Вилка карданного вала




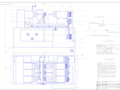
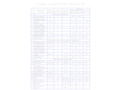
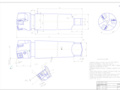
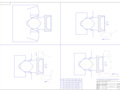
- Добавлен: 25.10.2022
- Размер: 3 MB
- Закачек: 0
Описание
Состав проекта
![]() |
![]() ![]() |
![]() ![]() |
![]() |
![]() |
![]() |
![]() |
![]() ![]() ![]() ![]() |
![]() ![]() ![]() ![]() |
![]() |
![]() |
![]() |
![]() ![]() ![]() ![]() |
![]() |
![]() ![]() ![]() ![]() |
![]() ![]() ![]() ![]() |
![]() |
![]() |
![]() ![]() |
![]() ![]() ![]() |
![]() ![]() |
![]() |
![]() ![]() ![]() ![]() |
![]() |
![]() ![]() ![]() ![]() |
![]() ![]() ![]() ![]() |
![]() |
![]() ![]() ![]() ![]() |
![]() ![]() |
![]() ![]() |
![]() ![]() |
![]() |
![]() ![]() ![]() ![]() |
![]() |
![]() ![]() |
![]() ![]() |
![]() ![]() |
![]() |
![]() ![]() |
![]() |
![]() |
![]() ![]() |
![]() ![]() ![]() ![]() |
![]() |
![]() ![]() ![]() ![]() |
![]() ![]() |
![]() ![]() |
![]() |
![]() ![]() ![]() ![]() |
![]() ![]() ![]() ![]() |
![]() ![]() ![]() ![]() |
![]() ![]() |
![]() ![]() ![]() ![]() |
![]() ![]() |
![]() ![]() |
- Архиватор zip файлов
- Компас или КОМПАС-3D Viewer
- AutoCAD или DWG TrueView
- Microsoft Word
- Microsoft Excel
Дополнительная информация
Алмазно расточной станок.dwg

Вид заготовки - поковка.
Обрабатывемый материал - сталь 35 ГОСТ1050-74.
Общее количество электродвигателей
Суммарная мощность электродвигателей
Компоновка алмазно-расточного
Кран управления установить в месте удобном
Несоосность осей шпинделей головок станка
и отверстия приспособления не более 0.005.
Допуск параллельности осей шпиндельных головок
станка и осей посадочных отверстий приспо-
собления направлению движения стола не более
025 на длине 500 мм.
собления в вертикальной плоскости не более
Кулачки в пазу подвижного стола установить
обеспечив выполнение цикла работы
Выдержка времени для торможения шпинделей
Технические требования
Техническая характеристика
Приспособ._контр.dwg

