Бетоносмесительный цех завода ЖБИ производительностью 30 тыс. м куб. в год


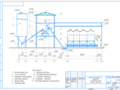
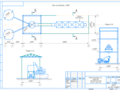
- Добавлен: 04.11.2022
- Размер: 243 KB
- Закачек: 0
Получить бесплатный доступ добавив свой материал или получить скидку оплатив сразу нескольких материалов
Подписаться на ежедневные обновления каталога:
Описание
Курсовой проект - Бетоносмесительный цех завода ЖБИ производительностью 30 тыс. м куб. в год
Состав проекта
![]() |
![]() |
![]() ![]() ![]() |
![]() ![]() ![]() |
![]() ![]() ![]() |
Дополнительная информация
Контент чертежей
БСУ Разрез.cdw
- Силос цемента 8 - Распределительная воронка
- Шнековый транспортер 9 - Скиповый подъемник
- Дозатор цемента 10 - Конвейер - дозатор
- Бункер воды 11 - Расходные бункера заполнителей
Бетоносмесительный цех
Пояснительная записка.docx
РАСЧЕТ СОСТАВОВ БЕТОНОВ7
1 Расчет состава БСТ В15 П37
2 Расчет состава БСМ В20 П29
ТЕХНОЛОГИЧЕСКОЕ ПРОЕКТИРОВАНИЕ11
1. Выбор технологической схемы производства11
2 Режим работы и фонд рабочего времени часовая производительность13
3 Определение потребности в заполнителях и вяжущих. Материальный баланс производства14
4 Смесительное отделение17
5 Дозаторное отделение19
6 Бункерное отделение22
7 Склады сырьевых материалов29
7.1 Склады цемента29
7.2 Склады заполнителей31
8 Конвейерное оборудование33
9 Бетонораздаточное отделение36
ОСНОВНЫЕ ТЕХНЕХНЕКО-ЭКОНОМИЧЕСКИЕ ХАРАКТЕРИСТИКИ БЕТОНОСМЕСИТЕЛЬНОГО ЦЕХА37
1 Расход основных и вспомогательных материалов37
2 Список оборудования цеха37
3 Список электродвигателей и расчет расхода электроэнергии38
БИБЛИОГРАФИЧЕСКИЙ СПИСОК43
Бетоносмесительный цех является одним из ведущих подразделений основного производства ЖБИ. Может выполнять такие функции как разгрузку накопление и хранение нормативного запаса сырьевых материалов на складах; подготовку сырьевых материалов подогрев заполнителей в зимнее время активацию вяжущих приготовление специальных растворов добавок и другие подготовительные операции; приготовление бетонных смесей и транспортирование их к формовочным постам технологической линии.
В состав бетоносмесительного цеха входят склады заполнителей вяжущих материалов и добавок с грузоподъемными устройствами система транспортных устройств и сооружений для внутрицехового перемещения материалов и бетоносмесительное отделение оснащенное необходимым технологическим оборудованием и размещенное в специальном производственном здании. Склады для хранения нормативного запаса заполнителей бывают различного типа и отличаются объемом способом разгрузки доставляемого на завод различными видами транспорта материала способом хранения и подачи материала в расходные бункера бетоносмесительного отделения.
Целью данного курсового проекта является разработка бетоносмесительного цеха (БСУ) завода железобетонных изделий производительностью 30 тыс. м куб. смесей в год.
- выбор материалов для приготовления бетонных смесей;
- расчет составов тяжелого и мелкозернистого бетонов;
- разработка технологической линии;
- выбор режима работы и фонда рабочего времени;
- составление ведомости расхода материалов и месячного материального
- разработка компоновки оборудования и оформление графической части.
ВЫБОР МАТЕРИАЛОВ ДЛЯ ПРИГОТОВЛЕНИЯ БЕТОННОЙ СМЕСИ
Класс цемента выбираем в зависимости от проектного класса бетона в соответствии со СНиП 82-02-95 «Федеральные (типовые) элементные нормы расхода цемента при изготовлении бетонных и железобетонных изделий и конструкций» [1]. Для бетонов БСТ В15 П3 и БСМ В20 П2 допускается использовать цемент класса 325. Плотность цемента принимаем равной 31 гсм3 (3100 кгм3).
В качестве крупного заполнителя будет использоваться серпентинитовый щебень (щебень-змеевик) фракции 20-40 мм средней плотностью 2500 кгм3 насыпной плотностью 1376 кгм3.
