Анализ и синтез кривошипно-ползунного, зубчатого и кулачкового механизмов




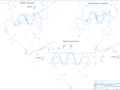

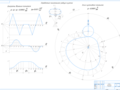
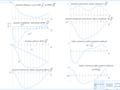
- Добавлен: 24.01.2023
- Размер: 321 KB
- Закачек: 1
Описание
Состав проекта
![]() |
![]() |
![]() ![]() ![]() ![]() |
![]() ![]() ![]() ![]() |
![]() ![]() ![]() ![]() |
![]() ![]() ![]() |
![]() ![]() ![]() ![]() |
![]() ![]() ![]() ![]() |
Дополнительная информация
Лист 2.cdw

Лист 1.cdw

Лист 5.cdw

Лист 3.cdw

Лист 4.cdw

Рекомендуемые чертежи
- 24.01.2023
- 21.05.2023
- 24.01.2023