Модернизация объемного насоса НШ-32У




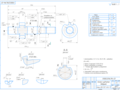
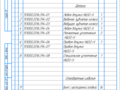
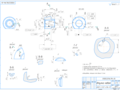
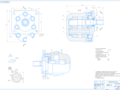
- Добавлен: 04.11.2022
- Размер: 1 MB
- Закачек: 2
Описание
Курсовой проект - Модернизация объемного насоса НШ-32У
Состав проекта
![]() |
![]() |
![]() ![]() ![]() |
![]() |
![]() |
![]() ![]() ![]() ![]() |
![]() |
![]() ![]() ![]() ![]() |
![]() |
![]() ![]() ![]() ![]() |
![]() |
![]() ![]() ![]() ![]() |
![]() ![]() ![]() ![]() |
![]() |
![]() |
Дополнительная информация
ПЗ.docx
Государственное образовательное учреждение высшего профессионального образования
Южно-Уральский государственный университет
Факультет «Механико - технологический»
Кафедра «Гидравлика и гидропневмосистемы»
«Объемные гидромашин и ГП»
РАСЧЕТНО - ПОЯСНИТЕЛЬНАЯ ЗАПИСКА
К курсовому проекту на тему
«Модернизация объемного насоса НШ-32У»
ЮУрГУ - 151000.2016.394 ПЗ
Нормоконтролер Руководитель
Студент группы П-457
Работа защищена с оценкой
Апаликов А.С. Модернизация объемного насоса НШ-32У. — Челябинск: ЮУрГУ П-457;2016 37с. 11 ил. табл. 4 библиогр. список — 7 наим. прил. 4.
В данном курсовом проекте произведена модернизация шестеренного насоса типа НШ-32У.
Проведены расчеты основных его частей.
Рассчитаны и построены основные характеристики.
ОСОБЕННОСТИ КОНСТРУКЦИИ И РАБОТЫ ОБЪЕКТА7
КОНСТРУКЦИЯ И РАСЧЕТ ДЕТАЛЕЙ И УЗЛОВ10
Выбор материала и способа термической обработки для шестерён12
Допускаемые напряжения при расчете зубьев на выносливость по изгибу15
Расчет диаметра вала16
Расчет разгрузочных канавок19
Расчет подшипников скольжения21
Расчет соединительных винтов23
ПРОВЕРОЧНЫЕ РАСЧЕТЫ24
Проверка кавитационного запаса24
Проверочный расчет подшипников скольжения25
Расчет зазоров. Обеспечение требуемого объемного КПД26
Тонкость фильтрации жидкости28
Пульсация потока жидкости29
Расчет характеристик насоса30
БИБЛИОГРАФИЧЕСКИЙ СПИСОК33
ПРИЛОЖЕНИ А Сборочный чертеж НШ32-У34
ПРИЛОЖЕНИЕ Б Чертеж ведущего зубчатого колеса НШ32-У35
ПРИЛОЖЕНИЕ В Чертеж левой втулки НШ32-У36
ПРИЛОЖЕНИЕ Г Характеристики НШ32-У37
Благодаря простоте конструкции шестеренные гидромашины получили очень широкое распространение в качестве нерегулируемых насосов применяемых для питания гидропередач небольшой мощности с дроссельным управлением для подачи смазки для питания систем управления. Шестеренные насосы применяют чаще всего для перекачивания вязких жидкостей: масла нефти мазута дизельного топлива легко застывающих жидкостей (например битума парафина или вискозы) не содержащих механических примесей. Они широко распространены в машиностроительной нефтяной и химической промышленности коммунальном и сельском хозяйстве мобильной технике [6]. Стоит отметить что шестеренные насосы высокого давления в современном производстве получили новую и весьма эффективную модификацию – соединение с двигателем посредством эластичной муфты. Оба этих механизма устанавливаются на эластичной рампе или плите. Данная разновидность конструкции получила название насосного агрегата а их прямое предназначение – это осуществление перекачки примесей нефтяных продуктов. Кроме того сейчас насосные агрегаты оснащаются специальными механизмами которые позволяют производить регулировку потока.
Современная рыночная экономика сильно влияет на нашу жизнь. И одно из главных правил экономики – минимизация затрат и максимизация прибыли. Для достижения этой цели создают технику с меньшими потерями энергии т.е. с большим КПД. Шестеренные насосы не стали исключением.
