцепления;
Trpt=(K2·L2·Kopt·4·Tmu)Kotпостоянная времени регулятора потокосцепления;
Krw=(Kot·J·2)(4·Tmu·Kow·3·Zp·K2)коэффициент регулятора скорости;
Trw=4·TmuKrwпостоянная времени регулятора скорости;
Результаты моделирования представлены на диаграммах рис. 4.2. – рис. 4.4. из которых следует что:
–максимальный момент развиваемый двигателем при пуске и торможении не превышает допустимых значений;
–разгон электропривода происходит за 075 с что соответствует заданным требованиям по быстродействию;
–пусковые токи не превышают 2.5·Iн.
Электропривод удовлетворяет предъявляемым к нему требованиям.
Рис. 4.2. Зависимость скорости от времени
Рис. 4.3. Зависимость момента от времени
Рис. 4.4. Зависимость действующего значения тока статора от времени
Самое главное направление в энергосбережении – снижение ненужных потерь энергии. Статистика утверждает что подавляющее большинство потерь (свыше 90%) происходит в сфере энергопотребления а вот при энергопередаче теряется максимум 10 %. Значит именно в сфере потребления нужно искать способы уменьшить потери.
Не меньшим перечнем преимуществ обладает и использование в целях экономии электроэнергии частотно-регулируемых приводов. Даже самые скромные подсчёты показывают что при использовании этих устройств уровень энергосбережения увеличивается примерно на 15-20%. Принцип действия основан на регуляции режима работы исполнительного оборудования путём подачи выходного напряжения различной частоты на контролируемые устройства. Применение преобразователей в дальнейшем позволят получить следующие преимущества:
– оптимизация рабочего режима контролируемого устройства (станка оборудования механизма) и как правило увеличение его срока службы. Не подверженное излишним нагрузкам оборудование будет находиться в более хорошем техническом состоянии;
– более удобное управление двигателем оборудования в том числе равномерный запуск и плавная остановка а также возможность обратной подачи вращения вала (реверса) двигателя. Сюда же можно отнести удобство регулирования частотой вращения. Это положительно сказывается на техническом состоянии оборудования.
– защита двигателя от перегрузок электрической сети или наоборот от недостаточного напряжения. Это очень важный положительный момент потому что предотвращает повреждение оборудования связанного с низким качеством напряжения что является актуальным.
Как видим использование энергосберегающего оборудования и рациональное использование электрической энергии ведет не только к прямому уменьшению потребления электроэнергии но и обеспечивает дополнительные преимущества. Особо актуально использование энергосберегающего оборудования на предприятиях тяжелой промышленности и на крупных производственных комплексах где нерациональное потребление электроэнергии ведёт к огромным финансовым потерям. Также разумным является использование энергосберегающих технологий в плане повышения качества электроэнергии что положительно отражается на качестве работы оборудования на сроке его службы.
Преобразователь позволяет экономить на непроизводительных затратах энергии кроме того он имеет функцию энергосбережения. Эта функция позволяет при выполнении той же работы экономить от 5 до 30 % электроэнергии путем поддержания двигателя в режиме оптимального КПД. В режиме энергосбережения преобразователь непрерывно контролирует потребление тока рассчитывает нагрузку и меняет выходное напряжение. Таким образом оптимизируется потребление мощности в соответствии с нагрузкой и повышается КПД.
1.Выбор установленной мощности и типа двигателя
Одним из важнейших организационно-технических мероприятий энергосбережения является правильный выбор установленной мощности асинхронного двигателя. Эта задача особенно актуальна при использовании нерегулируемых двигателей которые еще преобладают среди промышленных электроприводов.
Известно что при использовании АД номинальная мощность которого меньше чем требуемая по условиям работы механизма происходит перегрев электрической машины и ее преждевременный выход из строя. При завышении номинальной мощности двигателя по сравнению с требуемой возрастают капитальные затраты на электропривод не в полной мере используются заложенные в двигатель активные материалы (медь и сталь) снижается КПД и коэффициент мощности двигателя.
Энергоаудит проведенный на ряде предприятий Уральского региона показал что большинство установленных двигателей имеют завышенную мощность не соответствующую потребностям управляемого механизма а средняя загрузка двигателей по отношению к установленной мощности не превышает 04 06. Это подтверждает тот факт что в отечественной практике коэффициент загрузки двигателя зачастую равен всего лишь 03 04 т.е. КПД электропривода значительно ниже номинального [19] в то время как в промышленно развитых странах Западной Европы принято считать что средняя загрузка двигателей должна превышать 06 07. При столь низких в отечественной практике коэффициентах загрузки КПД электропривода уменьшается на 2 6 % cosφ на 20 30%. При кажущемся незначительным на первый взгляд снижении КПД недогруженных двигателей эта ситуация носящая массовый характер приводит к тому что потери электроэнергии составляют 1 15% всей вырабатываемой в стране электроэнергии. Поэтому нереально ставить задачу повсеместной замены двигателей с избыточной установленной мощностью однако при плановой замене приводных двигателей или модернизации производства целесообразно обеспечивать установленную мощность двигателей в соответствии с требованиями технологии т.е. увеличивать коэффициент загрузки двигателя. В технической литературе часто встречается такая рекомендация: если загрузка двигателя меньше 50 % то его нужно менять [19].
О важности повышения КПД нерегулируемых АД на несколько процентов говорит и тот факт что в 1970 – 1980-е гг. при существенном подорожании электроэнергии в США а затем и странах Западной Европы стали создаваться так называемые энергоэффективные двигатели в которых за счет увеличения количества активных материалов (меди и стали) обеспечивалось повышение КПД на 2 5 %. В России где стоимость электроэнергии пока еще в несколько раз ниже чем в европейских странах это направление в электромашиностроении не получило широкого развития. Повышение КПД учитывая отечественную специфику может быть получено в нашей стране повышением коэффициента загрузки двигателей.
2.Оптимизация режимов системы ПЧ-АД
Целью задачи оптимизации режимов частотно-регулируемого асинхронного электропривода является достижение экстремума функции качества (критерия оптимальности). Для электроприводов одним из важных критериев качества по энергетическим соображениям и надежности являются потери мощности. Требования оптимальности по потерям можно рассматривать по отношению к двигателю преобразователю частоты и в целом к электроприводу.
Выявление оптимального режима управления по минимуму потерь двигателя имеет значение в следующих случаях:
–при обеспечении минимума потерь для ограничения нагрева двигателя и расширения области допустимых по нагреву моментов нагрузки;
–для анализа эффективности законов частотного управления по критерию потерь при использовании в качестве эталона закона управления по минимуму потерь в двигателе.
Целью в этих случаях является обеспечение надежной работы двигателя так как даже незначительное повторяющееся превышение температуры обмотки статора сверх допустимой приводит к ускоренному старению изоляции и сокращению срока службы АД.
С позиции обеспечения экономичной и надежной работы ПЧ целесообразна постановка задачи оптимизации его режимов по критерию потерь мощности преобразователя.
Оптимизация режимов электропривода по минимуму потерь в системе ПЧ – АД имеет практический смысл при рассмотрении электропривода как потребителя электроэнергии. При этом важно знать в каком соотношении к условию минимума потерь в системе ПЧ – АД находятся потери в асинхронном двигателе и преобразователе частоты.
