Участок то-2 элкетровозов бкг в локомотивном депо гомель



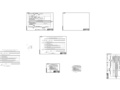

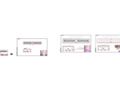
- Добавлен: 25.10.2022
- Размер: 23 MB
- Закачек: 0
Описание
Состав проекта
![]() |
![]() |
![]() ![]() ![]() |
![]() ![]() ![]() |
![]() ![]() ![]() |
![]() ![]() ![]() |
![]() ![]() ![]() |
![]() ![]() ![]() |
![]() ![]() ![]() |
![]() ![]() ![]() |
![]() ![]() ![]() |
![]() |
![]() |
![]() |
![]() ![]() ![]() ![]() |
![]() ![]() ![]() ![]() |
![]() |
![]() |
![]() ![]() ![]() ![]() |
![]() |
![]() ![]() |
![]() ![]() |
![]() ![]() |
![]() ![]() |
![]() ![]() |
![]() ![]() |
![]() ![]() |
![]() ![]() ![]() |
![]() ![]() ![]() |
![]() ![]() ![]() |
![]() ![]() ![]() |
![]() ![]() ![]() |
Дополнительная информация
4 свет.docx
1 Необходимость внедрения энергоэффективных осветительных
В настоящее время вопрос оценки эффективности искусственной освещенности территорий любого объекта обязательно должен рассматриваться с двух сторон: санитарно-гигиенические требования и энергоэффективность. Необходимо помнить что решение задачи экономии электроэнергии в осветительных установках без учета санитарно-гигиенических требований приведет к нарушению зрительной работоспособности рабочих и служащих следовательно увеличится травматизм и снизится производительность и качество труда.
К санитарно-гигиеническим критериям искусственного освещения относятся: освещенность рабочей поверхности показатель ослепленности и т.д. Наиболее целесообразные при современном уровне научно-технического развития страны значения санитарно-гигиенических критериев отражаются в ТКП 45-2.04-153-2009 [5].
Таблица 4.1 – Нормативные уровни искусственного освещения
Разряд и подразряд зрительной работы
Контраст объекта с фоном
Сочетание нормативных величин P и Kп
Комбинированное освещение
В том числе от общего
Введение более жестких норм освещенности рабочих мест требует дополнительных затрат электроэнергии. Поэтому при разработке освещения необходимо не только выполнение санитарно-гигиенических требований но и применение наиболее современных энергоэффективных осветительных установок со светодиодными лампами.
2 Светотехнический расчет
Выбор типа источника света определяется следующими основными
–электрическими характеристиками (напряжением мощностью родом тока силой тока);
–функциональными светотехническими параметрами (световым потоком силой света цветовой температурой спектральным составом излучения);
–конструктивными параметрами (диаметром колбы полной длиной ламп);
–средней продолжительностью горения;
–стабильностью светового потока;
3Светотехнический расчет общего освещения участка
Исходными данными для расчета являются:
–длина участка – 96 м;
–ширина участка – 18 м;
–высота подвеса светильников – 75 м;
–нормируемая поверхность освещенности располагается на полу согласно отраслевому стандарту;
–нормативная освещенность согласно СНБ 2.04.05-98 составляет 200 лк.
Для выбора необходимого по санитарно-гигиеническим требованиям светового потока источников света производится светотехнический расчет по методу коэффициента использования.
Коэффициент использования осветительной установки определяется по [6] в зависимости от формы кривой силы света (КСС) осветительного прибора коэффициента отражения поверхностей и индекса помещения вычисляемого по формуле
где А–ширина освещаемой территории помещения м;
В–длина освещаемой территории помещения м;
НР–высота подвеса светильников общего освещения над рабочей поверхностьюм.
гдеН–высота подвеса светильников от уровня пола м;
Нн–высота на которой нормируется освещенность согласно нормативным
Индекса помещения вычисляемого по формуле (4.1):
Выбираются несколько альтернативных вариантов осветительных приборов (ОП) с различными типами КСС и источниками света. Предварительный выбор типа КСС и расстояние между ОП общего освещения осуществляется согласно [6].
Для индекса помещения различных кривых силы света и коэффициентов отражения потолка стен и рабочей поверхности равных 05; 03 и 01 соответственно коэффициенты использования ОП берутся из таблицы 4.4 [6] и приведены в таблице 4.2.
По рациональному размещению осветительных приборов предварительное минимальное количество рядов ОП k1 можно определить по формуле:
Для остальных осветительных приборов расчет аналогичен результаты отражены в таблице 4.2:
Необходимо произвести проверку количества рядов по наименьшей площади затенения рабочей поверхности при фактической расстановке оборудования в помещении. Эта проверка производится графическим способом. Согласно представленным вариантам на рисунке 4.2 для рассматриваемого участка наиболее рациональным является расположение светильников в 3 ряда. Это количество рядов и принимается в качестве расчетного k1.
Таблица 4.2 – Основные характеристики осветительных приборов
Коэффициент отражения
использования осветительного прибора
а – три ряда ОП (КСС типа Г); б – три ряда ОП (КСС типа Д)
Рисунок 4.1 – Оценка затеняющего эффекта при различных вариантах расположения рядов
общего освещения участка технического обслуживания транспортных средств
Количество в ряду осветительных приборов
гдеd–отношение расстояний между ОП и рядами; принимается от 07 до 15.
Минимальное количество осветительных приборов N рассчитанное по критерию неравномерности определяется по формуле
Расчетный световой поток лампы FР при коэффициенте запаса k = 15 и поправочном коэффициенте Z = 115 определяется по формуле (6.6):
Расчетный световой поток лампы FР лм определяется по формуле
гдеEmin–минимальная (нормируемая) освещенность помещения согласно
ТКП 45-2.04-153-2009 [5];
S–площадь освещаемой территории м2;
k–коэффициент запаса учитывающий снижение освещенности от запыления перекрытий помещения и рассеивателей ОП а также от старения ламп по мере эксплуатации осветительной установки; обычно принимается: для ОП с газоразрядными лампами k=15 для ОП с лампами накаливания k=13 более точные значения коэффициента запаса для конкретных условий эксплуатации принимаются согласно ТКП 45-2.04-153-2009 [5];
Z–поправочный коэффициент равный отношению средней к минимальной освещенности на нормируемой плоскости; рекомендуется принимать: Z = 115 – для ЛН и ламп типа ДРЛ МГЛ НЛВД КЛЛ и т.п.;
Z = 11 – для трчатых ЛЛ при расположении ОП в линию; Z= 1 – при отраженном освещении;
с–коэффициент полезного действия осветительного прибора; принимается согласно паспортным данным на осветительного прибора или справочной литературе [6];
n–количество ламп в светильнике шт.
По рассчитанному значению светового потока лампы подбирается необходимый источник света с учетом допускаемых отклонений фактической освещенности рабочей поверхности в пределах от 09 до 12 нормированной освещенности.
Fр ≤ Fл ≤ 12Fр (4.7)
гдеFл–фактический световой поток лампы при номинальном напряжении в сети лм.
· 31887 ≤ Fл ≤ 12 · 31887
Источник света выбирается по рассчитанному фактическому световому
потоку [6]. Результаты расчета и выбора ламп сводим в таблицу 4.2.
Таблица 4.3 – Подбор оптимальной расстановки и типа лампы
Отношение расстояний между ОП в ряду и между рядами
Количество светильников в ряду k2
Общее количество светильников N
Количество ламп в светильнике n
Для сравнения различных рассчитанных вариантов освещения по критерию энергоэффективности необходимо определить удельную установленную мощность освещения w Втм2
где Р–мощность лампы Вт;
kпра–коэффициент мощности потерь в пускорегулирующей аппаратуре;
Таблица 4.4 – Удельные мощности осветительных проборов
Количество светильников N
Коэффициент потерь в ПРА
По результатам расчетов видим что светодиодные лампы ощутимо превосходят остальные. Для дальнейшего экономического расчета выбираем светодиодные лампы ДКУ-120 и FG-100.
Таблица 4.5 – Характеристики выбранных ламп
Цветовая температура К
Диапазон напряжений В
заключение.docx
Были решены следующие задачи:
) Организована работа участка ТО-2 по обслуживанию электровозов серии БКГ:
–рассчитаны фонды рабочего времени и программы ремонта. Календарный фонд рабочего времени на 2021 год составил 2050 ч. Программа ремонта ТО-2 – 280 секций для БКГ-1 и 245 секций для БКГ-2;
–рассчитаны трудоемкости производственной программы и численность работников. Трудоемкость обслуживания электровоза БКГ-1 составила 171 чел·ч численность рабочих – 8 чел для БКГ-2 трудоемкость – 86 чел·ч численность рабочих – 4 чел;
– рассчитан график загрузки работников и линейных график участка;
–построен план и поперечный разрез участка;
–подобранно необходимое оборудование.
) Рассчитана себестоимость обслуживания на участке – 1697 бел. руб. для БКГ-1 и 990 бел. руб. для БКГ-2.
) Созданы необходимые условия труда соответствующие всем стандартам.
) Подобранно эффективное освящение.
) Рассчитать срок окупаемости энергосберегающих мероприятий на участке ТО-2 – 2 года.
) Рассмотрены современные системы диагностики подвижного состава.
2 пунктдоп.docx
1 Расчет фондов рабочего времени
Производственные процессы связанные с ремонтом локомотивов в ремонтных участках в локомотивном депо Гомель выполняются в одну смену. Начало рабочего времени смены 8 ч 00 мин окончание 17 ч 00 мин продолжительность рабочей смены при этом составляет 8 ч.
Фонд рабочего времени – это система экономико-статистических показателей которые в первую очередь определяют потребляемые ресурсы рабочего времени в границах предприятия.
Фонды рабочего времени подразделяют на календарные номинальные и эффективные.
Трудового Кодекса Министерства труда и социальной защиты Республики Беларусь для различных режимов работы предприятия и публикуется в печати в виде производственного календаря и используется при определении номинальных и эффективных фондов рабочего времени оборудования а также численности работников.
Календарный фонд рабочего времени ч
где Др – число полных рабочих дней; принимаем Др = 251 дней [2];
tр – продолжительность полного рабочего дня; принимаем tр = 8 ч;
Др – число предпраздничных дней в году; принимаем Др = 6 дней [2];
tп – продолжительность предпраздничного дня; принимаем tп = 7 ч.
Таблица 2.1 – Количество полных сокращенных и всех дней в каждом месяце в 2021 году
Таким образом календарный фонд рабочего времени на 2021 год составил
Эффективный фонд рабочего времени ч
где До – продолжительность отпуска; принимаем До = 24 дня [2];
αр – коэффициент учитывающий невыходы на работу по уважительным причинам; принимаем αр = 096.
Годовой фонд рабочего времени оборудования при работе участка ч определяется в соответствии с выражением
где αоб принимаем αоб
S принимаем для участка ТО-2
Приведенные выше расчеты показывают что календарный фонд рабочего времени на 2021 год составил 2050 часов. Эффективный фонд рабочего времени равен 1784 часа. А годовой фонд рабочего времени – 1989 часов.
2 Расчет программы ремонта грузового электровоза серии БКГ
Программу ремонта рассчитывают по видам тяги и сериям отдельно пассажирских грузовых и маневровых локомотивов. Программа ремонта напрямую зависит от нормы продолжительности работы локомотива между КР ТР или ТО [1].
Количество ремонтов и обслуживаний для подвижного состава без учета обновления парка тягового подвижного состава определяется как деление общего годового пробега в границах участков обращения локомотивов на норму пробега между ремонтами и обслуживаниями данного вида принимаемую в соответствии межремонтными пробегами электровоза серии БКГ представленных в таблице 2.2.
Таблица 2.2 – Нормы продолжительности работы электровозов серии БКГ между техни-
ческими обслуживаниями и ремонтами
Расчет программы ремонта и технического обслуживания производится по формулам:
) Количество локомотивов проходящих КР
где – годовой пробег электровоза БКГ-1; принимаем 2100574 км;
– норма пробега локомотивов между КР км (ч).
) Количество локомотивов проходящих СР-2
где – норма пробега для ремонта СР-2
) Количество локомотивов проходящих СР-1
где – норма пробега локомотивов между СР-1 км (ч).
) Количество локомотивов проходящих ТР-2
где – норма пробега локомотивов между ТР-2 км (ч).
) Количество локомотивов проходящих ТР-1
где – норма пробега локомотивов между ТР-1 км (ч).
) Количество локомотивов проходящих ТО-3
где – норма пробега локомотивов между ТО-3 км (ч).
) Количество локомотивов проходящих ТО-2
где – норма пробега локомотивов между ТО-2 км (ч).
Программа ремонта электровоза БКГ-2 рассчитывается аналогично по формулам (2.4) – (2.10) годовой пробег электровоза БКГ-2 отличается от годового пробега электровоза БКГ-1 принимаем – годовой пробег электровоза
БКГ-2 численно равный 3674375 км.
Полученные данные о программе ремонта локомотивов серии БКГ приведены в таблице 2.3
Таблица 2.3 – Программа ремонтов и обслуживаний электровозов серии БКГ
Вид ремонта или обслуживания
Норма пробега между ремонтами или обслуживаниями тыс.км
Программа ремонта или обслуживания секций
Программа ремонта или обслуживания
По данным приведенным в таблице 2.3 в соответствии с объемом ремонта рассматриваемом в рамках дипломного проектирования принимаем вид ремонта в объеме ТО-2 для грузовых электровозов серии БКГ для которого будет осуществляется дальнейшее выполнение вычисления.
3 Расчет основных параметров производственного процесса
Производственный цикл– календарный период времени с момента запуска сырья материалов на первую операцию цикла до получения готовой продукции.
Параметром производственного процесса является такт выпуска – интервал времени через который периодически производится выпуск изделий или заготовок определенных наименований типоразмера и исполнения.
Такт выпуска – интервал времени через который периодически производится выпуск изделий или заготовок определенных наименований типоразмеров
исполнений. Расчет такта выпуска электровоза БКГ-1 производится по формуле:
где – годовой объем выпуска секций из ремонта секций.
Ритм выпуска – количество изделий или заготовок определенных наименований типоразмеров исполнений выпускаемых в единицу времени.
Расчет ритма выпуска электровоза БКГ-1 производится по формуле:
Расчет основных параметров производственного процесса участка ТО-2 для обслуживания грузового электровоза серии БКГ-2 производится аналогично по формулам (2.11) – (2.12).
Подставив значения в формулу (2.11) и (2.12) получаем
– такт выпуска электровоза БКГ-2
– ритм выпуска электровоза БКГ-2
Таким образом для электровоза БКГ-1 такт выпуска составил 71 чсекц. ритм выпуска составил 0141 секцч. Для электровоза БКГ-2 такт выпуска составил 81 чсекц. ритм выпуска составил 0123 секцч.
4 Расчет трудоемкости производственной программы участка ТО-2
Для составления технологического графика работ участка необходимо применять типовые нормы времени устанавливаемые в соответствии с видом обслуживания и ремонта.
