Восстановления балки задней оси





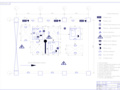
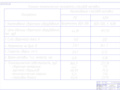
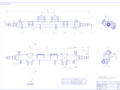
- Добавлен: 25.10.2022
- Размер: 2 MB
- Закачек: 1
Описание
Состав проекта
![]() |
![]() |
![]() ![]() ![]() |
![]() ![]() ![]() |
![]() ![]() ![]() |
![]() ![]() ![]() |
![]() ![]() ![]() |
![]() ![]() ![]() |
![]() ![]() ![]() |
![]() ![]() ![]() |
![]() ![]() ![]() |
![]() ![]() ![]() |
![]() ![]() ![]() |
![]() ![]() ![]() |
![]() ![]() ![]() |
![]() |
![]() ![]() |
![]() ![]() |
![]() ![]() ![]() ![]() |
![]() ![]() ![]() ![]() |
![]() ![]() |
![]() ![]() ![]() ![]() |
![]() ![]() ![]() ![]() |
![]() ![]() ![]() ![]() |
![]() ![]() |
![]() ![]() |
![]() ![]() ![]() ![]() |
![]() ![]() |
![]() ![]() |
![]() ![]() ![]() ![]() |
![]() ![]() ![]() ![]() |
![]() ![]() |
![]() ![]() ![]() ![]() |
![]() ![]() |
![]() ![]() ![]() ![]() |
![]() ![]() ![]() ![]() |
![]() ![]() |
![]() ![]() |
Дополнительная информация
ТИТУС.docx
ФЕДЕРАЛЬНОЕ ГОСУДАРСТВЕННОЕ БЮДЖЕТНОЕ ОБРАЗОВАТЕЛЬНОЕ УЧРЕЖДЕНИЕ ВЫСШЕГО ПРОФЕССИОНАЛЬНОГО ОБРАЗОВАНИЯ
«ТЮМЕНСКИЙ ГОСУДАРСТВЕННЫЙ НЕФТЕГАЗОВЫЙ УНИВЕРСИТЕТ»
Кафедра «Транспорт углеводородных ресурсов»
ПОЯСНИТЕЛЬНАЯ ЗАПИСКА
к дипломному проекту на тему:
«Разработка технологического плана участка по наплавке балки задней оси БЗМ-10»
Студент группы СПз-06
6 Безопасность и экологичность проекта - (Ершов).doc
1. Обеспечение безопасности работающих
1.1. Характеристика условий труда
Вредные вещества - вещества которые при контакте с организмом человека могут вызвать профессиональные заболевания или отклонения в состоянии здоровья обнаруживаемые современными методами как в процессе воздействия вещества так и в отдаленные сроки жизни настоящего и последующих поколений.
Рабочая зона - пространство высотой не менее 2 м над уровнем пола или площадки на котором находятся места постоянного или временного (непостоянного) пребывания работающих. На постоянном рабочем месте работающий находится большую часть своего рабочего времени (более 50 % или более 2 ч непрерывно). Если при этом работа осуществляется в различных пунктах рабочей зоны постоянным рабочим местом считается вся рабочая зона.
ПДК - концентрация вредного вещества которая при ежедневной (кроме выходных дней) работе в течение 8 ч и не более 40 ч в неделю в течение всего рабочего стажа не должна вызывать заболеваний или отклонений в состоянии здоровья обнаруживаемых современными методами исследований в процессе работы или в отдаленные сроки жизни настоящего и последующего поколений. Воздействие вредного вещества на уровне ПДК не исключает нарушение состояния здоровья у лиц с повышенной чувствительностью.
ПДК устанавливаются в виде максимально разовых и среднесменных нормативов.
Для веществ способных вызывать преимущественно хронические интоксикации (фиброгенные пыли аэрозоли дезинтеграции металлов и др.) устанавливаются среднесменные ПДК для веществ с остронаправленным токсическим эффектом (ферментные раздражающие яды и др.) устанавливаются максимальные разовые концентрации; для веществ при воздействии которых возможно развитие как хронических так и острых интоксикаций устанавливаются наряду с максимально разовыми и среднесменные ПДК.
Среднесменная ПДК - средняя концентрация полученная при непрерывном или прерывистом отборе проб воздуха при суммарном времени не менее 75 % продолжительности рабочей смены или концентрация средневзвешенная во времени длительности всей смены в зоне дыхания работающих на местах постоянного или временного их пребывания.
При производстве наплавке могут возникнуть следующие опасные производственные факторы:
Основными видами производственного травматизма на данном предприятии являются: поражение электрическим током действие лучистой энергии отравление поражение при взрыве и ряд других факторов связанных с производством сварочных работ (возникновение пожаров ожоги расплавленным металлом).
Поражение электрическим током может произойти как непосредственно во время сварки так и в процессе подключения источников питания а также при работе на неисправном и незаземленном оборудовании. Характер и степень поражения зависит от напряжения и тока электросопротивления тела человека и наличия защитных средств. Ток 0.05 А и выше является опасным и может вызвать смертельный исход.
Наиболее опасным является прикосновение к двум фазам одной и той же установки. Сопротивление человеческого тела непостоянно и зависит от многих причин. Оно резко снижается при переутомлении заболевании и принятии алкоголя.
Излучение лучистой энергии дуги при сварке в защитных газах чрезвычайно интенсивны. Тепловая радиация на уровне рук при сварке неплавящимся электродом составляет 1.5 калсм2мин и на уровне лица 1-1.5 калсм2мин. Это вызывает ожоги открытых частей тела и электроофтальмию.
Излучение дуги так же вредно действует на сетчатую и роговую оболочку глаз. Длительное воздействие дуги на незащищенный глаз вызывает через 1.5-2 ч сильные боли в глазах слезотечение через 1-3 ч вызывает ожоги на коже наподобие солнечного. Видимые световые лучи при коротком облучении действуют ослепляющее а при длительном вызывают ослабление зрения.
По требованиям руководящей документации опасные производственные факторы должны быть минимизированы и не превышать допустимых значений.
К химическим факторам относятся пары расплавленного основного металла пары от сгорания сварочного материала (проволоки и электродов).
Нормативные требования на предельно допустимую концентрацию вредных веществ в воздухе рабочей зоны приведены в ГОСТ 12.1.005-88.
Меры по защите от воздействия вредных производственных веществ:
Для оздоровления воздушной среды на производстве используются различные системы вентиляции такие как местные отсосы общеобменная вентиляция и т.д. Для индивидуальной защиты органов дыхания сварщиков используются бесклапанные респираторы ШБ-1 "Лепесток" по ГОСТ 12.4.028-76.
Общие требования по контролю за содержанием вредных веществ в воздухе:
отбор проб должен проводиться в зоне дыхания при характерных производственных условиях;
для каждого производственного участка должны быть определены вещества которые могут выделяться в воздухе рабочей зоны;
при наличии идентичного оборудования или выполнения одинаковых операций контроль проводится выборочно на отдельных рабочих местах расположенных в центре и по периферии помещения;
результаты полученные при однократном отборе или при усреднении последовательно отобранных проб сравнивают с величинами ПДК.
На данном предприятии содержание вредных веществ полностью удовлетворяет нормам и составляет для СО2 – 13 мгм3.
К физическим факторам относят колебания передаваемые от сварочной дуги на руки сварщика при ручной дуговой сварке а также статическая нагрузка на руки сварщика при сварке. Ввиду того что при производстве металлоконструкцци и при ее восстановительном ремонте используются в основном автоматическая и полуавтоматическая сварка влияние таких колебаний минимально. Ручным дуговым способом осуществляется постановка прихваток что составляет 15% от общего времени сварочных работ следовательно предлагаемой в данном дипломном проекте технологией изготовления обеспечивается минимальное воздействие от сварочной дуги на сварщика т.к. основная сварка выполняется в автоматическом и полуавтоматическом режимах.
Общие санитарно – гигиенические требования к температуре относительной влажности и скорости движения воздуха регламентируют ГОСТ 12.1.005-88 и СанПиН 2.2.4.548-96. Работы по сборке и сварке балки будут относиться к категории средней тяжести – IIа. Величины показателей микроклимата необходимые для оптимальной работы представлены в табл. 6.1.
Нормы температуры влажности и скорости движения воздуха
Относительная влажность%
Микроклимат предприятия полностью соответствует всем необходимым нормам и требованиям и обеспечивает оптимальные условия труда рабочим.
Нормативные требования по уровню шума изложены в СН 2.2.42.1.8.562-96. Допустимые уровни звукового давления в октавных полосах частот уровни звука и эквивалентные уровни звука на рабочих местах следует принимать: для широкополосного постоянного и непостоянного (кроме импульсного) шума — по таблице 6.2 согласно ГОСТ 12.1.003-83.
Допустимые уровни звукового давления
Уровни звукового давления дБ в октавных полосах со среднегеометрическими частотами в Гц
Уровни звука и эквивалентные уровни звука
Предприятия учреждения и организации
Постоянные рабочие места и рабочие зоны в производственных помещениях и на территории предприятий
Запрещается даже кратковременное пребывание в зонах с октавными уровнями звукового давления свыше 135 дБ в любой октавной полосе.
Меры борьбы с повышенным уровнем шума подразделяются на:
- методы снижения шума на пути к распространению от источника;
- снижение шума в источнике образования;
- средства индивидуальной защиты.
На данном предприятии для уменьшения влияния шума достаточно применения следующих мер:
- метод изоляции и звукоизоляции звукопоглощение;
- вывод трансформаторов выпрямителей и других источников питания из зоны рабочего помещения;
- применение средств индивидуальной защиты (ушные вкладыши наушники шлемофоны).
Уровень звукового давления на предприятии входит в допустимые пределы.
Требования к освещению помещений промышленных предприятий (КЕО нормируемая освещенность допустимые сочетания показателей ослепленности и коэффициента пульсации освещенности) следует принимать по табл. 6.3 в соответствии со СНиП 23.05.95.
Параметры освещенности
Характеристика зрительной работы
Наименьший или эквивалентный размер объекта различения мм
Разряд зрительной работы
Под разряд зрительной работы
Искусственное освещение
Естественное освещение
Сочетание нормируемых величин показателя ослепленности и коэффициента пульсации
При системе комбинированного освещения лк
Освещенность определяется отношением светового потока падающего на поверхность к площади освещаемой поверхности. Для искусственного освещения применяют осветительные установки с газоразделительными лампами. По анализу и установлению видов освещения определяют систему освещения. Выбор системы освещения предполагает решение вопроса о размещении источников света на производственной площади. При этом возникает необходимость одновременного решения вопроса выбора светильников по характеристикам таких как дальность действия допустимая высота подвеса единичная мощность. Общее равномерное освещение должно устраиваться в цехах где производят сборочно-сварочные работы крупных изделий или изделий которые состоят из большого количества малых сборочных единиц. Комбинированное освещение следует предусматривать на работах высокой и наивысшей точности причем устанавливать его таким образом чтобы выполнялись все требования. Для освещения высоких цехов как правило рекомендуется использовать газоразрядные лампы ДРЛ ДРИ; для цехов высотой до 4 м люминесцентные лампы. Допускается применение ламп накаливания. Для местного освещения должны применятся светильники с непрозрачными отражателями имеющие защитный угол не менее 30°. Если светильник расположен ниже глаз сварщика то защитный угол может быть в пределах 10-30°.
На данном предприятии применяется комбинированная система освещения соответствующая СНиП 23-05-95.
Классификация помещений по взрывопожарной и пожарной опасности
Характеристика веществ и материалов (образующихся) в помещении
взрывопожаро-опасная
Горючие газы легковоспламеняющиеся жидкости с температурой вспышки не более 28 С в таком количестве что могут образовать взрывоопасные парогазовоздушные смеси при воспламенении которых развивается расчетное избыточное давление взрыва в помещении превышающее 5 кПа.
Горючие пыли или волокна легковоспламеняющиеся жидкости с температурой вспышки более 28 С в таком количестве что могут образовывать взрывоопасные пылевоздушные или паровоздушные смеси при воспламенении которых развивается расчетное избыточное давление взрыва в помещении превышающее 5 кПа.
Горючие и трудно горючие жидкости твердые горючие и трудно горючие вещества способные при взаимодействии с водой кислородом воздуха или друг с другом только гореть при условии при условии что помещения в которых они имеются в наличии или применяются не относятся к категориям А или Б.
Негорючие вещества и материалы в горячем раскаленном Ии расплавленном состоянии процесс обработки которых сопровождается выделением лучистого тепла искр и пламени;
горючие газы жидкости и твердые вещества которые сжигаются или утилизируются в качестве топлива.
Негорючие вещества и материалы в холодном состоянии.
Цех №6 где проводятся сварочные наплавочные и токарные операции по взрывопожарной и пожарной опасности в соответствии с НПБ 105-95 относится к категории Г.
Для обеспечения пожарной безопасности на предприятии ЦБПО БНО предусмотрены пожарная сигнализация аварийное отключение электричества аварийное освещение. Средства пожаротушения: пожарный песок емкость с пожарной водой пожарный стенд пенные и порошковые огнетушители.
1.2. Электробезопасность и молниезащита.
Эксплуатация большей части сварочного оборудования связана с использованием электрической энергии.
Электрический ток оказывает на человека:
Термическое воздействие тока проявляется в ожогах нагреве кровеносных сосудов и других органов в результате чего в них возникает функциональные расстройства.
Электролитическое воздействие тока характеризуется разложением крови и других органических жидкостей вызывая нарушение их физико - химического состава.
Механическое действие тока проявляется в повреждениях (разрыве расслоении и др.) различных тканей организма в результате электродинамического эффекта.
Биологическое действие тока на живую ткань выражается в опасном возбуждении клеток и тканей организма сопровождающимся непроизвольными судорожными сокращениями мышц.
К средствам обеспечения электробезопасности относятся:
) Организационные мероприятия;
) Организационно-технические мероприятия;
) Технические средства.
К организационным мероприятиям относится: обучение людей правилам электробезопасности нарядно-допускная система надзор за соблюдением правил электробезопасности систематическая проверка исправности электроустановок.
К организационно-техническим мероприятиям относится: защитное заземление зануление выравнивание потенциалов малое напряжение электрическое разделение сетей защитное отключение изоляция оградительные устройства предупредительная сигнализация защитные предохранительные приспособления.
К техническим средствам относятся средства коллективной и индивидуальной защиты.
Электробезопасность обеспечивается путем обеспечения защиты персонала от соприкосновения с токоведущими частями а оборудования – от попадания внутрь посторонних тел и воды.
Расстояние между стальными контактами рукавами трубопроводами с кислородом должны быть не менее 05м а с горючими газами - не менее 1м. Нельзя прикасаться к токоведущим частям электрическим проводам (даже изолированным) кабелям клеммам наступать на лежащие на земле переносные электропровода т.к. при нарушении их изоляции может произойти поражение электрическим током.
Для обеспечения электробезопасности предусмотрены следующие требования:
токоведущие части сварочной цепи должны быть надежно изолированы: сопротивление изоляции должно быть не менее 05 МОм;
корпуса электросварочного оборудования агрегатов обратного провода должны быть заземлены; защитное заземление осуществляется путем присоединения корпуса сварочных источников питания снабженного специальным болтом к проводу заземляющего устройства а также заземлением свариваемого изделия;
однопостовые сварочные агрегаты со стороны питающей сети должны быть защищены предохранителями;
все рукоятки кнопки управления которые могут оказаться под напряжением должны быть выполнены из диэлектрического материала или надежно изолированы от корпуса;
во избежание накопления статического электричества необходимо: заземлять оборудование коммуникации и емкости в которых оно может возникнуть; применять материалы увеличивающие электропроводность; общее и местное увлажнение воздуха в опасных местах помещений до 75% относительной влажности и т.д.
Перед началом работы необходимо убедится в том что:
- ручка держателя хорошо изолирована и имеет надежный контакт с проводом;
- изоляция проводов не нарушена;
- корпус сварочной машины и зажим обратного провода надежно заземлены.
Затем следует проверить наличие и исправность защитных кожухов на рубильниках и предохранителях. Включать и выключать рубильник необходимо быстро. Кроме того следует проверить исправность изоляции сварочных проводов сварочного инструмента и оборудования а также надежность всех соединений сварочной цепи.
Во время работы при электросварке руки рукавицы обувь и одежда должны быть всегда сухими.
Рабочее место электросварщика должно быть защищено от атмосферных осадков. В электросварочных аппаратах и источниках их питания элементы находящиеся под напряжением должны быть закрыты оградительными устройствами.
Электросварочная установка (преобразователь сварочный трансформатор и т.п.) должна присоединяться к источнику питания через рубильник и предохранители или автоматический выключатель а при напряжении холостого хода более 70 В должно применяться автоматическое отключение сварочного трансформатора.
Металлические части электросварочного оборудования не находящиеся под напряжением а также свариваемые изделия и конструкции на все время сварки должны быть заземлены.
В качестве обратного провода или его элементов могут быть использованы стальные шины и конструкции если их сечение обеспечивает безопасное по условиям нагрева протекание сварочного тока.
Соединение между собой отдельных элементов применяемых в качестве обратного провода должно быть надежным и выполняться на болтах зажимах или сваркой.
Запрещается использовать провода сети заземления трубы санитарно-технических сетей (водопровод газопровод и др.) металлические конструкции зданий технологическое оборудование в качестве обратного провода электросварки.
На предприятии конструкция электроустановок полностью соответствует условиям их эксплуатации и обеспечивает защиту персонала от соприкосновения с токоведущими и движущимися частями а оборудования – от попадания внутрь посторонних твердых тел и воды.
Всё электрооборудование оборудовано заземлением либо занулением то есть преднамеренным электрическим соединением с нулевым защитным проводником металлических нетоковедущих частей которые могут оказаться под напряжением.
Также оборудование снабжено защитным отключением – быстродействующей защитой обеспечивающей автоматическое отключение электроустановки при возникновении в ней опасности поражения электрическим током.
Вся электрическая проводка заизолирована и проложена таким образом чтобы не мешать работе оборудования сварщиков и перемещению по цеху. Проводка проложена по специальным каналам находящихся в полу цеха.
Определение необходимой зоны защиты
- проводится по формуле 6.1.
Формула 6.1 предусматривает прямоугольную форму зданий.
h – наибольшая высота здания или сооружения м;
S L – соответственно ширина и длинна сооружения м;
n – среднегодовое число ударов молнии в 1 км2 земной поверхности в месте нахождения здания или сооружения.
Следовательно категория устройства молниезащиты III тип зоны защиты Б.
III категория – здания и сооружения защищаются от прямых ударов молний и заноса высоких потенциалов через наземные металлические коммуникации.
1.3. Расположение оборудования вспомогательных и бытовых помещений.
В цехе предусмотрены вспомогательные и бытовые помещения.
К числу бытовых помещений относятся:
склад обработанных деталей;
склад наплавленных изделий;
склад сварочных материалов;
склад готовой продукции.
Склады оборудованы пожарной сигнализацией основное назначение этой сигнализации в том чтобы предупредить персонал об общей пожарной тревоги или другом ЧП.
Склад сварочных материалов предназначен для хранения сварочной проволоки защитного газа а также электродов. Данный участок оборудован пожарным щитом предупредительной сигнализацией а также укомплектован порошковыми огнетушителями.
Склад заготовок предназначен для хранения осей подготовленных под наплавку.
К числу вспомогательных помещений относят:
-комната планерки цеха;
-комнату отдыха рабочих;
Все вышеперечисленные помещения оборудованы средствами пожаротушения и средствами централизованного оповещения при ЧП и ЧС. Также вспомогательные помещения укомплектованы средствами индивидуальной защиты и аптечками первой медицинской помощи (в количестве 3 комплектов).
Расстановка электрооборудования указана в графической части дипломного проекта.
Электрооборудование расстановлено в соответствии с ходом направлением технологического процесса наплавки.
1.4. Средства индивидуальной защиты и компенсация производственных вредностей.
Согласно ГОСТ 12.1.013-78 рабочие обслуживающие электроустановки должны пользоваться средствами индивидуальной защиты предусмотренными типовыми отраслевыми нормами. К общим средствам индивидуальной защиты сварщиков от поражения электрическим током относятся: перчатки которые изготавливают в соответствии с требованиями ЕУ 38-05977-76.
В комплект средств индивидуальной защиты сварщика выполняющего сварочные работы входят:
респиратор – для защиты дыхательных органов от паров металлов;
сварочная маска – для защиты глаз сварщика от вредного излучения исходящего от сварочной дуги в процессе наплавки;
спецодежда – для защиты тела сварщика от возможных брызг расплавленного металла;
индивидуальные наушники – необходимы в случаях сильного шума для защиты органов слуха сварщика.
