Кинематический расчет привода к транспортеру индукционной сушильной печи



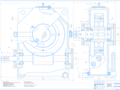
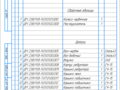
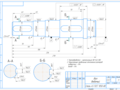
- Добавлен: 04.11.2022
- Размер: 2 MB
- Закачек: 0
Описание
Курсовой проект - Кинематический расчет привода к транспортеру индукционной сушильной печи
Состав проекта
![]() |
![]() ![]() ![]() ![]() |
![]() ![]() ![]() ![]() |
![]() ![]() ![]() |
![]() ![]() ![]() ![]() |
Дополнительная информация
DM_238_M1_b-9_01_01_00_000_SB.spw

Reduktor.cdw

Val.cdw

Рекомендуемые чертежи
- 13.04.2024
- 22.11.2015
Свободное скачивание на сегодня
- 22.08.2014
- 29.08.2014