Червячный редуктор с нижним расположением червяка, ременная передача, на выходе коническая передача




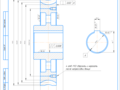
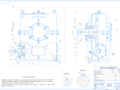
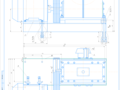
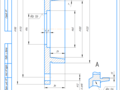
- Добавлен: 24.01.2023
- Размер: 523 KB
- Закачек: 1
Описание
Состав проекта
![]() |
![]() ![]() ![]() ![]() |
![]() ![]() ![]() ![]() |
![]() ![]() ![]() ![]() |
![]() ![]() ![]() ![]() |
![]() ![]() ![]() ![]() |
![]() ![]() ![]() ![]() |
![]() ![]() ![]() |
![]() ![]() ![]() ![]() |
Дополнительная информация
А1 СБ.cdw

Передаточное отношение
Межосевое расстояние
Технические требования
Внутренние поверхности корпуса и крышки покрасить маслостойкой эмалью ВЛ-515 ТУ 6-10-1052-75.
Перед окончательной сборкой стыки фланцев корпуса покрыть герметиком УТ-34 ГОСТ 24285-80.
л. масла И-Т-Д-220 ГОСТ 17479.4-87.
После окончательной сборки редуктор обкатать без нагрузки в течение 3-х часов
произвести замену масла.
Крышка червяка глухая
Маслоуказатель жезловый
Крышка червяка сквозная
Маслоотбойник червяка
Крышка ведомого вала сквозная
Маслоотбойник ведомого вала
Крышка ведомого вала глухая
Подшипник 7218 TУ37.006. 162-89
Подшипник 7311 TУ37.006. 162-89
Болт М10 х 50 ГОСТ 7798-70
Болт М12 х 35 ГОСТ 7798-70
Болт М14 х 160 ГОСТ 7798-70
Болт М16 х 38 ГОСТ 7798-70
Болт М18 х 20 ГОСТ 7798-70
Гайка М10 ГОСТ 5915-70
Гайка М14 ГОСТ 5915-70
Мaнжета 1-50 х 65-1 3 ГОСТ 8752-79
Мaнжета 1-85 х 110-1 ГОСТ 8752-79
Рым-болт М10.19 ГОСТ 4751-73
Шайба 10 Н ГОСТ 6402-70
Шайба 14 Н ГОСТ 6402-70
Шпонка 14 х 9 х 56 ГОСТ 23360-78
Шпонка 22 х 14 х 100 ГОСТ 23360-78
Шпонка 28 х 16 х 110 ГОСТ 23360-78
Уплотнение крышек ведомого вала
Уплотнение крышек червяка
Уплотнение сливной пробки
А3 Червяк.cdw

Коэф. диаметра червяка
Межосевое расстояние
Число зубьев сопряженного колеса
Твердость витков 50 56 HRCэ на глубину 1
Неуказанные предельные отклонения размеров: отверстий +t
Радиус галетлей r = 1 мм.
* размеры для справок.
А1 ОВ.cdw

Мощность электродвигателя Р = 9
Частота вращения вала электродвигателя nэд = 2940 обмин.
Частота вращения выходного вала редуктора nвых = 147 обмин
Общее передаточное отношение Uобщ = 84
Передаточное отношение редуктора Uред = 10
Передаточное отношение ременной передачи Uрем = 2
Передаточное отношение конической передачи Uк = 4
Крутящий момент на выходном валу редуктора Т = 416 Нм
Технические требования
Прогиб ветви ремня под воздействием силы 100 Н не более 6 мм (ГОСТ 1284.3-96).
Непараллельность осей шкивов не более 2
Смещение рабочих поверхностей шкивов не более 0
Привод обкатать без нагрузки в течение не менее 1 часа. Стук и резкий шум не допускаются.
Натяжение ремня периодическое перемещением рамы электродвигателя регулировочными винтами.
Ограждения условно не показаны. Ограждения установить и окрасить в оранжевый цвет.
