Механизм двухцилиндрового двигателя




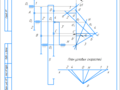
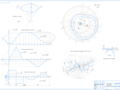
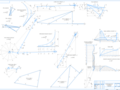
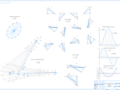
- Добавлен: 24.01.2023
- Размер: 673 KB
- Закачек: 0
Описание
Состав проекта
![]() |
![]() |
![]() ![]() ![]() ![]() |
![]() ![]() ![]() ![]() |
![]() ![]() ![]() ![]() |
![]() ![]() ![]() |
![]() ![]() ![]() ![]() |
Дополнительная информация
лист1.cdw

Диаграмма перемещений точки В
Диаграмма скоростей точки В
Диаграмма ускорений точки В
Схема и план положений механизма
Лист 1. Кинематический
лист2.cdw

План сил звеньев 4 и 5
Силовой анализ звеньев 4 и 5
Силовой анализ звена 1
План положения механизма
Индикаторная диаграмма поршня 5
Индикаторная диаграмма
План сил звеньев 2 и 3
Силовой анализ звеньев 2 и 3
График приведнных моментов сил
Диаграмма приращения кинетической энергии
лист3.cdw

Диаграмма аналогов ускорений
Диаграмма аналогов скоростей
Диаграмма удельных скольжений
и зубчатого механизмов
Диаграмма перемещений толкателя
№1964.doc
Ключевые слова: механизм структурная группа кинематическая пара звено план скоростей и ускорений сила.
Цель курсового проекта: приобретение практических навыков по кинематическому анализу и синтезу плоских рычажных кулачковых и зубчатых механизмов.
Методы проведения исследования: аналитический графический графологический.
В данном проекте определены структурные кинематические и динамические характеристики рычажного механизма спроектированы кулачковый и зубчатый механизмы по заданным условиям.
Пояснительная записка
исследование механизма
исследование механизма.
кулачкового и зубчатого
СТРУКТУРНЫЙ АНАЛИЗ МЕХАНИЗМА
КИНЕМАТИЧЕСКОЕ ИССЛЕДОВАНИЕ МЕХАНИЗМА
1 Построение плана положений механизма
2 Построение планов скоростей
3 Построение годографа скоростей точки S2
4 Построение планов ускорений
5 Построение кинематических диаграмм для точки D
КИНЕТОСТАТИЧЕСКОЕ ИССЛЕДОВАНИЕ МЕХАНИЗМА. ИССЛЕДОВАНИЕ ДВИЖЕНИЯ МЕХАНИЗМА
1 Определение моментов и сил действующих на звенья механизма
2 Силовой расчет группы состоящей из звеньев 4 и 5
3 Силовой расчет группы состоящей из звеньев 2 и 3
4 Силовой расчет начального звена
5 Расчет уравновешивающей силы по методу Н.Е. Жуковского
6 Определение мгновенного механического коэффициента полезного действия
7 Исследование движения механизма и определение момента инерции маховика
8 Определение приведенного момента инерции механизма
ПРОЕКТИРОВАНИЕ КУЛАЧКОВОГО МЕХАНИЗМА
1 построение диаграммы движения толкателя
2 Построение профиля кулачка с поступательно движущимся толкателем
ПРОЕКТИРОВАНИЕ ЭВОЛЬВЕНТНОГО ЗАЦЕПЛЕНИЯ ПРЯМОЗУБЫХ ЦИЛИНДРИЧЕСКИХ КОЛЕС
ПРОЕКТИРОВАНИЕ ЗУБЧАТОГО МЕХАНИЗМА
1 Аналитический метод
Создание современной машины требует от конструктора всестороннего анализа ее проекта. Конструкция должна удовлетворять многочисленным требованиям некоторые из которых могут находиться в противоречии. Например минимальная динамическая нагруженность должна сочетаться с быстроходностью достаточная надежность и долговечность должны обеспечиваться при минимальных габаритах и массе. Расходы на изготовление должны быть минимальны но обеспечивающими достижение заданных параметров.
Многовариантный характер инженерных решений в процессе конструирования требует достаточной детальной разработки методов расчета и методов принятия и реализации оптимальных решений. Вопросы синтеза структурной и кинематической схем механизмов компоновки механизма и согласования движения силовой анализ механизма определение закона движения механизма обусловленными заданными силами оценка виброзащиты и виброактивности механизмов управление движением и ряд других вопросов изучается в дисциплине «Теория механизмов и машин».