Комплекты средств индивидуальной защиты сварщика выдаются при поступлении на работы вместе со спецодеждой. Хранение спецодежды осуществляется в раздевалке в индивидуальном шкафчике.
Коврики изготавливаемые по ГОСТ 4997-75 предназначены для защиты от поражения электрическим током. Они являются дополнительным защитным средством при работе на электроустановках с напряжением до 1кВ применяются при температурах от -15 до +40 °С.
К средствам коллективной защиты относятся ограждающие защитные средства. Они предназначены для временного ограждения токоведущих частей находящихся под напряжением. К ним относятся щиты барьеры ограждения – клетки а также временные переносные заземления которые делают невозможным появление напряжения на отключенном оборудовании.
Принятые на данном производстве вышеуказанные мероприятия исключают поражение работающих электрическим током.
2. Экологичность проекта
При автоматической наплавке под флюсом проволокой НП-30ХГСА выделяются следующие основные вредные вещества: пыль неорганическая оксид марганца оксид хрома оксид никеля и углекислый газ.
Расчет выбросов вредных веществ при сварке проведен согласно «Методика расчета выделений (выбросов) загрязняющих веществ в атмосферу при сварочных работах».
Валовый выброс загрязняющих веществ при сварке определяется по формуле:
где - удельный показатель выделяемого загрязняющего вещества сварочного материала гкг;
В – количество сварочного материала используемого при сварке кг.
Максимальный разовый выброс определяется по формуле (6.2):
b – максимальное количество сварного материала расходуемого в течении дня кг;
t – время затрачиваемое на сварку в течении рабочего дня час.
Валовой выброс оксида хрома при электрошлаковой сварке составит:
Мо.х. = 002 × 4792 = 00000096 т.
Максимальный разовый выброс оксида хрома:
Результаты расчета выбросов вредных веществ при автоматической сварке под флюсом приведены в табл. 6.5.
Выбросы вредных веществ при автоматической сварке под флюсом
Удельный показатель гкг
Максимально разовый выброс гс
Таким образом выбросы вредных веществ при автоматической сварке под флюсом данной конструкции находятся в пределах допустимых норм (12.1.005 – 88).
На предприятии особое внимание уделяется экологии применяемых технологий а именно воздействию применяемых технологий изготовления продукции на окружающую среду. На предприятии предусмотрена общая и индивидуальная вытяжки причем все газы и производственная пыль втягиваемые вытяжкой проводятся по продольному каналу в очистные сооружения – скрубберы.
На предприятии существуют два вида скрубберов:
Использование очистных сооружений типа «скруббер» обеспечивает минимальный выброс загрязнений в атмосферу и делает производство более экологичным.
3. Чрезвычайные ситуации (ЧС) и гражданская оборона (ГО)
По статистическим материалам можно определить наиболее вероятные внутренние и внешние чрезвычайные ситуации (ЧС). Для сварочного участка характерны ЧС техногенного характера:
— внутренние (пожары отключение электроэнергии и тепла террористический акт взрыв газовоздушной смеси)
— внешние (разлив аварийно химически опасных веществ).
Отключение электроэнергии.
При отключении электроэнергии все работы на сварочном участке прекращаются.
Прекращается эксплуатация электрооборудования ввиду отсутствия аварийного генератора.
Определение вероятных параметров ударной волны при взрыве газовоздушной смеси.
Раскрой материала осуществляется с помощью кислородной резки. Предполагается взрыв 005 тонны пропан-бутановой смеси при не соблюдении техники безопасности («обратный хлопок»).
При взрыве газовоздушной смеси выделяется зона детонационной волны с радиусом R1 и зону ударной волны. Определяются также: радиус смертельного поражения людей Rспл.; радиус безопасного удаления Rбу.; радиус предельно допустимой взрывобезопасной концентрации газа Rпдвк.
Избыточное давление в зоне детонации волны ΔРф1 = 900 кПа.
Радиус зоны детонации волны R1 определяется по формуле:
R1 = 185 м где (6.3)
Q – количество газа т.
Радиус зоны смертельного поражения людей Rспл. определяется по формуле:
Rспл. = 30 = 1105 м.
Радиус безопасного удаления Rбу определяется из выражения:
Rбу. = R1 12 м. (6.5)
Rбу. = 68 12 = 816 м.
Степень разрушения элементов объекта ΔР определяется по формуле:
где r2 – расстояние от центра взрыва до элемента объекта в зоне ударной волны м.
По табличным данным избыточное давление ΔРф = 58 кПа. При данном избыточном давлении будет иметь место разрушение средней степени металлического каркаса здания.
Определение глубины распространения аварийно химически опасных веществ (АХОВ).
Разлив хлора (50 тонн) при аварии на железной дороге находящейся на расстоянии 5 км от данного производственного участка. При оценке ситуации принимаются наихудшие метеоусловия: скорость ветра 1 мс; температура воздуха +20 0С направление ветра – сварочный цех.
При разливе 50 тонн хлора образуется первичное облако пара (мгновенное испарение) и вторичное облако пара (испарение слоя жидкости).
Эквивалентное количество вещества по первичному облаку QЭ1 определяем из выражения:
QЭ1 = К1 К3 Q0 т. (6.7)
где К1 – коэффициент зависящий от условий хранения АХОВ (для хлора К1 = 018);
К3 – коэффициент равный отношению пороговой токсодозы хлора к пороговой токсодозе другого АХОВ в данном случае К3 = 10;
Q – количество разлившегося при аварии вещества (Q = 50 т).
QЭ1 = 018 1 50 = 9 т.
Эквивалентное количество вещества по вторичному облаку QЭ2 определяется по формуле:
QЭ2 = (1 – К1) К К3 (Q0 (h02 d02)) т (6.8)
где К2 – коэффициент зависящий от свойств АХОВ (для хлора К2 = 0052);
d – плотность АХОВ тм3 (d = 1553) тм3;
h – толщина слоя АХОВ м (при свободном разливе принимается равной 005 м).
QЭ2 = (1 – 018) 00520052 10 (50 (00502 155302)) = 3784.
Определяется максимальное значение глубин зон заражения первичным Г1 и вторичным Г2 облаком АХОВ по приложению 3.1 [24]. Полная глубина зоны заражения Г определяется из выражения:
Г = Г’ + 05 Г’’ км. (6.9)
где Г’ – наибольшее число из Г1 и Г2;
Г’’ – наименьшее число из Г1 и Г2;
Г = 454 + 05 192 = 55 км.
Количество пострадавших при разливе хлора (50 тонн) принимается из расчета что пострадает 100 % из находящихся вне помещений и 50 % находящихся внутри помещений.
Террористический акт.
При возможно террористическом акте могут возникнуть следующие последствия: травмы и гибель людей повреждение оборудования частичное или полное разрушение строений.
Для предупреждения террористических актов необходимы следующие меры: при обнаружении каких-либо подозрительных предметов срочно сообщать в службу безопасности; усилить охрану; установить строгую пропускную систему.
Вывод: при работе на участке сборки и сварки восстановительного ремонта задней оси балки соблюдаются меры предосторожности. Электрооборудование заземлено и не имеет оголенных токоведущих проводов что исключает поражение работающих электрическим током.
Работающие на участке снабжаются средствами индивидуальной защиты. Средства пожаротушения находятся на видном и легко доступном месте. Соблюдаются меры по предупреждению возникновения чрезвычайных ситуаций и загрязнения окружающей среды. Учитывая всё выше сказанное делаем вывод что применяемые в проекте технические решения соответствуют нормам и требованиям безопасности и экологичности.
Выбросы при альтернативном способе наплавки АФ предлагаемом проектом являются ниже чем при РДС твердых отходов меньше следовательно проект эффективней.
Проектируемый вариант производства своими техническими решениями соответствует требуемым нормам производственной безопасности экологическим и санитарно- эпидемиологическим нормативам по оздоровлению воздушной среды на рабочих местах в цехе и требованиям по предотвращению чрезвычайных ситуаций.
Режимы - расход (НАПЛАВКА).docx
Расход электродной проволоки:
где- потребность сварочной проволоки на единицу продукции кг;
- коэффициент использования проволоки по справочным данным ;
– масса наплавленного металла на единицу продукции (кг).
Потребность в сварочном флюсе зависит от расхода сварочной проволоки и определяется по формуле (2.16):
где- расход (масса) сварочного флюса на единицу продукции кг;
- коэффициент использования флюса по справочным данным .
Расход электродов для базового варианта наплавки определяется по формуле:
где - расход электродов с покрытием на единицу продукции кг;
- коэффициент расхода электродов определяется паспортным данным (17 гч).
6.1. Расчет режимов наплавки.
В процессе наплавки оси качество наплавленного металла форма валиков глубина проплавления металла зависят от выбранных режимов наплавки. Определяем силу сварочного тока Iсв.
При наплавке сила сварочного тока определяется по данным таблицы 2.7.
Диаметр наплавочной проволоки выбирается по данным таблицы 2.6.
Зависимость толщины наплавляемого слоя от диаметра электродной проволоки.
Толщина наплавляемого слоя мм
Диаметр электродной проволоки мм
Зависимость силы сварочного тока от диаметра детали и диаметра наплавочной проволоки
Сила тока Iсв (А) при диаметре электродной проволоки мм
При наплавки для снижения глубины проплавления коэффициент а≤30-40 Амм2. Диаметр сварочной проволоки выбирается таким чтобы он обеспечил максимальную производительность наплавки при требуемой глубине проплавления. Выбираем диаметр сварочной проволоки 2 мм.
Проанализировав данные таблицы 2.5 выбираем Iсв=320 А.
Определяем напряжение U по формуле 2.1:
Определим показатель характеризующий удельное значение скорости наплавки коэффициент наплавки Кн по формуле 2.2:
Определим толщину наплавляемого слоя:
Толщина наплавляемого слоя выбирается по таблице 2.1 в зависимости от диаметра сварочной проволоки.
Согласно данным таблицы 2.4 при диаметре электродной проволоки 20 мм толщина наплавляемого слоя составляет 4 мм.
Определяем скорость наплавки Vн.
Скорость наплавки определяем по формуле 2.3:
где F – площадь поперечного сечения валика см2 (при dпр=20 мм F=02 см2); γ – плотность металла шва гсм3.
Определим скорость вращения головки n по формуле 2.4:
Скорость подачи электродной проволоки определяется по формуле 2.5:
При увеличении вылета электродной проволоки повышается электрическое сопротивление цепи что приводит к росту коэффициента расплавления снижению тока наплавки а следовательно и глубины проплавления. Но при увеличении данного параметра ухудшается геометрия наплавленных валиков поэтому вылет электрода выбирается из пределов указанных в формуле 2.6.
Шаг наплавки определяется перекрытием валиков и влияет на волнистость наплавленного слоя:
S=(2-25)dПР мм (2.7)
Число проходов составляет 1 т.к износ поверхности оси составляет 18-23 мм.
Режимы наплавки оси задней балки БЗМ-10
Коэффициент наплавки гАч
Толщина наплавляемого слоя мм
Скорость наплавки мч
Скорость вращения сварочной головки обмин
Скорость подачи электродной проволоки мч
Расчет режима ручной дуговой наплавки покрытым электродом.
Учитывая то толщина наплавленного слоя (4 мм) равна 07 от диаметра электрода принимаем электрод диаметром 3 мм.
)Сварочный ток определим согласно следующей формуле:
где k- коэффициент зависящий от диаметра электрода (k=35-50);
)Определим плотность сварочного тока:
)Определяем оптимальное напряжение дуги:
) Для того чтобы рассчитать скорость сварки необходимо ввести значение коэффициента наплавки.
)Определим показатель характеризующий удельное значение скорости наплавки коэффициент наплавки Кн по формуле 2.2:
)Скорость наплавки определяем по формуле 2.3:
)где F – площадь поперечного сечения валика см2 (при dпр=30 мм F=09 см2); γ – плотность металла шва гсм3.
)Шаг наплавки определяется перекрытием валиков и влияет на волнистость наплавленного слоя:
)Число проходов составляет 1 т.к износ поверхности оси составляет 18-23 мм.
Во время процесса наплавки оси задней балки БЗМ-10 режимы могут регулироваться в пределах 10 %.
Проволока НП-30ХГСА + флюс ан348
Под флюсом: ВДУ506 + А -1408
3. Контроль качества при изготовлении изделия.doc
1. Требования к качеству сварных соединений.
Наплавленные оси подвергаются двум видам контроля: разрушающему и не разрушающему.
Не разрушающий контроль состоит из визуально измерительного контроля и ультразвуковой дефектоскопии. Последний вид контроля применяется не для всех изделий а лишь для изделий выбираемых из партии наплавленных в случайном порядке. Визуально-измерительному контролю подвергают все изделия без исключения.
Разрушающий контроль проводится при отработке технологии наплавки либо для изделий выбираемых в случайном порядке.
В общем случае для наплавленных поверхностей оси предъявляются следующие требования:
Размеры наплавленной поверхности должны полностью соответствовать размерам указанным в сборочном чертеже. С учетом допусков и отклонений в размерах.
На наплавленной поверхности не допускается наличие прожогов вмятин заусенцев трещин а также кратеров.
Наплавленная поверхность должна соответствовать должна иметь равномерную структуру.
Наличие внутренних дефектов таких как поры трещины непровары недопустимо.
Механические свойства наплавленной поверхности должны быть не ниже свойств основного металла (базовых значений).
Шероховатость обработанной поверхности должна соответствовать заданной.
2. Предварительный контроль.
Предварительному контролю подвергаются оси задних балок поступившие на наплавочный участок. Предметом контроля служит поверхность ступицы в месте посадки подшипников.
Предварительный контроль проводится в два этапа:
Контроль поступивших осей балок. В ходе проведения этого этапа предварительного контроля определяется степень износа поверхности ступицы также проверяется наличие загрязнений окалины и следов коррозии. Также контролю подвергается геометрия оси задней балки
Контроль осей задних балок после механической обработки. На данном этапе предварительного контроля предметом исследования является качество подготовленной (обработанной на токарно-винторезном станке) посадочной поверхности ступицы.
3. Операционный контроль.
Операционный (пооперационный) контроль состоит в наблюдении за выполнением и результатом каждой операции технологического процесса наплавки оси задней балки БЗМ-10.
В общем случае при наплавке оси задней балки операционный контроль состоит из следующих этапов:
Установка и закрепление оси задней балки БЗМ-10 во вращателе. В ходе выполнения этого этапа проверяется правильность установки и закрепления оси во вращателе. Также предметом контроля служит надежность закрепления и соблюдении соосности при установки оси задней балки БЗМ-10. Правильность установки дополнительной (удерживающей роликоопоры) также подвергается контролю ее положение должно соответствовать требованиям настоящей технологии (см. графическую часть ДП).
Наплавка. В ходе проведения наплавки контролю подвергается:
Правильность установки наплавочного оборудования;
соответствие установленных режимов расчетным;
правильность и очередность наложения слоев.
Термообработка. Проверке подвергается правильность установки режимов термообработки а также время ее проведения. Особого внимания заслуживает процесс охлаждения – скорость охлаждения не должна превышать расчетной т.к в противном случае возможно возникновение дефектов таких как трещины.
Механическая обработка. На данном этапе операционного контроля выполняется проверка соответствия установленных режимов токарно-винторезного станка 1М63-М расчетным.
4. Приемочный контроль.
4.1. Выбор метода контроля.
Геометрические размеры и форма поверхностей должны измеряться с помощью средств обеспечивающих погрешность не более 30% от установленного допуска на изготовление.
Габаритные размеры с следует определять путем суммирования размеров входящих в них сборочных единиц и деталей.
Контроль качества поверхностей на отсутствие плен закатов расслоений грубых рисок трещин снижающих качество и ухудшающих товарный вид должен проводиться путем визуального осмотра.
Обязательная проверка наличия содержания мест расположения клейм на сварных швах и маркировки (самостоятельно поставляемых сборочных единицах и деталях) должна осуществляться визуальным осмотром.
Контроль качества наплавленных поверхностей соединений возможно проводить следующими методами:
а) визуальным осмотром и измерением;
б) механическими испытаниями;
в) испытанием на стойкость против межкристаллитной коррозии;
г) металлографическими исследованиями;
д) стилоскопированием;
е) ультразвуковой дефектоскопией;
з) цветной или магнитопорошковой дефектоскопией;
и) другими методами (акустической эмиссией люминесцентным контролем определением содержания ферритной фазы и др.) предусмотренными в проекте.
Окончательный контроль наплавленных деталей (изделий) подвергающихся термической обработке должен проводиться после термической и механической обработки.
Контроль комплектности консервации окраски упаковки необходимо проводить путем сопоставления объема и качества выполненных работ с требованиями соответствующих стандартов и технических условий.
Разрушающий контроль необходимо проводить согласно требований ГОСТ 6996.
Методы определения механических свойств при следующих видах испытаний:
а) испытании металла различных участков сварного соединения и наплавленного металла на статическое (кратковременное) растяжение;
б) испытании металла различных участков сварного соединения и наплавленного металла на ударный изгиб (на надрезанных образцах);
в) испытании металла различных участков сварного соединения на стойкость против механического старения;
г) измерении твердости металла различных участков сварного соединения и наплавленного металла.
Виды испытаний типы образца и применение метода предусматривается в стандартах и технических условиях на продукцию устанавливающих технические требования на нее.
Допускается применять образцы и методы испытаний по международным стандартам ИСО 4136 ИСО 5173 ИСО 5177.
100% ВИК согласно РД 34.10.130-96;
100% УЗК (для выбранных образцов) согласно ГОСТ 14782.
4.2. Выбор параметров и схемы контроля.
Образцы для испытаний отбирают из проб вырезанных непосредственно из контролируемой конструкции или от специально сваренных для проведения испытаний контрольных соединений.
Если форма наплавленного слоя исключает возможность изготовления образцов данного типа то образцы могут быть отобраны от специально наплавленных плоских контрольных соединений.
При выполнении контрольных слоев характер подготовки под наплавку марка и толщина основного металла марки сварочных материалов положение шва в пространстве начальная температура основного металла режим наплавки и термической обработки должны полностью отвечать условиям изготовления контролируемого изделия или особому назначению испытания.
Для контрольных наплавки поверхностей выполняемых дуговой сваркой из плоских элементов ширина каждой свариваемой пластины если нет иных указаний в стандартах или другой технической документации должна быть не менее:
мм - при толщине металла до 4 мм;
мм « « « св. 4 до 10 мм;
0 мм « « « « 10 « 20 мм;
0 мм « « « « 20 « 50 мм;
0 мм « « « « 50 « 100 мм;
0 мм « « « « 100 мм.
Длина пластин определяется размерами и количеством подлежащих изготовлению образцов с учетом повторных испытаний припусков на ширину реза и последующую обработку и с добавлением длины неиспользуемых участков шва. Размеры неиспользуемых участков принимают равными:
- при ручной дуговой сварке покрытыми электродами и газовой сварке - не менее 20 мм в начале и не менее 30 мм в конце шва;
- при автоматической и полуавтоматической сварке с любым типом защиты кроме флюса при толщине металла до 10 мм - не менее 15 мм в начале и не менее 30 мм в конце шва а при толщине металла более 10 мм - не менее 30 мм в начале и не менее 50 мм в конце шва;
- при автоматической и полуавтоматической дуговой сварке под флюсом на токе до 1000 А при электрошлаковой сварке и дуговой сварке с принудительным формированием - не менее 40 мм в начале и не менее 70 мм в конце шва;
- при автоматической сварке под флюсом на токе более 1000 А - не менее 60 мм в начале шва. Длину неиспользуемого участка в конце шва для этого случая принимают равной длине кратера шва (участок имеющий неполное сечение).
Размеры проб вырезаемых из контролируемой конструкции определяются количеством и размерами образцов.
При кислородной вырезке проб их размеры определяют с учетом припуска на последующую механическую обработку обеспечивающую отсутствие металла подвергшегося термическому влиянию при резке в рабочей части образцов.
Вырезку заготовок для образцов из проб и контрольных соединений рекомендуется выполнять на металлорежущих станках. Допускается вырезать заготовки на ножницах штампах кислородной плазменной анодно-механической и другими методами резки.
Припуск на величину заготовки при котором обеспечивается отсутствие в рабочей части образца металла с измененными в результате резки свойствами назначают в зависимости от метода резки. Минимальное значение припуска должно быть:
- при толщине металла до 10 мм: кислородная и плазменная резка - 3 мм механическая в т. ч. анодно-механическая резка - 2 мм;
- при толщине металла более 10 до 30 мм: кислородная резка - 4 мм плазменная резка - 5 мм механическая в т. ч. и анодно-механическая резка - 3 мм;
- при толщине металла более 30 до 50 мм: кислородная резка - 5 мм плазменная резка - 7 мм механическая в т. ч. и анодно-механическая - 3 мм;
- при толщине металла более 50 мм: кислородная резка - 6 мм плазменная резка - 10 мм механическая в т. ч. и анодно-механическая - 3 мм.