Трудоемкость по обслуживанию грузовых электровозов серии БКГ в объеме ТО-2 составляется в соответствии с типовыми нормами на выполнение ремонтных работ предназначенные для нормирования труда рабочих выполняющих ремонт подвижного состава.
В типовых нормах помимо основного времени включено также время на подготовительно-заключительные операции Тпз обслуживание рабочего места Тоб на отдых и личные надобности Тотл (регламентированные перерывы).
Нормы времени рассчитываются по формуле
где Топ – норма оперативного времени (время затрачиваемое на непосред-
ственное выполнение работ) нормо-мин;
Тпз– норматив учитывающий время на подготовительно-заключитель-
ные операции (время затрачиваемое на получение задания и сдачи
работы получение инструмента материала приспособлений и сда-
чи их после выполнения работ проходы к рабочему месту в начале
и конце смены до и после обеденного перерыва оформление до-
пуска к работе и окончания ее включение и отключение оборудо-
вания в начале и конце производственного процесса); принимаем
Тоб– норматив учитывающий время на обслуживание рабочего места
(время затрачиваемое на раскладку и уборку инструмента сборку
разборку осмотр чистку смазку и регулировку и настройку аппа-
ратуры оборудования и приспособлений используемых при вы-
полнении производственного процесса); принимаем Тоб = 30 % [3];
Тотл– норматив учитывающий регламентированные технологические и
физиологические перерывы; Тотл = 27 % [3];
В соответствии с перечнем работ и трудоемкость трудоемкость по техническому обслуживанию грузовых электровозов серии БКГ в объеме ТО-2 представлена в таблице 2.4.
Таблица 2.4 – Трудоемкость ремонта грузовых электровозов БКГ по ТО-2
Норма на объем чел·чсекц
Работу оборудования электровоза до постановки на техническое обслуживание
под контактным проводом
Проверить состояние электрического оборудования токоприемник на подъем и
Проверить состояние измерительных приборов
Состояние и креплениетормозного и пневматического оборудования электропневматического тормоза песочного оборудования гребнесмазывателей
Продолжение таблицы 2.4
КЛУБ радиостанции УСАВП РПДА ЭПТ радиосвязи
Работу и нагрев подшипниковых узлов в ходовой части доступных для контроля местах проверить
Механическое оборудование
Состояние и крепление рам тележек колесно-моторных блоков и тяговых редукторов
Состояние и крепление колесной пары и буксового узла тормозной рычажной передачи и тормозные колодки
Состояние и крепление поручней лестниц переходных площадок межтележечного соединения стеклоочистителя
Состояние и крепление рамы кузова путеочистителей работу автосцепок и ручных тормозов
Состояние и крепление трубы санузла песочного оборудования проверить
Отстой (конденсат) из корпусов моторно-осевых подшипников слить механическое оборудование при необходимости смазать
Крепление исправность и действие гребнесмазывателей проверить
Состояние и крепление кузова его оборудования проверить детали закрепить неисправности устранить
Электрические машины
Состояние тяговых электродвигателей проверить: выводные кабели заземляющие устройста сопротивление изоляции.
Состояние вспомогательных машин: крепление машин к основаниям соединительных муфт моторвентиляторов и вспомогательного компрессора редукторов моторкомпрессоров подводящих проводов
Крышевое оборудование
Состояние и крепление токоприемника изоляторов пневматического привода токоподводящих шин велитовых разрядников ограничители перенапряжения антенны радиосвязи осмотреть
Состояние и крепление выключателей разрядников дросселей разъединителей и заземлителей резисторов кабелей шунтов герметичность шлангов трубопроводов
Электрическая аппаратура
Аппаратуру камер пульты управления продуть
Четкость и последовательность срабатывания аппаратов отсутствие утечек воздуха проверить сопротивление изоляции цепей замерить
Состояние и крепление электрических аппаратов вспомогательного оборудования кабелей проводов плотность прилегание и замыкание контактов работу подвижных частей аппаратов исправность электромагнитных защелок и блокировок безопасности заземляющих шин
Проверить крепление электропневматического вентиля работоспособность электрической схемы гребнесмазывателей
Состояние и крепление тягового трансформатора реакторы индуктивные шунты
Аккумуляторную батарею осмотреть напряжение уровень плотность электролита замерить. Общее напряжение аккумуляторной батареи без нагрузки и под нагрузкой проверить
Тормозное и пневматическое оборудование
Состояние и крепление трубопроводов приборов работу тормозного и пневматического оборудования плотность тормозной магистрали величину выхода штоков тормозных цилиндров чувствительность уравнительного поршня к торможению и отпуску
КЛУБ-У автоматическая локомотивная сигнализация автостоп скоростемеры радиосвязь УСАВП РПДА
Проверить состояние электрического оборудования
КЛУБ радиостанции УСАВП РПДА ЭПТ радиосвязи контрольно-измерительные приборы
Данная таблица показывает что общая трудоемкость программы по техническому обслуживанию грузовых электровозов серии БКГ в объеме ТО-2 составляет 86 челчсекц.
5 Расчет численности работников
Расчет потребной численности производственных рабочих а именно
списочного и явочного контингентов участка необходимого для производства технического обслуживания и ремонта подвижного состава выполняется для построении линейного графика обслуживания электровоза и загрузки рабочих.
Явочный контингент производственных рабочих – это та численность
производственных рабочих которая обеспечивает годовой объем производства
продукции и всю его производственно-хозяйственную деятельность иными словами это численность трудящихся ежедневно выходящих на работу.
Списочный контингент производственных рабочих – это все работники промышленно-производственного персонала числящиеся на предприятии.
Явочный контингент производственных рабочих участка (отделения)
определяется по формуле
где qi – трудоемкость ремонта или обслуживания секции локомотива для
данного участка (отделения) челчсекцию; принимается в соответ-
ствии расценочными ведомостями депо qТО-2 171челчсекцию;
Пi – годовой объем выпуска из ремонта или обслуживания данного вида
секций принимается по данным таблицы 2.3
Списочное (штатное) количество рабочих ремонтного подразделения в
состав которого входят рабочие находящиеся на данный момент на больничном в трудовом отпуске командировке и т. д. рассчитывается исходя из выражения
Явочный и списочный контингенты производственных рабочих необходимых для выполнения работ по обслуживанию грузовых электровозов серии БКГ по циклу ТО-2 определяется по формулам (2.13) (2.14). В соответствии с
перечнем работ и трудоемкость представленных в таблице 2.1.
Тогда явочный контингент производственных рабочих участка ТО-2 по обслуживанию грузовых электровозов БКГ-1 составляет
Списочный контингент производственных рабочих составляет
Расчет явочного и списочного штата рабочих для БКГ-2 производится аналогичным образом по формулам (2.13) – (2.14)
Явочный штат рабочих определяется по формуле (2.13)
Списочный штат рабочих определяется по формуле (2.14):
Расчетный явочный и списочный штат рабочих не отвечает требованиям технологии обслуживания электровозов серии БКГ принимаем значения приведенные в таблице 2.5.
Таблица 2.5 – Численность работников участка ТО-2 задействованных в ремонте электровозов
Трудоемкость ремонта или обслуживания челчсекцию
Программа ремонта или обслуживания секции
6Разработка графика загрузки рабочих и линейного графика
График работ участка показывает в какой последовательности когда и за какое время необходимо закончить выполнение всех работ по обеспечению технического обслуживания или ремонта подвижного состава.
Ведомость работ осуществляемых при техническом обслуживании грузовых электровозов серии БКГ в объеме ТО-2 представлена в таблице 2.6.
Таблица 2.6 – Работы по техническому обслуживанию электровоза БКГ-1
по техническому обслуживанию
Проверить состояние электрического оборудования токоприемник на подъем и опускание
Работу КЛУБ радиостанции УСАВП РПДА ЭПТ радиосвязи
Состояние и крепление поручней лестниц переходных площадок межтележечного соединения стеклоочистителя.
Продолжение таблицы 2.6
по техническому обслуживанию
Состояние тяговых электродвигателей проверить: крепление выводные кабели заземляющие устройста сопротивление изоляции отсутствие повреждений
Аккумуляторную батарею осмотреть напряжение уровень плотность электролита замерить. Общее напряжение аккумуляторно батареи без нагрузки и под нагрузкой проверить
Состояние и крепление трубопроводов работу тормозного и пневматического оборудования плотность тормозной магистрали величину выхода штоков тормозных цилиндров чувствительность уравнительного поршня
Общая трудоемкость технического обслуживания электровоза БКГ-1 составила 171 чел·ч. численность рабочих – 8 а затрачиваемое время равно 3 ч.
Таблица 2.7 – Работы по техническому обслуживанию электровоза БКГ-2
Продолжение таблицы 2.7
Общая трудоемкость технического обслуживания электровоза БКГ-2 составила 86 чел·ч. численность рабочих – 4 а затрачиваемое время равно 3 ч.
В соответствии с данными приведенными в таблице 2.6 построен график технического обслуживания грузовых электровозов серии БКГ в объеме ТО-2 и график загрузки рабочих.
7Подбор оборудования для участка ТО-2
С целью повышения технического уровня и укрепления ремонтной базы локомотивного депо Гомель выполняющего техническое обслуживание текущие ремонты и ремонт разработаны и утверждены технические регламенты технологического оснащения локомотивного депо.
Технические регламенты устанавливают требования к оснащенности предприятий основным специализированным технологическим оборудованием и средствами диагностики. Ими следует руководствоваться при оценке технологической оснащенности ремонтных предприятий а также при выполнении проектных работ по реконструкции и новому строительству.
Основными работами участка является – предупреждение появления неисправностей и поддержания локомотивов в работоспособном и надлежащем сани-
тарно-гигиеническом состоянии обеспечивающим его бесперебойную работу и
безопасность движения а также высокий уровень обслуживания пассажиров.
Перечень оборудования участка принимается исходя из условий технологической необходимости и комплектности. Перечень представляют в виде ведомости оборудования в которой указывают его габаритные размеры стоимость и нормативный процент амортизации. Нормативные сроки служб основных средств а также их шифры принимаются в соответствии с [4]. Стоимость оборудования принимается на основании карточек инвентарного учета оборудования соответствующего участка (отделения) локомотивного депо. Нормативный срок службы и соответственно процент амортизации определяются на основании постановления Министерства экономики РБ №161 от 30 сентября 2011 г.
В ведомость оборудования включают также подъемно-транспортные
средства. Подъемно-транспортные средства применяемые на участке должны
соответствовать техническим и организационным особенностям производства специализироваться на перемещении определенных видов грузов. Поэтому вид и количество подъемно-транспортных средств применяемых на участке по ремонту электровозов серии БКГ были определены типом производства сложностью и многообразием технологического процесса характером изготавливаемой или
ремонтируемой продукции расстоянием между начальным и конечным пунктом транспортировки характером расположения оборудования и типом производственного здания.
Ведомость оборудования для участка по обслуживанию электровозов серии БКГ в объеме ТО-2 представлена в таблице 2.6.
Таблица 2.8 – Ведомость оборудования участка ТО-2 до модернизации
Габаритные размеры мм
Сумма амортизационных отчислений бел. руб.
Шкаф для инструментов
Стеллаж для тормозных колодок
Инструментальные ящики
Стеллаж с токоприемниками
Устройство для подачи масла в МОПы
Продолжение таблицы 2.8
Площадка для осмотра
Таблица 2.9 – Ведомость оборудования участка ТО-2 после модернизации
Устройство для заправки гребнесмазывателей
ПЗУ «Передвижное зарядное устройство»
Доктор-100ПГ «Система контроля и диагностики токоприемников»
-пневматический блок
Доктор-100М «Прибор контроля качества изоляции»
8 Разработка плана и поперечного разреза участка ТО-2
Структура и компоновка производственных помещений при планировке депо зависит от конструктивных и технологических особенностей ремонтируемых узлов агрегатов и деталей объемов выпуска и типа производства сложности и разнообразия технологических процессов которые непосредственно влияют на сложность структуры предприятия и его размеры.
Основными задачами решаемыми при разработке рациональной планировки участков локомотивных депо являются:
– осуществление оптимальных решений по распределению потребных площадей и размещению средств производства;
– создание поточности и сокращение расстояний перемещения материалов заготовок изделий;
– создание условий для производительной и безопасной работы производственного персонала.
Главные задачи по разработке плана участка включаются в расстановке оборудования необходимого для обеспечения планового обслуживания и ремонта а также определение габаритов помещения.
Техническое обслуживание в объеме ТО-2 грузовых электровозов серии БКГ будет производиться уже в существующем участке при расстановке дополнительного оборудования учтены следующие требования:
–размещение в соответствии с установленным технологическим процессом обеспечивая при этом удобство его использования и обслуживания а также естественное освещение рабочего места;
–наименьший грузооборот между рабочими местами;
–габариты безопасности между оборудованием приближением стен и перегородок;
– наименьшие длины систем энергоснабжения.
План и поперечный разрез участка ТО-2 локомотивного депо Гомель с размещением оборудования необходимого для ремонта изображен на листе графической части в масштабе 1:150. На этом же листе показано размещение участка на плане производственного корпуса локомотивного депо Гомель в масштабе 1:1000.
9 Определение площади участка
Площадь и размеры участка определяем из тех условий что в нем должно поместиться все необходимое оборудование для ремонта и должны быть приняты строительные стандарты на строительство зданий локомотивного депо.
Длина ширина и высота зданий шаг колонн и расстояния между осями путей унифицированы. Участки депо проектируют с учетом шага строительных колонн – 6 или 12 м как правило прямоугольной формы ширина пролетов – 12 18 24 и 30 м. Высота зданий не менее 6 м и кратна 12 м.
Расстояние между технологическим оборудованием следует принимать не менее 1 м при этом необходимо учитывать установленные ограждения. Другую
оргоснастку (шкафы стеллажи верстаки) устанавливают вплотную к стенам.
Площадь отделения определяется по формуле
b – ширина отделения м; принимаем b = 18 м;
Объем отделения определяется по выражению
где М – высота участка м; М = 84 м.
Vо = 1728 84 = 14515 м3
В результате расчета получили площадь участка S = 1728 м2 объем –
введение.docx
Реконструкция ремонтной базы депо также приобретает важное значение так как ее оснащение современными средствами и новейшими технологиями восстановления деталей квалифицированным ремонтным и обслуживающим персоналом помогает более достоверно предупреждать появление неисправностей локомотивов в процессе эксплуатации.
На сегодняшний день обслуживание и ремонт электровозов серии БКГ производится только на базе локомотивного депо Барановичи в дальнейшем при росте перевозок и закупках большего количества электровозов депо Барановичи может столкнуться с проблемой нехватки ремонтных участков времени и рабочей силы. Для расширения ремонтных и обслуживающих участков выбрано локомотивное депо Гомель.
В дипломном проекте будет представлен участок технического обслуживания ТО-2 электровозов серии БКГ что поможет избежать проблемы излишней загруженности локомотивного депо Барановичи обеспечит высокую надежность и бесперебойность обслуживания грузовых электровозов серии БКГ.
