Выправочно-подбивочно-рихтовочная путевая машина DYNAMIC STOPFEXPRESS 09-3X



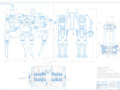

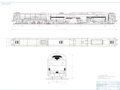
- Добавлен: 25.10.2022
- Размер: 3 MB
- Закачек: 1
Описание
Состав проекта
![]() |
![]() ![]() |
![]() ![]() |
![]() ![]() ![]() ![]() |
![]() ![]() ![]() ![]() |
![]() ![]() ![]() ![]() |
![]() ![]() ![]() |
![]() ![]() |
![]() ![]() ![]() |
![]() ![]() |
![]() ![]() |
![]() ![]() |
Дополнительная информация
A1_DYNAMIC_STOPFEXPRESS_09-3X_Chertezh_obschego_vida__KP_PM_VMS-41_2021_00_00_00_VO.dwg

КП.ПМ.ВМС-41.2021.00.00.00.
* Размеры для справок.
Максимальная скорость движения 96 кмч.
Мощность двигателя 440 кВт.
DYNAAMIC STOPFEXPRESS 09-3X
A1_Gidroskhema.dwg

Предохранительный клапан
Пневмогидроаккумулятор
КП.ПМ.ВМС-41.2021.00.00.00..
DYNAMIC STOPFEXPRESS 09-3X
Схема гидравлическая
A1_Blok_podbivochny.dwg

Сварные швы по ГОСТ 5264-80
Электрод Э46 ГОСТ 9467-75
Сварные швы зачистить от брызг металла
Горизонтальные перемещения рам поз.14
и вертикальные перемещения подбивочных блоков поз. 12 и 13
по направляющим должно быть свободным без рывков и заеданий
Подшипники и оси смазать смазкой ЦИАТИМ - 201 ГОСТ 6267-74
КП.ПМ.ВМС-41.2021.00.00.00.
DYNAMIC STOPFEXPRESS 09-3X
Titulnik_PM.docx
УЧРЕЖДЕНИЕ ОБРАЗОВАНИЯ
«БЕЛОРУССКИЙ ГОСУДАРСТВЕННЫЙ УНИВЕРСИТЕТ ТРАНСПОРТА»
Кафедра «Транспортно-технологические машины и оборудование»
ПОЯСНИТЕЛЬНАЯ ЗАПИСКА
к курсовому проекту по дисциплине:
студент группы МС-41
DYNAMIC STOPFEXPRESS 09-3X
PZ_Sudas.docx
НАЗНАЧЕНИЕ КРАТКОЕ ОПИСАНИЕ УСТРОЙСТВА И РАБОТЫ МАШИНЫ10
РАСЧЕТ ПОДБИВОЧНОГО БЛОКА12
1 Взаимодействие лопаток подбоек и уплотняемого балластного слоя12
2 Расчет эффекта уплотнения балласта подбивочным блоком20
3 Расчет энергетических характеристик приводов подбивочного блока23
РАСЧЕТ УСТОЙЧИВОСТИ МАШИНЫ26
1 Расчет устойчивости машины против опрокидывания26
2 Расчет устойчивости машины против схода с рельсов при движении в транспортном режиме29
ТЯГОВЫЙ РАСЧЕТ МАШИНЫ32
ТЕХНИКА БЕЗОПАСНОСТИ И ЭКОЛОГИЧЕСКАЯ БЕЗОПАСНОСТЬ ПРИ РАБОТЕ МАШИНЫ37
Железнодорожный путь является важным объектом т.к. обеспечивает большинство пассажирских и транспортных перевозок. Поэтому обеспечение его работоспособного состояния является одной из основных задач.
На путь постоянно воздействуют усилия от движущихся тяжеловесных поездов а также разнообразные климатические факторы вызывающие разрушение пути и износ его элементов.
В процессе эксплуатации на путевую решетку воздействуют поездные нагрузки которые передаются на балластный слой и вызывают его обратимые (упругие) и необратимые (остаточные) деформации. С течением времени деформации накапливаются как правило неравномерно по протяжению пути. Положение рельсошпальной решетки (РШР) изменяется сначала в пределах допусков а затем и за пределами допусков (натурное положение) т.е. наблюдаются расстройства пути вызывающие эксплуатационные ограничения (скорости движения поездов и др.). Для обеспечения плавного и безопасного движения поездов периодически требуется фиксировать РШР за счет уплотнения балластного слоя (производить подбивку). В путевом хозяйстве эти технологические операции выполняются машинами и механизмами для уплотнения балластной призмы.
В данном курсовом проекте рассматривается выправочно-подбивочно-рихтовочная машина Dynamic stopfexpress 09-3X предназначенная для уплотнения балласта под шпалами при строительстве реконструкции капитальном и среднем ремонтах а также текущем содержании пути. Машина может быть использована для подбивки деревянных и железобетонных шпал на различном балласте.
АНАЛИЗ ПАТЕНТНОЙ ЛИТЕРАТУРЫ
Шпалоподбивочная машина — путевая машина для подачи балласта под шпалы и его уплотнения. Применяется на железнодорожном транспорте при строительстве ремонте и текущем содержании железнодорожного пути.
Шпалоподбивочная машина создана в1951 годувШвейцариина фирме «Матиса» а в середине50-хгодовпоявилась и вСССР. Выпускаются главным образом самоходные шпалоподбивочные машины на рельсовом или комбинированном (колёсно- и гусенично-рельсовом) ходу для одновременной подбивки одной двух или большего числа шпал.
Существует большое количество патентов на конструкции как машин в целом так и рабочего оборудования отдельно. Рассмотрим некоторые из них:
1 Патент SU 145965 RU MПК Е01 В2716
На кафедре «Подъемно-транспортные путевые и строительные машины» Петербургского государственного университета путей сообщения разработано устройство для качественного уплотнения балластного слоя в шпальных ящиках на которое получен патент на полезную модель (RU № 145965 Е01В 2716 опубл. 27.09.14). Общий вид устройства представлен на рисунке 1.1.