спецификация_головка_раст.dwg

Головка расточная фланцевая
РТК.dwg

спецификакция зенкер.dwg

2170(3).doc
В данном дипломном проекте был спроектирован участок механической обработки вилки карданного вала. Было рассмотрена технология получения готовой детали из заготовки и разработана новая технология исключающая недостатки старой. Был принят современный станок позволяющий изготавливать деталь не используя другое оборудование. Было спроектировано и расчитано контрольное приспособление режущие головки. Был разработан план участка механической обработки. В экономическом разделе были проведены расчеты сравнения базового проекта и нового по разным показателям. В разделе безопасности жизнедеятельности были рассмотрены возможные вредные факторы и меры защиты от них.
1 Назначение и описание узла изделия7
2 Группирование деталей подлежащих изготовлению на участке10
3 Служебное назначение детали и технические требования предъявляемые к ней13
ТЕХНОЛОГИЧЕСКАЯ ЧАСТЬ14
1 Анализ технологичности детали14
2 Проектирование технологического маршрута обработки16
3 Описание действующего технологического процесса17
4 Выводы из анализа и предложения по разработке проектного варианта технологического процесса21
4.1 Анализ действующего технологического процесса21
4.2 Предложения по усовершенствованию технологического процесса21
5 Разработка проектного технологического процесса22
5.1 Обоснование и выбор методов обработки22
5.2 Оформление маршрутной технологии22
5.3 Расчет припусков и межоперационных размеров заготовки.25
5.4 Обоснование и выбор оборудования средств автоматизации и механизации29
5.5 Обоснование и выбор режущего инструмента средств оснащения и контроля33
5.6 Расчет режимов резания36
6 Проектирование участка59
6.1 Описание планировки участка59
6.2 Организация ремонта оборудования на участке60
6.3 Организация управления участком63
КОНСТРУКТОРСКАЯ ЧАСТЬ65
1 Проектирование станочного приспособления65
1.1 Расчет тягового усилия на штоке гидроцилиндров приспособления66
1.2 Расчет приспособления на точность69
2 Проектирование контрольного приспособления71
3 Проектирование режущего инструмента74
3.1 Проектирование и расчет торцовой фрезы74
3.2 Проектирование и расчет зенкера79
ЭКОНОМИЧЕСКАЯ ЧАСТЬ83
1 Годовая программа и форма организации производственного участка83
2 Потребность в производственном оборудовании83
3 Производственная площадь85
4 Основные и вспомогательные материалы85
5 Расчет численности работающих86
6 Расчет ФЗП и среднемесячной зарплаты93
7 Электроэнергия и энергоносители99
8 Себестоимость и цена продукции100
9 Капитальные вложения100
10 Эффективность рассматриваемых вариантов технологического процесса101
БЕЗОПАСНОСТЬ ЖИЗНЕДЕЯТЕЛЬНОСТИ104
1 Анализ проектного технологического процесса на наличие потенциально опасных и вредных факторов104
2 Мероприятия по электробезопасности111
3 Мероприятия по пожарной безопасности участка115
БИБЛИОГРАФИЧЕСКИЙ СПИСОК119
Технология машиностроения - это наука об изготовлении машин требуемого качества в установленном производственной программой количестве и в заданные сроки при наименьших затратах живого и овеществленного труда т.е. при наименьшей себестоимости.
Научно-технический прогресс в машиностроении в значительной степени определяет развитие и совершенствование всего народного хозяйства страны. Важнейшими условиями ускорения научно-технического прогресса являются рост производительности труда повышение эффективности общественного производства и улучшение качества продукции.
Совершенствование технологических методов изготовления машин имеет при этом первостепенное значение. Качество машины надежность долговечность и экономичность в эксплуатация зависят не только от совершенства ее конструкции но и от технологии производства. Применение прогрессивных высокопроизводительных методов обработки обеспечивающих высокую точность и качество поверхностей деталей машины методов упрочнения рабочих поверхностей повышающих ресурс работы деталей и машины в целом эффективное использование современных автоматических и поточных линий станков с программным управлением (в том числе и многооперационных) электронных вычислительных машин и другой новой техники применение прогрессивных форм организации и экономики производственных процессов - все это направлено на решение главных задач: повышения эффективности производства и качества продукции.
1 Назначение и описание узла изделия
Данная деталь «Вилка» является составным элементом карданного вала среднего моста автомобиля ПАЗ. Материалом детали служит сталь 35 твердостью 207 255 НВ.
Вилка предназначена для соединения карданного вала с механизмом дифференциала среднего моста и передачи крутящего момента. В процессе работы вилка испытывает напряжения кручения.
В два отверстия 035 мм (поверхность А) вставляется крестовина и запрессовываются два подшипника качения в которых и базируется крестовина. Крестовина затем вставляется в отверстия вилки привариваемой к трубе карданного вала.
С механизмом дифференциала вилка стыкуется по пазовой поверхности и крепится к нему с помощью шпильки вставляемой в центральное отверстие диаметром 20 мм. Шпилька обеспечивают силовое замыкание между вилкой и фланцем механизма дифференциала.
Поверхности вилки условно можно разделить на следующие группы:
Главные рабочие поверхности:
А - Внутренняя цилиндрическая поверхность мм - отверстие под подшипник качения - выполнена по 7-му квалитету точности имеет шероховатость поверхности Rz = 40. Допуск соосности отверстия относительно базовой оси в диаметральном выражении 0030 мм
Б - Наружная торцовая цилиндрическая поверхность паза под фланец механизма дифференциала - выполнена по 9-му квалитету точности имеет шероховатость поверхности Rz - 20. Допуск симметричности торцовых поверхностей относительно базовой плоскости симметрии в радиусном выражении 0.075 мм.
В - Наружная торцовая цилиндрическая поверхность паза под фланец механизма дифференциала - выполнена по 9-му квалитету точности имеет шероховатость поверхности Rz - 20. Допуск симметричности торцовых поверхностей относительно базовой плоскости симметрии в радиусном выражении 0.075 мм.
Поверхности неподвижных разъемных соединений:
Г - Внутренняя цилиндрическая поверхность мм - отверстие под шпильку -выполнена по 9-му квалитету точности имеет шероховатость поверхности Rz = 20. Допуск на позиционное отклонение отверстия в диаметральном выражении 0.4 мм.
Д - Внутренняя цилиндрическая поверхность мм - отверстие под болты -выполнена по 9-му квалитету точности имеет шероховатость поверхности Rz = 80.
Остальные поверхности:
Е - Торцовая поверхность проушин (размер 60 мм) - выполнена по 9-му квалитету точности имеет шероховатость поверхности Rz = 40. Допуск перпендикулярности торцовых поверхностей проушин относительно общей оси отверстий проушин 01 мм.
Рисунок 1.1 – Конструктивные элементы детали «Вилка»
2 Группирование деталей подлежащих изготовлению на участке
На данном участке обрабатываются детали схожей конфигурации и отличающиеся как правило друг от друга габаритными размерами поэтому будет целесообразно производить их на одном участке по одной технологии с учетом индивидуальных особенностей. На этом участке необходимо поместить оборудование которое сможет обрабатывать всю номенклатуру деталей и при этом имеет высокую степень переналаживаемости для снижения затрат на переналадку оборудования а также одним из самых важных факторов является загрузка оборудования. Всем этим требованиям отвечает алмазно-расточный станок на базе модели 2706 и отделочно-расточный полуавтомат 66.43.001.
Деталями представителями являются:
Скользящая вилка (рисунок 1.2)
Рисунок 1.2 – Скользящая вилка
Вилка-фланец (рисунок 1.3)
Рисунок 1.3 – Вилка-фланец
Фланец (рисунок 1.4)
Рисунок 1.4 – Фланец
Корпус наружного уплотнения (рисунок 1.5)
Рисунок 1.5 – Корпус наружного уплотнения
3 Служебное назначение детали и технические требования предъявляемые к ней
К вилке предъявляются следующие технические требования:
Твердость 207 255НВ.
Класс точности поковки Т4 группа стали М2 степень сложности С4 исходный индекс 14 ГОСТ 7505-89.
Технические требования к поковке по гр. И ГОСТ 8479-70.
Неуказанные штамповочные уклоны 7°.
Неуказанные штамповочные радиусы 3 мм.
ТЕХНОЛОГИЧЕСКАЯ ЧАСТЬ
1 Анализ технологичности детали
Отработка конструкции детали на технологичность представляет собой комплекс мероприятии по обеспечению необходимого уровня технологичности конструкции по установленным показателям направлена на повышение производительности труда снижение затрат и сокращение времени на изготовление изделия при обеспечении необходимого его качества Отработку конструкции на технологичность рекомендуется проводить в следующем порядке: подобрать и проанализировать исходные материалы требующиеся для оценки технологичности конструкции; уточнить объем выпуска; проанализировать показатели технологичности базовой конструкции определить показатели технологичности обрабатываемого изделия; разработать мероприятия по улучшению показателей технологичности.
Оценка технологичности конструкции может быть двух видов: качественная и количественная. Качественная оценка характеризует технологичность конструкции обобщенно на основании опыта исполнителя и допускается на всех стадиях проектирования как предварительная. Количественная оценка технологичности конструкции изделия выражается числовыми показателями и рациональна в том случае если эти показатели существенно влияют на технологичность рассматриваемой конструкции.
Анализируя технологичность конструкция по применяемым материалам следует учитывать их обрабатываемость стоимость и дефицитность материалов изучить возможность применения легкого но более прочного материала или повышения физико-механических свойств имеющегося.
В качестве материала для изготовления вилки принимаем сталь 35 ГОСТ 1050-74. Данный материал имеет широкое распространение и не является дефицитным обладает относительно невысокой стоимостью и хорошей обрабатываемостью и обеспечивает необходимые физико-механические свойства.
По геометрической форме деталь представляет собой набор элементарных поверхностей (плоскости наружные и внутренние цилиндрические поверхности) что значительно облегчает обработку. Плоские поверхности можно обработать фрезерованием внутренние цилиндрические - сверлением растачиванием и др. наружные цилиндрические — точением. Геометрическая форма приемлема для получения заготовки в штампах.
Оценка технологичности конструкции по простановке размеров связана с анализом нанесения размеров на чертеже детали определением размерных связей между конструкторскими технологическими и измерительными базами и возможности их совмещения. Особое внимание следует обратить на обоснованность значений допустимых предельных отклонений размеров и формы поверхностей детали значений шероховатостей.
Самыми точными размерами являются размеры внутренней цилиндрической поверхности диаметром 35 мм. Она выполняется по 7-му квалитету точности и имеет шероховатость поверхности Rz=40. Соответствующий данной точности размеров допуск соосности поверхности относительно базовой оси в диаметральном выражении 0030 мм.
Боковые поверхности проушин не являются рабочими поверхностями и могут быть выполнены с шероховатостью Rz=40 мкм.
Технологичность заготовки характеризуется возможностью ее получения наиболее рациональным для данных производственных условий способом с максимально возможным приближением ее формы и размеров к форме и размерам готовой детали при условии обеспечения технологичности дальнейшей механической обработки.
Заготовку вилки можно получить двумя способами: штамповкой или литьем. Поскольку материал стать 35 не льется то остается способ получения заготовки штамповкой.
Качественная оценка технологичности конструкции детали характеризуется следующими показателями: "хорошо" - "плохо" "допустимо" - "недопустимо". Базовый вариант конструкции после проведения качественной оценки можно охарактеризовать как "допустимо".
В ходе изменения требований к конструкции детали я попытался добиться оптимальных показателей точности и качества поверхностей детали после чего конструкции детали можно дать оценку "хорошо".
2 Проектирование технологического маршрута обработки
Основной задачей этого этапа является составление общей последовательности обработки детали формулировка содержания операций технологического процесса и выбор типа оборудования.
При этом рекомендуется учитывать следующие положении:
Каждая последующая операция должна уменьшать погрешности и улучшать качество поверхности.
В первую очередь следует обрабатывать поверхности будут выступать в качестве технологических баз при дальнейшей обработке.
Затем следует обрабатывать поверхности с которых снимается наибольший слой металла что позволит своевременно обнаружить возможные внутренние дефекты заготовки.
Операции при которых возможно появление брака из-за внутренних дефектов в заготовке следует производить в начале.
Обработка остальных поверхностей ведете в последовательности обратной степени их точности: чем точнее должно 6brfJ» поверхность тем позже она обрабатывается
Заканчивается обработка той поверхностью которая является наиболее точной и имеет наибольшее значение для эксплуатации детали.
Отверстия нужно сверлить в конце технологического процесса за исключением случаев когда они служат базами для установки.
Не рекомендуется совмещение черновой и чистовой обработки немерным инструментом на одном и том же станке.
Если деталь подвергается термической обработке по ходу технологического процесса то механическая обработка расчленяется на две части: до термической обработки и после нее.
Технический контроль намечают после тех этапов обработки где повышается вероятность повышения брака перед сложными и дорогостоящими операциями после законченного цикла а также в конце обработки детали.
3 Описание действующего технологического процесса
При анализе была рассмотрена документация по детали вилка карданного вала (51-2201022-А): чертеж детали режущий инструмент контрольное приспособление станочное приспособление технологические карты маршрутная карта операционные эскизы и т.д.
Базовый технологический процесс выглядит следующим образом.
Операция 005 Агрегатная.
Здесь производится предварительная подготовка установочной технологической базы в качестве которой выступает торец вилки и полная обработка вспомогательных баз в качестве которых выступают поверхности ушек вилки.
В качестве оборудования используется специальный станок. Состав данной операции:
поз. I. Установить и закрепить заготовку на станке.
поз. II. Подрезать торец выдержав размер 29 мм с Rz=20 .
поз. III Обточить фланец выдержав размер 76 мм и шероховатость Rz=20
поз. IV Обточить фланец выдержав размер 71 мм и шероховатость Rz=20.
поз. V Обточить фланец выдержав размер 71.5 мм и шероховатость Rz=80.
поз. VI. Подрезать торец выдержав размер 25 мм с Rz=80
поз. VII Зенковать 2×150 мм с шероховатостью Rz=80
поз. VIII Снять заготовку.
В качестве режущего инструмента используются сменные многогранные пластинки т твердого сплава сверла и зенкеры и быстрорежущей стали. Мерительный инструмент: штангенглубиномер ШГ-160-01 ГОСТ3882; штангенциркуль ШЦ-1-125-01 ГОСТ 166 штангенрейсмас ШР-250-005 ГОСТ 164