Передача клиноременная
Пдита электродвигателя
Болт М14 х 16 ГОСТ 7798-70
Болт 1.1 М12х210 Ст3пс2 ГОСТ 24379.1-80
Болт 1.1 М20х320 Ст3пс2 ГОСТ 24379.1-80
Винт М20 х 75 ГОСТ 1486-84
Гайка 2 М12 ГОСТ 5915-70
Гайка 2 М20 ГОСТ 5915-70
Шайба 12 Л ГОСТ 6402-70
Шайба 20 Л ГОСТ 6402-70
Электродвигатель 4А160МА2
А3 Колесо.cdw

Коэф. диаметра червяка
Межосевое расстояние
Число витков сопряженного червяка
отв. М12 сверлить и нарезать
после напрессовки венца
Неуказанные предельные
отклонения размеров:
* Размер для справок.
А3 Вал 2.cdw

Неуказанные предельные отклонения размеров валов - t
t:2 среднего класса точности по ГОСТ 25670-83
А4 Крышка 1.cdw

ПЗ версия .3.doc
Кинематическая схема привода
открытая коническая пара.
Мощность на выходном валу привода Рвых = 6 кВт
Частота вращения выходного вала привода nвых = 25 обмин
Ременная передача клиноременная
Червяк архимедов нижний
Открытая коническая передача прямозубая
Кинематический расчет привода5
Выбор материалов и допускаемых напряжений элементов червячной передачи9
1 Выбор материала червячной передачи9
1 Выбор материала конической передачи10
Расчет всех передач входящих в привод12
1 Расчет клиноременной передачи12
2 Расчет конической передачи16
3 Расчет закрытой червячной передачи21
Схема сил в зацеплении26
1 Определение сил в зацеплении открытой передачи26
2 Силовая схема нагружения валов редуктора27
Предварительный расчет валов28
Эскизная компоновка редуктора29
Уточненный расчет валов30
1 Определение реакций в опорах валов30
Подбор подшипников качения36
Уточненный расчет выходного вала39
1 Проверочный расчет выходного вала по переменным напряжениям39
2 Проверочный расчет выходного вала на статическую прочность41
Проверка прочности шпоночных соединений42
Библиографический список47
Механический привод в современном машиностроении является наиболее ответственным механизмом с помощью которого передается силовой поток с изменением его направления.
Создание машин отвечающих потребностям народного хозяйства должно предусматривать их наибольший экономический эффект и высокие тактико-технические и эксплуатационные показатели.
Основным требования предъявляемые к создаваемой машине: высокая производительность надежность технологичность ремонтопригодность минимальные габариты и масса удобство эксплуатации экономичность техническая эстетика. Все эти требования учитываются в процессе проектирования и конструирования.
Кинематический расчет привода
1 Определение требуемой мощности электродвигателя
Определяем требуемую мощность электродвигателя по формуле 1 [2]:
гдеРвых - мощность на выходном валу редуктора кВт;
общ – общий КПД привода.
Общий КПД определяем по формуле 2 [2]:
Частные КПД выбираем по таблице 3 [2]:
5 - КПД ременной передачи;
5 - КПД закрытой червячной передачи;
6 - КПД открытой конической передачи;
9 - КПД пары подшипников качения;
Полученные частные КПД подставим в формулу и получим общий КПД привода:
Определяем расчетную мощность электродвигателя:
2 Выбор электродвигателя
Прежде чем выбрать электродвигатель по найденной мощности Рдв.р. необходимо определить требуемое число оборотов электродвигателя для данного привода. Для этого вычислим общее передаточное отношение привода:
Первоначально примем передаточные числа из рекомендованных: i1 = 2 i2 = 10 i3 = 45.
Из формулы (3) определим требуемую частоту вращения вала электродвигателя:
По приложению 1 [2] принимаем электродвигатель типа 4А160МА2 номинальной мощностью Рдв = 11 кВт с частотой вращения ротора n1 = 2940 обмин.
Уточняем передаточное отношение привода:
Пересчитываем передаточное отношение ременной передачи:
Окончательно принимаем i1 = 26 i2 = 10 i3 = 45.
Силовые и кинематические параметры привода определяем по формулам из таблицы 4 [2].
3 Определяем мощность на каждом валу
4 Определяем обороты каждого вала
5 Определяем угловую скорость каждого вала
6 Определяем крутящий момент на каждом валу по формуле:
Результаты расчетов сводим в таблицу 1.