В конструкторской подготовке инженеров особое место отводится вопросам технологичности проектируемых машин. Конструктивные решения должны подчиняться требованиям технологических процессов изготовления и сборки обеспечения минимума производственных затрат при заданных параметрах и показателях эффективности проектируемой машины. Изделие достаточно технологичное в единичном производстве может быть малотехнологичным в массовом производстве и совершенно нетехнологичным в поточно-автоматизированном производстве.
Основная цель курсового проектирования – привить навыки использования общих методов проектирования и исследования механизмов для создания конкретных машин и приборов разнообразного назначения.
Курсовое проектирование ставит задачи усвоения студентами определенных методик и навыков работы по следующим основным направлениям:
- оценка соответствия структурной схемы механизма основным условиям работы машины.
- проектирование структурной и кинематической схем рычажного механизма по заданным условиям.
- анализ режима движения механизма при действии заданных сил.
- силовой анализ механизма с учетом геометрии масс звеньев.
- проектирование зубчатых планетарных механизмов.
- расчет оптимальных геометрий зубчатых зацеплений.
- разработка циклограмм и тактограмм для систем управления механизмами.
- защита механизмов от механических колебаний определение мощности и выбора типа двигателя.
Структурный анализ механизма
Число степеней свободы механизма W определяем по формуле академика П.Л. Чебышева:
n — число подвижных звеньев механизма
p5 — число кинематических пар пятого класса
p4 — число кинематических пар четвертого класса
В исследуемом механизме n = 5 р5 = 7 [O(01) A1(12) В1(23) B2(30) А2(14) С1(45) С2(50)] р4 = 0.
Следовательно исследуемый механизм имеет одну обобщенную координату: угол поворота начального звена.
Установим класс механизма который определяется наивысшим классом группы Ассура входящим в его состав. Отделение структурных групп начинаем с группы наиболее удаленной от начального звена. В данном механизме наиболее удалена от кривошипа группа второго класса второго вида со звеньями 4 и 5.
Затем отделяем группу второго класса второго вида со звеньями 2 и 3.
В результате остается механизм первого класса в состав которого входит начальное звено 1 и стойка 0.
Формула строения механизма имеет вид:
Таким образом данный механизм относится ко второму классу.
Кинематическое исследование механизма
1 Построение плана положений
Принимаем масштабный коэффициент построения
Зная величину отношения длины шатуна к длине кривошипа определим длину шатунов:
Определяем длину отрезков
Последовательность построения - по формуле строения механизма. Сначала показываем неподвижные элементы стойки: центр O кривошипа оси поршней.
Далее вычерчивается кинематическая схема механизма. На траектории точки В ползуна 3 находим ее крайние положения. Для этого из точки О радиусом делаем одну засечку на траектории движения ползуна и определяем правое крайнее положение а радиусом — другую засечку — левое крайнее положение.
Точки В0 и В6 будут крайними положениями ползуна 3. За нулевое положение механизма принимаем крайнее верхнее положение. Начиная от нулевого положения кривошипа делим траекторию точки А (окружность) на 12 равных частей и в сторону направления вращения обозначаем их A0 A1 A2 A11. Методом засечек находим соответствующие положения остальных точек и звеньев механизма. Для каждого положения механизма находим положения центров масс S2 и S4 соединив последовательно точки S во всех положениях звеньев плавной кривой получим траектории движения центров масс звеньев 2 и 4.
Положение механизма заданное для силового расчета вычерчиваем основными линиями и считаем его расчетным (в нашем случае 10-е положение).
Определение скоростей точек звеньев механизма производим методом планов в последовательности определяемой формулой строения механизма.
Вначале определяем линейную скорость точки А начального звена
— угловая скорость начального звена ОА
— частота вращения начального звена ОА
Подставляем числовые значения в формулы
Скорость точки А будет одинаковой для всех положений механизма.
Принимаем масштабный коэффициент плана аналогов v =025 . Тогда отрезки плана будут равны
Так как вектор аналога скорости при вращательном движении то из выбранного полюса p проводим отрезок в сторону 1.
Определяем аналог скорости точки В поршня 3 по следующим векторным уравнениям:
Где (оси движения поршня 3)
Векторные уравнения решаем графически проведя из точки a направление а из точки которая совпадает с полюсом как неподвижная направление .На пересечении этих направлений получается точка b и отрезок pb изображает в масштабе аналог линейной скорости .