Операция 010. Транспортная
Транспортировать тару с заготовками с операции 005 на загрузочную позицию автоматической линии.
Оборудование: кран подвесной электрический.
Вся дальнейшая обработка производится на автоматической линии (операция 015) состоящей т специальных агрегатных станков. Здесь выполняется обработка торцов проушин и отверстий в них.
поз I Загрузить заготовку вручную на транспортер автоматической линии. С транспортера заготовку автоматически загрузить на приспособление спутник с помощью манипулятора автоматическая рука.
поз II. Автоматически установить и нажать заготовку в ориентированном положении на приспособлении-спутнике.
поз.III IV Фрезеровать торцы проушин выдержав размеры 60*01 мм и Rz=40.
поз. V Сверлить 2 отверстия в проушинах вилки выдержав размеры 33±002 мм
поз. VI. Контролировать наличие отверстия 33 мм.
поз. VII. Расточить 2 отверстия в проушинах вилки выдержав размеры 35
поз. VIII Зенковать отверстия 1×450
поз. IX. Контролировать 2 отверстия 35
поз. X. Автоматически раскрепить деталь и передать ее на транспортер автоматической линии а приспособление-спутник на возвратный путь линии В качестве режущих инструментов используются фрезы с механическим креплением твердосплавных сменных режущих пластик сверла шнековые с механический креплением твердосплавных пластин расточные оправки с механическим креплением режущих пластин раскатка.
В качестве мерительных инструментов применяются калибры-пробки штангенциркули щуп контрольный.
С транспортера автоматической линии заготовка поступает на сверлильный станок.
Операция 020 Сверлильная
поз I. Установить и закрепить заготовку на станке
поз II. Сверлить два отверстия под резьбу напроход выдержав размеры 4 мм Rz=40.
Нарезать резьбу М6 кл2 на глубину 10 мм.
Зенковать 2 отверстия 1×900
поз.III Снять заготовку.
Оборудование: специальный вертикально-сверлильный станок
Режущий инструмент: цековка из быстрорежущей стали.
Со станка при помощи крана тара с заготовками поступает на позицию слесарной обработки (операция 030) где выполняется снятие заусенцев. После этого деталь промывают (операция 035) на моечной машине фирмы "Дюрр" и контролируют (операция 040).
4 Выводы из анализа и предложения по разработке проектного варианта технологического процесса
4.1 Анализ действующего технологического процесса
К недостаткам данного технологического процесса можно отнести следующие:
Между предварительным и окончательным этапами обработки торца вилки производится обтачка фланцев. Сначала должна быть полностью обработана торцовая поверхность поскольку она является базовой поверхностью при дальнейшей обработке и с нее снимается наибольший слой металла.
Торцевая поверхность проушин фрезеруется за два прохода хотя параметр шероховатости данной поверхности составляет Rz=40 и точность размеров соответствует 14-му квалитету что выдерживается и за один проход.
4.2 Предложения по усовершенствованию технологического процесса
В базовом варианте технологического процесса операции сверления отверстий расточки отверстий фрезерования фасок происходит на разном оборудовании. Предлагаю объединить все операции и выполнить изготовление детали на одном станке.
5 Разработка проектного технологического процесса
5.1 Обоснование и выбор методов обработки
Поскольку деталь не является телом вращения то в процессе обработки она должна находиться в неподвижном состоянии. При этом главное движения я движение подачи сообщается инструменту.
На первом этапе происходят следующие операции:
Подрезать торец у диаметра 715.
Проточить наружные диаметры 715 и 76.
Снять фаски наружные и внутренние.
Сверлить и расточить отверстие диаметром 20.
Зенкеровать отверстие диаметром 35.
Расточить отверстие 35 до .
Снять внутреннюю фаску.
Сверлить отв. под резьбу.
Снять резьбовые фаски.
5.2 Оформление маршрутной технологии
Маршрутная карта является обязательным документом и заполняется в соответствии с требованиями ГОСТ 3 1104-74 и ГОСТ 3 1105-74.
В маршрутной технологии производится сокращенное описание всех технологических операций в последовательности их выполнения без указания технологических переходов и режимов обработки
В первую очередь перед тем как приступить к реализации технологического процесса необходимо изучить требования техники безопасности на производстве в том числе пожарной безопасности.
Первым этапом технологического маршрута будет входной контроль (операция 005). Здесь необходимо проконтролировать следующие параметры исходной заготовки:
- марка материала (по маркировке);
- размеры заготовки (штангенциркулем);
- наличие поверхностных дефектов (визуально);
- наличие термообработки (твердомером).
Только после этого можно начинать механическую обработку. Выбор оборудования на данном этане является предварительным: Анализ рациональности использования данного оборудования будет осуществлен позже.
Операция 010 Агрегатная.
Подрезать торец у диаметра 715.
Оборудование: токарно-расточный станок.
Операция 015 Агрегатная.
Проточить наружные диаметры 715 и 76.
Операция 020 Агрегатная.
Снять фаски наружные и внутренние
Операция 025 Агрегатная.
Сверлить и расточить отверстие диаметром 20
Операция 030 Агрегатная.
Операция 035 Агрегатная.
Зенкеровать отверстие диаметром 35
Операция 040 Агрегатная
Расточить отверстие 35 до .
Оборудование: токарно-расточный станок
Операция 045 Агрегатная
Операция 050 Агрегатная
Сверлить 4 отверстия под резьбу.
Операция 055 Агрегатная
Снять резьбовые фаски.
Операция 060 Агрегатная
Операция 065 Слесарная.
Операция 070 Моечная.
Операция 075. Контрольная.
Контролировать деталь.
Маршрутная технология оформляется в виде маршрутной карты где указывается наименование операций применяемое оборудование приспособления и инструмент.
5.3 Расчет припусков и межоперационных размеров заготовки.
Рисунок 2.1 – Схема установки заготовки при обработке
Расчет притоков и назначение их по таблицам ГОСТ следует производить после отработки конструкции детали и заготовки на технологичность и технико-экономического обоснования метода получения заготовки.
Наряду с необходимыми исходными данными в начале расчета припусков необходимо выполнить эскиз заготовки с указанием схемы ее установка на станке или в приспособлении и выделением поверхностей для которых рассчитываются припуски на обработку.
Назначение припусков опытно-статистическим метолом следует вести по таблицам соответствующих стандартов. Для назначения припусков на стальные штампованные поковки используются данные ГОСТ 7505-74 где также приведены данные по допускам на штампованные поковки.
Произведем расчет припусков и межоперационных размеров для обработки отверстия 35 мм. Заданная точность достигается операциями сверления растачивания чернового и чистового и раскатывать.
Исходная заготовка — штамповка 4-го класса точности.штамповки 7.5 кг.
Схема базирования при обработке данного отверстия показана на рисунке 2.1.
Расчет припусков оформляют в виде таблицы в которую последовательно записывают технологический маршрут обработки отверстия и все значения элементов припуска.
Суммарное значение пространственных отклонений для заготовки данного типа:
Таблица 1 - Результаты расчета припусков для наружной цилиндрической поверхности 76
Технологический переход
Расчет. размер dр мм
Предельные размеры мм.
Предельные значения припусков мкм.
обтачивание черновое
Обтачивание чистовое
zmin=(Rzi-1+hi-1+ρi-1)=2(60+696)=13392 мкм
zmin=(Rzi-1+hi-1+ρi-1)=2(100+174)=548 мкм
zmin=(Rzi-1+hi-1+ρi-1)=2(600+2900)=7000 мкм
d= dmin(i-1)+ 2zmin1000
dmin(9)= 75978 +2·66961000=76112мм
dmin(13)= 76112 +2·2741000=76660 мм
dmin(заг.)= 76660 +2·35001000=77660 мм
Таблица 2 - Результаты расчета припусков для наружной цилиндрической поверхности 715
Обтачивание черновое
dmin(10)=71.428+2·66961000=71.561мм
dmin(13)=71.561 +2·2741000=72109 мм
dmin(заг.)=72109+2·35001000=76609 мм
Таблица 3 - Припуски для внутренней цилиндрической поверхности
Наименование перехода
Операционный размер мм
Тонкое растачивание
Таблица 4 - Припуски для внутренней цилиндрической поверхности 20
5.4 Обоснование и выбор оборудования средств автоматизации и механизации
Вопросы выбора групп типов и моделей оборудования рассматриваются на различных стадиях технологической подготовки производства Общие правила выбора технологического оборудовании установлены ГОСТ 14.404-73. Предварительный выбор группы оборудования производится при назначении метода обработки поверхности обеспечивающего выполнение технических требовании к обрабатываемым поверхностям. Затем при разработке технологического маршрута обработки и его технико-экономическом обосновании производится выбор конкретной модели станка на основании минимума приведенных затрат на рабочем месте. Для выполнения расчетов по приведенной методике необходимо располагать данными о цене габаритах мощности и производительности станка что ведет к необходимости назначения конкретной модели станка уже на этом этапе проектирования технологического процесса Таким образом для операций принятых на основании сравнения приведенных затрат рабочем месте вопрос о выборе оборудования решен уже на стадии составления маршрута механической обработки.
Однако в дипломном проекте при составлении маршрута механической обработки лишь небольшая часть операций принята на основании подробных экономических расчетов. Остальные операции намечены на основании имеющихся типовых решений рекомендуемых справочной литературой. Для этих операции необходимо производить выбор оборудования на данной стадии проектирования
Выбор модели станка прежде всего определяется его возможностью обеспечить точность размеров и формы а также качество поверхности изготавливаемой детали. Если эти требования можно обеспечить обработкой на различных станках определенную модель выбирают из следующих соображений:
) соответствие основных размеров станка габаритам обрабатываемых деталей устанавливаемых по принятой схеме обработки:
) соответствие станка по производительности заданному масштабу производства.
) возможность работы на оптимальных режимах резания
) соответствие станка по мощности;
) возможность механизации и автоматизации выполи немой обработки;
) наименьшая себестоимость обработки;
) реальная возможность приобретения станка;
) необходимость использования имеющихся станков.
Выбор оборудования производится уже на стадии составления технологического маршрута механической обработки.
В условиях массового производства нужно стремиться к тому чтобы на одной операции было задействовано не более одного-двух станков. Если это условие не выполняется следует выбрать более производительную модель станка.
Используя приведенные выше рекомендации произведем выбор оборудования для осуществления технологического процесса изготовления вилки.
Остановим свой выбор на станках с ЧПУ.
Режущий инструмент является составной частью комплексной автоматизированной системы станка с ЧПУ.
Режущий инструмент для станков с ЧПУ должен удовлетворять следующим требованиям: обеспечению высоких и стабильных режущих характеристик обеспечению заданных условий по точности обработки; универсальности применения для типовых обрабатываемых поверхностей деталей на разных моделях станков. В качестве материалов для изготовления лезвийного инструмента для станков с ЧПУ используют: твердые сплавы керамику сверхтвердые синтетические материалы и быстрорежущие стали.
Вспомогательный инструмент должен обеспечивать крепление основного инструмента и удовлетворять следующим основным требованиям: быть достаточно жестким иметь высокую точность и стабильность базирования и крепления режущего инструмента выполнять все технологические характеристики станка легко и быстро устанавливаться и сниматься обеспечивать настройку инструмента вне станка.
В настоящее время широко применяются системы унифицированного вспомогательного инструмента которые можно охарактеризовать как наборы вспомогательного и специального режущего инструмента обеспечивающие закрепление всего стандартного режущего инструмента с качеством необходимым для полной реализации технологических возможностей различных станков с ЧПУ. Системы вспомогательного инструмента предназначены для компоновки специальных функциональных единиц инструментальных блоков(комбинации режущего и вспомогательного инструмента) каждый из которых служит для выполнения конкретного технологического перехода. Требования: минимальность номенклатуры и стоимости инструмента; точность жесткость и виброустойчивость крепления; удобство обслуживания быстросменность.
Правила применения средств механизации и автоматизации технологических процессов установлены ГОСТ 14.309-74 Согласно стандарту» механизации и автоматизации подлежат объекты с целью снижения материальных и трудовых затрат повышения качества изделий и увеличения объема выпуска продукции. Выбранный вариант технологического процесса с установленными средствами механизации и автоматизации должен обеспечивать наибольшую экономическую эффективность.
При соответствующем технико-экономическом обосновании объектами механизации и автоматизации в дипломном проекте могут являться:
- загрузка перемещение и зажим заготовки;
- управление станком;
- рабочие движения станка и обрабатываемой детали в процессе обработки;
- уборка транспортирование стружки и др.
Объектами автоматизации могут быть:
- загрузка и зажим заготовки;
- рабочие движения станка и детали;
- межоперационный транспорт и др.
На токарно-расточном станке объектами механизации являются зажим и перемещение заготовки управление рабочими движениями станка Зажим заготовки осуществляется с помощью гидросистемы а перемещение - за счет поворота патрона станка. При этом стружка со станка удаляется в стружкоуборочный канал специальными скребками прикрепленными к тому же поворотному патрону станка.
Контроль размеров (позиции 6 и 9 левая) выполняется щупами.
В качестве межоперационного транспорта возьмем подвесной цепной грузонесущий конвейер. Также участок необходимо снабдить электрическим краном (электроталью).
5.5 Обоснование и выбор режущего инструмента средств оснащения и контроля
Правила выбора технологической оснастки (приспособления инструменты и средства контроля) устанавливает ГОСТ 14.305-84. При этом правила выбора средств технологического оснащения процессов технического контроля устанавливайся ГОСТ 14.306-84.
Выбор режущего и вспомогательного инструмента.
В операции 010 был использован следующий инструмент:
Сверло спиральное с цилиндрическим хвостовиком (по ОСТ 2И20-1-80) предназначено для обработки конструкционных материалов. Материал режущей части Р6М5.
Вспомогательный инструмент
Для данных операций (станок E-280) будем использовать систему вспомогательного инструмента регламентированную РТМ 2П10-2-84.
Сверло и фрезу устанавливаем в цанговый патрон используя вкладыши для патрона цангового для установки необходимого диаметра.
В операциях 015 - 035 был использован следующий инструментальный комплект:
Резец проходной с квадратной пластиной из твердого сплава используется для патронной обработки деталей тапа фланцев обеспечивает наружное обтачивание проточку торцев выточек и снятие фасок. Материал режущей части Р6М5. Сменные пластины резца крепятся конусной головкой винта непосредственно к опорной поверхности державки. Преимуществом этой конструкции резцов является компактность узла крепления хороший отвод стружки с открытой передней поверхности высокая надежность и быстрая смена пластин.
Резец проходной с ромбической пластиной из твердого сплава позволяет обтачивать деталь по цилиндру протачивать обратный конус отрабатывать радиусные и переходные поверхности и протачивать торцы. Материал режущей части Р6М5. Сменные пластины резца крепятся конусной головкой винта непосредственно к опорной поверхности державки.
Фреза концевая твердосплавная цельная с цилиндрическим хвостовиком (ГОСТ 18372-73) предназначены для чистовой и черновой обработки деталей.
Короткий метчик с проходным хвостиком для метрической резьбы (ГОСТ 3266-81) предназначен для нарезания метрической резьбы.
Резец расточной для глухих отверстий со стальным хвостовиком (ГОСТ 18063-72) предназначен для расточки глухих точных отверстий диаметром от 3 мм.
Для данных операций (станок Romi E-280) будем использовать набор унифицированного инструмента с цилиндрическим хвостовиком (Размеры державок 16х16 - 40х40 мм).
Резец 1 и 2 будет закреплен в резцедержатель с цилиндрическим хвостовиком с перпендикулярным открытым пазом.
Фрезу устанавливаем в цанговый патрон используя вкладыши для патрона цангового для установки необходимого диаметра.
Метчик необходимо установить в специальный патрон регулируемый резьбонарезной который предохраняет метчик от поломки. Патрон в свою очередь устанавливается в державку для регулируемых патронов втулок и оправок.
Резец необходимо установить в патрон регулируемый расточной который устанавливается в державку для регулируемых патронов втулок и оправок.
Крепление вспомогательного инструмента осуществляется через шпиндель.
Операция 040. Слесарная.
Режущим инструментом служит фреза ВК8 ГОСТ18945-73. Вспомогательный инструмент - рукавицы виброзащитные ГОСТ 2.4.002-97 очки защитные ГОСТ 12.4.013-97.
Выбор мерительного инструмента
Точность средств измерения должна соответствовать точности контролируемых поверхностей и иметь диапазон измерения больший чем измеряемый размер.
При выборе измерительных средств нужно также учитывать экономические показатели: их себестоимость; время затрачиваемое на настройку и измерение; надежность и стабильность работы; продолжительность работы до ремонта. Необходимо в максимальной степени использовать стандартные измерительные средства В массовом и крупносерийном производстве применяются специальные контрольные приборы для комплексной проверки деталей по многим показателям точности устройства активного контроля в процессе обработки и др.
Поскольку у нас производство крупносерийное то будем стремиться к использованию специальных средств измерения.
В технологическом процессе используются различные измерительные приборы: штангенциркули и микрометры.
Этими инструментами контролируется размер выборочно оператором одной из 10-20 деталей.
Характеристики измерительных инструментов.
Штангельциркуль ШЦ –1-125-0.1 ГОСТ 166-80
Пределы измерения 0-125 мм.
Микрометрический прибор МРИ по ГОСТ 4381-80
Пределы измерения 0-500 мм.
Цена деления 0.002 мм
Также используются: калибры и калибры-пробки меритель.
5.6 Расчет режимов резания
Назначение режимов резания на обработку торца – поверхность 1 припуск на обработку мм.
Для обработки детали берем резец подрезной оснащенный пластинкой из твердого сплава Т15К6.
Глубина резания при снятии припуска за один проход мм.
Рекомендуемое значение подачи ммоб
Определяем скорость резания в зависимости от глубины резания подачи и стойкости инструмента.
Рекомендуемая скорость резания определяется по формуле ммин:
где – коэффициент в формуле скорости резания;
– период стойкости инструмента мин;
– глубина резания мм;
– показатели степени в формуле скорости резания;
– коэффициент учитывающий влияние материала заготовки;
– коэффициент учитывающий состояние поверхности заготовки;
– коэффициент учитывающий материал режущей части инструмента.
По расчетной скорости резания и диаметру обрабатываемой детали находим требуемое число оборотов шпинделя:
где – расчетная скорость резания ммин;
– диаметр обрабатываемой детали мм.
Поз. I – Черновая проточка отв. 76
Поз. II – Черновая проточка отв. 715
Поз. III – Получистовая проточка отв. 76
Поз. IV – Получистовая проточка отв. 715
Поз. I – Фаска наружная 2×450
Поз. II – Фаска внутренняя 25×450
Поз. I – Сверление отв. 20
So(сверл)=SotK1soK4so (2.5)
K1so и K4so – поправочные коэффициенты учитывающие механические свойства обрабатываемого материала и глубину обрабатываемого отверстия;
So(сверл)=041х105=043 ммоб
по паспорту станка принимаем:
действительная скорость резания:
Поз. II – Получистовая расточка отв. 20
Глубина резания t=5 мм
Диаметр фрезы D=40 мм.
Определение величины подачи
Номинальное значение подачи Szt=013 ммзуб
Поправочные коэффициенты:
Ksm=095 KsH=11 KsB=1 Ksφ=09 KsP=1 KsC=1.
Окончательное значение подачи:
Sz= Szt Ksm KsH KsB Ksφ KsP KsC (2.7)
Sz= 0.13 0.95 1.1 1 0.9 1 1=0.14 ммзуб
Определение скорости и мощности резания.
Номинальное значение скорости резания - VT = 125 ммин.
Номинальное значение мощности резания -NT= 20 кВт.
Kvm=135 KNm=08 Kva=09 KNa=1 Kvn=KNn=08 Kvφ=KNφ=1 KVB=11 KNB=14 KVT=06 KNT=1 KVP=KNP=1
Окончательное значение скорости резания;
V0= VT Kvm Kva Kvn Kvφ KVB KVT KVP (2.8)
V0= 125 09 135 08 1 11 06 1=80 ммин
Окончательное значение мощности резания:
глубина резания t = 35 мм
длина зенкерования 14 мм
Поз. I – Черновая расточка отв. 35
Поз. II – Получистовая расточка отв. 35
Поз. III – Чистовая расточка отв. 35
Определение основного (машинного) времени:
где – длина обработки мм;
– величина врезания и перебега мм;
– число оборотов шпинделя обмин;
Таблица 5 – Сводная таблица режимов резанья
скорость резания ммин
число оборотов обмин
Оп. 010 – Агрегатная
Оп. - 020 Агрегатная
Оп.- 030 Агрегатная.
Зенкеровать отверстие 35
Фаска внутренняя 1×450
Сверлить 4 отверстия под резьбу М6
Снять резьбовые фаски 1×450 с 4 отв.
Нарезать резьбу 4 отв М6
Таблица 6 – Сводная таблица основного времени
Длина врезания и перебега мм
6 Проектирование участка
6.1 Описание планировки участка
Ширина пролета здания цеха где расположен проектируемый участок зависит от размеров обрабатываемых деталей применяемого технологического и грузоподъемного оборудования и средств транспорта. Шириной пролета здания L - называется расстояние между осями подкрановых стоек или колонн. Ширину пролета принимаем равную 18 м.
Высоту пролета механического цеха принимаем в зависимости от размеров изготовляемых изделий габаритных размеров технологического оборудования (по высоте) размера и конструкции мостового крана а также санитарно-гигиенических требований Н=18м по 9.
Выбираем сетку колонн сетка колонн: ширина пролета 18 метров шаг колонн 12 метров. Колонны данного пролета маркируются порядковыми номерами: поперек здания буквами А Б вдоль пролета цифрами 1 2 3 4.
Нормы расстояний между станкам и элементами здания цеха:
от проезда до фронта боковых сторон станков 700 мм
от колонн до тыльной стороны станка 1200 мм
Заготовки и готовые детали размещаются в специальных контейнерах.
В качестве транспортного средства для перемещения стружки к местам сбора выбираем тележку расположенную около. Транспортирование заготовок на станки от станка производится вручную.
Около проезда рядом с колонной располагаются первичные средства пожаротушения: ящик с песком и щит пожарной охраны.
На участке имеется мостовой кран грузоподъемностью 20 тонн для перемещения тяжеловесных грузов станков.
Общая высота здания цеха Н определяется по расстоянию от потолка до вершины кранового рельса Н и расстоянию от вершины головки подкранового рельса до нижней точки строительной затяжки К.
Согласно 9 Н состоит из следующих величин:
Н =h1+h2+h3+h4+h5м (2.12)
где h1 – высота наиболее высокого станка в цехе (центральный склад накопитель). Эта величина принимается равной 2800 мм.
h2 – расстояние между транспортируемым грузом поднятым в крайнее верхнее положение и верхней точки наиболее высокого станка. Это расстояние принимается равным 400 мм.
h3 – высота наибольшего по размеру перемещаемого груза в транспортном положении. Эту величину принимаем равной 2500 мм.
h4 – расстояние от верхней кромки наибольшего по размеру транспортируемого груза до центра кромки крана в верхнем его положении принимаем равной 400 мм.
h5 – расстояние от верхней кромки до горизонтальной линии проходящей через вершину головки рельса принимаем равной 1000 мм.
H1=2800+400+2500+400+1000=7100 мм
Корректируем согласно нормативным величинам и принимаем H1=71м
Высота до низа конструкции перекрытия H=8 м.
6.2 Организация ремонта оборудования на участке
Ремонтное хозяйство - это совокупность общепроизводственных и цеховых подразделений предприятия осуществляющих мероприятия по техническому обслуживанию и ремонту оборудования. Его основные задачи:
предупреждение преждевременного износа оборудования и поддержание его в постоянной технической готовности;
сокращение простоев при выполнении технического обслуживания и ремонта;
повышение качества ремонтных работ и уменьшение затрат на их выполнение;
внедрение прогрессивных форм средств и методов ремонта;
обеспечение постоянной безаварийной работы оборудования;
модернизация оборудования.
Основой организации ремонтного хозяйства его фундаментом является система технического обслуживания и ремонта - совокупность взаимосвязанных средств документации технического обслуживания и ремонта и исполнителей необходимых для поддержания качества машин и оборудования. Её составные части: ремонтно-обслуживающая база кадры западные части и ремонтные материалы нормативно-техническая документация. Цель функционирования системы - обеспечение требуемого уровня надежности изделия в заданных условиях эксплуатации при минимальных удельных затратах на техническое обслуживание и ремонт. Система технического обслуживания и ремонта включает конструкторскую технологическую и организационно-экономическую подготовку.
Исправное состояние и работоспособность машин и оборудования в течение всего периода их эксплуатации обеспечивается техническим воздействием которое подразделяется на техническое обслуживание и ремонты. Техническое обслуживание (ТО) - это комплекс операций или операция по поддержанию работоспособности или исправности оборудования при использовании по назначению ожидании хранении и транспортировании. Различают виды ТО: периодическое регламентированное сезонное. ТО может быть плановым и внеплановым. Типовой системой технического обслуживания оборудования предусмотрено выполнение осмотров. Ремонт - это комплекс мероприятий по восстановлению работоспособности исправности оборудования. Различают виды ремонта: капитальный средний малый. Технологическим элементом технического обслуживания и ремонта является диагностика - совокупность мероприятий в системе технического обслуживания и ремонта для получения информации о состоянии оборудования с целью прогнозирования его ресурса определения необходимого объема ремонтных работ управления своевременным и качественным их выполнением.
По концентрации выполняемых работ техническое обслуживание может быть организовано по централизованной децентрализованной или смешанной системе. Различают также следующие виды организации ремонта: обезличенный необезличенный тупиковый агрегатный последовательно-агрегатный смешанный.
Постоянная техническая готовность и высокая работоспособность оборудования предприятия обеспечивается единой системой планово-предупредительного ремонта (ППР). В условиях системы ППР потребность оборудования в технических обслуживаниях и ремонтах удовлетворяется через установленный объем наработки в соответствии с ремонтным циклом. Перечень и последовательность выполнения видов технического обслуживания и ремонтов представляет собой структуру ремонтного цикла.
О – М – О – М – О – С – О – М – О – М – О – С – О – М – О – М – К
где О - профилактический осмотр оборудования;
К - капитальный ремонт.
Управление системой технического обслуживания и ремонта осуществляется на предприятиях службой главного механика во взаимодействии с цеховыми и другими службами и отделами предприятия. Отдел главного механика (ОГМ) в своем составе имеет: бюро планово-предупредительного ремонта ремонтно-механический цех (РМЦ) конструкторское бюро склад запчастей.
Ремонтные работы осуществляются:
группой механика цеха - текущее обслуживание и профилактический осмотр оборудования малый средний и аварийный ремонты;
ремонтно-механическим цехом (РМЦ) - капитальные средние сложные ремонты;
отделом главного механика - заключает договора на проведение капитальных ремонтов на специализированных предприятиях и заводах изготовителях сложного и специального оборудования.
6.3 Организация управления участком
Основным структурным подразделением цеха является производственный участок на котором производится выпуск оговоренной продукции. Во главе производственного участка стоит мастер.
Цех совместно с производственными участками решает следующие задачи:
- выполнение плана производства заданной номенклатуры деталей;
- обеспечение качества выпускаемой продукции.
Мастер является организатором производства на своем участке.
- производить расстановку рабочих на участке; принимать совместно с начальником цеха на работу направляемых отделом кадров работников и отстранять от работы рабочих по установленным причинам;
- премировать рабочих за высокие производственные показатели;
- накладывать дисциплинарные взыскания на рабочих не добросовестно выполняющих свою работу или нарушающих производственную дисциплину;
- вносить предложения о присвоении в установленном порядке тарифных разрядах.
Обязанности мастера:
- максимально эффективно использовать производственные мощности участка обеспечивать выполнение производственных заданий предупреждать появление брака не допускать простоев в работе обеспечивать экономию сырья и материалов;
- следить за расходованием фонда заработной платы;
- участвовать в пересмотре норм и расценок внедрять обоснованные нормы;
- создавать условия для высокопроизводительного труда рабочих содействовать развитию рационализаторства и изобретательства;
- обеспечить соблюдение норм и правил охраны труда на участке.
КОНСТРУКТОРСКАЯ ЧАСТЬ
1 Проектирование станочного приспособления
Объектом проектирования является специальное протяжное приспособление на две детали. Опишем конструкцию данного приспособления.
Приспособление устанавливается на столе вертикально-протяжного станка входя в его пазы шпонкам которые крепятся к плите приспособления с помощью винтов и башмаками высота которых регулируется с помощью винтов. Корпус приспособления крепится к плите с помощью винтов.
Каждая из заготовок базируется в приспособлении на двух пальцах лишающих ее трех степенен свободы и по двум пластинам которые отнимают у нее еще три степени свободы и зажимается тремя гайками. Губки крепятся винтами к кулачкам которые перемешаются по направляющим пазам корпусов. В кулачках выполнены выточки в которые входя поршни. Поршни 21 крепятся винтами к гидроцилиндрам.