3.Основные пути повышения энергетической эффективности асинхронных электроприводов
Приведенное выше сопоставление разных способов и систем управления асинхронными электроприводами позволяет наметить следующие направления снижения потребления энергии АД.
Первое направление связано со снижением потерь в электроприводе при выполнении им заданных технологических операций по заданным тахограммам и с определенным режимом погружения. Это электроприводы работающие в пускотормозных режимах (краны лифты главные приводы слябингов и блюмингов вспомогательные позиционные механизмы прокатных станов и т.д.) или длительных режимах с медленно изменяющейся нагрузкой (насосы вентиляторы компрессоры транспортеры и т.д.). В таких электроприводах за счет снижения потерь электропривода в установившихся и переходных режимах возможна значительная экономия электроэнергии. В кинематически связанных электроприводах (рольганги многодвигательные приводы тележек и т.д.) равномерное деление нагрузок между двигателями позволяет также минимизировать потери в них.
Второе направление связано с изменением технологического процесса на основе перехода к более совершенным способам регулирования электропривода и параметров этого технологического процесса. При этом происходит снижение потребления энергии электроприводом.
Для обоих названных направлений характерным является то что в них снижается потребление энергии именно в электроприводе: в первом случае за счет снижения потерь энергии во втором за счет использования менее энергозатратного со стороны электропривода управления технологическим процессом.
Можно назвать и третье направление обеспечивающее реализацию энергосберегающих технологий. Известно что имеется ряд технологических процессов где электропривод сравнительно небольшой мощности управляет потоком энергии мощность которого в десятки и сотни раз превышает мощность электропривода. К таким объектам можно отнести дуговые сталеплавильные печи постоянного и переменного тока вакуумные дуговые печи рудо-восстановительные печи установки индукционного нагрева и т.д. На них электроприводы мощностью в несколько киловатт могут управлять процессом потребляющим десятки и даже сотни мегаватт. Очевидно что от совершенства электропривода его быстродействия и точности степени автоматизации процесса во многом зависит эффективное использование таких значительных объемов энергии. Это направление не связано с уменьшением потока энергии через электропривод чаще потребление энергии электроприводом даже увеличивается. Тем не менее так как это направление связано со значительной экономией электроэнергии рассмотрим его на примере дуговой сталеплавильной печи.
Сформулируем пути энергосбережения в асинхронном электроприводе.
В рамках первого направления для снижения потерь энергии в асинхронном электроприводе можно использовать следующие пути.
Обоснованный выбор установленной мощности двигателя соответствующей реальным потребностям управляемого механизма. Эта задача связана с тем что коэффициент загрузки многих двигателей составляет 50% и менее что говорит либо о низкой квалификации разработчиков либо о несовершенстве использованной методики расчета мощности электропривода. Очевидно что двигатель заниженной мощности быстро выходит из строя из-за перегрева а двигатель с большим запасом мощности преобразует энергию неэффективно т.е. с высокими удельными потерями в самом двигателе из-за низкого КПД и в питающей сети из-за низкого коэффициента мощности. Поэтому первый путь заключается в совершенствовании методик выбора мощности двигателя и проверки его по нагреванию а также в повышении квалификации разработчиков проектировщиков и обслуживающего персонала. На практике встречаются случаи когда вышедший из строя двигатель заменяется подходящим по высоте вала или его диаметру а не по мощности. Существующие методики выбора мощности двигателя и проверки его по нагреванию могут рассматриваться лишь как первое приближение. Необходима разработка более совершенных методик основанных на точном учете режимов работы электропривода изменении его энергетических показателей тепловых процессов в двигателе состояния изоляции и т.д. Разумеется это предполагает широкое использование вычислительной техники и специального программного обеспечения.
Переход на более экономичные двигатели в которых за счет увеличения массы активных материалов (железа и меди) применения более совершенных материалов и технологий повышены номинальные значения КПД и коэффициента мощности. Этот путь несмотря на высокую стоимость таких двигателей становится очевидным если учесть что по данным западноевропейских экспертов стоимость электроэнергии потребляемой ежегодно средним двигателем в 5 раз превосходит его стоимость. За время службы двигателя а это десятки лет экономия энергии значительно превысит капитальные затраты на такую модернизацию. Как уже отмечалось ранее этот путь пока не получил должного признания в отечественной практике.
Переход к более совершенной с энергетической точки зрения системе электропривода. Потери энергии в переходных режимах заметно изменяются при использовании реостатного регулирования систем ТПН – АД и ППЧ – АД с минимальными потерями при применении частотно-регулируемых электроприводов. Поэтому в рамках каждой из перечисленных систем имеются более или менее удачные в энергетическом и технологическом плане варианты. Задачей проектировщика является грамотный и всесторонне обоснованный выбор конкретного технического решения.
Совершенствование алгоритмов управления электроприводом в системах ТПН – АД и ППЧ – АД на основе энергетических критериев оценки его качества т.е. совершенствование известных решений разработка эффективных технических средств дня их осуществления и поиск новых решений оптимальных в энергетическом смысле.
В рамках второго направления снижения потребления энергии решающее значение имеет переход от нерегулируемого электропривода к регулируемому и повышение уровня автоматизации за счет включения в контур регулирования ряда технологических параметров (давления расхода температуры и т.д.). Так как это направление связано со снижением потребления энергии электроприводом за счет изменения технологического процесса появляется возможность регулировать ранее не регулировавшиеся технологические параметры или изменять способ их регулирования.
Для третьего направления снижения потребления энергии характерны совершенствование системы электропривода в сочетании с автоматизацией технологического процесса и правильный выбор соответствующего по качеству регулирования электропривода из уже имеющихся или разработка новых более качественных систем.
Заметим что при реализации конкретных проектов выявляется как правило не один а несколько возможных путей энергосбережения поэтому для получения максимального эффекта необходим комплексный подход к решению задачи энергосбережения в электроприводе.
4.Обеспечение технологических требований к показателям переходных процессов за счет систем управления электроприводом
Современные технологические установки и машины предъявляют самые разнообразные требования к качеству переходных процессов в электроприводе. Как правило это требования к точности и быстродействию в позиционных электроприводах формирование желаемой диаграммы скорости в системах регулирования скорости формирование требуемой диаграммы крутящего момента двигателя в тяговых силовых установках и т.д. Кроме того для всех этих устройств характерным является требование ограничения скорости и ее производных момента двигателя и его производных максимальной мощности и т.д. Следовательно из множества возможных траекторий движения электропривода необходимо выбирать такие которые обеспечивают максимальное быстродействие минимум потерь энергии и динамических нагрузок максимум полезной работы с учетом существующих ограничений.
Очевидно что использование неуправляемых переходных процессов пуска и торможения электропривода дает ограниченный набор возможных траекторий движения чаще всего не удовлетворяющих требованиям технологического процесса. Поэтому переход к регулируемому электроприводу с возможностью формирования управляемых переходных процессов является объективной необходимостью. Этот процесс перехода обусловленный непрерывным повышением технического уровня средств управления электроприводом позволяет не только удовлетворить все требования современных технологических установок но и дает возможность оптимизировать потребление энергии электроприводом.
