Разработка насоса для гидропривода автомобильного крана г. Челябинск




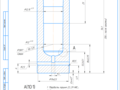
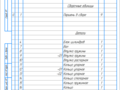
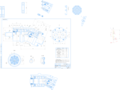
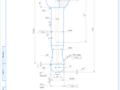
- Добавлен: 04.11.2022
- Размер: 1 MB
- Закачек: 1
Описание
Состав проекта
![]() |
![]() |
![]() ![]() ![]() |
![]() ![]() ![]() ![]() |
![]() ![]() ![]() |
![]() ![]() ![]() ![]() |
![]() ![]() ![]() ![]() |
![]() ![]() ![]() |
Дополнительная информация
Поршень в сборе.cdw

Твердость азотированного слоя сферы Б и поверхности А поршня
* Размер обеспечить инструментом.
Максимальный осевой зазор между шатуном и поршнем 0
Спецификация.spw
Винт М10-6gx55 ГОСТ 11738-84
Кольцо 122-128-25-1-0 ГОСТ 9833-73
Кольцо 125-130-25-2-0 ГОСТ 9833-73
Манжета 1.1-50x76-15 ГОСТ 8752-79
Подшипник 312 ГОСТ 8338-75
Подшипник 246312 ГОСТ 832-78
Шайба 10Л ГОСТ 6402-70
Шайба C 10.37 ГОСТ 10450-78
x6Хим. Фос. прм. ГОСТ 3129-70
Штифт 5x18Хим. Окс. прм. ГОСТ 3129-70
Поршень.cdw

Твердость поршня 22 29 HRC
Отклонение от соосности
Перед закаткой обезжирить и очистить отверстия.
* Раземр замерять до снятия факси.
Аксиально-поршневой.cdw

Номинальная частота вращения
Насос аксиально-поршневой
* Размеры для справок.
Перед сборкой очистить все внутренние поверхности от пыли
инородних предметов.
Все уплотняющие прокладки
поступающие на сборку должны быть
Входной вал должен вращаться от руки без усилия.
Курсовой.docx
Государственное образовательное учреждение высшего профессионального образования
Южно-Уральский государственный университет
Факультет «Аэрокосмический»
Кафедра «Гидравлика и гидропневмосистемы»
«Объемные гидромашины и ГП»
РАСЧЕТНО-ПОЯСНИТЕЛЬНАЯ ЗАПИСКА
к курсовому проекту на тему
«Разработка насоса для гидропривода автомобильного крана»
Студент Двойнова К.А. Группа АК-411
Руководитель проекта Барышев В.И.
1. Автомобильная техника5
2.1. История завода6
2.2. Деятельность завода8
3.1. Технические характеристики9
3.2. Гидравлическая система16
4. Аксиально-поршневые гидромашины24
4.1. Насос типа 31026
РАСЧЕТ ГИДРОНАСОСА28
1. Расчет блока цилиндров28
1.1. Расчет диаметра поршней29
1.2. Определение основных размеров блока цилиндров31
1.3. Проверка блока цилиндров на прочность34
2. Расчет геометрии торцевого распределителя36
2.1. Расчет сил действующих в распределительном узле39
3. Расчет и конструирование поршневых групп41
3.1. Проверка прочности поверхностей поршней в месте их контакта со сферическими головками шатунов42
3.2. Выбор зазоров в сопряжениях распределительного узла и блок – плунжер45
1. Расчет объемных потерь49
2. Расчет гидромеханических потерь51
3. Расчет коэффициентов полезного действия54
4. Расчет диаметра вала мотора подбор подшипников и шпоночного соединения55
4.1. Расчет крутящего момента и мощности мотора56
Уровень развития передовых стран определяется исключительно уровнем развития машиностроения.
Существует два пути развития отечественного машиностроения. Первый – создание традиционных машин с высокой конкурентоспособностью. Второй путь – создание нетрадиционных машин строительных и дорожных. В отечественном машиностроении опыт разработок уже имеется.
В моей курсовой работе я хотела бы рассмотреть гидрооборудование автомобильного крана КС-55732.
Кран автомобильный КС-55732 грузоподъемностью 25 т предназначен для выполнения погрузочно-разгрузочных строительно-монтажных работ в промышленности строительстве сельском хозяйстве и других отраслях народного хозяйства (выполнение рабочих операций с обычными грузами). Этим и обуславливаются основные параметры гидрооборудования необходимые для работоспособности автокрана.
В данной курсовой работе я разработаю аксиально-поршневой насос для гидропривода автомобильного крана КС-55732 с рабочим объемом 112 см3 при частоте вращения 1200 обмин.
1. Автомобильная техника
Автомобильный кран—кран стрелового типа который может быть снабжён башенно-стреловым оборудованием и может перемещаться с грузом или без груза не требуя специальных путей и устойчивость которого обеспечивается за счет силы тяжести.
Автомобильные краны— наиболее распространённые из всей группы стреловых самоходныхкранов.
Автомобильные краны собираются на шасси серийно выпускаемых грузовых автомобилей с установкой на раме передних и задних выносных опор для обеспечения устойчивости при работе крана с грузом и повышения грузоподъёмности. Они могут самостоятельно передвигаться по грунтовым дорогам и преодолевать подъёмы до 20°.
Основным достоинством автомобильных кранов является их высокая мобильность что даёт возможность оперативно перемещать их на удалённые друг от друга объекты.
Автомобильные краны различают:
Краны с одномоторным приводом где все механизмы приводятся в действие от основногодвигателя внутреннего сгорания— двигателя шасси.
Краны с многомоторным приводом в котором каждый механизм приводится в действие своим индивидуальнымдвигателем.
В автомобильных кранах применяются следующие типы привода:
Механический привод. Включает силовую установку базового шасси коробку отбора мощности коробку скоростей распределительную коробку силовые канатные барабаны.