Точка S2 шатуна строится на отрезке ab плана по свойству подобия отложив отрезок
Определяем аналог скорости точки С поршня по следующим векторным уравнениям:
Где (оси движения поршня 5).
Графически решая векторные уравнения получаем на плане аналогов точку с.
Точку S4 шатуна С получаем аналогично точке S2.
Замеряем отрезки планов аналогов pb pc ps2 ps4 ab ac и рассчитываем величины аналогов скоростей точек и звеньев. Результаты измерений отрезков аналогов скоростей для 12-ти планов приведены в табл. 2.1.
Для расчетного положения № 10:
Из построенного плана скоростей вычисляем абсолютные скорости точек:
Относительные скорости:
Результаты расчетов аналогов скоростей для 12-ти планов приведены в табл. 2.2.
3Построение годографа скоростей точки S2
Построение годографа скоростей точки S2 производится в такой последовательности:
— на свободном поле чертежа отмечается полюс р
— методом параллельного переноса сносим векторы скоростей выбранного центра масс S2 совмещая их начало с полюсом годографа
— соединяем концы векторов плавной кривой
4Построение планов ускорений
Построение начинаем от входного звена 1 определением ускорения точки A кривошипа.
При постоянной угловой скорости начального звена ОА точка А имеет только нормальное ускорение:
Где – нормальное ускорение;
Выбираем масштабный коэффициент вычисляем отрезок изображающий ускорение точки A :
Из полюса плана ускорений откладываем отрезок параллельный OA.
Теперь построим план ускорений группы образованной звеньями 23.
Ускорение точки В группы находится графически из системы векторных уравнений:
Где и – нормальное и тангенциальное ускорения точки В при вращательном движении звена 2 относительно точки A .
— ускорение точки В0 направляющей Оx;
- относительное ускорение точки В по отношению к точке В0.
Нормальное ускорение точки В относительно точки A:
Находим отрезок изображающий :
Через точку n1 проводим прямую в направлении вектора тангенциального ускорения перпендикулярно звену АВ.
В соответствии со вторым уравнением через полюс проводим прямую в направлении ускорения параллельно составляющей Ox.
По правилу сложения векторов и соединяем на плане ускорений точки a и b и получим вектор полного ускорения точки В относительно A.
Точку центра масс шатуна 2 строим на плане ускорений по свойству подобия замерив отрезок ab=73 мм и рассчитав отрезок :
Далее рассмотрим ускорение точек звеньев группы образованной звеньями 4 и 5.
Ускорение точки С группы находится графически из системы векторных уравнений:
Где и – нормальное и тангенциальное ускорения точки С при вращательном движении звена 4 относительно точки С .
— ускорение точки С0 направляющей Оy;
- относительное ускорение точки С по отношению к точке С0.
Нормальное ускорение точки С относительно точки А:
Через точку n2 проводим прямую в направлении вектора тангенциального ускорения перпендикулярно звену АС.
В соответствии со вторым уравнением через полюс проводим прямую в направлении ускорения параллельно составляющей Oy.
По правилу сложения векторов и соединяем на плане ускорений точки а и с и получим вектор полного ускорения точки С относительно А.
Точку центра масс шатуна 4 строим на плане ускорений по свойству подобия замерив отрезок ас=434 мм и рассчитав отрезок :
Из построенного плана ускорений вычисляем:
26 * 40 = 4504 ммс2
Полные ускорения точек В и C
Тангенциальные составляющие относительных ускорений звеньев 2 и 4
Угловые ускорения звеньев 2 и 4
Направление и получают путем помещения векторов и в точку A. Тогда поворот звеньев 2 и 4 под действием этих векторов вокруг точки A является направлением вращения и .
Аналогичные построения проводим для второго заданного положения 3.
Результаты расчетов ускорений приведены в табл. 2.3.
5Построение кинематических диаграмм для точки В
5.1Диаграмма перемещений
На оси абсцисс откладываем отрезок l изображающий время одного оборота кривошипа и делим его на 12 равных частей а в соответствующих точках откладываем перемещения точки В от начала отсчета из плана положений механизма.