Зажим заготовок осуществляется с помощью гидроцилиндров которые тянут поршни которые в свою очередь увлекают за собой кулачки. За счет того что кулачки расположены под углом к оси заготовки диаметр обхвата губок уменьшается и заготовка зажимается.
Поворот заготовок на угол 70° производится с помощью гидроцилиндров. Шток-рейки этих гидроцилиндров входят в зацепление с зубчатыми колесами и при их перемещении производится поворот корпусов вместе с кулачками в которых зажата заготовка и барабанов на которых крепятся гидроцилиндры .
Для защиты приспособления от грязи барабаны закрыты с задней стороны кожухом.
Для добавления масла в приспособление предусмотрена полость Е. которая закрывается крышкой. Для герметизации полости служит уплотнение .
На рисунке 3.2 представлен алмазно-расточный станок модификации 2607.
Рисунок 3.2 - Алмазно-расточный станок модификации 2607
1.1 Расчет тягового усилия на штоке гидроцилиндров приспособления
Рассчитаем силу зажима и усилие на штоке гидроцилиндра 3. Определение усилии зажима необходимых для надежного удержания обрабатываемых заготовок является основой для установления расчетно-конструктивных параметров силовых цилиндров приводов и зажимных устройств приспособлений. Расчет необходимых зажимных сил выполняется в следующей последовательности.
Выбирается оптимальная схема базирования и закрепления заготовки.
При этом следует определить места расположения размеры установочных элементов (постоянных опор) в приспособлении составить схему закрепления заготовки т.е. определить места приложения и направления зажимных сил и их моментов. По заданным режимам резания следует определить величину направление и место приложения сил резания для наиболее неблагоприятного случая требующего наибольших зажимных сил.
На составленной схеме изображаются стрелками все приложенные к заготовке силы: стремящиеся сдвинуть или повернуть ее в приспособлении (силы резания и их моменты) и удерживающие (зажимные силы силы трения и реакции опор).
Вводится коэффициент надежности закрепления к учитывающий возможное увеличение силы резания в процессе обработки. Величина коэффициента запаса (надежности) к устанавливается дифференциально с учетом конкретных условий обработки и закрепления заготовки:
где k0- гарантированный коэффициент запаса надежности закрепления (15)
k1 - коэффициент учитывающий увеличение силы резания из-за случайных неровностей на заготовке (1);
k2 - коэффициент учитывающий увеличение силы резания от затупления режущего инструмента (15);
k3- коэффициент учитывающий условия обработки при прерывистом резании (12);
k4 - коэффициент характеризующий погрешность зажимного устройства (1);
k5 - коэффициент характеризующий степень удобства расположения рукояток в ручных зажимных механизмах (1);
k6 - коэффициент учитывающий только наличие моментов стремящихся повернуть заготовку на опорах (1).
Устанавливаются усилия зажима. Величина зажимного усилия определяется на основе решения задачи статики на равновесие заготовки под действием все приложенных к ней сил и моментов.
Составим уравнение статики: сумма моментов всех сил приложенных к заготовке относительно точки N равна нулю:
где Рz- сила резания Н;
Q - усилие зажима Н;
f- коэффициент трения (0.2)
Рисунок 3.3– Геометрическая схема для расчета усилий на штоке гидроцилиндров
По найденной силе зажима рассчитываются зажимные механизмы приспособления определяется сила на штоке а по ней основные размеры силовых цилиндров.
Сила на штоке находится из геометрической задачи по схеме представленной на рисунке 3.3.
По найденному усилию на штоке выбираем минимально допустимый диаметр гидроцилиндра: D=125 мм диаметр штока d=60.
1.2 Расчет приспособления на точность
Основное требование предъявляемое к приспособлению - обеспечить заданную точность обработки на настроенном станке. Это значит что для каждого выдерживаемого на операции размера (отклонение расположения каждой обрабатываемой поверхности) должно соблюдаться следующее правило:
где а - допуск на размер на отклонение (от соосности параллельности и т.д) расположения обрабатываемой поверхности в
- максимальная результирующая погрешность обработки.
Результирующая погрешность обработки является следствием влияния совокупности различных факторов порождающих погрешности обработки.
При обработке заготовок в приспособлениях на настроенных станках можно выделить следующие погрешности:
К - коэффициент учитывающий закон распределения составляющих погрешностей;
с- погрешность станка в незагруженном состоянии вызываемая погрешностями изготовления и сборки его деталей и узлов и их износом;
рп- погрешность расположения приспособления на станке - расположения посадочных поверхностей приспособления относительно посадочного места станка.
по- погрешность расположения опорных поверхностей относительно посадочных поверхностей приспособления;
биб- погрешность базирования исходной базы заготовки в приспособлении;
э- погрешность вызываемая закреплением заготовки в приспособлении;
пп- погрешность расположения направляющих элементов относительно опорных элементов приспособления;
н- погрешность настройки связанная с погрешностью расположения инструмента относительно направляющих элементов приспособления;
и - погрешность инструмента порождаемая погрешностью его изготовления:
ри- погрешность расположения инструмента на станке;
д- погрешность возникающая вследствие деформации технологической системы СПИД под влиянием сил резания.
из-погрешность вызываемая износом режущего инструмента.
Указанные погрешности не всегда наблюдаются все одновременно. Чаще
приходится иметь дело с их частью так как значения остальных настолько малы что их влияние можно пренебречь.
Произведем расчет протяжного приспособления.
Размерами на точность которых влияет приспособление являются:
- 05 Б - допуск углового положения оси симметрии;
- 003 В - допуск на угол поворота 70°.
Из них выбираем самый жесткий допуск (003 мм).
Составляющие погрешности влияющие на точность проверяемого размера: с = 001 мм; биб = 0017 мм
= 0023 мм ≤ a=003 мм следовательно данное приспособление обеспечивает заданную точность обработки.
2 Проектирование контрольного приспособления
Контрольным приспособлением в данном дипломном проекте является специальное контрольное приспособление.
Приспособление состоит из плиты на которой располагается вращающийся барабан на который устанавливаете и контролируемая деталь. Барабан состоит из основания неподвижно закрепленного на плите с помощью винтов к штифтов и корпуса вращающегося на шарикоподшипнике расположенном между основанием и корпусом. Для защиты подшипника от загрязнения на корпусе предусмотрен кожух который крепится к нему с помощью шести винтов . сверху на корпусе располагаются подвижная и неподвижная призмы на которых и базируется деталь при измерении ее параметров.
Также к плите крепится с помощью винтов и штифтов кронштейн . На оси кронштейна вращается уголок в котором с помощью оси базируется призма накидываемая на оправку при измерений. На той же оси крепятся рукоятка с индикатором.
Кроме того на плите устанавливается стойка индикаторная с индикатором . Для более устойчивой установки приспособления на контрольный стол в плиту вворачиваются ножки.
Данное приспособление предназначено для контролирования допуска пересечения оси Б отверстий 35мм относительно базовой оси Г - оси пересечения плоскостей симметрии зубьев В и Д а также угла поворота оси Д симметрии зубьев относительно оси Б.
Принцип работы контрольного приспособления заключается в следующем. На призмы устанавливается эталон. Индикаторы настраиваются «0». Затем эталон снимается и аналогично на приспособление устанавливается контролируемое изделие. В отверстие 35мм вставляется оправка 17 и на нее накладывается призма 5.
После оттого снимаются показания индикаторов. Изделие считается годным если показание индикатора I (см. рисунок 3.4.) не более 05 мм.
При проверке допуска пересечения осей показание индикатора II должно быть не более ±004 мм.
Контрольное приспособление представлено на рисунке 3.4.
Рисунок 3.4 – Контрольное приспособление
3 Проектирование режущего инструмента
3.1 Проектирование и расчет торцовой фрезы
Для обработки плоской поверхности детали выбираем торцовую фрезу с механическим креплением сменных многогранных пластин. Торцовые фрезы по сравнению с цилиндрическими имеют большую поверхность контакта с обрабатываемой поверхностью а следовательно в работе участвуют большее число зубьев и колебание нагрузки снижаются а равномерность фрезерования повышается. Также торцовые фрезы отличаются большей производительностью. Применение сменных многогранных пластин исключает операции переточки инструмента пайки ножей снижает количество брака при изготовлении и при этом дает возможность многократного использования корпус и использование новых марок твердого сплава в том числе трудно поддающихся пайке.
Так как диаметр фрезы более 40 мм то фрезу выбираем концевую которая вставляется в шпиндель станка.
Выбираем корпус фрезы из стали 50ХФА ГОСТ 14959-81 а сменную многогранную пластину из твердого сплава ВК8 ГОСТ 26530-86.
Диаметр фрезы зависящий от ширины фрезерования В определим по формуле
D = (1.2 1.6) B(3.4)
Рассчитаем диаметр фрезы
Принимаем стандартный размер фрезы D = 40мм.
Число зубьев фрезы предварительно рассчитываем из условия равномерного фрезерования по формуле
где - угол контакта фрезы с заготовкой
=arctg (1-(2tD)) = arctg (1-(2*385540)) = 323
≥ 2 – коэффициент равномерности фрезерования = 2.
По данным расчетам число зубьев получается слишком большим. Для удобства размещения пластин с механическим креплением число зубьев берем меньше чем получено по формуле. Рекомендуемое число зубьев для торцевых фрез данного диаметра с механическим креплением пластин равно 6 поэтому принимаем z = 6.
Для выбора пластины рассчитаем число граней пластины по формуле
где φ и φ1 – углы в плане (главный и вспомогательный). φ = 75 и φ1 =15
Выбираем пластинку квадратной формы. Задний угол α принимаем 11 он необходим для устранения трения задней поверхности пластины об обрабатываемую поверхность в процессе резания. Передний угол выбираем в зависимости от физико-механических свойств обрабатываемого материала и характеристик материала режущей части инструмента.. Следовательно для обеспечения заданных углов у фрезы выбираем пластину с углами α = 11γ = 0.
Длину режущей кромки l пластины принимаем такую чтобы она обеспечивала удаление срезаемого слоя на всю толщину за один проход.
Рисунок 3.5 - Схема резания пластинами квадратной формы
lа = 3855tg75 = 42мм то
l = 3*lа2 = 3*422 = 63.
Принимаем длину режущей кромки l = 127мм.
Соответственно данной длине определяем остальные параметры пластины по ГОСТ 19050-81
Рисунок 3.6 - Эскиз пластины
d1 = 516; S = 476; r = 12 ic = 127
Закодируем пластину: SPAN - 120408
S – форма пластины: квадрат;
P – задний угол: α = 11;
A – допуск на размеры m S ±011; ±007;
N – тип пластины: односторонняя;
- длина режущей кромки без учета знаков после запятой
– толщина пластины без учета знаков после запятой S = 476;
– радиус при вершине : r = 08мм
Так как фреза предназначена для торцового фрезерования необработанной поверхности то главным условием является жесткое закрепление пластины. Поэтому выбираем закрепление пластины – через центральное отверстие винтом с конической головкой. Базируем пластину по двум сторонам. Выбираем способ крепления пластины к корпусу с помощью винта с конической головкой. Это наиболее широко применяемый способ крепления он наиболее технологичен и прост по сравнению с другими. Он обеспечивает поджим пластины к базовым поверхностям за счет смещения осей то есть точное позиционирование пластины в гнезде корпуса.
Во время работы инструмента оправка подвергается сложному изгибу из-за наличия крутящего и изгибающего моментов ( как балка защемленная одним кольцом)
Рисунок 3.7 - Расчетная схема оправки
Эквивалентный момент
Мэкв = √(М ²кр +М ²изг) [11]
где М кр – крутящий момент
М изг – изгибающий момент
М изг = Ризг * l = √ (Р2y + Р2 z) * d2 (3.7)
где Рz – главная составляющая силы резания при фрезеровании – окружная сила
Рy – радиальная составляющая силы резания
Рy = 04 *1943 =7772 Н
М изг= √ (77722+19432)* 0062 = 6278 Н*м
Мкр = ( Рz*D) 2*100 = (1943*250) 2*100 = 2428.75H*м
Тогда эквивалентный момент
Мэкв = √(6278² +242875 ²) = 242956 Н*м
Условием прочности является
Так как оправка выполнена из стали Ст5 то []экв = 200Мпа – допустимое эквивалентное напряжение.
– расчетное напряжение в опасном сечании
где W – момент сопротивления сечения
W = d³ 32 – для круглого сечения
W = 314*006332 = 0000021195 м2
Расчетное напряжение
= 2429560000021195 = 114628981 Па
Условие прочности соблюдается
4628981 Па 200000000Па
Таким образом диаметр оправки 60мм по прочности подходит для данной фрезы и условий обработки
Выбранная и рассчитанная фреза изображена на чертеже.
3.2 Проектирование и расчет зенкера
Зенкеры предназначаются для увеличения диаметров цилиндрических и конических отверстий полученных после сверления отливки ковки и штамповки.
Зенкеры для увлечения диаметра отверстий применяются для окончательной обработки отверстий 4 -5 –го классов точности.
Зенкеры изготавливаются с тремя или четырьмя канавками.
Режущая часть предназначается для удаления всего припуска на обработку поэтому длина режущей части выбирается в зависимости от глубины резания t.
Расчет режущего инструмента зенкера для обработки отверстия диаметром 35 мм.
оборудование : станок алмазно-расточный
материал заготовки: сталь35ГОСТ 1050-74
шероховатость обрабатываемой поверхности Ra 20
твердость заготовки HB 255
Для обработки поверхности 9 операции 005 выбираем зенкер диаметром 35 мм со сменными многогранными пластинами ВК8 ГОСТ 3882-72 регулируемыми в зависимости от размера обрабатываемой поверхности с использованием ключа ГОСТ 11737-74 для регулирования. Такой режущий инструмент – зенкер по сравнению с другими зенкерами отличается большей производительностью и в процессе резания участвует большее число зубьев. Повышение стойкости в 2 раза.
Определение параметров зенкера.
Диаметр зенкера D принимается равным диаметру обрабатываемого отверстия с учетом допуска по ГОСТ 12509-75.
Определение глубины резания.
где 35 мм на сторону.
Определение геометрических параметров и конструктивных параметров рабочей части зенкера. По ГОСТ 12489-71 ГОСТ 21541-76 выбираем по таблицам режимов резания:
задний угол на задней поверхности
задний угол на калибрующей поверхности
передний угол на фаске шириной f=05 мм.
Угол наклона канавки
Профиль канавок прямоугольный. Таким образом пластины СМП. мм
Принимаем главный угол в плане вспомогательный угол в плане . Обратную конусность на длине пластины СМП из твердого сплава принимаем равной 005 мм
Ширина ленточки f=15 мм.
Определение числа граней у пластины:
принимаем 4 грани у пластины.
Исходя из количества граней определяем углы пластин:
Угол при вершине пластин рассчитывается по формуле:
Угол определяющий положение плоскости относительно главной режущей кромки
Угол наклона пластины:
Угол между основанием державки зенкера и плоскостью сечения:
Геометрические размеры пластины: толщина пластины выбирается по ГОСТ19042-80
S=476 мм l=115 мм d=675 мм m=17562 мм
Материал пластины ВК8 ГОСТ 3882-77