Электрический. Состоит из силовой установки базового шасси коробки отбора мощности генератора питающего электрическим током электродвигатели механизмов крана.
Гидравлический. Также имеет силовую установку шасси соединённую с коробкой отбора мощности гидронасосами гидродвигателями и гидроцилиндрами.Гидравлический привод компактен и позволяет в широких пределах осуществлять бесступенчатое регулирование скоростей.
На сегодняшний день производством автокранов в Росии занимаются:
Производитель (марка)
Грузоподъемность мин.-макс. (втоннах)
Страна производитель
Среднетонник на свободном шасси
Челябинский механический завод является уникальным производителемгусеничныхспециальныхиавтомобильных кранов. Сегодня марка ЧЕЛЯБИНЕЦ на отечественном рынке грузоподъемной техники занимает лидирующие позиции в сегменте автомобильных кранов повышенной проходимости. Номенклатура автокранов постоянно расширяется и на сегодняшний день включает в себя более 35 серийных моделей грузоподъемностью 25 32 40 50 тонн на различных шасси. Краны специального назначенияЧЕЛЯБИНЕЦ производства Челябинского механического завода обладают большим набором опций и изготавливаются в соответствии с техническими требованиями заказчиков.
История Челябинского механического завода началась 27 января1942 года. Тогда в Челябинске в невероятно сложных условиях военного времени развернулся котельно-механический завод эвакуированный изХарькова. Место для него нашли на площадкеЧелябинской ТЭЦ-1. Первоначально завод был ориентирован на выпуск продукции для энергетиков производил котлы и другое нестандартное оборудование для тепловых электростанций. ПослеВеликой Отечественной войныпредприятие вошло в составМинистерства энергетики и электрификации СССР. В стране началось восстановление народного хозяйства поэтому Челябинский механический завод реконструировали и перевели на выпуск грузоподъемной техники. В 1946 году из ворот предприятия вышел первый автокранАК-3грузоподъемностью 3 тонны смонтированный на шассиЗИС-5. Всего за историю предприятия было выпущено 1500 таких машин. Тем временем на заводе был сформирован собственный конструкторский отдел создающий уникальные модели. С его помощью было освоено производство железнодорожных кранов сдизель-электрическим приводомДЖ-10 и ДЖ-15 крановПЖ-25с паровым приводом и гусеничных крановПК-3.
2.2. Деятельность завода
Производство грузоподъемной техники:
- Более 3500 автомобильных кранов ЧЕЛЯБИНЕЦ.
- Более 12000 гусеничных кранов ДЭК.
- Более 3000 специальных кранов ЧЕЛЯБИНЕЦ.
Кран автомобильный КС-55732 грузоподъемностью 25 т изготавливается на шасси грузовых автомобилей КАМАЗ-43118 КАМАЗ-65115 КАМАЗ-65111 КАМАЗ-53228 предназначен для выполнения погрузочно-разгрузочных строительно-монтажных работ в промышленности строительстве сельском хозяйстве и других отраслях народного хозяйства (выполнение рабочих операций с обычными грузами).
Кран рассчитан на эксплуатацию при температуре окружающего воздуха от минус 40 до
плюс 40 °C и относительной влажности 80 % при 20 °C и хранение при температуре окружающего воздуха не ниже минус 50 °C 1).
Транспортное передвижение крана между объектами работ предусмотрено по дорогам с твердым покрытием. В кабине водителя допускается перевозка не более одного пассажира.
Установка крана возможна на подготовленной площадке с размерами (70х70) м2 и уклоном не более 3°.
Допустимая скорость ветра для рабочего состояния 2) крана не должна превышать 14 мс на высоте 10 м для нерабочего состояния 3) – 27 мс.
3.1. Технические характеристики
Таблица 1 – Технические характеристики крана
Наименование показателей
Грузоподъемность максимальная* миди (на канатах) со стрелой 97 м на вылете 325 м т не менее
Максимальный грузовой момент т·м не менее
Высота подъема* максимальная м не менее
Глубина опускания максимальная при работе со стрелой 97 м с грузом равным 50 % максимальной грузоподъемности при кратности полиспаста 4 м
Грузоподъемность при телескопировании т не более:
- со стрелой от 97 до 157 м
- со стрелой от 157 до 217 м
Скорость подъема ммин не менее
- при максимальной грузоподъемности
Максимальная скорость подъема-опускания крюковой подвески без груза при кратности полиспаста – 6 ммин не менее
Скорость посадки ммин не более
Частота вращения обмин:
- наименьшая не более
- наибольшая не менее
Время полного изменения вылета с не менее
- от максимального до минимального
- от минимального до максимального
Транспортная скорость на горизонтальном участке дороги с твердым покрытием кмч
Преодолеваемый краном уклон % ( °) не более
Габаритные размеры крана с основной стрелой в транспортном положении мм не более
Нагрузка на оси шасси крана в транспортном положении кН (тс):
- без гуська: передняя ось
- с гуськом: передняя ось
Конструктивная масса крана т не более
Масса снаряженного крана т
Полная масса крана т
Контрольный расход топлива в транспортном режиме на 100 км пути при скорости 60 кмч л не более
Контрольный расход топлива в крановом режиме лч не более
Гарантийный срок службы мес.
