Бражная колонна брагоректификационного аппарата косвенного действия производительностью 2, 7 тыс. дал/сут



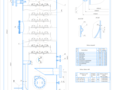
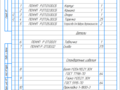
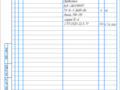
- Добавлен: 24.01.2023
- Размер: 1 MB
- Закачек: 0
Описание
Состав проекта
![]() |
![]() |
![]() ![]() ![]() |
![]() |
![]() |
![]() ![]() ![]() ![]() |
![]() ![]() ![]() |
![]() |
![]() ![]() ![]() |
Дополнительная информация
Спецификация (колонна) лист 2.CDW

Колонна бражная.cdw

Производительсность установки далс 3000
Давление в колонне МПа 0
Температура среды в кубе
Среда в аппарате взрывоопасная
Тип тарелок колпачковые
Обозначение или способ
Электрод или сварочная
испытании и поставке аппарата должны
выполняться требования:
а) ГОСТ 12.2.003-74 "Оборудование производственное. Общие
требования безопасности";
б) ОСТ 26-291-94 "Сосуды и аппараты стальные сварные.
Технические требования."
Монтаж аппарата произвести в соответсвии со СНИП 3.05.05-84.
Материал деталей колонны
соприкасающихся с разделяемыми
- сталь 12Х18Н10Т ГОСТ 5632-61
сталь Ст 3 ГОСТ 380-71.
Материал опоры - сталь В Ст 3 сп ГОСТ 380-71.
Материал прокладок - фторопласт 4 ГОСТ 10007-72.
Аппарат испытать на прочность гидравлически в горизонтальном
положении под давлением 0
в вертикальном положении
Сварные соединения должны соответствовать требованиям
ОСТ 26-01-82-77 "Сварка в химическом машиностроении
Сварные швы корруса контролировать УЗК ГОСТ 14782-76 или
рентгенопросвечиванием ГОСТ 7512-82 в объеме 100%.
недоступные контролю УЗК или рентгенопросвечиванием
контролировать в соответствии с отраслевой инструкцией
Покрытие наружной поверхности детали и сборочных единиц
выполненых из углеродистой стали
а также наружной и внутренней
Условия хранения-7 (ж
Срок защиты без переконсервации-2 года.
Действительное расположение штуцеров
Неуказанный вылет штуцеров 150 мм.
*Размеры для справок.
** Предельное отклонение на длину развёртки
Техническая характеристика
Для датчика температуры
Для датчика давления
Таблица сварных швов
Технические требования.
Курсовая.docx
ТЕМА: « Бражная колонна брагоректификационного аппарата
косвенного действия производительностью 27 тыс. далсут»
СПЕЦИАЛЬНОЕ УКАЗАНИЕ ПО ПРОЕКТУ: При разработке использовать 3-х
колонный брагоректификационный аппарат косвенного действия.
Технологическая часть
1. Описание брагоректификационных установок непрерывного
2. Описание машинно-аппаратурной схемы 3-х колонной
брагоректификационной установки косвенного действия
3. Описание конструкции бражной колонны
1. Материальный баланс
2. Определение оптимального флегмового числа и построение рабочих линий для верхней и нижней частей колонны
3. Определение объемных расходов пара и жидкости в колонне
4. Определение скорости пара и диаметра колонны
5. Гидравлический расчёт тарелок
6. Определение количества тарелок и общего гидравлического сопротивления колонны. Определение высоты колонны
Монтаж и ремонт брагоректификационной колонны
1. Монтаж брагоректификационной установки
2. Ремонт проектируемого аппарата
Список использованной литературы
Бродильная промышленность – одна из старейших отраслей промышленности в России. Анализ современного технического уровня предприятий бродильной промышленности показывает что его совершенствование осуществляется в направлении повышения единичной мощности сокращения вспомогательных операций повышения уровня механизации и автоматизации снижения материало- и энергоемкости улучшения санитарной обработки.
Модернизация предприятий бродильной промышленности строительство
крупных заводов требует четкой организации проектировочных работ с учетом достижений мировой практики внедрения новых технологических процессов и оборудования ликвидации диспропорций в мощностях цехов
повышения уровня механизации транспортно-складских работ.
На спиртовых и ликеро-водочных заводах внедрена новая современная техника. Многие заводы перешли на непрерывную тепловую обработку сырья с использованием вакуум-охлаждения при осахаривании широкое распространение получили непрерывно-поточный и циклический методы брожения а также современные методы и аппаратура для мембранного разделения и фракционирования на основе ультрафильтрации обратного осмоса и ионного обмена. Разработано новое оборудование для непрерывного приготовления и очистки водки а также экстракционно-выпарное оборудование.
Перед бродильной промышленностью стоят задачи по внедрению новой более эффективной техники и технологии обеспечивающих полное и комплексное использование сырья высокоэффективных машин и аппаратов непрерывного действия создающих возможность интенсифицировать и автоматизировать процессы и внедрять АСУТП. Эффективность предприятий бродильной промышленности определяется в основном степенью использования сырья и связанными с ней потерями а также издержками производства среди которых главными являются затраты электроэнергии.
Требования предъявляемые к качеству продуктов выпускаемых предприятиями бродильной промышленности определяют не только тип оборудования который выполняет ту или иную операцию но и условия принципы и методы его работы а также обуславливают наличие различных типов и марок машин и аппаратов применяемых в промышленности.
В бродильной промышленности применяются разнообразные виды оборудования которые классифицируются по следующим признакам: характеру воздействия на обрабатываемый продукт; структуре рабочего цикла; степени
механизации и автоматизации; принципу сочетания в производственном потоке; функциональному признаку.
Возрастающая потребность отраслей народного хозяйства в продуктах предприятий бродильной промышленности обуславливает разработку новых принципов подхода к проектированию технологических линий бродильных производств. Очевидно что разработка технологических линий должна осуществляться с учетом функционально-целевого назначения системы особенностей продукта производства и совокупности ограничений налагаемых спецификой объекта на структуру и функции системы.
При проектировании и разработке технологических схем на типы используемого оборудования виды сырья и способы реализации технологического процесса а также с учетом требований предъявляемых к качеству продукта эффективности разрабатываемой схемы экономии затрачиваемых на производственный процесс ресурсов и др. возможно получение большого числа вариантов структур технологических схем что создает определенные трудности для разработчиков. Такая задача может быть решена на основе системного анализа технологического потока.
Этот метод создания новой технологической схемы производства и оптимизации ее структуры заключается в рассмотрении различных аспектов базирующихся на выделении в исследуемой системе структурных составляющих и определении их роли относительно друг друга.
В настоящее время главным видом оборудования для выделения и очистки спирта в спиртовой промышленности являются брагоректификационные
установки. Основные критерии оценки совершенства этих установок – технологические и теплотехнические показатели их работы. Необходимо учитывать также условия эксплуатации установок и их металлоемкость как основной параметр определяющий стоимость установки. Основываясь на этом можем провести сравнительный анализ наиболее характерных типов брагоректификационных установок.
На протяжении уже многих лет типовыми в спиртовой промышленности были брагоректификационные установки (БРУ) косвенного действия обеспечивающие выработку спирта высокого качества при высоком его выходе. Обычно в состав БРУ косвенного действия входят бражная эпюрационная и ректификационная колонны с дефлегматорами конденсаторами и вспомогательными элементами. Изготавливают установки по чертежам «Гипропищепром II» Тамбовский машиностроительный завод Комсомолец (Россия) Сумской машиностроительный завод (Украина). Все оборудование и продуктовые коммуникации выполнены по традиции из меди.
Единственным но существенным недостатком таких установок является повышенный удельный расход тепловой энергии и воды. При наличии трех основных колонн они обычно потребляют около 52 кг пара на 1 дал выработанного спирта высшей очистки.
Стремясь уменьшить расход пара ВНИИПБТ разработал БРУ косвенно-прямоточного действия которая обеспечивает выработку спирта при меньшем удельном расходе пара на 15-25 %.
При оптимизации режима работы установки расход пара может быть снижен до 40 кгдал. В установке частично предусмотрено двукратное использование тепла греющего пара.
Киевский ТИПП разработал БРУ прямого действия в которой предусмотрено двукратное использование всего тепла греющего пара. Греющий пар вводится только в бражную колонну а эпюрационная и спиртовая колонны обогреваются спиртоводным паром из бражной колонны. Установка работает стабильно обеспечивая высокое качество спирта при удельном расходе пара 33-34 кг на 1 дал спирта проста в конструкции и
менее металлоёмка. Особенно эффективно применение таких установок на заводах небольшой производительности где эксплуатируются бражные колонны с тарелками двойного кипячения и межтарелочным расстоянием 280 – 340 мм.
Типовые установки выпускаются для номинальной производительности 15; 20; 30 и 60 тыс. дал спирта ректификованного в сутки. В состав установок по желанию заказчика включают колонны окончательной очистки или сивушную (для установок более 3 тыс. дал спирта в сутки).
На предприятиях типовые установки существенных изменений не претерпевают. Однако имеются тенденции применять более мощные установки чем номинальная (плановая) мощность завода. В ряде случаев колонны наращивают дополнительными тарелками (ректификационную до 70-80 эпюрационную до 50 тарелок) увеличивают поверхность теплообмена дефлегматоров. Проводят также некоторое совершенствование аппаратуры например увеличивают число ходов для хладагента в дефлегматорах улучшают конструкцию узла отделения сивушного масла.
Заводы большой производительности от 7 до 10 тыс. дал в сутки не имея типовых установок соответствующих их мощности используют по две установки производительностью 6 тыс. дал в сутки или комбинации таких установок что приводит к затруднениям в их эксплуатации.
В России повышение качества ректификованного спирта на типовых установках косвенного действия достигнуто в результате совершенствования технологии и аппаратуры ректификации. Наиболее распространенные мероприятия приведены ниже:
Увеличение числа тарелок от 66 до 72 и более в ректификационной колонне и до 25 – в бражной колонне;
Применение окончательной очистки спирта в специальных колоннах окончательной очистки.