В дипломном проекте необходимо решить следующие задачи:
)Организовать работу участка ТО-2 по обслуживанию электровозов серии БКГ:
– рассчитать фонды рабочего времени и программы ремонта;
– рассчитать трудоемкости производственной программы и численность работников;
– построить график загрузки работников и линейных график участка;
– рассчитать себестоимость обслуживания;
– разработать план и поперечный разрез участка;
– подобрать необходимое оборудование.
) Рассчитать себестоимость обслуживания на участке.
)Создать необходимые условия труда соответствующие всем стандартам.
)Рассчитать срок окупаемости энергосберегающих мероприятий на участке ТО-2.
1 пунктдоп.docx
1Система технического обслуживания и ремонта электрического
подвижного состава БелЖД
На Белорусской железной дороге широкое распространение получила планово-предупредительная система технического обслуживания и ремонта локомотивов и моторвагонного подвижного состава предназначенная для обеспечения устойчивой работы парка тягового подвижного состава (ТПС) поддержания его технического состояния и повышения эксплуатационной надежности.
В соответствии с приказом начальника Белорусской железной дороги от 30 ноября 2015 г № 370Н «Об утверждении Положения о системе технического обслуживания и ремонта локомотивов и моторвагонного подвижного состава на Белорусской железной дороге» устанавливаются следующие виды планового технического обслуживания и ремонта локомотивов [1]:
технические обслуживания ТО-1 ТО-2 ТО-3 ТО-4 ТО-5 а б в г д;
текущие ремонты ТР-1 ТР-2 ТР-3;
средние ремонты СР-1 СР-2;
капитальные ремонты КР КР-1 КР-2;
Технические обслуживания ТО-1 ТО-2 и ТО-3 служат для предупреждения появления неисправностей поддержания ТПС в работоспособном и надлежащем санитарно-гигиеническом состоянии обеспечивающем его устойчивую безаварийную работу и пожарную безопасность.
Техническое обслуживание ТО-4 служит для обточки колесных пар без выкатки из-под ТПС с целью поддержания профиля бандажей и колес цельнокатаных колесных пар в пределах установленных действующей технической документацией по ремонту и содержанию колесных пар ТПС.
Разрешается совмещать техническое обслуживание ТО-4 с техническим обслуживанием ТО-3 текущими ремонтами ТР-1 и ТР-2 увеличивая нормы продолжительности этих видов ремонта и обслуживания с учетом норм продолжительности технического обслуживания ТО-4.
Техническое обслуживание ТО-5а служит для подготовки ТПС в консервацию и резерв Управления Белорусской железной дороги ТО-5г – при вводе в эксплуатацию после изъятия из консервации и резерва Управления Белорусской железной дороги.
При необходимости подготовки ТПС к пересылке в недействующем (холодном) состоянии на капитальный средний или текущий ремонты и в связи с передислокацией а также подготовки ТПС к эксплуатации который
прибыл в недействующем (холодном) состоянии после постройки капитального среднего или текущего ремонтов и передислокации выполняется соответственно техническое обслуживание ТО-5б или ТО-5в.
Техническое обслуживание ТО-5д (диагностика) служит для оценки и контроля фактического технического состояния локомотивов их узлов для принятия мер по предотвращению отказов. Порядок организации и проведения ТО-5д устанавливается приказом заместителя Начальника Белорусской железной дороги.
Средний ремонт СР-1 СР-2 – ремонт выполняемый для восстановления исправности и частичного восстановления ресурса ТПС.
Средний ремонт ТПС и его узлов выполняется в специализированных локомотивных депо или в сторонних организациях.
Капитальный ремонт КР (КР-2) служит для восстановления эксплуатационных характеристик исправности ТПС и его ресурса близкого к полному путем ремонта или замены агрегатов узлов и деталей включая базовые и полной заменой проводов и кабелей а также модернизации.
Для обеспечения надежной и качественной работы по перевозке грузов в локомотивном депо Гомель ежедневно проводят различные виды технического обслуживания и ремонтов.
2Общая характеристика локомотивного депо Гомель
Локомотивное депо Гомель (ТЧ-8) одно из старейших предприятий
Белорусской железной дороги. Являясь высокотехнологическим предприятием оснащенным современным оборудованием технологической оснасткой располагающим высококвалифицированными кадрами локомотивное депо Гомель способно решать сложные задачи связанные с ремонтом локомотивов и организацией перевозочного процесса пассажиров и грузов. Основная задача стоящая перед коллективом предприятия обеспечение потребности государства в перевозках грузов и пассажиров содержание тягового и моторвагонного подвижного состава в исправном состоянии.
Гомельское локомотивное депо является обособленным структурным подразделение транспортного республиканского унитарного предприятия «Гомельское отделение Белорусской железной дороги» и действует на основании законодательства Республики Беларусь нормативных правовых актов объединения «Белорусская железная дорога» Устава транспортного республиканского унитарного предприятия «Гомельское отделение Белорусской железной дороги».
В производственную структуру локомотивного депо Гомель входят отделения и участки:
технического обслуживания и текущего ремонта тепловозов и электровозов;
технического обслуживания и текущего ремонта дизель-поездов;
топливный и автотормозной.
На высоком уровне поддерживается техническое состояние локомотивов благодаря работе в депо современных диагностических комплексов «Магистраль» «Вектор 2000» «Доктор ЗОМ» «Доктор 60Т» и дефектоскопов ВД12-НФМ УНМ300-2000 МД-12ПШ (ПЭ ПС) УН-5. Использование данных диагностических комплексов позволяет ежегодно экономить топливно-энергетические ресурсы путем настройки дизелей на экономичную и эффективную работу а также обеспечивать надежную и долговечную работу дизель-генераторная установка (ДГУ).
Основное направление производственной деятельности депо заключается в выполнении текущих видов ремонта ТР-2 тепловозов серии 2ТЭ10 ТГК2 ДР1А а также технического обслуживания ТО-4 ТО-3 ТО-2 и текущих ремонтов ТР-1 тепловозов маневрового подвижного состава электровозов и элетропоездов.
В локомотивном депо Гомель также выполняется ремонт тяговых электродвигателей ЭД-118 ТЕ-006 главных генераторов ГП311Б ТД802 ремонт топливной аппаратуры и дизелей 10Д100 и К6S310DR. В депо также одновременно с окончанием электрификации участка Жлобин-Гомель цехом ремонта освоен ремонт и техническое обслуживание электроподвижного состава электровозы ВЛ-80С и электропоезда ЭР9Е с 2016 г регулярно проходят качественное и своевременное обслуживание в цехах локомотивного депо. На очереди освоение технического обслуживания пассажирских электровозов ЧС4Т и грузовых – БКГ-1 и БКГ-2.
Нормы продолжительности работы электровозов серии БКГ между техническими обслуживаниями и ремонтами а также нормы продолжительности технического обслуживания и ремонта представлены в таблицах 1.1-1.2.
Таблица 1.1 – Нормы продолжительности работы электровозов серии БКГ между
техническими обслуживаниями и ремонтами
Таблица 1.2 – Нормы продолжительности технического обслуживания и ремонта
электровозов серии БКГ
Виды технических обслуживаний и ремонтов
Нормы продолжительности технического обслуживания и ремонта устанавливаются с учетом специфики эксплуатации ПС фактического уровня технологической оснащенности ремонтных баз локомотивных депо уровня использования средств технической диагностики.
Учет времени нахождения подвижного состава (ПС) на техническом обслуживании и ремонте осуществляется в соответствии с действующей Инструкцией по учету наличия и состояния локомотивов и моторвагонного подвижного состава на Белорусской железной дороге.
3 Структурная схема технологических потоков ТО-2 грузовых
электровозов серии БКГ
Техническое обслуживание ТО-2 выполняется работниками пунктов технического обслуживания локомотивов на специально оборудованных смотровых канавах. Объём работ включает осмотр ходовой части тормозной системы тяговых двигателей вспомогательных машин трансформаторов и электрических аппаратов.
Объем работ выполняемых в рамках технического обслуживания ТО-2 электровозов серии БКГ и отраслевые нормативы устанавливаются Министерством транспорта и коммуникаций Республики Беларусь исходя из документации завода изготовителя. Перечень обязательных работ выполняемых на электровозах серии БКГ при проведении технического обслуживания ТО-2 приведен в таблице 1.3.
Таблица 1.3 – Перечень обязательных работ выполняемых на электровозах серии
БКГ при проведении технического обслуживания ТО-2
Наименование работ операции (технологический процесс)
Произвести анализ замечаний локомотивных бригад по бортовому журналу формы ТУ-152 для определения объема дополнительных работ
Нагрев буксовых узлов проверить
Подъём и опускание токоприёмников проверить
Уровень масла в главных компрессорах проверить
Производительность пределы давления включения и отключения компрессоров проверить
Продолжение таблицы 1.3
Плотность тормозной питательной сети и тормозных блоков проверить
Правильность положения ручек разобщительных кранов и режимных переключателей воздухораспределителя КАВ в шкафу тормозной аппаратуры проверить
Зарядное давление в тормозной магистрали проверить
Темп ликвидации сверхзарядного давления проверить
Действие автоматического тормоза при служебном и экстренном положениях проверить
Предельное давление в тормозных блоках при полном торможении.
Функционирование сигнализатора разрыва тормозной магистрали проверить
Функционирование электрического и стояночного тормоза проверить
Проходимость воздуха через модуль управления BP-Compact проверить
Проходимость воздуха через концевые краны тормозной магистрали проверить
Функционирование аппаратуры КЛУБ-У срабатывание ЭПК автостопа проверить
Функционирование обогрева лобового стекла проверить
Функционирование стеклоочистителей и подачи омывающей жидкости проверить
Функционирование прожектора буферных фонарей освещения проверить
Функционирование звуковых сигналов проверить
Функционирование подачи песка под все колёсные пары проверить
Функционирование гребнесмазывателя проверить
Функционирование индикаторных ламп на целостность глазков и свечение проверить
Отсутствие ошибок на дисплее модуля мониторинга управления и модулей «ACDC» «DCDC50B» проверить
Пределы напряжения 95-110В цепей управления по вольтметру проверить
Отсутствие ошибок модулей: процессора ТС ввода и вывода цифровых данных; ввода и вывода аналоговых данных проверить
Функционирование подшипниковых узлов вспомогательных машин проверить
Функционирование тепловентиляторов кабины и машинного отделения проверить
Функционирование системы кондиционирования воздуха проверить
Функционирование счетчика электрической энергии проверить
Удалить конденсат из главных и вспомогательных резервуаров
Слить содержимое картера контаминации санузла
Снять данные и произвести анализ системы электровоза с помощью бортового компьютера и модуля мониторинга температуры подшипников
Произвести устранение и контроль несоответствий выявленных при контроле параметров работы оборудования анализе диагностических данных и замечаний локомотивных бригад
Контролировать и обеспечить нормальный уровень жидкостей:
- охлаждающей жидкости шкафов главных преобразователей;
- масла тягового трансформатора;
- масла редукторов колесно-моторных блоков;
- масла гребнесмазывателей;
- омывателей лобовых стекол
Контролировать наличие пломб на предохранительных клапанах регуляторах давления электропневматических клапанах автостопа №150И разобщительных кранах ЭПК разъемах электрического соединителя XI блока КОН кранах Z20 для перевода на резервный тормоз кнопках бдительности воздухораспределителе редукционных клапанах датчиках обрыва тормозной магистрали
Контролировать сроки поверки измерительных приборов
Протестировать систему пожаротушения контролировать наличие и исправность противопожарного инвентаря огнетушителей
Контролировать крепление модулей «ACDC» «DCDC50B» «Мониторинга и управления» шкафа зарядного устройства
Контролировать визуально в доступных для осмотра местах состояние электрической проводки
Очистить от загрязнений фильтрующую сетку кондиционера
Контролировать состояние фильтров вентиляционных установок
Очистить от пыли радиатор охлаждения комбинированного охладителя
Контролировать компрессоры на отсутствие утечек масла состояние деталей и соединений масляного контура
Контролировать визуально осушители воздуха на отсутствие осадка белого цвета в сливной системе целостность деталей и соединений воздушного контура
Удалить масло из фильтра тонкой очистки питательной магистрали
Контролировать визуально целостность щёток стеклоочистителя
Контролировать наличие и работу электрочайника микроволновой печи холодильника
Контролировать наличие ходового инструмента; тормозных башмаков
Контролировать наличие и целостность упаковочных коробок самоспасателей в кабинах машиниста
Контролировать крепления узлов крышевого оборудования
Очистить от пыли и загрязнений корпус высоковольтного ввода высоковольтного трансформатора напряжения высоковольтного разъединителя высоковольтного соединителя (на БКГ-1) крышевых изоляторов вакуумного выключателя грозоразрядники
Контролировать визуально состояние изоляторов
Контролировать износ угольных накладок токоприемников
Контролировать активное и пассивное нажатие полозов токоприемников на контактный провод
Контролировать и отрегулировать время подъёма и опускания токоприёмников
Для защиты токоприемников от обледенения при гололедообразовании необходимо производить покрытие нижних и верхних подвижных рам
Контролировать сроки поверки и действия периодических регламентных работ блоков
Контролировать наличие и целостность пломб состояние и крепление монтажных проводов кабелей разъемов работоспособность блоков КОН БКР-У-1М БСИ БЭЛ-У ИП-ЛЭ БИЛ-М
Контролировать наличие индикации на блоках БИЛ-М наличие восьми градаций яркости включение и выключение подсветки клавиатуры переключение режимов работы на блоке БИЛ-М
Контролировать работоспособность РБ (РБС) на локомотиве надежность их креплений
Осмотреть протереть блок БС-ДПС. Контролировать состояние и крепление блока разъемов. Включить КЛУБ проверить свечение четырех светодиодов на БС-ДПС после нажатия кнопки «СБРОС». Проверить свечение светодиода «Стыковка» при установленной заглушке
Контролировать правильность приема информации системой КЛУБ из рельсовой цепи проверить принудительный переход с «Красного» на «Белый» сигнала светофора проверить цепь контроля включения тяги
Контролировать правильность установки постоянных характеристик в блоке БЭЛ-У
Контролировать состояние преобразователей избыточного давления КРТ (ДДИ) проверить индицирование преобразователей давления на блоке БИЛ-М
Контролировать антенно-усиливающее устройство АУУ-1 на отсутствие повреждений
Записать электронною карту участка в энергонезависимую память блока БЭЛ-У
Осмотреть проверить датчики ДПС-У гермопереходы проверить работоспособность датчиков ДПС-У
Осмотреть протереть приемные катушки КПУ. Открыть крышки клеммных коробок детали протереть осмотреть состояние подводящих проводов рукавов уплотняющих прокладок проверить сопротивление изоляции электрических цепей замерить.