Основные направления развития шестеренных насосов:
- повышение рабочего давления частоты вращения с целью уменьшения массы и габаритов насоса
- повышение герметичности с целью увеличения объемного КПД
- повышение надежности за счет идейных средств в диагностике упрощения обслуживания и ремонта
- повышение функциональных возможностей
- повышение безопасности.
В данном курсовом проекте будут реализованы два направления развития: повышение герметичности и повышение надежности. Герметичность будет достигнута путем точного изготовления деталей с малыми допусками а надежность будет повышена при помощи увеличения времени безотказной работы насоса.
В качестве объекта разработки выбран шестеренный насос применяемый для нагнетания минерального масла в гидравлических системах (различных механизмов тракторов погрузчиков сельскохозяйственных машин строительно-дорожной техники).
Технические характеристики
Рабочий объём q = 32 (см3)
Частота вращения nн = 5000 (обмин)
Номинальное давление Pн = 16 (МПа)
Объёмный расход Qн = 63 (лмин)
Необходимо повысить объемный КПД на 136% при повышении надежности на 10%.
Описание прототипа насоса – шерстеного насоса НШ-32У.
Насос шестеренный предназначен для нагнетания минерального масла в гидравлических системах тракторов погрузчиков сельскохозяйственных коммунальных строительно-дорожных и агрегируемых с двигателями тракторов машин и другой техники [7].
Прототип рассчитан на среднее давление поэтому его корпус выполнен из алюминия а не из чугуна и насос остается компактным.
Табл.1. Технические характеристики прототипа.
Частота вращения nн обмин
Номинальное давление Pн МПа
Объёмный расход Qн лмин
Кинематическая вязкость рабочей жидкости м2с
Температура перекачиваемой жидкости оС
Рис. 2. Габаритный чертеж прототипа НШ32-У
Рис. 3. Характеристика прототипа насоса.
ОСОБЕННОСТИ КОНСТРУКЦИИ И РАБОТЫ ОБЪЕКТА
Для проектирования выбран шестеренчатый насос с наружным зацеплением он состоит из:
Ведущего и ведомого вала-шестерни
Камеру образуют зубья шестерни корпус и торцы подшипников скольжения. Вращаясь шестерни создают периодическое разряжение со стороны всасывания в линии всасывания. Из-за разности давлений жидкость заполняет впадины зубьев шестерен вышедших из зацепления. Далее жидкость переносится к линии нагнетания. Зубья шестерен входя в зацепление уменьшают объем рабочей камеры и выталкивают жидкость в линию нагнетания.
Рассмотрим элементы насоса в отдельности:
)Корпус – базовая деталь при сборке шестеренного насоса т.е. сборку начинают с корпуса. Его выполняют литым из чугуна или алюминия для снижения трения между зубьями шестерён и корпусом.
)Крышки служат для закрепления в осевом направлении валов-шестерен и втулок. Крышки также выполняются литыми как и корпус из-за их конструкции. Крышку дешевле и проще отлить и обработать чем выточить из цельного прутка или блока металла.
)Вал-шестерня – рабочий орган насоса т.к. он непосредственно изменяет рабочую жидкость (её давление скорость энергию) передавая энергию от электродвигателя жидкости. Вал-шестерня выполняется из стали в качестве термообработки применяется закалка токами высокой частоты или цементация (для упрочнения детали). Вал-шестерня по твердости выполняется более твердым чем подшипник скольжения по причине того что подшипник проще в изготовлении.
)Подшипник – опора вращающихся или качающихся валов и осей основанный на принципе трения качения (для подшипников качения) или трения скольжения (для подшипников скольжения). В нашей конструкции используются подшипники скольжения. Они изготавливаются из сплавов алюминия бронзы или металлокерамики (для образования антифрикционной пары вал – подшипник).
)Уплотнения служат для уменьшения зазоров и как следствие снижения утечек рабочей жидкости защиты от попадания пыли из окружающей среды. Уплотнения выполняют из резины.
)Винты и пружинные шайбы соединяют закрепляют крышки относительно корпуса насоса. Шайбы предотвращают развенчивание резьбового соединения. Винт и шайбы – стандартные изделия.
Насосы шестеренчатого типа широкое применение получили в автомобильных гидравлических системах и различных отраслях промышленности. Основное преимущество данных устройств – возможность перекачки жидкостей любой степени вязкости. К тому же шестеренные гидравлические насосы достаточно прочны и долговечны при этом данный агрегат способен пропускать через себя огромное количество перекачиваемой среды.