Таблица 1 – Результаты кинематического расчета привода
Выбор материалов и допускаемых напряжений элементов червячной передачи
1 Выбор материала червячной передачи
Выбор марки материала зависит от передаваемой мощности и скорости скольжения Ошибка! Закладка не определена. определяемой по формуле [3]:
При передаваемой мощности = 941 кВт и скорости скольжения Ошибка! Закладка не определена. = 38 мс принимаем по табл. 5 [3] из II группы материал БрА10Ж4Н4 для которого: Нмм²; Нмм².
Определяем допускаемые напряжения для червячного колеса по формуле из таблицы 6 [3]:
Где – коэффициент долговечности при расчете на изгиб:
2 Выбор материала конической передачи
Твердость материала шестерни должна быть на 20-30 единиц выше твердости колеса.
Принимаем по таблице 5 [2] материал – сталь 40ХН.
Термообработка – улучшение.
Шестерня – НВ1 = 302;
Пределы выносливости по контактным напряжениям вычисляем по формулам:
Вычисляем допускаемые контактные напряжения по формулам [2]:
где[Sн] – коэффициент безопасности равный 12;
KHL – коэффициенты долговечности шестерни и колеса учитывающий влияние срока службы и режима работы передачи. Для базового числа циклов N = 107 принимаем KHL = 1 [2].
Расчет прямозубых передач ведем по меньшему значению - по []H2 = 528 МПа.
Пределы выносливости по изгибным напряжениям вычисляем по формулам:
Вычисляем допускаемые изгибные напряжения:
где[Sf] – коэффициент безопасности равный 23 для поковок;
KFL – коэффициенты долговечности шестерни и колеса [2]. Принимаем KFL = 1 для базового числа циклов.
Расчет всех передач входящих в привод
1 Расчет клиноременной передачи
Принимаем тип ремня в зависимости от мощности и угловой скорости [2]. Выбираем тип ремня Б для которого: b = 14 мм h = 105 мм A0 = 133 мм² l = (560 4000) мм.
Принимаем диаметр ведущего шкива по рекомендациям [2]. Для получения передачи с минимальными размерами принимаем d1 = 125 мм.
Вычисляем скорость ремня:
Использование ремня выбранного типа допускается при данной скорости.
Вычисляем диаметр ведомого шкива:
По ГОСТ 17383-73 принимаем d2 = 340 мм.
Определяем фактическое передаточное отношение:
где = (001 002) – коэффициент упругого скольжения.
Определяем процентное отклонение фактического передаточного числа от заданного:
Отклонение находится в допустимых пределах.
Ориентировочно принимаем минимальное межосевое расстояние:
Определяем длину ремня без учета припуска на соединение концов по формуле [2]:
Полученное значение округляем до стандартного значения = 1400 мм по ГОСТ 1284.3-96.
Определяем число пробегов ремня с-1 по формуле [2]:
Окончательное межосевое расстояние определяем по формуле [2]:
Полученное межосевое расстояние проверяем по условию:
Определяем угол обхвата по формуле [2]:
Принимаем коэффициенты [2]: 0 = 118 МПа [k0] = 148 МПа.
Принимаем поправочные коэффициенты:
Cα – коэффициент учитывающий угол обхвата шкивов;
Сv – скоростной коэффициент;
Ср – коэффициент нагрузки и режима работы;
С – коэффициент зависящий от угла наклона осей центров ременной передачи к горизонту;
Вычисляем скоростной коэффициент [2]:
Ошибка! Закладка не определена.
Принимаем Cα = 094; Ср = 08; С = 08.
Вычисляем допускаемую удельную окружную силу:
Вычисляем окружную силу по формуле [2]:
Определяем площадь сечения ремня по формуле [2]:
Определяем число ремней по формуле [2]:
Определяем силу предварительного натяжения ремня по формуле [2]:
Силу Н нагружающую валы передачи определяем по формуле по формуле [2]:
2 Расчет конической передачи
При консольном расположении шестерни относительно опор и постоянной нагрузке принимаем: коэффициент ширины венца колеса по делительному диаметру bd = 04; коэффициент неравномерности распределения нагрузки по длине зуба = 112 и KHv = 112.
Вычисляем средний делительный диаметр шестерни:
Принимаем делительный диаметр ведущего колеса d1 = 200 мм
Вычисляем ширину зубчатого венца:
Вычисляем внешний делительный диаметр шестерни:
Вычисляем внешний делительный диаметр колеса:
При числе зубьев шестерни 18 28 рекомендуемые значения производственного модуля:
Принимаем по ГОСТ 9563-60 [1] me = 10.
