Резец призматический, фреза червячная модульная, протяжка профильной схемы резания




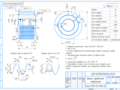
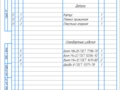
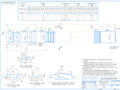
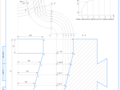
- Добавлен: 24.01.2023
- Размер: 599 KB
- Закачек: 0
Описание
Состав проекта
![]() |
![]() |
![]() ![]() ![]() ![]() |
![]() ![]() ![]() ![]() |
![]() ![]() ![]() ![]() |
![]() ![]() ![]() ![]() |
![]() ![]() ![]() ![]() |
![]() ![]() ![]() |
![]() ![]() ![]() ![]() |
![]() ![]() ![]() |
Дополнительная информация
второй лист.cdw

Спецификация нов..spw

державка.cdw

первый лист.cdw

Протяжка.cdw

Фреза.cdw

Рекомендуемые чертежи
- 17.03.2024
Свободное скачивание на сегодня
- 22.08.2014
- 29.08.2014