Срок службы при 15-сменной работе в паспортном режиме лет
Таблица 2 – Механизмы крана
КамАЗ-43118; КАМАЗ-53228
КамАЗ-65115; КАМАЗ-65111
От коробки отбора мощности через раздаточную коробку
От коробки отбора мощности с приводом от коробки передач
Редуктор цилиндрический двухступенчатый с передаточным числом – 4867;
тормоз колодочный нормально-замкнутый автоматический
Механизм подъема стрелы
диаметр поршня – 200 мм ход штока – 2275 мм
Редуктор планетарный двухступенчатый с передаточным числом – 34;
тормоз встроенный дисковый; нормально-замкнутый
Механизм выдвижения-задвижения секций стрелы
диаметр поршня – 125 мм ход поршня – 6000 мм;
Гидроцилиндры для вывешивания крана:
диаметр поршня – 125 мм ход штока – 580 мм;
Гидроцилиндры для выдвижения балок:
диаметр поршня – 63 мм ход штока – 1880 мм
Опорно-поворотное устройство
Опора поворотная шариковая с зубьями наружного зацепления
Управление механизмами крана
Гидрораспределители с ручным управлением
Привод управления двигателем
Педаль в кабине крановщика
Закрытая одноместная со стеклоочистителями
Таблица 3 – Заправочные емкости
Гидросистема (полная емкость) л
Масляный бак (полная полезная емкость) л
Картер механизма поворота л
Кран состоит из несущих сварных металлоконструкций механических и гидравлических агрегатов (сборочных единиц) которые конструктивно объединены в три основные части:
- неповоротная часть крана;
- поворотная часть крана;
- стреловое оборудование.
В неповоротную часть крана входят: шасси нижняя рама с гидроопорами поворотная опора стойка поддержки стрелы облицовка привод насоса пневмооборудование и управление выносными опорами.
Поворотная часть крана крепится к поворотной опоре. Она состоит из: поворотной рамы лебедки механизма поворота кабины отопителя приводов управления крановыми операциями и управления двигателем кожуха.
Стреловое оборудование состоит из трехсекционной телескопической стрелы грузового каната крюковой подвески.
Телескопическая стрела с помощью оси крепится к поворотной раме. Грузовой канат закрепляется на барабане лебедки.
Гидрооборудование и электрооборудование расположены на неповоротной и поворотной частях крана и на стреловом оборудовании.
Кран оборудован предохранительными устройствами. Для контроля состояния крана и его узлов а также управления краном служат контрольно-измерительные приборы и органы управления.
Работа всех крановых механизмов осуществляется от двигателя шасси. Мощность отбираемая от двигателя через фланец дополнительного отбора мощности коробки перемены передач (КПП) и привод насоса посредством рабочей жидкости гидросистемы передается исполнительным механизмам и гидроцилиндрам крана через пускорегулирующую аппаратуру.
Возможны следующие операции:
- вывешивание крана на выносных опорах;
- подъем и опускание телескопической стрелы;
- вращение поворотной части крана;
- подъем и опускание груза лебедкой;
- телескопирование секций стрелы;
- снятие крана с выносных опор.
С помощью привода управления крановыми операциями привода управления двигателем шасси и пускорегулирующей аппаратуры гидрооборудования можно регулировать скорости механизмов выполняющих основные крановые операции.
Возможны следующие совмещения рабочих операций:
- подъем (опускание) груза с вращением поворотной части;
- подъем (опускание) груза с подъемом стрелы;
- вращение поворотной части с подъемом (опусканием) стрелы (не более максимального вылета согласно грузовым и высотным характеристикам);
- подъем (опускание) груза с телескопированием стрелы.
3.2. Гидравлическая система
Гидравлический привод механизмов крана выполнен по открытой однонасосной гидравлической схеме и предназначен для передачи энергии силовой установки шасси к гидродвигателям крановой установки.
Гидравлическая принципиальная схема приведена в приложении 1 а перечень входящих в нее элементов в таблице 5.
Таблица 5 – Перечень элементов гидрооборудования
Обозначение по схеме
Гидрошарнир в сборе КС-65711.87.21.000
Бак масляный КС-45721Д.95.20.000
Блок ОПК в сборе КС-65711.86.21.010
Ду=20 мм; Рном=10 МПа
Вентиль в сборе КС-65711.86.12.000
Кран шаровый ФБ39.030.050.700
Ду=50 мм; Рном=16 МПа
Датчик давления ТКН40-Р112 (в составе ОГМ)
Дроссель ЯН.18.01.001-01
Дроссель ЯН.18.01.001-02
Гидрозамок гидроопоры в сборе
Ду=10 мм; Рном=20 МПа
Клапан «ИЛИ» КС-65711.86.21.020 в составе блока ОПК КС-65711.86.21.010
Клапан обратный в сборе КС-45721В.87.15.000
Клапан предохранительный 510.20.03А в составе КС-45731Г.86.60.000
Клапан обратно-предохранительный ОПК-20 в составе блока ОПК КС-65711.86.21.010
Клапан предохранительный в составе гидрораспределителя HC-D164
Клапан предохранительный в составе блока гидроклапанов 64011
Клапан предохранительный в составе клапана тормозного ГТК 1.16.00
Клапан предохранительный в составе гидрораспределителя HC-D45
Клапан предохранительный управляемый
Клапан тормозной ГКТ 1.16.01
Клапан тормозной ГКТ 1.16.00
Гидромотор 310.4.112.00.06
Гидромотор 303.4.112.503.000.0
Манометр МТП-4М-16МПа-4
Насос ручной КС-45721.31.500.01.000
Расширенный комплект ЗИП
Насос 310.4.112.03.06
Насос 313.4.112.500.4
Гидрораспределитель 1РЕ6.573Е.Г24.И.Н.М в составе КПУ КС-45721Г.86.60.000
Ду=6 мм; Рном=32 МПа;
Гидрораспределитель HC-D164 IL013(250)-C G05 W015B-H004-F0360-RS G05 (W001В-H004-F0370-RP G05)x03 TK-A G06
Ду=16 мм; Рном=35 МПа
Кран трехходовый D3 34G C.A.N
Ду=16 мм; Рном=25 МПа
Гидрораспределитель HC-D45 IL001(150)-А G04 (W001A-H002-F001A-RP G04)x05 TK-A G06
Ду=12 мм; Рном=35 МПа
Блок гидроклапанов 64011
Элемент фильтрующий ПЗМИ-ГС-661 («Реготмас» 661-1-05) в составе фильтра масляного бака КС-45721Д.95.20.000
Фильтр вентиляционно-заливочный ТМ 178 G150
Тормоз гидравлический в составе механизма поворота
Тормоз гидравлический в составе лебедки
Гидроцилиндр 100.125.6000А
Гидроцилиндр 160.200.2275
Гидроцилиндр 100.125.580
Гидроцилиндр 45.63.1880
При нейтральном положении золотников гидрораспределителя Р3 полости гидроцилиндров Ц5–Ц8 заперты золотником I гидрораспределителя Р3 полости гидроцилиндров Ц3 Ц4 Ц9 Ц10 заперты гидрозамками ЗМ1 ЗМ2 ЗМ3 ЗМ4. Напорная гидролиния через переливной канал гидрораспределителя Р3 соединена со сливом. Рабочая жидкость от насоса Н2 направляется в масляный бак Б.