Вычисляем число зубьев колеса:
Пересчитываем фактическое расстояние de2:
Отклонение от de2 -020% что допустимо.
Вычисляем число зубьев шестерни:
Вычисляем фактическое передаточное число:
Отклонение от i - 111% что допустимо.
Вычисляем углы делительных конусов:
Вычисляем основные геометрические размеры передачи:
Внешний делительный диаметр шестерни:
Внешний диаметр вершин зубьев шестерни и колеса:
Внешний диаметр впадин зубьев шестерни и колеса:
Рисунок 1 – Геометрические параметры конической зубчатой передачи.
Внешнее конусное расстояние:
Среднее конусное расстояние:
Проверяем рекомендации:
Условия соблюдаются.
Определяем средний модуль зацепления:
Вычисляем фактический делительный диаметр шестерни и колеса:
Вычисляем среднюю окружную скорость зубчатых колес:
Принимаем 9-ую степень точности [2].
Определяем окружное усилие в зацеплении:
Радиальное усилие на шестерне численно равное осевому усилию на колесе:
Радиальное усилие на колесе численно равное осевому усилию на шестерне:
Для прямозубых передач при НВ ≤ 350 и скорости м ≤ 5 мс динамические коэффициенты равны: KHV = 11 KFV = 14.
Вычисляем расчетное контактное напряжение:
Определяем процент перегрузки:
Полученный результат находится в допускаемых пределах (-15 + 5)%.
Определяем эквивалентное число зубьев шестерни и колеса по табл. 13 [2]:
Определяем напряжения изгиба в основании зубьев шестерни и колеса:
Найденное значение 44 МПа значительно меньше следовательно прочность зубьев передачи на изгиб обеспечена.
3 Расчет закрытой червячной передачи
При передаточном отношении u = 10 по таблице 3.21 принимаем число заходов червяка = 4 тогда число зубьев колеса :
Из условия жестокости определяем коэффициент диаметра червяка:
= (0212 025) · 40 = 85 10(5)
Принимаем по табл. 3.22 = 10.
Из условия контактной прочности находим межосевое расстояние по формуле 3.36
где – допускаемое напряжение материала колеса;
Кн – коэффициент нагрузки. Принимаем при скорости скольжения червяка Vs = 38 мс рекомендованное значение Кн = 146.
Полученное значение межосевого расстояния занижаем и округляем до стандартного значения = 250 мм по табл. 324.
Определяем модуль зацепления m:
Принимаем m = 10 мм по табл. 3.23.
Определяем фактическое межосевое расстояние:
!Синтаксическая ошибка ·(8)
Полученное значение соответствует стандартному значению поэтому не применяем корригирование и принимаем коэффициент x = 00 мм.
Определяем основные геометрические размеры червяка по формулам из табл. 3.25:
Основные размеры червяка мм:
Диаметр вершин витков
da1 = d1 + 2 · m = 100 + 2 10 = 120 мм(10)
Диаметр впадин витков
Длина нарезной части червяка (уменьшена на 21 мм из конструктивных соображений):
b1 = m · (125 + 009 · Z2) = 10 · (125 + 009 40) 140 мм(12)
Делительный угол подъема линии витков
Определяем основные геометрические размеры колеса мм:
d2 = m · Z2 = 10 40 = 400 мм(14)
Диаметр вершин зубьев
da2 = d2 + m · (2 + 2 · х) = 400 + 10 (2 + 2 · 00) = 420 м(15)
Наибольший диаметр вершин
Диаметр впадин зубьев
df2 = d2 - m · (24 – 2 · х) = 400-10 (24-2 · 00) = 376 мм(17)
b2 ≤ 067 · da1 = 067 · 120 80 мм(18)
Назначаем 8 степень точности передачи по табл. 3.26.
Рисунок 2 – Геометрические параметры червячной пары.
Уточняем КПД передачи:
По табл. 3.27 в зависимости от скорости скольжения передачи принимаем угол трения = 2º
Определяем силы действующие в зацеплении. Определяем окружную силу на колесе Н численно равную осевой силе на червяке :
Окружная сила на червяке численно равная осевой силе на колесе :
Определяем окружную силу в зацеплении:
Проверяем соблюдение условия контактной выносливости передачи:
Определяем отклонение действительной нагрузки от заданной:
Условие прочности выполняется т.к. действительная нагрузка находится в допустимом интервале (-20 + 5)%.