Самая общая постановка задачи оптимального управления электроприводом с учетом технологических требований хорошо известна и заключается в поиске экстремума некоторого обобщенного функционала в который может входить большое число зачастую противоречивых показателей в том числе энергетических. Решение этой задачи связано со значительными трудностями прежде всего из-за того что априори неизвестны весовые коэффициенты показателей входящих в этот функционал. Кроме того само решение этой задачи чрезвычайно громоздко и неоднозначно так как связано с использованием методов классического вариационного исчисления принципа максимума метода динамического программирования и других методов оптимального управления поэтому более известны частные решения задачи например задача позиционирования с минимумом потерь в двигателе. Очень важно учитывать при переходе к регулируемому электроприводу следующие обстоятельства.
Во-первых при переходе к регулируемому электроприводу экономия электроэнергии часто достигается не только и не столько за счет снижения потерь в самом электроприводе но и за счет того технологического процесса в котором участвует этот привод. При этом экономия энергии может многократно превосходить потребление электроэнергии собственно электроприводом. Так повысив качество регулирования в электроприводах перемещения электродов дуговой сталеплавильной печи мощностью в несколько киловатт можно повысить эффективность использования энергии дуги мощностью в несколько мегаватт. Другой пример оптимизация нагрева заготовок в термических установках за счет регулирования скорости транспортера подающего эти заготовки.
Во-вторых для получения энергетического и технологического эффектов часто нужны изменения координат электропривода в очень небольших пределах при невысоких требованиях к качеству регулирования что можно осуществить с помощью относительно простых технических средств. Например даже небольшое изменение скорости насоса водоснабжения дает ощутимую экономию электроэнергии и воды.
В-третьих особенностью таких задач является отсутствие каких-либо универсальных решений применимых для всех электроприводов и технологических процессов поэтому для каждого конкретного объекта из множества возможных вариантов необходимо выбрать один – лучший в определенном смысле. Многое в принятии правильного решения зависит как от квалификации и опыта инженера так и от умения комплексно подойти к решению этой задачи.
5. Эффективность применения преобразователей частоты на примере преобразователей Parvex
С переходом на рыночную экономику для предприятий России вопросы энерго- и ресурсосбережения приобрели особую важность. Устранение нерационального расхода средств сегодня всё чаще решается при помощи высоких технологий и здесь одну из ведущих позиций занимает автоматизированный электропривод.
Для многих инженеров не секрет что именно асинхронный привод находит сейчас всё большее применение благодаря своей экономичности простоте в обслуживании возможности использования на опасных объектах. Уделяя огромное внимание совершенствованию элементной базы преобразователей частоты (ПЧ) многие фирмы добились хороших результатов. Не стала исключением и японская корпорация Parvex преобразователи которой не уступают преобразователям других ведущих производителей ни по качеству ни по надёжности.
Частотные преобразователи Parvex - это высокотехничное изделие содержащие передовые (IGBT) транзисторы в составе силовой схемы интеллектуальную микропроцессорную систему управления позволяющую пользователю оптимально настроить преобразователь под конкретную задачу и далее не вкладывать никаких затрат в его эксплуатацию.
На сегодняшний день и в ближайшем будущем этот класс приборов силовой электроники занимает и будет занимать доминирующее положение для диапазона мощностей от единиц киловатт до единиц мегаватт. Дальнейшее развитие IGBT будет идти по пути:
–повышения диапазона предельных коммутируемых токов и напряжений (единицы килоампер 5-7 кВ);
–повышения быстродействия;
–повышения стойкости к перегрузкам и аварийным режимам;
–снижения прямого падения напряжения;
–разработки новых структур с плотностями токов приближающихся к тиристорным;
–развитие «интеллектуальных» IGBT (с встроенными функциями диагностики и защит) и модулей на их основе;
–создание новых высоконадежных корпусов в том числе прижимной конструкции.
Системная интеграция т. е. объединение в одном устройстве силовых коммутационных элементов с элементами управления диагностики и защит является одним из путей развития силовой электроники.
Таким образом для создания современного надёжного высокоэффективного энерго ресурсосберегаемого полупроводникового электропривода имеется несколько типов приборов силовой электроники каждый из которых занимает свои области наиболее целесообразного применения. Наиболее перспективными приборами силовой электроники являются MOSFET и IGBT для схем преобразователей мощностью от единиц ватт до единиц мегаватт.
Одним из главных достоинств частотных преобразователей является возможность их работы в локальных сетях. Это обеспечивает настройку параметров в режиме чтениезапись и управление всеми преобразователями со станции оператора. Очевидно что такая возможность выводит АСУ ТП на новый уровень обеспечивая удобство эксплуатации снижение материальных затрат на обслуживание повышение качества технологического процесса. Примеров использования сетевых технологий можно привести достаточное количество характерными конечно являются производства конвейерного типа производства с непрерывной обработкой материала транспортные линии.
Кроме того преобразователи Parvex имеют специальную функцию энергосбережения. Преобразователь работая в энергосберегающем режиме отслеживает потребление тока и если нагрузка невелика снижает выходное напряжение до минимально возможного. Т.е. увеличиватся КПД. Функцию можно применять в задачах где нагрузка является переменной величиной. Например на тех же насосных станциях расход воды зависит от времени суток. Активирование энергосберегающего режима в "мертвых зонах" даст дополнительный экономический эффект.
Преобразователь позволяет отслеживать и отображать на цифровом пульте основные параметры системы на заданную скорость выходную частоту ток и напряжение двигателя выходную мощность и момент состояние дискретных входов общее время работы преобразователя и т. д. В зависимости от характера нагрузки можно выбрать подходящую Vf характеристику или создать свою собственную.
Несмотря на немалую стоимость современных частотных преобразователей окупаемость вложенных средств за счёт экономии ресурсов не превышает двух лет. Это вполне реальные сроки а учитывая многолетний жизненный ресурс подобной техники можно подсчитать ожидаемую экономию на длительный период по приведённой выше формуле и принять правильное решение двигаясь в ногу со временем.
Технико-экономический расчет
Токарно-винторезные станки применяются в машиностроительной отрасли очень давно. Большинство станков сильно изношено и не отвечает всем современным требованиям предъявляемых к ним.
В данном дипломном проекте разработана частичная модернизация станка модели 16А20Ф3.
При проведении модернизации осуществлена замена комплектного электропривода Размер 2М-5-2111. В качестве главного был выбран комплектный электропривод PARVEX преобразователь 690C-011-4-BS с асинхронным двигателем MA-100 P-FB. Для привода подач преобразователь HA-75 с двигателем НА-13-17-2000 (17 Нм). Заменена измерительная система обратной связи на фотоимпульсных датчиках ВЕ-178 на круговые датчики типа ЛИР-158А. Осуществленна замена пускорегулирующей и защитной аппаратуры во встроенных шкафах управления станком фирмы Schneider El. напряжением питания 24 В.
Экономическая эффективность достигается за счет следующих факторов:
–снижение потерь электроэнергии благодаря более высокому КПД меньших расходов мощности на собственные нужды меньшей мощности управления;
–сокращения простоев увеличения времени работы оборудования;
–повышения производительности станка;
–уменьшения эксплуатационных расходов.