При вырезке заготовок для образцов из металла в котором под воздействием резки не изменяются свойства в рабочей части образца допускается уменьшение указанных выше припусков но не более чем в два раза.
Величина припуска для способов резки не перечисленных выше должна быть указана в нормативно-технической документации (НТД) на данный вид продукции или на метод отбора проб.
При изготовлении образцов необходимо принимать меры исключающие возможность изменения свойств металла в результате нагрева или наклепа возникающих при механической обработке.
Термическую обработку если она оговорена НТД проводят до чистовой обработки образцов. Термической обработке могут подвергаться пробы контрольные соединения или вырезанные из них заготовки для образцов. В случае нормализации или закалки термическая обработка заготовок для образцов не допускается.
Термическую обработку контрольных соединений или заготовок для образцов предпочтительно совмещать с термической обработкой контролируемого изделия. Порядок проведения термической обработки при изготовлении образцов из материалов с sВ более 1000 МПа (100 кгсмм2) оговаривается НТД.
Клеймение проб контрольных соединений заготовок и готовых образцов можно производить любым способом так чтобы клеймо располагалось вне рабочей части образца и сохранялось на нем после испытания.
Образцы имеющие отступления от чертежных размеров по чистоте обработки а также механические повреждения в рабочей части к испытаниям не допускаются и заменяются таким же числом новых образцов изготовленных из той же пробы или контрольного соединения. Если размеры пробы или контрольного соединения исключают возможность изготовления новых образцов производят вырезку новой пробы или сварку нового контрольного соединения.
При соответствии результатов механических испытаний требованиям стандартов или другой технической документации во всех случаях кроме арбитражных испытаний допускается использование образцов с более низким классом шероховатости поверхности.
Результаты по всем видам испытаний определяют как среднее арифметическое результатов полученных при испытании всех образцов. Если нет указаний в соответствующих стандартах или другой технической документации то для всех видов испытаний кроме испытаний на статический изгиб и измерения твердости допускается снижение результатов испытаний для одного образца на 10 % ниже нормативного требования если средний арифметический результат отвечает нормативным требованиям. Допускаемое снижение результатов испытания образцов на статический изгиб и при измерении твердости должно оговариваться в соответствующих стандартах или другой технической документации. При испытании на ударный изгиб допускаемое снижение ниже нормативных требований устанавливается не более 5 Джсм2 (05 кгс×мсм2).
Общие результаты испытаний определяют по показаниям полученным при повторных испытаниях. Результаты повторных испытаний являются окончательными.
Методика определения размеров образцов требования предъявляемые к оборудованию для испытаний условия проведения испытаний и подсчет результатов должны соответствовать:
- при испытании на статическое растяжение при комнатной температуре - ГОСТ 1497 при пониженных температурах - ГОСТ 11150 при повышенных температурах - ГОСТ 9651;
- при испытании на ударный изгиб при пониженной комнатной и повышенной температурах - ГОСТ 9454;
- при измерении твердости - ГОСТ 2999 ГОСТ 9013 и ГОСТ 9012.
Другие требования к условиям проведения испытаний определению размеров образцов оборудованию для испытаний и подсчету результатов должны оговариваться стандартом или другой технической документацией.
Протокол при всех видах испытаний должен содержать: обозначение ГОСТ 6996 толщину и марку основного металла способ наплавки вид термической обработки (если она выполняется) индекс образца (по клейму) тип образца место его отбора результаты данного вида испытаний всех образцов наличие дефектов в изломе образца при испытании сварных соединений - место разрушения (по металлу шва по металлу зоны термического влияния по основному металлу).
При испытании металла на статическое (кратковременное) растяжение определяют следующие характеристики механических свойств:
- предел текучести физический sТ МПа (кгсмм2) или предел текучести условный s02 МПа (кгсмм2);
- временное сопротивление sВ МПа (кгсмм2);
- относительное удлинение после разрываs5 %;
- относительное сужение после разрыва j %.
Испытания проводят для металла шва металла различных участков зоны термического влияния наплавленного металла при всех видах сварки плавлением.
Форма и размеры образцов применяемых для испытания должны соответствовать рис.3.1 и табл. 3.1.
Допускается увеличение размера диаметра образца и его высоты.
Рис.3.1. Общий образца для проведения испытания на кратковременное растяжение
Размеры образцов для проведения испытаний
на кратковременное растяжение в мм
Схема расположения образца по ГОСТ 6996
Толщина основного металла мм
Схема расположения образцов
Указания по вырезке образцов
Сварка покрытыми электродами в защитном газе и газовая сварка
q - не менее пяти слоев. Образец должен располагаться выше штрихпунктирной линии
Параметры визуально-измерительного контроля должны соответствовать требованиям РД 34.10.130-96.
Визуальный контроль материала (полуфабрикатов заготовок деталей) проводят с целью выявления участков металла с рисками выходящими на поверхность трещинами расслоениями закатами забоинами (вмятинами) рванинами раковинами пленами шлаковыми включениями волосовинами и другими дефектами недопустимость которых регламентируется действующей НД а также с целью подтверждения наличия и правильности маркировки.
Измерительный контроль полуфабрикатов заготовок деталей и изделий проводят с целью проверки их геометрических размеров и определения размеров поверхностных дефектов выявленных при визуальном контроле.
При входном визуальном контроле сварных труб с прямолинейным или спиральным швом контролю подлежит не менее 10 % длины каждого шва. Контроль рекомендуется выполнять на участках равномерно распределенных по длине шва трубы. Задачей контроля является выявление поверхностных трещин пор шлаковых и металлических включений прожогов свищей наплывов металла усадочных раковин подрезов грубой чешуйчатости шва брызг расплавленного металла непроваров оплавлений металла в результате зажигания сварочной дуги и прочих дефектов.
Измерительный контроль сварных швов выполняется на участках проконтролированных визуально. Измерение размеров сварного шва выполняется на каждом участке проконтролированном визуально но не менее чем в трех сечениях по длине шва. Измерение размеров поверхностных дефектов выполняется в местах отмеченных при визуальном контроле.
Кромки литых деталей поковок и штамповок подлежащие сварке визуально следует контролировать на участке шириной не менее 100 мм по всей длине.
Кромки элементов изделий (деталей) имеющих наплавку должны подвергаться визуальному контролю по всему периметру. Ширина зоны контроля должна составлять l + 20 мм где l - ширина наплавки мм. Контролю подлежит каждая кромка с наплавкой.
Визуальному контролю подлежит не менее 10 % длины сварных соединений (наплавленного слоя) если другие требования не указаны в НД ПТД или ПКД.
Визуальный контроль материала кромок наплавленных элементов и сварных швов проводится с целью выявления коррозии на поверхности и поверхностных дефектов (трещин расслоений забоин вмятин раковин пор подрезов грубой чешуйчатости западаний между валиками шва раковин свищей шлаковых включений и других несплошностей) вызванных технологией изготовления (условиями хранения) или транспортировкой подтверждения наличия и правильности клеймения а также соответствия формы (типа) разделки кромок подлежащих сварке требованиям рабочих чертежей и ТУ на изготовление.
Измерительный контроль проводится с целью измерения размеров наплавленных слоев и поверхностных дефектов выявленных при визуальном контроле а также подтверждения соответствия основных размеров изделий (деталей сборочных единиц) требованиям стандартов ТУ и паспортов изделий. Измерительный контроль сварных швов выполняют через один метр по длине каждого контролируемого шва но не менее чем в трех сечениях сварного шва.
Ультразвуковой контроль проводится в соответствии с требованиями ГОСТ 14782. Наплавленную поверхность подготавливают к ультразвуковому контролю при отсутствии наружных дефектов. Форма и размеры околошовной зоны должны позволять перемещать преобразователь в пределах обеспечивающих прозвучивание акустической осью преобразователя сварного соединения или его части подлежащей контролю.
Поверхность наплавленного слоя по которой перемещают преобразователь не должна иметь вмятин и неровностей с поверхности должны быть удалены брызги металла отслаивающаяся окалина и краска загрязнения.
При механической обработке слоя предусмотренной технологическим процессом на изготовление сварной конструкции поверхность должна быть не ниже Rz 40 мкм по ГОСТ 2789-73.
Требования к допустимой волнистости и к подготовке поверхности указываются в технической документации на контроль утвержденной в установленном порядке.
Контроль околошовной зоны основного металла в пределах перемещения преобразователя на отсутствие расслоений следует выполнять в соответствии с технической документацией на контроль утвержденной в установленном порядке если контроль металла до сварки не производился.
Наплавленный слой следует маркировать и разделять на участки так чтобы однозначно устанавливать место расположения дефекта по длине шва.
Угол ввода луча и пределы перемещения преобразователя следует выбирать такими чтобы обеспечивалось прозвучивание сечения шва прямым и однократно отраженным лучами или только прямым лучом.
Прямым и однократно отраженным лучами следует контролировать швы размеры ширины или катетов которых позволяют осуществлять прозвучивание проверяемого сечения акустической осью преобразователя.
Допускается контролировать сварные соединения многократно отраженным лучом.
Длительность развертки следует устанавливать так чтобы наибольшая часть развертки на экране электронно-лучевой трубки соответствовала пути ультразвукового импульса в металле контролируемой части сварного соединения.
Основные параметры контроля:
) длина волны или частота ультразвуковых колебаний (дефектоскопа);
) положение точки выхода луча (стрела преобразователя);
) угол ввода ультразвукового луча в металл;
) погрешность глубиномера (погрешность измерения координат);
) разрешающая способность по дальности и (или) фронту;
) характеристики электроакустического преобразователя;
) минимальный условный размер дефекта фиксируемого при заданной скорости сканирования;
) длительность импульса дефектоскопа.
Перечень параметров подлежащих проверке численные значения методика и периодичность их проверки должны оговариваться в технической документации на контроль.
Требования к стандартным образцам предприятия а также методика проверки основных параметров контроля должны быть указаны в технической документации на контроль утвержденной в установленном порядке.
Частоту ультразвуковых колебаний следует измерять радиотехническими методами путем анализа спектра эхо-сигнала на преобразователе от вогнутой цилиндрической поверхности стандартного образца СО-3 или измерением длительности периода колебаний в эхо-импульсе посредством широкополосного осциллографа.
Допускается определять длину волны и частоту ультразвуковых колебаний излучаемых наклонным преобразователем интерференционным способом по образцу СО-4 по ГОСТ 18576-85.
Условную чувствительность при контроле эхо-методом следует измерять по стандартному образцу СО-1 в миллиметрах или по стандартному образцу СО-2 в децибелах.
Измерение условной чувствительности по стандартному образцу СО-1 выполняют при температуре устанавливаемой в технической документации на контроль утвержденной в установленном порядке.
4.3. Выбор оборудования и оснастки.
Для проведения ВИК используется набор ВИК «Эксперт»
На рисунке 3.2 представлен общий вид универсального шаблона сварщика модель 00314. Шаблон предназначен для контроля элементов разделки под сварной шов электродов и элементов сварного шва на предприятиях и в организациях производящих сварочные и наплавочные работы. В таблице 3. 3 представлены технические характеристики универсального шаблона сварщика УШС-3 модель 00314.
- основание 2 - движок 3 - указатель 4 - ось
АБВ - установочные плоскости;
Л - торцовая грань М - продольное ребро линейци со шкалой Е для измерения велиин притупления и ширины шва; Г - шкала для измерения высоты усиления шва К - риска - индекс для снятия отсчета по шкале Г; Д - шкала для измерения углов скоса кромок; Ж - пазы для измерения диаметров электродов; И - шкала для измерения величины зазора.
Рисунок 2.5 Шаблон сварщика универсальный УШС 3. Модель 00314.
Технические характеристики универсального шаблона сварщика УШС-3 модель 00314
Диапазон измерения глубины дефектов (вмятин забоин) глубины разделки шва до корневого слоя превышения кромок мм
Диапазон измерения высоты усиления шва мм
Диапазон измерения величин притупления и ширины шва мм
Диапазон измерения величины зазора мм
Диапазон измерения углов скоса кромок град.
Номинальные значения диаметров электродов измеряемых шаблоном мм
Габаритные размеры мм
В табл. 3.4. приведен состав оборудования комплекта ВИК «Эксперт».
Универсальный шаблон Красовского УШК-1
Шаблон предназначен для контроля тавровых нахлесточных и стыковых сварных соединений а также для измерения зазора между кромками при проведении визуального и измерительного контроля по РД 03-606-03.
Шаблон для контроля катетов шва УШС-2
УШС-2 предназначен для контроля катетов угловых швов в диапазоне 4-14 мм в соответствии с требованиями СТБ 1133-98
Универсальный шаблон сварщика УШС-3
УШС-3 предназначен для измерения контролируемых параметров труб контроля качества сборки стыков труб а также для измерения параметров сварного шва при его контроле.
Угольник для проверки и разметки прямых углов контролируемых объектов. Размер 100х160 II класс точности.
Используется для измерений наружных и внутренних размеров а также глубин контролируемых объектов. Модель ЩЦ-1-125-0.1 диапазон измерений 0-125мм. I класс точности
Светодиодный фонарик для работы в условиях слабой освещенности. Мощность 05 Вт элемент питания – батарейка АА 1шт. (в комплекте)
Универсальный восковый маркер для промышленной маркировки. Цвет желтый или красный ширина 12 мм длина 95 мм.
Мелок маркировочный для маркировки нагретой поверхности металлических изделий. Маркировка устойчива к температуре до 2000 °C. Длина мелка 100 мм сечение 10 мм.
Лупа 3х со светодиодной подсветкой для контроля объектов в условиях недостаточной освещенности.
Для изучения внутреннего строения наплавленного салоя на наличие дефектов используем УЗК дефектоскопию.
Лупа измерительная 10х
Лупа для визуального контроля и измерений на плоскости. Длина измерительной шкалы 15 мм цена деления 0.1 мм
Набор щупов №4 (01 -1мм)
Набор для контроля зазоров между поверхностями. Класс точности II диапазон толщин 01-10мм
Набор радиусов №1 (1-6мм)
Шаблоны радиусные для оценки радиусов выпуклых и вогнутых поверхностей.
В каждом наборе шаблоны для контроля внутреннего и наружного радиусов.
Набор радиусов №3 (7-25мм)
Лупа складная ЛПП 7х для осмотра мелких деталей контролируемой поверхности.
Рулетка измерительная
Рулетка измерительная STAYER длина 2м. или 10м в зависимости от комплектации
Линейка измерительная
Линейка измерительная стальная длина 20 и 30 см. в зависимости от комплектации.
Ультразвуковые портативные дефектоскопы общего назначения Epoch 4 Epoch 4B Epoch 4plus и Epoch LT предназначены для выполнения ультразвукового контроля и измерения толщины изделий из различных материалов проводящих ультразвук разнообразных типоразмеров и полученных различными способами.
Дефектоскопы позволяют: обнаруживать дефекты измерять координаты залегания дефектов и толщину с выводом информации на дисплей измерять эквивалентную площадь и условные размеры дефектов.
Дефектоскопы Epoch нашли широкое применение в энергетике нефтегазовом комплексе машиностроении на транспорте и в других отраслях промышленности для контроля трубопроводов сосудов работающих под давлением котлов элементов транспортных и грузоподъемных механизмов.
Дефектоскопы Epoch могут использоваться также для контроля точечной сварки для работы в поточных линиях для измерения параметров ультразвукового сигнала для совместной работы с ручными сканерами с получением информации в виде В.сканов и С.сканов и др.
Для УЗК дефектоскопии выбираем ультразвуковой портативный дефектоскоп EPOCH 1000.
Рис.3.4. Общий вид дефектоскопа EPOCH 1000
Возможность подключения фазированных решеток;
Более 30 цифровых фильтров;
ЧЗИ 6 кГц для высокоскоростного сканирования;
Автоматическое распознавание датчиков;
Интуитивная калибровка задержки в призмах и усиления для всех законов фокусировки;
Программируемые аналоговые входы и выходы сигнализации;
Соответствие стандарту IP67 для работы в жестких условиях;
Цифровой приемник с большим динамическим диапазоном;
Набор опций визуализации для упрощения интерпретации A-
Стандартные динамические кривые DACВРЧ;
Встроенные АРД диаграммы.
Программное обеспечение:
Контроль сварных швов;
Контроль и определение размеров трещин;
Энергетическая промышленность;
Контроль литых и кованных изделий;
Определение размеров дефектов по АРД диаграммам;
Использование с промышленными системами контроля и сканерами;
Определение дефектов и отслоений в композитах;
Аэрокосмическая промышленность;
Автомобильная промышленность;
8. Список Литературы ЭТАЛОН.doc
Технология и оборудование сварки плавлением и термической резки: учебник для студентов вузов А.И. Акулов В.П. Алехин С.И. Ермаков и др.; ред. А.И. Акулов. - 2-е изд. испр. и доп. - М. : Машиностроение 2003. - 560 с.
Хромченко Феликс Афанасьевич. Справочное пособие электросварщика: справочное издание Ф.А. Хромченко. - М. : Машиностроение 2003. - 416 с.
Сварка и резка материалов: учебное пособие М.Д. Банов Ю.В. Казаков М.Г. Козулин; ред. Ю.В. Казаков. - 3-е изд. стереотип. - М. : Академия 2003. - 400 с.
Кошкарев Б. Т. Теория сварочных процессов: учебное пособие для студентов вузов Б. Т. Кошкарев ; Донской государственный технический университет НГГТИ. - Невинномысск : НГГТИ 2003. - 217 с.
Моисеенко Владимир Павлович. Сварочно-технологические свойства цветных металлов и сплавов: учебное пособие для студентов вузов В. П. Моисеенко В. И. Эйдельнант ; НГГТИ. - Невинномысск : НГГТИ 2003. - 81 с.
Специальные методы сварки и пайки: учебник для подготовки дипломированных специалистов В. А. Фролов [и др.]. - М. : Интермет Инжиниринг 2003. - 184 с.
Сварка. Резка. Контроль: справочник. В 2-х т. Н.П. Алешин Г.Г. Чернышев Э.А. Гладков; Ред. Н.П. Алешин Ред. Г.Г. Чернышев. - М. : Машиностроение. Т. 1. - 2004. - 620 с.
Сварка. Резка. Контроль: справочник. В 2-х т. Н.П. Алешин Г.Г. Чернышев Э.А. Гладков; Ред. Н.П. Алешин Ред. Г.Г. Чернышев. - М. :
Машиностроение. Т. 2. - 2004. - 479 с.
Сварка: введение в специальность: учебное пособие для подготовки дипломированных специалистов В. А. Фролов [и др.] ; ред. В. А. Фролов. - М. : Интермет Инжиниринг 2004. - 295 с.
Аттестация сварщиков и специалистов сварочного производства: сборник документов Госгортехнадзор России ; сост. В. С. Котельников сост. Н. А. Хапонен сост. А. А. Шельпяков. - М. : Научно-технический центр по безопасности в промышленности Госгортехнадзора России 2004. - 140 с.
Материаловедение и технология металлов: учебник для студентов вузов Г.П. Фетисов М.Г. Карпман В.М. Матюнин; ред. Г.П. Фетисов. - 3-е изд. испр. и доп. - М. : Высшая школа 2005. - 862 с.
Левадный В. С. Сварочные работы: учебное пособие В.С. Левадный А.П. Бурлака. - М. : Аделант 2005. - 448 с.
ПОТ Р М-020-2001 Межотраслевые правила по охране труда при электро- и газосварочных работах: нормативный документ. - СПб. : ДЕАН 2005. - 80 с.
Гладков Эдуард Александрович. Управление процессами и оборудованием при сварке: учебное пособие для студентов вузов Э. А. Гладков. - М. : ИЦ "Академия" 2006. - 431 с.
Люшинский Анатолий Владимирович. Диффузионная сварка разнородных материалов: учебное пособие для студентов вузов А. В. Люшинский. - М. : Академия 2006. - 204 с.
Акулов Александр Иванович. Сущность и техника различных способов сварки плавлением: учебное пособие А. И. Акулов ; МГИУ. - 2-е изд. стер. - М. : МГИУ 2006. - 104 с.
Справочник мастера строительно-монтажных работ. Сооружение и ремонт нефтегазовых объектов: учебно-практическое пособие В. А. Иванов [и др.] ; ред. В. А. Иванов. - М. : Инфра-Инженерия 2007. - 831 с.