Для приведения крана в рабочее положение необходимо выдвинуть балки выносных опор. Для выдвижения выносных опор крана из транспортного положения в рабочее необходимо золотник I гидрораспределителя Р3 установить в крайнее правое по схеме положение 1).
Рабочая жидкость от насоса Н2 через гидрораспределитель Р3 поступает в поршневые полости гидроцилиндров Ц5–Ц8 штоки гидроцилиндров выдвигаются и приводят выносные опоры крана в рабочее положение. Из штоковых полостей гидроцилиндров Ц5–Ц8 рабочая жидкость поступает на слив в масляный бак Б.
Возврат выносных опор крана из рабочего положения в транспортное производится тем же золотником гидрораспределителя Р3 для чего золотник необходимо установить в крайнее левое положение. При этом рабочая жидкость поступает в штоковые полости гидроцилиндров Ц5–Ц8 рабочая жидкость из поршневых полостей гидроцилиндров поступает на слив в масляный бак Б.
Для установки крана на опоры необходимо установить золотники I II IV V гидрораспределителя Р3 в крайнее правое положение. При этом рабочая жидкость от насоса Н2 через гидрораспределитель Р3 и гидрозамки ЗМ1 ЗМ2 ЗМ3 ЗМ4 поступает в поршневые полости гидроцилиндров (гидроопор) Ц3 Ц4 Ц9 Ц10; штоки гидроцилиндров выдвигаются кран устанавливается на гидроопоры; рабочая жидкость из штоковых полостей поступает на слив в масляный бак Б.
После выдвижения штоков гидроцилиндров (гидроопор) Ц3 Ц4 Ц9 Ц10 гидрозамки ЗМ1 ЗМ2 ЗМ3 ЗМ4 автоматически запирают рабочую жидкость в поршневых полостях предотвращая самопроизвольное втягивание штоков в случае обрыва трубопроводов либо утечек через гидрораспределитель Р3.
Для приведения гидроопор в транспортное положение необходимо установить золотники I II IV V гидрораспределителя Р3 в крайнее левое положение.
При этом рабочая жидкость поступает в штоковые полости гидроцилиндров (гидроопор) Ц3 Ц4 Ц9 Ц10 и в гидролинии управления гидрозамков ЗМ1 ЗМ2 ЗМ3 ЗМ4. По достижению в штоковых полостях гидроцилиндров (гидроопор) Ц3 Ц4 Ц9 Ц10 давления соответствующего по величине давлению открытия гидрозамков ЗМ1 ЗМ2 ЗМ3 ЗМ4 последние открываются и пропускают рабочую жидкость из поршневых полостей гидроцилиндров на слив в масляный бак Б.
После приведения крана в транспортное положение выносные опоры должны быть застопорены фиксаторами!
5.2.2 Работа гидрооборудования поворотной части крана
Для выполнения крановых оперций трехходовый кран Р2 необходимо установить в положение «крановые операции». При этом подача рабочей жидкости на поворотную часть крана и обратно осуществляется через гидрошарнир А (соединение вращающееся).
При нейтральном положении золотников гидрораспределителя Р1 рабочие отводы заперты напорная гидролиния через переливной канал гидрораспределителя Р1 соединена со сливом. Рабочая жидкость от насоса Н2 направляется в масляный бак Б.
Работа гидрооборудования механизма поворота поворотной части крана.
Для поворота поворотной части крана золотник I гидрораспределителя Р1 необходимо установить в зависимости от направления поворота в крайнее нижнее либо в крайнее верхнее положение. При этом рабочая жидкость от насоса Н2 через гидрораспределитель Р1 поступает к гидромотору М1 и гидравлическому тормозу механизма поворота ТГ1. Тормоз механизма поворота отключается вал гидромотора М1 начинает вращаться производится поворот платформы.
Клапаны КП1 и КП2 предназначены для защиты гидромотора М1 от превышения давления при резком изменении частоты вращения или останове поворотной части крана.
Работа гидрооборудования механизма грузовой лебедки
Подъем-опускание груза производится при перемещении золотника II гидрораспределителя Р1.
Для подъема груза золотник II гидрораспределителя Р1 необходимо установить в крайнее нижнее положение. Рабочая жидкость от насоса Н2 через гидрораспределитель Р1 тормозной клапан КТ3 поступает к гидромотору М2 и одновременно через блок гидроклапанов РК к гидравлическому тормозу лебедки ТГ2. Тормоз лебедки размыкается вал гидромотора М2 начинает вращаться груз поднимается а отработанная рабочая жидкость поступает на слив в масляный бак Б.
Для опускания груза золотник II гидрораспределителя Р2 необходимо установить в крайнее верхнее положение. Рабочая жидкость поступает в противоположную полость гидромотора М2 блок гидроклапанов РК и гидролинию управления тормозного клапана КТ3. Открывающийся тормозной клапан КТ3 пропускает рабочую жидкость на слив в масляный бак Б обеспечивая стабильность частоты вращения вала гидромотора М2 для всего диапазона нагрузок.
Редукционный клапан встроенный в блок гидроклапанов РК предназначен для поддержания в линии управления тормозом грузовой лебедки ТГ2 более низкого давления (2 МПа (20 кгссм2)) чем давление в напорной гидролинии.