Определяем напряжение изгиба зубьев колеса Нмм²:
где - коэффициент формы зуба колеса зависящий от эквивалентного числа зубьев колеса ZV2 = 32. Принимаем по табл. 3.28 = 177.
Условие прочности выполняется.
Тепловой расчет. Условие работы редуктора без перегрева:
tМ = tВ + (1 - ) · ≤ [tМ] = 70 80 ОC(25)
Принимаем охлаждение редуктора через змеевики КТ = 80 Вт(м² · ОС). Площадь охлаждения корпуса редуктора:
А = 20 · aw² = 20 · 250² · 10-6 = 125 м²(26)
Температура окружающего воздуха tВ = 20 ОC.
tМ = 20 + (1 - 082) · = 32 ОC [tМ]
Расчет червяка на жесткость. Приведённый момент инерции поперечного сечения червяка:
Таким образом жесткость обеспечена так как .
Схема сил в зацеплении
1 Определение сил в зацеплении открытой передачи
Определяем окружную силу на колесе Н численно равную осевой силе на червяке :
Определяем окружную силу на червяке Н численно равную осевой силе на колесе :
Условно заменяем силы действующие в полосе зацепления конической пары консольной силой: [2 стр. 269]:
Консольная сила от ременной передачи Fp = 446 Н.
2 Силовая схема нагружения валов редуктора
Рисунок 3 – Силовая схема нагружения валов редуктора.
Предварительный расчет валов
В качестве материала для изготовления валов принимаем сталь 45 с пределом прочности []В = 560 МПа. Диаметр ведущего вала редуктора определяем по формуле:
где[] – допускаемое напряжение кручения.
Диаметр выходного конца ведущего вала принимаем d1 = 45 мм;
Диаметр выходного конца ведомого вала принимаем d2 = 80 мм;
Диаметры остальных участков валов находим последовательным изменением диаметра предыдущего участка на 2 5 мм.
Таблица 2 – Предварительный расчет валов.
Эскизная компоновка редуктора
Определяем расстояние между силами приложенными к валу и реакциями опор: l1 = 209 мм l2 = 130 мм l3 = 117 мм l4 = 115 мм.
Уточненный расчет валов
1 Определение реакций в опорах валов
Вертикальная плоскость
Ошибка! Закладка не определена. Н
Горизонтальная плоскость
Суммарные радиальные реакции подшипников:
Строим эпюры моментов.
Крутящий момент Т = 56 Нм
Рисунок 4 – Расчетная схема ведущего вала.
- Fr l3 + Yd 2 l3 + Fr2 l4 + Fak1 0.5 d1 + Fa2 05 d2 = 0
Fr l3 - Yc 2 l3 + Fr2 (2 l3 + l4) + Fak1 0.5 d1 + Fa2 05 d2 = 0
Yc + Yd - Fr2 - Fr = 0
08 + (-2430) - 697 - 981 = 0
- Xd · 2 · l3 + Ft · l3 – Ftk · l4 = 0
47 - 4148 + 4281 - 1480 = 0
Определяем значения моментов
Вертикальная плоскость:
Горизонтальная плоскость
Mх4 слева = Yd (2 l3 + l4) – Fr (l3 + l4) + Yc l4 + Fa2 05 d2 = 10 Нм
Mх4 справа = Fak1 0.5 d1 = 136 Нм
Крутящий момент Т = 534 Нм
Рисунок 5 – Расчетная схема ведомого вала.
Подбор подшипников качения
Таблица 3 – Предварительный выбор подшипников
Ведущий вал - шарикоподшипник серии 7311: d = 55 мм е = 034 у = 216.
Ведомый вал - шарикоподшипник 7218: d = 90 мм 033 у = 183.
Определяем радиальные силы в подшипниках:
Осевые составляющие:
Rsa = 083 е Fra = 083 034 4070 = 1149 Н
Rsb = 083 е Frb = 083 033 4747 = 1300 Н
Rsс = 083 е Fc = 083 034 8653 = 2442 Н
Rsd = 083 е Frd = 083 033 1516 = 415 Н
Т.к Rsa > Rsb то расчетная осевая нагрузка:
Fап2 = Rsa + Fa = 1149 + 2080 = 3229 Н
Faп4 = 2442 + 8320 = 10762 Н
В соответствии с условиями работы подшипников назначаем расчетные коэффициенты V = 1 Кб = 115; Кt = 1.