Расчет экономической эффективности ведется на основе сравнения двух вариантов:
–после модернизации.
1.Расчет капитальных затрат
Капитальные затраты на внедрение нового типа электропривода состоят из стоимости электрооборудования: преобразователей двигателей системы ЧПУ NC-201М затрат на монтаж и т.д.
Капитальные затраты на приобретение оборудования
УЧПУ NC-201М USBLAN Комплектация:
Блок выходных сигналов NC-210-401 (24)
Блок входных сигналов NC-210-402 (32)
Продолжение табл. 6.1.1
Кабели связи разъемы
Привод главного движения PARVEX с двигателем MA-100 P-FB 11кВт. с принуд. охлаждением
Привод с двигателем НМ-НА-13-17-2000 (17 Нм)
Датчик ЛИР-158А-500 (1000) с муфтой ЛИР 801
Реле промежуточное =24V 18 А (Schneider El.) с колодкой и скоба
Блок питания 24В 25А
Кнопка SB7 пуск (черная) стоп (красная) (Schneider El.)
Выключатель автоматический:
GV2_МЕ32 3 пол. 32А (Schneider El.Telemecanique)
GV2_ME14 пол. 14А (Schneider El.Telemecanique)
Трансформатор ОСМ 1-063 УЗ 3805-22-22024
Трансформатор ОСМ 1-063 УЗ 38011024
Общая стоимость 2956058
Затраты на оборудование:
Затраты на транспортировку оборудования принимаем в размере 5 % от его стоимости и они составят
Затраты на монтаж оборудования принимаем в размере 15 % от его стоимости и они составят
Сумма капитальных затрат составит
2.Расчет эксплуатационных расходов
2.1.Сокращение затрат на электроэнергию потребляемую электрооборудованием станка
Стоимость электроэнергии потребляемой станком в год
где Цэ = 2 рубкВт×ч – стоимость 1 кВт×ч электроэнергии; Т – число часов использования оборудования в год; Ра – общая активная мощность потребляемая электрооборудованием станка которая составляет:
Ра1 = 24 кВт – до модернизации;
Ра2 = 20 кВт – после модернизации.
где к = 09 – коэффициент использования оборудования; п = 285 – количество дней работы оборудования в год; р = 7 – продолжительность рабочей смены час (с учётом времени на обед и пересменку) s = 3 – сменность работы оборудования.
2.2.Сокращение затрат на переналадку станка
Переналадка станка до модернизации осуществляется через каждый месяц работы. Переналадка станка после модернизации осуществляется через каждые 3 месяца. Работу производят два наладчика 6 разряда.
до модернизации tнал1 = 4 ч;
после модернизации tнал2 = 1 ч;
Время наладки станка в год:
до модернизации Тнал1 = (п × tнал1) 30= (285 × 4)30 = 38 ч;
после модернизации Тнал2 = (п × tнал2)(30 × 4) = (285 × 1)90 = 24 ч.
Сокращение затрат времени на наладку:
DТнал = Тнал1 - Тнал2 = 38 24 = 356 ч.
Сокращение затрат на зарплату наладчиков:
DСЗпнал = ч × ЗЧнал × DТнал = 2×11875×356 = 8455 руб.
где ч = 2 – количество наладчиков; ЗЧнал = 11875 руб.ч. – средняя зарплата наладчика 6 разряда за час.
2.3.Сокращение затрат на ремонт и обслуживание станка
Периодичность профилактических работ по обслуживанию оборудования составляет:
до модернизации - через 2 недели работы (42 смены);
после модернизации – через 6 недель работы (126 смен).
до модернизации tрем1= 4 ч
после модернизации tрем2= 1 ч.
Время обслуживания в год:
до модернизации Тэл1 = (п × t рем1)14 = (285 × 3)14 = 811 ч
после модернизации Тэл2 = (п × t эл2)42 = (285 × 1)42 = 68 ч.
Сокращение затрат времени на ремонт и обслуживание:
DТэл = Трем1 - Трем2 = 811-68 = 743 ч.
Сокращение затрат на зарплату электромонтеров:
DСЗПэл = ч × ЗЧэл ×DТэл =2 × 11875 × 743 = 176463 руб.
2.4.Суммарное сокращение эксплуатационных расходов
DС = DСэ + DСЗПнал + DСЗПэл = 49238+8455+176463 = 753393 руб.
3.Расчет годового экономического эффекта
Экономический эффект от модернизации получается за счет сокращения эксплуатационных расходов и производительности станка
Э = DС - DК × Ен руб
где DК = 3547269 руб. – капитальные дополнительные вложения; DС = 753393 руб. – сокращение эксплуатационных расходов; Ен = 016 - нормативный коэффициент эффективности капиталовложений.
Э = 753393 3547269 × 016 = 18583 руб.
Эффективность дополнительных капиталовложений характеризует срок окупаемости
Токуп = DК DС = 3547269753393= 45 года.
Новый вариант является эффективным если:
Тн = 7 лет – нормативный срок окупаемости дополнительных капиталовложений.
Наименование показателей
1. Стоимость оборудования
2. Транспортные расходы
3. Монтажные расходы
Эксплуатационные расходы
1. Потребление электроэнергии
2. Расходы на зарплату наладчиков
3. Расходы на зарплату электромонтёров
Годовой экономический эффект
Срок окупаемости капитальных вложений
Из приведённых расчётов видно что при проведении модернизации в токарного станка модели 16А20Ф3 уменьшилось время простоя оборудования и внепланового ремонта снизились эксплуатационные расходы за счёт снижения потребления и потерь электроэнергии а значит увеличился объём выпускаемой продукции. Срок окупаемости составляет 45 года.
Безопасность и жизнедеятельность
В настоящем дипломном проекте производится модернизация электрооборудования токарного станка 16А20Ф3.
С целью обеспечения высокопроизводительной работы и предотвращения несчастных случаев на производстве необходимо проводить мероприятия по улучшению условий труда и контроля над соблюдением правил техники безопасности.
Обеспечение безопасности труда реализуется как при реконструкции производственных цехов так и в процессе их работы. Главным направлением улучшения условий труда и снижения травматизма производства является техническое переоснащение предприятия новой безопасной техникой.
При проектировании стоит задача создания оборудования не только высокопроизводительного и экономически эффективного но и безопасного в эксплуатации. Особое внимание при проектировании новых видов оборудования обращается на соблюдение стандартов по безопасности труда правил техники безопасности санитарных норм и правил инструкций по охране труда.
1.Безопасность проекта
1.1.Общая характеристика производства (рабочего места участка) и электрооборудования с точки зрения безопасности
Токарный станок 16А20Ф3 установлен в инструментальном цехе № 35. Станок предназначен для механической обработки металлов и других материалов. На станке производятся операции точения отрезания нарезания резьбы. Основные используемые материалы и сырье для механической обработки - это конструкционные углеродистые стали например 5ХНМ Ст45 Ст3.
Напряжение - до 1000 В.
Категория персонала - рабочая.
Форма организации труда - индивидуальная.
Форма организации производства - серийная мелкосерийная единичная.
Рабочее место закрепленное за указанным оборудованием соответствует профессии станочника (токаря).