В качестве мелкого заполнителя для бетона принимаем серпентинитовый отсев. Содержание зерен менее 014 мм не более 10 % содержание илистых глинистых и пылевидных примесей определяется отмучиванием не должно превышать 3 %. Содержание комков глины не допускается. Ограничивается содержание органических примесей аморфного кремнезема сернистых и сернокислых соединений. Истинная плотность мелкого заполнителя 2500 кгм3. Модуль крупности 25. Насыпная плотность 1500 кгм3. Крупный и мелкий заполнитель соответствует ГОСТ 26633-2015 «Бетоны тяжелые и мелкозернистые. Технические условия» [2].
Вода соответствует ГОСТ 23732-2011 «Вода для бетонов и строительных растворов. Технические условия» [3]. Для затворения бетонной смеси может быть использована природная или водопроводная вода не содержащая солей кислот и органических примесей выше допустимых норм.
РАСЧЕТ СОСТАВОВ БЕТОНОВ
Состав бетона выражается в виде расхода составляющих материалов по массе на 1 м3 бетона.
Расчет состава бетона призван обеспечить заданные показатели свойств бетонной смеси и готового бетона при наименьшей стоимости материалов и наименьших производственных затратах с учетом технологических режимов изготовления железобетонных изделий.
1 Расчет состава БСТ В15 П3
Состав тяжелого бетона рассчитываем в следующем порядке.
Определяем водоцементное отношение по формуле 2.1.
ВЦ = АRц (Rб + А05 Rц)
где Rц – класс прочности или активность цемента МПа;
Rб – класс прочности бетона МПа;
А – коэффициент учитывающий качество заполнителя принимаем А = 06 (рядовой) в соответствии с методическими указаниями «Проектирование бетоносмесительного цеха» [4].
ВЦ = 06325 (15 + 0605 325) = 08
Определяем расход воды по таблице 6 методических указаний «Проектирование бетоносмесительного цеха».
Для бетона класса В15 при максимальной крупности щебня 40 мм и подвижности смеси П3 расход воды составит В = 200 лм3.
Определяем расход цемента по формуле 2.2.
Ц = 20008 = 27174 кгм3
Определяем расход заполнителей по методу абсолютных объемов.
Расход крупного заполнителя рассчитываем по формуле 2.3.
Расход мелкого заполнителя рассчитываем по формуле 2.4.
где VПЩ – пустотность щебня которую определяем по формуле 2.5;
α – коэффициент раздвижки зерен щебня который рассчитываем интерполяцией значений таблицы 8 методических указаний [4] α = 142;
γЩ – насыпная плотность щебня кгм3;
ρЩ; ρП; ρЦ; ρВ – плотность цемента песка щебня воды кгм3;
Ц В П Щ – расходы цемента воды песка щебня кгм3.
VПЩ = 1 – (13762500) = 039.
Расход материалов на 1 м3 бетонной смеси БСТ В15 П3 представлен втаблице 2.1.
Таблица 2.1 – Расход материалов на 1 м3 бетонной смеси БСТ В15 П3
Расчетная плотность бетонной смеси
2 Расчет состава БСМ В20 П2
Определяем водоцементное отношение по формуле 2.6.
ВЦ = АRц (Rб + А08Rц)
где А – коэффициент учитывающий качество заполнителя принимаем А=075 (для материалов среднего качества).
ВЦ = 075325 (20 + 07508325) = 062.
Соотношение между количеством цемента и мелкого заполнителя обеспечивающее требуемую подвижность определяем по рисунку 1 методических указаний [4]:
Расход цемента определяем по формуле 2.7.
где n – отношение между количеством песка и цемента равное 4.
Расход воды рассчитываем по формуле 2.8.
В = 39683 062 = 24603 лм3.
Расход мелкого заполнителя рассчитываем по формуле 2.9.
П = 4 39683 = 158732 кгм3.
Расход материалов на 1 м3 бетонной смеси БСМ В20 П2 представлен в таблице 2.2.
Таблица 2.2 – Расход материалов на 1 м3 бетонной смеси БСМ В20 П2
ТЕХНОЛОГИЧЕСКОЕ ПРОЕКТИРОВАНИЕ
При выборе технологического оборудования прежде всего разрабатывается оптимальная технологическая схема производства на основе тщательного изучения современных освоенных а также осваиваемых методов изготовления (производства) тех или иных материалов. Далее устанавливают плановый фонд рабочего времени оборудования разрабатывают производственную программу и определяют необходимую часовую производительность оборудования по которой его и выбирают. Затем рассчитывают потребность в сырьевых материалах т. е. составляют материальный баланс производства [4].