Дальнейшее увеличение (на 12-15 кгдал) расхода пара на эпюрацию и увеличение с этой целью дефлегматоров колонны.
Оснащение колонн выносными кипятильниками.
Внедрение средств автоматизации работы БРУ.
Упорядочение отбора и возврата загрязненных спиртовых фракций.
В России и за рубежом разрабатываются новые БРУ. При этом работы ведутся по следующим направлениям:
Разрабатываются принципиально новые более эффективные технологические схемы установок;
Проводятся выбор и испытания в промышленных условиях массообменных тарелок.
В основном в России продолжается работа по совершенствованию отдельных узлов и технологических приемов в установках ректификации спирта косвенного действия. К сожалению экономичность эксплуатации установок ректификации спирта косвенного действия оставляет желать лучшего (от 40 до 60 кг пара на 1 дал произведенного спирта тогда как зарубежные установки используют лишь до 20 кг пара на 1 дал спирта). Тем не менее качество спирта признано хорошим.
Из новых контактных устройств предложенных для колонн браго-ректификационных установок БРУ необходимо отметить чешуйчатые однонаправленные тарелки для бражных колонн и провальные тарелки для колонн большой мощности. Существенным преимуществом чешуйчатых тарелок является большой диапазон нагрузок по жидкости и по пару (таблица 2) малый брызгоунос при скорости бара > 15 мсек высокая удельная производительность (удельная нагрузка на живое сечение тарелки) и скорость перегонки.
Исследования и опытная эксплуатация показали что для эпюрационных и ректификационных колонн перспективными являются клапанные ректификационные тарелки обеспечивающие необходимую устойчивость в условиях меняющихся нагрузок по жидкости в первую очередь и по пару. Клапанные ректификационные тарелки обеспечивают эффективную работу при значительно больших скоростях пара (08 – 15 мс). При этом съем
спирта с 1 м3 колонны достигает 9-10 далчас что в 15 раза превышает показатель для многоколпачковой тарелки типовой ректификационной тарелки.
Следует отметить значение качества греющего пара и очистки котловой воды для технологии ректификации и обеспечения высокого ректификованного спирта. Обычно в косвенных установках одна или несколько колонн обогреваются открытым паром. При этом если конденсат пара имеет щелочную реакцию проба на окисляемость спирта и особенно его дегустационные показатели будут низкими.
На заводах где нет системы автоматизации БРУ отсутствуют и другие средства редуцирования в частности редукционные пружинные вентили что усложняет работу и нарушает технологию.
Охлаждающая вода поступает на БРУ преимущественно из открытых водоемов (рек озёр прудов) и артезианских скважин. Нередко повышенная жесткость воды вызывает инкрустацию накипью поверхностей теплообмена.
Для предотвращения накипи применяют методы фосфатирования воды с замещением солей жесткости растворимыми солями насыщение воды углекислотой с целью ограничить декарбонизацию солей временной жесткости. Большой интерес представляет магнитный и ультразвуковой способы обработки воды.
Наиболее полно решается проблема водоснабжения установок с внедрением системы оборотного водоснабжения когда горячая вода из дефлегматоров направляется на градирни и повторно направляется в дефлегматоры. Основная проблема при этом – это потери воды на испарение которые могут составить до 10 %. Например расход охлаждающей воды на дефлегматоры составляет от 100 до 200 м3час это значит что подпитка градирни должна быть организована химически чистой водой в объеме от 10 до 20 м3час. К тому же градирня снижает температуру оборотной воды лишь на 5 градусов ниже температуры атмосферного воздуха а этого иногда не достаточно. Решить эту проблему можно применив абсорбционную установку использующую вторичное (бросовое) тепло.
Для размещение БРУ строятся здания высотой 25-30 метров и площадью в плане не менее 70 м 2. Здания преимущественно капитальные с несущими стенами и перекрытиями на 23 площади по высотным отметкам +6 +12 +18 +24 м.
В целом брагоректификационное отделение вместе со зданием и установкой является дорогостоящим и составляет около 20% основных фондов предприятия.
Зарубежный опыт показывает что достаточным будет размещение в здании операторской станции а для насосов и дефлегматоров сооружать облегченную закрытую козырьком и остекленную площадку. При этом необходимо заранее оговорить данные условия с поставщиком (разработчиком) технологии БРУ.
Технологическая часть.
1. Описание брагоректификационных установок непрерывного действия.
Брагоректификационные установки нашли самое широкое применение на спиртовых заводах.
В их состав как правило входят три основных колонны: бражная эпюрационная и спиртовая а также 1-3 дополнительных устанавливаемых по мере необходимости.
Бражная колонна служит для выделения летучей части бражки от нелетучей и ее освобождения от экстрактивных веществ твердой фазы и большей части воды. Побочный продукт полученный из бражки после отгонки спирта в бражной колонне называется бардой. Она выводится из нижней части колонны с ней удаляются взвешенные частицы экстрактивные вещества часть воды и большая часть хвостовых примесей. Летучая часть бражки которая содержит этиловый спирт воду и сопутствующие летучие примеси выходит в виде пара или бражного дистиллята. Спирт-сырец спиртово-водный пар которые выходят из бражной колонны и бражной дистиллят различаются только по концентрации в них спирта: спирт-сырец имеет крепость не менее 88 % по объему спиртово-водный пар и бражной дистиллят - 40-55 % по объему. Состав примесей в них примерно одинаков.
Бражной дистиллят может быть представлен 5 основными компонентами: этиловый спирт С головные примеси Г хвостовые примеси Х промежуточные примеси П и концевые примеси К. Два последних компонента можно представить как головные или хвостовые тогда рассматриваемая смесь может рассматриваться как смесь 3 компонентов С Г Х. Для разделения 3-х компонентной смеси достаточно 2 колонн. Для этой цели используют эпюрационную и спиртовую колонны.
Эпюрационная колонна служит для выделения головных примесей (головной или эфироальдегидной фракции). Этот процесс называется эпюрацией а спирт освобожденный от головных примесей получил название эпюрата.
В спиртовой колонне спирт-эпюрат разделяется на практически чистый этиловый спирт (спирт-ректификат) и лютерную воду т.е. освобождается от
промежуточных примесей.
Последовательность включения основных колонн в установку может быть различной однако следует учитывать ряд основных закономерностей определяющих наилучшие условия отделения примесей спирта:
известно что коэффициент ректификации почти всех головных примесей меньше при низкой концентрации спирта поэтому их выделение из слабоградусных растворов идет в колоннах с меньшим числом тарелок при меньшем расходе пара поэтому эпюрационная колонна включается в установку сразу за бражной и питается бражным дистиллятом;
освобождение спирта от промежуточных примесей лучше всего проводить из зоны максимального их концентрирования; это возможно в средней части колонны в которой по высоте концентрация спирта изменяется от 0 до азеотропной точки то есть в спиртовой колонне;
извлечение концевых примесей лучше проводить в верхней части колонны в которой концентрация спирта максимальна тогда концевая примесь имеет характер головной и отделяется в зоне выше зоны концентрирования этанола; на практике фракцию спирта обогащенного метанолом (концевой примесью) отделяют в самой верхней зоне спиртовой колонны в виде так называемого непастеризованного спирта. Для получения спирта полностью освобожденного от метанола необходима установка еще одной колонны называемой колонной окончательной очистки. Для выделения и концентрирования промежуточных примесей устанавливают сивушную колону.
Брагоректификационные установки бывают прямого полупрямого и косвенного действия.
В установках прямого действия (рис 1.1.1.) эпюрации (выделению головных примесей) подвергается бражка. Бражка представляет собой
слабоконцентрированный раствор спирта и примесей. При низких концентрациях спирта коэффициенты ректификации примесей имеют большие
Рис. 1.1.1. Принципиальная схема брагоректификационной установки прямого действия.
значения; следовательно их удаление будет более интенсивным. После выделения основной массы головных примесей и значительной части промежуточных примесей в эпюрационной колонне бражка поступает в
бражную колонну 1. Здесь из бражки выделяются этиловый спирт хвостовые примеси и остатки головных и промежуточных примесей. Основную массу паров из бражной колонны 1 направляют в ректификационную колонну 9. Некоторая часть паров из бражной колонны 1 поступает в эпюрационную колонну 3 для ее обогревания; для этой цели служит труба 2 снабженная дроссельным клапаном. Количество пара поступающего в эпюрационную колонну регулируется дроссельным клапаном.
Хвостовые и промежуточные продукты а также остатки головных продуктов отбирают в ректификационной колонне. Ректификат отводя в жидком виде с одной из верхних тарелок ректификационной колонны.
Рис 1.1.2. Принципиальная схема брагоректификационной устаноки полупрямого действия.
В установке полупрямого действия (рис 1.1.2) бражка не подвергаясь предварительной эпюрации поступает непосредственно в бражную колонну 1.В этой колонне выделяются спирт и все примеси. Пары направляются через ловушку-сепаратор 3 в эпюрационную колонну 2 здесь из них выделяются головные примеси.
Очищенный от головных примесей спиртсодержащий хвостовые и прможуточные примеси (эпюрат) в жидком виде поступает в ректификационную колонну 9. Отбор спирта-ректификата сивушного масла и промежуточных продуктов производится так же как и в аппаратах прямого
Рис. 1.1.3. Принципиальная схема брагоректификационной установки косвенного действия.
В установках косвенного действия (рис. 1.1.3) водно-спиртовые пары поднимающиеся из бражной колонны 1 полностью сгущаются в конденсаторе 2 и в жидком виде поступают на эпюрацию в колонну 4. Эпюрат направляется
в ректификационную колонну 9 где выделяются промежуточные продукты сивушное масло и спирт-ректификат. Данная установка принята как типовая благодаря высоким эксплуатационным показателям.
брагоректификационной установки косвенного действия.
На спиртовых заводах СНГ в качестве типовых приняты установки косвенного действия. Они стабильны в работе легки управлении эксплуатации управлении обеспечивают высокое качество спирта; примеси
выделенные при ректификации выводятся в концентрированном виде.