Шестеренчатый насос представлен в виде агрегата в котором рабочим органом являются шестерни. Принцип работы такого насоса базируется на их вращении. Шестерни на стороне всасывания формируют разрежение воздуха. За счет этого происходит перепад давления (в камере всасывания создается пониженное давление) жидкость приходит в движение и заполняет собой все пространство между зубьями. Благодаря этому шестеренный насос инициирует перемещение жидкости в сторону нагнетания а далее вытесняет ее в нагнетательный патрубок. Конструкция и схема шестеренного насоса достаточно проста а главным преимуществом является достаточно недорогое обслуживание. Насосы шестеренчатого типа нашли свое применение в различных сферах промышленности – пищевой нефтеперерабатывающей сельскохозяйственной и других отраслях. Шестеренчатые насосы высокого давления активно применяются во многих отраслях химической промышленности а именно для осуществления перекачки щелочей нефтепродуктов и эмульсий. В пищепроме – для проведения перекачки какао меда сливок карамелей. Также их используют в лакокрасочной и нефтепромышленной областях. Гидравлические шестеренчатые насосы обладают рядом неоспоримых преимуществ: простота и высокая степень надежности при эксплуатации; способность к перекачке жидкостей обладающих различными степенями вязкости (вплоть до густой среды); длительные сроки эксплуатации.
Особенности работы шестеренного насоса:
Энергия передается от насоса жидкости за счет вращения роторов.
Пульсация подачи т.е. подача идет порциями равными объему камер. Выделяют среднюю мгновенную подачу и отклонения от нее.
Защемленный объем от которого стараются избавиться при помощи разгрузочных канавок следящего привода и др. Приводит к резким перепадам давления в зоне зацепления зубьев.
Давление в насосе постепенно возрастает от линии всасывания к линии нагнетания.
КОНСТРУКЦИЯ И РАСЧЕТ ДЕТАЛЕЙ И УЗЛОВ
Объем рабочей камеры q=32(см3) ширина шестерни b=32(мм) – данные взяты с прототипа.
Теоретический объём:
Qт=bn100=160(лмин) (1)
Где n=5000(обмин)- частота вращения шестерён.
Объемный кпд задан тогда номинальная подача:
предварительный модуль:
m=(024 044)=294 539(мм)
Удельная производительность:
По монограмме I (стр.136 [6]) определяем модуль и число зубьев для q’=1(см3):
Табл.2. Соотношение m и z.
ближе к 539 значит принимаем m=55(мм).
По таблице 1 (стр.138 [6] ) определяем параметры корригированного зуба.
Табл.3. Параметры корригированного зуба.
Расстояние между центрами мм
Ад=m(z+1)=5.5(10+1)=77
Диаметр начальной окружности мм
Диаметр окружности головок мм
Диаметр окружности впадин мм
Df=Df1m=1163255=63976
Диаметр основной окружности мм
dо=dо1m=12216055=67188
tо=tо1m=2952155=1623655
Угол зацепления передачи
Профильное смещение рейки мм
Размер для зубомера:
Толщина по начальной окружности мм
h*=h1*m=1048755=576785
Размер блочной скобы на 2 зуба мм
M=M1m=4998255=274901
Толщина зуба у вершины мм
sе=sе1m=0378855=20834
Боковой зазор между зубьями (по дуге начальной окружности) мм
Площадь зуба (полная) мм2
Sz=Sz1m=33735552=102048375
Площадь впадин (полная) мм2
Sw=Sw1m=39155552=118443875
Рис. 5. Профиль зубьев шестерни.
Выбор материала и способа термической обработки для шестерён
Для выбора материала и способа термической обработки нужно знать контактные напряжения действующие на зубья шестерни. Материал и способ обработки выбирается из соображений что допустимые контактные напряжения для выбранного материала при заданном способе обработки будут больше контактных напряжений действующих на зуб шестерни.
Теоретическая мощность сообщаемая жидкости:
N=pQт=2810616060000=747(кВт) (3)
Момент развиваемый на валу:
Рис. 6. Силы в зацеплении.
Допускаемые контактные напряжения при расчете на выносливость активных поверхностей зубьев
Допускаемые контактные напряжения:
где =12 – минимальный коэффициент запаса прочности.
=1380(МПа) – предел контактной выносливости для цементированной стали 20Х ГОСТ4543-71.