Масштаб по оси ординат определяется как
Масштаб по оси абсцисс определим по формуле
5.2 Диаграмма скоростей
Диаграмма скоростей точки В строится по данным планов скоростей путем переноса длин векторов скоростей точки В на соответствующие ординаты диаграммы скоростей.по оси ординат принимаем равным масштабу скоростей.
5.3 Диаграмма ускорений
Диаграмма ускорений построена графическим дифференцированием диаграммы скоростей.
Для нашего случая полюсное расстояние принято равным Н=10 мм.
Масштабный коэффициент по оси ординат определяется по формуле:
5.4 Точность построения диаграммы ускорения
Сравним величины ускорения точки В полученные с помощью графического дифференцирования диаграммы скоростей и методом планов.
Определяем величину ускорения для 10-го положения механизма по диаграмме
Ранее из планов ускорений получена величина ускорения точки В
Определяем расхождение значений ускорений
Полученная погрешность имеет небольшую величину и не превышает допустимой что подтверждает достоверность расчетов и построений.
Кинетостатическое исследование механизма
1 Определение сил и моментов сил действующих на звенья механизма
Расчет производится для положения № 10. Изображаем кинематическую схему и план положений механизма в данном положении используя масштабный коэффициент мс план скоростей план ускорений и диаграмму усилий на поршнях.
Определение движущих сил на поршнях ДВС
Движущие силы на поршнях 3 и 5 зависят от величин давлений в цилиндрах ДВС
Где - площадь поршня.
Величины давлений определяем по заданной индикаторной диаграмме которая показывает изменение давления от перемещения поршня. Заданную диаграмму воспроизводим на листе 2 в масштабе рядом с планом положений направив ось S параллельно оси поршня (ось SВ OD ось SС OС). Масштабный коэффициент давления диаграммы ось МПАмм.
Из планов положений точки В и С поршней 3 и 5 проектируем линии диаграммы и расставляем номера положений на соответствующих кривых диаграммы. При движении поршня 3 с точкой В влево в пол. 0 1 2 5 совершается рабочий ход такт расширения и давление уменьшается от до 01 МПа а при движении поршня 3 вправо в пол. 6 7 8 11 совершается холостой ход с тактами выхлопа-всасывания и сжатия. Аналогично для поршня 5 с точкой С — точки 11 0 1 4 – рабочий ход 5 6 10 - холостой ход. Замеряем ординаты и от осей до точек диаграммы и рассчитываем давления на поршнях по формулам а движущиеся силы на поршнях
Например для расчетного положения № 10:
Результаты измерений ординат диаграмм и расчета сведены в табл. 3.1.
Силы тяжести звеньев приложены в их центрах тяжести.
Определяем силы тяжести звеньев:
Силы инерции звеньев приложены в центрах их масс.
Определяем силы инерции звеньев:
моменты инерции шатунов 24 относительно точек S2 S4:
Определяем моменты сил инерции звеньев 4506 2438
2 Силовой расчет группы состоящих из звеньев 45.
Строим план звеньев 45 в масштабе и прикладываем все внешние силы действующие на звенья4 и 5. Отброшенные связи заменяем векторами реакций (реакция воздействия звена 1 на звено 4)и (реакция воздействия опоры 0 на звено 5).
Под действием внешних сил сил инерции и реакций группа будет находиться в равновесии
Составляем условие равновесия группы приравнивая к нулю сумму всех сил действующих на группу:
Неизвестными в данном уравнении являются реакции и .
Линия действия реакции известна она перпендикулярна направляющей Oy. Величину данной реакции определим если зададимся ее направлением и решим уравнение моментов всех сил приложенных к звеньям 45 относительно точки А:
Поскольку значение получено со знаком «плюс» то направление реакции выбрано верно.
Принимаем масштабный коэффициент сил и вычисляем отрезки плана сил:
На плане сил соединяем точки 1-7 и получаем реакцию .
Строим план сил звеньев и из него определяем:
Для определения внутренней реакции в шарнире С рассмотрим равновесие шатуна 4:
Из уравнения видно что для определения достаточно на имеющемся плане сил группы соединить точки 3 и 7 а следовательно
3 Силовой расчет группы состоящих из звеньев 23
Строим план звеньев 23 в масштабе и прикладываем все внешние силы действующие на звенья 2 и 3. Отброшенные связи заменяем векторами реакций (реакция воздействия звена 1 на звено 2 и (реакция воздействия опоры 0 на звено 3).