Устройство работает следующим образом. С помощью гидравлического привода 5 опускают раму 8 уплотнителя балластного слоя в шпальных ящиках
до соприкосновения уплотнительных инструментов 1 с балластным слоем. Затем включают привод вибраций 7. При этом машина непрерывно движется
по пути. Уплотнительные инструменты 1 соприкасаются со шпалой за счет чего вращается барабан 3 и опускается следующий уплотнительный инструмент 1 в очередной шпальный ящик. Уплотнительные инструменты вращаются в плоскости параллельной оси пути и оказывают на балластный слой в шпальном ящике виброударное воздействие.
Компенсация изменения расстояния между шпалами осуществляется благодаря тому что уплотнительные инструменты соединены между собой с помощью пружин сжатия 2 которые при необходимости сжимаются и растягиваются.
Рисунок 1.1 – Устройство для уплотнения балластного слоя в шпальных ящиках:
— уплотнительный инструмент; 2 — пружина сжатия; 3 — барабан; 4 — ступица; 5 — привод; 6 — вал; 7 — привод вибраций; 8 — рама
) Машина для уплотнения балласта железнодорожного пути содержащая опирающуюся на ходовые тележки раму смонтированные на ней рабочий орган уплотнения плеч и откосов балластной призмы. включающий в себя размещенные на раме с обеих сторон от продольной оси машины уплотнительные плиты и вибраторы связанные с плитами и рабочий орган для уплотнения балласта в шпальных ящиках состоящий из уплотнительных башмаков установленных с возможностью перемещения друг относительно друга связанных с виброприводом и располагаемых по обеим сторонам каждой рельсовой нити в смежных шпальных ящиках отличающаяся тем что с целью повышения качества уплотнения балласта она снабжена дополнительными уплотнительными плитами направляющими закрепленными на вибраторах и кронштейнами на которых шарнирно закреплены дополнительные уплотнительные плиты с возможностью поворота в вертикальной плоскости причем уплотнительные плиты и кронштейны установлены на указанных направляющих н связаны между собой посредством механизма перемещения.
) Машина по п. 1 отличающаяся тем что каждый шарнир закрепления дополнительных уплотнительных плит на кронштейнах состоит из болта средняя часть которого выполнена в форме усеченного конуса размещенного в коническом отверстии кронштейна разрезной конической втулки установленной в коническом Ф отверстии дополнительной уплотнительной плиты гайки и упругого элемента размещенного между гайкой и указанной втулкой. Изобретение относится к устройствам для строительства и ремонта железнодорожного пути в частности к устройствам для уплотнения его балласта. (Приложение А).
Рисунок 1.2 – Машина для уплотнения балласта железнодорожного пути:
— рама машины; 2 — ходовая тележка; 3 — рабочий орган для уплотнения плеча и откоса балластной призмы; 4 — рабочий орган для уплотнения балласта в шпальных ящиках
Цель изобретения - повышение качества уплотнения балласта. Эта цель достигается тем что машина для уплотнения балласта железнодорожного пути содержащая опирающуюся на ходовые тележки раму смонтированные на ней рабочий орган для уплотнения плеч и откосов балластной призмы включающий в себя размещенные на раме с обеих сторон от продольной оси машины уплотнительные плиты вибраторы связанные с плитами и рабочий орган для уплотнения балласта в шпальных ящиках состоящий из уплотнительных башмаков установленных с возможностью перемещения друг относительно друга связанных с виброприводом снабжена дополнительными уплотнительными плитами направляющими закрепленными на вибраторах и кронштейнами на которых шарнирно закреплены дополнительные уплотнительные плиты с возможностью поворота в вертикальной плоскости причем уплотнительные плиты и кронштейны установлены на указанных направляющих и связаны между собой посредством механизма перемещения. Кроме этого каждый шарнир закрепления дополнительных уплотнительных плит на кронштейнах состоит из болта средняя часть которого выполнена в 60форме усеченного конуса размещенного в коническом отверстии кронштейна разрезной конической втулки установленной в коническом отверстии дополнительной уплотнительной плиты гайки и упругого элемента размещенного между гайкой и указанной втулкой.
Изобретение относится к строительству и ремонту железнодорожного пути в частности к уплотнению балласта под шпалой шпалоподбивочной машиной. Способ подбивки шпал заключается в том что определяют величины подъемки рельсов в каждой точке обрабатываемого участка пути задают величины заглубления подбоек с последующей выправкой пути посредством перемещения подбоек в зону над обрабатываемой шпалой. Далее осуществляют подъемку пути и опускание подбоек в балласт на заданную глубину. Заглубление подбоек в балласт производят на величину отличную для каждой точки пути от предварительно заданной величины. Величина отличия прямо пропорциональна величине подъемки пути и расстоянию от оси задней тележки машины до центра подбивочного блока и обратно пропорциональна расстоянию от оси задней тележки до оси колеса измерительного устройства. Далее перемещают подбойки к шпале поднимают с разведением в исходное положение и перемещают машину к следующей шпале и повторением цикла выправки. Технический результат заключается в обеспечении получения оптимального зазора между верхней кромкой лопатки подбойки и низом шпалы на всей длине обрабатываемого участка железнодорожного пути что приводит к стабильной максимальной плотности балласта под шпалой и обеспечивает стабильное положение пути в течение более длительного времени.
Осуществить предлагаемый способ подбивки шпал железнодорожного пути можно с учетом углового положения подбоек в перпендикулярной пути плоскости. В этом случае опускание подбивочного блока производится до положения Н4=Н1-h-R·(l-S- угол отклонения оси подбойки от вертикального положения. После чего производится перемещение подбоек к шпале их подъем с разведением в исходное положение и перемещение машины к следующей шпале. Это также обеспечивает требуемое положение лопаток подбоек относительно низа шпалы. Расчет величины R·(1-Sin) в случае неизменного углового положения подбоек в процессе обработки всего участка пути может быть произведен заранее и записан в память компьютера совместно с величиной подъемки Н. В этом случае перед началом работ подбойки должны быть установлены в соответствии с углом. В случае изменения углового положения подбоек во время производства работ расчет величины R·(l-Sin) следует производить при каждом цикле подбивки шпал.