Форма – квадратная № 2008-1854МС1460
Материал корпуса зенкера – сталь 45 ГОСТ 1050-88
Материал хвостовика – сталь 45Х ГОСТ 4543-71
Определение конструктивных элементов зенкера. По справочнику по ГОСТ 3231-71 зенкер оснащен пластинами из твердого сплава с коническим хвостовиком.
Длина рабочей части хвостовика по формуле:
- глубина зенкерования
=14 мм мм принимаем 98 мм
длина заборной части;
принимаем 5 мм =5 мм
Профиль канавки принимается по ГОСТ 3231-71 с пластинами ВК8
число зубьев зенкера - 3
Хвостовик выбирается по ГОСТ 25557-82 - конус Морзе 3
Конусность: 1:19922=0005020 или
Параметры хвостовика: D=29 мм D=313 мм c=10 мм – толщина лапки l=19мм R=10
Определение режимов резания зенкера на обработку: - удаляется за один проход
- путь проходящий инструментом в направлении подачи – глубина зенкерования.
- величина перебега инструмента
y - величина врезания
S=101 ммоб n=1363 обмин T=014 мм
На данную пластину действует осевая сила и момент сопротивления: КГС мм
Для материала сталь 35 из справочника режимов резания машиностроительные нормативы:
Осевая сила и момент при зенкеровании вследствие малой глубины резания имеют малую величину подсчитывается редко при обработке чугунов.
Износ режущего инструмента – зенкера принимается по уголкам пластин мм и по задней поверхности технические требования к зенкерам оснащенным пластинами из твердого сплава ГОСТ 12509-75.
1 Годовая программа и форма организации производственного участка
На основании принятого объёма выпуска продукции рассчитывается объём её запуска в производство. Результаты сведены в таблицу 1.
Годовой объём запуска рассчитывается по формуле:
где Qв – годовой объём выпуска изделий установленный заданием по дипломному проекту Qв = 3000 шт.;
– процент учитывающий расход изделий на наладку и потери на возможный брак = 05%.
Qз принимается для обоих вариантов технологического процесса.
2 Потребность в производственном оборудовании
Расчетное количество оборудование Wр определяется по формуле:
где T' – машиноемкость изготовления продукции ч
T" – время в течение которого оборудование занято заменой
и переналадкой штампов ч
– коэффициент перевыполнения нормы = 11
– коэффициент допустимой нагрузки = 090
– годовой эффективный фонд времени работы оборудования.
где – штучное калькуляционное время выбирается по наиболее
загруженному оборудованию технологической линии мин.
Для базового варианта:
Для проектного варианта:
где – время на одну переналадку = 30мин;
– число переналадок на программу.
где Tст – стойкость штампов до переналадки принимаем = 40 = 34.
где – годовой номинальный фонд времени смены = 2024ч;
S – режим работы оборудования смен S = 1;
P – потери от номинального фонда времени учитывающие простои
оборудования в плановом ремонте P = 9%.
для обоих вариантов.
Принимаем по одному станку. В базовом варианте используется 7 единиц оборудования а в проектном 1 по одному на каждую операцию.
Коэффициенты загрузки принимаем = 08 09.
Исходные данные и результаты расчетов представлены в таблице 2 а технико-экономические показатели оборудования – в таблице 3.
3 Производственная площадь
В базовом варианте используется 390 при цене за 2006 год
370 руб в месяц в проектном варианте будет использоваться 378 за эту же цену.
Затраты на аренду производственной площади:
4 Основные и вспомогательные материалы
Расход основного материала в тоннах на годовую программу рассчитывается по формуле:
где qм – расход основного материала на изделие qм = 866 кг.
Величина возвратных отходов Qво определяется из соотношения:
где qво – вес возвратных отходов на изделие qво = 096 кг;
qn – вес изделия (отливки) qn = 776 кг.
Уточненная норма расхода qн основного материала на изделие определяется как:
Расчет затрат на основные материалы См производится по формуле:
где Zм – оптовая цена материала Zм = 24800 рубт;
tм – процент транспортно-заготовительных расходов tм = 4%.
Рассчитывается выручка от реализации лома и стружки – отходов основного материала:
где Zво – сбытовые цены на лом и отходы основного материала.
5 Расчет численности работающих
Общее количество участвующих в работе механического цеха составляют:
производственные рабочие главным образом станочники;
вспомогательные рабочие;
служащие: инженерно-технические работники (ИТР) и счётно-конторский персонал (СКП);
младший обслуживающий персонал (МОП).
Численность работающих в цехе определяется по категориям:
а) Расчёт численности основных производственных рабочих:
гдеFд - действительный годовой фонд времени работы оборудования;
hз - средний коэффициент загрузки;
Fэ – 1820 ч – годовой эффективный фонд времени работы одного рабочего;
Кв – коэффициент выполнения норм;
коэффициент многостаночности;
- для универсальных станков;
- для станков с ЧПУ и полуавтоматов
принимаем Кор.ток= 1 чел.
принимаем Кор.св-раст= 1 чел.
принимаем Кор.шлиф-зат= 1 чел.
принимаем Кор.фрез= 1 чел.
принимаем Кор.пресс= 1 чел.
принимаем Кор.друг= 1чел.
Общая численность основных производственных рабочих проектируемого цеха:
Кор= Кор.ток-ЧПУ+ Кор.ток+ Кор.св-раст+ Кор.шлиф-зат+ Кор.фрез+ Кор.пресс + Кор.друг (4.7)
Кор=1+1+1+1+1+1+1=7 чел
Кроме того к основным рабочим принимаем слесарей для выполнения слесарных операций из расчета 3-5% от числа производственных рабочих станочников.
Кр.слес=005×7=035чел.
Принимаем Кслес=1 чел.
Общее количество производственных рабочих:
Таблица 7 – Сводная ведомость состава производственных рабочих цеха
Наименование профессии
Общее количество рабочих
Токарь – оператор ЧПУ
б) Расчет численности вспомогательных рабочих
Общее количество вспомогательных рабочих в серийном производстве принимается 30-40% от количества производственных рабочих. Принимаем 35%:
Принимаем Квсп=5 чел.
Таблица 8 – Сводная ведомость состава вспомогательных рабочих цеха
Количество вспомогательных рабочих
Слесарь по ремонту оборудования
Общее количество рабочих цеха:
Кобщ=Кпроизв+ Квсп (4.11)
Кобщ=Кпроизв+ Квсп=8+5=13чел
в) Расчет численности служащих
Численность ИТР составляет 1113% от общего числа рабочих
КИТР =13%×Кобщ (4.12)
Принимаем КИТР=2 чел
Численность СКП составляет 1-3% от общего числа рабочих
КСКП =2%×Кобщ (4.13)
Принимаем КСКП=1 чел
Общее число служащих:
Кслуж=КИТР+КСКП (4.14)
г) Расчет численности МОП
Младший обслуживающий персонал составляет 2-3% от общего количества рабочих
Принимаем КМОП=1 чел.
Таблица 9 - Сводная ведомость производственных рабочих проектируемого цеха
Наименованиепрофессии
Общее кол-во рабочих
Средний тарифно-квалиф. коэф.
Тарифный коэффициент
Общее число человеко–разрядов: 2×1+3×2+4×2+5×2+6×1=32
Средний тарифно-квалификационный разряд: 328=40
Таблица 10 - Сводная ведомость вспомогательных рабочих проектируемого цеха
Средний тарифный коэф-нт
Средний разряд по цеху
Средний тарифно-квалификационный коэффициент работников цеха: 169
Таблица 11 – Сводная ведомость общего состава работающих на участке
Наименование категории
В % от количества основных рабочих
В % от общего количества всех работающих в цехе
Вспомогательные рабочие
6 Расчет ФЗП и среднемесячной зарплаты
а) Заработная плата основных рабочих:
Зо.р.=Т× Сpl× Кср (4.16)
где Т нчас – общая трудоемкость работы;
Кср = 174 – средний тарифный коэффициент основного рабочего;
Зо.р .= 24600×34×174=1455336руб
Премия основных рабочих:
Зпр.о =45% Зо.р. (4.17)
Зпр.о =045×1455336=654901 руб
Дополнительная зарплата основных рабочих:
Здоп.о =11% Зо.р (4.18)
Здоп.о =011×1455336=160087 руб
Районный коэффициент основных рабочих:
Зр.к .о=15%×( Зо.р+ Зпр+ Здоп) (4.19)
Зр.к .о= 015(1455336+654901+160087)= 340549 руб
Общий фонд заработной платы основных рабочих:
Зобщ .о=Зо.р.+Зпр.+Здоп +Зр.к (4.20)
Зобщ.о =1455336+654901+160087+340549=12621873 руб
Среднемесячная зарплата основных рабочих:
где Ко.р.- количество основных рабочих.
б) Заработная плата вспомогательных рабочих:
Зв.р.=Т×Сpl×Кср×Кв.р. (4.22)
где Т= 1820 часгод – трудоемкость работы вспомогательных рабочих;
Кср = 166 – средний тарифный коэффициент;
Кв.р. - количество вспомогательных рабочих;
Зв.р. = 1820×33×166×5=1196395 руб
Премия вспомогательных рабочих:
Зпр.в = 35% Зв.р (4.23)
Зпр.в =035×1196395=418738 руб
Дополнительная зарплата вспомогательных рабочих:
Здоп.в = 11% Зв.р. (4.24)
Здоп.в =011×1196395=131603 руб
Районный коэффициент вспомогательных рабочих:
Зр.к.в = 15% × (Зв.р.+ Зпр.+ Здоп) (4.25)
Зр.к.в = 15% × (Зв.р.+ Зпр.+ Здоп) = 015(1196395+418738+131603) = 262010 руб
Общий фонд зарплаты вспомогательных рабочих:
Зобщ.в = Зв.р.+ Зпр.в.+ Здоп.в +Зр.к..в (4.26)
Зобщ.в =1196395+418738+131603+262010 =2008746 руб
Среднемесячная зарплата вспомогательных рабочих:
в) Расчет фонда зарплаты ИТР СКП и МОП
Начальник цеха – 15000 руб
Зам. начальника –12000 руб
Энерго-механик – 10000 руб
Мастер(2 ед) – 9500 руб.
Инженер ПРБ –8000 руб.
Средняя зарплата ИТР:
ЗИТРср = (15000+12000+10000+2·9500+8000)5=10667 руб
Нормировщик – 7500 руб.
Уборщица – 3500 руб.
Премия для служащих:
Зслуж.пр = 30% от оклада (4.28)
Дополнительная зарплата для ИТР:
ЗИТРдоп = 15% от оклада (4.29)
Дополнительная зарплата для СКП и МОП:
ЗСКПМОПдоп = 12% от оклада (4.30)
Районный коэффициент для служащих:
Зслуж.р.к. = 15% (оклад + Зпр.+ Здоп) (4.31)
Среднемесячная зарплата для ИТР СКП и МОП:
Зср= Зокл + Зпр + Здоп + Зр.к. (4.32)
ЗИТРпр = 03×10667 = 3200 руб
ЗИТРдоп = 015×10667 = 1600 руб
ЗИТРр.к. = 015 (10667+3200+1600) = 2320 руб
ЗИТРср = 10667+3200+1600+2320=17787 руб
ЗИТРгод = Зср×12×КИТР = 17787×12×6 = 1280664 руб
ЗСКПпр = 03×7500 = 2250 руб
ЗСКПдоп = 012×7500 = 900 руб
ЗСКПр.к. = 015 (7500+2250+900) = 1598 руб
ЗСКПср = 7500+2250+900+1598= 12248 руб
ЗСКПгод = ЗСКПср×12×КСКП = 12248×12×1 = 146976 руб
ЗМОПпр = 03×3500 = 1050 руб
ЗМОПдоп = 012×3500 = 420 руб
ЗМОПр.к. = 015 (3500+1050+420) = 746 руб
ЗМОПср = 3500+1050+420+746 = 5716 руб
ЗМОПгод = ЗМОПср×12×КМОП = 5716×12×1 = 68592 руб
Таблица 12 - Сводная ведомость заработной платы работающих цеха
Среднемесячная зарплата на одного работающего:
7 Электроэнергия и энергоносители
Годовой расход электроэнергии находят как сумму расходов электроэнергии по группам оборудования. Для каждого вида оборудования расход электроэнергии определяется по формуле:
где kc – коэффициент спроса учитывающий полноту использования установленной мощности называемый также коэффициентом использования или одновременности kc = 025.
Для станка токарно-вертикальный па 1К282 : кВт;
Для станка вертикально-фрезерный 6Р12 : кВт;
Для станка агрегатно-сверлильный АМ7427: кВт;
Для станка агрегатно-сверлильный АМ7428: кВт;
Для станка вертикально-сверлильный 2135: кВт;
Для станка вертикально-сверлильный 2Н125: кВт;
Для станка вертикально-сверлильный 2Н135: кВт;
тогда сумма расходов электроэнергии для базового варианта:
Для токарного станка с ЧПУ Rom
тогда для проектного варианта:
8 Себестоимость и цена продукции
Затраты на годовой выпуск продукции:
базовый вариант = 50997333 руб;
проектный вариант = 468245 руб.
9 Капитальные вложения
Капитальные вложения (инвестиции) в строительство и организацию работы цеха включают в себя:
где Кпр – прямые капитальные вложения в цех руб.;
Ксопр – сопряженные капитальные вложения в цех руб.;
Kоб – минимально необходимые оборотные средства.
Для базового варианта:
Ксопр = 50997333 руб;
Kоб = 10% Кпр = 496243руб.
Кн = 496243+50997333+496243= 105584063 руб.
Принимаем Кн.баз = 1100000 руб.
Kоб = 10% Кпр = 407617руб.
Принимаем Кн.пр = 1000000 руб.
10 Эффективность рассматриваемых вариантов технологического процесса
Чистый дисконтированный доход (ЧДД>0)
где Т – горизонт расчета (равный номеру шага расчета на котором производится ликвидация объекта) Т = 10;
Е – норма дисконта равная приемлемой для инвестора норме доходности на капитал Е = 015;
– капитальные вложения;
– прибыль за год и амортизация.
Индекс доходности (ИД>1)
Внутренняя норма доходности
Внутренняя норма доходности (ВНД) представляет собой ту норму дисконта (Евн) при которой величина приведенных эффектов равна приведенным капиталовложениям.
Иными словами Евн (ВНД) является решением уравнения:
где – затраты на t-ом шаге при условии что в них не входят капиталовложения.
Срок окупаемости – минимальный временной интервал (от начала осуществления проекта) за пределами которого интегральный эффект становится и в дальнейшем остается неотрицательным. Иными словами это период (измеряемый в месяцах кварталах или годах) начиная с которого первоначальные вложения и другие затраты связанные с инвестиционным проектом покрываются суммарными результатами его осуществления.
В дипломном проекте определяются сроки окупаемости:
БЕЗОПАСНОСТЬ ЖИЗНЕДЕЯТЕЛЬНОСТИ
1 Анализ проектного технологического процесса на наличие потенциально опасных и вредных факторов
Заготовка – вилка карданного вала. Материал заготовки – сталь 35 ГОСТ 1050-74.заготовки составляет 15 кг масса готовой детали – 13 кг. Сменная норма перемещения заготовок определяется по формуле:
где D = 3000годовая программа выпуска деталей
к = 2 количество перемещений заготовок
m = 15кг масса заготовки
n = 253 число рабочих дней в году
S = 1 число рабочих смен.
Часовая норма перемещения заготовок:
где Nh- часовая норма перемещения заготовок
l = 8 - количество часов в смене.
Часовая норма перемещения заготовок удовлетворяет нормативным величинам приведенным в таблице 13.
Таблица 13 - Нормативы часовой нормы перемещения заготовок
Характеристика перемещений
Суммарная масса перемещаемого груза в течение часа смены (допустимая средняя нагрузка) кг
С рабочей поверхности:
Заготовки на всех операциях устанавливаются вручную. Перемещение заготовок от операции к операции происходит посредством тележки.
В данном техпроцессе для обработки вилки применяется многоцелевой станок алмазно-расточный станок модификации 2706. Оборудование соответствует ГОСТ 12.2.003-82 ССБТ « Оборудование производственное. Общие требования безопасности» и ГОСТ 12.2.009-80 ССБТ «Станки металлообрабатывающие. Общие требования к безопасности».
В качестве режущего инструмента в данном технологическом процессе применяются следующие инструменты: фреза торцовая с СМП зенкер сверла метчики. Наиболее опасным является инструмент с СМП.
Работающее оборудование является источником шума. Шумом называется сочетание звуков различной частоты и интенсивности оказывающих неблагоприятное воздействие на человеческий организм он создает помехи которые могут привести к несчастному случаю.
Шум на производстве неблагополучно воздействует на нервную систему работающего:
- ослабление внимания
- замедление скорости психических реакций
- снижение производительности труда
- ухудшение качества работы.
Значение уровня звукового давления на расстоянии 1м от источника шума металлорежущего станка соответствует 80дБ.
Нормируемые параметры шума на рабочих местах определены ГОСТ 12.1.003-83 ССБТ “Шум. Общие требования безопасности”. В них установлены допустимые уровни звукового давления в активных полосах частот уровни звука и эквивалентные уровни звука.
Так как все оборудование соответствует ГОСТ 12.2.003-82 ССБТ « Оборудование производственное. Общие требования безопасности» и ГОСТ 12.2.009-80 ССБТ «Станки металлообрабатывающие. Общие требования к безопасности» значит на этом оборудовании уровень шума соответствует нормативным показателям. Следовательно мероприятия и средства защиты от воздействия шума в данном проекте не приводятся.