Оценка условий труда по степени вредности и опасности 2.
При проведении технологических процессов обработки металлов резанием на рабочих могут воздействовать следующие опасные и вредные производственные факторы:
–подвижные части производственного оборудования;
–передвигающиеся заготовки и детали;
–движущиеся механизмы;
–острые кромки заусенцы и шероховатости на поверхности заготовок;
–разрушение инструмента приспособлений;
–падение инструмента приспособлений заготовок;
–повышенное значение напряжения в электрической цепи;
–металлизированная пыль;
–повышенный уровень шума;
–недостаток естественного света;
–физические перегрузки.
Основными источниками опасных и вредных производственных факторов являются:
–производственное оборудование;
–обрабатываемый материал;
–применение смазочно-охлаждающей жидкости;
–электрооборудование станка.
В проекте используются материалы и энергоресурсы:
–конструкционные углеродистые стали например 5ХНМ Ст45 Ст3;
1.2.Категория помещения по электробезопасности
Электробезопасность – это система организационных и технических мероприятий и средств обеспечивающих защиту людей от опасного и вредного воздействия на человека электрического тока электрической дуги электромагнитного поля и статического электричества.
Инструментальный отдел цеха № 35 по опасности поражения электрическим током относится к категории помещений с особой опасностью. Это можно утверждать так как имеется более двух признаков категории помещений с повышенной опасностью
Помещения с повышенной опасностью характеризуются наличием в них одного из следующих условий создающих повышенную опасность:
–наличие токопроводящих полов;
–в помещении имеется токопроводящая пыль;
–наличие возможности одновременного прикосновения человека к заземленным частям металлоконструкций зданий технологических аппаратов и механизмов - с одной стороны к металлическим корпусам электрооборудования - с другой.
На электрооборудовании станка имеется опасное для жизни напряжение 380 В. Конструкция станка такова что доступ к токоведущим частям находящимся под напряжением исключен.
Производственный персонал имеет доступ только к органам управления расположенным на подвесном пульте управления станком и вводному автоматическому выключателю. На всех электрошкафах и распределительных коробках установленных на станке нанесен знак электрического напряжения. Положения вводного автоматического выключателя надежно фиксируются и имеют надписи соответствующие положениям «ВКЛЮЧЕНО» и «ОТКЛЮЧЕНО». Подвесной пульт и шкаф управления оборудованы кнопкой аварийного останова с грибовидным толкателем красного цвета «ОБЩИЙ СТОП». При нажатии на эту кнопку схема автоматически производит отключение вводного автоматического выключателя станка при этом все электрооборудование теряет питание. Корпус станка шкафа управления электродвигателя и преобразователя частоты имеют надежное заземление согласно ГОСТ 12.1.030-81 «Защитное заземление и зануление». Путем болтового соединения обеспечивается электрический контакт с контуром заземления цеха.
Производственный персонал эксплуатирующий станок имеет группу по электробезопасности I.
1.3.Анализ электротравматизма
Электротравматизм – это совокупность электротравм характеризуемая определенными причинно-следственными связями между элементами системы «человек–электроустановка-среда» (Ч-Э-С). В этой системе человек является непосредственным объектом поражения электроустановка – непосредственным источником поражения а среда оказывает влияние как на человека так и на электроустановку. Решение вопросов предупреждения электротравматизма должно вестись в направлении изучения свойств и взаимосвязи всех элементов этой системы. Свойства элементов системы влияющие на электротравматизм учитываются совокупностью признаков. Поскольку возникновение электротравмы при различных обстоятельствах связано с большой степенью неопределенности то анализ причинно-следственных связей должен быть основан на использовании теории вероятностей и математической статистики на всех этапах анализа: выявления опасностей и опасных действий разработки логических процедур формулирования защитных мер выбора лучшей защитной меры для внедрения.
Динамика несчастных случаев с 2007 по 2009 годы приведена в табл. 7.1.3.1.
Динамика несчастных случаев с 2008 по 2010 годы
Наименование показателя
Количество несчастных случаев
В том числе смертельных несчастных случаев
Среднегодовая численность работников цеха
Расчетная степень риска
Степень риска несчастных случаев
где N – число несчастных случаев за год (согласно данным отдела ТБ и ОТ); Р – среднесписочный состав цеха в год (согласно данным БОиНТ цеха).
От электротравматизма и его предупреждения применяют различные средства защиты. При случайном прикосновении к токоведущим частям являются хорошим изолятором резиновые перчатки служащие для предохранения работающего. Такую же аналогичную функцию выполняют резиновые галоши боты различные изолирующие подставки коврики и дорожки уменьшая тем самым опасную возможность образования контакта между токоведущими частями соединенными с землёй и работающим.
При модернизации станка уровень электротравматизма должен снизиться за счет следующих блокировок: включение вводного автоматического выключателя невозможно при открытых дверях электрошкафа; на шкафах соединительных коробах содержащих электрическую аппаратуру помещены знаки электрического напряжения; кнопки для аварийного отключения снабжены защелками.
1.4.Средства индивидуальной и коллективной защиты
Основные технические средства безопасности токаря работающего на данном электрооборудовании подразделяют на средства коллективной и индивидуальной защиты. Средства коллективной защиты включают оградительные тормозные устройства сигнализацию об опасности разрывы и габариты безопасности средства дистанционного управления и др.
Оградительные устройства преграждают доступ к движущимся и токоведущим частям станка и механизмов защищают от летящей стружки и отходов распыления жидкостей.
Тормозные устройства обеспечивают возможность быстрой остановки производственного оборудования или отдельных его элементов для предупреждения возможных аварий и несчастных случаев. Например металлорежущие станки снабжены тормозным устройством позволяющим быстро остановить шпиндель станка.
Сигнальные устройства предупреждают о наступающей опасности световыми показывающими или звуковыми сигналами. Эффективность действия сигнальных устройств зависит от внимания и оперативности действий рабочего что зависит от его знаний оборудования и условий эксплуатации. К средствам сигнализации можно отнести подачу или снятие напряжения с лампочки или звукового устройства стрелочного прибора манометра уровнемера и т. п.
Средства индивидуальной защиты предназначены - для защиты рабочего от опасных и вредных факторов внешней среды и выдаются рабочим бесплатно в соответствии с действующими нормами. К ним относят защитные очки которые предохраняют от ранения глаз и лица разлетающейся стружкой и осколками инструмента средства защиты головы (каски); органов дыхания (респираторы).
Спецодежда также предохраняет тело рабочего от вредного воздействия внешней среды от ожогов и ранений. Рукава спецодежды должны облегать руки и застегиваться на пуговицы. Завязки на рукавах не допустимы так как их концы могут быть захвачены шпинделем станка или другими вращающимися деталями. Работать следует в головных уборах с тем чтобы избежать захвата волос.
Электрозащитные средства предназначены для защиты персонала работающего на электроустановках от поражения электрическим током воздействия электрической дуги и электромагнитного поля.
Электрозащитные средства в электроустановках до 1000 В по назначению подразделяются на: а) изолирующие; б) ограждающие; в) вспомогательные.
Изолирующие служат для изоляции человека от токоведущих частей и в свою очередь подразделяются на основные и дополнительные.