1. Выбор технологической схемы производства
Под технологическим процессом принято подразумевать последовательную совокупность технологических операций приводящую к изменению формы или состояния материала либо изделия (полуфабриката) в целях получения из него материала или изделия необходимого вида и качества.
Технологическая схема – есть графическое изображение последовательности производственных операций
В настоящее время используются две технологические схемы производства бетонных смесей: одно- и двухступенчатая.
Выбираем двухступенчатую технологическую схему производства бетона (рисунок 3.1).
Двухступенчатая схема характеризуется двукратным подъемом материалов. Дополнительный подъем происходит при передаче материала от дозаторов в бетоносмесители. это позволяет уменьшить высоту производственного здания однако усложняет технологический процесс.
Рисунок 3.1 – Технологическая схема производства
При двухступенчатой схеме весь процесс приготовления смеси разбивается на две ступени. В первой ступени обычно предусматривают дозирование заполнителей с получением сухой смеси. Далее эта смесь транспортируется (поднимается) на вторую ступень где расположены бетоносмесители и осуществляется перемешивание и выдача бетонной смеси.
2 Режим работы и фонд рабочего времени часовая производительность
Режим работы бетоносмесительного цеха с двумя выходными днями принимаем следующим:
- количество рабочих суток в году – 260;
- количество рабочих суток в году с учетом плановых остановок на ремонт: 253 (согласно ОНТП 07-85 [5] для цехов и установок по приготовлению бетона и раствора длительность плановых остановок на ремонты 7 суток);
- количество рабочих суток по выгрузке сырья и материалов с автомобильного транспорта – 260;
- количество рабочих смен в сутки – 2;
- продолжительность рабочей смены – 8 ч.
- количество рабочих часов в году – 2024.
Производительность бетоносмесительных и растворосмесительных цехов (отделений установок) рассчитывается по максимальной часовой потребности.
где Qч – часовая производительность м3;
К2 – коэффициент обеспечивающий запас (резерв) производительности 20% К2 = 12;
m – число рабочих часов в сутки;
n – число рабочих дней в году;
К1 – коэффициент неравномерности выдачи бетонной (растворной) смеси К1= 08;
Pб – проектная производственная мощность м3.
3 Определение потребности в заполнителях и вяжущих. Материальный баланс производства
Годовой расход сырьевых материалов рассчитывают исходя из количества заданных видов бетонных и растворных смесей по результатам расчетов их составов выполненных ранее. Расход каждого материала на 1 м3 смеси умножается на заданный годовой объем выпуска.
Годовой объем смесей определяют с учетом их безвозвратных потерь при транспортировании которые принимаются 05 % [4] (формула 3.2).
где Vг – годовой объем м3;
Q – производительность бетоносмесительного узла м3год.
Vг = 30000 + (30000 05)100 = 30150 (м3)
Таблица 3.1 – Годовая производительность (с учетом потерь бетонной смеси) по отдельным маркам бетона и раствора
Объем бетонной смеси
Часовая производительность бетоносмесительного цеха для БСТ В15 П3 по формуле (3.1) равна:
Затем считают практический расход сырьевых материалов с учетом производственных потерь по формуле (3.3):
МП = МТ (100 (100 – П))
где П – производственные потери для заполнителей принимаются 2 % для цемента – 1 %.
Далее рассчитывается практический расход материалов (заполнителей) в состоянии естественной влажности по формуле (3.4):
МПW = МП (100 (100 – W))
где W – влажность материала принимаемая для щебня – 4 % для отсева – 3%.
Результаты расчета сырьевых материалов представлены в таблице 3.2.
Таблица 3.2 – Результаты расчета расхода сырьевых материалов
Далее составляется материальный баланс производства бетонных и растворных смесей (таблица 3.3) и ведомость расхода сырьевых материалов (таблица 3.4).
Таблица 3.3 – Материальный баланс производства
Поступило на предприятие
Отпущено с предприятия
Крупный заполнитель
Потери технологические 05%
Потери при транспортировке и хранении:
Крупный заполнитель 13 %
Таблица 3.4 – Ведомость расхода сырьевых материалов
Требуемый годовой объем бетона
Расход компонента кгм3
Расход компонентов т
4 Смесительное отделение
Для двухступенчатых установок «товарного бетона» (подвижные смеси для тяжелого бетона) выбирается один бетоносмеситель гравитационного или принудительного действия минимального объема обеспечивающего проектную мощность.