Ненастными в данном уравнении являются реакции и .
Линия действия реакции известна она перпендикулярна направляющей Ox. Величину данной реакции определим если зададимся ее направлением и решим уравнение моментов всех сил приложенных к звеньям 23 относительно точки А:
Для определения внутренней реакции в шарнире С рассмотрим равновесие шатуна 2:
Строим план положения входного звена. В точке A кривошипа со стороны звеньев 45 прикладываем реакцию со стороны звеньев 23 реакцию и уравновешивающую силу перпендикулярную звену ОА.
Уравнение равновесия кривошипа
Определяем уравновешивающие силы:
Выбираем масштабный коэффициент сил
Отрезки плана сил кривошипа 1:
Строим план сил по уравнению. Замыкающий отрезок отображает реакцию действующую на кривошип со стороны стойки.
5 Определение уравновешивающей силы по методу Н.Е. Жуковского
Найдем уравновешивающую силу методом Жуковского. Вычерчиваем план скоростей повернутый на 90 градусов и укажем все силовые факторы действующие на механизм (силы тяжести инерции сопротивления моменты инерции) а затем составляем уравнение равновесия относительно полюса плана скоростей.
Пересчитываем значения моментов из-за того что изменились плечи приложения:
Погрешность проведения силового анализа:
Мгновенный коэффициент полезного действия механизма определим для расчетного положения 10.
Зададимся радиусами шарниров цапф r=20 мм. Считаем что коэффициенты
Трения в шарнирах и направляющих ползунов соответственно
Реакции в кинематических парах определены силовым расчетом
Определяем относительные угловые скорости звеньев:
Мощности затрачиваемые на трение в кинематических парах в данный момент времени
Определяем общую мощность сил трения
Мощность сил производственных сопротивлений
Мгновенный коэффициент полезного действия механизма
Так как внутри цикла установившегося движения машины не наблюдается равенства работы движущихся сил и работы сил сопротивления и постоянства приведенного момента инерции механизма то угловая скорость начального звена оказывается переменной. Величина колебаний этой скорости оценивается коэффициентом неравномерности движения.
За среднюю угловую скорость можно принять номинальную угловую скорость начального звена .
Колебания скорости начального звена механизма должны регулироваться в заданных пределах.
Роль аккумулятора кинетической энергии механизма обычно выполняет маховик. Поэтому необходимо подобрать массу маховика такой чтобы данный механизм мог осуществить работу с заданным коэффициентом неравномерности движения .
Определение приведенных моментов сил сопротивления
В машине сначала определяем приведенный момент движущих сил из равенства мгновенных мощностей на звене приведения и суммы мощностей внешних сил и моментов на подвижных звеньях от действия движущих сил и .
Равенство мощностей:
Знак «плюс» принимается при рабочем ходе механизма «минус» при холостом.
Для расчетного положения № 10 получим
Результаты расчетов для 12-ти положений приведены в табл. 3.6. По результатам расчетов строится график приведенных моментов сил с выбранным масштабным коэффициентом моментов с ординатами приведенными в табл. 3.2
Масштабный коэффициент по оси абсцисс:
Работа выражается интегралом от моментов сил
Графическим интегрированием диаграммы приведенных моментов сил строим диаграмму работ движущих сил.
Масштабный коэффициент по оси ординат диаграммы работ определяем по формуле:
Примем постоянным приведенный момент сил сопротивления. Тогда работа движущих сил
Соединив начальную и последнюю точку диаграммы работы движущих сил получим наклонную прямую представляющую собой диаграмму работы сил сопротивления.
Продифференцировав графически полученную прямую на диаграмме приведенных моментов получим горизонтальную прямую определяющую величину постоянного приведенного момента сил сопротивления.
Приращение кинетической энергии определяется как
Для построения диаграммы приращения кинетической энергии необходимо из ординат диаграммы работы сил сопротивления вычесть ординаты диаграммы работы движущих сил.
Масштабы по координатным осям остаются те же что и для диаграммы работ.
Приведенный момент инерции определяем из равенства кинетических энергий звена приведения 1 и звеньев 2345 рычажного механизма:
Равенство кинетических энергий в соответствии со схемой запишем:
Рассчитываем положения № 10:
Результаты расчетов для остальных 11-ти положений представлены в табл. 3.3.