Методы и средства защиты:
- метод снижения шума на пути его распространения от источника;
- метод снижения шума в источнике его образования.
Таблица 14- Уровень шума для постоянных рабочих мест по ГОСТ 12.1.003-83 ССБТ
Уровень звукового давления в дБ и октавных полосах со среднегеометрическими частотами Гц
Причиной возникновения вибрации являются возникающие при работе агрегатов неуравновешенные силовые воздействия. По характеру воздействия на организм человека различают общую локальную комбинированную. Общая вибрация вызывает сотрясение всего организма. Общей вибрации подвержены в основном транспортные рабочие. Локальной вибрации подвержены люди работающие с ручным электрическим механизированным инструментом. Вибрация вызывает спазмы сосудов воздействует на нервные окончания мышечные и костные ткани.
Вибрация возникающая при работе оборудования:
Вибрация - это колебания механической системы в результате действия совокупности случайных и неуравновешенных сил. Вибрация оказывает вредное воздействие на организм человека. Нормированные значения вибрации по ГОСТ 12.1.012-90 ССБТ приведены в таблице 15.
Таблица 15 - Значения вибрации по ГОСТ 12.1.012-90 ССБТ
Среднеквадратичное значение вибрации в октавных полосах со среднегеометрической частотой Гц
На постоянных рабочих местах
Общая технологическая вибрация
Применяемое оборудование является серийным соответствует ГОСТ 12.2.003-83 ССБТ поэтому уровень шума не будет превышать допустимый.
Смазывающе-охлаждающая жидкость применяемая в техпроцессе
В процессе механической обработки на металлорежущих станках применяется СОЖ которая способствует повышению режимов резания стойкости инструмента снижает запыленность рабочей зоны. В качестве СОЖ используется эмульсионный раствор на водной основе. Подача его в рабочую зону осуществляется методом полива. Ориентировочные количества паров воды и тумана эмульсии выделяемых за один час работы станка в расчете на 1 кВт мощности приведено в таблице 16.
Таблица 16 - Выделение паров воды и тумана эмульсии за час работы оборудования
Металлорежущие станки
Мероприятия и средства по созданию безопасных и безвредных условий труда:
Нормируемые параметры микроклимата и способы создания их оптимальных величин:
К нормируемым параметрам микроклимата относятся:
температура воздуха;
скорость движения воздуха.
Нормируемые параметры микроклимата не должны выходить за пределы нормативных величин приведенных в таблице 17.
Таблица 17 - Нормируемые параметры микроклимата
Относительная влажность %
Скорость движения воздуха Дмс
Холодный и переходный
Выполнение этих норм осуществляется путем проведения следующих мероприятий:
в теплое время за счет вентиляции
в холодное время за счет вентиляции отопления;
защитой от вредных параметров являются средства индивидуальной защиты: комбинезоны очки спец. обувь.
Мероприятия и средства по созданию безопасных и безвредных условий труда
Мероприятия проводимые при использовании СОЖ:
на состав применяемой СОЖ необходимо разрешение санитарного надзора;
состав СОЖ на водном растворе их антимикробная защита и пастеризация должны удовлетворять требованиям ГОСТ 121.3.025-80 ССБТ.
Обработка металлов резанием. Общие требования безопасности;
приготовление и подача СОЖ к станкам должна быть централизованной;
периодичность и промывка систем для подачи её должна быть не реже 1 раза в 6 месяцев;
станки должны быть оборудованы специальными сборниками и экранами защиты оператора;
помещение оборудуется обще обменной вентиляцией с подачей приточного воздуха в рабочую зону со скоростью не более 05 мс. общая производительность вентиляции должна составлять 850-900 м3час на один станок;
рабочие должны использовать дерматологические кремы и пасты;
необходимо проводить санитарный инструктаж.
Заготовка на всех операциях устанавливается вручную. Отвод стружки от станка осуществляется с помощью тележек. Надзор за выполнением техпроцесса осуществляется инженером предприятия.
Технические средства и организационные мероприятия по защите от подвижных частей оборудования и разлетающейся в процессе резания стружки. Для спроектированного техпроцесса предусматриваются следующие виды защиты:
ограничивающие закрывающие доступ к опасным частям оборудования. Для этого используются кожухи щиты решетки сетки. Ограждения должны быть достаточно прочными надежно крепиться к фундаменту или частям машины;
предохранительные автоматически отключающие оборудование при выходе какого-либо параметра за пределы допустимого;
сигнализирующие окраска опасных частей оборудования в красный цвет;
для защиты от разлетающейся стружки используются очки щитки экраны.
Для безопасной эксплуатации режущего инструмента необходимо постоянно следить за его состоянием проверять крепление резцов в расточных оправках и твердосплавных ножей в сборных инструментах.
2 Мероприятия по электробезопасности
Электробезопасность - система организационных мероприятий и технических средств обеспечивающих защиту людей от опасного и вредного действия электрического тока.
Электрический ток проходя через организм человека оказывает электролитическое термическое и биологическое действие вызывая местные и общие травмы. Характер действия электрического тока на организм человека в зависимости от его величины приведен ниже в таблице.
Таблица 18 - Действие электрического тока на организм человека
Вызывает ощущение раздражения
Пороговый неощутимый
Вызывает сильные судороги мышц рук которые человек не в состоянии преодолеть
Пороговый фибриляционный
Непосредственное влияние на мышцу сердца при протекании тока более чем 5 секунд может произойти остановка сердца
Согласно ПУЭ помещение участка механической обработки относится к особо опасному с точки зрения электрической безопасности. Основные причины несчастных случаев на участке:
случайное прикосновение или приближение на опасное расстояние к токоведущим частям находящимся под напряжением;
появление напряжения на металлических частях оборудования кожухах корпусах в результате повреждения изоляции;
возникновение напряжений на поверхности земли в результате замыкания токоведущего провода на землю.
На участке необходимо проводить следующие мероприятия по эдектробезопасности. Так как для питания электрооборудования применяются трехфазные четырезпроводные цепи с глухо заземленной нейтралью напряжением 380220В необходимо:
изолировать токоведущие части что защищает электроустановки от чрезмерной утечки токов предохраняет людей от поражения током и исключает возникновение пожаров;
сделать токоведущие части недоступными для случайного прикосновения;
применять двойную изоляцию состоящую из рабочей изоляции и дополнительной повышающей надежность работы т.е. защищающей человека от поражения при повреждении изоляции;
зануление обеспечивающее быстрое отключение поврежденной установки или участка цепи максимальной токовой защиты вследствие короткого однофазного замыкания (рисунок 5.1);
заземление нейтрали обеспечивающее невозможность появления напряжения относительно земли на корпусе машины;
использование изолирующего трапа.
проводятся также следующие организационные мероприятия:
периодический инструктаж на рабочем месте с изложением требований безопасности;
обязательный контроль исправности проводника защитного заземления или зануления наличия трапа у станка;
запрещение операторам ремонтировать электрооборудование;
привлечение к ремонту оборудования лиц электротехнического персонала своевременно прошедших инструктаж;
применение предупредительных надписей и указательных знаков.
Рисунок 5.1- Принципиальная схема зануления
Проектирование общего равномерного искусственного освещения на участке
Световой поток одной лампы на участке рассчитывают по формуле:
где Ен = 300 лк - необходимая освещенность рабочих мест операторов;
S = 648 м2 - площадь освещаемого участка;
N = 28 - количество ламп на участке;
к = 15 - коэффициент запаса;
Z = 115 – коэффициент минимальной освещенности для ламп накаливания и ДРЛ.
h=55 – коэффициент использования светового потока определенный в зависимости от соотношения при rп = 70% и rс = 60% для светильников УПМ-15:
где А и В - длина и ширина участка;
НР - расстояние от потолка где подвешены лампы до рабочей поверхности.
Такому световому потоку соответствуют лампы ДРЛ400 ГОСТ 16354-70 у которых Фл = 19 клм.
Схема расположения светильников на участке приведена на рисунке 5.2.
Рисунок 5.2 - Схема расположения светильников на участке
3 Мероприятия по пожарной безопасности участка
Пожар - это неконтролируемое горение вне специального очага наносящее материальный ущерб. Горение - это химическая реакция окисления сопровождающаяся выделением тепла. Для возникновения горения необходимы:
Загорание – горение не причинившее материальный ущерб.
Опасными факторами пожара являются:
повышенная температура воздуха и предметов;
открытый огонь и искры;
токсичные продукты горения;
повреждения и разрушения зданий и сооружения.
Оценка пожарной опасности участка
Спроектированный участок размещается в помещении пожарной опасности категории D. Это помещения в которых находятся и обрабатываются негорючие вещества и материалы в холодном состоянии.
Перечень причин возникновения пожара на участке
Пожары на участке возможны по следующим причинам:
металлообработка связана с применением масел масло используется для смазки станков и в гидроприводах;
недостатки в эксплуатации технологического оборудования системы электроснабжения освещения вентиляции отопления главным образом из-за нарушения графиков их обслуживания и ремонта это может привести к перегрузке оборудования и короткому замыканию в сетях электроэнергии;
возможные нарушения требований пожарной безопасности на участке связанные с курением в не установленных местах проведением сварочных и других работ без предварительной подготовки неудовлетворительное состояние промасленной ветоши несвоевременной уборкой пролитого масла.
Выбор первичных средств пожаротушения
На участке располагаются следующие первичные средства пожаротушения:
огнетушитель углекислотный ОУ-5 (1 шт.) применяется для тушения электроустановок;
огнетушитель водно-пенный ОВП-5 (1 шт.) применяемый для тушения горящей масляной ветоши и других очагов горения не находящихся под напряжением;
кусок асбестового полотна м.;
Огнетушители ящик с песком и пожарный стенд располагаются у ряда колонн около проезда участка.
Мероприятия предупреждающие пожар на участке
Пожарная профилактика - комплекс организационно-технических мероприятий направленных на предупреждение пожаров уменьшение его размеров. Пожарная профилактика осуществляется по следующим направлениям:
устранение непосредственных или возможных причин пожаров в процессе эксплуатации зданий технологического оборудования систем отопления вентиляции освещения электроснабжения;
ограничения возможного распространения пожара и взрыва;
обеспечение эвакуации людей и оборудования из горящего здания;
обеспечение быстрого развертывания действий по пожаротушению;
разработка наглядных пособий по пожарной безопасности;
разработка инструкций по пожарной безопасности.
Спроектированный технологический процесс позволяет изготавливать данную деталь годной обеспечивая заданную конструктором точность. Применение режущего инструмента оснащенного твердым сплавом позволяет добиться высокой производительности высокого качества обработанной поверхности; снизить себестоимость обработки.
В предложенной дипломной работе был проведен анализ технологичности детали-представителя «вилка карданного вала». Также был проведен анализ действующего технологического процесса. Разработан технологический процесс. С целью повышения производительности были совмещены операции на одном станке. Рассчитаны режимы резания и нормы штучного времени. Был рассчитан и сконструирован режущий инструмент: фреза и зенкер. Было разработана и спроектирована координатно-измерительная машина. По предложенному технологическому процессу был спроектирован участок механической обработки деталей типа «вилка». Была разработана часть по безопасности жизнедеятельности.
БИБЛИОГРАФИЧЕСКИЙ СПИСОК
Шамин В.Ю. Теория и практика решения конструкторских и технологических размерных цепей: Учебное пособие. - Челябинск: ЧГТУ 1999 - 429 с.
Справочник технолога-машиностроителя в 2 томах Т. 1 Под ред. А.Г. Ко-силовой Р.К. Мещерякова. - М.: Машиностроение 1985 - 656 с.
Общемашиностроительные нормативы времени и режимов резания для нормирования работ выполняемых на универсальных и многоцелевых станках с ЧПУ в 2 частях Ч. 2. - М.: Экономика 1990 - 473 с.
Техническое нормирование операций механической обработки деталей: Учебное пособие И.М. Морозов В.И. Гузеев С.А. Фадюшин. - Челябинск: Изд. ЮУрГУ 2000. - 76 с.
Общемашиностроительные нормативы времени и режимов резания для нормирования работ выполняемых на универсальных и многоцелевых станках с ЧПУ в 2 частях Ч. 1. - М.: Экономика 1990 - 206 с.
Егоров М.Е. Основы проектирования машиностроительных заводов: Учебник для машиностроительных вузов. - М.: «Высшая школа» 1969 - 480 с.
Мясников Ю.И. Проектирование технологической оснастки в 4 частях Ч. 2. Примеры проектирования станочных приспособлений: Учебное пособие для студентов специальностей 1201 и 1202. - Челябинск: ЧГТУ 1996. - 84 с.
Справочник технолога-машиностроителя в 2 томах Т. 2 Под ред. А.Г. Косиловой Р.К. Мещерякова. - М.: Машиностроение 1985 - 496 с.
Мясников Ю.И. Проектирование технологической оснастки в 4 частях Ч. 1. Методика инженерного проектирования станочных приспособлений: Учебное пособие для студентов специальностей 1201 и 1202. - Челябинск: ЧГТУ 1996. - 105 с.
Координатно-измерительные машины и их применение В.-А. А. Гапшис А.Ю. Каспарайтис М.Б. Модестов и др. - М.: Машиностроение 1988 - 328 с.
Справочник конструктора-инструментальщика Под общей ред. В.И. Баранчикова.- М.: Машиностроение 1994 - 560 с.
Пилипчук В.А. Организация производства: Учебное пособие. - Челябинск: Издательство ЮУрГУ 2003 - 42 с.
Хашковский А.В. Сидоров А.И. Охрана труда: Текст лекций. Ч. 1. - Челябинск: ЧПИ 1989 - 176 с.
Охрана труда в машиностроении: Учебник для машиностроительных вузов Е.Я. Юдин C.B. Белов С.К. Баланцев и др. Под ред. Е.Я. Юдина C.B. Белова. -М.: Машиностроение 1983 - 432 с.
Голотин Г.И. Безопасность жизнедеятельности в примерах и задачах. Учебное пособие Ч. 4 Под ред. А.И. Сидорова. - Челябинск: Изд. ЧГТУ 1997-45 с.
Щербина Я.Я. Основы противопожарной техники: Учебное пособие. - Киев: Издательское объединение «Вища школа» 1977 - 236 с.
Дипломное проектирование по специальности 1201 - «Технология машиностроения»: Учебное пособие Н.А. Каширин И.М. Морозов С.А. Фадюшин В.Ю. Шамин; Под ред. И.М. Морозова. - Челябинск: Изд. ЮУрГУ 1999 - 56 с.
Оформление технологической документации при выполнении курсовых и дипломных проектов: Методические указания В.Н. Выбойщик Н.А. Каширин В.И. Клочко И.М. Морозов Т.В. Столярова; Под ред. - В.Н. Выбойщика. - Челябинск: ЧПИ 1989-62 с.
Стандарт предприятия. Курсовое и дипломное проектирование. Общие требования к оформлению. СТП ЮУрГУ 04-2001 Сырейщикова Н.В. Гузеев В.И. Сурков И.В. Винокурова Л.В. - Челябинск: ЮУрГУ 2001 - 49 с.
Планировка.dwg