Промышленностью выпускаются БРУ производительностью 1000 1500 2000 дал спирта в сутки с 3 или 4 колоннами (с колонной окончательной очистки) и 3000 и 6000 дал спирта в сутки (с двумя дополнительными колоннами: окончательной очистки и сивушной). На ряде крупных заводов устанавливается также разгонная колонна для выделения спирта из головной фракции.
Бражная колонна имеет 21-28 одноколпачковых или ситчатых тарелок с межтарелочным расстоянием 280-550 мм. Ситчатыми тарелками оснащены бражные колонны установок производительностью 3000 дал сут и более.
В эпюрационной колонне независимо от производительности 39-41 многоколпачковых тарелок с межтарельчатым расстоянием 170 мм.
Спиртовая колонна имеет 71-74 многоколпачковых тарелок такого же типа как в эпюрационной с межтарельчатым расстоянием 170 мм.
Колонны обогреваются открытым или закрытым паром. К каждой подключены теплообменники для конденсации пара.
Бражка поступающая в установку проходит подогреватель бражки (8) где нагревается до температуры 70-85 0С в сепараторе (5) освобождается от СО2 и других неконденсирующихся газов затем вводится в бражную колонну (1).
Вместе с неконденсирующимися газами уносится некоторое количество
паров спирта. Для улавливания спирта из СО2 установлен конденсатор (4) конденсат из которого направляется в верхнюю часть эпюрационной колонны. В нижней части к бражной колонне подключен гидравлический затвор (13) с пробным холодильником (12).
Спиртоводный пар из бражной колонны проходит пеноловушку (иногда ее встраивают внутрь колонны) частично (приблизительно на 50 %) конденсируется в подогревателе бражки и возвращается в колонну в виде флегмы (сконденсированная жидкость в дефлегматоре).
Остальная часть пара конденсируется в основном (6) и дополнительном конденсаторе (7) отдавая теплоту конденсации охлаждающей воде.
Полученный бражной дистиллят крепостью 40-50 % направляется для питания эпюрационной колонны (2) на 20-ую 27-ую или 36-ую тарелку снизу. Пар выходящий из эпюрационной колонны конденсируется в основном в дефлегматоре (15) и небольшая часть в конденсаторе (16) в результате отвода теплоты охлаждающей водой. Часть пара которая конденсируется в конденсаторе имеет максимальную концентрацию головных и концевых примесей и называется головной фракцией (ГФ).
Учитывая что коэффициенты испарения большинства головных примесей увеличиваются с понижением концентрации спирта для более полного их выделения в эпюрационную колонну предусматривается подача воды. Этот прием получил название гидроселекции. Предельное количество воды которое может быть подано в колонну - 09 кг на 1 кг вводимого спирта. В этих условиях улучшается отделение уксусно-этилового и уксусно-изоамилового эфиров но несколько ухудшается извлечение уксусного альдегида. Чтобы улучшить процесс отделения уксусного альдегида следует увеличить подачу пара в колонну.
Освобожденный от головных и частично от концевых примесей бражной дистиллят - спирт-эпюрат крепостью 30-35 % поступает на питание спиртовой колонны (3) на 16-ую тарелку снизу. Спиртовая колонна оснащена дефлегматором (17) и конденсатором (18). Часть водно-спиртовых паров конденсируется в дефлегматоре и возвращается для питания колонны.
Наибольшая часть пара направляется в конденсатор где после конденсации образуется так называемый непастеризованный спирт который подается в верхнюю часть эпюрационной колонны. Отбирается он из конденсатора с 1-3-й тарелки сверху в количестве 3 %. С ним отводятся головные и концевые примеси которые выделяются и концентрируются в пастеризационной части (выше места отбора ректификованного спирта) спиртовой колонны. Пар конденсируется за счет отвода теплоты охлаждающей водой.
Спирт-ректификат (пастеризованный спирт) обычно отбирается с 4-10-й тарелки сверху проходит через холодильник (20) и направляется в спиртоприемное отделение через фонарь (19) и контрольный снаряд (23) для учета спирта.
Промежуточные примеси выводятся из спиртовой колонны в виде двух продуктов сивушной (парообразной) фракции и сивушного спирта.
Сивушный спирт в количестве 2 % отбирается с 17 20 и 25-й тарелки в жидком или парообразном состоянии и направляется в бражную или эпюрационную колонну или выводится как товарный продукт. Сивушная фракция отбирается в количестве 3-4 % в виде пара с 5 7 9 и 11-й тарелки снизу конденсируется охлаждается в холодильнике (21) и направляется в экстрактор (22) для освобождения от этанола путем промывки водой.
С сивушной фракцией в основном выводятся нижние промежуточные примеси - изоамиловый изобутиловый и частично пропиловый спирты с сивушным спиртом - верхние (эфиры и частично пропиловый спирт).
После конденсации охлаждения и экстрагирования из сивушной фракции спирта получают сивушное масло которое выводится как товарный продукт. Сивушный спирт охлаждается и удаляется из установки в виде побочного продукта. Промывная вода из экстрактора возвращается в спиртовую колонну на 12-14-ую тарелку снизу.
Лютерная вода (флегма освобожденная от спирта) отбирается снизу колонны через гидравлический затвор (13) и используется частично для промывки сивушной фракции частично сбрасывается в канализацию. Возможно
использование ее для приготовления замеса. Для улавливания спирта из несконденсировавшихся газов служат спиртоловушки (14). Все колонны снабжены вакуум-прерывателями регуляторами подачи воды пара термометрами.
Для непрерывного контроля работы установок на линии подачи бражки отбора головной фракции непастеризованного сивушного и ректификованного спирта а также сивушной фракции устанавливают ротаметры.
БРУ монтируют в отдельном изолированном помещении на 4-х этажах.
Широкое распространение приобретают установки полупрямого или косвенно-прямоточного действия разработанные ВНИИПБТ. Они выпускаются производительностью 100 500 1000 1500 2000 3000 6000 дал в сутки. Отличительной особенностью этих БРУ является предварительная эпюрация бражки в бражной колонне и использование части спиртоводного пара выходящего из бражной колонны на обогрев эпюрационной колонны.
Бражная колонна в верхней части имеет 6-11 тарелок на которых осуществляется эпюрация бражки (освобождение от головных примесей). Нижняя отгонная часть имеет 17-23 тарелки. Бражка нагретая до 70-75 єС пройдя сепаратор СО2 поступает на верхнюю тарелку эпюрирующей часть бражной колонны и освобождается от головных примесей за счет спиртоводного пара из отгонной части колонны. Спиртоводный пар с головными примесями из верхней части брагоэпюрационной колонны конденсируется в подогревателе бражки и конденсаторах и в виде бражного дистиллята подается на питание эпюрационной колонны. Бражка освобожденная от основной части примесей стекает в отгонную часть бражной колонны и из нее испаряется оставшийся спирт. Спиртоводный пар из отгонной части делится примерно на 2 равных потока: один идет на эпюрацию бражки а другой - через пеноловушку на обогрев эпюрационной колонны. При этих условиях 60-80 % спирта содержащегося в бражке идет на питание эпюрационной колонны оставшаяся часть - на ее обогрев в виде
спиртоводного пара. Остальные режимы работы установки косвенно-прямоточного действия аналогичны работе БРУ косвенного действия.
Выход спирта определяется как его объем в декалитрах полученный из 1-й т сбраживаемых углеводов (крахмала сахаров) в пересчете на крахмал.
Теоретический выход вычисленный по уравнению спиртового брожения составляет 7198 дал из 1-й т условного крахмала.
Практический выход колеблется от 815 до 93 % от теоретического и нормируется для различных видов сырья. Его значение меньше теоретического на величину потерь. В производстве спирта учитывают механические и технологические потери.
Рис. 1.2.1. Аппаратно-технологическая схема трехколонной брагоректификационной
установки косвенного действия.
Механические потери вызваны неисправностью оборудования нарушениями в организации процесса производства. К ним относят потери от рассыпания зерна картофеля от утечки через неплотности в трубопроводах потери полупродуктов при мойке оборудования испарения спирта через фланцы колонн конденсаторов и др.
Технологические потери обусловлены сущностью процессов спиртового производства и имеют скрытый характер. Они могут быть выявлены только при постадийном контроле и учете производства. К ним относят потери крахмала при измельчении сырья при разваривании потери на синтез биомассы дрожжей на образование побочных продуктов брожения на несброженные сахара потери спирта с газами брожения с бардой и т.д. Пути снижения этих потерь связаны с совершенствованием технологических процессов соблюдением режимов на каждой производственной стадии.
В трехколонной брагоректификационной установке (граф. часть-1 лист)
бражка насосом 37 подается в подогреватель (конденсатор) 4.
Подогревание бражки происходит за счет конденсации паров поступающих
из бражной колонны 35. Пары проходят при этом через ловушку 3 где отделяются увлеченные жидкие частицы. Подогретая бражка поступает в сепаратор 2 где из нее выделяется диоксид углерода. Выделившийся в сепараторе газ поступает в конденсатор 1 где конденсируются увлеченные газом пары спирта и примесей а затем напрвляются в спиртоловушку.
Бражка поступает в бражную колонну 35 с регулятором 36 для выпуска барды. Из конденсаторов 1 5 7 подогревателя бражки 4 и спиртоловушки 8 конденсат водно-спиртовых паров направляется в эпюрационную колонну 10 которая имеет дефлегматор 11 и конденсатор 12. Головные продукты из конденсатора 12 поступают в холодильник 26 а далее через ротаметр 28 в фонарь 27. Освобожденный от основной части головных примесей водно-спиртовой раствор (эпюрат) направляется в ректификационную колонну 20.
Эта колонна снабжена дефлегматором 13 и конденсатором 15. Из последнего часть конденсата (нестандартный или непастеризованный спирт) отводится в эпюрационную колонну 20.
Спирт-ректификат в жидком виде с 3 4 5 6 и 7-й тарелок (считая сверху) ректификационной колонны поступает в холодильник 23 откуда через ротаметр 25 направляется в фонарь 24. Сивушное масло поступает в виде паров через сепаратор 18 в конденсатор 16. Конденсат направляется в маслоотделитель 17. Выделенное в нем сивушное масло направляется в хранилище; водно-спиртовой раствор из этого маслоотделителя возвращается в ректификационную колонну через подогреватель 22. Греющей средой в этом подогревателе служит лютерная вода отводимая из ректификационной колонны в сборник 31 насосом 32. В ректификационной колонне также отбираются промежуточные продукты (сивушный спирт) и направляются в холодильник 21.