ZH= – коэффициент долговечности для шестерни.
NHlimb(HHB)=20106 – базовое число циклов напряжений определяется по рис.6 (стр. 28 [5]).
Эквивалентное число циклов контактных напряжений для типового режима нагружения определяется по формуле:
=60nTэ=602593454=14106
Tэ=Tti(m’i)3=13200(0990853+0113)=93454
m1=MнMmax=1426168=085
t1=T1n1Tncp=099T5000T5000=099
t2=T2n2Tncp=01T5000T5000=01
- число циклов нагружения зуба шестерни за весь срок службы
=60nT=608313200=657106
T =13200 - время безотказной работы насоса ч.
Окружная сила действующая по касательной к начальным окружностям создающая на валах вращающие моменты:
Ft=2Md=214260077=37(кН)
Радиальная сила действующая по радиусу зубчатых колес:
Fr=Fttg()=37103tg29о14’=211(кН)
Сила взаимодействия между сопряженными зубьями:
Удельная расчетная окружная сила:
WHt==1105107=235(Нмм)
где =1 – коэффициент учитывающий распределение нагрузки между зубьями в связи с погрешностями изготовления.
=105 – коэффициент учитывающий неравномерность распределения нагрузки по длине контактных линий при расчете на контактную выносливость активных поверхностей зубьев (рис.10 стр. 35 [5])
=1+ – коэффициент учитывающий динамическую нагрузку возникающую в зацеплении.
WHV==0014738=125(Нмм) - удельная окружная динамическая сила.
=47 – коэффициент учитывающий влияние разности шагов зацепления зубьев шестерен (табл. 17 стр.43 [5])
=001 – коэффициент учитывающий влияние вида зубчатой передачи и модификации профиля зубьев (табл. 16 стр. 42 [5])
V=314dn60000=3140077500060000=20.1(мс) – окружная скорость в зацеплении.
Расчетное контактное напряжение:
=097 – коэффициент учитывающий суммарную длину контактных линий.
Условие контактной прочности шестерен выполнено.
Допускаемые напряжения при расчете зубьев на выносливость по изгибу
Проверочный расчет цилиндрической передачи на выносливость зубьев по изгибу
Цель расчета – предотвращение усталостного излома зубьев у основания вследствие действия переменных напряжений изгиба.
Допускаемые напряжения при расчете зубьев на выносливость по изгибу:
=680 МПа - предел выносливости при изгибе для стали 20Х.
=17 – коэффициент запаса.
KF=115 – коэффициент учитывающий неравномерность распределения нагрузки по длине контактных линий при расчете зубьев на выносливость при изгибе (определяется по рис.14 стр.56 [5])
KFα=KHα=1 – коэффициент учитывающий распределение нагрузки между зубьями.
WFV==00114738=1375(Нмм) - удельная окружная динамическая сила.
WFt==11151675=223(Нмм) – удельная окружная сила.
YFS(z=13)=42 – коэффициент учитывающий форму зуба и концентрацию напряжений (определяется по графику рис.15 стр. 58 [5])
Y=1 – коэффициент учитывающий перекрытие зубьев.
Y=1-120=1-0=1 – коэффициент учитывающий наклон зуба.
Расчетное напряжение изгиба на переходной поверхности зуба определяется по формуле
Условие прочности при изгибе выполнено.
Расчет диаметра вала
Диаметр вала определим по допускаемому сопротивлению кручения. Для стали 20Х предел выносливости при кручении =75(МПа) (стр.42 [2]).
Примем коэффициент запаса n=2 значит допустимое сопротивление кручению:
Диаметр вала шестерни определяется по формуле:
Будем изготавливать цельный вал-шестерню в связи с тем что Dfdвала=4071230=13516.
Диаметры отверстий всасывания и нагнетания выбираем из условия ограничения скорости:
- в линии всасывания v≤2 (мс) v= при dвс=30(мм).
- в линии нагнетания v≤6 (мс) v= при dн=13(мм).
Напряжение на стенках корпуса:
DК – наружный диаметр корпуса мм
Dе – диаметр головок шестерни мм
Как говорилось ранее корпус выполняется из алюминия или чугуна поэтому рассчитаем наружные диаметры корпусов для алюминиевого и чугунного корпусов [6].
Для алюминиевого литья 49 МПа.
5 – 17556210-6=+56210-6
DК==010723(м)110(мм).
Для чугунного литья 686 МПа.