При наличии замечаний в журнале ТУ-152 о сбое огней АЛСН произвести проверку электрических параметров приемных катушек
Контролировать визуально состояние блоков радиостанции кабельного монтажа креплений на отсутствие повреждений
Контролировать визуально детали подвески и их крепления на отсутствие повреждений деформаций трещин изломов ослаблений контролировать гидравлические гасители колебаний визуально на отсутствие утечки масла
Колесные пары осмотреть в соответствии с требованиями Инструкции по формированию ремонту и содержанию колесных пар ТПС. Контролировать визуально наличие крепёжных деталей состояние креплений буксового узла и буксы МОП. Контролировать смещении ступицы колеса по контрольным полосам
Контролировать визуально корпус редуктора. Проверить целостность и комплектность крепежных деталей
Контролировать крепления электродвигателя с буксой МОП с тяговым редуктором и устройство подвески ТЭД на отсутствие повреждений деформаций трещин изломов ослаблений
Контролировать элементы тяговых устройств на исправность укомплектованность отсутствие смещений
Контролировать толщину тормозных колодок
Контролировать крепление узлов гребнесмазывателя при необходимости отрегулировать положение форсунок гребнесмазывателя относительно обода колеса
Контролировать целостность камнесбрасывателя отрегулировать положение камнесбрасывателя относительно головки рельса
Контролировать состояние трубопроводов подачи песка
Контролировать крепление резьбовых соединений путеочистителя
Контролировать крепление узлов автосцепного устройства
Контролировать визуально на отсутствие трещин любого размера и характера видимую часть: корпуса автосцепки тягового хомута; маятниковые болты центрирующую балочку корпус поглощающего аппарата планку поддерживающую тяговый хомут кронштейн крепления расцепного рычага клин тягового хомута цепь расцепного привода.
Заправить санитарный узел водой
Проверка электровоза после обслуживания
Выполнить обтирочные работы в объёме установленном начальником депо
Время подъёма и опускания токоприёмников проверить
Производительность пределы включения и отключения компрессоров проверить
Время наполнения тормозных блоков при экстренном торможении проверить
Предельное давление в тормозных блоках при полном торможении вспомогательным тормозом отсутствие недопустимого снижения давления проверить
Проходимость воздуха через модуль управления BP-Compact
Функционирование аппаратуры КЛУБ срабатывание ЭПК автостопа проверить
Напряжения 95-110В цепей управления по вольтметру проверить
Поставить в журнале формы ТУ-152 штамп с указанием названия депо даты времени проведения технического обслуживания и росписи
Структурная схема технологических потоков составлена на основании технического регламента текущего ремонта ТО-2 и правил технического обслуживания электровозов серии БКГ.
Техническое обслуживание ТО-2 локомотивов осуществляют слесари по осмотру и ремонту локомотивов на пунктах технического обслуживания
–7 разрядов слесари по ремонту подвижного состава 4–7 разрядов.
Структурная схема технологических потоков технического обслуживания в объеме ТО-2 представлена на первом листе графической части дипломного проекта.
реферат.docx
источника 7 листов графической части проекта.
Ключевые слова: техническое обслуживание электровоз трудоемкость организация работы участка программа ремонта.
Объект исследования: техническое обслуживание грузовых электровозов серии БКГ.
Цель работы: организация технического обслуживания ТО-2 электровозов серии БКГ на основе участка ТО-2 тепловозов.
При выполнении работы были рассмотрены: участок ТО-2 тепловозов локомотивного депо Гомель и технология обслуживания ТО-2 электровозов серии БКГ. Составлена структурная схема обслуживания. Рассчитаны фонды рабочего времени программы ремонта основные параметры производственного процесса трудоемкости численность работников. Разработаны линейные графики и графики загрузки рабочих подобрано оборудование. Рассчитана себестоимость обслуживания.
Подобрано новое энергоэффективное и экономически обоснованное светодиодное освещение.
В дипломном проекте была рассмотрена техническая диагностика состояния подвижного состава и перспективы ее развития в Западной Европе и США.
Степень внедрения результатов дипломного проекта: материалы полученные в ходе работы после соответствующей доработки в локомотивном депо могут быть использованы при организации ТО-2 электровозов серии БКГ.
Практическая значимость работы: организация технического обслуживания грузовых электровозов серии БКГ в условиях локомотивного депо Гомель позволит снизить нагрузку на локомотивное депо Барановичи.
6 оборудование.docx
1 Общее представление переносных диагностических устройств
Переносные автоматизированная система технического диагностирования (АСТД) находят всё более широкое применения. Причина тому – развитие микропроцессорной техники средств отображения информации и систем передачи данных. Можно выделить два подхода к созданию переносных АСТД: создание специализированных устройств на базе специальной аппаратной части и использование стандартных измерительных средств с настройкой и адаптацией их под диагностируемый объект. Оба варианта построения систем одинаково распространены на транспорте. Однако использование стандартных промышленных узлов и устройств в т.ч. планшетных компьютеров становится всё более популярным.
Унифицированное построение аппаратной части и относительная простота разработки программного обеспечения с использованием языков программирования высокого уровня позволяют достаточно быстро разрабатывать различные виды переносных систем поэтому их число измеряется десятками. Далее описаны наиболее распространенные из них.
Серия мобильных приборов контроля и диагностики «Доктор-060».В НИИТКД разработана и широко внедрена серия приборов диагностирования (переносных АСТД) для различных видов оборудования. В состав комплекса входит рабочее место мастера «Доктор-060ММ» стационарный блок приёма-передачи данных «Доктор-060СТ» и набор мобильных приборов контроля и диагностирования
Процесс измерения диагностических параметров и показателей оборудования осуществляется оператором при помощи мобильных приборов и диагностирования. Результаты замеров отображаются на встроенном дисплее мобильного прибора и передаются в базу данных Мастера где происходит их качественная оценка и хранение. Результаты диагностирования (норма не норма) передаются обратно на мобильные приборы и выводятся на дисплей.
На основании накопленной информации на рабочем месте мастера формируется протокол испытаний оборудования который при необходимости может быть выведен на печать. Связь между составными частями системы беспроводная питание блоков контроля и диагностики автономное от встроенных аккумуляторных батарей.
Использование«Доктор-060» в цехах при техническом обслуживании позволяет выявлять неисправности на ранних стадиях что сокращает число отказов электрического оборудования во время эксплуатации.
«Доктор-060Z»предназначен для контроля параметров и выявления дефектов обмоток тяговых электродвигателей и другого электрооборудования тягового подвижного состава железнодорожного транспорта. Для подключения к объекту диагностирования «Доктор-060Z» комплектуется специальным щупом с зажимами типа «крокодил» на концах. Оператор управляет процессом измерения при помощи клавиатуры расположенной на лицевой стороне прибора путем выбора соответствующих пунктов меню выводимого на дисплее. Служебные операции
связанные с идентификацией диагностируемого оборудования выбором вида ремонта и передачей данных на рабочее место мастера также осуществляются при помощи клавиатуры.
«Доктор-060Z» позволяет производить измерение (вычисление) и оценивать в соответствии с нормированными значениями следующие параметры диагностируемого оборудования:
– фактор потерь (тангенс угла диэлектрических потерь) который характеризует потери вызываемые токами проводимости в изоляции. Несоответствие данного параметра нормативному свидетельствует об увлажнении местном разрушении или загрязнении изоляции;
– добротность (величина обратная фактору потерь) измерение которой наиболее рационально при контроле наличия межвитковых замыканий ухудшения изоляционных свойств обмоток;
– емкость также позволяет оценивать качество изоляции: степень увлажнения изоляции загрязнение местное разрушение и ухудшение характеристик масла;
– индуктивность измеряется для контроля состояния катушек электрических аппаратов выявления межвитковых замыканий и обрывов;
– сопротивление (активное) катушек (обмоток) контролируется на соответствие заводским нормам и требованиям Правил ремонта и ТО электрических аппаратов;
– в автоматизированном режиме осуществлять поиск межвитковых замыканий в обмотке якоря.
«Доктор-060М»предназначен для контроля параметров и выявления дефектов изоляционных конструкций различного электрооборудования подвижного состава. Может использоваться как в составе комплекса диагностического оборудования серии «Доктор-060» так и в качестве самостоятельного измерительного устройства.
Рисунок 6.1 – Доктор-060М
«Доктор-060Е»предназначен для диагностирования электрических цепей подвижного состава при проведении периодических обслуживания а также по выходу локомотива из обслуживания.
«Доктор-060ПГ»предназначен для контроля технических характеристик токоприемников электроподвижного состава в цехах по его ремонту вне контактной сети. Позволяет выполнять измерения и контроль параметров токоприемников производить идентификацию локомотива на котором они установлены и идентификацию работника производящего измерения.
Рисунок 6.2 – Доктор-060ПГ
«Доктор-060АТ» позволяет выполнять измерения и контроль параметров автотормозного оборудования производить идентификацию локомотива и идентификацию персонала производящего измерения.
Рисунок 6.3 – Доктор-060АТ
Рабочее место мастера«Доктор-060ММ»предназначено для:
– сбора обработки и хранения данных полученных от приборов серии
«Доктор-060»в результате выполнения операций диагностики;
– управления процессом контроля и диагностики;
– передачи нормированных значений диагностируемых параметров на приборы серии «Доктор-060»;
– самодиагностики системы;
– визуального отображения информации о ходе процесса диагностики на дисплее;
– формирования протоколов испытаний с возможностью вывода на печать;
– передачи данных в общую базу для создания электронного паспорта локомотива.
Охлаждение ТЭД. Важный показатель для надежной работы ТЭД – напор охлаждающего воздуха. Необходимо контролировать статический напор воздуха в системе охлаждения тяговых электродвигателей в условиях локомотивного депо и ремонтных заводов. Прибор «ОКО-Д» позволяет дополнительно контролировать дифференциальное давление воздуха измерять температуру.
Переносные системы контроля вибрациименее распространены чем стационарные однако их применение также может быть полезным. Системы могут быть полезны для определения мест разбалансировки ослабления креплений потери соосности и отказа подшипников.
Силовые и низковольтные цепи. Кроме проверки отдельных аппаратов и узлов при обслуживании подвижного состава необходима проверка цепей управления в целом. Для этого используются приборы проверки секвенции. Например система «ОКО-Е» позволяет проверить секвенцию силовых и низковольтных цепей локомотивов электрических параметров машин и аппаратов в т.ч. переходное сопротивление коммутационных аппаратов. Встроенная база данных позволяет произвести идентификацию исполнителя качественную оценку процесса диагностирования и автоматическую загрузку данных по беспроводной связи на сервер рабочего места мастера для формирования электронного паспорта локомотива.
Переносные системы диагностирования также используются для измерения конечного нажатия контакторов контроля параметров полупроводниковых силовых приборов (диодов тиристоров и др.) контроль электромагнитных контакторов диагностирование пневмоприводов диагностирования реле и резисторов и многого другого.
В последнее время всё большую популярность набираюттепловизоры. Любая неисправность как правило приводит к нарушению (увеличению и или уменьшению) теплообмена. Плохой контакт или не затянутое болтовое соединение приводит к повышению температуры в зоне контакта неработающий электронный узел – к понижению температуры загрязненность холодильных камер – к перераспределению температуры в системе охлаждения дизеля. Увеличивается нагрев и при наличие дефекта в механических передачах подшипниках и др. Всё это можно наглядно увидеть с помощью тепловизора. Тепловизор идеально подходит для технического обслуживания электроустановок электромеханического оборудования контрольно-измерительных приборов систем обогрева вентиляции и кондиционирования воздуха.
2 Расчет расхода электрической энергии
Произведем расчет потребляемой электроэнергии в год на ТО-2 для расчета
возьмем комплексную систему диагностики оборудования «Доктор-060» в нее входит пять переносных приборов описанных ранее и рабочее место мастера. Большинство приборов приходят в действие за счет аккумуляторных батарей. В данном случае будет учитываться мощность зарядного устройства и время между зарядками аккумуляторов. Потребление персонального компьютера мастера принимаем 100 Вт·ч.
Величину технологических затрат электрической энергии на ремонт ТО-2 определяют как
kз коэффициент загрузки оборудования по мощности;
kс коэффициент загрузки оборудования по времени.
Таблица 6.1 – Определение технологического расхода электрической энергии потребляемой АСТД на ремонт ТО-2
Коэффициент загрузки по мощности
загрузки по времени х10-4
Э = (308410-41989) + (3081510-41989) +
+ (508510-41989) + (5008310-41989) +
+ (100082510-41989) + (308410-41989) = 45238 Вт.
Затраты на потребляемые энергоресурсы сведены в таблицу 6.2.
Таблица 6.2–Затраты на питание АСТД для обслуживания электровозов серии БКГ
Расход на единицу секции
Общая стоимость энергоресурса бел. руб.
По итогам расчета затраты на работу АСТД составили 702 р.
5 экономика.docx
1Капитальные вложения
Экономическое обоснование необходимо проводить для наиболее энергоэффективных вариантов освещения. В данном случае в качестве наиболее рациональных вариантов общего освещения цеха ТО-2 принимаются:
– 44 светильника LED с лампами ДКУ 120 Вт;
–40 светильников LED с лампами FG 200 Вт.
Стоимость осветительных приборов
где Цоб –цена светильника с лампами и пускорегулирующей аппаратурой бел. руб.
Стоимость строительно-монтажных работ согласно [7]
Ошибка! Закладка не определена..(5.2)
Стоимость проекта на освещение согласно [7]
Стоимость пуско-наладочных работ согласно [7]
Суммарные капитальные вложения
Капитальные вложения могут быть вложены в проект по частям в течение нескольких лет поэтому в обозначении этой величины имеется индекс t (год вложения инвестиций).
Стоимость осветительных приборов определяется по формуле (5.1):
Стоимость строительно-монтажных работ – согласно формуле (5.2):
Стоимость проекта на освещение – согласно формуле (5.3):
Стоимость пуско-наладочных работ – согласно формуле (5.4):
Суммарные капитальные вложения – согласно формуле (5.5):
Принимаем что инвестиции в проект (капитальные затраты) вкладываются единовременно.
2Затраты на электроэнергию
Годовой расход электроэнергии осветительным оборудованием W кВт·чгод
кc–коэффициент спроса осветительной нагрузки;
гдекcтехн–коэффициент спроса осветительной нагрузки обусловленный
технологическим процессом осуществляемым в рассматриваемом
кcтехн–коэффициент учитывающий дополнительное число часов работы осветительного оборудования в пасмурное время дня; кдоп=108
кау–коэффициент учитывающий автоматизацию управления освещением.
Годовые затраты финансовых средств на потребляемую электроэнергию
где сээ – тариф электроэнергии ркВт·ч.
Годовой расход электроэнергии осветительным оборудованием W рассчитывается в соответствии с формулой (5.6):
Расчет ведется при времени использования максимума осветительной нагрузки Тmax=4800ч. и коэффициенте спроса осветительной нагрузки кс = 092. Результаты расчета сводятся в таблицу 5.1.
Годовые затраты финансовых средств на потребляемую электроэнергию находим по формуле (5.8):
Результаты расчета приведены в таблице 5.1.
Таблица 5.1 – Капитальные вложения и затраты на электроэнергию
Капитальные затраты Кt бел. руб.