Рисунок 1.3 – Машина для подбивки стрелочных переводов и подбивочный блок
НАЗНАЧЕНИЕ КРАТКОЕ ОПИСАНИЕ УСТРОЙСТВА И РАБОТЫ МАШИНЫ
Машина выправочно-подбивочно-рихтовочная DYNAMIC STOPFEXPRESS 09-3X предназначена для выправки железнодорожного пути в продольном и поперечном профилях и в плане а также для уплотнения балласта под шпалами и с торцов шпал. Машина выправочно-подбивочно-рихтовочная DYNAMIC STOPFEXPRESS 09-3X является сверхпрочной высокоскоростной путевой машиной непрерывного действия для ускоренной выправки и стабилизации железнодорожных путей. Стабилизирующие блоки смонтированы на отдельной самоходной раме. В то время как спутниковые сигналы передаются компьютеру машины чтобы связать время процессов работы (подъема подкладка выравнивания и трамбовки) с вычислительной базой аппарата и с системой стабилизатора машина движется плавно и непрерывно. Высокая производительная способность особенно важна для железных дорог на участках с высокой плотностью железнодорожного полотна. Процесс трамбовки и стабилизация осуществляется одновременно одним оператором. STOPFEXPRESS Express 09-3x оснащен оборудованием стабилизации способным трамбовать бетон а также другие покрытия. Это уникально разработанное оборудование в сочетании с системами ATLAS и Атта Plasser в полностью регулируется для автоматической выправки железнодорожного пути даже при нерегулярном и неравномерном расстояния между шпалами.
Машина применяется как при строительстве новых так и при ремонтах и текущем содержании действующих железных дорог колеи 1435 и 1520 мм с рельсами до Р-65 включительно с деревянными или железобетонными шпалами на различного рода балластах. DYNAMIC STOPFEXPRESS 09-3X является универсальной путевой машиной непрерывного действия производящей одновременную или независимую выправку рихтовку и подбивку железнодорожного пути в полуавтоматическом или ручном режимах на магистральных и станционных путях.
Рисунок 2.1 – Выправочно-подбивочно-рихтовочная машина машина DYNAMIC STOPFEXPRESS 09-3X
Машина оснащена микропроцессорным управлением выправочными системами. Бортовой компьютер снабженный клавиатурой для ввода оперативной информации предназначен: для сбора и хранения информации о состоянии пути до и после выправки и о проектных параметрах пути для выполнения вычислительных операций и формирования управляющих сигналов системы выправки пути для обеспечения диалогового режима с пользователем.
Благодаря высокой транспортной скорости наличию радиостанции системы безопасности движения автоматизированной системы обнаружения и тушения пожара силовой установки DYNAMIC STOPFEXPRESS 09-3X может самостоятельно перемещаться по магистральным путям к месту работы.
Вид климатического исполнения У1 ГОСТ 15150 но для работы при температурах от -10° до +40° С при несмерзшемся балласте.
РАСЧЕТ ПОДБИВОЧНОГО БЛОКА
Подбивочный блок – это вибрационное устройство предназначенное для уплотнения балластного слоя под подошвами шпал. Шпалоподбивочный механизм блока имеет привод вибраций в виде эксцентрикового вала соединенного через шатунные элементы с концами рычагов подбоек и механизм обжима балласта (подачи лопаток подбоек) в виде гидроцилиндров. Дополнительные приводы блока – механизм его вертикального перемещения (опускания с заглублением подбоек и подъема) и механизм перемещения блока в поперечном направлении при работе в кривых.
Процесс уплотнения балластного слоя рабочими органами машин является сложным многофакторным процессом. Для его реализации взаимодействуют два сложных объекта: путевая машина и верхнее строение пути (в общем случае это РШР и балластная призма). На практике наибольшее распространение получил метод силового вибрационного воздействия с поступательным движением уплотнительной поверхности рабочего органа. Технические расчеты подбивочных блоков выполняются в целях оценки: производительности блока и машины технологического эффекта работы блока через показатели качества уплотнения усилий в элементах механизмов при расчете на прочность и надежность параметров рабочих органов и режимов работы характеристик энергоемкости при выборе параметров приводов экипажной части машины по характеристикам рабочих органов. Кроме того производить оценку рабочих свойств верхнего строения пути при эксплуатации в требуемом режиме и др.
1 Взаимодействие лопаток подбоек и уплотняемого балластного слоя
Расчет ведется в соответствии с рекомендациями [2] и [3].
Кинематический и силовой анализ взаимодействия поступательно движущейся вибрирующей лопатки подбойки с массой балласта в слое рассматривается на модели горизонтального вибрационного воздействие подбойки 1 с объемом балласта 2 под шпалой 2 (рисунок 3.1). Угловая частота колебаний подбойки радс амплитуда A м а скорость подачи Vп мс.
При рассмотрении стационарного процесса взаимодействия подбойки с балластом начало отсчета времени можно принять в момент начала нового колебательного цикла. Тогда начальная фаза колебаний принимает нулевое значение. С этим моментом времени свяжем локальные системы координат 0St и 0Vt (рисунок 3.2 а б).
Рисунок 3.1 – Вибрационно-поступательное движение лопатки:
– подбойка; 2 – шпала; 3 – объем балласта
Рисунок 3.2 – График взаимодействия лопаток и подбойки с балластом
На рисунке 3.2 левее точки начала координат 0 показаны части графиков соответствующие предыдущему циклу а правее – текущему циклу. При отрывном режиме работы часть периода колебаний T лопатки находятся в контакте с балластом – с точки 1 графика до точки 2. Подбойка движется к шпале производя обжим балласта. Пройдя точку максимального отклонения подбойка начинает движение от шпалы и в точке 2 ее скорость выравнивается со скоростью отдачи балласта Vб. В дальнейшем движении она отрывается от балласта. На участке 2-4 подбойка сначала движется от шпалы а затем пройдя точку 3 максимального отклонения начинает движение к шпале. В точке 4 положение которой отражено на графике подбойка встречается с балластом. Происходит удар лопатки о балласт аналогичный удару в точке 1 предыдущего цикла.
Движение подбойки является результатом наложения ее колебательного и поступательного движений условно показано в виде графика 1-2-3-4 (рисунок 3.2 а). Уравнение лопатки подбойки в показанной локальной системе координат в абсолютном движении
где – угловая частота колебаний подбойки радс; =1363 радс;
А – амплитуда колебаний м; для DYNAMIC STOPFEXPRESS 09-3X А=55мм=0011 м;
Vп – скорость подачи мс; для DYNAMIC STOPFEXPRESS 09-3X Vп = 035 мс;
t – время рабочего цикла (без учета перемещения машины между шпалами); для DYNAMIC STOPFEXPRESS 09-3X t = 6 с.