Определяем коэффициенты радиальной и осевой нагрузки:
Принимаем х1 = 04 у1 = 216 х2 = 1 у2 = 0 х3 = 04 у3 = 183 х4 = 04 у4 = 183.
Определяем эквивалентную динамическую нагрузку:
Re = (X · V · Rr + Y Faп) · Кб · Кt (35)
Reа = (04 · 4070 + 216 1149) · 115 · 1 = 4726 Н
Reb = (1 · 4747 + 0 3229) · 115 · 1 = 5459 Н
Reс = (04 · 8653 + 183 2442) · 115 · 1 = 9120 Н
Red = (04 · 1516 + 183 10762) · 115 · 1 = 23346 Н
Наиболее нагружены опоры А и D.
Подшипник пригоден при условии:
Определяем расчетную динамическую грузоподъемность:
гдеRe – эквивалентная динамическая нагрузка Н;
m – показатель степени. = 333 - для роликоподшипников;
Lh – требуемый ресурс подшипника.
Подшипник 7311 пригоден.
Подшипник 7218 пригоден.
Уточненный расчет выходного вала
1 Проверочный расчет выходного вала по переменным напряжениям
Сечение под червячным колесом. Концентрация напряжений обусловлена наличием шпоночного паза.
Материал Сталь 45 термообработка – улучшение .
Определение запасов прочности вала для опасных сечений по нормальным напряжениям.
гдеK = 172 – эффективный коэффициент концентрации напряжений;
= 073 – коэффициент учитывающий влияние масштабных факторов;
- амплитуда нормальных напряжений.
где М – изгибающий момент действующий на вал колеса;
Wи – момент сопротивления сечения изгибу:
Суммарный изгибающий момент в горизонтальной и вертикальной плоскостях:
- среднее напряжение отнулевого цикла:
Проверка вала по касательным напряжениям
гдеK = 156 – эффективный коэффициент концентрации напряжений;
= 063 – коэффициент учитывающий влияние масштабных факторов;
- амплитуда касательных напряжений численно равная среднему напряжению цикла:
= 01 – коэффициент учитывающий влияние постоянной составляющей цикла на усталостную прочность.
Коэффициент запаса прочности по касательным напряжениям:
Результирующий коэффициент запаса прочности:
Условие прочности вала выполняется т.к. коэффициент запаса прочности находится в допустимых пределах [n] = (15 4).
Проверка прочности шпоночных соединений
Производим расчет шпонок на смятие по формуле [рв стр. 24-26]:
Где h - высота сечения шпонки мм;
t1- глубина паза вала мм;
b - ширина шпонки мм.
[см] - допускаемое напряжение на смятие [см] = 90 МПа - при стальной ступице.
Результаты расчета приведены в таблице 4.
Таблица 4 - Проверочный расчет шпоночных соединений.
Передаваемый момент Нм
Высота сечения шпонки мм
Напряжение на смятие МПа
Условие прочности для всех шпоночных соединений выполняется.
При скорости скольжения = 38 мс принимаем по табл. 12.29 [3 стр. 241] смазочное масло И-Т-Д-220 ГОСТ 17479.4-87. Это индустриальное масло для тяжело нагруженных узлов с присадками.
Объём масляной ванны V определяется из расчёта 025 дм³ масла на 1 кВт передаваемой мощности:
V = 025 · 22 = 55 дм³
Выбираем жезловый маслоуказатель. Сливное отверстие закрываем пробкой с метрической резьбой.
Уровень масла: до середины тел качения подшипников вала-червяка.
Смазка подшипников вала-червяка осуществляется маслом И-Т-Д-220 ГОСТ 17479.4-87.
Смазка подшипников вала колеса осуществляем консталином УТ-1 ГОСТ 7957-73. Закладываемой в подшипниковые камеры примерно 23 объема камеры при сборке редуктора. В сквозные крышки подшипников устанавливаем манжетные уплотнения.