Выбираем смесители и определяем их производительность.
Для всех типов бетонов выбираем бетоносмеситель принудительного действия с вертикально расположенными смесительными валами (тарельчатый) СБ-146А с объемом смесительного барабана 075 м3. Технические характеристики данного бетоносмесителя приведены в таблице 3.5.
Таблица 3.5 – Технические характеристики бетоносмесителя СБ-146А
Объем готового замеса л
Вместимость по загрузке л
Число циклов в 1 ч при приготовление:
Наибольшая крупность заполнителя мм
Частота вращения рабочего органа обмин
Мощность двигателя кВт
После выбора конкретного смесителя проверяется его производительность по формуле (3.5):
где V – объем смесительного барабана (вместимость по загрузке) м3;
n – число замесов в час;
– коэффициент выхода бетонной смеси по нормам технологического проектирования примерно равен 067 для тяжелого и конструкционного бетона;
КИ – коэффициент использования во времени в час (КИ = 091).
Число замесов в час определяют по формуле (3.6):
n = 3600 (t1 + t2 + t3)
где t1 –время загрузки принимаем 20 с;
t2 – продолжительность перемешивания по таблице 19 методических указаний [4] принимаем равное 50 с;
t3 – время разгрузки принимаем 30 с.
n = 3600 (20 + 50 + 30) = 36.
QСМ. Ч = 075 36 067 091 = 1646 м3ч.
Рассчитываем количество бетоносмесителей по формуле (3.7):
где Qч – часовая производительность бетоносмесительного цеха определенная по формуле (3.1);
Qсм. ч – производительность бетоносмесителя определенная по формуле (3.5).
На основе расчетов принимаем 1 бетоносмеситель.
5 Дозаторное отделение
Для выбора дозатора необходимо рассчитать объем мерника подобрать затвор и тензодатчики.
Объем мерника считается на максимально возможное количество компонента идущего на один замес бетоносмесителя (руководствуясь номенклатурой составов бетонных и растворных смесей и учитывая запас 10–15 %). Затем подбирают конфигурацию и размеры мерника и выбирается затвор. После этого определяют тип и марку тензодатчиков [4].
Расход материалов на один замес находим исходя из того что объем готового замеса для бетоносмесителя СБ-146А равен 05 м3 расчет представлен в таблице 3.6.
Таблица 3.6 – Расход материалов на один замес
Результаты выбора дозатора приведены в таблице 3.7
Таблица 3.7 – Выбор дозирующего устройства
Пределы взвешивания кг на один замес
дозируемого материала в рыхлом состоянии м3
Объем мерника с учетом запаса м3
дозирующего конвейера в случае если дозировка заполнителей производится им
Дисковый затвор V2FS200SN
6 Бункерное отделение
Расходные бункера БСУ проектируются так чтобы они могли содержать необходимые для приготовления бетонной смеси материалы на 2–4 часа работы. Как правило запас материалов в расходных бункерах принимают равным: для заполнителей на 1–2 часа для цемента 2–3 часа. Количество бункеров или их отсеков назначается при разработке технологической схемы производства и зависит от номенклатуры смесей производительности линии выбора компоновки БСУ (одно- двухступенчатая и др.). Обычно их количество принимается не менее двух для каждого вида материалов. Расходные бункера располагаются над дозаторами и снабжены затворами на выпускных отверстиях.
Объем бункеров для заполнителей подсчитывается по необходимой массе заполнителей и известной или определенной опытным путем их насыпной плотности. При этом насыпную плотность песка следует принимать наименьшей по соответствующей влажности.
Для ориентировочных расчетов насыпная плотность влажного песка может приниматься равной 1500 щебня – 1350 кгм3.
Порядок расчета бункера с верхней призматической частью.
Определим объем бункера по формуле (3.8):
где W – количество расходуемого материала кгч;
t – время на которое запасается материал ч;
K – коэффициент перехода от полезного к геометрическому объему К = 110-115;
γ – насыпная плотность материала с естественной влажностью кгм3 [4].