Наилучший эффект достигается при скорости вибрирования
Тогда скорость движения лопатки подбойки может быть рассчитана как производная по времени t от перемещения Sлп
На участке 1-2 лопатка находится в контакте с балластом и производит его обжим. На этом участке совершается работа по уплотнению балласта причем часть работы выполняет механизм привода вибраций а часть работы механизм подачи. В точке 2 происходит отрыв лопатки от балласта после чего она совершает возвратное движение а балласт под действием сил упругости смещается. Смещение балласта м
где S2 – отклонение лопатки с балластом от начального положения в точке отрыва 2 м;
Vб – скорость отдачи балласта мс (Vб = 013 – 014 мс);
t2 – время от начала цикла до момента отрыва с.
Период колебаний T (T = 2) с складывается из времени контакта tк лопатки с балластом и времени ее отрыва tо от балласта (T = tк + tо). В точке 4 положения лопатки (точка 4б и точка 4п принадлежащие балласту и подбойке совпадают) наблюдается удар по балласту (рисунок 3.2 а). При ударе происходят интенсивные смещения частиц балласта и его уплотнение поэтому сначала определим tк и tо.
Момент времени отрыва лопатки подбойки от балласта с
Момент времени t4 удара лопатки подбойки и уплотнения балласта определится из трансцендентного уравнения:
Это уравнение легко решается методом итераций. При итерационных вычислениях последовательно наращивается значение t4 по формуле t4=t2+Δt (Δt – сколь угодно малый интервал наращивания времени с). Итерации прекращаются если левая часть уравнения станет ≤ 0.
Время отрыва и время контакта лопатки подбойки и балласта составляет
Скорость удара лопатки подбойки о балласт мс (рисунок 3.2 б)
Для анализа силовых и энергетических соотношений процесса уплотнения балласта необходимо определить смещение лопатки подбойки Sк вместе с балластом м
Sп – величина подачи лопатки за цикл колебаний м;
S4 – смещение относительно исходного положения в момент удара м.
Максимальному смещению лопатки подбойки Smax соответствует его нулевая скорость поэтому
где tmax – время от начала цикла до достижения лопаткой максимального отклонения с.
Время соответствующее максимальному отклонению лопатки с
Величина подачи лопатки за цикл колебаний м
Смещение Smax и S4 определяются при подстановке соответствующих значений tmax и t4.
Момент времени соответствующий минимуму траектории лопатки с
Моменту времени tmin соответствует максимум отрыва лопатки подбойки от балласта. С учетом этого максимальный отрыв лопатки от балласта
На графике (рисунок 3.2 а) величина Smin принимает отрицательное значение.
Таким образом взаимодействие рабочего органа с балластом характеризуется полностью пятью параметрами:
Sк – обжим (подача) балласта за каждый цикл колебаний Sк = 0067 м;
Sо – максимальный отрыв лопатки подбойки от балласта за цикл колебаний Sо=0016 м;
tо – время отрыва лопатки от балласта за цикл колебаний tо = 001 с;
tк время контакта лопатки с балластом за цикл колебаний tк = 0036 с;
Vу – скорость удара в момент встречи рабочей лопатки с балластом Vу=00242 мс.
Для оценки характера взаимодействия лопатки с балластом используется параметр С режима уплотнения значение которого с учетом упругой отдачи балласта определяется по формуле
В числителе этого выражения приводится скорость взаимного сближения лопатки и балласта а в знаменателе – амплитудное значение скорости вибрирования. Как показывает опыт эксплуатации уплотнительных рабочих органов машин эффективное уплотнение происходит при взаимодействии лопатки и балласта с отрывом и ударами это соответствует C 1. При безотрывном режиме взаимодействия лопатки и балласта эффективность уплотнения резко падает так как контакты частиц друг с другом малоподвижны частицы оказываются взаимно заклиненными. При отрывном режиме взаимодействия контакты частиц становятся подвижными имеют возможность перестроиться образуя более плотную текстуру.
Экспериментально установлено что результат уплотнения несвязного материала (щебня) выраженный через относительную осадку Eу является случайной гиперболической функцией от общего количества относительных перемещений частиц материала происходящих под действием внешних силовых импульсов с учетом сил инерции и внутреннего трения (активные перемещения) а также сил упругости и веса вызывающих отдачу щебня при циклических разгрузках (пассивные перемещения) и выражается формулой
где = 0 –2 – коэффициент определяющий степень использования для уплотнения пассивных и активных относительных перемещений частиц;
λ = 0 –1 – коэффициент определяющий долю объема материала охваченного относительными перемещениями;
tв – время воздействия на балласт с;
A B – эмпирические коэффициенты зависящие от рода уплотняемого материала и способов вибровоздействия.
Для щебня при рациональных параметрах виброуплотнения = 2; λ = 1; A=3300; B = 10 (tв)min = 600 – 800.
Эффективность виброуплотнения щебеночного балласта обеспечивается если параметры взаимодействия и их соотношения составляют
2 Расчет эффекта уплотнения балласта подбивочным блоком
Требуемый результат уплотнения балластного слоя в зоне под шпалами достигается в зависимости от ряда факторов либо при однократном либо при многократном виброобжиме балласта лопатками подбоек подбивочного блока (рисунок 3.2).
Вначале определим относительную осадку уплотнения Eу объема балластного слоя под шпалой после однократного обжима. Пусть начальное состояние слоя характеризуется относительной осадкой уплотнения Eн. Отсутствует локализация зон уплотнения. Обжим объема балласта в слое толщиной hсл м производится из положения лопаток характеризуемого максимальным раскрытием Smax м в положение минимального раскрытия Smin м (рисунок 3.3). Подбивка (уплотнение балластного слоя в зонах под шпалами) производится с технологической выправочной подъемкой hпод м. Начальный объем уплотняемой зоны м3
где Vосн – основной объем балласта под шпалой подлежащий уплотнению на длине (Lш – e)2 м;
Lш – длина шпалы м (для железобетонной шпалы Lш = 27 м а для деревянной шпалы Lш = 275 м) е – ширина не уплотняемой зоны в середине шпалы м;
Vдоп – дополнительный объем балласта м3 подаваемый подбойками в зону уплотнения при вибрационном обжиме с учетом угла передачи давления αп град.