Для предохранения от смятия колонны снабжены вакуум-прерывателями 6 9 14 29 33. Пробный холодильник 30 предназначен для конденсации паров выделяемых бардой и лютерной водой. В конденсате этих паров также содержится спирт. Подача греющего пара в бражную и ректификационную колонну регулируется паровыми регуляторами 19 и 34. В эпюрационную колонну пар поступает из выварной части ректификационной колонны.
Разделение жидких однородных или многокомпонентных растворов и га-зовых смесей на индивидуальные практически чистые компоненты или их фракции методами ректификации широко применяется как основной технологический процесс во многих производствах химической и нефтеперерабатывающей отраслях промышленности. Кроме того ректификация используется в спиртовой промышленности в технологиях получения редких и рассеянных элементов в установках разделения природного газа и воздуха.
Процессы ректификации основаны на тепло- и массообменном взаимодействии между паровой и жидкой фазами компонентов входящих в бинарный раствор.
Техническая характеристика брагоректификационных
установок косвенного действия
Производительность далсут
Площадь поверхности бражного
Эпюрационная колонна
в концентрационной части
Площадь поверхности дефлегматора м 2
Ректификационная колонна
Физическая сущность процесса ректификации состоит в том что в по-догретом однородном жидком растворе низкокипящий компонент (НКК)
обладая более высокой упругостью паров переходит более интенсивно в паровую фазу которая при этом обогащается им. Одновременно жидкая фаза обогащается высококипящим компонентом (ВКК). При конденсации паров фазы образуется раствор нового состава с более высоким содержанием низкокипящего компо-нента по сравнению с исходным раствором. Если процесс испарения жидкости и конденсации паров производится однократно то реализуется процесс перегонки – дистилляции исходной смеси если процессы испарения и конденсации повторяются в одном аппарате
многократно то такой процесс многоступенчатой перегонки называют
Процесс ректификации осуществляется в колонных аппаратах тарельчатого или насадочного типа. На каждой ступени контакта (на тарел-ке или в слое насадки определенной высоты) происходит конденсация паров поступающих с нижележащей тарелки. За счет тепла конденсации находящаяся на тарелке жидкость закипает и выделяет пары обогащенные низкокипящим компонентом и поднимающиеся на вышележащую тарелку. Обогащенная высококипящим компонентом жидкость по переливному устройству перетекает на нижележащую тарелку.
Осуществляя на тарелках многоступенчатый тепло- и массообменный противоточный контакт между парами поднимающимися снизу вверх по колон-не и стекающей сверху вниз жидкостью реализуют процесс разделения исход-ной смеси на отдельные практически чистые компоненты или фракции с близ-кими температурами кипения компонентов [1].
В результате разделения исходного раствора из верхней части колонны отводят пары после конденсации которых получают дистиллят состоящий из НКК с небольшой примесью другого компонента. Из нижней части колонны от-водят кубовый остаток состоящий из ВКК с примесью НКК.
Способ контактирования потоков может быть ступенчатым (в тарель-чатых колоннах) или непрерывный (в насадочных колоннах).
Назначение контактных устройств (тарелок насадки) состоит в созда-нии условий способствующих максимальному приближению парового и жидкост-
ного потоков. Чтобы эти потоки могли обмениваться веществом и энергией они должны быть неравновесны друг другу. При контактировании парового и жидкостного потоков в результате массо- и теплообмена величина неравно-весности уменьшается затем потоки отделяются один от другого и процесс продолжается путем нового контактирования этих фаз уже на другой смежной ступени с другими жидкими и паровыми потоками. В результате многократно повторяющегося на последовательных тарелках (ступенях) кон-тактирования движущихся в противотоке по высоте колонны жидкости и
пара состав взаимодействующих фаз существенно изменяется: паровой поток при движении вверх обогащается НКК а жидкостный стекая вниз обедняется им т.е. обогащается ВКК. При достаточно большом пути контактирования противоположно движущихся потоков можно получить пар выходящий из верхней части колонны - сравнительно чистый ВКК так называемый кубовый остаток.
Флегма образуется в результате частичной конденсации паров выходящих из верхней части колонны в специальных теплообменных аппаратах — дефлегматорах или вводится в колонну в виде питания.
3. Описание конструкции бражной колонны.
Объект проектирования бражная колонна брагоректификационной установки для производства этилового спирта представляет собой цилиндрический вертикальный аппарат (рис.1.3.1) состоящий из отдельных царг 1 которые соединены между собой болтовыми фланцевыми соединениями. Колонна в вертикальное положение устанавливается на опору 3 цилиндрического типа.
Внутри царг горизонтально установлены колпачковые тарелки. Бражка подается на питательную тарелку колонны через штуцер Н. Перетекая с тарелки на тарелку и находясь в непрерывном контакте с поднимающимся по колонне паром бражка освобождается от этилового спирта и других летучих компонентов (примесей). Пар насыщенный легколетучими компонентами укрепляется в верхней части колонны и выводится через штуцер расположенный в крышке 2 колонны.
Из бражки стекающей сверху вниз по колонне выделяются осадки которые засоряют тарелки поэтому над каждой тарелкой встроен люк А для осмотра и чистки.
Над верхней тарелкой расположен штуцер для ввода флегмы – конденсата бражного дистиллята. Для контроля и управления процессом ректификации в колонне предусмотрены штуцера для подключения вакуум-прерывателей и установки гильз термометров М1 2
В днище колонны предусмотрен штуцер Т для полного слива жидкости в кубовой части колонны. Для технологических целей в кубовой части колонны предусмотрен лаз Щ.
Жидкость обедненную спиртом выводят из кубовой части аппарата через штуцер Р. Обогрев колонны осуществляется острым паром поступающим в кубовую часть колонны через барботер С. В кубовой части колонны имеются патрубки Н для подключения устройства регулирования уровня жидкости.
При выборе конструкционных материалов основным критерием является их химическая и коррозионная стойкость в заданной среде. Обычно выбирают материал абсолютно или достаточно стойкий в среде при ее рабочих
параметрах. К расчетным толщинам как правило добавляют соответствующие прибавки (на компенсацию коррозии и эрозии минусового допуска и т.д.) в зависимости от срока службы аппарата. В месте с тем следует учитывать и другие виды коррозии которым подвержены некоторые материалы в агрессивных средах.
Другим критерием при выборе материала является расчетная темпера-тура. Если температура является положительной для аппаратов установленных в не отапливаемых помещениях необходимо учитывать абсолютную минимальную зимнюю температура воздуха при которой аппарат может находиться под давлением или вакуумом.
Таким образом выбор конструкционного материала производится в зависимости от его коррозионной стойкости в заданной среде при рабочих условиях – давлении и температуре.
Кроме названных выше критериев относящихся к химической промышленности существует специфический критерий присущий пищевой промышленности. Таким критерием является влияние материала на вкусовые качества продукта и его товарный вид.
Рис. 1.3.1 – Эскиз бражной колонны.
В проектируемом аппарате – бражной колонне – рабочей средой является водно-спиртовой раствор а также его пары. Данная среда не является коррозионной. Аппарат работает при незначительном избыточном давлении необходимом для поддержания требуемого гидродинамического режима поэтому основным фактором влияющим на выбор конструкционного материала является влияние материала на органолептические свойства этилового спирта. Исходя из этого условия согласно рекомендациям [34] для смеси «этиловый спирт-вода» с заданными концентрационными и температурными характеристиками предложены следующие марки сталей в качестве конструкционного материала для корпуса и внутренних устройств бражной колонны выбираем легированную сталь марки 12Х18Н10Т. Для изготовления частей колонного аппарата не контактирующих с рабочей средой выбираем углеродистую сталь марки Вст3 20К и сталь 35[34] материал прокладок – фторопласт-4 [4].
Сталь 12Х18Н10Т не подвергается коррозии при взаимодействии с водно-спиртовым и его парами при температурах и концентрациях необходимых для нормального протекания технологического процесса. Прибавка на компенсацию коррозии зависит от проницаемости материала. Для стали 12Х18Н10Т проницаемость П=01 ммгод. Выбранный материал удовлетворяет требованиям к чистоте получаемого продукта. Немаловажным показателем при выборе конструкционного материала является его экономическая характеристика. Сталь 12Х18Н10Т является менее дорогостоящей кроме того она менее дефицитна.
Сталь 12Х18Н10Т ГОСТ 5632-72. Заменители: Сталь 08Х18Г8Н2Т Сталь 10Х14Г14Н4Т Сталь 12Х18Н9Т Сталь 12Х17Г9АН4.
Назначение: сварные аппараты и сосуды работающие в разбавленных растворах азотной уксусной фосфорной кислот.
Вид поставки (сортамент): сортовой (Шестигранник калиброванный ГОСТ 8560-78 Квадрат гкатаный ГОСТ 2591-88 Круг гкатаный ГОСТ 2590-88 Круг калиброванный хкатаный ГОСТ 7417-75) листы (Лист толстый гкатаный ГОСТ 19903-74тонкий хкатаный ГОСТ 19904-90) лента (Лента хкатаная коррозионностойкая ГОСТ 4986-79) проволока (Проволока коррозионностойкая ГОСТ 18143-72) трубы (Труба бесшовная холоднодеформи-рованная коррозионностойкая ГОСТ 9941-81 Трубка капиллярная ГОСТ 14162-79 Труба бесшовная особотонкостенная ГОСТ 10498-82 Труба электросварная коррозионностойкая ГОСТ 11068-81 Труба электросварная квадратная ТУ 14-105-566-93 Труба электросварная прямоугольная ТУ 14-105-566-93 Труба ГОСТ 19277) сетка (Сетка тканая ГОСТ 3826-82).
Основные физико-механические свойства:
-Модуль упругости EМПа 198000
-модуль сдвига GМПа 77000
-плотность кгм3 7900
-предел прочности В МПа не менее ..510
-предел текучести Т МПа не менее ..196
-относительное сужение % 55
-относительное удлинение % 38
Свариваемость: сваривается без ограничений.