Николаева Н.А. Методические указания к выполнению организационно экономического раздела дипломного проекта для студентов специальности 150202 «Оборудование и технология сварочного производства»
Генкин Б.М. Организация нормирование и оплата труда на промышленных предприятиях: Учебник для вузов. – 4-е изд. изм. и доп. – М.: Норма 2007. – 464 с.
Организация и планирование машиностроительного производства (производственный менеджмент): учебник для студентов вузов обучающихся по машиностроительным и приборостроительным специальностям К. А. Грачева М. К. Захарова Л. А. Некрасов - М.: Высшая школа 2008.
Фатхутдинов Р. А. Организация производства: Учебник для студентов обучающихся по экономическим и техническим специальностям - 3-е изд. перераб. И доп. – М.: ИНФРА – М 2009.
СанПиН 2.2.3.538-96 "Гигиенические требования к микроклимату производственных помещений".
СН 2.2.42.1.8.562-96 «Шум на рабочих местах в помещениях жилых и общественных зданий и на территории жилой застройки».
СН 2.2.42.1.8.566-96 «Производственная вибрация вибрация в помещениях жилых и общественных зданий».
СНиП 2.09.87. Санитарно-бытовые помещения.
СНиП 23-05-95. Естественное и искусственное освещение.
Методика расчета выделений (выбросов) загрязняющих веществ в атмосферу при сварочных работах (по величинам удельных выделений). НИИ Атмосфера. СПб 2000.
РД-13.100.00-КТН-196-06 «Правила безопасности при эксплуатации магистральных нефтепроводов».
Технический регламент о требованиях пожарной безопасности. ФЗ № 123.
001. Аннотация.doc
Сущность процесса восстановления состоит в наплавке изношенных поверхностей ступицы в районе крепления подшипников. В качестве способа наплавки предлагается использовать автоматическую наплавку под слоем флюса.
В работе представлено расчет и описание основного и вспомогательного сварочного оборудования представлен расчет основных режимов наплавки. Также приводится технико-экономическое обоснование выбранного процесса наплавки применяемого основного и вспомогательного сварочного оборудования.
002. Введение.doc
В повышении технического уровня сборочно-сварочных работ большая роль отводится сборочно-сварочным приспособлениям различным средствам механизации и автоматизации использование которых эффективно не только в условиях цехов мастерских и производственных баз но и на строительных площадках трассах.
Технологические процессы заготовительного и сборочно-сварочного производства оснащаются различными средствами термической и механизированной резки обработки кромок под сварку сборки изделия испытания контроля в которых широко используются приспособления. Эти средства позволяют существенно сократить трудоемкость работ обеспечивают стабильное качество изделий облегчают и улучшают условия труда. Сами приспособления являются изделиями индивидуального производства т.к. имеют специфические конструктивные особенности и конкретное назначение. Несмотря на их большое конструктивное разнообразие устройство правила конструирования имеют общие закономерности и единую элементарную базу.
В области сварочного производства трудовые затраты собственно на сварочные работы обычно не превышают 30 %. Большой объем занимают заготовительные сборочные и вспомогательные особенно транспортные операции. Следовательно повышение производительности только сварочных работ не может дать существенного эффекта. Отсюда возникает необходимость комплексной механизации и автоматизации охватывающей не только основные (заготовительные сборочные сварочные отделочные) но и вспомогательные (транспортные контрольные) операции.
Механизация и автоматизация производства снижает трудоемкость изготовления продукции улучшает условия труда рабочих создает экономию металла и времени. Наибольшая экономия времени достигается в условиях непрерывного поточного автоматизированного производства при крупносерийном и массовом выпусках продукции когда все операции согласованы во времени и выполняются механизмами. Но т.к. доля сварных конструкций изготовляемых в условиях крупносерийного и массового производства относительно невелика то основными производствами выпускающими сварочную продукцию являются серийное и мелкосерийное производства с часто меняющейся номенклатурой продукции но здесь традиционные методы механизации и автоматизации малоэффективны особенно при выполнении операций сборки и сварки. Более широкую перспективу автоматизации сварочного производства открывает использование современных промышленных роботов. Универсальность промышленных роботов дает возможность автоматизировать практически любые операции выполняемые человеком.
4. конструкторская часть.doc
1. Обоснование выбора сборочно-сварочных приспособлений.
В процессе изготовления сварных конструкций должны быть обеспечены заданные технологическим процессом взаимное положение соединяемых деталей и условия наиболее благоприятные для образования качественного соединения. Это достигается применением технологических приспособлений и оснастки.
Технологические приспособления делятся на сборочные предназначенные для сборки под сварку и фиксации деталей при помощи прихваток или простейших механических устройств; сварочные предназначенные для сварки заранее собранных деталей с зафиксированным взаимным положением; сборочно-сварочные позволяющие совместить операции сборки и сварки.
Тип технологического приспособления выбирают в зависимости от производственной программы (единичное серийное или массовое производство) конструкции изделия (листовые или решетчатые конструкции детали машин и др.) технологии и степени точности изготовления заготовок (механическая обработка газовая резка и т. д.) и технологии сборки и сварки (необходимость в зазорах допустимые их изменения или допустимые превышения кромок и т. д.).
Сварочные приспособления должны допускать свободное перемещение отдельных элементов конструкции вследствие нагрева и последующего остывания зоны сварки а при необходимости уменьшить или по возможности исключить деформации возникающие в сварном изделии и в самом приспособлении вследствие температурных воздействий. При сварке крупногабаритных конструкций обладающих малой жесткостью (рамные решетчатые листовые) приспособления должны обеспечивать фиксацию отдельных свариваемых кромок а не всего изделия в целом. При проектировании приспособления необходимо предусмотреть доступ к местам сварки и прихватки быстрый отвод теплоты от мест интенсивного нагрева сборку узла с минимального числа установок свободный доступ для проверки размеров изделия и свободный съем собранного или сваренного изделия.
Технологические приспособления могут быть специализированными (для сварки определенного типа изделий) или универсальными. В ряде случаев для прижима может быть использован вес свариваемых деталей.
Исходя из конструктивных особенностей балки задней оси БЗМ-10 для проведения наплавки необходимы следующие приспособления:
Приспособление для поворота и удержания оси в процессе наплавки;
Приспособление для перемещения сварочной головки;
Приспособление для отбора флюса.
2. Разработка принципиальной схемы приспособления.
Разработка принципиальной схемы приспособления начинается с составления принципиальной схемы базирования. На которую наносятся основные вспомогательные и технологические базы; места приложения зажимных усилий и их величина.
Принципиальная схема базирования должна обеспечивать максимальную неподвижность закрепленной детали или изделия однако не должна быть громоздкой. Также при составлении схемы базирования должен учитываться беспрепятственный доступ рабочего инструмента.
Также приспособление должно учитывать тип производства производственную и операционную партии такт выпуска и т.д.
Программа выпуска - установленный для данного предприятия перечень изготовляемых или ремонтируемых изделий с указанием объема выпуска по каждому наименованию на планируемый период.
Производственную партию составляют предметы труда одного наименования и типоразмера запускаемые в обработку в течение определенного интервала времени при одном и том же подготовительно-заключительном времени на операции.
Интервал времени от начала до окончания производственного процесса изготовления или ремонта изделия называют производственным циклом.
Цикл технологической операции - это интервал календарного времени от начала до конца периодически повторяющейся технологической операции независимо от числа одновременно изготовляемых изделий.
Такт выпуска - это интервал времени через который периодически производится выпуск изделий определенного наименования типоразмера и исполнения.
Ритм выпуска - это количество изделий определенного наименования типоразмера и исполнения выпускаемых в единицу времени.
Тип производства (ГОСТ 14.004-74) - это классификационная категория производства выделяемая по признакам широты номенклатуры регулярности стабильности и объема выпуска изделий. Различают типы производства: единичное серийное и массовое. У каждого из этих типов производственный и технологический процессы имеют свои характерные особенности и каждому из них свойственна определенная форма организации технологических процессов. На одном и том же предприятии и даже в одном и том же цехе могут существовать различные типы производства. Поэтому характеризовать производство всего завода или цеха можно только по признаку преимущественного характера производственных и технологических процессов.
Понятие “тип производства” необходимо четко разграничивать с понятием “вид производства”.
Вид производства - это классификационная категория производства выделяемая по признаку применяемого метода изготовления изделия. Примерами видов производства являются литейное сварочное и т.д.
Единичным называется такое производство при котором изделия изготавливаются единичными экземплярами разнообразными по конструкции и размерам причем повторяемость этих изделий очень редкая или совсем отсутствует.
Так как в единичном производстве выпускают изделия широкой номенклатуры то оно должно быть универсальным и гибким. Поэтому характерным признаком единичного производства является выполнение на рабочих местах разнообразных операций для чего завод должен располагать комплектом универсального оборудования оснастки режущего и мерительного инструмента. Этот комплект должен быть подобран таким образом чтобы с одной стороны можно было применять различные виды обработки а с другой - чтобы количественное соотношение отдельных видов оборудования гарантировало определенную пропускную способность завода т.е. выполнение заданной программы.
Технологический процесс изготовления деталей при этом типе производства имеет уплотненный характер: на одном станке выполняется несколько операций и часто производится полная обработка деталей разнообразных конструкций изготовленных из различных материалов. Для этого типа производства ввиду разнохарактерности работ выполняемых на одном станке и неизбежности вследствие этого в каждом случае подготовки и переналадки станка для новой работы время обработки () в общей структуре нормы времени невелико.
Оборудование на предприятиях единичного производства располагают в цехах по групповому признаку т.е. с разбивкой на участки токарных фрезерных строгальных станков и т.д. При сборке применяют подгоночные работы.
В целях предотвращения брака основные металлоемкие дорогостоящие детали изготавливают раньше чем сопрягаемые с ними более дешевые детали за счет которых при сборке компенсируются отклонения размеров основных деталей.
Квалификация рабочих как правило очень высокая а оплата труда чаще всего повременная. Себестоимость продукции высокая а производительность труда сравнительно низкая.
Единичное производство существует в тяжелом машиностроении (производство крупных турбин уникальных металлорежущих станков прокатных станов и др.) на предприятиях выпускающих оборудование для химических и металлургических заводов в ремонтных цехах на опытных предприятиях и т.д.
Серийное производство занимает промежуточное положение между единичным и массовым производством.
При серийном производстве изделия изготавливают партиями или сериями состоящими из одноименных однотипных по конструкции и одинаковых по размерам изделий запускаемых в производство одновременно. Основным принципом этого типа производства является изготовление всей партии (серии) целиком как в обработке деталей так и в сборке.
В зависимости от количества изделий в серии их характера и трудоемкости частоты повторяемости серий в течение года различают производство мелкосерийное среднесерийное и крупносерийное. Такое подразделение является условным для разных отраслей машиностроения: при одном и том же количестве машин в серии но различных размеров сложности и трудоемкости производство может быть отнесено к разным типам.
В серийном производстве технологический процесс преимущественно дифференцирован т.е. расчленен на отдельные операции которые закреплены за определенными станками.
Применяются станки разнообразных видов: универсальные специализированные специальные автоматизированные агрегатные. Станочный парк должен быть специализирован в такой мере чтобы был возможен переход от производства одной серии машин к производству другой несколько отличающейся от первой в конструктивном отношении.
При использовании универсальных станков должны широко применяться специализированные и специальные приспособления и режущий инструмент измерительный инструмент в виде предельных (стандартных и специальных) калибров и шаблонов.
Серийное производство значительно экономичнее чем единичное т.к. лучше используется оборудование применяется специализация рабочих. За счет этого происходит увеличение производительности труда обеспечивается снижение себестоимости продукции.
Серийное производство является наиболее распространенным типом производства в общем и среднем машиностроении. К этому типу производства относятся: станкостроение производство прессов компрессоров оборудование нефтяной газовой и лесной промышленности.
В массовом производстве выпускаются изделия узкой номенклатуры с большим объемом выпуска непрерывно изготавливаемые в течение продолжительного времени. На каждом рабочем месте выполняется только одна закрепленная за ним операция.
Технологические процессы разрабатываются детально и точно в отношении как методов обработки так и расчетов основного (технологического) и вспомогательного времени.
Оборудование должно быть точно определено и расставлено таким образом чтобы его количество типы комплектность и производительность соответствовали заданному выпуску изделий.
Массовое производство характеризуется:
высокой степенью механизации и автоматизации производственных процессов;
применением наиболее совершенных способов получения заготовок обеспечивающих высокое значение коэффициента использования металла;
широким применением специализированного и специального оборудования;
четкой организацией снабжения рабочих мест основными и вспомогательными материалами полуфабрикатами режущим измерительным и вспомогательным инструментом приспособлениями и т.д.
Себестоимость одного и того же вида продукции при массовом производстве значительно ниже чем при серийном производстве т.к. оборачиваемость средств выше расходы на транспорт меньше выпуск продукции больше.
Массовое производство получило широкое применение в автомобиле- и тракторостроении двигателестроении и т.д.
Приспособление первой группы является наиболее важным т.к от его конфигурации работоспособности напрямую зависит качество наплавленной поверхности. Также приспособление для поворота и удержания должно обладать зажимным механизмом а также устройством поворота. Для обеспечения стабильности процесса наплавки и как следствие достижения требуемых свойств наплавленного слоя должно обладать электроприводом.
Основание (рама корпус) приспособления представляет собой элемент объединяющий в одну конструкцию все части приспособления. Основание принимает массу изделия и все усилия возникающие в процессе наплавки. При этом оно должно обеспечивать точность расположения установленных деталей изделий сборочных единиц. Основание приспособления должно быть технологичным иметь рациональное конструктивное исполнение обладать возможно меньшей и быть компактным.
3. Расчет сварочных деформаций и зажимных усилий.
В процессе наплавки деталей сварочные деформации рассчитываются при составлении (выборе расчете) основных режимов сварки т.к. наплавка ведется без полного проплавления.
Расчет зажимных усилий следует вести таким образом чтобы исключались возможные повреждения детали в процессе закрепления но обеспечивалось надежное закрепление.
Определение усилия прижатия Р детали массой Q:
где к – коэффициент запаса принимаем равным 15;
- коэффициент трения скольжения стали о сталь принимаем 02;
4. Выбор типа установочных и зажимных элементов.
В сварочном производстве наиболее широкое применение получили следующие типы зажимных элементов:
пневматические прижимы;
гидравлические прижимы.
Исходя из расчетов необходимого усилия прижатия а также мелкосерийного производства выбираем механические винтовые прижимы.
В качестве основания приспособления выбираем сварную раму т.к сварная конструкция легче литой а также в связи с тем что масса балки задней оси невелика.
На рис.4.1. показан общий вид основания и примерные габаритные размеры.
1 Основные элементы основания
5. Расчет зажимных элементов приспособлений.
Расчет зажимных элементов проводить нецелесообразно т.к исходя из конструктивных особенностей необходимо приспособление имеющее устройство для зажатия и вращения оси. Как правило такие приспособления поставляются в сборе с приспособлением.
6. Расчет электромеханического оборудования приспособлений.
Так как для привода механизма вращения необходим электродвигатель то:
Определяем крутящий момент на валу Мкр:
Определяем требуемую мощность двигателя при nм:
Определяем необходимую мощность приводного электродвигателя:
Из выполненных расчетов следует что для достижения необходимой скорости вращения достаточно электродвигателя мощностью 18 кВт.
7. Выбор стандартного механического оборудования.
Согласно проведенных выше анализа и расчетов выбираем следующие приспособления:
для поворота и удержания оси в процессе наплавки выбираем вращатель наплавочный специализированный ВН-320С однако для запаса мощности выбираем двигатель АД80 мощностью 22 кВт;
для перемещения сварочной головки выбираем тележку ПКТ-17;
для отбора флюса емкость ЕФ-1 с роликоопорами.
1. Общая часть.doc
Балка задней оси БЗМ-10 разработана и производится немецкой фирмой BPW. Данная балка предназначена для установки на трейлеры. Прицепы и полуприцепы.
Балка оси БЗМ-10 изготавливается из квадратного сварного профиля с толщиной стенки 15 мм. Наличие профиля толщиной до 15мм обусловлено тем что в процессе эксплуатации балка воспринимает различные нагрузки:
собственный вес прицепа полуприцепа;
вес груза перевозимый трейлером прицепом полуприцепом;
В табл. 1.1 приведены основные технические характеристики балки БЗМ-10.
Технические характеристики балки БЗМ-10
Длина (общая вместе с осью) мм
Расстояние между креплениями мм
При эксплуатации балки задней оси возникает ряд проблем. Основной проблемой является износ цапфы в местах крепления подшипников. Повреждения цапфы в основном вызваны низким качеством дорожного покрытия и суровыми климатическими условиями.
Основным повреждением цапфы является: заклинивание подшипников отворачивание гайки ступицы и ослабление момента затяжки подшипников. Как следствие на ступицу в места крепления подшипников попадает загрязнение приводящее к абразивному износу и занижению размеров посадочных размеров подшипников.
Балка БЗМ-10 предназначена для работы в районах с температурой от +500С до -450С. Согласно СНиП 23-01-99 III III климатические районы.
2. Требования нормативной документации.
Основными требованиями предъявляемыми к наплавленным поверхностям являются:
Твердость после термообработки не ниже 250НВ;
Временное сопротивление разрыву наплавленной поверхности не ниже 600МПа;
Минимальное проплавление основного металла;
Минимальное перемешивание наплавленного слоя с основным металлом;
Минимальное значение остаточных напряжений и деформаций металла в зоне наплавки;
На наплавленной поверхности не допускается наличие трещин раковин.
3. Характеристика материала для изготовления изделия оценка его свариваемости.
3.1. Структура и свойства материала изделия.
Балка оси бзм-10 изготавливается из стали 35ХМЛ.
В табл.1.2 – 1.7 приведены основные свойства материала.
Назначение стали 35ХМЛ
Сталь для отливок обыкновенная
Валы шестерни крестовины втулки зубчатые венцы и другие детали работающие с повышенными нагрузками и требующие повышенной твердости.
Химический состав в % стали 35ХМЛ
Механические свойства при Т=20oС материала 35ХМЛ
Нормализация 860 - 880oCОтпуск 600 - 650oC
Основные физические свойства стали 35ХМЛ
Технологические свойства материала 35ХМЛ
ограниченно свариваемая.
Флокеночувствительность:
Склонность к отпускной хрупкости:
Литейно-технологические свойства материала 35ХМЛ
Механические свойства :
- Предел кратковременной прочности [МПа]
- Предел пропорциональности (предел текучести для остаточной деформации) [МПа]
- Относительное удлинение при разрыве [ % ]
- Относительное сужение [ % ]
- Ударная вязкость [ кДж м2]
- Твердость по Бринеллю [МПа]
Физические свойства :
- Температура при которой получены данные свойства [Град]
- Модуль упругости первого рода [МПа]
- Коэффициент температурного (линейного) расширения (диапазон 20o - T ) [1Град]
- Коэффициент теплопроводности (теплоемкость материала) [Вт(м·град)]
- Плотность материала [кгм3]
- Удельная теплоемкость материала (диапазон 20o - T ) [Дж(кг·град)]
- Удельное электросопротивление [Ом·м]
3.2. Расчет свариваемости.
Т.к сталь 35ХМЛ относится к группе низколегированных качественных сталей то расчет свариваемости сводится к определению склонности стали к образованию холодных и горячих трещин.
Расчет на холодные трещины ведется по формулам 1.1-1.3 «Расчет полного эквивалента углерода». Склонность к образованию горячих трещин определяется «Показателем Итамуры» формула 1.4.
где [С]х – химический эквивалент углерода;
[С]р – размерный эквивалент углерода.
Химический эквивалент углерода определяется по формуле:
Размерный эквивалент углерода определяется по формуле:
где S – толщина стали мм.
Рассчитанный эквивалент углерода более 046 следовательно сталь склонна к образованию холодных трещин.
Полученное значение 4 следовательно сталь не склонна к образованию горячих трещин.
Как видно из вышеприведенного расчета сталь 35ХМЛ сваривается ограниченно т.к склонна к образованию холодных трещин. Поэтому для предотвращения появления холодных трещин следует проводить предварительный подогрев до 1200С.
4. Прокат для изготовления изделия.
Т.к в предлагаемом дипломном проекте рассматривается процесс восстановления изношенной детали путем восстановления до рабочих размеров наплавкой то прокат в ходе технологического процесса наплавки не применяется.
В качестве способа получения заготовок используется литье.
Номинальный размер отливки следует принимать равным номинальному размеру детали для необрабатываемых поверхностей и сумме среднего размера детали и общего припуска на обработку - для обрабатываемых поверхностей. При определении номинальных размеров отливок учитывают технологические напуски.
Номинальную массу отливки следует принимать равной массе отливки с номинальными размерами.