Рисунок 3.3 – Схема уплотнения балласта
Основной и дополнительный объемы м3
где = (09 – 10) – коэффициент притока (выдавливания) балласта при виброобжиме;
kдоп = (12 – 13) – коэффициент учитывающий дополнительную подачу балласта подбойкой за счет угла αп передачи давления (для путевого щебня подвергаемого вибрационному воздействию αп = (15 – 20)º;
Jпод – число одновременно работающих в рассматриваемой зоне подбоек;
dп – начальный обжим балласта равный толщине подбойки dп =0019 м;
kп – коэффициент приведения площади лопатки kп = (a+d)(b+d)(ab);
kп = (014+004)(028+004)(00398)=145. Здесь d = 004 м – средний диаметр частиц балласта;
Fр – рабочая площадь лопатки Fр = ab=00398 м2.
Объем уплотненной зоны (ядра уплотнения) м3 характеризуемый искомой относительной осадкой уплотнения Eу с учетом технологической подъемки hпод
Далее рассмотрим относительную осадку уплотнения Eу щебеночного балласта в ядре уплотнения под шпалой после двукратного виброобжима балласта подбойками. После первого обжима подбивочный блок приподнимается лопатки подбоек выходят из балласта. Под действием вибраций при подъемке пути образующиеся пустоты заполняются обсыпающимся из шпальных ящиков балластом. При повторном обжиме образовавшиеся новые дополнительные объемы балласта должны заполнять ядро уплотнения.
Без разрушения сформированное в первом цикле ядро уплотнения может пополняться новыми объемами балласта только в случае если его степень уплотнения ниже чем формируемая в дополнительных объемах. В этом случае может происходить выравнивание (диффузия) степени уплотнения в ядре. Повторное уплотнение ядра не требуется при достижении степени уплотнения ядра близкой к предельной.
В основу модели процесса повторного вибрационного обжима балластного слоя положена гипотеза что происходит разрушение ядра уплотнения сформированного после первого цикла и формирование нового ядра из двух объемов характеризуемых разной степенью уплотнения. Кинематика движения лопаток подбоек и балластного слоя при втором обжиме идентична кинематике первого обжима поэтому используем аналогичную расчетную схему (рисунок 3.2)
Обозначим объемы м3: Vн1 = Vосн = 0085 м3; Vн2 = Vдоп = 000664 м3; Vу=Vосн=0085м3 а соответствующие относительные осадки уплотнения в зонах: Eн1 = Eу(1); Eн2 = Eн. Для получения относительной осадки уплотнения Eу в ядре после второго цикла подставим полученные значения в формулу (3.19).
При многократном обжиме необходимо особое внимание обращать на наличие в балластной призме достаточного для получения требуемой степени уплотнения количества балластного материала. При недостатке материала в технологии работ должна быть предусмотрена дополнительная дозировка балласта и несколько проходов подбивочной машины.
3 Расчет энергетических характеристик приводов подбивочного блока
При обжиме балласта лопатка подбойки захватывает частицы по периметру поэтому учитывается ее площадь и дополнительная площадь образуемая частицами по периметру. Значение максимального усилия обжима балласта кН
где a b – ширина и высота лопатки а = 014м b = 028 м;
d – средний диаметр частиц балласта м (d = 004 м);
kп – коэффициент приведения площади лопатки kп = 145;
Fр – рабочая площадь лопатки Fр = ab=00398 м2;
Максимальное усилие обжима достигается в точке максимума смещения 4 лопатки (рисунок 3.2 а). Работа по уплотнению балласта совершается на участке обжима от точки 1 соответствующей удару о балласт в предшествующем цикле до точки максимума.
При обжиме балласта лопаткой подбойки в каждом цикле возрастает степень уплотнения. В начальном состоянии степень уплотнения характеризуется коэффициентом пористости н а после подачи подбойки на величину рабочего хода Sпп уплотненное состояние балласта соответствует коэффициенту пористости у. Поэтому в момент касания подбойки и балласта в первом цикле и завершения последнего обжима реактивные усилия балласта кН (рисунок 3.4)
Общее смещение Sк обусловливается смещением связанным с механизмом подачи Sпп и механизмом вибрации Sпв м
Рисунок 3.4 – Работа уплотнения совершаемая подбойкой
где qн qу – опытные коэффициенты для состояний балласта до и после уплотнения qн = 061 qу = 056.
Работа в каждом цикле отражается площадями заштрихованных фигур а общая произведенная работа уплотнения получается в результате их суммирования кДж
где kу – коэффициент учитывающий динамические явления при обжиме балласта и нелинейность нарастания реакции балласта при его обжиме kу = 08 – 10;
kбз – коэффициент учитывающий трение боковых поверхностей лопатки и затекание балласта сзади лопатки при обжиме kбз = 12 – 15.
Средняя мощность развиваемая приводом вибраций и подачи подбойки за время ее сведения кВт
Мощности развиваемые механизмом вибраций и механизмом подачи кВт
РАСЧЕТ УСТОЙЧИВОСТИ МАШИНЫ
1 Расчет устойчивости машины против опрокидывания
Расчет ведется в соответствии с методическими указаниями [9].
Произведем оценку устойчивости машины DYNAMIC STOPFEXPRESS 09-3X против поперечного опрокидывания при движении с максимальной конструкционной скоростьюVм= 222 мс (80 кмч) в кривой радиусомR= 600 м с возвышением наружного рельсаhв= 012 м (120 мм). В расчете учитываются активные и реактивные силы показанные на рисунке 4.1. Эффектом «заваливания» корпуса машины относительно осей при недостатке или избытке возвышения допускается пренебрегать и считать в расчетной модели оси и корпус монолитным жестким диском: боковое смещение центра тяжести корпуса = 0.