Сталь Ст3 ГОСТ 380-94. Заменители: Сталь Сталь Ст2 Сталь Ст5 Сталь Ст6.
Назначение: прокат профильный рамы каркасы щитки кожухи - для свар-ных и клепаных конструкций.
Вид поставки (сортамент): сортовой (Квадрат гкатаный ГОСТ 2591-88 Круг гкатаный ГОСТ 2590-88 Полоса ГОСТ 103-76 Катанка ГОСТ 30136-95) листы (Лист толстый гкатаный ГОСТ 19903-74тонкий хкатаный ГОСТ 19904-90тонкий гкатаный из стали обыкновенного качества ГОСТ 19903-74) проволока (Проволока общего назначения ГОСТ
82-74) фа-сонный (Швеллер гкатаный ГОСТ 8240-89 Уголок гкатаный равнополочный ГОСТ 8509-93 Уголок гкатаный неравнополочный ГОСТ 8510-86 Уголок хгнутый равнополочный ГОСТ 19771-93 Балка двутавровая гкатаная ГОСТ 8239-89 Швеллер хгнутый равнополочный ГОСТ 8278-83) трубы (Труба водогазопроводная ГОСТ 3262-75 Труба электросварная ГОСТ 10704-91 Труба электросварная квадратная ТУ 14-105-566-93 Труба электросварная прямоугольная ТУ 14-105-566-93) сетки (Сетка тканая ГОСТ 3826-82).
-модуль упругости E МПа 200000
-модуль сдвигаGМПа 74000
-предел прочности В МПа не менее ..420
-предел текучести Т МПа не менее ..230
Свариваемость: хорошо сваривается всеми видами сварки.
Фторопласт-4 ГОСТ 10007-80 Е.
Назначение: каркасы катушки панели основания изоляционные покрытия антифрикционные.
Вид поставки (сортамент): пленки (Пленка фторопластовая ГОСТ 24222-80) трубы (Труба фторопластовая ТУ-6-05-1876) ленты (Лента фторопластовая ГОСТ 24222-80) листы (Пластина прессованная ТУ 6-05-810-88строганный ТУ 044-24) трубки (Трубка фторопластовая ГОСТ 22056-76) прутки (Втулка фторопластовая ТУ 6-05-810-88 Стержень фторопластовый вертикального прессования ТУ 6-05-810-88 Стержень фторопластовый экструзионный ТУ 6-05-041-535 Стержень фторопластовый горизонтального прессования ТУ 6-05-810-88 Втулка фторопластовая прессованная ТУ 6-05-810-88).
-модуль упругости при растяжении E МПа ..650
-плотность кгм3 2200
-прочность при изгибе МПа 16
-прочность при разрыве МПа . 25
-удлинение при разрыве % .250-500
-температура плавления tmax раб 0С 260
1. Материальный баланс
Расчёт ведётся согласно по методике приведённой в [5-8].
Рис. 2.1.1 – Схема к материальному балансу бражной колонны ректификационной установки с основными материальными потоками
где 7893 - относительная плотность 1 дал безводного спирта к 1 л воды;
- производительность установки по условному безводному спирту;
08 - коэффициент учитывающий потери спирта при ректификации;
- концентрация спирта в бражке масс. доля.
) Котельный пар Gr – расход пара на бражную колонну составляет 18 25 кгсут на 1 дал условного спирта. Принимаем предварительно 20 кгсут.
Gr = 20 2700 = 54000 кгсут
) Пар бражного дистиллята Gd.
) Пары образующие флегму Fd.
) Барда включая конденсат котельного пара Gw + Gr.
Таким образом уравнения материального баланса будут иметь следующий вид:
Gf + Gr + Fб = Gб + Fб + Gw + Gr (2.3)
- по низкокипящему компоненту:
Решая совместно уравнения (2.3) и (2.4) находим количество бражного дистиллята и кубового остатка (барды) :
Проверяем правильность составления материального баланса:
Материальный баланс составлен верно
2 Определение оптимального флегмового числа и построение рабочих линий для верхней и нижней частей колонны
Расчёт ведётся согласно по методике приведённой в [581011].
Для дальнейших расчетов необходимо концентрации исходной смеси дистиллята и кубового остатка выразить в мольных долях.
Перевод производим по формуле:
где - мольная масса этилового спирта; =46 кгмоль [5];
- мольная масса воды; =18 кгмоль [5]
Аналогично определяем концентрацию спирта в барде и бражном дистилляте:
Нагрузки бражной колонны по пару и жидкости определяются рабочим флегмовым числом .
Рабочее флегмовое число для бражной колонны определяется по зависимости:
где - коэффициент избытка флегмы; в бражных колоннах обычно принимается =11 25;
- минимальное флегмовое число.
где - содержание низкокипящего компонента в паровой фазе находящейся в равновесии с исходной смесью кмолькмоль смеси. Для =00302 =02 (см. приложение А).
Оптимальное флегмовое число позволяет использовать бражную колонну минимального объема при работе ее на заданную производительность и с требуемой полнотой разделения.
Зная оптимальное флегмовое число находим относительные мольные расходы из уравнения материального баланса:
где - число питания;
Определяем число питания по формуле:
Определяем кубовое число по формуле:
Определяем паровое число по формуле:
Проверяем материальный баланс:
Материальный баланс составлен верно.
Записываем уравнения рабочих линий процесса для верхней и нижней частей бражной колонны:
Определяем графическим путем число теоретических тарелок в бражной колонне. Для этого строим x-y диаграмму процесса ректификации (см. приложение А).
Ордината точки А пересечения рабочих линий:
= - следовательно расчёт выполнен верно.
3 Определение объемных расходов пара и жидкости в колонне
Расчёт ведётся согласно по методике приведённой в [5-810].
В дальнейших расчётах параметры определяемые для верхней части колонны обозначим знаком «'» параметры определяемые для нижней части колонны - «''».
Определяем количество паров поднимающихся в колонне по формуле:
Определяем количество жидкости стекающей вниз соответственно в верхней и нижней части колонны:
Определяем молекулярную массу пара:
где - определяем из уравнения рабочей линии процесса;
Определяем плотность паров по формуле:
где - давление в аппарате =012 МПа; =0106 МПа
- температура в верхней и нижней частях колонны соответственно;
Молекулярную массу жидкости определяем по формуле:
где - содержание спирта в жидкой фазе в верхней и нижней частях соответственно.
Плотность жидкости определяем по формуле:
- плотность спирта в верхней части колонны при температуре 84 0С =7312 кгм3 [5];
- плотность спирта в нижней части колонны при температуре 98 0С =7178 кгм3 [5];
- плотность воды в верхней части колонны при температуре 84 0С =9699 кгм3 [5];
- плотность воды в нижней части колонны при температуре 98 0С =9592 кгм3 [5].
Определяем объемные расходы фракций в верхней и нижней частях колонны:
4 Определение скорости пара и диаметра колонны
Расчёт ведётся согласно по методике приведённой в [6710].
Допустимую скорость пара определяем отдельно для верхней и нижней частей колонны:
где - фактор вспениваемости жидкости;
- плотность жидкости и пара соответственно;
- коэффициент зависящий от расстояния между тарелками.
Предварительно принимаем расстояние между тарелками =600 мм и коэффициент вспениваемости =075 [6].
Согласно [5] определяем значение коэффициента :
Определяем скорость пара в верхней части колонны:
Определяем скорость пара в нижней части колонны:
Ориентировочный диаметр для верхней и нижней частей колонны определяем из уравнения расхода:
Согласно рекомендациям [7] принимаем =07 м. Данный диаметр примерно соответствует рекомендациям [89] относительно проектирования брагоректификационных установок.
Пересчитываем действительную рабочую скорость газа в колонне:
5 Гидравлический расчёт тарелок
Расчёт ведётся согласно по методике приведённой в [6].
Зададимся необходимыми данными для дальнейшего расчёта.
В общем случае при выборе давления в колонне необходимо учитывать как эксплуатационные так и экономические показатели процесса ректификации. Однако если нет специальных требований к процессу следует предпочесть работу ректификационной колонны под атмосферным давлением. По условию давление в укрепляющей и исчерпывающей частях колонны заданы
Расчётная температура - 100°С (максимальное значение по t-x-y-диаграмме – см. приложение А).
По справочным данным [6] определяем основные характеристики колпачковой тарелки для колонны диаметром D=1800 мм.
Таблица 2.1 Характеристики колпачковой тарелки ТСК-Р D=1800 мм
Площадь слива Fсл м2
Площадь прохода пара F0 м2
Длина пути жидкости на тарелке lж м
Зазор под сливным стаканом а м
Количество колпачков m
Диаметр колпачка dк мм
В задачу дальнейших гидравлических расчётов основных параметров тарелки входит определение высоты сливного порога hпор подпора жидкости над сливным порогом hсл высоты прорезей колпачка hпр сопротивления тарелки и общего сопротивления колонны.
Рис. 2.5.1 – Расчётная схема к гидравлическому расчёту колонны с колпачковыми тарелками
Высота подпора жидкости над сливным порогом:
где - расход жидкости протекающей через сливное устройство м3с.
Высота прорезей в колпачках:
Примем [6 с. 231] колпачок с прямоугольными прорезями шириной b=4 мм. Количество прорезей в одном колпачке z=26.
Принимаем высоту прорези =25 мм [6].
В этом случае пар будет проходить через полностью открытые прорези.
Высота сливного порога:
hгб-hсл+hпр+hу (2.41)
В нашем случае высота установки колпачка hу=10 мм.
Высота пены образующейся на тарелке:
где - табличные коэффициенты определяемые в зависимости от типа тарелки; =023;=44·10-2;=46 [6 с.223 табл. 8.3]; – поверхностное натяжение жидкости на границе с паром Нм;
'=16·10-3 Нм; "=155·10-3 Нм [6].
Относительный унос жидкости:
где - табличные значения; =23·10-5; =116 [6].
Следовательно расстояние между тарелками выбрано верно.