По результатам расчетов строим график приведенных моментов инерции . Масштабный коэффициент графика момента инерции
Методом исключения общего параметра из графиков приращения кинетической энергии и приведенных моментов инерции строим диаграмму энергомасс.
По заданному коэффициенту неравномерности движения и средней угловой скорости определяем углы образуемые касательными к оси абсцисс:
По отрезку mn определяем момент инерции маховика
Выбрав форму маховика – диск с параметром
Определяем его маховый момент и примерную массу :
Момент инерции маховика небольшой и масса небольшая кг к тому же неравномерность движения имеет небольшой коэффициент . Можно сделать вывод что его установка существенно не понизит КПД механизма.
Синтез кулачкового механизма.
1 Построение диаграмм движения коромысла
Вычерчиваем диаграмму аналога ускорения коромысла для чего на оси абсцисс в произвольном масштабе откладываем заданные углы .
Рабочий угол кулачка
Для принятой длины диаграммы Х=270 мм величины отрезков изображающих фазовые углы:
В соответствии с заданием в интервале угла удаления и в интервале угла возвращения закон движения толкателя линейный.
Строим графики перемещения и скорости толкателя по заданному графику ускорения. Для построения графика первой производной от перемещения выходного звена по углу поворота кулачка и графика перемещения выходного звена необходимо выполнить двукратное интегрирование второй производной от перемещения выходного звена по углу поворота кулачка. Интегрирование производим графически для этого:
а) построим ординаты а1b2 соответствующие точкам 1 2 и отложим отрезки a’0=a1 b’0=b2 на оси ординат;
б) соединим произвольно взятую точку Р1 на продолжении оси Х с точками a’b’ ;
в) из точки О1 проводим отрезок O1a’ в интервале О11 параллельно лучу P1a’ отрезок a”b” в интервале 1-2 параллельно лучу P1b’ и т.д.
Аналогично интегрируем и для того чтобы получить .
Определяем масштабы полученных зависимостей:
По оси абсцисс диаграмм
По оси ординат диаграммы перемещений
По оси ординат диаграммы аналогов скоростей
По оси ординат диаграммы аналогов ускорений
2 Определение минимального радиуса кулачка и межосевого расстояния в кулачковом механизме
Из произвольной точки А проводим дугу радиусом равным длине коромысла на которой отмечаем точку — начальное положение центра ролика коромысла.
От точки откладываем ход центра ролика и переносим на него разметку траектории при удалении и возвращении с диаграммы .
Через полученные точки из центра вращения коромысла A проводим прямые определяющие положения коромысла.
Аналоги скоростей находим по формуле:
Из точек на положения толкателя откладываем отрезки равные значениям в масштабе . Причем для фазы удаления эти отрезки откладываются в сторону вращения кулачка а для фазы возвращения— в обратную.
Соединив плавной кривой концы отложенных отрезков получим кривую . Через концы отрезков проводим прямые под углами передачи движения к соответствующему направлению толкателя. Точка О пересечения этих касательных определит положение центра вращения кулачка.
Минимальный радиус кулачка:
3 Построение профиля кулачка поступательно движущимся толкателем
Из центра О проводим окружности радиусами .
Oт центра O в сторону противоположную вращению кулачка откладываем фазовые углы . Делим их в соответствии с графиком. Проводим к полученным отрезкам касательные. Полученные касательные 1'2' 3' и т.д. дадут места положения точек профиля кулачка в обращенном движении.
Находим положения центра ролика в обращенном механизме. Для этого производим следующие построения из центра вращения кулачка О радиусами равными ОВ1 ОВ2 ОВ3 проведем дуги окружностей а из точек1’ 2’ 3’ и т.д. на касательных получаем соответственно точки 1’ 2' 3' Соединив полученные точки 1" 2" 3" плавной кривой получим теоретический (центровой) профиль кулачка соответствующий углу удаления.
Центровой профиль получаем уменьшением теоретического на радиус ролика.
Для определения действительного профиля кулачка необходимо определить радиус ролика который должен быть меньше минимального радиуса кривизны pmin центрового (теоретического) профиля кулачка:
Из конструктивных соображений радиус ролика не рекомендуется принимать больше половины минимального радиуса:
Действительный профиль кулачка получим если построим эквидистантную кривую радиусом равным .
Проектирование эвольвентного зацепления прямозубых цилиндрических колес
Модуль колес планетарного механизма: m = 5 мм
Число зубьев простой передачи: Z1= 12 Z2=15
Схема планетарной передачи.