5 – 24556210-6=+56210-6
DК==008638(м)90(мм).
Будем выполнять корпус из чугуна т.к. габариты корпуса в этом случае меньше значит насос будет более компактным.
Выбор рабочей жидкости
Рабочую жидкость выбирают в зависимости от её вязкости при различных температурах т.к. вязкость жидкости влияет на потери давления и уровень кавитации.
Выбранный шестеренный насос часто применяется в мобильной технике поэтому диапазон температур окружающей среды для районов средней полосы РФ и южных районов РФ от -35 до +50 С. Так как температура застывания должна быть на 15-20 ниже минимальной температуры окружающей среды а минимально допустимая вязкость масла должна быть при температуре на 70-80С [3] поэтому температура рабочей жидкости у нас изменяется от -45 до +80 С. Минимально допустимая вязкость для шестеренчатых насосов равна 18сСт а максимально допустимая вязкость масла равна 1000сСт (взята из назначенной вязкости масла прототипа). По рис.4 выбираем марки масла. Так как температурный диапазон достаточно большой можно применять зимнее и летнее масло для работы гидросистемы.
Рис. 8. Температурно-вязкостные характеристики масел
В качестве основных рабочей жидкости выбраны:
АМГ-10 (зимнее масло)
ВНИИНП-401 (летнее масло).
Расчет разгрузочных канавок
В момент вступления в зацепление новой пары зубьев между ними остается защемленный объем жидкости который по мере вращения шестерен уменьшается. А запертая в этом объеме жидкость выдавливается через торцы в полость нагнетания так как жидкость практически несжимаема и при уменьшении её объема давление в ней резко возрастает. Это явление не желательно. Можно устранить резкое повышение давления в защемленном объеме жидкости путем введения разгрузочных окон (канавок).
При расчете исходим из того что канавка должна сообщаться с нагнетательной полостью до момента расположения точек касания симметрично относительно полюса т.е. на расстоянии от него равном tо2. При этом положении суммарный объем является минимальным.
Рассмотрим только суммарный объем исходя из предположения что наличие боковых зазоров между зубьями делает затвор жидкости по нерабочей стороне зуба недействительным.
Запертый объем разгружается обычно с помощью глухих канализационных канавок небольшой глубины выполненных на подшипниках насоса. Запертый объем уменьшающийся при вращении шестерен соединяется канавкой с полостью нагнетания а увеличивающийся – с полостью всасывания [6].
На рис. 9 изображен торец расточки корпуса и торец подшипника.
Рис. 9. Схема разгрузочных канавок.
Наклонная прямая идущая под углом α к линии центров представляет собой касательную к профилям зубьев шестерен при зацеплении их в точке отстоящей от полюса зацепления на расстоянии tо2. Значит данная точка ограничивающая профиль разгрузочной канавки находится от линии центров на расстоянии равном tоcosα где α=29о14’ – угол зацепления передачи tо=1623655(мм) – основной шаг. Найдем координату точки:
с=t02cosα=162365505cos29о14’=93(мм).
Так как между подшипниками и шестернями нет зазора то профиль канавки делается параллельным линии центров. Расстояние b между разгружающими канавками выбирается наименьшим из возможных при котором обеспечивается надежное разделение канавок текущим зубом:
где m – модуль зацепления мм;
==АдcosαАт=770873715=094 – косинус угла зацепления режущего инструмента;
Ад – действительное расстояние между центрами мм;
Ат – теоретическое расстояние между центрами мм;
α – угол зацепления передачи.
Длина канавки определяется по формуле:
Ширина канавки а=13m=0355=455(мм).
Глубина канавки c=005m=0555=175(мм).
Расчет подшипников скольжения
Расчет производится по удельной нагрузке Р в подшипнике и величине Рv в некоторой мере характеризующей износ подшипника скольжения [6].
Окружная скорость на шейке вала:
где d – диаметр подшипника мм;
n – частота вращения вала обмин.
Реакция действующая на подшипник рассчитывается по формуле:
где р – давление в линии нагнетания МПа;
b – ширина шестерни м;
Dе – диаметр окружности головок м.
Определим требуемую длину подшипника скольжения – l(мм):
l=P[p]d=213251510630=48(мм) (12)
где [p]=pn – допускаемое давление на подшипник МПа;
p=245(МПа) – допускаемое давление на подшипник из АО9-2 по ГОСТ14113-78;
n=16 – коэффициент запаса;
d – диаметр подшипника мм.