Оценку запаса устойчивости против поперечного опрокидывания производим по критерию
Рисунок 4.1 - Схема к расчету запаса поперечной устойчивости машины DYNAMIC STOPFEXPRESS 09-3X при движении в транспортном режиме:
G– вес машины;Q- центробежная сила инерции действующая на машину при движении в кривой;Pв– суммарная сила бокового ветрового давления;RAиRB– реакции рельсов на силовое воздействие;hв– возвышение наружного рельса в кривой; α – угол наклона плоскости УВГР к горизонту;S– расстояние между осями рельсов (точками вероятного опрокидывания A и B);HGиHв– высоты от УВГР до центра тяжестиСти центра парусностиСпмашины
С учетом допустимых упрощений реакции рельсов кН определим из решения уравнений равновесия относительно точек опрокидывания
где G– вес машины G = 54000 кг = 52974 кН;
Q- центробежная сила инерции действующая на машину при движении в кривой;
Pв– суммарная сила бокового ветрового давления;
RAиRB– реакции рельсов на силовое воздействие;
hв– возвышение наружного рельса в кривой hв = 012 м;
α – угол наклона плоскости УВГР к горизонту;
S– расстояние между осями рельсов (точками вероятного опрокидывания A и B) S = 161 м;
HGиHв – высоты от УВГР до центра тяжести Ст и центра парусности Сп машины.
Угол наклона УВГР к горизонту
Центробежная сила инерции кН
где К – радиус кривой К= 600 м.
Высота HG центра тяжести совпадает с высотой центра масс. HG = 124 м.
Для вычисления высоты Hв составим схему подветренных площадей машины (рисунок 4.2). Результаты заносим в таблицу 4.1.
Таблица 4.1 – Результаты вычислений положений центров парусности
Подветренная площадь м2
Высота до центра парусности м
Суммарная площадь 6479
Рисунок 4.2 – Схема к определению подветренной площади машины:
Hві – высота расположения центра парусности і-того элемента; Fві – площадь парусности і-того элемента;
Высоту центра парусности машины Hв определим из уравнения статических моментов подветренных площадей относительно УВГР
где – боковая подветренная площадь
- высота расположения центра парусности i-того элемента м.
Расчетная сила бокового ветрового давления кН
где – расчетное ветровое давление ;
По формулам 4.2 и 4.3 определяем реакции рельсов
Отсюда искомый коэффициент запаса устойчивости
Запас поперечной устойчивости машины DYNAMIC STOPFEXPRESS 09-3X при движении со скоростьюVм= 222 мс (80 кмч) в кривой радиусом R = 600 м с возвышением наружного рельсаhв= 012 м (120 мм) гарантируется.
2 Расчет устойчивости машины против схода с рельсов при движении в транспортном режиме
Произведем оценку устойчивости машины DYNAMIC STOPFEXPRESS 09-3X против схода с рельсов при движении с максимальной конструкционной скоростьюVм= 222 мс (80 кмч) в кривой радиусомR= 600 м с возвышением наружного рельсаhв= 012 м (120 мм). Условия движения аналогичны приведенному примеру расчета устойчивости машины против поперечного опрокидывания что дает возможность воспользоваться некоторыми полученными в расчете результатами.
Критичной с точки зрения потери устойчивости является одна из колесных пар машины для которой соотношение вертикальных и горизонтальных нагрузок в контакте гребня и поверхности катания рельса минимально (рисунок 4.3).
Рисунок 4.3 - Схема к расчету запаса устойчивости колесной пары против схода с рельсов:
P1д– вертикальная нагрузка на колесо с учетом динамики движения; Pд– статическая вертикальная нагрузка на колесо;Yр1д- передаваемая через буксы на колесную пару горизонтальная нагрузка от корпуса машины и рамы ходовой тележки (рамная сила)
Произведем оценку запаса устойчивости колесной пары против схода с рельсов по зависимости
где f– расчетный коэффициент сцепления боковой поверхности гребня колеса и головки рельсаf= 025;
– угол наклона боковой поверхности гребня к УВГР; DYNAMIC STOPFEXPRESS 09-3X = 60°.
При определении вертикальных нагрузок сделаем допущение что статические вертикальные нагрузки передаваемые через колеса на рельсы по модулю равны реакциям рельсовRAиRB деленных на количество колесных пар. DYNAMIC STOPFEXPRESS 09-3X имеет четырехосный экипаж. Тогда
Для упрощения расчета спроектируем силы действующие на машину на направление УВГР. Центробежную силуQи суммарную ветровую нагрузкуPв проектируем без учета угла α так как они на порядок меньше силы веса машиныG. Считаем что эта нагрузка распределяется равномерно между колесными парами и обусловливает рамную силуYр1д.
Тогда грубое оценочное значение рамной силы в статике
Учитывая динамику движения обусловленную погрешностями рихтовки пути и боковыми ударами при вхождении экипажа с прямой на кривую примемYр1д= 3 кН.
Расчетная вертикальная нагрузка на колесо (на рисунке 4.3 слева) кН
гдеPср– средняя нагрузка на колесо тележки Pср= G8 = 529748 = 6622 кН;
q– неподрессоренный вес приведенный к одному колесу; для оси с диаметром колес 450 мм и осевым редуктором пример;
kдин– коэффициент вертикальной динамики; для скорости 80 кмчkдин= 033;
Подставим полученные значения в формулу 4.6
Таким образом запас устойчивости против схода с рельсов машины DYNAMIC STOPFEXPRESS 09-3X при движении со скоростьюVм= 222 мс (80 кмч) в кривой радиусомR= 600 м с возвышением наружного рельсаhв= 012 м (120 мм) гарантируется.
ТЯГОВЫЙ РАСЧЕТ МАШИНЫ
Технической характеристикой шпалоподбивочной машины DYNAMIC STOPFEXPRESS 09-3X предусмотрены следующие режимы движения:
- движение в составе поезда в качестве прицепной несамоходной подвижной единицы со скоростью до 80 кмч;
- движение самоходом без нагрузки со скоростью до 40 кмч на площадке;
- движение на уклоне
- рабочее передвижение машины самоходом без нагрузки при ручном или автоматическом режиме. Скорость передвижения в этом режиме не превышает 5 кмч.
В начале движения необходимо преодолеть дополнительные сопротивления начала движения связанные с силами трения покоя и силами инерции возникающими при разгоне.
Произведем оценку возможности движения и начала движения (трогания) машины самоходом без нагрузки со скоростью 40 кмч на расчетном подъемеi= 0012 в кривой расчетного радиусаR= 150 м. Определим также длительную мощность кВт которую должен развивать двигатель машины передающий крутящий момент на переднюю ось машины.
Расчетная схема приведена на рисунке 5.1.