К основным изолирующим электрозащитным средствам для электроустановок напряжением до 1000 В относятся: изолирующие штанги всех видов; изолирующие клещи; указатели напряжения; электроизмерительные клещи; диэлектрические перчатки; ручной изолирующий инструмент.
К дополнительным изолирующим электрозащитным средствам для электроустановок напряжением до 1000 В относятся: диэлектрические галоши; диэлектрические ковры и изолирующие подставки; изолирующие колпаки покрытия и накладки; лестницы приставные стремянки изолирующие стеклопластиковые.
Персонал обслуживающий электроустановки снабжается всеми необходимыми защитными средствами обеспечивающими безопасность работы.
1.5.Квалификационные требования к персоналу эксплуатирующему и обслуживающему станок
Для обслуживания и ремонта электромонтёры должны иметь группу не ниже III.
Персонал обслуживающий электроустановки в части его касающейся должен знать:
–правила технической эксплуатации электроустановок потребителей (ПТЭЭП);
–правила устройства электроустановок (ПУЭ);
–руководства по устройству и эксплуатации закрепленных за ним электроустановок;
–должностные и эксплуатационные инструкции применительно к занимаемой должности и выполняемой работе;
–правила освобождения человека от действия электрического тока;
–правила оказания первой помощи пострадавшему от действия электрического тока.
1.6.Организационные и технические мероприятия обеспечивающие безопасное обслуживание и ремонт разрабатываемой в проекте электроустановки
Организационными мероприятиями обеспечивающими безопасность работ в электроустановках являются:
–оформление работ нарядом распоряжением или перечнем работ выполняемых в порядке текущей эксплуатации; допуск к работе; надзор во время работы;
–оформление перерыва в работе перевода на другое место окончания работы.
Ответственными за безопасное ведение работ являются:
–выдающий наряд отдающий распоряжение утверждающий перечень работ выполняемых в порядке текущей эксплуатации;
–ответственный руководитель работ;
–производитель работ;
Электрик обязан ежедневно проверять исправность заземления станка исправность кнопок управления отсутствие доступа не электротехническому персоналу в электрошкафы защиту токоведущих проводов от случайных повреждений исправность выключателя местного освещения. Проводить ремонтные работы согласно годового плана ППP.
В процессе труда в производственном помещении человек находится под влиянием определенных метеорологических условий или микроклимата. Под микроклиматом производственных помещений понимают климат внутренней среды этих помещений который определяется действующими на организм человека сочетанием температуры влажности и скорости движения воздуха а также температурой окружающих поверхностей. К основным нормируемым показателям микроклимата воздуха рабочей зоны относятся: температура окружающей среды; относительная влажность воздуха; скорость движения воздуха; интенсивность теплового излучения различных нагретых поверхностей.
Создание оптимального микроклимата на рабочем месте обуславливает производительность и качество выполняемой работы.
Нормы производственного микроклимата едины для всех производств и всех климатических зон и устанавливаются системой стандартов безопасности труда ГОСТ 12.1.005-88 и САНПиН 2.2.4.548-96. В нормативных документах введены понятия оптимальных и допустимых параметров микроклимата.
Для второй категории тяжести (2А) выполняемых работ величины избытков явного тепла в помещениях и периода года приведены таблице 7.1.7.1.
Фактические значения температуры относительной влажности воздуха и скорости движения воздуха в летний период
ПДК ПДУ допустимый уровень.
Фактический уровень.
Класс условий труда степень вредности и опасности
Продолжительность воздействия за смену мин
Температура воздуха °С
Скорость движения воздуха мс
Фактические значения температуры относительной влажности воздуха и скорости движения воздуха в зимний период
Для поддержания нормальных параметров микроклимата в рабочей зоне приведенных в табл. 7.1.7.1. и 7.1.7.2. применяются мероприятия: механизация и автоматизация технологических процессов защита от источников теплового излучения установка систем вентиляции кондиционирования воздуха и отопления согласно СНиП 41.01-2003.
1.8.Производственное освещение
Производственное освещение - неотъемлемый элемент условий трудовой деятельности человека. При правильно организованном освещении рабочего места обеспечивается сохранность зрения человека и нормальное состояние его нервной системы а также безопасность в процессе производства. Производительность труда и качество выпускаемой продукции находятся в прямой зависимости от освещения. Производственное освещение должно соответствовать СНиП 23-05-95.
Различают следующие виды освещения: естественное искусственное и комбинированное.
На рабочем месте применяется общее и местное освещение. Применение только местного освещения на рабочем месте на производстве запрещается.
Нерациональное освещение (слишком тусклое или же наоборот очень яркое) может стать источником травматизма из-за следующих факторов:
–Слабое освещение опасной зоны;
–Слепящих источников света бликов резких теней могущих вызвать полную потерю ориентации.
Наилучшим видом освещения является дневное солнечное. Все производственные помещения как правило должны иметь естественное освещение. Дневной свет не может обеспечить нужное качество освещения в течение всего рабочего дня к тому же его достаточность зависит от погодных условий и времени суток. Все производственные помещения оснащаются комбинированным освещением или если невозможно применение солнечного света искусственным.
Для улучшения условий естественного освещения помещение и оборудование необходимо окрашивать в светлые тона повышающие освещенность рабочих мест за счет отраженного света. Очищение оконных рам и фонарей должно производиться не реже 4 раз в год.
Согласно строительным нормам и правилам СНиП 23-05-95 для каждого рабочего места существуют свои нормы освещенности которые необходимо строго соблюдать при проектировании производственного освещения.
Освещение может быть общим равномерным общим локализованным (выполненным с учетом расположения рабочих мест) или комбинированным состоящим из общего освещения помещения и местного освещения рабочих поверхностей.
Применению системы комбинированного освещения благоприятствуют:
–высокая точность выполняемых работ;
–специфические требования к качеству освещения;
–ограниченная площадь рабочих поверхностей;
–большая площадь помещения приходящаяся на одно рабочее место;
–возможность перестановки рабочих мест.
Общее освещение производственных помещений при возможности предпочтительно устраивать локализованным чему благоприятствуют большие размеры освещаемых поверхностей или размещение их сосредоточенными группами или рядами.
Нормы рекомендуют комбинированное освещение для помещений с работами разрядов I-IV Vа и Vб но при невозможности или нецелесообразности устройства такого освещения допускается система одного общего освещения имеющая некоторые гигиенические и эстетические преимущества.
Дополнительное местное освещение требуемое нормами для некоторых помещений при необходимости устраивается на единичных рабочих местах и это требование не надо понимать как требование устройства комбинированного освещения. Мостовые краны имеют светильники необходимые для освещения затемненных мест цеха при прохождении над ними мостового крана.
ПДК ПДУ допустимый уровень лк.
Фактический уровень лк.
Пульсация освещенности
1.8.1.Расчет искусственного освещения
Расчет освещенности рабочего места станочника осуществляется в данном случае методом коэффициента использования.
Метод коэффициента использования предназначен для расчета общего равномерного освещения горизонтальных поверхностей при отсутствии крупных затеняющих предметов. При расчете по этому методу учитывается как прямой так и отраженный свет. Переход от средней мощности к минимальной осуществляется в этом методе приближенно.