Для обеспечения взаимозаменяемости деталей сопряжения деталей выполняем со следующими посадками [2 табл. 10.13 стр. 263]:
посадка муфты колеса звездочки на валы - Н7р6;
посадка подшипников на вал
посадка подшипников в корпус H7
шейки валов под манжетами –
крышки подшипников в корпус –
Перед сборкой внутреннюю полость корпуса тщательно очищают и покрывают маслостойкой краской. Сборку редуктора производят в соответствии с чертежом общего вида. Начинают сборку с того что на червячный вал надевают крыльчатки и конические роликовые подшипники предварительно нагрев их в масле до 80° 100 °С. Собранный червячный вал вставляют в корпус.
При установке червяка выполненного за одно целое с валом следует обратить внимание на то что для прохода червяка его диаметр должен быть меньше диаметра отверстия для подшипников. В нашем случае диаметр червяка da1 = 120 мм а наружный диаметр подшипников 7311 12 мм. Поэтому для нормальной сборки устанавливаем стакан.
В начале сборки вала червячного колеса закладывают шпонку и напрессовывают колесо до упора в бурт вала; затем надевают распорную втулку и устанавливают роликовые конические подшипники нагретые в масле. Собранный вал укладывают в основании корпуса и надевают крышку корпуса покрывая предварительно поверхности стыка фланцев спиртовым лаком. Для центровки крышку устанавливают на корпус с помощью двух конических штифтов и затягивают болты. Закладывают в подшипниковые сквозные крышки резиновые манжеты и устанавливают крышки с прокладками.
Для регулировки червячного зацепления необходимо весь комплект вала с червячным колесом смешать в осевом направлении до совпадения средней плоскости колеса с осью червяка. Этого добиваются переносом части прокладок с одной стороны корпуса на другую. Чтобы при этом сохранялась регулировка подшипников суммарная толщина набора прокладок должна оставаться без изменения. Ввертывают пробку масло – спускного отверстия с прокладкой и маслоуказатель. Заливают в редуктор масло и закрывают смотровое отверстие крышкой с отдушиной. Собранный редуктор обкатывают и испытывают на стенде.
При работе над курсовым проектом были закреплены знания методик расчетов типовых деталей машин общего назначения получены навыки принятия решений при компоновке редуктора и конструировании его деталей.
Был выбран электродвигатель. При разбивке передаточного отношения редуктора были учтены рекомендации. Передаточные числа отдельных передач приняты согласно ГОСТ 2885-76 и 12289-76.
Проектный расчет зубчатых передач выполнен по критерию контактной прочности активной поверхности зубьев. После определения размеров передач проведены проверочные расчеты по критерию контактной и изгибной выносливости а также при действии пиковых нагрузок. Все условия прочности выполняются. При компоновке механизма проработан вопрос оптимального размещения зубчатых передач в корпусе редуктора определены схемы установки опор валов способы осевой фиксации зубчатых колес подшипников на валах. Были определены способ изготовления и размеры конструктивных элементов зубчатых колес форма и размеры элементов корпуса редуктора.
Выбранные подшипники проверены на пригодность по их долговечности из расчета по динамической грузоподъемности.
Шпоночные соединения проверены на прочность по напряжениям смятия.
Решены вопросы смазки передач редуктора и подшипников. Для смазки подшипников валов применена раздельная от передачи смазка пластичным материалом (Литол-24).
Для соединения вала редуктора с валом электродвигателя была выбрана муфта с упругими элементами компенсирующие погрешности монтажа агрегатов.
Полученная конструкция привода в полной мере отвечает современным требованиям предъявляемым к механизмам данного типа.
Библиографический список
Курмаз Л.В. Детали машин. Проектирование: Справочное учебно - методическое пособие Л.В.Курмаз А.Т.Скойбеда – 2 –е изд. исп. М Высшая школа 2005. – 309 с. ил.
Курсовое проектирование деталей машин: учеб. пособие для учащихся машиностроительных специальностей техникумов С.А. Чернавский К.Н. Боков И.М. Чернин и др. – 2-е изд. перераб. и доп. – М.: Машиностроение 1988. – 416 с.: ил.
Шейнблит А.Е. Курсовое проектирование деталей машин: учебное пособие для техникумов. – М.: ВШ 1991. – 432 с.: ил.
А4 Крышка 2.cdw

Рекомендуемые чертежи
- 20.04.2020