Включение ускоренного режима работы лебедки возможно при подаче управляющего электрического сигнала на гидрораспределитель встроенный в гидромотор М2. При этом рабочая жидкость из гидролинии нагнетания гидромотора М2 поступает в узел управления и переключает его в режим увеличенной частоты вращения.
Вентиль ВН служит для соединения рабочих гидролиний гидромотора М2 при проверке тормоза грузовой лебедки а также для опускания груза при выходе из строя привода грузовой лебедки.
Клапан КП5 предназначен для защиты гидромотора М2 от превышения давления при резком изменении частоты вращения или обрыве груза.
Работа гидрооборудования механизма подъема стрелы
Управление гидроцилиндром Ц2 подъема стрелы производится золотником III гидрораспределителя Р1.
Для подъема стрелы золотник III гидрораспределителя Р1 необходимо перевести в крайнее нижнее положение. При этом рабочая жидкость от насоса Н2 через гидрораспределитель Р1 клапан тормозной КТ2 поступает в поршневую полость гидроцилиндра Ц2. Шток гидроцилиндра Ц2 выдвигается производится подъем стрелы. Из штоковой полости гидроцилиндра Ц2 рабочая жидкость поступает на слив в масляный бак Б.
Для опускания стрелы золотник III гидрораспределителя Р1 необходимо перевести в крайнее верхнее положение. Рабочая жидкость от насоса Н2 через гидрораспределитель Р1 поступает в штоковую полость гидроцилиндра Ц2 и в гидролинию управления тормозного клапана КТ2 шток гидроцилиндра втягивается производится опускание стрелы. Из поршневой полости гидроцилиндра Ц2 рабочая жидкость через открывающийся тормозной клапан КТ2 поступает на слив в масляный бак Б.
Клапан тормозной КТ2 обеспечивает стабильность скорости опускания стрелы для всего диапазона нагрузок.
Работа гидрооборудования механизма телескопирования секций стрелы
Гидроцилиндр Ц1 механизма телескопирования секций стрелы управляется золотником IV гидрораспределителя Р1.
Для выдвижения секций стрелы золотник IV необходимо установить в крайнее верхнее положение. При этом рабочая жидкость от насоса Н2 через гидрораспределитель Р1 тормозной клапан КТ1 поступает в поршневую полость гидроцилиндра Ц1. Шток гидроцилиндра Ц1 соединен с основной секцией а гильза со средней подвижной секцией. Гильза гироцилиндра Ц1 выдвигается перемещая среднюю и дальнюю подвижные секции стрелы (посредством полиспаста).
Из штоковой полости гидроцилиндра Ц1 рабочая жидкость поступает на слив в масляный бак Б.
Для задвижения секций стрелы золотник IV необходимо установить в крайнее нижнее положение. Рабочая жидкость от насоса Н2 через гидрораспределитель Р1 поступает в штоковые полости гидроцилиндра Ц1 и в гидролинию управления клапана тормозного КТ1. При этом клапан КТ1 открывается пропуская рабочую жидкость из поршневой полости гидроцилиндра Ц1 на слив в масляный бак Б.
Клапан тормозной КТ1 обеспечивает стабильность скорости перемещения секций стрелы для всего диапазона нагрузок.
Срабатывание приборов безопасности
При срабатывании прибора безопасности обесточивается электромагнит управления предохранительного клапана КП3 встроенного в напорную секцию гидрораспределителя Р2: напорная гидролиния гидрораспределителя Р1 соединяется со сливной; тормоза грузовой лебедки и механизма поворота замыкаются и выполнение крановых операций становится невозможным до момента подачи электрического сигнала на электромагнит управления предохранительного клапана КП3.
4. Аксиально-поршневые гидромашины
Насос — гидравлическая машина преобразующая механическую энергию приводного двигателя в энергию потока жидкости служащая для перемещения и создания напора жидкостей всех видов механической смеси жидкости с твёрдыми и коллоидными веществами или сжиженных газов. Следует заметить что машины для перекачки и создания напора газов выделены в отдельные группы и получили название вентиляторов и компрессоров. Разность давлений жидкости в насосе и трубопроводе обусловливает её перемещение.
Изобретение насоса относится к глубокой древности. Первый известный поршневой насос для тушения пожара который изобрёл древнегреческий механик Ктесибий упоминается ещё в I веке н. э.
Процесс объёмных насосов основан на попеременном заполнении рабочей камеры жидкостью и вытеснении её из рабочей камеры.
Общие свойства объёмных насосов:
Цикличность рабочего процесса и связанные с ней порционность и пульсации подачи и давления. Подача объёмного насоса осуществляется не равномерным потоком а порциями.
Герметичность то есть постоянное отделение напорной гидролинии от всасывающей (лопастные насосы герметичностью не обладают а являются проточными).
Самовсасывание то есть способность объёмных насосов создавать во всасывающей гидролинии вакуум достаточный для подъёма жидкости вверх во всасывающей гидролинии до уровня расположения насоса(лопастные насосы не являются самовсасывающими).
Независимость давления создаваемого в напорной гидролинии от подачи жидкости насосом.
Аксиально-поршневая гидромашина — один из видов роторно-поршневых гидромашин.
Аксиально-плунжерные и аксиально-поршневые гидромашины отличаются тем что в первых в качестве вытеснителей используются плунжеры а во вторых — поршни.
Выпускают гидромашины с наклонным диском (шайбой) и с наклонным блоком цилиндров. Аксиально-поршневые механизмы отличаются небольшими габаритами и незначительным весом. Возможно быстрое регулирование частоты вращения так как используются рабочие органы маленьких радиальных размеров а значит с небольшой инерцией.