Требуемый световой поток ламп в каждом светильнике ФР лм
где ЕН – заданная нормированная освещенность согласно таблице «Нормы освещенности рабочих поверхностей в производственных помещениях» для разряда и подразряда зрительных работ IIIв при проведении работ высокой точности с объектом различения 0305 мм при проектировании общего освещения Е=300 лк; k – коэффициент запаса для производственных помещений при содержании в воздухе пыли дыма и копоти не более 5 мгм3 при использовании в качестве общего освещения ламп ДРЛ k=15; S – освещаемая площадь
где a – длина механического участка цеха (оси 1137) a=156 м (согласно чертежу ЭОЗ-763.00.СБ Отдел инструментальный. Электроосвещение); b – ширина инструментального отдела цеха (оси ПУ) b=24 м (согласно чертежу ЭОЗ-763.00.СБ Отделы инструментальный. Электроосвещение).
z – коэффициент минимальной освещенности характеризующий неравномерность освещения является функцией многих переменных и в наибольшей степени зависит от отношения расстояния между светильниками к расчетной высоте (Lh) с увеличением которого сверх рекомендуемых значений z резко возрастает. При отношении расстояния между светильниками к расчетной высоте (Lh) не превышающем рекомендуемых значений можно принять для ламп ДРЛ z=115; N – число светильников N=111 (согласно чертежу ЭОЗ-763.00.СБ Отдел механической обработки. Электроосвещение); h - коэффициент использования светового потока в долях единицы.
Для определения коэффициента использования h находится индекс помещения i и предположительно оцениваются коэффициенты отражения поверхностей помещения: потолка стен и рабочей поверхности.
Оценка коэффициентов отражения поверхностей помещения.
Согласно таблице «Приблизительные значения коэффициентов отражения стен и потолка» [19]:
–SС»10 % - для бетонных стен с окнами;
–SП»30 % - для бетонного потолка;
–SР»10 % - для рабочей поверхности.
Индекс помещения i определяется
где a – длина отдела механической обработки цеха (оси 1137) a=156 м (согласно чертежу ЭОЗ-763.00.СБ Отдел инструментальный. Электроосвещение); b - ширина отдела механической обработки цеха (оси ПУ) b=24 м (согласно чертежу ЭОЗ-763.00.СБ Отдел инструментальный. Электроосвещение); h – расчетная высота подвеса светильника над рабочей поверхностью h=12 м (согласно чертежу ЭОЗ-763.00.СБ Отдел инструментальный. Электроосвещение)
По таблице «Коэффициенты использования светового потока. Светильники с лампами ДРЛ» для светильников типа СД ДРЛ при коэффициентах отражения: от стен SС»10 %; потолка SП»30 %; рабочей поверхности SР»10 % и индексе помещения i=175 - коэффициент использования соответствует 52 %.
По рассчитанному световому потоку выбираем ближайшую стандартную лампу с близким световым потоком.
По таблице «Технические данные ламп ртутных дуговых высокого давления с исправленной цветностью» (ГОСТ 16534-70 с изменением 1) [19] выбираем лампу тип лампы: ДРЛ.
Световой поток лампы после 100 часов горения: 33000 лм.
Проверка правильности выбора лампы
где ФР – расчетный световой поток лампы ФР=33567567 лм (из расчета); ФГОСТ – световой поток лампы по ГОСТ 16534-77 для ламп ДРЛ 700 ФГОСТ=33000 лм [19]
Рассчитанный световой поток находится в пределах от –10 % +20 % что соответствует правильному выбору лампы.
Расчет общего освещения газоразрядными лампами высокого давления
Наименование помещения
Инструментальный отдел
Размеры помещения м: длинаширинавысота
Площадь освещаемой поверхности м
Нормативная освещенность от общего в
составе комбинированного лк
Тип светильника (предварительно)
РСП05 (с ДРЛ потолочный для производственных помещений) тип КСС К-1.
Расстояние от потолка до светильника (свес) м
Расстояние от пола до рабочей поверхности м
Высота подвеса светильника м: Hp = H – hc – hc
Коэффициент неравномерности освещения
Коэффициенты отражения: потолок стены пол
Выбор расположения светильников
Оптимальное расстояние (между рядами) м
Оптимальное расстояние м:
Расстояние от стены до ряда светильников м:
(желательно =(03 05))
Продолжение табл. 7.8.1.1
Расстояние от стены до светильника в ряду м:
(по условиям помещения)
Число рядов светильников
Число светильников в ряду
Число светильников в помещении
Число ламп в помещении
Требуемый световой поток лампы лм:
Ф=( Кз·Z· Eнор ·S)(N·)
Тип выбранной лампы накаливания
Световой поток выбранной лампы лм
Мощность выбранной лампы Вт
Отклонение светового потока выбранной лампы от требуемой величины %:
в допустимых пределах
Мощность системы освещения Вт: Рo =N· Рл
Удельная мощность Втм: Руд = Рo S
Итак для освещения отдела механической обработки цеха принимаем общее освещение на лампах ДРЛ мощностью 700 Вт в количестве 111.
2.Чрезвычайные ситуации
Чрезвычайная ситуация – это внезапно возникшая внешне неожиданная ситуация характеризующаяся резким нарушением установившегося процесса или явления и оказывающая значительное негативное воздействие на окружающую среду жизнедеятельность населения и функционирование экономики.
2.1.Пожарная безопасность
Инструментальный цех в котором установлен проектируемый станок по категории пожарной опасности относится к категории «Д» согласно НПБ 105-03. Здание по степени огнестойкости относится к категории III с пределом огнестойкости 45 час согласно СНиП 21.01-97.
В целях снижения пожарной опасности в цехе предусмотрено:
–для тушения пожара внутри здания – водопроводная сеть в виде стояков с внутренними пожарными кранами количество которых принимается из расчета полива любой точки помещения из двух соседних кранов при развернутых рукавах длиной 10 метров.
–для тушения пожара с внешней стороны – наружная кольцевая сеть водопровода. Для эвакуации людей при пожаре предусмотрены проезды и проходы по длине и ширине цеха.
–цех обеспечивается пенными огнетушителями а отдельные производственные участки углекислотными огнетушителями. В цехе расположены ящики с песком щиты с необходимым инструментом предусмотрена электрическая пожарная сигнализация.
–при возникновении пожара в установленном месте указанном табличкой «МЕСТО СБОРА ЧЛЕНОВ ДПД ПРИ ПОЖАРЕ» собирается добровольная пожарная дружина возглавляемая заместителем начальника цеха. Состав ДПД назначается приказом по цеху. ДПД предназначена для проведения оперативных мероприятий по эвакуации людей и тушению пожара до прибытия пожарных расчетов и оказания посильной помощи пожарным.
–телефонная связь с пожарной охраной по телефону 01. Табличка с надписью «ПРИ ПОЖАРЕ ЗВОНИТЬ 01» находится в каждом помещении где установлен телефон в непосредственной близости от него.
–до всего персонала доведен порядок действий при возникновении пожара.
–все средства пожаротушения содержатся в надлежащем порядке. Контроль за состоянием цеха в отношении пожарной безопасности осуществляется пожарной частью предприятия.