Подшипник скольжения должен работать в режиме жидкостного трения поэтому между валом и подшипником необходимо обеспечить зазор для смазывающей жидкости.
е – абсолютный эксцентриситет мкм;
где =Rвала-Rподшипника – радиальный зазор мкм;
– относительный эксцентриситет;
=Rподшипника – относительный зазор;
=ρмасла=90807510-4=00681(кгмс)=0681(гсмс)=0681(П) – динамическая вязкость рабочей жидкости;
w – окружная скорость на шейке вала.
По таблице 2 (стр. 142 [6]) определяем значение безразмерной нагрузки при =06 и lD=16.
hmin=1214(1-06) = 4856(мкм).
По рекомендациям hmin = 4 8(мкм).
Момент трения в подшипнике:
Мт=05fpldп2=050008161064830210-9=484(Нм).
Потери мощности на трение в подшипнике:
А=Мт2n1020=4842314831020=0745(кВт).
Количество жидкости которое надо прокачать через подшипник для отвода тепла трения для случая подвода смазки в круговую канавку расположенную на конце подшипника определяется по формуле:
Qп=016(1+152)-=016(1+15062)-=
464-00308=02156(лмин).
Рис. 10. Подшипник скольжения (разрез).
Расчет соединительных винтов
В связи с тем что в конструкции данного насоса используется гидравлический поджим подшипников к шестерням с целью уменьшения торцевых зазоров и как следствие уменьшение утечек на крышки насоса действует давление в 16 МПа. Сила действующая на крышку:
N=рSк=16106520710-6=145796(Н).
Где р=16(МПа) – давление действующее на крышку;
Sк=520710-6(м2) – площадь крышки.
Расчетная нагрузка на винт:
Где Nз = 400Н – усилие от затяжки на 1 винте;
=075 – коэффициент для прокладки из резины;
Для креплений будем использовать винт с шестигранной головкой ГОСТ Р ИСО 4017 – М8 x 25. Его площадь поперечного сечения
[]=РiS – допускаемое напряжение при растяжении МПа.
Для крепления крышек нужно использовать 8 винтов.
Проверка кавитационного запаса
Кавитация(отлат.cavita— пустота)— процесс парообразования и последующего схлопывания пузырьков пара с одновременным конденсированием пара в потоке жидкости сопровождающийся шумом и гидравлическими ударами образование в жидкости полостей (кавитационных пузырьков или каверн) заполненныхпаромсамой жидкости. Кавитация возникает в результате местного понижения давления в жидкости которое может происходить либо при увеличении еёскорости(гидродинамическая кавитация) либо при прохождении акустической волныбольшой интенсивности во время полупериода разрежения (акустическая кавитация) существуют и другие причины возникновения эффекта. Перемещаясь с потоком в область с более высоким давлением или во время полупериода сжатия кавитационный пузырёк схлопывается излучая при этомударную волну.
Явление кавитации носит локальный характер и возникает только там где есть условия. Перемещаться в среде возникновения не может. Кавитация разрушает поверхность насоса [6].
Кавитационный запас насоса определяется по формуле:
где – давление паров жидкости при температуре t=80С МПа;
– потери давления жидкости на пути прохождения её от бака до впадин зубьев вызываемые сопротивлениями труб фильтров расходомеров и др. МПа;
= 908 удельный вес жидкости кгм3;
- высота бака над насосом м;
Fвс – площадь сечения всасывания м2;
z – число зубьев насоса;
n – частота вращения шестерен обс;
m – модуль зубьев шестерни мм;
- 000267106 - – кавитационный запас насоса.
Данный насос может работать в системах с потерями на сопротивление в подводящем трубопроводе равным 27996(МПа)
Проверочный расчет подшипников скольжения
Где р – давление в линии нагнетания МПа;
Давление действующее на подшипник:
p=P(dl)=21325(3048)=148(Нмм2)=148(МПа)
где l – длина подшипника мм.
Допускаемое давление на подшипник [p]=245(МПа) по ГОСТ14113-78.
Расчетное давление меньше допускаемого в 16 раз значит по давлению условие выполнено.
Режим нагружения подшипников pv=1482356=348688(МПамс).
Для пары трения сталь по алюминиевому сплаву допускаемый режим нагружения pv=60(МПамс).
По режиму нагружения условие выполнено т.к. расчетный режим нагружения в 17 раз меньше допускаемого режима нагружения.