При вращении вала 40 шатуны 38 через внутренние конические расточки поршней передают тангенциальную составляющую силы необходимой для приведения блока цилиндров 20 во вращательное движение. Фиксация блока в пространстве осуществляется с помощью центрального шипа 1 сферическая головка которого закреплена во фланце вала 40 а хвостовик опирается на втулку 33 запрессованную в центральное отверстие неподвижного сферического распределителя 32. В силу наклонного расположения блока цилиндров относительно оси влаа при вращении блока поршни совершают сложное движение: вращательное вместе с блоком цилиндров и возвратно-поступательное относительно стенок блока цилиндров. За один оборот вала каждый поршень в относительном движении совершает один двойной ход соответствующий последовательному увеличению и уменьшению объемов рабочих камер цилиндров. При этом за первую половину оборота вала распределитель обеспечивает коммутацию рабочих камер со всасывающей а во второй – с напорной линией гидросистемы подключенными к отверстиям в задней крышке 27 корпуса 37 насоса.
1. Расчет блока цилиндров
Если рабочий объем гидронасоса известен то задача расчета состоит в определении размеров основных деталей и узлов обеспечивающих получение требуемой частоты вращения вала при заданном номинальном потоке удовлетворяющих условиям прочности при расчетном давлении в напорной линии учитывающих необходимость обеспечения минимальных потерь мощности и оптимальной долговечности.
Определяющее влияние на размеры гидромашины оказывает блок цилиндров и принятая схема компоновки. Исходными данными для расчета блока служат: рабочий объем насоса q число цилиндров z давление нагнетания и угол наклона .
Рис. 5 – Блок цилиндров
Блок цилиндров показан на рисунке 5. Основными размерами блока являются: диаметр цилиндра d диаметр делительной окружности диаметр внутренней расточки наружный диаметр длина цилиндра и высота блока Н.
Рабочий объем определяется по формуле:
теоретическая подача;
фактическая подача которая нам задана в техническом задании т.е. подача без учета утечек;
объемный КПД гидронасоса принимаем .
1.1. Расчет диаметра поршней
угол наклона блока цилиндров = 30;
z количество поршней принимаем z = 9 рабочий объем одного цилиндра будет равен:
А – относительная толщина толстостенного цилиндра определяется по формуле:
максимальное давление нагнетания МПа; принимаем МПа т.к. МПа по условию; принимаю материал блока цилиндров сталь 40Х [] = 180 МПа.
принимаем относительную толщину цилиндра с запасом А = 15.
дезаксиал определяется по формуле:
с добавочный коэффициент с = 15
Полученный размер округляем по ГОСТ 12447 – 80 т.е. принимаем мм.
1.2. Определение основных размеров блока цилиндров
Определим диаметр делительной окружности блока цилиндров:
А – относительная толщина толстостенного цилиндра;
z количество поршней;
Наружный диаметр блока цилиндров:
b – размер перемычки между двумя соседними цилиндрами
Внутренний диаметр блока цилиндров:
Конструктивно принимаем мм
Приму минимальную толщину дна блока цилиндров равную:
Определим диаметр окружности заделки шатунов в диске:
Конструктивно принимаем мм.
Определение максимального хода поршней
Размер b1 определяется по формуле (15):
Длина заделки поршня определяется по формуле (18):
Величина полного хода поршня от крайнего внешнего до крайнего внутреннего положения определяется по формуле (19):
Длина цилиндра определяется по формуле (21):
где ц запас (как правилоц=01-02 мм) мм.
Толщина дна цилиндра определяется по формуле (22):
Высота блока цилиндров определяется по формуле (23):
Подвнутрение b4 определяется по формуле (24):
1.3. Проверка блока цилиндров на прочность
Проверка на прочность проводится по формуле:
максимальное давление насоса берется из технического задания МПа;
коэффициент запаса принимаем =12.
Выбираем для блока цилиндров сталь 40Х для этой стали предельно допустимое значение напряжений =180 МПа.
Расчет блока на жесткость выполняется приближенно по формуле для радиальной деформации толстостенной трубы:
коэффициент Пуассона принимают для сталей равным 028
допускаемая деформация принимается равной 12-14 мкм для блоков из сталей;
Е модуль упругости Е = 2 МПа.
По допустимым напряжениям блок цилиндров удовлетворяет существующим нормам.
Во всех случаях уточнения размеров при конструировании необходимо следить чтобы толщина материала на всех участках разделяющих внутреннюю полость цилиндров и внешние поверхности блока включая проточки фаски и т.п. была не меньше чем во избежание нарушения прочности блока.
2. Расчет геометрии торцевого распределителя
Определим диаметр окружности на котором размещается ось окон всасывания и нагнетания. Для уменьшения окружных скоростей на уплотняющих поверхностях конструктивно принимаем мм.
Рис. 6 – Торцевой распределитель
Рассчитаем радиус закругления окна по формуле:
отношение площади окна и площади цилиндра принимаем равным 05.
Конструктивно принимаем = 045 см.
= = 1566 – 689 = 877.
Скорость жидкости в окне цилиндра не должна превышать 75 мс.
V0 – скорость жидкости в окне цилиндра;
F0 – площадь окна цилиндра.
Угол конструктивно принимаем равным .
т.е. предельная скорость не превышена.
Толщина окна цилиндра:
Определим угол наклона шатуна к оси поршня по формуле:
диаметр окружности заделки шатунов в диске.
Определим ширину уплотняющего пояска по формуле:
диаметр окружности на которой размещается ось окон всасывания и нагнетания;
F0 – площадь окна цилиндра;
F – площадь цилиндра;
конструктивно принимаем а = 8 мм.
2.1. Расчет сил действующих в распределительном узле
Допущения при расчете:
Давление в масляном слое между торцами ротора и распределительного диска на уплотняющих поясках меняется по линейному закону.
Давление в уплотняющей перемычке и уплотнительных поясках расположенных на стороне всасывания принимается равными нулю.
Момент от сил опрокидывающих ротор и нагружающих торцевой распределитель не учитывается.