Технологические напуски устанавливает изготовитель и указывает в чертежах отливки или детали с указанием размера отливки.
Нормы точности устанавливают на отливку в целом ее отдельные поверхности и размеры.
Точность отливки в целом характеризуют классом размерной точности отливки степенью коробления степенью точности поверхностей классом точности массы.
Обязательному применению подлежат классы размерной точности и точности массы отливки. Использование других показателей точности отливок а при необходимости и специфические требования к точности литых деталей в зависимости от их назначения и условий эксплуатации регламентируется в отраслевой нормативно-технической документации.
Нормы точности отливок: классы размерной точности степень коробления степень точности поверхностей классы точности масс а также ряды припусков на обработку для различных технологических процессов и условий изготовления и обработки отливок приведены в табл. 1.8-1.10
На отдельные размеры и поверхности отливок допускается устанавливать более жесткие нормы точности чем в целом на отливку.
Допуски линейных размеров отливок изменяемых и неизменяемых обработкой должны соответствовать указанным в табл. 1.8
Допуски размеров мм отливок для классов точности
Интервал номинальных размеров мм
Класс точности отливки
* - согласно ГОСТ 26645 за номинальный берется наибольший размер отливки. При изготовлении оси БЗМ-10 наибольшим является размер 318мм.
Допуски формы и расположения элементов отливки
Номинальный размер нормируемого участка отливки мм
Допуск формы и расположения элементов отливки мм не более для степеней коробления элементов отливки
Общий припуск на сторону мм
Общий допуск элемента поверхности мм
Вид окончательной механической обработки
Общий припуск на сторону мм не более для ряда припуска отливки
За номинальный размер нормируемого участка при определении допусков формы и расположения следует принимать наибольший из размеров нормируемого участка элемента отливки для которого регламентируются отклонения формы и расположения поверхности.
5. Выбор способа получения заготовок.
Получение заготовок не рассматривается т.к. в дипломном проекте рассматривается ремонт бывшего в эксплуатации изделия.
6. Требования к основным и сварочным материалам.
Техническое условие на поставку сварочной проволоки указаны в табл.1.13.
Сварочная проволока поставляется согласно ГОСТ 2246-70.
По требованию потребителя проволока должна изготовляться из стали выплавленной электрошлаковым (Ш) или вакуумно-дуговым (ВД) переплавом или в вакуумноиндукциоиных печах (ВИ). При этом дополнительные требования к металлу проволоки (ужесточение норм но содержанию вредных и посторонних примесей введение ограничений по содержанию газов неметаллических включений и т. п.) устанавливаются соглашением сторон.
Диаметры проволоки и предельные отклонения по ним должны соответствовать значениям указанным в табл. 1.13.
Стальная наплавочная проволока поставляется в мотках перевязанных мягкой проволокой не более 3 мм не менее чем в трех местах равномерно расположенных по окружности мотка.
По требованию потребителя мотки бухты или катушки проволоки должны быть обернуты упаковочной водонепроницаемой бумагой по ГОСТ 8829-77 или упаковочной битумной бумагой по ГОСТ 515-77.
Предельные отклонения диаметров для проволоки
Предельное отклонение для проволоки предназначенной
для сварки (наплавки)
для изготовления электродов
К каждому мотку или катушке должна быть прочно прикреплена металлическая бирка на которой должны быть четко указаны:
наименование организации – поставщика;
марка стали проволоки;
Для предохранения от коррозии проволоку покрывают сплошным слоем чистой нейтральной смазки хорошо растворимой в бензине.
Потребитель имеет право производить контрольную проверку качества поступившей проволоки и соответствия ее показателей требованиям ГОСТ 10543 – 75. Химический анализ проволоки должен проводиться в соответствии с требованиями ГОСТ 2604 – 77.
Перед использованием проволоку необходимо очистить промыть бензином если на проволоку была нанесена смазка и перемотать кассеты которые рекомендуется подавать на рабочее место непосредственно перед заправкой в автомат.
Сварочные плавленые флюсы по ГОСТ 9087 – 69 должны поставляться на ремонтные предприятия упакованными в бумажные мешки или другую тару обеспечивающую их сохранность. На каждом упаковочном месте должен быть прикреплен ярлык содержащий:
товарный знак предприятия – изготовителя;
номер настоящего стандарта;
Перед употреблением флюсы необходимо просушить до допустимой влажности.
Флюсы выбираются в соответствии с проволокой по химическому составу структуре по способу защиты формированию шва и стоимости. В таблице представлены марки флюсов для различных видов сварки (табл. 1.12):
Флюсы сварочные для наплавки
АН-348-а АН-348-АМ АН-348-В АН-348-ВМ ОСЦ-45 ОСЦ-45М ОСЦ-45П ФЦ-9 АН-60 АН-65
Механизированная сварка и наплавка углеродистых низколегированных сталей углеродистой и низколегированной сварочной проволокой
Сварка низколегированных сталей углеродистой и низколегированной сварочной проволокой
АН-20С АН-20СМ АН-20П АН-15М АН-18
Дуговая автоматическая сварка и наплавка высоколегированных и среднелегированных сталей соответствующей сварочной проволокой
Дуговая автоматическая наплавка и сварка низколегированных и среднелегированных сталей соответствующей сварочной проволокой
Для наплавки поверхности оси сварочные материалы (сварочная проволока флюс) выбираются в соответствии с основным металлом. Используемые сварочные материалы должны обеспечивать устойчивый процесс наплавки и бездефектный наплавленный слой. При выборе сварочных материалов следует обращать внимание на химический состав основного металла и подбирать сварочные материалы которые бы обеспечивали равновесную наплавленного слоя.
Подбор сварочных материалов ведется комплексно то есть сварочная проволока и флюс выбираются в комплексе для обеспечения необходимых физических и химических свойств наплавленного слоя.
7. Выбор типа производства.
Тип производства выбираем-единичное т.к. в дипломном проекте рассматривается наплавка штучного изделия бывшего в эксплуатации.
Единичным называется такое производство при котором изделия изготавливаются единичными экземплярами разнообразными по конструкции и размерам причем повторяемость этих изделий очень редкая или совсем отсутствует.
Так как в единичном производстве выпускают изделия широкой номенклатуры то оно должно быть универсальным и гибким. Поэтому характерным признаком единичного производства является выполнение на рабочих местах разнообразных операций для чего завод должен располагать комплектом универсального оборудования оснастки режущего и мерительного инструмента. Этот комплект должен быть подобран таким образом чтобы с одной стороны можно было применять различные виды обработки а с другой - чтобы количественное соотношение отдельных видов оборудования гарантировало определенную пропускную способность завода т.е. выполнение заданной программы.
Технологический процесс изготовления деталей при этом типе производства имеет уплотненный характер: на одном станке выполняется несколько операций и часто производится полная обработка деталей разнообразных конструкций изготовленных из различных материалов. Для этого типа производства ввиду разнохарактерности работ выполняемых на одном станке и неизбежности вследствие этого в каждом случае подготовки и переналадки станка для новой работы время обработки () в общей структуре нормы времени невелико.
Оборудование на предприятиях единичного производства располагают в цехах по групповому признаку т.е. с разбивкой на участки токарных фрезерных строгальных станков и т.д. При сборке применяют подгоночные работы.
В целях предотвращения брака основные металлоемкие дорогостоящие детали изготавливают раньше чем сопрягаемые с ними более дешевые детали за счет которых при сборке компенсируются отклонения размеров основных деталей.
Квалификация рабочих как правило очень высокая а оплата труда чаще всего повременная. Себестоимость продукции высокая а производительность труда сравнительно низкая.
Единичное производство существует в тяжелом машиностроении (производство крупных турбин уникальных металлорежущих станков прокатных станов и др.) на предприятиях выпускающих оборудование для химических и металлургических заводов в ремонтных цехах на опытных предприятиях и т.д.
5. Организационно-экономическая часть - ЕРШОВ (Эталон).doc
1 Анализ экономической эффективности выбора способа сварки
Опираясь на нормативную документацию согласно которой осуществляется производство балки задней оси HZF 12010-16 EC ECO-P только ручной дуговой сваркой покрытыми плавящимися электродами механизированной сваркой в среде защитных газов (при цеховых условиях) допускается способ сварки АФ. Но в нашем дипломном проекте рассматривается не процесс ее производства а процесс восстановления изношенных частей путем наплавки. В связи с этим примем за базовый вариант наплавку РД способом за проект – АДФ.
Основные преимущества и недостатки технологий ручной дуговой наплавки покрытыми электродами и автоматической наплавки под слоем флюса (предлагаемой в проектном варианте) представлены в пункте 2.3 Технологической части проекта.
Основываясь на расчетах произведенных в технологической части (см. п.2.8) можно сделать вывод что автоматическая наплавка под слоем флюса будет более высокопроизводительным процессом потому что:
- общая имеется большая длина площадь для наплавки
- в металлоконструкциях имеются длинные элементы для восстановления изношенного металла
- имеется необходимость разнотолщинной наплавки в отдельных частях балки (в зависимости от степени износ аи утоньшения металла)
- в заводских условиях имеется возможность использования сварочного трактора за счет применения средств механизации и автоматизации в нашем случае приспособления роликового вращателя;
- качество наплавленного валика мало зависит от квалификации сварщика; Сваркой управляет оператор (АДФ);
- сокращается время процесса наплавки за счет отсутствия действия смены электрода так как проволока подается беспрерывно;
- восстановление металлоконструкций данным способом сварки осуществляется примерно в 4 раза (АДФ) быстрее по сравнению со способом РДС АДФ имеет еще большие скорости сварки потому что есть возможность соединения материалов за один проход и возможность наплавлять большее количество металла за 1 проход.
Сварочно - восстановительный процесс осуществляется на вращателе. Объем работ выполняемых на нем составляет до 80% от общего объема работ на ремонт металлоконструкции. Поэтому расчет режимов наплавки и экономический расчет произведен для основной толщины корпуса на котором необходимо обеспечить слой наплавки равный в 4 мм.
Для ручной дуговой наплавки в качестве сварочного материала используются покрытые металлические электроды. Согласно сертификатам качества на металлоконструкции при ручной дуговой сварке используют покрытые электроды марки ОК 83.28 (подобраны по хим.составу стали и предельному сопротивлению на разрыв МПа – см. п. 2.4 Тех. части проекта).
Производительность наплавки составляет – 14 кгч. Расход электродов на 1 кг наплавленного металла равен 1608 кг. Для сварки используются электроды диаметром 3 мм – в один слой (базовый вариант).
Для автоматической наплавки в качестве сварочных материалов используются сварочная проволока НП-30ХГСА d=2 мм и флюс АН-348. Сварочная проволока выбирается согласно ГОСТ 2246-70 «Проволока стальная сварочная. Технические условия» (см.п.2.5 Технологической части проекта).
Для наплавки оси задней балки HZF 12010-16 EC ECO-P наиболее подходящими способами наплавки являются:
ручная дуговая наплавка;
полуавтоматическая наплавка;
автоматическая наплавка.
Однако существенным отличием автоматической от полуавтоматической наплавки является лишь степень автоматизации процесса. Сварочная проволока применяемая при этих способах наплавки идентична. Также следует учитывать что качество наплавленной поверхности при автоматической наплавке под слоем флюса выше.
Поэтому для выбора наиболее эффективного и экономически способа наплавки следует исследовать ручную дуговую и автоматическую наплавку.
Основными требованиями к источникам питания для ручной дуговой сварки являются:
Безопасность эксплуатации.
Падающая внешняя статическая характеристика источника питания.
Пределы регулирования сварочного тока от 50 до 250А.
Номинальный сварочный ток при ПВ=60% не ниже 70А.
Диапазон регулирования напряжения на дуге от 12 до 36В включительно.
Дополнительные требования к источникам питания для ручной дуговой сварки а также для автоматической сварки приведены в технологической части проекта (см. п. 2.7.1).
Основными требованиями к источникам питания для автоматической сварки под слоем флюса и полуавтоматической сварки в среде защитных газов являются:
Жесткая внешняя статическая характеристика источника питания.
Пределы регулирования сварочного тока от 50 до 500А.
Номинальный сварочный ток при ПВ=60% не ниже 250А.
Диапазон регулирования напряжения на дуге от 16 до 37 В включительно.
Оборудование для наплавки подобрано по таким же критериям как и для процесса сварки поэтому к источникам питания как для операций сборки конструкций так и для операций восстановления предъявляются одинаковые требования.
Данным условиям удовлетворяет отечественный выпрямитель дуговой универсальный ВДУ-306 (базовый вариант); и ВДУ–506 в комплекте с А1408 (проектный вариант).
Исходные для экономического анализа выбранных способов наплавки представлены в Таблице 5.1.
Исходные данные для экономического анализа выбора способа сварки
Наименование способа наплавки
- сила сварочного тока А
- напряжение на дуге В
- коэффициент наплавки
Сварочное оборудование:
Наименование сварочного оборудования:
- пределы регулирования тока А
Выпрямитель дуговой универсальный ВДУ – 306
ВДУ–506головка А 1408
Наименование источника питания:
Выпрямитель дуговой универсальный ВДУ-306
Сварочные материалы:
- наименование материала
- коэффициент расхода сварочного материала на 1 кг. наплавленного металла кг
Экономический расчет проведем для одной операции: наплавка способом РД и АДФ по ГОСТ 8713-79-С4 так как на данной операции возможно наиболее детальное сравнение технико-экономических показателей имеется немалая протяженность наплавочной полосы а также существует координальное отличие проектного способа сварки от базового за счет применения приспособления – роликового вращателя.
2 Расчет технологической себестоимости 1 кг наплавленного металла. Базовый вариант (наплавка - РД)
2.1 Вспомогательные материалы технологического назначения (сварочные материалы)
а)Стоимость сварочных материалов (См)
- цена 1 кг сварочного материала руб.; цена 1 кг. покрытых электродов ОК 83.28; См' = 260 руб. .
- коэффициент расхода сварочного материала на 1 кг наплавленного металла; арм = 17 кг. (см.п.2.8.2 Технологической части проекта)
Расчёт произведем по каждому виду сварочного материала используемого для определённого способа сварки.
См = 260×17 = 442 руб.
Цены на сварочные материалы принимаются по прейскурантам цен с учетом транспортных расходов.
2.2 Расчет средств на оплату труда
Расчет средств на оплату труда работающих ведется в следующем порядке:
Заработная плата основных рабочих (сварщиков) определяется по
- основная заработная плата сварщиков руб.;
- дополнительная заработная плата сварщиков руб.;
- оплата по районному коэффициенту руб.(15% от )
Основная заработная плата сварщиков рассчитывается по формуле:
где: - тарифный фонд заработной платы сварщиков тыс. руб.;
- премиальный фонд заработной платы руб.
Тарифный фонд заработной платы определяется в зависимости от системы оплаты труда:
- для основных рабочих – по сдельной оплате труда: (5.6)
где - часовая тарифная ставка сварщика занятого на выполнении данного вида работы (операции) принимаемая исходя из тарифного разряда сварщика руб.; Тс сварщика четвертого разряда составляет 110 руб.час;
- время на наплавку 1 кг. металла час.
где Кг - коэффициент учитывающий время горения дуги в общем времени сварки (коэффициент основного времени сварки); в расчетах можно принять для ручной дуговой сварки Кг=055.
В дипломном проекте премиальный фонд заработной платы принят в размере 50 % от тарифного фонда заработной платы. Дополнительная заработная плата принимается в размере 10% от основной.
Зтар – тарифный фонд заработной платы сварщиков:
Зосн = 1639 руб.+8195 руб = 24585 руб.
З = 24585+2458+4056=31099 руб.
Страховые взносы от заработной платы производственных рабочих:
Страховые взносы от заработной платы включают отчисления на социальное страхование на обязательное медицинское страхование в пенсионный фонд. Размер указанных отчислений в 2012 году составляет 30% от общей заработной платы рабочих что равняется 9329 руб.
2.3 Электроэнергия для технологических целей
Расчет стоимости электроэнергии на технологические цели проводится по формуле: где: (5.8)
qэ – норма расхода электроэнергии на 1 кг. наплавленного металла кВт×ч;
Сэ’ - тариф за 1 кВт×ч потребляемой электрической энергии руб; Сэ’ = 192 руб.
Норма расхода электроэнергии на 1кг. наплавленного металла может быть принята по укрупнённым нормативам или рассчитана по формуле:
2.4 Общепроизводственные расходы
При расчете технологической себестоимости 1 кг наплавленного металла в состав общепроизводственных расходов входят:
а)амортизация сварочного оборудования и источников питания а также транспортных средств:
где Соб – стоимость сварочного оборудования и источников питания руб. Стоимость оборудования принята с учётом затрат на транспортировку и монтаж; Соб = 44 390 руб.
На – годовая норма амортизации по соответствующим видам сварочного оборудования % за 7 лет; На = 1428%
Тном – номинальный (режимный) фонд времени работы за год ч; Тном = 1986 ч. (см. пп.1.7 Общей части проекта; усредненный фонд времени работы)
Ки – коэффициент использования номинального (режимного) фонда времени работы оборудования; Ки=075. (5.11.1)
Транспортные расходы принимаем:
Свс. – стоимость конкретного вида основных производственных фондов тыс.руб
Стоимость монтажа принимаем: См=(15%)*Свс. тыс.руб.(особый монтаж для ИП марки ВДУ-306 ручной дуговой сварки и наплавки не требуется поэтому примем данную статью расходов за 0 руб.)
Полная стоимость: (5.11.2)
Расчет полной стоимости источника питания представлен в таблице 5.2.
Расчет стоимости основных фондов
Наименование видов основных производственных фондов
Стоимость источника тыс.руб.
Выпрямитель дуговой универсальный
б) Затраты на ремонт и межремонтное обслуживание оборудования:
Прем – норма отчислений затрат на ремонт и межремонтное обслуживание; Примем Прем = 5% для единицы источника питания.
в) Прочие затраты по эксплуатации сварочного оборудования:
Затраты по данному направлению можно принимать в размере 5-10%
от суммы предыдущих расходов данной статьи калькуляции “ Общепроизводственные расходы ” что составляет:
4 + 222 = 856*01= 085 руб.
3 Расчет технологической себестоимости 1 кг наплавленного металла. Проектируемый вариант ( наплавка - АДФ)
3.1 Вспомогательные материалы технологического назначения (сварочные материалы)
а) Стоимость сварочных материалов (См) (согласно формуле 5.1)
- цена 1 кг сварочного материала руб.; цена 1 кг. Сварочной проволоки НП – 30ХГСА ; См' = 55 руб.
- коэффициент расхода сварочного материала на 1 кг. наплавленного металла; арм = 11(см.п.2.8.2 Технологической части проекта)
См = 55×11 = 605 руб. на один кг наплавленного металла
б) Стоимость флюса (Сф) (согласно формуле 5.2):
Сф' - цена за 1 кг флюса АН-348 принимается 35 руб.; по формуле(5.3):
3.2 Расчет средств на оплату труда
Согласно формулам (5.4); (5.5); (5.6); (5.7) и п. 5.2.2 и источнику следует:
где Кг - коэффициент учитывающий время горения дуги в общем времени сварки (коэффициент основного времени сварки); в расчетах можно принять для механизированных и автоматизированных способов сварки Кг=065.
Зосн = 418 руб.+209 руб. = 627 руб.
З = 627 + 627 + 1034 = 7931 руб.
Страховые взносы составляют 30% от общей заработной платы и в нашем случае составляют 2379руб.
3.3 Электроэнергия для технологических целей
Согласно пп.5.2.3 формулам (5.8); (5.9) и источнику следует:
3.4 Общепроизводственные расходы
а) Расчет стоимости и амортизации оборудования транспортных средств.
Количество и наименование оборудования выбрано и обосновано в п. 2.7.2 2.7.3 2.7.4 настоящей пояснительной записки. Согласно формулам (5.10) (5.11.1) (5.11.2) и источнику следует:
Стоимость единицы тыс.руб.
Согласно формуле (5.12)
от суммы предыдущих расходов данной статьи калькуляции “ Общепроизводственные расходы ” что составляет (698 руб.+244 руб. )*01 = 094 руб.
Технологическая себестоимость 1 кг. наплавленного металла руб.
Сварочные материалы всего:
- проволока ОК 83.28 НП-30ХГСА
Заработная плата сварщика - общая:
Страховые взносы от заработной платы сварщика
Технологическая электроэнергия
Амортизация оборудования и источников питания
Ремонт и межремонтное обслуживание сварочного оборудования
Прочие затраты по эксплуатации сварочного оборудования
Итого технологическая себестоимость
В заключении обобщим результаты анализа предлагаемых способов сварки оцененные с технологической и экономической точки зрения.