Действительная нагрузка сливного устройства:
Действительная высота подпора жидкости (2.36) (2.37) мало отличается от
Проверим работоспособность сливного устройства тарелки.
Скорость жидкости в сливном устройстве:
Условие нормальной работы тарелки без её захлёбывания:
где - табличные значения; =0225; =08 [6].
Условие соблюдается и захлёбывания сливного устройства не произойдёт.
Скорость жидкости в зазоре между основанием тарелки и нижней кромкой сливного стакана:
Из приведённых расчётов следует что выбранная однопоточная тарелка обеспечит нормальную работу сливных устройств.
Гидравлическое сопротивление тарелки:
где - гидравлическое сопротивление сухой тарелки Па;
- сопротивление обусловленное силами поверхностного натяжения Па;
- сопротивление парожидкостного слоя на тарелке Па.
Гидравлическое сопротивление сухой тарелки:
где – коэффициент сопротивления;
- скорость пара в отверстиях тарелки мс.
Для колпачковой тарелки
Сопротивление обусловленное силами поверхностного натяжения:
где - эквивалентный диаметр м.
Сопротивление парожидкостного слоя на тарелке:
где - перепад уровня жидкости на тарелке м.
где - эквивалентный коэффициент сопротивления перетоку жидкости по тарелке.
Для колпачковых тарелок
Таким образом общее сопротивление контактного устройства:
6 Определение количества тарелок и общего гидравлического сопротивления колонны. Определение высоты колонны
Расчёт ведётся согласно по методике приведённой в [1011].
Графический метод определения числа тарелок (приложение А) дал следующие результаты:
Число реальных тарелок:
где - к.п.д. тарелки.
Определяем значение комплекса при средних величинах скорости пара и его плотности по высоте колонны:
Определяем высоту аппарата без опоры:
где - высота тарельчатой части;
- высота сепарационного пространства над верхней тарелкой =08 м [6];
- высота кубовой части =2 м [6].
где - количество тарелок
- расстояние между тарелками.
Монтаж и ремонт бражной колонны.
1. Монтаж бражной колонны. Испытание и пуск брагоректификационной
Правильность выбора метода и способа установки оборудования опреде-ляет трудоемкость сроки экономические показатели и степень безопасности проведения этих работ. Ниже приводятся основные методы монтажа применяемые в настоящее время.
Метод последовательного монтажа по месту из отдельных деталей и узлов. При этом методе монтажа начинают с установки базовой детали (или узла) к которой в последовательности обусловленной конструкцией аппарата или механизма подсоединяют остальные детали и узлы. Метод этот прост не требует мощного такелажного оборудования но трудоемок отнимает много времени и неэкономичен. В настоящее время когда монтажные организации хорошо оснащены самой разнообразной техникой применение его может быть оправдано только в исключительных случаях.
Метод монтажа укрупненными блоками. Этот метод находит сейчас самое широкое применение и является основным при монтаже тяжелого оборудования. Преимущество его в том что укрупнительную сборку узлов в блоки можно производить в стороне от места установки аппарата или механизма на специально оборудованных площадках или в при объектных мастерских с широким применением механизированного инструмента и специальных приспособлений. Кроме того укрупнительная сборка может производиться заблаговременно или параллельно с монтажом аппарата или механизма. При этом способе заметно снижаются трудовые затраты и резко уменьшается общая продолжительность монтажа.
Метод этот требует наличия в зоне установки аппарата или меха-низма достаточно мощных грузоподъемных средств.
Метод монтажа аппаратов и механизмов в полностью со-бранном виде. Этот метод экономически наиболее выгоден так как полно-стью исключает производство работ на высоте и устройство лесов и подмостей. Однако для его применения необходимо иметь грузоподъемные средства способные поднять полностью собранное оборудование.
В тех случаях когда для осуществления монтажа этим методом требуется создание специальных порой уникальных грузоподъемных механизмов целесообразность применения этого метода следует проверить расчетом. Экономия получаемая от применения этого метода должна перекрывать затраты связанные с изготовлением специальных грузоподъемных средств.
В тех случаях когда вес полностью собранного оборудования не превышает грузоподъемности имеющихся в наличии кранов метод монтажа оборудования в полностью собранном виде должен применяться безусловно.
Установку оборудования на фундамент по выбранному методу можно осуществить различными способами и с использованием различных грузоподъемных механизмов.
Способ наращивания. Монтаж ведется начиная с нижней части аппарата или механизма путем последовательного наращивания вышерасположенных частей аппарата или механизма. Этот способ требует устройства лесов и подмостей так как по мере наращивания оборудования работы приходится производить на все большей и большей высоте. Способ этот наиболее характерен для метода последовательного монтажа из отдельных деталей и узлов и применяется также при монтаже укрупненными блоками.
Способ подращивания. При этом способе монтаж ведется начиная с верхней части аппарата или механизма. Смонтированную часть поднимают на высоту достаточную для установки под ней нижележащей части после чего обе части стыкуют производят снова подъем смонтированной части оборудования на необходимую высоту и так до полной сборки всего аппарата или механизма. Способ этот обладает тем преимуществом что все работы производятся внизу и нет необходимости устраивать леса и подмости. Для своего осуществления способ требует наличия механизмов грузоподъемность которых не меньше веса полностью собранного аппарата или механизма.
Способ установки поворотом. Этот способ может быть осуществлен не только при помощи мачт и порталов но и при помощи стреловых кранов и трубоукладчиков и часто применяется наряду с другими способами при
монтаже вертикальных аппаратов в полностью собранном виде.
Потребная грузоподъемность механизмов при этом способе может оказаться значительно меньше веса аппарата особенно если центр тяжести аппарата расположен близко к основанию.
Способ установки подъемом с подтаскиванием нижней части аппарата к фундаменту в процессе подъема. При этом способе аппарат поднимают за верхний конец а нижний конец уложенный на салазки подтягивают в процессе подъема при помощи трактора или лебедки так чтобы грузовые полиспасты все время располагались вертикально. Этот способ применяется при монтаже полностью собранных аппаратов.
Способ установки подъемом в горизонтальном или наклонном положении с последующим поворотом аппарата. При этом способе строповка аппарата производится за цапфы или ложные штуцера расположенные чуть выше центра тяжести аппарата. При подъеме аппарат удерживают в горизонтальном положении при помощи оттяжки и вспомогательной лебедки. После подъема аппарата на необходимую высоту оттяжки ослабляется аппарат занимает вертикальное положение и опускается на фундамент в проектное положение. Область применения этого способа монтажа оборудования та же что и предыдущего способа.
Способ установки подъемом с последующим переводом аппарата к месту установки путем поворота или изменения вылета стрелы крана перемещением крана либо наклоном мачты или портала. Этот метод является основным при использовании стреловых кранов и часто применяется при использовании мачт и порталов. Хотя установка качающихся мачт и порталов более сложна и трудоемка чем неподвижных но при этом отпадает необходимость затаскивания аппарата на фундамент и производить подготовительные работы можно в стороне от фундамента на ровном месте что полностью оправдывает дополнительные работы по установке качающихся мачт и порталов. Этот способ применим как для горизонтальных так и для вертикальных аппаратов.
Способ установки натаскиванием на фундамент тракторами или лебедками
по наклонным плоскостям. Применяется при монтаже горизонтальных аппаратов монтируемых на невысоких фундаментах и является основным способом при монтаже цилиндрических горизонтальных аппаратов и вспомогательным при подготовке к установке на фундамент вертикальных цилиндрических; аппаратов.
Способ установки оборудования с подъемом при помощи домкратов на шпальные клетки с последующей надвижкой на фундамент. Этот способ применяется при монтаже горизонтальных аппаратов и механизмов на невысокие фундаменты в случае отсутствия иных возможностей.
Этим перечислением не исчерпываются все возможные способы монтажа и установки оборудования на фундамент. С совершенствованием техники появляются принципиально новые методы монтажа как например способ монтажа с применением вертолетов.
Для бражной колонны применим метод монтажа укрупненными блоками и способ наращивания с помощью мостового крана расположенного в цехе. В цех царги подаются автотранспортом собираются на месте в укрупненные блоки а дальнейшая сборка идет на высоте.
Регулирование вертикальности оси колонны состоящей из отдельных царг на прокладках в некоторых пределах можно производить подтяжкой болтов на выпученной стороне в пределах упругости прокладок.
При горизонтальном положении аппарата тарелки устанавливают строго вертикально; их положение проверяют по отвесу. Значительно легче обеспечить строгое горизонтальное положение тарелок в уже установленном выверенном и закрепленном на фундаменте корпусе аппарата; в этом случае до-статочной точности добиваются либо с помощью уровня либо заливая на поверхность тарелки воду.
Порядок монтажа тарелок снизу вверх; такой порядок обеспечивает больший простор работающим внутри колонны рабочим позволяет сократить число временных подмостей и производить проверку тарелок на барботаж при последовательном креплении люков также снизу вверх.
Технология регулирования барботажа тарелок заключается в следующем.
Тарелку заливают водой так чтобы избыточное количество воды сливалось через сливные устройства. Слив по всему периметру должен быть одинаковым поэтому предусматривается возможность его регулирования.
Колпачки обычно регулируют по высоте так чтобы верхний край их прорезей был погружен в жидкость на глубину 20-50 мм в зависимости от режима работы.
Колонны испытываются гидравлическим или пневматическим способом. Вели-чина испытательного давления при гидравлическом способе принимается равной 15 рабочего но не ниже 2 ат для колонн работающих при давлении до 5 ат. Для колонн работающих при давлении более 5 ат испытательное давление должно превышать рабочее на 25% но не менее чем на 3 ат. Колонны работающие под вакуумом испытываются избыточным давлением 2 ат. Колонны работающие при температурах свыше 400°С испытываются давлением равным 15 рабочего.
После монтажа и гидравлического или пневматического испытания про-водится подготовка установки к пуску. Помещение цеха тщательно убирают из цеха удаляют посторонние предметы и все оборудование для гидравлического и пневматического испытания кроме инструментов; проводят маркировку запорной арматуры на коллекторе пара и воды пробных холодильников контрольно-измерительных приборов фонарей. Контрольно-измерительные приборы (в том числе и контрольные снаряды для спирта) проверяют и тарируют.