Кран мостовой с кабиной
Тара для готовых деталей
спецификация_приспособление_контр.dwg

Детали-представители.dwg

Сталь 45Х ГОСТ 4563-71
Корпус наружного уплотнения
Детали - представители
спецификация фреза.dwg

Экономика.dwg

ственного оборудования
Мощность установлен-
ных электродвигателей
Съем продукции с еди-
Съем продукции с 1 м
производственной площади
загрузки оборудования
Электровооруженность
труда (потенциальная)
Себестоимость годово-
го выпуска продукции
ТЕХНИКО-ЭКОНОМИЧЕСКИЕ ПОКАЗАТЕЛИ
Масштабы производства
Производственная площадь
Себестоимость детали
Годовая выработка рабочего
Эффективность производства
Организационно-технический уровень производства
Годовой расход металла
Зенкер.dwg

материал хвостовика - сталь ГОСТ 4543-71.
Пластины из твердого сплава ВК8 ГОСТ 3882-77 форма
квадратная №2008-1854 МС 1460.
Материал опорной пластины - твердый сплав ВК15 ГОСТ
Зазор между корпусом и опорной пластиной
и режущей пластинами не допускается.
Допуск биения режущих кромок относительно оси 0
Корпус комплектовать одним ключом ГОСТ 11737-74.
Предельные отклонения размеров конуса по ГОСТ 2848-75.
Схема мех. обработки_торец.dwg

карданного вала автомобиля ПАЗ
Вилка_заготовка+деталь.dwg

Твердость - НВ 207 255.
Вид заготовки - поковка.
* Размер для справок.
Заусенцы и острые кромки не допускаются.
Поверхности обработки
Зажим гидравлический
Сталь 35 ГОСТ1050-74
Деталь после обработки
Техническая характеристика
Технические требования
Условные обозначения
Фреза.dwg

сплава Т15К6 по ГОСТ 3883-80.
Твердость корпуса 32 42 HRC.
Завалы и выкрашивания на главных режущих и
вспомогательных режущих кромках не допускаются.
Допуск перпендикулярности опорного торца относительно оси
Допуск биения главных режущих кромок
перпендикулярно к ним относительно оси посадочного отверстия
должен быть для двух смежных зубьев 0
для двух противоположных зубьев 0
Допуск биения вспомогательных режущих кромок
Неуказанные предельные отклонения размеров по
Головка расточная.dwg

алмазно-расточного станка
* Размеры для сравок
спецификация_станок.dwg

Привод ременный левый
Зажимное приспособление
Шкаф инструментальный
Привод ременный правый