Результаты анализа представлены в таблице 5.5
Технико-экономические показатели способов сварки
Наименование способов сварки
Наименование сварочного оборудования
Цена единицы сварочного оборудования тыс. руб.
Сила сварочного тока А
Напряжение на дуге В
Время наплавки 1кг. металла час.
Технологическая себестоимость руб.в т.ч.
- зарплата сварщиков
- сварочные материалы
- технологическая энергия
Исходя из данных представленных в таблицах 5.1 5.5 можно сделать вывод о том что технологическая себестоимость 1кг. наплавленного металла автоматическим способом наплавки под флюсом будет стоить дешевле чем ручной дуговой сваркой. Разница составляет 64272 руб. Экономия происходит прежде всего за счет заработной платы сварщиков которая напрямую зависит от времени наплавки 1 кг металла в час. При АДФ – время наплавки сокращается значительно – это происходит за счет внедрения в проекте средств механизации и автоматизации и за счет применения оборудования не требующего контроля сварщика (процессом управляет оператор). Технологический анализ рассматриваемых способов также показал что автоматическая сварка под слоем флюса имеет ряд преимуществ над ручной дуговой сваркой основными из которых являются более высокая производительность и меньший расход сварочных материалов высокое качество шва. При внедрении АДФ повышается объем выпуска продукции снижается трудоемкость изготовления снижается коэффициент использования ручного труда.
4 Организация энергетического хозяйства предприятия
Энергетическое хозяйство предприятия — это совокупность энергетических установок и вспомогательных устройств с целью обеспечения бесперебойного снабжения предприятия различными видами энергии и энергоносителей таких как натуральное топливо (газ мазут и др.) электрический ток сжатый воздух горячая вода конденсат.
К основным видам промышленной энергии относятся: тепловая и химическая энергия топлива тепловая энергия пара и горячей воды механическая энергия и электроэнергия.
Задачи энергетического хозяйства предприятия (рис. 5.1):
обеспечение бесперебойного снабжения производства всеми видами энергии;
наиболее полное использование мощности энергоустройств и их содержание в исправном состоянии;
снижение издержек на потребляемые виды энергий.
Рис. 5.1 Задачи энергетического хозяйства
В зависимости от особенностей технологических процессов на предприятиях потребляются различные виды энергий и энергоносителей для обеспечения которыми и создается энергетическая служба. Это электроэнергия тепловая энергия (перегретый пар горячая вода) сжатый воздух газы (природный газ углекислота аргон азот хлор кислород водород) вода разной степени очистки а также централизованные системы отопления канализации (ливневой сточной фекальной химически загрязненной) вентиляции и кондиционирования воздуха.
Структура энергетической службы приведена на рис. 5.2.
Рис. 5.2. Структура энергетической службы предприятия
Функции энергетической службы предприятия:
разработка нормативов касающихся энергетической службы;
планирование потребности во всех видах энергии и энергоносителей составление энергетического баланса предприятия;
планирование ППР оборудования;
планирование потребности в запчастях;
организация выработки (обеспечения) предприятия всеми видами энергии;
оперативное планирование и диспетчирование обеспечения предприятия всеми видами энергии;
организация ремонтных работ оборудования;
разработка технической документации для проведения монтажных ремонтных работ оборудования и энергетических коммуникаций (сетей);
организация обслуживания энергетического оборудования сетей линий связи;
контроль за качеством ремонтных работ;
организация монтажных пусконаладочных работ нового оборудования демонтаж и утилизация списанного энергетического оборудования;
надзор за правилами эксплуатации оборудования;
контроль за расходами всех видов энергии.[22]
Рациональная организация энергетического хозяйства в определенной мере зависит от правильности планирования своей производственно-хозяйственной деятельности нормирования и учета потребления энергоресурсов.
Энергоснабжение предприятия имеет специфические особенности которые заключаются в одновременности производства и потребления энергии. Подача электроэнергии на предприятие на каждый момент времени должна регулироваться объемом потребления. Недостаточно полное ее использование ведет к неизбежным потерям к недоиспользованию мощности. При повышенном против графика потреблении возникают "пиковые" нагрузки.
Определение потребности предприятия в энергоресурсах и учет их расхода основываются на составлении энергетических и топливных балансов. Балансовый метод планирования дает возможность рассчитать потребность предприятия в энергии и топливе различных видов исходя из объема производства на предприятии и прогрессивных норм расхода а также определить наиболее рациональные источники потребления этой потребности за счет получения энергии со стороны и собственного производства ее на предприятии.
Энергетические балансы классифицируются по следующим признакам:
назначению - перспективные текущие отчетные;
видам энергоносителя - частные по отдельным видам энергоносителя (уголь нефть пар газ вода) и общие по сумме всех видов топлива;
характеру целевого использования энергии (силового технологического производственно-хозяйственного значения).
Перспективные балансы составляются на длительный срок и используются при проектировании реконструкции производства и для развития энергохозяйства предприятия в целом.
Текущие плановые балансы составляются на год с разбивкой по кварталам и являются основной формой планирования и потребления энергии всех видов.
Главная задача разработки планового баланса - обоснование плановой потребности предприятия в топливе и энергии для выполнения производственной программы предприятия по выпуску продукции - это расходная часть баланса. Обоснование наиболее рациональных возможность рассчитать потребность предприятия в энергии и топливе различных видов исходя из объема производства на предприятии и прогрессивных норм расхода а также способов покрытия этой потребности получение энергии со стороны и на собственных генерирующих установках - приходная часть баланса.
Отчетные (фактические) балансы предназначены для контроля за потреблением энергоносителей и выполнением плановых балансов а также служат основным материалом для анализа использования носителей оценки работы в области рационализации энергохозяйства и экономии (перерасхода) топлива и энергии.
Определение потребности предприятия в энергоресурсах базируется на использовании прогрессивных норм расхода. Для использования топлива и энергии различных видов применяются удельные нормы.
Под прогрессивной нормой расхода энергии и топлива понимается минимально допустимый ее расход необходимый для изготовления единицы продукции или выполнения единицы работы в наиболее рациональных условиях организации производства и эксплуатации оборудования.
Нормы энергопотребления бывают суммарными на единицу (времени) продукции или вид работ и операционными (дифференцированными) - на деталь операцию отдельный технологический процесс.
Основным методом определения норм расхода является расчетно-аналитический позволяющий рассчитать плановую норму с учетом изменений в режиме работы параметров технологических процессов и других факторов влияющих на величину удельного расхода.
В зависимости от характера целевого использования энергии удельные нормы подразделяются на технологические и вспомогательные нужды (освещение отопление вентиляцию и т. д.). При этом учитываются допустимые потери энергии в сетях.
7. Заключение.doc
В соответствии с выбранным способом наплавки цех планировался таким образом чтобы не создавать затор производства тем самым повышая производительность труда.
Ппредлагаемая технология позволяет снизить выбросы в атмосферу за счет сокращения время наплавки и всего производственного процесса в целом.
2. Технологическая часть.doc
1.Технологическая схема наплавки изделия
Схема технологического процесса наплавки имеет следующую последовательность:
Снятие подшипников со ступицы.
Удаление загрязнений и ржавчины механическим способом. Допускается применение активных реагентов (травление поверхности) с последующей механической обработкой.
Визуальный осмотр изношенной поверхности. Для проведения визуально измерительного контроля используется набор для ВИК. Осмотр проводить согласно РД 03-606-03 «Инструкция по визуальному и измерительному контролю» ПНАЭ Г-7-016-89 «Визуальный и измерительный контроль».
Механическая обработка поврежденной поверхности. Механическая обработка выполняется на токарно-винторезном станке 1М63-М.
Закрепление и центровка балки во вращателе специализированном.
Наплавка. Наплавка ведется в один слой с использованием проволоки НП-30ХГСА и флюса АН-348. В качестве сварочного оборудования используется автоматическая сварочная головка А-1408 и источник питания ВДУ-506.
Визуально-измерительный контроль наплавленной поверхности. Осмотр проводить согласно РД 03-606-03 «Инструкция по визуальному и измерительному контролю» ПНАЭ Г-7-016-89 «Визуальный и измерительный контроль».
Термообработка наплавленного слоя. Для термообработки используется печь ПКМ 6.12.5125. Термообработка служит для снятия внутренних напряжений и выравнивания механических свойств наплавленного металла. Термическая обработка оси состоит из закалки и последующего отпуска. Сначала ось нагревают до 890-910 °С затем следует охлаждение в масле. После закалки для снятия внутренних напряжений проводится отпуск. Ось нагревают до 620-660 °С затем медленно охлаждают на воздухе.
Механическая обработка наплавленной поверхности.
2. Сборка подготовка кромок и предварительный подогрев
Перед наплавкой подготовлена поверхность не должна содержать следов ржавчины оксисных пленок пор трещин наплывов впадин пленов. Для этого необходимо проведение внешнего визуального контроля. Визуальный контроль выполняется набором ВК «Эксперт» по правилам описанным в РД 03-606-03 «Инструкция по визуальному и измерительному контролю» ПНАЭ Г-7-016-89 «Визуальный и измерительный контроль».
Согласно расчетам проведенным в п.1.2.2. перед наплавкой наплавляемую поверхность следует подогреть до 1200С т.к. сталь 35ХМЛ является ограниченно свариваемой.
3. Выбор способа наплавки.
Наплавка - нанесение с помощью сварки слоя металла на поверхность изделия. При восстановлении ремонте наплавку выполняют примерно тем же металлом из которого изготовлено изделие однако такое решение не всегда целесообразно. Иногда при изготовлении новых деталей (и даже при ремонте) целесообразней на поверхности получить металл отличающийся от металла детали. В ряде случаев условия эксплуатации поверхностных слоев значительно отличаются от условий эксплуатации всего остального материала изделия. Так например если деталь (изделие) должна определять общую прочность которая зависит от свойств металла и его сечения то поверхностные слои часто дополнительно должны работать на абразивный или абразивно-ударный износ (направляющие станин зубья ковшей землеройных орудий желоба валков канатно-подъемных устройств и др.). Условия работы могут усложняться повышенной температурой эрозионно-коррозионным воздействием окружающей среды (морской воды различных реагентов в химических производствах и др.). В качестве примера можно указать клапаны двигателей уплотнительные поверхности задвижек поверхности валков горячей прокатки и т.п. Иногда такие детали и изделия целиком изготовляют из металла который обеспечивает и требования к эксплуатационной надежности работы его поверхностей. Однако это не всегда наилучшее и как правило не экономичное решение. Часто оказывается целесообразней все изделие изготовлять из более дешевого и достаточно работоспособного металла для конкретных условий эксплуатации и только на поверхностях работающих в особых условиях иметь необходимый по толщине слой другого материала. Иногда это достигается применением биметаллов (низкоуглеродистая сталь + коррозионно-стойкая сталь; сталь + титан и др.) а также поверхностным упрочнением (поверхностной закалкой электроискровой обработкой и др.) нанесением тонких поверхностных слоев (металлизацией напылением и пр.) или наплавкой слоев значительной толщины на поверхность.
При изготовлении новых изделий в целях обеспечения надлежащих свойств конкретных поверхностей обычно применяют относительно простые стали (например низкоуглеродистые) а на рабочие поверхности наплавляют например бронзу заменяя тем самым целиком бронзовую деталь кислотостойкую сталь (для работы в условиях воздействия соответствующей химически агрессивной среды) или материал хорошо работающий на истирание (при наличии трения с износом) и т.п.
Такие слои можно наносить на наружные поверхности деталей (например валы валки прокатного оборудования рельсовые крестовины и др.) или внутренние поверхности - обычно цилиндрических изделий (корпуса химических и энергетических реакторов оборудование химических производств и др.).
Наплавку осуществляют нанесением расплавленного металла на поверхность изделия нагретую до оплавления или до температуры надежного смачивания жидким наплавленным металлом. Наплавленный слой образует одно целое с основным металлом (металлическая связь). При этом как правило (кроме некоторых случаев ремонтной наплавки применяемой для восстановления исходных размеров деталей) химический состав наплавленного слоя может значительно отличаться от состава основного металла. Толщина наплавленного металла образованного одним или несколькими слоями может быть различной: 05 10 мм и более.
Необходимые свойства металла наплавленного слоя зависят от его химического состава который в свою очередь определяется составом основного и дополнительного металлов и долями их участия в образовании шва. Влияние разбавления слоев основным металлом тем меньше чем меньше доля основного металла в формировании слоя (γ0). В связи с этим для случаев (а их большинство) когда желательно иметь в наплавленном слое состав максимально приближающийся к составу наплавляемого металла необходимо стремиться к минимальному проплавлению основного металла т.е. к уменьшению доли основного металла в металле шва (γ0).
При многослойной наплавке состав каждого слоя различен так как различна доля участия основного металла (на который наплавляют) в образовании наплавленного слоя. Если при наплавке 1-го слоя основной металл непосредственно участвует в формировании шва то при наплавке 2-го и последующих слоев он участвует косвенно определяя состав предыдущих слоев. При наплавке большого числа слоев при некоторых условиях наплавки состав металла поверхностного слоя может быть идентичен дополнительному наплавляемому металлу.
Доля участия основного металла в формировании наплавленного металла зависит как от принятого способа так и от режима наплавки. Различные дуговые методы наплавки отличаются друг от друга тепловой подготовкой основного и наплавляемого металлов. Так например при плазменной наплавке с токоведущей присадочной проволокой тепло-вложение преимущественно осуществляют в присадочную проволоку основной металл подогревается достигающими его поверхности остывающими потоками плазмы дуги и теплотой перегретого жидкого наплавляемого металла. Проплавление основного металла в этом случае может быть заметно уменьшено. Наоборот при дуге прямого действия когда на основном металле располагается катодное или анодное пятно дуги ограничить расплавление основного металла значительно труднее особенно при значительном сосредоточении дугового разряда (уменьшении диаметра плавящегося электрода увеличении плотности тока в электроде). Рассредоточение тепловложения в основной металл например при ленточном электроде когда дуга перемещается по торцу ленты от одного конца к другому и иногда возникает одновременно в нескольких местах может заметно снизить долю расплавляемого основного металла.
Сопоставление долей участия основного металла в 1-м слое различными способами наплавки на обычных режимах приведено в виде диаграммы на рисунке 2.1. Естественно что γ0 зависит также от свойств основного и наплавляемого металлов в частности от их температуры плавления. Например дуговая наплавка покрытыми электродами обеспечивающими наплавленный металл типа алюминиевой бронзы (Тпл = 1000 0С) на низкоуглеродистую сталь дает меньшую долю γ0 чем показано на рис. 2.1 для того же способа наплавки но высоколегированной стали (Тпл = 1420 0С). Определенную роль в этом снижении γ0 играет и увеличение коэффициента наплавки αн (гА*ч) который при бронзовых электродах составляет ~18 г(А*ч) а при электродах из высоколегированной стали ~13 г(А*ч).
Рис 2.1. Доля участия основного металла в первом слое наплавки выполненной различными способами на обычных режимах
- автоматическая под флюсом;
-ручная дуговая покрытыми электродами;
- автоматическая под флюсом с дополнительной присадочной проволокой;
- автоматическая под флюсом ленточным электродом;
- плазменной струей с токоведущей проволокой
Аналогично может влиять и применение при наплавке выполняемой под флюсом или в защитных газах электродной ленты спрессованной из порошков по сравнению с прокатной. Большее электрическое сопротивление спрессованной ленты и ее меньшая теплопроводность приводят к более быстрому ее расплавлению и возможному уменьшению доли основного металла в наплавленном слое.
Обеспечение в наплавленном металле (особенно при однослойной наплавке) требуемого состава в некоторых случаях может потребовать использования дополнительных (присадочных электродных) металлов таких составов при которых ухудшается их деформируемость. Поэтому оказывается невозможным из таких сплавов изготовить электродную проволоку прокатать ленту. В этом случае наплавочные материалы могут быть получены в порошкообразном либо зернообразном виде. Использование порошков и зерен затрудняет наплавку в частности в связи с возможным раздуванием порошков и отсутствием стабильности легирования по длине наплавки из-за сепарации частиц получить необходимый состав металла даже в 1-м слое (правда в основном для небольшой площади наплавки на деталях малых размеров) можно наложением на наплавляемую поверхность предварительно спрессованных из порошков (иногда спеченных или скрепленных какой-нибудь связующей добавкой) наплавочных заготовок (колец и пр.) с последующим их расплавлением и подплавлением располагающегося под заготовкой основного металла.
В целях уменьшения локализации напряжений целесообразно предварительно на основной металл наплавлять подслой с промежуточным значением коэффициента линейного расширения. Такой подслой ограничивает развитие диффузионных прослоек (обезуглероживание в углеродистой стали и появление карбидной прослойки в более легированной аустенитной стали возле линии сплавления) которые после длительной работы наплавленной детали при высоких температурах или после термообработки изделия в некоторых случаях могут снижать эксплуатационные характеристики изделия.
Таким образом в различных случаях при наплавке необходимо комплексно решать ряд сложных вопросов: выбор материала обеспечивающего соответствующие условиям эксплуатации свойства; возможность наплавки этого материала непосредственно на основной металл детали или подбор материала для наплавки подслоя; выбор способа и режима наплавки формы и методов изготовления наплавочных материалов; выбор термического режима для выполнения наплавки (сопутствующего подогрева для исключения получения хрупких подкаленных зон в металле детали или в хрупком наплавленном слое; интенсификации охлаждения наплавляемой детали когда для металла нежелательно длительное пребывание при высоких температурах); установление необходимости последующей термической (общей или местной) обработки (для получения необходимых эксплуатационных характеристик или возможности промежуточной механической обработки).
Способ наплавки выбирают в зависимости от конфигурации наплавляемой поверхности серийности производства требований к качеству наплавленной поверхности.
В таблице 2.1 приведена производительность разных способов наплавки.
Ручная дуговая наплавка покрытым электродом благодаря простоте возможности наплавки на поверхности любой формы широко применяется в промышленности. Доля участия основного металла (m) в образовании слоя при использовании режима обеспечивающих устойчивое горение дуги составляет m=03÷045. Использование поперечных колебаний позволяет снизить долю участия металла до m=025. Однако дальнейшее снижение m увеличивает вероятность образования непровара.
Основные недостатки способа – низкая производительность тяжелые условия труда непостоянство химического состава наплавленного металла из-за неизбежных колебаний проплавления это особенно проявляется при однослойной наплавке.
Ручная дуговая наплавка угольным электродом – используется для наплавки порошковых наплавочных смесей. В частности для создания износостойких слоев на деталях работающих в условиях интенсивного абразивного изнашивания. Наплавку ведут с использованием флюсов. Следует отметить что использование только шлаков не обеспечивает достаточной защиты. По этой причине наблюдается некоторое окисление легирующих элементов и образование в наплавленном металле дефектов: пор неметаллических включений.
Примерная производительность разных способов наплавки
Производительность кгч
Ручная плавящимися электродами
Автоматическая под флюсом:
Автоматическая и полуавтоматическая в углекислом газе
Автоматическая и полуавтоматическая самозащитной порошковой проволокой:
Автоматическая самозащитной порошковой лентой:
электродной проволокой
электродом большого сечения
с токоведущей присадочной проволокой
плазменно-порошковая
с подачей двух плавящихся электродов
Дуговую наплавку в газовой среде производят как в инертных газах так и в активных – главным образом в углекислом газе; реже используют пары воды.
При использовании обычных режимов характерных для сварки в атмосфере защитных газов плавящимся электродов m=045-065. Значительное снижение m достигают использованием наплавки расщепленным электродом порошковой проволокой и особенно лентой импульсного питания дуги.
Дуговая наплавка в газовой среде находит все большее применение благодаря высокой производительности отсутствием трудоемкой операции по удалению шлаковой корки универсальности процесса.
Вибродуговая наплавка – разновидность дуговой наплавки позволяющая за счет использовании вибрации электрода и подачи в зону дуги охлаждаемой жидкости дополнительно воздействовать на свойства наплавляемого металла. При осуществлении процесса амплитуду колебаний (05-3мм) электрода вдоль его оси и расстояния между электродом и наплавляемой поверхностью выбирают таким образом чтобы при вибрации наблюдались короткие замыкании электрода на деталь. При коротком замыкании происходит принудительный перенос электродного металла на поверхность наплавляемого металла. Это стабилизирует процесс наплавки.
Особые условия формирования наплавленного слоя путем последовательного наложения валиков в условиях интенсивного охлаждения приводят к получению наплавленного металла со значительной структурной и механической неоднородностью.
С помощью вибродуговой наплавки обычно осуществляют наплавку слоя металла толщиной 05-3мм. Преимущество способа является возможность наплавки на детали диаметром 8-10мм.