Расчет зазоров. Обеспечение требуемого объемного КПД
При давлении P= 16(МПа) объемный КПД равен о=09375 это значит что подача насоса должна быть QН=09375QТ=150(лмин) а расход утечек через насос равен Qут=QТ-QН=160-150=10(лмин).
При расчете подшипника было определено что минимальный зазор =1214(мкм). Поэтому для соединения подшипник – вал назначим посадку с зазором 12(мкм) – N5h5. Максимальный зазор для этой посадки равен 30(мкм) [1].
Расход через зазор между подшипником и валом можно определить по формуле:
Qп=Dпhmax = 0753140033010-6 = 0043(лс)=26(лмин).
Соответственно на оставшиеся утечки остаётся 74(лмин).
Шероховатость торцевых поверхностей шестерни и подшипников (которые контактируют между собой) примем Ra=04(мкм). Соответственно максимальный зазор между шестерней и подшипником исходя из шероховатости h=16(мкм). Давление в насосе постепенно возрастает по мере перемещения от линии всасывания к линии нагнетания [4]. Эпюра распределения давления представлена на рис. 11.
Рис. 11. Эпюра давления в НШ.
Давление возрастает на угле φ=360-1-2=230-50-70=240о. На один зуб приходится угол равный φ1зуба=360z=2769о. Давление в насосе при переносе жидкости изменяется по закону pi=p φiφ. Значит перепад давления на одном зубе равен р1зуба=161062769240=32305(МПа).
Утечки на шестернях будут происходить по торцам и зубьям шестерен. Qш= (14)
где - коэффициент расхода;
b – ширина зубчатого венца мм;
hз – зазор между зубьями и корпусом мкм;
h – зазор между торцами мкм;
– перепад давления на зубе МПа;
= 908(кгм3) – плотность перекачиваемого масла.
Выполняя зубья шестерни по 6 степени точности максимальное отклонение от диаметрального размера головок зубьев – 19(мкм). Выполнив корпус с полем допуска JS7(+-0017) то hзmax=19+17=35(мкм).
Это значит что при заданных допусках деталей будет выдерживаться объемный КПД не менее 097.
Тонкость фильтрации жидкости
Загрязнение жидкостей различными примесями снижает надежность и срок службы гидравлических агрегатов. Механические частицы попадая в рабочую жидкость способствуют разрыву масляной пленки ухудшая режим смазки а также могут вызывать заклинивание пар трения и закупорку каналов малых сечений [4]. Поэтому принято считать фильтрацию удовлетворительной если размер капиллярных каналов фильтрующего материала не превышает половины наименьшего зазора в скользящих парах агрегата для проектируемого насоса НШ32-У hmin=16(мкм). Значит фильтр должен иметь предельный размер пор равный 08(мкм).
По ГОСТу28028-89 выбираем 7 класс чистоты жидкости при этом в гидроприводе будет производиться её фильтрация тонкими фильтрами поэтому код требования чистоты к рабочей жидкости будет выглядеть:
где 13 – класс чистоты;
– код таблицы классов промышленной чистоты;
– коэффициент измельчения.
Пульсация потока жидкости
Текущая подача жидкости шестеренным насосом носит пульсирующий характер и является периодической функцией с периодом равным =2z=04833(рад). Соответственно частота пульсаций f=zn60=325(Гц) [6].
Так как у НШ32-У одинаковые шестерни т.е. z1=z2=z=13 – число зубьев w1=w2=w=157(радс) – угловая скорость r1=r2=r=245(мм) – радиус начальной окружности h1=h2=h=367045(мм) – высота зуба.
Средняя подача рассчитывается по формуле:
(qх)ср=bw(2rh+h2-to212)=32157(2245367045+3670452-1033235212)=093(см3с).
Максимальная разница подач:
qmax==0134(см3с) (15)
Степень неравномерности подачи можно оценить коэффициентом который равен отношению разности между наибольшей и наименьшей подачами к наибольшей подаче:
Степень неравномерности уменьшается с увеличением угла зацепления и с увеличением числа зубьев.
Расчет характеристик насоса
Производительность насоса (подача насоса) – это объемный расход перекачиваемой насосом жидкости. Измеряется в м3ч или лмин.
Напор насоса – энергия сообщаемая насосом потоку жидкости отнесённая к единице веса жидкости. Измеряется в ДжН=м.
В насосах объемного действия в качестве одного из параметров характеризующих работу насоса вместо напора часто используют давление создаваемое в линии нагнетания. Измеряется в МПа.