Рисунок 5.1 – Расчетная схема:
FkN Fkсц– развиваемые машиной касательные силы тяги по условиям сцепления ведущих колесных пар с рельсами и мощности силовой установки и тяговых электродвигателей;W1– основное сопротивление движению состава;W2– дополнительное сопротивление движению на расчетном уклоне;W3– дополнительное сопротивление движению в кривой;W4– дополнительное сопротивление движению возникающее при трогании с места
Расчет произведем сначала для случая движения с расчетной скоростью в принятых расчетных условиях. Для того чтобы происходило устойчивое движение рассматриваемой машины необходимо выполнить условия связанные с ограничением по сцеплению
где – коэффициент учитывающей необходимость наличия избыточной силы тяги .
Трогание машины с места возможно при выполнении условия наличия достаточного сцепления ведущих колес с рельсами
Кроме того необходимо выполнить условие отражающее наличие достаточной подводимой к ведущей колесной паре мощности
Основное сопротивление движению машины
где 1м – основное удельное сопротивление движению машины кН;
G– вес машиныG= 52974 кН.
Основное удельное сопротивление машины
Дополнительное сопротивление движению машины возникающее при движении на подъем
где 2– удельное сопротивление состава движению на подъем численно равное расчетному уклону .
Дополнительное сопротивление движению машины возникающее при движении в кривой
где 3– удельное сопротивление машины движению в кривой .
Расчетное сопротивление троганию машины с места
где 4– удельное сопротивление троганию машины с места кН.
гдеqо– усредненная по машине нагрузка на одну ось кНqо= (52974)4 = 13244 кН.
Машина имеет четыре колесные пары две из которых приводные поэтому сцепной вес машиныGсц=G*12 = 5297412 = 26487 кН.
Максимальное тяговое усилие развиваемое машиной DYNAMIC STOPFEXPRESS 09-3X по условию отсутствия буксования ведущих колесных пар
где сц– расчетный коэффициент сцепления колесной пары с рельсами; сц= 025.
Проверим выполнение условия (5.2)
Условие выполняется.
Касательная сила тяги развиваемая машиной по условию наличия достаточной мощности дизель-электрического агрегата
где Nдэ– мощность дизельного агрегата агрегата кВтNдэ= 220 кВт;
тр– коэффициент полезного действия гидромеханической трансмиссии привода колесных пар тр= 080;
kдо– коэффициент учитывающий затраты энергии на привод вспомогательного оборудования (компрессора тормозной системы)kдо= 09;
Vм– расчетная скорость движения машины мсVм= 111 мс (40 кмч).
Проверим выполнение условия (5.3)
Выполненный тяговый расчет позволяет сделать выводы:
обеспечивается устойчивое движение и трогание с места машины по условиям наличия достаточного сцепления колесных пар с рельсами;
мощности дизель-электрического агрегата достаточно чтобы обеспечить устойчивое движение машины на затяжном подъеме крутизной
устойчивое движение машины гарантируется в прямой на площадке когда действует только основное сопротивление движению.
ТЕХНИКА БЕЗОПАСНОСТИ И ЭКОЛОГИЧЕСКАЯ БЕЗОПАСНОСТЬ ПРИ РАБОТЕ МАШИНЫ
Требования безопасности перед началом работы:
Осмотреть привести в порядок и надеть спецодежду. Застегнуть и заправить ее так чтобы она не имела свисающих и развевающихся концов и не стесняла движений.
Убедиться в исправности и комплектности средств индивидуальной защиты.
Пройти предсменный медицинский осмотр. Получить направление на работу от механика по эксплуатации выправочно-подбивочно-рихтовочной машины.
Получить от машиниста сдающего смену сведения о неполадках которые наблюдались в течение предыдущей смены и мерах принятых для их устранения. Совместно с машинистом сдающим смену осмотреть и проверить выправочно-подбивочно-рихтовочную машину (при сменной работе).
При односменной работе необходимо проверить состояние выправочно-подбивочно-рихтовочной машины.
Проверить наличие и исправность ручного инструмента аптечки и средств пожаротушения. На шпалоподбивочной машине должен быть установлен углекислотный огнетушитель.
Убедиться в отсутствии людей около выправочно-подбивочно-рихтовочной машины подать звуковой сигнал и запустить двигатель.
Опробовать работу всех механизмов. Устранить неисправности обнаруженные при осмотре машины.
Требования безопасности во время работы:
Во время работы машинист своими действиями должен обеспечить безопасную и безаварийную работу обслуживаемой им машины.
К месту работы выправочно-подбивочно-рихтовочная машина транспортируется своим ходом со скоростью не более 80 кмч - по перегонам и не более 10 кмч - по стрелочным переводам.
Прибыв на место работы получить от мастера пути задание на работу и инструктаж по технике безопасности связанный с особенностями работы.
Выполнение работ с применением выправочно-подбивочно-рихтовочной машины должно производиться на тупике или перегоне закрытом для движения поездов под руководством и постоянным наблюдением руководителя работ (мастера бригадира пути) который несет ответственность за безопасное производство работ.
Выезд выправочно-подбивочно-рихтовочной машины на закрытый перегон (тупик) и возвращение на станцию производятся по разрешению оформленному на бланке (белого цвета с красной полосой по диагонали) с выдачей предупреждения о порядке скорости следования и пункта остановки.
При работе на перегоне и тупике места работы должны быть ограждены в соответствии с действующей инструкцией по сигнализации.
У мест работы выправочно-подбивочно-рихтовочной машины должен выставляться сигналист для оповещения работающих о приближении поездов по соседнему пути. Оповещение производится сигналом рожка.
В темное время суток место работы выправочно-подбивочно-рихтовочной машины должно быть освещено.
При приближении поездов по соседнему пути все рабочие должны сойти с междупутья внутрь колеи закрытого пути или на обочину противоположную действующему пути.
Работа выправочно-подбивочно-рихтовочной машины во время прохода поездов должна быть прекращена.
При дистанционном управлении выправочно-подбивочно-рихтовочной машиной машинист ВПРС должен находиться около рабочего органа машины на обочине земляного полотна с полевой стороны.
находиться в междупутье во время работы машины;
работать на шпалоподбивочной машине в сильный туман снегопад и т.д.;
находиться ближе 5 м спереди или сзади шпалоподбивочной машины во время ее работы;
производить крепление смазку и регулировку рабочих узлов во время работы выправочно-подбивочно-рихтовочной машины;
подлезать под машину приподнятую на гидравлических домкратах;
производить осмотр рабочих узлов машины со стороны соседнего пути не убедившись в отсутствии проходящих поездов.