Наплавка лежачим пластинчатым электродом осуществляется за счет теплоты выделяемой в электрической дуге возбуждаемый между пластинчатым электродом и наплавляемой деталью. Для осуществления процесса на поверхность наплавляемой детали насыпают слой флюса толщиной 3-5мм. На слой флюса накладывают пластинчатый электрод конфигурация и размеры которого должны соответствовать контуру наплавляемого слоя. Затем насыпают слой флюса толщиной 12-20мм для создания шлаковой защиты обеспечивающей нормальное протекание процесса. Сверху флюс прижимают медной или графитовой пластиной.
Плазменная наплавка позволяет раздельно регулировать нагрев и плавление как присадочного так и основного металла. Благодаря этому появляется возможность производить наплавку при малой доли участия основного металла в образовании наплавленного слоя.
Способ плазменной наплавки с токоведущей присадочной проволокой обеспечивает устойчивое протекание процесса наплавки с малой долей участия основного металла: при наплавки коррозионно-стойкой стали на низкоуглеродистую m=003-005; при наплавке бронзы на сталь m=0005. Помимо присадочной проволоки для плазменной наплавки используют порошки.
Автоматическая дуговая наплавка под флюсом обеспечивает m=045-065. Введение в зону дуги дополнительно изолированной присадочной проволоки позволяет снизить m до 017. Замена проволоки лентой или использовании электродной проволоки в сочетании с поперечными колебании обеспечивает надежную наплавку при m=008-015. Снижение m до 02-03 достигается при многоэлектродной наплавки когда несколько электродных проволок присоединяют к одному зажиму источнику питания а дуга блуждает с одного электрода на другой и горит в другой полости. Наплавка ведется при использовании плавленых флюсов. Состав флюса и электродной проволоки выбирают в зависимости от состава наплавленного слоя. В качестве электродного металла используют сварочную проволоку применяемую при сварке сплавов из стали специальную электродную проволоку для наплавки по ГОСТ 10543-82 порошковую проволоку и ленту.
Проанализировав все вышеописанные способы наплавки выбираем автоматическую наплавку под флюсом так как этот метод экономически выгоднее а также обеспечивает необходимые химические и физические свойства наплавленного слоя.
Автоматическая наплавка под флюсом обеспечивает стабильные химические и механические свойства наплавленного слоя. Но самое главное преимущество заключается в том что твердость наплавленного слоя составляет в среднем 250НВ то как у заводской детали.
Для сравнения технологий выберем в качестве базового варианта наплавки – наплавку покрытым электродом.
4. Выбор сварных соединений.
Т.к в рассматриваемом дипломном проекте рассматривается процесс наплавки то разделка кромок не производится.
5. Выбор сварочных материалов.
Руководствуясь требованиями к сварочным материалам и тем что твердость наплавленного слоя должна быть не ниже 250 HВ выбираем сварочную проволоку НП-30ХГСА и флюс АН-348 химический состав проволоки приведен в таблице 2.2 химический состав флюса приведен в таблице 2.3.
При выборе электродной проволоки были учтены химический состав наплавляемой детали условия работы характер и вид нагрузки требуемая износостойкость и химический состав наплавочной проволоки.
Используемый при наплавке флюс АН-348 ГОСТ 9087-69 способствует стабильности горения дуги хорошему формированию наплавочного валика обладает пониженной склонностью к образованию пор в наплавленном металле.
Химический состав проволоки НП-30ХГСА
Проволока поставляется в мотках массой 20-80 кг или в бунтах массой
Химический состав флюса АН-348
Для наплавки ручным дуговым способом в качестве сварочного материала выбираем наплавочные электроды ОК 83.28.
Данный электрод используется для наплавки деталей с целью восстановления геометрических пропорций а также для нанесения буферного слоя методом упрочняющей наплавки. С его помощью может осуществляться наплавка таких деталей как зубчатые колеса цапфы бурава для земли валы и рельсы изготовленные из углеродистых сталей; наплавка зубьев ковшей роликов и др. деталей которые постоянно работают в условиях ударного износа и трения металла о металл. Наплавка сталей ведется без предварительного подогрева а температура между проходами составляет менее 90 градусов по Цельсию.
DIN 8555 E1 - UM-300
Типичные механические свойства металла шва
Сопротивление ударному износу
Сопротивление износу при трении металла о металл
6. Технология наплавки.
6.1. Расчет режимов наплавки.
В процессе наплавки оси качество наплавленного металла форма валиков глубина проплавления металла зависят от выбранных режимов наплавки. Определяем силу сварочного тока Iсв.
При наплавке сила сварочного тока определяется по данным таблицы 2.7.
Диаметр наплавочной проволоки выбирается по данным таблицы 2.6.
Зависимость толщины наплавляемого слоя от диаметра электродной проволоки.
Толщина наплавляемого слоя мм
Диаметр электродной проволоки мм
Зависимость силы сварочного тока от диаметра детали и диаметра наплавочной проволоки
Сила тока Iсв (А) при диаметре электродной проволоки мм
При наплавки для снижения глубины проплавления коэффициент а≤30-40 Амм2. Диаметр сварочной проволоки выбирается таким чтобы он обеспечил максимальную производительность наплавки при требуемой глубине проплавления. Выбираем диаметр сварочной проволоки 2 мм.
Проанализировав данные таблицы 2.5 выбираем Iсв=320 А.
Определяем напряжение U по формуле 2.1:
Определим показатель характеризующий удельное значение скорости наплавки коэффициент наплавки Кн по формуле 2.2:
Определим толщину наплавляемого слоя:
Толщина наплавляемого слоя выбирается по таблице 2.1 в зависимости от диаметра сварочной проволоки.
Согласно данным таблицы 2.4 при диаметре электродной проволоки 20 мм толщина наплавляемого слоя составляет 4 мм.
Определяем скорость наплавки Vн.
Скорость наплавки определяем по формуле 2.3:
где F – площадь поперечного сечения валика см2 (при dпр=20 мм F=02 см2); γ – плотность металла шва гсм3.
Определим скорость вращения головки n по формуле 2.4:
Скорость подачи электродной проволоки определяется по формуле 2.5:
При увеличении вылета электродной проволоки повышается электрическое сопротивление цепи что приводит к росту коэффициента расплавления снижению тока наплавки а следовательно и глубины проплавления. Но при увеличении данного параметра ухудшается геометрия наплавленных валиков поэтому вылет электрода выбирается из пределов указанных в формуле 2.6.
Шаг наплавки определяется перекрытием валиков и влияет на волнистость наплавленного слоя:
S=(2-25)dПР мм (2.7)
Число проходов составляет 1 т.к износ поверхности оси составляет 18-23 мм.
Режимы наплавки оси задней балки БЗМ-10
Коэффициент наплавки гАч
Толщина наплавляемого слоя мм
Скорость наплавки мч
Скорость вращения сварочной головки обмин
Скорость подачи электродной проволоки мч
Расчет режима ручной дуговой наплавки покрытым электродом.
Учитывая то толщина наплавленного слоя (4 мм) равна 07 от диаметра электрода принимаем электрод диаметром 3 мм.
)Сварочный ток определим согласно следующей формуле:
где k- коэффициент зависящий от диаметра электрода (k=35-50);
)Определим плотность сварочного тока:
)Определяем оптимальное напряжение дуги:
) Для того чтобы рассчитать скорость сварки необходимо ввести значение коэффициента наплавки.
)Определим показатель характеризующий удельное значение скорости наплавки коэффициент наплавки Кн по формуле 2.2:
)Скорость наплавки определяем по формуле 2.3:
)где F – площадь поперечного сечения валика см2 (при dпр=30 мм F=09 см2); γ – плотность металла шва гсм3.
)Шаг наплавки определяется перекрытием валиков и влияет на волнистость наплавленного слоя:
)Число проходов составляет 1 т.к износ поверхности оси составляет 18-23 мм.
Во время процесса наплавки оси задней балки БЗМ-10 режимы могут регулироваться в пределах 10 %.
6.2. Техника выполнения сварных швов мероприятия по предотвращению и устранению сварочных деформаций.
Технологические приемы и режимы дуговой наплавки зависят от формы и размеров изделий и весьма важны для получения надлежащего качества и состава наплавленного слоя. При этом приходится учитывать разбавление наплавленного металла основным. Такое разбавление необходимо ограничивать. Это может быть достигнуто выбором перекрытия валиков при наплавке каждого (особенно первого) слоя. Так при наложении 1-го доля основного металла γ0 составляет ~065 а при перекрытии по ширине mb = 046 эта доля уменьшается до ~045. В связи с этим такой метод перекрытия весьма распространен при наплавке. При ручной наплавке mb примерно 035 при автоматической под флюсом проволоками кругового сплошного сечения mb = 04 05. Увеличение mb может привести к неблагоприятной форме выпуклости валика и непровару места перехода от предыдущего валика к последующему. Заметно может быть уменьшено значение mb при наплавке ленточным электродом или несколькими плавящимися электродами обеспечивающими в один проход достаточно широкий слой.
Рис. 2.2. Влияние шага наплавки на долю основного металла
в составе наплавленного слоя
а - шаг m близок к ширине валика б; γ0 = 065; b - шаг m = 046 b γ0 = 045
В связи с тем что в большом числе случаев наплавленный слой необходимо подвергать механической обработке наплавка лишнего металла нецелесообразна. Следует стремиться к тому чтобы припуск на обработку не превышал 15 2 мм и после наплавки поверхность была бы достаточно ровной без значительных наплывов и провалов между валиками.
Для обеспечения такой поверхности необходимо наплавку выполнять на оптимальных режимах с применением соответствующих технологических приемов. При сварке под флюсом рекомендуются определенные соотношения между Iсв и Uд (рис. 2.3). При этом увеличение напряжения позволяет получать более широкие валики с плавными переходами у границы сплавления хотя превышение напряжения выше оптимального создает трудности в обеспечении необходимого провара.
Рис. 2.3. Напряжение дуги в зависимости от силы сварочного тока при наплавке под флюсом. Заштрихован оптимальный диапазон
Режимы наплавки определяются также размерами и формой наплавляемой детали. Так при наплавке цилиндрических (и конических) деталей небольшого диаметра по винтовой линии (наиболее распространенная технология) приходится учитывать и возможность стекания ванны усиливающуюся с увеличением ее длины что ограничивает выбор режимов по силе тока и напряжению и увеличивающийся разогрев детали что ограничивает выбор режимов по силе тока и напряжению и увеличивающийся разогрев детали что повышает γ0 и изменяет состав наплавки.
Рекомендации по выбору этих параметров режима для автоматической наплавки под флюсом приведены на рис 2.4.
Определенные технические трудности возникают при наплавке вблизи торца детали и в местах перехода от меньшего диаметра к большему. Для удержания расплавленных шлака и металла у торца прикреплять (приваривать) к нему диск-фланец большого диаметра а в местах перехода к большому диаметру наплавлять валик захватывающий проваром стенку этого перехода.
При наплавке плоских поверхностей небольшой ширины (например торцов ножей ножниц блюмингов) приходится ограничивать стекание шлака и металла в процессе наплавки дополнительными устройствами хотя иногда этого удается избежать подбором режима (уменьшением Iсв и Uд и увеличением Vсв).
Рис. 2.4. Оптимальные диапазоны силы сварочного тока I (а) и скорости перемещения дуги Vд (б) при наплавке под флюсом тел вращения по винтовой линии в зависимости от диаметра наплавляемого изделия.
-одним электродом (диам. 3 35 мм); 2 - то же (диам. 4 5 мм); тремя электродами (диам. 3 35 мм).
При наплавке больших плоских поверхностей когда повышение производительности наплавочной операции становится весьма важным наиболее целесообразно использование многоэлектродных автоматов или ленточных электродов. В частности эти способы благоприятны для уменьшения деформаций наплавляемой детали особенно при ее небольшой толщине.
В связи с тем что процессах наплавки следует стремиться избежать непосредственного воздействия высокотемпературного сварочного источника теплоты на наплавляемую поверхность а соединение наплавляемого слоя с основным металлом осуществляется при минимальном подплавлении наплавляемой поверхности к чистоте этой поверхности при подготовке к наплавке предъявляются весьма высокие требования. В целом наплавка требует тщательной отработки техники и режимов различных для конкретных решаемых задач.
Расплавленный металл электрода и детали защищаются от вредного действия газов воздуха сыпучим флюсом который одновременно сохраняет тепло дуги и предотвращает разбрызгивание металла. Подача электродной проволоки из мотков производится сварочной головкой. Флюс на поверхность детали поступает из бункера.
Электрическая дуга расплавляет конец электродной проволоки и основной металл детали и вытесняет его из кратера. В образовавшийся сварочной ванне происходит перемешивание расплавленного металла электрода и детали и удаление растворенных газов. Начало кристаллизации расплавленного металла происходит на границе с нерасплавленным после этого металл постепенно затвердевает во всем наплавленном объеме.
Флюс плавится позади электрода образуя шлак. Жидкий флюс надежно защищая расплавленную ванну от соприкосновения с воздухом вместе тем не препятствует удалению тазов.
Имея значительный запас тепла расплавленный шлак обеспечивает постепенное охлаждение наплавленного металла. Сам же шлак оставаясь до конца затвердевания металла затем превращается в легкooтделяемую твердую корку.
При автоматической наплавке можно наносить слой металла толщиной от 1 до 40 мм составляющий одно целое с деталью.
Производительность однодуговой автоматической наплавки от 4 до 15 кгч что в 5-10 раз выше производительности ручной электродуговой наплавки. Объясняется это непрерывностью автоматического процесса и возможностью применения большого сварочного тока. Другим важным преимуществом автоматической наплавки является высокое качество наплавленного металла; обусловленное более совершенной защитой жидкой ванны от вредного воздействия воздуха и увеличенной продолжительностью пребывания расплавленного металла в жидком состоянии. Качество автоматической наплавки мало зависит от индивидуального мастерства рабочего. Ее можно вести беззащитных очков щитков или шлемов и без специальной местной вентиляции.
Важнейшим условием получения качественной наплавки является устойчивость дуги которая зависит от многих факторов: рода тока состава флюса соотношения между силой тока и диаметром электрода и др. При автоматической наплавке на переменном токе из-за больших колебаний напряжения в промышленной сети дуга менее устойчива чем при наплавке на постоянном токе от сварочного преобразователя.
Поэтому чаще автоматическую наплавку ведут на постоянном токе. В этом случае напряжение холостого хода должно быть не ниже 60 в.
При автоматической наплавке по неровной поверхности электрическая дуга способна саморегулироваться т.е. не обрываясь удлиняться и укорачиваться.
Наплавку вести постоянным током обратной полярностью (электрод - положительный полюс деталь - отрицательный). Скорость плавления при прямой полярности больше чем при обратной полярности но зависит от состава флюса.
Пpoцесс наплавки протекает нормально если разность уровней жидкого металла в картере поддерживается постоянной. Гидростатическое давление жидкого металла и флюса ypaвновешивается давлением дуги. Поэтому наклон восстанавливаемой детали в ту или иную сторону по отношению к направлению движения электрода создает различные условия для формирования наплавленного валика. При наклоне детали в сторону перемещения электрода т.е при наплавке «на спуск» глубина провара уменьшается а ширина валика увеличивается.
Влияние режима наплавки (силы тока диаметра электрода напряжения и скорости перемещения электрода) на формирование наплавленного валика проявляется следующим образом.
Если при данных напряжении и скорости перемещения электрода повышать силу тока то это вызывает увеличение глубины провара и общей высоты валика при сравнительно малом изменении его ширины так как по мере увеличения силы тока возрастает объем жидкой ванны повышается давление дуги и усиливается вытеснение жидкого металла из кратера. С изменением диаметра электродной проволоки меняется плотность тока а следовательно и давление дуги. При увеличении диаметра проволоки плотность тока и давление дуги падают уменьшается глубина провара и уширяется наплавленный валик.
По мере увеличения напряжения дуги (при прочих равных условиях) возрастает количество тепла приходящееся на единицу длины валика удлиняется дуга уменьшается нагрев краевых участков ванны и повышается количество расплавленного флюса. В результате ширина наплавленного валика увеличивается а глубина провара почти не изменяется. При значительном повышении напряжения дуги расплавляется чрезмерно большое количество флюса и он вытекает из зоны наплавки нередко увлекая за собой и расплавленный металл. Поэтому при автоматической наплавке применять напряжение дуги не более 50 В (расчетное 34 В) тем более что при большем напряжении устойчивость дуги заметно падает.
При различных скоростях наплавки изменяются количества наплавленного металла и тепла приходящиеся на единицу длины валика. Когда наплавку ведут в диапазоне малых скоростей (в пределах до 20 мч) провар получается неглубокий а ширина валика нормальная. В диапазоне средних скоростей (20 – 40 мч) глубина провара увеличивается а ширина валика уменьшается.
От формы поперечного сечения наплавленного валика в большой мере зависит характер кристаллизации металла и взаимное расположение кристаллов после затвердевания всего объема наплавленного металла. Так в узком наплавленном валике с глубоким проваром возможно возникновение стыка кристаллов в котором скапливаются примеси; это может привести к образованию трещин. Более благоприятная форма сечения валика в котором указанные стыки не образуются.
Служебные свойства наплавленного металла в частности износостойкость в значительной степени зависят от его химического состава. Состав наплавленного металла отличается от исходного электродной проволоки и ocновного металла детали так как при наплавке металлы смешиваются и происходит химическое воздействие флюса.
В процессе наплавки в реакцию с железом и примесями стали вступают только некоторые из компонентов флюса – кремнезем закись марганца закись железа. Фосфор из флюса переходит в наплавленный металл в небольших количествах. По-разному ведут себя и примеси входящие в состав основного металла детали и электродного металла. Окисляются и частично удаляются из металла такие элементы как углерод хром ванадий и др. Слабо окисляются никель молибден и медь. Кремний восстанавливаете из флюса и переходит в металл.
Перед наплавкой восстанавливаемую ось очистить от ржавчины масляных и других загрязнений. Использовать флюсы неувлажненные и не загрязненные маслом или другими органическими веществами. Кроме того применять некоторые специальные меры. Уменьшая скорости охлаждения расплавленного металла и скорости перемещения электрода облегчают тем самым удаление газов из зоны наплавки.
Одной из основных мер предупреждающих образование пор в наплавляемом металле является создание таких условий при которых водород окажется связанным в прочных химических соединениях стойких при 7000-8000°С и нерастворимых в расплавленном металле. Такими соединениями является например гидроксил ОН и фтористый водород HF. Фтористый водород - продукт взаимодействия водорода с газообразным тетрафторидом кремния (SiF 4) образующимся в процессе наплавки при взаимодействии содержащихся в флюсе фтористого кальция и кремнезема.
Трещины возникающие в наплавленном металле делятся на горячие и холодные. Горячие трещины образуются в процессе кристаллизации наплавленного металла. Склонность к горячим трещинам при наплавке обусловливается наличием в ней серы и углерода. Марганец образуя сульфиды более тугоплавкие чем сульфиды железа препятствует образованию трещин.
Уменьшить опасность возникновения трещин можно путем ведения наплавки на малых токах с минимальным проплавлением основного металла детали. Другой способ позволяющий избежать горячих трещин - это предварительный подогрев детали перед наплавкой до 1200С.
Холодные трещины возникают под действием остаточных напряжений (главным образом в процессе охлаждения наплавленной детали) вследствие низкой пластичности и малого сопротивления отрыву остываемого наплавленного металла.
Возникновение холодных трещин предупреждается путем сквозного прогрева всей или большей части детали с последующим медленным охлаждением. Охлаждение производят тем медленнее чем больше масса восстанавливаемой детали. Этим достигают плавного и одновременного сокращения: наплавленного слоя и детали. К флюсам используемым при автоматической наплавке предъявляются более жесткие требования в части формирования наплавленного металла устойчивости горения дуги и отделимости шлаковой корки чем к флюсам применяемым при автоматической сварке.
7. Сварочное и вспомогательное оборудование.
7.1. Требования к источникам сварочного тока.
Для осуществления автоматической наплавки под флюсом необходимы в автоматическая сварочная головка и источник питания постоянного тока.
Источник питания сварочной дуги для автоматической наплавки (сварки) под флюсом должен выбираться таким образом чтобы обеспечить выполнение следующих условий:
должен обеспечивать расчетные режимы наплавки.;
должен обладать требуемой (жесткой) вольт-амперной характеристикой (ВАХ);
соответствовать работе в определенных условиях (цеховые) и климатическом районе;
стоимость оборудования должна быть максимально мала при условии сохранения качества и обеспечения постоянства выбранных режимов сварки.
7.2. Выбор сварочного оборудования.
Проанализировав рассчитанные режимы сварки в качестве источника питания сварочной дуги выбираем универсальный сварочный выпрямитель ВДУ-506 по ГОСТ 13821-77.