Расход электроэнергии W кВтчгод
Тариф электроэнергии Сээ
Оплата за электроэнергию Сээ
пусконаладочных работ
3Затраты на замену ламп
Процесс выхода из строя ламп в течение срока их службы можно условно аппроксимировать зависимостью представленной на рисунке 5.1. Принимаем допущение что в период эксплуатации меньше среднего срока службы ламп из них перегорают 50 % установленных ламп причем равномерно. После среднего срока службы ламп одновременно перегорают оставшиеся 50 % ламп.
Рисунок 5.1 – График выхода из строя ламп
Согласно аппроксимирующей зависимости рисунок 5.1 стоимость замены ламп в t-том году определяется по выражениям:
где t–номер года по порядку (целое число);
Цл–цена лампы бел. руб.
Как указывалось в [6] средний срок службы лампы в значительной степени зависит от напряжения в осветительной электросети поэтому справочный срок службы 0 [6] должен быть приведен к фактическому по преобразованной формуле
Регулирующий эффект срока службы источника света по напряжению kUпринимается по [6].
Средний срок службы лампы в значительной степени зависит от напряжения в осветительной электросети. В соответствии с рисунком 5.2 фактическое значение напряжения превышает номинальное в среднем на 7%.
Рисунок 5.2–График отклонения от номинального значения
напряжения в цеховых электросетях 04 кВ
Справочный срок службы 0 приводится к фактическому по формуле(5.12):
Стоимость замены ламп в t-том году определяется по формулам (5.9) – (5.10):
4Амортизация оборудования
Отчисления на амортизацию оборудования определяются по формуле:
срок полезного использования светильников лет; рекомендуется принимать от 7 до 15 лет
Необходимым условием окупаемости нового оборудования является снижение текущих (эксплуатационных) затрат. Перечень статей этих затрат в реальности очень большой и учет всего перечня при обосновании мероприятий по замене осветительных установок нецелесообразен. В данном случае предлагается сравнивать изменение только затрат на электроэнергию и замену ламп а также включить в текущие затраты амортизацию. Последнее допущение сделано в нарушение классического подхода к определению затрат (не в соответствии с нормативным документом [8]) но позволяет значительно упростить расчеты для специалистов-энергетиков не имеющих экономического образования. При названных выше допущениях текущие затраты в t-том году на искусственное освещение определяются по формуле
Текущие затраты в t-том году на искусственное освещение определяются по формуле
6Ликвидационная стоимость
Под ликвидационной стоимостью понимают разность между доходом полученным от реализации ликвидируемого объекта (например заменяемого энергооборудования) и затратами на его ликвидацию. Ликвидационная стоимость применяется только к осветительному и другому оборудованию которое входит в состав основных средств предприятия.
Расчет ликвидационной стоимости производится для существующего осветительного оборудования по формуле
где–стоимость существующего освещения бел. руб.;
aр–норма амортизации %;
Тэкспл–фактический срок эксплуатации существующих светильников лет;
ликв–затраты на ликвидацию существующего освещения бел. руб.
Стоимость демонтажа (ликвидации) осветительного оборудования можно принять на уровне 20 % от стоимости существующего освещения
Ошибка! Закладка не определена..(5.16)
Расчет ликвидационной стоимости производится для существующего осветительного оборудования по формулам (5.14) – (5.16):
Результаты расчета приведены в таблице 5.2.
Таблица 5.2 – Затраты на содержание ламп
Средний срок службы
замены ламп Cзлt бел. руб.
Амортизация А бел. руб.
Доля амортизационных отчислений aр
Затраты на ликвидацию освещения
в год окончания среднего срока службы
7Чистый дисконтированный доход
Под чистым дисконтированным доходом ЧДД понимают прибыль полученную за весь срок реализации проекта и дисконтированную (приведенную) к началу расчетного периода (t = 0).
ЧДД при замене осветительного оборудования на более эффективное может быть определен по формуле
где t – расчетный год;
Е – норма дисконтирования (дисконта).
Верхний индекс 1 относится к статьям текущих затрат существующего варианта освещения а 2 – планируемого варианта.
Под нормой дисконта Е понимают минимальную норму прибыли ниже которой инвестору вложение капитала невыгодно. Обычно норма дисконта Е принимается равной ставке рефинансирования Национального банка.
ЧДД при замене осветительного прибора ДКУ-36 на ДКУ-120 за первый год определяется по формуле (6.25):
Результаты расчета ЧДД удобно представлять в виде таблиц 5.3 (лампы
FG-100 200 Вт) 5.4 (лампы ДКУ-120 120 Вт) и графика изображенного на
рисунке 3. Точка пересечения графика ЧДД с осью «Расчетный год t» соответствует динамическому сроку окупаемости мероприятия.
Таблица 5.3 – Чисто дисконтированный доход ламп FG-100
Капи-тальные вложе-ния Кt бел. руб.
Прибыль с учетом ликвидационной стоимости
Коэффицент приведения
Экономический эффект за t-тый год приведенный к расчетному году
Таблица 5.4 – Чисто дисконтированный доход ламп ДКУ-120
Прибыль с учетом ликвидационной стоимости
Коэффициент приведения
Рисунок 5.3 – Результаты расчета ЧДД
Наиболее рациональным вариантом замены светильников в участке ТО-2 локомотивного депо является применение светодиодных ламп ДКУ с мощностью
0 Вт. При такой замене будет достигнута экономия электроэнергии 7 тыс. кВт·ч в год и окупаемость вложенных инвестиций составит около двух лет.
8 от.docx
1 Анализ опасных и вредных производственных факторов в
технологическом процессе отделения. Оценка
профессиональных рисков
Одной из основных причин производственного травматизма являются недостатки в организации производства работ при ремонте ЭПС.
Установление опасных и вредных производственных факторов в технологическом процессе участка приводится в пояснительной записке в виде таблицы 8.1.
Опасные и вредные производственные факторы отражены в таблице в виде знака « + » а безвредные в виде знака « – » отдельно по каждой выполняемой операции технологического процесса осмотра колёсных пар
Таблица 8.1 –Опасные и вредные производственные факторы
Технологический процесс
Движущиеся машины и механизмы
Отклонения от нормированных значений микроклимата
Повышенное значение электрического тока под который может попасть человек
Отклонение от нормы значений освещенности
Расположение рабочего места на высоте
запыленности воздуха
загазованности воздуха
крышевого оборудования
механического оборудования
Осмотр электрического оюорудования
Для разработки конкретных мероприятий по улучшению условий труда и обеспечению безопасности необходимо выполнить анализ опасных и вредных производственных факторов которые могут воздействовать на работников при производстве ТО.
Опасные и вредные производственные факторы подразделяются по природе действия на физические химические биологические и психофизиологические.
2Меры по управлению рисками
Мероприятия по управлению рисками подразделяются на технические и организационные:
а) технические мероприятия по управлению рисками направлены на снижение рисков и повышение безопасности производства в том числе:
использование безопасных материалов и технологий при эксплуатации;
использование эффективных систем контроля за технологическими процессами;
предупреждение доступа работников к источнику опасности;
соблюдение правил эксплуатации технических средств и оборудования;
б) организационные мероприятия разрабатываются для устранения и ликвидации опасного или вредного производственного фактора и включают в себя:
видоизменение процессов или порядка работы с высокой степенью риска;
уменьшение рабочих мест с опасными и вредными производственными факторами;
своевременное обучение и переподготовку работников занятых на работах с опасными и вредными производственными факторами;
выдачу современных индивидуальных средств защиты для постоянного пользования а также их своевременную замену.
Мероприятия по ограничению масштабов возможных последствий аварий включают:
разработку планов по ликвидации (локализации) возможных аварий;
применение различных технических средств ограничивающих действие поражающих факторов (системы пожаротушения аварийная вентиляция заградительные устройства предотвращающие распространение огня и взрывной волны и т.п.);
создание необходимых резервов материальных и финансовых ресурсов для ликвидации последствий чрезвычайных ситуаций.
3Разработка мероприятий по устранению опасных и вредных
производственных факторов
Для создания нормальных и безопасных условий труда при техниче-
ском обслуживании электровозов в данном разделе дипломного проекта разработаны мероприятия которые соответствуют действующим на Белорусской железной дороге нормативным правовым и нормативно-техническим актам системе стандартов безопасности труда санитарным правилам и нормам Республики Беларусь.
Требования к производственным зданиям и помещениям:
производственные здания и сооружения должны соответствовать требованиям строительных норм и правил санитарных правил и норм СанПин № 24 от 04.04.2014 «Основные санитарные правила и нормы при проектировании строительстве реконструкции и вводе объектов в эксплуатацию» утвержденных постановлением Совета Министров Республики Беларусь от 28 октября 2011 г. №1446 других нормативноправовых актов технических нормативных правовых актов определяющих требования охраны труда.
оснащение зданий сооружений помещений и других объектов локомотивного хозяйства мест производства работ средствами обнаружения и тушения пожаров пути эвакуации должны соответствовать специфическим требованиям утверждёнными постановлением министра Республики Беларусь 20.11.2019 «Специфические требования по обеспечению пожарной безопасности для объектов на железнодорожном транспорте» и нормам оснащения объектов и подвижного состава первичными средствами пожаротушения.
подходы к зданиям и сооружениям должны располагаться в безопасных местах с минимальным числом пересечений железнодорожных путей.
в производственных и служебных помещениях должны быть обеспечены безопасные условия труда в соответствии с действующими правилами и нормами. Окраска помещений и оборудования должна соответствовать рекомендациям по оптимальному цветовому оформлению производственных помещений с учетом характера выполняемой работы. Материалы применяемые для внутренней отделки помещений должны иметь гигиеническую регистрацию и сертификацию согласно установленному порядку.
проходы внутри цехов и отделений должны иметь ширину не менее 1 м. Ширина проездов для авто- и электрокаров вдоль цеха должна быть 18 м а вдоль торцовых стен 3м. Границы проходов и проездов должны быть размечены белыми линиями. Не допускается загромождать проходы и проезды.
производственные помещения должны соответствовать требованиями установленных санитарных норм правилам пожарной безопасности и содержаться в исправном состоянии и чистоте. Для них должен быть установлен порядок уборки и очистки от пыли и загрязнений оконных проемов и фонарей.
производственные участки на которых возможно возникновение и
воздействие на работников вредных производственных факторов должны быть изолированы от других производственных участков.
полы расположенные в производственных помещениях всегда
должны соответствовать выполняемым в них технологическим процессам иметь твердое ровное покрытие обеспечивающее установленные нагрузки и безопасную работу машин и механизмов.Они должныбыть не скользкими водонепроницаемыми стойкими против износа и образования неровностей и обеспечивать удобную чистку.
Рабочее место слесарей должно содержаться в чистоте и иметь необходимые устройства для размещения инструмента ремонтируемых деталей и приборов. Необходимо чтобы верстаки имели устойчивое (жесткое) закрепление на полу а их высота соответствовала размеру который бы обеспечивал нормальное положение корпуса работающего. Тиски на верстаке укрепляются так чтобы их губки располагались на высоте локтя слесаря.
Рабочее место верстак и станки размещают в цехе так чтобы в дневное время суток обеспечивалась нормальная их освещенность. Искусственное освещение в темное время суток в значительной степени зависит от выбора типа ламп и способа их подвески у рабочего места. Обычно устраиваются навесные лампы или стенные на раздвижных кронштейнах которые дают возможность удалять или приближать источник света к месту ремонта детали.
Личный инструмент слесаря должен содержаться в исправном состоянии. Нельзя применять при работе инструмент ударная поверхность которого расклепана имеет разорванные кромки металла так как при работе с таким инструментом от него могут отлетать куски металла. Молотки кувалды зубила крейцмейсели и бородки должны быть изготовлены по установленным чертежами и хорошо заправлены. Режущие кромки зубила и крейцмейселя необходимо делать прямыми а ударную часть – оттянутой на конус; при этом стержни их не должны иметь изгибов и искривлений. Слесарные молотки и кувалды изготавливаются с незначительной выпуклостью ударной поверхности и надежно укрепляются на ручках стальным клином.
Ручки должны иметь гладкую поверхность и быть овальной формы причем большая ось поперечного сечения ручки должна располагаться в плоскости размаха (при ударе молотком).
Гаечные ключи должны иметь размеры установленные ГОСТом. Эти размеры необходимо строго выдерживать так как большинство случаев травматизма вызывается срывом ключей с гайки при закреплении болтов и шпилек из-за увеличенного размера зева ключа вследствие его разборки.
Рабочие места с точки зрения эргономики должны удовлетворять следующим условиям:
иметь достаточное рабочее пространство для работающих позволяющее осуществлять все необходимые движения и перемещения при эксплуатации и техническом обслуживании оборудования;
оптимально размещаться в производственных помещениях;
иметь безопасные и достаточные проходы для работающих людей;
уровень акустического шума и вибрации создаваемых оборудованием рабочего места или другими источниками шума не должны превышать допустимой величины;
должны быть предусмотрены необходимые средства защиты работающих от действий опасных и вредных производственных факторов и др.
Предлагаю разработать и произвести расчет вытяжной вентиляции от моечной машины которая обеспечит наилучшие санитарно-гигиенические условия а также необходимую взрывопожаробезопасность.
4Требования безопасности при техническом обслуживании
К работе допускаются лица не моложе 18-ти лет прошедшие медицинское освидетельствование профессиональное обучение и проверку знаний устройства соответствующего оборудования и правил его эксплуатации в том числе безопасных приемов работы инструктаж по охране труда на рабочем месте и получившие допуск к работе. Повторный инструктаж на рабочем месте должен проводиться не реже чем раз в квартал.
Работник депо должен соблюдать правила внутреннего распорядка предусмотренные уставом для работников железнодорожного транспорта. Не курить в производственных и складских помещениях. Курение допускается лишь в специально отведенных для этого местах. Не употреблять алкоголь и наркотические средства. Это резко увеличивает опасность травматизма. Работать только на том оборудовании которое было изучено и на котором есть допуск к самостоятельной работе. Выполнять только ту работу которая поручена администрацией цеха мастером участка. Быть внимательным во время работы не отвлекаться и не отвлекать других от работы. Не работать без полагающихся защитных ограждений предохранительных устройств и приспособлений если они отсутствуют требовать скорейшей их установки. Не допускать на свое рабочее место лиц не имеющих отношения к выполняемой работе. Без разрешения мастера не доверять свое рабочее место другому рабочему. Содержать рабочее место в чистоте и в течение всего рабочего дня не загромождать его посторонними предметами. Не загромождать установленных проездов и проходов как общих так и у обслуживаемого оборудования.
