Привод силовой





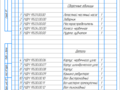

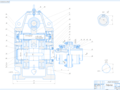
- Добавлен: 04.11.2022
- Размер: 2 MB
- Закачек: 0
Описание
Курсовой проект - Привод силовой
Состав проекта
![]() |
![]() ![]() ![]() ![]() |
![]() ![]() ![]() ![]() |
![]() ![]() ![]() ![]() |
![]() ![]() ![]() ![]() |
![]() ![]() ![]() ![]() |
![]() ![]() ![]() |
Дополнительная информация
на сдачу 3.cdw

Спецификация 3.spw

на сдачу.cdw

на сдачу 2.cdw

Спецификация.spw

Рекомендуемые чертежи
Свободное скачивание на сегодня
- 22.08.2014
- 29.08.2014