Мощность насоса – количество энергии потребляемое насосом в единицу времени(Вт).
Полезная мощность – энергия передаваемая насосом жидкости в единицу времени (Вт).
Из вышеприведенных расчетов и данных прототипа известны:
- изменение подачи в зависимости от давления
- изменение объемного КПД
- потери на трение в узлах и гидравлическое трение принимаем постоянным и равным Nпо=198(кВт).
Табл.4. Характеристики насоса.
Nп=РнQ – полезная мощность кВт;
Где Рн – давление в линии нагнетания МПа;
Q – подача насоса лмин.
NОб=QРн – объемные потери мощности Вт;
Где Q – утечки лмин.
N=Nп+NОб+Nмех – мощность на приводном валу насоса необходимая для работы насоса кВт.
Графики характеристик насоса представлены в приложении Г.
В курсовой работе выполнен расчет шестеренного насоса НШ32-У в результате которого объемный КПД был увеличен на 174% а надежность повышена на 10%. Значит задачи поставленные при проектировании выполнены.
БИБЛИОГРАФИЧЕСКИЙ СПИСОК
Анурьев В.И. Справочник конструктора-машиностроителя. В 3 т. Т.1 и т.2: Справочник конструктора-машиностроителя В.И. Анурьев. – М.: Машиностроение 2001. – 1768 с.
Анухин В.И. Допуски и посадки. Выбор и расчет указание на чертежах: учебное пособие В.И. Анурьев. – СПБ.: Изд-во СПбГТУ 2001. – 219 с.
Барышев В.И. Объемные гидромашины. В 2 ч. Ч 2: Шестеренные гидромашины: учебное пособие по курсовому проектированию В.И. Барышев К.К. Лайко. – Ч.: ЮУрГУ 2013. – 219 с.
Башта Т.М. Объемные насосы и гидравлические двигатели гидросистем: учебник для вузов Т.М. Башта. – М.: Машиностроение 1974. – 606 с.
Устновский Е.П. Многовариантное проектирование зубчатых цилиндрических конических и червячных передач с применением ЭВМ: учебное пособие к курсовому проектированию по деталям машин Е.П. Устиновсий Ю.А. Шевцов Ю.К. Яшков. – Челябинск: ЧГТУ 1995. – 105с.
Юдин Е.М. Шестеренные насосы. Основные параметры и их расчет: учебник для вузов Е.М. Юдин. – М.: Машиностроение 1964. – 238с.
ПРИЛОЖЕНИЕ А Сборочный чертеж НШ32-У
ПРИЛОЖЕНИЕ Б Чертеж ведущего зубчатого колеса НШ32-У
ПРИЛОЖЕНИЕ В Чертеж левой втулки НШ32-У
ПРИЛОЖЕНИЕ Г Характеристики НШ32-У
НШ 32-У.cdw

Номинальное давление на выходе
Номинальная мощность
КПД при номинальном режиме
Несовпадение контуров корпусов и крышки не более 2мм.
Перед сборкой все детали продуть сжатым воздухом.
зубчатых колёс и внутреннюю поверхность
корпуса перед сборкой смазать рабочей жидкостью.
нижние и зубчатые колёса должны быть попарно одной
* Размеры для справок.
Спецификация.spw

Ведущее зубчатое колесо
Манжетные уплотнения
Правая втулка НШ32-У
Специальное уплотнение
Винт с шестигранной головкой
ГОСТ Р ИСО 4017-М8 x 40
Манжета 1.1-30 x52-1
Шайба 8 ГОСТ 6402-70
Втулка.cdw

Абразивные включения на поверхностях Ж и И не допускаются.
При изготовлении детали из бронзы поверхности Ж и И
освинцевать; толщина слоя свинца 1-3 мкм.
Зубчатое колесо1.cdw

Сталь 20Х ГОСТ 4543-71
Кромки Д скруглить R 0
Детали сортировать по размеру Е.
* Размеры обеспечиваются инструментом.
Маркировать номер группы селиквитности.
Клеймить после окончательной приёмки ОТК.
Коэффициент смещения
Нормальный исходный контур
Характеристики.cdw

Жидкость - масло ВНИИНП-401.
Кинематическая вязкость - 0
Частота вращения - 83 с
График пульсации потока
График зависимости мощности от давления
График зависимости расхода от давления
График зависимости КПД от давления