Проектируемый механизм соответствует требованиям безопасности средства обучения и инструктажа выполнены в соответствии с нормативными требованиями безопасности к рабочему месту.
Применение эффективных средств защиты обеспечивает полную нейтрализацию вредных воздействий на окружающую среду.
Гарантированы оптимальные условия и безопасность производства.
Все вредные факторы соответствуют ПДК и ПДН для второго класса условий труда.
Для обеспечения оптимальных условий труда микроклимата производственного помещения предусмотрены вентиляция и отопление в холодное время года.
Проведены расчеты искусственного освещения. Рассмотрены вопросы: техники безопасности электробезопасности охраны окружающей среды чрезвычайных ситуаций.
При соблюдении рекомендаций указанных в данном проекте работа связанная с обслуживанием токарного станка не вызовет заболеваний или отклонений в состоянии здоровья и травм.
В данном дипломном проекте осуществлена замена устаревшей системы ЧПУ «Электроника НЦ31» с приводами «Размер 2М-5-21».
Была установлена система УЧПУ NC-201М фирмы Балт-Систем.
В качестве главного привода был выбран реверсивный комплектный электропривод PARVEX преобразователь 690C-011-4-BS с асинхронным двигателем MA-100 P-FB.
Для привода подачи продольного перемещения (ось Z) на основании технического задания требований технологического процесса тахограммы и требований к электроприводу выбран и проверен по нагреву электродвигатель HM-13-17.0-020-Z. Электродвигатель HM представляет собой синхронный вентильный электродвигатель переменного тока с возбуждением от постоянных магнитов расположенных на роторе. В качестве силового преобразователя выбран реверсивный комплектный преобразователь серии НА HA-75. Электропривод серий HA-HM представляет собой регулируемые (следящие) однокоординатные реверсивные электроприводы переменного тока. Электропривод применяются для быстродействующих механизмов подачи металлообрабатывающих станков в том числе с числовым программным управлением для исполнительных механизмов промышленных роботов и для других механизмов следящих систем которые требуют точных перемещений и регулирования скорости вращения в широком диапазоне.
Согласно выполненным расчетам данный электропривод полностью удовлетворяет технологическим параметрам механизма и техническому заданию.
Заменена измерительная система обратной связи на фотоимпульсных датчиках ВЕ-178 на круговые датчики типа ЛИР-158А для повышения контроля линейного перемещения ходового винта исполнительного механизма.
Произведен расчет сечения питающих линий произведена проверка на нагрев и просадку напряжения. Также был произведен расчет и выбор распределительного коммутационного и защитного электрооборудования. Замена пускорегулирующей и защитной аппаратуры во встроенных шкафах управления станком фирмы Schneider El. напряжением питания 24 В.
В данном проекте произведен расчет экономического эффекта замены электрооборудования при модернизации и представлен срок окупаемости новых капиталовложений.
В разделе безопасности при эксплуатации и ремонте оборудования данного проекта рассмотрены вопросы охраны труда и техники безопасности работы на проектируемом станке представлен расчет общего равномерного искусственного освещения.
Библиографический список
ЗиминЕ.Н. Автоматическое управление электроприводамиЕ.Н. Зимин В.И. Яковлев. – М.: Высш. шк. 1979.
ФедоровА.А. Основы электроснабжения промышленных предприятий. Издание 2-е переработанное и дополненное. - М.:Энергия 1972.
КудринБ.И. Прокопчик В.В. Электроснабжение промышленных предприятий. - Минск: Высш. шк. 1988. – 358 с.
КнязевскнйБ.А. ЛипкинБ.Ю. Электроснабжение промышленных предприятий. – М.: Высш. шк.. 1986. – 400 с.
Правила устройства электроустановокМинэнерго СССР. – 6-е издание переработанное и дополненное. - М.: Энергоатомиздат 1985.
СоколовН.Г. Расчеты по автоматизированному электроприводу металлорежущих станков: учеб. пособиеН.Г.Соколов В.А.Елисеев. – М.: Высш. шк. 1969.
АндреевГ.И. Электроприводы главного движения металлообрабатывающих станков с ЧПУГ.И.Андреев . – М.: Машиностроение 1980.
СандлерА.С. Электропривод и автоматизация металлорежущих станковА.С.Сандлер. – М.: Высш. шк. 1972.
Справочная книга для проектирования электрического освещения. Под редакцией Г.М. Кнорринга- Л.; Энергия 1976.
Браславский И.Я. Энергосберегающий асинхронный электропривод» Учебник для ВУЗов. – М.: Академия; 2004. – 256 с.
Москаленко В.В. Автоматизированный электропривод Учебник для ВУЗов. - М.: Энергоатомиздат; 1986.
Системы подчиненного регулирования электроприводов переменного тока с вентильными преобразователями О.В. Слежановский Л.Х. Дацковский; - М.: Энергоатомиздат 1983.
Безопасность жизнедеятельности. Технические расчеты
параметров электробезопасности: учеб. пособие по выполнению раздела ВКР В.В.Гоман ;. – Нижний Тагил: НТИ (ф) УГТУ-УПИ 2009 – 108с.
Содержание 1 лист.doc
Перечень листов графических документов
Обзор литературных источников
1. Готовый к производству проект модернизации станка 16А20Ф3 на базе системы ЧПУ NC-210
2. Готовый к производству проект модернизации станка 16А20Ф3 на базе системы ЧПУ Sinumerik-802D
3. Готовый к производству проект модернизации станка 16А20Ф3 на базе системы ЧПУ NC-201М с приводами фирмы Parvex НМ-НА
Технологическая часть
1.1.Технологический процесс всего цеха выпускаемая продукция
1.2.Технологический процесс токарного станка с ЧПУ мод. 16А20Ф3 .
1.3.Роль станка в общем технологическом процессе
2. Конструкция и кинематическая схема механизма
2.1. Конструктивное исполнение установки параметры паспортные данные кинематические схемы
2.2. Основные технические параметры
2.3. Описание кинематической схемы
2.4. Краткая характеристика электрооборудования
3. Характеристика существующей системы электроснабжения установки..
3.1. Конструктивное исполнение распределительной сети
3.2. Анализ существующие проблемы пути решения
4. Требования предъявляемые к электрооборудованию
4.1. Требования приводу механизма главного движения металлорежущего станка
4.2. Требования приводу механизма подачи металлорежущего станка
4.3. Требования к надежности
4.4. Требования к безопасности
Конструкторская часть
1. Расчет требуемой мощности электропривода и электрооборудования
1.1 Определение мощности двигателя главного привода
3. Схема кинематическая станка мод. 16А20Ф3.cdw

Схема кинематическая станка 16А20Ф3
5. Схема принципиальная на 1 привод подачи .cdw

питание модулей ввода-вывода УЧПУ
2. план цеха.cdw

1. ктп 53 готов.cdw

мод.7А256 Руст-269квт
мод. 7212 Р уст.=145квт
эл. снабжения участка
станок 6М610Ф11.20.3
Резервное питание ПЭВМ
Нормальное питание ПЭВМ
Прод.стр.7210 Руст=130квт
Рекомендуемые чертежи
- 29.05.2022