Детали машин привод к элеватору




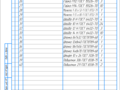
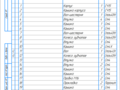
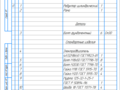
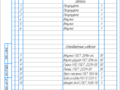
- Добавлен: 24.01.2023
- Размер: 938 KB
- Закачек: 0
Описание
Состав проекта
![]() |
![]() ![]() ![]() |
![]() ![]() ![]() ![]() |
![]() ![]() ![]() ![]() |
![]() ![]() ![]() ![]() |
![]() ![]() ![]() ![]() |
![]() ![]() ![]() ![]() |
![]() ![]() ![]() ![]() |
![]() ![]() ![]() ![]() |
![]() ![]() ![]() ![]() |
![]() ![]() ![]() ![]() |
![]() ![]() ![]() ![]() |
![]() ![]() ![]() ![]() |
![]() ![]() ![]() ![]() |
Дополнительная информация
Муфта.cdw

привод1.cdw

Колесо .cdw

Чертеж2.cdw

Чертеж3.cdw

спецификация привод.cdw

Чертеж.cdw

Муфта комб2.cdw

спецификация редуктор.cdw

спецификация редуктор2.cdw

спецификация муфта.cdw

вал.cdw

Рекомендуемые чертежи
- 24.01.2023