На территории депо и цеха необходимо соблюдать следующие правила:
быть внимательным к сигналам подаваемых крановщиками грузоподъемных кранов и водителями транспорта;
не проходить в местах не предназначенных для прохода не перебегать путь перед движущимся транспортом;
не находиться и не проходить под поднятым грузом;
не открывать электрошкафы не прикасаться к токоведущим частям электрооборудования клеммам и электропроводам арматуре общего освещения;
не исправлять самостоятельно вышедшее из строя электрооборудование в случае необходимости обратится к электромонтеру не включать и не останавливать (кроме аварийных случаев) оборудование работа на котором поручена другому рабочему;
не прикасаться к находящимся в движении механизмам и не огражденным частям машин;
не чистить одежду бензином и другими легковоспламеняющимися жидкостями – это пожароопасно;
при возникновении пожара немедленно приступить к его тушению имеющимися местными средствами и сообщить администрации;
заметив нарушение требований инструкции техники безопасности другими работниками или какую-либо опасность для окружающих необходимо предупредить их в необходимости соблюдения требований гарантирующих безопасность работ и немедленно сообщить мастеру.
Производственное оборудование машины и механизмы должны соответствовать требованиям санитарных правил и норм СанПиН № 85 от 28.07.2016 «Требования и условия труда работающих и содержание производственныхобъектов».
Каждая машина станок агрегат стенд должны иметь технический паспорт и инвентарный номер. Нестандартное оборудование должно быть обеспечено принципиальными схемами и технической документацией.
Электрооборудование а также оборудование и механизмы которые могут оказаться под электрическим напряжением должны иметь защитное заземление (зануление) в соответствии с требованиями эксплуатационных документов организаций – изготовителей электрооборудования.
Устройство содержание и эксплуатация электрических установок электроинструмента и переносных электрических светильников должны соответствовать ГОСТ 12.1.019-2009 «ССБТ. Электробезопасность. Общие требования и номенклатура видов защиты».
Внешние электрические сети питания переносных диагностических приборов напряжением более 42 В переменного тока или 110 В постоянного тока должны быть оборудованы защитным заземлением (занулением или устройством защитного отключения).
Перед началом и во время испытаний на станции (площадке) не должны находиться посторонние лица.
Сборка схем на испытательных стендах должна производиться при полном снятии напряжения. Питающие кабели для испытания электрических машин и аппаратов высоким напряжением должны быть надежно подсоединены к зажимам а корпуса машин и аппаратов заземлены.
Подача и снятие напряжения должны осуществляться контакторами с механическим или электромагнитным приводом или рубильником имеющим защитный кожух.
Пересоединение на зажимах испытываемых аппаратов должно производиться после отключения всех источников питания и полной остановки вращающихся деталей.
При возникновении аварийных ситуаций немедленно отключить
испытательные приборы стенды от сети и оказать первую медицинскую помощь:
устранить воздействие на организм повреждающих факторов угрожающих здоровью и жизни пострадавшего (освободить от действия электрического тока) оценить состояние пострадавшего принять меры по его дальнейшей безопасности;
определить характер и тяжесть травм представляющих наибольшую угрозу для жизни пострадавшего и последовательность мероприятий по его спасению;
выполнить необходимые мероприятия по спасению пострадавшего в порядке срочности (восстановить проходимость дыхательных путей провести искусственное дыхание наружный массаж сердца остановить кровотечение и т.д.)
поддержать основные жизненные функции пострадавшего до прибытия медицинского работника.
Необходимо помнить что обслуживаемое рабочее место является источником повышенной опасности причиной механических травм в том числе с тяжелым исходом.
Структурная схема.dwg

Схема структурная технологических потоков текущего ремонта ТР-1 тепловоза М62
Дизель-вспомогательное оборудование
Механическое оборудование
Электрическое оборудование
Реостатные испытания
Аккумуляторные батареи
Топливная аппаратура
Автотормозное оборудование
выполняемые на ремонтных позициях участка ТО-2
выполняемые в специализированных отделениях
выполняемые комплексной бригадой
Работы выполняемые на ремонтных позициях участка ТР-1
Работы выполняемые в специализированных отделениях
Работы выполняемые комплексной бригадой
Контроль параметров работы оборудования электровоза
Крышевое оборудование
радиосвязь и дополнительные устройства безопасности
Подкузовное оборудование
Участок ТО-2 электровозов серии БКГ в локомотивном депо Гомель
Схема структурная технического обслуживания ТО-2 электровозов серии БКГ
выход электровоза из ТО-2
Схема структурная технического обслуживания ТО-2 электровозов серии БКГ
ТО-2.dwg

Планы пункта технического осмотра тепловозов и электромашинный цех
Планировка технического осмотра локомотивов ТО-2
Кладовая инструментов и запасных частей
Гараж и ремонтное отделение
Разработка технологического процесса и конструкции
специального оборудования для ремонта ЭПС
рифленое железо по прогонам
Шкаф для инструментов
Стеллаж для тормозных колодок
Стеллаж с токоприемниками
Устройство для подачи масла в МОПы
Участок ТО-2 электровозов серии БКГ в локомотивном депо Гомель
План и поперечный разрез участка ТО-2 локомотивного депо Гомель
Инструментальные ящики
Площадка для осмотра
Расположение участка ТО-2 на плане
локомотивного депо Гомель (1:1000)
Устройство для заправки гребнесмазывателей
Доктор-100М «Прибор контроля качества изоляции»
Доктор-100ПГ «Система контроля и
диагностики токоприемников»
ПЗУ «Передвижное зарядное устройство»
Освещение участка ТО-2 локомотивного депо Гомель после модернизации
Температура эксплуатации
Диапазон напряжений питания
Цветовая температура
Светильник светодиодный
формы отличной от линейной
Условные обозначения:
Таблица 6.1 - Характеристики светильника
БКГ1 график22222.dwg

Электродвигатель от компрессора отсоединить
Шестерню отсоединить
Работу электродвигателя
осевой разбег якоря или ротора
вибрацию на холостом ходу проверить
Маркировку на подшипниковых щитах
при необходимости восстановить
Электродвигатель разобрать
крышки подшипников очистить
посадочные поверхности зачистить
Активное сопротивление катушек замерить
Катушки на межвитковое замыкание проверить
Обмотки статора осмотреть
крепления клиньев проверить
наружную изоляцию обмоток восстановить
наконечники зачистить
изоляцию наружную восстановить
покрасить с отсоединением и подсоединением выводов
Трещины на остове или статоре
крышках подшипников разделать
заварить (работа со сварщиком)
крышки подшипников покрасить
Якорь и ротор продуть
Якорь или ротор осмотреть
крепление деталей проверить
резьбу вала проверить
к дефектоскопии подготовить
Кольца подшипников с вала якоря или ротора спрессовать
Сопротивление изоляции
активное сопротивление якоря или ротора замерить
на межвитковое замыкание и пайку петушков проверить
Вентиляторы очистить
трещины в корпусе вентилятора агрегата разделать
Кольца подшипников подобрать
Электродвигатель собрать
смазку в подшипники заложить
торцовое биение коллектора
зазоры между полюсами и якорем замерить
Электродвигатель продуть
Работу электродвигателя на холостом ходу после ремонта проверить
Шестерню на вал якоря напрессовать
Электродвигатель с компрессором соединить
Электродвигатель снаружи покрасить
кафедра "Локомотивы"
График ремонта продукции и график загрузки рабочих
Проектирование электромашинного отделения локомотивного депо
Проектирование механического отделения локомотивного депо
Переформирование буксового поводка
Поводок роликовой буксы снять
Колесно-моторный блок разобрать
Осмотреть колесную пару
Отремонтировать колесную пару
Осмотреть зубчатое колесо
Отремонтировать зубчатую передачу
Кожух зубчатой передачи отремонтировать
Колесно-моторный блок собрать
Колесно-моторный блок отрегулировать
Колесно-моторный блок обкатать
Проектирование электроаппаратного отделения локомотивного депо
Демонтировать токоприемники с электровоза
Разобрать токоприемники
Контролировать визуально шунты на обрыв проволок
Контролировать подшипники скольжения на наличие повреждений. Заменить подшипники скольжения. Произвести смазку подшипников
Контролировать стальные канаты на отсутствие обрыва. Произвести испытания на растяжение стальных канатов. Смазка стальных канатов
Контролировать визуально целостность элементов токоприемника. Заменить поврежденные элементы токоприемников
собрать каретки токоприемников
Полоза токоприемника заменить на новые
Контролировать герметичность воздушной системы токоприемника
Осмотреть амортизаторы
проверить плавности хода штоков амортизаторов и отсутствие утечки масла. При необходимости амортизаторы заменить
Собрать токоприемники. Произвести смазку шарнирных соединений
Монтировать токоприемники на электровоз
Контролировать крепление токоприемников к изоляторам
Произвести техническую диагностику параметров токоприемников (величину нажатия
время подъема и опускания
соосность элементов) путем проведения динамических испытаний. Отрегулировать параметры токоприемников
Проектирование участка СР-1 локомотивного депо
Чердачное помещение осмотреть
потолочное оборудование осмотреть
предохранительные ремни
цепочки отремонтировать
неисправности устранить
Листы фанеры и пластика дефектные
петли каналов отремонтировать
форточки разъеденить
открыть для ремонта и промывки стёкол
межрамных поверхностей
их оборудо- вание осмотреть
неисправности и неплот- ности рам
работу форточек отрегулировать
Рамы форточки поле промывки стекoл закрыть
обшивку стен осмотреть
дефектные листы пластика
крючки вешалочные осмотреть
Сидения подлокотники
их арматуру в кабине машиниста снять
их оборудование осмотреть
резину и уплотнения заменить
трущиеся части смазать
зазор между порогом и дверью отрегулировать
Трещины дверей заварить (работа со сварщиком)
бобышки деревянные на крыше при необходимости сменить
неисправно- сти устранить
для подъема на крышу кузова
трещины заварить (работа со сварщиком)
Вмятины на стенках кузова и крыши выправить
пробоины заварить (работа со сварщиком)
Полы подвагонную обшивку осмотреть
изношенные места линолеума
угольники армированные выправить
Крышки люков пола отремонтировать
по месту постановки подогнать
Рисунок А2- График загрузки рабочих
Рисунок А1- График ремонта расчетной единицы
Главный выключатель снять и поставить
Главный выключатель разобрать
Главный выключатель резистор нелинейный ВНКС-25 разобрать
Главный выключатель провести гидравлические испытания воздушного резервуара
Проверить состояние электрического оборудования
токоприёмник на подъем и опускание.
Проверить состояние измерительных приборов.
Состояние и крепление тормозного и пневматического оборудования
электропневматического тормоза
песочного оборудования
Работу и нагрев подшипниковых узлов в ходовой части
доступных для контроля местах проверить.
Состояние и крепление рам тележек колесно-моторных блоков и тяговых редукторов.
Состояние и крепление колесной пары и буксового узла
тормозной рычажной передачи и тормозные колодки.
Состояние и крепление поручней
межтележечного соединения
Состояние и крепление рамы кузова
работу автосцепок и ручных тормозов.
Состояние и крепление трубы санузла
песочного оборудования проверить
Отстой (конденсат) из корпусов моторно-осевых подшипников слить
механическое оборудование при необходимости смазать
исправность и действие гребнесмазывателей проверить.
Состояние и крепление кузова
его оборудования проверить
Состояние тяговых электродвигателей
проверить: коллектор
заземляющие устройста
сопротивление изоляции.
Состояние вспомогательных машин: крепление машин к основаниям
соединительных муфт моторвентиляторов и вспомогательного компрессора
редукторов моторкомпрессоров
подводящих проводов.
Состояние и крепление токоприёмника
пневматического привода
велитовых разрядников
ограничители перенапряжения
антенны радиосвязи осмотреть.
Состояние и крепление выключателей
разъединителей и заземлителей
герметичность шлангов
пульты управления продуть
Четкость и последовательность срабатывания аппаратов
отсутствие утечек воздуха проверить
сопротивление изоляции цепей замерить.
Состояние и крепление электрических аппаратов
вспомогательного оборудования
прилегание и замыкание контактов
работу подвижных частей аппаратов
исправность электромагнитных защелок и блокировок безопасности
Проверить крепление электропневматического вентиля
работоспособность электрической схемы гребнесмазывателей.
Состояние и крепление тягового трансформатора
Аккумуляторную батарею осмотреть
плотность электролита замерить. Общее напряжение аккумуляторно батареи без нагрузки и под нагрузкой проверить.
Состояние и крепление трубопроводов
работу тормозного и пневматического оборудования
плотность тормозной магистрали
величину выхода штоков тормозных цилиндров
чувствительность уравнительного поршня к торможению и отпуску.
автоматическая локомотивная сигнализация
контрольно-измерительные приборы.