ВДУ-506С - регулируемый тиристорный выпрямитель с жесткой или падающей внешней характеристикой. Предназначен для комплектации полуавтоматов и автоматов а так же для ручной дуговой сварки изделий из стали покрытыми электродами на постоянном токе в среде защитных газов. Оптимален для цеховых условий при сварке на токах дуги до 450А (ПВ=100%) Предназначены для работы с любыми сварочными тракторами.
ВДУ-506 является универсальным источником питания обладает необходимыми жесткими ВАХ.
Что немаловажно ВДУ-506 выпускается в Российской Федерации что благоприятно сказывается на его стоимости и на себестоимости готового изделия в целом.
Краткие характеристики выпрямителя:
Плавное регулирование тока в режиме ММА и напряжения в режиме МIGMAG
Защита от тепловой перегрузки
Быстросъемные токовые разъемы
Принудительное охлаждение
Технические характеристики ВДУ-506 приведены в табл. 2.9.
Технические характеристики ВДУ-506
Напряжение питающей сети В
Частота питающей сети Гц
Номинальный сварочный ток А (ПВ ПН %)
Пределы регулирования сварочного тока А
Напряжение холостого хода В не болеет
Рабочее напряжение на дуге В
Потребляемая мощность кВА не более
Габаритные размеры мм
Для осуществления автоматической наплавки под слоем флюса балки задней оси БЗМ-10 использовать автоматическую сварочную головку А-1408.
Рис.2.5 Сварочный автомат А-1408:
-подающий механизм; 2-суппорт; 3-механизм вертикального перемещения; 4-флюсовая аппаратура; 5-кассета с электродной проволокой; 6-пульт управления.
А-1408 обеспечивает сварку и наплавку под флюсом.
Автомат подвесной самоходный предназначен для дуговой сварки сплошной проволокой под слоем флюса низкоуглеродистых и легированных сталей на постоянном токе с независимыми от параметров дуги скоростями сварки и подачи электродной проволоки. Глубокое регулирование скорости подачи электродной проволоки и скорости сварки получаемое сменными шестернями обеспечивает широкий диапазон применения автомата.
Технические характеристики сварочного автомата А-1408
Технические характеристики
Номинальное напряжение сети В
Частота тока питающей сети Гц
Номинальный сварочный ток А
Диапазон регулирования сварочного тока А
Количество электродов
Диаметр сплошной электродной проволоки мм:
Пределы плавного регулирования скорости подачи электродной проволоки мч
Диапазон ступенчатого регулирования скорости сварки мч
Поперечное перемещение сварочной головки:
Габаритные размеры мм:
Для наплавки покрытым электродом используется в качестве источника питания отечественный выпрямитель ВД-306.
Технические характеристики ВД-306
Продолжительность нагрузки (ПН)
Диапазон регулирования сварочного тока
Напряжение холостого хода
Сварочный выпрямитель ВД-306 предназначен для питания электрической сварочной дуги постоянным током при ручной дуговой сварке резке и наплавке металлов при трехфазном питании от сети переменного тока.
Климатическое исполнение сварочного выпрямителя ВД-306 "У" категория размещения 3 тип атмосферы по ГОСТ 15543-70 и ГОСТ 15160-69 но для работы при нижнем значении температуры окружающей среды от 233К (-40°C) до 313К (+40°C). Оборудован устройством тепловой защиты обмоток трансформатора и блоков диодов от перегрева.
7.3. Выбор средств технологической оснастки.
Рис.2.6 Вращатель специализированный
-основание; 2-направляющая; 3-регулируемая роликоопора; 4-подвижное основание; 5- рукоять регулировки упора; 6-рукоять регулировки опоры; 7-бабка с зажимами;
-механизм привода вращателя; 9-шкаф управления; 10-приборная доска.
Для поворота оси во время наплавки используем вращатель специализированный. Общий вид вращателя представлен на рис.2.6.
Для удержания автоматической сварочной головки А-1408 выбираем передвижную сварочную тележку ПКТ-17.
Общий вид тележки ПКТ-17 представлен на рис.2.7
Рис.2.7 Передвижная сварочная тележка ПКТ-17
-холостое шасси; 2-приводное шасси; 3-напраляющая (рельс); 4-блок продольного передвижения; 5- тяга (для буксировки и установки); 6-опорная штанга; 7-направляющая штанга
-траверса; 9-приводная колонна траверсы; 10-электродвигатель траверсы; 11-инспекционный лючок; 12-ограничитель; 13-корпус электропривода траверсы
7.4. Выбор вспомогательного оборудования.
Для перемещения заготовок в ходе технологического процесса наплавки используется консольный кран.
Технические характеристики крана приведены в таблице 2.12– 2.13.
Технические характеристики консольного крана
На рисунке 2.8 показан общий вид консольного крана.
Рис. 2.8. Консольный кран.
Скорость вращения консоли
Угол поворота консоли
Общее передаточное число
А 100L BB У3 №=15 кВт; n=750 обмин
С подвесного кнопочного пульта
Для перемещения партии наплавленных осей используется кран балка грузоподъемностью до 10 тонн. Технические характеристики крана приведены в таблице 2.11.
Рис.2.9 Кран балка КР-10
Технические характеристики крана балки КР-20
Скорости механизмов мс
диапазоны регулирования скорости
Основные габаритные размеры мм.
Тип подкранового рельса.
Нагрузка на колесо при раб. не более Кн
Для выполнения механической обработки оси перед и после процесса наплавки выбираем токарно-винторезный станок 1М63-М.
На рис. 2.10 приведен общий вид станка 1М63-М.
Рис.2.10 Токарно-винторезный станок 163-М
Отличительные особенности станка 1М63-М:
Тяжелые токарно-винторезные станки с отличным комплектом поставки отличающиеся повышенной плавностью хода и отсутствием вибраций.
Закаленные и шлифованные направляющие станины.
Закаленный шпиндель из высокопрочной легированной стали установленный на регулируемые прецизионные роликоподшипники.
Закаленные шлифованные шестерни и валы передней бабки.
Быстродействующая коробка подач закрытого типа с закаленными шлифованными шестернями и валами работающими в масляной ванне и установленными на прецизионные подшипники.
Все метрические и дюймовые резьбы устанавливаются рукоятками на панели управления без использования сменных шестерен.
Центральная система смазки направляющих.
Система подачи СОЖ: удобный и гибкий шланг подачи СОЖ с дозирующим краном.
Задняя бабка может быть смещена на ± 13 мм для точения длинных конусов
Продольная и поперечная подачи суппорта.
Поворотная на 360° верхняя каретка суппорта
Кнопка аварийного отключения станка запирающийся главный выключатель.
Возможна установка привода быстрого хода суппорта
Подставка под станок с отделениями под инструмент
Произведено согласно нормам DIN 8606
Технические характеристики станка 1М63-М
Наибольшая длина обрабатываемой детали мм
Наибольший диаметр обработки над станиной мм
Наибольший диаметр обработки над суппортом мм
Наибольший диаметр обработки над выемкой станины мм
Длина выемки станины мм
Частота вращения шпинделя обмин
Частота вращения шпинделя модификации Vario обмин
Количество ступеней
Внутренний конус шпинделя
Присоединительная поверхность шпинделя
Диаметр сквозного отверстия в шпинделе мм
Ход верхней каретки суппорта мм
Ход поперечной каретки суппорта мм
Внутренний конус пиноли задней бабки
Перемещение пиноли задней бабки мм
Продольная подача ммоб
Поперечная подача ммоб
Пределы шага нарезаемых метрических резьб мм (54 шага)
Пределы шага нарезаемых дюймовых резьб ниток на дюйм (60 шагов)
Пределы шага нарезаемых трапецеидальных резьб (42 шага)
Пределы шага нарезаемых модульных резьб (46 шага)
Высота державки резца мм
Среди многообразия токарных станков особо стоит выделить токарно-винторезные станки. Это один из самых эффективных видов металлорежущих станков. Они позволяют проводить обработку черных и цветных металлов их применяют при изготовлении шпинделей осей гильз и многих других деталей. С помощью таких станков возможно как мелко серийное так и единичное производство. Токарно-винторезные станки способны выполнять различные виды токарных работ при этом отличаются высокой точностью. На них производится также нарезка резьбы. В качестве материала для изготовления режущего инструмента применяются композитные материалы обладающие значительной износостойкостью. Мы предлагаем своим клиентам станки полностью отвечающие всем требованиям современного производства. Эти станки обеспечивают обработку деталей с прогрессивными режимами резания удобны в управлении высокомеханизированы. Несмотря на свои небольшие размеры они отличаются высокой производительностью а их демократичная цена делает приобретение подобного станка еще и экономичным.
8. Нормирование сварочных работ.
8.1. Расчет норм времени.
Нормативы времени на установку отдельных деталей и узлов при сборке конструкции прихватку дуговой сваркой крепление деталей а также кантовку узлов в процессе сборки определяются по соответствующим таблицам "Общемашиностроительных нормативов времени на слесарно-сборочные работы при сборке металлоконструкций под сварку и наплавку". Расчет времени на сборку металлоконструкции под наплавку производится по формуле:
где - подготовительно-заключительное время на сборку металлоконструкций под сварку (мин);
- сумма затрат времени на установку деталей конструкции при сборке в приспособлении (мин);
- сумма затрат времени на крепление и открепление деталей конструкции при сборке в приспособлении (мин);
- сумма затрат времени на прихватку деталей конструкции при сборке в приспособлении (мин);
- сумма затрат времени на поворот и кантовку узлов (сборочных единиц) конструкции при сборке в приспособлении (мин).
Ввиду специфики проведения наплавки формула 2.8 упрощается и имеет вид:
Нормы подготовительно – заключительного времени устанавливаются на основе фотографий рабочего дня сварщика.
Нормативы подготовительно – заключительного времени приведены в таблице 2.16
Подготовительно – заключительное время при автоматической сварке под флюсом
Автоматическая сварка под флюсом
Время на партию в минутах
Получение производственного задания указания и инструктажа
Ознакомление с работой
Установка величины сварочного тока
Установка скорости сварки изменением положения рукоятки
Установка подачи электродной проволоки изменением положения рукоятки
Подготовка приспособлений:
регулирование подставки под наплавку
Исходя из данных таблицы 2.16 рассчитываем подготовительно – заключительное время путем суммирования показателей:
ТП.З=50+30+03+01+01+20+30+03=128 мин.
Основное время при автоматической сварке под флюсом – это время плавления электрода или время чистого горения дуги.
Основное время 1 пог.м. рассчитывается по формуле 2.10:
γ – удельный вес наплавленного металла; принимается равным удельному весу основного металла (785 гсм3);
F1 Fn – площадь поперечного сечения первого и последующего слоев мм;
I1 In – сварочный ток первого и последующих слов А;
αн – коэффициент наплавки гАч.
αн зависит в основном от плотности тока а также от состава электродной проволоки и флюса напряжения дуги диаметра электродной проволоки и вылета проволоки из мундштука. С увеличением плотности тока αн возрастает.
В нашем случае αн=127 гАч.
Вспомогательное время считается в зависимости от длинны шва. Оно охватывает следующие элементы рабочего времени: очистка наплавленного слоя от шлака промер и осмотр наплавленного слоя сбор флюса и ссыпку его в бункер возврат сварочной головки в исходное положение засыпание флюса в процессе наплавки.
Нормы времени на эти элементы работы установлены на основе хронометража наблюдений.
Вспомогательное время рассчитывается путем суммирования показателей указанных в таблице 2.17.
Вспомогательное время связанное со свариваемым швом при автоматической наплавке под флюсом
Наименование элемента работы
Норма времени на 1 пог.м шва в минутах
Очистка наплавленного слоя от шлака
Промер и осмотр наплавленного слоя
Сбор флюса и ссыпка его в бункер
Возврат сварочной головки в исходное положение
Засыпание флюса в процессе наплавки
Тв=030+28+04+07+70=112 (мин) (2.11)
Нормирование времени обслуживания рабочего места. Время обслуживания рабочего места при автоматической сварке под флюсом затрачивается на: раскладку и уборку инструмента включения и выключения источника питания сварочной дуги регулировку режимов сварки (тока скорости сварки подачи проволоки) установку кассеты с электродной проволокой в автомат и заправку флюсом в бункер вначале работы уборку электродной проволоки и флюса после окончания работы смену кассет подналадку оборудования уборку рабочего места.
Нормы времени на обслуживание рабочего места определяются по данным фотографии рабочего дня сварщика и исчисляются в процентах к оперативному времени.
В нашем случае время на обслуживание рабочего места составляет 75 минут.
Нормирование времени на отдых и естественные надобности ведется на основе фотографий рабочего дня сварщика и эти нормы времени исчисляются в процентах к оперативному времени.
Норма времени на естественные надобности составляет 2 % от оперативного времени а время на отдых 8 % от оперативного времени.
В нашем случае опираясь на фотографии рабочего дня сварщика:
время на естественные надобности Тен=3 мин;
время на отдых Тотд=5 мин.
Для облегчения подсчета нормы штучного времени вводится коэффициент к оперативному времени учитывающий затраты времени на обслуживание рабочего места отдых и естественные надобности.
Расчет нормы времени производят по формуле 2.12.
Тв – вспомогательное время зависящее от длины шва на 1 пог.м. шва;
Тв.и – вспомогательное время связанное с изделием и работой оборудования мин;
К1 – коэффициент учитывающий затраты времени на обслуживание рабочего места отдых и естественные надобности сварщика. Учитывая то что наплавка ведется в три прохода:
Рассчитаем время затрачиваемое на наплавку одной оси с учетом закрепления и механической обработки:
ТИ=ТШ+ТМ+ТТ мин. (2.13)
ТМ – время затрачиваемое на механическую обработку мин.
ТТ – время транспортировки от токарно-винторезного станка до наплавочного участка включая время на транспортировку после наплавки от наплавочного участка до токарно – винторезного станка составляет и обратно также учтено время на транспортировку гтовой оси 10 мин.
ТМ=ТЗ + ТО + ТC мин. (2.14)
ТЗ – время закрепления (в это время учтено и время наладки оборудования) составляет 10 мин.
ТО – время обработки оси на токарно-винторезном станке составляет 15 мин (предварительная обработка) 25 мин. обработка после наплавки итого 40 мин.
ТС – время снятия детали составляет 15 мин.
ТМ=10+ 40+ 15=515 мин
ТИ=144+515+10=2055 мин.=34 ч.
Также необходимо учесть время термообработки и предварительного подогрева 25 часа термообработка и 05 часа предварительный подогрев.
8.2. Расчет расхода сварочных материалов.
Расход электродной проволоки:
где- потребность сварочной проволоки на единицу продукции кг;
- коэффициент использования проволоки по справочным данным ;
– масса наплавленного металла на единицу продукции (кг).
Потребность в сварочном флюсе зависит от расхода сварочной проволоки и определяется по формуле (2.16):
где- расход (масса) сварочного флюса на единицу продукции кг;
- коэффициент использования флюса по справочным данным .
Расход электродов для базового варианта наплавки определяется по формуле:
где - расход электродов с покрытием на единицу продукции кг;
- коэффициент расхода электродов определяется паспортным данным (17 гч).
9. Разработка плана участка.
На наплавочном участке предусмотрены проточная и принудительная вентиляции пожарные щиты и краны. Также предусмотрены емкости с песком и технической водой. Наплавочный участок снабжен аварийной пожарной сигнализацией при ее срабатывании аварийно прекращается подача электрического тока на участок и срабатывает сигнал тревоги. В обеспечение пожарной безопасности наплавочного участка также включено аварийное потолочное и напольное освещение.
Планом участка предусмотрен подвод электрической энергии ко всему оборудованию. Все кабели и провода заизолированы и проложены по специальному каналу находящимся под полом участка. Такое технологическое решение было принято для сведения повреждения токопроводящих кабелей к минимуму.
Также планом участка предусмотрена расстановка обогревательного оборудования для поддержания рабочей температуры.
Осветительное оборудование расставлено таким образом чтобы оно не мешало работе сварщиков но и не было слишком тусклым.
План цеха обеспечивает максимальную загрузку и минимальный простой оборудования. Технологический план наплавочного участка представлен в графической части дипломного проекта.
001. Содержание.doc
2. Требования нормативной документации.
3. Характеристика материала для изготовления изделия оценка его свариваемости.
3.1. Структура и свойства материала изделия.
3.2. Расчет свариваемости.
4. Прокат для изготовления изделия.
5. Выбор способа получения заготовок.
6. Требования к основным и сварочным материалам.
7. Выбор типа производства.
Технологическая часть.
1.Технологическая схема изготовления изделия.
2. Сборка подготовка кромок и предварительный подогрев.
3. Выбор способа сварки.
4. Выбор сварных соединений.
5. Выбор сварочных материалов.
6. Технология сварки.
6.1. Расчет режимов сварки.
6.2. Техника выполнения сварных швов мероприятия по предотвращению и устранению сварочных деформаций.
7. Сварочное и вспомогательное оборудование.
7.1. Требования к источникам сварочного тока.
7.2. Выбор сварочного оборудования.
7.3. Выбор средств технологической оснастки.
7.4. Выбор вспомогательного оборудования.
8. Нормирование сварочных работ.
8.1. Расчет норм времени.
8.2. Расчет расхода сварочных материалов.
9. Разработка плана участка.
Контроль качества при изготовлении изделия.
1. Требования к качеству сварных швов.
2. Предварительный контроль.
3. Операционный контроль.
4. Приемочный контроль.
4.1 Выбор метода контроля.
4.2. Выбор параметров и схемы контроля.
4.3. Выбор оборудования и оснастки.
Конструкторская часть.
1. Обоснование выбора сборочно-сварочных приспособлений.
2. Разработка принципиальной схемы приспособления.
3. Расчет сварочных деформаций и зажимных усилий.
4. Выбор типа установочных и зажимных элементов.
5. Расчет зажимных элементов приспособлений.
6. Расчет электромеханического оборудования приспособлений.
7. Выбор стандартного механического оборудования.
Организационно-экономическая часть.
Безопасность и экологичность проекта.
Список использованной литературы.
Приложения: технологическая карта процесса изготовления теплообменника.
1-1 ось.dwg

10 План цеха - Ершов.dwg

Склад наплавленных деталей.
Участок проведения механической обработки.
Склад обработанных деталей.
Участок проведения термообработки.
Склад готовых деталей.
Установка наплавочная.
Выпрямитель ВДУ-1202.
Токарно - винторезный станок 1М63-М.
Печь для термообработки.
Местный вентиляционный отсос.
Приточно - вытяжная вентилялиция
Зона опасности движущихся машин
Рабочее место сборщика.
Рабочее место сварщика.
Заезд автотранспорта.
Условные обозначения:
9. Организация энергетического хозяйства.dwg

Организация монтажных
пусконаладочных работ
демонтаж и утилизация
Обеспечение бесперебойного снабжения
производства всеми видами энергии
Наиболее полное использование мощности
энергоустройств и их содержание в
Снижение издержек на потребляемые
Организация энергетического хозяйства на предприятии
Задачи энергетического хозяйства
3 головка наплавочная.dwg

Механизм подачи флюса
Предохранительный щиток
Блок предохранителей
Барабан с проволокой
Патрубок подачи флюса
8. Экономический Лист - Ершов.dwg

Технологическая себестоимость
- сварочные материалы
- зарплата сварщиков
- технологическая энергия
Технико-экономические
Наименование способов наплавки
Технико-экономические показатели способов наплавки
Наименование сварочного оборудования
Сила сварочного тока
Время наплавки 1 кг. металла
6 схема расположения оборудования.dwg

2 схема базирования.dwg

8 режимы наплавки.dwg

Подготовка поверхности
Токарно-винторезный станок 1М63-М
обработанной поверхности
Предварительный подогрев
Печь для термообработки
Механическая обработка
УЗК дефектоскоп EPOCH-1000
1 сборочник балки.dwg

Неуказанные предельные отклонения по IT142
Допускается сварка в смеси газов
5 вращатель.dwg

Рукоять регулировки упора
Рукоять регулировки опоры
Механизм вращателя с электроприводом
Шкаф управления вращателем
Технические характеристики
Длинна основания 3340 мм
Общая длинна (с механизмом и шкафом управления) 3920мм
Допустимый диаметр загтовки:
Допустимая длинна заготовки:
максимальная 2450 мм
Нагрузка на роликоопору не более 500 кг.
* Размер для справок
4 тележка.dwg

Блок привода продольного передвижения
Приводная колонна траверсы
Электродвигатель привода траверсы
Корпус электропривода траверсы
* Размер для справок
Возможно использование для автоматической сварки
Рекомендуемые чертежи
- 25.10.2022
- 22.07.2023