Все оборудование тщательно промывают остатки воды выпускают через дренажные устройства (спускные краны).
Проверяют правильность установки сливных стаканов в бражных колоннах с одноколпачковыми тарелками плотность закрытия всех люков и лазов на колоннах и вспомогательном оборудовании уплотнения крышек дефлегматоров конденсаторов и другого теплообменного оборудования. Проверяют исправность и легкость открытия запорной арматуры. Еще раз проверяют соответствие трубопроводов монтажной схеме; обращают внимание на то чтобы не было местных понижений трубопроводов
образующих «мешки» па горизонтальных участках.
Вначале установку пускают на воде и паре (пароводяное испытание).
После проверки работы колонн на паре и моде и устранения замеченных недостатков переходят на обогрев колонн через испарители при их наличии.
Работа установки в процессе испытании на парс и воде должна длиться (>8 ч при условии полного устранении всех дефектов). В ходе испытаний выявляют и устраняют все дефекты монтажа а внутреннюю поверхность всех элементом установки и коммуникаций пропаривают и промывают.
Работа установки на воде и паре считается нормальной если нет течи установка работает спокойно давление в колоннах удерживается устойчиво жидкость во все фонари и пробные холодильники поступает плавно и легко поддается регулировке уровень жидкости в кубовой части колонн поддерживается постоянным.
После испытания установки на паре и воде не останавливая ее работы переключают насос на подачу бражки из расчета половинной нагрузки установки подключают контрольные снаряды для учета спирта. В конденсаторы колонн увеличивают подачу воды чтобы они были полностью охлажденными.
При условии нормальной работы всех элементов установки постепенно увеличивают подачу бражки в бражную колонну систематически следя за содержанием спирта в барде и лютерной воде за температурой в кубах колонн за загрузкой спиртовой колонны по термометру на тарелке питания и за температурой конденсаторов. По мере увеличения подачи бражки при необходимости увеличивается подача пара в колонны и отбор ректификованного спирта (по мере загрузки спиртовой колонны). С увеличением подачи пара пропорционально увеличивается и подача воды на дефлегматоры колонны (в начале пуска рекомендуется все конденсаторы держать переохлажденными вплоть до окончательной отработки режима работы всех колонн). Включение в работу дополнительных колонн производится после выведения на оптимальный режим работы основных колонн.
Во время работы ректификационной установки необходимо следить за выходом барды и лютерной воды из колонн подачей бражки воды и пара за давлением и температурным режимом в колоннах за концентрацией и количеством отбираемого спирта за показателями контрольно-измерительных приборов. Работу ректификационной установки необходимо вести строго придерживаясь утвержденного технологического регламента. При регулировании работы установки нельзя допускать перерывов в подаче пара и воды снижения концентрации ректификованного спирта ниже допустимой стандартом.
Ректификационная установка может работать без остановки продолжительное время. Остановка ректификационной установки может быть плановой (профилактическая) или аварийной причем плановая остановка может быть кратковременной (без стяжки спирта из колонн) или длительной (с полной стяжкой спирта из колонн).
Аварийная остановка как правило бывает внезапной из-за непредвиденной причины (отсутствие пара воды электроэнергии и т. д.). При аварийной остановке всей установки из-за отсутствия пара прекращают подачу бражки в бражную колонну закрывают задвижки для отвода барды и лютерной воды из колонн кран на трубопроводе подачи эпюрата в спиртовую колонну (в том числе и краны на уравнительных трубах) краны отбора пастеризованного спирта из спиртовой колонны краны для отбора сивушного спирта и сивушной фракции кран отбора спирта из холодильника на фонарь ректификованного спирта (при наличии колонны окончательной очистки). Прекращается подача воды в эпюрационную колонну (в случае применения гидроселекции) ц в экстрактор сивушного масла. Спустя 15 мин после снижения избыточного давления в нижней части колонны до нуля прекращают подачу воды в конденсаторы дефлегматоры ловушки и холодильники.
Для облегчения пуска колонн желательно кубовую жидкость перед пуском выпускать из спиртовой и сивушной колонн в сборник лютерной воды туда же желательно сбросить жидкость и из эпюрационной колонны (но не через
спиртовую колонну); из бражкой колонны жидкость выкачивается в сборник бражки. Спускают жидкость до установления нормального рабочего уровня жидкости по водомерному стеклу.
При кратковременной остановке из-за отсутствия бражки или остановки бражной колонны эпюрационную и спиртовую колонны оставляют под паром. При этом слегка стягивают спирт из спиртовой колонны затем прекращают отбор непастеризованного спирта. Охлаждают конденсаторы колонн с таким расчетом чтобы не было погона в их фонарях снижают подачу пара в колонны (температура в нижней части эпюрационной спиртовой сивушной колонн и колонны разгонки ГФ должна быть не ниже чем при нормальном режиме работы) прекращают отбор сивушного спирта и сивушного масла закрывают подачу воды на гидроселекцию и экстрактор сивушного масла.
При возобновлении подачи; бражки предварительно прогревают бражную колонну и по мере насыщения эпюрационной и спиртовой колонн спиртом восстанавливается нормальный режим работы установки. Ректификационная часть установки может находиться под паром до 4—6 ч.
При остановке на длительное время или для проведения ремонтных работ связанных со сваркой проводят полную стяжку спирта из всех колонн и всего вспомогательного оборудования. Предварительно прекращают подачу бражки на бражной насос. Вместо бражки на насос подают воду которой вытесняется бражка из всех коммуникаций и подогревателей бражки. С повышением температуры на тарелке питания бражной колонны до 100°С через 10 мин прекращают подачу пара и воды в бражную колонну.
Накипь с поверхности теплопередачи в дефлегматорах может быть удалена механическим или химическим способом. При механической очистке пользуются шарошками а затем металлическими щетками — ершами. Химическую очистку проводят сначала щелочным раствором (смесь карбоната натрия и гидроксида натрия) а затем после 5—10-минутной промывки водой— раствором соляной кислоты.
На некоторых заводах удаляют накипь путем прокачивания через теплообменник в течение 15—2 ч лютерной воды.
Для предотвращения или уменьшения накипеобразования в теплообменной аппаратуре на заводах пользуются различными приемами.
На ряде заводов практикуют подачу диоксида углерода (непрерывно из бродильной батареи) в ток воды перед дефлегматором или непосредственно в коллектор воды с целью уменьшения накипеобразования.
На некоторых заводах воду идущую на дефлегматоры предварительно умягчают на химводоочистке а затем используют дефлегматорную воду для питания паровых котлов. При получении пара со стороны или питания котлов конденсатом водяного пара иногда применяют замкнутую систему дефлегматор — градирня — дефлегматор с подпиткой системы умягченной водой от химводоочистки. тся межтрубное пространство. Для очистки рекомендуется промывка межтрубного пространства раствором синтетических моющих средств в течение часа методом круговой циркуляции.
Для предотвращения накипи в испарителях (кипятильниках) целесообразно организовать их работу по режиму выпарной установки питая их лютерной водой.
2. Ремонт проектируемого аппарата.
Техническое обслуживание. Осмотр состояния всех соединений корпуса арматуры люков тарелок контрольно-измерительных приборов; очистка внутренних поверхностей тарелок барботёра куба; проверка состояния и при необходимости замена изношенных деталей уплотнений; сборка проверка герметичности.
Ремонт текущий первый. Выполняются все работы ТО и кроме того производятся промывка внутренних поверхностей; ремонт или замена изношенных арматуры тарелок стоек тарелок стаканов царг фланцевых соединений; замена изношенных прокладок крепежных изделий; ремонт теплоизоляции; сборка испытание покраска.
Ремонт текущий второй. Выполняются все работы Т и кроме того
производятся разборка и демонтаж всей колонны; проверка толщины стенок методом неразрушающей дефектоскопии; полная замена теплоизоляции. Дефлегматоры конденсаторы холодильники
Техническое обслуживание. Очистка и промывка внутренних поверхностей аппарата и трубных пучков от накипи и грязи; проверка состояния всех соединений корпуса арматуры; подтяжка креплений; набивка сальников; осмотр крепления корпуса на опорах.
Характер износа. Большинство колонных аппаратов работает при высокой температуре под давлением или в вакууме и содержит огне- и взрывоопасные среды. Корпуса колонных аппаратов и их внутренние устройства могут изнашиваться в результате коррозионного эрозионного и термического воздействия среды. Скорость износа зависит от многих факторов и в первую очередь — от физико-химических свойств среды условий ведения процесса конструктивного исполнения и качества металла корпуса применения соответствующих ингибиторов коррозии.
Стоимость колонн обычно очень высока демонтаж и монтаж их — кропотливый трудоемкий и продолжительный процесс. Смена колонных аппаратов производится в подавляющем большинстве случаев вследствие износа корпусов. Поэтому при эксплуатации необходимо принять надежные меры для предохранения корпусов от преждевременного износа. Коррозионная стойкость корпусов ректификационных колонн должна быть не выше семи баллов при оценке по десятибалльной шкале а в случае колонн больших диаметра и высоты — не выше пяти баллов т. е. скорость коррозии не должна превышать 01 ммгод.
Колонные аппараты подвержены коррозии различных видов. Она охватывает всю поверхность корпуса или отдельные ее участки. Так в ректификационных колоннах нефтеперерабатывающих заводов химической коррозии подвергаются в основном участки работающие в условиях повышенных температур. Агрессивными составляющими сред в колоннах являются сернистые соединения и продукты их разложения содержащиеся в
нефтях нафтеновые кислоты а также соли буровых вод не отстоявшихся в дегидраторах.
Электрохимической коррозии подвержены участки ректификационных колонн на которых возможны образование гальванических пар и возникновение коррозионного электрического тока. Такая коррозия в частности наблюдается в верхней части ректификационных колонн атмосферных установок для переработки нефти где вместе с парами углеводородов интенсивно конденсируются водяные пары. Вода гидролизует содержащиеся в сырье и дистиллятах хлориды магния и кальция; получающийся в результате хлористый водород образует в водной среде электролит — соляную кислоту.