Принимаем что зубчатые колеса изготовлены без смещения исходного контура (Х1=Х2=0). Тогда угол зацепления равен углу профиля инструмента
Радиусы делительных окружностей:
Радиусы основных окружностей:
Радиусы окружностей вершин:
— коэффициент высоты головки зуба
Радиусы окружностей впадин:
— коэффициент радиального зазора
Окружной шаг по делительной окружности
Окружная толщина зуба по делительной окружности
Межосевое расстояние:
Принимаем масштаб построения с учетом того чтобы высота зуба равнялась на чертеже 45 мм.
Построим внешнее эвольвентное зацепление по рассчитанным параметрам.
Откладываем межосевое расстояние . Из центров О1 и О2 проводим начальные окружности они касаются в точке Р. Через нее проводим касательную к начальным окружностям и образующую N-N (линию зацепления) под углом a к касательной. Из О1 и О2 опускаем перпендикуляры О1А и О2В которые будут радиусами основных окружностей. Затем проводим окружности головок ножек и основные окружности для обоих колес.
Разделим отрезок АР на четыре равные части. Пронумеруем их от А к Р. Получим точки А 1 2 3 р. По дуге основной окружности от точки а отложим вправо четыре таких же отрезка получим точки 1 2 3 4. Точка 4 будет началом эвольвенты. Затем соединяем полученные точки с центром О1 радиусами и из этих точек проводим касательные к основной окружности в сторону точки Р которые будут перпендикулярами к их радиусам. На касательных из 1 2 3 откладываем соответственно 1-Р 2-Р 3-Р. Затем подобные построения делаем по другую сторону от точки А. От точки А влево по дуге основной окружности откладываем такие же дуговые отрезки. Получаем точки 5 6 7. Соединив их с О1 проводим касательные к основной окружности в сторону точки Р и откладываем 5-Р 6-Р 7-Р. Соединяем концы всех касательных и получаем эвольвенту. Для профилирования зуба используем участок эвольвенты между окружностями головок и основными окружностями.
Отложив толщину зуба по начальной окружности из точки пересечения эвольвенты с начальной окружностью проводим через центр О1 ось зуба. Затем проводим несколько произвольных дуг от эвольвенты на эти дуги по другую сторону оси переносим точки эвольвенты и получаем второй профиль зуба. Остальные зубья вычерчиваются переносом точек построенного зуба лежащих на начальной окружности на расстояние равное шагу по делительной окружности с последующим простым геометрическим построением. Построим радиусы скругления оснований зуба. Вычерчиваем по три зуба на каждом колесе.
Теоретической частью линии зацепления является отрезок образующей между точками А и В.
Крайние точки практической линии зацепления определяются пересечением окружностей головок колес с линией зацепления. аb=923 мм
Построим рабочие участки профиля зуба. Из центра радиусом равным расстоянию О1а делаем засечку на профиле зуба. Участок зуба от этой точки до вершины зуба и будет рабочим.
Аналогичные построения проводим для второго колеса.
Из графических построений получаем.
Длина дуги зацепления по основной окружности колеса равна длине ga активной линии зацепления ab. Углы и называются углами перекрытия. Отношение угла перекрытия зубчатого колеса к его угловому шагу называется коэффициентом перекрытия.
Вычислим коэффициент перекрытия проектируемой передачи:
Из чертежа длина активной линии зацепления
Коэффициент перекрытия определяется и как отношение зацепления к шагу по основной окружности:
Определяем коэффициент перекрытия аналитическим методом:
Определим передаточное отношение внешнего зацепления
Вычислим удельное скольжение в нескольких точках зацепления и построим диаграммы удельного скольжения. Ось абсцисс диаграмм проведем параллельно линии зацепления а ось ординат — перпендикулярно к ней через точку А. спроектируем на ось абсцисс точки АаРbB.
Удельное скольжение определяем по следующим формулам:
— соответственно радиусы кривизны эвольвент первого и второго колес в точке зацепления.
— длина теоретической линии зацепления (в нашем случае 92 мм)
Значения текущей координаты Х возьмем с интервалом 15 мм в пределах от Х=0 до Х=90 мм.
Результаты расчета сведем в таблицу 5.1 и по ним построим диаграммы удельных скольжений в масштабе .
Толщину зубьев колес по окружности вершин определим по формуле:
— угол профиля эвольвенты по делительной окружности.
