Качающийся конвейер



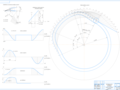
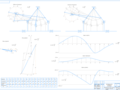
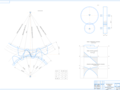
- Добавлен: 24.01.2023
- Размер: 1 MB
- Закачек: 0
Узнать, как скачать этот материал
Подписаться на ежедневные обновления каталога:
Описание
Качающийся конвейер
Состав проекта
![]() |
![]() |
![]() ![]() ![]() ![]() |
![]() ![]() |
![]() ![]() ![]() ![]() |
![]() ![]() ![]() |
![]() ![]() ![]() ![]() |
![]() |
![]() |
![]() |
![]() |
![]() |
![]() |
![]() |
![]() |
![]() |
Дополнительная информация
Контент чертежей
Зубчатое зацепление.cdw

Кинематика.cdw

Кулачек.cdw

Рекомендуемые чертежи
Свободное скачивание на сегодня
Обновление через: 10 часов 57 минут
Другие проекты
- 14.05.2021