Участок ТО-2 электровозов серии БКГ в локомотивном депо Гомель
Схема структурная технического обслуживания ТО-2 электровозов серии БКГ
График ремонта ТО-2 электровоза БКГ1 и график загрузки рабочих
Отстой из корпусов моторно-осевых подшипников слить
График ремонта ТО-2 электровоза БКГ2 и график загрузки рабочих
Линейный график ремонта и загрузки рабочих участка ТО-2 электровоза БКГ-1
Линейный график ремонта и загрузки рабочих участка ТО-2 электровоза БКГ-2
Перечень работ ТО-2 электровоза БКГ-1
токоприёмник на подъем и опускание
Проверить состояние измерительных приборов
Проверить состояние и крепление тормозного и пневматического оборудования
Проверить работу КЛУБ
Проверить работу и нагрев подшипниковых узлов в ходовой части
доступных для контроля местах проверить
Проверить состояние и крепление рам тележек колесно-моторных блоков и тяговых редукторов
Проверить состояние и крепление колесной пары и буксового узла
тормозной рычажной передачи и тормозные колодки
Проверить состояние и крепление поручней
Проверить состояние и крепление рамы кузова
работу автосцепок и ручных тормозов
исправность и действие гребнесмазывателей проверить
Проверить состояние и крепление кузова
Проверить состояние тяговых электродвигателей
сопротивление изоляции
Проверить состояние вспомогательных машин: крепление машин к основаниям
Проверить состояние и крепление токоприёмника
антенны радиосвязи осмотреть
Проверить состояние и крепление выключателей
Проверить четкость и последовательность срабатывания аппаратов
сопротивление изоляции цепей замерить
Проверить состояние и крепление электрических аппаратов
работоспособность электрической схемы гребнесмазывателей
Проверить состояние и крепление тягового трансформатора
Проверить аккумуляторную батарею осмотреть
плотность электролита замерить. Общее напряжение аккумуляторно батареи без нагрузки и под нагрузкой проверить
Проверить состояние и крепление трубопроводов
чувствительность уравнительного поршня к торможению и отпуску
контрольно-измерительные приборы
График ремонта ТО-2 электровоза БКГ-1 и график загрузки рабочих
Перечень работ ТО-2 электровза БКГ-1
Перечень работ ТО-2 электровоза БКГ-2
токоприемник на подъем и опускание
проверить: выводные кабели
Проверить состояние и крепление токоприемника
Линейный график обслуживания и загрузки рабочих участка ТО-2 электровоза БКГ-2
сопротивление изоляции
Линейный график обслуживания и загрузки рабочих участка ТО-2 электровоза БКГ-1
Расчет себестоимости технического обслуживания электровозов серии БКГ
Себестоимость ремонта одного обслуживания
=1484 бел.рубпреобразователь
Расчет себестоимости технического обслуживания электровозов серии БКГ
Расходы на обслуживание
Основная заработная плата
Добавки и надбавки компенсационного характера
Дополнительная заработная плата
Отчисления на социальные нужды
Материалы и покупки изделия
Полуфабрикаты собственного изготовления
Энергоресурсы на технологические цели
Содержание и эксплуатация оборудования
Амортизация оборудования
Накладные и общехозяйственные расходы
Для электровоза БКГ-1
Для электровоза БКГ-2
=868 бел.рубпреобразователь
Круговая диаграмма себестоимости ТО-2 электровоза БКГ-1
Круговая диаграмма себестоимости ТО-2 электровоза БКГ-2
Измеряемые параметры
Погрешность измерения
Tread View (Великобритания)
высота и толщина гребня
Высота и толщина гребня
прокат на поверхности катания
Профиль и диаметр колеса
; для диаметра колеса ±0
ширина изнашиваемой части поверхности катания
- внешняя поверхность колеса; 2 - платформа; 3 - рельс; 4
- совокупность лучей; 8 - часть колесного центра; 9 - внешняя поверхность обода; 10 - поверхность катания; 11 - гребень; 12
- граничные траектории лучей; 14
- фотоприемники i3.54583
- модуль измерения проката и овальности; 2 - модуль определения дефектов колеса; 3 - модуль WIS для измерения профиля и диаметра колеса; 4 - датчик положения состава; 5 - помещение (бокс) для установки контрольно-измерительной аппаратуры; 6 - модуль автоматической идентификации подвижного состава; 7 - канал для прокладки кабелей и волоконно-оптических световодов
Комбинированный детектор: размещение датчиков контроля температуры греющихся букс
обода колеса и тормозных дисков
Структура себестоимости обслуживания ТО-2 электровозов серии БКГ
Технические характеристики систем бесконтактного оптического контроля параметров
=1697 бел.рубобслуживание
=990 бел.рубобслуживание
Круговая диаграмма общих расходов ТО-2 электровоза БКГ-1
Круговая диаграмма общих расходов ТО-2 электровоза БКГ-2
Схема измерения профиля колеса при помощи системы Argus
Анализ систем мониторинга состояния ходовых частей подвижного состава на железных дорогах
Комплексная система контроля колесных пар WISE
Освещение участка ТО-2 локомотивного депо Гомель после модернизации
Система WIS для контроля параметров колесных пар
Титульный лист.doc
«БЕЛОРУССКИЙ ГОСУДАРСТВЕННЫЙ УНИВЕРСИТЕТ ТРАНСПОРТА»
Кафедра «Локомотивы»
УЧАСТОК ТО-2 ЭЛКЕТРОВОЗОВ БКГ В ЛОКОМОТИВНОМ ДЕПО ГОМЕЛЬ
Пояснительная записка
Главный руководитель
Студент группы МЭ-51
Основной руководитель
Консультант по охране труда
Консультант по энерго-
Консультант по экономике
содержание.docx
1 Система технического обслуживания и ремонта электрического
подвижного состава 7
2 Структурная схема технологических потоков ТО-2 грузовых электровозов
ОРГАНИЗАЦИЯ РАБОТЫ УЧАСТКА ТО-2 ГРУЗОВЫХ ЭЛЕКТРОВОЗОВ
СЕРИИ БКГ .. .. . .16
1 Расчет фондов рабочего времени 16
2 Расчет программы ремонта грузового локомотива серии БКГ 17
3 Расчет основных параметров производственного процесса участка ТО-2 . .19
4 Расчет трудоёмкости производственной программы участка ТО-2 . 20
5 Расчет численности работников . 23
6 Разработка графика загрузки рабочих и линейного графика участка ТО-2 . 25
7 Подбор оборудования для участка ТО-2 . 28
8 Разработка плана и поперечного разреза участка ТО-2 . 30
9 Определение площади участка . ..31
РАСЧЕТ СЕБЕСТОИМОСТИ ОБСЛУЖИВАНИЯ НА УЧАСТКЕ .. . ..33
РАСЧЕТ СИСТЕМЫ ОСВЕЩЕНИЯ УЧАСТКА ТО-2 . . .. 38
1Необходимость внедрения энергоэффективных осветительных установок ..38
2Светотехнический расчет . ..38
3Светотехнический расчет общего освещения участка.. ..39
ЭКОНОМИЧЕСКОЕ ОБОСНОВАНИЕ РАЦИОНАЛЬНОГО ВАРИАНТА
1Капитальные вложения 44
2Затраты на электроэнергию . 45
3 Затраты на замену ламп ..46
4 Амортизация оборудования 48
5 Текущие затраты .48
6 Ликвидная стоимость . .48
7 Чистый дисконтированный доход . 49
ПЕРЕНОСНЫЕ ДИАГНОСТИЧЕСКИЕ УСТРОЙСТВА . . 52
1 Общее представление переносных диагностических устройств .. 52
2 Расчет расходы электрической энергии . .. 55
ТЕХНИЧЕСКАЯ ДИАГНОСТИКА СОСТОЯНИЯ ПОДВИЖНОГО
СОСТАВА И ПЕРСПЕКТИВЫ ЕЕ РАЗВИТИЯ .. ..57
ОХРАНА ТРУДА И ОКРУЖАЮЩЕЙ СРЕДЫ 67
1 Анализ опасных и вредных производственных факторов в технологическом
процессе отделения. Оценка профессиональных рисков. 67
2 Меры по управлению рисками . 68
3 Разработка мероприятий по устранению опасных и вредных производственных
4 Требования безопасности при техническом обслуживании подвижного
СПИСОК ИСПОЛЬЗОВАННЫХ ИСТОЧНИКОВ . 75
Бланк задания по ДП Воробьев МЭ-51.doc
«БЕЛОРУССКИЙ ГОСУДАРСТВЕННЫЙ УНИВЕРСИТЕТ ТРАНСПОРТА»
Факультет механический Кафедра «Локомотивы» у
специальность «Тяговый состав железнодорожного транспорта (электрический транспорт и метрополитен)»
по дипломному проекту (работе) студента
Воробьева Вячеслава Сергеевича.
(фамилия имя отчество)
Тема проекта (работы) Участок ТО-2 электровозов серии БКГ в локомотивном депо Гомель
Утверждена приказом по университету от « 23 » марта 2021г. № 249
Исходные данные к проекту (работе) по материалам локомотивного депо
Содержание расчётно-пояснительной записки (перечень подлежащих разработке вопросов)
1 Характеристика локомотивного депо Гомель.
2 Организация работы участка ТО-2 грузовых электровозов серии БКГ в локомотивном депо Гомель.
3 Расчет себестоимости обслуживания на участке.
4 Расчет системы освещения участка ТО-2.
5 Экономическое обоснование рационального варианта освещения.
6 Переносные диагностические устройства.
7 Техническая диагностика состояния подвижного состава и перспективы ее развития.
8 Охрана труда и окружающей среды.
Перечень графического материала (с точным указанием обязательных чертежей)
1 Схема структурная технического обслуживания ТО-2 электровозов
2 Линейный график обслуживания и загрузки рабочих участка ТО-2 электровоза БКГ-1 ремонта и график загрузки рабочих.
ОД-210037 (продолжение)
3 Линейный график обслуживания и загрузки рабочих участка ТО-2 электровоза БКГ-2
4 План и поперечный разрез участка ТО-2 локомотивного депо Гомель
5 Расчет себестоимости технического обслуживания электровозов серии БКГ.
6 Освещение участка ТО-2 локомотивного депо Гомель после модернизации.
7 Анализ систем мониторинга состояния ходовых частей подвижного состава на железных дорогах.
Консультанты по проекту (работе) с указанием относящихся к ним разделов проекта
выдачи задания 15 февраля 2021 г.__
Наименование этапов
Дипломного проекта (работы)
Срок выполнения этапов
Характеристика локомотивного депо Гомель
Организация работы участка ТО-2 по обслуживанию грузовых электровозов серии БКГ в локомотивном депо Гомель
Расчет себестоимости ремонта
Выбор энергоэффективного осветительного прибора
Экономическое обоснование выбора осветительного прибора
Проектирование специального оборудования для обслуживания электровоза БКГ
Исследовательская часть комплекс мониторинга технического состояния локомотивов
Охрана труда и окружающей среды
7 исслед.docx
ПОДВИЖНОГО СОСТАВА И ПЕРСПЕКТИВЫ ЕЕ
Рост объема перевозок повышение скорости движения и тоннажа
поездов заставляют обращать все большее внимание на оперативный контроль состояния ответственных частей подвижного состава.
Решение этой задачи может быть достигнуто в частности путем
создания ряда измерительных устройств располагаемых на железнодорожном пути и вблизи него и способных выполнять измерения бесконтактным способом непосредственно при движении поезда.
Обзор систем дистанционного контроля ходовой части подвижного
состава. Системы дистанционного мониторинга являются важнейшими среди технических средств контроля состояния подвижного состава и инфраструктуры. Их совершенствованию и развитию уделяется пристальное внимание со стороны разработчиков производственных компаний и железных дорог во многих странах мира. Это дает возможность прогнозировать появление и
дальнейшее развитие дефектов ходовой части и элементов инфраструктуры
а также последствия для перевозочного процесса и его технического
Автоматизированный контроль параметров колесных пар. Сравнительно недавно на железных дорогах ряда стран стали внедрятся системы контроля параметров колесных пар подвижного состава в движении работающие на принципе бесконтактного оптического измерения. Эти системы позволяют выявлять дефекты колеса задолго до того как они могут стать причиной аварии. С их помощью можно измерять в динамике такие параметры колеса как диаметр высота и толщина гребня ширина изнашиваемой части поверхности катания толщина обода [9].
В таблице 7.1 приведены технические характеристики ряда систем бесконтактного оптического контроля параметров колесных пар. Основными функциональными
элементами данных систем использующих триангуляционный принцип для измерения расстояний до соответствующих участков поверхности колеса являются:
– источник излучения – лазерный диод работающий как правило в видимом диапазоне длин волн (630–670 нм) и реже – в инфракрасном (ИК) диапазоне;
– фотоприемник регистрирующий излучение отраженное от поверхности колеса;
– средства обработки результатов измерения необходимые для определения текущих параметров колеса и их сравнения с требуемыми значениями.
Таблица 7.1 Технические характеристики систем бесконтактного оптического контроля параметров
Профиль колеса высота и толщина гребня
Высота и толщина гребня толщина обода прокат на поверхности катания
Профиль колеса высота и толщина гребня диаметр колеса толщина обода прокат на поверхности катания ползуны
Профиль и диаметр колеса высота и толщина гребня толщина обода
±02; для диаметра колеса ±04
Высота и толщина гребня толщина обода ширина изнашиваемой части поверхности катания
Профиль и диаметр колеса ползуны некруглости колес
Из таблицы 7.1 видно что максимальные значения скорости подвижного состава при которых выполняются измерения заявленные компаниями-производителями систем не превышают 100 кмч. Реально они еще ниже. В большинстве систем зондирующий луч лазера расположенного ниже уровня рельса проектируется под некоторым углом на боковую поверхность колеса. Такая схема реализована в системах Tread View WPMS Wheel Spec GeoTech и ряде других.
Достоинство таких систем – возможность проведения измерений при установленной скорости движения подвижного состава.
Рассмотрим общие принципы построения таких систем на примере WIS (International Electronic Machine США) показанной на рисунке 6.1 [9]. Измерительные триангуляционные модули этой системы размещены в корпусах расположенных с обеих сторон колеса 1 на платформах 2 находящихся ниже уровня головки рельса и прикрепленных к рельсам 3. Между платформой 2 и рельсом 3 размещен демпфер поглощающий удары и вибрации возникающие при прохождении состава. Корпуса снабжены окнами для ввода и вывода излучения.
– внешняя поверхность колеса; 2 – платформа; 3 – рельс; 4 5 – лазеры;
7 – совокупность лучей; 8 – часть колесного центра; 9 – внешняя поверхность обода;
– поверхность катания; 11 – гребень; 12 13 – граничные траектории лучей;
Рисунок 7.1 – Система WIS для контроля параметров колесных пар
Каждый измерительный модуль включает источник зондирующего излучения (лазер) и фотоприемник регистрирующий отраженное от поверхности колеса излучение. Для того чтобы лазерный луч попадал на рассматриваемую поверхность лазер и фотоприемник располагают под определенными углами относительно друг друга.
Из рисунка 7.1 видно что освещается внешняя поверхность колеса 1. Лазеры 4 и 5 проектируют совокупность лучей 6 и 7 освещающих часть колесного центра 8 внешнюю поверхность обода 9 поверхность катания 10 и гребень 11 причем лучи ориентированы таким образом что центральный луч пересекает обод колеса в радиальном направлении а линии 12 и 13 представляют граничные траектории лучей. Отраженные лучи регистрируются фотоприемниками 14 и 15.
Начало измерительного цикла инициируется сигналами поступающими с датчиков положения колеса которые фиксируют его появление в зоне измерений. Сигналы с выходов фотоприемников поступают на специальное устройство захватывающие кадр и преобразующее его в цифровую форму и далее подаются в процессор где производится окончательная обработка результатов и расчет требуемых параметров колеса.
Другой принцип построения систем контроля параметров колесных пар основанный на облучении поверхности катания колеса лазером плоскость луча которого перпендикулярна этой поверхности реализован в таких измерительных системах как Argus (Hegenscheidt-MFD Германия) и EVA (Talgo Group Испания) [10]. Лазер в этом случае располагается ниже уровня головки рельса рисунок 7.2.
Рисунок 7.2 – Схема измерения профиля колеса при помощи системы Argus
Как видно из рисунка 6.2 плоский V-образный луч лазера пересекает профиль колеса а отраженный луч который соответствует линии пересечения регистрируется цифровой фотокамерой. С выхода фотокамеры сигнал поступает в компьютер где осуществляется обработка изображения с целью устранения искажений и выполняется расчет параметров профиля.
Для измерения диаметра колеса используются два лазера с V-образно расходящимся в одной плоскости лучом размещенные ниже уровня головки рельса. Точность измерения параметров колеса при использовании системы Argus составляет 02 мм.
Проведение измерений на высокоскоростных магистралях во многом лимитируется параметрами используемых камер. Появление нового поколения цифровых камер таких например как выпускаемая компанией Kodak ПЗС-матрица KAI-0340DM со скоростью регистрации до 3500 кадрс позволит осуществить мониторинг колеса при скорости подвижного состава свыше 100 кмч. Компания Proximaat сообщила о проведении измерений при скорости движения до 100 кмч за счет использования в своей системе GeoTech камеры с высокой скоростью регистрации (до 500 кадрс). Для повышения точности измерений снимается информация о положении восьми точек поверхности колеса. В результате при различных угловых положениях колеса измеряются восемь значений его диаметра.
В системах контроля параметров колесных пар все большее распространение для обработки информации находят нейронные сети позволяющие повысить чувствительность системы. Так в системе Wheel Scan процессор удаленного компьютера используя алгоритм расчета основанный на применении искусственной нейронной сети производит окончательную обработку данных и вычисление измеренных параметров колесной пары.