Требования безопасности в аварийных ситуациях:
При сходе выправочно-подбивочно-рихтовочной машины с железнодорожного пути:
сообщить об этом диспетчеру указав место схода и возможность движения составов по соседним путям;
ожидать прибытия ремонтной бригады.
При пожаре приступить к тушению очага пожара имеющимися средствами пожаротушения; сообщить об этом по телефону или другими средствами связи диспетчеру или мастеру (начальнику) смены.
При обрыве провода запрещается приближаться к опасному месту на расстояние ближе 8 м. При этом необходимо принять меры исключающие попадание других работников в опасную зону и сообщить о случившемся диспетчеру или другому должностному лицу.
Уходить из зоны растекания тока следует короткими шажками не отрывая одной ноги от другой.
Требования безопасности по окончании работы:
Возвращение выправочно-подбивочно-рихтовочной машины на станцию после окончания работы должно производиться в полном соответствии с выданными поездными документами.
Снимать с пути сигналы остановки поездов разрешается только после уборки машины и приспособлений с железнодорожного пути за пределы габарита приближения строений.
Путевые машины с ДВС загрязняют воздух оксидом углерода оксидами азота и серы углеводородами альдегидами сажей а также свинцом и его соединениями. Топливо и отработавшие газы двигателей путевых машин по-разному влияют на организм человека но наиболее токсичными являются свинец и его соединения.
Оксид азота в соединении с водяными парами образует азотную кислоту которая раздражает легочную ткань что приводит к хроническим заболеваниям. Диоксид азота раздражает слизистую оболочку глаз легких и вызывает необратимые изменения в сердечнососудистой системе. Соединения свинца вызывают в организме нарушения в обмене веществ и кроветворных органах.
Загрязнение окружающей среды токсичными компонентами отработавших газов приводит к большим экономическим потерям. Это связано прежде всего с тем что токсичные вещества вызывают нарушения в росте растений приводят к снижению урожаев и потерям в животноводстве.
Непосредственную опасность для растений представляют диоксид серы оксид азота продукты фотохимических реакций и этилен.
Грунтовые и поверхностные воды в большей степени подвержены опасности загрязнения топливом маслами и смазочными материалами. Пленка из углеводородов на поверхности воды затрудняет процессы окисления отрицательно влияет на живые организмы и изменяет качество воды.
Отработавшие газы способствуют ускорению процессов разрушения изделий из пластмассы и резины оцинкованных поверхностей и черных металлов а также покраски облицовки и конструкции зданий.
На концентрацию в воздухе токсичных веществ влияют сорт топлива тип двигателя скорость и равномерность движения состав парка машин и интенсивность движения возможности распределения этих продуктов в атмосфере.
Еще одним фактором воздействия транспорта на окружающую среду и человека является шум создаваемый двигателем внутреннего сгорания.
Поэтому для снижения экологической нагрузки на окружающую среду от путевых машин очень важно поддержание в течение всего срока службы экологических параметров заложенных заводом-изготовителем.
Так разрабатываются методы повышения к.п.д. существующих ДВС путем создания конструкции регулирования степени сжатия и рабочего объема. Теоретические и экспериментальные исследования показывают что путем оптимизации степени сжатия и рабочего объема ДВС может быть улучшена эксплуатационная топливная экономичность и обеспечено снижение выброса парниковых газов (СО2) в условиях городского движения от 20 до 40 %.
Перспективы альтернативного топлива таковы что уже сегодня мировые автопроизводители говорят о внедрении к 2010 году порядка 50 различных моделей работающих на альтернативном виде горючего. В Европе к примеру особенно активны в этой области компании Mercedes-Benz BMW MAN. А к 2020 году согласно резолюции ООН нацелившей страны Европы на переход автомобилей на альтернативные виды моторного топлива ожидается увеличение «альтернативщиков» до 23% всего автопарка из них 10% (порядка 235 млн. единиц) – на природном газе.
В настоящее время также разрабатываются конструкции гидридных силовых установок что может положительно сказаться на экологии.
В данном курсовом проекте была рассмотрена выправочно-подбивочно-рихтовочная машина DYNAMIC STOPFEXPRESS 09-3X в качестве машины для подбивки балласта под шпалами предназначенная для уплотнения балласта под шпалами при строительстве реконструкции капитальном и среднем ремонтах а также текущем содержаниипути. Были рассчитаны основные параметры машины изучена конструкция основных узлов и агрегатов произведен расчет подбивочных блоков а также тяговый расчет машины и расчет на устойчивость в транспортном и рабочем положении.
Данный курсовой проект развивает способность к логическому мышлению и саморазвитию помогает развить навык которые понадобятся в последующей работе по инженерной специальности.
Машины и механизмы для путевого хозяйства: Учебник для техникумов
ж.-д. трансп. С. А. Соломонов В. П. Хабаров Л. Я. Малицкий Н. М. Нуждин; Под ред. С. А. Соломонова. — 3-е изд. перераб. и доп. М.: Транспорт 1984. 440 с.
Путевые машины: Учебник для вузов ж.-д. транс
С.А. Соломонов. М.В.Попович. В.М. Бугаенко и др. Под ред. С.А. Соломонова. — М.: Желдорнтдат 2000 —- 756 с.
Исаев К. С. Федулов В. Ф. Щекотков Ю. М. Машинизация текущего содержания пути. М. : Транспорт 1981.
Совершенствование организации и механизации путевых работ Под ред. К. И. Исаева. М.: Транспорт 1976.
Механизированная выправка и подбивка железнодорожного пути : учеб. пособие М. В. Попович [н др.]; под ред. М. В. Поповича. - Л.: ЛИИЖТ 1984. -102 с.
Гребенюк П. Т. Тяговые расчеты. Справочник П. Т. Гребенюк А. Н. Долганова А. Н. Скворцова: под ред. П. Т. Гребенюка. - М.: Транспорт 1987. - 272 с.
Фришман М. А. Конструкции железнодорожного пути и его содержание
М.А. Фришман Н. Л. Пономаренко С. И. Финицкий. - М.: Транспорт. 1987 350 с.
Гидроцилиндры. Конструкции и расчет Марутов В.А. Павловский С.А.
Машиностроение1966г.