Результаты расчета объема бункеров для БСТ В15 П3:
- объем бункера для щебня:
- объем бункера для отсева:
- объем бункера для воды:
Результаты расчета объема бункеров для БСМ В20 П2:
Определим геометрические размеры бункера методом подбора. Высота бункера как правило не должна превышать 6-8 м. Объем верхней призматической части бункера рассчитывается по формуле (3.9):
где Sпр – площадь призматической части бункера в плане;
hпр – высота призматической части бункера.
Объем нижней части бункера рассчитывается по формуле (3.10):
где F – площадь выходного отверстия;
hн – высота нижней части бункера.
При расчете должны соблюдаться условия (3.11) (3.12) и (3.13):
где a и b – размеры бункера в плане причем наибольший размер не должен превышать 5 м (для одноступенчатых БСУ).
Необходим бункер для щебня с объемом не менее 704 м3.
a = 2 м b = 2 м F = 025 м hпр = 2 м hн = 1 м. Тогда:
- площадь призматической части по формуле (3.13):
- объем верхней призматической части бункера по формуле (3.9):
-объем нижней части бункера по формуле (3.10):
- общий объем бункера по формуле (3.11):
4 м3 ≤ 1013 м3 геометрические размеры бункера соответствуют требуемым.
На случай экстренных ситуаций установим 2 бункера объемом 1013 м3.
Необходим бункер для отсева с объемом не менее 1374 м3 принимаем:
a = 2 м b = 25 м F = 025 м hпр = 2 м hн = 1 м. Тогда:
74 м3 ≤ 1263 м3 так как геометрические размеры бункера не соответствуют требуемым устанавливаем два бункера объемом 1263 м3.
Далее рассчитываем бак для воды с объемом не менее 391 м3.
a = 2 м b = 15 м F = 025 м hпр = 1 м hн = 07 м. Тогда:
м3 ≤ 391 м3 геометрические размеры бака соответствуют требуемым.
Итого: 4 бункера: 2 бункера для щебня с объемами 825 м3 1 бункер для отсева объемом 1625 м3 1 бункер для воды объемом 414 м3.
Далее подбираем затворы выпускного отверстия для бункеров. Все результаты представлены в таблице 3.8.
Таблица 3.8 – Расходные бункера
Часовой расход в состоянии естественной влажности кг
Оперативный запас материала ч
Масса материала обеспечивающая оперативный запас кг
Требуемый объем бункера м3
Геометрический объем одного бункера м3
Затвор челюстной 3Ч-500х500-МР
шиберный Затвор дисковый Water Тechnics BVGR WT Ду500
7 Склады сырьевых материалов
Для бесперебойной работы предприятия в течение всего года в любых погодных условиях должен быть предусмотрен запас сырьевых материалов. Для хранения этих материалов на предприятиях создаются склады. Складское хозяйство должно обеспечивать механизированную приемку качественное складирование рациональное хранение и выдачу сырьевых материалов представляющих собой значительную материальную ценность.
Расчет склада цемента сводится к определению объемов и размеров силосов.
Запас цемента требуемый для выполнения производственной программы БСУ рассчитывают по формуле (3.14):
где Пг – годовая производительность БСУ по базовой смеси м3;
Ц1 – средний расход цемента на 1 м3 базовой смеси т;
Зц – запас цемента сут.;
К – коэффициент учитывающий потери цемента при разгрузке и транспортных операциях (К = 101);
– коэффициент заполнения силоса;
Р – расчетный годовой фонд рабочего времени сут.
Общий запас цемента:
Ц = 73 + 159 = 232 т.
Выбираем 2 силоса SP 110 (рисунок 3.1) каждый вместимостью 138 т и объемом 110 м3. Основные характеристики данного силоса представлены в таблице 3.9.
Рисунок 3.1 – Базовая комплектация панельного силоса SP 110
Таблица 3.9 – Основные характеристики панельного силоса SP 110
Объем хранения материала
Высота силоса без ограждений
Высота цилиндрической части
Высота конической части
Угол наклона конусной части
Высота а которой находится выходной фланец силоса
Размеры инспекционного люка на крыше
Максимальная масса цемента для хранения
7.2 Склады заполнителей
Емкость склада заполнителей рассчитывается по формуле (3.15):
где Qсут – суточный расход материалов м3;
Тхр – норма запаса хранения материалов сут.;
– коэффициент разрыхления;
13 – коэффициент учитывающий потери при транспортировке.