Современной тенденцией организации систем мониторинга колесных
пар является интегрирование в рамках единого комплекса функций нескольких модулей обеспечивающих получение полной информации о параметрах колесной пары. Примером этого может служить комплексная система WISE показанная на рисунке 7.3. Кроме устройств измерения профиля и диаметра колеса эта система включает модули определения дефектов колеса и измерение проката и овальности.
– модуль измерения проката и овальности; 2 – модуль определения дефектов колеса;
– модуль WIS для измерения профиля и диаметра колеса; 4 – датчик положения состава;
– помещение (бокс) для установки контрольно-измерительной аппаратуры;
– модуль автоматической идентификации подвижного состава; 7 – канал для прокладки
кабелей и волоконно-оптических световодов
Рисунок 7.3 – Комплексная система контроля колесных пар WISE
Принцип действия модуля определения дефектов основан на использовании электромагнитно-акустических (ЭМА) преобразователей [11]. Первый датчик генерирует волну распространяющуюся в поверхностном слое колеса и обегающую его по окружности при этом параметры волны выбираются с учетом глубины ее проникновения в колесо и чувствительности к дефектам. Отраженный от дефекта сигнал принимается вторым датчиком. Метод по своей сути является бесконтактным и в отличие от традиционного ультразвукового контроля не требует использования согласующих материалов. Размер определяемых дефектов:
– глубина – не менее 0 25 мм;
– протяженность – не менее 635 мм.
Время мониторинга одного колеса составляет 4 мс.
Погрешность измерения овальности колеса составляет не более 01 мм. Весь комплекс измерений проводится при скорости подвижного состава 8 кмч.
Представляет интерес инновационный комплекс внешнего мониторинга WCM (Wheel Condition Monitor) который предназначен для измерения с высокой точностью сил возникающих в пятне контакта колеса с рельсом. Он является гибридной системой использующей представление о состоянии
0 % поверхности катания колеса и позволяет комплексно решать проблему возникновения дефектов. Полученные результаты замеров вертикальной вибрации (биения) рельса при прохождении колеса сравниваются с нормальным уровнем вибрации. Это позволяет нормировать значения различных дефектов обода колеса [12].
Система представленная на рисунке 7.4 состоит из групп датчиков которые крепятся на подошве рельса и расположенных рядом процессоров оценки и обработки замеро.
В комплексах WCM предусмотрена автоматическая адаптация к различным путевым модулям и климатическим условиям при температуре от минус 40 до плюс 70 ºС. Комплекс работает с поездами любой длины движущимися со скоростью от 25 до 130 кмч. При двухминутном интервале попутного следования комплекс способен обрабатывать информацию о 1500 колесных парах выявляя дефекты диаметром до 5 мм.
Рисунок 7.4 – Путевое оборудование комплекса WCM
Система поддерживает работу с радиочастотными датчиками вагонов системы автоматической идентификации подвижного состава (Radio Frequency IDentification – RFID) [13].
Мониторинг состояния буксовых подшипников. Вероятность обнаружения греющихся букс и дефектов приводящих к этому нагреву на сети дорог (при определенной плотности размещения систем мониторинга) характеризует достаточность инфраструктуры защитных мероприятий. При этом следует помнить что каждый предотвращенный сход поезда позволяет избежать потенциального ущерба который минимум на порядок выше затрат на применение систем контроля. В Западной Европе широкое применение получил бесконтактный детектор греющихся букс представленная на рисунке 7.5 типа ТК 99 [14; 15]. В состав детектора входят следующие элементы: путевые датчики; блок обработки и управления; блок передачи данных; известительное устройство.
Рисунок 7.5 – Комбинированный детектор: размещение датчиков контроля
температуры греющихся букс обода колеса и тормозных дисков
Блок обработки и управления монтируют в сигнальном шкафу а на пути устанавливают инфракрасные датчики для измерения температуры буксы и обода колеса а также счетчики осей.
В базовой конфигурации устройства ТК 99 с каждой стороны пути устанавливают по два датчика для измерения температуры букс. Дополнительно отдельным датчиком можно замерять температуру дисковых тормозов а с помощью еще одного датчика – температуру ободов колес для выявления заклиненных тормозов.
Используя прогрессивный метод обработки сигнала при помощи линейной решетки датчиков представленный на рисунке 7.6 оптимизирующий определение азимута источника звука в дальнем поле компания TrackIQ разработала комплекс акустического мониторинга состояния буксовых подшипников RailBAM [16].
Рисунок 7.6 – Оборудование комплекса RailBAM
Эксклюзивным дистрибьютором системы является компания Siemens – партнер TrackIQ. Комплекс позволяет обнаруживать развивающиеся дефекты подшипников на ранней стадии. На поездах могут быть выявлены люфт в подшипнике выработка на внутренней и внешней обоймах дефекты роликов наличие коррозии и другие акустически выявляемые повреждения. В комплексе используется два модуля акустических сенсоров расположенных рядом с путями и напольный блок обработки данных.
При неограниченной длине поезда и скорости движения от 25 до 130 кмч RailBAM может обработать до 1500 осей при межпоездном интервале 1 мин. Результаты контроля полностью совместимы с радиочастотной системой идентификации RFID. Применение RailBAM возможно на одно- и двухпутных линиях и разъездах в любых климатических условиях [17].
Использование сборки из нескольких микрофонов позволяет детектору снимать акустические характеристики подшипников при скорости до 100 кмч а система скоростной обработки данных – распознавать дефекты. Перспективные направления и тенденции развития систем бесконтактного контроля и диагностики подвижного состава. Анализ систем диагностики ходовых частей вагонов позволил выявить основные направления совершенствования и развития систем бесконтактного контроля подвижного состава и обеспечения безопасности движения.
) Все вновь создаваемые системы безопасности строятся на базе микропроцессорной техники. Это позволяет значительно уменьшить объем аппаратуры что в свою очередь сокращает расходы на капитальное строительство снижает потребление электроэнергии. Использование микропроцессоров в устройствах систем управления сделало их более «интеллектуальными» расширило их функциональные возможности. Особое внимание при разработке микропроцессорных систем уделяется вопросам безопасности. Зарубежные фирмы применяют при этом различные решения:
– разрабатывают специализированные безопасные микропроцессоры и резервируют их создавая многоканальные устройства (S
– помещают стандартные ЭВМ в специальные контуры безопасности являющиеся совокупностью аппаратных и программных средств (A
– обрабатывают одну и ту же информацию разными программами и осуществляют сравнение результатов (Westinghouse Великобритания) [18] и т.д.
) Стремление повысить экономическую эффективность железнодорожных перевозок привело к появлению большого числа систем безопасности специально предназначенных для линий с разной интенсивностью движения.
) Поскольку железные дороги Европы тесно связаны между собой существует тенденция применения унифицированных решений в разных странах. Так начато широкое использование цифровой радиосвязи стандарта GSM-R. Этот стандарт используется в системах автоматического управления движением поездов. Причем по каналам цифровой радиосвязи передается не только известительная информация но и команды управления. Широко используются стандарты спутниковой системы глобального позиционирования – GPS. Бортовые устройства локомотивов снабжают приемниками GPS что позволяет с высокой точностью определять координаты и скорость движения транспортных средств. Поскольку повышение скоростей движения требует получения более оперативной информации о состоянии подвижного состава то существует тенденция переноса «интеллектуальной составляющей» этих систем на поезд а также расширения функциональных возможностей систем контроля отдельных ходовых узлов до систем комплексного контроля с ранней диагностикой и прогнозированием технического состояния подвижного состава.
Таким образом можно полагать что в настоящее время на железных дорогах Западной Европы и США наметились определенные тенденции в развитии систем и средств ранней диагностики ходовых частей вагонов которые заключаются в следующем.
) Наибольшее распространение получили системы выявления предаварийного состояния греющихся буксовых узлов на основе точного бесконтактного измерения температуры перегрева датчиками ИК-излучения.
) Средства выявления греющихся предаварийных буксовых узлов дополняются средствами ранней задолго до появления перегрева диагностики дефектов (повреждений неисправностей) буксовых подшипников а также средствами диагностики с точным измерением параметров механических дефектов тележек и колес ускоряющих повреждения подшипников завершающиеся отказами буксовых узлов.
) Более сложные дорогостоящие сетевые посты точной ранней диагностики обеспечивают совместно с системой прогнозирования контроль поездов в зоне обслуживания одного поста в несколько тысяч километров при стоимости комплекта средств акустического контроля подшипников например системы TADS 450 тыс. дол. В постах комплексного контроля высокая эффективность достигается:
– интеграцией ряда систем и технологий диагностики различных объектов: подшипников колес тележек тормозов;
– объединением постов комплексного контроля в сети централизованного сбора обработки и анализа данных с прогнозированием развития неисправностей и повреждений вагонов и тележек во взаимодействии с системой идентификации подвижного состава в масштабах железной дороги или сети дорог;
– более точным прогнозированием ситуаций развития дефектов подшипника во взаимосвязи с неисправностями и повреждениями тележек и с дефектами колес что обеспечивается информационными технологиями централизованной комплексной обработки данных с формированием баз данных для подразделений обслуживания и ремонта подвижного состава.
) Технически созданы все условия для организации системы предупредительного технического обслуживания и ремонта подвижного состава не по сроку службы или пробегу а по фактическому состоянию ответственных компонентов ходовых частей вагонов: буксовых подшипников колес и колесных пар двухосных тележек.
) Акустические лазерные оптические видео цифровые информационные многоуровневые (сетевые) «высокие» технологии осваиваются с привлечением аэрокосмических оборонных и других предприятий специализирующихся на создании конкретных технологий и работающих по оборонным стандартам.
3 пункт.docx
Себестоимость ремонта – один из важнейших показателей характеризующих качественную сторону деятельности отделения. В ней отражается степень использования трудовых и материальных ресурсов результаты внедрения новой техники и технологии уровень организации труда и производства а также рационального управления.
Годовые затраты участка (отделения) на обслуживание тех или иных сборочных единиц локомотива
где Зо – затраты на основную заработную плату производственных рабочих бел. руб.;
Дз – затраты на доплаты и надбавки компенсационного характера бел. руб.;
Зд–затраты на дополнительную заработную плату производственных рабочих бел. руб.;
Ос – начисления на заработную плату бел. руб.;
М–затраты на потребляемые материалы и покупные изделия (без НДС) бел. руб.;
Пс – затраты на полуфабрикаты собственного изготовления бел. руб.;
Сэ – затраты на потребляемые энергоресурсы (без НДС) бел. руб.;
Соб – затраты на эксплуатацию и содержание оборудования бел. руб.;
Ао – затраты на амортизацию оборудования бел. руб.;
Сн – накладные и общехозяйственные расходы бел. руб.
Затраты на основную заработную плату производственных рабочих
где Т – месячная тарифная ставка бел. руб.;
kпр – коэффициент учитывающий премию; kпр = 03.
Месячная тарифная ставка включает расчетную тарифную ставку и доплату по контракту
где Тр – расчетная тарифная ставка бел. руб.;
Тк – доплата по контракту бел. руб.; принимается в размере 50% от Тр
Расчетная тарифная ставка
где Т1 – месячная тарифная ставка I разряда бел. руб.; для локомотивных депо при-
нимаем Т1 = 195 бел. руб.;
kт – коэффициент повышения тарифных ставок по технологическим видам
работ бел. руб.; для ремонта подвижного состава
kср – средневзвешенный тарифный коэффициент работ участка
ki – тарифный коэффициент i-го разряда
Доплаты и надбавки к тарифной заработной плате компенсационного характера
где Дi – доплата i-го вида (за непрерывный стаж работы и профессиональное
Двр – доплата за работу во вредных условиях труда р;
При ремонте в зависимости от стажа работы доплаты принимаются
–30 % (для дальнейшего расчета надбавка за непрерывный стаж работы принимается в размере 10 %); доплата за профессиональное мастерство с учетом средневзвешенного тарифного коэффициента работ участка – 20%; доплата за работу во вредных условиях труда – по классу 3.2.
Дополнительная заработная плата производственных рабочих составляет примерно 10 % от суммы основной заработной платы доплат и надбавок компенсационного характера
Начисления на заработную плату принимают от ФОТ:
– в фонд социальной защиты населения – в размере 34 %;
– страховой взнос по обязательному страхованию от несчастных случаев на производстве и профзаболеваний – в размере 06 %.
Начисления на зарплату при этом
Затраты на потребляемые материалы (смазку керосин ветошь) и покупные изделия определяются как
Примерные затраты на полуфабрикаты собственного изготовления
Величину технологических затрат электрической энергии на ремонт ТО-2 определяют как
kз коэффициент загрузки оборудования по мощности;
kс коэффициент загрузки оборудования по времени.
Таблица 3.1 – Определение технологического расхода электрической энергии на ремонт ТО-2
Коэффициент загрузки по мощности
загрузки по времени х10-4
Устройство для подачи масла в МОП
Продолжение таблицы 3.1
ПЗУ «Передвижное зарядное устройство»
Доктор-100ПГ «Система контроля и диагностики токоприемников»
Э = (410308510-41989) + (35103081510-41989) +
+ (910308510-41989) + (110308310-41989) = 1917396 Вт.
Затраты на потребляемые энергоресурсы сведены в таблицу 3.2. и 3.3.
Таблица 3.2–Затраты на энергоресурсы при ТО-2 БКГ-1
Расход на единицу секции
Общая стоимость энергоресурса
Электрическая энергия кВт ч
Таблица 3.3 –Затраты на энергоресурсы при ТО-2 БКГ-2
Амортизационные отчисления
где Вст стоимость оборудования бел. руб.;
а норматив амортизации i-го вида оборудования % [4].
Амортизационные отчисления посчитаны ранее в таблице 2.6 и составляют
Ао = 1850 бел. руб.
Отчисления на эксплуатацию оборудования
Соб = 01 18500 = 1850 бел. руб.
Накладные и общехозяйственные расходы участка (отделения)
Сн = 16 9272892 = 14836627 бел. руб.
Таким образом годовые затраты участка ТО-2 на ремонт электровоза БКГ-1
Сг = 475227067 бел. руб.
Себестоимость ремонта ТО-2 электровоза БКГ-1
Себестоимость ремонта электровоза БКГ-2 рассчитывается аналогично по формулам (3.1) – (3.16) полученные данные заносим в таблицу 3.4.
Таблица 3.4 – Структура себестоимости обслуживания ТО-2 электровозов серии БКГ
Расходы на ремонт продукции
Величина расходов бел. руб.
Основная заработная плата
Добавки и надбавки компенсационного
Дополнительная заработная плата
Отчисления на социальные нужды
Материалы и покупки изделия
Полуфабрикаты собственного изготовления
Энергоресурсы на технологические цели
Содержание и эксплуатация оборудования
Амортизация оборудования
Накладные и общехозяйственные расходы
По итогам экономического расчета себестоимость ТО-2 электровоза БКГ-1 составила 1697 бел. руб. и 990 бел. руб. для электровоза БКГ-2.