Режущий инструмент (резец, фреза, протяжка)



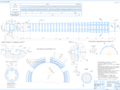
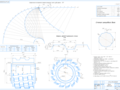
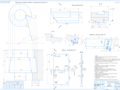
- Добавлен: 04.11.2022
- Размер: 6 MB
- Закачек: 0
Узнать, как скачать этот материал
Подписаться на ежедневные обновления каталога:
Описание
Курсовой проект - Режущий инструмент (резец, фреза, протяжка)
Состав проекта
![]() |
![]() ![]() ![]() |
![]() ![]() ![]() ![]() |
![]() ![]() ![]() |
![]() |
![]() ![]() ![]() ![]() |
![]() ![]() ![]() ![]() |
![]() |
![]() |
![]() |
![]() ![]() ![]() |
Дополнительная информация
Контент чертежей
резец.cdw

протяжка.cdw

фреза.cdw

Рекомендуемые чертежи
- 24.01.2023
Свободное скачивание на сегодня
Обновление через: 10 часов 56 минут