Эрозионный износ корпусов колонн является следствием воздействия сильных струй жидкости и паровых потоков содержащих абразивные включения. Участки корпусов подверженные эрозии защищают протекторами и специальными устройствами уменьшающими кинетическую энергию струй жидкости и пара (улиты маточники и т. д.).
Износ колонных аппаратов опасен не только из-за нарушения их прочности; образовавшиеся продукты коррозии могут закупорить или загрязнить трубопроводы небольшого сечения теплообменники и конденсаторы.
Подготовка колонных аппаратов к ремонту. Колонные аппараты ремонтируют при планово-предупредительных ремонтах технологической установки. Порядок подготовки аппарата к ремонту и проведения ремонтных работ зависит от особенностей установки.
В большинстве случаев колонные аппараты готовят к ремонту следующим образом. Доводят давление в колонне до атмосферного из аппарата удаляют рабочую среду после чего его пропаривают водяным паром который вытесняет оставшиеся в колонне пары и газы. После пропарки колонну промывают водой. В некоторых случаях пропарку и промывку чередуют несколько раз. Время операций оговаривается в производственной инструкции (технологическом регламенте) каждой
технологической установки или технологического блока.
Промывка колонн водой способствует также более быстрому их остыванию. Нельзя приступать к ремонтным работам если температура промывной воды превышает 50 °С.
Пропаренную и промытую колонну отсоединяют от всех аппаратов и коммуникаций глухими заглушками устанавливаемыми во фланцевых соединениях штуцеров. Установку каждой заглушки и последующее ее снятие регистрируют в специальном журнале.
Технология ремонта. Ремонт аппарата начинают с его вскрытия которое необходимо производить строго соблюдая следующие правила. Вначале открывают верхний люк причем перед этим в аппарат в течение некоторого времени подают водяной пар чтобы избежать возможного подсоса воздуха в результате которого может образоваться взрывоопасная смесь. Далее последовательно (сверху вниз) открывают остальные люки. Категорически запрещается одновременно открывать верхний и нижний люки. Нельзя также открывать сначала нижний а затем верхний люк так как вследствие разности температур происходит сильный приток воздуха в колонну что может привести к образованию взрывоопасной смеси. С целью сокращения продолжительности ремонтных работ еще при промывке колонны водой отворачивают частьтичности.
После открывания люков колонна некоторое время проветривается в результате естественной конвекции воздуха. Возможность ремонтных работ в болтов на тех люках которые будут вскрываться не нарушая при этом герме колонне устанавливают исходя из результатов лабораторного анализа пробы воздуха взятого из нее. Доступ людей в колонну возможен если концентрация углеводородов в пробе не превышает 300 мгм3 а содержание сероводорода—10 мгм3. Предельно допустимые концентрации других веществ указываются в технологической карте (технологическом регламенте) каждой установки блока или отделения. При работе внутри колонны необходимо тщательно соблюдать правила техники безопасности. Рабочий должен надевать предохранительный пояс с веревкой конец которой выводится
наружу и надежно закрепляется; за работой находящегося внутри колонны рабочего постоянно наблюдает специально выделенный для этой цели рабочий. Продолжительность непрерывной работы в колонне должна быть не более 15 мин. После этого необходим такой же по продолжительности отдых вне колонны (обычно рабочий и наблюдатель меняются местами). При первых же признаках появления внутри ремонтируемого аппарата взрывоопасных горючих или токсичных жидкостей паров и газов всякую работу следует немедленно прекратить. подготовке колонны предъявляют особенно высокие требования в том случае если в ней должны производиться огневые (сварочные) работы. Участок колонны на котором производится сварка отделяется металлическими или пропитанными водой деревянными настилами накрытыми кошмой. Для освещения внутри колонны применяют лампы напряжением не более 12 В. Переносное освещение должно быть взрывобезопасным. Корпус колонны а также ее внутренние устройства подвергают тщательному осмотру. При необходимости осмотра всей поверхности корпуса разбирают внутренние устройства или их часть. Например в ректификационных колоннах для доступа к тарелкам на уровне которых люки отсутствуют разбирают проходы на тарелках лежащих выше. Выявление дефектов корпуса требующее высокой квалификации включает визуальный осмотр для определения общего состояния корпуса и участков подверженных наибольшему износу; измерение остаточной толщины корпуса с помощью ультразвуковых дефектоскопов путем микрометрирования и контрольного просверливания отверстий; проверку на плотность сварных швов и разъемных соединений и т. д.
По характеру обнаруженного дефекта устанавливают содержание и способ ремонта корпуса. Неплотные сварные швы вырубают зачищают и заваривают соответствующим электродом. Весьма важно правильное перекрывание нового и старого швов.
Изношенные штуцера и люки вырезают и заменяют новыми с обязательной установкой укрепляющих колец. Желательно чтобы укрепляющие кольца новых штуцеров имели несколько больший диаметр чем
старые: это позволяет приваривать их в новом месте. Ремонту подвергают все штуцера сигнальные отверстия на укрепляющих кольцах которых во время эксплуатации были заглушены пробками.
При каждом ремонте измеряют фактическую толщину стенки корпуса эксплуатируемого колонного аппарата. Наиболее изношенные участки корпуса колонны вырезают а на их место ставят новый участок заранее свальцованный по радиусу колонны. Сварку производят встык. Вырезание больших участков корпуса может привести к ослаблению сечения и нарушению устойчивости. Поэтому до вырезания дефектного участка его укрепляют стойками проставляемыми внутри или снаружи (рисунок 4.1). Число и сечение стоек и размеры опорных лап рассчитывают исходя из условия равенства их сопротивлений сопротивлению вырезанного сечения.
Промежуточные обечайки легко заменяют следующим образом. Устанавливают подъемные мачты удерживающие верхнюю неповрежденную часть колонны отделяют эту часть от поврежденного участка газорезкой и опускают на землю. Поврежденную часть колонны стропят и с помощью тех же мачт опускают на землю. Заранее подготовленную новую часть колонны поднимают и стыкуют с нижней частью колонны затем поднимают верхнюю ее часть.
Рис. 4.1 . Усиление колонны в местах вырезаемых поясов:
а — внутренними стойками; б — наружными стойками; в — схема крепления стойки; 1 — лапа; 2 — стойка.
Очень часто учитывая трудоемкость таких замен участков корпуса признают целесообразной полную замену изношенной колонны. Демонтаж изношенной колонны производят в порядке обратном монтажу. После соответствующих проверок демонтируемая колонна может быть использована для установки монтажных мачт точно так же как новая колонна — для демонтажа.
Ремонт внутренних устройств.
При ремонте внутренние устройства колонн очищают от грязи кокса и других отложений. Твердую и тестообразную массу выгребают лопаточками или скребками-чистилками кокс удаляют с помощью пневматических отбойных молотков. Удаление отложений всегда сопровождается повышением концентрации вредных газов в колонне; в этот период внутри колонны рекомендуется работать в шланговых противогазах.
Ремонт внутренних устройств связан с многократным подъемом новых и спуском изношенных деталей; такие операции желательно механизировать. К верхней части корпуса колонны крепят поворотный или неподвижный кран-укосину (рисунок 4.2). Кран можно прикрепить также к стойкам центральных пилонов лестничных клетей. Электролебедку с электродвигателем во взрывобезопасном исполнении или пневмолебедку к крану-укосине устанавливают у основания колонны или на площадке которую обслуживает кран-укосина.
Определение износа и отбраковка внутренних устройств производятся согласно действующим методикам и нормам. Изношенные детали а иногда и целые узлы заменяют новыми.
Довольно трудоемкими являются операции связанные с разборкой закоксованных тарелок и отбойников. Сначала их освобождают от кокса механической чисткой (скребками) затем с помощью цепных талей подвешиваемых внутри колонны за надежные конструкции (например опорные балки) отдирают каждый элемент от места посадки. Для этой операции нельзя применять трос с лебедкой: за счет силы упругости троса
вырванный элемент сильно отскакивает и может повредить колонну или причинить травму находящимся в колонне рабочим.
Рис. 4.2 - Кран-укосина на корпусе аппарата:
— стойка; 2— кронштейн; 3 — блок; 4—ролик.
В данной работе был осуществлен расчет бражной колонны в данной работе четко просматривается зависимость геометрических размеров бражной колонны от количества-дистиллята продукта и абсолютной температуры пара.
Кретов И.Т. Антипов С.Т. Шахов С.В.
Инженерные расчеты технологического оборудования предприятий бродильной промышленности.-М.:КолосС 2004. – 391 с.
Справочник по производству спирта. Под ред. Яровенко В.А. Усмиш-никова Б.А. и др.: М. Легкая промышленность 1981.
Лащинский А.А. Толчинский А.Р. Основы конструирования и расчета хи-мической аппаратуры. Л. 1976.
Лащинский А.А. Конструирование сварных химических аппаратов. Л. «Машиностроение» 1981.
Павлов К.Ф. Романков П.Г. Носков П.А. Примеры и задачи по курсу про-цессов и аппаратов химической технологии. К. «Химия» 1987.
Машины и аппараты химических производств. Примеры и задачи. Под общ. ред. Соколова Л.Н. 1982.
Попов В.И. Кретов И.Т. Стабников В.Н.
Технологическое оборудование предприятий бродильной промышленности. – М.:
Легкая и пищевая промышленность 1983. – 464 с.
Цыганков П.С. Ректификационные установки спиртовой промышленности. М.: «Лёгкая и пищевая пром-сть» 1984. – 336
Технический регламент на производство спирта ректификованного из пищевых видов сырья (крахмалосодержащего и сахаросодержащего): К. ВНИИ ПД 1987.
Врагов А.П. Михайловский Я.Э. Оптимизационное проектирование рек-тификационных колонн с использованием ПЭВМ: Учебное пособие. – Сумы: Изд-во СумГУ 2000. – 65 с.
Ковалевский К.А. Технология бродильных производств. – Киев: Фирма
«ИНКОС» 2004. – 340 с.
Спецификация (колонна) лист 1.CDW

Рекомендуемые чертежи
- 24.01.2023
- 17.05.2020
- 24.01.2023
- 24.01.2023