— угол профиля эвольвенты на окружности вершин зубьев.
По таблице инвалют определяем для угла значение
Для нормальной работы зубчатой передачи необходимо чтобы соблюдались следующие условия:
Для заданной передачи и т.е. условие нормальной работы соблюдается
Проектирование зубчатого механизма
По заданной схеме механизма и передаточному отношению (32) необходимо спроектировать зубчатый механизм т.е. подобрать числа зубьев колес.
Из схемы видно что механизм состоит из двух ступеней: простая непланетарная (звенья 1 2 2’ 3) и планетарная (звенья 3’ 4 5 и водило).
Передаточное отношение заданного механизма будет равно произведению передаточных отношений его трех ступеней:
При подборе зубьев колес планетарной передачи учитываем соблюдения условия соосности для планетарной ступени.
Поскольку в задании известны числа зубьев колес 1 и 2 то можно определить передаточное отношение ступени :
Общее передаточное число
Принимаем =-064 и Z2’ = 25 тогда
Определим передаточное отношение от колеса 3’ к водилу:
Определим передаточное отношение от колеса 1 к водилу по формуле Виллиса:
Z4 = 05* (Z5 – Z3’) = 05* (60 – 20) = 20
Определяем передаточное отношение от колеса 1 к водилу Н:
Определяем расхождение между заданным и спроектированным передаточным числом:
Проведем графическое исследование спроектированного механизма Для этого вычертим кинематическую схему механизма в масштабе длин
где — длина отрезка изображающего на чертеже делительный диаметр колеса мм.
Принимаем для простоты построений
Строим план скоростей. Проводим линию yy параллельную линии центров и проектируем на нее все характерные точки.
Скорость точки А изображаем отрезком произвольной длины (p1a) перпендикулярным оси yy. Точки скорости которых не равны 0 на чертеже будут иметь в обозначении штрих т.е будут обозначать начало векторов скоростей этих точек. На полюсную прямую переносим точки o a’ b’ o2’ c’ o4’ d. Под картиной линейных скоростей пересекаем полюсную прямую горизонтальной линией и точку пересечения обозначим точкой m которая является полюсом плана угловых скоростей. Отступая от нее некоторое расстояние ставим точку S.
Зная угловую скорость колеса 1 откладываем скорость точки А принадлежащей колесу 1 и 2 получаем точку а. Через полученную точку а и о проводим картину скоростей колеса 1. Через a и о2 проводим картину скоростей блока колес 2 и 2’ на которую проектируем точку b получая вектор bb’. Через b и 0 проводим картину скоростей колеса 3 и колеса 3’. На нее проектируем скорость точки С получая с. Через точку с и d проводим картину скоростей колеса 4 на нее проектируем скорость точки О4 получая о4. Через нее и 0 проводим картину скоростей водила Н. Теперь под картиной линейных скоростей пересекаем полюсную прямую горизонтальной линией и точку пересечения обозначим точкой p которая является полюсом плана угловых скоростей. Отступая от нее некоторое расстояние ставим точку S из которой проводим лучи параллельно картинам скоростей колес и водила получаем точки 1 2 4 5 6 Н.
Полученные отрезки (р1’) (р2’) (р5) пропорциональны соответствующим угловым скоростям
Тогда передаточные отношения
Измерив на плане угловых скоростей отрезки (01’) (0Н) получим
Так как точки 1 и 5 находятся на разных сторонах линии уу. То передаточное отношение отрицательное.
Поскольку точки 1и 2 находятся по разным сторонам от оси уу это передаточное отношение отрицательное.
Курсовое проектирование по теории механизмов и машин под ред. Девойно Г.Н. - Мн: Вышейшая школа 1986. - 288 с.
Теория механизмов машин и манипуляторов. Курсовое проектирование: Учебно-метод пособие для студентов заочников машиностроительных специальностей П. П. Анципорович [ и др.]; Мн : БНТУ 2004 - 67 с..
Теория механизмов и машин под ред. Фролова К.В. - Мн: Вышейшая школа 1987. - 496 с
Методические указания по выполнению курсового проекта по ТММ для студентов- заочников Анципорович П. П. Астахов В. И. и др. - Мн : БПИ 1990.
зуб мех.cdw

Рекомендуемые чертежи
- 24.01.2023
Свободное скачивание на сегодня
- 24.01.2023