Расчет склада для щебня:
- суточный расход материалов Qсут = 66110 1376 = 4805 м3;
- емкость склада по формуле (3.15):
Расчет склада для отсева:
- суточный расход материалов Qсут = 1434601500 = 9564 м3;
Емкость слада заполнителей:
После определения емкости склада выбирают его тип в зависимости от климатических условий района и определяют площадь склада. По типу емкостей склады делятся на штабельные бункерные полубункерные штабельно-полубункерные силосные.
Выбираем открытый штабельный склад.
Длина открытого штабельного склада при угле естественного откоса заполнителей α подсчитывается по формуле (3.16):
где V – емкость склада заполнителей м3;
h – высота штабеля принимаем 6 м;
α – угол естественного откоса заполнителей (α = 40°);
K3 – коэффициент учитывающий полноту заполнения склада K3 = 115–125.
Полезная площадь штабельного склада определяется по формуле (3.17):
8 Конвейерное оборудование
Средняя теоретическая производительность горизонтального конвейера тч:
- для плоской ленты при перемещении сыпучего груза по формуле (3.18):
- для желобчатой ленты при перемещении сыпучего груза по формуле (3.19):
- для желобчатой ленты при перемещении бетонной смеси по формуле (3.20):
где B – ширина ленты м;
v – скорость движения ленты мс;
γ – насыпная плотность транспортируемого груза.
В соответствии с технологической схемой для инертных материалов выбираем конвейер-дозатор марки КД-2500 с плоской лентой для перемещения груза. Технологические характеристики данного конвейера:
- ширина ленты B = 08 м;
- скорость движения ленты v = 25 мс;
- насыпная плотность транспортируемого груза: для щебня γ = 1376 кгм3; для отсева γ = 1500 кгм3.
Теоретическая производительность горизонтального конвейера с плоской лентой при перемещении щебня согласно формуле (3.18) равна:
Теоретическая производительность горизонтального конвейера с плоской лентой при перемещении отсева согласно формуле (3.18) равна:
Основную мощность привода на валу барабана определяется по формуле (3.21):
где Пр – производительность конвейера тч;
H – разность уровней концевых барабанов конвейера м применяемое со знаком «+» при подъеме и со знаком «-» при спуске;
– удельное сопротивление движения ленты;
L – длина конвейера м;
k – коэффициент зависящий от массы ленты и роликоопор;
v – скорость ленты мс.
Характеристики данного конвейера:
- производительность конвейера Пр = 270 тч;
- разность уровней концевых барабанов конвейера м применяемое со знаком «+» при подъеме и со знаком «-» при спуске H = 0;
- удельное сопротивление движения ленты = 004;
- длина конвейера L = 100 м;
- коэффициент зависящий от массы ленты и роликоопор k = 7000;
- скорость ленты v = 25 мс.
При длине ленточного конвейера меньше 30 и больше 400 м вводят поправочные коэффициенты к мощности которые изменяются от 105 до 12. Следовательно
Мощность двигателя определяется по формуле (3.22):
где – КПД привода зависит от конструкции передаточного механизма и может изменяться от 08-09.
Так как в данной технологической схеме используется ленточный горизонтальный конвейер-дозатор необходимо использовать скиповый подъемник. Выбираем Скип-600 технологические характеристики которого приведены в таблице 3.10.
Таблица 3.10 – Технологические характеристики скипового подъемника Скип-600
Мощность эл. дв. кВт
Скорость подъемника мс
При использовании скипового подъемника необходимо использовать воронку для перемещения компонентов в бетоносмеситель для того чтобы исключить потери материалов. Принимаем размеры воронки: D = 10 м; Н = 15 м и d = 025 м.
9 Бетонораздаточное отделение
Доставка бетонной смеси от бетоносмесительного цеха к постам формования может осуществляться с помощью бадей самоходных бункеров автосамосвалов автобетоносмесителей автобетоновозов бетононасосов конвейеров и т. д.
Выбираем автобетоносмеситель КамАЗ 581453 технические характеристики которого представлены в таблице 3.11.
Таблица 3.11 – Технические характеристики автобетоносмесителя КамАЗ 581453
Тип базового автомобиля
Объем перевозимой смеси м3
ОСНОВНЫЕ ТЕХНЕХНЕКО-ЭКОНОМИЧЕСКИЕ ХАРАКТЕРИСТИКИ БЕТОНОСМЕСИТЕЛЬНОГО ЦЕХА
1 Расход основных и вспомогательных материалов
Расход основных и вспомогательных материалов представлен в таблице 4.1.