Воспользуемся секторным методом расчета гидростатических сил для этого рассмотрим центральный сектор на распределителе с углом охвата и центральным размещением в этом секторе оси цилиндра.
Запишем равновесие сил действующих на цилиндровый блок.
усилие действующее в направлении прижатия блока цилиндров кН; определяется по формуле:
номинальное давление насоса в полости нагнетания МПа;
давление в полости всасывания МПа.
усилие действующие в направлении отжатия блока цилиндров кН; определяется по формуле:
а ширина уплотняющего пояска;
радиус закругления окна;
площадь канала на распределителе.
Получили что Fпр> Fотж следовательно условие обеспечения прочного контакта выполняется.
3. Расчет и конструирование поршневых групп
Поршневая группа является ответственным узлом гидромашины так как от ее исполнения во многом зависят объемный и механический КПД и общий ресурс.
Определим диаметр головки шатуна со стороны упорного диска.
Определим диаметр головки шатуна со стороны поршня.
Определим длину поршня.
Длину шатуна выбираем исходя из условия что:
диаметр делительной окружности блока цилиндров
Диаметр шатуна определяем конструктивно:
Диаметр отверстия для подвода смазки в шатуне конструктивно принимаем мм .
3.1. Проверка прочности поверхностей поршней в месте их контакта со сферическими головками шатунов
Материал поршня бронза [доп ]=50МПа.
Проверка прочности по опорным поверхностям сферических шарниров.
рр – расчетное давление
рр = 125рн = 12520 = 25 МПа;
Кс – коэффициент использования площади опорной поверхности; принимаем Кс = 1.
То есть условие прочности выполняется.
Рассчитаем шатун на продольную устойчивость и прочность для этого учтем силу продольного сжатия.
Определим момент трения в шарнирах возникающий при вращении блока цилиндров:
fтр– коэффициент трения принимаем fтр = 013;
сила продольного сжатия;
диаметр головки шатуна со стороны упорного диска.
Принимаем материал шатунов – сталь марки 12 ХН3А ГОСТ 4543 – 61 [доп] = 150 МПа.
Напряжение сжатия определим по формуле:
диаметр отверстия для подводки смазки в шатуне.
условие сжатия выполняется.
Wмин – момент сопротивления наиболее ослабленного сечения при изгибе;
Суммарные напряжения:
б – коэффициент снижения допускаемого напряжения зависит от гибкости λ и определяется (приближенно) по таблице.
КШ запас прочности принимаем КШ = 18;
предел усталостной прочности при продольном сжатии и пульсирующем характере нагружения -1 = 700 МПа
Условие прочности выполняется.
3.2. Выбор зазоров в сопряжениях распределительного узла и блок – плунжер
Масла обладают хорошей смазывающей способностью в гидродинамических условиях при обеспечении достаточно больших зазоров между трущимися парами более 05 мкм. При повышении нагрузок и уменьшении зазоров наступает переход к граничному трению характеризующемуся соприкосновению граничных пленок которые предотвращают контакт чистых металлов и их схватывание.
При повышении точности обработки цилиндра позволяет повысить КПД и обеспечить взаимозаменяемость при сборке поршневой группы.
При уменьшении зазора между блоком цилиндров и сферическим распределителем увеличивается градиент скорости .
При больших градиентах скорости сдвига происходит ориентация молекул загущающей присадки вдоль оси потока молекул основы что ведет к уменьшению вязкости загущенного масла. При вязкость некоторых загущенных масел приближается к вязкости основы.
Технологический диаметр поршня назначают так чтобы между поршнем и цилиндром обеспечивался гарантированный зазор:
Оптимальным считаем зазор .
Масло ВМГЗ производится на минеральной основе малой вязкости и низкой застываемости путем гидрокаталитического процесса. Кроме того масло проходит дополнительную очистку. Полученная основа обрабатывается загущающей присадкой — полиметакрилатом. Также в масло добавляется еще ряд присадок.
Масло ВМГЗ относится к классу внесезонных гидравлических масел и обеспечивает бесперебойную работу гидросистем при самых непростых условиях среды. Согласно ГОСТ 17479.3-85 данное масло имеет обозначение — МГ-15-В и полностью соответствует ТУ 38.101479-86.
Благодаря содержанию композиции присадок масло вмгз обладает массой полезных эксплуатационных свойств:
— прекрасными вязкостно-температурными характеристиками (в широком температурном диапазоне);
— хорошими антипенными свойствами;
— высокой химической и антиокислительной стабильностью;
— масло стойко к коррозии износу и деструкциям механического характера;
— хорошо фильтруется.
Кроме того масло ВМГЗ легко отделяется от воды не является токсичным и совместимо с резинотехническими устройствами гидросистем.
Сферы применения ВМГЗ
Благодаря своим свойствам и преимуществам масло находит применение:
как всесезонный сорт в системах гидравлики и гидроприводах следующих устройств:
— дорожного и лесозаготовительного оборудования;
— строительной и подъемно-транспортной техники.
Масло пригодно для использования в условиях таких регионов как Сибирь Дальний Восток Крайний Север при температурах от -30 до +60 °С.
как сезонный сорт его применяют в условия зимы для территорий с умеренным климатом. При этом диапазон температур составляет от 58 до +70 °С.
Технические характеристики ВМГЗ
Наименование показателя
Плотность при 20 °С кгм³ не более
Кинематическая вязкость м²с при 50 °С не менее
Кинематическая вязкость м²с при - 40 °С не более
Индекс вязкости не менее
Массовая доля % не более:
- механический премесей
Температура °С вспышки в открытом тигле не ниже
Температура °С застывания не выше
Испытание на коррозию
Кислотное число масла без присадок мг КОНг не более
Стабильность против окисления: массовая доля осадка после окисления % не более
Цвет на колориметре ЦНТ единицы ЦНТ не более
1. Расчет объемных потерь
Утечки масла в аксиально-поршневых гидромашинах происходят по зазорам между цилиндрами и поршнями и между блоком цилиндров и сферическим распределителем. Эти утечки в зазорах определяются по формуле:
Δp – перепад давления на щели;
- динамическая вязкость; определяется по формуле:
ρ- плотность жидкости
кинематическая вязкость при номинальной температуре
= d – периметр щели;
– длина поршня оставшегося в цилиндре при h = hмах .