Таблица 4.1 – Расход основных и вспомогательных материалов
Технологическая вода
2 Список оборудования цеха
Список оборудования цеха представлен в таблице 4.2
Таблица 4.2 – Список оборудования цеха
Наименование характеристика оборудования
Масса 1или комплекта
Бетоносмеситель СБ-146А
Дозатор для цемента ДЦ-400
Дозатор для воды ДВ-300
Конвейер-дозатор КД-2500
Скиповый подъемник Скип-600
Бункер для заполнителей
Цементный силос SP 110
Шнековый транспортер
Автобетоносмеситель КамАЗ 581453
3 Список электродвигателей и расчет расхода электроэнергии
Список электродвигателей представлен в таблице 4.3.
Штаты цеха представлены в таблице 4.4.
Таблица 4.3 – Список электродвигателей
Наименование проводимого механизма
Мощность устанавливаемого электродвигателя кВт
Суммарная мощность установленных механизмов кВт:
Суммарная потребляемая мощность электродвигателей работающих механизмов кВт
Фактическое время работы механизмов чгод
Количество расходуемой электроэнергии в год
Таблица 3.4 – Штаты цеха
Количество рабочих данной должности и разряда на смене
Бетоносмесительный цех:
- оператор бетоносмесителей и дозаторов
- оператор расходных бункеров
Складское хозяйство:
- моторист разгрузочной машины
- моторист на конвейере
Основой для выполнения графической части является ранее разработанная и уточненная в процессе проведения расчетов часовой производительности оборудования технологическая схема.
Цель графической части – скомпоновать (расположить в пространстве) основное технологическое оборудование линии связать его в единую технологическую цепь и задать его координаты («привязать»).
В конце курсового проекта находятся чертежи которые выполнены на двух листах формата(план и разрезы БСУ) в компьютерном графическом редакторе. На чертежах изображено здание БСУ с размещенным в нем основным технологическим оборудованием показаны координационные оси здания основные строительные размеры и вертикальные отметки нанесены монтажные и габаритные размеры основного технологического оборудования и его привязки. Основное оборудование обозначено позициями и составлена его спецификация.1:100.
При выполнении данного курсового проекта был запроектирован бетоносмесительный цех завода железобетонных изделий производительностью 30 тыс. м3 смесей в год.
Для дозирования компонентов в бетоносмеситель были подобраны современные тензодатчики учитывая пределы их измерения и расход компонентов. Бункерное отделение было запроектировано таким образом что инертные материалы дозируются и транспортируются на скиповый подъемник при помощи конвейера-дозатора. Скиповый подъемник доставляет материалы к разделительной воронке которая направляет их в бетоносмеситель для получения нужной бетонной смеси. Конвейер был рассчитан для обеспечения необходимой производительности по транспортировке материалов.
Кроме того был подобран режим работы предприятия который будет обеспечивать выполнение производственной программы. В заключение также были подобраны штаты цеха которые будут задействованы в процессе производства.
БИБЛИОГРАФИЧЕСКИЙ СПИСОК
СНиП 82-02-95 Федеральные (типовые) элементные нормы расхода цемента при изготовлении бетонных и железобетонных изделий и конструкций Минстроя России. – М.: 1996. – 40 с.;
ГОСТ 26633-2015 Бетоны тяжелые и мелкозернистые. Технические условия. – Введ. 2016-09-01. – М.: Росстандарт 2017 – 30 с.;
ГОСТ 23732-2011 Вода для бетонов и строительных растворов. Технические
условия. – Введ. 2012-10-01. – М.: Стандартинформ 2012. – 35 с.;
Беднягин С.В. Проектирование бетоносмесительных цехов предприятий по
производству бетонных и железобетонных изделий и конструкций: учеб. пособие С.В. Беднягин Е.С. Герасимова. – Екатеринбург: УрФУ 2019. – 95 с.;
Общесоюзные нормы технологического проектирования предприятий сборного железобетона ОНТП-07-85 Минстройматериалов СССР. – М.: Стройиздат 1986. – 51 с.;
СНиП 3.09.01-85 Производство сборных железобетонных конструкций и изделий Госстрой СССР. – М.: 1985. – 40 с.;
Гершберг О.А. Технология бетонных и железобетонных изделий О.А. Гершберг. – М.: Стройиздат 197. – 360 с.
Рекомендуемые чертежи
Свободное скачивание на сегодня
Обновление через: 3 часа 2 минуты