Определим утечки по зазорам между цилиндрами и поршнями:
Определим утечки по зазорам в распределительном узле:
– периметр щели на распределителе найдем по формуле:
– угол полукольцевого окна входа на распределителе принимаем равным
– длина щели принимаем равной величине уплотняющего пояска;
Определим суммарные утечки:
2. Расчет гидромеханических потерь
Преобразование энергии – механической в гидравлическую в гидронасосах обеспечивается за счет движения рабочих элементов которое сопровождается потерями энергии на трение механических частей.
Определим момент трения развиваемый при движение поршней в цилиндрах блока.
Определим момент трения развиваемый при движении блока цилиндров относительно распределителя:
нормальная сила прижатия блока цилиндров к сферическому распределителю определяется как:
Определим момент затрачиваемый на преодоление гидравлических сопротивлений во время движения поршня в цилиндре Мг:
NГ - гидравлические потери мощности; определяются по формуле:
-угловая скорость вращения вала насоса;
hдл – потери удельной механической энергии по длине; определяются по формуле:
λ-коэффициент гидравлического трения;
мах – максимальная скорость поршня;
Для определения коэффициента гидравлического трения сначала определим число Рейнольдса т.к. именно от этого параметра зависит по какой зависимости находить коэффициент гидравлического трения.
Это зона турбулентного режима течения жидкости. В этой области коэффициент гидравлического трения определяется по формуле Блазиуса :
Рассчитаем потери удельной механической энергии по длине
Рассчитаем потери мощности
Рассчитаем момент затраченный на преодоление гидравлических сопротивлений
Определим суммарный момент трения
3. Расчет коэффициентов полезного действия
Определим гидромеханический КПД мотора
В гидромашине имеют место потери мощности на трение в подшипниковых парах: п =098 – КПД одного подшипника;
Мтр – теоретический крутящий момент на валу мотора;
Определим объемный КПД мотора
Определим общий КПД мотора
4. Расчет диаметра вала мотора подбор подшипников и шпоночного соединения
Так как на данном этапе расчета нам неизвестно расстояние между опорами вала гидромашины то диаметр вала определим грубо в первом приближении из расчета на чистое кручение по формуле:
допускаемые напряжения при изгибе. Чтобы косвенно учесть изгиб вала допускаемые напряжения занижаем. Принимаем
Полученный диаметр округляем до ближайшего стандартного значения. Принимаем
Расчет шпоночного соединения на прочность проводится по напряжениям смятия:
Рисунок 13 – Расчетная схема шпоночного соединения
– допускаемые напряжения на смятие.
Шпонка для фиксации цилиндрического зубчатого колеса на тихоходном валу:
Шпонка 12×8×60 ГОСТ 23360-78:
Т= Мтр=3562 (Нм) – момент на валу;
lp – рабочая длинна шпонки:
b=12 (мм) – ширина шпонки;
d=42 (мм) – диаметр посадочной части вала;
h=8 (мм) – высота шпонки;
t=5 (мм) – глубина паза на валу.
Условие прочности выполнено запас прочности обеспечен.
4.1. Расчет крутящего момента и мощности мотора
Определим эффективный момент на валу гидромотора по формуле:
гидромеханический КПД мотора.
Определим полезную (выходную) мощность гидромотора по формуле:
В курсовом проекте необходимо было разработать насос для привода крана автомобильного КС-55732 нерегулируемый рассчитанный на среднее номинальное давление и номинальный поток. Прототипом послужил гидронасос аксиально-поршневой типа 310.
Барышев В.И. Лайко К.К. Объемные гидромашины. Часть 1. Аксиально-поршневые гидромашины: учебное пособие по курсовому проектированию. – Челябинск: Изд. ЮУрГУ 2010. – 131 с.
Атлас конструкций гидромашин и гидропередач: Учебное пособие для студентов машиностроительных специальностей вузовБ.М. Бим – Бад М.Г. Кабаков В.Н. Прокофьев и др. – М.: Машиностроение 1990. – 136 с.: ил.
Барышев В.И. Подзерко А.В. Объемные гидромашины и гидроприводы: Учебное пособие к практическим занятиям. – Челябинск: Изд. ЮУрГУ 2003. – 54 с.
Башта Т.М. Машиностроительная гидравлика: Справочное пособие. – 2-е изд. перераб. и доп. – М.: Машиностроение 1971. – 672 с.
Башта Т.М. Объемные насосы и гидравлические двигатели гидросистем. – М.: Машиностроение 1974. – 606 с.
Борисов Б.П. Саков В.А. Аксиально-поршневые гидромашины. Ч.1. Анализ конструкций: Учеб. пособие для курсового и объемного проектирования по курсу «Теория и расчет объемных гидромашин». Под ред. Д.А. Бутаева. – М.: Изд. МГТУ 1993. – 55 с.
Кулагин А.В. и др. Основы теории и конструирования объемных гидропередач. – М.: Высшая школа 1968. – 400 с.
Методические указания к курсовому пректированию объемных гидромашин Составители: В.И. Барышев В.Л. Троицкий; под ред. А.Г. Бургвица – Челябинск: ЧПИ 1982. – 27 с.
Орлов Ю.М. Механика жидкости гидравлические машины и основы гидропривода агрегатов ракетных комплексов: Учебное пособие. – Мин. Обороны РФ. Пермь –2001. – 379 с.
Юдин А.П. Гидравлика гидравлические машины и гидропривод. – М.: Высшая школа 1965. – 428 с.
Рекомендуемые чертежи
Свободное скачивание на сегодня
Другие проекты
- 20.08.2014